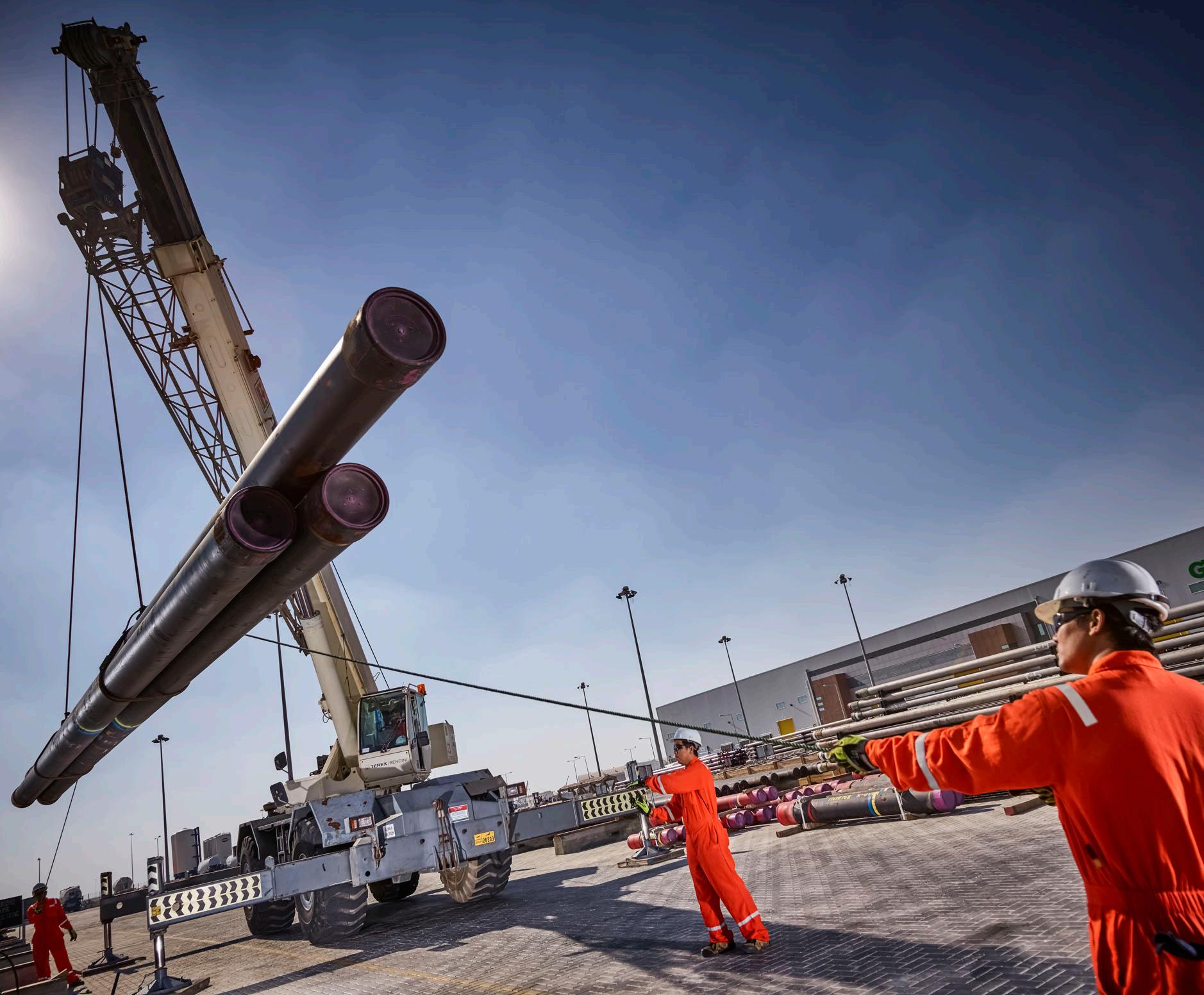
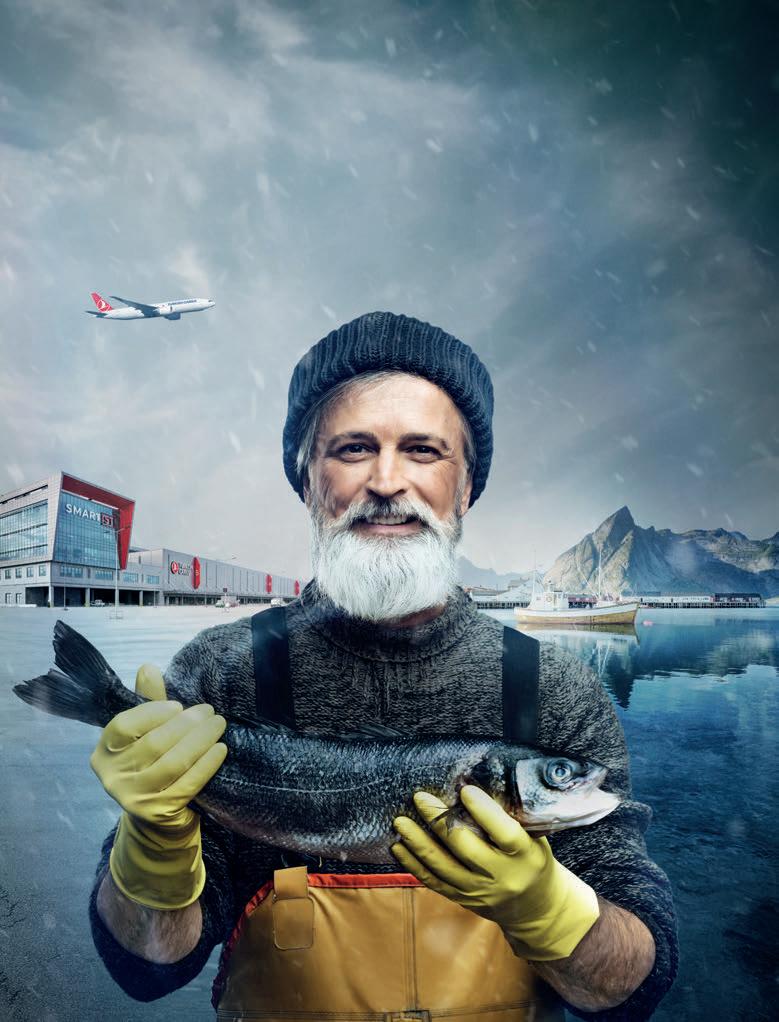
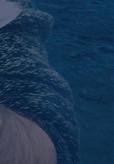
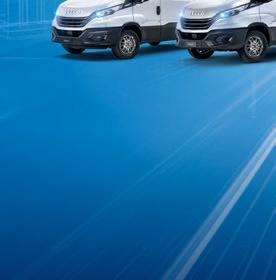
Full offering
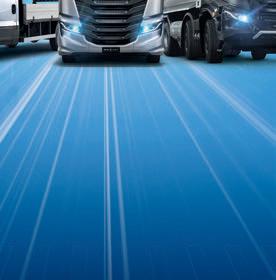
Full offering
- Full range vehicles with the most advanced technologies
- Highly customized product driven by market needs and optimized Total Cost of Ownership
High capillarity of aftersales
- Repair and Maintenance contracts and competitive warranty conditions
- Origin 100% IVECO Parts and a widespread network coverage
European technology
- High quality complete line-up in terms of tonnage, power, torque, safety, ergonomics
- High performance and robust trucks for extreme Off-road conditions
Customer centricity
- Comfort, ergonomics and the latest safety technology to make on board easier
- Driver Style Evaluation tool on Heavy ON-road range and optimized vehicle design to improve customer profitability
Empowering Your Chemical Supply Chain Beyond Boundaries...
SIGNATURE MEDIA FZ LLE
P. O. Box 49784, Dubai, UAE
Tel: 04 3795678
Email: info@signaturemediame.com
Exclusive Sales Agent
Signature Media LLC
P.O. Box 49784, Dubai, UAE
Publisher: Jason Verhoven jason@signaturemediame.com
Editor: Abigail Mathias abigail@signaturemediame.com
Art Director: Johnson Machado johnson@signaturemediame.com
Production Manager: Roy Varghese roy@signaturemediame.com
Printed and Distributed by Masar Printing and Publishing L.L.C., Part of Dubai Media Incorporated Dubai, UAE
Contributor’s opinions do not necessarily reflect those of the publisher or editor and while every precaution has been taken to ensure that the information contained in this magazine is accurate and timely, no liability is accepted by them for errors or omissions, however caused. Articles and information contained in this publication are the copyright of Signature Media FZ LLE & SIGNATURE MEDIA LLC and cannot be reproduced in any form without written permission.
“Supply Chain is like nature, it is all around us.” - Professor Dave Waters
Welcome to the November issue of our action-packed magazine.
We bring you detailed insights from the region’s leading warehouse company, GWC. We also offer a front seat to the largest technology event of the year, where Alain Kaddoum, Managing Director of Savoye offers an in-depth look at how software is transforming supply chain operations. As the festive season beckons, we analyse the art of gifting with the experts at IGP. This issue also examines Logsquare and its expansion into Saudi Arabia. There’s also an academic insight on Industrial Design by Dr. Ahmed Kassab. Global Supply Chain is also delighted to discuss Etihad Cargo’s role in enhancing cool chain solutions. Bachir Sentissi, Co-Founder, Atracio explains how the use of RFID, blockchain, IoT (Internet of Things) sensors, and Artificial Intelligence (AI) play a part in reducing costs and enhancing decision-making.
Besides several topical pieces on monumental events from the industry, we also offer an exclusive look at how TIACA’s Deputy General, Glyn Hughes balances international logistics and living. We look forward to your timely suggestions as we embrace the future together. Happy reading.
Abigail Mathias Editor
abigail@signaturemediame.com www.globalsupplychainme.com
GWC (Gulf Warehousing Company) has established itself as a trailblazer in the logistics industry, not only through its impressive growth across the GCC (Gulf Cooperation Council) and globally, but also through its firm commitment to sustainability and digitalisation. The company has aligned its operations with Environmental, Social, and Governance (ESG) principles, integrating cutting-edge technologies to enhance its service delivery while reducing its environmental footprint. Global Supply Chain explores.
Ranjeev Menon, Group CEO of GWC
Madhu Vallur, Executive Director of GWC Energy
This combination of innovation and responsibility positions GWC as a key player driving the future of logistics.
GWC’s commitment to ESG initiatives is central to its corporate strategy. The company strives to balance its rapid expansion with responsible practices that promote sustainability. GWC has developed a comprehensive framework aimed at reducing its carbon footprint, improving transparency, and fostering community engagement. These initiatives focus on reducing waste, optimising energy use, and adopting green technologies across its extensive logistics infrastructure.
According to Ranjeev Menon, Group CEO of GWC, “Sustainability is no longer an option but a necessity in today’s logistics landscape. GWC is dedicated to leading the industry in adopting environmentally friendly practices while continuously improving our operational efficiency through digitalisation. Our goal is to create value for our clients while ensuring that our growth is sustainable and aligned with global environmental standards.”
The company’s state-of-the-art facilities, spanning over 4 million square metres, are designed to operate efficiently with a focus on reducing energy consumption and minimising waste. GWC also partners with local and international stakeholders to ensure that its operations are in line with global best practices for sustainability.
At the heart of GWC’s sustainability efforts is its strategic use of advanced technologies. GWC is leveraging AI (Artificial Intelligence), automation, and IoT (Internet of Things) to enhance its logistics operations, making them more efficient and environment friendly. The implementation of AI-powered solutions has enabled GWC to optimise its supply chain management, reduce fuel consumption, and improve delivery
times – all of which contribute to a greener environmental footprint.
Madhu Vallur, Executive Director of GWC Energy, adds, “Technology is a gamechanger for us, especially when it comes to our sustainability efforts. By integrating AI and IoT into our operations, we’ve been able to optimise everything from fleet management to energy consumption, drastically reducing our environmental impact. GWC Energy is committed to ensuring that our operations are both digitally advanced and sustainable.”
“Sustainability is no longer an option but a necessity in today’s logistics landscape. GWC is dedicated to leading the industry in adopting environmentally friendly practices while continuously improving operational efficiency.”
— RANJEEV MENON, Group CEO of GWC
The company’s adoption of digital platforms also extends to real-time tracking and supply chain transparency, allowing clients to monitor their shipments while minimising waste. This not only increases operational efficiency but also strengthens customer relationships by providing greater visibility and accountability.
GWC has experienced rapid growth across the GCC region, positioning itself as a logistics leader. With a growing footprint in international markets, GWC continues to expand its operations, offering its industryleading logistics services to a global client base. The company’s comprehensive service portfolio includes everything from warehousing and distribution to specialised logistics solutions such as hazardous materials handling, fine art logistics, and equestrian logistics.
“Our growth in the GCC and globally is a testament to the trust our clients place in us,” says Menon. “We’re constantly innovating, investing in technology, and expanding our capabilities to meet the growing demands of global trade. Our vision is to remain at the forefront of the logistics industry by combining world-class service with a commitment to sustainability and innovation.”
GWC’s commitment to ESG principles, digitalisation, and sustainable growth has firmly positioned it as a leading logistics provider across the GCC. Through divisions such as GWC Energy and GWC Fine Art, the company continues to innovate and integrate advanced technologies that not only enhance efficiency but also align with global sustainability goals.
With GWC’s continued investment in digital solutions and its dedication to fostering sustainable practices, the company is well on its way to shaping the future of the logistics industry. The team is excited to participate at this year’s ADIPEC. The conference held in Abu Dhabi from November 4-7, brings together more than
2,200 international organisations from the full spectrum of the global energy ecosystem to discuss critical challenges, foster global partnerships and inspire credible solutions.
At ADIPEC, the GWC team will share more about their ground breaking initiatives in logistics for the energy and fine art sectors.
As Menon states, “GWC is more than just a logistics company – we are a technologydriven, sustainability-focused leader in the industry, constantly reaching new heights and setting new standards for what logistics can achieve.”
GWC Energy is a specialised division of GWC that focuses on providing logistics
services for the energy sector, including oil, gas, and renewable energy industries. As one of the most energy-intensive sectors, logistics for the energy industry faces significant challenges in terms of sustainability. GWC Energy is rising to these challenges by integrating sustainable practices into its operations and embracing digitalisation to streamline processes.
The division has adopted smart fleet management systems that use AI to reduce fuel consumption and carbon emissions, contributing to GWC’s broader sustainability goals. GWC Energy also employs advanced tracking systems, enabling real-time monitoring of shipments, which reduces operational inefficiencies and enhances safety standards.
GWC’s presence at ADIPEC in the UAE further underscores its commitment to innovation in the energy logistics sector. Vallur invites industry professionals to visit their stand at ADIPEC to explore their latest solutions, “We’re proud to showcase our cutting-edge logistics services for the energy sector at ADIPEC. Our solutions not only enhance efficiency but are also designed with sustainability in mind.”
Set to play a key role in the region, GWC Energy W.L.L was established as a wholly owned subsidiary of GWC Group to serve the growing needs of the global energy market.
