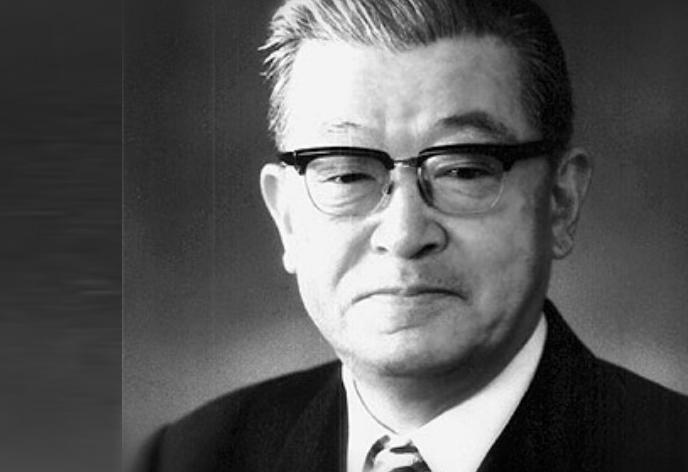
11 minute read
Provide quality advice by which it is intended to
KAORU ISHIKAWA (1915 - 1989)
A representative of quality in Japan since he promoted the implementation of suitable quality systems valuing the business process.
Advertisement
“The ideas of controlling and improving are often confused since they are inseparable”.
Kaoru Ishikawa was born in Japan on July 13th, 1915. He was an industrial chemist, manager of companies and expert in quality control. He graduated from Chemical Engineer at Imperial University in Tokyo, where he got his Ph.D. in engineering, he was also a teacher.
In 1949, he was a member of the Union of Japanese Scientist and Engineers (JUSE) where he was a researcher in quality control. Then, in 1960, he was at the International Organization for Standardization (ISO), an international association created to develop standards in quality with different companies and products. He was the president of Japan deputation in 1977. Also, Ishikawa was president of the Institute of Technology in Musashi in Japan.
Kaoru Ishikawa was considered, the founder of the scientist analysis in Industrial processes. He created the Ishikawa Diagram, where the graphics classify causes of issues. 1. Control sheets (implies the frequency used in the process, variables and defects)
2. Histogram (a graphic of variables).
3. Pareto analysis (problems classification, identify and solve).
4. Cause and effect analysis or Ishikawa Diagram (search for the main factor of issues to analyze them).
5. Scatter diagram (relations definition).
6. Control graphics (variation measure and control).
7. Stratification graphics (divide the available data to compare its characteristics).
ISHIKAWA QUALITY PHILOSOFY
Quality stars with education and finishes with education.
The first step of quality it’s to know what the client wants.
Eliminate the cause and not the symptoms.
The quality control employees rely on them.
Do not mix-up mean with targets.
Quality shall be the priority and then profits.
Trading is the input and output of quality.
The manager shouldn’t be angry when employees present facts.
95% of issues in a company can be solved by analysis and problem solutions
Data with no scattered information (variability) is considered false.
The Ishikawa diagram also named cause-effect diagram used as a systematic tool to find, select and document quality variation on production and organize its relation. This graphic indicates that each issue has specific causes to analyze and test one by one in order to prove which one is causing that effect (issue) when the causes have eliminated the issue as well.
The chart helps us to see the problem and effect on different variables, providing a solution and useful tool in quality management.
I S H I K AWA I M P O RTA N T WO R KS
The main ideas of Ishikawa are found in one of his most popular books, what is the total control of quality: the Japanese modality. This book points out that quality management is characterized by everyone involved in the company, from senior executives to lower-level employees. Some benefits of this concept improve the job’s environment and lower fees and better competitive status. The main ideas of Ishikawa are found in one of his most popular books, what is the total control of quality: the Japanese modality. This book points out that quality management is characterized by everyone involved in the company, from senior executives to lower-level employees. Some benefits of this concept improve the job’s environment and lower fees and better competitive status.
“By the total control of quality with the participation of all employees, including the president, any company can create better products and services at a minor cost, as well as increasing its sales, improving utilities and turns the company in a higher organization. Quality control starts with education and ends up in education, to promote it, we need to train employees, from the manager to employeess”.
