




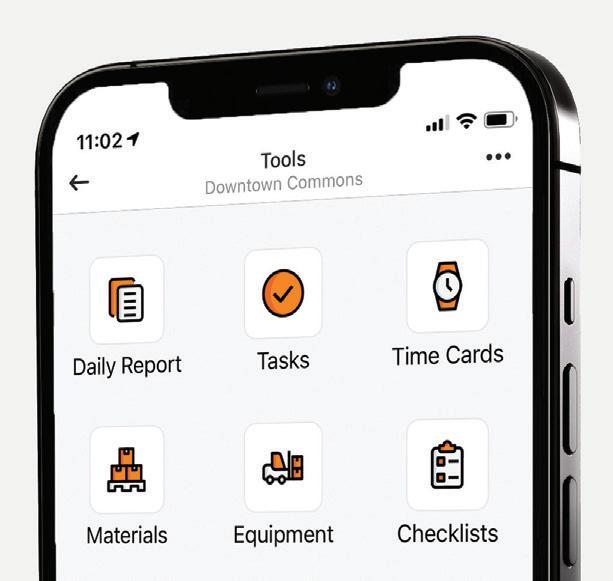

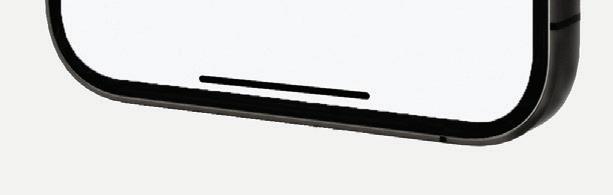

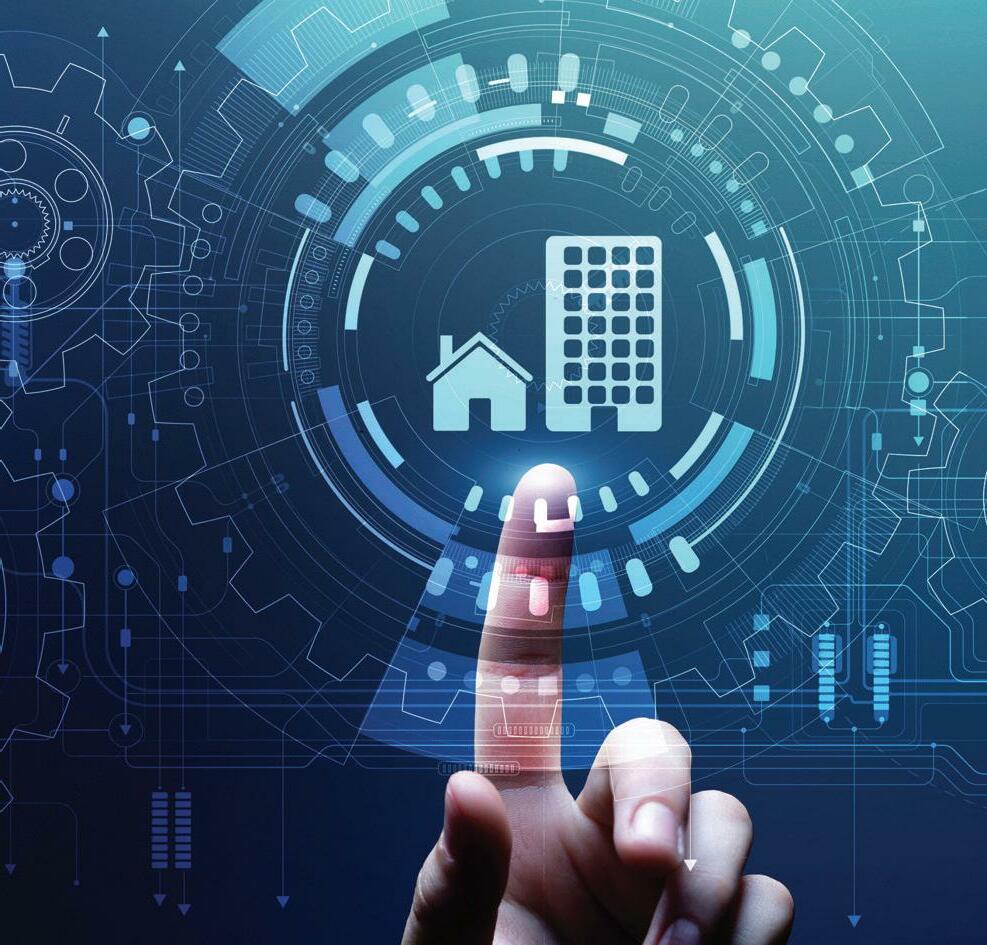
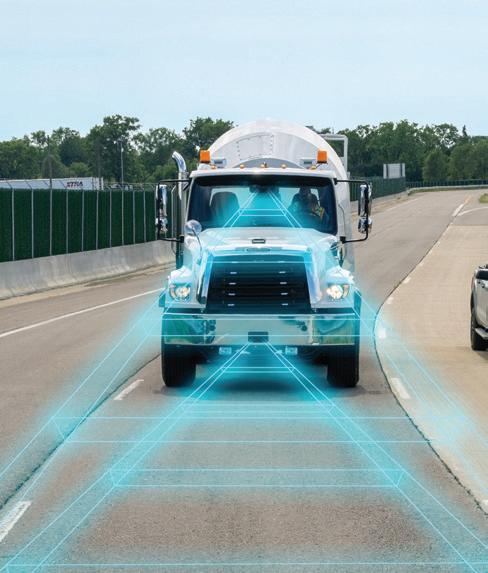
HOW
AN
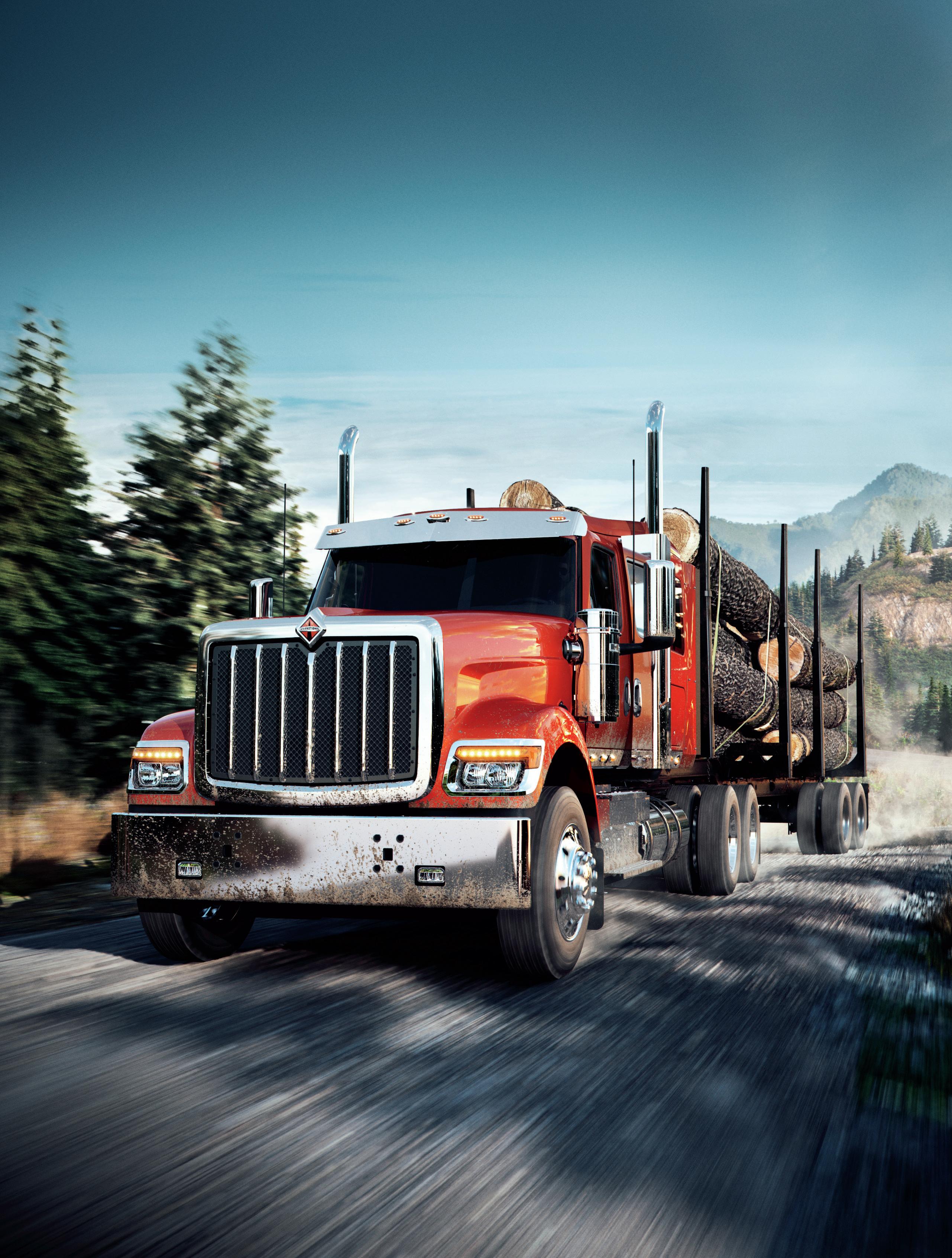
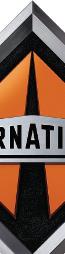

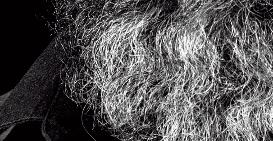

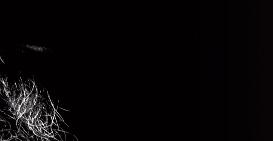

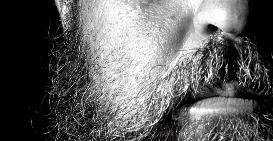
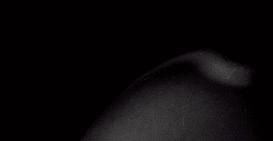
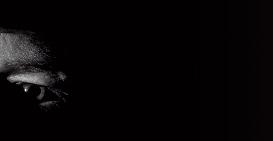

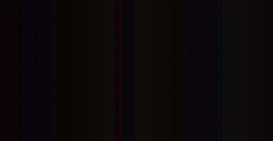

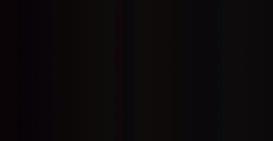
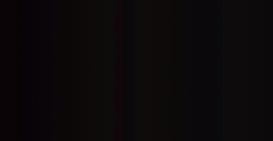
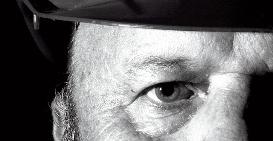
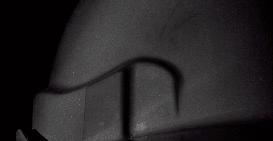
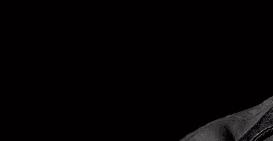

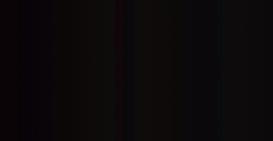
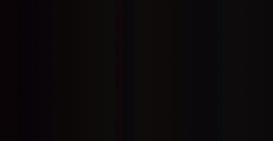

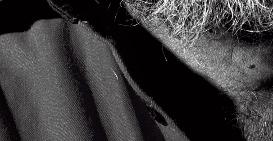
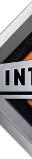
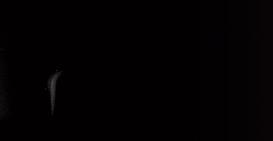
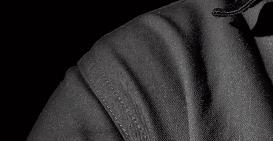
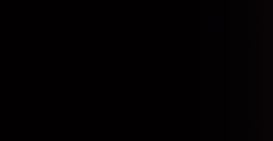



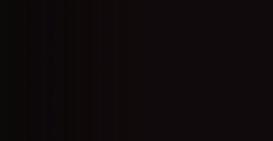

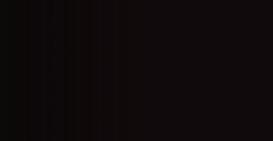
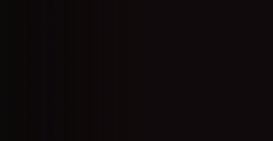

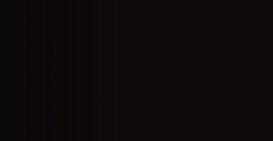





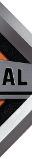
Having worked at and toured far too many construction sites to count, some of the things I’ll never get comfortable seeing are coroner’s reports and news stories about yet another acci dent or death on a construction site, especially since so many of them are preventable.