GWC Energy offers complete shipping, maritime, and logistics solutions that are customized for clients in the energy sector. Manpower, equipment, marine logistics, warehousing, supply base management, bunker supply and rig, husbandry and mob/demob assistance are among the
core service.
“By integrating AI and IoT, we’ve optimised everything from fleet management to energy consumption, drastically reducing our environmental impact.”
— MADHU VALLUR, Executive Director of GWC Energy
Along with onshore and offshore services, GWC Energy also offers support for paperwork and customs. Its facilities, huge operational yards, pipe inspection areas, hazardous storage, bulk areas with overhead cranes and numerous capacities, and air-conditioned warehouses with big rack capabilities.
Register now to get your complimentary visitor pass and be part of our journey as we help shape the future of energy.
GWC is delighted to invite visitors to its stand at ADIPEC 2024, taking place from 4-7 November2024 at the Abu Dhabi National Exhibition Centre (ADNEC), Abu Dhabi, UAE. Stand number 15505 is located in Hall 15. Register at www.adipec.com to get your complimentary visitor pass.
The SSI Exyz is a fully automated pallet storage system that operates across three-dimensional axes—X, Y, and Z. Its intelligent system optimizes travel, lifting, and storage retrieval movements to achieve maximum energy e ciency with minimal investment. With the ability to reach heights of up to 45 meters, the SSI Exyz can deliver up to 25% energy savings and reduce the system footprint significantly.
Handling fragile and sensitive cargo? Consider the high-quality SSI Mini Load System. The system is designed to handle a variety of shapes and sizes, including bins, cartons, and pallets, seamlessly during storage, retrieval and bu ering operations. It is also available in single or double configurations, and can extend to a height of 24 meters. The angled supports o er a lightweight yet powerful solution, ensuring high throughput while occupying minimal floor space.
The best part? Both solutions are built to perform even in deep freeze conditions.
Scan the QR code now to discover proven solutions that will transform your warehouse!
Global Supply Chain’s Editor, Abigail Mathias, sat down with Alain Kaddoum, Managing Director of Savoye Middle East, at the recently concluded GITEX GLOBAL 2024. The week-long event held in Dubai, is considered the world’s most iconic large-scale tech exhibitions and a fitting venue to discuss the supply chain and logistics landscape, key growth trends and the company’s plans for the region, along with their advanced technologies.
Abigail Mathias: We already have a lot of insights on Savoye, but let’s begin with your expectations for this year’s GITEX event and what Savoye brings to the table.
Alain Kaddoum: GITEX is one of the largest technology events in the world, and for a company like Savoye, which specialises in warehouse automation and supply chain software solutions, it’s the perfect place to be.
This year’s event focuses on supply chain solutions, which aligns seamlessly with what we do. In collaboration with INCUBE, our partner for integrating advanced software solutions, we are showcasing the modularity and flexibility of our software, highlighting our innovative solutions in warehouse management, order management, and transport management systems. The exposure and networking opportunities offered by the event are invaluable, especially since it is being held in a highly tech-forward region like the Middle East.
AM: There’s a lot of buzz about incorporating Artificial Intelligence (AI) into these systems. What are your thoughts on that?
AK: AI has indeed become a popular buzzword, and its significance is rapidly growing. It is not a new concept, and has remained a theoretical idea for the past several decades, but its practical applications are now being explored. We have already integrated AI into several of our solutions like the ODATiO platform, which combines transport management, order management, and warehouse management systems. Moreover, we use AI-driven learning algorithms to support supply chain and logistics managers by improving predictability in areas like inventory and labour management.
We also leverage AI for the creation of digital twins for our automated solutions. This allows us to simulate real warehouse operations digitally, for testing and finetuning solutions in a virtual environment, thereby avoiding costly on-site tests and reducing deployment time.
We also utilise AI in the field of robotics. Through machine learning and image processing algorithms, we have given robots the ability to recognise and handle items based on their shape, size, and
Alain Kaddoum, Managing Director of Savoye Middle East
texture. Robots have been used in various industries over the past 50 years. However, the real innovation lies in making them smarter by teaching robots to make decisions rather than simply repeat actions. This gives them the ability to adapt, learn from mistakes, and improve autonomously.
For example, in our industry, robots might be tasked with picking items of varying shapes and sizes. Through AI, they can learn how to adapt their grip based on whether the item is soft, hard, or irregularly shaped— just like a human does. This adaptability makes the robot not only efficient but also capable of handling diverse tasks that are beyond the capacity of traditional robots.
AM: Can you share more about Savoye’s future innovations in AI?
AK: We are currently working on an exciting R&D project launched this year- ‘warehousefree barcode.’ Today, most warehouses rely on barcodes for tracking and sorting items, but we are exploring how AI can be used to
eliminate the need for barcodes altogether. Imagine a warehouse where barcode scanning is no longer needed, instead, cameras are used to instantly recognise and validate items through Lidar technology. We are also using smart radar technology to detect an item’s location within the warehouse, eliminating the need for manual confirmation. This could help streamline warehouse operations, with items being transported seamlessly without the need for scans and manual checks. It is an ambitious project, but we aim to implement it within the next decade to enhance the efficiency of supply chain operations.
AM: That sounds like a revolutionary step for warehousing. When do you anticipate this technology being fully deployed?
AK: It’s certainly a long-term project, but as pioneers in this field, we are confident that it will positively transform the future of supply chain management. Over the next
decade, we aim to develop and refine this technology so that it can be widely adopted across the industry.
AM: Shifting gears slightly, there’s a growing conversation in supply chain management around sustainability and software evolution. What happens to older software versions as new ones are introduced? How does Savoye handle that? Consider the scenario of transitioning from version 1.9 to 2.0. What happens to version 1.9?
AK: That is an important question, especially as sustainability becomes a critical aspect of various operations. At Savoye, we build our software on a foundation of continuous evolution. For instance, our warehouse execution software which controls robots, is designed using microservices, enabling its different modules to be reused and repurposed across various projects. This allows us to utilise our diverse innovations for various clients without starting from scratch. So, for instance, when we move from version 1.9 to 2.0, we do not discard the older version but only add new features and capabilities.
Our flagship platform, ODATiO, is a perfect example of this modularity as it integrates warehouse management, transport management, and order management systems. Each of these modules can function independently or together, and when we upgrade the platform, we build upon the existing foundation. As a result, even older software versions remain relevant and usable, offering clients continuous upgrades rather than impelling them to perform costly system overhauls.
AM: So, the software evolves along with the client’s needs?
AK: Yes, it is crucial for our clients to know that they are not investing in software solutions that will become obsolete in a few years. With ODATiO, for instance, we have created a platform that allows clients to configure and redefine warehouse functions themselves, without the need for significant upgrades or custom coding. This is made possible by our business rule engine, which empowers clients to modify their operations in real-time.
In today’s fast-changing world, supply chains should be made adaptable. Five years
ago, eCommerce was a growing trend, but today it has become a necessity. Moreover, businesses are faced with crises like supply chain disruptions and regional conflicts. Our software is designed to grow and adapt to these changes, prioritising integration capability, followed by automation.
AM: Given that Savoye is known for its expertise in automation, it’s surprising to hear integration take precedence. Could you elaborate on why that is?
AK: Integration is at the heart of everything we do. Savoye has been in this field for over 35 years, and one of the biggest lessons we have learned is that true success does not come from merely owning the fastest or most powerful machines, rather, it comes from how cohesively those machines, software, and systems work together. In today’s world, integration is more important than ever since the supply chain landscape is constantly evolving. Our software, particularly ODATiO, is built with this in mind. Whether clients are implementing manual processes, partial automation, or fully automated systems, they need a solution that can smoothly integrate diverse aspects.
Though many people are surprised to hear that we prioritise integration, we firmly believe that automation should be implemented only after the software and integration framework is well-established. It is crucial to first define the technology stack and integration vision before introducing automation. Without a clear integration plan, one cannot leverage the full potential of robots and similar automation solutions.
AM: Looking ahead to 2025, what’s on the horizon for Savoye?
AK: In 2025, we will continue to focus on providing solutions that evolve with our customers. Our modular platforms like ODATiO are central to this strategy. We are also enhancing focus on AI-driven solutions such as barcode-free warehouses and robotic integration.
The goal is to offer clients flexible, futureproof solutions that can adapt to changing business needs. Savoye has always been committed to innovation, and we are excited to see how these new technologies will shape the supply chain industry in the coming years.
Benefits of having Automatic transmission.
• The optional automatic transmission knows the best gear to engage in any situation and allows for quicker yet efficient and optimal cruising speeds. That means more trips per day and a boost to overall productivity.
• Direct coupling “lock up” function for enhanced fuel efficiency and performance.
Wide range of choices to keep every type of business on schedule.
• 3 GVW ranges from 19 – 10.4 Tones.
• Up to 21 different basic configurations.
• 8 & 5ltr engines with 180hp – 280hp.
• Euro 5 emission levels.
As Saudi Arabia and the UAE push beyond their oil-dependent economies, they are emerging as dynamic players in the global logistics arena. Investments in specialised manufacturing zones and tourism are not only diversifying their revenue streams but also positioning these nations as pivotal logistics and warehousing hubs.
Oped By Rami Younes, General Manager, Swisslog Middle East
With their growing centrality to international supply chains, there is an increasing urgency for sophisticated omnichannel distribution solutions to handle the complexities of modern commerce. Omnichannel distribution introduces multiple challenges to the general merchandise supply chain. Inventory management becomes more complex, variability in order volumes becomes more extreme, and the pressure to hold down costs increases. Automation enables retailers to address these challenges with solutions that support more efficient store replenishment and faster, lower-cost e-commerce fulfilment. Equally important, the right solution can provide the flexibility to manage resources and inventory across channels. Think with Google research shows that omnichannel strategies can increase store visits by 80%, underscoring the need for flexible solutions to manage resources and inventory across channels effectively.
Omnichannel warehouses can benefit from a broad range of automation technologies, including pallet and/or carton automated storage and retrieval systems (ASRS), mobile robotics, goods-to-person technologies, sortation systems, and packaging equipment.
Designing the right solution for a particular facility requires a holistic approach that identifies where automation can deliver the greatest value and considers all viable technologies for each process in the warehouse. Whether automating a single process or the entire warehouse, it’s
also beneficial to consider how the chosen solution can accommodate future changes and integrate with scalable automation technologies.
One important decision that deserves attention and focus when considering your automated warehouse design strategy is the automation control system software and execution platform. It’s crucial to avoid software that imposes constraints on operating flexibility or requires extensive customisations, which can add unnecessary costs and delay implementation.
Instead, deploy flexible, agile software with robust functionality that minimises the need for customisation while offering intelligent synchronisation of automation equipment, robotics, people, and processes to optimise omnichannel operations on a single, integrated, modular platform. This approach ensures optimal omnichannel operations today and in the future, allowing you to deliver on your promise to customers efficiently.
High-volume retailers often leverage separate distribution networks for store replenishment and direct-to-consumer fulfilment, simplifying warehouse design but potentially complicating inventory management and cost control. However, as e-commerce surges, an integrated approach becomes increasingly appealing. Merging e-commerce fulfilment with retail store replenishment within a single warehouse simplifies inventory management and enhances operational flexibility. In the MENA region, where the e-commerce market is projected to soar to AED183.6 billion by 2028, automating these warehouses is crucial.
This integrated strategy offers several benefits: it reduces order cycle times to meet customer expectations more effectively, provides late-stage inventory flexibility to adapt to demand fluctuations, and enables businesses to handle order spikes more efficiently. The result is a streamlined operation that could reduce the need for additional warehouse space
compared to maintaining separate facilities for different channels.
A light-goods shuttle system is ideal for high-volume omnichannel warehouses as it combines high throughput and loadhandling capabilities with unmatched operating flexibility. They can handle cartons (both large and small) and totes or bins in the same system. This unified approach allows products destined for both e-commerce and retail store channels to coexist in a common storage system. Omnichannel retailers benefit from more dynamic options for optimised storage, enhanced control, and improved visibility across warehouse operations, inventory, and material flow.
In an omnichannel environment, some shuttle workstations can be configured to support cluster picking for e-commerce fulfilment. In contrast, others are optimised for picking totes for store replenishment or delivering sequenced cartons to a palletising station. A proven software platform such as Swisslog’s SynQ can orchestrate inventory management,
automation, goods-to-person/manual picking, downstream sortation, labelling, and packing. As a result, the light goods shuttle system can achieve the ultimate blend of speed, efficiency, and flexibility for omnichannel distribution operations.
Automating the omnichannel warehouse through strategic design and deployment of warehouse automation and software, in collaboration with a logistics partner, empowers retailers to achieve several critical goals. Automation streamlines processes, ensuring faster order fulfilment and improved customer satisfaction by reducing order cycle times. It also allows retailers to adapt swiftly to demand peaks and accommodate growth without compromising efficiency, enhancing agility and operational efficiency. Furthermore, automation provides better visibility and management of inventory across channels, enabling more effective inventory control. By adopting a holistic and consultative approach to omnichannel solution design, retailers can optimise overall omnichannel operations, maximising flexibility and efficiency.
Partnership to leverage the extensive network of Widect, a Turkish Airline brand, and AJEX last-mile expertise for efficient and reliable shipping solutions
Left to right: Ibrahim Yigit, Financial and Administrative Manager, Widect; Mustafa Akis, Sales and Operations Manager, Widect; Enes Yilmaz, Managing Director Widect; Mohammed Albayati, CEO, AJEX; Ken Robertson, Chief E-Commerce Solutions Officer, AJEX; Elhadi Seffar - International Sales Director, AJEX Logistics Services; Akin Sakar, International Sales Manager, AJEX.
AJEX Logistics Services (AJEX), a leading Middle East-based specialist in express distribution and shipping solutions, has announced a new strategic partnership with prominent logistics brand Widect, a 100% subsidiary of Turkish Airlines and highly valued partner in e-commerce space. This agreement aims to expand shipping solutions on the Turkiye-(formerly Turkey)-to-Middle East route and enhance last-mile delivery services for the growing e-commerce sector across the MENA region.
As a 100% subsidiary of Turkish Airlines, Widect operations integrate the extensive flight network of Turkish Airlines, providing access to 340 destinations worldwide. Thanks to this latest collaboration, AJEX customers will benefit from daily flights between Istanbul and Riyadh, Jeddah, and Dammam, enhancing the speed of services including last-mile deliveries.
Meanwhile, AJEX will provide its lastmile expertise, including a robust fleet, infrastructure, and distribution services,
alongside customer service excellence, all supported by state-of-the-art technology for fast and flexible deliveries. Together, the partners will leverage their combined capabilities to develop joint projects that expand service offerings and improve operational efficiencies for e-commerce businesses serving the MENA region.
Trade between Turkiye and Saudi Arabia is on the rise, with both countries serving as major aviation hubs in the region.
Direct flights between Istanbul and Riyadh typically take around three to four hours, facilitating efficient business and trade connections. In 2021, Turkish exports to Saudi Arabia reached approximately USD 3 billion, while the trade volume between the two countries rose to USD 8.2 billion in 2022. This upward trend is expected to continue, highlighting the strengthening economic ties between the nations.
