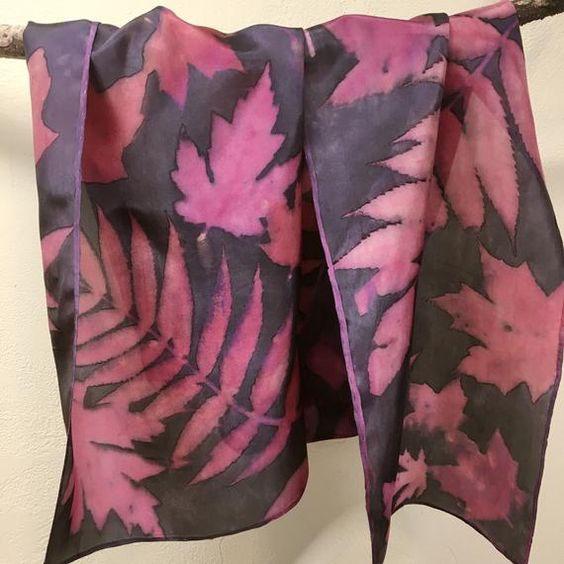
2 minute read
what is eco printing?
Eco printing can be suggested as a different approach to conventional natural dyeing. This technique is very rich application field involved in combination of art and scientific method. It allows designers and artists to present their imagination unrestrictedly. Unpredictible results, patterns, colours and visual effects are possible. Eco dyeing and printing is a kind of art form creating visual effects through natural colourants existing in plants, fruits, vegetables, waste materials, by-products etc. These techniques are contact methods using plants as natural stencils consequently producing astonishing and interesting shades, textures, traces and marks on fabric surface. Different kinds of fabrics such as cotton, linen, jute, hemp, viscose, Tencel, wool, silk, specialty protein fibers, etc. can be used. On the basis of practices and core knowledge of traditional natural dyeing methods, contact dyeing and printing process can be guided to obtain unique surface properties on the fabric.
This sustainable technique can be defined as an alternative way to produce random/symmetrical asymmetrical patterns, marks and partially coloured surfaces through direct use of different parts of plants/trees/fruits/vegetables etc. Unlike conventional natural dyeing and printing methods, vegetal parts are directly enclosed and bundled in fabric with or without rod. Single fabric layer or multiple layers containing plants like sandwich can also be employed. Fabric pockets are post treated to extract, activate and fix the dye molecules into the fabric. This fixation step which is made by steaming, boiling or batching is crucial to generate satisfactory print effects, textures, darkness, colour shades and colour yields. An intriguing and attractive characteristic of an eco printed surface is the tendency of plant pigments to separate into unexpected constituent colors, giving impressions of “broken colour” on the substrate, with patterning and colourings of spontaneous nature. These effects can be made more predictable by the selective use of mordants and dye assistants such as iron or copper, by applying acid or alkalis to shift pH, or by combining dye plants in the bundle in order to mix new colors right on the substrate. Plant materials should be securely wrapped in a premordanted textile or layered between sheets of watercolor paper; the bundle is tied tightly with string and perhaps weighted with a brick, then steamed over water or simmered in water or natural dye. Different print effects are obtained by layering, tying, folding, clamping or stitching metals, rocks, twigs, etc. onto the substrate Different colors can be obtained depending on recipe, mordant and extraction. Use of ferrous sulfate will create browner areas while copper sulfate will produce green areas. Although natural dyes are generally are associated with protein fibres in terms of achieving more vivid, dark colours and satisfactory results than cellulosic fabrics, nowadays researchers, designers and artists also focuse on other textile fibres. It is known that cotton fibre generally produces more dull colour shades. Papers and nonwovens can also be substrates for contact dyeing/eco printing
Advertisement
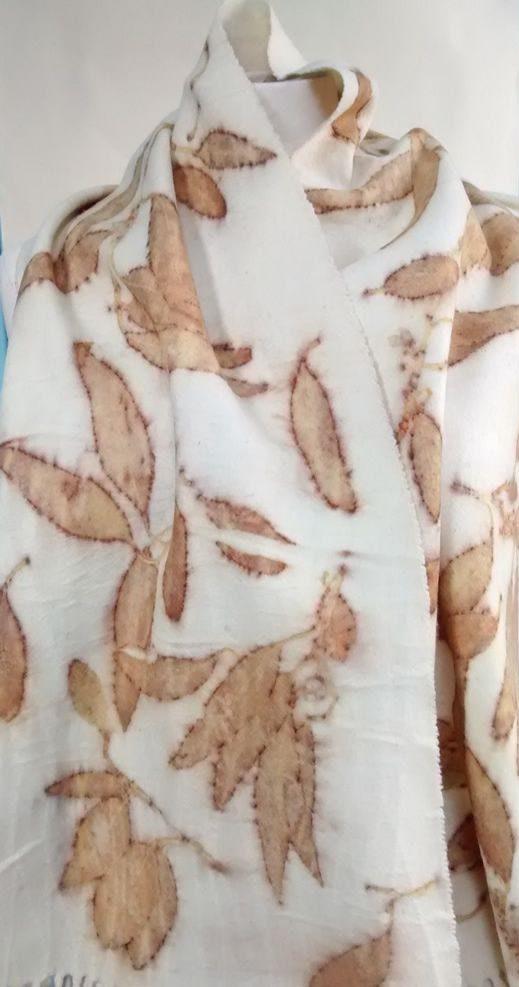