Construction has always been a danger ous occupation. In 2020, 193 of the 921 workplace deaths reported in Canada were in the construction sector. That’s more than 20 per cent, and number 1 on a list that nobody wants to lead.
While it is too soon to have the consolidat ed figures for 2021 and 2022, you don’t have to spend much time on Google to find reports about incidents involving cranes, trenches, falls and heavy machinery from the past two years, including multiple reports about incidents this past summer that will be included when the 2022 fatality figures are compiled.
A few years back, former Blue Jays catcher and current broadcaster Buck Martinez ex plained to me that the play gets faster the clos er you get to the field, and his comment rings loud in my head when I hear workers explain why they didn’t go back to the truck for their harness, or that they were just hopping into a machine to quickly move it without thinking about a spotter, or that they thought they could save a little time by stretching a little further rather than moving scaffolding or a ladder.
It’s easy to point out flaws after the fact, especially since things can happen quickly on a jobsite and small mistakes or the pushing of boundaries can suddenly result in unexpected consequences. It’s why I’m impressed when I hear someone on a site remind a fellow worker about things like eye protection or moving a ladder, or when I tour a site and see a priority placed on safety, and that workers are made
aware of potentially dangerous situations.
With the construction sector in need of a massive influx of new workers, a focus on safety is going to be even more important than ever over the next few years. Young workers, new Canadians, and even mid-career workers who are new to the sector should all be made aware of safety regulations, including their responsibilities. And it should not be assumed that “common sense” will prevail. It falls on an employer to ensure that the people on their sites have proper training, have appropriate licenses, and are acting in a proper manner.
The most recent job vacancy figures show that Canadian construction firms were look ing to fill more than 80,000 openings this past July alone. This level of opportunity is a double-edged sword. On the one hand, if a worker doesn’t feel safe they should be able to move to another company fairly quickly. On the other hand, it increases the risk that employers may have to hire anyone they can get, includ ing workers who either don’t know how to work safely, or worse, who refuse to do so.
Companies that put a focus on safety can influence new workers to watch out not only for their own safety, but also that of their fellow workers, which goes a long way towards building a jobsite culture that attracts workers who foster a positive work experience.
By prioritizing safety and making it an expectation and part of a company’s culture, it is possible to reduce the risk of yet another headline announcing that one less worker will make it home tonight.
Until next time, stay safe and do good work.
Adam Freill / EditorOn vocational trucks:
“The focus on comfort, safety and technology is simply a reflection of driver demand and industry trends.”
On remotely operated equipment:
“As the industry has seen with recent innovations such as GPS and mobile apps, the key to adoption will be absorbing changes to existing work processes.”
VOLUME 67, NO.6/October 2022 www.on-sitemag.com
Print and digital subscription inquiries or changes, please contact Angelita Potal
Email: apotal@annexbusinessmedia.com Tel: (416) 510-5113 Fax: (416) 510-6875
Mail: 111 Gordon Baker Road, Suite 400, Toronto, ON M2H 3R1
PUBLISHER | Peter Leonard (416) 510-6847 pLeonard@on-sitemag.com
EDITOR | Adam Freill (416) 510-6821 afreill@annexbusinessmedia.com
MEDIA DESIGNER | Lisa Zambri lzambri@annexbusinessmedia.com
ASSOCIATE PUBLISHER | David Skene (416) 510-6884 dskene@on-sitemag.com
ACCOUNT COORDINATOR | Kim Rossiter (416) 510-6794 krossiter@on-sitemag.com
diversifying the workforce:
roughly
than 15 per cent of the jobs in Canada’s
On cyber security and risk:
“The construction sector is much more vulnerable to cyber-attack than other industries.”
On scanning technology for construction:
“Contractors and owners should consider the additional costs of having consistent scans taken in light of the overall size and cost of the project and the likelihood of disputes arising.”
AUDIENCE DEVELOPMENT MANAGER | Urszula Grzyb (416) 510-5180 ugrzyb@annexbusinessmedia.com COO | Scott Jamieson sjamieson@annexbusinessmedia.com
Established in 1957, On-Site is published by Annex Business Media 111 Gordon Baker Road, Suite 400, Toronto, ON M2H 3R1 Publications Mail Agreement No. 40065710
ISSN: 1910-118X (Print) ISSN 2371-8544 (Online)
SUBSCRIPTION RATES Canada $49.50 per year, United States $113.00 per year, Other foreign $136.50, Single Copy Canada $13.50. On-Site is published 7 times per year except for occasional combined, expanded or premium issues, which count as two subscription issues. Occasionally, On-Site will mail information on behalf of industry-related groups whose products and services we believe may be of interest to you. If you prefer not to receive this information, please contact our circulation department in any of the four ways listed above.
Annex Business Media Privacy Officer privacy@annexbusinessmedia.com Tel: 800-668-2374
Content copyright ©2022 by Annex Business Media may not be reprinted without permission.
On-Site receives unsolicited materials (including letters to the editor, press releases, promotional items and images) from time to time. On-Site, its affiliates and assignees may use, reproduce, publish, re-publish, distribute, store and archive such unsolicited submissions in whole or in part in any form or medium whatsoever, without compensation of any sort.
DISCLAIMER This publication is for informational purposes only The content and “expert” advice presented are not intended as a substitute for informed professional engineering advice. You should not act on information contained in this publication without seeking specific advice from qualified engineering professionals.
Coming soon: CONEXPO-CON/AGG 2023
Registration is open for CONEXPO-CON/ AGG 2023, which includes the Interna tional Fluid Power Exposition (IFPE). The set of shows are set to take over the Las Vegas Convention Center and Las Vegas Festival Grounds this coming spring, running from March 14 to 18, 2023.
Held every three years, the upcom ing edition of North America’s largest construction trade show will feature more than 1,800 exhibitors across over 2.7 million square feet of exhibition space as they showcase the industry’s most advanced equipment and construction industry innovations.
“We are thrilled to return to Las
Vegas in March of 2023 to bring the construction industry together. If you’re a construction professional, you won’t want to miss this opportunity to see the industry in action and learn new ways to take your business to the next level,” said CONEXPO-CON/AGG show director Dana Wuesthoff. “No other show brings together as many segments of the construction and aggregates industries in one place. Be sure
Global manufacturer of materials processing machinery and aerial work platforms, Terex Materials Processing (MP), has announced its acquisition of Canadian company ProAll, a specialist producer of mobile volumetric concrete mixers.
ProAll, which was initially an importer of volumetric mixers into Canada before producing its own volumetric mixer products for the North American and global markets, employs 170 people with a main production base in Olds, Alta., and a service and installation site in Keller, Texas.
The addition of the brand will allow Terex to expand its overall presence in the concrete mixer space as ProAll joins Terex Advance, which makes front-discharge mixer trucks, and Terex Bid-Well, which manufactures roller pavers for bridge and canal work.
“ProAll will provide us with exciting prospects to expand into new markets and
grow our knowledge and market share in the mobile concrete pouring industry. We look forward to embarking on this journey together with our new colleagues in Alberta and Texas,” stated Jason Talbot, Terex’s vice-president and GM, MPS and Environmental for the United States and Australia, to whom the ProAll team will report.
to register early so you can take advantage of the best badge and travel rates.”
In addition to the equipment exhibi tions, an educational component of the event will offer more than 170 sessions covering everything from aggregates to technology solutions.
More information about the show and its learning opportunities can be found at www.conexpoconagg.com.
“For the past 50 years, ProAll has been a leader in mobile concrete delivery,” said Larry Koop, co-owner and former managing director of ProAll. “The existing resources at Terex MP will bring huge benefits and global opportunities to our existing team and I am delighted to see their hard work pay off.”
Walmart Canada is investing $1 billion in its infrastructure this year as part of the retailer’s efforts to speed up and transform the business for its customers. A cornerstone of its spending in Canada is $100 million earmarked for the building of a new high-tech sortable fulfillment centre near Montreal, in Vaudreuil-Dorion, Que.
The first such centre for Walmart in the province, the facility will be built by Harden, a second-generation family-owned real-estate company that owns and operates commercial, residential and industrial properties in Quebec and Ontario.
“We are thrilled to partner with a brand and business as strong and reputable as Walmart,” said Tyler and Chris Harden, co-CEOs of Harden. “This state-of-the-art fulfillment centre is a true testament to their vision for the future of retailing and
a long-term commitment to Vaudreuil and the province of Quebec as a growing hub. We are proud to be executing the construction of this project on behalf of Walmart Canada, with our in-house construction team, and to add this asset to our portfolio.”
The new fulfillment centre will be approximately 457,000 square feet and
will serve as a delivery hub for millions of customer orders in Quebec and Atlantic Canada. The facility, which is expected to open in 2024, will be capable of ship ping 20 million items annually from the facility to local customers and will create approximately 225 new jobs in Quebec, in addition to the construction and engineer ing jobs.
Supported by TCA, BOMA, BILD, Concrete Ontario and CABA, The Buildings Show is set to roll in the South Building of Toron to’s Metro Toronto Convention Centre from November 30 to December 2, and On-Site will be live, on site, in booth 453. Be sure to drop by to pick up the latest edition and to say hello to our crew.
Comprised of Construct Canada, PM Expo, HomeBuilder & Renovator Expo, and the World of Concrete Toronto Pavilion, The Buildings Show provides a unique platform for the industry to see first-hand a complete overview of the built environment as it showcases the construction, building design, renovation and property manage ment industries.
In addition to a considerable trade show floor, the event also offers numerous learn ing sessions, with continuing education credits available from such organizations as BOMA, OAA, BSSB, CAHPI and ARIDO, as well as networking events and supplemental presentations. Full details are available at www.thebuildingsshow.com.
PHOTO COURTESY OF WALMART CANADA (CNW GROUP/WALMART CANADA CORP.)Walmart Canada to build its first fulfillment centre in QuebecHarden to construct delivery hub to service Walmart customers in Quebec and Atlantic Canada. TRIMBLE
Trimble has purchased privately held B2W Software, a provider of estimating and operations solutions for the heavy civil construction industry.
“With the acquisition of B2W, Trimble will be able to provide an unparalleled end-to-end digital experience—connecting the digital to the physical—for heavy civil and infrastructure contractors,” said Elwyn McLachlan, vice-president of Trimble’s Civil Solutions Division.
The addition of B2W’s suite of pre-construction and operations capabilities will expand Trimble’s civil infrastructure portfolio and Trimble Construction One, a purpose-built connected construction management platform.
B2W’s integrated suite of applications includes estimating, scheduling, field tracking, equipment maintenance, data capture and business intelligence. By combining these capabilities with Trimble’s rich field data, project management, finance and human capital management solutions, civil contractors will be able to bridge the gap between office and field in new ways, promoting transparency, efficiency and ultimately profitability.
Alberta’s legislation mandating owners to provide payment to their contractors within 28 days of receiving a proper invoice for construction services and requiring contractors who receive payment from an owner to subsequently pay their subcontractors within seven days is now in force.
Formerly known as the Builder’s Lien Act, the Prompt Payment and Construction Lien Act creates rules for the timing of payments and sets out a streamlined adjudication process for disputes related to payment or work performed as an alternative to court.
David Bowcott and Adrian Pellen have joined NFP to co-lead the company’s North America Construction & Infrastructure Group. The group will provide comprehensive construction and surety services designed specifically for complex national and cross-border projects.
In addition to writing a regular column for On-Site magazine, Bowcott has experience in global construction and enabling clients and partners to achieve optimal risk profiles for their organizations and projects. He also serves as a board member for the Canadian Construction Association and The Institute of Asset Management.