The growing e-commerce markets in
both countries create ample opportunities for collaboration, as Turkish products gain traction in Saudi Arabia and vice versa. AJEX is well-positioned to support businesses with its comprehensive suite of customercentric solutions in reaching these key markets, leveraging its expertise in the express and e-commerce categories to facilitate efficient trade flows.
“United by a commitment to delivering superior logistics solutions based on speed, reliability, and agility, AJEX is delighted to announce our new partnership with Widect,” said Mohammed Albayati, CEO of AJEX Logistics Services.
“At Widect, we are collaborating with AJEX to leverage our shared resources and expertise to deliver cutting-edge products that can drive the industry forward. As e-commerce continues to boom and bilateral trade grows, we look forward to our continued partnership to deliver enhanced services and ever greater value to businesses across the region,” Enes Yilmaz, Managing Director of Widect added.
Tarun Joshi, Founder and CEO, IGP
The grand arrival of International Gifts Platform (IGP) in the United Arab Emirates (UAE) in 2023 set a new standard in the realm of gifting experiences.
Celebrating an extraordinary legacy of delivering over 10 million gifts worldwide across 100+ countries, the company unveiled a fascinating plethora of personalised and heartfelt gifts to the region.
IGP Middle East was the first to introduce flower food with bouquets, requiring consumers to add it on alternate days, ensuring a minimum of five-day freshness for all flowers, driving consumer satisfaction and setting a new industry standard.
Global Supply Chain speaks to Tarun Joshi, Founder and Chief Executive Officer of the company to discover how it functions.
GSC: Can you describe the time IGP began its operations in the UAE?
Tarun Joshi: We began our journey sometime during November- December 2023, specifically during the festive period. The event was marked by a specially curated ‘Wall of Delights’ which guided guests to unforgettable surprises, while a personalisation booth offered a gateway to etch one’s name on gifts swiftly and seamlessly with IGP’s personalised touch.
The launch marked the beginning of an era where each gift becomes an extraordinary expression, promising unparalleled gifting experiences for the UAE’s discerning clientele.
GSC: Share some of your plans for the UAE and GCC region.
TJ: The UAE has over 10 million people, out of which 85% are immigrants who want to stay connected to their families and build and enhance their social graph in the UAE. Our primary goal is to help our consumers stay connected to their friends and families back home and to enrich new relationships whether personal or corporate. We look at UAE as our entry into the MENA (Middle East North Africa) region as the culture is very warm and social and similar across the entire region.
GSC: What would you consider your delivery grey areas?
TJ: We’ve worked tirelessly to perfect our supply chain and operations, ensuring there are no grey areas when it comes to delivery. Our dedicated team consistently strives to ensure that all gifts are delivered promptly,
providing the best possible gifting experience for our customers.
GSC. What is the total strength of the company?
TJ: We have a dedicated team in Dubai to oversee the smooth execution of all on-ground tasks, including logistics and operations. They work closely with our head office and central teams based in India and Singapore. While top management is based in India, they travel to Dubai on a monthly basis to gain in-depth insights into the market and ensure the business is running efficiently.
We’re in the business of enriching relationships, and this philosophy resonates throughout our internal team and culture. We seek talent that understands and embodies the pillars of our brand, ensuring that our values are reflected in every aspect of our operations.
GSC: How many areas does IGP operate from the UAE?
TJ: Our operations are spread across Dubai, Sharjah, Abu Dhabi and Ajman.
GSC: Please give us an insight on your expansion plans.
TJ: We have created a state-of-the-art 20,000-square-foot facility in the heart of Dubai and will look at opening similar facilities in Sharjah, Abu Dhabi, Riyadh and Jeddah.
GSC: Where do you see the company in the next five years?
TJ: IGP has a plethora of gifting solutions and has plans to expand operations in Sharjah, Abu Dhabi, Riyadh and Jeddah and our goal is to become the preferred International Gifting Platform for customers across the UAE.
GSC: Could you describe any of the challenges the company faces?
TJ: One notable challenge was the lack of a well-established supply chain and the need for a captive last-minute delivery network.
Adapting to the dynamic digital landscape, where technological advancements and changing consumer behaviours require constant evolution. Lessons learned emphasised the importance of adaptability and staying attuned to market dynamics. The key factors propelling our success includes a commitment to innovation, a customercentric approach, and the ability to identify and capitalise on emerging trends.
Commitment to Sustainability: IGP Middle East emphasises on reducing its carbon footprint through eco-friendly packaging, optimised transportation, and warehousing practices.
Support for Farmers: The company has trained over 10,000 farmers, standardising processes to ensure a high-quality produce and support local agricultural ecosystems. Product Longevity: IGP has implemented measures to enhance product longevity, including introducing flower food for bouquets to ensure freshness for at least five days. Use of AI (Artificial Intelligence) and ML (Machine Learning): Leveraging AI and ML for route optimisation and infrastructure reassessment has helped reduce emissions and optimise distribution efficiency.
Comprehensive Support for Artisans and Growers: Through training and market insights, the company helps uplift over 10,000 artisans and growers, fostering economic empowerment.
Global Presence and Ethical Gifting: With services reaching over 100 countries, IGP promotes sustainable practices while enhancing the emotional impact of gifting with a positive environmental focus.
By fostering a culture of purposeful leadership and investing in talent, we cultivated an agile and innovative team that has been instrumental in our rapid growth.
GSC: With this being the Year of Sustainability in the UAE, what are your plans for the country and region as a whole?
TJ: We want the world to be a happy place and we strive to ensure to give back to the society and the environment at large. We therefore monitor the carbon footprint of every single product including the flower stems used in our bouquets and make sure that we run a carbon neutral organisation.
• IGP holds the Guinness World Record for the longest chain of bracelets made using over 125,000 Rakhis (festive threads).
• The company’s international operations are India, Singapore, and Dubai.
Sustainability has become a global priority, with businesses, governments, and individuals recognising the urgent need to address environmental challenges. Noman Ali, Founder & CEO, Inv-X Technologies Limited, offers a perspective on what this means for the region.
For Saudi Arabia, sustainability is a critical pillar of Vision 2030, a transformative plan to diversify the nation’s economy, reduce its dependence on oil, and promote sustainable development.
However, despite the growing emphasis on sustainability, several organisations still struggle to embrace and implement sustainable practices. A key reason behind this hesitation is the perceived cost of integrating sustainability into business operations. Sustainability is largely seen as an additional expense rather than a valuecreating strategy.
This is where the concept of an Integrated Circular Supply Chain (ICSC) comes into play. Rather than viewing sustainability as a cost burden, the ICSC model enables organizations to turn it into a driver of operational efficiency and competitive advantage. By reducing inventory obsolescence, minimizing waste, and fostering collaboration across industries, the ICSC offers a pathway to sustainable growth that aligns with both environmental and business goals.
Numerous organisations are aware of the benefits of sustainability, but achieving concrete results often seems elusive.
From the high cost of transitioning to renewable energy to the complex logistics of waste management, the journey toward sustainability is filled with perceived barriers. For most businesses, sustainability initiatives are a direct hit to the bottom line, requiring upfront investment without the immediate promise of returns.
Furthermore, companies that operate within traditional linear supply chains find themselves constrained by the limitations of a “take-make-dispose” model. This approach, in which resources are extracted, products are manufactured, and waste is discarded, contributes to environmental degradation, resource depletion, and rising costs for companies dealing with unused or obsolete inventory. As a result, while organizations may desire to be sustainable, they often lack the means or knowledge to make the transition.
An Integrated Circular Supply Chain challenges the linear model by creating a closed-loop system where resources are continuously reused, shared, or repurposed across different sectors and industries.
The ICSC model is not merely a tool for reducing waste but a holistic approach, powered by technology, to managing resources efficiently, ensuring that products and materials stay in circulation for as long as possible. This is done through repair, recycling, refurbishing, or redistributing materials between businesses.
In the ICSC model, sustainability is not an add-on or an extra cost—it is built into the very fabric of supply chain management. The goal is to cut down on unnecessary production, reduce waste and emissions, and optimize inventory levels by connecting multiple organizations in a single, seamless value chain. In doing so, businesses can mitigate the impact of inventory obsolescence, reduce waste
disposal costs, and unlock new revenue streams by redistributing or reusing excess or non-moving inventory.
Resource Efficiency: The ICSC ensures that materials are used to their fullest potential. Rather than letting excess inventory become obsolete, companies can find new uses for them, either within their operations or by collaborating with other businesses that can benefit from the excess.
Collaborative Networks: The ICSC creates a network where different industries share resources and collaborate on sustainability initiatives. For example, a manufacturing company may provide surplus raw materials to another company in a different industry, reducing waste while creating a new revenue stream.
Waste Reduction: By rethinking how resources are managed, the ICSC aims to minimize waste across all stages of the supply chain. This includes reducing overproduction, preventing inventory obsolescence, and finding innovative ways to repurpose unused materials.
Cost savings and profitability: By focusing on sustainability, companies can lower costs associated with waste disposal, inventory management, and supply chain inefficiencies. These savings, combined with the potential to generate revenue from unused inventory, make the ICSC a financially viable strategy.
Compliance and reputation: With growing pressure from consumers, regulators, and investors for more responsible business practices, adopting the ICSC can help organisations meet regulatory requirements and build a strong, sustainability-focused brand image.
Inv-X Technologies, with its SaaS B2B platform, is dedicated to smart liquidation of excess and non-moving inventory across the industry. Inv-X plays a pivotal role in helping businesses adopt the ICSC model by providing the tools and platform needed to manage inventory efficiently, reduce waste, and drive sustainability. The Inv-X’s platform
facilitates the identification, tracking, and redistribution of excess inventory across industries. Rather than allowing non-moving inventory to sit idle, taking up space and losing value, Inv-X enables businesses to list their surplus products on a digital marketplace, wherever other companies can purchase or repurpose them.
Inventory Optimisation: By offering realtime visibility into excess and non-moving inventory, Inv-X helps organisations avoid unnecessary production and reduce overstocking. This minimises waste and lowers the environmental impact of manufacturing and disposal.
• Cross-Industry Collaboration: Inv-X’s platform encourages collaboration between companies from different sectors, fostering the creation of a circular supply chain network. Businesses can discover potential buyers or partners who can repurpose their excess inventory, turning waste into a valuable resource.
• Cost Reduction: Through efficient inventory management, companies can reduce the costs associated with waste disposal, storage and related factors. Moreover, by selling unused inventory through Inv-X’s platform, organizations can unlock new revenue streams that offset the costs of sustainability initiatives.
• Environmental Impact: By minimizing the need for new production and promoting the reuse of materials, Inv-X directly contributes to reducing emissions, lowering energy consumption, and conserving natural resources. This aligns with the Kingdom’s Vision 2030 objectives of promoting environmental stewardship.
• Streamlined Onboarding and Analytics: Inv-X provides businesses with easy-to-use onboarding processes and robust analytics to track sustainability metrics. This allows companies to quantify their environmental impact, demonstrate progress, and make data-driven decisions for continuous improvement.
Noman Ali is a seasoned expert in supply chain management, with over 20 years of strategic and operational experience. Throughout his career, he has held pivotal roles in multinational firms across diverse industries such as pharmaceuticals, textiles, and FMCG. Companies like Unilever, Siemens, and Sanofi have benefited from his expertise. He is the Founder and CEO of Supply Chain Talks and Inv-X Technologies, offering consultancy, training, sustainability solutions and executive headhunting.
In an increasingly interconnected world, businesses cannot afford to operate in isolation, especially when it comes to sustainability. The Integrated Circular Supply Chain represents a forwardthinking approach that not only addresses environmental concerns but also opens new opportunities for collaboration, innovation, and profitability.
Inv-X’s role in facilitating this transition is critical. By offering a platform that seamlessly connects businesses and helps them manage inventory in a sustainable way, Inv-X empowers organizations to turn sustainability from an expense into an asset. With the support of such technologies and frameworks, companies can make meaningful strides toward achieving their sustainability goals and contribute to the Kingdom’s Vision 2030 objectives. By adopting the ICSC model and leveraging Inv-X digital B2B platform, businesses can achieve a balance between environmental responsibility and operational success, ultimately redefining what it means to be sustainable in today’s global economy.
• 16 MoUs with leading companies to expand collaborations in the energy, chemicals, refining, industrial, healthcare, and aviation sectors.
• Partnerships with Aramco Digital, SAP, and Oracle valued at over SAR 300 million (over USD 81 Million) to digitalize and advance the transformation of the supply chain and procurement landscape.
• Company unveils new headquarters at the Asharqia Chamber of Commerce Tower, Dammam, Saudi Arabia
ASMO (Advanced Supply Management Operations), a joint venture established by DHL and Aramco through the Saudi Aramco Development Company, has signed Memorandum of Understandings (MoUs) with industry leaders and agreements with multinational technology providers to advance its vision to be a supply chain market leader in the Middle East and North Africa (MENA) region. The company launched earlier this year to meet the energy, chemical, and industrial sectors’ complex end-to-end supply chain and procurement demands.
As Saudi Arabia’s first procurement and supply chain services hub of its kind serving the region’s energy, chemical, and industrial sectors, ASMO has signed 16 MoUs with industry leaders across multiple sectors, to explore value-creation opportunities and create more resilient, efficient, sustainable, and integrated end-to-end supply chain services. Also, ASMO signed agreements worth over SAR 300 million (over USD 81 Million) with Aramco Digital, SAP, and Oracle to accelerate its digital transformation and
drive operational excellence across the supply chain and procurement landscape in Saudi Arabia. The signings took place at ASMO’s new headquarters at the Asharqia Chamber of Commerce Tower, Dammam.
“Today, I am proud to announce our strategic partnerships that are in line with Vision 2030 objectives and contribute to the Kingdom’s economic growth by creating a more resilient, efficient, and sustainable supply chain ecosystem. We aim to enable our customers to focus on their core business activities while benefiting from improved service levels, reduced carbon emissions, and enhanced operational efficiency, helping them to pursue and attain new growth opportunities. The establishment of our new headquarters at the Asharqia Chamber of Commerce Tower in Dammam and these newly concluded partnerships and MoU signings represent a defining chapter in ASMO’s journey,” said Salem Al Huraish, ASMO Chairman.
ASMO’s strategic partnerships with leading technology providers will enable ASMO to leverage innovative technologies and solutions to optimize its supply chain services, finance, and HR operations. Through collaborations with Aramco Digital, SAP, and Oracle, ASMO will implement advanced ERP systems, procurement control towers, and B2B eMarketplace to enhance decision-making, asset utilization, and operational efficiency. These partnerships aim to streamline planning and procurement functions, automate finance and HR processes, and improve overall productivity and employee experience.
The 16 MoUs aim to identify opportunities to create value, drive
efficiencies across supply chain operations, and support growth:
• In the chemical and refining sectors, ASMO signed MoUs with Luberef, Rabigh Refining and Petrochemical Co (Petro Rabigh), Saudi Aramco Jubail Refinery Company (SASREF), Saudi Aramco Total Refining and Petrochemical Company (SATORP), and Yanbu Aramco Sinopec Refining Company (YASREF).
