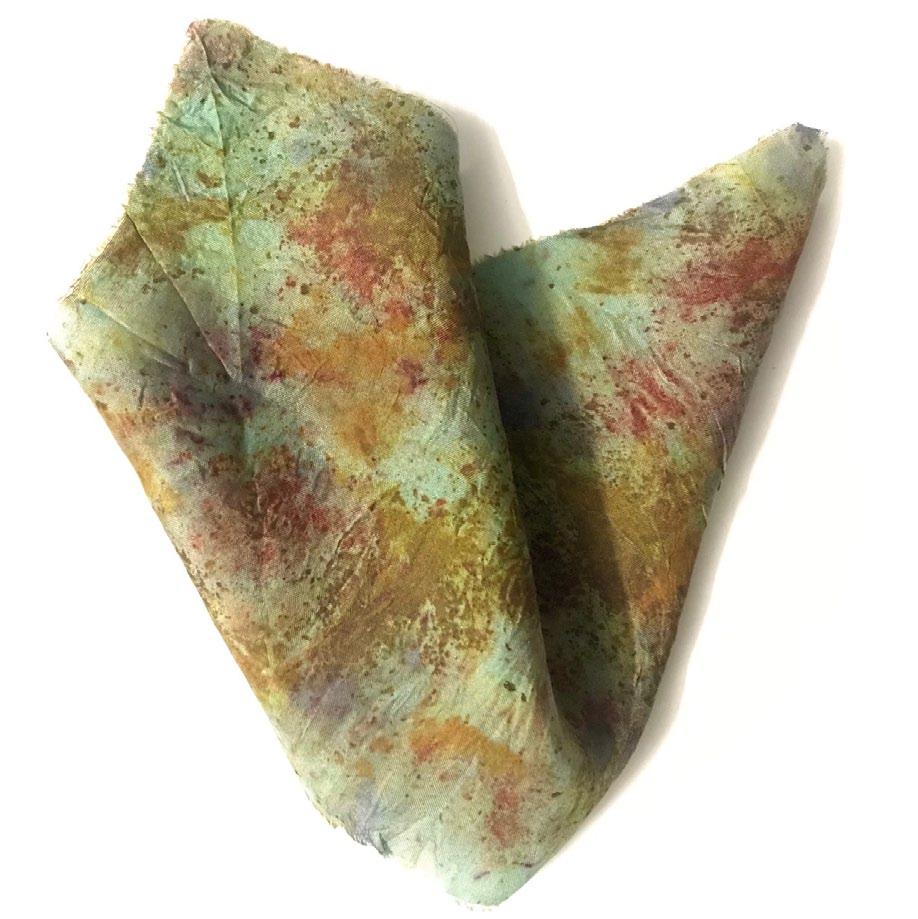
9 minute read
fabrics used
Techniques used
Bundle Dyeing : It is a natural dyeing process done using flowers, leaves, natural dye powders, etc. on paper or fabric.
Advertisement
Unlike eco-printing, bundle dyeing will not have a proper form to it. The structures are rather abstract giving it a very mordern and unconvetional texture and look.
We tried doing bundle dyeing using several natural dye powders like madder, marigold, annatto, etc. , garden and food waste.
Fig 17: Bundle dyed Tulsi Silk
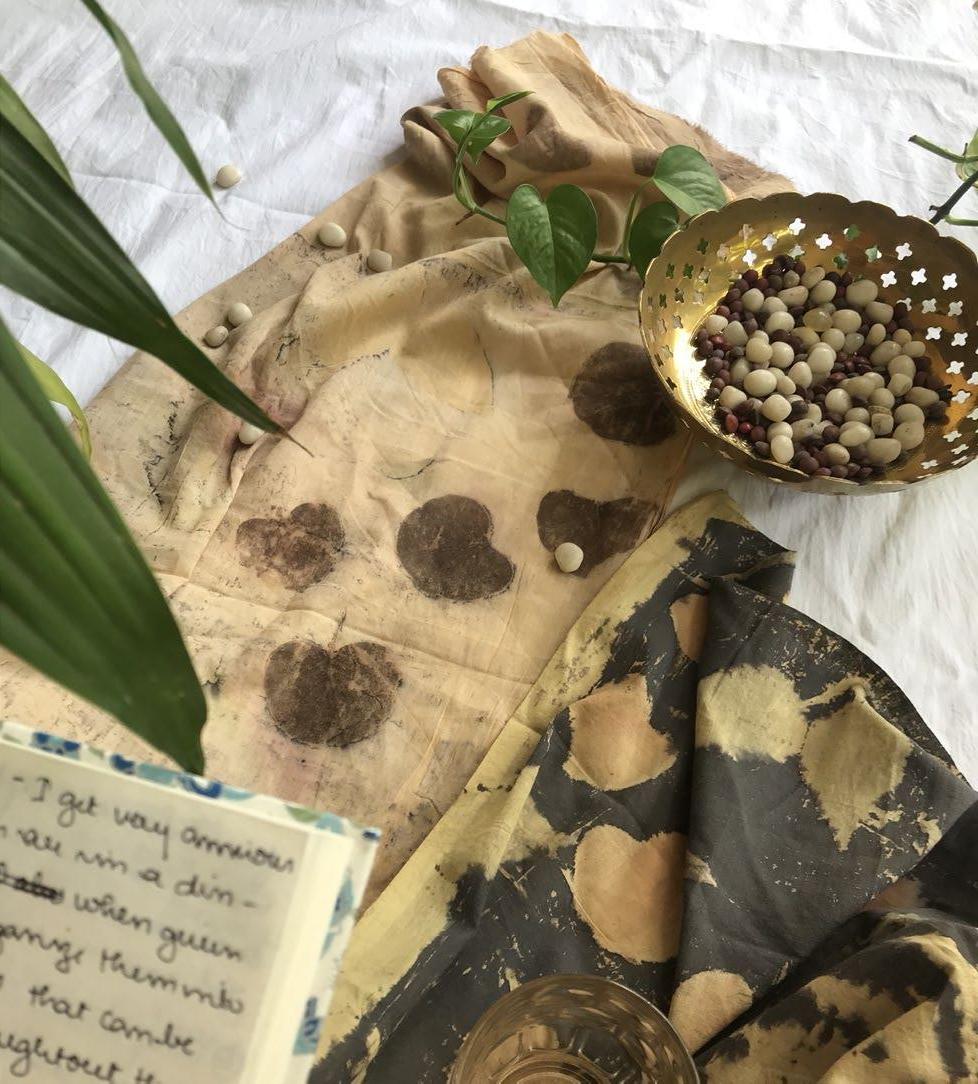
Fig 18: Eco resist printed cotton tannin and iron blankets Resist Eco Printing : It is a natural printing process done using flowers, leaves as barriers. The flowers or leaves used in this technique need not have tannin in them. It is a completely different technique compared to the normal technique of eco printing.
Here we use the reaction between a tannin (Myrobalan) and FeSo4 (Iron Water) that produces beautiful shades of greys and browns to create lovely pieces of apparel that are distinctive and every bit special
We used several wild leaves and flowers to create the beautiful formations. Eco Printing : It is a natural printing process done using flowers, leaves and other organic materials. The materials used in this technique need to have tannin, natural pigments or acids in them which reacts with different mordants to leave an imprint on the base fabric when it boiled or steamed.
The most commonly used mordants are alum and iron. which is readily available. Each mordant gives out different shades and shapes proving us a wide spectrum to play with.
Each eco printed peice is an art form. It is unique and one of a kind.