Pellen has cross-border experience serving the infrastructure sector, addressing project risk, account management and claims. He is also a U.S. Branch Council member for IPFA, the global professional association for the infrastructure and energy financing industry.
“Appointing these two industry leaders and establishing an integrated NFP North America Construction and Infrastructure business strengthens our position in the marketplace and ability to help clients navigate complexities and protect their assets,” said Doug Hammond, NFP’s chairman and CEO.
The new act applies to all private construction contracts in Alberta created on or after August 29, 2022. Current contracts that extend past two years must become compliant with the new rules by August 29, 2024.
22_002424_On_Site_OCT_CN Mod: September 6, 2022 2:54 PM Print: 09/14/22 11:13:26 AM page 1 v7
Speaking from a recent Cement Associ ation of Canada (CAC) event at Lafarge Canada’s cement plant in St-Constant, Que., Canada’s minister of environment and climate change, Steven Guilbeault, announced the launch of the Net-Zero Challenge, a new national voluntary initiative for businesses operating in Canada. Businesses that join the challenge commit to developing and implementing credible and effective plans to transition their facilities and operations to net-zero emissions by 2050.
“Businesses planning for the future can see already that it pays to be part of the low-carbon economy of the 21st century,” stated Guilbeault. “The Net-Zero Challenge is designed to challenge businesses, big and small, to transition to cleaner ways of doing business, and offers both the tools and recognition to support their efforts.”
The CAC is one of a dozen founding organizations and companies that have joined the program, which seems appropriate as Canadian cement industry is a prime example of an entire industry that is in the process of transitioning to net-zero emissions, in close collaboration with the Government of Canada.
“Climate change is our industry’s most significant challenge,” said Adam Auer, CAC president and CEO. “By charting a credible, transparent path to net-zero emissions, our indus try continues its history of leadership in building the sustainable world of tomorrow.”
For companies to join and remain in the program, they must meet minimum requirements, submit annual progress reports, and produce five-year updates of their net-zero plans. Companies that fail to meet the requirements will be removed from the program.
Andy Trewick, president and CEO of Graham, took on the gruelling challenge of running five kilometres per day, for five days, across five Graham locations to raise more than $280,000 for the Canadian Mental Health Association (CMHA) and National Alliance on Mental Illness (NAMI) in the United States.
The 5/5/5 Moving for Mental Health runs were an initiative born out of Trewick’s commitment to building awareness about the positive impact physical activity can have on mental health. Setting out with an initial fundraising goal of $100,000, he hit that number and just kept running, doubling the target to raise $200,000, and going beyond even that target to reach more than $280,000 at last count. Those funds will be used to provide mental health resources for youth and adolescents on both sides of the border.
“I’m not a serious athlete, but I am serious about physical and mental health. We’re all on our own mental health journey. At Graham, we’re committed to helping our employees build healthy and happy lives. The mental health and psychological safety of our workforce, partners and community is a critical focus area across our company. We believe an investment in wellness is essential to ensuring our employees’ best performance and their overall wellbeing,” explained Trewick. “If living through a pandemic has taught us anything, it’s that mental health matters and affects everyone no matter who they are.”
In addition to the outpouring of donations received, five Graham corporate partners, Borden Ladner Gervais, headversity, RBC, Travelers Bond and Zedcor Security Solutions generously donated sponsorship money to offset expenses to ensure 100 per cent of the donations go directly to the charities.
“CMHA National is inspired and thrilled by Graham and this initiative,” said Margaret Eaton, national CEO of the Canadian Mental Health Association. “This generous contribution will aid in providing mental health care and support for youth, their families and communities across Canada. Our huge thanks and admiration to all who participated in the run and donated.”
In the insurance world, it’s often said that ‘water’ is the new ‘fire.’ And the new normal for annual catastrophic losses related to water damage is around $2 billion, according to the Insurance Bureau of Canada (IBC).
But the problem is even more acute in high-rise construction projects, where it can be hard to pinpoint a leak, or when a leak occurs at night, or on the weekend when the site is unoccupied. That means a small leak can turn into millions of dollars in damage during a project.
Severe water damage causes several challenges for construction companies. Related project delays can translate into increased costs in labour and materials and can also drive up financing costs from lenders to finish the project, heavily impacting developers’ bottom lines. The reality is that water damage during the construction stage of a building is one of the largest risks to completing a project on time and on budget.
“Water damage is a very common occurrence these
days with high-rise construction, in both residential and commercial occupancies. Each loss is unique but the common denominator is water and gravity — a destructive combination,” says Jonathan Graham, Underwriting Director of Construction & Contracting with Northbridge Insurance, a leading Canadian commercial insurance provider.
“We look at the frequency and severity of water losses, and in the last five years both have been trending in the wrong direction,” he says.
The impact on losses and project delays is why both the insurance and construction industries have begun seeking out risk mitigation strategies, such as water leak and flood protection technology. This technology – widely being retrofitted for years into existing buildings and structures — also has applications during the construction phase of a building.
Recently, Northbridge worked with two developers and their brokers to roll out water IoT (Internet of Things) technology during the construction phase of two high-rise
Photo © Alex Drai / iStock / Getty Images Plusprojects. The goal was to test the technology’s effectiveness in mitigating and reducing water damage. To better support the construction industry, Northbridge has since partnered with a leading water IoT solutions provider to offer discounts to customers on construction water leak and flood protection.
Here’s how the technology works: Temperature, humidity, moisture, and water detection sensors are strategically placed around a building and communicate via a Long Range Wide Area Network (LoRaWAN) — since construction projects are unlikely to have internet availability.
The sensors are connected in real-time to a dashboard and mobile app, providing 24/7 monitoring. If water is detected where it shouldn’t be, or water supply exceeds a predetermined parameter, alerts are sent to key contacts and water valves are shut off automatically or remotely
through the app.
The technology is sophisticated enough to sense moisture levels and to differentiate between normal and excess water flow for a duration of time. And while it may not prevent a leak from happening, it can catch a leak in real time to mitigate damage.
On a project in partnership with Northbridge, Jones DesLauriers Insurance Management Inc. (JDIMI), a professional services firm specializing in corporate risk management and employee benefits solutions, worked with Tribute Communities, a builder of high-rise and low-rise communities.
Together, they tested a water IoT solution in a high-rise construction project which was of particular interest to Tribute, as they’d had to make four water-related claims on a state-ofthe-art commercial space about a decade ago. As a result of the damage, they had to rebuild the space three times over the life of that project.
“Those four leak claims cost us close to a year and a half,” says Gus Stavropoulos, Chief Financial Officer with Tribute Communities. “We learned a lot in that building and we learned there has got to be a better way to do this.”
When they rolled out water IoT sensors during the recent construction project, they didn’t have any significant water claims and credit the risk mitigation benefits of the technology for that outcome.
“We had one case where we got ahead of it,” he says. “There was a report of a pressure leak, and our staff quickly got the alert and dealt with it and it was done. It was a loose valve, but that could have turned into a quarter-of-a-million-dollars in damage—and a couple turns of a wrench saved us a lot of problems.”
He believes water IoT technology will revolutionize loss exposure on high-rise construction projects — and that the industry as a whole needs to be at the forefront.
“I wish this technology was available 10 years ago when we had a $3.5 million water damage loss,” says Michael Kucharuk, Partner and Account Executive with JDIMI. “Overall, I’m glad to hear Northbridge is proactively addressing water damage in construction projects through technology and connecting with GCs and brokers on the issue.”
We look at the frequency and severity of water losses, and in the last five years both have been trending in the wrong direction.
While there are hundreds of insurance providers registered in Canada, only a handful specialize in course of construction projects.
While there are hundreds of insurance providers registered in Canada, only a handful specialize in course of construction projects.
“There are definitely fewer insurers now than prior to 2020. Of those still available, they may not be comfortable covering 100 per cent of the risk and so multiple insurers are needed to cover a portion of the risk to reduce their exposure in the event of a loss. This means that more negotiations are required due to the nature of having multiple insurers participate — especially on large multi-tower projects,” says Cathy Ciccolini, Partner at Masters Insurance Limited, which also partnered with Northbridge on a water IoT pilot project.
She believes water IoT technology will be useful to the construction industry in the future — it may even become a requirement, like sprinklers or smoke detectors. Future projects
will be marketed with ‘no water damage claims’ from past projects, allowing new insurers to offer potentially more capacity, as well as better rates and deductibles.
“I strongly recommend developers adopt this type of protection. Most of them have had a water damage claim — some small, some larger,” says Ciccolini. “I impress upon them that water damage claims will affect the next project I have to place for them.”
“While it is still very much in its infancy in this part of the world, genuine interest from both developers and insurers is prevalent and gaining momentum,” Kucharuk says. “Not that long ago, developers heard about IoT technology as a new ‘thing’ that may come to fruition one day. This clearly isn’t the case anymore — forward thinking developers are familiar with how to use the technology to their benefit.”
Indeed, he says it’s a natural, pragmatic progression to help reduce both frequency and severity of claims, which is key for insurers and vital to developers — as it will greatly aid in keeping their construction timelines on track and reducing water damage costs.
“There’s a lot of opportunity to reduce the likelihood but also the size of a water leak, so we can prevent or mitigate the risk by using this technology. It’s about identifying where the issues are and also being able to act remotely,” says Christopher Mastro, Director of Risk Services with Northbridge Insurance.
Developers also have the ability to pass on the cost of water IoT technology to the building owner once the project has wrapped up. And building owners can benefit from the technology post-construction, as it can help mitigate potential ongoing risks and insurance costs.
“It’s probably more cost-effective to put it in during construction because you can protect the site and ensure owners occupy the building on
time. If your building is 98 per cent done and a hose comes off a toilet on the 12th floor, you could set your whole project back by months,” says Mastro. “But for building owners, it offers ongoing risk management.”
While the technology can’t necessarily prevent the frequency of water-related events, it can have a dramatic impact on severity — providing timely insights to reduce the severity of loss — which is a win-win-win for construction companies, insurers and ultimately building owners.
Northbridge Insurance, Northbridge and the Northbridge Insurance Logo are trademarks of Northbridge Financial Corporation,licensedbyNorthbridgeGeneralInsurance Corporation (insurer of Northbridge Insurance policies).
This resource is provided for information only and is not a substitute for professional advice. We make no representations or warranties regarding the accuracy or completeness of the information and will not be responsible for any loss arising out of reliance on the information.
The impact on losses and project delays is why both the insurance and construction industries have begun seeking out risk mitigation strategies, such as water leak and flood protection technology.
Statistics Canada reports that investment in building construction continued on an upward trend that started in October 2021, rising almost one per cent this past July to hit $21 billion. Both the residential and the non-residential sectors showed increases, with invest ment in non-residential construction nudging up 0.1 per cent to $5.3 billion in July.
Commercial investment was up a half per cent at $3 billion for the month, cool ing down after posting strong gains in June. New warehouse construction contributed significantly to the growth. Warehouses have increased of 42 per cent since March 2021 Conversely, investment in new office buildings has been on a downward trend.
Investment in the industrial component reached $1 billion in July, with gains in seven provinces. Institutional construction dipped 2.3 for the month, coming in at $1.4 billion, the largest decline for the component since April 2020.
Investment in residential building construction grew to $15.7 billion in July.
The number of women working on construction sites in Quebec is rising, despite the existence of persistent obstacles. That’s according to a recently released report outlining the first two phases, and six years, of the Programme d’accès à l’égalité des femmes dans l’industrie de la construction (PAEF) 2015-2024, published by the Commission de la construction du Québec (CCQ).
In 2021, female workers on construction sites in that province numbered 6,234, or 3.27 per cent of the total workforce. That was an increase from 2015, when they represented just 1.49 per cent of workers on sites. Today, 15 per cent of companies in the industry employ at least one woman; this figure stood at eight per cent when the program was adopted.
The report noted the existence of persistent obstacles, including the work climate, as impeding progress, and found that a higher proportion of women (21 per cent) leave the industry after one year than men (15 per cent).
Investment in non-residential construction, July 2022 (in $Millions)
Canada 5,344.8 Newfoundland and Labrador 31.2 Prince Edward Island 19.2 Nova Scotia 68.7 New Brunswick 57.1 Quebec 1,284.1 Ontario 2,144.7 Manitoba 163.5 Saskatchewan 104.8 Alberta 671.1 British Columbia 778.6 Yukon 12.4 Northwest Territories 3.8 Nunavut 5.5
STATISTICS CANADA
Statistics Canada has indictated that the total value of building permits in Canada dipped by 6.6 per cent in July, to come in at $11.2 billion. Declines in both the residential and non-residential sectors contributed to the slip.
