OCTOBER 2022 fluidpowerjournal.com PRESSURE COMPENSATED FLOW CONTROL VALVES PRECISION LUBRICATION IN FOOD AND BEVERAGE APPLICATIONS PULP (non)FICTION Hydraulics in Paper Manufacturing Test Your Skills Figure It Out PostageOrganizationNonprofitUS PAID Bolingbrook,IL Permit#323 Innovative Designs & Publishing • 3245 Freemansburg Avenue • Palmer, PA 18045-7118

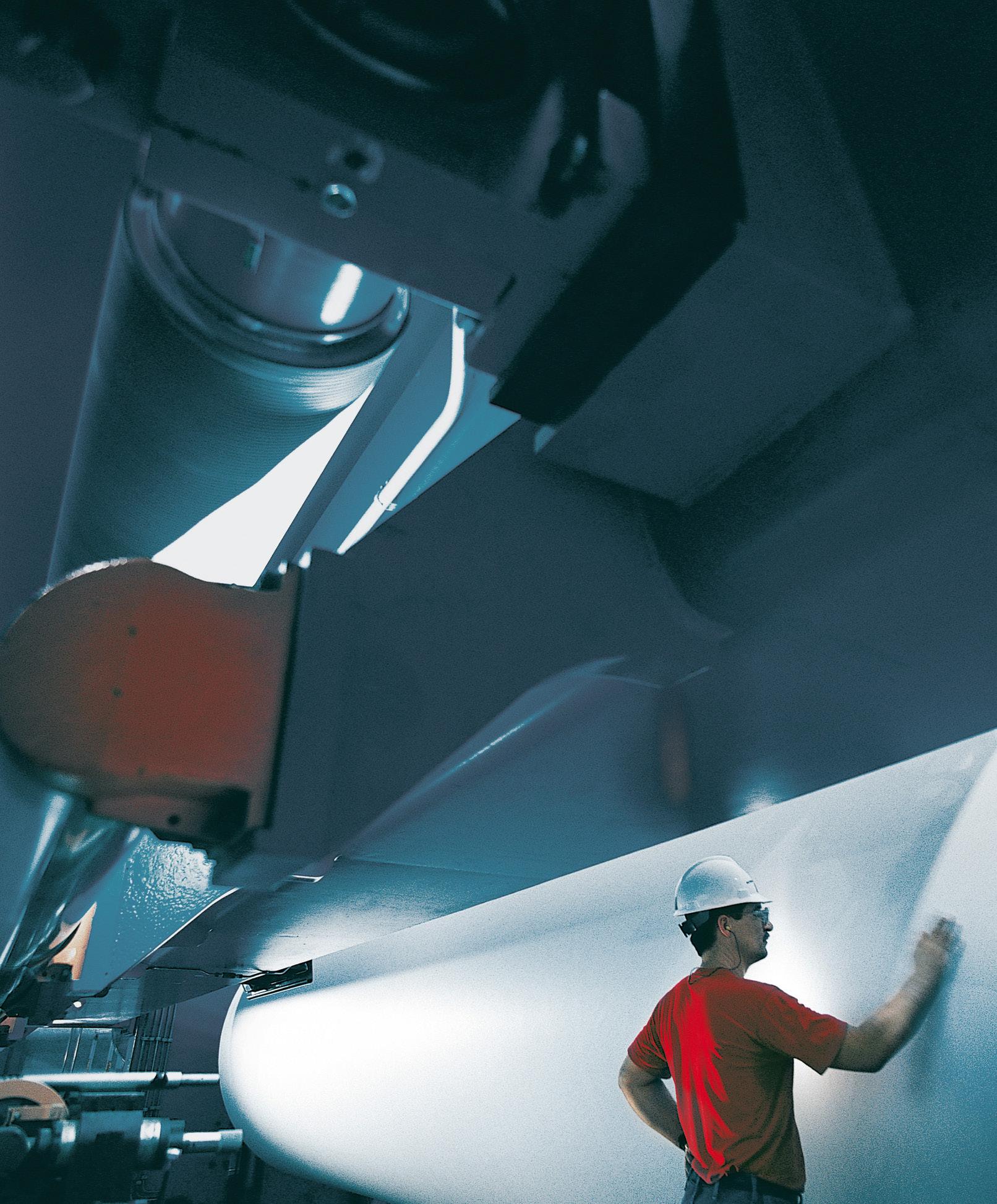
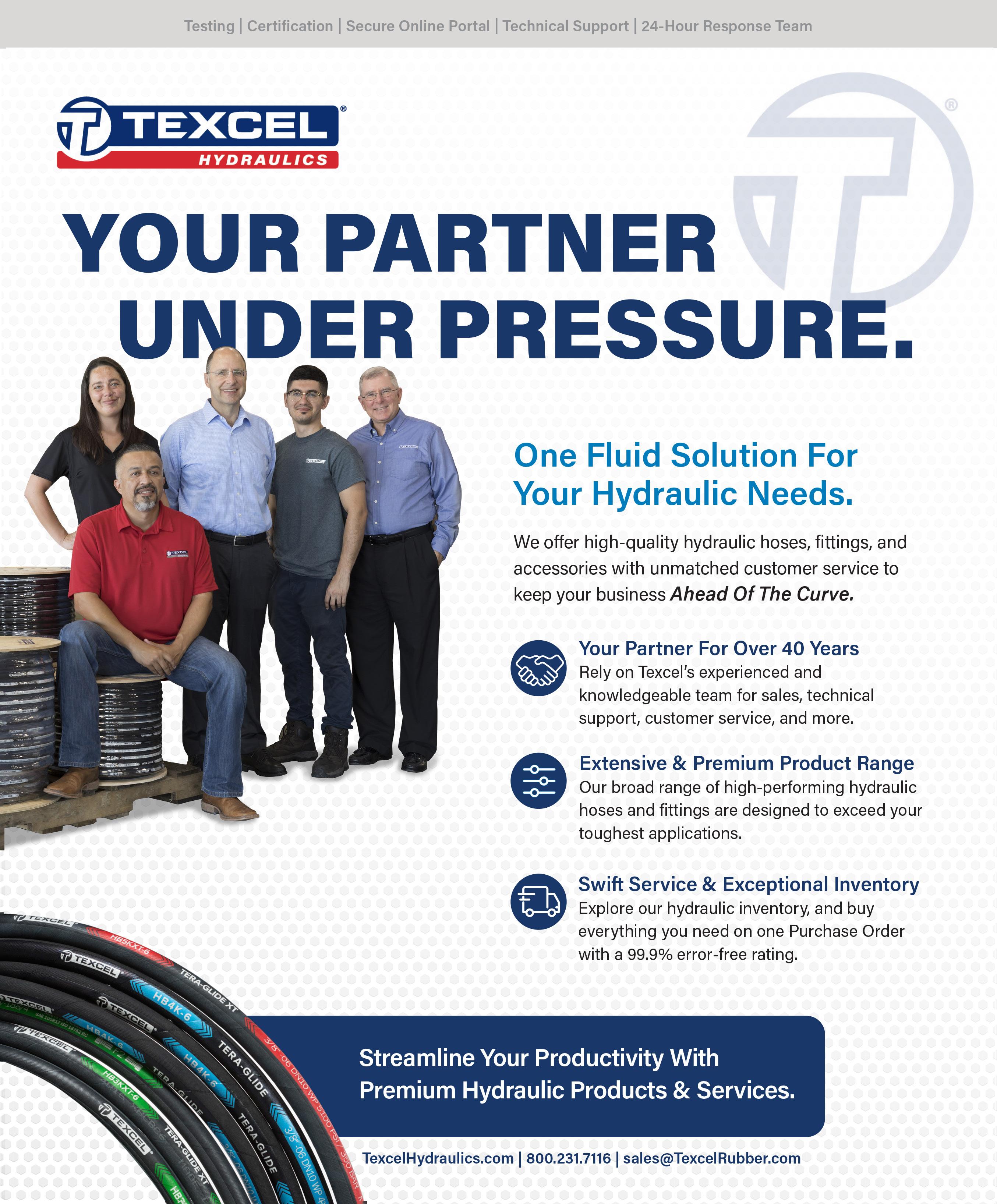
WWW.IFPS.ORG • WWW.FLUIDPOWERJOURNAL.COM OCTOBER 2022 1 y er Tie Rod Cylinder Welded Cylinder YATES INDUSTRIES INC 23050 E. Industrial Dr. St. Clair Shores, MI, 48080 Phone: 586-778-7680 sales@yatesind.com YATES CYLINDERS ALABAMA 55 Refreshment Place Decatur, AL, 35601 Phone: 256-351-8081 alsales@yatesind.com YATES CYLINDERS GEORGIA 7750 The Bluffs Austell, GA, 30168 Phone: 678-355-2240 gasales@yatesind.com YATES CYLINDERS OHIO 550 Bellbrook Ave. Xenia, OH, 45385 Phone: 513-217-6777 ohsales@yatesind.com WE REPAIR AND MANUFACTURE NEW CYLINDERS Yates will cross over any cylinder manufacture and designs. PROUDLY WORKING WITH THE WORLD’S LARGEST PAPER, PULP, AND WOOD PROCESSING COMPANIES CREATING COST SAVINGS ALONG THE WAY.
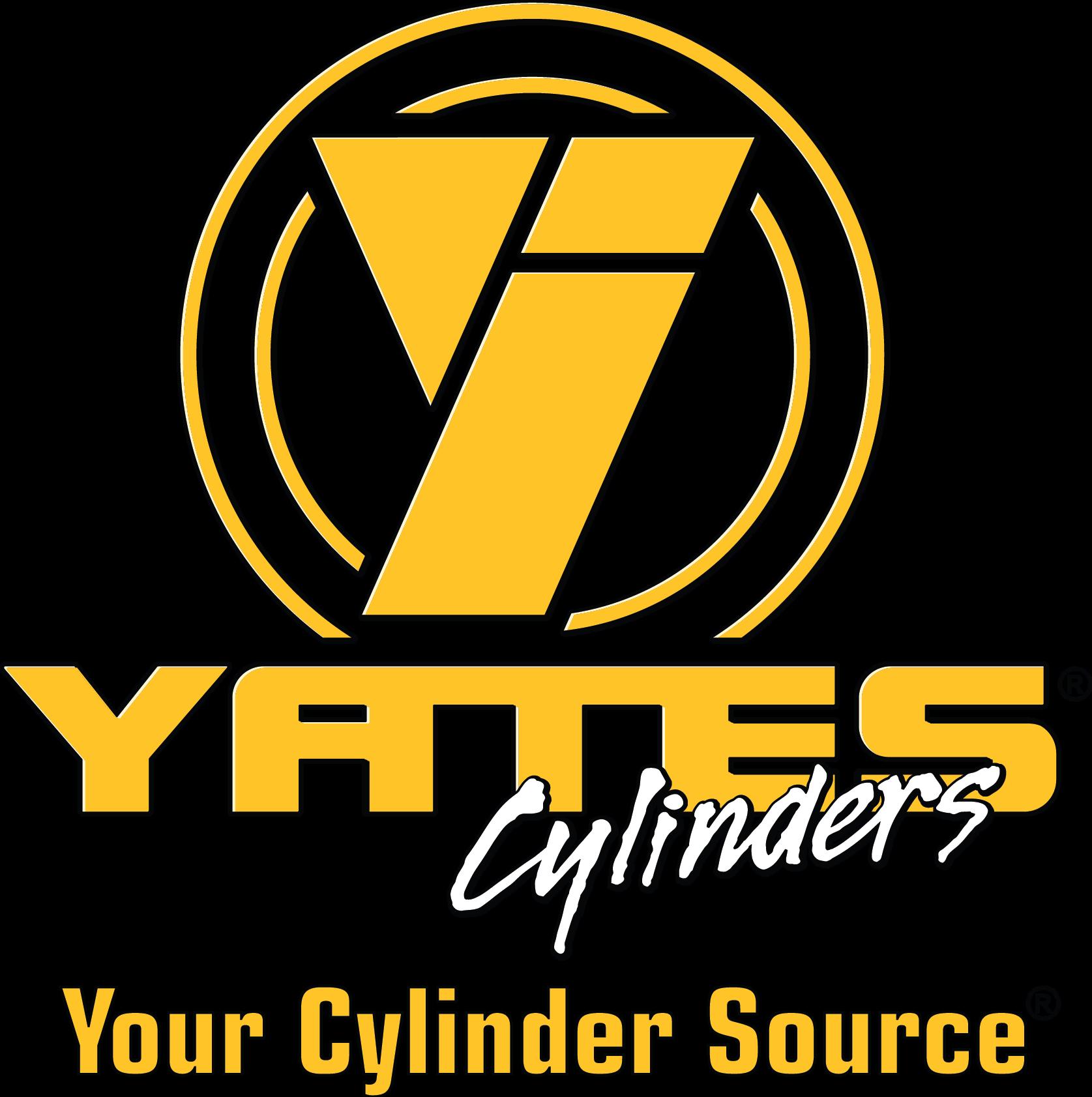

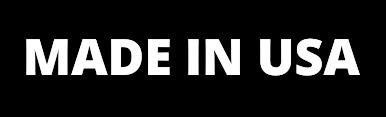
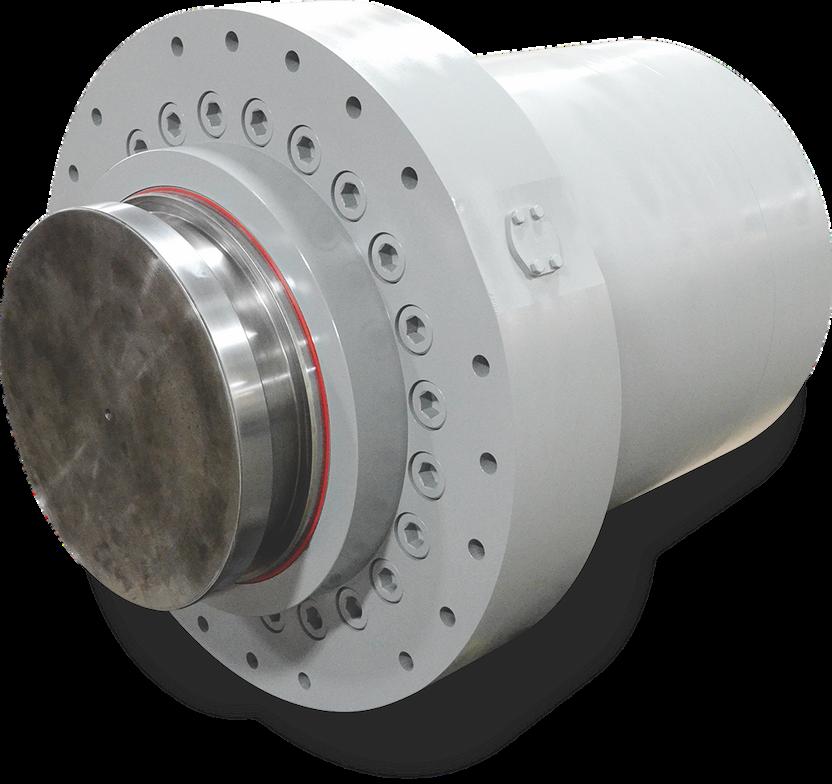
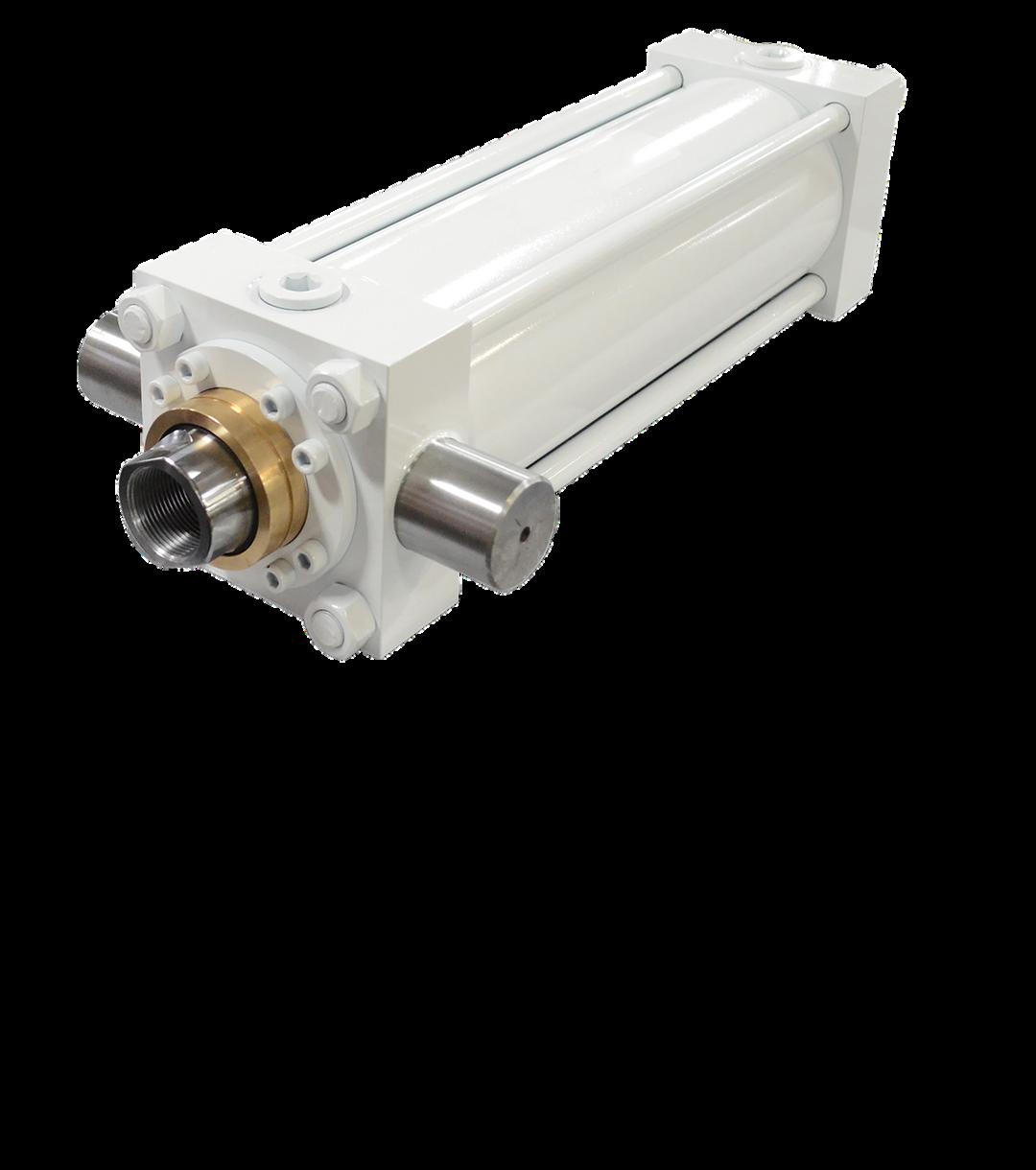

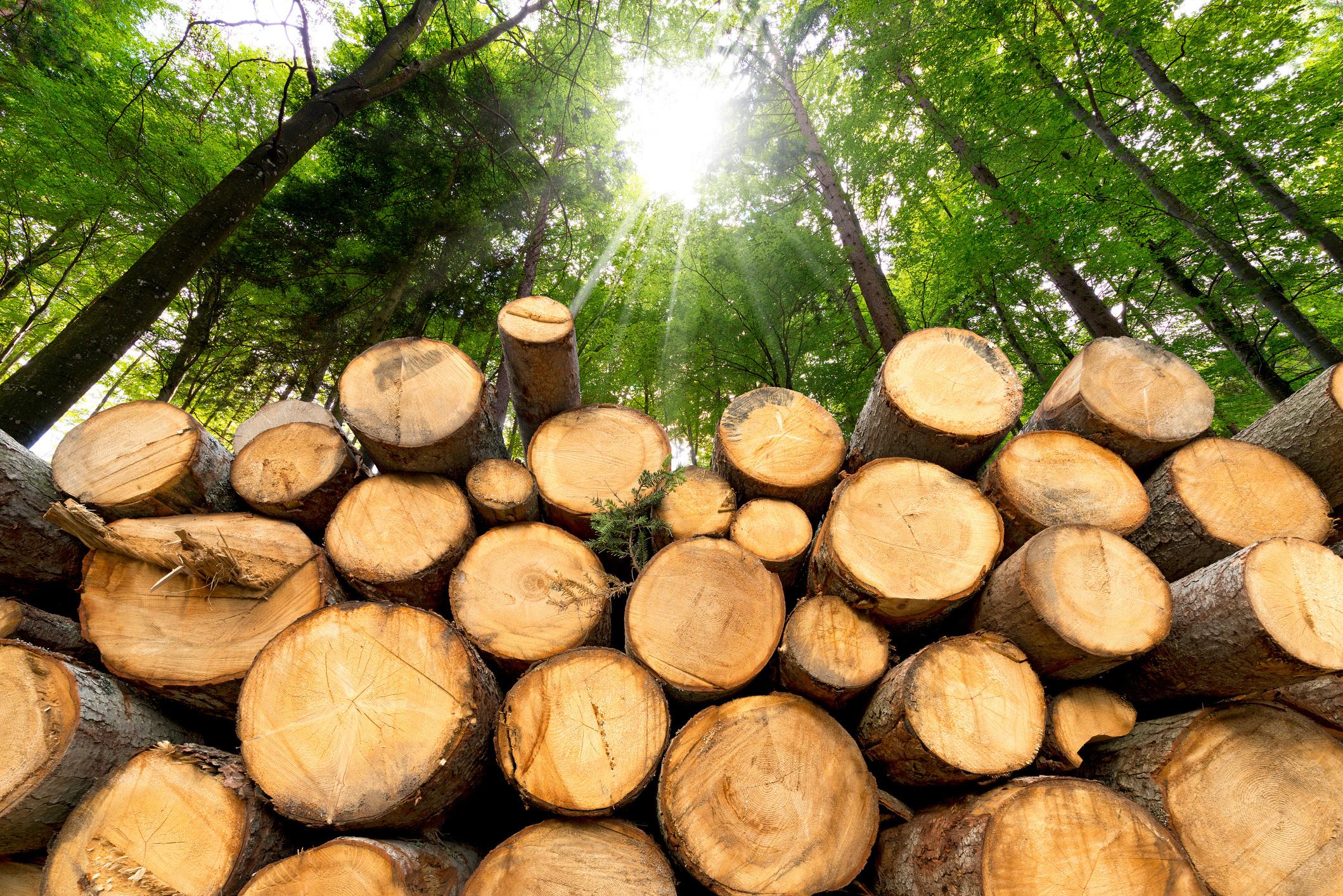
The industry requires a holistic approach to system lubrication.
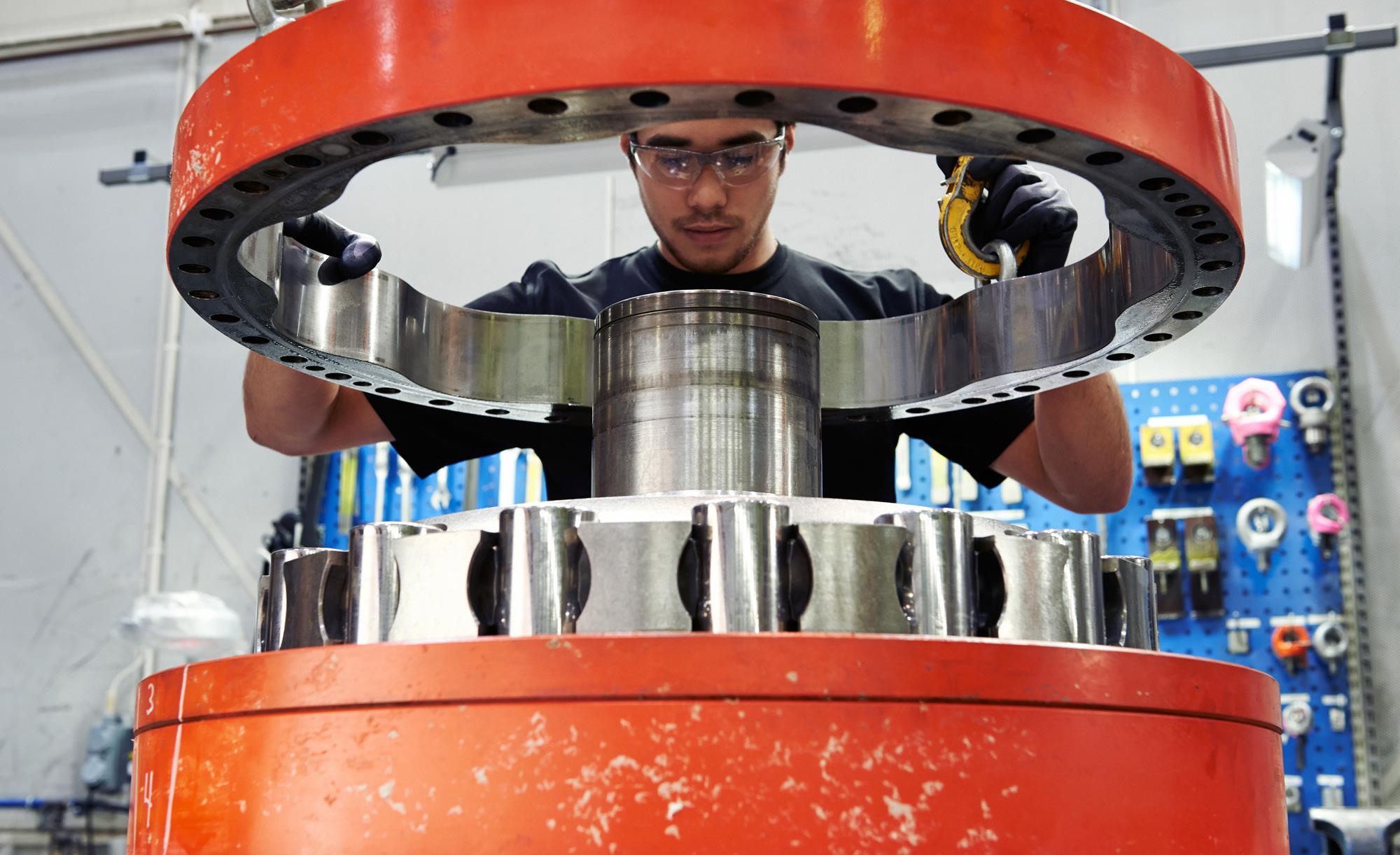