WHAT’S THE TOTAL CONTROL QUALITY? THE JAPANESE MODALITY 1985
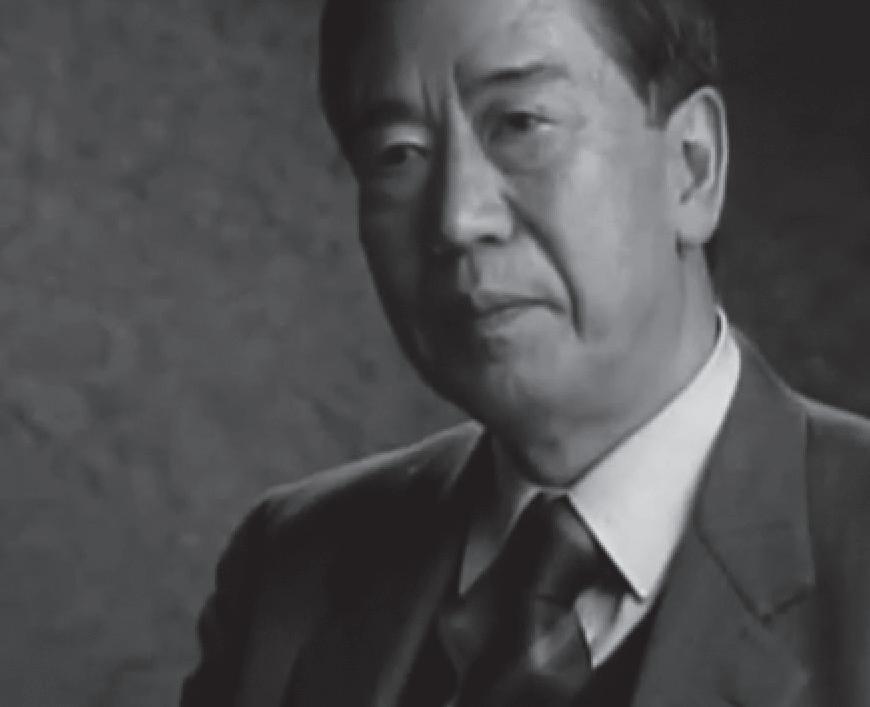
Engineer and Japanese statistics were known for developing a methodology for statistics application in order to improve the quality of products and manufacturing processes.
“The ongoing improvement of quality in a product manufacturing shall be an internal philosophy of importance in business”.
Taguchi was born in 1924. He graduated as a textile engineer in the technical school of Kiryu University, then he became a Mechanical Engineer and, he got a doctorate in Mathematics Statistics. In 1950, he worked at the Electronic Communications Laboratory (ECL), of Nippon Telegraph and Telephone Corporation, when the statistic quality control became popular in Japan, and where he worked twelve years making methods to improve quality. Moreover, he was a teacher at the Aoyama Gaukin University of Tokyo and quality consultant for Toyota and Fujifilm.
He was an advisor of the Japanese Standards Institute and Manager of Suppliers of America, an institutional organization of consultancy.
Genichi Taguchi is known as the creator of Quality Engineering. He mixed statistics and engineering methods to improve better fees and quality by optimizing products and manufacturing processes.
• Online quality engineering: Manufacturing, process control and correction of processes, and preventive maintenance.
• Offline quality engineering: Optimizes products and process design. Makes use of experiments, for its application.
ROBUST DESIGN TAG U C H I O U T STA N D I N G WO R KS In the United States, Taguchi was the leader of the industrial quality movement and founder of the Robust design in Japan, for more than 30 years. Every time a product is designed by complying with the client’s needs, but within the standard; this is named acceptable quality. The robust design suggests overpassing the consumer needs and at the same time, avoiding unnecessary expenses. Taguchi engineering method of quality reduces undesirable variations in products and processes to improve production, reduce cost, and raises client satisfaction. Genichi Taguchi published more than twenty technical or scientific books. He was four times awarded with Deming’s awards due to his contributions in the literature of quality. Moreover, he received the W. F. Rockwell medal, for technical excellence in 1986. In May 1989, he received the purple stripe of Economic and Technologic Progress by Akihito, the Japanese emperor. He was the honorary chairman of the American Supplier Institute and Japanese Institute, a Manager of Industrial Technology.
