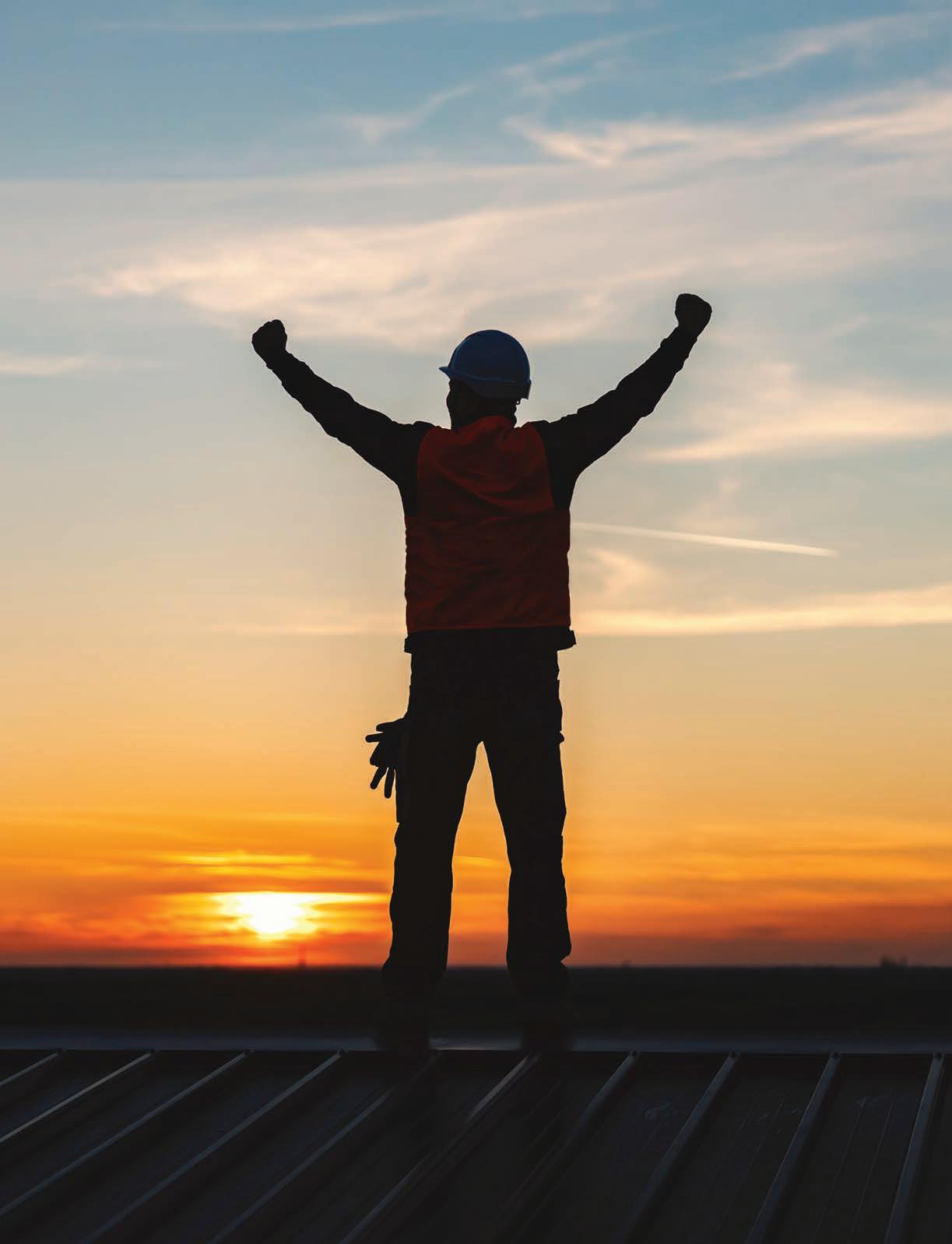
ELECTRIFYING DEVELOPMENTS IN MOBILE LIFT EQUIPMENT
ENHANCING THE WORKFORCE DIVERSITY, EQUITY, INCLUSION
ROBOTS & AUTOMATION AMPLIFYING CAPABILITIES
ELECTRIFYING DEVELOPMENTS IN MOBILE LIFT EQUIPMENT
ENHANCING THE WORKFORCE DIVERSITY, EQUITY, INCLUSION
ROBOTS & AUTOMATION AMPLIFYING CAPABILITIES
Tired of project delays, communication gaps, and inefficient workflows?
Time to try Bluebeam, the most easy-to-use solution for PDF markups, digital workflows, and effective project collaboration.
Collaborate from anywhere
Securely access documents on any device, digitally collaborate in real time, and keep teams in sync from start to finish
Improve efficiency and productivity
Automate time-consuming tasks with AI-powered tools, and stay productive with expert technical support and training resources
Take full control of projects and workflows
Customize and share tool sets for infrastructure projects, or build custom workflows that simplify end-to-end tasks and maximize ROI
www.on-sitemag.com
In their push to reduce the cost of housing, government incentives are likely to have an opposite effect on affordability, at least in the short-term, with the impact of rising construction costs being felt in housing, as well as in Canada’s ICI and civil construction segments.
A recent RBC Economics report suggests that a million of the 1.9 million new households expected to be created by 2030 will not be able to buy a home if affordability stays where it is, and 40 per cent of these households won’t be able to afford rent either.
“The current affordability crisis has been driven by a massive undersupply of housing in the face of booming demand,” explained RBC Economics’ Robert Hogue.
To help with affordability, the federal government put forward a housing plan for 3.87 million new homes by 2031, or 2 million more than what would typically be built by 2031. In addition to this acceleration of residential building, new roads, sewers, plazas, schools, and so forth will be needed to support this growing population, bringing even more construction activity forward.
The timing for this extra activity may not be ideal, however, as many segments of the non-residential industry are already busy and have healthy backlogs. As more segments start to pick up, demand for labour and materials will bring additional cost strains to all segments.
Increases to the industry’s labour pool are part of the federal plan, but finding new workers is something that the industry has struggled with for decades, and importing workers actually adds to the housing crisis.
So, where does that leave us?
Get the latest construction news!
Follow us on @OnSiteMag
Well, despite having to pay more for materials and compete harder for workers (and yes, we need to encourage immigration of trade professionals), having the ability to choose your projects is not a bad spot to be in.
Ensuring that you have the personnel and subcontractors available to tackle these projects could be a challenge, however, so keep the good people you have. Perhaps check out Jesse Unke’s column, as well as our DEI Summit coverage for some tips. And keep a close eye on your costs so that there are still a few dollars of profit left at the end of each project.
Until next time, stay safe and do good work.
Adam Freill / Editor afreill@annexbusinessmedia.comREADER SERVICE
Print and digital subscription inquiries or changes, please contact Angelita Potal
Email: apotal@annexbusinessmedia.com
Tel: (416) 510-5113
Fax: (416) 510-6875
Mail: 111 Gordon Baker Road, Suite 400, Toronto, ON M2H 3R1
PUBLISHER | Peter Leonard (416) 510-6847 pleonard@on-sitemag.com
EDITOR | Adam Freill (416) 996-2391 afreill@annexbusinessmedia.com
MEDIA DESIGNER | Lisa Zambri lzambri@annexbusinessmedia.com
ASSOCIATE PUBLISHER | David Skene (416) 510-6884 dskene@on-sitemag.com
ACCOUNT COORDINATOR | Kim Rossiter (416) 510-6794 krossiter@on-sitemag.com
AUDIENCE DEVELOPMENT MANAGER | Urszula Grzyb (416) 510-5180 ugrzyb@annexbusinessmedia.com
CEO | Scott Jamieson sjamieson@annexbusinessmedia.com
Established in 1957, On-Site is published by Annex Business Media 111 Gordon Baker Road, Suite 400, Toronto, ON M2H 3R1 Publications Mail Agreement No. 40065710
ISSN: 1910-118X (Print) ISSN 2371-8544 (Online)
SUBSCRIPTION RATES Canada $50.49 CAD per year, United States $115.26 CAD per year, Other foreign $139.23 CAD, Single Copy Canada $13.50 CAD. On-Site is published 5 times per year except for occasional combined, expanded or premium issues, which count as two subscription issues. Occasionally, On-Site will mail information on behalf of industry-related groups whose products and services we believe may be of interest to you. If you prefer not to receive this information, please contact our circulation department in any of the four ways listed above.
Annex Business Media Privacy Officer privacy@annexbusinessmedia.com Tel: 800-668-2374
Content copyright ©2024 by Annex Business Media may not be reprinted without permission.
On-Site receives unsolicited materials (including letters to the editor, press releases, promotional items and images) from time to time. On-Site, its affiliates and assignees may use, reproduce, publish, re-publish, distribute, store and archive such unsolicited submissions in whole or in part in any form or medium whatsoever, without compensation of any sort.
DISCLAIMER This publication is for informational purposes only The content and “expert” advice presented are not intended as a substitute for informed professional engineering advice. You should not act on information contained in this publication without seeking specific advice from qualified engineering professionals.
MEMBER OF
Canadian-owned Béton Provincial Ltée has expanded its footprint with the purchase of concrete and cement assets in Quebec, Newfoundland and Labrador, as well as in the state of New York. The company, the largest Canadian-owned entity in the concrete and cement sector, has concluded a transaction with CRH Canada Group Inc. adding cement plants and terminals, ready-mix concrete plants, and quarries to its operations, which will bear the Ciment St-Laurent/St. Lawrence Cement brand.
In addition to the Ash Grove cement plant in Joliette, Que., as well as the activities of Demix Béton and certain activities of Demix Agrégats, the company now owns six cement terminals, including three in Newfoundland and Labrador, two in the
Greater Montreal, and one in Solvay, NY; nine ready-mix concrete plants, including seven in Greater Montreal and a pair in the Quebec City region; and two quarries near Montreal, located in Saint-Jacques-le-Mineur and Mirabel.
The company says all cement activities will be operated under the name Ciment St-Laurent/St. Lawrence Cement, reviving a historically recognized brand in Quebec and Eastern North America.
“This significant milestone highlights the journey undertaken by Béton Provincial since its foundation in Matane [Québec] in 1960. We are very proud to see that a
100 per cent Canadian-owned company is now making its mark alongside the major multinational players in its industry,” stated company president André Bélanger.
With an extensive network of strategic contact points, Béton Provincial says it now operates one of the largest distribution networks in eastern North America, adding that the acquisition has strengthened the vertical integration of its operations.
Béton Provincial employs over 2,700 people at its facilities, which include 94 ready-mix concrete plants, five precast concrete plants, a cement plant and 21 asphalt plants.
Retrofitting Canada’s residential, commercial and institutional building stock to incorporate sustainable fuel sources, technologies and materials could require as many as 57,000 additional construction workers and generate more than $81 billion in new construction investments by 2032, says BuildForce Canada in its latest labour report, Building a Greener Future: Estimating the impact on construction labour demands from transitioning buildings in Canada away from fossil fuels
The paper considers the implications of retrofitting existing buildings to improve their energy efficiency and reduce their carbon footprints in support of the Government of Canada’s goals to achieve net-zero greenhouse gas emissions by 2050. This is occurring at a time when construction labour markets have been operating at, or near, full capacity in many regions of the country.
The report was developed with input from industry associations and businesses engaged in the retrofit work. It models a scenario in which two types of green-building activities are performed: converting space and water heating equipment from fossil fuels to electric power sources, and retrofitting buildings to improve energy efficiency and minimize heat loss.
The study found that as many as 16,300 new jobs relating to fuel switching could be created in the residential sector alone, while a further 40,600 may be created to perform energy-efficiency
retrofits. The labour needs to accommodate the conversion of, and renovations to, Canada’s stock of commercial and institutional buildings would represent an additional strain to the labour pool, explained BuildForce.
“The challenge for the construction sector is that this transition is being considered at a time when non-residential construction demands are already reporting peak or near-peak levels in many provinces, and when the residential construction sector is confronted with the additional challenge of building millions of new housing units to address Canada’s housing crisis,” said Tania Johnston, chief executive officer at the Mechanical Contractors Association of Canada.