The MHR radio controller combines up to 16 hydraulic proportional valve controllers into a single unit.
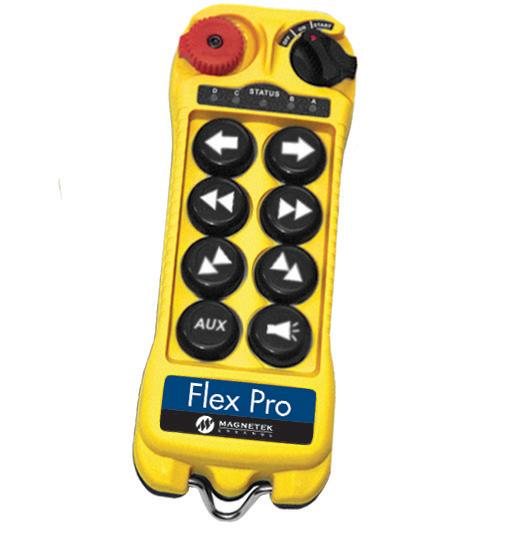

Publisher’s Note: The information provided in this publication is for informational purposes only. While all efforts have been taken to ensure the technical accuracy of the material enclosed, Fluid Power Journal is not responsible for the availability, accuracy, currency, or reliability of any information, statement, opinion, or advice contained in a third party’s material. Fluid Power Journal will not be liable for any loss or damage caused by reliance on obtained in this 29 ISSUE 10
28 6 Departments 4 Notable Words 11 Web Marketplace 11 Product Review 12 IFPS Update 21 NFPA Update 22 Product Spotlight 24 Product Review 25 Figure It Out 31 Classifieds Cer tification Empowers Opportunity. 18
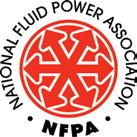
Best practices for direct drive systems to prevent breakdowns and maintain uptime.
•
IN THIS ISSUE
publication. OCTOBER 2022 VOLUME
18 It’s All Right: Precision Lubrication for Food and Beverage Hydraulics

information
26 The Versatile Remedy: Pressure Compensated Flow Control Valves Their closed loop technology provides stable rates with varying pressure drops.
Replacing Hydraulic Valves
Features
28 Case Study: Wireless Controls for Tracked Carrier
10 Test Your Skills
6 Cover Story Pulp (non)Fiction: Hydraulic Maintenance in Paper Manufacturing
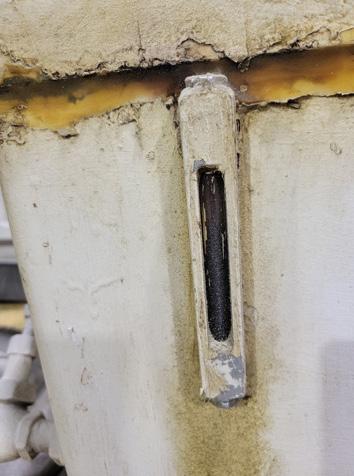
IO-Link Enabled - From air-prep and sensors to valves, switches and actuators
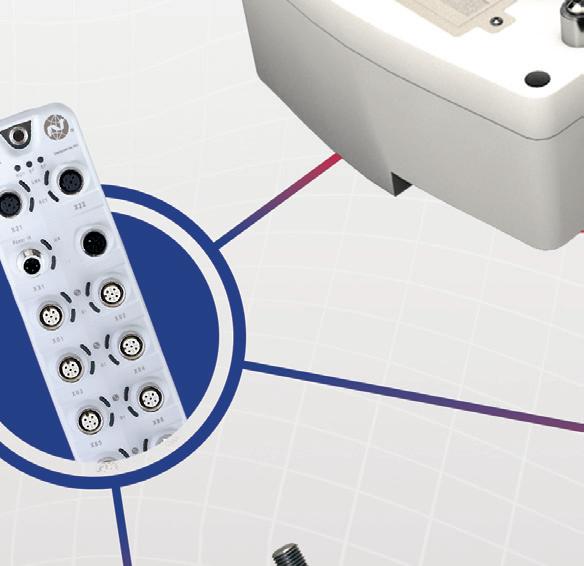
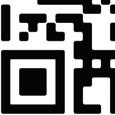


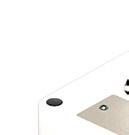
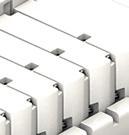
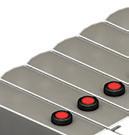
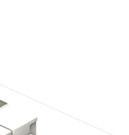
For engineers, there’s no time to waste. That’s why Norgren makes it easy to complete your pneumatic circuit with confidence. With Norgren’s IO-Link enabled pneumatic components, it’s simple to set up your machines and access the data you need to increase productivity and reduce downtime. Save time with Norgren.

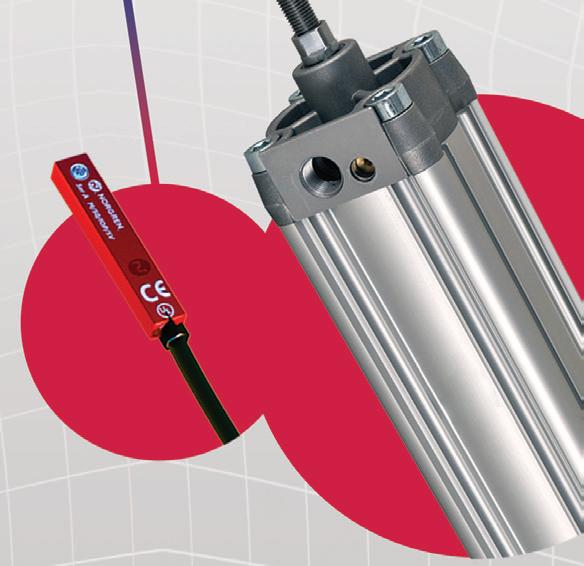
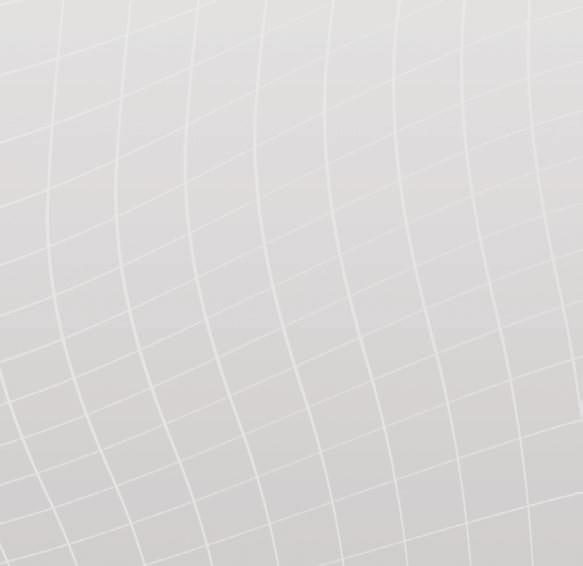


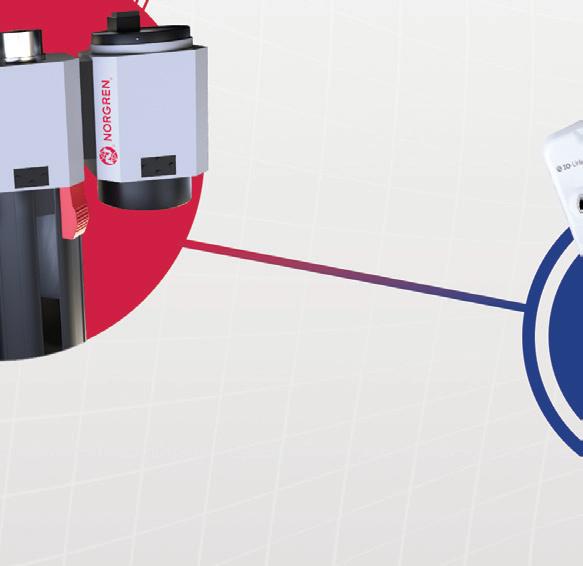

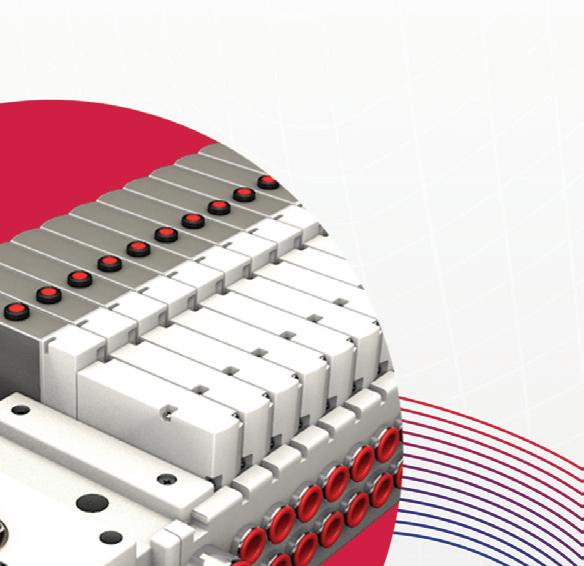
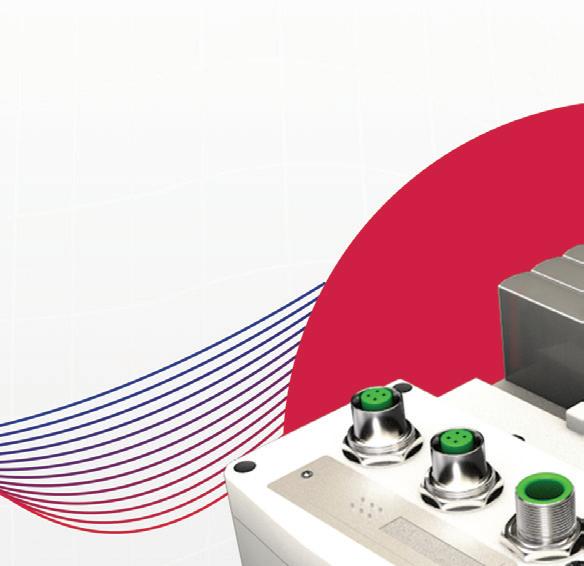
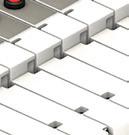
Product Spotlight:
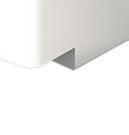
VR Series Valve Manifolds A simple plug-in, sub-base style design allows for easy installation, maintenance and valve exchange. Complete. Connected. Confident. Find out more norgren.com
»
Renowned Reliability - We deliver and support products through our global service network
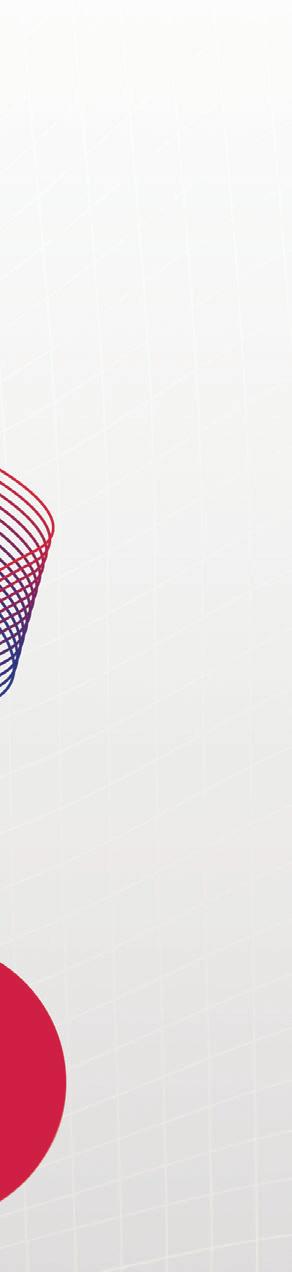
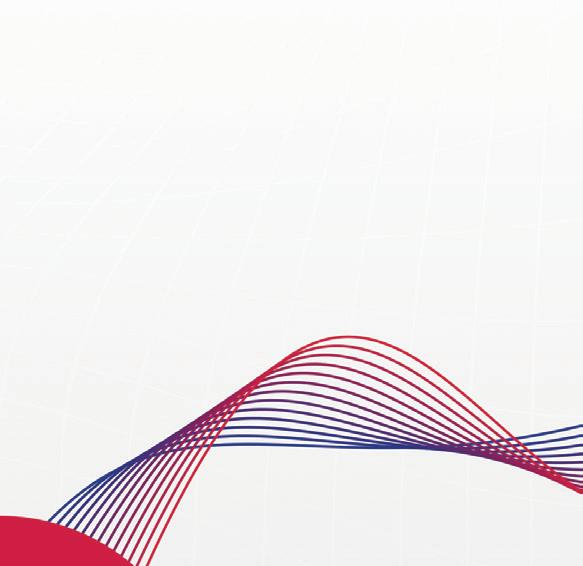
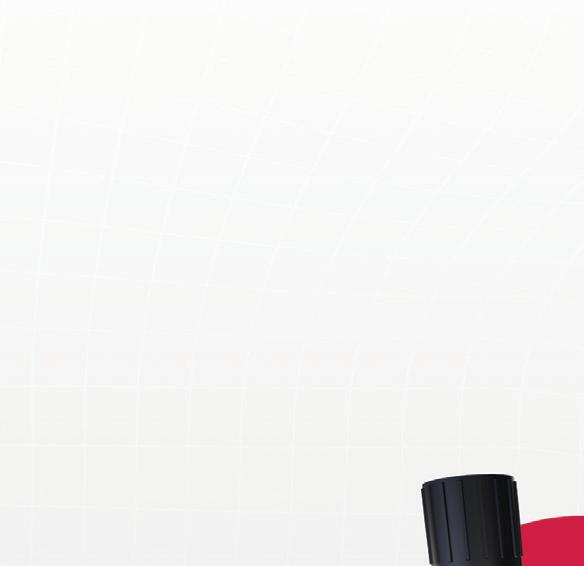
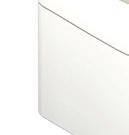

»
Engineered Solutions - Collaborate with us on your machine design challenges
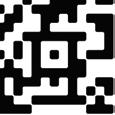
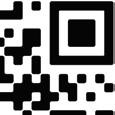
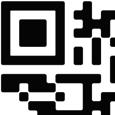
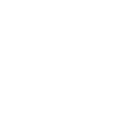
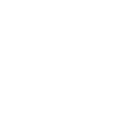
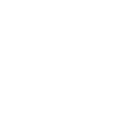
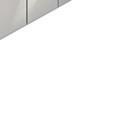
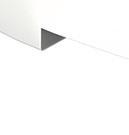
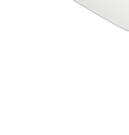
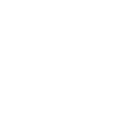


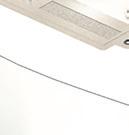
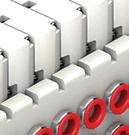

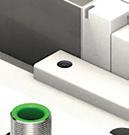
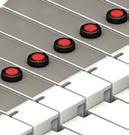
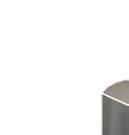
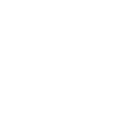
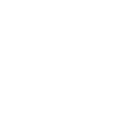

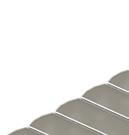
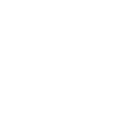
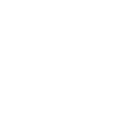
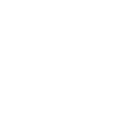
VR Series Valve Manifolds - Plug and play into flexibility and modularity like never before
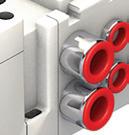


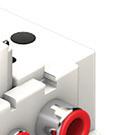
»
»
Complete your pneumatic circuit with Norgren
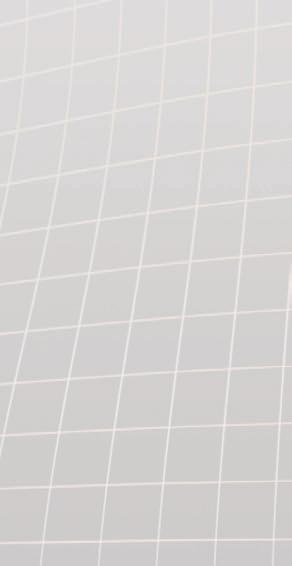
» THIS IS WHAT we know: An electromechanical system operates at about 96% overall efficiency. A typical hydraulic system operates at about 78% overall effi ciency. Down at the bottom of the list we find that a typical pneumatic system is about 6% efficient. This begs the question: with the price of energy constantly increasing and the pressure to “go green,” why would any right-minded person use fluid power as a means to do work?
The users of fluid power have come to us professionals and asked us to provide a solution to their power transfer needs. Many of them would not know a kilowatt from a horse radish or a BTU from a lemon drop. But we do! For us to design their systems, we have to calculate the forces, speeds, pressures, and flows required to get the job done.
Can Fluid Power Focus on Energy?
For years fluid power professionals have complained about giving away engineering to be competitive and sell products. The irony is that the complaint spotlights the fact that we are the ones that have designed the very inefficient systems that are now haunting the fluid power industry.
I had the opportunity to supply a system in which an upward acting press had a 143-kN (32,000-pound) platen that had to be lifted at a rate of 0.127 m/sec (5 in/sec) and then move 0.0254 m/sec (1 in/sec) applying a force of 1,333 kN (150 tons). I proposed a system using a 30-kW (40-hp) electric motor. The machine designer was skeptical and told me he did not think it would work. His company had built similar machines before, and the hydraulic supplier always provided systems that required 445-kW (60-hp) electric motors to drive the hydraulic pumps.
I was on a guided tour at a major plastics injection molding facility accompanied by a group of about 20 mechanical engineers. The tour led us to an experimental molding machine that was entirely electromechanical. There was not so much as a cooling air jet blowing on the equipment. The tour guide proudly announced that the company was looking at this machine in the hope of getting away from fluid power because everyone knows, and I quote, “Hydraulics is messy and expensive.” I was a guest and quietly and painfully bit my tongue while everyone else nodded in unquestioning agreement.Iknowthat
The point is this: the users of fluid power have placed themselves at our mercy. In the story I told above, neither the machine designer nor the plant engineer had done the math to see the actual requirements for moving the load. They had left it up to us, the fluid power professionals, to tell them what they needed. We failed them. We gave them systems that worked and met the stated requirements, but they were not the best we could have done. The result was that, for years, the machine designer had been supplying inefficient systems, and the manufacturer had been paying the energy bill for that inefficiency. They had accepted the wasted energy as simply the cost of doing business, an inherent characteristic of fluid power.
•
When the finished machine arrived at its new home in a manufac turing facility, the plant engineer was skeptical because we had placed a relatively small heat exchanger on the system. He was convinced the power unit would overheat. He had several other machines with 60-hp electric motors, and they all had large heat exchangers.
I asked him to do the math with me. The greatest amount of power was consumed in lifting the platen. The pressing force required relatively little power because of the slow speed. He knew that HP = 550 lb/ft/sec, so I asked him to tell me how much power would be needed to lift the platen at the rated speed. He got out his calculator and did (32,000 / 550) * (5/12) = 24.24 or about 25 hp. My 40-hp unit was a concession to the inefficiency of the system and to the availability of the type of electric motor I planned to use.
By Dan Helgerson, CFPAI/AJPP, CFPS, CFPECS, CFPSD, CFPMT, CFPCC, Fluid Power Journal Technical Editor
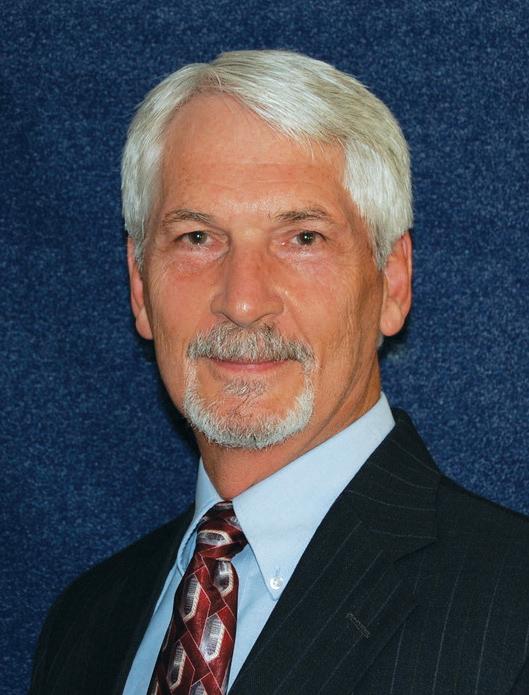
story is anecdotal, but anecdotes can show a pattern, and enough of them may even be considered data. The fact is that a substantial group of design engineers currently planning the equipment of tomorrow do not question the idea that it is wise to avoid fluid power if at all
4 OCTOBER 2022 WWW.FLUIDPOWERJOURNAL.COM • WWW.IFPS.ORG NOTABLE WORDS
The frustrating fact is that fluid power does not have to be so inefficient.
Thosepossible.ofuswho
We are fluid power professionals. That means we are professionals at transferring energy. We need to think of ourselves as energy professionals specializing in fluid power. We need to involve the users of fluid power in the decision-making process, let them know the cost of inefficiency, and offer them the most efficient system available. We need to begin thinking about the entire energy-transfer system, from the combustion engine or electric motor to the work being performed. We need to view every kW wasted, every scfm tossed away, and every BTU removed as an opportunity for improvement. To do less would be a disservice to our profession and those who depend on our expertise.
are passionate about fluid power know that there are very good reasons to consider fluid power as a means to do work. There is the power density, the removal of heat, the flexibility, and the ability to produce both linear and rotary motion from a common power source. With the aid of electronic controls, we can take very heavy objects and repeatedly position them within .0005 inches. We can create vacuum that allows us to pick up delicate and oddly shaped material and safely move it. These are all appropriate things to discuss when presenting the case for fluid power, and many of us have been successful in doing so. However, if fluid power cannot be shown to be an efficient alternative to other forms of power transfer, then we may as well start packing up our formulas and find some other line of work.
Account Executive: Kristy O'Brien
Robert Sheaf, CFPAI/AJPP - CFC Industrial Training
Email: AskUs@ifps.org • Web: www.ifps.org
for Compact,HydraulicLeak-FreeSystems © 2022 Adaconn® + Inserta® ADACONN® + INSERTA® Blue Bell, PA www.adaconn.com215.643.1900 www.inserta.com215.643.0192
Executive Donna Pollander, ACA Thomas Blansett, CFPS, CFPAI Kyle Pollander Piro
Fluid Power Journal (ISSN# 1073-7898) is the official publication of the International Fluid Power Society published monthly with four supplemental issues, including a Systems Integrator Directory, Off-Highway
Director:
Mohaned Shahin, CFPS Parker Hannifin
Whether you are in need of some assistance that will build your brand through traditional media, or are looking for some non-traditional solutions, we are here to help. Simple to complex—we will work with you to clearly understand your project and translate those creative concepts into effective solutions. Let us launch your project forward and help bring your business to new
Fax: 610-923-0390 • Email: www.FluidPowerJournal.comArt@FluidPowerJournal.com

