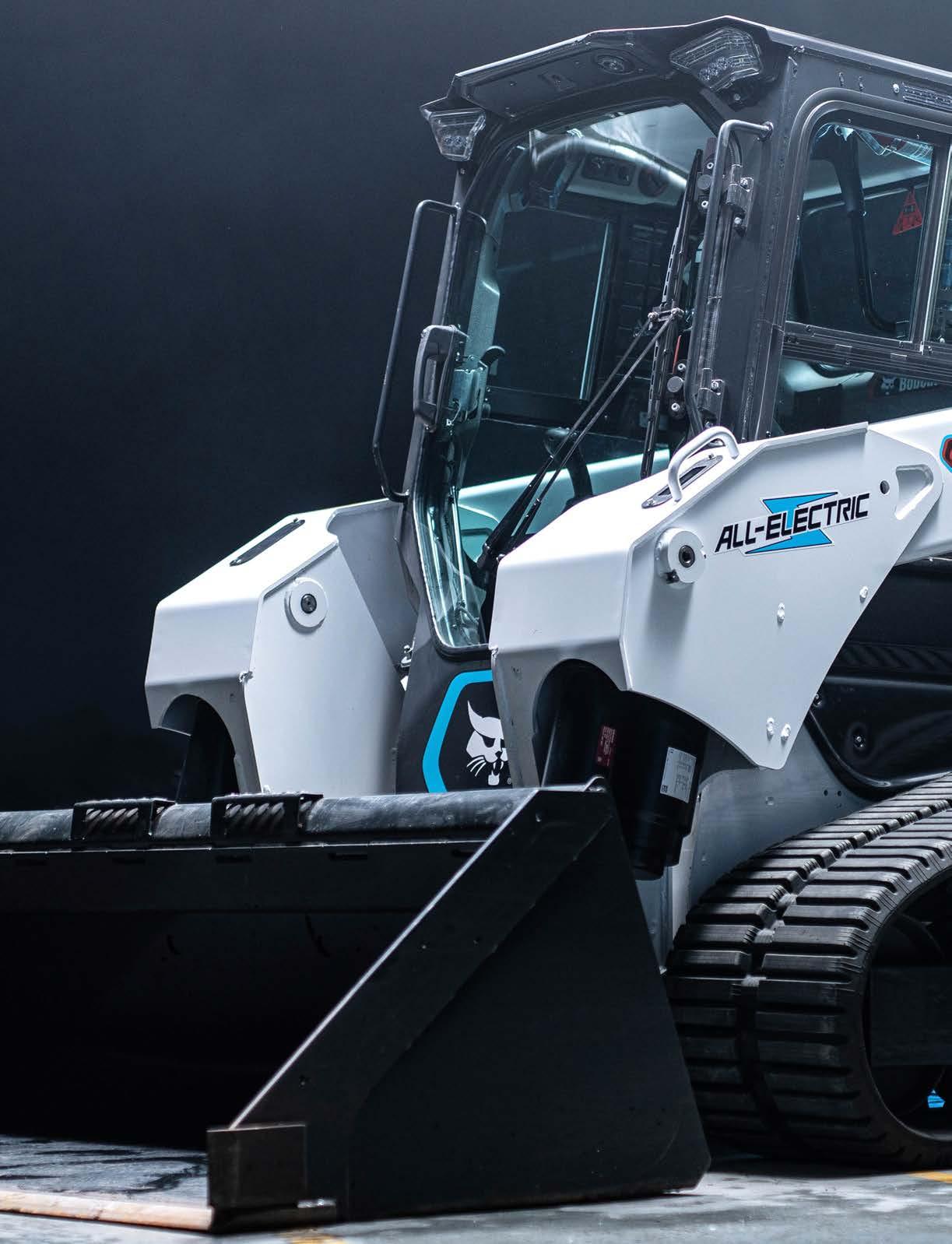
TOP 40 UNDER 40 CLASS OF 2024
CONSTRUCTION LAW: GETTING PAID FOR CHANGES
TECHNOLOGY: MAKING YOUR SOFTWARE WORK FOR YOU
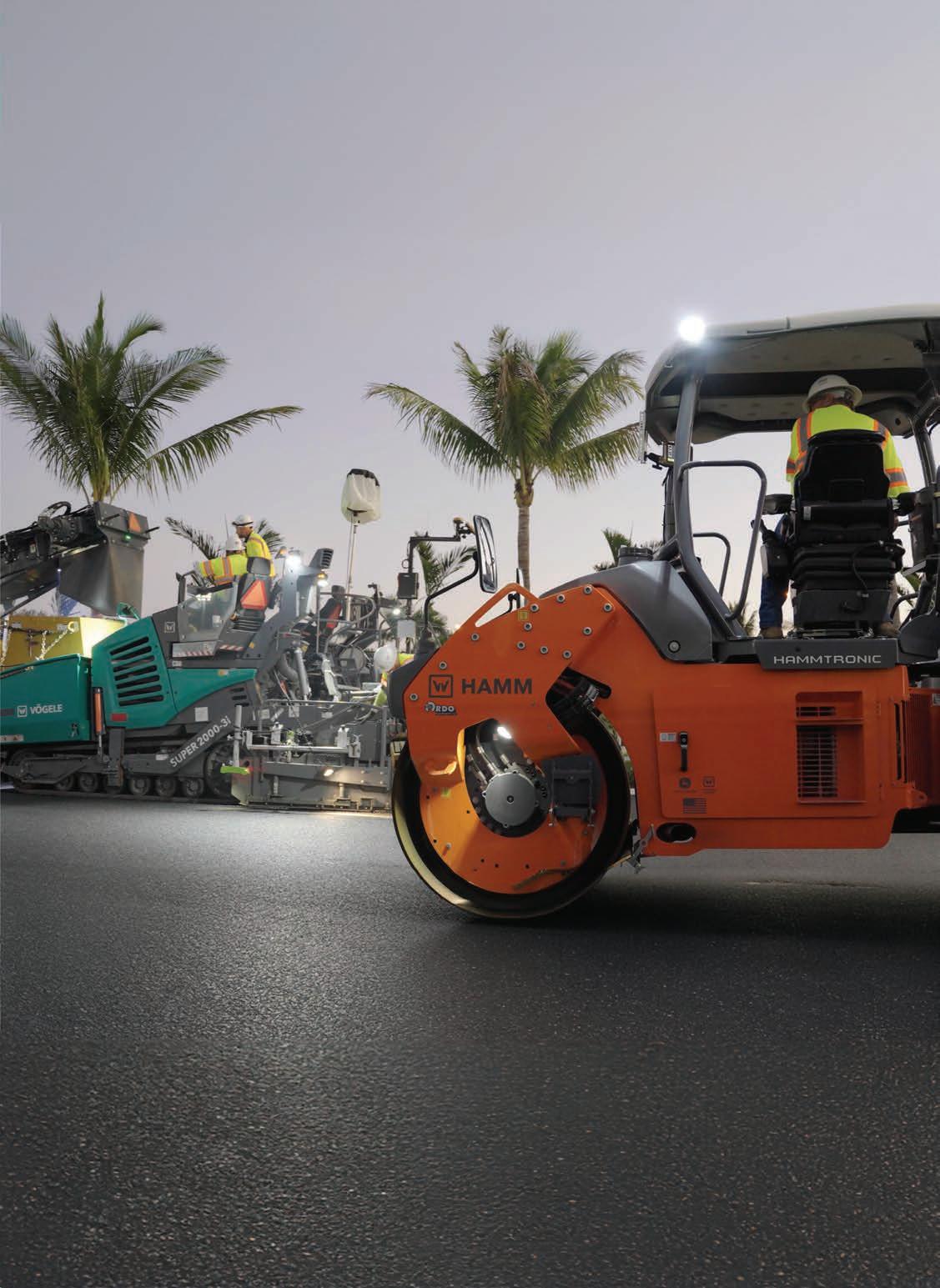

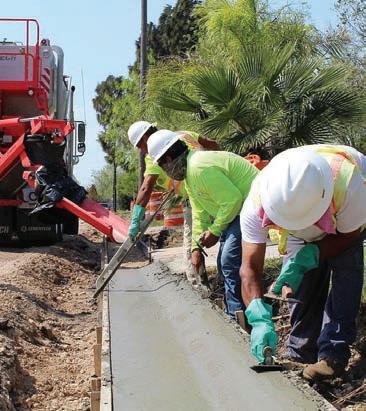
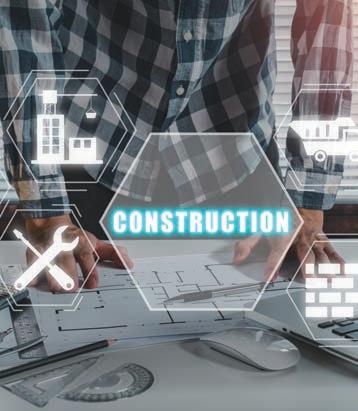

TOP 40 UNDER 40 CLASS OF 2024
CONSTRUCTION LAW: GETTING PAID FOR CHANGES
TECHNOLOGY: MAKING YOUR SOFTWARE WORK FOR YOU
The summer months have put infrastructure into the spotlight, although it’s been more of a “you don’t know what you’ve got until it’s gone” casting, rather than a celebratory “look what we built” story.
At the time of writing this column, the City of Calgary was still navigating water-use restrictions following its major water main break in June, and a subsequent break in July, and it was not the only major city experiencing issues with its water lines. Montreal had a similar break in August.
The line in Montreal was installed in 1985, while the one in Calgary dates to 1975 and both breaks point to the need to inspect and maintain our critical infrastructure, so that we can avoid headlines that make attention-grabbing splashes.
In a better light, but no less splashy, we’re celebrating the industry with our annual 40 Under 40 in Canadian Construction recognition program (Page 17).
The 40 individuals recognized in this year’s class come from a wide variety of companies and serve a considerable mix of roles, reflecting the range of opportunities that exist in today’s world of construction.
Congratulations to those who made this year’s list and thank you to everyone who submitted nominations. If you nominated someone and don’t see them on the list, I encourage you to nominate them again next year, provided they are still 39 or younger by the end of 2025.
www.on-sitemag.com
READER SERVICE
Print and digital subscription inquiries or changes, please contact Angelita Potal
Email: apotal@annexbusinessmedia.com
Tel: (416) 510-5113
Fax: (416) 510-6875
Mail: 111 Gordon Baker Road, Suite 400, Toronto, ON M2H 3R1
PUBLISHER | Peter Leonard (416) 510-6847 pleonard@on-sitemag.com
EDITOR | Adam Freill (416) 996-2391 afreill@on-sitemag.com
MEDIA DESIGNER | Lisa Zambri lzambri@annexbusinessmedia.com
ASSOCIATE PUBLISHER | David Skene (416) 510-6884 dskene@on-sitemag.com
ACCOUNT COORDINATOR | Kim Rossiter (416) 510-6794 krossiter@on-sitemag.com
AUDIENCE DEVELOPMENT MANAGER | Urszula Grzyb (416) 510-5180 ugrzyb@annexbusinessmedia.com
CEO | Scott Jamieson sjamieson@annexbusinessmedia.com
Established in 1957, On-Site is published by Annex Business Media 111 Gordon Baker Road, Suite 400, Toronto, ON M2H 3R1 Publications Mail Agreement No. 40065710 ISSN: 1910-118X (Print) ISSN 2371-8544 (Online)
SUBSCRIPTION RATES Canada $50.49 CAD per year, United States $115.26 CAD per year, Other foreign $139.23 CAD, Single Copy Canada $13.50 CAD. On-Site is published 5 times per year except for occasional combined, expanded or premium issues, which count as two subscription issues. Occasionally, On-Site will mail information on behalf of industry-related groups whose products and services we believe may be of interest to you. If you prefer not to receive this information, please contact our circulation department in any of the four ways listed above.
Annex Business Media Privacy Officer privacy@annexbusinessmedia.com Tel: 800-668-2374
Get the latest construction news!
Follow us on @OnSiteMag
Speaking of people advancing the industry, our judges are part of the infrastructure of our program, so I would like to formally acknowledge and thank each of them. Helping to select our 40 this year were Ashvin Ghurburrun of PCL, Brandon Bird of Bird Mechanical Ltd., Jesse Unke of Maven Consulting Limited, Lewis Cowan of BDA Inc. and the Ontario General Contractors Association, and Taylor Lefebre of Green Infrastructure Partners Inc. Thank you all for the hours spent reviewing the nominations, and for your dedication to our industry.
And congratulations to our newest 40 Under 40 honourees.
Until next time, stay safe and do good work.
Adam Freill / Editor afreill@annexbusinessmedia.com
Content copyright ©2024 by Annex Business Media may not be reprinted without permission.