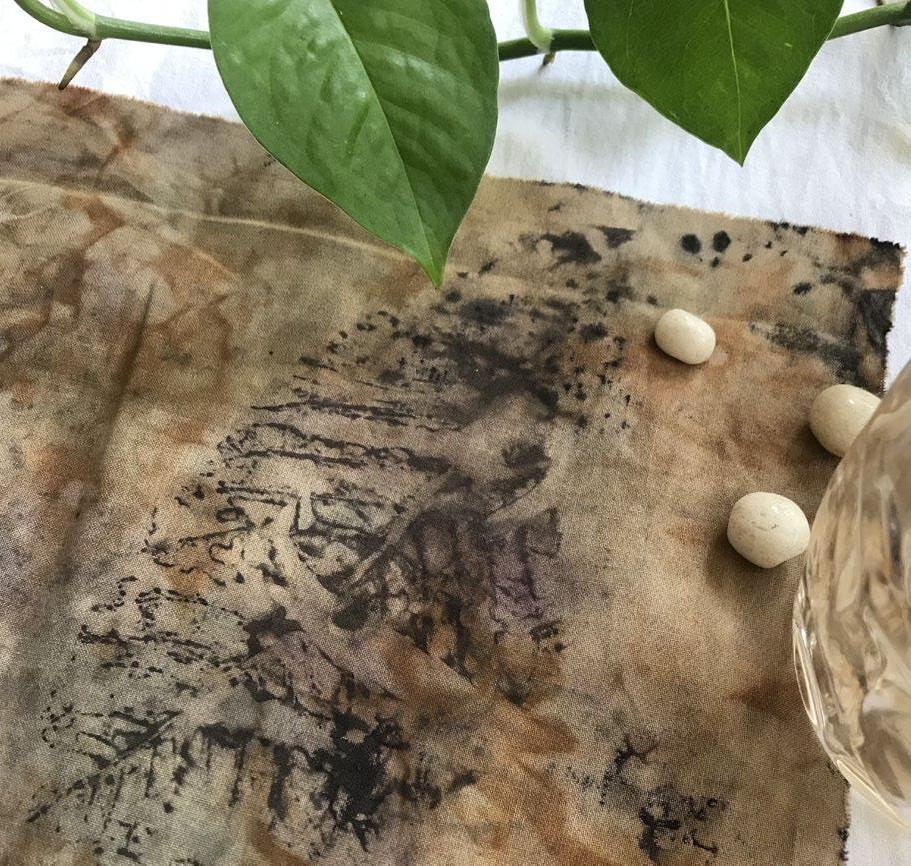
Fig 19: Eco print using guava leaves
Fabrics used
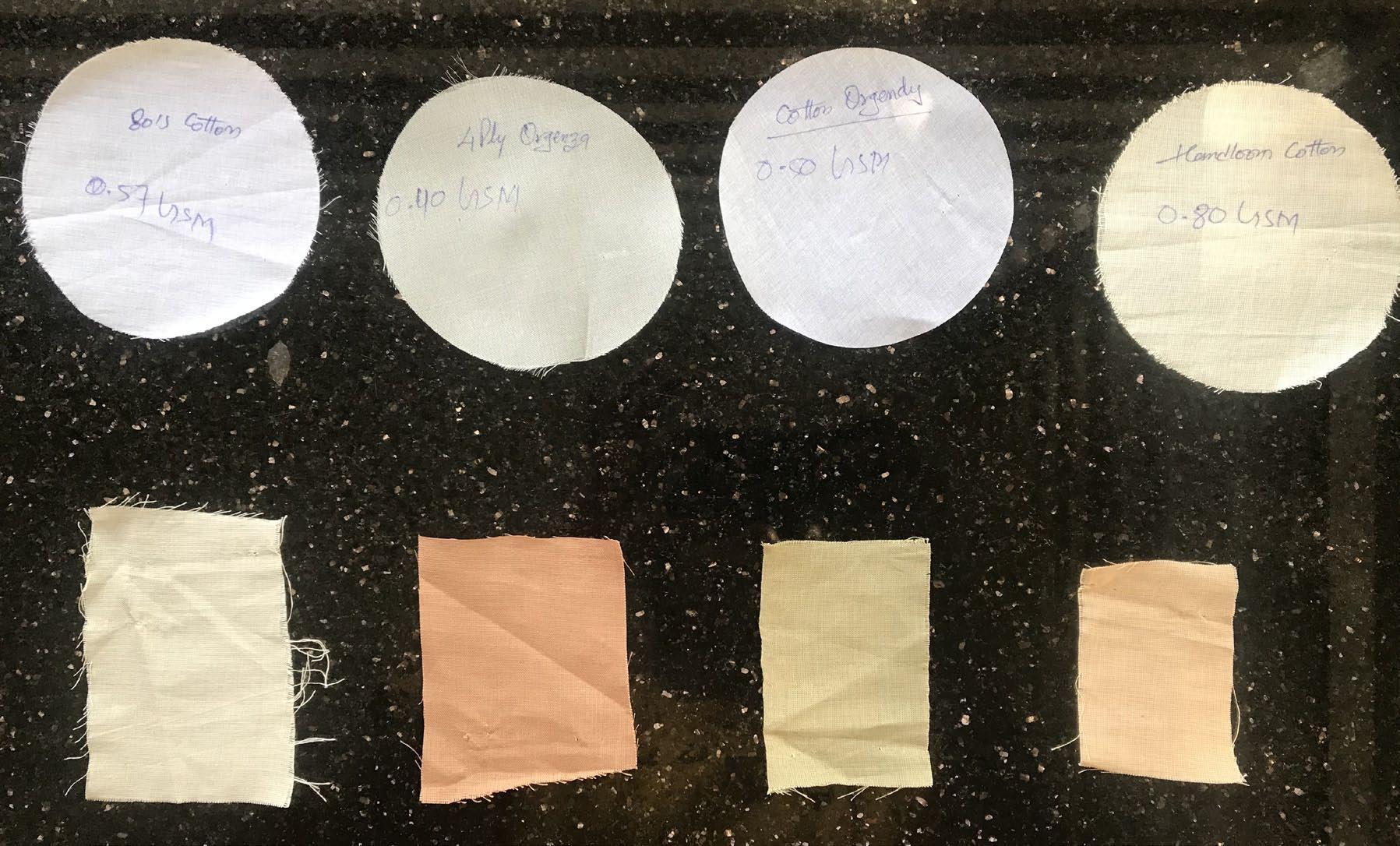
Fig 20: Final Fabric Swatches

• Fabric - Cotton Voile
• GSM - 0.57
• EPI - 68
• PPI - 55 • Colour - white • Not print/dye ready. • Fabric - Cotton Organdy • GSM - 0.50

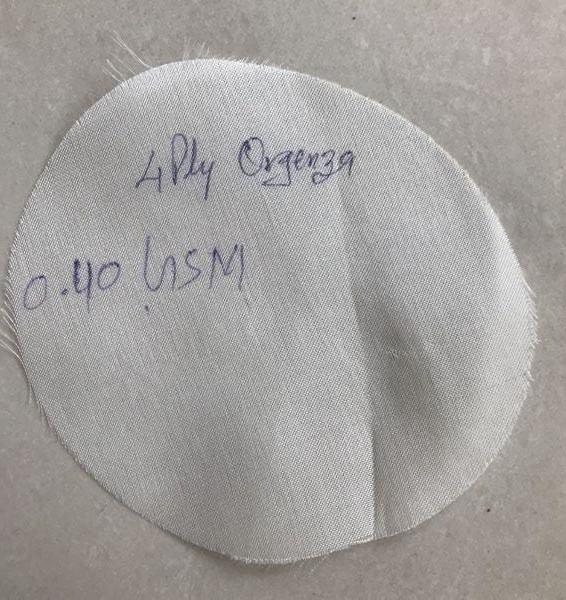
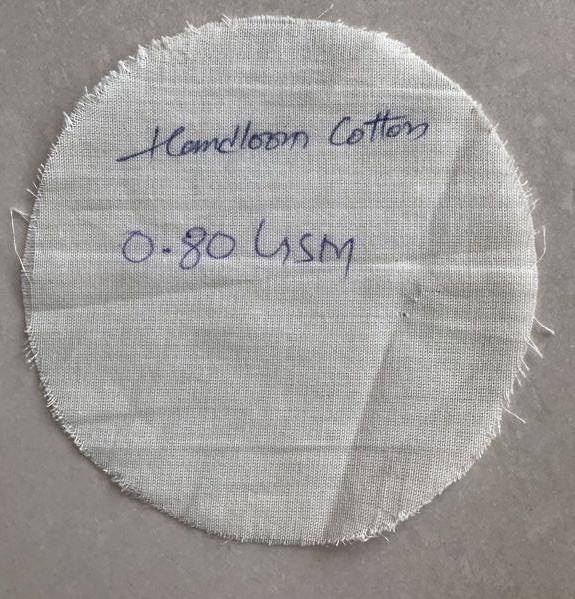
• EPI - 65
• PPI - 30 • Colour - white • Not print/dye ready.
