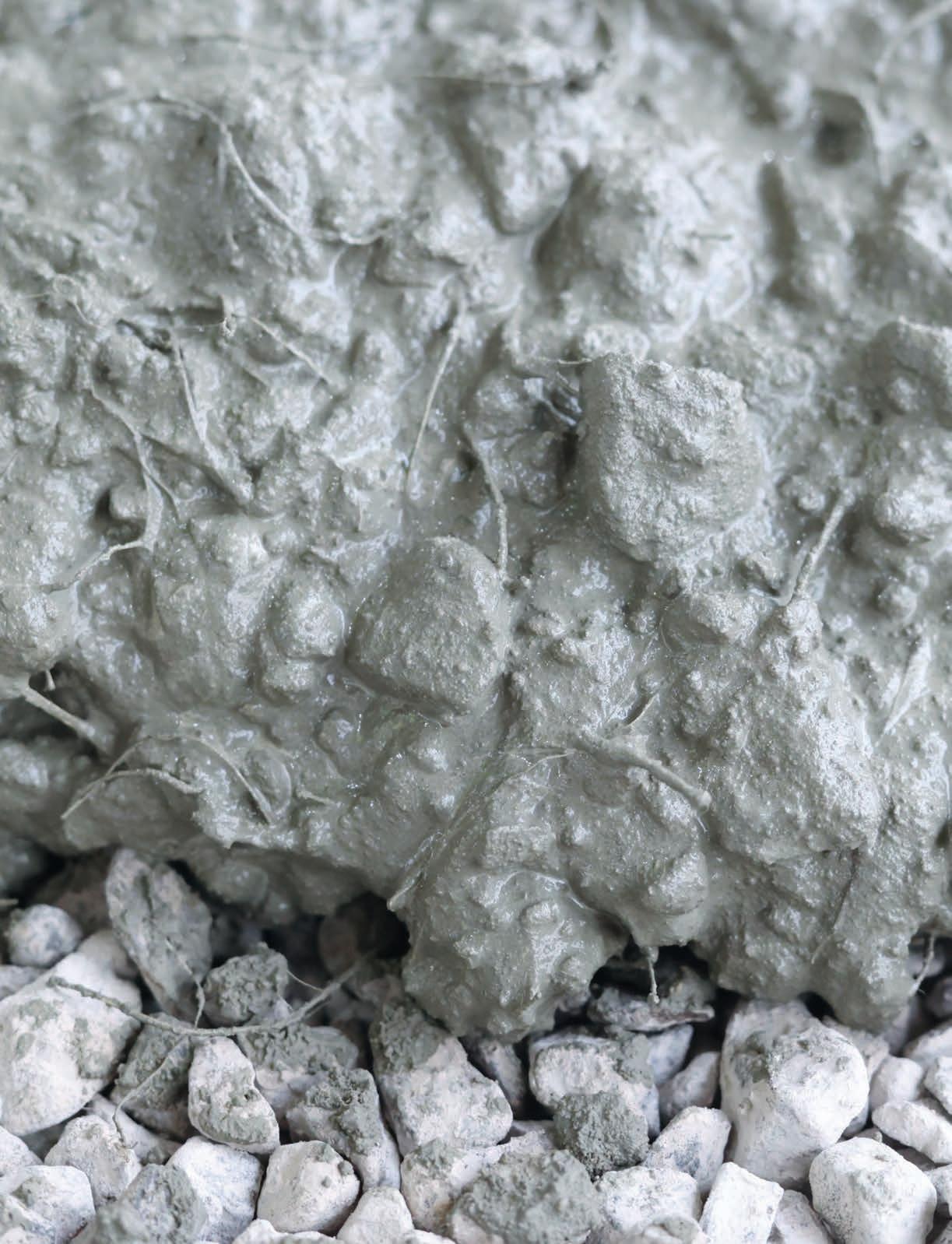
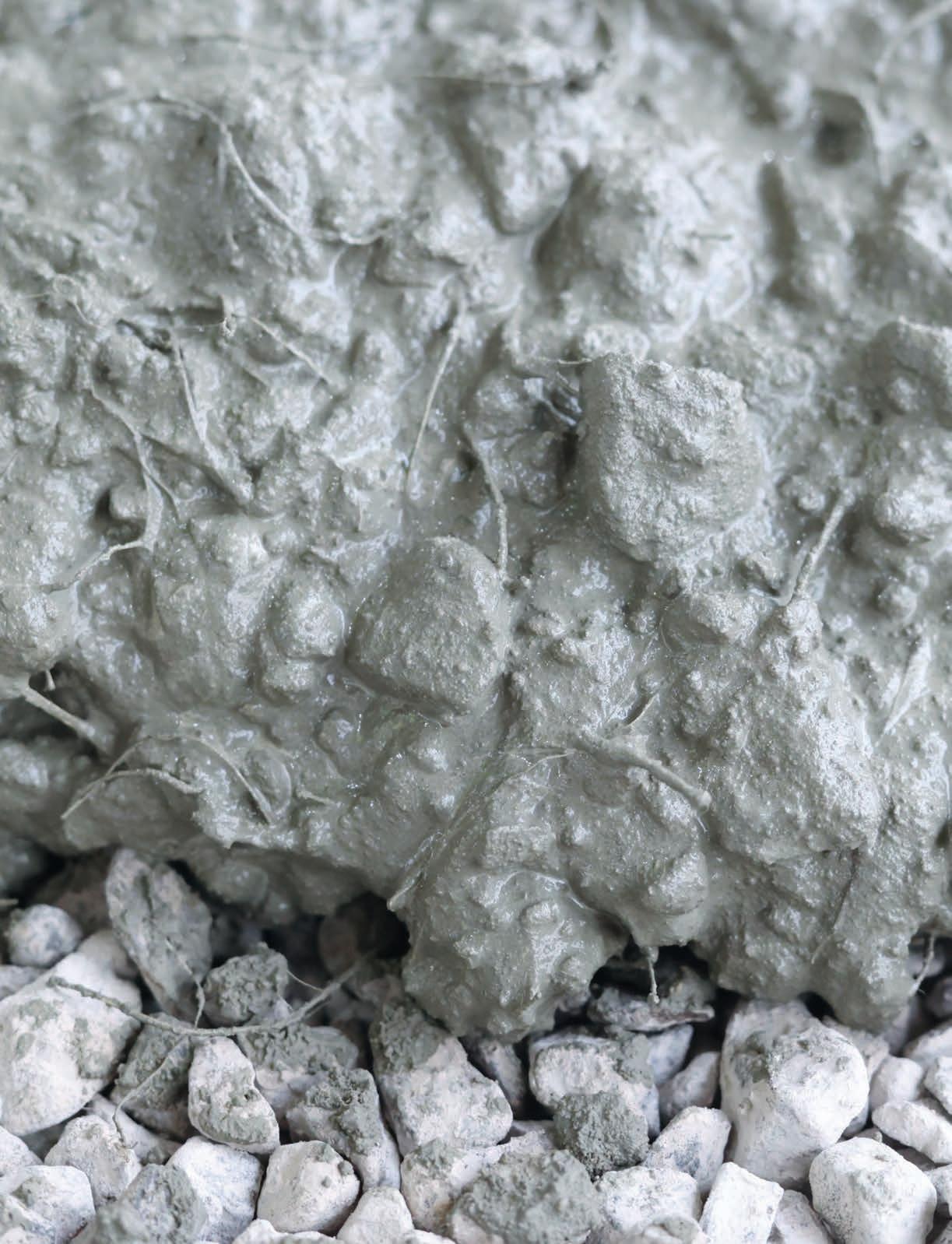
REDUCING CONCRETE’S CARBON FOOTPRINT
USING FIBRES TO GO GREEN
The Worldwide Leader in Concrete Paving Technology
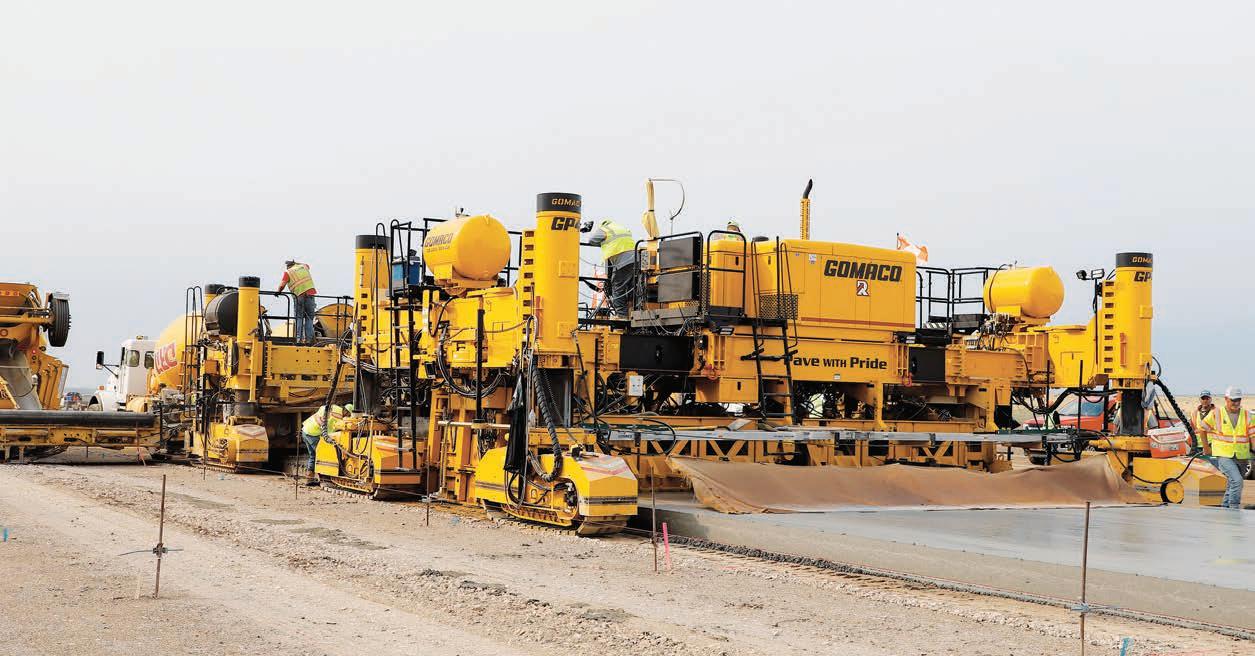
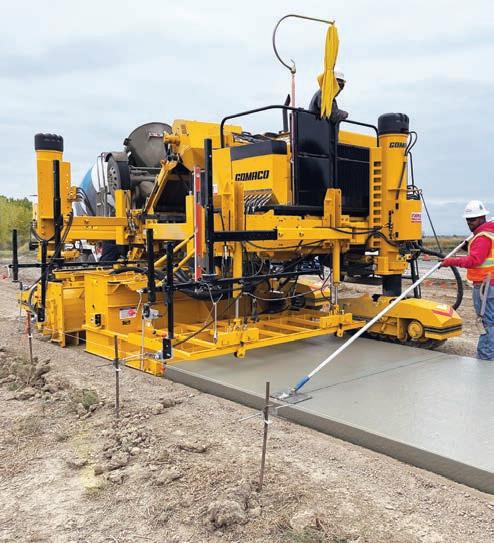
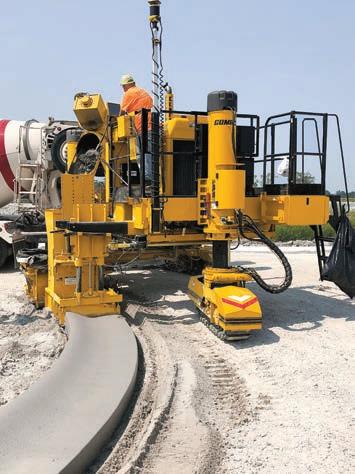
GOMACO offers the full range of concrete slipform pavers, curb and gutter machines, trimmers, placer/spreaders, texture/ cure machines and bridge/canal finishing equipment. GOMACO equipment features our exclusive and proprietary G+® control system, created in-house by our software engineers from the wants and needs of contractors paving in the field. At the heart of GOMACO equipment is our passion for concrete and our commitment to our customers. We look forward to visiting with you about your upcoming paving projects and your concrete paving equipment needs. Our worldwide distributor network and our corporate team always stand ready to serve and assist you.