On-Site receives unsolicited materials (including letters to the editor, press releases, promotional items and images) from time to time. On-Site, its affiliates and assignees may use, reproduce, publish, re-publish, distribute, store and archive such unsolicited submissions in whole or in part in any form or medium whatsoever, without compensation of any sort.
DISCLAIMER This publication is for informational purposes only The content and “expert” advice presented are not intended as a substitute for informed professional engineering advice. You should not act on information contained in this publication without seeking specific advice from qualified engineering professionals.
OF
MEMBER
In June, the Toronto Community Benefits Network (TCBN) celebrated leaders and organizations championing diversity, equity and inclusion in Canada’s construction industry as it presented its annual Building Diversity Awards (BDA) at the Meridian Arts Centre in North York, Ont.
This year’s event saw submissions from across the country and culminated in an inspiring evening gala hosted by media personalities Sebastian Clovis and Patricia Jaggernauth.
“Toronto is strong; Canada is strong, because we are diverse…
SkyTrain stations contract awarded
South Fraser Station Partners, a consortium comprised of Aecon, ACCIONA and Pomerleau, has reached financial close for the stations contract on the Surrey Langley SkyTrain Project in British Columbia.
The contract, valued at $928 million, is part of the work that will see the existing Expo Line extended along Fraser Highway from King George Station to a new terminus station in Langley City Centre. The project includes the design and construction of eight stations, three transit exchanges, nine power substations, and 250 metres of guideway at the SkyTrain’s terminus station.
Certain early works are underway, and construction is expected to commence
We are diverse. And we cooperate. We work together. This is what community benefits is about,” stated Toronto Mayor Olivia Chow, who talked about the need to build the infrastructure and supporting programs that can allow for communities to thrive. “When we build, the only way we can build properly is together, with neighbours, with communities, so everyone can benefit.”
Established by TCBN in partnership with its community, labour and industry partners, and presented by Desjardins Group, the BDAs acknowledge the importance of championing diversity and leveraging local talent to build the construction industry.
“The Building Diversity Awards Gala is our way of acknowledging leaders that are paving the way for a more inclusive construction industry and contributing to sustainable communities across Canada,” stated TCBN executive director Rosemarie Powell. “We’re encouraged by a growing recognition that there is value in community partnerships and that endeavouring to reflect the communities that we serve just makes sense.”
One of the most heartfelt commentaries about the industry came from NexGen Builders Award winner in the Mentor category, Bubba Qwulshemut, a Red-Seal plumber from the Somena Tribe who is active in outreach to underrepresented jobseekers. He spoke about some of the challenges he faced in becoming a tradesperson, and how his experiences motivate him to help others.
“I walk the jobsite every day in Cowichan on Vancouver Island, and I see the amount of young people that are contributing to the project,” he said. “I see in many of those young people, I see myself, so many years ago.”
Visit www.on-sitemag.com for a list of this year’s award recipients.
late this year, with anticipated substantial completion in
“We look forward to working with the Province of B.C. and our partners to deliver this critical transit extension – improving mobility for one of the fastest growing areas in Metro Vancouver,” said Jean-Louis
Servranckx, president and CEO at Aecon Group Inc.
“This project underscores our dedication to creating lasting infrastructure that connects our communities and strengthens the B.C. economy,” added Philippe Adam, president and CEO at Pomerleau.
Join the power players of concrete and masonry. OPERATOR
There’s only one place you’ll find the heavy hitters of concrete and masonry this January: Vegas, baby — at World of Concrete 2025, the largest and only annual international event dedicated to your business. Be here to mix with industry giants. Get your hands on the latest technologies revolutionizing safety, performance and speed. And learn what it takes to not only claim a piece of our industry’s massive projected growth but dominate the field.
EXHIBITS: JANUARY 21-23, 2025
EDUCATION: JANUARY 20-23
LAS VEGAS CONVENTION CENTER
A pair of Canadian and American ironworkers were the first to celebrate the connection of the Gordie Howe International Bridge as the final two edge girders were put in place this past June. A little over a month later, the bridge deck was connected between Windsor, Ont., and Detroit, Mich., making the bridge an official border crossing.
Casey Whitson, a second-generation American ironworker from Michigan, and a member of Iron Workers Local 25, and Jason Huggett, a second-generation Canadian ironworker from Ontario, a member of Iron Workers Local 700, shook hands to mark the point where the bridge officially become an international crossing.
Although the connections have been made, Work continues so that the bridge can officially open to public traffic next year. Measuring 853 metres (0.53 miles), the Gordie Howe International Bridge is
the longest cable-stayed bridge in North America and tenth longest in the world. It is the first new crossing to connect Ontario and Michigan in more than 60 years and is expected contribute to economic growth by strengthening the fluidity and resiliency at the Windsor-Detroit trade corridor.
“Canada and the United States have always done big things, together. As the largest and most ambitious infrastructure
project along the Canada-United States border, the Gordie Howe International Bridge is proof of just that,” said Canada’s Minister of Housing, Infrastructure and Communities Sean Fraser. “Beyond further strengthening the deep connection between our two nations, this bridge will drive economic growth for both countries while creating more jobs and increasing border security.”
From legal and technology discussions to infrastructure and decarbonization outlooks, this year’s Canadian Institute of Quantity Surveyors (CIQS) Congress, held in Toronto in early summer, featured a strong lineup of speakers and panellists, as well as awards recognizing the contributions of CIQS members to Canada’s construction industry.
“Although I focus on the legal documents, the majority of problems on our files are driven by cost related issues,” said keynote speaker Danna Donald, a partner at Osler, Hoskin & Harcourt LLP as she discussed such issues as the need for new and renewed infrastructure projects throughout Canada.
“I think all of us in the room need to understand the impact of the infrastructure deficit that we have in Canada today,” she said. “Every day, we all use our shared infrastructure and many of the core components are failing.”
With diversity and inclusion being at the heart of its corporate values, Procore has announced a pair of strategic partnerships in Canada’s construction industry. The technology giant has linked up with the Afro Canadian Contractors Association (ACCA) and the Canadian Association of Women in Construction (CAWIC) with a commitment to support diversity, inclusion and innovation within the construction industry.
By joining forces with the two organizations, Procore says it is aiming to empower Canadian contractors and construction professionals by providing training, technology solutions and support to minority contractors, diverse-owned firms, and women in construction across the country.
Included in the partnerships are comprehensive training programs, access to the Procore construction management platform, and discounted buying programs
She pointed to a 2021 report on Canada’s infrastructure that indicated that a third of the country’s core public infrastructure was in poor condition, adding that there is opportunity for quantitative surveyors to play a role in the projects that will help fill in the $200 billion to $1 trillion infrastructure gap – a figure that varies since, as she pointed out, Canada does not currently have a way to formally track the full infrastructure picture, making it possible to only estimate the issue.
Other opportunities for members of CIQS exist in the carbon market, explained Ross Huartt of MBC Group, who discussed the movement towards assessing and measuring carbon emissions in the construction sector.
“Whether it’s quantity of bricks, quantity of dollars, or quantity of carbon, in this case, we have an opportunity to be at the forefront of an emerging market,” he explained.
Next year’s CIQS Congress is scheduled to take place in Winnipeg. Watch for details to be posted on the organization’s website.
to eligible members.
“As the president of the Afro Canadian Contractors Association, I am proud to partner with Procore in this significant initiative,” stated Stephen Callender. “This collaboration is a testament to our shared commitment to fostering diversity and inclusion within the construction industry. By providing minority contractors with cutting-edge technology and comprehensive training, we are equipping them with the tools they need to thrive in a competitive market. Together, we are paving the
way for a more equitable and innovative future in construction.”
“We are excited to partner with ACCA and CAWIC to empower minority contractors and diverse firms in Canada with the technical tools and skills they need to thrive in the construction industry,” added Irish Horsey, Procore’s director of industry advancement. “By providing access to Procore’s innovative construction management solutions and training resources, we aim to break down barriers and foster a more inclusive ecosystem.”
A selection of data reflecting trends in
Investment in building construction grew 2.8 per cent to reach $21.4 billion in June, reports Statistics Canada. The increases, says the agency, reflect April’s record high of $13.4 billion in building permits. The June increase in investment was primarily driven by the residential sector, which rose by 3.8 per cent, to $15 billion. Gains in the non-residential sector were more modest, rising 0.4 per cent to hit $6.4 billion across all segments. Year over year, investment in building construction was up by 10 per cent compared to June of 2023.
Investment in multi-unit construction grew six per cent, reaching $8.1 billion in June, while growth in non-residential construction was paced by gains in the commercial component, which rose by $27.2 million to sit at $3.2 billion. Investment in both the industrial and institutional components was virtually unchanged.
Total Employment in Canada
20,514,000
Unemployment Rate 6.4%
Construction Employment
1,563,400 (SOURCE: STATISTICS CANADA, THE DAILY, AND TABLE 14-10-0287-01.)
While overall employment was little changed across Canada in July, dropping just 2,800 positions, the news was more positive in the construction sector, where 7,000 additional positions were filled since June, reports Statistics Canada in its July 2024 Labour Force Survey. The additional workers engaged in construction in July resulted in a 0.4 per cent gain from June, and contributed to an increase of 1.7 per cent, or 25,500 positions, in the sector over the past 12 months. On a seasonally adjusted basis, there were 1,563,400 workers in Canada’s construction industry in July. The flat curve on overall employment kept the unemployment rate at 6.4 per cent for the month, while the employment rate fell to 60.9 per cent.
in non-residential construction, June 2024
The total value of building permits in Canada fell to $9.9 billion in June, off 13.9 per cent from May, reports Statistics Canada. Decreases were reported in 11 of the 13 provinces and territories, with both residential and non-residential sectors experiencing reductions. The only segments not sitting in red ink for the month were single-family dwellings and institutional construction, which posted gains of four and one per cent, respectively.
A substantial decline of almost 20 per cent in multi-unit construction intentions led the overall residential decline. Ontario and British Columbia were the main drivers of the drop in multi-family dwelling permit values, with Ontario reporting its largest monthly decrease since December 2023.
The 18 per cent drop in the non-residential sector permits, which put the cumulative figure at $3.5 billion for June, resulted from a 42.6 per cent decline in the industrial component, a 15.6 per cent dip in the commercial component, and a one per cent gain the institutional component.
While monthly totals were not hot, the total value of building permits in the second quarter was up 2.1 per cent from the first quarter, reaching $34.6 billion. This represents a second consecutive quarterly increase and the fourth highest quarterly value in this series of StatCan reports.
BY NATE HENDLEY
Electrification continues to be a growing trend, with construction OEMs turning out electric-powered excavators, wheel loaders and skid steers loaders, to name a few.
As to why manufacturers have so eagerly embraced electric vehicles (EVs) and machinery, Ray Gallant, vice-president of sustainability and productivity services with Volvo Construction Equipment, gives two answers.
“The short answer is because we care about the environment and the planet, so it’s the right thing to do,” he says. “Here’s the longer answer: The on-road industry has been transitioning to electric machines for a long time now, and the off-road industry is following suit.”
Government emission regulations are getting stricter, and more companies are adopting ambitious sustainability
goals, giving OEMs all the more reason to pursue electrification and other alternative energy solutions, he adds. As it is, electric battery machines already offer some major performance advantages over their fossilfuel counterparts.
“One of the biggest perks of electric equipment is that it doesn’t idle when it’s not in use. Most electric machines turn off when the operator stops for a few seconds, and they can start right back up to provide immediate power. When you consider that diesel machines can spend 40 per cent to 50 per cent of their shift idling, this is a big deal,” states Gallant.
Today’s lithium-ion batteries also offer longer life, more consistent performance, faster charging and less maintenance than earlier lead-acid and nickel-cadmium batteries.
For all that, plenty of obstacles need
to be overcome before electric machines gain greater acceptance. Concerns about battery life, charging time and infrastructure continue to linger.
“Construction machines often operate in areas where there is no electricity, or it cannot be accessed,” says Grant Van Tine, product manager for electric vehicles at John Deere. “Long-term or permanent project sites are generally more accommodating to electric machines because of the access to [charging] infrastructure. For all other construction sites, some form of mobile energy delivery or on-site renewable power generation will be needed to increase the adoption of battery electric machines.”
That said, “there is a lot of innovation and growth happening in the charging technology space because it’s essential for widespread electrification,” notes Brady Lewis, product manager, emerging prod-
ucts and technology at CASE Construction Equipment. “For electric vehicles located far from the grid, there are off-grid or weak-grid charging solutions available that use renewables such as solar and wind power, hydrogen fuel cells and biofuel power generators.”
While Volvo CE and other companies have produced mobile charging units, EV charging infrastructure is far from comprehensive. As a result, certain types of machinery benefit more from electrification than others.
“In the near term, compact and sub-compact EV machines are well suited for electrification because they can be easily transported to jobs further afield, and afterward can easily be loaded on a trailer and returned to the shop for charging,” says Lewis.