• In the energy sector, MoUs have been signed with Baker Hughes, Cameron AlRushaid, Halliburton, Schlumberger Middle East S.A. (SLB), and Weatherford.
• In the global manufacturing sector, MoUs have been signed with ArcelorMittal, Jubail Energy Services Company (JESCO), Tenaris, and Vallourec.
• In the aviation and healthcare sectors, MoUs have been signed with Aloula Aviation and Johns Hopkins Aramco Healthcare (JHAH).
The new headquarters is an eightfloor, LEED-certified facility anticipated to accommodate over 1,200 employees. ASMO is focused on leveraging innovative technologies to deliver substantial value to its partners and customers, helping to drive innovation, efficiency, and sustainability in supply chain and procurement operations.
With these developments, the joint venture is well-positioned to become a key player in redefining the procurement and supply chain landscape across the energy, chemical, and industrial sectors. By leveraging innovative technologies and aligning with Saudi Arabia’s Vision 2030, ASMO aims to deliver substantial value to its partners and customers in the Kingdom and the wider MENA region.
Addverb, a global robotics company, excels in tailored warehouse automation solutions, redefining innovation in the supply chain with intelligent robots driven by modular software and boosting a diverse product portfolio for end-to-end operational efficiency.
As the region witnesses a rise in its logistics and warehousing activities driven by Saudi Arabia’s massive investments, more and more customers are embracing automation to address the challenges in Warehouse Logistics or Intralogistics. Logsquare, with its tailored solutions and advanced technology integration, is expanding to Saudi Arabia, setting up an office in Riyadh. We discuss this with industry veteran Jean-Maroun Zacca, Logsquare Country Manager, Saudi Arabia.
By establishing a new office Logsquare KSA is working closely with new customers in various verticals, such as e-commerce, automotive, pharma, retail, beverage, and general warehousing, to deliver proven, reliable engineered solutions that meet the requested applications.
Logsquare’s plans are ambitious in KSA, and it looks forward to a prosperous future.
GSC: How has Logsquare established itself as one of the pioneers of logistics from the time of its inception?
Logsquare (LS) provides Intralogistics Specialised Materials Handling Solutions within the supply chain across multiple industries. We followed two approaches that helped us become a pioneer of Intralogistics solutions in the last 15 years:
a. LS focused on business partnerships with leading OEM vendors, which created a synergy between technological know-how and local engineering knowledge.
b. LS followed a tailor-made solution approach, as opposed to a one-size-fits-all
methodology, that ensured Customers got precisely what they needed each time.
Moving forward, the company has built up on its success stories and repeat customers to establish itself as a pioneer of Intralogistics solutions.
GSC: With its unmatched ability to offer a complete range of comprehensive integrated solutions, how does the company enter strategic partnerships?
Logsquare solutions range from consulting to equipment provision, system integration, and advanced IT packages. Engineering is our core strength, and this is where the focus, dedication, and momentum of our people and our management play a pivotal role in building trust with customers. This dedication has helped us forge strong alliances with existing customers and partners over the years.
Moreover, our commitment to quality was always the key to selecting our OEM partners and establishing a strategic partnership with them.
GSC: What are some of the mega projects that Logsquare has helped facilitate across the Middle East?
In the realm of E-commerce, LS has achieved several remarkable milestones, particularly in recent years. Here are a few notable projects:
Landmark Group: LS engineered and installed the High Bay Warehouse (Rack Clad) for Dematic: 36,000 pallet positions, 43m high.
Emirates Flight Catering (EKFC 3): LS delivered the complete Material Handling and Automated Storage System, including the multi-story conveyor system running within the building and servicing its different tasks.
Mondelez International: LS delivered the high-density automated storage system with 11,000 pallet positions and 25m high, along with the entire software suite.
The services were in partnership with Noon, Amazon, Areej, Shaya and others.
GSC: How many people make up the organisation and what is the next major event the company is looking forward to?
The Logsquare core team currently consists of around 30 professionals distributed throughout the company’s departments, such as engineering, software, operations, and administration. An additional workforce handles project executions and after-sales
services like preventive maintenance and customer support. The team is continually enriched with new talent from the region.
GSC: Any final thoughts about the future of the company.
We would like to mention that Logsquare invested in its own Experience Centre where products and software can be tested to ensure adequate system performance and reliability. Customers are welcome to visit our facility and witness a running cross-belt sorter loop, a robotic palletizer and AMR and ASRS deployed systems.
Jean-Maroun Zacca, a veteran in Material Handling Systems, with 24 years of experience in the Intralogistics industry, has led branding projects with leading companies in the region. Currently, Jean-Maroun serves as the Country Manager for Saudi Arabia, where he is dedicated to developing the business of Logsquare in this fast-growing market. Jean-Maroun holds an engineering degree and has acquired various certificates during his long career.
Group
United Diesel, a member of the Al Rostamani Group, proudly marked its 50th anniversary, celebrating five decades of significant contributions to the UAE’s transport and logistics sector.
To celebrate this milestone, Al Rostamani Group hosted a grand event in Dubai, attended by distinguished figures from the transport and logistics industry, senior management from Al Rostamani Group and United Diesel, as well as long-standing partners Renault Trucks, Tata Motors, UD Trucks, and Daewoo Trucks. United Diesel recognised its partners in a special ceremony, which included video messages of goodwill and appreciation from each brand.
Since its establishment in 1972, United Diesel has been providing customercentric, innovative, and advanced transport solutions, establishing itself as a leader in the UAE’s logistics infrastructure. The company has consistently set itself apart by adopting the latest global technologies to improve transport efficiency and meet the varied needs of its clients. Beyond providing high-quality products, United Diesel has prioritised the development of comprehensive after-sales services and maintenance programs, ensuring the ongoing high performance of its vehicles.
The anniversary event featured a panel discussion with participation from Al Rostamani Group CEO Mazen Dalati, Chief Human Capital and Transformation Officer Abdulrahman Saqr, and United Diesel’s General Manager David Sawiras. They highlighted the core values of Al Rostamani Group: commitment, care, and vision, which continue to guide its strategic transformation.
Mazen Dalati, CEO of Al Rostamani Group, expressed his pride in the company’s longevity, stating: “Only 4 percent of companies make it past 50 years, and we are incredibly proud that United Diesel has joined this exclusive club. This milestone is not just a testament to our resilience and adaptability, but also to the trust and loyalty of our customers and partners. As we look to the future, we remain committed to driving innovation and sustainability in the transport sector, ensuring that we continue to play a key role in the UAE’s growth and development.”
Abdulrahman Saqr, Chief Human Capital and Transformation Officer, said: “Our focus on smart infrastructure and sustainable modernization reflects our commitment to transforming United Diesel from a strong company to an even stronger one, ensuring
we not only meet but exceed the evolving needs of our industry and community. The values of commitment, care, and vision are deeply ingrained in our strategy and drive every decision we make.”
David Sawiras, General Manager of United Diesel, reflected on the company’s journey. He said,”As we celebrate 50 years of United Diesel, we honour the vision of our late founder, Mr. Abdulla Hassan Al Rostamani, who set out to build a company that would be a cornerstone of the UAE’s growth. Today, our focus is on embracing new technologies and leading the way in sustainable mobility solutions, ensuring that we continue to meet the evolving needs of our customers and contribute to the UAE’s ambitious goals for the future.”
As it celebrates 50 years, United Diesel remains committed to expanding its product portfolio with smart, environmentally friendly transport solutions, in line with the UAE’s goals to reduce carbon emissions and achieve carbon neutrality. Looking ahead, United Diesel announced exciting new partnerships with Yutong electric trucks, CHL material handling equipment, and StarkGen generators, further reinforcing the company’s role as a key driver of innovation in the transport and logistics sector.
In today’s fast-paced, interconnected world, businesses across industries must stay agile and adaptable, especially in sectors where consumer expectations are constantly evolving. The fashion and sportswear industry, driven by seasonal trends and the rapid rise of e-commerce, exemplifies such a sector. For one of the world’s leading third-party logistics (3PL) providers operating in this space, omnichannel fulfilment presented a formidable challenge.
Maersk managed an extensive fulfilment network, handling both business-to-business (B2B) and business-to-consumer (B2C) orders for their fashion and sportswear clients. The facility was facing a complex challenge: to keep up with fluctuating customer and supplier demands, maintain high accuracy levels, and streamline a vast inventory of over 68,000 SKUs—all while optimizing costs and ensuring timely deliveries.
Faced with the need to transform their fulfilment operations, Maersk turned to a solution that combined advanced automation and industry expertise. Addverb, a globally recognized leader in robotics and warehouse automation, delivered just that. With Addverb’s support, Maersk successfully implemented an automated omnichannel
fulfilment system, significantly enhancing efficiency, reducing errors, and optimizing their entire operation.
The fashion and sportswear business are inherently dynamic. Seasonal peaks—such as Black Friday and Christmas — place immense pressure on 3PL providers to manage sudden surges in demand. For Maersk, the challenge was especially complex. They needed to handle a vast volume of orders and returns, often under tight deadlines. In addition to seasonal fluctuations, the diversity of their inventory added another layer of complexity. With 68,307 unique SKUs—comprising 60% footwear, 30% apparel, and 10% accessories— Maersk required a solution that could
efficiently manage this range of products while ensuring high levels of order accuracy.
Another significant hurdle was the growing demand for omnichannel fulfilment, where customers expect seamless experiences whether shopping online, instore, or a combination of both. This meant that the 3PL provider needed a system capable of rapidly processing both B2B and B2C orders, without compromising on speed or accuracy.
The stakes were high: failure to meet these challenges would result in delayed deliveries, increased returns, customer dissatisfaction, and lost revenue. The provider needed to transform their existing system into an operation that could not only handle peak demands but also ensure smooth, yearround operations.
Addverb’s Comprehensive Solution: Automation tailored to omnichannel needs
For this project, Addverb brought a comprehensive suite of advanced automation technologies, including Autonomous Mobile Robots (AMRs), Automated Storage and Retrieval Systems (ASRS), and intelligent software solutions to streamline the Maersk operations. These technologies were tailored to meet the specific needs of omnichannel fulfilment.
Fixed and Flexible Automation
At the core of Addverb’s solution was a blend of fixed and flexible automation. To maximise space utilisation, streamline order processing, and manage complex inventory flows, Addverb integrated multiple systems:
• Autonomous Mobile Robots (AMRs): These robots enabled flexible material movement throughout the warehouse, ensuring fast and efficient order picking and replenishment. Their autonomous navigation facilitated real-time adaptability in inventory management.
• Automated Storage and Retrieval Systems (ASRS): With both pallet and carton shuttles, the ASRS optimised storage density and prioritised orders. This system significantly reduced retrieval times, accelerating order processing, particularly during peak periods.
• Multi-Carton Robot System: Designed for returns processing, this system automates sorting and handling of returned items, streamlining the returns workflow, which is critical in the fashion industry, where returns rates can reach 30%.
• Carton Shuttle and Sortation Robot (Quazzy Solution): These robots facilitated rapid order consolidation, especially for B2C orders with higher item volumes, ensuring efficient dispatch.
• Mixed-Case Palletisers and Box-It Workstations: Ergonomically designed to reduce manual labour, these stations integrated seamlessly with automated systems, allowing operators to interact with automation safely and efficiently.
• Strategically Planned Conveyor Lines: Addverb designed conveyor systems to transport goods between zones, reducing bottlenecks and increasing throughput.
Central to the success of this solution was Addverb’s proprietary Warehouse Execution System (WES), Concinity. This AI-powered platform orchestrated the entire facility’s operations, ensuring all components— from AMRs to ASRS—worked together seamlessly. Concinity provided real-time visibility into inventory levels and order status, dynamically adjusting picking and routing strategies to optimise material flow throughout the warehouse.
The software integrated smoothly with the provider’s existing Warehouse Management System (WMS), Warehouse Control System (WCS), and Fleet Management System, ensuring a smooth, non-disruptive transition to automation. By coordinating the various automated elements, Concinity enabled faster, more reliable, and more accurate fulfilment.
The impact of Addverb’s solution was transformative. It streamlined operations, reduced errors, and significantly improved key performance metrics:
• Dispatches 100,000 pieces daily to 2,500 distribution nodes.
• Sorts 3,600 items per hour with a doublelayer sortation system and 300 bin locations.
• Achieves the throughput of 125 Tasks/ hr as single and double cycles through Autonomous Mobile robots.
• Achieves throughput of 150 Pallets in/hr * and 150 Pallets out/hr through Pallet ASRS.
• Achieves throughput of 1600 Totes in/hr and 1,600 Totes out/hr through Tote ASRS.
• Total of 14 GTP Stations achieves picking throughput 110 totes per station/ hour (* indicates per hour)
These KPIs highlight the efficiency gains from integrating Addverb’s automation technologies and intelligent software. The combination of hardware and software enabled the 3PL provider to exceed their fulfilment targets, setting a new standard for omnichannel fulfilment.
Beyond the physical components, Addverb’s AI-driven Concinity software unlocked the full potential of automation. By continuously analysing warehouse data, it optimised picking strategies and route planning, allowing Maersk to respond to demand changes in real time.
With real-time inventory visibility, stockouts were reduced, and customer satisfaction is enhanced. The seamless integration of data across systems fosters collaboration and communication, further boosting efficiency.
Addverb’s innovative solution not only met but exceeded the expectations of Maersk. By combining advanced robotics, flexible automation, and intelligent software, Addverb has set a new benchmark for omnichannel fulfilment. As the future of fulfilment continues to evolve, Addverb’s commitment to innovation positions them as a leader in the transformation of smart, sustainable, and highly automated warehouse systems.
Industrial design is a unique field where creativity meets functionality, offering the opportunity to impact people’s lives through the creation of products, services, and systems. It’s an incredibly rewarding career for those who are passionate about solving real-world problems and improving user experiences.
Dr. Ahmed Kassab, Assistant Professor of Industrial Design at Effat University a highly respected industrial design expert and consultant, widely regarded as the “Godfather of Industrial Design in the Middle East” highlights more about this fascinating industry.
Industrial design involves developing products that are both practical and aesthetically pleasing. Think of everything from smartphones to furniture, cars to kitchen appliances. Industrial designers make sure these items are not only useful but also look and feel great.
GSC: What is industrial design, and how does it differ from other design disciplines?
Industrial design is the practice of designing products, both physical and digital, as well as services and systems, with the aim of improving how users interact with the world around them. Unlike other design disciplines—such as graphic or interior design, which may focus primarily on aesthetics or specific environments— industrial design is concerned with
functionality, manufacturability, and user experience. It blends creative thinking with technical expertise to deliver solutions that not only look good but also work well and are efficient to produce. Industrial designers often operate at the intersection of art, science, and business, creating products and services that meet user needs and business objectives.
GSC: What are the key skills required for a successful career in industrial design?