The residential sector was off 8.6 per cent, at $7.6 billion, while the non-residential sector had a more modest fall, dropping 2.1 per cent to $3.6 billion as gains in the commercial and institutional sectors were more than offset by losses in industrial permits.
The value of industrial sector permits tumbled 16.9 per cent as a 31.1 per cent drop in Ontario, its third consecutive monthly decline, weighed heavily on the numbers. Commercial permit values edged up 0.1 per cent, while construction intentions in the institutional component rose 7.9 per cent. British Columbia led the charge in the segment with a 207.2 per cent jump.
On the residential side, single-family home intentions dropped 5.7 per cent. Despite the decline, this component remained 14.8 per cent higher than the same month of 2021. The value of building permits in the multi-family homes component was also down significantly as six provinces posted drops, including a sizable 32.8 per cent fall in Ontario, pacing the component to an 11.1 per cent fall.
A selection of data reflecting trends in the Canadian construction industry
MTWO is a construction cloud solution that connects all stakeholders, processes, and data in one platform enabling better collaboration, driven decision making. With applications that address the plan, build, and operate phases of construction, MTWO is the next generation of construction project lifecycle management software.
On behalf of SoftwareONE, we are pleased to be sponsoring On-Site magazine’s 2022 Construction Technology Report. Technology is such an integral part of the building process and has transformed the way projects are completed. It has also played a pivotal role in keeping teams connected and businesses up and running during the challenges of the past few years.
While the industry has historically been slower to adopt new technologies, we’ve seen an uptick in recent years. Mobility and real-time project insights are no longer “nice-to-haves.” They are business critical in order to survive and thrive in this competitive landscape.
Even though technology usage is up in the AEC space, productivity remains largely stagnant. This can, in part, be attributed to the prevalent use of unintegrated point solutions. Utilizing disparate systems can lead to a number of problems, including redundant and error-prone doubling and tripling (and sometimes more) of data entry, and data silos.
Although construction businesses generate a ton of data, this information is severely underutilized. In fact, 95 per cent of data in the AEC industry goes unused. Luckily, we are making strides to remedy this. Connected systems such as an integrated cloud platform can help ensure businesses are maximizing the power of their data. Cloud platforms are equipped with comprehensive functionality and customizable workflows while connecting the entire construction lifecycle. Plus, with an open API, businesses can integrate different functions and data from existing standalone systems.
The industry is beginning to catch on to these advantages. A recent Deloitte study found that 76 per cent of engineering and construction decision-makers are putting more money into connected technologies because of the connected data that comes with them. Connected platforms will continue to have a big impact on the industry as businesses turn to technologies that deliver streamlined workflows and significant productivity gains.
Contractors work hard to stay on top of their businesses and meet the growing demands of the industry. But it’s not always easy. With bigger and more complex projects, unstable supply chains, and low profit margins, there’s little room for error.
Amidst these challenges, we strive to make things simpler. At SoftwareONE, we empower AEC firms and owners to digitally transform their businesses while winning purposeful work, improving project predictability, balancing risk, and reducing their environmental impact. We provide solutions and services on a truly global scale with a local touch. Our people are where it matters most – by our customers’ sides.
As the needs of the industry change and grow, so do we. We never stand still when searching for the best solutions and services to help our customers build faster, smarter, and better.
We are proud to serve this dynamic industry as a trusted technology partner and are excited to see what the future holds. The sky’s the limit to what we can build together!
All my best,
In late August, On-Site magazine hosted a panel of Virtual Design and Construction (VDC) experts to explore how 3-D models are currently being used in the building world, as well as how they are evolving in their capabilities and application.
In addition to providing advice about entering into this digital project workflow environment, panellists, Aaron Akehurst of PCL, Stephen Bianchi of Hatch, Hammad Chaudhry of EllisDon, and Steve Rollo of Graham Construction, shared insights into how their companies have been integrating such technologies as Building Information Modelling (BIM) and 3-D digital modelling into their projects.
They also discussed the evolution of
these digital technologies and how the next generations of the platforms are looking to integrate jobsite and third-party data, which will open the door to more robust modelling in the years to come.
“All of our major projects are lever aging some form of VDC workflows,” stated Akehurst, explaining that the use of VDC and BIM may not be as prevalent on smaller projects, generally due to the time necessary to set each project up, but acknowledging that even smaller or specialty projects are becoming targets to take in the benefits offered with 3-D visual ization and planning tools.
“The biggest thing that defines whether it makes sense to implement these VDC processes or BIM processes is the scope
and the complexity of said scope,” added Rollo. “Five to 10 years ago, we might have looked to assign a dollar-value of a project to define if we’re going to imple ment BIM or VDC processes on it. And while typically, the larger the dollar value, the more complex the project is, and the more benefit you would gain from these processes, that’s not always true.”
Using a basic but large warehouse and a smaller but more complicated renovation as examples, he illustrated how the smaller project and its scheduling and building system integration concerns would glean greater VDC benefit than the relatively basic design of the warehouse project that could be four-times the cost to build.
“I do believe VDC is a must for all
Contractors making greater use of digital models as capabilities continue to evolve.
major projects, as well as most minor proj ects, but it does depend on the scope and the scale of the job,” agreed Bianchi.
He explained that it wasn’t long ago that most of his company’s projects would be designed in 2-D, with VDC elements being designed from that step, if they were needed. “For some time now, we’ve been shifting away from the old traditions, and we’re pushing to generate our designs in 3-D.”
Going that route from the get-go offers such benefits as clash detection and the early identification of issues for more efficient resolution, but there are other benefits as well, he stated. “It also generates a very collaborative environment for the team.”
And companies are growing their digi tal teams to harness the benefit of having more experts and stakeholders weighing in at the planning stages. Not long ago, a BIM department may have consisted of a single digital expert who could provide insights when a BIM or 3-D question came up. Those departments are growing, and digital tools are making companies adjust focus. For example, Akehurst explained that his company is moving to take the idea of VDC and BIM to “move it to the centre of the project so that our entire proj ect teams have access to the 3-D model.”
With that focus, digital departments are expanding to play a role in more projects, and staff from outside digital departments are also expanding their skill
sets to provide input into the planning and execution ecosystems.
“I think a little bit of the shift is coming as upskilling of traditional project coordinators to be able to use those tools without having dedicated VDC folks,” explained Chaudhry.
“It allows a lot of the different disci plines to come together in a coordination model,” added Bianchi.
Looking at external members of digital teams, the panel agreed that collaboration was a key to success when working with these technologies, adding that collabora tion works best when it includes property owners as well as subtrades.
“The projects where we are having the best data structure and just general
setup are the projects where the owner is requesting something as a deliverable,” said Akehurst. “But the more stakeholders that we engage in that process, the more we get out of it, and the more the project benefits as a whole.”
“We see almost tenfold greater success when the sub-trades are brought into it as well,” stated Rollo. “They’re the ones that are constructing on site… the more input we get from those people actually executing the construction, the better, in my opinion.”
Having a strong team is not the only key to success, however. Much like how a tower’s strength is dependent upon the quality of its base, when it comes to VDC, BIM and the use of digital twin technologies, the quality and format of the data can be critical.
“We still have to understand that there is a disconnect in the industry from a garbage-in garbage-out perspective, as far as what data we receive inside the model to effectively extract that data,” warned Rollo. “If those parameters aren’t specified at the right time, or if we, as the GCs, are not at the table at the right time to articulate what we would want to extract, that makes it very difficult to effectively and efficiently do those takeoffs properly.”
“Making sure of that similar work breakdown structure in your schedule and your model is critical,” explained Akehurst. “If you’re starting from two different
places, you’re just going to be square peg-round hole for the entire project. You have to know where you want to go when you start your schedule and your model so that you can combine those two pieces together efficiently.”
Bianchi said that a major focus for him at Hatch has been “to try to ensure that these models are set up with trustworthy quantities, the right attributes, the classi fications, so that it could feed into these types of systems and provide a little bit more automation and trust.”
His company has also been putting a lot of focus on data-rich models. “These models will contain many attributes built into the model, so it’ll be a lot more than just a 3-D shape,” he said.
Chaudhry also illustrated some of the benefits that modelling tools can offer when they extend beyond simply visualizing a project to bring more business-side attributes into the integrated plans – a theme that was extended on by the rest of the panel. “We have had clients and projects at EllisDon where we’ve done that cashflow analysis with the model and tracking. But again, that’s not commonplace,” he said
When a time component is included in the digital model, some in the industry have suggested the use of the term 4-D, with the term 5-D being used to reference a cost management feature of an evolved digital modelling application, although
much debate remains about the naming conventions used. Despite some disagree ment on terminology, the theories at play do point to the growth potential that exists for VDC systems that rely on jobsite feed back from various inputs, including digital Internet of Things (IoT) sensors.
“The thing that we’re shifting towards a lot now is this overall idea of digital construction as opposed to just BIM or VDC,” said Rollo. “Because it encompasses so much more than things like drone capture and amazing scanning.”
“The naming convention, I don’t agree with, but the idea behind it, I think there are bits and pieces that are getting into the industry; maybe not at a Hollywood-level style, but definitely in terms of, ‘Hey, how do we get that in that process?’” said Chaudhry.
While it may be a little early to be rely ing on digital models to automatically track projects and forecast any costing or timing changes, the needle is moving, and many companies are starting to incorporate more advanced capabilities housed within some VDC software offerings, or at least exploring the ability to use such capabilities.
“The anticipation or the drive is there within the industry to want to leverage it for specific model-based quantity, takeoffs and everything like that,” said Rollo, although he warned that the ability to make effective use of the information is reliant on the quality of the data being measured
and collected. “The drive is there for it, but I think it’s still in its infancy as far as finding out the best way to most efficiently execute,” he said.
The path to making effective use of data from a jobsite, said Akehurst, is going to be reliant on data structure and data standards. “I think that that’s the founda tion that we need to be able to build out. Whether it’s connecting IoT sensors or tracking progress, or all of those kinds of things, we need that well-built data foun dation to be able to connect.”
“Ultimately this goes right back to the beginning of when you have a project. ‘I have a plot of land. I want to come up with different design scenarios, and different methods of schedule execution…’ but with technology as the focal point,” said Chaudhry. “The evolution of VDC is not about how do we do 3-D coordination; it’s more about the sophisticated technologies that are trying to look at automated data capture to inform decision making.”
While this may look daunting for companies that have yet to dive into the VDC ocean, the panel offered some guid ance to help contracting firms get started.
“My first piece of advice is start,” advised Akehurst. “The second piece would be… leveraging champions. One thing we’ve done at PCL, around when I started in this role, was we identified that we needed these technology champions in each of our districts. So, we created this role for that.”
“I think, the onus is on the GCs now to start to educate our clients about the different complementary construction technology around VDC and the evolution of how these artificial intelligence-based systems can start to come back and inform decisions,” said Chaudhry.
And while not all contractors have the ability to take on a full-time VDC or BIM expert of champion, Akehurst explained that finding someone within the company who could take on the task of exploring
how to best leverage technology and BIM in a way that aligns with the contractor’s structure can only help as more and more projects go digital.
He also advised to not get hung up on the odd misstep along the learning curve. “Every single time we start a new project, we’re adding to what we already what we did on the previous project,” he stated.
“We accept that it may not work on the first go-round. We’re going to learn on the next project or the next segment of work within that project.”
“If you’re not already engaged in leveraging these technologies and processes… I think one of the biggest things that I’d say coming from not only the GC end but from a previous life working for an implementation firm is, don’t anticipate doing everything at once,” said Rollo. “Take it in small chunks… Define your strategy and take it in steps. Understand that it’s going to be a journey, and it’s going to take some time to gain efficiencies on it.”
Remotely operated equipment is expected to ease the worker shortage while improving safety, job quality, and efficiency on construction sites. It will also be an important step towards autonomous operation.
First page web search results for remote-control construction equipment are mostly about toys. As we’ve seen with radio-controlled airplanes, racing cars, boats, and drones, operating a scaled-down dozer or excavator has immediate appeal for hobbyists, and sales appear to be brisk.