As EV infrastructure grows and battery technology evolves, however, the benefits of electric power will spread to a broader range of equipment.
When charging an electric battery takes no longer than filling a tank with gas, “the market for EVs will change dramatically. It’s getting there,” predicts Joel Honeyman, vice-president of global innovation at Doosan Bobcat.
With this in mind, here’s a look at what’s new and/or noteworthy in electric construction machinery.
Volvo Construction Equipment describes itself as “the construction industry leader with the largest EV lineup.”
“We have seven products available in North America, giving us the industry’s largest lineup, and we have more on the way,” says Gallant. “With three mini excavator models, a mid-size excavator, two compact wheel loaders and an asphalt compactor, we have electric machines in a variety of sizes and across multiple product lines available right now.”
In recent years, Volvo launched the EC18 Electric, ECR18 Electric and ECR25 Electric compact excavators and the L20 and L25 electric wheel loaders. These machines offer similar performance as their diesel counterparts but are well-suited for environments where emissions and noise
aren’t welcome. This would include residential neighbourhoods, indoor spaces, and night shifts.
In addition to those machines, the company also offers its DD25 Electric asphalt compactor, which has an operating weight of 5,899 pounds (narrow drum) or 6,140 pounds (wide drum) and a runtime of up to four hours.
Earlier this year at the Advanced Clean Transportation (ACT) Expo in Las Vegas, Volvo also announced that its EC230 Electric excavator was now commercially available in North America and introduced the PU130 and PU740 mobile charging units.
Developed by Volvo CE and Portable Electric, the PU130 is “a portable AC and DC fast charger for smaller machines,” says Gallant. “Using the DC fast charge plugs, the PU130 can bring a compact machine’s battery from empty to full in under an hour while also providing up to 40 kW of site
power … It will be available through the North American Volvo CE dealer network later this year.”
The PU750, which was developed by Utility Innovation Group (UIG) in cooperation with Volvo CE and Volvo Penta, is a transportable charging unit that can fastcharge larger equipment without a converter or secondary charger. The PU750 will be available next year.
Volvo says the PU150 and PU750 will work with most brands of EVs and electric heavy construction equipment.
Going forward, “Volvo CE’s goal is to electrify 35 per cent of our full product lineup by 2030 and to reach net-zero value chain greenhouse gas emissions by 2040,” states Gallant.
In 2022, John Deere pledged, in its own words, “to deliver 20+ electric and hybrid-electric [construction] models by 2026” in conjunction with the Wirtgen Group.
Since then, the company has introduced the E-Drive 744 and 824 X-Tier wheel loaders with the Wirtgen Group and is on track to fulfill its earlier promise, says Van Tine.
John Deere is currently working on several electric models, including the 145 X-Tier E-Power excavator, the 310 X-Tier E-Power backhoe and the 244 X-Tier E-Power compact wheel loader.
“The 145 X-Tier concept excavator is a demonstration of the future of John Deere excavators,” explains Van Tine. “Deere continues to test and develop the E-Power battery electric architecture and other innovative solutions so they can be scaled
across the line-up.”
The company is currently testing the 310 X-Tier E-Power backhoe and making design improvements along the way. The company is putting the 244 X-Tier E-Power compact wheel loader through its paces as well.
“The 244 X-Tier E-Power is also in [test stage]. It is performing well in a variety of applications and has demonstrated numerous performance benefits of a battery electric design in addition to being quiet with zero tailpipe emissions. More details on the 244 X will be released in the future,” says Van Tine.
Doosan Bobcat unveiled its T7X, the world’s first all-electric compact track loader, at the consumer technology and electronics trade show CES 2022 in Las Vegas. A year later, the company demonstrated the S7X, the world’s first all-electric skid steer loader, at CONEXPO-CON/AGG, also in Vegas. Currently, the company is working on a breakthrough all-electric, fully autonomous machine.
The T7X, which has been released commercially, offers quiet operation, no fumes, no hydraulics, and a 4.5-hour battery life. It also packs more power than a compact diesel track loader, says Honeyman.
“With a diesel machine, you have to idle in order to get the
engine at the proper RPM and to get the hydraulic system going. With an electric machine, there is no idle time and as soon as you hit the press to operate button, you essentially have the ability to have 100 per cent torque at any RPM or at no RPM,” he explains.
Thanks to the no-idling function, you only consume energy “when you’re actually moving the joysticks in the machine,” he says. The manufacturer says this means the T7X’s battery life is more than adequate for most applications.
The machine’s software-driven controls come with a few unique features, such as bucket shakeout. “You hit a button on the left joystick and it will violently shake the bucket so you get material out. And that’s simply software … You can’t do that on a diesel hydraulic machine that easily,” says Honeyman.
“Beast Mode” is another innovative joystick-based feature on the T7X. Once activated, it “puts the full current to the drive system … [This] allows you to take a 75 hp machine from a performance standpoint and put 125 hp to the drives instantaneously,” he explains. “If you’re going into a pile of dirt, or if you had a tough area you wanted to plow into, you could use that feature to get more power.”
The all-electric S7X has a 60.5-kWh lithium-ion battery capable of functioning for up to eight hours for some applications, electric drive motors, and requires minimal maintenance. It has not yet been released commercially.
In addition to those machines, Bobcat technicians continue to work on the Bobcat RogueX, a futuristic, all-electric, autonomous machine that resembles a track loader but is “in a category all its own,” states the company.
Containing a lithium-ion battery and an electric-drive system, the RogueX has no cab, no hydraulics, and produces no emissions. Taking the design even further, a new, enhanced iteration called RogueX2, remains in the conceptual stage… for now.
Case Construction Equipment recently launched the CX15EV electric mini-excavator and SL22EV electric small articulated loader on the market.
Meet the International ® S13 ® Integrated powertrain. Now available in the HX™ Series.
After revolutionizing highway driving in the LT ® and RH™ Series, the S13 Integrated is now ready for severe duty work in the HX Series. A huge step forward in performance, design, and operating economy, the S13 Integrated is the lightest 13L in North America. But it still brings 515 horsepower, 1,850 lb-ft of torque, and optional factory-installed PTOs. Not to mention simpler serviceability for more uptime. Now all that’s left to do is get to work.
Case’s first all-electric mini-excavator, the CX15EV is small but powerful. It weighs 3,186 pounds, with a transport length of 10 feet, five inches, and is “an ideal solution for indoor and outdoor jobsites where a minimal footprint is required,” says Lewis.
With a 21.5 kWh lithium-ion battery that lasts between four to eight hours, depending on work duties, the CX15EV is easily transportable, produces zero on-site emissions, makes minimal noise, and requires limited maintenance. Thanks to its diminutive size, the CX15EV can fit through narrow gates and doorways. Zero tail swing, short-tail and conventional swing designs are available. Case plans to put a new, larger CX25EV mini-excavator into production shortly.
The highly versatile SL22EV all-electric small articulated loader uses lithium-ion batteries with a nominal battery voltage of 48 volts. Compatible with over 100 Case attachments, the SL22EV generates zero emissions and little noise, making it a good choice for residential neighbourhoods or commercial spaces where high volumes and
exhaust fumes are frowned on.
The SL22EV boasts “an expected run time of five to six hours, with overnight charging using a 240V single phase connector, or rapid recharging in less than two hours with the optional fast charge,” says Lewis.
Case is also working on a newer, bigger CL36EV compact wheel loader. The CL36EV
“will complement the SL22EV, especially for contractors in need of greater performance capability or an upgraded cab environment in a larger machine,” says Lewis.
Nate Hendley is a freelance writer and author, and is a regular contributor to On-Site Magazine.
On behalf of Northbridge Insurance, we are honoured to be the sponsor of On-Site Magazine’s 2024 Top 40 Under 40 in Canadian Construction Celebration. This year has been a significant one for the construction industry, marked by growth and innovation. Keeping pace with these changes can be challenging, but the remarkable individuals in this year’s 40 Under 40 have not only adapted to these changes but have excelled beyond expectations.
At Northbridge, we are proud to celebrate this group of exceptional, progressive, and innovative young leaders who are at the forefront of the evolution of the construction industry in Canada. These individuals are not only shaping the future of the construction sector but are also deeply committed to nurturing the next generation of industry professionals.
Each of the nominees share some key common traits, such as operating ethically, fostering innovation, and leading by example. They represent companies involved in some of Canada’s largest and notable infrastructure and ICI projects, utilizing cutting-edge construction techniques and the latest technologies available to the construction sector. Their confidence in the future of our vibrant and diverse sector is inspiring, and we share that optimism.
We would also like to extend our sincerest appreciation and gratitude to everyone who took the time to recognize and nominate members of their organization or work communities, as well as the companies that provide these individuals with the opportunity to grow and excel in their roles.
A heartfelt congratulations to all who have been recognized. Northbridge Insurance sincerely thanks you for your contributions to the construction industry, which has spurred remarkable growth. We’re proud of everything you have achieved thus far, and excited to see what you will achieve in the future. We are committed to supporting the construction industry as a trusted insurance partner and are excited to contribute to building a safer and brighter future.
Sincerely,
Adam Collier Underwriting Director Northbridge Insurance
Since 2020, On-Site Magazine and SitePartners have been recognizing exceptional, progressive and innovative young leaders who are advancing the movement of construction in Canada. With this year’s fifth edition of the Top 40 Under 40 in Canadian Construction, we are pleased to recognize the following 40 talented individuals who are making their marks on the construction industry in Canada. From developing forward-thinking processes to ensuring that the generations following them will have the tools, knowledge and support they need to forge their own careers, these young professionals represent the best of the best, illustrating the great opportunities that exist in today’s construction sector.
ADAM LATTA Director, Field Operations
Magil Construction Canada Inc.
Over the course of 22 years in the construction industry, Adam Latta, director of field operations at Magil Construction Canada Inc., has carved out a remarkable career from the ground up. Starting as an apprentice carpenter in 2006, he steadily progressed through roles of general carpenter, carpenter foreman, asst. superintendent, superintendent, and field operations manager, becoming director in 2024. Adam has significantly contributed to such notable projects as Grand River Transit in the Waterloo Region, Erin Meadows Retirement Residence and the Hyundai L&C Canada Manufacturing Plant. With qualifications from Fanshawe College and Algonquin College, his leadership has been pivotal in overcoming project challenges, promoting EV initiatives, and advocating for women in construction. He is committed to mentorship, industry involvement, and community service, including volunteering with Habitat for Humanity and Million Dollar Smiles.
ALEX SCOPACASA Chief Operating Officer Fero
International
Alex Scopacasa is the co-founder and chief operating officer of Fero International Inc., a pioneering volumetric modular manufacturer. Instrumental in Fero’s rise, particularly during the COVID-19 pandemic, Alex played a crucial role in scaling the company’s workforce from two to over 65 employees and integrating operations at a sprawling 300,000 sq. ft. facility acquired in 2023. His leadership was pivotal in the development of Fero’s prototype modular medical unit, which was recognized with the Most Innovative Technology award at the Natural Disaster Innovation Awards. With a background in business administration and project management, Alex brings over a decade of experience in overseeing diverse operations, supply chain management, and industry advocacy through engagements like the Modular Building Institute. His commitment to operational excellence and innovation not only drives Fero’s success but also sets new standards in modular manufacturing, positioning him as a leader in the industry.
ALEXANDRE S. BOUCHER
President-General Manager
JCB Construction Canada
Alexandre S. Boucher is the president-general manager of JCB Construction Canada, a leading Quebec construction firm. Joining JCB as an estimator in 2011, he rose through the ranks to become president-general manager in 2023. Under his leadership, JCB manages over $150 million in revenues and 115 employees across Quebec and Ontario, achieving significant accolades such as the ACQ Excellence Builder award. Known for overseeing landmark projects like the Ring and the carbon-neutral Sainte-Anne Campus, Alexandre’s strategic vision has enhanced JCB’s profitability and expanded its training initiatives fourfold. Actively involved in industry organizations and within the ETS-Montreal, he champions innovation and sustainable development, exemplified by JCB’s pioneering use of trailblazing technology and equipment. Alexandre’s commitment to excellence and community involvement underscores his impact on both JCB and the construction industry at large.
CALEB PALAM
Project Director
Maple Reinders
Caleb Palam is the project director at Maple Reinders. Starting his career as a field coordinator, he ascended to his current position where he oversees major projects like the Royal B.C. Museum PARC Campus in Victoria. His leadership spans coast-tocoast projects, implementing best practices in a variety of markets including ICI, dams, water/wastewater and social infrastructure. Notably, Caleb pioneered a PPE recycling program during the pandemic, underscoring his commitment to sustainability and safety. With over 15 years in construction, he is committed to lifelong learning with industry certifications such as the GSC, NCSO and PMP. Actively involved in industry education, he advises George Brown College and the Toronto Construction Association, shaping curriculum and credential recognition. Caleb’s dedication to innovation and commu-
nity involvement continues to elevate Maple Reinders and set industry standards.