A successful industrial designer must possess a blend of creative and technical skills. Key competencies include a deep understanding of materials, manufacturing processes, and human-centred design principles. Proficiency in digital tools, such as CAD (Computer-Aided Design) software and rendering programs, is essential for
visualizing and prototyping concepts. Strong problem-solving abilities are crucial, as designers often need to address complex challenges. Communication and collaboration skills are also important for working with multidisciplinary teams, including engineers and marketers. Ultimately, adaptability and a passion for continuous learning will set a designer apart in this rapidly evolving field.
GSC: How do industrial designers approach the process of creating a new product?
The industrial design process begins with user research to identify problems, needs, or opportunities. From there, industrial designers move into ideation, generating a wide range of potential solutions through sketching and brainstorming. As ideas are
“I’ve found that the best designs always emerge from a deep understanding of the people who will interact with them.”
refined, digital models are created, often using CAD software, followed by prototyping to test functionality and usability. Throughout this process, feedback from users, engineers, and other stakeholders is critical for refining the design. Industrial designers continuously balance form, function, user experience, and manufacturability, ensuring that the final product not only meets aesthetic and functional requirements but can also be produced efficiently.
GSC: What role does user research play in industrial design?
User research is fundamental to the industrial design process. It provides the insights needed to design products, services, and systems that truly meet users’ needs. Through techniques such as interviews, observations, and surveys, industrial designers can better understand user pain points, preferences and behaviours. This research helps to inform design decisions, ensuring that the final product or service is intuitive, efficient, and enhances the user experience. In my career, I’ve found that the best designs always emerge from a deep understanding of the people who will interact with them.
GSC: How do sustainability and environmental concerns influence industrial design today?
Sustainability is no longer a peripheral concern—it’s a central component of industrial design. Designers are now tasked with creating products that reduce environmental impact, use sustainable materials, and minimize waste across the product lifecycle. This involves not only selecting eco-friendly materials but also designing products that are durable, repairable, and recyclable. In the context of Saudi Arabia and Vision 2030, sustainability plays a crucial role, with a strong emphasis on designs that contribute to environmental stewardship while still meeting modern consumer needs. Industrial design today must balance innovation with environmental responsibility.
Dr. Ahmed Kassab is an Assistant Professor of Industrial Design at Effat University and a highly respected industrial design expert and consultant, widely regarded as a pioneering figure in the Middle East. Known as the “Godfather of Industrial Design in the Middle East,” he brings over 20 years of experience spanning product design, automotive design, furniture design, home appliances, industrial engineering, electrical transformer projects, and more.
Dr. Kassab has made significant contributions as a consultant, advising on numerous high-impact projects that shape the cultural, industrial, and educational landscape. As the Vice President of the Industrial Design Division at the Saudi Umran Society, he focuses on enhancing industrial design’s role within the community, fostering collaboration and innovation among designers and stakeholders. Additionally, as the founder of Saudi Industrial Design Week, he creates opportunities for designers to connect with industry leaders and showcase their work.
In addition to his extensive industry expertise, Dr. Kassab has made significant contributions to design education worldwide. He has developed bachelor’s, master’s, and PhD programs for several leading universities globally, playing a key role in shaping the future of industrial design education.
His work has left a lasting legacy in industrial design, driving innovation and raising the profile of the discipline throughout the Middle East and beyond. A passionate advocate for the power of design, Dr. Kassab continues to mentor and inspire young designers while offering expert consultation across various industries. Committed to fostering innovation and sharing expertise, Dr. Kassab remains a valuable asset to any project, consistently pushing the boundaries of design excellence.
Top 5 Highlights of Industrial Design:
1Industrial Design’s Purpose: It focuses on creating functional and aesthetically pleasing products that enhance user experiences.
2Key Skills: Industrial designers need creativity, technical expertise, problem-solving, and proficiency in digital design tools like CAD.
3
Design Process: The process involves research, ideation, prototyping, and refining products based on user and stakeholder feedback.
4Sustainability: Modern industrial design emphasizes eco-friendly materials, durability, and waste reduction.
5
Collaboration: Designers collaborate with engineers and marketers while being mindful of cultural and social contexts in product development.
GSC: What technologies and tools are commonly used in the industrial design process?
Industrial designers rely heavily on digital tools throughout the design process. CAD software like SolidWorks and Rhino are used to create detailed 3D models and test the feasibility of designs. Rendering tools such as KeyShot help visualise how products will look and feel in real environments. Rapid prototyping technologies, including 3D printing, allow for the creation of physical models quickly and affordably, enabling iterative testing and refinement. In addition, user experience (UX) design tools are increasingly important as industrial design expands into digital products and services. These technologies enable designers to simulate, test, and improve both physical and digital products before production.
GSC: Can you share examples of successful industrial design projects and their impact on users?
One example is the Smart Life Vest, a graduation capstone project I supervised for my student Areej Alghonaim. This design incorporates sensors and smart technology to enhance swimming safety, functioning as a traditional life vest while also monitoring user distress and automatically inflating when needed.
Another notable project is a children’s furniture piece that merges play with functionality, which I supervised my student Layan Alhamed. This design fosters creativity in children while providing practical benefits for parents. Both projects demonstrate how industrial design can significantly improve user experiences, making products safer, more efficient, and enjoyable. Beyond academic projects, I also supervised the Shada Hotels Project, where students designed unique solutions tailored for the luxury hospitality experience. This
project allowed students to apply their skills in a real-world context, directly contributing to the guest experience of Shada Hotels. Additionally, through a collaboration with AlBalad Development Company, our students created products and user services for historical Jeddah, merging traditional craftsmanship with modern design practices. These projects highlight the broader impact of industrial design beyond classrooms, fostering real-world skills and bridging industry and academia.
All of these projects demonstrate how industrial design can significantly improve user experiences, whether by enhancing safety, promoting creativity, or preserving cultural heritage through innovative design.
GSC: How important is collaboration with engineers and marketers in industrial design?
Collaboration with engineers and marketers plays a significant role in industrial design, yet it’s crucial to acknowledge the unique strengths of industrial designers themselves. Designers are equipped with the skills to manage the entire design process, from ideation to manufacturing. This autonomy allows them to create innovative solutions that meet user needs while considering manufacturability and cost-efficiency.
While engineers provide valuable insights into technical feasibility, industrial designers are often capable of implementing design for manufacturing (DFM) principles independently. This enables them to ensure that their concepts can be effectively produced without heavy reliance on engineering intervention.
Marketers, on the other hand, contribute essential knowledge about consumer desires and market trends, helping to shape a product’s positioning. However, industrial designers are adept at synthesizing this information to craft designs that resonate with users and align with market demands.
In many of my projects, including collaborations with organisations in Saudi Arabia, I have witnessed how the comprehensive skill set of industrial designers leads to impactful products. While collaboration can enhance outcomes, the ability of designers to independently navigate the design process empowers them to innovate and create solutions that effectively address user needs.
GSC: How does industrial design address cultural and social issues in product development?
Industrial design must be culturally sensitive and socially aware. Industrial designers need to consider the cultural context in which their products will be used, ensuring that they respect local values, traditions, and social norms. In regions like the Middle East, understanding these cultural aspects is critical to developing products that resonate with users. Socially, designers are increasingly tasked with addressing issues such as accessibility, inclusivity, and sustainability, ensuring that their products contribute positively to society as a whole.
GSC: Why pursue industrial design?
Industrial design is a unique field where creativity meets functionality, offering the opportunity to impact people’s lives through the creation of products, services, and systems. It’s an incredibly rewarding career for those who are passionate about solving real-world problems and improving user experiences. Industrial designers get to innovate across a broad spectrum of industries, from consumer electronics to healthcare and sustainability.
In Saudi Arabia, there are a lot of job opportunities in industrial design, especially with the implementation of Vision 2030, which aims to diversify the economy and promote innovation. This vision not only fosters growth in various sectors but also creates a demand for skilled industrial designers who can contribute to this transformation.
For me, industrial design has always been about pushing boundaries and creating solutions that make a tangible difference in the world. It’s a dynamic and evolving field that challenges you to keep learning, adapting, and driving innovation.
10 – 11 December 2024
Dubai World Trade Centre
Secure your spot at Dubai's premier logistics & mobility event
Launch Edition
Collocated with: Meet 2,000+ Visitors Join our Mainstage Conferences Network with 125+ Speakers
Globally companies have found that use of technology is one of the most optimum ways to go. Transforming supply chains through digitalisation can make processes more efficient, transparent, and responsive. Bachir Sentissi, Co-Founder, Atracio explains how the use of RFID, blockchain, IoT (Internet of Things) sensors, and Artificial Intelligence (AI) all play a part in this evolution, reducing costs and enhancing decision-making.
The rapid digitalisation is partly happening through the adoption of a wide range of new technologies commonly called Industry 4.0 technologies. One technology that has had a major impact on SCM is the IoT and more specifically the Radio Frequency Identification, referred to commonly by its acronym: RFID. “At Atracio, we have indepth expertise of partnering with leading organizations in the world to leverage the financial and operational value-add of RFID implementation. Before any RFID transformational journey it is very important to understand what RFID is and how and it can concretely contribute to the top and bottom-line of a business,” says Sentissi. RFID is a wireless communication
technology used to capture data, which may be linked to different identification attributes of entities carrying RFID labels (tags).
Initially dubbed as a ‘wireless barcode’, RFID goes beyond the capabilities of barcode identification by being able to be read in bulk, without a line of sight, from a distance reaching 10 meters.
One of the key advantages of RFID tags is the universally unique identifier associated with each individual tag thanks to its EPC. The Electronic Product Code (EPC) is a comprehensive numbering system created to uniquely identify physical objects and their groupings. It uses a large code structure that can incorporate all existing and future naming conventions, adhering to industry standards such as those established
by GS1, including the Uniform Product Code (UPC) among others.
The EPC is designed to be universally recognized and primarily links physical items to networks, serving as an effective informational reference.
EPCIS stands for Electronic Product Code Information Services. It’s a standard designed to enable the sharing of information about the movement and status of goods in the supply chain. Developed by GS1, EPCIS allows organizations to capture and share data about products, including their location, condition, and handling throughout their lifecycle.
The main components of EPCIS include:
1. Event Data: Information about specific events in the supply chain, such as shipping, receiving, and inventory changes.
2. EPC (Electronic Product Code): A unique identifier for each item, allowing for tracking and tracing.
3. Visibility: Enhances supply chain visibility by providing real-time data that can be accessed by authorized stakeholders.
EPCIS is widely used in industries like retail, pharmaceuticals, and food safety to improve transparency, compliance, and efficiency in supply chain operations.
EPCIS is closely integrated with RFID (Radio Frequency Identification) technology to enhance supply chain visibility and efficiency. Here’s how they work together:
1. Unique Identification: RFID tags equipped with EPCs (Electronic Product Codes) provide unique identifiers for items. This allows for precise tracking of products as they move through the supply chain.
2. Data Capture: RFID readers capture data from the tags automatically and in realtime. When an RFID tag is read, the EPCIS standard helps to structure this data into meaningful events.
3. Event Tracking: EPCIS defines various events related to the movement and status of products, such as “Object Registered,” “Object Dispatched,” or “Object Received.” This structured event data allows organizations to track the entire lifecycle of a product.
4. Visibility and Reporting: By using EPCIS, businesses can aggregate and share event data across systems and partners, improving visibility into inventory levels, shipment statuses, and supply chain processes.
5. Interoperability: EPCIS facilitates interoperability among different systems and technologies in the supply chain, making it easier to integrate RFID data with other enterprise systems like inventory management or ERP.
6. Compliance and Traceability: In regulated industries, EPCIS supports compliance by providing traceability and ensuring that detailed records of product movement are maintained.
Overall, the combination of EPCIS and RFID enhances the ability to track products in real-time, streamline operations, and improve decision-making in the supply chain.
Standardization has always been a catalyzing factor to disseminate innovation, assure safety and reliability for consumers and allow the interoperability of devices and software entities. In the realm of RFID and sensors, standards offer a unified framework that ensures seamless interaction between tags, readers, and software architectures, even when developed independently by different vendors. In global RFID deployments, like those in supply chain applications, these standards and their architectures are vital for data collection and sharing between business partners. As a result, standards are essential components in a globalized world, benefiting businesses, consumers, innovators, and governments alike. This adoption of RFID technology has been adapted to a large number of applications across various industries:
• Retail Management: RFID tags are extensively used in retail to optimize inventory management, prevent theft and enhance customer experience.
• Supply Chain Management: RFID tags track goods through the supply chain from manufacturing to distribution to retail.
• Asset Tracking: Many organizations use RFID to track assets such as machinery, equipment, and vehicles.
• Access Control: RFID is a common technology for controlling access to buildings (for personnel) or to parking lots (for vehicles)
• Transportation and Toll Payment: RFID tags have become the default technology to automate toll collection on highways and to identify containers in and out of ports.
• Healthcare: RFID can be used to track hospitals’ equipment, tools, and even patients and staff.
Apparel and Footwear industry is rapidly expanding the use of RFID in its Operations. RFID (Radio Frequency Identification) can significantly enhance operations in the apparel and fashion industry through
various applications. Below are some of the use cases that we tackle at Atracio when we engage with our customers on RFID implementation projects:
1. Inventory Management:
• Real-Time Tracking: RFID tags on clothing items allow for real-time tracking of inventory levels in stores and warehouses, reducing the likelihood of stockouts or overstock situations.
• Automated Stock Counts: RFID readers can quickly scan large quantities of items, streamlining stock audits and ensuring accurate inventory records.
2. Supply Chain Visibility:
• Tracking Shipments: RFID enables the tracking of shipments from manufacturers to distribution centers and retail stores, providing visibility into the supply chain and helping to prevent delays.
• Status Updates: Retailers can receive automatic updates on the status of inventory as it moves through the supply chain.
3. Loss Prevention:
• Anti-Theft Measures: RFID tags can serve as security devices that trigger alarms if items are removed from the store without being properly checked out, reducing theft.
• Trackable Returns: Returns can be processed quickly and efficiently by scanning the RFID tags to verify items and their condition.
4. Enhancing Customer Experience:
• Smart Fitting Rooms: RFID can be integrated into fitting rooms, allowing customers to scan items for additional information (like sizes and colors available) or even request different sizes without leaving the room.
• Personalized Marketing: Retailers can gather data on customer preferences and shopping habits through RFID, enabling personalized promotions and offers.
5. Sustainability and Waste Reduction:
• Efficient Manufacturing: RFID can help in monitoring production processes, ensuring that resources are used efficiently and reducing waste.
• Lifecycle Tracking: Apparel companies can use RFID to track the lifecycle of garments, enabling recycling and sustainable practices.
6. Production and Quality Control:
• Process Monitoring: RFID can track items during production, ensuring that all steps are followed and quality standards are met.
• Batch Tracking: In case of quality issues, RFID enables quick identification of affected batches, facilitating timely recalls. By leveraging RFID technology, apparel companies can improve operational efficiency, enhance customer satisfaction, and drive profitability throughout the supply chain.
Financial
high-value items.