LOSS FUNCTION
“Quality is the loss of a product or service caused to society since it’s issued”.
TAGUCHI’S QUALITY ENGINEERING HANDBOOK 2004
Quality is related to price and money loss, not only for the manufacturer but for the client as well. Genichi’s definition considers the client when measuring product quality. In mathematics, the loss is related to product variability; if the product is closer to quality, less will be the loss.
ROBUST ENGINEERING 1999
ON ROBUST TECHNOLOGY DEVELOPMENT 1993
PHILIP BAYARD CROSBY (1926 - 2001)
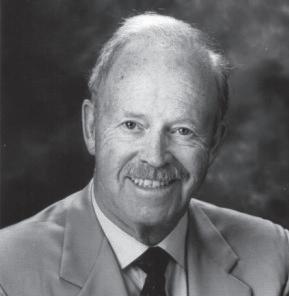
The American businessman who created quality management through his book, the quality is free, a philosophy zero flaws.
“Quality is free, isn’t a gift, its free, things made with no quality cost money; all the resulting actions for not doing things right”.
He was born on June 18th, 1926, in Wheeling Virginia, United States. During his youth, he served in the Marine in his country, participating in the Second World War and the Korean War. He worked with Martin-Marietta as a quality engineer and developed his philosophy known as zero defects. He states that to keep quality, you need to do things right the first time before any contingency or failure is presented.
Crosby was a quality manager at the International Telephone and Telegraph (ITT), where he applied his method. In 1979, he created his own consultancy company where he taught a course of quality management and how to establish a preventive culture to doing it right the first time.
T H E P R I N C I P L E O F “D O I N G I T R I G H T T H E F I R ST T I M E”
Includes four basic concepts:
• The quality definition agrees with the needs. • The quality system is prevention. • A standard management is equal to zero mistakes. • The quality measure is the price to nonconformance.
The engineering method of quality created by Taguchi reduces undesirable variations in products and processes, improves productivity, lower cost, and raise client satisfaction. The main Crosby idea is that companies don’t pay for quality since is free. What really costs are things that don’t have quality, meaning every action made due to not doing right the first time, therefore considers that quality generates profit, since each penny not spent by the company for doing something wrong it becomes profit.
Cosby’s quality improvement is achieved by the following steps:
1. The management committee shall define and commit to the quality improvement policy.
2. Quality improvement teams, where each department representative supervises the work team.
3. Quality actions working in data and statistics gathering, to analyze trends and issues of the organization.
4. Quality price is the consequence of doing things wrong, and not do it the first time.
5. Awareness of quality, teaching the organization the price of not doing things right the first time and how to avoid it.
6. Corrective actions, actions that will be done to correct likely deviations.
7. Planning zero-defects and defining a program to prevent likely mistakes.
8. Supervisor training and knowledge about making and carrying out the improvement plan.
9. Zero-defects day, a date for the company to carry out the change.
10. Establishing goals and fixing targets to reduce mistakes.
11. Eliminating error causes and barriers, preventing the ideal compliance of the zero-defects program.
12. Recognize people by rewarding them, since they helped to comply with the goals.
13. Provide quality advice by which it is intended to unify workers through communication.
14. Start again, quality improvement is a moving cycle that never stops and continually change.
OUTSTANDING COSBY’S WORK
Cosby published 13 books; the first one named Quality if free, which was accredited as a spearhead of quality revolution in the United States and Europe, it was translated in 15 languages.
QUALITY IS FREE THE ART OF VERIFY QUALITY 1979
“Every penny not spent in doing things wrong, doing it again instead of other turns in a halfpenny towards profit. If you focus on assuring quality, you might increase your profit from 5 % to 10% on your sales”.
PETER M. SENGE (1947 - UP TO NOW)

Founder of the term organizational culture, he was distinguished for developing a theory of smart organization, where people align talents and capacities, to success together and achieve intended results.
“The continual improvement of quality when manufacturing a product shall be an internal philosophy, important for organizations”.
Peter Senge was born in 1947, in Stanford. He got a degree in Engineering at a local University and a master’s degree in Modeling Social Systems at the Technology Institute of Massachusetts, then he got a Ph.D. in Management.