CAMERON ARCHER Director, Sales and Marketing
Orion Construction
Cameron Archer, director of sales and marketing at Orion Construction since 2022, has been pivotal in propelling the company’s growth and diversification. With over a decade in construction, Cameron has delivered over 1.5 million sq. ft. of real estate and managed 65 projects, exceeding $250 million in cumulative value. He has been key part of Orion’s award-winning performance, including being recognized as Canada’s Fastest Growing Company in 2022 by the Globe and Mail. A Red Seal millwright with extensive industry experience, Cameron blends practical expertise with strategic vision, exemplified by his leadership in sustainability initiatives and community engagement through Orion Building Futures.
Actively involved in industry advocacy and mentorship, he fosters innovation and community well-being, driving progressive changes across Metro Vancouver’s industrial development sector. His dedication to client satisfaction and community impact underscores his influence within Orion and the broader construction industry.
Partner
Singleton Urquhart
Reynolds Vogel
A good lawyer is invaluable in construction. Catherine Gleason-Mercier, partner at Singleton Urquhart Reynolds Vogel LLP, is a distinguished leader in its construction and infrastructure group and is renowned for her strategic counsel on complex disputes. With over a decade devoted to the construction industry, she has shaped pivotal cases, including disputes regarding major infrastructure projects in the country. A graduate
We
of McGill University with both an LLB and BCL, she is actively involved in industry associations and contributes extensively to construction law discourse through publications and presentations. Catherine’s leadership extends to mentoring junior lawyers, serving on committees for professional development and workplace conduct, and advocating for collaborative approaches in construction contracting. Her commitment to excellence and client advocacy has earned her recognition from Best Lawyers, Lexpert, Who’s Who Legal and Benchmark Litigation Canada, highlighting her impact as a trusted advisor and leader within the legal and construction communities.
CHELSEA A. WILSON Partner
Dentons
Chelsea Wilson specializes in construction and infrastructure disputes, providing strategic
advice on negligence, warranty, delay and defects claims, and builders lien issues. Recognized as one of The Best Lawyers in Canada – Ones to Watch from 2021 to 2024, Chelsea’s expertise in builders lien law has led her to publish numerous resources and speak at industry events. Her notable achievements include leading negotiations for a $25 million defects and delays dispute in B.C. and handling a nine-figure fraud and misrepresentation claim. Wilson is a member of the law societies of Yukon, British Columbia and Alberta, and a partner at Dentons’ Vancouver office within the construction, infrastructure and PPP, and litigation and dispute resolution practice groups. With extensive courtroom experience and a commitment to mentoring young lawyers, Chelsea is also an early adopter of legal AI technologies. Her leadership in educational initiatives and thought leadership further cements her reputation as an authority in builders lien law, ensuring the success of her clients and colleagues alike.
For 40 years, JCB Construction Canada has helped major clients build their projects, solve their challenges and propel their growth.
Let’s raise your ambitions off the ground!
Expansion
CHRIS SMITH Construction Risk Manager
PCL Construction
Chris Smith is a construction risk manager for PCL
Constructors Canada Inc., with a strong portfolio of complex project pursuits, especially Public-Private Partnership agreements. Since joining PCL in 2012, Chris has played a key role in acquiring over $8.6 billion in projects, including the billion-dollar LAX ConRAC Facility and healthcare megaprojects. With 19 years of industry experience in Canada and Australia, and holding a bachelor of applied science in construction management and economics from Curtin University, a diploma of building from TAFE Western Australia, and Gold Seal Certified Estimator accreditation, Chris has progressed from estimator to design manager to his current
Congratulations, Dan! Being awarded the Top 40 Under 40 in Canadian Construction is a remarkable achievement and a testament to your outstanding contributions and leadership in the industry.
role. He excels in cost estimation, risk management, and leading multidisciplinary teams. Known for his meticulous attention to detail and superior client service, Chris is lauded for his leadership and ability to distill complex information into actionable insights, setting PCL up for success on its most challenging projects.
DAN LEWIS Chief Operating Officer Bird Mechanical Ltd.
Before becoming chief operating officer at Bird Mechanical Ltd.,
Dan Lewis showcased his technical expertise and dedication through various roles. He was instrumental in expanding operations into Atlantic Canada, supporting major ongoing projects such as the $74.4 Million Northside Health Centre mechanical rough-ins and interior fit-up in Nova Scotia. Dan managed company acquisitions, including his key
role as president at Tin Knockers Custom, where he led that company’s integration into Bird Mechanical Ltd., boosting Bird’s capabilities and growth. His journey from project manager to executive vice-president, achieving his P.Eng designation, and now chief operating officer, underscores his skills and commitment. He has overseen major projects such as the $19.5 Million Peel Region HVAC Redevelopment Project and the $15 Million E.C. Drury Mechanical and Electrical Upgrades Project. Dan also mentors employees, supports children’s charities, and leads environmental initiatives, demonstrating his dedication to both industry and community.
JIM BLAIR Vice-President –Business Development Michael+Clark Construction
Jim Blair is a trailblazer in the construction
industry. He serves as a vice-president at Michael+Clark Construction, bringing 15+ years of expertise in delivering ICI projects with values ranging from $1 million to over $100 million. As a certified Construction Engineering Technologist (CET) and Gold Seal certified in project management, Jim has successfully led projects like Conestoga College’s Skilled Trade Campus and several Maple Lodge Farms expansions, contributing to over $700 million in projects over the past 15 years, all while sitting on several boards and committees throughout the community. Recognized as a 40 Under 40 Construction Champion, Jim has played a pivotal role in corporate growth and expansion of the companies from $10 million to $150 million in annual revenue, championing innovations like VDC/BIM and construction AI. As the youngest chairman in the Ontario General Contractors Association’s history and an active industry leader, Jim is committed to mentoring and advancing the construction industry.
PCL Construction congratulates Chris Smith on being named to the On-Site Magazine + SitePartners Top 40 Under 40 in Canadian Construction list. His leadership and unwavering commitment to excellence ensures PCL’s continued success atop Canada’s construction industry.
JOEL GOY
Area
Manager, Electrical and Instrumentation
Strike Group
Joel Goy is a seasoned leader in the construction industry, currently serving as the Saskatchewan electrical and instrumentation area manager at Strike Group. Holding a B.Sc. in electrical engineering from the University of Saskatchewan, Joel brings over 15 years of expertise to the table, having managed electrical and instrumentation projects up to $40 million. His credentials include a P.Eng designation and PMP certification. Promoted to area manager in 2020, Joel has consistently demonstrated his ability to lead high-performing teams. As president of the Project Management Institute of North Saskatchewan Chapter, he oversees programming for over 500 members, further showcasing his dedication to professional development. Committed to mentorship and community involvement, Joel also actively contributes to advancing STEM education and fostering industry innovation through APEGS and the IEEE.
KAYLA MURRELL Architect
WZMH Architects
Kayla Murrell, an architect with WZMH Architects, is known for her expertise in retail architecture and construction. Since joining the firm in 2019, she has played a key role in projects totaling over 2 million square feet and valued at nearly $500 million. Regarded by her peers for her technical and interpersonal skills, her notable projects include Consilium Place, Lime Ridge Mall and Promenade Mall. Kayla’s previous focus on healthcare architecture includes significant contributions to Oakville Trafalgar Memorial Hospital and ErinoakKids. Licensed as an OAA architect in 2023, she is also a member of RAIC and a dedicated mentor. As a leader in diversity, equity, and inclusion, Kayla co-founded
the Black Architects and Interior Designers Association and spearheaded WZMH’s Mentorship & Education Committee. She has received prestigious awards like the OAA Guild Medal and RAIC Honour Roll. Through her innovative approach and commitment to mentorship, Kayla significantly impacts the architecture, engineering and construction industry.
Infrastructure Health & Safety Manager
NorLand Limited
Krista Chisholm is a dynamic force in the construction industry, driving safety as the infrastructure health and safety manager at NorLand Limited. With a Canadian Registered Safety Professional designation, she leads a team overseeing safety for more than 800 employees, ensuring compliance and championing innovative safety measures. Since joining NorLand in 2020, Krista has overhauled its health and safety program and introduced digital software that significantly improves the visibility of key statistics, helps drive consistent improvement and delivers results, including zero recordable injuries for the Broadway Subway Project. With a B.Sc. (Hons) in Biomedical Sciences from the University of Aberdeen, Krista discovered her passion for health and safety after rescuing and resuscitating someone after an incident. As an advocate for mental health, Krista introduced the Mental Health Stewards course and proudly supports the LGBTQ2 community. Krista’s dedication to health and safety makes her an invaluable asset to NorLand and the construction industry.
KYLE RAUSCHER Director of Finance Operations
Ledcor
As a director of finance operations at Ledcor, Kyle Rauscher’s journey in construction finance showcases exemplary leadership and innovation. Kyle over-
sees a team of more than 40 professionals, managing a portfolio of more than 25 projects valued at over $6 billion. Since joining Ledcor in 2016, Kyle has quickly advanced on his career path, reflecting the value his expertise adds to the team. With a bachelor of commerce from the University of Victoria, supplemented by continual industry focused training, Kyle brings more than 20 years of industry experience to his role. Notable achievements include supporting the negotiation of key client contracts, spearheading tax credit collections, and developing a financial framework for joint venture agreements. His contributions extend to refreshing financial processes and transitioning teams to remote models that significantly enhance efficiency. His dedication to mentorship and industry involvement further underscore his commitment to excellence and innovation.
LYNDSEY SHAW
Sr. Project
Manager
Ledcor Construction Limited
Lyndsey Shaw, senior project manager at Ledcor Construction Limited, knows how to get things done under challenging circumstances. Working in the construction industry for 13 years, Lyndsey excels in managing high-stakes projects, including a multimillion-dollar hospital in northern Saskatchewan that is vital for local communities. Her leadership shines through her skillful management of challenges, including resource scarcity and remote locations, ensuring projects remain on track to meet critical deadlines. During COVID-19, despite the unprecedented challenges, her team worked closely with the health, safety and environment teams to implement the use of QR codes for daily health questionaries. This ensured not only the safety of the workers on-site, but also the timely completion of a high-rise project without downtime. Her advocacy for inclusivity extends beyond project management, with initiatives like increasing baby-changing stations and converting single-compartment washrooms
to unisex facilities. Lyndsey’s commitment to mentoring and community involvement, alongside her professional achievements, underscore her dedication to advancing the construction industry and fostering a safe and inclusive work environment.
MALLORY ZIMMERMAN
Project Director
Novacom Buliding Partners
Mallory Zimmerman, project director at Novacom Building Partners, is a leading force in construction. Renowned for her transformative impact on complex projects, she was instrumental in the preconstruction of the Deloitte Summit building and managing the LEED Platinum-certified Emily Carr University of Art and Design P3 project. Her project management experience includes overseeing a $10-million design/build maintenance facility and a
sewer upgrade in New Westminster, B.C. Holding high-level certifications like P.Eng. and Certified Passive House Consultant, Zimmerman excels in various contract types, from lump sum to public-private-partnerships. Her leadership extends beyond projects, as she mentors women in infrastructure through the weWIN program and contributes to industry associations and charitable causes. Her advocacy for gender diversity and work with Engineers Without Borders underscore her commitment to advancing industry standards and global welfare.
MANIK RAINA Vice-President, Legal Services
EllisDon
Manik Raina is a pivotal figure in EllisDon’s legal team. Utilizing his expertise in complex infrastructure procurements and financings, Manik has
been critical to EllisDon’s successful pursuit of some of North America’s largest public infrastructure projects, including the South Niagara Hospital project and the Trillium Health Partners Queensway Health Centre redevelopment project. Rising from legal counsel to the company’s vice-president of legal services in just six years, Manik’s contributions were crucial to EllisDon’s legal department winning the Canadian Law Award for Construction, Infrastructure, and Transportation Law Department of the Year in 2022. His qualifications include a bachelor of medical sciences and juris doctor from Western University, coupled with 10 years of experience in infrastructure and real estate law. Known for his strong business acumen and collaborative spirit, Manik is celebrated for his influential role in shaping industry standards. His impact extends beyond EllisDon, driving innovative solutions and improving risk allocation frameworks in the construction sector.