• Fabric - 4 Ply Organza • GSM - 0.40
• EPI - 74
• PPI - 65 • Colour - white • Print/Dye ready.
• Fabric - Handloom Cotton (Ayur Fabric) • GSM - 0.80
• EPI -50
• PPI -44 • Colour - white • Print/Dye ready.
Dyeing the fabric - Myrobalan
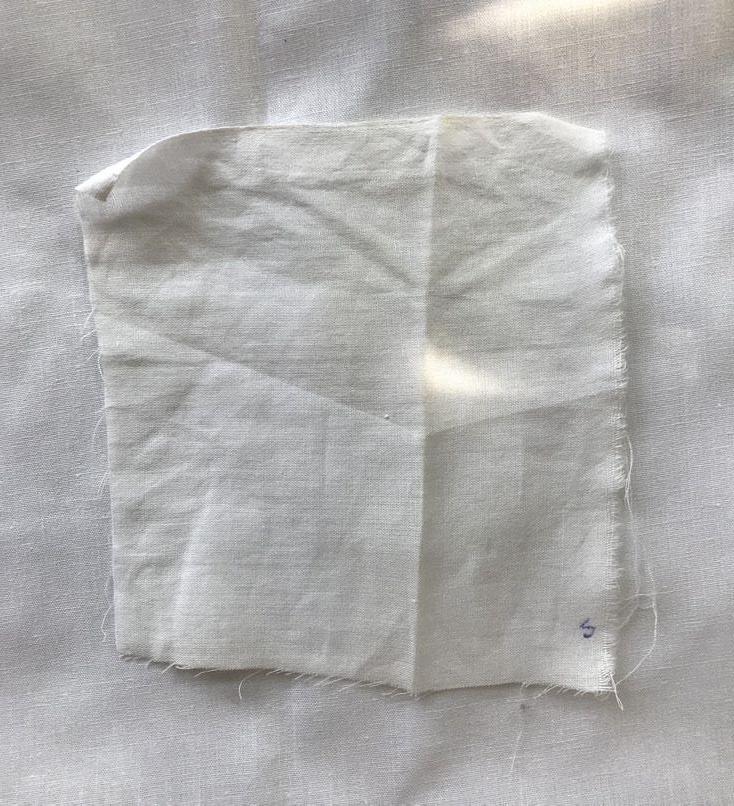
Fig 21: Scoured Cotton Fabric Fig 22: Myrobalan dyed Fabric. Left - 10% for 30 mins Middle - 15% for 30 mins Right - 30% 30 mins
Fig 23: Iron dipped Myrobalan dyed Fabric in lower concentrations Left - 10% dipped in 2% iron Right - 15% dipped in 2% iron

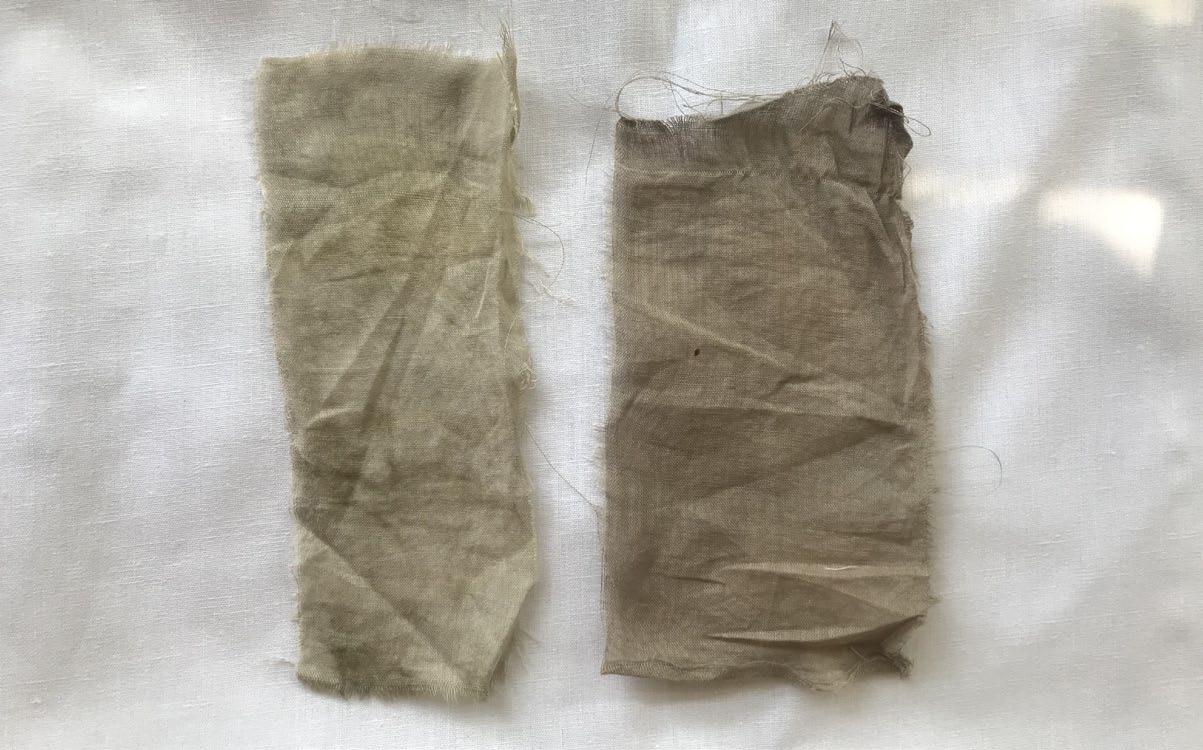
Finalised concentration