The expanded system of the Trans Mountain Pipeline reached its commercial commencement milestone at the beginning of May. In late April, the Canada Energy Regulator (CER) approved the final leave to open (LTO) application, meaning that the pipeline is now authorized to carry crude oil from Trans Mountain’s Edmonton Terminal, located in Strathcona County, Alta., to its Westridge Marine Terminal in Burnaby, B.C.
Mechanical completion of the pipeline happened on April 30 and, with both the existing and expanded pipelines now able to transport crude oil, tankers were expected to be able to receive oil from Line 2 by mid-May (past press time).
“Trans Mountain has demonstrated that challenging, long linear infrastructure can be built in Canada,” said Dawn Farrell, president and CEO of Trans Mountain Corporation. “With our project management team and contractors, we were able
193 kilometres of reactivated pipeline, 12 new pump stations, 19 new storage tanks, and three new berths at Westridge Marine Terminal in Burnaby. We did this while adhering to the highest environmental, safety and social standards including respecting and working with local First Nations and Métis communities throughout the entire process.”
In a joint statement, Alberta Premier Danielle Smith and that province’s Minister of Energy and Minerals, Brian Jean, stated, “Alberta is celebrating an important achievement for the energy industry – the startup of the twinned Trans Mountain Pipeline expansion project [TMX]. It’s great news for Albertans and Canadians, as this will welcome a new era of prosperity and economic growth.”
The pair pointed to the export opportunities the province will be able to meet, adding, “We are excited that Canada’s
than a decade can now bring oil from Edmonton to tidewater in B.C. This will allow us to get our energy resources to Pacific markets, including Washington State and California, and Asian markets like Japan, South Korea, China and India.”
Moving quickly during the off-season brings major upgrades to the home of the Toronto Blue Jays.BY ADAM FREILL
Some teams think of heading south to find the sun once baseball season wraps up, but not the team at PCL Construction, which sprang into action to ensure that the home of Canada’s MLB team would have fresh new look to start the 2024 baseball season.
Almost as soon as the 2023 Toronto Blue Jays season wrapped up, construction ramped up on Phase 2 of what has been a multi-year renovation project aimed at progressively transitioning the 35-year-old Rogers Centre stadium to feel more like a ballpark. This winter, the original 100-level infield seating bowl was fully demolished from foul pole to foul pole, getting redesigned for a baseball-first viewing experience. Along with changes to lower-bowl seating, the demolition and excavation that were part of the almost $400-million renovation also made room for a new clubhouse and player facilities.
“We have now utilized every square foot of space under our bowl,” said Sanj Perera, director of project development and construction management with the Toronto Blue Jays. “The majority of the player clubhouse is now under the bowl, in addition to a new umpires’ area and three new premium clubs.”
PCL broke ground on the second phase of the renovations on October 13, 2023, knowing that they had to complete the demolition and rebuild in time for opening pitch of the Jays’ home opener in April. The work saw an average of 350 tradespeople on-site daily, who logged some 400,000 worker hours.
“Planning a project of this magnitude took considerable effort. Working within an
existing facility and infrastructure – which has undergone only minor renovations over the last 30 years – required a lot of design and engineering,” explained Perera. “The project itself had no certain start date, but a definitive end date.”
They had to be ready for first pitch.
“There was no option for a deadline extension with the home opener already set,” said Perera. “To undertake demolition, excavation, foundations, infrastructure, steel and precast in three months meant that we only had the remaining three months to complete the amenities beneath the bowl. This was a fast-tracked project and required everyone’s pledge for success.”
“With a staggering level of coordination and activity averaging 350 workers on site daily, six to seven days per week over the past six months, our workforce was fuelled by the passion of being part of a project that provides a sense of community,” said Monique Buckberger, vice-president and district manager for PCL Constructors Canada.
Working with many of the subcontractor partners who gained experience during
Phase 1 helped keep the project moving, he added. Between the two phases of the project there were roughly 32 million pounds of materials removed and recycled, with 6,500 cubic metres of concrete poured between the two off-seasons, along with 3.3 million pounds of structural steel installed. The recycling efforts earned the Toronto Blue Jays the MLB 2023 Green Glove award for the organization’s commitment to diverting waste from landfills.
“We were able to achieve over 93 per cent waste diversion due to recycling during the renovation project,” said Perera. “Although we have been named as finalists for this award, it is our first time receiving the top honour.”
“Reimagining the home of the Blue Jays required an astonishing scope of work in a short timeframe,” said Mark Shapiro, president and CEO of the Toronto Blue Jays. “To build a sustainable championship organization, we needed a home that is specifically for baseball.”
Sensera Systems offers technology that redefines jobsite intelligence. Our portable solar and cellular solution is easy to install, use, and scale, providing real-time site visibility and insights. We empower you to build confidently, ensuring your project is safe, secure and successful.
Break away from the ordinary ‒ choose Sensera Systems and confidently manage your next project.
“ Partnering with Sensera Systems enhances the stringent monitoring and safety standards demanded by busy construction projects. We’ve been impressed with Sensera Systems’ products and services and are excited about where the technology can go to further our vision for the smart and integrated jobsite of the future.
Mark Bryant CIO, PCL Construction “www.senserasystems.com | 800.657.0437 | sales@senserasystems.com
A selection of data reflecting trends in the Canadian construction industry
Month over month, investment in building construction increased 4.5 per cent to $20.4 billion in March, reports Statistics Canada. The residential sector rose 5.4 per cent to $14.3 billion, while the non-residential sector posted a 2.3 per cent gain to land at $6.1 billion. Multi-unit residential investment was up 4.4 per cent to $7 billion, with the biggest gains coming in Ontario and British Columbia.
Non-residential construction investment was up across all components. Industrial investment rose 3.1 per cent to $1.3 billion, and investment in the commercial component rebounded after eight consecutive months of declines to post a two per cent gain, reaching $3 billion. Notably, investment in the institutional component grew 2.1 per cent to reach $1.8 billion in March, a record high. The monthly increase recorded in March was the ninth monthly increase in a row.
Canada’s construction sector posted the largest reduction in employment across all sectors in Statistics Canada’s April Labour Force Survey. Employment in the sector fell by more than 11,000 positions. Despite the drop from March, Canada’s overall employment picture grew for the month, with the economy gaining 90,000 workers. According to the seasonally adjusted figures used by Statistics Canada in its report, which it uses to analyze for trends and cyclical movements, the construction sector had 1,589,800 workers in April, down from 1,600,900 in March, and off from April of last year by 5,100 positions. Without the seasonal adjustment, the sector reported in with 1,547,600 workers in April, higher than the raw March figure, but well off the non-adjusted 12-month high of 1,654,200 reported this past August.
Total Employment in Canada 20,373,400
Investment in non-residential construction, March 2024 (in $Millions)
Employment 1,547,600
SOURCE: STATISTICS CANADA, THE DAILY, AND TABLE 14-10-0022-01.
The commercial segment was the only component to buck the trend of falling permit values in March. Looking at the latest month over month figures, as reported by Statistics Canada in mid-May, the total value of building permits in Canada decreased 11.7 per cent to $10.5 billion in March. Construction intentions in the non-residential component declined 16.7 per cent to $4 billion, while the residential sector contracted by 8.3 per cent to land at $6.5 billion. Declines were observed in all components except for the commercial component, which rose 5.8 per cent.
A lack of major industrial permits issued in March, compared with February, was a major driver of the retreat in the non-residential sector. The industrial component fell 46.1 per cent to come in at $736.9 million. The institutional segment was also in decline, falling 22.2 per cent to land at $1.03 billion. The commercial component’s growth helped temper the declines in the non-residential sector as it reported in at $2.2 billion for March. On the residential side, 16,800 new multi-unit dwellings and 4,200 new single-family homes were authorized for the month. Between April 2023 and March 2024, a total of 260,200 new units were authorized. Despite the new permits, permit values for both single-family and multi-family dwellings were down.
ever on
The crowds were out in full force for the 26th edition of the National Heavy Equipment Show as more than 13,400 heavy equipment industry professionals made the trip to the International Centre in Mississauga, Ont., in mid-April for the two-day, sold-out event.
“To say this edition surpassed our expectations would be an understatement,” stated national show manager, Mark Cusack. “Our exhibitors really set the bar high, and we can’t thank everyone enough for coming out.”
The 2024 event expanded to include the addition of another hall in the exposition centre, making the show one of the largest editions in recent years, reported Master Promotions Ltd., organizers of the show.
In addition to the machines, supplies and services on display on the show floor, this year’s event also featured the Ontario Asphalt Pavement Council’s Spring Operations Seminar and Canadian Associated Equipment Distributors’ industry breakfast.
The next edition of the NHES show is set to take place in the
The 2024 edition of the Atlantic Heavy Equipment Show attracted thousands of visitors to the Moncton Coliseum Complex over the course of the two-day event at the end of March. Those attending were able to explore the latest trends and innovations within the forestry and heavy equipment industries, including the newest models of machinery, machine and project technologies, as well as to have conversations with
spring of 2026. Complete details will be posted on the National Heavy Equipment Show website, www.nhes.ca.
dealers and vendor staff.
“We are blown away by the response to this year’s edition,” stated Mark Cusack, national show manager at Master Promotions Ltd., which presents the event every two years. “The industry was out in full force… we cannot thank everyone enough for coming out and making this one of the best ones yet.”
months leading up to the event and featured both indoor and outdoor exhibits showcasing products and services across all parts of the industry.
The show floor was sold out in the
The show will return to the Moncton Coliseum in the spring of 2026, when the event will mark its 40th anniversary. Watch for details to be shared at www.ahes.ca.
www.wirtgen-group.com/technologies
The mobile lift equipment sector includes telescopic and articulating boom lifts, scissor lifts and mobile cranes. Broad as the category is, new lift equipment is becoming progressively more high-tech, with sensors, software, cameras and data management systems. Electrification continues to be a major trend as well.
“Over the last decade, but especially in the past few years, the pace at which things are electrifying has really accelerated … While there is still a place for diesel-powered equipment, there are a number of factors that are driving a move to electric,” says Zach Gilmor, senior product manager at Genie.
These factors include stricter noise and pollution regulations, jobsite requirements, corporations setting sustainability goals and “lower total cost of ownership than diesel-powered machines, when the technology is implemented thoughtfully and in the right way,” explains Gilmor.
Customers concerned about environmental impact are embracing features and formats, including zero emission electric equipment, that reduce their carbon footprint, echoes Corey Connolly, senior product manager for Skyjack.
As for data management, “equipment owners are becoming increasingly sophisticated when it comes to using data to manage their fleets and maintain equipment,” notes Gilmor.
Other industry trends include compactness and an emphasis on operator comfort.
“We are seeing the sub-compact class of machine starting to gain in popularity,” says Lee Tice, product manager for telehandlers, mini-excavators, skid steers and compact loaders at JCB.
“Comfort of the operator inside the cab is a big one as well,” continues Tice. “People are running these things eight hours, 10 hours a day, so the operators are in the machine for longer periods of time. So, it really comes down to keeping the operator comfortable. If he’s comfortable in the machine, he’ll want to stay in there longer.”
In terms of future developments, JCB has extended its vision beyond electric, producing a telehandler prototype powered by an internal hydrogen combustion engine.
With change afoot in this sector, here’s a look at what’s new and noteworthy in mobile lift equipment.
Bobcat has launched four new telehandlers in recent years: the TL519, TL619, TL723 and TL923.
“The Bobcat R-Series telehandler lineup offers the extended
reach and superior lift capacity of a heavy-duty telescoping boom combined with a range of attachment offerings for leading versatility,” says Mike Fitzgerald, marketing manager at Doosan Bobcat.
With a 74 hp engine, the TL519 is compact at six feet wide and 13 feet long and weighs less than 10,000 pounds, making it well-suited for tight quarters. The 10,428-pound TL619 also has a 74 hp engine, while both telehandlers feature a Power Bob-Tach attachment mounting system, which allows operators to change non-hydraulic attachments from within the cab.
The 100-hp, 16,163-pound TL723 and 135 hp, 18,158pound TL923 both feature a wraparound rear window that provides excellent rear and side visibility. Also included is a Power QuickTach attachment mounting system. Operators in the cab “push a button to retract and release the pins to quickly secure an attachment,” explains Fitzgerald.