On real-life construction sites, however, remote control operation, also known as supervised autonomy, isn’t as easy as these simulations suggest. While there have been several recent examples of far-away loaders and excavators controlled from trade show booths, there are hurdles that make wide adoption several years away.
“Many of the prerequisites for this are already in place — the technology maturity and so on,” says Christian Spjutare, advanced engineering program manager at
Volvo Construction Equipment AB. “The main challenge related to adoption is scaling the technology to be competitive not only in special use cases, but in more general mainstream applications.”
Many hope the technology will help ease the perennial shortage of skilled workers and support the existing workforce by eliminating hazards, reducing physical stress and strain for operators, and making heavy equipment operation more appealing for younger workers.
“The three main reasons why compa nies are exploring supervised autonomy in construction are safety — keeping workers out of harm’s way, operator recruitment and retention, and the operational improve ments that lead to predictable results, reduced wear and tear, and volume gains,” says Kris Troppman, manager of smart
construction at Edmonton-based equip ment solution provider SMS Equipment.
Much of the technology is seeing wide use in mining, where work sites are static in comparison with construction, making them easier to automate. In construction, use cases for remote control on large machines like excavators, dozers and trucks tend to be industrial-type operations where the equipment remains static over an extended period. These include remote timber handling sites, concrete batch plants, aggregate production, or deconstruction of old mine sites.
A key barrier to broader deployment in construction is the cost and effort of setting up jobsite control networks.
“There’s a mesh network that’s required to be set up in order to utilize this technology, and that’s not easy to do,”
says Troppman. “When a contractor has a dynamic workflow where the equipment moves on every few days, that contractor is not likely to use supervised autonomy right now.”
Remote technology for heavy equipment can be deployed at several levels, each progressively more difficult to implement. A machine might be controlled from a handheld device a few feet away, from a control shack on the site, or from a control room many kilometres away.
“We distinguish between two types of remote control,” says Spjutare. “One is the traditional remote control, where you can see the machine and control it from a handheld device. We have solutions in that area, but what we’re working on mainly right now is tele-operations, where the operator is at a distant location.”
The advantages of tele-operations include all the safety benefits of on-site remote control, plus better utilization of both equipment and operators. By dividing the work between operators in different time zones, it’s easier to keep an operation going for extended hours. As well, contrac tors can avoid the perennial problem of having to move operators to where the work is and can deploy their best operators in situations where they are needed the most.
“Operating at a distance avoids the cost of transporting people,” says Alan Pumklin, a market professional at Caterpil lar, “and it also makes it easier to attract and retain the best talent, because they’re not having to leave their families.”
Another important aspect of remote control is that it is seen as a step, both by vendors and adopters, towards completely auton omous operation where no operator is required. A strong precedent already exists in mining.
“There’s a lot of autonomy in mining, particularly in ultra class haul trucks at various deployments around the world,” says Troppman. “The oil sands in Fort McMurray have a large number, and we’re starting to see that technology in construc
tion. That pathway will be built upon supervised autonomy where there will be an operator.”
“I think the real power of this tech nology comes into play when we start seeing this as an enabler for autonomous operation,” says Spjutare. “A system can do the bulk of the repetitive work auton omously, but you can get support from an operator when you need to move into some sort of complex motion. And then, over time, as the autonomous system gets more advanced, you can phase out the tele-operation and have a completely autonomous system.”
Remote control is not just about heavy equipment. Husqvarna Construction has introduced remote control in machines such as trench rollers, wall saws, floor grinders, and demolition robots. “Remote control is becoming more prevalent in a lot of our machines,” says Mark Michaels, senior director of product market manage ment at Husqvarna. “Some of our tools have gone to 100 per cent remote control, and we expect many of them to become completely autonomous.”
As with larger machines, the most popular advantage is protecting workers from unexpected hazards, repetitive stress, vibration, noise, and dust. “The most
applicable situations are situations where it’s desirable to get the operator further from the machine,” says Michaels.
As the industry has seen with recent inno vations such as GPS and mobile apps, the key to adoption will be absorbing changes to existing work processes.
“The most difficult challenge of this technology isn’t necessarily the technology itself; it’s the change management, where we take the technology and incorporate that into specific work processes,” says Pumklin.
One of the keys is helping workers develop confidence that the technology won’t make them less productive.
“We’ve found that the most experienced operators are the ones you need to convince first,” says Michaels. “They might be more resistant to the technology because they are so used to feeling their work. They can feel their productivity through the noise that the machine or the tool makes, or through the amount of vibration. It might even be sense of smell, for example, when they hit a reinforcement bar, or they’re not using enough water. So, they’re afraid that if they lose all that, they won’t be as productive. Especially when they’re on a learning curve and a little awkward with the controls.”
The adjustment, however, is generally successful. Workers find that feedback signals, such as sound, are different, but they get used to them. Additionally, being a few feet away from the equipment can provide a “big picture” view of the work.
“Our experience is that once operators get used to remote, they say they would not go back to manual operation,” says Michaels.
When operating large machines at a distance, the adjustment factors are differ ent, but the transition is similar.
“We get a lot of feedback from oper ators, and the first thing they say they miss is the sound of the machine,” says
Spjutare. “But when they’ve tried this for a number of days, generally sound is not a problem. What’s more important is sensing distance; how far they are from an object.”
“These operators go from a 3-D to a 2-D world, and that’s challenging,” says Pumklin. “There is a transition period. But overwhelmingly, operators around the world that have been using this have been successful.”
Another aspect operators miss is the feeling of motion. Volvo and other vendors use remote operator seats that provide motion feedback, much like the flight simulators used to train commercial pilots but, says Spjutare, operators often say
they no longer need that after an adjust ment period.
As in other areas of automation, rapid technology improvements are narrowing the gap between remote control and manual operation, improving operator comfort with the technology and expanding the range of tasks where the technology can be applied.
“When you’re operating a machine remotely, you lose a lot of sensory input,” says Spjutare, “so we need to work on introducing different diagnostics or systems where we can compensate for that.”
The consumerization of remote control, as we’ve seen with drones, is driving rapid improvements in the user experience.
“With gaming devices, we’ve seen that handheld controllers are getting a lot more sophisticated, and the same is happening in construction,” says Michaels. “As remote-control systems get more sophisticated, you can add more features to them. So, the ergonomics of the controllers are better, and the screens are more intuitive and user-friendly.”
Improving wireless communications to reduce latency and improve resolution is another top priority.
“At Caterpillar, we’ve done a lot of research and development on optimizing bandwidth,” says Pumklin, “so that we can pack video and sound machine control information into a single stream back to the operator who might be on site, or in a different country.”
The technology is expected to evolve rapidly over the next few years thanks to parallel developments in manufacturing, mining, and agriculture.
“It’s a growing segment for us, and it’s getting more and more popular,” says Michaels, “and we believe that as it gets more exposure, it’s going to create an even bigger demand.”
Jacob Stoller is principal of Stoller Strategies. Send comments to editor@ on-sitemag.com.
The technology sector, or as we often refer to it, “Silicon Valley,” loves to disrupt industries, and specifically legacy industries, so the construction sector has been a prime target, but we’ve yet to see the kinds of change that removed VCRs from our homes and companies like Blockbuster from our shopping malls.
So, what’s the hold-up? Disruption is kind of like a puzzle; solving it requires understanding all the pieces. In the case of construction, that means understanding the development, design and enough of the construction process to better plan and mitigate risks. If technology wants to disrupt our industry, it will need a complete picture, and an understanding of how all the pieces fit together.
Organizations throughout the industry are diving into data collection. Be it in the design, construction, or operational phases of a project, the fragmentation of our industry is making it difficult to
both collect data and see how it fits together. There are multiple reasons for this, including the confusion and risk surrounding what information you can and cannot share, whether it is confidential or proprietary, etc. In addition, developers, designers, and construction firms are not eager for their competitors to benefit from their data, so they often hold it close to their chests.
Unfortunately, this siloed approach in the industry has not yielded great results for technological innovation. We have seen attempts to implement foundational changes, such as the introduction of differ ent contract types (public-private partner ships, design-builds, integrated project deliveries, alliance, etc.) coupled with advancements in technology like BIM and reality capture (laser scanning, drones) to mobile devices (iPads, phones, apps) but we have not yet been able to see the entire industry unlock its full disruptive potential. Still, we are betting that that will change
soon, thanks in part to the advancements in computer vision as well as artificial intel ligence and its subset of machine learning.
Developers and government bodies are trending toward a data-forward approach, accelerating the progress towards better leveraging data for future use, however it is not as simple as having Silicon Valley enter with a new platform or solution, or even throwing venture capital money at a new approach to industrializing construc tion projects. The key here will be to have skin in the game; having the knowledge of design and construction so that it can be paired with technology to offer efficient solutions effectively.
So, it is not a technology problem we are facing in the industry; it is a paradigm shift towards embedding these new tech nologies into how we do business.
Construction sites have seen an influx of sensors — data collectors — all through the supply chain. These are installed in drones, cranes, trucks, software and handheld devices. Through the use of these sensors, projects have become data found ries. Our jobsites make mountains of data every day, but they can quickly become data sieves. Machine learning programs
PHOTO: © SOMKID / ADOBE STOCKare the only thing capable of crunching the numbers, but even artificial intelligence has to know what to look for. Feed an AI system 10,000 dots and it will find the shortest line between them in seconds, but construction has never been that simple.
Artificial intelligence and machine learning are missing context. Different sites have different circumstances, different clients and different contractors, and no two are the same. The reality is that differ ent builders build differently. If artificial intelligence is going to make sense of all that, even with the advances in machine learning, it will need some help.
It might be helpful to look at machine learning as it’s been deployed to optimize climate controls in facility management. Smart buildings can control all of their parts, so it is possible to harness machine learning to monitor and adjust the climate as needed throughout the day.
Machine learning and artificial intel ligence can learn the particulars of our
hypothetical building and its climate, and the optimized climate controls will reduce waste as well as save on operational costs, so it sounds like tech has saved the day. The problem is that the building’s life-cy cle maintenance cost schedule is now shot since most mechanical rooms are not built to be switched off and on 10 times a day. That’s the power of machine learning minus the operational context.
As another example, let’s examine the use of AI to help monitor the progress of a construction project.
We have a lot of technology available to use. We can create sophisticated 3-D models that serve as the base of our design. We can fly drones that capture hundreds of photos to create a digital replica of the project. And an AI system can compare the data gathered to our project schedule. All of this can provide an objective breakdown of current prog ress compared to the planned schedule, and it can be broken down even further
into scopes of work.
It sounds like another area where technology should be revolutionizing the industry, right? The only caveat is that the current industry and paradigm do not support a data-first approach to projects. Therefore, the vast majority of projects would not be able to use a robust 3-D model as a base.
Disruption will inevitably come to the construction industry; there is simply too much opportunity to ignore the sector. But, from all that we have seen, it will take a marriage of the latest technology with legacy expertise. In the quest to find the best path forward, Silicon Valley will need us as much as we need them.
Rory Smith and Hammad Chaudhry are both with EllisDon where Rory is the manager of DDE marketing and Hammad is national director of digital project delivery services.
If you’re running a construction site today, safety, productivity and sustain ability are probably three key priorities where technology is helping you stay ahead of the game, but new and emerging technologies, including remote-operation stations, hold much promise on the human resource front as well. These digital systems can help support diversity and inclusion ini tiatives in the construction industry which, in turn, can help offset labour shortages.
As remote technology advances for machinery operation, an emerging concept is the ability to move operators fully off-site. Remote-operator stations completely replicate the cab environment and provide multiple video feeds for a steady stream of data, as if the operator were operating the equipment right on-site Onboard electronic and visual systems even
allow several machines to be controlled remotely at once.
Still new to the construction sector, remote operation has proven itself in heavy equipment applications like mining, so the technology is now gaining ground for the construction industry as well.
The safety benefits from these stations are significant as operators are completely removed from hazardous areas. Productivity gains are also substantial as operators can control more than one piece of equipment at a time.
While safety and productivity are important benefits, the industry also has the opportunity to harness the technology to help with the additional priorities of diversity and inclusion.
Worker retirements, skills gaps and overall labour shortages are big challenges
ahead for the construction sector. Build Force says Canada’s construction industry needs 309,000 new workers by 2030.