Fig 24: Myrobalan dyed Fabric 30% Fig 25: Iron dipped Myrobalan dyed Fabric. Left - 30% in 2-3% FeSO4 Middle - 30% in 5% FeSO4 Right - 30%in 7-8% FeSO4
Fig 26: Left - myrobalan dyed 4 ply Organza Right - Iron Dipped 4 ply Organza Fig 27: Left - myrobalan dyed Organdy Right - Iron Dipped Organdy
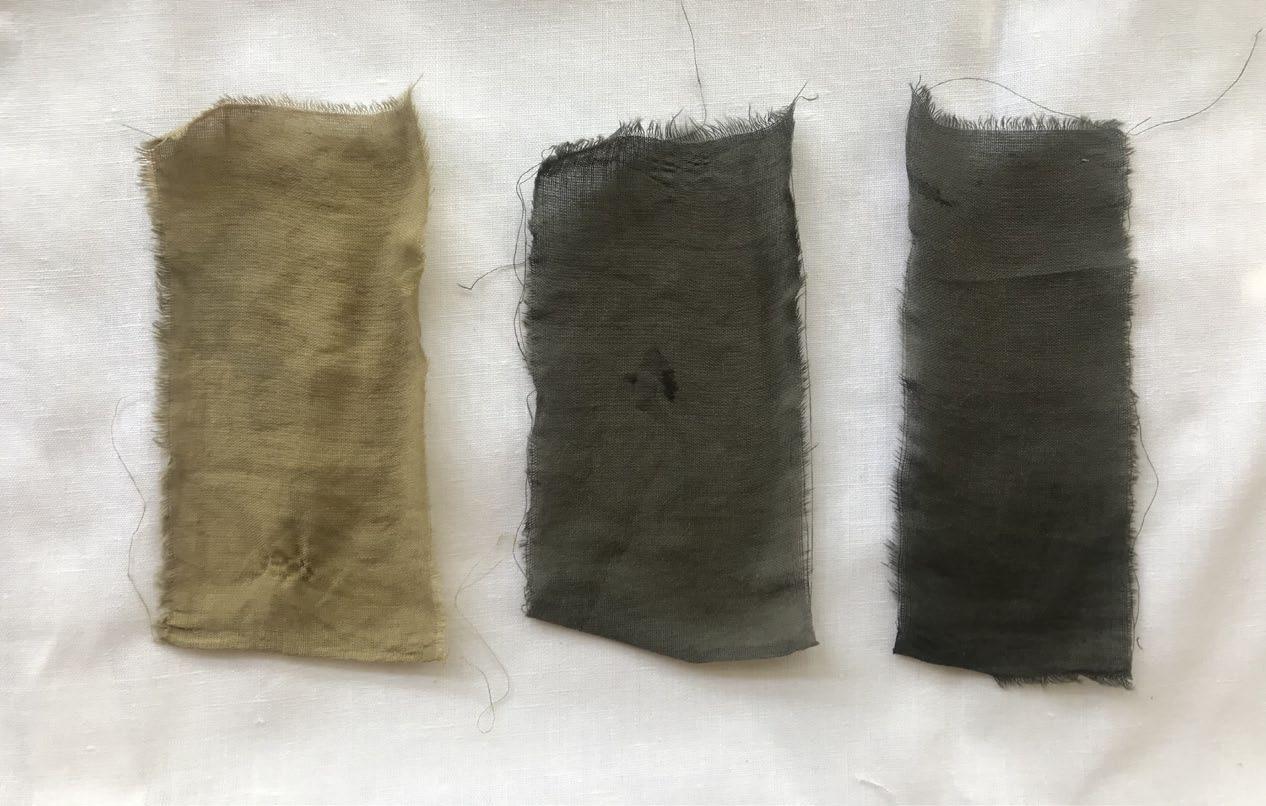
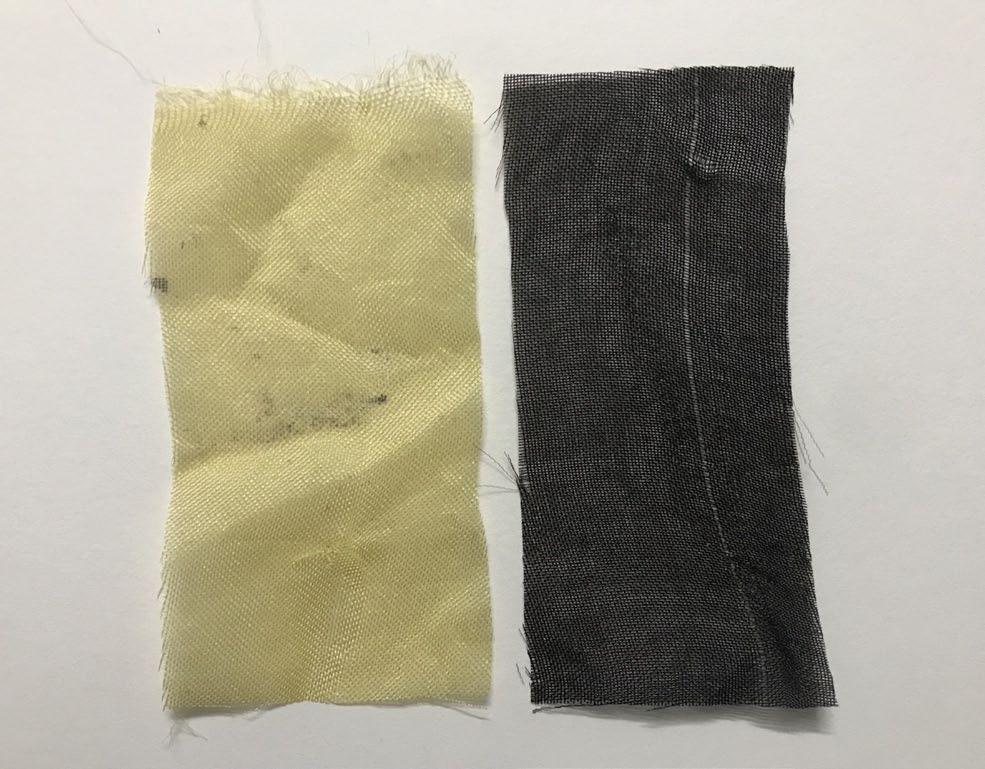
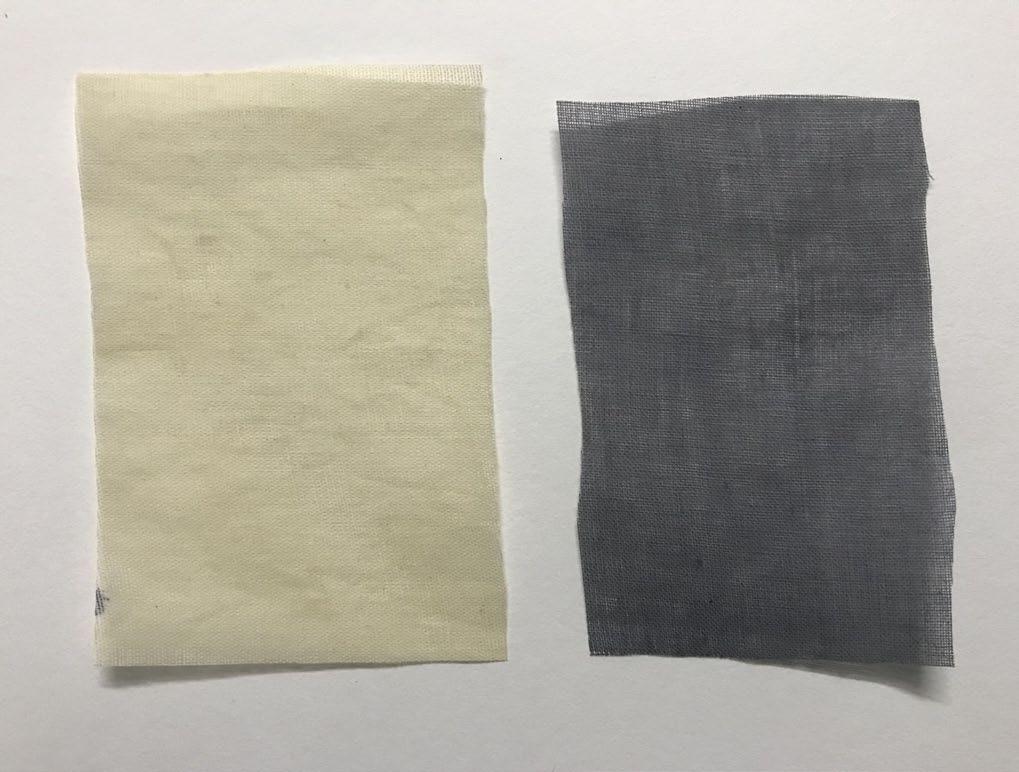
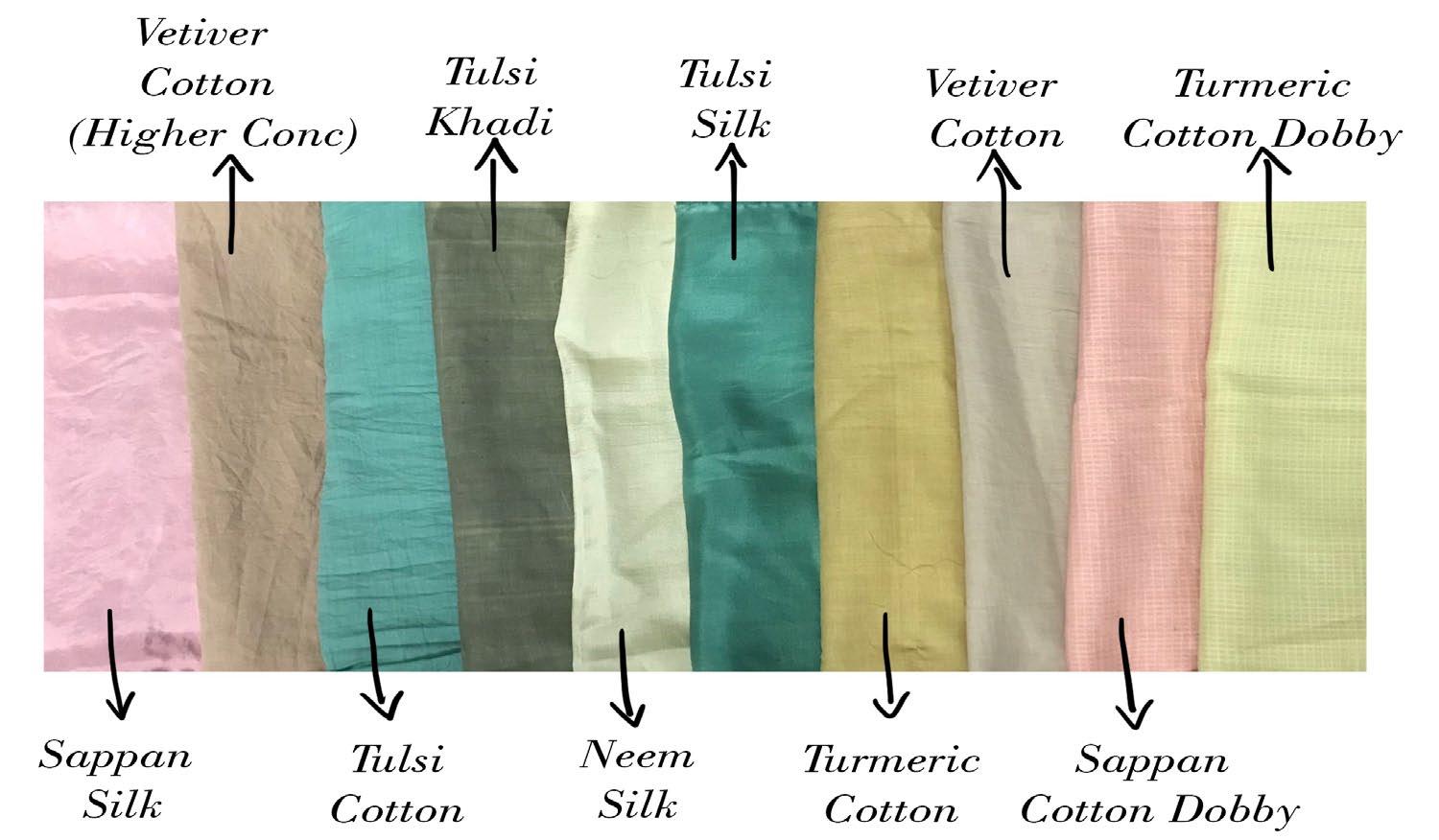
Mordanting the fabrics
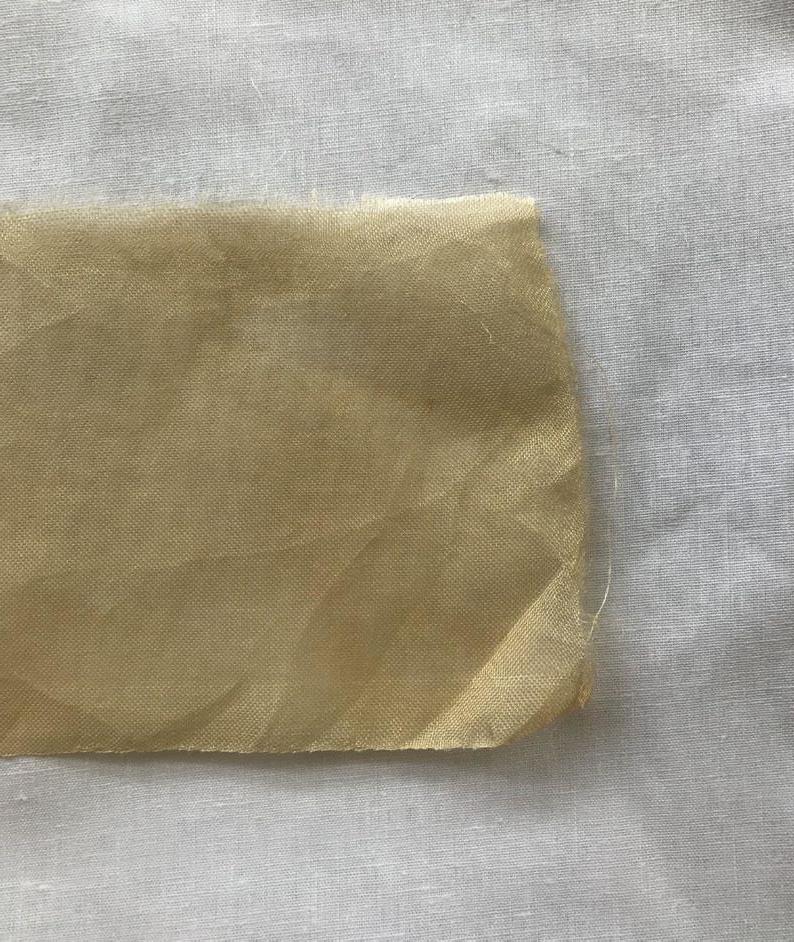
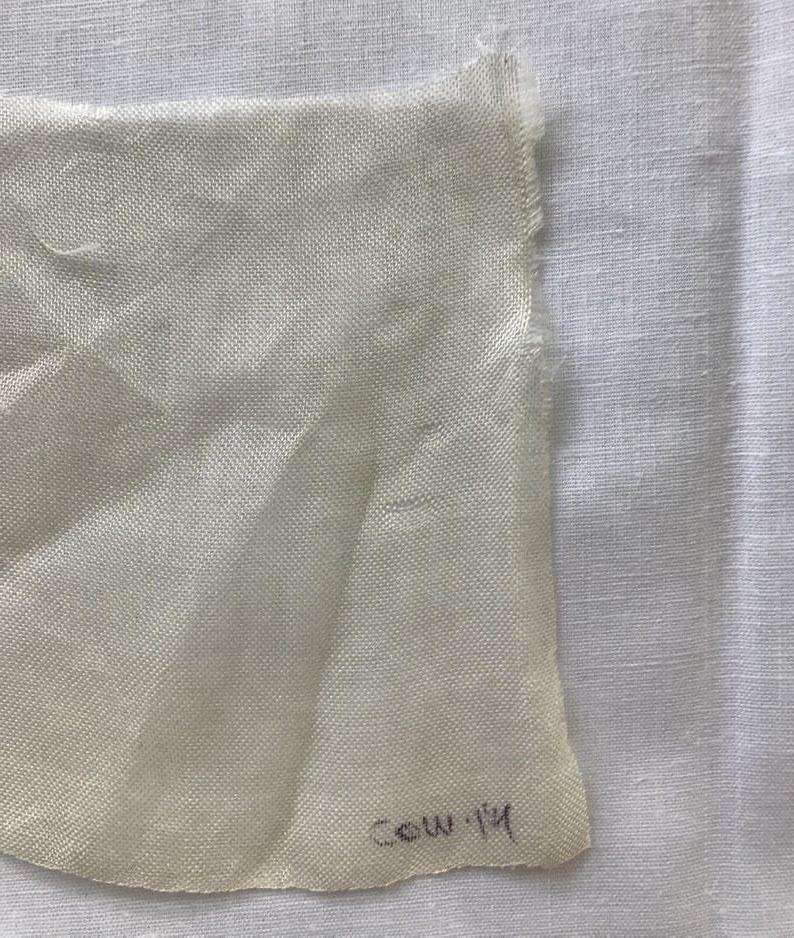
Fig 28: Organza Mordanted with 5% FeSO4 Fig 29: Organza Mordanted with Cow Milk
Fig 29: Organza Mordanted with 20% Alum Fig 30: Cotton Mordanted with 20% Alum