All Bobcat R-Series telehandlers have Tier-4 turbo charged engines, four steering modes and five operation modes, ECO mode, Smooth Drive mode, Dynamic Drive mode, Flex Drive mode and Advanced Attachment Control mode. R-Series telehandlers also feature automatic tilt positioning for attachments, intuitive joysticks and heavy-duty hydrostatic transmissions.
The TL619, TL723 and TL923 models are equipped with automatic ride control, which reduces material spillage and enables operators to travel at higher speeds to increase productivity.
Genie recently introduced a new Micro Access Deck Kit, as well as carriage options, attachments, a track system, and a virtual training program for telehandlers.
Designed for use with micro scissor lifts in space-restricted areas, the Micro Access Deck “provides a secondary surface to work from, elevating operators 22 inches/0.56 metres above the platform floor,” states Christian Dube, the company’s senior global product manager.
The Micro Access Deck is designed to boost productivity and safety and eliminates the need to rent a second lift. An existing version of the Deck is already in use with standard-size slab scissor lifts.
The manufacturer introduced new carriage options and attachments for its GTH telehandlers at this year’s ARA Show in New Orleans, including a multi-purpose auger tool for the GTH-5519 telehandler among the new wares.
“For the larger GTH-636, GTH-844, GTH-1056, and GTH-1256 models, contractors can swap forks for a truss boom and two multi-purpose buckets. In addition, two new carriage options increase load handling productivity and flexibility,” adds Amalija Kopac, senior global product manager at Genie.
Genie’s truss boom attachments are used to lift and place
heavy or bulky beams, columns and utility poles, and can position roof trusses during construction and renovation work.
Genie also introduced Next Generation TraX, an updated version of the company’s four-point track system for boom lifts, at the show. Featuring four independent tracks and oscillating axles, Next Generation TraX is designed for use on uneven ground.
Electrification also continues to be a major focus for the manufacturer.
“Genie has been at the forefront of electrifying our industry,” says Gilmor. “In fact, more than 70 per cent of our product portfolio is already electrified [hybrid and electric] or offers an electrified equivalent.”
Electrified equipment includes the company’s Lithium-Ion GS scissor lifts, and hybrid S-60 FE, and electric S-60 DC boom lifts.
Genie also has a new Virtual Reality (VR) training program for its Z-45 FE articulated boom lift, bringing even more electronics into its ecosystem. Using a headset, operators can learn how to control the boom lift virtually.
While the Z-45 FE was specifically chosen for this program because articulated boom lifts are challenging to master, “the hazard awareness portion of the training is applicable to any type of equipment,” notes Scott Owyen, the company’s training director.
Skyjack, a division of Linamar Corporation, has been introducing new electric lift equipment and updating its telematics system.
Last year, the company announced the launch of the SJ3213 micro and SJ3219 micro electric scissor lifts. The lifts offer raised indoor platform heights of 13 and 18 feet one inch, respectively, and optional raised outdoor platform heights of 12 and 16 feet, respectively. Both have a 500-pound platform capacity.
Small enough to fit into passenger elevators and cramped workspaces, these micro lifts are a good choice for indoor locales with “sensitive type flooring” that clients prefer to keep intact, says Connolly.
But changes to the lineup are not just focused on the smaller end. “As of the beginning of this year, we are now in full production for our standard size electric scissor lifts,” says Connolly.
The brand’s new full-size E-drive scissor lifts feature improved torque and runtime per charge versus previous models. Like their micro counterparts, these machines don’t give off any emissions and operate at low volume.
Last year, Skyjack introduced Elevate Live 2.0, a new version of its Elevate Live telematics solution. Version 2.0 features an improved interface and gives operators easier access to performance metrics, manuals and technical data, says the manufacturer.
JCB has developed what it says is a potentially revolutionary Loadall telescopic handler prototype powered by an internal hydrogen combustion engine.
This zero-emissions, low-noise telehandler is a “really exciting thing for us,” says Tice. “We’ve seen a couple hydrogen fuel cell pieces of construction equipment in the market, but when it comes to hydrogen combustion engines, I’m not sure anyone else is doing that.”
The hydrogen prototype reflects JCB’s keen interest in fossil
Optimize your cash flow and reduce delays and downtime so you can complete your projects on time and on budget.
Rent from our Construction Equipment and get access to the latest technology in efficiency and reliability for all your needs. dedicated Rental Fleet of new Volvo
Smart commercial Account
Finance your rental today by using your Volvo Smart Commercial Account. Find out more and apply now.
fuel alternatives. A few years ago, the company launched the 505-20E compact telehandler, “the first compact electric telehandler to market, to my knowledge,” says Tice.
While proud of its electric heritage, JCB discovered that electrification does not scale well in all machine types. “When we start talking mid-range machines, larger excavators, and heavy-line equipment, maybe electric’s not the solution,” says Tice. “So, we started looking at some other solutions, such as hydrogen fuel cells.”
Hydrogen lift equipment won’t become commercially available until sufficient infrastructure exists to support such machines, he notes, but the exploration of the technology is an exciting development for the segment.
Beyond its work with hydrogen, JCB has been working to improve safety and visibility in its existing mobile lift fleet. Camera systems offering bird’s eye, side and rear-views are becoming ubiquitous on JCB equipment and the company’s telehandlers will soon feature pulse radar. Pulse radar serves as a “backup alarm” by sensing and warning operators if they are “getting too close to a pole or someone walks behind you while you’re backing up,” explains Tice.
JLG has introduced an all-electric scissor lift and new telehandlers, and has made its ClearSky Smart Fleet connectivity solution
standard on most new equipment.
ClearSky uses Internet of Things (IoT) technology to collect, receive and analyze data. It is “more than just a telematics system,” says Ara Eckel, director of product management –connected solutions at JLG.
The system offers a machine location feature, status updates on battery and fuel level, a built-in analyzer for wireless diagnostics, and access to digitized documents, manuals, and other important information.
In 2023, the company introduced the 6034 and 6042 SkyTrak telehandlers and will launch an updated 8042 SkyTrak telehandler this year. All three machines have a hydrostatic transmission for ease of operation, an electric over hydraulic joystick for enhanced multifunction capabilities, and an advanced control system featuring a Load Stability Indication (LSI) option.
The LSI system is “one part of a comprehensive three-part SmartLoad Technology package” that also includes automatic attachment recognition and a load management information system, explains John Boehme, senior product manager for telehandlers at JLG.
The 6034 has a maximum lift height of 34 feet, five inches, and maximum lift capacity of 6,000 pounds, while the 6042 has a 42-foot, four-inch maximum life height and 6,000 pound lift capacity. The 8042 can lift 8,000 pounds with a maximum lift height of 42 feet, four inches.
JLG also recently introduced the fully electric DaVinci Series AE1932 scissor lift, with a 19-foot platform height, 606-pound platform capacity, a single battery designed to last the lifetime of the machine, and no hydraulic components, which the company pointed out translates into zero leaks.
Nate Hendley is a freelance writer and author, and is a regular contributor to On-Site Magazine.
Stay ahead with Dynapac’s decades of expertise in compaction and paving. Our dedicated and purpose-driven line of equipment excels in confined spaces, small parking lots, and landscaping projects. Whether you're working with sand, soil, rock, or asphalt, contractors nationwide prefer Dynapac’s soil and asphalt rollers, plate compactors, and rammers.
A few simple steps could add double-digit returns from your machinery.BY FRANK MCGILLICUDDY
Most business owners understand that they should not own the land and buildings where their business operates, meaning inside your operating business corporation (OpCo), but did you know that once you also separate the ownership of equipment from your OpCo, you reduce risk of loss from legal action against the OpCo while also adding improved wealth creation? Owning the equipment inside your OpCo may be costing you money and creating unnecessary legal risk.
There are some simple steps necessary to create the structures that allow you to take financial advantage of this arrangement, and as long as your company is financially sustainable, it opens the door to an extra stream of income that you may not realize is available. Keeping in mind that this approach will only rarely be relevant for a start-up, let’s look at how a company can arrange their business to take advantage of this net-positive structure.
This first step is to establish a Limited Liability Partnership (LLP). The group of Limited Partners (LPs) could include yourself, your family members, your Holding Company (HoldCo) or other individuals that you trust to be in business with you. There also has to be an arm’s-length person who fills the role of General Partner (GP). They have the exclusive duty to run the LLP. The LPs may not involve themselves in running the LLP, so the choice of GP will be key.
Your equipment — that heavy machinery that makes you money — will be purchased by this LLP. Of course, if you’re going to put the equipment to be leased into an LLP, the LPs collectively have to be able to invest (or borrow to invest) enough money for the LLP to purchase the equipment. Any interest paid on such borrowing is tax-deductible.
The GP will purchase the equipment and arrange a lease with OpCo on ordinary commercial terms. A primary goal of the lease will be to allow the LLP to maximize depreciation over as short a period as is allowed. This will likely make the lease shorter in term (and the lease payments higher) than you would see in a lease from a leasing company.
The lease payments for the equipment will be tax deductible to your OpCo, but they will be tax-free income to the LPs as long as the depreciation expense offsets the lease cash income. There is no statutory limit to how large the LLP can be regarding asset value. Once the equipment is fully depreciated, and assuming it still has value, then you can convert the LLP to a private corporation (NewCo), where NewCo is fully, 100 per cent owned by the LPs. NewCo can then be sold to, or merged with, your OpCo, another party, or even donated to charity. The choice need not disrupt the use of the equipment by the OpCo. All of these options create different tax and wealth generation benefits.
In the worst-case scenario, where
the equipment is worthless at the end of its depreciation schedule, you and your fellow LPs would still receive double-digit after-tax returns. The ultimate value of this whole arrangement depends on the value of the equipment after depreciation is exhausted and the tax-rate gap between the owner of the OpCo and any family members who are LPs.
No investment in business is risk-free, however the inherent risk in this structure is the same business risk that you run every day, only it’s structured to drive more benefits to you. Since you own and operate OpCo, the biggest risk to the LLP is if your OpCo goes bankrupt and cannot pay the lease. If that happens, the reality is that you will already have a host of more important problems to deal with first.
You can begin this process at any time, but the sooner you act, the sooner you and your company can start receiving the benefits, which leaves us with how to start. These steps should be familiar to your accountant or lawyer, but if they have not mentioned these types of opportunities to you before, it might be best to seek out professionals who have experience structuring the necessary agreements and partnerships.
Frank McGillicuddy is a general partner at Thermocline Advisory Incorporated, a business consulting services firm in the Greater Toronto Area.
Virtual summit share insights on building a workforce that reflects the rich tapestry of Canada’s talent.
Attracting and retaining more workers from under-represented populations to fill the thousands upon thousands of jobs currently available in Canada’s construction sector, and the even more that will open in the coming years, is a strategy that can only benefit the industry.
To help put a spotlight on the labour needs of the industry and provide some practical advice about attracting and retaining workers from equity deserving groups, On-Site Magazine, along with HPAC and Electrical Business magazines, hosted the Pursuing DEI virtual summit this past April.
The summit, sponsored by Procore Technologies, Jacques Cartier + Champlain Bridges, Electricity Human Resources Canada, and EMCO Corp., opened with a keynote address by Rubiena Duarte, vice-president of global diversity and inclusion at Procore Technologies, and was rounded out with a series of panel discussions exploring Diversity, Equity and Inclusiveness (DEI) with the aim of helping construction leaders build up their companies to be viewed as employers of choice, in an industry that is open to all.
“Last year, it was reported that Canadian construction companies missed out on $9.6 billion in revenue oppor-
tunities because of the labour shortage,” said Duarte.
Given the massive number of job openings, she explained that companies need to think about enticing the next generation of workers, the Gen Zs, new Canadians, women, Indigenous communities, and other equity deserving groups that are under-represented on jobsites, into the industry.
Contributing to the low levels of diversity in the industry’s labour pool, where women represent only five per cent of the on-site workforce, are unconscious biases. Duarte explaining that “it really refers to assumptions, stereotypes and reactions about a person, or group of people that are formed by our experiences, our upbringing and societal influences.”
The ability to recognize when unconscious bias is being detrimental opens us up to exploring new ideas and ways of conducting business, she explained. “The main thing with unconscious bias is being self-aware.”
She said being self-aware and catching ourselves when a subconscious bias kicks in allows us to assess, “Why am I doing that? And how might I need to shift my thinking?” adding, “When we ignore some of those biases, when they exist, it really becomes detrimental to people and cultures.”