RFID in Apparel and Fashion Industry
Based on industry standards, benchmarks and our own experience, the figures below illustrate the financial benefits of RFID in the apparel industry:
1. Inventory Accuracy:
• Fashion Retailers using RFID can achieve inventory accuracy rates of over 95%, compared to around 60-70% with traditional inventory methods. This leads to reduced stockouts and improved sales.
2. Sales Uplift:
Fashion Retailers have reported a 5-20% increase in sales after implementing RFID due to better inventory visibility and improved customer experience.
3. Labor Savings:
• Automated inventory counts with RFID can reduce labor costs by up to 70%. For instance, it might take just 2-3 hours to count inventory in a store compared to 1-2 days with manual methods.
4. Reduction in Shrinkage:
• RFID can decrease inventory shrinkage (loss of inventory due to theft or errors) by as much as 30-50%. This can translate into substantial savings, especially for
5. Return on Investment (ROI):
• Companies often see a ROI of 100-150% within the first year of RFID implementation, depending on the scale and efficiency gains achieved.
6. Stock Turn Rate:
• RFID can improve stock turn rates (the rate at which inventory is sold and replaced) by 20-30%, leading to better cash flow and reduced holding costs.
7. Reduction in Out-of-Stock Rates:
Implementing RFID can reduce out-of-stock rates by 10-30%, significantly improving customer satisfaction and sales opportunities.
8. Operational Efficiency:
Companies have reported reductions in supply chain costs by 10-30% due to enhanced efficiency and better inventory management. In today’s fast-paced retail environment, efficiency and accuracy are paramount. Imagine a world where you have real-time visibility of your inventory, streamlined operations, and a significantly enhanced customer experience—all while reducing costs and boosting sales. Our RFID capability at Atracio can make that a reality for your business.
Warehouses in the Middle East are increasingly adopting automation technologies such as automated guided vehicles (AGVs), robotic picking systems and automated storage and retrieval systems (AS/RS). These technologies help in increasing efficiency improving accuracy in warehouse operations. In recent years, the warehousing and logistics sector in the Gulf Cooperation Council (GCC) region has undergone a significant digital transformation. This shift is driven by technological advancements and the increasing demands of e-commerce, which require warehouses to be more efficient and data-driven.
Companies in the region are adopting innovative solutions to streamline their operations, manage inventory better, and improve customer service. A key player in this transformation is Falcon Autotech, a leading provider of intralogistics solutions. The company’s efforts have not only helped modernise warehousing practices but also earned industry recognition.
The GCC has experienced a rapid rise in e-commerce, with customers expecting faster and more efficient delivery. To meet these demands, warehousing companies are adopting digital technologies like automation, artificial intelligence (AI), and data analytics. Here are some key aspects of this digital shift:
Automation: Automated systems are changing traditional warehouse operations.
Automated Storage and Retrieval Systems (ASRS) optimize storage space and reduce human error, allowing quick access to products and better inventory management.
Data Analytics: Using data analytics helps warehouses understand inventory levels, turnover rates, and customer preferences. This insight enables informed decisions about stock management, cutting costs and boosting efficiency.
Integration with E-commerce: By integrating warehousing systems with e-commerce platforms, companies can manage online orders more effectively, improving customer experiences with faster delivery.
Smart Technologies: IoT (Internet of Things) devices track inventory in realtime, providing visibility into supply chain operations. This helps companies quickly
respond to changes in demand and maintain optimal stock levels.
Falcon Autotech has played a crucial role in helping warehousing companies in the GCC undergo a digital transformation.
Award-Winning Solutions: The establishment’s excellence was recognised after it received the Best Intralogistics Automation Company award on May 1, 2024, at the Saudi E-Commerce and Retail Conference. This award highlights leadership in providing automation solutions that improve efficiency in warehouses across the region.
ASRS Implementation: Falcon Autotech also received the Best ASRS Intralogistics Solution award on September 11, 2024, at the BigBox Retail event in Dubai. This recognition emphasises the effectiveness of Falcon Autotech’s automated systems in optimizing warehouse operations, which are crucial as companies handle increasing amounts of inventory.
Customised Solutions: Falcon Autotech understands that each warehouse is unique. It offers tailored solutions to meet the specific needs of their clients, ensuring that companies can implement systems that fit their operations best.
Training and Support: Falcon Autotech emphasises the importance of training and support for warehouse staff. Their training programs equip employees to effectively operate new systems, maximizing the benefits of digital tools.
The future of warehousing in the GCC looks bright as more companies recognize the value of digital transformation. With the continued growth of e-commerce, the demand for efficient and flexible warehousing solutions will only increase.
Umer Saleem, is the Regional Head for Falcon Autotech Middle East and Turkey, with over 15 years experience in the intra-logistics (smart automation, warehousing robotics) with a broad range of innovative experience in Design Engineering, Sales Market analysis and reporting for UK, European, Middle Eastern business strategies.
Falcon Autotech is well-positioned to lead this charge, providing the necessary tools and expertise for companies to succeed in a digital world.
The digitalisation of warehousing in the GCC demonstrates the region’s adaptability and commitment to innovation. As the sector evolves, companies like Falcon Autotech play a vital role. Their awardwinning solutions in intralogistics and ASRS not only improve operational efficiency but also set a standard for excellence in the industry. With ongoing advancements in technology and rising consumer demands, the future of warehousing in the GCC will continue to be shaped by digital transformation, with Falcon Autotech at the forefront of this change.
Pharmaceutical companies play a crucial role in ensuring that lifesaving medicines reach the people who need them most. Therefore, a reliable supply chain is essential to maintain the trust of customers and ensure the consistent availability of critical medications.
Managing a pharmaceutical supply chain comes with significant challenges, as the industry operates in a highly regulated and complex environment. A well-managed pharmaceutic supply chain ensures that the right product reaches the right patient, in the right condition, at the right time.
To better understand the complexities of supply chain management in the pharmaceutical industry, it is essential to explore the unique characteristics of a pharma company’s product assortment. Every medicine will have an Active Pharmaceutical Ingredient (API), which is the central component of the medicine that produces the required effect on the body to treat a condition.
A single API can be formulated into multiple products, leading to different items within a company’s portfolio that treat the same condition. For some patients or distribution channels, these products may be interchangeable. However, substitution isn’t always possible due to factors such as patient needs, regulatory restrictions, or insurance coverage. As a result, pharmaceutical companies must
establish precise business rules to manage substitutions and ensure compliance with legal and safety standards. Setting up these rules correctly is critical, not just for operational efficiency, but for patient safety.
Another challenge pharma companies face is the division between prescription drugs and over the counter (OTC) products in their assortment. Prescription medications require stricter regulatory compliance, documentation, and storage, while OTC products have fewer restrictions. Demand patterns differ as well— prescription drugs often experience volatile demand, whereas OTC products follow more predictable, seasonal trends.
Additionally, margins vary between the two categories, with prescription drugs typically yield higher margins compared to OTC items. Given this diverse assortment and the wide variance in product value, segmentation in inventory management becomes crucial.
In the MEA region, insurance companies typically operate using formularies, which are lists of drugs that are covered or reimbursed based on cost-effectiveness assessments. These formularies play a crucial role in determining which medications are accessible to insured patients. If a drug is not included on a formulary, its demand may drop significantly.
Incorporating the formularies of the region’s largest insurance providers into demand planning can greatly enhance forecast accuracy. When a medication is added to or removed from a formulary, it can trigger significant shifts in demand. As such, regular monitoring of these formulary changes and adjusting sales forecasts accordingly is essential for optimizing inventory and ensuring supply meets the actual market needs.
The diverse assortment of pharmaceutical products necessitates a strategic segmentation approach, allowing companies to establish target service levels tailored to the unique characteristics of each product. This segmentation can be mapped across two axes: demand volatility and sales value. By categorizing products accordingly, companies can prioritize their planning efforts and effectively manage service levels.
For example, Paracetamol is inexpensive and has steady demand. Typically available over the counter, they don’t fluctuate highly and can be easily replenished. Their predictability allows for efficient stock management with minimal intervention, enabling target service levels to be set at moderate to high levels without significantly increasing costs. Given their low volatility, the safety stock needed to account for demand uncertainty is relatively low, making this a manageable investment. This approach typically allows companies to
fully automate, having a no-touch approach while ensuring high availability.
Similarly, products like Insulin, which have a higher value than Paracetamol but still exhibit steady demand, can be managed similarly by automating the process, trusting the statistics, and letting the system run the show. However, due to the higher value of Insulin, closer attention to exceptions is necessary, as excess stock ties up more capital, and stockouts can lead to significant profit loss.
On the other hand, speciality and rare disease medicines exemplify high volatility and high value. These drugs are expensive, and their demand can be unpredictable, influenced by new therapies, changing treatment guidelines, and insurance coverage.
For such critical products, target service levels must be set high to avoid stockouts, as lost sales can significantly impact revenue and can cause great harm to patients if unavailable. When actual demand deviates strongly from the forecast, consensus planning becomes crucial in aligning various stakeholders—such as sales, marketing, finance, and supply
Ibrahim Mohammedi, Chief Product Officer at Slimstock MEA, is a supply chain innovator driven by a clear ambition: to reduce waste and boost sustainability across the Middle East’s retail and distribution sectors. Guided by the mantra “perfection is the enemy of progress,” he focuses on actionable steps that deliver impactful, sustainable change.
chain—to create a unified demand forecast. Consensus planning, which integrates external inputs like market data, clinical insights, and patient trends, ensures a more holistic approach.
Both flu vaccines and ORS are highly volatile items, just like the speciality medicines. This volatility necessitates careful planning based on a management-byexception approach. Despite their lower value compared to specialty drugs, their volatility necessitates higher buffer stock levels to maintain service levels, especially during peak seasons. Implementing a dynamic buffer stock strategy based on the seasonality of these products ensures a reliable supply when demand surges, such as during flu outbreaks.
Optimising pharmaceutical supply chains requires a nuanced understanding of the diverse product assortment and the specific challenges posed by regulatory frameworks and insurance practices. By implementing strategic segmentation based on demand volatility and sales value, pharmaceutical companies can enhance inventory management, forecast accuracy and spend time on items that actually need their attention, ensuring that critical medications are readily available. This proactive approach not only improves operational efficiency but also safeguards patient health by ensuring timely access to life-saving treatments.
The vast majority (97.6%) of CEOs and senior managers of organisations in the UAE plan to increase their investments in AI for cybersecurity amid a continuing uptick in cyberattacks, according to new research by Censuswide, commissioned by Palo Alto Networks.
The research, which included insights from 250 CEOs and senior managers from companies in the UAE between September 18-25, 2024, revealed that respondents saw a significant increase in attacks, with 63% reporting higher attacks compared to 2023, and 14% reporting the same level of attacks as 2023.
However, UAE businesses also appeared to be confident that they can protect their operations through investments in AI. 94% of respondents said that they were confident in the effectiveness of AI tools in detecting or mitigating cyber threats compared to traditional cybersecurity solutions.
90%1 of respondents had already implemented AI for cybersecurity, with 52% saying they had made extensive implementations, and 38% having made limited deployments.
Opinion was more mixed on the precise ways in which AI can most help UAE organisations to improve their cybersecurity posture, with 42% saying that AI would be most effective in boosting speed and efficiency through automation, 39% believing it would primarily aid threat detection, and 35% saying it would improve vulnerability management.
“While it is reassuring to see that so many CEOs and business leaders in the UAE are keen to invest in AI to improve their security profile, it is imperative that organizations deploy AI in the right way and understand the importance of embracing a fully integrated approach with platformisation
Ercan Aydin, Regional VP, Palo Alto Networks, MEA
at its core,” said Ercan Aydin, Regional Vice President at Palo Alto Networks, Middle East and Africa (MEA). “A fully integrated approach enables organisations to remove the confusion that often accompanies AI implementations, allowing them to fully leverage the power of AI to stay ahead of ever-changing threat dynamics while simplifying their security posture.”
The research revealed that while most business leaders surveyed in the UAE understand the importance of AI for cybersecurity, they still see barriers to investment, with cost (45%), complexity of integration (45%), uncertainty about ROI (41%), and a lack of clear business benefits (30%) cited as key concerns.
Moreover, leaders also have concerns over the potential implications of using
the technology. For example, 50% of respondents were concerned about privacy issues, 48% worried about potential misuse of AI, 46% cited integration challenges as a concern, and 45% expressed concern over the cost.
Palo Alto Networks showcased its leading cybersecurity technology at the recently concluded GITEX Global 2024, in the UAE with live demos of its best-in-class cybersecurity Precision AI, a proprietary, innovative AI system that brings together the power of machine learning, deep learning and generative AI to ensure realtime security and safety.
The research was conducted with 250 CEOs and senior business leaders across the UAE aged 25 and over between 18th to 25th September this year.
Qatar Airways Cargo and Qatar Postal Services Company (Qatar Post) recently signed a cooperation agreement, demonstrating a shared commitment towards enhancing their strategic partnership in postal activities and mail transportation to and from Doha.
The agreement aims to efficiently meet customer needs in accordance with international postal union standards, and reflects the ongoing efforts of both parties to enhance logistical infrastructure, ensuring smooth and effective coordination in the transportation and delivery of postal shipments.
It also covers competitive rates specifically designed for postal shipments transported by Qatar Airways Cargo to Qatar Post, the national provider of postal services in Qatar.
Qatar Airways Group Chief Executive, Engr. Badr Mohammed Al-Meer, said: “As the world’s leading air cargo carrier, our robust fleet and expansive network enable us to meet customer needs efficiently, in-line with international standards.
“This strategic cooperation agreement reflects our commitment to improving logistical infrastructure, and ensuring smooth and effective coordination in delivery to and from Doha.”
Chairman and Managing Director of Qatar Post, Faleh Bin Mohammed Al-Naemi, said: “We are pleased to strengthen our cooperation with Qatar Airways and look forward to achieving sustainable and mutually beneficial successes in postal and logistical services that serve our customers’ interests. We emphasise the importance of forming strategic partnerships between Qatar Post and national companies adhering to global standards such as Qatar Airways.
“In addition, our Mail product provides seamless 100 per cent EDI integration for bookings, a dedicated hub warehouse for streamlined operations, and end-to-end track and trace capabilities for real-time shipment visibility.”
The collaboration with Qatar Airways Cargo is part of Qatar Post’s efforts to enhance postal and logistical services, and achieve the highest levels of customer satisfaction, particularly in the area of
shipping and delivery operations.
With a daily handling capacity of up to 500 tonnes, Qatar Airways Cargo ensures efficient and secure mail transportation across its extensive global network.
Miebach Consulting held its 2nd Annual Insights Summit on October 17 in Dubai, attracting over 50 supply chain leaders from across the Middle East. With presence from MNCs and local companies alike, the gathering served as a for sharing innovative ideas and best practices in an industry that is rapidly evolving.
The agenda featured insightful partner sessions with NEOM, Panda Retail, and SIAM Trading, showcasing real-world applications and collaborations that are redefining the supply chain landscape. Miebach CEO Jorge Motje delivered a compelling talk on the transformative role of AI in supply chains, backed by intriguing use cases that span
various industry segments. His insights emphasized that leveraging AI is no longer optional but essential for staying competitive.