Lyndsey Shaw Senior Project Manager, Construction
MARK
GAGLIONE Director, Building & Material Sciences
EllisDon
Mark Gaglione, director of building and material sciences at EllisDon, is a leading figure in advancing emerging construction technology in Canada. With a background in engineering from the University of Toronto, Mark has been pivotal in pioneering sustainable building practices, notably mass timber, through the development of the Hybrid Timber Floor System and has played a key role in EllisDon’s various ongoing low-carbon research initiatives. His leadership in projects like the Humber Cultural Hub and the PNE Amphitheatre underscores his role in transforming construction technologies. His contributions to the field have been recognized with the Vancouver Regional Construction Association’s Innovation & Productivity Award in 2023. Mark is an active participant at industry events and dedicates time to guiding new talent in the industry. His forward-thinking approach and focus on sustainable materials continue to influence the evolution of Canada’s construction sector.
MARK SCHILDROTH Director, Corporate Affairs
Aecon
Mark Schildroth, director of corporate affairs at Aecon, excels in stakeholder engagement, public relations, reputation management and crisis communications. Over his eight years with the company, he has significantly improved digital media performance, spearheaded communications on major infrastructure projects, driven Aecon’s Project Communications Centre of Excellence, as well as the company’s Emergency Management Communications Committee. He holds a master of corporate communications and provincial crisis management credentials and has extensive experience working in corporate
and operational construction. His leadership is marked by his ability to foster team growth, implement innovative processes and drive major project communications. His communications work has spanned programs focusing on talent acquisition, diversity and inclusion, sustainability, investor relations, and community engagement, including strategies to reach underrepresented talent through Aecon Women in Trades and communications on the Indigenous Reconciliation Action Plan steering committee. His dedication and vision make him pivotal in enhancing Aecon’s communications strategies and promoting industry excellence.
MATTHEW PEDROS
CEO/Project Manager
Elgin Contracting and Restoration
Matthew Pedros, CEO and project manager at Elgin Contracting and Restoration Ltd., has advanced from estimator and project coordinator right to the top of the company, overseeing all company operations. With a diploma in architectural technology, a P.GSC in project management, and LEED AP credentials, he brings 14 years of experience to the role. Matthew leads the firm’s largest projects, implements innovative project management and safety software, and fosters strong relationships with subtrades. His leadership is characterized by promoting work-life balance, encouraging continuous education, and prioritizing safety. Active in industry associations and local networks, Matthew is dedicated to exploring new business avenues and solving complex problems, making him a respected and effective leader in his field.
MIKE TRACEY Vice-President, Infrastructure Markets and Strategy
Kiewit
Mike Tracey, vice-president of infrastructure markets and strategy at Kiewit, is a driving force behind the company’s growth across
North America. Since joining Kiewit in 2009, Mike has spearheaded a shift in major infrastructure project delivery, pioneering innovative delivery models such as Integrated Project Delivery and Alliance contracting on projects like the Waaban Crossing and Toronto Union Station Enhancement. His leadership has been instrumental in building a collaborative culture and setting new industry standards for high performing teams. With a focus on strategic growth, he has overseen billions in added backlog in Canada and leads a team of over 120. His commitment extends beyond technical expertise to mentorship and community involvement, advocating for diversity, mental health, and industry best practices. Mike’s transformative impact on the construction sector and his dedication to fostering future leaders positions him as a standout candidate for industry recognition.
MICHAEL
Owner
and
BEATON
President
Centurion Contracting Success began young for Michael Beaton. Launching Centurion Contracting at just 23, he transformed the company into a leading restoration subcontractor with over 120 employees. In 2021, he co-founded The Advantage One Group (AD1), which now includes six companies and employs more than 250 people. Michael’s innovative leadership style has helped to expand the group of companies annually. A Red Seal carpenter with more than 20 years of experience, Michael is known for his problem-solving skills and a strong commitment to his team and community. He established the 20-Year Kwantlen College Endowment Annual Scholarship for Leadership in Construction and supports various local initiatives. His vision to integrate multiple trades under one roof and his dedication to developing future talent exemplify his significant impact on the construction industry.
MOHAMED ATIA
Director, Project Controls
Aecon
Mohamed Atia, director of project controls at Aecon, is renowned for his expertise in managing complex, multi-billion-dollar infrastructure projects globally. His notable projects include the Doha Metro, Egypt’s National Railway Modernization, and the National Railway Program of UAE – Etihad Rail. As a Chartered Project Management Professional with a robust background in civil engineering and construction project management, Mohamed has pioneered innovative project control methods and tools. His leadership has been instrumental in successfully establishing the Project Controls and Estimating teams, currently delivering the Development Phase of the Scarborough Transit Extension—the first Progressive Design and Build collaborative contract for Metrolinx. Beyond his proj-
ect achievements, Mohamed is dedicated to mentoring future leaders and contributing to industry advancements through publications and speaking engagements. His unwavering commitment to excellence and innovation, coupled with his significant contributions to both his field and the community, make him a distinguished candidate for recognition.
MOHAMMAD FAKOOR
Associate RJC Engineers
Mohammad Fakoor, associate at RJC Engineers, is leading the charge in building performance, decarbonization and energy efficiency. Spearheading major projects like Vancouver Community College’s Centre for Clean Energy and Automotive Innovation and UBC Gateway, he excels in integrating advanced carbon reduction techniques and mass-timber designs. With a PhD in applied science from Simon Fraser University
and over 14 years in the industry, Fakoor has transformed energy modelling practices and championed tools like the RJC Aspire carbon calculator. His leadership in projects such as George Pringle Secondary School demonstrates his commitment to sustainability and innovative problem-solving. Beyond his engineering role, Fakoor is a dedicated academic, guest lecturer and mentor, significantly contributing to industry knowledge and development. His relentless pursuit of net-zero goals and active involvement in academia and industry associations highlight his exceptional impact on the construction sector.
NADIA TODOROVA Executive Director RCCAO
Nadia Todorova is a leading force in Ontario’s infrastructure and construction sectors, heading the Residential and Civil Construc-
tion Alliance of Ontario (RCCAO) as executive director. In the first decade of her career, Nadia has significantly advanced critical infrastructure projects like the Bradford Bypass and Highway 413 through strategic advocacy and collaboration. Her leadership extends across multiple roles, including chairing the Labour Management Immigration Coalition and serving on the executive committees of CDAO and OCCA. Nadia’s expertise in government relations, public policy and data-driven advocacy has reshaped infrastructure policy and communication in Ontario. Known for her commitment to mentorship and supporting women in construction, she actively fosters a supportive environment for emerging female leaders. Nadia’s professional integrity, strategic vision, and advocacy have positioned her as a pivotal figure in the industry, driving meaningful progress and championing both infrastructure development and advancing the growth of women throughout the sector.
Managing Director, Infrastructure and Energy Transition
Desjardins
Olivier Lacaille, managing director of infrastructure and energy transition at Desjardins, has helped redefined the landscape of Canadian infrastructure finance with his visionary leadership. From orchestrating the successful financing of monumental projects like the new Samuel de Champlain Bridge and Eglinton Light Rail Train to spearheading cutting-edge energy transition initiatives such as the Apuiat Wind Farm, Olivier has consistently set benchmarks in the industry. His extensive experience spans large-scale PPP transactions and transformative projects, including hospitals and renewable energy ventures. With a CFA designation and advanced degrees in economics, finance and
financial markets, he excels in integrating sustainable finance strategies and engaging First Nations communities. His impact on infrastructure and energy transition is profound, driving innovation and shaping the future of Canadian construction.
OSAMA MOIN
Lead, Civil Engineer
RAM
Osama Moin, lead civil engineer at RAM, is elevating the landscape of civil engineering with his visionary leadership and exceptional accomplishments. Starting as an intermediate project engineer in 2019 and swiftly rising to civil engineering lead, Osama has revitalized RAM’s civil engineering department, significantly increasing both annual revenues and project margins within the company. His negotiation prowess was pivotal in advancing a major federal infrastructure project, breaking a six-year
We’re Aecon Proud of our appointees to the 40 under 40 list:
Mohamed Atia
Sofiane Mesbahi
Mark Schildroth
Congratulations to all the esteemed nominees!
Building What Matters to Enable Future Generations to Thrive.
As a broker recognized for excellence, we proudly salute and applaud those who strive to achieve the same high st a ndards.
American Global is a vibrant, values-driven community with an exceptional team. Together, we’re transforming the construction industry and revolutionizing the role of broker. Whether you’re a colleague or our client, we’re demonstrating why it’s time to expect more. Expect more from your broker.
100% Privately Owned & Solely Construction Focused
• Non-Traditional Resources with Deep Industry Expertise
• Local Presence with a Global Platform
• Collaboration That Drives True Innovation
• P3 Awards: 2023 Insurance/Risk Advisor of the Year
•
• 5X Winner: ‘Best Places to Work’ by Business Insurance
www.americanglobal.ca
deadlock with local municipalities. With a decade of experience and a bachelor’s in civil engineering from the University of British Columbia, Osama has reshaped RAM’s strategic focus, leading to substantial new project wins and significant improvements in project outcomes. His innovative approach includes streamlining processes through custom scripts and leading RAM’s Innovation Council to enhance internal practices. Actively involved in mentoring and industry engagement, he supports emerging engineers and contributes to a number of charitable initiatives, underscoring his commitment to both professional excellence and community impact.
RAVINDER SANDHU
General Manager, Lafarge Metro Vancouver Ready Mix
Lafarge Canada
Ravinder Sandhu stands as a solid
figure in the concrete industry, having transformed Lafarge Metro Vancouver Ready Mix through his visionary leadership and commitment to innovation. As general manager, Ravinder has overseen the supply of concrete for major projects like the Canada Line Skytrain and the Port Mann Bridge, managing an extensive network of plants and personnel. His strategic initiatives, including the consolidation of dispatch offices and the implementation of sustainability measures, have led to a seven per cent increase in plant capacities and significant reductions in energy and water usage. His dedication to continuous improvement is evident in his adoption of Kaizen principles and digital tools, which have optimized operations and boosted profitability. With 17 years at Lafarge and a strong track record in both industry advancement and community engagement, Ravinder exemplifies leadership that drives both business success and social responsibility.
RENATO SOUZA Vice-President, Construction Technology & Innovation
Axiom Builders
Renato Souza is revolutionizing the construction technology landscape with his dynamic approach and innovative spirit. As the vice-president of construction technology and innovation at Axiom Builders, Souza has been instrumental in advancing the use of technology in construction, supporting a broad range of projects from concrete towers to mass timber developments. His leadership has driven significant achievements, including winning the BIM Hero Award and leading Axiom Builders to be named 2023 Partner of the Year by Suffolk Technologies. His commitment to technology and mentorship, combined with his role in expanding and guiding a rapidly growing team, showcases his dedication to pushing
on being featured in
the boundaries of what’s possible in the construction industry.
ROBERT JACKSON Partner
Fast + Epp
Robert Jackson is known in his industry of structural engineering for his groundbreaking work in hybrid timber structures. As a partner at Fast + Epp, Robert has quickly ascended through the ranks, earning accolades for his designs and significant contributions to landmark projects such as the UBC TallWood House and The Hive. His expertise in pioneering mass timber structures and seismic technology has earned him recognition as a leader in his field. Robert’s commitment to advancing engineering through research, publications, and the establishment of the Concept Lab at Fast + Epp underscores a dedication to exploration in structural design. With a
career marked by exceptional achievements and a profound impact on the industry, Robert continues to inspire and elevate the standards of engineering excellence.
SAM JOHNSON
Director, Development
Graham Capital, A Graham Group Company
With a lengthy track record of success, Sam Johnson is a standout leader in the construction industry. Serving as the director of development at Graham Capital with over 15 years of experience, Sam has led significant infrastructure projects across North America, including the innovative 100 Street Funicular, the Groat Road Bridges and Road Renewal Project, and the Wetaskiwin Wastewater Treatment Facility, all in Alberta. His expertise spans complex transportation infrastructure, water and wastewater facilities, social infrastructure, and heavy
civil projects. His leadership is evident in his strategic contributions to Graham’s business planning and expansion efforts, notably contributing to the firm’s positioning in priority markets. His commitment to mentoring future leaders and his role in advancing construction technology and financing models highlight his dedication to industry innovation and excellence.
SARAH REEVES Director, Geocycle Canada
Lafarge Canada
Sarah Reeves is the director of Geocycle Canada at Lafarge Canada Inc., where she drives sustainability by managing waste diversion projects that reduce landfill use and cut carbon emissions. Starting her career in 2006 with her family’s trucking business and later working in Zambia, Sarah joined Lafarge in 2011. She advanced from administrative roles
Renato Souza Vice President, Construction Technology & Innovation
Builders proudly congratulates Renato Souza for being recognized on the Top 40 Under 40 list for his contributions to advancing the use of technology in construction.
for this award.
to collaborating on cutting-edge projects, including North America’s first Ductal project delivered via RMX truck and Brock Commons at UBC. Under her leadership, Geocycle focuses on circular solutions, turning waste into alternative fuels and raw materials for Lafarge’s cement kilns. Sarah is also a passionate advocate for women in construction and mentors young professionals through Lafarge’s leadership programs. Her commitment to diversity and sustainability has shaped high-performing teams and innovative strategies, aligning with Lafarge’s vision for a sustainable future.