For an industry in need of more workers, these biases can cause talent pools to be ignored, dismissed or overlooked.
“Studies have shown that applicants with similar resumes and experience are 50 per cent more likely to be contacted if they had a white sounding name, versus somebody of an ethnicity or with a black-sounding name,” she explained.
“It’s inclusivity that actually matters, especially in this era where we are actually having a shortage of workers in the industry,” said Kenny Leon, vice-president of the Canadian Construction Association, and moderator of the “Building and maintaining your culture of inclusion” panel discussion.
“We need a set of company expectations to take this forward. We need to communicate those expectations. And we also need to be ready to enforce the rules of our roads if we are going to be viewed as progressive employers who value all workers,” he explained.
That discussion, which featured Brandi Ferenc, founder of Fair-Trades Toolbox, Graeme Aitken, executive director of the Electrical Contractors Association of Ontario, Maraika De Groot, director of corporate services with Maven Consulting Limited, and Luanne Whitecrow, director of the Progressive Aboriginal Relations Program with the Canadian Council for Aboriginal Business, outlined some of what inclusive culture is, what it is not, and how it can impact a workforce.
“Inclusive culture doesn’t mean everyone is given a pair of work boots,”
said Ferenc. “It means everyone gets a pair of work boots that fit and the ones that they want.”
“It’s all about creating an environment where there’s a safe space for your groups or your employees to participate safely,” added Whitecrow.
There is no single recipe to build that environment, but for De Groot, being selfaware, both individually and as a company, factor into developing policies and practices that lead to a healthy corporate culture that works for everyone in the company.
Policy cannot be a one-and-done effort, however, and the establishment of a DEI committee is not a guarantee of success. As Aitken put it, “A committee is not enough, unless you simply want to check a box.”
“It’s critical to when you’re looking at creating a cultural shift inside an organization, to set that policy commitment, that strategy, along with the work plans, for longterm commitment,” explained Whitecrow. “Is having a committee enough? No. It’s all about getting executive leadership buy-in and reflecting on the intent in developing an inclusive culture for the long term.”
The long-term plan should feature affinity groups and encourage allies.
“Twenty years ago, we didn’t have social media and my affinity group was one other woman that was working in the trades. And without that, I probably wouldn’t be sitting here on that panel today with you,” said Ferenc. “It’s absolutely critical to have these affinity groups to help get people past barriers, to help support them through those little bumps in the road, because they are going to happen.”
The willingness to develop and support these groups falls to management. “I don’t
always think we spend enough time focused on what great management looks like,” said De Groot.
A focus on building an inclusive industry and inclusive companies is critical to recruiting new talent for all sectors of the construction and trades related industry, explained Martin Luymes of the Heating, Refrigeration and Air Conditioning Institute of Canada.
Luymes was the moderator of the panel discussing recruitment and how DEI factors into attracting the best talent from groups that are under-represented in the trades. That session featured Bill Ferreira of BuildForce Canada, Kim Rutherford from Emco Corporation, Viktoriya Syromyatova of Boralex and Craig Swanberg from PCL Construction.
“We estimate that we’re going to need about 88,000 additional workers over the next 10 years just to keep pace,” explained Ferreira. “When we factor in the retirement of 263,000 individuals during that period, the industry is going to need to hire about 350,000 individuals.”
And Ferreira said that figure is likely on the low side as net-zero retrofits, increases in homebuilding targets, and government funding of infrastructure and ICI projects are not fully factored in.
To fill this need, human resources teams and hiring organizations will need to broaden their search parameters.
“When partnering with a recruiting organization, I like to look at what their commitment is to diversity and inclusion,” said Rutherford. “What are they doing to be an accessible and equitable organization, casting a wide enough net that we’re
getting the best possible candidate, not just for my industry, but broadly throughout the community, so that we represent the community we serve?”
“I don’t think that there’s a lot of people that are scrolling through pages and pages of job ads just waiting to see that we’re an inclusive employer,” added Swanberg. “It’s about getting in front of people and messaging to them that this is an industry that’s for you. This is a place that that you belong, and you can be your authentic self.”
While DEI efforts in hiring have generated some gains within certain groups, including attracting more women to the construction sector, much more needs to be done.
“Where we haven’t been seeing significant progress has really been in newcomers,” said Ferreira. “We’ve actually been seeing that number of slightly declining when we look at the overall number of newcomers involved in the trades… That’s an area that, in part, needs to be corrected through policy changes.”
The final panel of the event, moderated by Michelle Branigan of Electricity Human Resources Canada, focused on becoming an employer of choice through the application of DEI-driven policies and principles. Panel members Meg Mathes of Modern Niagara, Elaine Carelse of Orion Construction, and Lindsay Janca from Hatch, shared insights about what jobseekers want from their employers.
“They’re looking at employers’ annual reports, your senior leadership team, and if they don’t see themselves represented there, that’s going to make a difference to your ability to attract and retain,” stated Branigan. “Organizations that can build truly inclusive workplaces are going to have the edge when it comes to both the recruitment and retention of that workforce, and really position themselves as employers of choice.”
Full videos of each panel session, as well as the keynote, are available online at www.on-sitemag.com (type DEI into the search box to quickly find the page).
Started as an informal way to stay fit and connect with friends, I encourage others to take part in our Hike Club, or to start one of their own.
Over the past year, I became a father for the first time and started a new role as president and CEO at Maven Consulting Limited. I quickly found that keeping up with my networking, ensuring I have quality time with my family, and leading a growing consulting firm was a big challenge. I needed to do something that would have a beneficial outcome, not just for me, but also everyone around me, and I literally walked into a solution: Hike Club.
I have always been physically active, and I find that I get some of my clearest thinking and ability to reflect while taking in some fresh air on a hiking trail. Moreover, the exercise helps me maintain my physical and mental health in a stressful industry.
The birth of Hike Club actually goes way back to the early 2000s with one of the first friends I made while studying civil engineering at the University of B.C., Shervin Teymouri – someone who to this day is one of my best friends.
Shervin and I got into the habit of hiking the Grouse Grind, a trail on Grouse Mountain, on Wednesday evenings and Sunday mornings in the spring and summer months. Shervin and I have kept up with the Sunday morning Grouse Grind hikes over the years.
For me, it is important to be home for dinner with my family every night, reading my daughter a story and tucking her in for bed, so over the past year I have found that early Sunday mornings were one of the only free times on the weekends that I had in my schedule to connect with friends, colleagues and clients.
Shervin and I started to casually invite people to join us for our Sunday morning hikes. One week, a friend of mine who was with us suggested starting a LinkedIn group to extend the invitation to the engi-
neering and construction community. From there, Hike Club was born.
The club now has over 300 active members in the Lower Mainland of B.C., fostering many new connections in the industry, and allowing folks to connect in person.
We start each hike with a round of introductions. The group learns who each person is, what they do, and what brought them to Hike Club. We also have a topic of discussion each week that we share at the start of the hike. This can be anything from how to deal with risk management, to your approach to recruiting and retaining staff.
Once we reach the top of the mountain, we debrief on the different discussions that took place on the way up over a coffee. And we make sure that we mark the moment with a group photo. Hike Club has grown to have between six and eight regular weekly hikers, with anywhere from five to 10 additional hikers joining on a given Sunday.
At the end of the day, networking in engineering and construction is important because consulting and construction is all about relationships. You want to work with people you can trust and rely on, and climbing a mountain allows you to form those bonds and relationships.
“Whether it’s sunny, raining, or snowing, I’ve been going every Sunday morning for the past six months. This commitment stems from the tremendous value that Hike Club offers,” notes one of our Hike Club regulars, Tuan Troung. “Where else can you get in shape, meet leading industry professionals, share insights on business and leadership, and explore the beautiful landscape that surrounds us at the same time? Our choices define us; either sleep in or conquer a mountain.”
Knowing the positives that I’ve experience via our group, I challenge other leaders in engineering and construction to start their own groups in their cities. Given the range of geography and interests, it doesn’t even have to be hiking. Any physical activity that is conducive to conversation while getting in an intense workout holds potential.
And, last but not least, next time you are in Vancouver, come join me for a Sunday morning hike. Everyone is welcome!
Jesse Unke is the president and CEO of Maven Consulting Limited. To check out Hike Club, and to keep up to date on the group’s hikes connect on LinkedIn at: https://www.linkedin.com/groups/14365729.
THE TOP 40 Page 31
CAUTIOUS OPTIMISM Page 34 TOP 5 UNDER 50 Page 38 LISTINGS Page 42
On behalf of Aon, we are proud to continue our sponsorship of the Top Contractors issue of On-site for the seventh consecutive year. Over the past four years, we have witnessed disruptive events that significantly stressed the global economy The pandemic and our governments’ response of lockdowns, throttling of trade, and forced business closures followed by several stimulus packages disrupted global trade and monetary systems. Adding to a pre-pandemic trade war environment, the increasing prospect of global armed conflict originating in Eastern Europe has boiled over to manifest the most disruptive economic events that the modern world has ever seen.
The sum of the resulting consequences has started to manifest in multiple ways. The just-in-time delivery and global supply chain system is showing structural cracks in its foundation. Central bank induced inflation has continued to create price uncertainty for businesses and has eroded living standards for families and individuals. Rapidly increased interest rates have further aggravated pricing risk and have had an immense impact on budgets, both in the private and public sectors. While the labour market has remained strong and infrastructure spending remains robust, slowdowns in some sectors of the economy remain inevitable. The best hope is for a soft-landing however given the current global economic and geo-political environment, clarity is not expected anytime in 2024.
As the world’s leading risk advisor and broker to the construction and infrastructure industry, Aon’s Global Construction and Infrastructure Group remains committed to helping you navigate through this uncertainty. Our best-in-class Canadian practice is here to support the Canadian construction and infrastructure sector at all levels of the marketplace, bringing the best advice and experience from around the world to help you make better decisions.
Despite the underlying stressors, the re-opened world economy is attempting to normalize with commodity prices now similar to those last seen pre-pandemic. However, the disruption of the past four years witnessed high volatility evidenced in supply chain fragility, product shortages and price variability. This created systemic vulnerability and individuals and enterprises are now exposed to increased counter-party risk. High interest rates have caused more pain and will continue to do so until price stability is achieved. Project economics, whether private or publicly sponsored, are exposed to the cost of capital and cost uncertainty. Subcontractors and suppliers also need to manage shortages of key supplies and labour, as well as an increased cost of capital and constrained cash flow. It is safe to assume that all of the counter-parties you engage with are themselves exposed to systemic counter-party risk and the ability to fully untangle the opaque web of inter-connected risk is challenging for all participants.
There are several tools available to mitigate counter-party risk, however none are panaceas and they can be sector, transaction and named-peril specific. Risk transfer tools are also only available once the risk has been identified and quantified. Relationships with risk advisors who specialize in and understand your business is of paramount importance, as is investment in counterparty risk assessment and mitigation of customers and suppliers. This will remain a key skill going forward.
While the future is always uncertain, with the right contractual terms, operational practices, data, technology and risk finance solutions, we can help you find opportunities for sustainable growth. We consider it an honour to partner with an industry that serves as a cornerstone of the Canadian economy and our Aon team looks forward to helping your firm — and our industry — remain resilient and well-positioned for the future. Sincere congratulations to this year’s Top Contractors.
On behalf of Aon Global Construction and Infrastructure Group Leadership team and colleagues throughout Canada and the world, we thank you for the opportunity to work with you.
Chris McLean, Managing Director, National Leader, Construction & Infrastructure Doug Correa, EVP and Specialties Leader CanadaWe are your construction team of choice, passionate about what we do and about our partners’ needs. PCL is Canada’s Top Contractor and proud to lead the way with innovative building strategies and sustainable delivery. PCL is driving transformational change in the construction industry through leading by example, delivering Edmonton’s first net-zero energy building.
Last year presented a mix of revenue results within Canada’s construction sector, but the overall picture kept to a steady climb, with this year’s amalgamated list of the Top 40 contractors in Canada reporting 2023 revenues that were more than $4 billion higher than the Top 40 from 2022.
The greatest segments for revenue growth were related to publicly funded projects, as infrastructure appears to be gaining government attention, with new mass transit systems, bridgeworks, roadways and energy-related projects underway, or soon to be. Hospitals and other institutional projects are also helping to nudge revenues ever higher.