Tapping into a wider talent pool of skilled workers will be an important component of remaining competitive, safe and productive, and this technology holds potential to attract workers who may have not have considered a job on an active construction site.
For people with disabilities, remote operation opens new opportunities. Oper ator stations remove the barriers found on a traditional jobsite, including having to maneuver through muddy, rocky or uneven terrain to sit in a machine. Climate-con trolled, safe and comfortable, the consoles increase longevity for all operators, reducing issues associated with machine vibration, dust and noise.
Remote operation also has the poten tial to support Indigenous communities with the technology holding potential to provide new employment opportunities as remote operating stations can be installed within communities to help remove barriers like the need to travel far or move away for work opportunities.
Although these modern devices may sound like the perfect solution to the construction industry’s problems, no tech nology can solve all problems immediately.
Making the shift to remote applications is a complex undertaking, particularly in isolated locations. The infrastructure needed for connectivity has been a barrier to wider adoption. And we’ve learned from early implementers that the biggest challenge isn’t the technology itself but the impact it has on people and process. A significant amount of time needs to be spent on change management.
Successfully implementation of remote technology holds significant potential to help the construction industry, however.
Matt Williams is the technology platform specialist for CAT Command at Finning Canada.
Advancements in remote technology are increasing safety while creating new opportunities for diversity.PHOTO: COURTESY OF CATERPILLAR
Since the end of 2020, when the construction industry began recovering from pandemic-related shutdowns, Canada’s construction sector has entered a period of rapid growth. Some analysts, including the firm Research and Markets, suggest this period will run at a compound annual growth rate of five per cent through at least 2026. A significant obstacle to meeting that demand, however, is that the Canadian construction indus try is in the midst of a growing workforce shortage as fewer workers are choosing careers in the construction industry.
This workforce shortage goes deeper than the short-term labour market issues that can be expected as an economy cycles between supply and demand peaks and troughs. A number of long-term trends have collided to create a workforce crisis that the industry cannot ignore.
A pressing concern, and one of the biggest causes of the crisis, is the aging of the construction industry’s current workforce. The rate of retirement is leading to the loss of experienced workers as they reach retirement age. Another is the overall aging of Canada’s population. A smaller number of workers are entering the general workforce each year. Another factor is a long-term demographic change stretching back more than a decade that has resulted in more students pursuing college degrees and not considering construction as a career.
That last demographic trend is particularly important because it reflects a perception problem. Modern construction no longer resembles the image that so many people have from the past, but it is a shadow that is hard to cast off. Today’s reality, however, is that construction is a
technology-driven industry that relies on highly educated personnel and very often high-tech tools. Unfortunately, this percep tion issue, along with these other workforce trends, means that the construction indus try is not attracting the talent it needs.
For the industry to solve this workforce challenge, we need to have a better strategy for attracting workers, especially those who might not otherwise think about careers in construction. That means making construction careers more attractive to a more diverse set of potential workers, including women and minorities.
In Canada, women are an enormous potential workforce for the construction industry. Females represent roughly 50 per cent of the population yet hold fewer than 15 per cent of the jobs in Canada’s construction
Expansion of view can help the industry meet its future growth needs.Nine of the female tradespeople who were working on one of Pitt Meadows Plumbing & Mechanical Systems’ projects in B.C. last year. PHOTO: RYAN BRODA
industry, and likely less than three per cent of the skilled trades on a site. The limited number of women with careers in the industry often fill office roles, but that does not reflect the much larger role that they could play.
Another highly under-represented demographic in construction is the Indigenous Peoples in Canada. This group represents only one in 10 jobs in the industry today but represent a massive untapped talent pool to draw upon to meet the Canadian construction industry’s future staffing needs.
While some tasks are still physically demanding, many aspects of construction have evolved dramatically, with new tools and processes helping to move the indus try from the need for brute strength and toughness to put a greater focus on skill and adaptability.
Modular construction is a prime example of how the industry is chang ing. Modularity and a more industrial ized approach to construction paves the way for abbreviated on-site production and creates the safety, quality, cost savings and predictability that make construction jobs more desirable to a broader swath of talent.
Modular design hinges on off-site manufacturing as building components are built in a more controlled and safer environment, which is accessible to more people. In addition to enhanced safety at the jobsite, in the controlled, off-site manufacturing environment, employees enjoy regular hours, predictable commutes, better training and consistent supervision. There are also fewer unknowns compared to the working conditions on a construction site.
It’s a tremendous step forward to have so many aspects of the construction process be possible in off-site settings that are more controlled than construction sites of the past, but the unavoidable truth is that some construction work will always need to take place on a worksite. So, the next step to making construction work more welcom-
ing and appealing to all potential workers is addressing the work environment that exists on those construction sites.
Physical safety is paramount to making sites more welcoming to diverse groups, but it is equally essential to create a verbally and emotionally safe space as well.
In a 2021 survey by WomanACT and The Society for Canadian Women in Science & Technology (SCWIST), it was reported that four in 10 Canadians expe rienced some form of harassment in the workplace. The rate was significantly higher for women (50 per cent) than men (33 per cent) and is quite simply unacceptable. A concerted effort needs to be made to call out bad actors and behaviours.
Empowerment and engagement of team leads (foremen and superintendents) to collaborate and call out opportunities for improvement, and to maintain a productive, protected and healthy work environment, is key to creating a non-hostile work environment — the kind of place people want to show up to daily. The goal is to create a place where workers feel respected and valued.
Beyond the elimination of bad behaviour, proactive companies are investing in a shift toward good behaviours. Leaders, make eye contact, take input from teams, and don’t talk over people. Create a jobsite where people feel valued and safe. This can be encouraged by:
• Making it a condition of employment that people call out bad or hostile behaviour when they see it.
• Making sure jobsite signage and safety posters reflect diversity
• Amplifying the voice of women and other underrepresented people in meetings.
• Incentivizing subcontractors and supply chains to diversify workforces.
• Providing a suggestion box so people can anonymously provide recommen dations or elevate issues.
• Making sure there’s a women’s locker room and lavatory.
• Providing PPE for women.
Not only can technology help us advance
projects with safety and efficiency, but it can also help crews and managers work smarter while putting a spotlight on the changes in the kinds of tools used by the trades — including those that will appeal to young potential workers.
We can thank the pandemic for expediting the use of drones for surveying and augmented reality for jobsite inspections. These new tools are enabling project owners and managers to stay abreast of what’s happening without having to be physically on a site. Getting the needed insights to familiarize crews with the site and enable fast decision making to keep projects on track is another huge benefit. Not to mention, an “advance crew” of flying robots keeps workers safe and out of potentially hazardous situations.
In the end, it’s imperative to appeal to future workers in terms that speak to their motivations. Construction is often misunderstood as gritty, labourious and monotonous. As an industry, we must demonstrate that a career in construction comes with opportunity, purpose and security. This vibrant field ensures that its participants are never bored. Each new build brings the opportunity to learn about an entirely new business. It is truly the ideal industry for individuals who are passionate about being continuous learners.
It only takes a few leaders to champion change. It is possible to create a jobsite culture that’s inviting to a more diverse mix of potential new workers. And it is possible to change the perception of the industry so that workers view jobsites as safe places for people of all stripes to work hard, feel valued and build meaningful careers, in a sector that is technology-driven and ever-evolving. Greater diversity and inclusion hold a lot of potential to strengthen Canada’s construction industry and build for the future.
Nancy Novak is the chief innovation officer at Compass Datacenters. With more than 30 years of experience in the construction industry, she brings extensive expertise in cutting edge technology, lean practices and innovative culture through diversity for the construction industry.
In addition to highlighting power, performance and durability, makers of vocational trucks are increasingly emphasizing driver comfort, safety, and vehicle technology — the kind of attributes usually associated with automo biles, not dump trucks, crane trucks, con crete mixers, and other off-highway work vehicles. So, the question seems to ask itself, “Are vocational truck manufacturers are taking design cues from the consumer car sector?”
Looking at Volvo’s website for its voca tional truck lineup, it’s not hard to find such comments as, “For decades, conven tional wisdom said vocational truck drivers and owners only cared about dependabil ity. Considerations like safety, efficiency, comfort, and body design couldn’t be part of the decision when choosing a dump truck or mixer.” Of course, the webpage then outlines how Volvo’s most recent iterations of its VHD trucks meet these overlooked considerations.
Promotional material for other vocational trucks reveals similar content, with references to ergonomics, low-noise cabs, comfy seats, smooth suspension, remote
PHOTO: COURTESY OFdiagnostics, collision avoidance systems and user-friendly instrument panels.
Industry pundits dispute the idea that vocational truck makers are imitating consumer car designs, however. They say the focus on comfort, safety and technology is simply a reflection of driver demand and industry trends.
“Sometimes it may appear as though the commercial truck industry is following the automotive industry, but International
is committed to delivering industry-specific features that increase productivity, safety and comfort for our customers,” states Andy Hanson, director of vocational marketing at Navistar, parent company of International Truck.
Duane Tegels, powertrain product marketing manager at Volvo Trucks, offers a similar perspective.
“I’m not sure if we’re necessarily following the lead of the automotive indus-
try. [Driver comfort, safety and technology] are kind of what or customers are requesting,” he states.
Clients are requesting such features and manufacturers are incorporating them on vocational trucks for a simple reason: “Driver comfort and productivity are integral to a safe and successful operation,” states Hanson.
Regardless of the inspiration behind such features, here’s a look at some voca-
Released in November 2020, the HX520 and HX620 from International are wellsuited for dump and heavy haul applications on construction sites. The new HX Series is intended to augment International’s HV Series of vocational trucks.
HX and HV trucks are all built with a
view towards maximum comfort. Controls and gauges are close and convenient and “are also designed in a way which makes them easy to read and operate, allowing the driver to focus on the jobsite or road,” says Hanson.
Both series boast a comprehensive HVAC system and a low-noise cab, which helps “keep the driver comfortable, and comfortable drivers are more attentive and safer drivers,” he adds.
Additional comfort and safety features in both HX and HV trucks include a 2,385-square-inch windshield for heightened visibility, and front and rear Bendix air brakes. Fitted with a Cummins X15 engine, HX520 and HX620 models are capable of reaching 605 hp and 2,050 lb-ft of torque.
Both the HV and HX Series feature a customizable Diamond Logic electrical system. This system enables International dealers and technicians to “write custom logic within minutes to reprogram anything … all this programming is stored on International’s servers, making the programs recoverable and repeat able,” says Hanson.
OnCommand Connection, a remote diagnostics solution, is standard on the HX Series and some HV Series trucks. Next year, OnCommand Connection will be a standard offering on all Interna tional trucks. For added levels of safety, HX and HV vocational trucks will also feature a backup camera starting in 2023.
Introduced in early 2020, the website for Mack Truck’s MD vocational line says the vehicles were “engineered to put a premium on driver comfort and control.”
To this end, MD6 and MD7 trucks both boast an air suspension driver seat, a tilt/telescopic steer-
ing column, smooth suspension, intuitive dashboard design, standard air conditioning, power steering, cruise control and a flat-bottom steering wheel. Both trucks can offer 300 hp and 660 lb-ft of torque and are fitted with the Bendix Antilock Braking System and Geotab for telematics.
Mack’s longstanding Granite voca tional line has equally impressive features, including premium seating, a user-friendly instrument panel designed to reduce driver fatigue and increase productivity, and an industry-first flat bottom steering wheel
that the company says provides more space for the driver to enter and exit the cab.
Granite trucks, which can be used as mixers, multi-axle dump trucks and equipment/material haulers, also come with Command Steer, a steering-assist feature that reduces driver strain and enhances comfort and safety while improving maneuverability and maintaining directional stability.
series from Freightliner, a division of Daimler Truck North America, consists of improved versions of medium-duty and vocational models.
The series, which the company says was “built for next-level safety, simplified uplift and operator comfort,” includes the 114SD Plus and 108SD Plus vocational trucks.
Well-suited for construction, utility, and oil and gas duties, the 114SD Plus offers 525 maximum horsepower and 1,850 lb-ft of torque, while the 108SD Plus can achieve 380 horsepower and up to 1,250 lb-ft of torque. Both trucks include a multitude of “operator comfort features” as DTNA puts it, ranging from noise-reducing cab insulation to increased storage space, ergonomically designed seats, a redesigned dash with highly visible controls, and easily reachable electric door and window locks.