IFPS
Ethan Stuart, CFPS, CFPECS - Wainbee Limited
Lisa DeBenedetto, CFPS - GS Global Resources
Daniel Fernandes, CFPECS, CFPS - Sun Hydraulics
Jon Rhodes, CFPAI, CFPS, CFPECS - CFC Industrial Training
INTERNATIONAL FLUID POWER SOCIETY
Circulation Manager: Andrea Karges
Donna Pollander, ACA
HONORARY DIRECTORS-AT-LARGE AND EX OFFICIO
STAFF
Communications Coordinator: Victoria
Layout/Graphics Designer: Chalie Clair Assistant Director: Jenna Mort
LAUNCH YOUR NEXT MARKETING PROJECT
| Easton, PA | 610.923.8000
Tel: 800-730-5904 or 610-923-0380
heights.idpcreative.com
Founders: Paul and Lisa Prass
Cary Boozer, PE, CFPE - Motion Industries
Suppliers Directory, Tech Directory, and Manufacturers Directory, by Innovative Designs & Publishing, Inc., 3245 Freemansburg Avenue, Palmer, PA 18045-7118. All Rights Reserved. Reproduction in whole or in part of any material in this publication is acceptable with credit. Publishers assume no liability for any information published. We reserve the right to accept or reject all advertising material and will not guarantee the return or safety of unsolicited art, photographs, or manuscripts.
2020 BOARD OF DIRECTORS
Innovative Designs & Publishing, Inc. 3245 Freemansburg Avenue, Palmer, PA 18045-7118
Liz Rehfus, CFPE, CFPS
Randy Smith, CFPHS - Northrop Grumman
Paul Prass, Fluid Power Journal
Vice President Marketing: Chauntelle Baughman, CFPHSOneHydraulics
Editor: Michael Degan
Certification Logistics Manager:
Accounting: Donna Bachman, Sarah Varano
PUBLISHER
DIRECTORS-AT-LARGE
WWW.IFPS.ORG • WWW.FLUIDPOWERJOURNAL.COM OCTOBER 2022 5
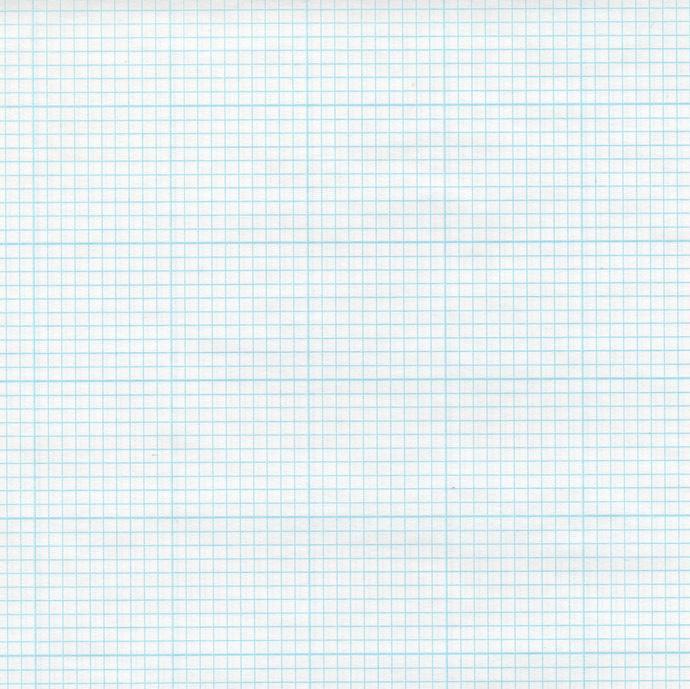
Treasurer: Jeff Hodges, CFPAI/AJPP, CFPMHM - Altec Industries
Vice President Certification: James O’Halek, CFPAI/AJPP, CFPMIP, CMPMM - The Boeing Company
President: Denis Poirier Jr., CFPAI/AJPP, CFPHS, CFPIHM, CFPCCDanfoss Power Solutions
Vice President Membership: Garrett Hoisington, CFPAI/AJPP, CFPS, CFPMHM - Open Loop Energy
Brian Kenoyer, CFPHS - CemenTech
Stephen Blazer, CFPE, CFPS, CFPMHM, CFPIHT, CFPMHT - Altec Industries
Technical Editor: Dan Helgerson, CFPAI/AJPP, CFPS, CFPECS, CFPSD, CFPMT, CFPCC
Use AdaconnR InsertaR Components
Bookkeeper: Beth Borodziuk
Director of Creative Services: Erica Montes
Associate Publisher: Bob McKinney
Immediate Past President: Rocky Phoenix, CFPMMHOpen Loop Energy
Technical Director:
Vice President Education: Randy Bobbitt, CFPAI, CFPHSDanfoss Power Solutions
Brian Wheeler, CFPAI/AJPP, CFPMM, CFPMIPThe Boeing Company
1930 East Marlton Pike, Suite A-2, Cherry Hill, NJ 08003-2141 Tel: 856-489-8983 • Fax: 856-424-9248
First Vice President: Scott Sardina, PE, CFPAI, CFPHS, CFPECS - Waterclock Engineering
Steve Bogush, CFPAI/AJPP, CFPHS, CFPIHM - Poclain Hydraulics
Diane McMahon Administrative Assistant:
Hydraulic Maintenance for Paper HydraulicManufacturersMaintenance for Paper Manufacturers PULP (non)FICTION
By Timothy McCrea, Market Segment Manager, Aftermarket Hägglunds, Bosch Rexroth Corp
PULP (non)FICTION
Large, low-speed/high-torque hydraulic direct drive systems are often used to power demanding pulp and paper manufacturing oper ations in which heavy masses of materials are moved under variable
COVER STORY
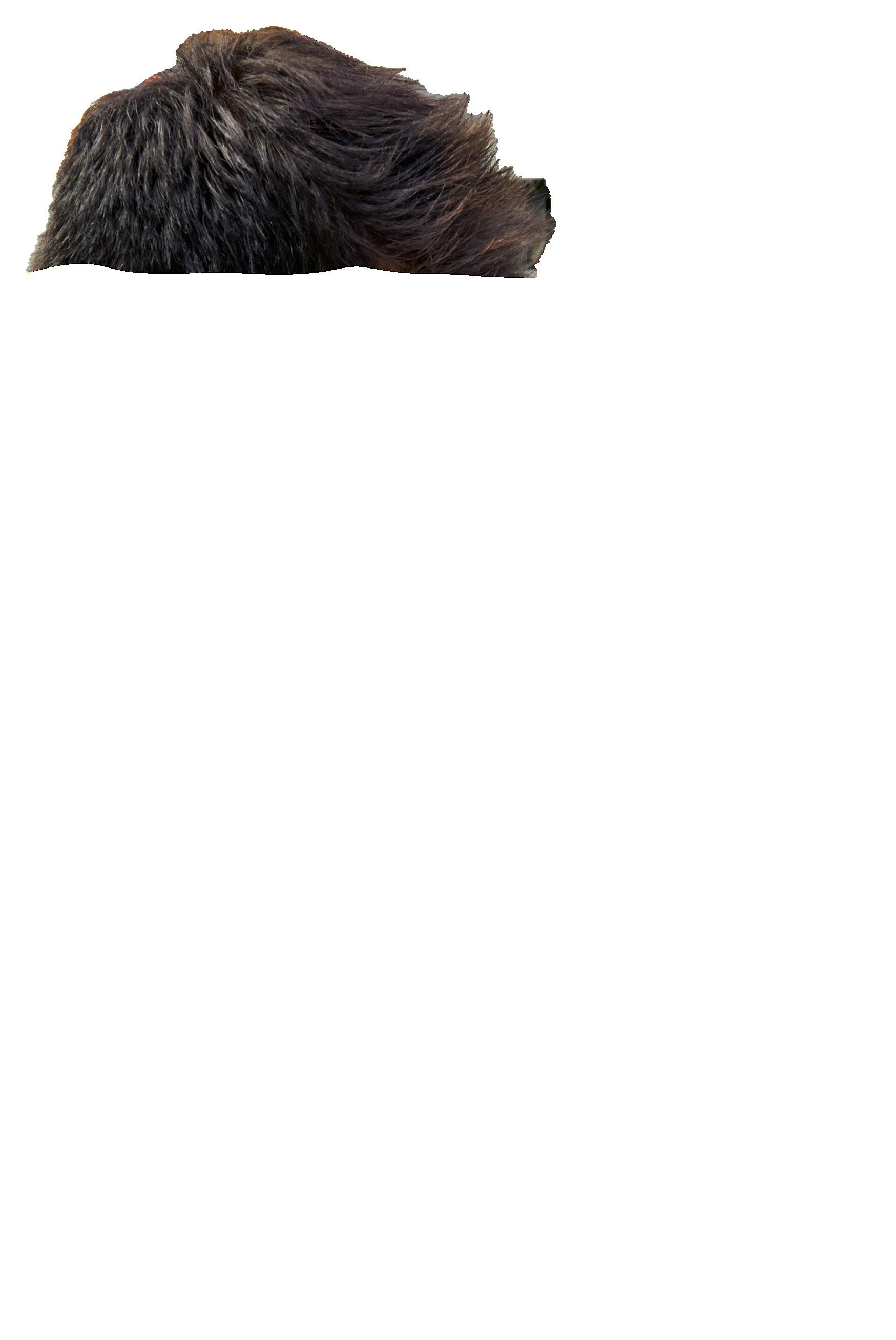
drive systems are heavily used in pulp mill and wood yard operations for critical equipment such as twin roll presses and high-pressure feeders, digester outlet devices, and log decks. Radial piston direct drive hydraulic motors are well suited for these applica tions because of their low-speed/high-torque capabilities, space-saving design, and well-established record for maximum uptime and operating efficiency, particularly for operations in pulp mills requiring near roundthe-clock performance.
6 OCTOBER 2022 WWW.FLUIDPOWERJOURNAL.COM • WWW.IFPS.ORG
As with any system in a demanding environment, routine hydraulic service is critical to maintaining uptime. To reap the full benefit and potential of direct drive hydraulic systems, there are several maintenance best practices and techniques to follow. These include proper initial fluid selection, routine fluid analysis and troubleshooting, evaluating and replacing internal components, and condition monitoring.
Hydraulic
Hydraulic direct drives are engineered for longevity; but preventive maintenance is often overlooked for this type of equipment until it is too late. As with any system in a rugged environment, routine service is critical to maintaining the uptime of radial piston motors. When break downs occur, they can take valuable equipment off the line or even shut downImplementingoperations.a few effective maintenance and service best practices can prevent major breakdowns, plus it saves time, money, and effort compared to allowing equipment to deteriorate, then shipping it off to a repair center. More importantly, these best practices can help pulp and paper manufacturers ensure that the drives powering vital equipment provide the years of operation they were engineered to deliver.
Value of hydraulic direct drives
radial piston motors meet these challenges, producing extremely high torques in a compact package. The radial piston motor mounts directly on the machine’s drive shaft, while other hydraulic drive components can be located away from the machine.
speeds. Whether it's lifting or lowering loads at a steady speed, executing straight-line or rotating movements, generating steady accelerations and maintaining set speeds, or efficiently transferring power, hydraulic direct drives are proven to handle the operating conditions in harsh pulp mill environments as well as handle shock loading, two of the most common operatingLow-speed/high-torqueconditions.
Several essential maintenance practices can prevent potential hydraulic direct drive failures and keep you from operating in breakdown main tenance mode.
When periodic predictive maintenance practices are performed intermit tently or not at all, even the most well-engineered hydraulic system breaks down. This “breakdown maintenance” can have serious impacts, like these:
• Small issues such as fluid leaks from worn-out seals become big issues when preventable fixes are overlooked.
• Safety incidents and injuries occur more often due to sudden failures or jams on conveyors and other systems moving loads over distances.
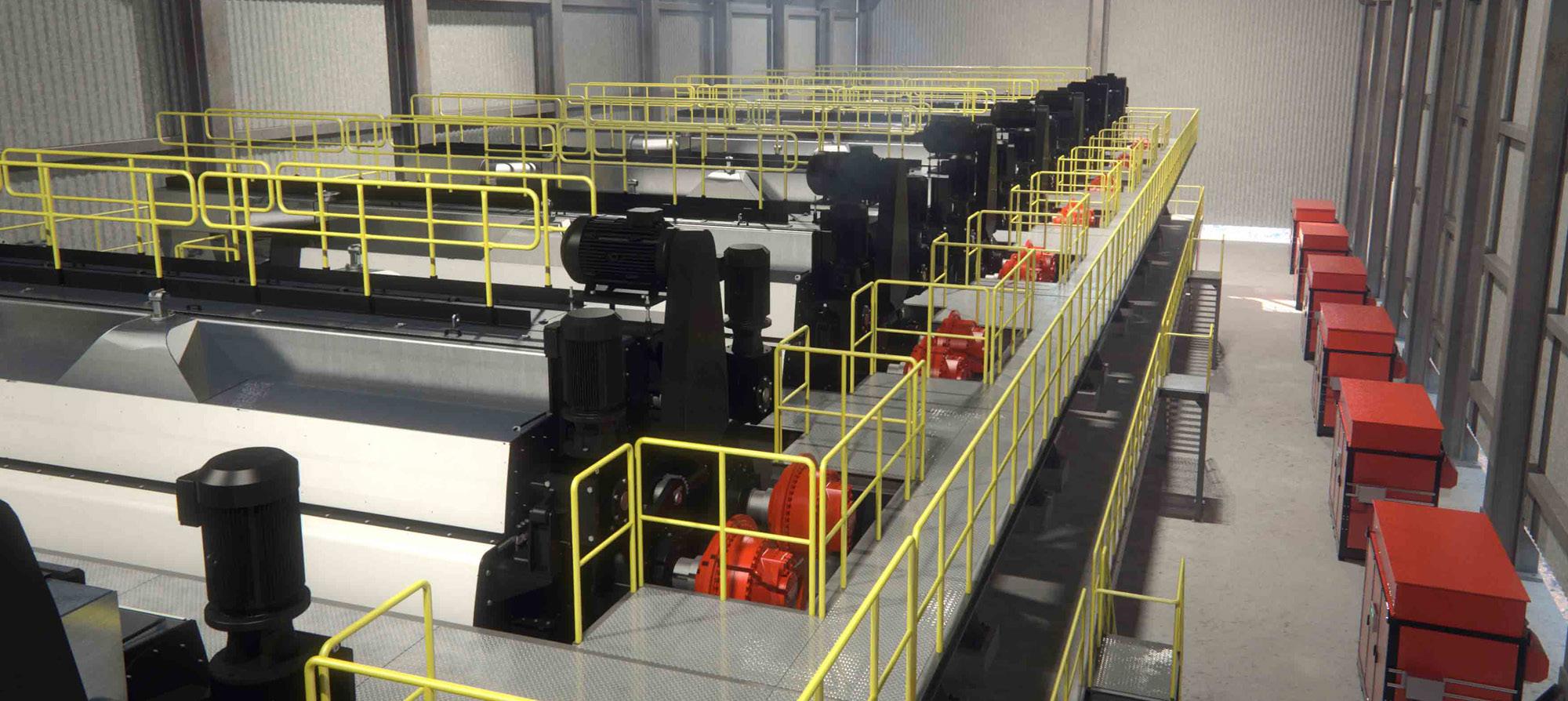
Best practices
WWW.IFPS.ORG • WWW.FLUIDPOWERJOURNAL.COM OCTOBER 2022 7
• Maintenance teams are under pressure to complete fixes on a time crunch, potentially overlooking stan dard safety practices.
Risks of ‘breakdown maintenance’
Periodic inspection and maintenance checks. Periodic inspection lays the foundation for maintenance best practices. Equipment inspec tions should follow a standard schedule. Standard intervals should be monthly at a minimum, whereas some of the best facilities conduct weekly inspections. Inspections should document danger signs, such as main pump pressure changes, fluctuations in desired motor speed, increased oil temperatures compared to standard operating levels, increased case drain flows, hydraulic oil leaks, and oil reservoir levels.
Some of the better radial piston hydraulic drives are designed to prevent equipment damage via set points and limits that prevent overtorque in case of upstream or downstream equipment failure. Diagnostics and machine health indicators are additional advantages available on these types of radial piston hydraulic drive systems. Given the central role hydraulic direct drives play in the smooth operation of pulp mill and papermaking equipment, proper care for their operating condition should be included in any effective maintenance strategy.
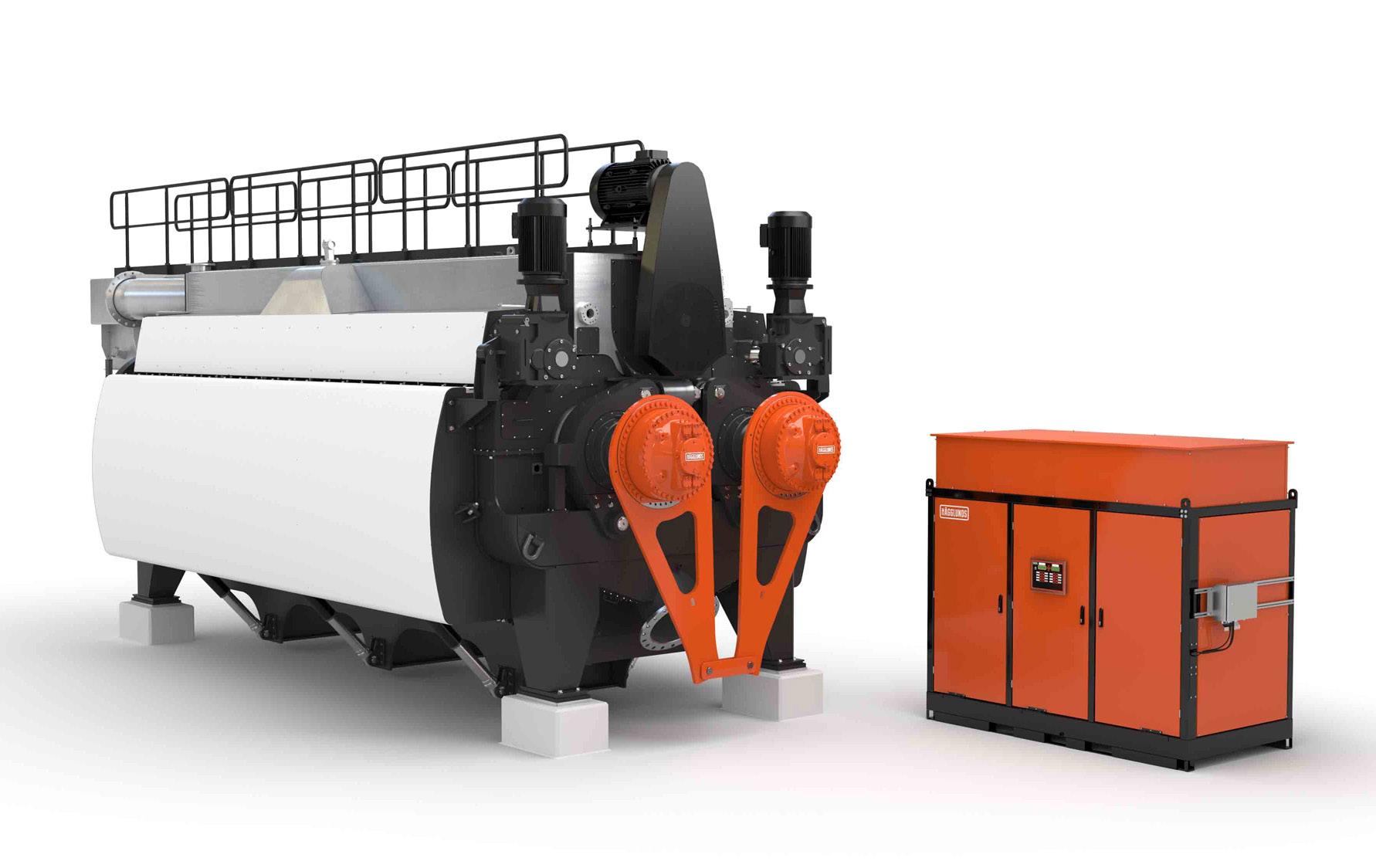
• Equipment deterioration results directly from neglect, increasing energy costs, and reducing efficiency.
• Emergency repairs are more difficult to schedule, often incur higher costs, and can take technical personnel away from regular duties to support removing and transporting damaged direct drive equipment.
In addition, if a facility or location practices breakdown maintenance, failures in multiple pieces of equipment can happen on top of each other. These types of failures typically have longer repair times if systematic neglect forces repair of surrounding components and equipment as well as the hydraulic direct drives.
Large-scale operations such as pulp and paper mills use these inspec tions to do more than prevent breakdowns. They also capture data about
Continued to Page 8
It's important to specify that any repairs should use original OEM parts supplied from the manufacturer and not those pulled from scrapped equipment. In fact, some hydraulic direct drive manufacturers, such as the Hägglunds group from Bosch Rexroth, do more than repair their equipment; they can provide fully remanufactured drives and radial piston motors with “like new” warranties to ensure long-term performance.
Equally important is regular monitoring of hydraulic fluid conditions for contaminants, discoloration, or particles, along with other sensor data the direct drive may offer. Oil condition is a critical warning sign that there may be components in the motor that are wearing or damaged.
Use OEM parts. With radial piston motors, it may be assumed that a local repair shop has the expertise to complete a repair to OEM speci fications. However, to complete a repair to a “like new” condition, it is critical to use the right replacement parts.
Choose OEM-certified suppliers. The specialized design and operating characteristics of hydraulic direct drives call for a higher level of expertise and resources, which is typically supplied exclusively by OEM-certified facilities that concentrate on this equipment. Third-party repair facilities will not have the original manufacturer specifications to properly repair, calibrate, and test the motor to new condition – and they will not typically perform a fully warrantied remanufacture.
Preventive maintenance programs. Many of the practices we’ve dis cussed can be incorporated into comprehensive preventive maintenance programs that identify risks and correct issues before they lead to failures or downtimes. Effective PM programs include annual major inspections and quarterly minor ones carried out in the field by factory-trained and certified technicians.
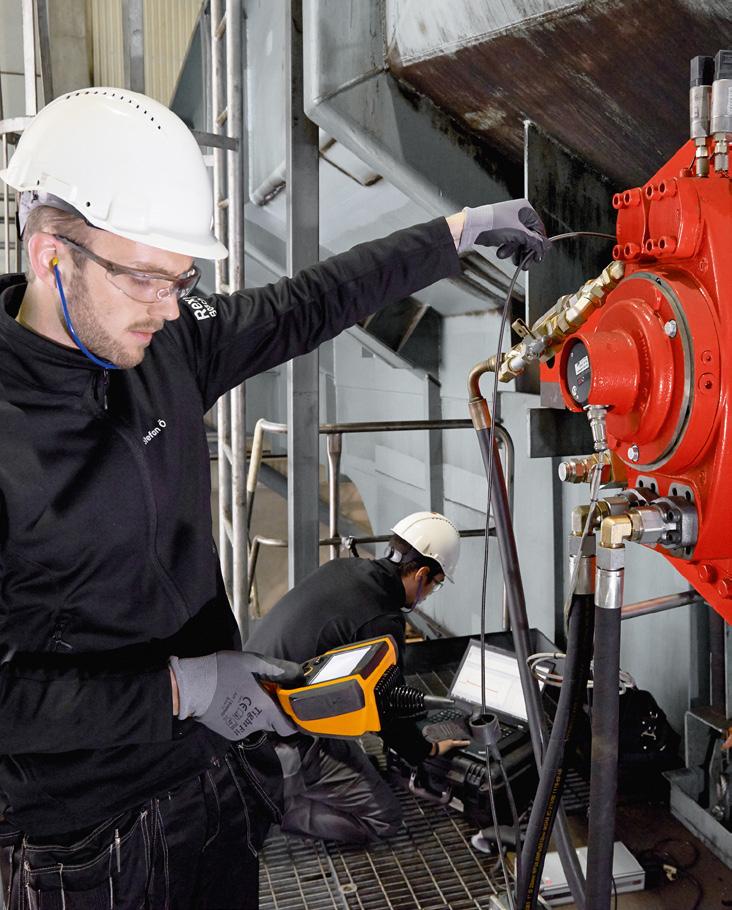
Servicing filters and seals. Filter changes at specific intervals are important to reduce contamination buildup and, in turn, reduce wear on all hydraulic system components. Direct drive manufacturers specify the type of filter their system should use and may provide more detailed recommendations – filter medium and micron level, for example –depending on the level of dust and contaminants present in the operating environment.Inaddition,
Good PM programs include detailed inspections of all accessible equipment, oil temperature, pressure and nonintrusive motor tempera ture inspections, pump settings, speed and motor parameter setting inspections, and validation against operating specifications, case drain flow measurement, and oil analysis, as well as shaft coupling and O-ring inspection and replacement. An effective PM program will also supply a detailed report of findings, recommended maintenance, spares, and follow-up actions.
8 OCTOBER 2022 WWW.FLUIDPOWERJOURNAL.COM • WWW.IFPS.ORG
• Continued from page 7
It’s quite common to see motors repaired with used parts taken from a scrapped component, or with aftermarket parts not necessarily designed to perform under the harsh conditions of high shock load equipment. In addition, sometimes motors have parts that require a special proprietary coating that may improve service life or efficiency. These coatings are utilized on internal wear parts designed specifically for high shock load applications, where there is a risk of cavitation. Cavitation can cause a reduction of oil film between the metal wear parts.
OEM-certified service suppliers also provide the most effective and up-to-date preventive maintenance programs, with factory-trained tech nicians to inspect, service, and maintain the OEM’s equipment. Certain proprietary components that cannot be duplicated or obtained from scrapped drives and motors may only be available from OEM-certified facilities. There also may be specific equipment tolerances that only the factory or OEM service shop is equipped to work with.
OEM facilities have the technical personnel, original specifications, direct access to manufacturer’s parts, and the field experience necessary to keep hydraulic direct drives operating smoothly through their full life cycle. In addition, they can advise pulp and paper plant operators when it makes sense to retire legacy equipment once it becomes cost prohibitive to maintain. They can help develop a cost-effective direct drive upgrade or migration plan based on the unique needs of specific locations, operations, and production equipment. That is one more way to leverage the maximum value from partnering with experts to extend the life of hydraulic direct drive systems.
Advantages of OEM expertise
machine performance to improve their maintenance and production processes.
most hydraulic systems have fittings that use O-rings to prevent leakage. However, due to shock loading, vibration, and other factors, these O-ring seals may tend to wear out more frequently. Peri odic maintenance inspection finds those leaks so you can replace used and worn O-rings, tighten loose fittings, or replace any damaged ones.
In addition, these proprietary coatings were developed to deliver long life in applications requiring extremely slow and extremely high motor speeds where oil viscosity levels can be reduced. This detailed knowledge may not be available from local third-party repair shops that work on a wide range of industrial hydraulics equipment from multiple manufacturers.
The goal of truly effective maintenance and service programs is to significantly reduce downtime, improve safety, and ensure hydraulic direct drives maximize their operational value. Hydraulic direct drives are engineered to provide years of service, even in demanding pulp and wood yard operations, which is why proper maintenance programs from service facilities operated by or authorized by the equipment’s OEM make the most sense in the long run.
Hydraulic fluid selection and condition. As with other hydrau lic systems, be sure to use the manufacturer’s recommended fluid with the viscosity for which the hydraulic direct drive is engi neered. Environmental factors can influence this selection. Pulp mill operations can experience temperature extremes based on their locations, especially in hightemperature environments. If equipment manufactured for use in Canada is used in South Carolina or Georgia, doublecheck the hydraulic system specifications as to whether a change from a moderate viscosity fluid, such as ISO 46, to a denser viscosity, such as ISO 68 or 100, is advisable.
WWW.IFPS.ORG • WWW.FLUIDPOWERJOURNAL.COM OCTOBER 2022 9 9 0763 Tele Radio America, LLC Member of: RE M O TE C ONT R OL F O R HYD R A U LI C A P PLI C A TION S AN COMPANY Visit our webpage: teleradio.com
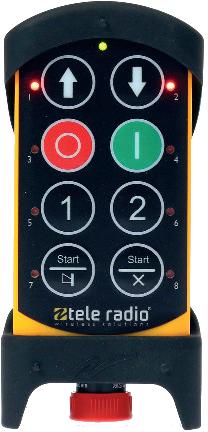
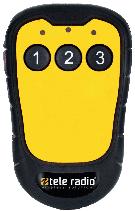
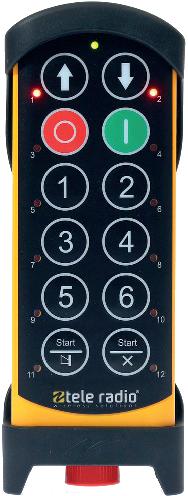
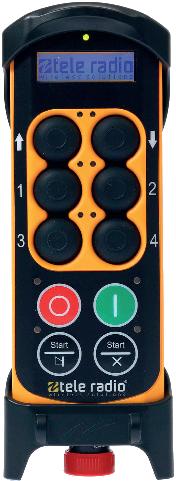