Only one segment in On-Site’s industry polling was without a company reporting an increase in revenues in 2023, as gainers outpaced companies seeing declines by a significant margin in most segments.
Looking ahead, there is cautious optimism in the air, along with an anticipation of interest rate reductions that will help on the financing front. The latest Construction Monitor report from the Royal Institution of Chartered Surveyors (RICS) and Canadian Institute of Quantity Surveyors showed an improved picture for the Canadian market, with growth seen across both the private residential and non-residential sectors in terms of workload in the first quarter of 2024, marking a positive start on next year’s report.
Once again, the team at On-Site would like to thank all of the companies that took the time to participate in our annual survey. Your valuable contributions make this research possible and allow us to share trends and insights with our industry.
1 2 3 4 5
When it comes to health and safety (H&S), every accident is one too many. The construction industry is one of the first to be impacted by incidents, and there is a collective need to raise industry H&S standards. At Pomerleau, H&S is not only about statistics. It is also about getting people back home to their families every night. Pomerleau’s vision for its employees is reflected in its actions and commitments toward physical and mental well-being.
This year, Pomerleau is reinforcing its commitment to advocate for H&S by including it as a priority in its Environment, Social and Governance (ESG) strategy. Several H&S initiatives have been outlined in the company’s most recent report.
Through a combination of prevention, awareness, training and information sharing, the company is seeking to continuously improve its H&S practices and standards. Last year, Pomerleau brought together more than 1,050 site and project team members across Canada for training about the environment, quality and H&S in its operations.
To continue this momentum, the company will also roll out its Builder Training program to promote its H&S management tools to its construction managers.
Furthering its commitment to H&S, Pomerleau has received several certifications, including COR®. The company has a 100%
“Health and safety must be a natural reflex in our operations, focused on the well-being of everyone who works on our sites, without compromise, at all times. People, above all!”
- Steve Ceolin, Vice President of Health and Safety at Pomerleau
average Certification of Recognition across the country, and is a member of numerous organizations that operate to improve H&S standards and practices across the industry.
In October of 2023, Pomerleau became a member of the Construction Research Safety Alliance (CRSA), a non-profit organization based at the University of Colorado. Its goal is to eliminate serious injuries and fatalities in the construction industry through scientific research.
As a member of the Canadian Construction Safety Council (CCSC), Pomerleau is working with other industry leaders to evaluate and reinforce industry standards, like examining the alignment of fall protection standards.
At the beginning of May, Pomerleau dedicated a week to H&S awareness with the message: People Above All. A minute of silence was held for the National Day of Mourning, H&S moments were conducted on sites, mental health toolboxes were distributed, and employees participated in a helmet contest.
To inaugurate its new innovative protective helmets, Pomerleau held an illustration contest for its employees’ children. Partici-
pants were asked to draw a design for the company’s old helmets as they were phased out. The winner and their parent received helmets with their design on them.
Pomerleau’s new helmets include a full-brim helmet designed to repel rain while providing better ventilation, side impact protections, a magnetic buckle with an adjustable strap for easy on-handed use with gloves and an RFID chip to store medical and contact information for medical personnel to use in case of an emergency. The unique design enables the helmet to absorb maximum force and protect heads from direct and angled impacts. In addition to the introduction of the helmets, a new policy regarding the mandatory wearing of gloves on site was also launched.
To honour those affected by workplace tragedies, Pomerleau sponsored and participated in Threads of Life’s Steps for Life Walks and organized Montreal’s event, which was the first in Quebec. Over 150 employees across Toronto, Montreal, Halifax, St. John’s, Vancouver and Ottawa gathered with colleagues and family members to commemorate the lives of the more than 1,000 workers who are killed on the job or die because of workplace injury or illness every year. They raised $8,426 for the cause.
Having
weathered significant inflation and elevated lending rates, government-funded ICI and infrastructure projects, and incentives in the housing market,
have Canada’s construction sector feeling good for 2024.BY ADAM FREILL
Publicly funded projects had Canada’s construction sector busy in 2023, and government-driven activity is filling the industry’s backlog nicely for the foreseeable future. This drive to build and repair much-needed infrastructure and institutional buildings is helping certain segments of the industry, and masking the challenges faced in other segments, however, as residential and certain commercial sectors are more susceptible to a tight lending market.
Overall, despite the worry about finances and the ongoing labour crunch, there’s a whiff of optimism permeating the construction sector as the national housing plan moves forward and anticipation builds for relief from the Bank of Canada on lending rates.
“With the current economic conditions, we cautiously expect the feds to slowly lower the interest rates this year, which will help projects get closer to becoming viable,” said Mike Wieninger, COO of Cana-
dian operations with PCL Construction.
In On-Site Magazine’s annual Top Contractors survey, readers from almost every segment of the market indicated an expectation for a growth curve of flat or better in 2024. A quick look within the Top Contractors rankings indicates that the 2023 revenues of the Top 40 outpaced those of the 2022 Top 40 by more than $4 billion, indicating that spending in the sector is on the rise, although not all segments are sharing equally in the spoils.
“There still remains caution in the market that is pushing project starts further out,” advised Wieninger. “Construction costs have stabilized with more normal escalation, which again provides some confidence on cost predictability. While the private sector construction market has slowed, there continues to be a strong public construction market.”
“On the public side, we are optimistic. Government has not invested in public infrastructure in years, and now it’s aging and it needs to be repaired, retrofitted, and constructed. On the public side, we’re not that concerned,” stated Rod Gilbert, president of the Canadian Construction Association. “On the private side, interest rates are still high, but we’ve not seen the cancellation of many projects.”
With public sector work rolling as it is, that has put some strain on availability of labour, equipment and materials, with labour being a core limiting factor in the industry.
“It’s a major issue in the industry. We’ve been talking about that for years,” acknowledge Gilbert. His organization has shifted some of its focus to changing perceptions about the industry, targeting parents of the students that CCA would like to see join the industry’s ranks.
“It’s really the parents that are directing what their children should be doing,” he said. “We’re trying to explain to parents that it’s good jobs; it’s well paid; it’s safe. There’s so much emphasis put on safety now and our companies are doing very well on that.”
“There’s so much opportunity in the construction industry. And it’s not necessarily just construction, but it’s all of the ancillary businesses and avenues that feed into construction,” added Cameron Archer, director of sales and marketing with Orion Construction. His company works hard to be an employer of choice. “There are so many things that we do in this office to ensure that staff are happy and healthy, because without that, they can’t be productive.”
“Leaders in the industry need to emphasize that construction has some of the highest job satisfaction levels,” stated Nadia Todorova, executive director of the Residential and Civil Construction Alliance of Ontario (RCCAO). “Being part of building critical infrastructure for Ontario’s longterm success is something that should be highlighted, especially as industry works to attract young people into the skilled trades. The ability to say that ‘I build that bridge, or house’ is something powerful.”
“Having worked at a GC for 15 years before I came to Procore, recruiting was a problem back then, so it’s nothing new. And I think the key is you not only need to recruit talent; you need to keep them,” said Kris Lengieza, Global Technology Evangelist at Procore. “I can tell you from personal experience, one of the reasons that I changed companies was that I felt that the company I was working for was way behind the times with the technology they were using. The younger generation wants to know that they’re getting the best tools to do their job.”
Attracting students is a necessary component of replenishing the workforce, but Canada needs more than schools can produce, so looking abroad for immigrants with construction experience makes sense.
“The demographics of the country point to more workers exiting the workforce over the next 15 years than younger workers available to replace them. This will place significant pressure on all industries and force Canadian employers to turn increasingly to immigration to help support domestic recruitment,” suggested Bill Ferreira, executive director with BuildForce Canada.
Current immigration policies do not favour trades workers, since the points system used values degrees over trade certifications and experience, he explained.
“We’re working closely with the federal government. We believe that short-term, immigration could be a solution,” said Gilbert. “But in order to do that they need to change their pointing system because right now, the way that immigration Canada is selecting their newcomers is not beneficial to the trades.”
Regardless of where the workers come from, ultimately projects will move forward, with many companies turning to technologies like Artificial Intelligence (AI) to aid with planning and tracking, as well as to gain efficiencies on administrative tasks.
“The Canadian construction industry is gradually adopting AI, with certain segments such as non-residential more receptive to its integration,” said Wieninger.
While the cost and training needed to incorporate AI into a company’s workflow may favour larger companies, the efficien-
cies from using the right AI-powered tool can help small and medium-sized enterprises as well.
“In our office, the very first place that we saw some value in AI was because we have an in-house design and architecture team. We’ve been using AI for a lot of our rendering work,” said Archer. “We’ve also been integrating it and leveraging the use of it in tracking meeting minutes, which has been incredibly helpful. You think about the time that it’s saving us, it’s been pretty incredible.”
“There is a bigger focus on technologies that support the efficient management of the sites, the organization of the workforce and tracking of progress of the work,” said Wieninger. “Over time, it’s exciting to see this moving even closer to the activities that workers do to build.”
And while it may be beneficial to learn about open and closed AI systems, from a cybersecurity perspective, it is not necessary to build a propriety system to tap into this next level of technological advancement.
“I’ve been encouraging customers to talk to their existing vendors and understand what they’re doing with AI,” explained Lengieza. “You don’t have to do the lift yourself. Let the experts do the lift for you. And then use it inside of tools that you’re already using.”
Knowing that a company will get good value, and extended use, from a new set of tools, like AI, can also foster the adoption of technology.
“The problem with innovation and technology in the industry is it’s expensive. It’s a big financial commitment. We need longterm planning,” commented Gilbert, who says that CCA is pressing government at the federal level to commit to a 25-plus-year planning process for infrastructure, which would provide a long-range outlook that would allow for greater industry commitment to spend on such things as new technologies. “Our companies are willing to embrace technology, and make it better and build faster, but we need commitment.”
Even in the absence of a long-range federal plan, Canada’s construction sector is seeing increased demand for its services, and there are expectations that interest rate reductions over the remainder of 2024 will see private-sector projects grow alongside the publicly funded projects that have keep momentum moving forward this past year.
“I think, in general, contractors are pretty confident in their backlog and that the projects are going to continue to come,” said Lengieza, who pointed to a recent industry survey his company helped to produce. “Seventy per cent of Canadian civil contractors said that they expect their backlogs not only to be solid, but to continue to increase.”
As Ferreira observed, “We continue to see very strong investment levels and demand for construction services across the country, which should keep the industry very busy for the foreseeable future.”
Behind every great project, are great people.
At EllisDon, we work with the best of the best. It’s about working with values-based people, letting them embrace their unique talents, and providing them with opportunities to grow and take on exciting challenges.
Passion and excellence are driving forces that have our Top 5 Under 50 in Canadian Construction navigating amazing projects with their smaller teams.
BY ADAM FREILLBeing extremely focused, highly organized, and fostering teams that are dedicated and attentive are some of the traits that have allowed this year’s Top 5 in Canadian Construction with Under 50 employees to rise to the top of a massive list of smaller enterprises within Canada’s construction community.
“We love being at the forefront and leading edge of economic development. Whether building new food processing facilities, mixed-use commercial-professional developments, multi-family projects or building for new brands coming into Canada, being involved in, and helping to drive growth in Western Canada is exciting,” explains James Behnke, business and project development manager at Fillmore Construction Management Inc., which topped the 5 Under 50 list for a
We are up for any challenge. Complex projects are opportunities to demonstrate our unmatched skill, outside-the-box innovations, and unyielding strength. Whether you are looking to replace aging water/ wastewater infrastructure or need a trenchless solution with minimal impact on the surrounding environment, we will exceed your expectations for quality, safety and sustainability.
Partner with Michels Canada and expect more.
1 2 3 4 5
FILLMORE CONSTRUCTION MANAGEMENT INC
H eadquarters: Edmonton, Alta. 2023 Revenue: $170,226,000 www.fillmoreconstruction.com
M BUILDS
H eadquarters: Thunder Bay, Ont. 2 023 Revenue: $154,000,000 www.mbuilds.ca
JR CERTUS CONSTRUCTION CO. LTD.