Safety features on the 114SD Plus include a 2,500-square-inch windshield for enhanced visibility, and wider door open ings for hassle-free entrances and exits. The 108SD Plus offers wide door openings, and a low step-in height. Both trucks come with an optional Bendix Intellipark Electronic Parking Brake System that is designed to prevent the truck from rolling away.
Additional high-tech features on the 114SD Plus and 108SD Plus include the company’s Detroit Assurance suite of safety features that includes lane depar ture warning, adaptive cruise control, side guard assist and active brake assist, as well as Detroit Connect. The latter is a suite of connectivity solutions such as Virtual Tech
nician for remote diagnostics and Detroit Connect Portal for fleet managers.
Volvo literature describes the company’s VHD as “the most comfortable vocational truck on the market.” The series consists of the VHD 300F axle forward, VHD 300B axle back, VHD 400F axle forward and VHD 400B axle back trucks. VHD trucks can be used for dump, crane and concrete mixing purposes, and offer 1,900 lb-ft maximum torque. Interiors were designed with ergonomics and comfort in mind.
“We had a lot of clinics before designing the trucks,” says Ashley Murickan, product marketing manager for safety and connected services at Volvo Trucks. “We interviewed drivers, asked where they wanted switches positioned, where they wanted steering wheel controls positioned.
We took all that feedback and designed [the VHD line]. If you notice, all the steering controls are at your fingertips and other switches, you don’t have to stretch for them.”
Other comfy offerings include seats with heating, cooling and massage options, a refrigeration box beneath the passenger seat for storing snacks and beverages, an insulated cab for reduced noise and vibrations, and LED headlamps for improved visibility.
On the high-tech front, Volvo Dynamic Steering (VDS) enhances driver productivity, safety, and comfort, says Murickan.
This assisted steering function means “you don’t have to strain your shoulders and arms [to steer]. You can pretty much steer it with one finger, although that’s not recommended,” he explains.
The VHD series also features Remote Diagnostics and Remote Programming for wireless software updates; Volvo Active Driver Assist (VADA), a collision mitigation system that emits audio and visual warnings; and Volvo Enhanced Stability Technology (VEST) to prevent rollovers and loss of control. A Position Perfect steering wheel system lets drivers to set the wheel to whatever height and angle they prefer.
Volvo was also the first manufacturer to install driver-side airbags on vocational trucks, a feature that continues in its VHD trucks. Also to be found in the cab is an optional infotainment system with seveninch colour touchscreen, GPS and audio system, bringing yet more car feel to the vocational segment.
And a world of experience to build that road. As the global leader in road construction and minerals processing technology, we‘ve seen just about everything there is to see. In every climate, every condition, every twist, turn and terrain. And we put that world of experience in your hands, so you can use Smart technologies to perform better and provide results that drive efficiency in every phase of the road construction cycle.
wirtgen-group.com
Within the fleet industry, the construction sector has been one of the slowest to adopt new technologies and digital business solutions. A lot of that has to do with the difficulty around finding a cost-ef fective and scalable solution that’s easy to implement and use.
A scalable solution doesn’t just need to grow and adapt with your business, it needs to be able to integrate with your business solutions to provide a more comprehensive — yet easier — way to manage your fleet and business operations. Choosing a Fleet Management Software (FMS) package that aligns with your systems is just as critical as ensuring that you have the right equipment in your fleet and on your jobsites.
According to the 2020 FMI report, Where Construction Firms Are Finding Value, the leading software being used in construc tion includes project financials, project management, safety/risk management,
equipment management, and field/labour management. While 51.4 per cent of firms are using construction software to maintain safety, fewer than half the firms surveyed were using software to tackle two other leading industry concerns: skilled labour retention and maximizing field productivity.
Communication and data transpar ency are huge when it comes to keeping employees engaged and reducing turnover. Communication bottlenecks are not only frustrating for employees; they also slow down productivity.
A cloud-based FMS with a mobile app, integration features, and an open Applica tion Programming Interface (API) facilitates real-time communication while consolidat ing data onto a single platform for more impactful insights.
Data transparency makes it quick and easy to find out who’s assigned to a vehicle or piece of equipment, who performed service on an asset, the current status of an asset (active, inactive, in the shop, etc.) and helps promote accountability at every level. Additionally, FMS takes on the role of
equipment management and aids in safety, risk and field management.
Alberta-based Barmac Contracting, a company with roughly 60 pieces of equip ment and 35 employees, recently adopted a new FMS, and the company did not take the decision lightly.
Management there had previously implemented payroll software that they discovered came with a major financial catch. When they needed it to scale up, the company found out that it was going to cost upwards of $30,000 to do so, and that was on top of a monthly fee. Consid ering the difficulties the company had when implementing the payroll software, it should not be surprising that it took a cautious path when looking for a digital fleet management solution.
“I almost lost a bookkeeper. She was getting so stressed trying to work through it,” explains Norma Block, the company’s CEO, about the payroll system implemen tation. “Anyway, got it done and that was fine, and it worked for a while. But then once we started needing [something more], it was $10,000 here, $20,000 there, plus there was a monthly fee. We started realiz ing this was going to bankrupt us.”
Construction businesses are all too familiar with this scenario. It’s hard not to be hesitant when it comes to adopting a new technology when faced with the potential for implementation failure, loss of
Fleet management software is helping construction fleets maintain safety, improve employee engagement and retention, and maximize productivity.PHOTOS: COURTESY OF FLEETIO
money, and a huge waste of time trying to figure out a new system. Luckily, with the right understanding of what your business, and specifically what your fleet, needs to reduce expenses and maximize productiv ity, it’s easier to determine what software might be right for you.
For Barmac, the initial thought was to build a solution that fit their fleet and busi ness, but a proprietary or bespoke system is not without risks either, so they were open to an existing product, but it had to match to their needs. They also knew the system had to be intuitive and easy to use, otherwise it would not get the necessary buy-in from its staff. Their research-based cautious approach has paid off so far.
“Everybody has loved it,” says Block. “I haven’t had one complaint from any of our workers about the ease of use and just the way that the information is presented. They’ve all really bought into the program.”
A key takeaway from the process for Barmac was that when researching a new business solution or technology, it is crit ical to determine your needs as precisely as possible, and to get buy-in from end users. Advice from peers and other industry professionals is also beneficial as is, ulti mately, the software’s ability to scale with your business.
assets, and increasing asset ROI, there’s just a lot to manage.
A cloud-based FMS doesn’t just help with these issues, it improves productivity through real-time communication, auto mated workflows, and data transparency. Properly implemented FMS should make a fleet manager’s job easier as it helps them address safety, accounting, maintenance and data tracking.
“We use [our FMS] for daily inspec tions because that’s a must… We have to be able to supply the operators with information on the units that they operate,” says Block about the integration of safety inspection forms into the system. “Our safety coordinator loves them.”
And the benefit of the use of digital forms doesn’t stop with the safety check lists, she explains.
“We have the drivers do a daily check in,” she says, adding that Barmac’s accounts department then uses the forms. “Before we would wait until the drivers dropped those forms off, they would leave it in a dropbox by the shop and within two to three days, somebody would go pick them up. Now we get that information instantly, daily, from the drivers.”
That allows the company to more easily track hours worked, and who worked.
“In this world, a lot of things happen between 11 at night and 3 in the morn ing. Weather changes everything; people get sick. I have to know who’s onsite. I love that I can just go in and watch who’s doing their inspections, so I can confirm that way who worked and who didn’t work,” she says.
And with the ability to digitally pull up service histories, the FMS makes life easier for other departments as well.
with the mechanics over ‘When is this going to be fixed?’” adds Block.
For Barmac, a major issue that needed to be resolved was how the company went about maintenance. It got to the point where work orders weren’t being filled out and trying to be proactive seemed a thing of fiction.
“We really set out on a path to get to that point where we change from a business that just fixes things… to being a company that actually starts being proac tive and predicting and preventing things,” she explains. “I can’t even predict the amount of years that it has put us ahead of the game to getting to that final goal. Are we at that final goal now? Not quite yet, but I see where we can get there.”
While construction is trending toward the adoption of more technology, it’s clear that old habits die hard and there’s still a stigma about software and solutions that are hard to ignore, which was illustrated when Barmac leased some of its equip ment to another company.
“I was trying to track our hours and I was trying to convince them to allow me to set up the app and invite their operators using our equipment as guests, but they pushed back hard,” says Block, explaining that the company didn’t want to confuse its operators with new technology. “Next time that’s just going to be a must — that they have to get the app. We [will] bring them on as guests so I can watch the equipment.”
Fleet is a large expense for construction companies. Between asset procurement and management, adhering to safety and other regulatory concerns on the road and on the jobsite, reducing liability in the case of accidents, improving the lifecycle of
“The mechanics love the fact that if they want to know, ‘Hey, when was the last time we did anything on this engine?’ it’s information at their fingertips,” says Block. “They don’t have to rely on somebody else to weed through huge, horrible spread sheets or papers.”
It also lets operators know whether items they notice have already been reported.
“They can have real-time conversations
Block and her team are already looking toward the future with the company’s chosen FMS. With the goal of bringing their parts inventory in line within the software using its barcode feature, plus adding in a GPS integration, Block hopes even more fleet elements will fall under easy management.
With a history in automotive journalism, Rachael Plant is a content marketing specialist with Fleetio, a developer of fleet management software that helps organi zations track, analyze and improve their fleet operations.
According to a recent federal task force report, flooding — particularly in urban areas — accounts for the largest portion of disaster recovery costs annually in Canada. Hence, the urgently growing awareness among government and private sector players in the building sector to reduce flood risk as a key to developing and supporting resilient and prosperous communities across the country.
The major challenge is that flood mitigation planning and modelling, which is used to better understand the impact, relative risk, and potential for flood risk reduction, is complex and we lack data on many vulnerabilities.
No question, major floods can have a wide-ranging impact, including direct property damage, indirect supply chain issues, diverted resources, and intangible mental health strains and contamination releases. And while life safety and well-being are rightfully the top priority for municipal engineers, planners and officials charged with devising solutions to the flooding problem, the financial cost of flood damage to Canadians is a major and growing impediment to our prosperity.
Nearly 70 years ago, American geographer Gilbert White, known as the father of flood plain management, wrote, “Floods are ‘acts of God,’ but flood losses are largely acts of man.”
A pioneer in adopting an approach to flood mitigation that considered the influence of human behaviour, White cautioned against being overly confident on structural mitigation solutions and insufficient building design standards to reduce the damaging impact of floods. His concern then, which has proven to be extraordinarily prescient, was that people would let down their guard and assume that all would be well even after an unanticipated flood did occur.
In the years since, we have continued to rely on prevention strategies and, in many cases, increased our exposure to potential flood hazards. However, the costs of flooding and climate change are making it clear that an adaptive approach is necessary to increase our resilience and recovery from flooding.
In other words, because natural floods can’t be prevented, addressing urban flood exposure through such mechanisms as land use regulations, for example, or by addressing vulnerabilities by way of everything from building standards to permitted uses, cultural awareness and disaster preparedness, is more in keeping with an adaptive approach to urban flood damage prevention.
Of course, structural approaches are easier to assess through standard cost-benefit analyses. Non-structural options, on the other hand, occur over time and in complex ways, making it much harder to account for the costs and benefits of such alternatives in a dynamic social and built environment,
Fortunately, our ability to assess non-structural alternatives with risk modelling has improved and we can model alternative exposure and vulnerability options to assess these benefits.
Risk is a broadly used term but has a
Incorporating long-term adaptation and resilien cy strategies along with structural mediation into flood risk models.PHOTO: GEORGECLERK / ISTOCK /GETTY IMAGES
The construction business is a tough business. That’s why Kubota builds construction equipment to work through tough jobs and tough demands. Our quality compact track loaders, wheel loaders, excavators and attachments get the work done and then some.
specific meaning in the context of urban flood mitigation. Consider a typical building within the floodplain of a nearby river. Water that floods a metre deep on the main floor would cause significant property damages — one of the many consequences of that single flood event. In the meantime, a different flood event at that same location may only lead to some minor basement flooding, with less damage and ensuing repair cost.
While the likelihood of a flood occurring and the consequences that follow are hugely variable, viewed together, a measurable risk value begins to emerge.