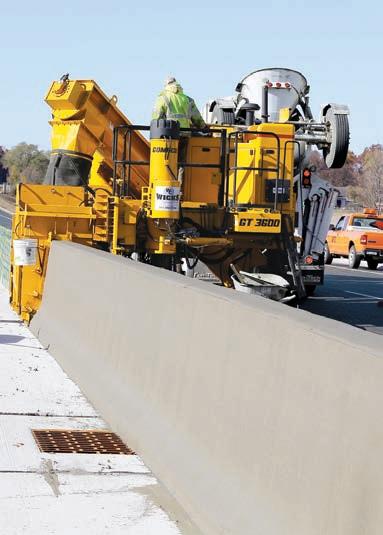
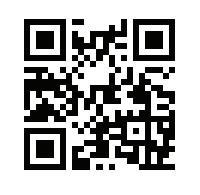
REDUCING THE CARBON FOOTPRINT OF CONCRETE CONSTRUCTION
The use of fibre reinforcement in concrete not only improves durability; it also reduces the embodied carbon in the materials of construction.
BY GUSTAVO POLIDORO
It is no secret that concrete is one of the largest contributors to the emission of carbon dioxide around the world. To their credit, the concrete and cement industries have recognized that they must play a role in reducing their carbon impact. As such, the industry is exploring all aspects of a build, from adjusting the components in our building materials, to the choice of material components used in projects.
Cement manufacturers have been working on low-carbon recipes to help bring down the carbon levels produced through the manufacturing process for the core ingredient in concrete. Others in the industry have been doing research to bring down the carbon footprint of concrete projects as well, including through the use of recycled aggregate and even alternative aggregate materials. The use of fibre-reinforced concrete (FRC) is another industry innovation that holds the potential to make a sizable net-positive impact in the ongoing battle to reduce the carbon footprint of our projects.
Over the past several years, there has been a renewed interest in the use of fibre reinforcement in concrete pavements for parking lots, white toppings, bridge decks and roadways. As interest rises, various technical organizations such as the American Concrete Institute (ACI), American Concrete Pavement Association (ACPA) and the National Concrete Pavement Technology (CP Tech) Center have stepped forward with new guidance and recommendations on how to properly select and use fibre types in concrete.
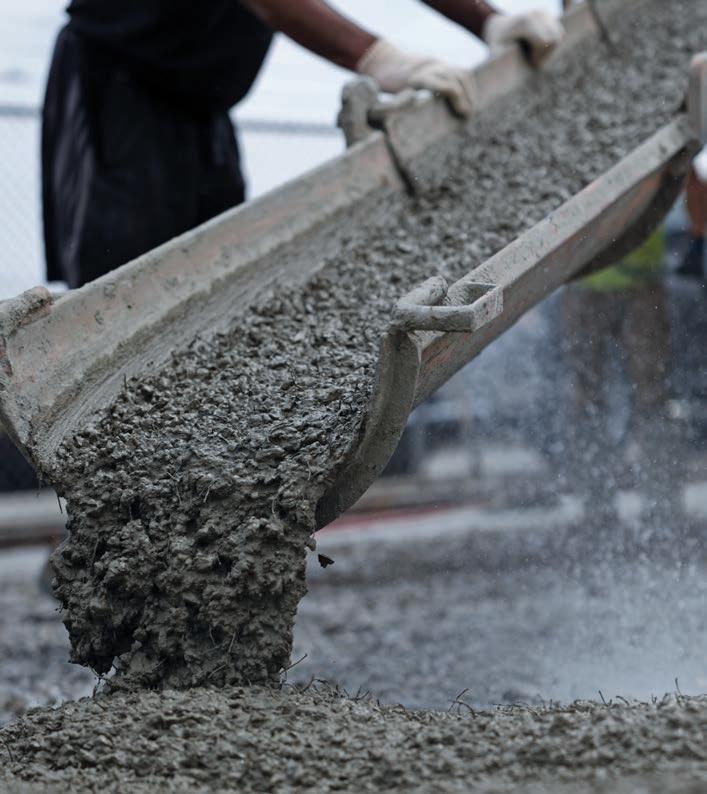
MAKING THE GOOD BETTER
Despite some of the negative marketing and connotations, concrete is already one of the most environmentally friendly materials available when properly used. It is durable, cost effective, is made from locally sourced ingredients, is relatively easy to work with, has minimal waste, can be customized, and
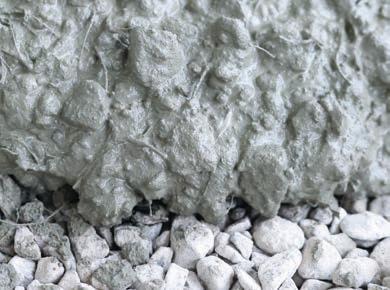
has a thermal mass that can be advantageous. It has a long history of use because of all its positive qualities.