Headquarters: Vaughan, Ont. 2023 Revenue: $98,600,000 www.jrcertus.com
ROSATI CONSTRUCTION
Headquarters: Windsor, Ont. 2023 Revenue: $95,089,332 www.rosatigroup.com
CIF CONSTRUCTION
Headquarters: Prince George, B.C. 2023 Revenue: $73,000,000 www.cifcon.com
second consecutive year. “It is truly exciting and fun to wake up every day coming into the office to see what new opportunities are coming up.”
“What we enjoy most about the construction industry is its profound impact on communities, collaborative nature, and dynamic opportunities for learning and growth,” says Frank Aquino of JR Certus Construction Co. Ltd., whose 5 Under 50 company is led by a family-based team with more than 100 years of combined construction experience and knowledge. “Each project is an opportunity to create meaningful change, collaborate with talented individuals, and stay at the forefront of industry trends.”
Whether working with their clients, their supporting trades partners or suppliers, a common theme amongst this year’s Top 5 is their teams’ willingness to support each other and look for the most positive outcome for their company and their clients.
“Most people are wearing multiple hats and taking on tasks that may not traditionally be part of a defined role,” explains Scott Fomenoff, director with CIF Construction, who shared some of the secret sauce that helped land his company in this year’s Top 5. “The secret isn’t really a secret; each member of our teams knows what has to be done, when to do it, and how to do it,” he says. “For this to happen, everyone needs a great deal of trust in everyone else… our teams have worked together for years, we know each other’s strengths and weaknesses and work together to get everything across the finish line.”
That sense of camaraderie helps staff from different departments or with different responsibilities on a project sort out how to get to the finish line in the most efficient and best way possible.
“We strive for cooperation between departments, with a continual focus on teamwork,” says Peter Belluz, partner/principal at M Builds. “It means loyalty to one another and a helping hand or suggestion when needed.”
Having confidence in their workers also allows for these companies to be flexible, when necessary.
“M Builds project managers and superintendents know that working cooperatively with the owner and the consultant, and not making an issue of every single little issue, will ultimately be the best for all stakeholders in the project. There is give-and-take in most daily activities we pursue, and construction work is no different,” he adds. “Despite the contracts and procedures and policies that are put in place, M Builds personnel recognize that each project is unique, and that the project management methodologies can be altered to suit, with the appropriate notification and consultation with the partner in charge.”
“Passion for construction and getting things done right is what we are all about,” agrees Behnke.
“By optimizing resource allocation, fostering open communication, and empowering team members to take ownership, we maximize productivity and quality,” says JR Certus’ Joseph Aquino.
With teams that know and rely on each other so well, sometimes growth becomes more of a decision rather than a default pathway, but that can be a strength, says Behnke.
“We aren’t afraid of growth, but it must be measured,” he explains. “Our reputation in the industry and relationships with repeat clients, consultants, subcontractors and vendors are the secret to our success. Stretching ourselves too thin would jeopardize those two things.”
He is not the only one navigating growth with a keen handle on the control stick.
“We do not bid every project that comes along. We select the right opportunity and match that opportunity with our skilled field staff,” says Belluz.
“The biggest challenge we’ve actually faced is related to the growth of the company,” says CIF Construction’s Fomenoff. “We’ve had a lot of work in the past year, so we’ve had to hire some new faces to help take it on. This has its risks… Ultimately though, it’s been a very positive experience.”
And the work of these companies tends to speak for itself.
“As a small company, we value our agility, camaraderie, and pride in delivering exceptional results on large-scale projects,” says Joseph Aquino. “Our flexibility, sense of ownership, and commitment to excellence drive us to exceed expectations and make a meaningful impact on the communities we serve.”
“We take a lot of pride in building things,” sums up Fomenoff. “It’s a really cool experience seeing a project’s growth from nothing to a functional building, knowing that we played a crucial role in making that happen.”
In construction, bigger may be better. But when choosing a broker, bigger isn’t always best. Top contractors often face unique challenges and complex risk that requires the attention and expertise of the right resources. At American Global, our talented team is focused on nding innovative solutions that give clients a competitive edge and keep you on the critical path to success. Expect more from your broker.
• National Presence with a Global Platform
100% Privately Owned & Construction Focused
• Cross Border Broker for Seamless US/CAN Service & Advisory
• Non-Traditional Resources with Deep Industry Expertise
•
• Collaboration That Drives True Innovation
www.americanglobal.ca
0940625 BC LTD
1995 Garner Rd
Kelowna, BC
V1P 1E5
T: 250-862-6046
AAA Striping & Seal Coating 9519 42 Ave Edmonton, AB T6E 5R2
T: 780-435-2214
www.aaastriping.ca
W
Avondale Construction Limited
49 Hobsons Lake Dr
Halifax, NS
B3S 0E4
T: 902-876-1818
www.avondaleconstruction.com
C, H, M, N, O, V B
Badger Backhoe Services Ltd.
14836 1 St SE Calgary, AB T2X 1A1
T: 403-804-4688
E, G, J, U, X, Z
Baycrest Project & Construction Management
5/6 - 23 Railside Rd
Toronto, ON
M3A 1B2
T: 416-444-0200
www.baycrestgc.com
C, D, F, M, O
Bockstael Construction Ltd.
200 - 100 Paquin Rd Winnipeg, MB
R2J 3V4
T: 204-233-7135
www.bockstael.com
C, H, M, N, O, V
Bomanite Toronto Ltd.
111 Zenway Blvd Vaughan, ON L4H 3H9
T: 905-265-2500
www.bomanite.ca
Broccolini
500 - 16766 Trans-Canada Hwy
Kirkland, QC H9H 4M7
T: 514-737-0076
www.broccolini.com
C, N, V
Buttcon ltd
300 - 6240 Highway 7
Woodbridge, ON L4H 4G3
T: 647-888-3860
www.buttcon.com
C, F, H, K, M, N, O, T, V
CCambridge Concrete Pumping
226 Boida Ave Ayr, ON N0B 1E0
T: 519-624-2112
www.concretepumping.ca
Campbell Building Group
202 - 20 Stavebank Rd Mississauga, ON L5G 2T4
T: 905-274-8880
www.campbellbuildinggroup.ca
Canadian Turner Construction
510 Seymour St Vancouver, BC V6B 3J5
T: 604-626-3865
www.turnerconstruction.com
CGI Constructors
25 Watline Ave
Mississauga, ON L4Z 2Z1
T: 905-564-6560 www.cgigc.com
C, F, M, O
Chandos Construction 9604 - 20 Ave NW Edmonton, AB T6N 1G1
T: 780-436-8617
www.chandos.com
F, H, M
CIF Construction PO Box 2159
Prince George, BC V2N2J6
T: 778-835-5357 www.cifcon.com
E, M, N, S, W, X, Z
Clark Builders
800 - 5555 Calgary Trail NW Edmonton, AB T6H 5P9
T: 587-341-0640
www.clarkbuilders.com
C, E, G, H, M, N, O, R, S, V, Z
Clobracon Construction Inc. 1 - 2535 Halpern Saint-Laurent, QC H4S 1N9
T: 514-731-0035
www.clobracon.com
C, E, M, V, Y
Dawson Wallace Construction Ltd 4611 Eleniak Rd Edmonton, AB T6B 2N1
T: 780-966-2999
www.dawsonwallace.com
A, B, C, D, E, F, G, H, M, N, O, V
Delnor Construction Ltd. 3609 74 Ave Edmonton, AB T6B 2T7
T: 780-469-1304
www.delnor.ca
C, M, V
EBC inc.
1095, rue Valets
L’Ancienne-Lorette, QC G2E 4M7
T: 418-872-0600
www.ebcinc.com
B, C, E, F, G, H, J, M, N, O, Q, R, T, V, W, X, Y, Z
EllisDon Corporation 1000 - 1004 Middlegate Road Mississauga, ON L4Y 1M4
T: 905-896-8900
www.ellisdon.com
A, B, C, D, E, F, G, H, J, K, M, N, O, Q, R, S, T, U, V, W, X, Y, Z
Emcon Services Inc. 105 - 1121 McFarlane Way Merritt, BC V1K 1B9
T: 250-315-5984 www.emconservices.ca
The following letter codes are used to indicate areas of activity for the contractors in the listings on these pages.
A Aggregates
B Bridges
C Commercial Buildings
D Communication Engineering
E Concrete
F Contract Management
G Demolition
H Design/Build
J Electric Power/Utilities
K Environmental Remediation
M General Contracting
N Industrial Buildings
O Institutional Buildings
Q Marine-Related
R Mining-Related
S Oil and Gas-Related
T Other Transportation Construction
U Residential Houses
V Residential Multi-Unit
W Roadbuilding
X Sewer
Y Structural Steel
Z Waterworks
Evolve Builders Group Inc
101 - 123 Woolwich St Guelph, ON N1H 3V1
T: 519-265-6546
www.evolvebuilders.ca
H, M, U
Fillmore Construction Management Inc
9114 - 34a Ave Edmonton, AB T6E 5P4
T: 780-235-6015
www.fillmoreconstruction.com
A, B, C, D, E, F, G, H, J, K, M, N, O, Q, R, S, T, U, V, W, X, Y, Z
Flatiron
4020 Viking Way Richmond, BC V6V 2N2
T: 778-888-6464
www.flatironcorp.com
A, B, E
From morning to night, EBC proudly builds alongside you in a responsible, equitable and sustainable way since 1968.
The future is bright for EBC. Our employees are ready to take on upcoming challenges motivated by deep values, unparalleled expertise and an ambition to shine throughout Canada.
FLINT
3500 - 205 5 Ave SW
Calgary, AB
T2P 2V7
T: 403-370-2689
www.flintcorp.com
E, H, J, K, M, N, R, S, Y
Flynn Group of Companies 6435 Northwest Dr Mississauga, ON L4V 1K2
T: 647-741-5381
www.flynncompanies.com
Fortis Construction Group Inc.
416 Advance Blvd
Tecumseh, ON N8N 5G8
T: 519-419-7828
www.fortisgroup.ca
C, F, H, M, N, O, V
FWS Group of Companies
375 Commerce Dr Winipeg, MB R3P 1B3
T: 204-805-1995
www.fwsgroup.com
A, H, M, R, Y
GGillam Group 3 - 36 Northline Road
Toronto, ON M4B 3E2
T: 647-465-7251
www.gillamgroup.com
C, H, M, N, O, V
Govan Brown & Associates Ltd.
108 Vine Ave
Toronto, ON M6P 1V7
T: 647-821-8535
www.govanbrown.com
C, H, N, O, V
Graham Construction 10840 27 St SE Calgary, AB T2Z 3R6
T: 403-570-5106
www.grahambuilds.com
B, C, H, J, N, O, R, S, T, V, W, Z
Grascan Construction Ltd 61 Steinway Blvd Toronto, ON M9W 6H6
T: 416-644-8858
www.grascan.com
HHahn Builders Inc 54 Wilfred Laurier Ave St. Catharines, ON L2P 0A3
T: 905-650-2699
www.hahnbuilders.ca
HKC Construction 26/27 - 145 Traders Blvd E Mississauga, ON L4Z 3L3
T: 905-565-1220
www.hkcconstruction.com
C, F, H, M, N, O
HR Pacific Construction Management Ltd 901 10th St N Golden, BC V0A 1H0
T: 250-344-4999 www.hrpacific.com
IIntegricon Property Restoration and Construction Group Inc. 219 Westcreek Dr Vaughan, ON L4L 9T7
T: 647-402-7973
www.integricongroup.ca
C, H, K, M, N, O, U, V
JEN COL Construction 100-9620 266 St Acheson, AB T7X 6H6
T: 780-963-6523 www.jen-col.com
JR Certus Construction Co. Ltd. 3 - 281 Zenway Blvd., Second Floor Vaughan, ON L4H 0S5
T: 647-494-0150 www.jrcertus.com
C, H, M, N, O, V
Kiewit Canada Group Inc.