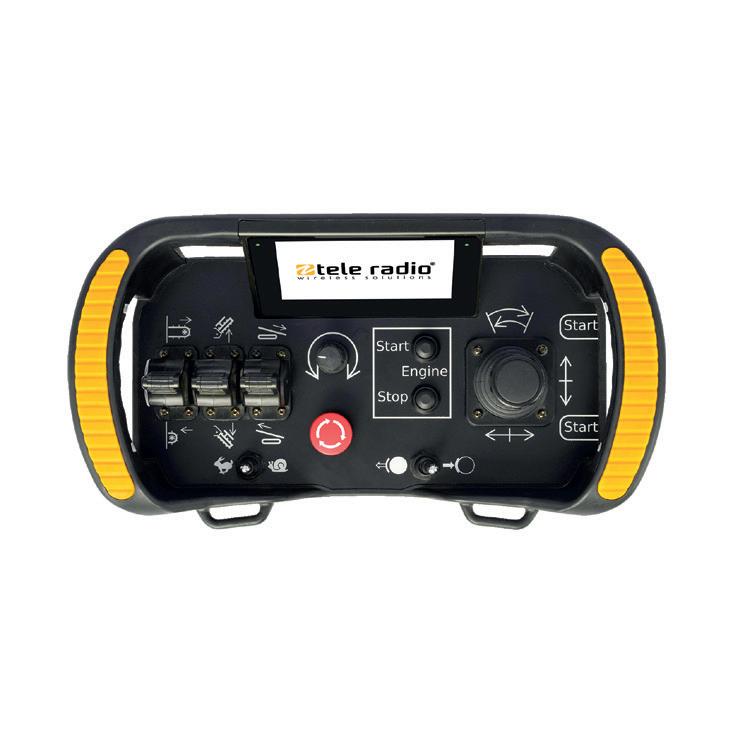
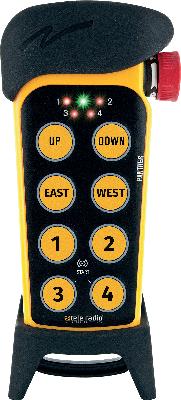
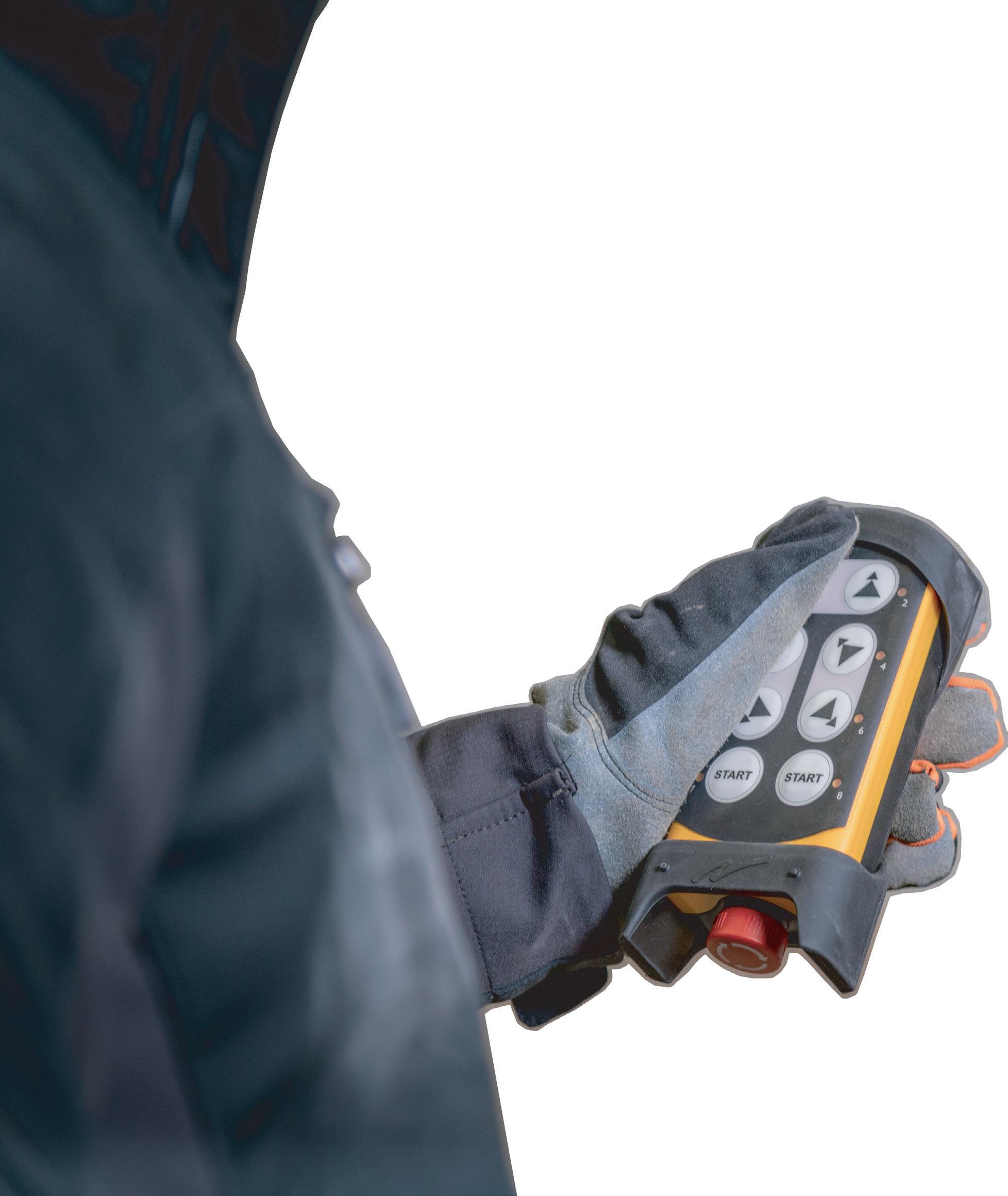
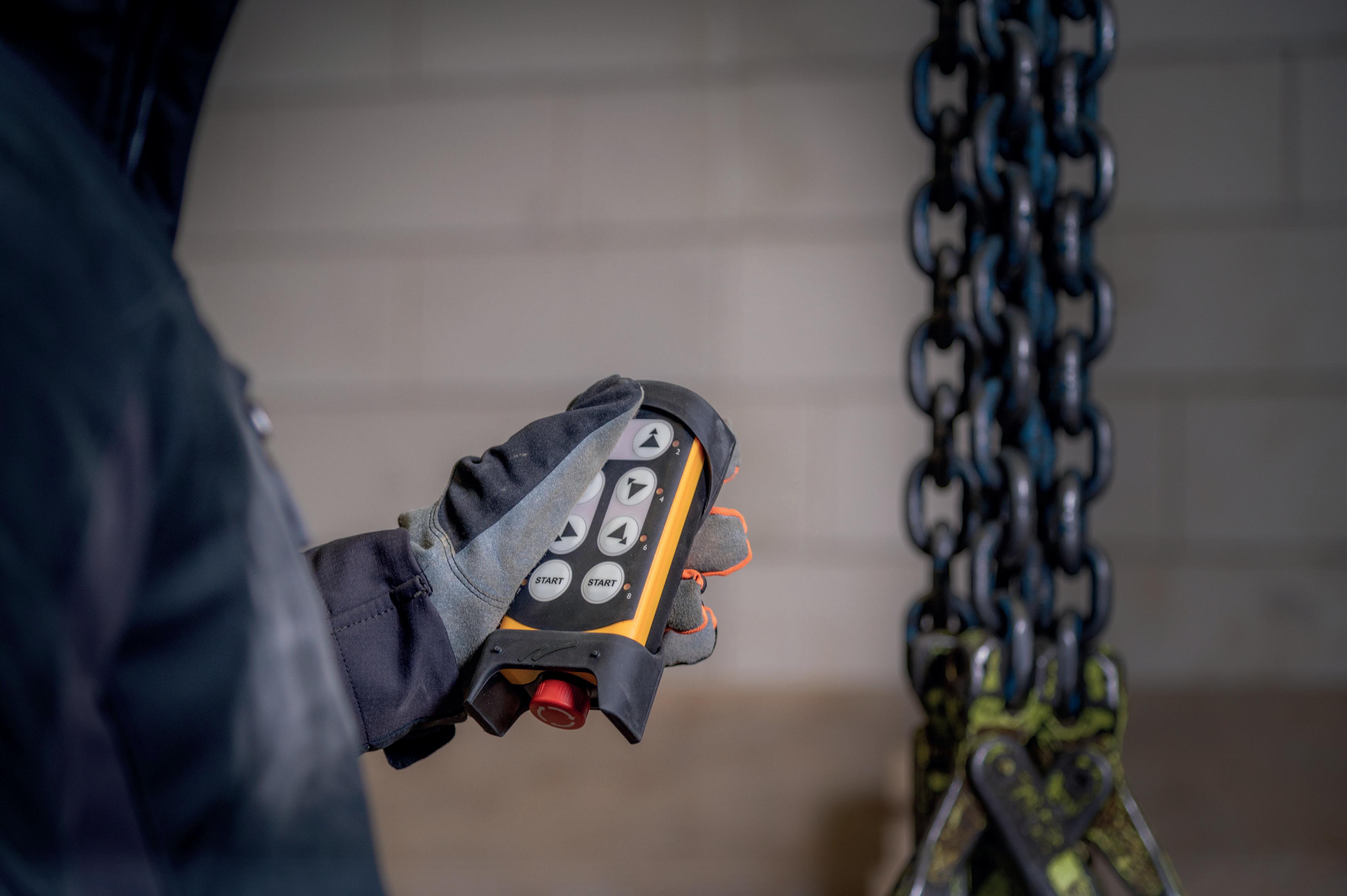
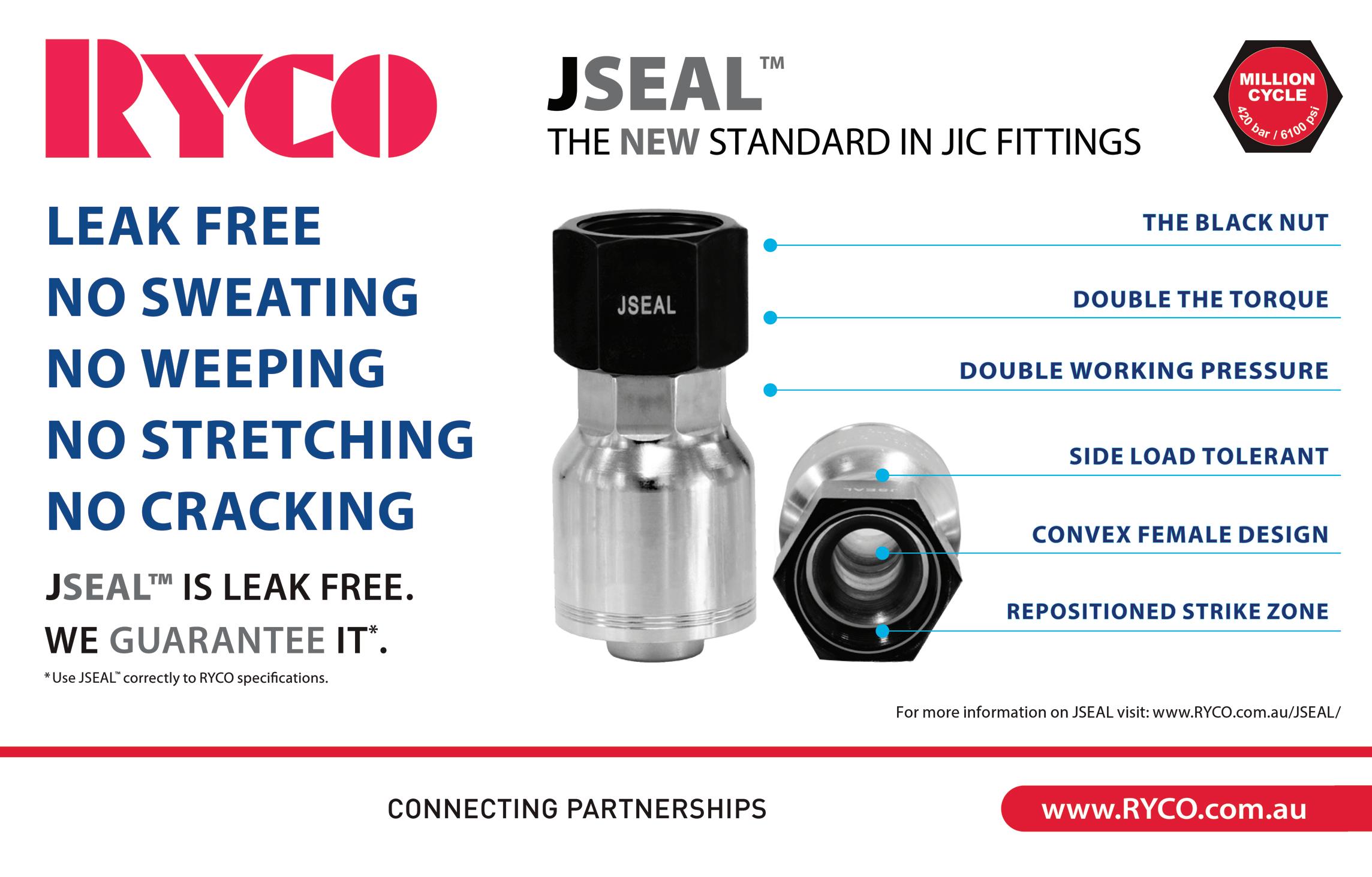
Before removing the old valve, the machine must be put into a safe state, with all supported loads lowered or blocked with a suitable sup port. Suitable containment must be in place. If shut-off valves exist,
all valves have locating dowell pin. If no pin is present, verify proper valve orientation.
In the drawing, note that the shoulder where the mounting bolt head rests is below the centerline of the valve to minimize the chance of spool binding due to uneven torque applied to the mounting bolts. When installing a new valve, special attention must be paid to ensure any O-rings remain in place and are not cut or pinched during the installation process. The O-rings should not be installed dry. A common practice is to use a small amount of hydraulic fluid, grease, Vaseline, or retaining compound specifically designed for retaining O-rings. Ensure the material is com patible with the O-ring material and the hydraulic fluid (see illustration).
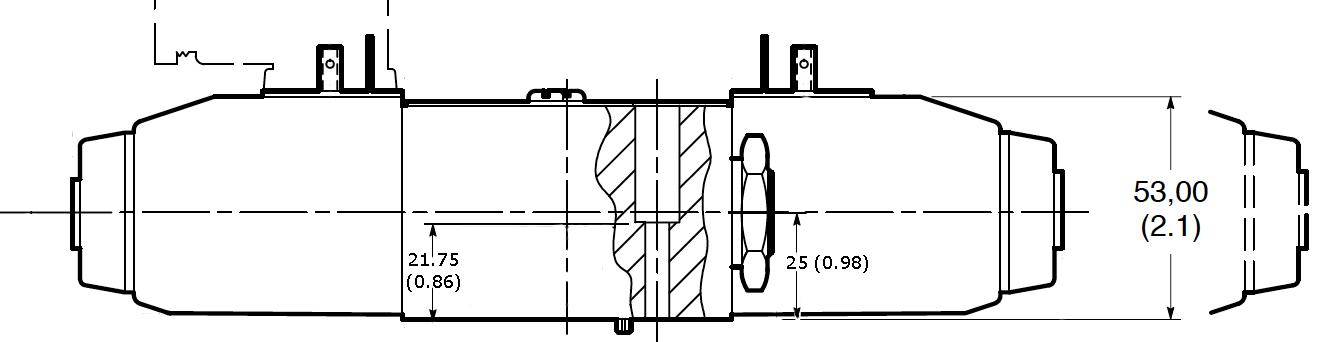
Replacing Hydraulic Valves
Identifying the valve to be removed from a machine can be difficult, if not impossible, due to paint applied after the valve was installed, a buildup of dirt, or physical damage to the data tag. The repair manual or bill of materials should also be consulted. The part number of the replacement valve should match exactly with the valve to be replaced. Even a single digit change in the model code can indicate a significant difference, such as an open center versus closed center valve.
Why would a counterbalance valve be used that is nonadjustable? a. Internal drain prevents valve adjustment. b. Valve is pressure balanced. c. Pressure is adjusted by second pilot. d. Prevent improper or mismatched field adjustment. e. Spring adjustment would interfere with check valve. When replacing a cartridge-style valve, the replacement valve: a. Must exactly match the old valve. b. Can be shorter, as long as it fits into the cavity. c. May not have an adjustment screw because it is factory set. d. May have a solenoid instead of an adjusting screw indicating it is proportional. e. Will have the same function as long at it has the same number of ports. 1.2.
they should be closed to reduce fluid loss, but they must be opened again before starting the machine. Any hoses or tubes that are removed should be capped to minimize spillage and prevent introducing dirt into the hydraulic Load-holdingsystem.valves require special attention when being serviced. One manufacturer’s counterbalance valve pressure setting is increased by turning the adjustment counterclockwise, unlike most other pressure controls that increase the setting by turning the adjustment clockwise. Field adjustment of the setting on counterbalance valves is not recom mended, especially if there are two parallel cylinders with counterbalance valves that move the load. Equipment builders may specify nonadjustable counterbalance valves to prevent improper or mismatched settings. Cylinders with integral dual counterbalance valves may have different settings for extend and retract. Identifying which counterbalance valve controls the extend or retract function may be difficult to determine without details of the cylinder plumbing.
Valve installation drawing.
10 OCTOBER 2022 WWW.FLUIDPOWERJOURNAL.COM • WWW.IFPS.ORG
Even though hydraulic valves are relatively simple devices, often with only one or two moving parts, close attention needs to be paid when replacing them. Subplate-mounted solenoid-controlled valves can have a variety of spool conditions and solenoid voltage options. Even though the replacement valve may physically fit in place of the original valve, the function can be different and result in a potentially hazardous unin tended movement when the machine is started. Mobile-style sectional valves not only can have different spool configurations but also multiple other options. These options can be in the individual valve sections as well as in the inlet and outlet sections. Cartridge-style valves, both the common cavity style that conforms to an ISO standard and valves that fit a proprietary cavity, can be flow control, directional control, or pressure control that fits into the same cavity. Cartridge valves may have the same mounting thread but a different cavity profile to accommodate the three or four flow paths compared to a simple two-flow path cavity. The extra paths connect to a third drain or pilot port. The same mounting thread can also fit a four-way directional valve or pressure valves with both separate drain and pilot ports with different cavity profiles.
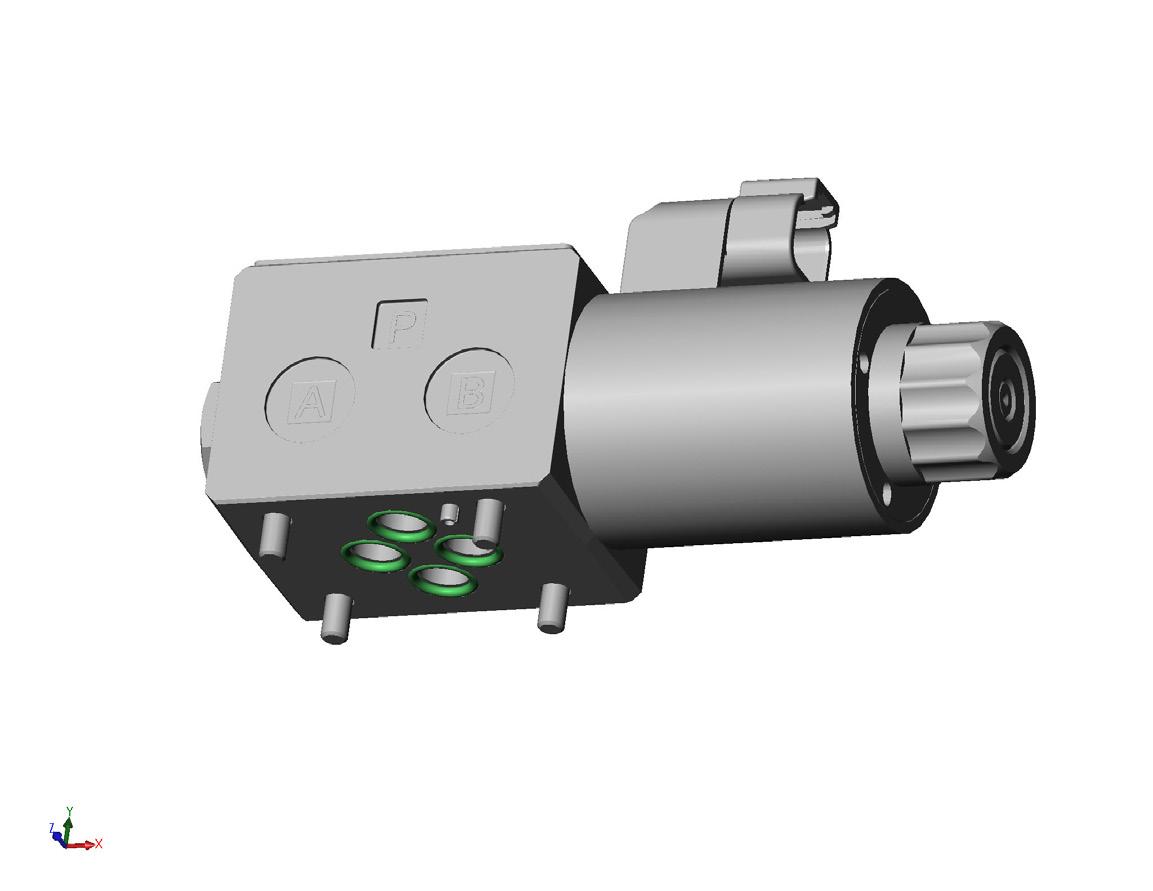
See
TEST YOUR SKILLS
Pilot-operated check valves do not have spring adjustments but may have an adjustment or manual override that will permit manually opening the valve without pilot pressure present. •
O-rings remain in place during valve installation.
When replacing any valve, all the O-rings should be replaced. Care fully inspect the mounting surface or cavity once the old valve has been removed to confirm the old seals have also been completely removed.
Ensure these
page 31 for the solutions.
TEST YOUR SKILLS
Not
It is important when installing a new valve that the manufacturer's torque specifications are followed. Be sure the proper mounting bolts are used, as the use of incorrect bolts may affect valve operation (see drawing below).
EC881 hose outperforms standard EN 857 type 2SC hose specifications, with a 35% higher pressure rating, 26% higher operating temperature, eight times more abrasion resistance, 67% greater flexibility (⅓ SAE bend radius), and five times more impulse life (1 million qualified impulse cycles). These benefits are enabled by Danfoss’ patented Dura-Pulse inner tube technology, patented hybrid wire braid reinforcement, and Dura-Tuff cover.