SCOTT TAYLOR
Western Canada
Commercial Manager
Kiewit
Scott Taylor is a transformative force in Western Canada’s construc-
tion landscape, wielding 16 years of expertise to lead Kiewit’s most ambitious civil infrastructure and design-build projects. As the Western Canada commercial manager, he oversees major initiatives like the Port Mann Highway 1 Improvement and the Turcot Design-Build, driving innovation and excellence across the region. Scott’s strategic vision and leadership extend to shaping Kiewit’s business plan and regional strategy. His impactful projects, including the Big Bar Fish Passage, demonstrate his ability to set industry benchmarks and enhance community ties. Beyond his professional achievements, Scott actively supports local schools and charities, embodying a commitment to both quality and community. His role in engineering, project controls, and business strategy solidifies his status as a pivotal figure in advancing Kiewit’s operations and upholding high industry standards.
SOFIANE MESBAHI
IDD Director
Aecon Infrastructure
Sofiane Mesbahi is revolutionizing digital delivery at Aecon Infrastructure with his inventive approach and hands-on leadership. As IDD director, he expertly navigates BIM, GIS, document control, and data analytics, driving efficiency and innovation across projects. Sofiane’s forward-thinking strategies, like his pioneering automated application for model data integration and his solutions for augmented field data capture and analysis, are setting new standards in the industry. An advocate for diversity and empowerment, he leads a team where gender equality is a core value. Beyond his role at Aecon, Sofiane actively contributes to the development of
24_007772_OnSite_Magazine_SEP_CN Mod: August 16, 2024 9:31 AM Print: 08/16/24 page 1 v2.5
industry standards and software advancements, collaborating with major developers and sharing insights through platforms like BIMpedia.org. His dedication to excellence and supportive leadership style not only enhances project outcomes but also fosters a positive and inclusive work environment, making him a standout figure in the field.
Director, Maintenance and Turnarounds
Flint
Taylor Brookes, director of maintenance and turnarounds at Flint, boasts over 20 years of experience in maintenance, construction, and turnaround operations. Rising from tradesperson to director, Taylor founded Flint’s Specialty Services Division and established a best-in-
class turnaround program, achieving consistent growth and leading over 30 large-scale turnaround events in 2022. His strategic leadership was crucial during Flint’s largest turnaround season in 2024. Taylor’s contributions include pioneering advancements in turnaround methodologies, implementing a continuous improvement framework, and optimizing workforce utilization. Actively involved in community initiatives and industry training programs, his blend of technical expertise, innovation and leadership has positioned Flint as a leader in the industry.
THERON DAVIS
Senior Associate Borden Ladner Gervais LLP
Theron Davis, senior associate at Borden Ladner Gervais LLP, holds a BA from St. Francis Xavier Univer-
Graham congratulates Sam Johnson for being recognized as a Top 40 Under 40 in Canadian Construction for 2024.
Johnson Director, Development Graham Capital
sity, a master’s from the University of Calgary, and a JD from Dalhousie University. Awarded the Robert E. Bamford Memorial Award and Alistair Fraser Award in Commercial Law, Theron specializes in construction law, focusing on drafting and negotiating contracts and advising on risk management. With experience as a project manager, he supports clients from project inception to completion, working on innovative project delivery models and representing clients in disputes. He also offers his expertise to aspiring lawyers. Theron is a sessional lecturer at the University of Calgary, leads training programs for incoming lawyers at his firm, mentors associates, and contributes prolifically to industry literature. His involvement includes pro bono work and community initiatives, highlighting his dedication to both professional excellence and social responsibility.
TRAVIS PARKER
Principal & Engineer
co-elevate, The Engineering Group
Travis Parker, principal and engineer at co-elevate, has significantly grown the company from nine employees and $1 million in revenue to 38 employees and revenues greater than $6 million. With a bachelor of engineering science from Western University and professional engineer registration in Ontario and Nunavut, Travis has been instrumental in numerous prominent projects over the past 15 years, including those using advanced materials like mass timber. In less than five years, his leadership has more than sextupled the company’s success while innovating with a new work culture focusing on employee well-being, limiting overtime, and implementing agile project delivery, reducing staff stress and achieving zero turnover in nearly two years. Active with the LDCA and local engineering chapters, Travis champions an employee-centric agenda. His remarkable achievements and compassionate leadership make him a standout figure in the industry.
VINCENT DAVENPORT
Director, Building & Material Sciences
EllisDon
Vincent Davenport, director of building and material sciences at EllisDon, has progressed from intern to a pivotal role, emphasizing emerging construction technologies and reducing carbon footprints. With over 14 years in the industry, Vincent has led innovative projects like the Centennial College A-Building Expansion, Ontario’s first large-scale mass timber post-secondary building. Co-developing the Hybrid Timber Floor System, he won the 2023 Vancouver Regional Construction Association’s Innovation & Productivity Award. His leadership in mass timber design and low carbon research and development has positioned EllisDon as a leader in sustainable construction. His technical
expertise, mentorship, and commitment to environmental stewardship drive his impactful contributions to the industry.
WAYNE TAN
MEP Manager
Canadian Turner
Construction Company
Wayne Tan is the MEP department manger at Turner Vancouver, where he shapes the company’s strategic approach to MEP construction. With 15 years of experience, and a robust mechanical engineering and construction management educational background, Wayne offers a unique perspective thru his multi-faceted roles as a consultant, HVAC manufacturer’s representative, and mechanical and electrical project manager. Wayne’s portfolio spans over $500 million of construction projects, from tenant improvements to turnkey healthcare projects. His projects ensure the same high standard and successful outcomes through his leadership in quality assurance, safety and effective project management. Notable projects include the Amazon Post Redevelopment, VGH JR Segal Health Centre and Red Fish Healing Centre. Currently, he focuses on advancing Turner’s business by implementing MEP industry advancement, sustainability, and technology integration. Active in professional associations like VRCA and ASHRAE, Wayne promotes diversity and mentorship in construction. Recognized for his integrity, teamwork, and commitment, he is a respected leader in Canadian construction industry.
ZAIN JESSANI
Vice-President, Project Management and Business Development
SEMA Railway Structures Inc.
Zain Jessani, vice-president of project management and business development at SEMA Railway Structures Inc., excels in managing railway bridge repair and rehabilitation projects, notably with Metrolinx across the Greater Toronto Area. With a bachelor of applied science in
environmental engineering, P.Eng. designation, and project management certification, Zain leads a team of 10 project managers and coordinators, fostering a culture of continuous improvement. His innovative project cost reporting methodology has significantly boosted company profitability. Zain’s systematic approach ensures the efficient delivery of complex railway work blocks within tight timelines. Beyond his professional role, Zain is the national vicechair for donor services at Aga Khan Foundation Canada, actively volunteering and training others for the World Partnership Walk. His dedication to mentorship, safety, and efficiency, coupled with his significant industry impact, underscores his outstanding leadership and makes him a force for good in Canadian construction.
It would have been impossible to put together this fifth edition of the Top 40 Under 40 in Canadian Construction without the support, and time, provided by our panel of judges. The teams at On-Site and SitePartners would like to thank: Ashvin Ghurburrun – Ashvin Ghurburrun is a senior project manager for civil projects with PCL. He joined the 40 Under 40 in Canadian Construction in 2023.
Brandon Bird– Brandon Bird is the CEO of Bird Mechanical Ltd. He was recognized as a member of the 40 Under 40 in 2023.
Jesse Unke – President and CEO of Maven Consulting Limited, Jesse was recognized in the inaugural edition of our 40 Under 40 in Canadian Construction program in 2020.
Lewis Cowan – Lewis Cowan is the president of BDA Inc. and is the pastchair of the Ontario General Contractors Association.
Taylor Lefebre – Taylor Lefebre is the director of quality and production for Eastern Canada at Green Infrastructure Partners Inc. Taylor became a member of the 40 Under 40 in Canadian Construction last year.
Vincent Davenport Director, Building & Material Sciences
At EllisDon, our values drive innovation and our culture breeds excellence, shaping the best in the industry. We proudly celebrate our people who exemplify these ideals and lead the way forward. Congratulations to those recognized by On-Site Magazine's Top 40 Under 40 Awards.
Gaglione Director, Building & Material Sciences
Manik Raina Vice President, Legal Services
From digitizing blueprints to machine learning, and modular components to carbon reduction, our 40 Under 40 alumni shared insights into the evolution of the sector.
BY ADAM FREILL
This year’s 40 Under 40 in Canadian Construction Symposium, held online on August 27, provided a platform for our 40 Under 40 alumni to put a spotlight on the use of new materials, processes and technologies within Canada’s construction sector. The discussions centred on how digital and product technologies are changing the face of the sector, and how the industry is riding the next wave that is driving productivity forward.
Keynote speaker Hammad Chaudhry, who was recognized as a 40 Under 40 honouree in 2022, discussed the technological revolution that is underway in the sector, with a look at some of the steps within the industry that have brought us to today’s use of cutting-edge tools and systems. Chaudhry, the vice-president of innovation and construction technology at EllisDon, noted that we appear to be entering a sixth wave of innovation-driven productivity that has its roots in the first wave of the industrial revolution.
He explained that the fifth wave, the digital revolution, has consumed the past 20 to 30 years, bringing significant changes as computers tackled many manual processes, saving time and energy.
“You could argue the sixth wave is among us now with artificial intelligence, machine learning, computer vision, connected devices, IoT, the clean tech revolution, robotics and drones,” he explained. “All of these things are posing a new wave of innovation that could unlock economic growth in a way that we’ve seen with the past waves.”
Walking attendees through some of the more notable innovations that have driven the construction sector forward, he pointed at hydraulics entering the equipment universe in the 1960s, changes to materials in the ’70s, and then computers and software from the ’80s and through to the early 2000s. The next advance, beyond Software As A Service (SAAS), he explained, is the confluence of systems and technol-
ogies, with advanced tools being able to provide insights and predictions based on this computer learning.
“Before, with your normal time-lapse camera, your drone, your laser scanner, 360-photo, they wouldn’t really be overlapping. They’re separate technologies and tools. But now, the way that the industry is moving with laser scanning and scan-to-BIM process, we’re seeing a convergence,” he said. “Artificial intelligence tools like Builddots are letting us not only do the capture, but to overlay the model, bring in our schedule and as-built information, and let the AI do a comparison through computer vision.”
This makes it easier to see if a project is on schedule, or if changes were made to a plan, which he noted is a significant departure from the days of hand-drawn blueprints.
“If you look at drafting originally with pen and paper, every line that you would make, you would think very deeply about. If I ripped that sheet of paper that I was drafting on, I would have to redo the entire sheet,” he said. “With BIM, you’re getting these cool 3D models that have a lot of information. You can use them for everything from logistics scheduling to fabrication and quantities.
“Our industry has been innovative… It’s remarkable to see things like BIM, VDC,
sensors, IoT, VR, drones and robotics, all within the past 20 years,” said Chaudhry. “And there’s been a lot of innovation when you think about prefab modular, using renewables, and the focus towards sustainability and new materials as well.”
Those topics were discussed in more detail with the event’s panel discussion, which featured 40 Under 40 alumni Dan Bockstael of Bockstael Construction, Jeff Murphy of PCL, Andrew Neill of ANC Group of Companies, and Jesse Unke of Maven Consulting Limited.
One of the generational shifts that’s underway, said the panel, is a movement to more collaboration, regardless of the delivery model in play.
“Having team members that have experience in executing these contracts all around the table is important, and can lead to better outcomes on projects,” said Unke.
“To me, it’s changed almost everything, processes, technology, tool structures, arrangements,” added Murphy. “They’ve all changed pretty dramatically with the common theme of increased collaboration.”
These collaboration efforts offer a lot of gains when the right people are engaged, explained Bockstael, who used the example of being able to evaluate options and adjust components impacting, for example, plumbing and heating systems prior to work starting. “As soon as you go past schematic design, it becomes really costly or cumbersome to change those, so when you get someone at the table that can really evaluate
those options and figure out which one is the best fit for that specific project, there’s a lot of value there,” he said.
Rethinking methods to gain efficiencies is alive in other ways as well, such as with the use of modular components.
“A volumetric, modular unit will come with every finish, all your drywall, even furniture in them, potentially,” said Neill. “We’ve done projects where we’ve actually had the beds, the chairs and the desks in the units in our factory, and we’ll ship them to the site and put them in place with a crane.” These kinds of large block-style components lend themselves well for builds with highly repeatable units, such as with hospitals and hotels, but prefabrication can bring efficiencies for smaller assemblies as well. Where floorplans change from storey to storey, some prefabrication of wall assemblies and other components is often possible.