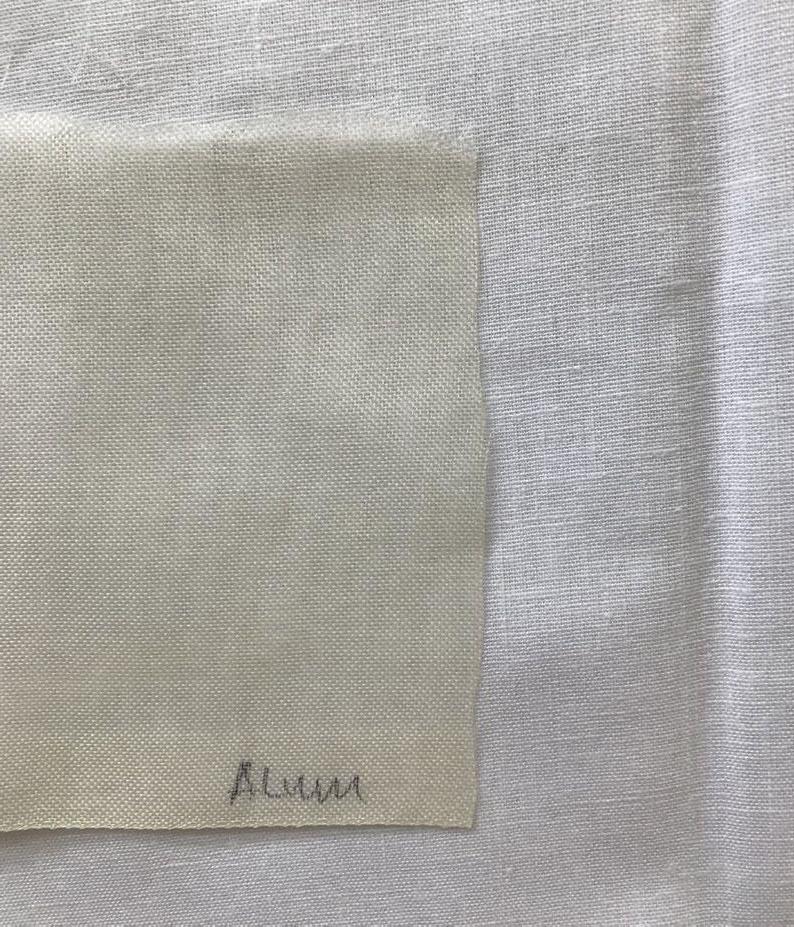
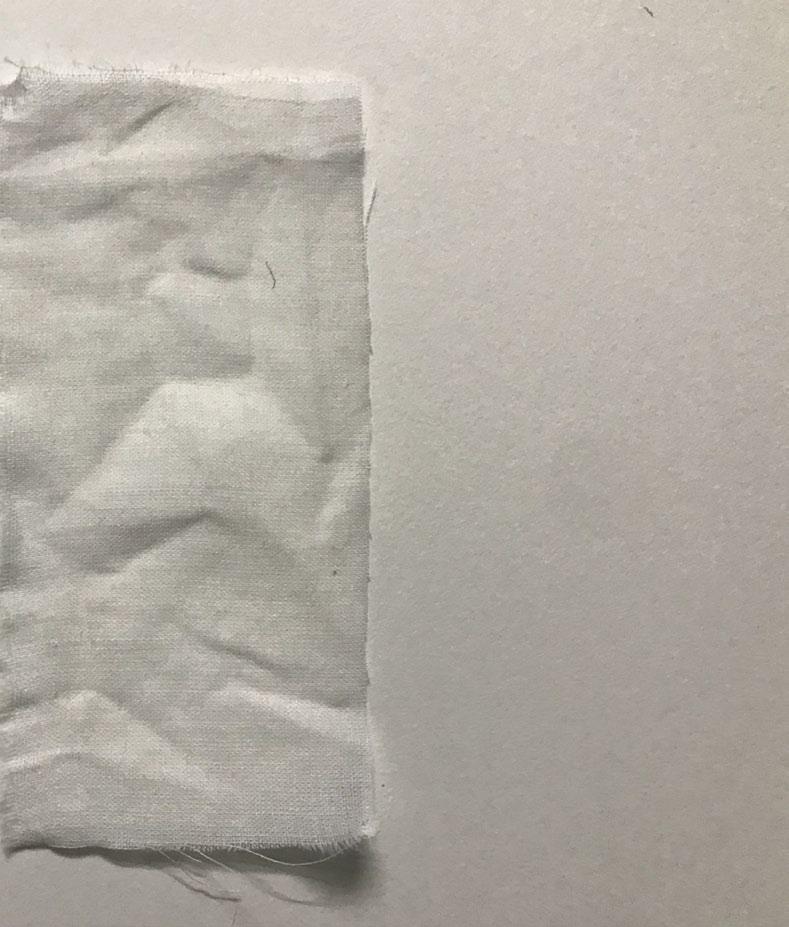
Knowing ayur vastra
What is Ayur Vatra?
Ayurvastra or medical dress is made of 100% pure organic cotton or silk, wool, jute & coir. These eco-friendly garments made from natural fibers and herbal dyes. They are easy on the skin and are well suited for hot and humid climatic conditions. Ayurvastra helps the human body to shed toxins and to improve metabolism. The cloth is woven with special herbs and is permeated with oils that can cure various ailments including diabetes, skin infections, psoriasis, arthritis, rheumatism, hypertension, and asthma among others, and are found to enhance the immune system of the body.
Why Ayur Vastra?
• With people becoming more health-conscious all over the world, ‘Ayurvastra’ fabrics have a great scope in times to come. • Ayurvastra not only reinforces the importance of sustaining the planet for future generations but also considers the well-being of current generations using age-old practices. • Ayurvastra can play an effective role in the revival and elevation of the market for eco-friendly fabrics. Thus, it may be taken as an emerging or new area of entrepreneurship and job opportunity for young people on one hand and on the other contribute towards offering economic stability to the nation.