To help address some of its less desirable traits, the construction industry has embarked on a pathway leading to sustainable concrete practices and technologies that can save energy, reduce CO2 emissions,
CARBON REDUCTION
protect the environment and maximize economics. By taking a big-picture approach to the reduction of global carbon emissions, and focusing on embodied carbon, the use of fibre in place of steel reinforcing bars can indeed result in reduced CO2 footprints for our infrastructure and other major projects.
ASSESSING THE IMPACT
Globally, it is estimated that the construction industry accounts for a quarter of total carbon emissions. Cement production claims about seven per cent of global emissions, and steel reinforcement accounts for 1.5 per cent of world-wide carbon emissions. With the large volume of reinforced concrete floors used worldwide, roughly 45 per cent of steel consumption is destined for concrete reinforcement. That’s a lot of opportunity for improvement.
The energy required to produce one metric ton of reinforced concrete is 2.5 GJ/t. This compares with 30 GJ/t for steel and 2.0 GJ/t for wood. A study comparing the emissions of several different building materials per 1,000 kg found that concrete produced 147 kg of CO2, metals produced 3,000 kg of CO2, and wood produced 127 kg of CO2
When exploring ways to reduce carbon emissions, there appears to be some opportunity in exploring how floors, walls, roadways and foundations could be reinforced at a lower carbon cost.
With a focus on reducing environmental impact, the knowledge, testing and experience of using synthetic macrofibre-reinforced concrete continues to grow for use in infrastructure projects, and its successful use and benefits are now being realized through full scale and long-term demonstration projects.
With positive anecdotal case studies, many prospective engineers, architectural firms and clients are now requesting additional information as to the environmental impacts of using fibres in replacement of traditional reinforcement, or as an added material in concrete to improve durability and useful service life. The industry is working on environmental product declarations and other materials to officially
qualify much of what has been observed via demonstration projects.
A BRIEF FRC HISTORY
Although FRC has been used since the 1960s, there has been little change to its use in North America for many potential applications, until recently. New developments in materials technology and the addition of field experience to the engineering knowledge base have expanded the applications of FRC to include design guides that are now material independent and recognized by the engineering community.
Over the past two decades, FRC technology has gained acceptance from industry bodies such as UL, Steel Deck Institute (SDI) and ACI thanks to multi-million-dollar research programs. Structural designs and software tools have been designed, and calculations for equivalent reinforcing options to allow for comparison to conventional designs have also been developed. As such, FRC is being used in high-profile projects, including applications where failure is not acceptable and where durability is key, such as in bridge decking and paving.
DIFFERENTIATING THE FIBRES
The physical characteristics of fibres varies, with each type having its ideal application. In general, the industry has accepted that steel macrofibres and older micro synthetic fibres (fibrillated, monofils, etc.) are not used under the same conditions.
Micro synthetics are generally used as secondary reinforcement, addressing plastic shrinkage only. Steel fibres are more suitable for industrial floor designs and can replace heavier reinforcing configurations.
Synthetic macrofibres can be strong, like steel fibres, but simply not made of steel. The physical characteristics of these fibres, such as their length, tensile strength and diameter, are all different when compared to traditional micro synthetics.
Synthetic macrofibre composites can be used to replace steel reinforcement or in conjunction with steel reinforcement to increase durability and extend service life. The contribution to sustainable construc-
tion through lowered environmental, social and economic impacts is currently being documented.
To ensure proper performance of the concrete, macrofibres dosages should be calculated based on the engineering requirements of the project. Since the fibres are worked into the concrete mix, significant savings may be realized in construction time, labour and overall costs.
Once placed, FRC has an increased resistance to cracking, impact and fatigue as the reinforcement is randomized and three-dimensional throughout the structure, rather than being provided along a more defined plane that exists with more traditional reinforcement components.
WHY FRC?
We are in the midst of a massive infrastructure deficit. A quarter of our existing roads, bridges and other structures will need to be repaired or replaced by 2030, and these projects need to be completed with a lower environmental impact. The use of innovative material substitutions, like fibre-reinforced concrete, can help with both the longevity of these structures and their carbon footprints.
The use of FRC has been found to reduce CO2 emissions by more than 50 per cent compared to more traditional reinforcing means used in typical industrial floors and pavements.
And other materials, such as chemical admixtures, advanced cements and supplemental cementitious materials, can demonstrate additional significant reductions in overall upfront global warming potential (GWP) values.
We know that sustainability, or building better, needs to include a hard look at building practices, materials and long-term costs over time. If FRC lasts longer than normal concrete, is that not the exact definition of improving sustainability?
Based in Toronto, Gustavo Polidoro is the product manager of marketing and technology for fibre reinforced concrete at Euclid Chemical.