Risk includes the probability of a consequence being experienced. Conse quences for an asset, such as a building, can further be understood as the product of the exposure to a flood hazard and the vulnerability of that asset to the hazard in question.
For example, a home with an empty undeveloped basement has different vulnerability than if the basement was developed with bedrooms, a home theatre, art collections, storage of family documents and keepsakes, etc. Vulnerability is not only value, however, and the fully developed basement could have less vulnerability if it was thoroughly floodproofed to prevent the entry of any water.
Therefore, risk can be illustrated as the cumulative interaction of hazard, exposure, and vulnerability, as in Figure 1:
Figure 1: Illustration of risk as an interaction of hazard, exposure, and vulnerability.
This simplified illustration of risk is useful to illustrate that all three elements are needed to complete a proper risk assessment.
Flooding alone is not a risk. In fact, many landscapes have evolved to be dependent on regular flooding. Likewise, without exposure or vulnerability, there is no risk. Adding probability to the hazard allows us to quantify the risk, which can help us understand if minor basement flooding every year or the potential for a rare but severe flood is of most concern for the metrics measured.
If we are only measuring repair costs, we may find that small but frequent flooding represents greater financial risk than a devastating but rare event. However, if we are only concerned about life safety risk, we may find the opposite.
Risk as a product of hazard, exposure, and vulnerability is also useful for understanding the inputs for risk modelling. Estimating flood exposure, consequences, and risk requires spatial analysis to determine exposure and object-based estimates involving a significant number of calculations. The development of software tools has made risk modelling more accessible and efficient.
To this end, IBI Group’s flood risk and mitigation planning team has worked closely with Natural Resources Canada (NRCan) to develop Canada’s first flood
An open-source QGIS plugin, CanFlood was first released in the spring of 2021 and the development of new features continues. The plugin is available directly within the QGIS repository or as a download on GitHub. Documentation and tutorials are also available on the
With CanFlood, we now have a standardized toolset for flood risk assessments. However, the greatest model is only as good as
the data it is fed. Even the most tangible of flood impacts — building damages — requires new data on the vulnerability of the structure to flooding.
To achieve this, NRCan is working with IBI Group to provide a Canadian framework and vulnerability function library for flood risk assessments and is engaging directly with a range of industries, including design, construction, and restoration specialists to provide data input.
If you have experienced flood losses or have identified any vulnerabilities or adaptations in your work and would like to contribute data to the project, I encourage you to get in touch with us at http://ibiengage.com/floodrisk/. We will be collecting data at least until the end of this year.
Risk assessments may be used to provide an indication of the protection, or benefits, provided by flood control structures. However, mitigation plan ning should consider the lifecycle of the structure and the community, includ ing the additional hazard of structures failing, future increases in exposure from continued development, and the resulting consequences.
Rather than simply assessing how to protect what we have built today from a dynamic and uncertain future hazard, we should also consider how dynamic our communities are and how we can adapt to the hazard and increase our resilience.
To do so, we need to adopt a longerterm outlook and we all need to work together and incorporate risk through the policy, planning, design, and construction phases of our communities’ redevelop ment processes.
The tools are there to make it happen. With engagement, you can help us better our understanding of flood vulnerabilities and the impacts on your work.
David Sol is an associate and manager of planning at IBI Group Inc. where he leads a multidisciplinary team to complete flood risk assessments and mitigation planning all across Canada.
Navigating a growing threat to the construction industry.
There is absolutely no doubt that the digitally aware, and sometimes predictive, jobsite is allowing contractors to make better decisions faster, but when the jobsite is shipping data to the cloud and throughout the corporate structures of all construction stakeholders, the chance of cyber-at tack cannot help but rise. As the construction sector continues to connect and integrate the component parts of the built envi ronment digital twin, it is also increasing its exposure to digital vulnerabilities, or cyber threats.
These unwanted intrusions can take many forms. Some of the more common attacks in the construction sector include malware attacks, phishing, password attacks, man-in-the-middle, distributed denial-of-service, and exploitation of IoT component vulnerabilities.
A malware attack happens when someone implants malicious software viruses into the target company’s IT systems. Ransomware is, by far, one of the most common malware attacks facing the construction sector today.
Attempts to discover and use a victim’s password have existed almost as long as passwords have been around, but the technology and techniques used to crack the victim’s passwords have evolved. Once a password is cracked, the hacker gains access to formerly secure systems and data. Phishing attacks are a social engineering variant whereby the attacker impersonates somebody the victim trusts to gain access to funds or the victim’s technology systems. In a “man in the middle” attack, the attacker comes between two parties communicating in an attempt to steal and manipulate data.
Sometimes an attack is looking to disrupt a company’s opera tions, rather than gain access to data. Distributed denial-of-service attacks involve an attacker overwhelming the victim’s servers or networks with traffic to cause a computer system to crash.
With more and more devices having access to connected critical systems, Internet of Things (IoT) attacks are becoming more of a threat. An attacker who cracks a weakness in the security of a connected device may be able to take control of parts of the built environment, either during construction or in operations.
As more data emerges about cyber-attacks, we are learning that the construction sector is much more vulnerable to cyber-at tack than other industries. In 2021, cloud content security and governance platform Egnyte published a report called The State of Ransomware Report for Architecture, Engineering and Construc tion. Among the highlights from that report were that AEC compa nies were more than twice as likely to a fall victim to a ransomware attack.
The report’s researchers found that a vast majority of reported attacks happen in North America, large companies are most at risk, and companies that have been victims of a ransomware attack once are likely to get hit again.
Based on the growth of digital solutions within the construction sector and the apparent increased risk to the construction sector specifically, it appears that construction stakeholders need to up their game when it comes to cyber security best practices.
To help your firm better navigate the growing threat of cyber-attack:
• Appoint a Cyber Security Leader: Have somebody within your organization take on full or part time responsibility for tracking and managing cyber security.
• Retain Cyber Security and Legal Experts: Don’t wait for a threat to occur. Get experts into your organization and have them identify the threats most likely to occur, given your organiza tion’s operations, people and technology systems.
• Know Your Data: Know the “what and where” when it comes to your data. What data do you have within your organization, and which is most vulnerable? Where is that data located, and how could it be put a risk?
• Train Employees: Cyber attacks are often facilitated by employ ees. It is imperative that your organization trains employees to recognize, avoid and mitigate cyber threats. A key part of training is performing tests and “fire drills” with employees to see if the training is working, and if the response to an event is optimal.
• Know Technology: Stay current on the technologies being used within your organization, and at your jobsites, in particular. Ensure you are assessing those technologies for vulnerabilities they may be creating.
• Protect Money Movement: Ensure that all transfers of funds are highly secure. Many cyber threats target these funds. Weak fund-transfer protocols and practices increase vulnerabilities.
• Use Virtual Private Networks: Use more than encryption and get everyone working on a VPN.
• Use Risk Finance (Insurance): Though the market for cyber insurance is growing tighter with each passing year, invest time with your risk advisor/broker to find the ideal way to risk finance this growing risk.
There are many benefits to harnessing the power of digital in the construction space, so long as we don’t let the threats slow this very positive transformation. If you pay attention to the risks, you can ensure your organization reaps maximum benefit, and reduced risk, on your path to a fruitful digital future.
David Bowcott is the Managing Director, Construction, at NFP Corp. Please send comments to editor@on-sitemag.com.
Adrian Steel www.adriansteel.com 10
Atlas Copco www.atlascopco.com 13
B2W Software www.b2wsoftware.com/Tom 37
Canadian Concrete Expo www.CanadianConcreteExpo.com 41
Canadian Construction Association www.ApprenticeSearch.com/CAS 47
Canadian Institute of Quantity Surveyors www.count-on-us.org 25
CONEXPO www.conexpoconagg.com 9, 55
Construction Jobsite www.constructionjobsite.ca 35
GCPay www.gcpay.com 29
Hitachi Construction www.hitachicm.us 56
Kubota www.kubota.ca 49
Navistar www.navistar.com 4
Northbridge Financial www.northbridgeinsurance.ca 14-17
OpenCircle www.opencircle.ca/pizza-party 33
Raken www.rakenapp.com 2
SoftwareOne www.softwareone.com/construction 20
Superior Glove www.superiorglove.com/construction 31
Takeuchi www.takeuchi-us.com 7
The Buildings Show www.thebuildingsshow.com 45
Uline www.uline.ca ......................................................11
Wirtgen www.wirtgen-group.com 43
The increasing demand for laser scanning in construction is largely due to its extremely accurate digital record of an object or space as it pertains to a construction site. The advanced scanners use laser light to create 3-D repre sentations known as “point clouds.” These point clouds create a database of connecting points in a 3-D-coordinate-system to create a map of the precise shape and size of physical objects. The scans, and the resulting images they create, could have useful applications in construction disputes.
Laser scanning technology can be used in various areas of a construction project. In respect to site design, laser scanning is often used contemporaneously with other design processes to validate proper design execution or aid in the overall design process. For example, implementing a 3-D laser scan of an in-progress construction site allows contractors to create a model of existing conditions, which they can use for accurate quality assurance in comparison to as-de signed drawings.
Another example is a scan-toBIM method to capture detailed information that will be used in a holistic design process to manage digital representations of physical and functional characteristics of the site.
Laser scanning should be used throughout the life of a construction project, not just during design processes. It is extremely helpful during coordination of different systems (i.e. electrical, plumbing) to avoid conflicts. Laser scanning also helps to document timelines and milestones, as it has the ability to measure and evaluate progress using a precise record of every phase of construction.
The data created by laser scanning is also useful for building operations, retrofits and renovations as it creates a permanent as-built record to be used by owners, facility managers and other key personnel. At times, it is required to create a virtual model of a site on a quick turnaround to communicate to its various stakeholders. This makes 3-D laser scanners an attractive tool since they have the ability to make the process of creating building models quick, with high accuracy compared to other processes.
Laser scanning and the accompanying point-cloud software have numerous legal applications. As mentioned, through consis tent creation of laser scans during the course of a project, there will be a clear record of all progress made on the project. This will provide the contractor (or owner, as the case may be) arguing for changes to the contract valuable evidence in support.
Any disputes arising from what may or may not have been done from one scan to the next can be quickly quashed by clear and identifiable evidence of the milestones met or missed using the data collected by laser scanning. As such, laser scanning can help to mitigate against costly litigation arising out of these types of disputes during the course of the contract.
If litigation does occur, parties can use the evidence gathered using laser scanning and point-cloud software in a number of ways. Firstly, it provides counsel with a clear visualization of the scope of the project and its steps.
Many projects are so large that it can be difficult for counsel on either side to assess the scope of the project, the areas worked on by their clients, and the milestones outlined in the contract. By providing counsel with VR-assisted scanning of the project, they will have a clearer picture of the entire project and can narrow the issues at hand.
FACT: Three-dimensional laser scanning is not new technology. It dates back as early as the 1960s, but its demand in construction is rapidly growing. It is expected to grow to a $10 billion industry by 2024.
Secondly, point clouds can be invalu able as factual bases for providing opin ions on all manner of issues in litigation. Schedule experts can use this data to assess whether the contractual mile stones were met or missed. Engineering experts are able to use point clouds to determine whether the construction of structural, electrical, HVAC, or other engineered elements were completed or coordinated according to the speci fications of the contract. Other liability experts can rely on the data to determine who might be at fault for certain errors in the construction of the project.
Contractors and owners should consider the additional costs of having consistent scans taken in light of the overall size and cost of the project and the likelihood of disputes arising. For larger public projects where schedules and budgets are already fairly tight, including a provision for the usage of laser scanning and point clouds on a regular basis may very well save more money than the scans will cost.
Callan MacKinlay and Grace Jiyeon Shory are construction lawyers at Borden Ladner Gervais LLP. This article provides an overview and is not intended to be exhaustive of the subject matter contained therein. Although care has been taken to ensure accuracy, this article should not be relied upon as legal advice.
An invaluable asset in resolving construction disputes.
A thousand factors impact your bottom line every day. Some in your control, some well beyond it. But you’re not slowing down, not anytime soon. Neither are we.
Our job is to keep you moving forward. Our machines are engineered with a “get it done” mentality and our After Sales Solutions are designed to keep you up and running.
Your reputation is always on the line. And we’re always working to protect it.