Web MARKETPLACE
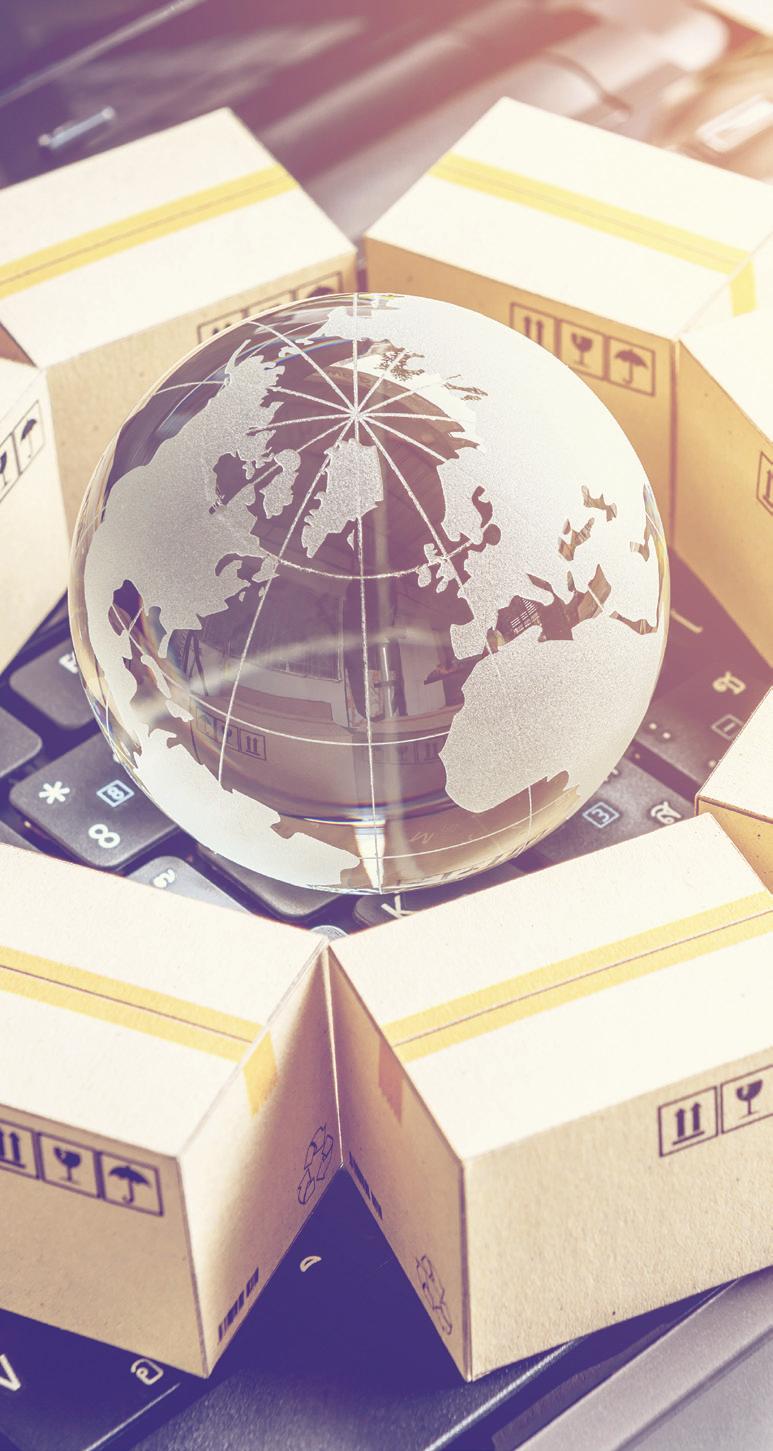
Main's website provides quick access to the 120 page catalog that includes popular styles of MAIN Manufacturing’s extensive offering of carbon and stainless Hydraulic Flanges and Components – ready for immediate shipment. Metric ordering information, weld specs, and dimensional information included. The “Quick Reference Guide” helps specify less popular items often stocked or quickly manufactured (generally 3-4 days) at our US plant. “Create-AFlange” offers more parts than the catalog — by picture. If it’s not here, or for questions, E-mails may be sent to get your answer
To learn more, visit www.danfoss.com/en-us/
info@mainmfg.com1-800-521-7918quickly.
PRODUCT REVIEW
Danfoss Launches Aeroquip Dynamax Hose Line
With its higher pressure capabilities, EC881 hose can replace heavy, rigid
Aeroquip EC881 Dynamax hose is available in sizes -4 through -24 (0.25-inch to 1.5-inch inner diameter). The hose is ideal for a variety of appli cations, including compact construction equipment, agricultural equipment, forestry equipment, mining, oil and gas, refuse trucks, aerial lifts, and railway.
» DANFOSS POWER SOLUTIONS, a global supplier of mobile and industrial hydraulics and electric powertrain systems, recently launched its Aeroquip EC881 Dynamax line of hose.
Genuine Metaris® Orbital Motors are your best low speed high torque motor option in an economical and compact design. The motors are engineered with Roller-Star technology, come in a range of displacements and we offer multiple flange options including wheel mount. You’ll find that our motors are a perfect fit, form and function replacement for common OEM motors in the market today, such as Eaton®/ Char-Lynn®, Danfoss®, Parker ® and White ®
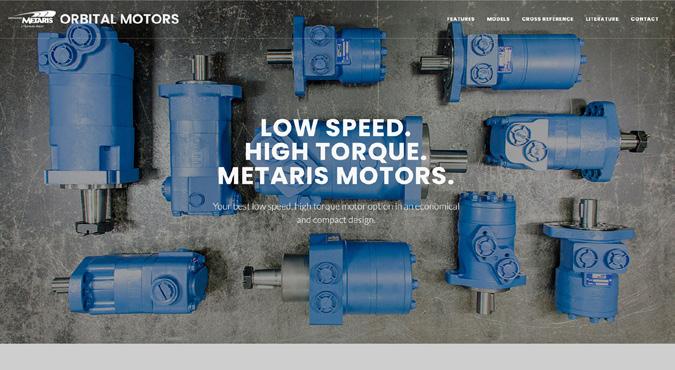
WWW.IFPS.ORG • WWW.FLUIDPOWERJOURNAL.COM OCTOBER 2022 11 SPECIAL AD SECTION
This two-wire braided hose offers higher reliability and extended service life, reducing maintenance time, costs, and waste.
www.mainmanufacturing.com
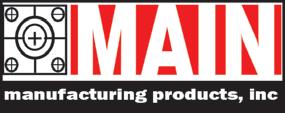
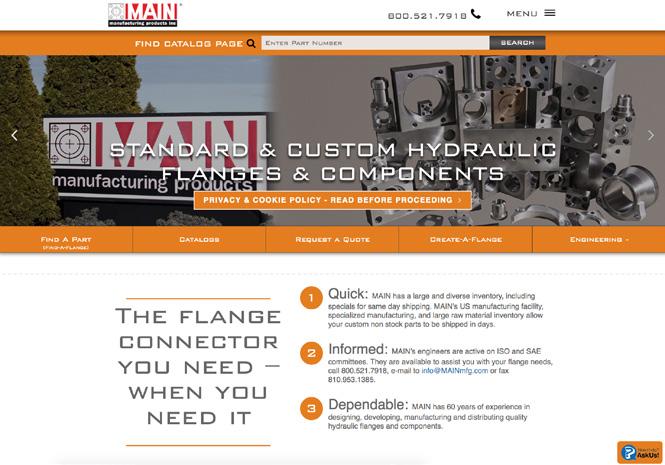
www.orbitalmotors.netHydraulex
Visit our website for more information (www. orbitalmotors.net), give us a call (1-800-3238416), or email us at seattlesales@hydraulex.com
four-wire spiral hose in certain applications, providing a direct cost savings of up to 30% as well as several design benefits. Braided hose is much more flexible than spiral hose, which may enable OEMs to reroute and reduce hose assem bly lengths, contributing to further cost savings. Braided hose is also lighter in weight than spiral hose, which reduces the overall weight of the machine, improving fuel efficiency.
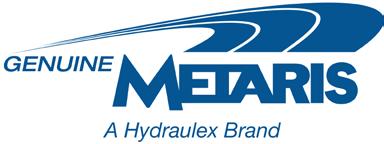
A. I became certified as a condition of employment, and I do not regret the choice. To date, I have been successful in advancing my career partly due to the official certifications I hold and the knowledge and experience they represent.
12 OCTOBER 2022 WWW.FLUIDPOWERJOURNAL.COM • WWW.IFPS.ORG IFPS UPDATE
A. Get certified. Actively reach out to others and network. Do not be afraid to ask questions or say you do not understand. Be open and try new technologies. R&D is fundamental for advancement.
Q. What advice would you give someone starting out in the industry?
A. I see the industry staying stable, as there are many applications in which fluid power is the optimal solution. I am often encouraged by new innovative solutions that hydraulic component OEMs unveil, and I actively direct my engineers to push the envelope and embrace these technologies.
A.I enjoy home DIY projects and spending time with my family. When time permits, I enjoy pickup basketball and slow-pitch softball.
A. I am a Detroit Lions fan.
A. I was hired as a hydraulic engineer with JLG Industries. I had little prior experience besides specifying hoses and fittings, but I was able to successfully learn on the job from some of the best and experienced engineers in the industry.
Q. What is something people would be surprised to learn about you?
Q. Where do you see the industry heading in the next 10 years?
Q. Why did you pursue certification, and how has it helped your career?

Brian Kenoyer, CFPHS, Director of Engineering, Cemen Tech Executive Profile
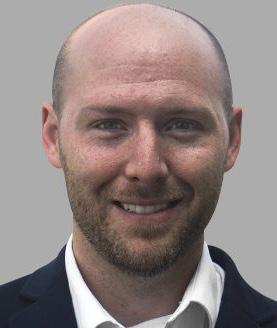
Cer tification Empowers Opportunity.
A. The wide range of viable applications. There are many instances in which fluid power offers either the best power, control, or economical combination. It is flexible, cost-effective, and advancing.
Q.What are some of your hobbies and interests?
A. [Getting involved with IFPS was] a condition of employment. I took the hydraulic specialist exam early in my employment with JLG and thankfully learned enough to pass. IFPS has provided me with fantastic educational resources for myself and my employees to overcome many engineering obstacles. I also have gained a substantial network of hydraulic professionals eager to promote the industry.
Q. What have you learned by working in this industry?
Q. How and why did you get involved in IFPS, and what have you gained professionally and personally?
Q. How did you get started in the fluid power industry?
INTERNATIONAL FLUID POWER EXPOSITION
Mark Your Calendar
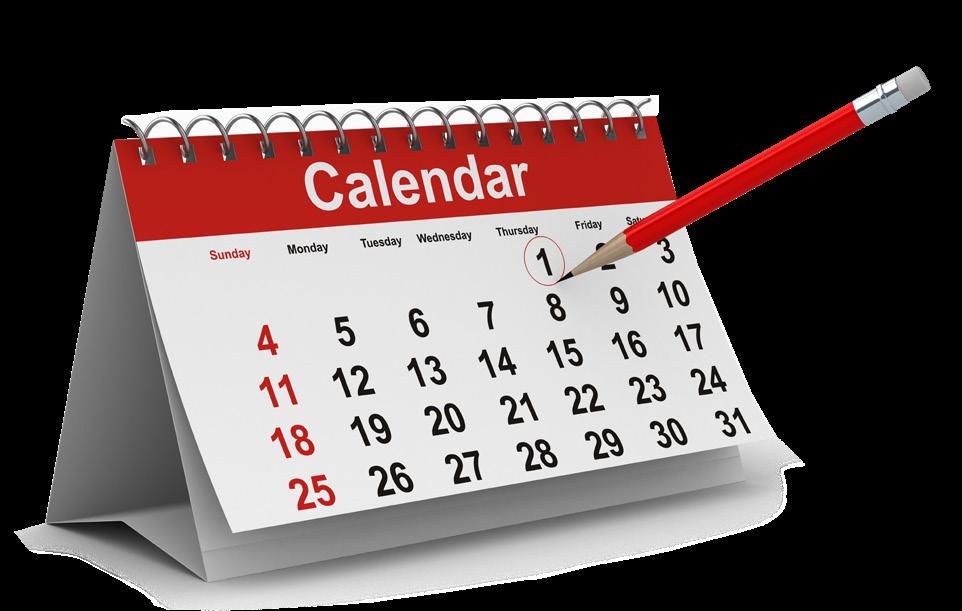
The fee includes a calculator, the Fluid Power Math book, and two-year access to the IFPS learning management system.
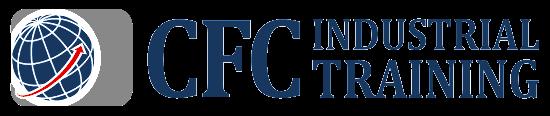
Presented by Ed Rybarczyk, CFPAI. When: Nov. 11, 12-1 p.m. [ET].
2024 IFPS SPRING MEETING
Dan Helgerson, CFPAI, and Tom Blansett, CFPAI, conduct this seven-week series covering fundamental math skills and laying a foundation to calculate more complex formulas.
IFPS
IFPS recently launched a live chat option on its website. IFPS is available to answer questions and more. To see the feature and for more information, visit www.ifps.org. Have a chat while you’re there.
FLUIDUPDATEPOWERTECHNOLOGY

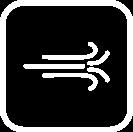
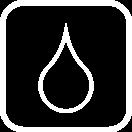
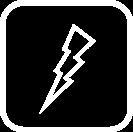

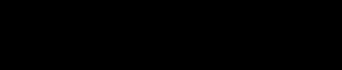
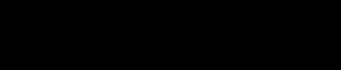
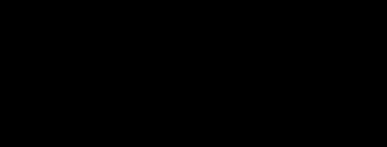
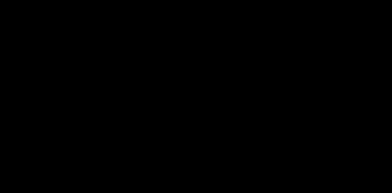
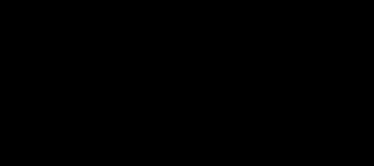
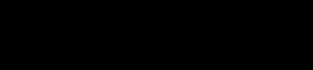
Upcoming Virtual Training
THE CONSTRUCTION, OPERATION, SIZING, AND APPLICATIONS OF USING

When: Wednesdays, Oct. 5 through Nov. 16, 11 a.m. to 12:15 p.m. [ET].
DISCUSSING THE TYPES, DESIGNS, TERMINOLOGY, FUNCTION, AND USE OF VARIOUS AIR COMPRESSORS
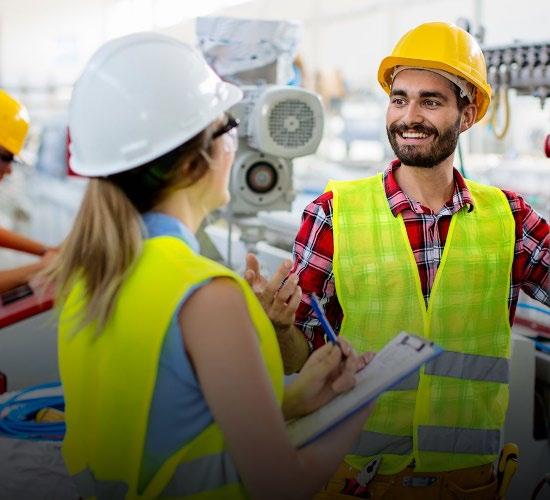
Oct. 12-13, Detroit, MI
2023 IFPS SPRING MEETING
2023 IFPS ANNUAL MEETING AND HALL OF FAME CEREMONY
For more information, visit www.ifps.org
Cost: $199 for members and $299 for nonmembers.
WWW.IFPS.ORG • WWW.FLUIDPOWERJOURNAL.COM OCTOBER 2022 13 CFCINDUSTRIALTRAINING.com 7042 Fairfield Business Drive Fairfield, Ohio 45014 +1 info@cfcindustrialtraining.com513.874.3225 UPSKILL ONSITEWORKFORCE!YOURTRAINING CFC provides direct, Industry and/or Machine specific training to companies the world over. Electrical Techs & Engineers Hydraulic Techs & Engineers Pneumatic Techs & Engineers Our Hands-On Training Equipment is mobilized directly to your facility with Certified Instructors traveling on site. This turnkey approach includes all books, materials, equipment, and travel arrangements. We have the capability to upskill your entire workforce NOW! Multicraft Techs & Engineers
CONFERENCE
IFPS Launches Live Chat
When:ACCUMULATORS
FLUID POWER MATH
Dec. 21, 12-1 p.m. [ET]. Presented by Medhat Khalil, CFPAI, CPFHS. Register at www.ifps.org/web-seminars.
Feb. 27-March 2, 2023, New Orleans, LA
Sept. 25-28, 2023, Milwaukee, WI
March 14-18, 2023, Las Vegas, NV
March 11-14, 2024, San Antonio, TX
For more information and to purchase, visit www.ifps.org/training-resources-handbook
• New and enhanced graphics.
P.O. Box 6479, Fort Worth, TX 76115 V. www.hydraulicsinc.com817/923-1965 SERIES INVESTMENT CAST SWIVELS
14 OCTOBER 2022 WWW.FLUIDPOWERJOURNAL.COM • WWW.IFPS.ORG
New Handbook Edition Released
IFPS UPDATE Cer tification Empowers Opportunity.
—Ernie Parker, CFPAI
The “9S” Series swivels represent one of the most complete range of sizes and configurations available to the industry. This series has been redesigned to incorporate a one piece barrel arrangement thus eliminating the need for braze joints. These swivels are pressure balanced with operating pressures up to 5,000 psi. All configurations are designed with a 4:1 Safety Factor and include RoHS compliant zinc plating.