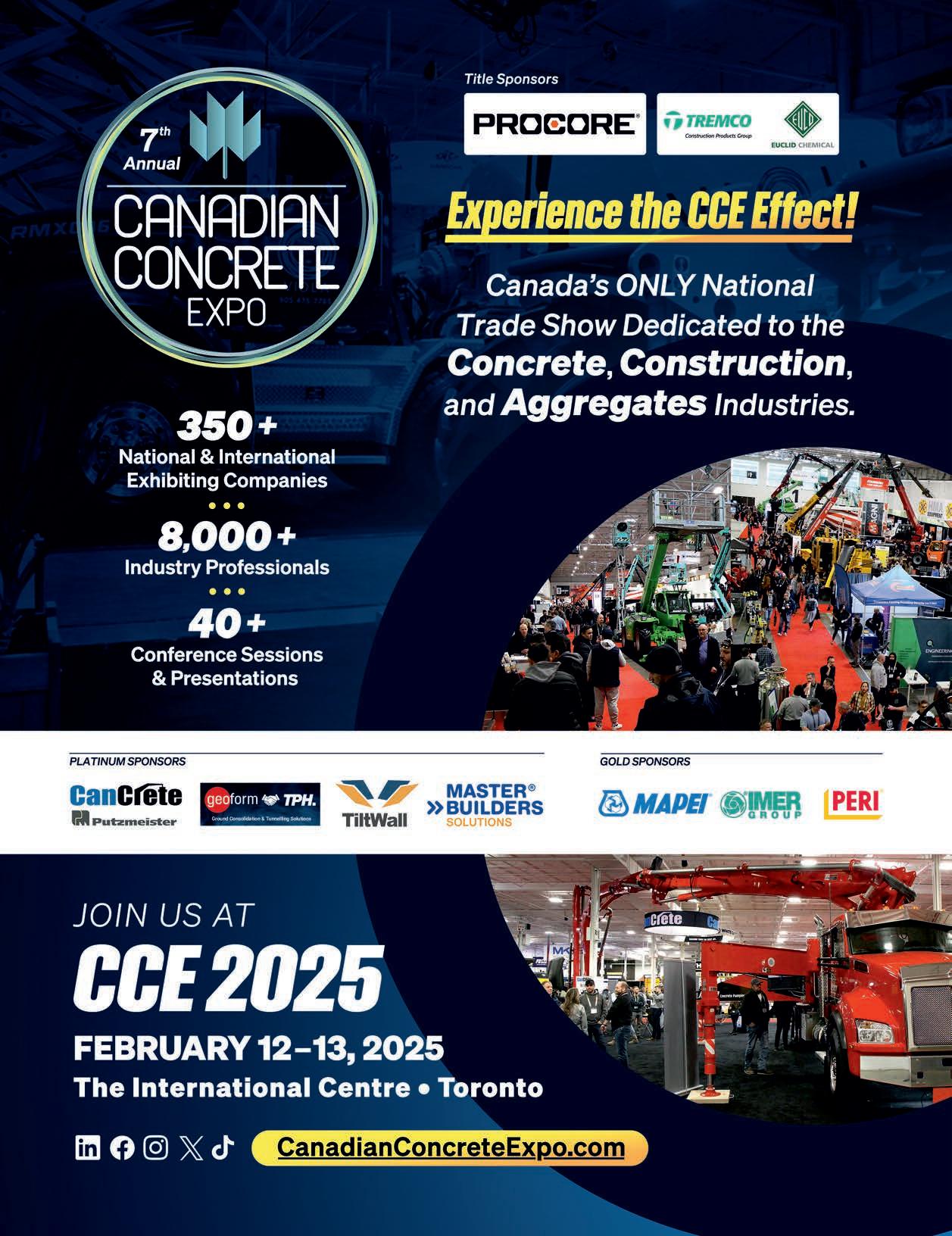
TRANSFORMING CONCRETE PRODUCTION
Volumetric mixers providing flexibility and material control on site.
BY JAY FASO
In today’s fast-paced and competitive construction industry, efficiency and precision are non-negotiables. Whether tackling large commercial projects or detailed residential builds, the right tools and technology can make all the difference. Across Canada, owners and contractors increasingly embrace volumetric technology’s innovative capabilities, transforming concrete production and driving new business growth.
Volumetric concrete mixers offer a unique approach from the traditional drum truck, measuring and dispensing concrete directly at the jobsite by volume rather than weight. Each component — sand,
stone, cement powder, water, additives and supplementary cementing materials — is stored in a separate compartment. At the jobsite, concrete is mixed on demand in the precise amount needed.
If you own a volumetric concrete mixer or have considered adding one to your fleet, the following information and tips will help you get the most from your investment for years.
WORKING WITH MULTIPLE MIXES
Proportioning by volume versus weight is at the heart of a volumetric mobile mixer. The result is a final product capable of accuracies better than plus or minus one per cent.
A typical volumetric truck features divided side-by-side open bins for sand and stone. A watertight bin equipped with automatic vibrators securely contains cement. Automatic vibrators guarantee precise cement proportioning and a steady flow to the mixer. Water is stored in an auxiliary tank and introduced into the mixer via flowmeters that ensure accurate monitoring.
The versatility of mobile volumetric trucks delivers virtually unlimited concrete mixes. Aggregates are carried separately or combined according to the design mix. For other concrete output requirements or specialty jobs, liquid admixtures such as accelerators, retarders, air-entraining agents

A whole new edge in building
The industry’s newest profiles and trims
Expect more. For the most complete line of high-quality, durable, colorcomplementary profiles and trims – with more than 4,500 pieces to match your creative design – visit www.mapei.ca

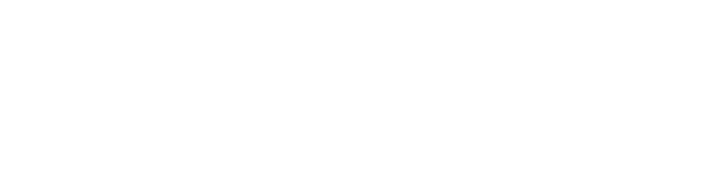
MATERIALS
and modified latex are carried in a separate system. These ingredients are introduced as needed, via precise flow controls.