Finalised ayur vastra
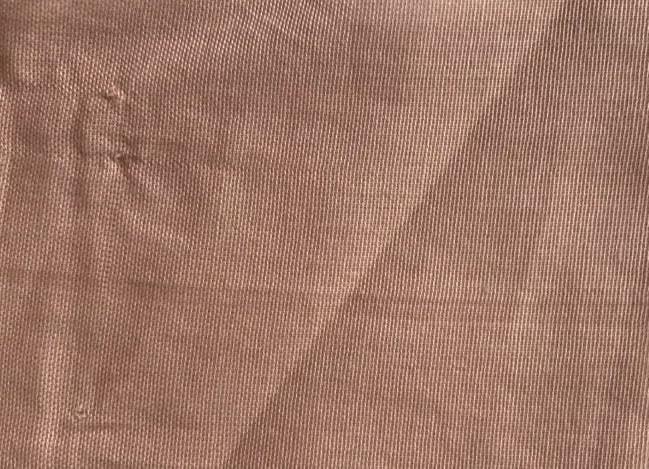
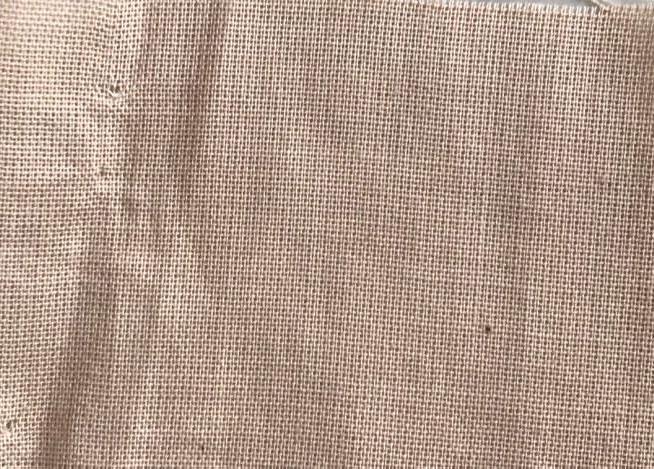
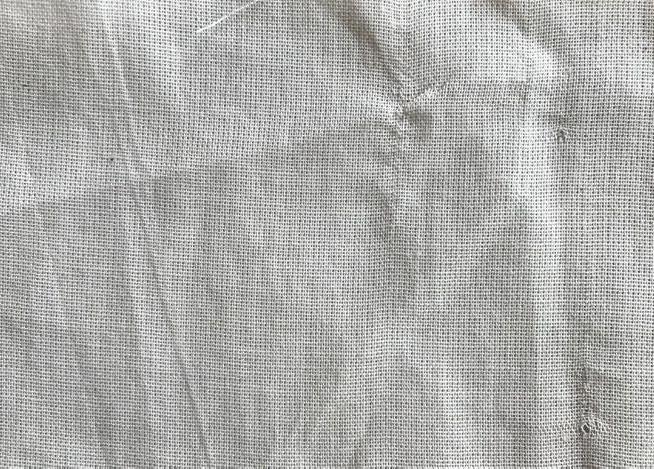
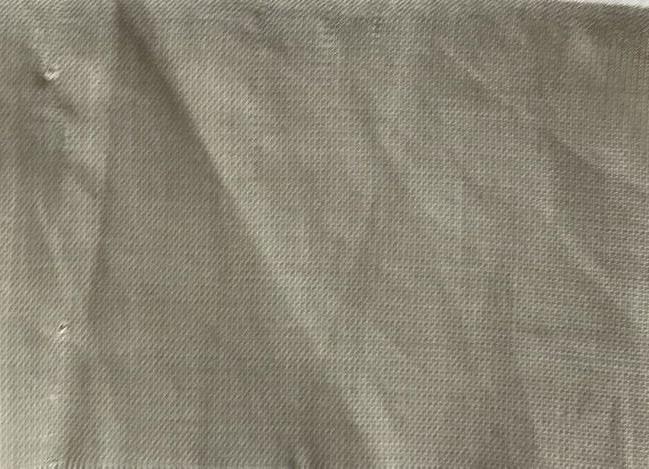
• Fabric - Sappan Ayur Vatsra • GSM - 0.80gms • Colour - Brick Red • Print ready.
• Fabric - Vetiver Ayur Vastra • GSM - 0.80gms • Colour - Brown • Print ready.
• Fabric - Neem Ayur Vastra • GSM - 0.80gms • Colour - white • Print ready.
• Fabric - Tulsi Ayur Vatsra • GSM - 0.80gms • Colour - Olive • Print ready.
How it is made
Materials required :
• Mordants (Alum, FeSO4) • Dye powders (for bundle dyeing) • Myrobalan Powder (for resist eco printing) • Plant materials (leaves, flowers, seeds, etc) • Fabric • Wooden dowels
• Steamer • White twine • Plastic sheets
• Measuring cup • Buckets • Other relevant stationary like scissors, measuring tape etc. Iron Sulphate (FeSO4)
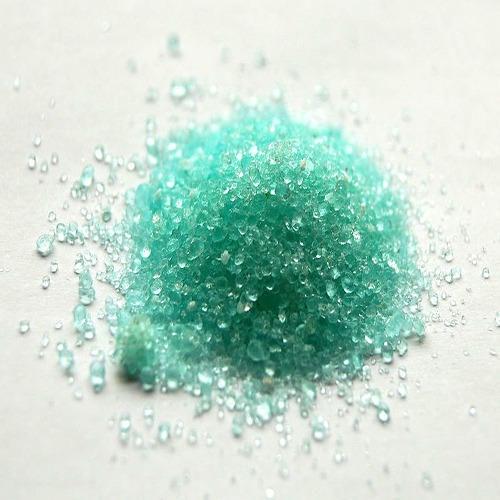

Alum
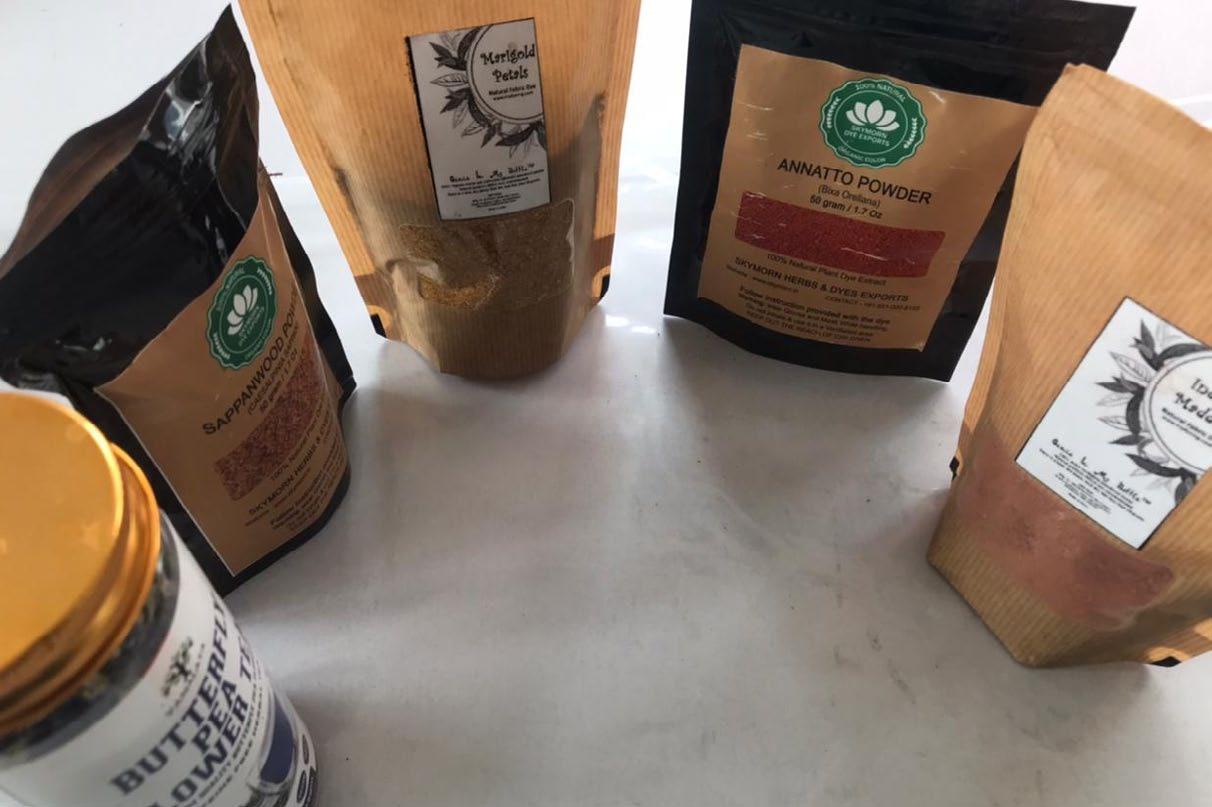
Dye Stuff Twine, plastic sheet and other stationary

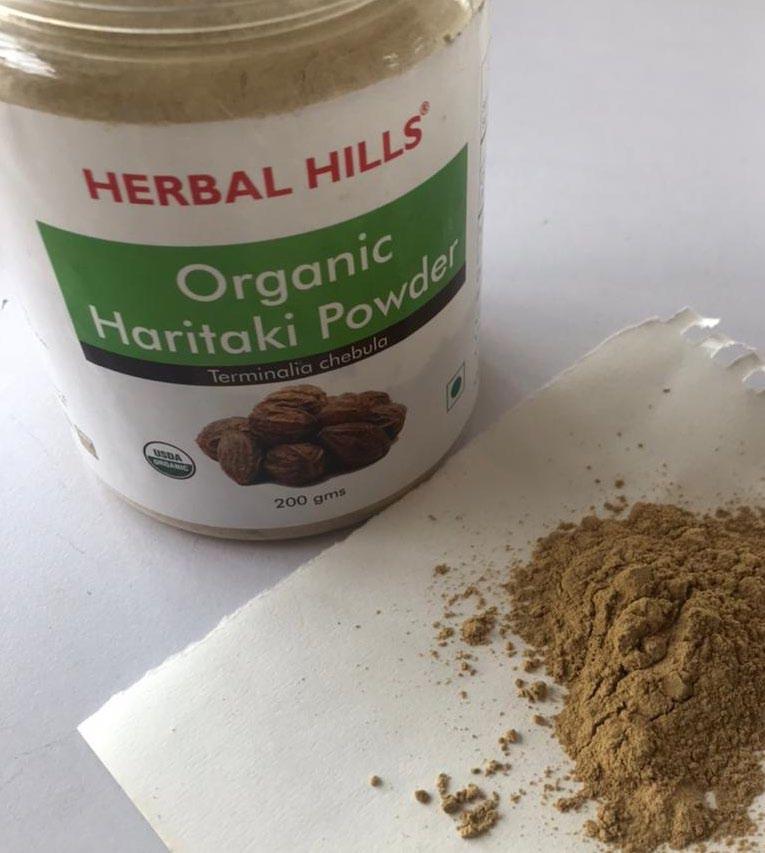
Myrobalan Powder Leaves and Flowers
Process (eco print/ bundle dyeing) :
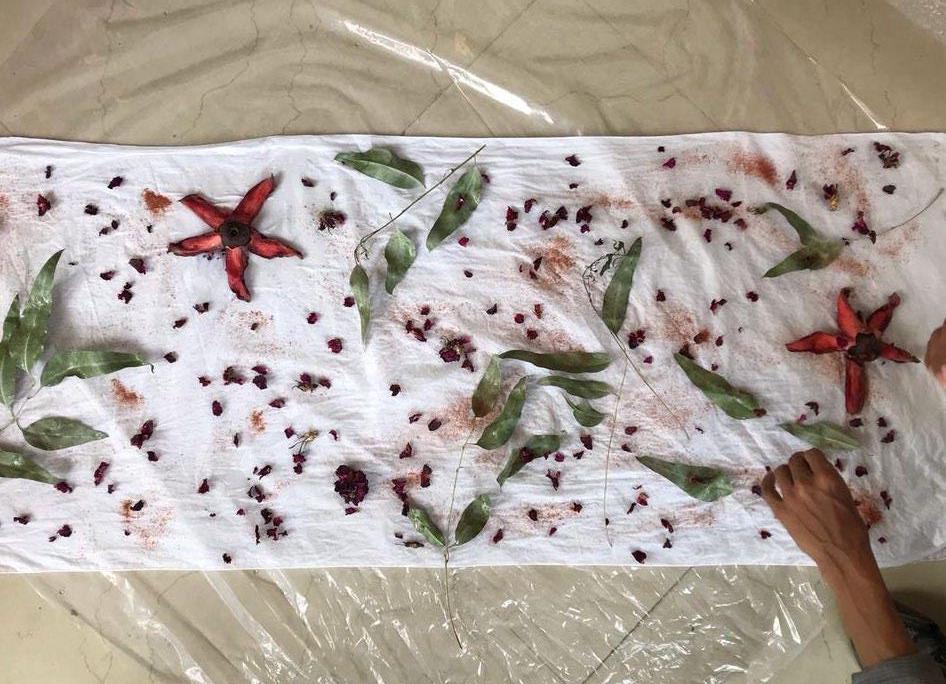
• Scouring the Fabric (Boiling for 4 to 6 hours in water) • Soaking plant materials required in water so they are malleable and easy to work with. • Treating the scoured fabric with the required mordant in this case we used alum. • Placing the fabric on a plastic sheet and laying the plant materials on the fabric according to the placement. • Creating a barrier by placing another sheet of plastic so the colours don’t transfer to the other side of the fabric • Folding the fabric and rolling it on a wooden dowel and tightly tying using a white twine ensuring there’s good contact between the fabric and plant material. • Steaming the fabric from 30 mintues to an hour depending on the shade of colour required and plant materials used. (eucalyptus requires a minimum of 30 mins to give out colour)
Ș
Note: ✴ Some plants like eucalyptus need to be soaked for more than a week before starting to work with them. This helps release their oils and makes them easy to print with. ✴It is also suggested to soak the plant materials in iron water (FeSO4 solution) for darker prints.
Ș
Calculations:
WOF (weight of fabric after scoring) = X gm
Alum required = 15% -20% WOF = 20/100(X)
FeSO4 required = 2% - 5% WOF = 5/100(X)