Introducing!
The 388-page Fluid Power Reference Handbook is the gold standard on-the-job reference tool of choice for any fluid power professional. IFPS has sold over 2,000 copies since its first publication in 2020.
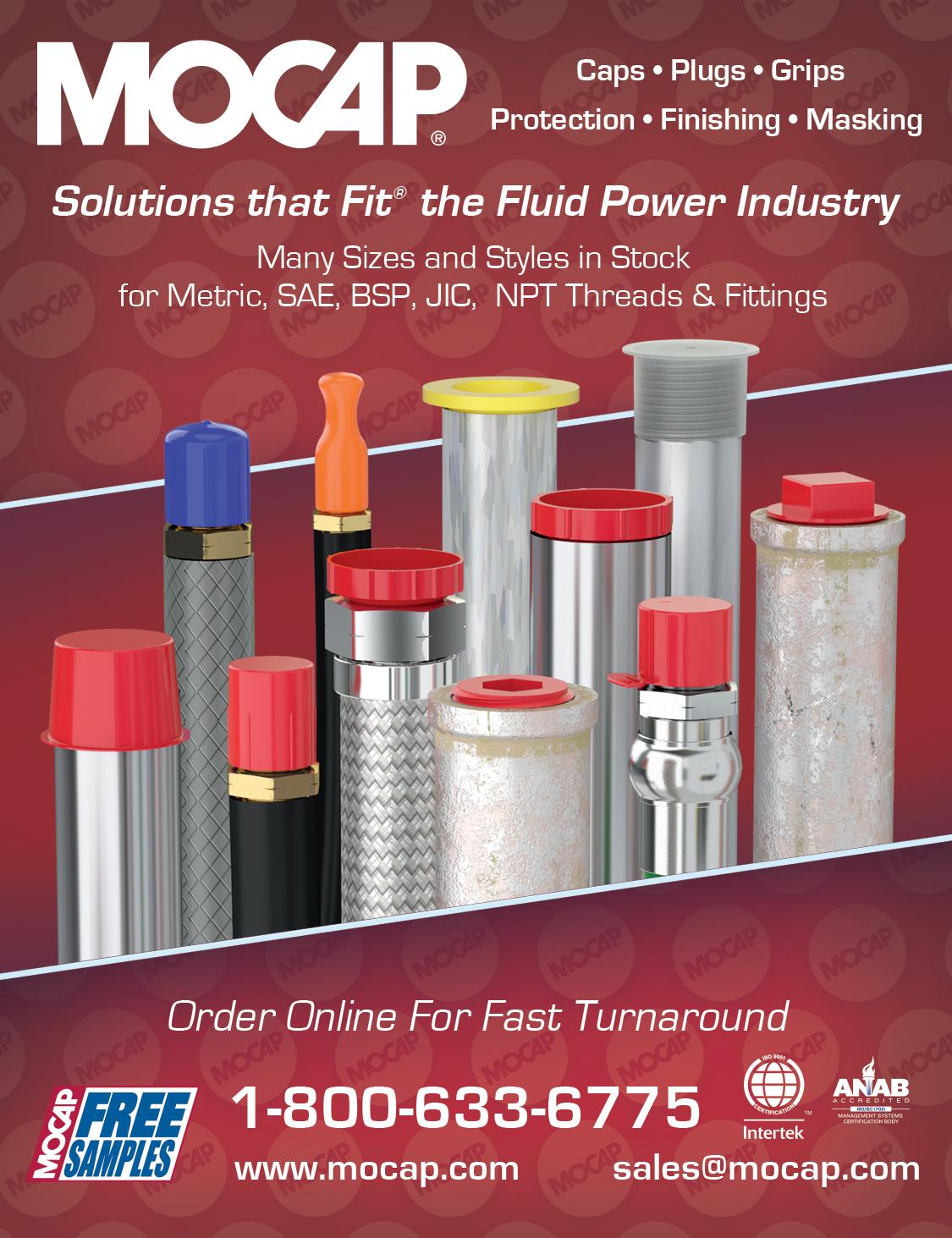
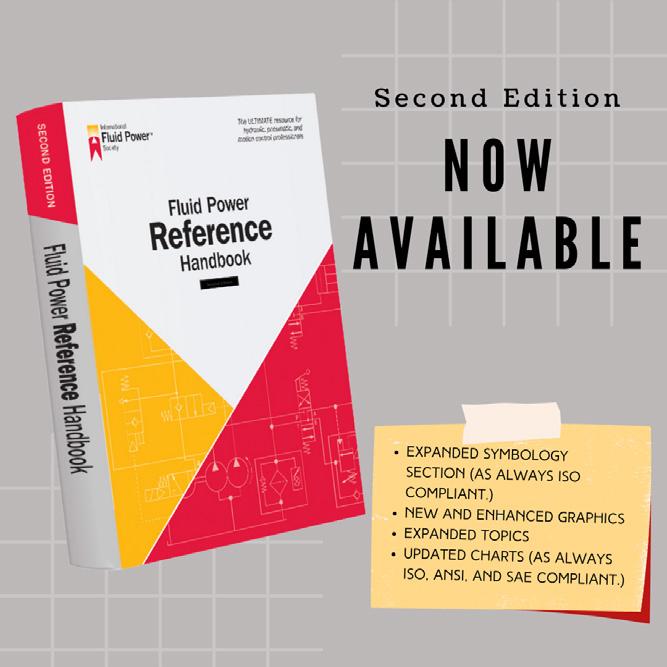
The Fluid Power Reference Handbook second edition is the best resource I have seen for the fluid power industry. It contains all the formulas that you will use in our industry, including formulas needed for fluid power certification tests. It is much more than just a reference manual. The handbook explains many concepts, in reasonable detail, for an excellent overview of how various components work with both pneumatics and hydraulics. I have over 50 years of experience in the fluid power industry, and I still learned some things that I hadn’t thought about. I’m sure you will too. The handbook is also color-coded for easy reference, with no short-cuts taken. IFPS put its full effort into making this handbook for education and industry reference.”
• Expanded topics.
• An expanded symbology section ISO 1219 compliant.
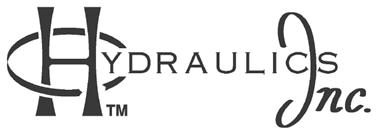

» A SECOND EDITION of the Fluid Power Reference Handbook is now available. Highlights of the second edition include:
• Updated charts that are ISO, ANSI, and SAE compliant.
Soft-cover: Members - $74.95 | Retail - $125.95
Hard-cover: Members - $149.99 |Retail - $165.99
9S
July 2022
Joelle Andres-Beck, Airline Hydraulics Corporation
Cassandra Ryan, Womack Machine Supply
5. IFPS certifications are highly recognized industry wide.
Kamran Rostami, Transcanada Ian Klein, GCC
PNEUMATIC SPECIALIST
8. IFPS is approved by the U.S. Department of Veterans Affairs to reimburse certification test fees. The VA may reimburse eligible veterans for taking IFPS certification tests.
6. The IFPS certification designations that appear after your name are portable and remain with you wherever your career takes you.
10. IFPS certification empowers fluid power distributors, manufacturers, and end users to set standards for assessing the skill level of current or potential employees.
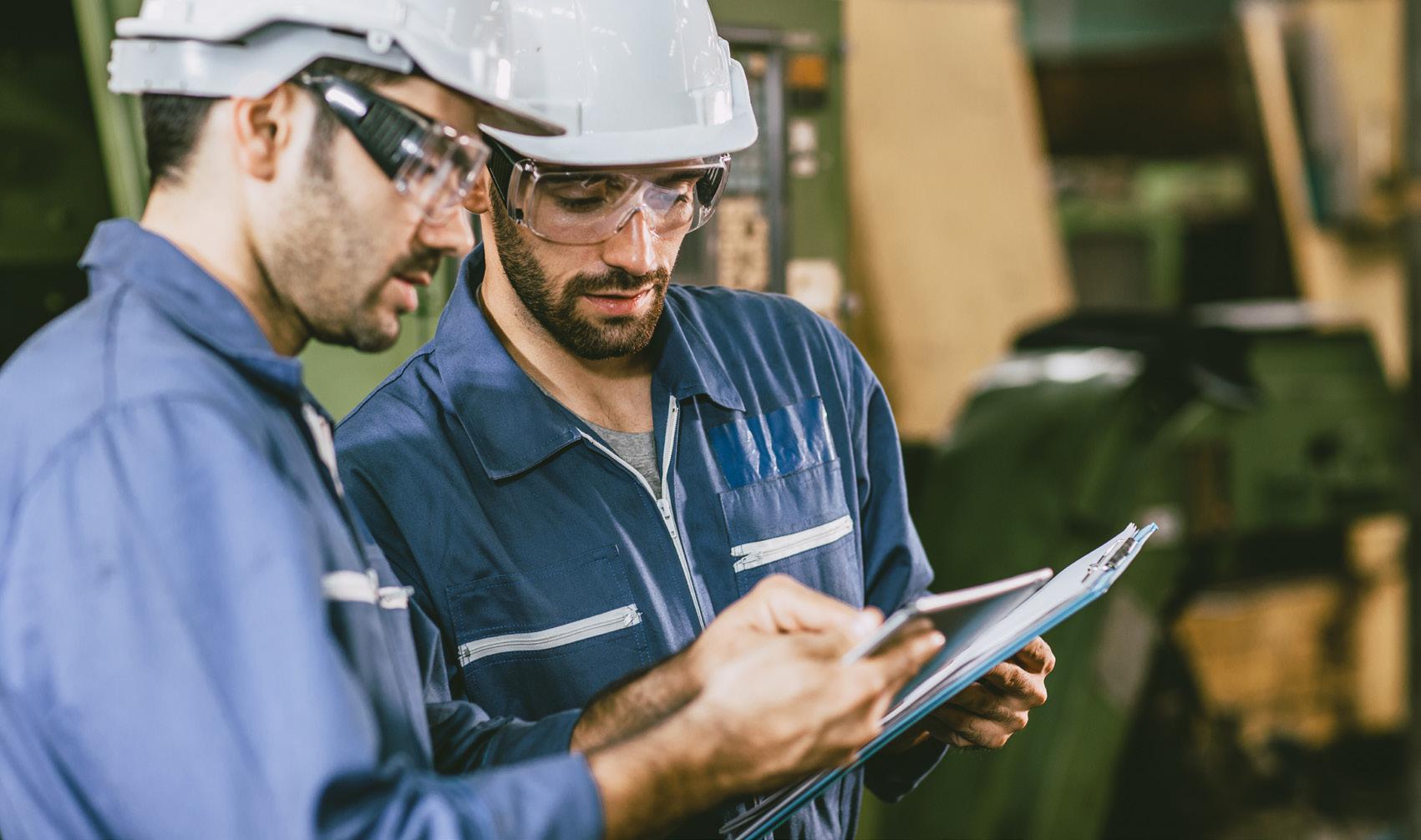
Ray Haskins, Applied Industrial Technologies
Robert Sullivan, Altec Industries
Daniel Sanchez, Applied Industrial Technologies
Chengwu Deng, Disneyland Resort
Certification Facts
Elizabeth Walker
9. IFPS certifications are valid for five years, then you must recertify. While certified, you must accrue professional development points and work in the fluid power industry for at least three years.
7. IFPS certifications are approved through the NAM-endorsed skills certification system as a stackable credential that can be earned in postsecondary education. For more information, visit www.themanufacturinginstitute.org.
Steven Price, Southern California Edison
Kamran Rostami, Transcanada Ian Klein, GCC
Freddie Bates, Altec Industries
Victor Cabrera, Southern California Edison Salvador Martinez, Southern California Edison
Elizabeth Walker
Morgan Webber, Applied Industrial Technologies
Maximino Sanchez, Altec Industries
SPECIALIST
2. Certification tests provide an objective, third-party assessment of an individual’s skill level.
Nicholas Youngers, Hyspeco Donald Steinhart, Gulf Controls Company
HYDRAULIC SPECIALIST
4. IFPS certifications are the industry standard for assessing the knowledge and skill level of professionals in fluid power and motion control.
Newly Certified Professionals
Carlo Garcia, Applied Industrial Technologies
Josh Remmer, Altec Industries Conrado Rios, Altec Industries
Cassandra Ryan, Womack Machine Supply
3. All IFPS certification tests are psychometrically evaluated and meet defensible standards.
Jerry Rubio, Southern California Edison
Holds HS and PS certifications
Chengwu Deng, Disneyland Resort
Isaac Boraas, SunSource
IFPS UPDATE
» IFPS OFTEN RECEIVES QUESTIONS from fluid power professionals about certification and how to become certified. Here are 10 things everyone should know about IFPS certification.
WWW.IFPS.ORG • WWW.FLUIDPOWERJOURNAL.COM OCTOBER 2022 15
MOBILE HYDRAULIC MECHANIC
1. IFPS has certified thousands of professionals since 1960.
QUEBEC Côte Saint-Luc, QB Montreal, QB SASKATCHEWAN Melfort, SK Moose Jaw, SK Nipawin, SK Prince Albert, SK Saskatoon, SK YUKON TERRITORY Whitehorse, YU
Tuesday
ALASKA Anchorage, AK Fairbanks, AK
LOUISIANA Bossier City, LA Lafayette, LA Monroe, Natchitoches,LA LA New Orleans, LA Shreveport, LA Thibodaux, LA MARYLAND Arnold, MD Bel Air, CollegeMDPark, MD Frederick, WyeWoodlawn,Westminster,LaHagerstown,MDMDPlata,MDMDMDMills,MD
NORTH DAKOTA Bismarck, ND OHIO Akron, Cincinnati,OH OH Cleveland, Columbus,OHOH Fairfield, OH Findlay, NorthNewark,Maumee,Lima,Kirtland,OHOHOHOHOHRoyalton, OH Rio Grande, OH Toledo, OH Warren, Youngstown,OH OH
HAWAII Laie, HI
JOB TESTPERFORMANCELOCATIONS NewMontanaMinnesotaMichiganMaineGeorgiaFloridaColoradoCaliforniaArizonaJersey Nova WesternWyomingWashingtonTexasPennsylvaniaScotiaAustralia

ONTARIO Brockville, ON Hamilton, ON London, ON Milton, Mississauga,ON Windsor,Welland,Toronto,Ottawa,NorthNorthONNiagara-on-the-Lake,ONBay,ONYork,ONONONONON
If your test was postponed due to the pandemic, please contact headquarters so that we may reschedule.
Tuesday
OKLAHOMA Altus, OklahomaNorman,Edmond,Bethany,OKOKOKOKCity, OK Tonkawa, OK Tulsa, OK OREGON Bend, OR Coos Bay, OR Eugene, KlamathGresham,ORORFalls, OR Medford, OR Oregon City, OR Portland, OR White City, OR PENNSYLVANIA Bloomsburg, PA Blue Bell, York,Wilkes-Barre,Pittsburgh,Philadelphia,Newtown,Lancaster,Harrisburg,Gettysburg,PAPAPAPAPAPAPAPAPA
16 OCTOBER 2022 WWW.FLUIDPOWERJOURNAL.COM • WWW.IFPS.ORG IFPS UPDATE
CALIFORNIA Aptos, Arcata,CACA Bakersfield, CA Dixon, Encinitas,CA CA Fresno, CA Irvine, Marysville,CA CA Riverside, CA Salinas, CA San Diego, CA San Jose, CA San Luis Obispo, CA Santa Ana, CA Santa Maria, CA Santa Rosa, CA Tustin, Yucaipa,CACA
FLORIDA Avon Park, FL Boca Raton, FL Cocoa, FL Davie, DaytonaFLBeach, FL Fort Pierce, FL Ft. Myers, MiamiJacksonville,Gainesville,FLFLFLGardens, FL Milton, FL New Port Richey, FL Ocala, PanamaOrlando,FLFLCity, FL Pembroke Pines, FL Pensacola, FL Plant City, FL Riviera Beach, FL Sanford, FL
TESTING DATES FOR ALL LOCATIONS: November 2022
Tuesday
KANSAS Kansas City, KS Lawrence, Wichita,Manhattan,KSKSKS
DELAWARE Dover, Georgetown,DE DE Newark, DE
COLORADO Aurora, Pueblo,Littleton,Lakewood,Greeley,Ft.Durango,Denver,Springs,Boulder,COCOCOCOCOCollins,COCOCOCOCO
NEW MEXICO Albuquerque, NM Clovis, Farmington,NM NM Portales, NM Santa Fe, NM NEW YORK Alfred, Syracuse,Rochester,NewGardenBuffalo,Brooklyn,NYNYNYCity,NYYork,NYNYNY
NORTH CAROLINA Apex, Asheville,NC NC Boone, Wilmington,Raleigh,Pembroke,MountMisenheimer,Jamestown,Greenville,Fayetteville,Durham,ChinaCharlotte,NCNCGrove,NCNCNCNCNCNCAiry,NCNCNCNC
IDAHO Boise, ID Coeur d ‘Alene, ID Idaho Falls, ID Lewiston, ID Moscow, ID Nampa, TwinRexburg,IDIDFalls,ID
MINNESOTA Alexandria, MN Brooklyn Park, MN Duluth, MN Eden Prairie, MN Granite Falls, MN Mankato, MN
KENTUCKY Ashland, KY Bowling Green, KY Erlanger, KY Highland Heights, KY Louisville, Morehead,KYKY
ILLINOIS Carbondale, IL Carterville, Schaumburg,Peoria,Normal,Malta,Joliet,GlenEdwardsville,Decatur,Champaign,ILILILILEllyn,ILILILILILIL Springfield, IL University Park, IL
UTAH Cedar City, UT Kaysville, UT Logan, UT Ogden, UT Orem, UT Salt Lake City, UT VIRGINIA Daleville, Fredericksburg,VA VA Lynchburg, VA Manassas, VA Norfolk, VirginiaSuffolk,Staunton,Salem,Roanoke,VAVAVAVAVABeach, VA Wytheville, VA WASHINGTON Auburn, Bellingham,WA WA Bremerton, WA Ellensburg, WA Ephrata, Rockingham,Pasco,Olympia,WAWAWA WA Seattle, Spokane,Shoreline,WAWAWA
1/10 • Thursday 1/26 February 2023 Tuesday 2/7 • Thursday 2/23 Cer tification Empowers Opportunity.
NEVADA Henderson, NV Las Vegas, NV North Las Vegas, NV Winnemucca, NV
Contact headquarters if you do not see a location near you. Every effort will be made to accommodate your needs.
Tallahassee, FL Tampa, FL West Palm Beach, FL Wildwood, FL Winter Haven, FL
IOWA Ames, IA Cedar Rapids, IA Iowa City, IA Ottumwa, IA Sioux City, IA Waterloo, IA
Written Certification Test Locations
SOUTH CAROLINA Beaufort, Spartanburg,RockOrangeburg,Greenwood,Greenville,Graniteville,Conway,Columbia,Charleston,SCSCSCSCSCSCSCSCHill,SCSC TENNESSEE Blountville, TN Clarksville, Nashville,Murfreesboro,Morristown,Memphis,Knoxville,JohnsonGallatin,Collegedale,TNTNTNCity,TNTNTNTNTNTN TEXAS Abilene, WichitaWeatherford,Waxahachie,Victoria,SanMesquite,Lufkin,Lubbock,Laredo,Huntsville,Houston,ElDenison,Dallas,CorpusCommerce,Brownsville,Beaumont,Austin,Arlington,TXTXTXTXTXTXChristi,TXTXTXPaso,TXTXTXTXTXTXTXAntonio,TXTXTXTXFalls,TX
MISSOURI Berkley, MO Cape Girardeau, MO Columbia, MO Cottleville, MO Joplin, KansasMOCity, MO Kirksville, MO Park Hills, MO Poplar Bluff, MO Rolla, Sedalia,MOMO Springfield, MO St. Joseph, MO St. Louis, Warrensburg,MO MO
MASSACHUSETTS Boston, Bridgewater,MA MA Danvers, Shrewsbury,Holyoke,Haverhill,MAMAMAMA
COLUMBIABRITISH Abbotsford, BC Burnaby, PrinceNanaimo,Kamloops,Delta,Castlegar,BCBCBCBCBCGeorge, BC Richmond, BC Surrey, Vancouver,BC BC Victoria, BC MANITOBA Brandon, Winnipeg,MBMB
Individuals wishing to take any IFPS written certification tests can select from convenient locations across the United States and Canada. IFPS is able to offer these locations through its affiliation with the Consortium of College Testing Centers provided by National College Testing Association.
UNITED KINGDOM Elgin, UK
ARKANSAS Bentonville, AR Hot Springs, AR Little Rock, AR
ALABAMA Auburn, Birmingham,AL AL Calera, Tuscaloosa,Normal,Montgomery,Mobile,Jacksonville,Huntsville,Decatur,ALALALALALALALAL
GEORGIA Albany, GA Athens, GA Atlanta, Valdosta,Tifton,Statesboro,Savannah,Oakwood,Morrow,Lawrenceville,ForestDunwoody,Dublin,Dahlonega,Columbus,Carrollton,GAGAGAGAGAGAPark,GAGAGAGAGAGAGAGA
St. John’s, NL NOVA SCOTIA Halifax, NS
GHAZNI Kingdom of Bahrain, Thomasville,GHA GHA EGYPT Cairo, EG
MISSISSIPPI Goodman, MS Jackson, MississippiMSState, MS Raymond, MS University, MS
NEW BRUNSWICK Bathurst, Moncton,NBNB
JORDAN Amman, JOR NEW ZEALAND Taradale, NZ
WEST VIRGINIA Ona, WV WISCONSIN La Crosse, Mukwonago,Milwaukee,WIWIWI
ANDNEWFOUNDLANDLABRADOR
MICHIGAN Ann Arbor, MI Big Rapids, MI Chesterfield, MI Dearborn, EastDowagiac,MIMILansing, MI Flint, GrandMIRapids, MI Kalamazoo, MI Lansing, MI Livonia, MI Mount Pleasant, MI Sault Ste. Marie, M Troy, UniversityMI Center, MI Warren, MI
INDIANA Bloomington, IN Columbus, IN Evansville, IN Fort Wayne, IN Gary, Indianapolis,IN IN Kokomo, Lawrenceburg,Lafayette,ININ IN Madison, IN Muncie, IN New Albany, IN Richmond, TerreSouthSellersburg,ININBend,INHaute,IN
NEBRASKA Lincoln, NE North Platte, NE Omaha, NE
ALBERTACANADA Calgary, FortEdmonton,ABABMcMurray, AB Lethbridge, RedOlds,Lloydminster,ABABABDeer,AB
MONTANA Bozeman, MT Missoula, MT
WYOMING Casper, Torrington,Laramie,WYWYWY
TENTATIVE
NEW JERSEY Branchburg, NJ Cherry Hill, NJ Lincroft, NJ Sewell, NJ Toms River, NJ West Windsor, NJ
12/6 • Thursday 12/15 January 2023
ARIZONA Flagstaff, AZ Glendale, AZ Mesa, Yuma,Tucson,Thatcher,Tempe,SierraScottsdale,Prescott,Phoenix,AZAZAZAZVista,AZAZAZAZAZ
11/8 • Thursday 11/17 December 2022
CFPE
Online review. Contact info@cfcindustrialtraining.com. Reviews includes stations 1-6 of the IFPS mechanic and technician job performance tests. Members can email askus@IFPS.org for a 20% coupon code. Test fees not included. To register, contact info@cfcindustrialtraining.com
Certified Fluid Power Pneumatic Technician
CFPPM
CFPS
For dates, call 513-874-3225 or contact info@cfcindustrialtraining.com
JOB PERFORMANCE TRAINING
MOBILE HYDRAULIC MECHANIC Oct. 10-12, Fairfield, OH. Contact info@cfcindustrialtraining.com. Written and JP test Oct. 13. Online review for written test. Contact info@cfcindustrialtraining.com. IFPS members can email askus@IFPS.org for a 20% off coupon code. Test fees not included.
PNEUMATIC TECHNICIAN and PNEUMATIC MECHANIC For dates, call 513-874-3225 or contact info@cfcindustrialtraining.com
CFPAIIFPSAVAILABLECERTIFICATIONS
Fluid Power System Designer
Certified Fluid Power
Certified Fluid Power Pneumatic Mechanic
CFPIHM
Certified Fluid Power
CFPMT
Oct. 25-28, Charlotte, NC. Contact mzanon@hydeparkpartners.us Livingston & Haven. Written test: Oct. 28.
IFPS offers onsite review training for small groups of at least 10 persons. An IFPS accredited instructor visits your company to conduct the review. Contact kpollander@ifps.org for details of the scheduled onsite reviews listed below.
Certified Fluid Power Specialist (Must Obtain CFPHS & CFPPS)
Certified Fluid Power Accredited Instructor
WWW.IFPS.ORG • WWW.FLUIDPOWERJOURNAL.COM OCTOBER 2022 17 IFPS UPDATE
CFPMMH
Onsite review training for small groups. Contact IFPS for details.
Certified Fluid Power Industrial Hydraulic Mechanic
Certified Fluid Power Master of Mobile Hydraulics (Must Obtain CFPMHM, CFPMHT, & CFPCC)
CFPAJPPCC
Mobile Electronic Controls
Certified Fluid Power Mobile Hydraulic Technician
Certified Fluid Power Authorized Job Performance Proctor
Certified Fluid Power Mobile Hydraulic Mechanic
CFPMHM
Certified Fluid Power Industrial Hydraulic Technician
CFPMIH
LIVE DISTANCE LEARNING JOB PERFORMANCE STATION REVIEW Contact info@cfcindustrialtraining.com for information.
CFPIEC (In Development)
Certified Fluid Power Master Technician (Must Obtain CFPIHT, CFPMHT, & CFPPT)
CFPPS
Certified Fluid Power Connector & Conductor
Industrial Electronic Controls
CFPMIP
CFPMHT
HYDRAULIC SPECIALIST
Certified Fluid Power Authorized Job Performance Proctor Connector & Conductor
MOBILE HYDRAULIC TECHNICIAN
CONNECTOR & CONDUCTOR Nov. 15-16, Fairfield, OH. Contact info@cfcindustrialtraining.com. Written test Nov. 17.
CFPCC
Certified Fluid Power Pneumatic Specialist
INDUSTRIAL HYDRAULIC TECHNICIAN
CFPPT
Certified Fluid Power Master Mechanic (Must Obtain CFPIHM, CFPMHM, & CFPPM)
CFPIHT
CFPAJPP
Certified Fluid Power Electronic Controls Specialist
CFPSD
Master of Industrial Pneumatics (Must Obtain CFPPM, CFPPT, & CFPCC)
Certified Fluid Power Engineer
CFPHS
CFPECS
CFPMM
Certified Fluid Power Hydraulic Specialist
Master of Industrial Hydraulics (Must Obtain CFPIHM, CFPIHT, & CFPCC)
CFPMEC (In Development)
Tentative Certification Review Training
It’s RightAll
The right condition
It is important to examine the needs of the system and establish a goal for oil cleanliness. Considering factors like valve and pump clearances can help determine an appropriate target ISO cleanliness level, as the most dangerous particles to a machine are those similar in size to the clearances designed in the system. The table on the next page lists typical fluid cleanliness specifications based on component type.
To combat these risks and realize the benefits of extended machine life, a precision lubrication approach should be taken to the maintenance of the system. Defining such an approach requires looking at all potential issues and developing a holistic plan to tackle those risks. Such a plan ensures that the right oil, in the right condition, is delivered in the right way, to the right places, at the right time, and in the right quantity.
Precision Lubrication for Food and Beverage Hydraulics