He was the principal of the Organizational Learning Center at the Technology Institute of Massachusetts and founder of the Organization Learning Society, an institute focused on people wanting to develop their capacities and organizations. Senge was named one of the 24 strategists of the XXI century, by the Journal of Business Strategy. Also, he has known by his book the fifth discipline: the art and practice of an organization. This book changed the theory of organization management, stating that an organization is capable of learning, resulting in a new direction, and new content to the manager’s action.
Peter Senge uses the term Smart Organization, describing an organization searching for its members to earn and practice their potential; this means understanding the complexity, new commitments, take ownership, look for a continually self-growth and create joint effort through teamwork.
This approach considers every team member of the organization as a valuable element, capable of contributing, and commit 100% with the company’s vision, adopting it and acting with responsibility; therefore, they’re capable of deciding to enrich the organization using their creativity, acknowledging their qualities and limitations.
SENGE OUTSTANDING WORK
THE FIFTH DISCIPLINE THE ART AND PRACTICE OF AN ORGANIZATION 1990
Peter Senge’s book describes the task of building smart organizations by unfolding his vision over organizational thinking, showing how these organizations will be overcoming difficulties, identifying threats, and face new opportunities.
Senge’s work changes the management with the theory of an organization capable of learning. The fifth discipline leads to identify practices, aptitudes, and specific methods that help to build smart organizations. Also, it describes how to design training and prepare processes able to provide new ways, and contents for the organization.
1. PERSONAL DOMAIN: Learn to expand personal capacity and create a business field that encourages all the members, to improve themselves, looking to achieve goals and targets.
2. MENTAL MODEL: To think, know and manage the individual thinking process and ideas about the environment perception, this will allow a better and effective communication within the company.
3. COMMON UNDERSTANDING: Creating a group commitment by sharing the same goal over the future they want to see.
4. TEAM LEARNING: Common abilities based on communication, interaction, and talent alignment, so the group of people develops intelligence, and capacity, in addition to individual contributions.
5. SYSTEMATIC THINKING: The language to describe and understand strengths and correlation modeling the behaviors of the system to achieve important and lasting improvements.
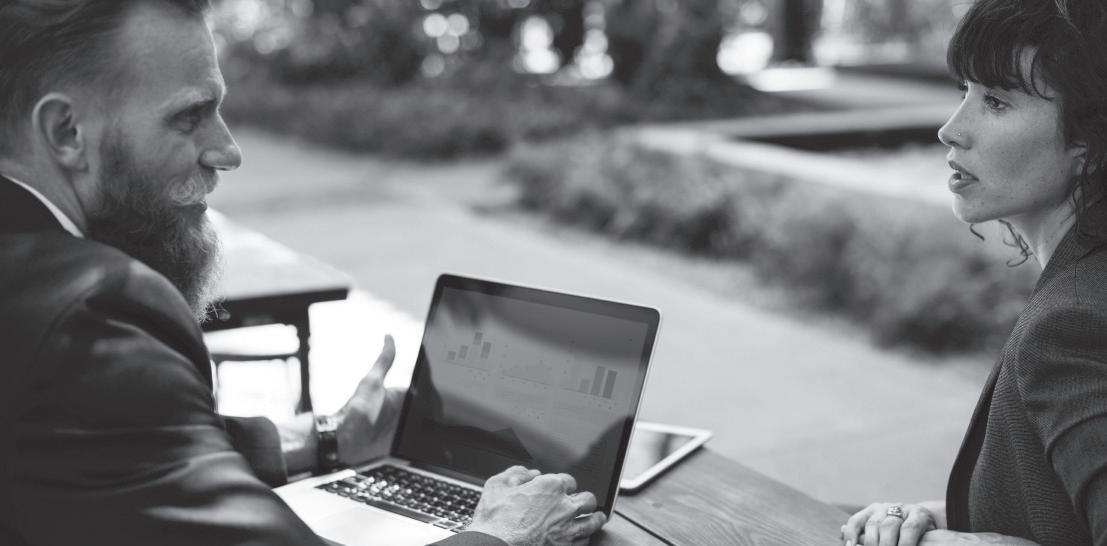
www.globalstd.com