A diverse panel of experts, including leaders from Kenvue, AstraZeneca, and New East, engaged in a robust discussion about the unique challenges and potential solutions for demand planning specifically in the Middle East and Africa. Their perspectives highlighted the region’s complexities, emphasizing that tailored strategies are crucial for success.
Overall, the summit not only facilitated meaningful discussions among supply chain professionals but also fostered connections that could drive future
collaborations. The energy in the room was palpable, and the discussions laid a strong foundation for future advancements in the field. The success of this year’s summit sets a promising foundation for next year’s gathering, as the organisers continue to lead in industry thought leadership.
The 4th Annual Global Trade and Supply Chain (GTSC) Summit was held on October 8th and 9th in Dubai.
The event discussed critical aspects of how outdated supply chains hinder efficiency. With the support of the New Economy Academy in Dubai, the two-day conference helped attendees navigate the complexities of the current trade landscape and ensure that supply chains remain efficient, resilient and sustainable.
International commerce and logistics is changing to overcome new difficulties and seize opportunities. Amid protectionism and international conflict, new commercial hubs and the need for sustainable operations, there is the promise of technology, growth markets and new supply and procurement models. At the summit a group of highly distinguished
speakers explored the practical impacts of AI technology on procurement and supply chains. Another panel discussed ‘financing
a sustainable trade future,’ while ‘powering up trade through tech innovation,’ was also closely examined.
Falcon Autotech is a global intralogistics automation solutions company. With over 10 years of experience, Falcon has worked with some of the most innovative brands in E-Commerce, CEP, Fashion, Food/FMCG, Auto and Pharmaceutical Industries.
CONTACT US:
Email: salesenquiry@falconautoonline.com
Website: www.falconautotech.com
The International Air Transport Association (IATA) will create the Sustainable Aviation Fuel (SAF) Matchmaker to link airlines and SAF suppliers. The development was announced at the World Sustainability Symposium (WSS) with an expected launch date in the first quarter of 2025.
“Our vision is to create a transparent, efficient, and accessible matchmaking platform that will accelerate the uptake of SAF as the aviation industry progresses towards net zero CO2 emissions by 2050. The platform will do that by reducing the costs and complications that airlines face when looking for SAF suppliers. The SAF market’s maturity and globalization will be enhanced by the transparency that the SAF Matchmaker will enable. Every step in that direction is of great importance, considering that SAF is air transportation’s most significant decarbonization tool,” said Marie Owens Thomsen, IATA’s Senior Vice President Sustainability and Chief Economist.
The SAF Matchmaker will address three critical issues:
• Connectivity: SAF producers and suppliers will be able to post available or planned SAF volumes and airlines will be able to register their interest in purchasing shown or desired SAF volumes. Any subsequent trades will take place outside the platform.
• Visibility: The platform will carry comprehensive information on the SAF available, such as volumes, feedstock used, the location and technology of production, the emissions reductions, as well as compliance with the Carbon Offsetting Reduction Scheme for International Aviation (CORSIA) or the European Union’s Renewable Energy Directive (EU RED).
• Efficiency: The availability of a central platform will simplify SAF procurement by making it easier and faster for all parties to connect. It will also facilitate the development of market intelligence based on data that the platform will generate. The initial focus of the platform will be airlines and SAF suppliers. In due course governments and non-aviation corporate SAF buyers will also be able to participate.
Cool chain solutions ensure that products stay fresh and safe from farm to table, or from lab to patient. The cool chain industry is booming, driven by the need for efficient temperature management in various sectors. In fact, the global cold chain logistics market is projected to reach $526.11 billion. At the recently concluded World Cold Chain Expo 2024 held in the UAE, Abigail Mathias, Editor Global Supply Chain caught up with Fabrice Panza, Manager Global Cool Chain Products, Etihad Cargo. He offers a perspective on pharma movements.
GSC: How has Etihad Cargo established itself as one of the pioneers of pharma logistics in the region?
Etihad Cargo has positioned itself as a key player in pharma logistics by enhancing our PharmaLife product to meet the specific needs of life sciences and healthcare shipments. Over the last four years, we have implemented new Standard Operating Procedures (SOPs) and Service Level Agreements (SLAs) to ensure compliance and reliability. A strict monitoring system, supported by supplier and performance management, has resulted in a 99.7% compliance rate.
Our PharmaLife product has shown consistent growth, with a 10% increase in 2024 following a 37% growth in 2023, demonstrating its continued relevance in the pharma logistics sector. Etihad Cargo follows Good Distribution Practice (GDP) guidelines and holds IATA CEIV Pharma certification, which ensures adherence to industry standards. We continue to innovate, with recent developments including launching a dedicated pharma centre, and introducing thermal covers for temperature-sensitive cargo and cool dollies in Abu Dhabi and at more than 25 stations in its network.
We also contribute to industry knowledge through our role as a co-founder and partner of the Pharma Logistics Masterclass, which we have supported for four consecutive years. Our Pharma Champions programme comprises 16 highly trained experts from across the globe, each equipped with specialised knowledge of our pharmaceutical logistics solutions. These champions are dedicated to ensuring that our services not only meet but exceed
customer expectations, tailoring their expertise to suit the specific requirements of every client. Their training encompasses a deep understanding of Etihad Cargo’s innovative products and solutions, enabling them to offer unparalleled support and personalised care, ensuring the seamless and secure transport of pharmaceutical goods worldwide.
GSC: What has been the impact of your presence at the World Cold Chain Expo 2024? Please tell us a little bit about the event?
Etihad Cargo’s participation at the World Cold Chain Expo 2024 reinforced our presence beyond the UAE and provided an opportunity to engage with local customers and stakeholders. The event enhanced Etihad Cargo’s visibility and facilitated discussions on the importance of collaboration in managing complex and sensitive supply chains, such as perishables and pharmaceuticals.
During the event, we emphasised the need for cooperation across the ecosystem to reduce lead times and minimise the time cargo spends outside temperaturecontrolled environments. We also highlighted the importance of collaboration with government bodies like customs and healthcare authorities, which enables preclearance and faster last-mile delivery.
Etihad Cargo also used the event to connect with new technology providers, including those offering IoT solutions, which contribute to supply chain transparency. This transparency is key to building trust and ensuring smoother operations, as it allows for more responsive actions when disruptions occur. Overall, the event served as a platform for strengthening relationships and showcasing Etihad Cargo’s commitment to improving cold chain logistics.
GSC: When it comes to embracing sustainable methods of operation, how does the Middle East compare with the rest of the world?
In the Middle East, Etihad Cargo is actively embracing sustainable methods, investing in the latest aircraft models that produce significantly less CO2 than previous generations. Additionally, by reducing lead
times, Etihad Cargo optimises energy use, ensuring operations are more efficient.
A key element of our sustainability efforts is waste reduction and minimising weight, which we have achieved through lighter Unit Load Devices (ULDs), further contributing to energy efficiency. Etihad Cargo has also developed a tool that allows customers to track the precise CO2 emissions associated with our shipments, reinforcing transparency and accountability. By focusing on reducing both CO2 emissions and waste, we are aligned with global efforts to minimise environmental impact. This is particularly important given that 30-50% of vaccines and 30-40% of perishables are wasted globally, according to IATA figures. These initiatives also support Abu Dhabi’s broader sustainability vision, which seeks to foster environmentally responsible growth across industries.
n WeRide, a global leading autonomous driving technology company, and Uber Technologies, Inc., the world’s largest mobility and delivery technology platform, recently announced a strategic partnership to bring WeRide’s autonomous vehicles onto the Uber platform, beginning in the United Arab Emirates.
The partnership is expected to launch first in Abu Dhabi later this year. A dedicated number of WeRide vehicles will be made available to consumers using the Uber app. After launch, when a rider requests a qualifying ride on the Uber app, they may be presented with the option to have their trip fulfilled by a WeRide autonomous vehicle. The partnership does not contemplate any launches in the United States or China.
WeRide currently operates the largest robotaxi fleet in the UAE, where residents can access its robotaxi services through the TXAI app. In addition, in July 2023, WeRide was granted the UAE’s first and only national
license for self-driving vehicles, enabling it to test and operate its autonomous vehicles on public roads across the entire country.
Tony Han, founder and CEO of WeRide said: “We are honoured to partner with Uber to continue to bring our technology to global markets. Together, we aim to combine our collective experience and expertise to deliver much needed, affordable, sustainable and safe mobility
solutions to a global audience.”
Dara Khosrowshahi, CEO of Uber said:
“Uber is very excited to partner with WeRide. It’s clear that the future of mobility will be increasingly shared, electric, and autonomous, and we look forward to working with leading AV companies like WeRide to help bring the benefits of autonomous technology to cities around the world.”
n From October 2024, Globe Air Cargo began to exclusively represent Air Serbia’s cargo services in the U.S., significantly boosting the airline’s presence in this key market. Under this agreement, Globe Air Cargo will manage sales and marketing for Air Serbia, offering 60 tons of weekly freight capacity on five A330 flights between New York (JFK) and Chicago (ORD) to Belgrade (BEG).
including Bosnia (SJJ), Montenegro (TGD), Albania (TIA), North Macedonia (SKP), Zurich (ZRH), Istanbul (IST), and others. Additionally, the partnership will extend Air Serbia’s reach into China, with service to Guangzhou (CAN), Tianjin (TSN), and a new route to Shanghai Pudong International Airport (PVG) launching January 11, 2025.
Under this agreement, Globe Air Cargo will manage sales and marketing for Air Serbia, offering 60 tons of weekly freight capacity on five A330 flights between New York (JFK) and Chicago (ORD) to Belgrade (BEG). This expanded service provides connections to key European destinations,
The partnership will also leverage an extensive Road Feeder Service (RFS) network across the U.S., connecting Air Serbia’s key stations at JFK and ORD to ensure efficient transfers to Eastern Europe and beyond.
Francisco Hernandez, Managing Director of Globe Air Cargo USA, commented: “This partnership is a pivotal step in
strengthening our presence in the U.S. market. By combining Globe Air Cargo’s expertise with Air Serbia’s growing network, we aim to deliver seamless global logistics solutions.”
Veselin Djordjevic, Head at Air Serbia Cargo says,“With over 50 drop-off points covered by extensive RFS connections via ORD and JFK, our product is well-regarded in the USA. Serving both Chicago and New York year-round, we provide high-quality, reliable service to support the US export community“.
This collaboration demonstrates a shared commitment to growth and delivering high-quality cargo services in an evolving global market.
n Dubai Helishow 2024 recently took off in the UAE. Held from October 22-24, 2024, at Skydive Dubai this year’s show was a pivotal event for companies looking to fill their order books while showcasing the latest advancements in the VTOL (Vertical TakeOff and Landing), UAV (Unmanned Aerial Vehicles), and helicopter industries.
Attendees witnessed three action packed days of exhibitions, live demonstrations, and insightful discussions. A highlight of the event was the NSRC; National Search and Rescue Center’s Sea rescue display, taking place on the first day. The live demonstration showcased the skill, bravery, and cutting edge technology behind search and rescue operations, offering attendees a real time look at life saving missions in action.
Maysoon Abulhoul, Chief Operating Officer of Domus Group, the organisers of Dubai Helishow 2024, shared her
excitement for this year’s edition, “Dubai Helishow 2024 was our most exciting event yet. We were not only showcasing the future of vertical flight but also creating opportunities for industry professionals to
connect and collaborate. This event offers the perfect platform to build relationships, exchange ideas, and stay at the forefront of what’s happening in the UAV and helicopter sectors.”
n Etihad Cargo has announced an expanded winter schedule, increasing belly hold cargo capacity via 880 passenger flights per week, growing to over 900 by March 2025.
Starting November 2024, the enhanced schedule will introduce additional frequencies to existing routes and a new passenger destination—Nairobi. Etihad Cargo will offer belly capacity on 880 passenger flights per week in November 2024, increasing to over 900 flights per week by March 2025.
Etihad Cargo will enhance its operations with additional weekly widebody flights. In Europe, the carrier will add 36 weekly flights, with destinations including Frankfurt, Paris, Rome and Milan moving to double-daily services. Additional flights will also boost capacity in Zurich, Manchester, and Düsseldorf. In Southeast Asia, services to Thailand will increase by nine flights, with Bangkok reaching triple-daily frequency and Phuket increasing to 20 flights weekly. In the US, flights to Boston will increase from four to daily.
The cargo carrier will also upgrade existing services in South Asia and the Indian Ocean. The Malé route, which currently
has 14 weekly flights, will switch entirely to widebody aircraft starting from December 15. Additionally, widebody frequencies will increase for Bengaluru from two to three flights per week, and Hyderabad will increase from nine to 11 flights weekly.
The capacity will further grow with the introduction of new A320 flights, including a new route to Nairobi, launching on December 15 with four weekly flights. This will strengthen the carrier’s footprint in the Middle East and Africa, supporting
increased regional connectivity.
Stanislas Brun, Vice President Cargo, said: “Etihad Cargo’s customers are at the core of its operations. This expanded schedule offers more access to the airline’s global network, with increased flight frequencies and a new destination providing more capacity and flexibility for cargo transport. Whether moving goods between continents or ensuring quick connections, Etihad Cargo is dedicated to supporting its customers with reliable and efficient services.”
n King Salman International Airport Development Company (KSIADC) announced the signing of strategic partnerships with both Special Integrated Logistics Zone (SILZ) and FedEx on the sidelines of the Global Logistics Forum 2024.
KSIADC also announced joining the International Air Cargo Association (TIACA) to transform Riyadh into a regional and global logistics hub and enhance logistics services in the Kingdom, positioning it among the top 10 countries globally in logistics and air cargo services.
KSIADC acting chief executive Marco Mejia indicated that the partnerships mark a significant step in the company’s efforts to strengthen the Kingdom’s position as a global logistics hub. The collaboration between KSIADC and SILZ, the first special economic zone in Saudi Arabia, aims to enhance coordination in operational processes and develop infrastructure to boost air cargo capabilities in Riyadh.
The airport boasts a strategic location connecting three continents, enhancing the efficiency of the economic zone located
within the airport. The zone offers unique access to global air routes and the largest consumer market in the Middle East.
The partnership aims to accelerate the movement of goods and improve logistics operations for businesses in Riyadh.
SILZ chief executive Dr. Fadi Al-Buhairan stated that the partnership with King Salman International Airport is a pivotal step in strengthening Riyadh’s position as a regional and global hub for logistics and air cargo services. “Together, we will create an attractive environment for international investors and drive economic growth forward,” he said.
As part of the partnership with FedEx, both parties will work to enhance logistics solutions and supply chains at King Salman International Airport.
The partnership aims to transfer knowledge, adopt best practices, and implement advanced logistics solutions, in addition to exploring new opportunities in the logistics, distribution, and shipping sectors in the Kingdom.
FedEx managing director for Middle
East operations Abdulrahman Al-Mubarak stated that the aim of such collaboration is to enhance the efficiency of the logistics sector in the Kingdom and elevate its services in the region. He said, “By leveraging our expertise and the strategic location of King Salman International Airport, we will work to improve supply-chain operations and implement the best innovative solutions, aligning with the Saudi Vision 2030 to transform the Kingdom into a global logistics hub with high efficiency, quality, and speed.”