MANAGING MULTIPLE PROJECTS
As part of a contractor’s fleet, a volumetric mixer can significantly improve speed and efficiency between deliveries and when projects require changing mix designs as the separate material compartments on volumetric trucks allow operators to change mix designs on the fly without returning to the batch plant.
For example, if the slump changes halfway through a curb and gutter project, work stops only long enough to adjust the design mix. What formerly may have taken more than a day can be completed in hours with a volumetric concrete truck.
Another example is working on bridge decks. Latex-modified concrete is often used to counteract the freeze-thaw cycle in colder months. A volumetric mixer can efficiently produce latex-modified and regular concrete, streamlining the project
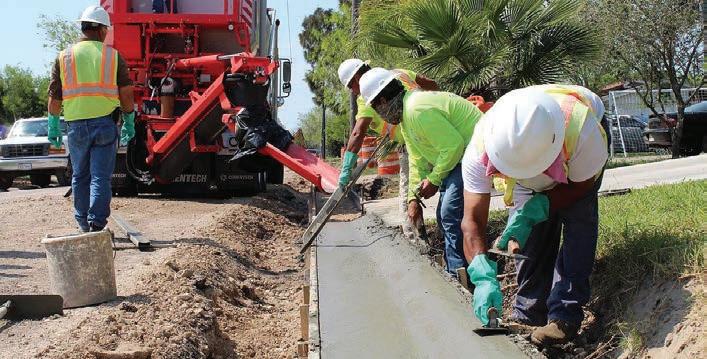
as operators can effortlessly transition from pouring high-strength 5,000 PSI concrete to a low-strength flowable fill in seconds by selecting a different mix design via the control panel on the mixer.
Volumetric technology allows pre-programmed information for each job and mix using an onboard electric control panel. Uploaded admixes can be saved in the system memory to easily navigate frequently used designs, including the history of all mixtures and quantities.
Once an admixture is selected, the operator sets gate controls, pushes a button and pours. Automated admixture tanks ensure the exact amount is used every time.
A two-speed cement bin provides adjustable cement discharge, making switching between concrete mixers and flowable fill applications easy.
HUMIDITY’S UPS AND DOWNS
Water is essential in making concrete, activating cement and causing it to harden and bind to the aggregates. The amount of water used affects quality, however. Too much causes concrete to weaken and easily crack, while too little makes the mix difficult to work with.
Volumetric concrete mixers measure and mix concrete on-site to the exact specifications for a fresh product with every
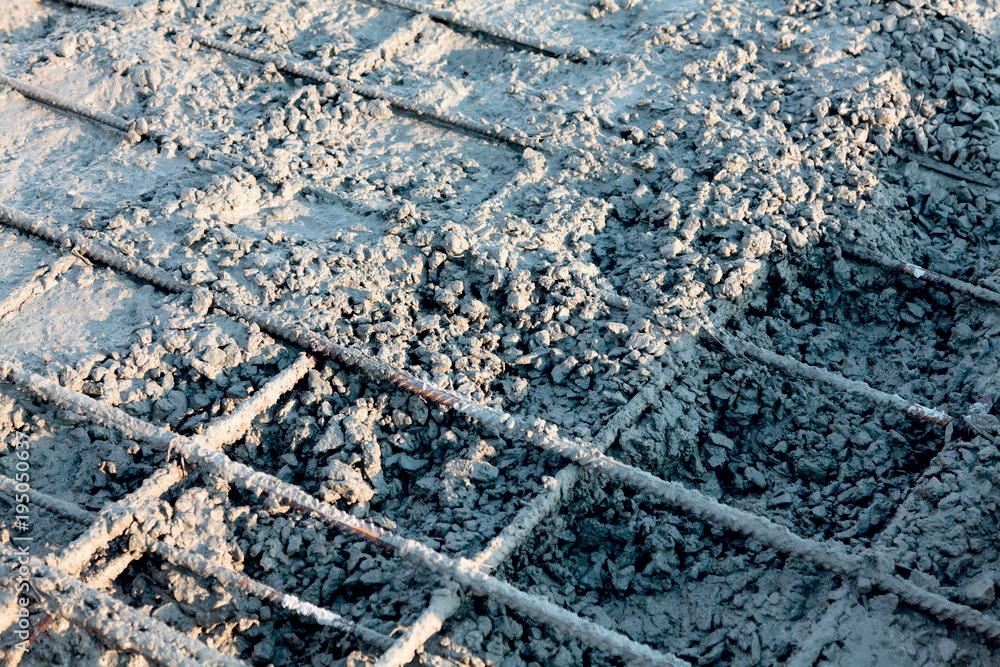
TIEREBAREVENFASTER!