Of course, technology has been the biggest game-changer for the industry over the past decade.
“What amazes me, excites me, what I’m passionate about in terms of technology is, is those tools that can help make us better builders,” said Murphy. I’d argue we’ve grown more in the last 10 years, than the last 100. The impact of the broad term of technology has been very significant in construction and that pace of change over the last five years has been remarkable.”
These technologies are ranging from drones on sites, to scanners and software to build 3D models, and even to the use of AI
in a number of different applications.
“With $500 and basic computer literacy, anyone can create basic 3D models of structures,” said Bockstael.
Murphy and Unke shared that they are seeing more use of AI in things like compliance monitoring and navigating standardized processes, but they noted a need to remain cautious when using the advanced technology, and when to believe its outcomes.
“We’re exploring and testing uses of AI, but I call it in a safe manner, in a trial, walk, and then run approach,” said Murphy. “The current AI environment is, ‘Trust, but verify.’”
“You still need to have that human touch,” agreed Unke. “It’s just like using any kind of design application that you use, say in structural engineering; you still need to validate what comes out of the machine so that it actually makes sense.”
Overall, the panel is bullish on the opportunities within the sector, as well as with its ongoing evolution.
As Bockstael summed it up, “The extent of opportunity and the diversity of what you can get into in a construction environment is actually quite vast. I think there’s a ton of opportunity.”
To check out this year’s keynote or panel discussions, visit the On-Site YouTube page by scanning the QR code.
This industry builds the impossible and it’s the people who make it happen. They face risks. They create order from the chaos. They push forward. They’re contractors. Owners. Engineers. Architects. We call them Groundbreakers. They build the future. We make the software that connects them.
Learn more at procore.com
We are up for any challenge. Complex projects are opportunities to demonstrate our unmatched skill, outside-the-box innovations, and unyielding strength. Whether you are looking to replace aging water/ wastewater infrastructure or need a trenchless solution with minimal impact on the surrounding environment, we will exceed your expectations for quality, safety and sustainability.
Partner with Michels Canada and expect more. Energy • Infrastructure • Power Construction
GOMACO offers the full range of concrete slipform pavers, curb and gutter machines, trimmers, placer/spreaders, texture/ cure machines and bridge/canal finishing equipment. GOMACO equipment features our exclusive and proprietary G+® control system, created in-house by our software engineers from the wants and needs of contractors paving in the field. At the heart of GOMACO equipment is our passion for concrete and our commitment to our customers. We look forward to visiting with you about your upcoming paving projects and your concrete paving equipment needs. Our worldwide distributor network and our corporate team always stand ready to serve and assist you.
The use of fibre reinforcement in concrete not only improves durability; it also reduces the embodied carbon in the materials of construction.
BY GUSTAVO POLIDORO
It is no secret that concrete is one of the largest contributors to the emission of carbon dioxide around the world. To their credit, the concrete and cement industries have recognized that they must play a role in reducing their carbon impact. As such, the industry is exploring all aspects of a build, from adjusting the components in our building materials, to the choice of material components used in projects.
Cement manufacturers have been working on low-carbon recipes to help bring down the carbon levels produced through the manufacturing process for the core ingredient in concrete. Others in the industry have been doing research to bring down the carbon footprint of concrete projects as well, including through the use of recycled aggregate and even alternative aggregate materials. The use of fibre-reinforced concrete (FRC) is another industry innovation that holds the potential to make a sizable net-positive impact in the ongoing battle to reduce the carbon footprint of our projects.
Over the past several years, there has been a renewed interest in the use of fibre reinforcement in concrete pavements for parking lots, white toppings, bridge decks and roadways. As interest rises, various technical organizations such as the American Concrete Institute (ACI), American Concrete Pavement Association (ACPA) and the National Concrete Pavement Technology (CP Tech) Center have stepped forward with new guidance and recommendations on how to properly select and use fibre types in concrete.
Despite some of the negative marketing and connotations, concrete is already one of the most environmentally friendly materials available when properly used. It is durable, cost effective, is made from locally sourced ingredients, is relatively easy to work with, has minimal waste, can be customized, and
has a thermal mass that can be advantageous. It has a long history of use because of all its positive qualities.
To help address some of its less desirable traits, the construction industry has embarked on a pathway leading to sustainable concrete practices and technologies that can save energy, reduce CO2 emissions,
protect the environment and maximize economics. By taking a big-picture approach to the reduction of global carbon emissions, and focusing on embodied carbon, the use of fibre in place of steel reinforcing bars can indeed result in reduced CO2 footprints for our infrastructure and other major projects.
Globally, it is estimated that the construction industry accounts for a quarter of total carbon emissions. Cement production claims about seven per cent of global emissions, and steel reinforcement accounts for 1.5 per cent of world-wide carbon emissions. With the large volume of reinforced concrete floors used worldwide, roughly 45 per cent of steel consumption is destined for concrete reinforcement. That’s a lot of opportunity for improvement.
The energy required to produce one metric ton of reinforced concrete is 2.5 GJ/t. This compares with 30 GJ/t for steel and 2.0 GJ/t for wood. A study comparing the emissions of several different building materials per 1,000 kg found that concrete produced 147 kg of CO2, metals produced 3,000 kg of CO2, and wood produced 127 kg of CO2
When exploring ways to reduce carbon emissions, there appears to be some opportunity in exploring how floors, walls, roadways and foundations could be reinforced at a lower carbon cost.
With a focus on reducing environmental impact, the knowledge, testing and experience of using synthetic macrofibre-reinforced concrete continues to grow for use in infrastructure projects, and its successful use and benefits are now being realized through full scale and long-term demonstration projects.
With positive anecdotal case studies, many prospective engineers, architectural firms and clients are now requesting additional information as to the environmental impacts of using fibres in replacement of traditional reinforcement, or as an added material in concrete to improve durability and useful service life. The industry is working on environmental product declarations and other materials to officially
qualify much of what has been observed via demonstration projects.
Although FRC has been used since the 1960s, there has been little change to its use in North America for many potential applications, until recently. New developments in materials technology and the addition of field experience to the engineering knowledge base have expanded the applications of FRC to include design guides that are now material independent and recognized by the engineering community.
Over the past two decades, FRC technology has gained acceptance from industry bodies such as UL, Steel Deck Institute (SDI) and ACI thanks to multi-million-dollar research programs. Structural designs and software tools have been designed, and calculations for equivalent reinforcing options to allow for comparison to conventional designs have also been developed. As such, FRC is being used in high-profile projects, including applications where failure is not acceptable and where durability is key, such as in bridge decking and paving.
The physical characteristics of fibres varies, with each type having its ideal application. In general, the industry has accepted that steel macrofibres and older micro synthetic fibres (fibrillated, monofils, etc.) are not used under the same conditions.
Micro synthetics are generally used as secondary reinforcement, addressing plastic shrinkage only. Steel fibres are more suitable for industrial floor designs and can replace heavier reinforcing configurations.
Synthetic macrofibres can be strong, like steel fibres, but simply not made of steel. The physical characteristics of these fibres, such as their length, tensile strength and diameter, are all different when compared to traditional micro synthetics.
Synthetic macrofibre composites can be used to replace steel reinforcement or in conjunction with steel reinforcement to increase durability and extend service life. The contribution to sustainable construc-
tion through lowered environmental, social and economic impacts is currently being documented.
To ensure proper performance of the concrete, macrofibres dosages should be calculated based on the engineering requirements of the project. Since the fibres are worked into the concrete mix, significant savings may be realized in construction time, labour and overall costs.
Once placed, FRC has an increased resistance to cracking, impact and fatigue as the reinforcement is randomized and three-dimensional throughout the structure, rather than being provided along a more defined plane that exists with more traditional reinforcement components.
We are in the midst of a massive infrastructure deficit. A quarter of our existing roads, bridges and other structures will need to be repaired or replaced by 2030, and these projects need to be completed with a lower environmental impact. The use of innovative material substitutions, like fibre-reinforced concrete, can help with both the longevity of these structures and their carbon footprints.
The use of FRC has been found to reduce CO2 emissions by more than 50 per cent compared to more traditional reinforcing means used in typical industrial floors and pavements.
And other materials, such as chemical admixtures, advanced cements and supplemental cementitious materials, can demonstrate additional significant reductions in overall upfront global warming potential (GWP) values.
We know that sustainability, or building better, needs to include a hard look at building practices, materials and long-term costs over time. If FRC lasts longer than normal concrete, is that not the exact definition of improving sustainability?
Based in Toronto, Gustavo Polidoro is the product manager of marketing and technology for fibre reinforced concrete at Euclid Chemical.
BY JAY FASO
In today’s fast-paced and competitive construction industry, efficiency and precision are non-negotiables. Whether tackling large commercial projects or detailed residential builds, the right tools and technology can make all the difference. Across Canada, owners and contractors increasingly embrace volumetric technology’s innovative capabilities, transforming concrete production and driving new business growth.
Volumetric concrete mixers offer a unique approach from the traditional drum truck, measuring and dispensing concrete directly at the jobsite by volume rather than weight. Each component — sand,
stone, cement powder, water, additives and supplementary cementing materials — is stored in a separate compartment. At the jobsite, concrete is mixed on demand in the precise amount needed.
If you own a volumetric concrete mixer or have considered adding one to your fleet, the following information and tips will help you get the most from your investment for years.
Proportioning by volume versus weight is at the heart of a volumetric mobile mixer. The result is a final product capable of accuracies better than plus or minus one per cent.
A typical volumetric truck features divided side-by-side open bins for sand and stone. A watertight bin equipped with automatic vibrators securely contains cement. Automatic vibrators guarantee precise cement proportioning and a steady flow to the mixer. Water is stored in an auxiliary tank and introduced into the mixer via flowmeters that ensure accurate monitoring.
The versatility of mobile volumetric trucks delivers virtually unlimited concrete mixes. Aggregates are carried separately or combined according to the design mix. For other concrete output requirements or specialty jobs, liquid admixtures such as accelerators, retarders, air-entraining agents
The industry’s newest profiles and trims
Expect more. For the most complete line of high-quality, durable, colorcomplementary profiles and trims – with more than 4,500 pieces to match your creative design – visit www.mapei.ca
and modified latex are carried in a separate system. These ingredients are introduced as needed, via precise flow controls.
As part of a contractor’s fleet, a volumetric mixer can significantly improve speed and efficiency between deliveries and when projects require changing mix designs as the separate material compartments on volumetric trucks allow operators to change mix designs on the fly without returning to the batch plant.
For example, if the slump changes halfway through a curb and gutter project, work stops only long enough to adjust the design mix. What formerly may have taken more than a day can be completed in hours with a volumetric concrete truck.
Another example is working on bridge decks. Latex-modified concrete is often used to counteract the freeze-thaw cycle in colder months. A volumetric mixer can efficiently produce latex-modified and regular concrete, streamlining the project
as operators can effortlessly transition from pouring high-strength 5,000 PSI concrete to a low-strength flowable fill in seconds by selecting a different mix design via the control panel on the mixer.
Volumetric technology allows pre-programmed information for each job and mix using an onboard electric control panel. Uploaded admixes can be saved in the system memory to easily navigate frequently used designs, including the history of all mixtures and quantities.
Once an admixture is selected, the operator sets gate controls, pushes a button and pours. Automated admixture tanks ensure the exact amount is used every time.
A two-speed cement bin provides adjustable cement discharge, making switching between concrete mixers and flowable fill applications easy.
Water is essential in making concrete, activating cement and causing it to harden and bind to the aggregates. The amount of water used affects quality, however. Too much causes concrete to weaken and easily crack, while too little makes the mix difficult to work with.
Volumetric concrete mixers measure and mix concrete on-site to the exact specifications for a fresh product with every
pour, and the onboard mixing technology controls water content to adjust for varying humidity levels, ensuring consistency regardless of weather changes or unexpected site conditions.
Volumetric mobile mixers also seamlessly switch between wet and dry processes, such as when working with gunite and shotcrete, with precise material measurements along the way. A simple adjustment of the water flow allows contractors to adapt the slump of the mix throughout the pour.
Implementing an easy-to-follow daily process for unloading and cleaning volumetric concrete trucks is crucial for maintaining consistent mix quality, enhancing safety, reducing costs and extending the equipment’s lifespan. It is recommended that a standardized procedure, or checklist, be used for unloading and cleaning trucks each day. This checklist should include:
• Confirming that the hydraulic systems are functioning properly.
• Ensuring all remote controls are clean and in working order.
• Hosing down the back of the truck and chute before unloading.
• Creating windrows for extra product.
• Rinsing off the chute before leaving the jobsite to prevent safety hazards for other drivers.
Any good heavy equipment owner also knows the importance of routine maintenance. Regular inspections will help keep the volumetric concrete mixer and its machinery at peak performance. Following daily and monthly checkups, owners will begin to see a wear pattern and can determine an appropriate maintenance plan for the unit.