200 - 10333 Southport Rd SW Calgary, AB T2W 3X6
T: 647-927-9326
www.kiewit.com
KingsRidge Building Group
2 - 223 Main St S Newmarket , ON L3Y 1V3
T: 905-715-5451
www.kingsridge.ca
H, M, U
Lanca Contracting Limited
35 Bury Crt
Brantford, ON N3S 0A9
T: 519-861-1329
www.lanca.com
Ledcor Group of Companies
500 - 1055 W Hastings St Vancouver, BC V6E 2E9
T: 604-681-7500
www.ledcor.com
B, C, E, F, G, H, J, K, M, N, O, Q, R, S, T, V, W, Y
Maple Reinders 2660 Argentia Rd Mississauga, ON L5N 5V4
T: 905-821-4844
www.maple.ca
B, C, E, F, G, H, J, M, N, O, Q, S, T, V, X, Z
Marco Group Limited
78 O’Leary Ave
St. John’s, NF A1B 4B8
T: 709-754-3737
www.marcogroup.ca
C, F, H, M, N, O, V
Matheson Constructors
245 Industrial Parkway N Aurora, ON L4G 4C4
T: 905-669-7999
www.mathesonconstructors.com
A, B, C, D, E, F, G, H, J, K, M, N, O, Q, R, S, T, U, V, W, X, Y, Z
Metric Contracting Services Corporation 34 Bramtree Crt Brampton, ON L6S 5Z7
T: 905-793-4100
www.metricgroup.ca
W, X
Michels Canada Co. 1102 16 Ave Nisku, AB T9E 0A9
T: 780-955-2120 www.michelscanada.com
J, N, S, X, Z
M Builds
955 Cobalt Cr
Thunder Bay, ON P7K 1B9
T: 807-346-1650
www.mbuilds.ca
C, F, M, V
Magil Construction Canada Inc.
Plaza 2, Suite 101 - 2000 Argentia Rd Mississauga, ON L5N 1V8
T: 905-890-9193
www.magil.com
C, E, J, M, N, O, W
Miller Paving 287 Ram Forest Rd Stouffville, ON L4A 2G8
T: 905-626-8514 www.millergroup.ca
Mongolian Construction & Management Services Ltd.
231 - 7184 120 St Surrey, BC V3W 0M6
T: 778-918-4405
www.mongolianconstruction.com
A, B, E, F, G, H, K, M, N, Q, R, S, T, W, X, Y, Z
Nexrock Design Build 40 Snidercroft Rd Concord, ON L4K 0B5
T: 905-669-9654
www.nexrock.com
C, F, G, H, M, N, T
NorLand Limited 8648 Commerce Crt Burnaby, BC V5A 4N6
T: 778-879-0581 www.norlandlimited.com
North Construction
378 Esplanade E North Vancouver, BC V7L 1A4
T: 604-904-2300 www.north-construction.com
A, B, E, G, J, K, Q, T, U, V, W, X, Z
O.B. Services Ltd. 15 - 308 Jackson Rd Edmonton , AB T6L 6W1
T: 780-462-7225
O.N.Site Construction Inc. 40 - 2861 Sherwood Heights Drive Oakville, ON L6J 7K1
T: 905-829-8895
www.onsiteconstruction.ca
C, M
OCL Group 4010 76 Ave Edmonton, AB T6J 7C4
T: 780-914-2076
www.oclgroup.ca
On Side Restoration
Bay 11 - 3905 32nd St NE
Calgary, AB
T1Y 7C1
T: 403-829-7949
www.onside.ca
C, M, O, U, V
Orion Construction
105 - 19923 80A Ave
Langley Twp, BC V2Y 0Y3
T: 778-251-2743
www.orionconstruction.ca
C, H, M, N, V
PCL Construction 9915 56 Ave NW Edmonton, AB T6E 5L7
T: 780-733-5107
www.pcl.com
B, C, D, F, H, J, K, M, N, O, Q, R, S, T, V, W, X, Z
Pomerleau
343 Preston St. Ottawa, ON K1S 1N4
T: 519-318-5678
www.pomerleau.ca
B, C, J, N, O, Q, S, T, V, W, X
Priestly Demolition
3200 Lloydtown Aurora Rd
King, ON L7B 0G2
T: 289-552-3228
www.priestly.ca
B, C, E, G, K, N, O, R, S, V
Project X Construction Ltd.
1 - 165 Alvin St Waterloo, ON N2J 3J7
T: 519-577-9453
www.projectxconstruction.ca
PW Trenchless Construction Inc 12343 104 Ave
Surrey, BC V3V 3H2
T: 604-580-0446
www.pwtrenchless.com
E, X, Z
Rain City Industrial 319 - 9440 202 St
Langley Twp, BC V1M 3Z4
T: 778-347-5989
www.raincityindustrial.com
A, B, C, D, E, F, G, H, J, K, M, N, O, Q, R, S, T, U, V, W, X, Y, Z
Reliance Construction of Canada Ltd.
3285 J.B. Deschamps
Lachine, QC H8T 3E4
T: 514-631-7999
www.relianceconstruction.com
C, F, H, M, N, V
Robust Shield inc 324943 Norwich Rd Norwich, ON N0J 1P0
T: 519-424-9438 www.robustshield.ca
Rosati Construction 6555 Malden Rd Windsor, ON N9H 1T5
T: 519-734-6511
www.rosatigroup.com
C, E, F, H, M, N, V, X, Y
Royalcrest Paving & Contracting 864 Tapscott Rd Toronto , ON M1X 1C3
T: 416-335-9336 www.royalcrest.ca
Self Storage Contracting Inc. 4 - 200 Brock Street Barrie, ON L4N 2M4
T: 905-526-0202 www.selfstoragecontracting.com N
Snyder Construction 920 Brawley Rd W Ashburn, ON L0B 1A0
T: 905-655-5000
www.snyderconstruction.ca
C, E, F, G, H, M, N, O, U
Solid Site Works
176 Sagers Corners Rd
Stirling, ON
K0K 3E0
T: 519-531-0122
Stormys Maintenance and Construction LTD
177 Raymel Rd
Grand Barachois, NB
E4P 7M7
T: 416-816-0771
Strike Group
1300 - 505 3rd St SW
Calgary, AB
T2P 3E6
T: 403-775-1031
www.strikegroup.ca
A, B, E, G, J, K, M, N, R, S, Y, Z
TTimberline Custom Homes
754 Northeys Bay Rd
Woodview, ON K0L 3E0
T: 705-741-6731
www.timberlinecustomhomes.ca
A, G, H, W, X
TriAxis Construction
100 - 2 Queen Elizabeth Blvd Toronto, ON M8Z 1L8
T: 416-896-3832
www.triaxis.ca
VVersailles 48 Inc
139 Avenue de Montréal-Est Montreal-Est, QC H1B 5P1
T: 514-923-1710
www.versailles48.com
Vixman Construction LTD. 4919 7th Line Rockwood, ON N0B 2K0
T: 519-856-2000
www.vixman.com
C, N, O, V
WWally’s Backhoe Services Ltd Box 839
Stettler, AB T0C 2L0
T: 403-741-8528
www.wallysbackhoe.ca
Westcor Construction Ltd. 2420 39th Ave Calgary, AB T2E 6X1
T: 403-663-8677
www.westcor.net
The following letter codes are used to indicate areas of activity for the contractors in the listings on these pages.
A Aggregates
B Bridges
C Commercial Buildings
D Communication Engineering
E Concrete
F Contract Management
G Demolition
H Design/Build
J Electric Power/Utilities
K Environmental Remediation
M General Contracting
N Industrial Buildings
O Institutional Buildings
Q Marine-Related
R Mining-Related
S Oil and Gas-Related
T Other Transportation Construction
U Residential Houses
V Residential Multi-Unit
W Roadbuilding
X Sewer
Y Structural Steel
Z Waterworks
Using project controls with the integrated approach of contracting methods.BY MICHELLE THROSSELL
The use of integrated project controls can help achieve successful outcomes, especially with collaborative delivery approaches that share the burden of risk.
Canada is a recognized leader of Public Private Partnerships (P3s) and continues to successfully deliver significant and complex P3s, when used on the right projects. The model typically puts most design and delivery risk onto the supply chain, but recent changes in the market have led to an increase in alternative procurement models being used to distribute this risk more evenly, and to gain other advantages in enabling successful project outcomes.
In recent years, projects have become increasingly larger and more complex, leading to increased delivery challenges. These challenges, when combined with material and labour shortages and the rising cost of goods, have led to alternative contracting models such as Alliancing and Progressive Design-Build (PDB) gaining popularity. These more collaborative contracts focus on building a relationship between the owner and the delivery team. They involve a collaborative “one team” culture, shared risk profile, open book policy and data transparency, all of which are foundational to securing mutually beneficial outcomes.
These alternative contract models require a shift in data management requirements to effectively support the development and execution of the contract. Significantly more data points will become available that need to be identified, tracked and collated in a
meaningful way to effectively support status reporting and decision making.
Crucial to the successful management of this data, and overall implementation of this newer, more progressive way of contracting, is to have an integrated project controls function to provide a single source of truth and heartbeat for the project.
The integrated project controls function continually measures, monitors and interprets inter-disciplinary data to meet the requirements of the stakeholders. By establishing the function from the outset, information can be organized and understood to better guide the project strategy, to define the delivery plan and, ultimately, inform the owner’s decision on how to proceed with the project through its lifecycle.
When an Alliance or Progressive DB contract type is selected, the chosen delivery team will often be entering into a contract with an immature design, high-level budget and limited understanding of the delivery risk. Their first tasks involve working with the owner to develop the design, plan the construction, and refine the project schedule and cost; typically, on an open-book cost reimbursable basis.
During the development phase, the owner will have access to more performance and cost data than would normally be the case under a P3 or fixed-price arrangement. To leverage the power of this information, an integrated project controls function can efficiently capture, analyze and report the available data to support the owner’s role as contract administrator.
The project controls team plays an important role as the design is developed and the parties work together to collectively establish the scope, cost and delivery schedule by providing benchmarked data, data analysis and helping to plan the project.
Another fundamental role of project controls is to develop and analyze the project risk profile, first identifying and assessing the risks and undertaking statistical analysis to determine the potential cost and schedule impact, which then informs the contingency budget and allocation of responsibilities between the parties. Taking the time to properly understand and assess risk is crucial in a contracting arrangement that shares risk. Given the nature of these contracting methods, a high volume of change is expected as the project develops. An integrated project controls approach ensures that these changes are accurately identified, quantified, reviewed and implemented, and any residual risk is managed.
This shift in contracting approach is an exciting development for Canada. It presents an opportunity to bring the best elements, and the learnings, from early adopters of the strategy in the United Kingdom, Australia and elsewhere in the world.
Michelle Throssell is a director with Turner & Townsend with more than 15 years of experience in program and project controls. She currently leads her company’s Project Controls practice in Canada.
The 2024 Canadian Construction Association conference in Punta Cana, Dominican Republic, will be remembered for great weather and a lot of food for thought. The event, which attracted more than 600 attendees to the Caribbean in March, was an unofficial changing of the guard as it was the final annual conference for outgoing-president Mary Van Buren.
Rod Gilbert succeeded her as president of the national organization in May of this year. Van Buren expressed her gratitude to the organization and industry during the conference’s closing gala.
Opening the event was keynote speaker, and lead singer of the band moist, David Usher, who proclaimed, “Change is the new normal.” The singer, and founder of artificial intelligence creative studio Reimagine AI, explained that “big disruption is coming to all industries.” He shared his insights about how Artificial Intelligence (AI) is augmenting the creative process in music as well as many other sectors, including construction. “In this rapidly changing world, creative thinking is your competitive advantage,” he advised.
Tim Coldwell also talked AI, discussing challenges facing the industry. “Imagine an AI system where you’re in a design and it
tells you exactly where in the world to buy a certain material, and whether to buy from a specific distributor or supplier,” he said, painting a picture of efficiency through technology. “I think there’s a huge opportunity for distilling down all the stuff that’s in our supply chain into smart applications.”
In addition to sessions putting a focus on productivity, housing and infrastructure, speakers also addressed the industry’s need for workers.
“We are not replacing ourselves, which is putting more pressure on immigration system to help backfill,” said BuildForce Canada’s Bill Ferreira as he discussed birthrates and the need for immigration to support labour needs. He spoke about the need for reform to the process used to better align immigration openings to workforce needs. “Immigration policy clearly has not been supporting the construction industry the way it needs to be supported.”
“Infrastructure is a political football,” said Paul Smetanin, president of the Canadian Centre for Economic Analysis, as he painted a dour picture of Canada’s economy and the impact of infrastructure spending. “The lack of investment in infrastructure is now not a long-term problem. It’s here. And it is going to affect everyone in this room.”