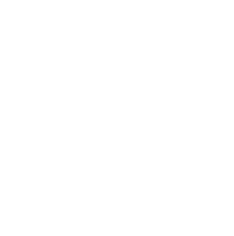
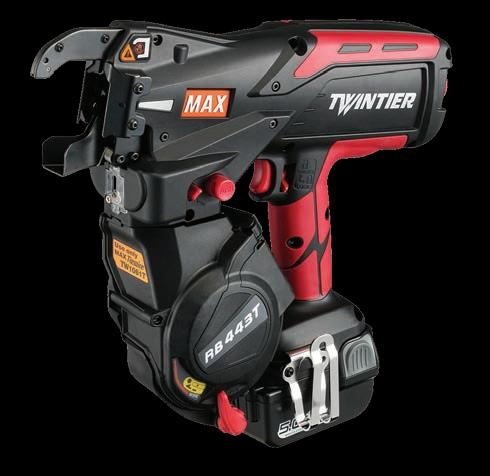

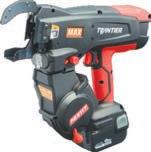
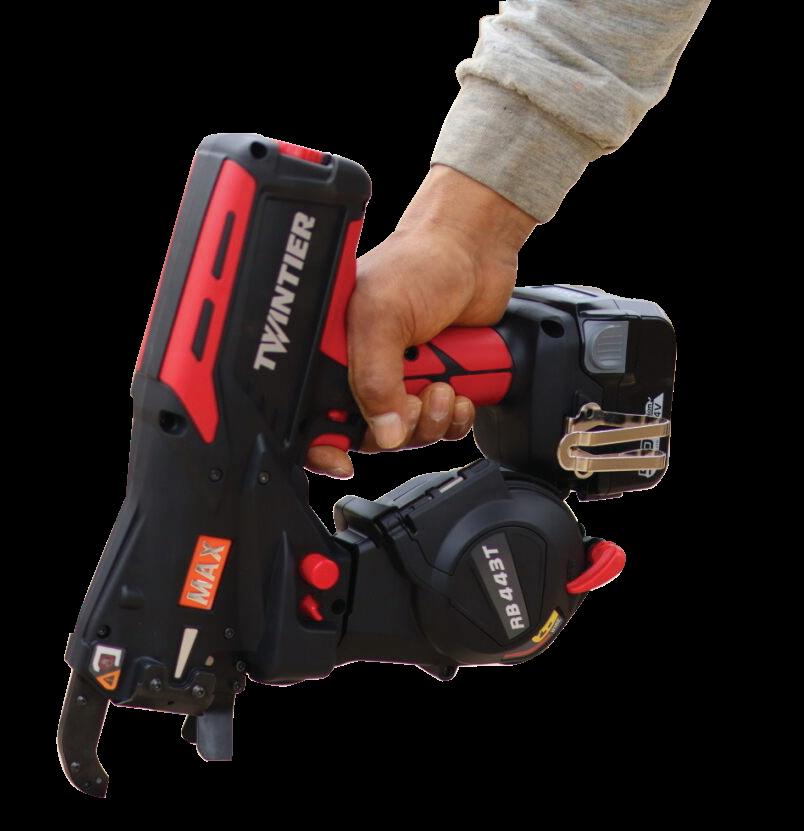


pour, and the onboard mixing technology controls water content to adjust for varying humidity levels, ensuring consistency regardless of weather changes or unexpected site conditions.
Volumetric mobile mixers also seamlessly switch between wet and dry processes, such as when working with gunite and shotcrete, with precise material measurements along the way. A simple adjustment of the water flow allows contractors to adapt the slump of the mix throughout the pour.
CLEANING AND MAINTENANCE
Implementing an easy-to-follow daily process for unloading and cleaning volumetric concrete trucks is crucial for maintaining consistent mix quality, enhancing safety, reducing costs and extending the equipment’s lifespan. It is recommended that a standardized procedure, or checklist, be used for unloading and cleaning trucks each day. This checklist should include:
• Confirming that the hydraulic systems are functioning properly.
• Ensuring all remote controls are clean and in working order.
• Hosing down the back of the truck and chute before unloading.
• Creating windrows for extra product.
• Rinsing off the chute before leaving the jobsite to prevent safety hazards for other drivers.
Any good heavy equipment owner also knows the importance of routine maintenance. Regular inspections will help keep the volumetric concrete mixer and its machinery at peak performance. Following daily and monthly checkups, owners will begin to see a wear pattern and can determine an appropriate maintenance plan for the unit.
Depending on the materials and series of units, the mixer is generally the first component requiring repairs on most mobile concrete mixers. The more time spent looking over the unit, the more likely you’ll develop a well-rounded schedule, including how to plan for downtime. A volumetric concrete mixer typically produces 3,000 to 5,000 yards before there is a
need to replace wear blades, the lower boot and bearings.
My company has developed a few maintenance checklists and task lists to help equipment owners and operators keep their machines in peak condition, especially during periods of more frequent use. As part of a daily routine, while cleaning we recommend noting any items showing wear or need replacing by inspecting wear blades, the belt wiper, the mixer motor for leaks,
the lower and upper mixer bearings, and for concrete build-up inside the unit.
On a monthly basis, it is beneficial to inspect the conveyor belt and tension, check the side and centre guide material, adjust the conveyor belt wiper, and flush the admix system with water.
Jay Faso is the regional sales manager for Canada at Cemen Tech, a manufacturer of volumetric concrete mixers.
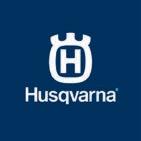
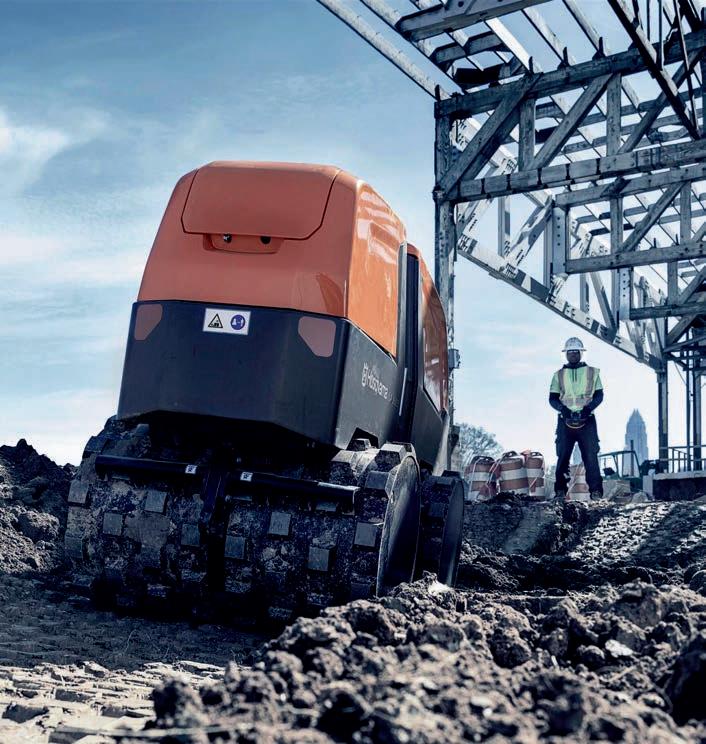
POWERFUL TRENCH COMPACTOR
The Husqvarna LP 9505 is a powerful, easy-to-operate trench compactor essential for demanding compaction jobs. Maintenance is quick and easy with all service points clearly marked under the easy-to-access protective hoods. Featuring smartly designed solutions, the LP 9505 can be used on a wide range of applications. Visit our website to learn more.