Depending on the materials and series of units, the mixer is generally the first component requiring repairs on most mobile concrete mixers. The more time spent looking over the unit, the more likely you’ll develop a well-rounded schedule, including how to plan for downtime. A volumetric concrete mixer typically produces 3,000 to 5,000 yards before there is a
need to replace wear blades, the lower boot and bearings.
My company has developed a few maintenance checklists and task lists to help equipment owners and operators keep their machines in peak condition, especially during periods of more frequent use. As part of a daily routine, while cleaning we recommend noting any items showing wear or need replacing by inspecting wear blades, the belt wiper, the mixer motor for leaks,
the lower and upper mixer bearings, and for concrete build-up inside the unit.
On a monthly basis, it is beneficial to inspect the conveyor belt and tension, check the side and centre guide material, adjust the conveyor belt wiper, and flush the admix system with water.
Jay Faso is the regional sales manager for Canada at Cemen Tech, a manufacturer of volumetric concrete mixers.
The Husqvarna LP 9505 is a powerful, easy-to-operate trench compactor essential for demanding compaction jobs. Maintenance is quick and easy with all service points clearly marked under the easy-to-access protective hoods. Featuring smartly designed solutions, the LP 9505 can be used on a wide range of applications. Visit our website to learn more.
www.husqvarnaconstruction.com
By Jacob Stoller
Functionality doesn’t always accommodate the nuances of established processes.
Construction, more than most industries, is highly variable. Accordingly, business processes differ widely according to location and job type. This diversity calls for frequent variation in requirements for software functionality.
“We get requests from all across the board,” says Samantha Erlich, director of product in the Digital & Data Engineering division at EllisDon Corporation, which maintains its own construction software platform, Gate Three. “Processes are done differently depending on the location that we’re working in or the type of project that we’re working on. It can also depend on the requirements of the contract to the client. So, there are many reasons why we tend to modify and make software more efficient for projects.”
It’s important, however, to balance local requirements with the goal of establishing consistent data standards which, in turn, will enable the sharing of business intelligence and best practices across the enterprise.
“Without standardized data, standard processes, and standard platforms, you’re never going to get to the point where software can be used to help shape the way that you’re executing a task across your company,” explains Erlich. “On the other hand, there’s always an evaluation of the cost of change – how long does it take people to learn and understand a new platform? So, it’s a bit of a trade off, but based on what I’ve seen, the standardized approach definitely helps the business in the long run.”
Another challenge is that not all processes are ready to digitize. Customizing software to accommodate a poorly designed process might mean codifying extra steps that not only make customization difficult, but entrench unnecessary inefficiencies into the system.
“I don’t think customization is a bad thing, but people sometimes tend to take it too far,” says Kris Lengieza, global technology evangelist at Procore Technologies. “If we over-design and we overcustomize, it becomes a question of, ‘How many additional fields are we adding for every single unique situation?’ That way, I wind up with this form that is 700 fields long, and I have to fill this thing out every day. We need our processes to be simple.”
Lengieza has found that the workflows designed into Procore’s platform are often simpler and more efficient than what a contractor may have in place, particularly if the contractor is a small company with limited technical resources.
“A lot of our customers are able to use the out-of-the-box features in our software,” he says. “The reason that this works for them is that we’ve developed the tools around industry best practices. So, for the most part, it’s a better process than they
may have today.”
Changing a process to accommodate software can be risky, however.
“You really do have to think about the impact to your business processes,” says Erlich. “Construction is a high-risk industry. If something’s working for your company, sometimes the disruption of change can increase that risk.”
“In construction, processes were likely invented to mitigate risk,” says Jason Glover, principal strategic development consultant at Toronto-based Procore Partner SDC Partners. “So, if you’re talking about changing a process, you have to look at the why. What is the reason for the change? Is the process itself not working, or is it more of a people problem where they’re not actually following the process? I think that’s probably the main reason, because everything in construction is potentially at risk—that’s why those processes exist in the first place.”
Ultimately, the customer needs to see what the outcome of a change might look like to make the right decision. Glover finds that providing a side-by-side comparison is the best way to accomplish that.
“I’ve had clients with rough processes even before digitizing them. We’ve made suggestions they weren’t necessarily okay with, so we build our suggestion in a test environment, build what they wanted in their environment, and then show them the differences. This allows them to make an educated decision,” he says. “It’s a lot of work, but it’s worthwhile because the value of these solutions is paramount. We strive to ensure the end users’ lives are made easier while management still achieves their goals and vision.”
Jacob Stoller is principal of StollerStrategies. Send comments to editor@on-sitemag.com.
By David
onstruction industry project budgets have far too much capital allocated to unknown costs and risks. Sure, construction is an industry fraught with many unknowns, but with advancements in data science and technologies that allow us to better capture and organize data, it seems like it might be a good time to rethink the way capital is
allocated when setting a budget.
Traditional construction budgets combine direct costs, unknown costs (contingencies), and profits to arrive at a final construction price.
Direct costs are easily defined. These are costs to develop the project design, procure project materials, and construct project materials in line with the project design.
More challenging is the fact that the construction industry has perhaps the most unknown risks (costs) of any industry. To manage these unknown risks, a substantial amount of capital is allocated on most projects as a “shock absorber.” The two primary unknown risks on a construction project are profit and contingency.
A third source of project capital, and one that is often overlooked when it comes to unforeseen project costs/risks, are the premiums given to insurers and surety companies to take on traditional insurable risks.
Given advancements in data science, and technologies that more effectively capture construction data, there appears to be clear opportunity for the construction industry to re-allocate these three sources of shock absorber capital to more precisely manage known and unknown risks, and to drive better project outcomes.
Figure 1 is an example of how these three sources of project shock-absorber capital are traditionally invested and how they are generally used to finance project risks.
This example imagines a $1 billion hospital project with a three-year construction duration. As you can see, the combined amount of project capital that is used to arrive at project profit, project contingencies and project premium is substantial — in excess of 10 per cent of the construction budget.
Under these traditional structures, there is no mingling of the insurance/surety premiums used to finance traditionally insurable project risks, and the contingency and profit funds which are used to fund uninsurable costs/risks.
With access to tools that can better quantify probability and severity of all project risks, both insurable and uninsurable, could the
construction industry devise a risk finance structure that co-mingles these three sources of project capital? And if there is such a structure, what would that look like?
Figure 2 illustrates a potential structure that represents a rethinking of the way project shock-absorber capital could be reallocated and better integrated with the more risk-specific framework of insurance and performance security covers.
In this structure, you see more of the project profit being temporarily allocated to project contingency with the project contingency being broken into a more risk-specific framework. The project contingency is now funding the previously unfunded deductibles/ retentions, and a higher retention level is being put forward for each of the project insurance covers. This reduces premium spend, given a greater level of risk retention, and there is a more creative way to fund uninsured risks by creating a quota share structure with insurance/performance security capital.
This novel risk investment and risk finance structure creates several potential benefits.
It presents a more efficient and better thought-out process for identifying and financing project risk. It is a more granular approach than just having a pool of capital for all risks not insured. Such a framework, once fully developed, will make the “go or no-go” decision making framework more effective.
There is also less money being transferred, and forever lost, to the insurance sector. There is also a potential to create more funding for uninsured losses using quota-share structure for general risks.
Given that deductibles/retentions are funded (either fully or partially) using project continency and profit, and given these funds are allocated on a risk specific, more granular basis, it becomes possible to use these funds to drive better adherence to risk controls through the potential bonusing of a portion of these funded retentions. Such frameworks have been proven effective, with subcontractor default insurance and retrospective programs for workers compensation in the United States being good examples.
A much more thoughtful approach to managing project risk should result in better risk management story to share with insurance partners, and potentially your clients, as well as other construction stakeholders.
A rethinking of how project capital is allocated can drive better project outcomes, but a key first step to creating such a structure is to develop a solid data architecture or data strategy, and to begin harnessing the power of construction technologies to better capture, organize and analyze project data.
These discussions may be a compelling reason to bring together key management within your company, including the CFO, COO, CTO/CIO and risk manager, to rethink the way project profit, project contingency and project premiums are combined and structured.
David Bowcott is the executive vice-president of the Construction Industry Group at Platform Insurance Management. Please send comments to editor@on-sitemag.com.
By Krista Johanson
hange is inevitable. Most construction contracts include a procedure for agreeing to the scope and cost of changes to the work, and prohibit payment for unapproved extras. The best practice, always, is not to perform any extra work without first agreeing to a written change order. But deadlines are tight, and paperwork can lag. If you didn’t get a written change order, can you still get paid?
It can be difficult, but it is not impossible. So, the answer is yes, if you can prove all of the following:
1. That you performed work that was different from the original scope;
2. The owner instructed or authorized you to perform the work;
3. The extra work added to your costs;
4. The owner knew, before you performed the work, that the cost would increase; and
5. The owner waived, or acquiesced in ignoring, any contract requirement to obtain a written change order
The fifth requirement poses a special challenge. In cases where contractors or subcontractors have succeeded in proving their claims for extra work, the courts have usually found either that the owner’s instruction was a change directive, such as in Fast Trac Bobcat & Excavating Service v. Riverfront Corporate Centre Ltd., 2009 BCSC 268, where the owner wrote, “This is not a change order but permission to proceed,” or the parties had established an on-the-job pattern of practice where the owner approved extra work after the fact, meaning that the owner had lost the right to use the contract as a shield. An example of this can be found in Rich Van Electric Ltd. v. Dhaliwal, 2009 BCSC 1383
In the case of Ridge Rock Construction Ltd. v. Beckmyer Builder Ltd., 2006 ABQB 850, the defendant contractor argued that its subcontractor’s claims for extra work must fail because no written change orders were issued. However, the contractor acknowledged that it had given oral acceptance for pricing for a change on at least one occasion, so the court examined each of the disputed changes, which included additional excavation work and piping modifications.
After the site was excavated to the contract elevations, the designer determined that the elevation needed to be lower. The contractor and subcontractor agreed orally that further excavation was the only solution. As the contractor ought to have known that this would increase costs, this claim was allowed.
With the piping, the subcontractor had quoted based on piping for one brand of card-lock dispensers but the contractor,
without notice, supplied a different brand. This required the piping to be modified.
The contractor had discussed how to resolve the problem and watched the subcontractor perform the fix. This claim was allowed. A claim for supplying extra quantities of pipe failed, however, because the subcontractor did not provide any evidence that the contractor knew this extra pipe was required.
To avoid having to jump through these hurdles, it is advisable to notify the owner in writing as soon as you learn that extra work will be necessary. Submit a quotation and get it approved in writing, even informally, before doing the extra work.
Approval doesn’t mean much if the owner doesn’t understand that you believe the work to be outside the contract scope and how much you are expecting to be paid for it. If things are moving too fast, propose time and materials and give a rough budget. It’s up to the owner to decide whether they prefer speed or cost certainty. Don’t do the work without a change order or a change directive.
If the owner insists that the work is within the contract scope, ensure that you’ve (1) given notice, (2) sought a ruling from the consultant and given notice of dispute, if required, and (3) confirmed that you are performing the work “under protest.” And ensure that you carefully document the costs of the extra work.
Owners wishing for certainty in pricing and to avoid disputes typically have several contract clauses to rely on. For example, the standard CCDC-2 form prohibits extra work without a change order or change directive. It requires notice of claims and states that no act will constitute a waiver of rights unless agreed in writing.
To avoid losing the benefit of these clauses, owners should never permit the contractor to perform extra work before pricing has been approved and should make use of change directive provisions where it is not possible to agree on pricing before work is carried out.
If it is necessary to waive a contract requirement in respect of one change, owners should stress, in writing, that this waiver does not apply to future changes. Take every opportunity to communicate your expectations.
Krista Johanson is a partner in the construction group at Borden Ladner Gervais LLP. This article provides an overview and is not intended to be exhaustive of the subject matter contained herein. Although care has been taken to ensure accuracy, this information should not be relied upon as legal advice.
Sized right for tight spaces. Steel-built for heavy-duty work. With groundbreaking power in a nimble package, Takeuchi Compact Excavators are proof positive that it’s not the size of the machine in the work, it’s the size of the work in the machine.
EXTENSIVE EXCAVATOR LINEUP: INCLUDES CONVENTIONAL TAIL SWING, SHORT TAIL SWING, SIDE-TO-SIDE (STS) OFFSET BOOM, HYBRID AND FULLY ELECTRIC MODELS.
Optimize your cash flow and reduce delays and downtime so you can complete your projects on time and on budget.
Rent from our Construction Equipment and get access to the latest technology in efficiency and reliability for all your needs. dedicated Rental Fleet of new Volvo
Smart commercial Account
Finance your rental today by using your Volvo Smart Commercial Account. Find out more and apply now.