Taking the conference in a more positive direction, several individuals, companies and associations were recognized during CCA’s National Awards ceremony. Winners included Ledcor Group, the Vancouver Island Construction Association, Giatec, Ledcor Pipeline, Kinetic Construction, Graham Group, the Construction Association of Nova Scotia, PCL’s Dave Filipchuk, and Ryan Davis of Marco.
And CCA’s annual exploration of new products, the Innovators Pitch, featured presentations from three companies that have benefited from mentorship from CCA members, with one winner being selected from the trio.
“Ladders are well over 10,000 years old and are still the most commonly used piece of access equipment globally. Unfortunately, they’re also the leading cause of falls… That’s why I built my product,” explained Jordan Spencer, founder and CEO of Ladder Spike, and winner of the competition for its ladder anchoring system.
Next year’s conference is scheduled for March 11 to 14 at the Fairmont Chateau Frontenac in Quebec City.
ne of the most important trends in automation is the rise of collaborative robots or cobots – robots that work side-by-side with humans to enhance their productivity. This model is particularly applicable in construction, where a dwindling supply of skilled workers is making productivity an imperative.
Productivity-enhancing automation is well established with heavy construction equipment. Today, a worker can operate an excavator from a remote device, allowing it to operate in dangerous areas without compromising operator safety. With dozers, geo-enhanced precision blade control enables an operator to complete a grade with fewer passes.
Technology that extends the capabilities of humans reduces time, effort, and energy consumption, enables novice operators to come up to speed more quickly, improves safety, and encourages more people, notably women, to join the workforce.
A few years ago, Kevin Albert, co-founder and CEO of construction technology provider Canvas, wondered why the same thinking couldn’t be applied elsewhere in the construction industry.
“When we look at construction as a whole, we have great high-leverage equipment in the exterior spaces – excavators, bobcats, dozers – that we can use,” says Albert. “But when you go into the interior, the best we have is a scissors lift that somebody stands on, and the rest are hand tools. The problem is that we don’t have the tools to handle the precision of interior work.”
Albert and his colleagues saw an opportunity in drywall finishing and founded Canvas in 2017.
“Drywall finishing is one of the most labour-intensive trades in construction, because for every wall you finish, you have to come back multiple times to trowel on more compound,” says Albert. “If you want to get a 20,000 square foot wall done, you’re actually doing 100,000 square feet of finishing work.”
With the robot, the work is done with two passes instead of the
usual five, increasing a worker’s productivity by between 50 and 100 per cent, he says. “It’s really a very different process.”
Canvas uses a robotic arm by Universal Robotics (UR). The machine has a user-friendly video game-like interface that makes it easy for the drywaller to set up. The worker typically undertakes the more skilled aspects of the work, such as corners, and leaves the high-volume repetitive work to the machine.
“We don’t think of full autonomy the way we think of autonomous vehicles,” says Albert. “It’s more like a semi-autonomous excavator where an operator can produce so much more than they could manually.”
Canvas is typical of a current trend that is seeing the introduction of task-specific robotic applications in construction.
“We’re seeing mechanization of specific build areas that are being explored now due to the cost of labour,” says Thomas Strong, principal at construction tech firm wired.construction and CEO of Building Transformations, a not-for-profit serving the digital needs of the construction industry. “Canvas would be an example of that, where someone has built a purpose-built robot.”
Other examples include Raise Robotics, which takes over dangerous tasks such as installing façade brackets on building exteriors, the Hilti Jaibot, which drills overhead holes and hangs pipe and mechanical equipment, Semi-Autonomous Mason (SAM), which builds brick walls, and Dusty Robotics, which deploys a mobile robot to print layouts directly on concrete floors.
While many construction workers approach robotics with some apprehension, the technology brings the benefits of removing monotony and safety risks.
“I think the unions are going to see that these robots are just sophisticated tools that don’t necessarily replace workers, but help workers be safer and more productive,” says Strong. “And right now, we have a labour shortage. So, anything we can do to keep our skilled labourers happy so they work longer and don’t retire is something everybody is going to be supportive of.”
The technology can also help companies attract more young people to the profession.
“Right now, we’re retiring two people for every one that enters the industry,” says Albert. “We really need to figure out how to make these jobs more relevant for the next generation. If you’re getting paid to learn how to use robots, that’s not just a skill set that’s useful in construction, but in many other industries.”
Jacob Stoller is principal of StollerStrategies. Send comments to editor@on-sitemag.com.
Strategies to solve one of the top risks facing the construction industry.
ike many industries, the construction sector has a labour supply crunch. With one-fifth of the nation’s construction workforce nearing retirement, the construction sector will not be able to keep up with the substantial demand for its services, and contractors and design professionals will be left trying to find ways to fill the positions left vacant in the coming years. Human resources strategies of all types are needed to attract and retain not only talent, but ideally top talent.
Strategies to achieve optimal attraction and retention outcomes for your organization may include some of the following tactics.
Compensation matters. It is often the prime driver of a person’s decision to change jobs, or to stay. Know the market price for talent in each role you need to fill by using compensation benchmarking solutions.
If possible, try to find a way to open up ownership within your organization to your employees. Compensation is annual but equity in a successful organization can build wealth. This can be a tremendous driver to attract and retain the best talent. Further, companies that have broad employee ownership through structures like an Employee Stock Ownership Plan (ESOP) have very strong alignment between management and employees given the vested interest all, or most, employees have to drive revenue growth and profitability.
Compensation also includes the benefits provided by the employer. Make sure your health and dental benefits are not only competitive, but offer creative “value-adds” to your employees.
For example, flexible accounts continue to grow in popularity. It is difficult for a traditional benefit design to encompass all the elements that are important to individuals as we all have different needs and areas of importance based on our situation/family. Augmenting plan designs with employer-funded flexible accounts such as health spending accounts and personal spending accounts provides employees funds that can be used in a way that is most meaningful to them. Because the allotment is pre-determined and set by the employer, it is a cost-effective approach.
Ensuring your employees have strong health and dental benefits will also ensure your employees are given the opportunity to show up strong and healthy to drive more value for your organization. Once again, take advantage of benchmarking solutions within the market to ensure that you have a program that will optimize attraction and retention of talent.
The construction industry can be dangerous. The best employees know this and look for employers that respect and plan for risk. Having strong safety and wellness offerings, in combination with strong health and benefits offerings, drives better talent acquisition outcomes. Consider tapping into your risk and insurance partners to benchmark your safety programs against your peers and to uncover wellness solutions that can attract talent to your company.
Financial wellness is also a vital human capital solution used by top employers to ensure they obtain the best levels of talent from the sector. Helping employees create wealth and be ready for retirement tells the employee you want to help them now and throughout their entire life. Benchmarking pension plans against your peers is, once again, a great way to ensure competitiveness.
Draw on the entire potential workforce by ensuring your compensation and benefits offering is designed for all talent in the market. The more candidates you have to draw from, the greater the likelihood you will fill your organization’s talent needs with the best quality employees. Exploring how your company can meet the needs of various generations, backgrounds and family situations is important.
Talent often wants to be part of something meaningful. They want to work with great people with great values. Vision, values and culture absolutely matter, and it will drive talent acquisition outcomes. Your vision will attract individuals who share a passion for your journey, which will accelerate your journey to that vision destination.
The best talent is curious and has a thirst for growth. Ensure your organization has outlets for that demand. Have a strong education, development and mentoring offering.
FUN – Fun absolutely matters. It creates a release for days where stress levels peak, and it allows people to develop more genuine relationships with each other. Having fun and creating a fun environment allows employees to get to know each other and thus have more honest and meaningful relationships. These relationships will drive better outcomes.
David Bowcott is the managing director, construction, at NFP Corp. Please send comments to editor@on-sitemag.com.
GCPay keeps work flowing, so you can finish on schedule and on budget.
Move away from tedious manual subcontractor payments, and put an end to headaches. Easily manage contracts and meet deadlines.
Guarantee lien waivers are present and error free. Stop back and forth emails with automatic and custom waiver generation. All with ERP integrations with platforms like Viewpoint, CMIC, and Sage. Help
ffective project claims management necessitates a comprehensive understanding and strategic consideration of applicable limitations legislation that imposes crucial deadlines and restrictions on the commencement of a legal action. Time can be a pivotal factor in determining the success or failure of project claims.
Construction claims are sometimes raised in litigation or arbitration proceedings as an afterthought or in reaction to an opposing party’s claims, which makes them more susceptible to a successful limitations defence. Missing a limitation period has, with few exceptions, the effect of barring the claim, regardless of the strength of its merits. By the same token, limitations statutes provide parties with certainty and finality for liability exposure from past projects.
While limitations legislation is not entirely consistent across Canada, provincial statutes have been periodically reformed to achieve a more consistent framework across the country. Prior provincial legislation was rooted in archaic English law and contained different limitation periods for specific causes of action, which often resulted in confusion. In general, the defining feature of these reforms has been to simplify and shorten the applicable limitation periods.
In Ontario, the Limitations Act sets out a basic limitation period that a legal proceeding shall not be commenced after the second anniversary of the day on which the claim was “discovered.” Discovery is fact-specific, but it essentially means that the two years starts to run from the day on which the person knew, or a reasonable person with commensurate abilities ought to have known, of the injury, loss or damage in question.
The basic two-year limitation period does not apply where a particular statute establishes a different limitation period. For instance, in Ontario, the precise timelines in the Construction Act related to lien matters remain unchanged. In addition, parties must remain aware of circumstances where they have agreed, by contract, to more constrained timelines for notifying and initiating claims.
There is an ultimate limitation period adopted in the Ontario act, and in such provinces as Alberta, B.C., New Brunswick, and some others. There, no proceeding shall be commenced after the 15th anniversary from the date upon which the act or omission underpinning the claim took place. This ultimate limitation period operates to extinguish a claim, regardless of whether the relevant act or omission has been discovered or was discoverable by the injured party.
This represents a major change from the previous framework, which provided for a 30-year ultimate limitation period that was subject to a discoverability principle. The practical consequence of
this ultimate limitation period for contractors and owners cannot be understated. It provides a great deal more certainty and finality with respect to potential claims from past projects.
Certain exceptions to the ultimate limitation rule do exist, including in relation to environmental claims and fraudulent conduct, but their application can be complex and should be considered with the benefit of professional legal advice.
While these limitations reforms have been in force in certain provinces for many years now, the body of case law is still developing. For example, in a case concerning storm sewer installation in St. Catharines, the Ontario Superior Court recently confirmed the strict interpretation of the 15-year ultimate limitation period on the basis that the initial act of negligence was determinative of when the clock started to run, and not its continuing consequences.
Tolling agreements: Some provinces, including Ontario, allow a limitation period to be suspended or extended by agreement of the parties, subject to certain requirements. In these circumstances, a tolling agreement can be used to provide the parties with additional time to negotiate and potentially resolve disputes without risk of breaching the limitation period.
Keep diligent records: Organizing and cataloging contracts, change orders and other documents systematically serves as a critical resource when navigating potential claims. Timely documentation of incidents, delays, and damages can significantly bolster the validity of claims and provide essential evidence.
Take a conservative approach: Parties should think and act conservatively when approaching limitations periods to avoid the risk of losing their legal right to raise a claim due to a missed deadline. In the St. Catharines case, the court ruled that the timing of the defendant’s response to the claimant’s correspondence had no bearing on the applicable limitation period. Parties should refrain from allowing issues to linger unresolved through correspondence and instead assert their rights promptly and proactively to safeguard their interests.
Joseph Campbell is counsel in BLG’s Toronto office and is a member of the construction and international trade and arbitration group. This article provides an overview and is not intended to be exhaustive of the subject matter contained therein. Although care has been taken to ensure accuracy, this article should not be relied upon as legal advice.
GOMACO offers the full range of concrete slipform pavers, curb and gutter machines, trimmers, placer/spreaders, texture/ cure machines and bridge/canal finishing equipment. GOMACO equipment features our exclusive and proprietary G+® control system, created in-house by our software engineers from the wants and needs of contractors paving in the field. At the heart of GOMACO equipment is our passion for concrete and our commitment to our customers. We look forward to visiting with you about your upcoming paving projects and your concrete paving equipment needs. Our worldwide distributor network and our corporate team always stand ready to serve and assist you.