www.husqvarnaconstruction.com

SMOOTH

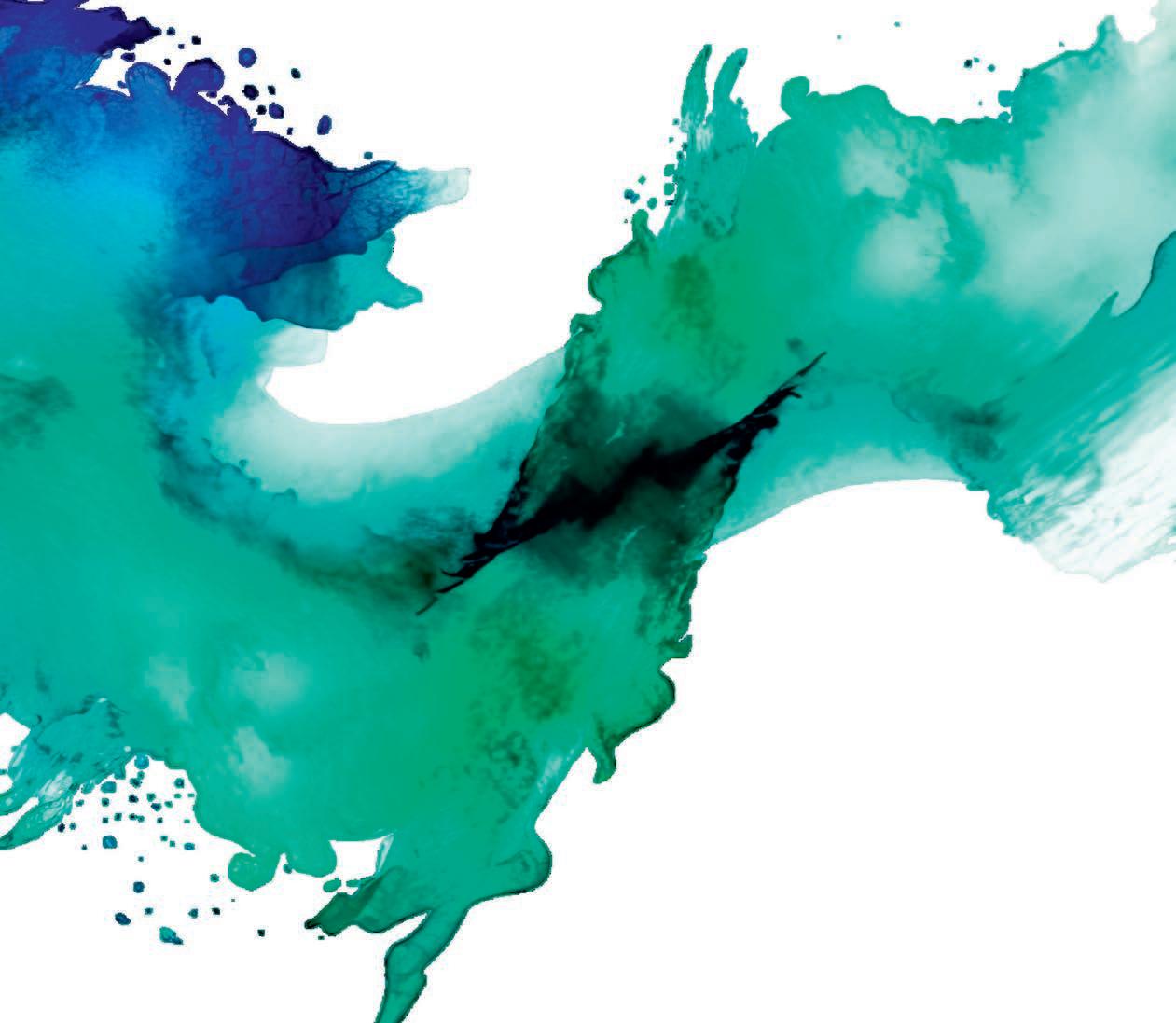
Join the power players of concrete and masonry. OPERATOR
There’s only one place you’ll find the heavy hitters of concrete and masonry this January: Vegas, baby — at World of Concrete 2025, the largest and only annual international event dedicated to your business. Be here to mix with industry giants. Get your hands on the latest technologies revolutionizing safety, performance and speed. And learn what it takes to not only claim a piece of our industry’s massive projected growth but dominate the field.

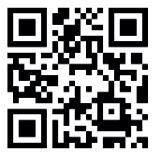
EXHIBITS: JANUARY 21-23, 2025
EDUCATION: JANUARY 20-23
LAS VEGAS CONVENTION CENTER