The food and beverage industry adds an additional layer of complexity to specifying lubricants: food grade. While not all equipment within a plant will require food-grade lubricants, there are advantages and disadvantages to specifying that all plant lubricants are food grade. The primary advantage is that any cross contamination (that is, using the wrong lubricant for an application) has fewer risks to a customer, as it will all be food grade. The other advantage is that it allows for more inventory consolidation – requiring fewer lubricants and other supplies on hand, also making it easier to specify or color-code the lubricants.
Hydraulic systems harness, control, and transmit power in many industrial facilities. Well-maintained hydraulic systems are highly responsive and efficient, capable of transmitting reliable power to indus trial equipment. However, this reliability depends on that key descriptor of a given hydraulic system: well-maintained. Money well spent on a state-of-the-art system will only remain well spent as long as the system is maintained to continue delivering the function and reliability for which it was engineered.
However, if records from the OEM were lost, the correct oil can be specified for a given piece of equipment through a third-party. Ambient temperatures, operating conditions, and machine specifications are taken into account when specifying the oil to be used in a system. These considerations determine the best combination of viscosity, base oil, and additive package for the overall health and operation of the system. For example, some machine components may require zinc-free oil to avoid corrosion issues from the incompatibility between zinc and the component material. Determining the best oil and ensuring it is used in a system is the first step in precision lubrication best practices.
18 OCTOBER 2022 WWW.FLUIDPOWERJOURNAL.COM • WWW.IFPS.ORG
The right oil
Original equipment manufacturers often indicate the correct oil to use in their equipment. It is important to note that the oil specified is an option and often not the only compatible oil for a system. Major lubricant manufacturers offer a slate of options for your equipment.
A well-maintained hydraulic system has a comprehensive maintenance plan to keep it running as intended. One of the most critical areas of maintenance of hydraulic systems is a lubrication program. A precision lubrication program reduces the occurrence of machine failures and extends machine life. Within the food and beverage industry, protecting processes and products from lubrication failures is an even more critical concern. A failed hydraulic system can lead to significant oil contamina tion events as well as the potential for broken parts (i.e., a broken shred of hydraulic hose) to enter the process.
Simply being the “right” oil is not the system’s only requirement, how ever. New oil from a distributor can contain thousands of damaging particles per milliliter. Hydraulic oil must also be in the right condition to properly do its job. A critical factor is how clean the oil is.
After establishing a target for oil cleanliness, contamination becomes a two-headed beast: you must remove particles already inside the system while excluding further particles from entering. It can be as much as ten times cheaper to exclude contamination as it is to remove it; however, both are necessary to truly build a precision lubrication program.
By Kate Harnage, MLTI, MLAII, Lubrication Engineer SME, Des-Case Corporation
The most direct source of lubrication-related damage to a system comes from contamination. A contaminant is any material that should not be in the system, such as water, dirt, dust, or wear particles. Contaminants cause problems for the machine and the lubricant. In fact, contamination is the number one cause of lost machine life in lubricated equipment. It is also said that 82% of mechanical wear is caused by particle contamination.
For contamination already inside a system, filtering, flushing, and cleaning it are all options for removal. Especially when establishing a new precision lubrication program, it is prudent to flush and clean existing reservoirs. Years of sludge and varnish can build up in reservoirs, providing a source of contamination even as new oil is put into service. This is most easily seen in old sight glasses that are stained a dark brown
Delivered in the right way
For systems with high volumes of particulate contamination, a filtration system can bring particle counts to the target ISO cleanliness level. It is important to note that for extremely dirty systems, filters may need to be stepped down to prevent a loss of pressure due to the volume of particles overwhelming the media. A plan that starts with capturing the largest particles before stepping down to a filter to catch smaller-micron particles can work to clean the system without interfering with its functionality.
The dirty oil-level indicator on the left is hard to see. Right: a clean 3D-viewable oil leveler.

For the food and beverage industry, solid particle contamination is often shadowed by another harsh contaminant – water. Due to the requirement of frequent washdowns, water can easily find its way through damaged seals, loose fittings, or other cracks or gaps in machinery housings.
Using quick connect fittings and sealed oil transfer containers greatly reduces the ingress of contamination into the oil during the transfer process. For transferring large quantities, an additional pass through a
Continued to page 20
As contamination removal methods perform their job, it is essential to also stop the ingress of new contaminants into the system. Fill ports, breather caps, and sampling ports are three areas that often create an ingress of particles. Again, removing particles from the system takes more time and is more costly than taking steps to prevent particles from entering.Breather caps on hydraulic reservoirs allow the system to breathe during operation. For unbalanced systems, large amounts of air enter and exit the system to replace the space occupied by the moving hydraulic oil. For balanced systems, the heating and cooling of hydraulic oil causes expansion and contraction. As the heated oil expands, it forces air out of the reservoir, and vice versa.
OEM breather caps are often very basic and, at most, contain a small wire mesh filter to prevent insects or large contaminants from entering. However, they still allow dust, dirt, moisture, and water into the system. Advanced breather elements address these risks. Breathers with silica gel dehumidify the air entering the system and draw moisture out of the air already in the headspace of the reservoir. These advanced desiccant breathers also contain a media filter to prevent dirt and dust particles from entering the system.
WWW.IFPS.ORG • WWW.FLUIDPOWERJOURNAL.COM OCTOBER 2022 19
Fill ports and open ports used for sampling create an ingression event each time they open. By unsealing the unit, dust or water in the air easily enters the machine, posing a further risk if a cap is not properly fitted back on. An open fill port can cause catastrophic consequences for a machine after a washdown when an HPU is suddenly filled with a 50/50 mix of oil and water.
As previously discussed, whenever the system is open to the atmo sphere, there is the potential for dust, dirt, water, and humid air to enter. One of the most common occurrences of this is during an oil change or top off. When a maintainer opens a fill cap, any debris at the opening can fall into the system. Inserting a funnel or hose into the opening introduces more debris into the system. If the hose transferring oil into the reservoir is not sealed, it could compound the problem and intro duce even more debris. In a study where an oil sample was taken from a 55-gallon drum of hydraulic oil with one teaspoon of dirt added, the resulting ISO contamination code was at 19/17/14. That is more than 2,500 particles per milliliter that were 4µm or larger.
Table: Typical fluid cleanliness targets for hydraulic components.
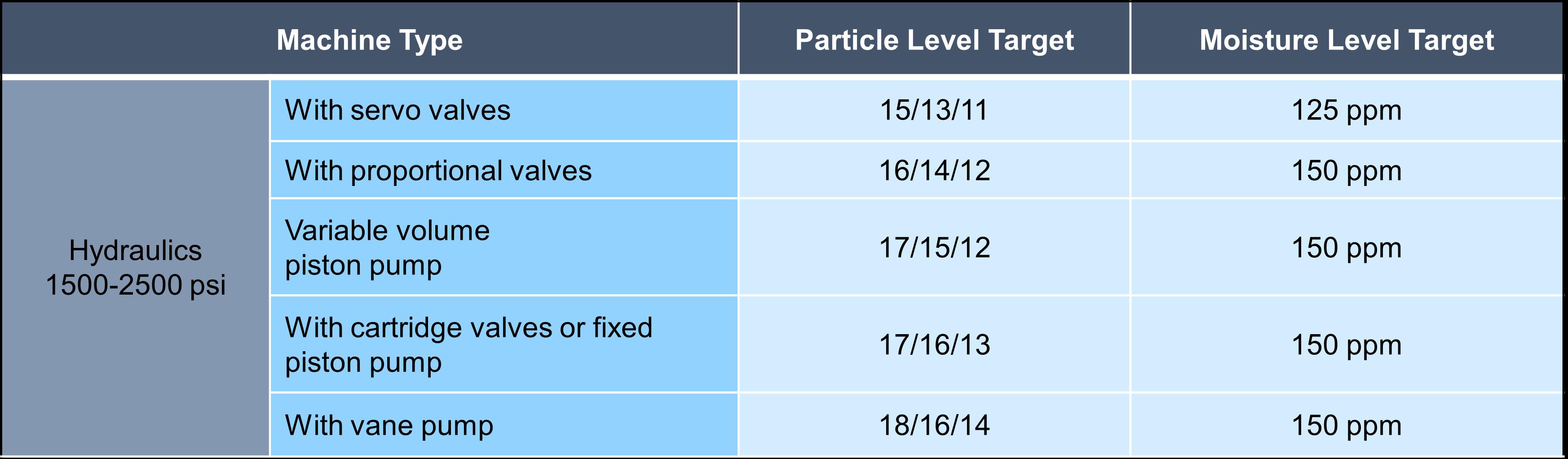
color. Sometimes, these sight glasses make it look as if the oil is at a proper level even when empty.
To combat water as a contaminant, understand what state that water is, that is, free, emulsified, or dissolved. Polymer and coalescing filters and centrifugal separators can remove free and emulsified water from a system, but they are unable to remove dissolved water in a system. For dissolved water, a vacuum dehydrator is necessary to remove the water contamination from the oil.
At the right time
In the right quantity
Proper oil levels should be established and documented for each piece of machinery. For certain equipment configurations, an operating and shutdown level may need to be shown. This can be particularly true for a system where a significant amount of oil is suspended in the process during operation but drains to the reservoir when shut down. A reservoir in such a system that is topped off during operation will be overflowed and spill oil through breathers or other openings when shut down; likewise, a reservoir being filled while shut down, but only to the point normally indicated during operation, will not have enough oil to operate properly.
New oil should be sampled before it goes into service. A complete oil-sample report with an elemental analysis will provide a baseline for additive elements, wear debris, particle count, viscosity, acid number, and other characteristics. Comparing current samples to the baseline optimizes oil-change intervals on a proactive basis instead of a timebased preventative maintenance schedule.
These oil levels should be clearly marked on oil sight glasses, and the sight glasses need to be in a location that is easily seen by the technicians responsible for filling and maintaining the system. When oil levels cannot be monitored during filling operations, it is easy for a technician to overfill the reservoir. While simply overfilling can be easily fixed when caught soon, overflowing a reservoir through a breather (or by blowing out seals) can create both a safety and environmental hazard and a housekeeping headache, especially if that oil leaks into food products.
The “Swiss cheese” model of error illustrates how failures can occur when the holes and gaps in procedures and execution line up. By taking a holistic approach to lubrication in hydraulic systems, each effort is an additional layer of defense against each failure opportunity. The redun dancy of alsothesebeveragetheultimatelyoccurrencestherintohydraulicbeforepotentialaddressingproblemsandafteroilgoesservicefurreducesfailureandextendslifeofthesystem.Withthefoodandindustry,redundanciesprotectprocesses
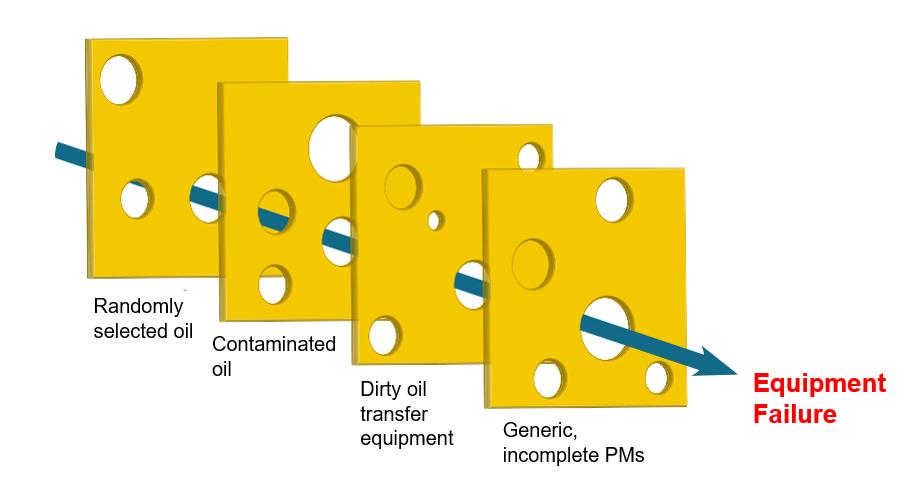
Oil transfer equipment should be clearly labeled with the oil type and viscosity for which the equipment is intended. Color-coding and shapes or symbols can reduce the risk of mixing oils and provide another indi cator to check before filling a piece of equipment.
20 OCTOBER 2022 WWW.FLUIDPOWERJOURNAL.COM • WWW.IFPS.ORG
Within the food and beverage industry, the requirement for foodgrade lubricants makes labeling an even more valuable step in creating a comprehensive lubrication program. In a system in which contamination from non-food-grade lubricants can cause significant losses of product as well as production downtime, reservoir labels reduce the risk of using the wrong type of oil. Labeling also makes it easier for work teams to train new members – a benefit provided to all industries.
Oil transfer equipment, such as containers, mobile bulk tanks, and filter carts, should be used for only one type of oil. Mixing incompatible oils can negatively impact filterability, foaming tendencies, air release time, and other characteristics. Mixing oils of different viscosities also results in an oil with a proportionally average viscosity, which may be much higher or lower than the equipment is specified to use. By ensuring that oil transfer equipment is used only for a single type of oil or lubricant, these risks are avoided.
New oil delivered on site should be filtered at least three times before being put into service. Oil samples should be taken of the oil to determine a baseline just prior to the oil going into service. This provides a confir mation of cleanliness as well as a baseline of additives and ensures the appropriate viscosity is present (and that someone didn’t accidentally deliver the wrong oil.)
Labeling equipment used in the field and for lubricant storage and transfer is a critical step in the process. It is often overlooked, but this documentation ensures that the correct oil and filter are specified.
and products from contamination risks. At a time when industries actively seek to improve production without increasing budgets, investing in lubrication can have high returns. By developing a precision lubrication program for any given hydraulic system, the decrease in overall maintenance costs provides a direct cost savings as well as incidental savings by decreasing both maintenance wrench time and operational downtime. •
Continued from page 19
Dirty OEM dust cap versus a desiccant breather to protect the equipment from the ingress of water and particle contamination.
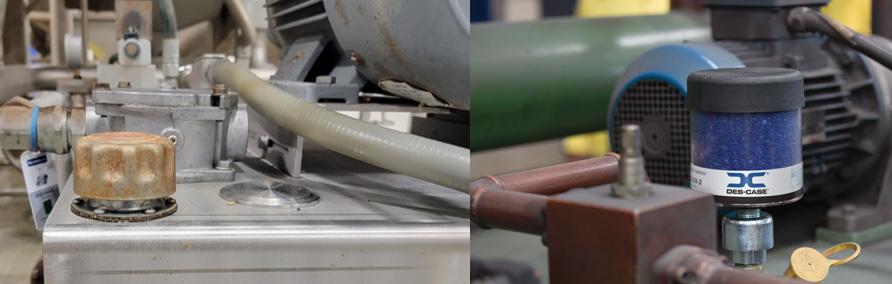
The “Swiss cheese” model of error.
To the right place
filtration system is another way to ensure clean oil is entering the system. However, filtering oil only once before transferring it into a system is not always sufficient. From the refinery to your facility, oil goes through several transfers between reservoirs, and with each transfer, contami nation levels rise. While some companies offer to deliver oil certified to a specific ISO cleanliness level, generic deliveries of oil will be too dirty to immediately put into machinery without damaging the equipment.
SHIPMENTS
Each point on this graph represents the most recent 12 months of orders compared to the previous 12 months of orders. Each point can be read as a percentage. For example, 126.8 (the July 2022 level of the industrial hydraulic series) indicates that industrial hydraulic orders received from August 2021 to July 2022 were 126.8% of the orders received from August 2020 to July 2021. (Base Year 2018 = 100)
Raw Index Data, Index: 2018=100
Shipments – Cumulative year‐to‐date % change (2022 vs. 2021)
MONTH POWERFLUIDTOTAL HYD.TOTAL PNEU.TOTAL
WWW.IFPS.ORG • WWW.FLUIDPOWERJOURNAL.COM OCTOBER 2022 21 NFPA UPDATE
Pneumatic, Mobile and Industrial Hydraulic Orders 12/12 Ratio
May 2022 14.9 17.0 8.4
This graph of 12-month moving averages shows that in July 2022, the moving averages for total fluid power and total hydraulic increased while pneumatic appears to be approaching a plateau. (Base Year 2018 = 100)
*Preliminary data subject to revision.
This graph of raw index data is generated by the total dollar volume reported to NFPA by CSS participants and compared to the average monthly dollar volume in 2018. For example, the July 2022 total dollar volume for pneumatic shipments is 103.0% of the average monthly dollar volume in 2018. (Base Year 2018 = 100)
Hydraulic and Pneumatic Shipments
June 2022 15.5 18.2 7.6
Fluid Power Shipments Drop in July
July 2022* 15.2 17.8 7.1
The table above is expressed in terms of cumulative percent changes. These changes refer to the percent difference between the relevant cumulative total for 2022 and the total for the same months in 2021. For example, July 2022 pneumatic shipments figure of 7.1 means that for the calendar year through July 2022, pneumatic shipments increased 7.1% compared to the same time-period in 2021.
Total ‐ Hydraulic and Pneumatic Shipments 12 Month Moving Average
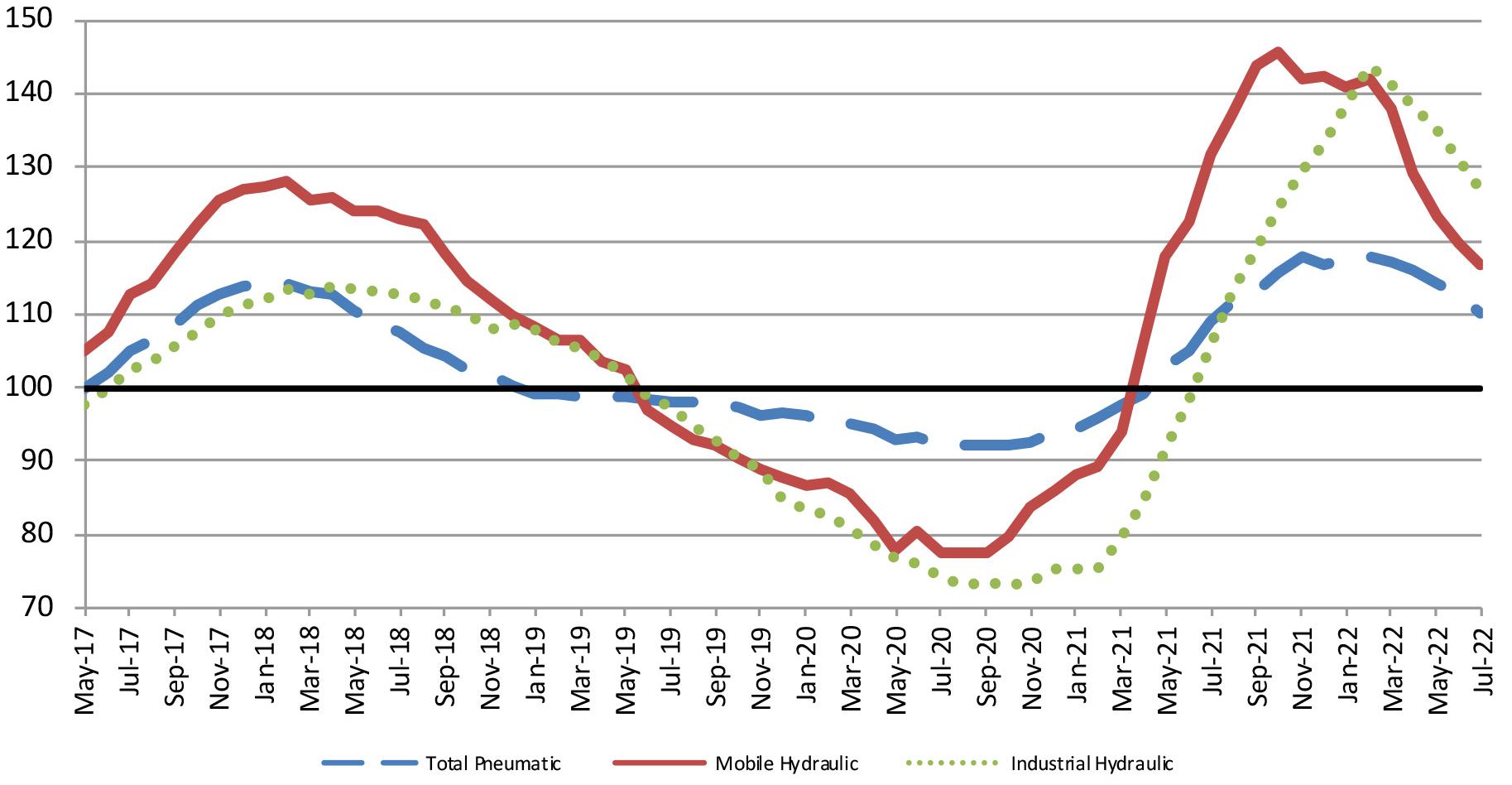
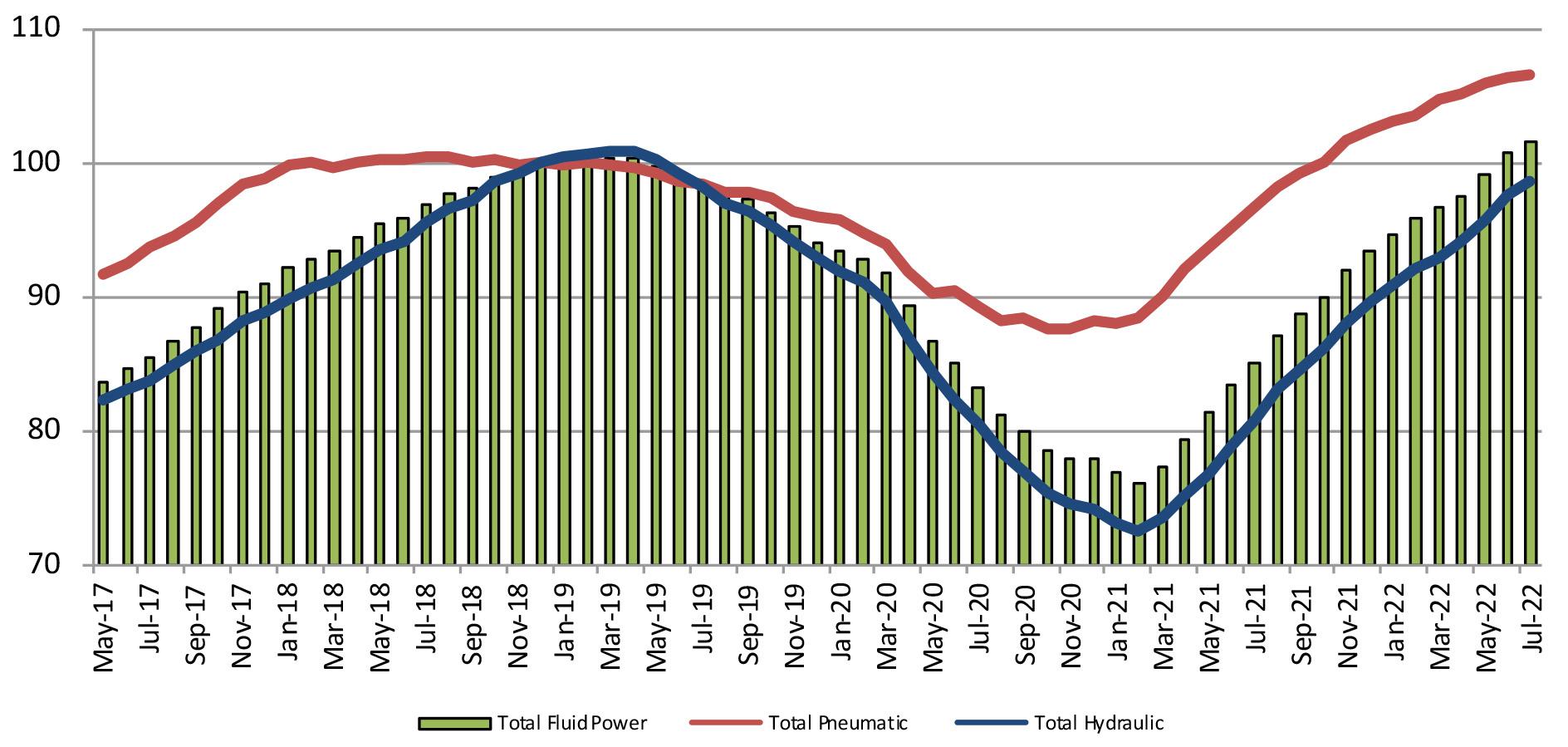
Fluid power shipments fell in July, according to the latest data from the National Fluid Power Association. Raw index data shows that pneumatic, mobile hydraulic, and industrial hydraulic shipments all decreased in July when compared to June. But the 12-month moving average of shipments for hydraulics and total fluid power continues to grow, while pneumatics is approaching a plateau. The year-to-date percent change for total fluid power shipments in July is 15.2%. The figures are from NFPA's Confidential Shipment Statistics (CSS) program.
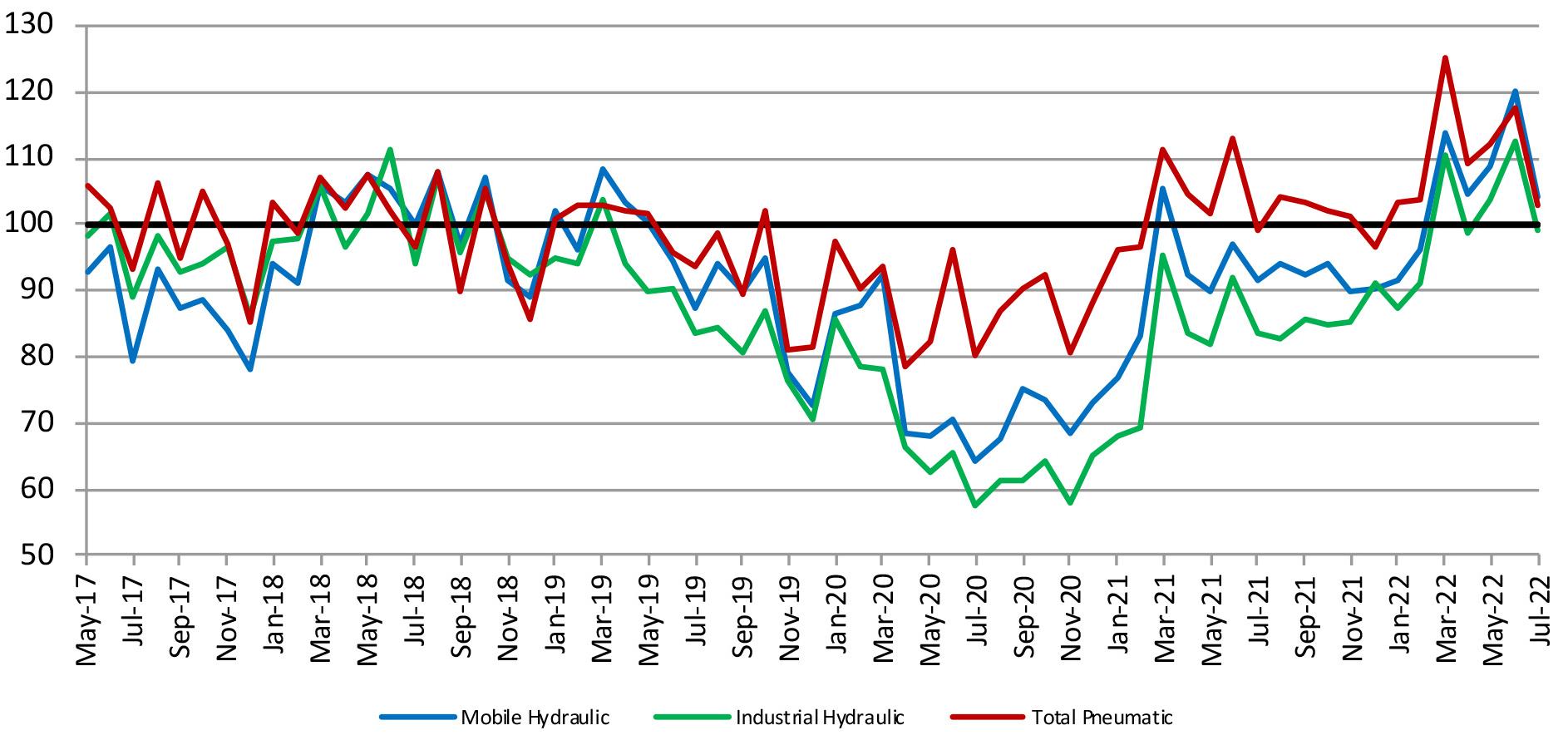
Blue Bell, Pennsylvania USA
•
New – Texcel 10K Mud & Cementing Hose. A heavy duty 10,000 PSI WP hose designed for cementing services in the oil field. Recommended coupled with Texcel F6-1502 Hammer Unions. In stock and available in variable lengths, with raw ends or fabricated. Contact us to learn more.
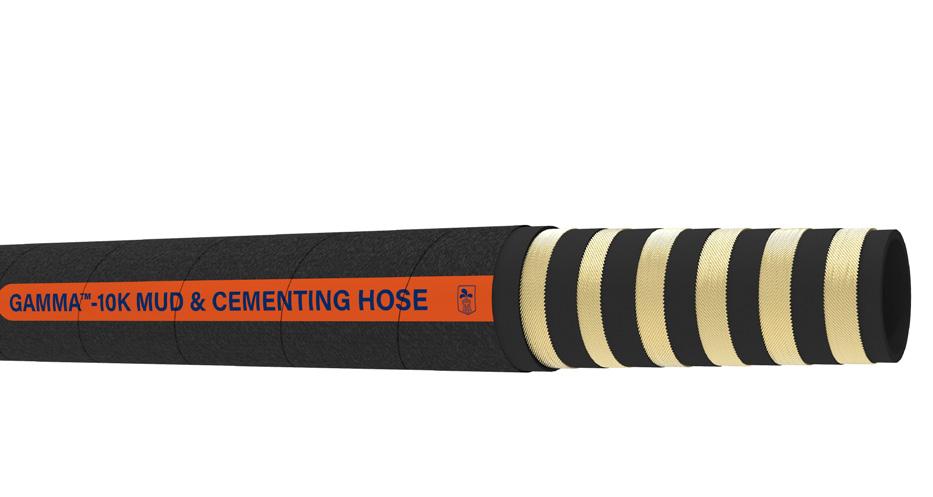
•
800-231-7116sales@texcelrubber.com
•
•
Contact us to showcase your products and services in the Product Spotlight. This special section is a high-profile area offering product-specific advertising.
SPECIAL AD SECTION
Inserta® IGSP Slip-In Check Valve Retaining Assembly, Flange Type, provides an effective means to retain an Inserta® IGS Slip-In Check Valve in a 90 degree flow path application (oil inlet-axial, oil outletradial). These are available to retain nominal valve sizes from one inch to two inches inclusive, for flows up to 200 gpm, and pressures up to 6000 psi. Inserta® IGS Slip-In Check Valves used with a 90 degree flow path may be considered as potentially more efficient alternatives to typical thread-in cartridge check valves.