To solidify its presence in the global air cargo sector, KSIADC joined TIACA as a member to enable the company to expand its access to global markets and enhance the efficiency of its operational processes, contributing to the Kingdom’s ambition to become a leading regional hub for logistics and shipping. TIACA Director General Glyn Hughes, said that KSIADC’s joining the association will enhance the shared vision for a secure and economically thriving air cargo sector, aiming to address current challenges and advance towards a sustainable future for the industry.
n Leading third-party logistics company, CEVA Logistics, and Al Majdouie Logistics, a leading end-to-end logistics solutions provider in the Middle East, signed the final agreement to create a joint venture in the Kingdom of Saudi Arabia (KSA). The signing took place during the inaugural Global Logistics Forum in Riyadh.
First announced in July 2024 and subsequently approved by the relevant Saudi authorities, the newly created joint venture—CEVA Almajdouie Logistics—will leverage the strengths of both companies to meet the growing demand for integrated logistics solutions in Saudi Arabia to support the Kingdom’s growing logistics sector and overall economy. CEVA Logistics controls a majority stake of the joint venture.
Mathieu Friedberg, CEO of CEVA Logistics, said: “With the Saudi market experiencing significant growth, seamless logistics and global connectivity are essential for the domestic economy. Both companies contributing to this joint venture have a shared vision for growth and a commitment to providing our customers
with world-class logistics services. Our partner’s existing business and reputation in KSA will ensure the JV starts off as one of the top five logistics players in the Kingdom of Saudi Arabia. We see the deal as a strong, strategic move for both partners and great news for our customers.”
CEVA Logistics has been in KSA since the 1980’s. It has collaborated with Al Majdouie Logistics for many years, including in a separate joint venture addressing the
n Agility, a supply chain services, infrastructure and innovation company, signed a memorandum of understanding with the Saudi Railway Company (SAR) today to look at requirements for intermodal storage, transportation and processing facilities in Sudair City for Industry and Businesses and near King Khalid International Airport.
Under its Vision 2030 national strategy, Saudi Arabia has set out to establish itself as a global hub for logistics and trade through massive investment in the modernization and expansion of its logistics and transportation infrastructure. “Saudi Arabia is rapidly moving toward achieving its goal to be one of the world’s most important centers of trade, transportation and logistics,” said Agility Vice Chairman Tarek Sultan. “Agility has been a long-time supporter, partner and investor in the Saudi logistics sector. We have decades of experience here, and we’ve built some of the Kingdom’s most advanced logistics infrastructure. We see a future where Saudi
finished vehicle logistics market.
This strategic partnership combines both companies’ transport and logistics operations in Saudi Arabia. Customers will benefit from Al Majdouie’s domestic infrastructure integrated with CEVA’s global network. Headquartered in Damman, the joint venture organisation will be led by CEO Bassel El Dabbagh, with around 2,000 employees in KSA and a local fleet of more than 2,000 assets.
and the region lead the world’s supply chain sector. We thank SAR for giving us the opportunity to be part of this future and the opportunity to contribute to Saudi’s growth and success story”
Agility has been investing in Saudi Arabia for two decades. Its Agility Logistics Parks (ALP) business developed and operates world-class logistics parks and warehousing facilities in Riyadh and Dammam. A third large ALP
complex is under construction in Jeddah. Agility’s Riyadh Logistics Park includes “green” buildings that are the first EDGE Advancedcertified warehousing in the GCC.
Other Agility businesses serve Saudi Arabia’s energy, aviation and e-commerce sectors. The company’s corporate venture arm is an investor in Saudi startups in e-commerce and digital freight matching for the trucking industry.
n Swiss World Cargo resumed its partnership with Globe Air Cargo Bulgaria on 1st June, reviving their long-standing collaboration that began in 2008. Globe Air Cargo has hired an additional team member to support Swiss World Cargo, focusing on sales, booking, operational supervision, and post-flight activities.
The 16-year partnership highlights the value of trust and reliability between the two companies. Tania Mlechenkova, Managing Director of Globe Air Cargo Bulgaria, expressed delight in resuming the partnership, emphasizing their shared commitment to exceptional customer service and long-term stability.
Swiss World Cargo operates an A220 service between Zurich and Sofia, providing Bulgarian freight forwarders with connections across Europe, North and South America, and the Far East. The airline specializes in handling highvalue, temperature-sensitive cargo such
as pharmaceuticals, perishables, and valuables, in addition to offering its X-Presso transportation solution. Mlechenkova noted Globe Air Cargo’s expertise in managing
special cargo shipments and highlighted the addition of a fully-trained team member to provide even more dedicated support for Swiss World Cargo.
n Riyadh Airports Company (RAC), which manages and operates Riyadh’s King Khalid International Airport (KKIA), has announced it will deploy intelligent purchasing management solutions from global technology company SAP to modernize its procurement infrastructure and enhance the supplier experience.
As a leading player in the aviation industry working with suppliers across the region and globally, RAC needed an advanced procurement system to increase efficiencies and streamline its operations. SAP was selected for the project due to its aviation industry experience, particularly in the realm of procurement technology. The comprehensive range of solutions to be implemented includes SAP’s Ariba suite of programs.
SAP’s Ariba portfolio offers an end-to-end spend management system with integrated supplier information, lifecycle, performance, and risk management functions. Among the solutions deployed by the airports company, the SAP solutions will enhance procurement collaboration with suppliers through a fully digital integrated system, while the benefits of SAP Ariba Strategic Sourcing Suite include
Officer,
enabling employees to manage contracts, suppliers and compliance globally and in multiple currencies.
Ariba solutions will be seamlessly integrated with existing systems, enabling RAC to synchronize its procurement operations across various departments, enhancing overall efficiency.
RAC’s CEO, Ayman Abdulaziz AboAbah, commented, “King Khalid International Airport is a gateway to the region, and partners and
suppliers expect consistently high standards across the board and an enhanced airport experience. To achieve this, RAC manages a vast network of suppliers and resources, and we needed a secure, scalable cutting-edge procurement solution capable of streamlining, automating and enhancing procurement processes, workflows and insights. With Ariba, both our employees and suppliers will benefit from an upgraded experience and timesaving benefits, as we continue to enhance our travel gateway for millions of passengers from around the globe.”
Fahd Nawwab, Vice President of SAP Saudi Arabia, commented, “Riyadh Airports Company and King Khalid International Airport are viewed as beacons of efficiency and connectivity for millions of passengers and partners. SAP Ariba solutions will help employees to collaborate with suppliers worldwide in multiple currencies and with real-time insights informing purchasing decisions and supplier selection. In line with the unique requirements of Riyadh Airports Company, Ariba solutions offer unparalleled customization and scalability to ensure a tailored experience that can evolve as the company’s needs grow.”
n Emirates Transport, the UAE’s leading transport provider, has partnered with Al Ghurair Motors to pilot hydrogen and electric commercial vehicles. Announced at GITEX Global 2024, this initiative aims to accelerate the adoption of eco-friendly transportation and aligns with the UAE’s goal of achieving net-zero emissions by 2050, as well as having half of all vehicles on the road electric by that year.
Emirates Transport, which operates over 32,000 vehicles across various sectors, will conduct pilot projects to evaluate the feasibility of integrating hydrogen and electricpowered vehicles into its national fleet. These projects will serve its clients in business, government, and the public, contributing to the development of sustainable transportation solutions.
As part of this partnership, the company’s 46 workshops across the UAE will be equipped to maintain these alternative-fuel vehicles. Mechanics will receive specialized training to ensure the proper support and expansion of these technologies.
Additionally, the agreement includes plans
to develop infrastructure for electric vehicle (EV) charging stations and hydrogen refueling technology, which are critical for scaling the adoption of these eco-friendly vehicles.
Dominic Hagerty, Emirates Transport’s Chief Transport and Lease Officer, emphasized that this collaboration marks a new era
for the UAE’s transport sector, aligning with governmental sustainability goals and contributing to policy development. The partnership sets the stage for future advancements in both vehicle technology and national infrastructure, positioning the UAE as a leader in green transportation.
n Saudia Cargo announces the signing of a new Standard Ground Handling Agreement(SGHA) with Swissport International AG, which will serve as its official ground-handling agent at Nairobi Airport. Swissport will handle all aspects of ground support, including cargo handling, loading and unloading, and special care for temperature-sensitive products.
Commenting on the strategic collaboration, Mohanned Badri, Vice President of Operations at Saudia Cargo, said: ” Our strategic collaboration with Swissport is designed to streamline the ground-handling processes, thus minimizing transit times and ensuring that goods reach their destinations in optimal condition. Swissport brings a wealth of experience and expertise that will play a crucial role in our operations at Nairobi Airport, and we are delighted to extend our partnership with them.
Saudia Cargo operates eight weekly flights to Nairobi Airport, including four weekly freighter flights utilizing Boeing
747-400 aircraft and four passenger flights using Airbus A330 aircraft. “
“We’re thrilled to expand our partnership with Saudia Cargo at Nairobi Airport,” said Racheal Ndegwa, CEO
of Swissport Nairobi. “Our expertise in handling temperature-sensitive goods and our innovative flower corridor project will ensure seamless and efficient logistics solutions for Saudia Cargo.”
n The newly added freighters, registered as 9H-CAD and 9H-CAH under the Maltese AOC, bring the total number of B767300BDSF aircraft in the Group’s fleet to four. Each aircraft boasts a cargo capacity of approximately 52 tons and 400 cubic meters, with advanced features designed for air cargo operations. These enhancements include reinforced floors, wide cargo doors for large shipments, and optimized fuel efficiency, making them ideal for both shortand medium-haul routes.
This additional capacity enabled the successful launch of a new service to Delhi in early October in addition to the three existing weekly frequencies to Mumbai, taking to five the weekly flights catering to India’s growing industries, including pharmaceuticals, automotive, textiles, electronics and high tech. The launch of these freighters also frees up capacity on the 747 aircraft, allowing for increased long-haul destinations and enhanced connectivity between Europe, the Far East and the US. “The introduction of these two B767-300 freighters is a significant step forward in Challenge Group’s strategic
expansion,” said Or Zak, Chief Commercial Officer. “Their versatility and fuel efficiency empower us to increase flight frequencies, enhance flexibility for charter operations, and explore new market opportunities. These aircraft will help meet the rising demand for complex verticals and e-commerce, reinforcing Challenge Group’s leadership in the air cargo industry.”
n ECS Group’s subsidiary AVS GSA, in collaboration with Thai Vietjet and Lactasoy, recently collaborated to provide crucial support to flood-affected communities in Chiang Rai, Thailand. In response to the devastating floods that have impacted over 8,000 families in the northern part of the country, this partnership has focused on delivering essential relief supplies to those in need.
As part of this initiative, AVS GSA’s team collaborated with Lactasoy to donate 900 boxes of soybean milk, weighing 7.7 tons, to support affected communities. The shipments were successfully delivered on flights VZ130 and VZ132 on September 18 and 19, 2024. Additionally, AVS-GSA acted as the General Sales Agent (GSA) for Thai Vietjet Air, which offered complimentary air transportation of relief items, including food, water, and clothing, to the flood-hit areas.
Now operating a total of 10 aircraft, Challenge Group continues to solidify its position as a key player in the air cargo industry and enabler to the global trade. The introduction of these new freighters underscores the company’s commitment to delivering tailored and reliable endto-end logistics solutions to meet diverse customer needs.
International Benefits:
+ The FIATA member certificate
+ Use of the Fiata logo
+ Entry in the FIATA members directory & networking events
+ Advertising in the FIATA members directory, review and information (FIATA e-Flash)
+ Special Rates for FIATA publication and articles
+ Access to secretariat›s assistance
+ FIATA arbitration code
+ Use of FIATA documents
+ FIATA worldwide member connectivity
+ Talent Connect Worldwide, E-Learning
+ Discountes rates in participating in global and regional conferences
+ Asssistance in case of legal advocacy
+ Discounts for cargo/logistic events and exhibition stands
+ Discount training for NAFL members
+ Training/Certification for regional/international courses
+ Insurance at discounted rates (cargo/liability/medical)
+ Complimentary internship, Skill upgrade and Mentoring & Innovation ideas
+ Discounted supplier rates for industry products
Owing to the phenomenal success of our previous issue, we dedicate this space to outstanding individuals who are the driving force of the logistics industry. Explaining how every single day poses a different dynamic, we present Glyn Hughes, Director General, The International Air Cargo Association (TIACA) in conversation with Abigail Mathias, Editor, Global Supply Chain.
AM: What do you do to keep yourself fit?
GH: I have the pleasure of living in quite a remote part of Switzerland at about 1,100 meters altitude. I often hike or ride my bike in the beautiful mountains. Sometimes though local traffic can be quite busy as cows roam freely about. In summer, I also enjoy swimming.
AM: What time do you break for lunch?
AM: What is the advice you’d give other business professionals juggling time?
Glyn Hughes, Director General, The International Air Cargo Association (TIACA)
AM: What’s your typical day like?
GH: I have a very strange eating pattern in that most days I don’t eat breakfast or lunch, but do try to eat healthy dinners.
AM: Around what time of day do you wrap up work at the office?
GH: I had to look up what the word ‘typical’ meant. In air cargo that doesn’t exist. Whatever I plan is often impacted by evolving market conditions, influenced by macroeconomic scenarios, government regulations, conflict and disasters as well as industry operational challenges that impacts capacity or connectivity. TIACA has the objective of supporting the entire industry so we like to contribute to industry solutions wherever we can.
GH: Balance is key but balance means different things to different people. Throughout the early years of my working life when I had small children, I made a commitment to be home early enough to spend the evenings with them and then I would resume work, from home after their bedtime. I still continue with that late night working approach, even though my children are now 29 and 27 and live in different countries. Everyone needs to ensure they have adequate down time to restore inner peace and ensure that signs of stress can be quickly identified and addressed.
GH: My office is either sitting on an airplane seat or my home office. Either way, I wrap up when the work is done. Often at home I am working into the small hours beyond midnight.
AM: How do you unwind in the evening?
AM: When do you catch up on world/business events?
AM: Are you a coffee or tea person?
If so, how many cups a day?
GH: I have never had a single cup of coffee, so I’m definitely in the tea camp, however, I only drink hot tea from October to March, about 4 cups a day, and iced tea from March to October.
GH: I am a big movie fan, so I often work with a movie on in the background. We also have a very competitive fantasy football league within my family so quite a bit of time is spent on managing that. I’m the defending champion so I feel the pressure.
AM: When is your next holiday?
GH: Sadly, nothing is planned until next year, possibly during Easter. Hopefully then you will find me relaxing by a pool somewhere.
GH: I am an avid absorber of news and events from multiple sources as I feel the truth can best be determined from multiple perspectives. Our industry, being global in nature, is always impacted by what goes on in the world so it’s crucial we all maintain current with events that will ultimately impact our work.
AM: To me and our Association Global Supply Chain Magazine is…
GH: A great source of information related to all aspects of supply chain activity.