Water required for FeSO4 solution = 2:1 (2 parts water to 1 part iron)
• Iron makes bright colours dull • Alum may react with pre-dyed fabrics creating stains.
left: onion eco printed fabric by adiv Right: onion eco printed fabric when treated with iron Alum leaving stains on neem dyed silk

Precautions:
• Since plastic is used as the barrier make sure there is enough water in the steamer otherwise the heat could melt the plastic and fabric could get spoiled. • While handeling FeSO4 or any other chemical use golves. Rememeber to take them off during the steaming process. • If not used in lower concentration iron can degrade the fabric • While using ayur vastra as the base fabric make sure the temperature is below 75°C to ensure the ayurvedic properties retain in the fabric.
Scoured fabric treated with alum
Ș Ș Ș Ș Ș
Laying plant materials and folding Rolling and Tying Steaming Unrolling Wash, rinse and iron
Process (resist eco printing) :
• Scouring the Fabric (Boiling for 4 to 6 hours in water) • Soaking plant materials required in water so they are malleable and easy to work with. • Soaking rough cloth (preferably old cotton fabric) in iron solution to be used as iron blanket for 5-10 minutes • Dyeing the scoured fabric with the a tannin in this case we used Myrobalan. • Placing the fabric (slightly wet) on a plastic sheet and laying the plant materials on the fabric according to the placement. • Placing the iron blanket on top of the plant materials touching the base fabric. • Creating a barrier by placing another sheet of plastic so the colours dont transfer to the other side of the fabric • Folding the fabric and rolling it on a wooden dowel and tightly tiying using a white twine esuring there’s good contact between the fabric and plant material. • Steaming the fabric from ideally for 30 mins or more for dark shades.
Note: ✴ Any type of plant materails can be used for this techniques since they act simply as barriers, restricting the reaction between iron and the tannin from happening. ✴Stronger concentration of myrobalan gives darker shades of greys and browns and vice versa. ✴While folding the fabric turn it over to see if all the areas are equally dark. You can use a small cloth dipped in iorn water to take care of the unevenness.
Calculations:
WOF (weight of fabric after scoring) = X gm
myrobalan required = 20% -30% WOF = 30/100(X) (lesser conc for lighter shades and vice versa)