New—Flatwww.inserta.comFace
Visit fluidpowerjournal.com for more information or to view our media guide.

22 OCTOBER 2022 WWW.FLUIDPOWERJOURNAL.COM • WWW.IFPS.ORG
SPOTLIGHTPRODUCT
Design "TVF" Series Quick Disconnect Up to 6,000 PSI Operating Pressure— Coupled or Uncoupled Full 4:1 Safety Factor Superior Flow Characteristics—Minimal Pressure Drop RoHS Compliant Plating Multiple Port Options—Female NPTF, Female SAE O-Ring, Female BSPP, Code 61 & 62 Flange Port/Head
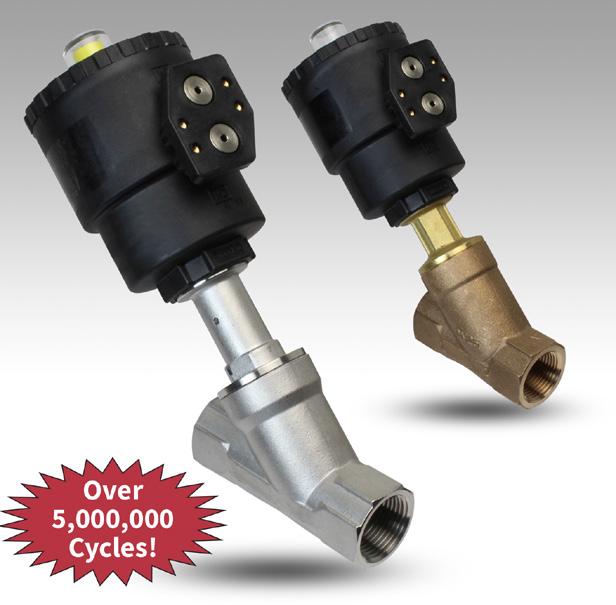
Slip-In Check Valve Retaining Assembly

Inserta® Products
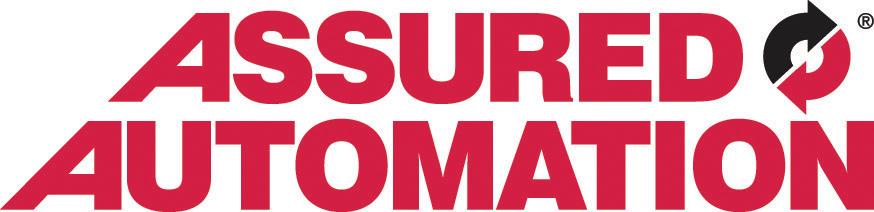
•
P.O. Box 6479 • Fort Worth, TX 76115 817.923.1965 • www.hydraulicsinc.com
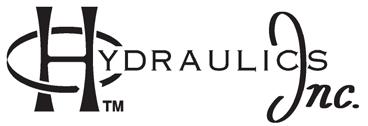
HIGH ANGLECYCLE-LIFEVALVE 2-way topistonThegases,areactuatedpneumaticallyangleseatvalvessuitableforliquids,andsteam.uniquedesignoftheenablestheplugretractfurtherfromthe flow path, ensuring the highest flow capacity. The dual packing design, and a large diameter self-aligning stem ensures the highest cycle life. 3/8" to 2" NPT & Tri-clamp. Bronze or 316SS. IN STOCK! sales@assuredautomation.com800-899-0553https://assuredautomation.com/anglevalve/

Don’t Compromise – that hydraulic flange you want maybe at MAIN
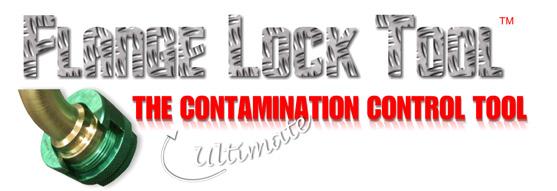
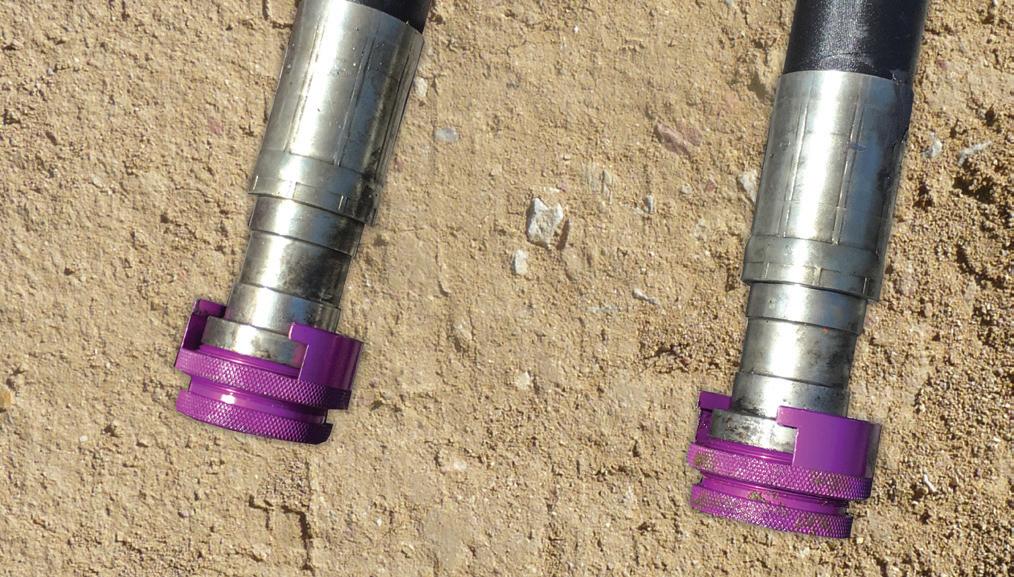

Contact us to showcase your products and services in the Product Spotlight. This special section is a high-profile area offering product-specific advertising. Visit www.fluidpowerjournal.com for more information or to view our media guide. SPECIAL AD SECTION WWW.IFPS.ORG • WWW.FLUIDPOWERJOURNAL.COM OCTOBER 2022 23 Go ahead. Push me. Ordinary heavy duty not heavy enough? Heavy-Duty Mill Cylinders for: • Induction-Hardened,Chrome-PlatedRods • Heavy Wall Tubing • Replaceable Glands & Retainer Rings • High-Load Piston Design Think indestructible and call Yates. www.yatesind.com Yates Industries (HQ) Yates586.778.7680Cylinders Alabama Yates256.351.8081Cylinders Georgia Yates678.355.2240Cylinders Ohio 513.217.6777
FluiDyne Fluid Power Stocks

MAIN stocks 10,000+ hydraulic flanges and manufactures components in 4-7 days in the USA. SAE J518 Code 61 and J518 Code 62, JIS, DIN, ISO 6162, ISO 6164, and specials with socket-weld, butt-weld, ORB, BSPP, etc.; all geometries, flange heads, flange adapters; in carbon, stainless, cupro-nickel, ductile, aluminum, etc. Sixty years’ experience plus SAE and ISO technical committee experience.
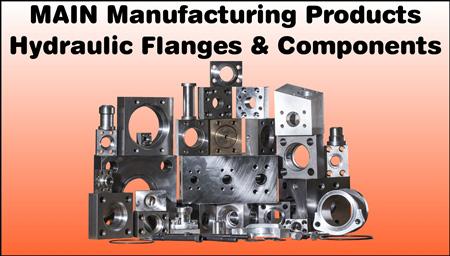
FluiDyne carries a complete line of A4V piston pumps that are available in displacement of: 40, 71, 125, 180, 250. Our units are used in many different applications: agriculture, forestry machinery, construction, on-highway, commercial vehicles, offshore, marine, wind/ocean energy, automotive and more.
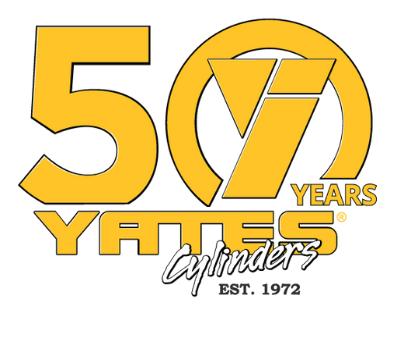
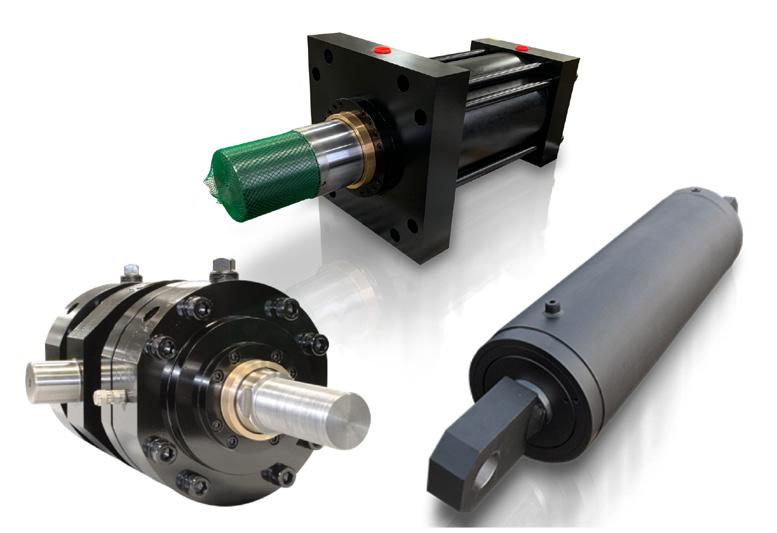
Controls include: DR, DRG, FR, FRG, DFR, and LR2. They are available in SAE or metric. The versatile A4V units carry the industry leading 18 month warranty. Units are fully tested, documented and guaranteed to perform 100% to the original manufacturer’s specification.
MAIN https://mainmanufacturing.com/block-categories800.521.7918Products,ManufacturingInc.

Call, email, chat…we’re ready to help! 586.296.7200 • www.fluidynefp.comsales@fluidynefp.com
A4V Piston Pumps & Parts
Hitachi have packaged FlangeLock tool and caps specifically for Hitachi mining excavators. The Hitachi customised kits make sure no matter which component routine maintenance is being performed on, you will always have the exact number of FlangeLocks™* and caps to help reduce contamination. *Note: FlangeLocks™ are not to be used under pressure Call you local Hitachi Muswellbrook representative or the branch on 02 6541 6300 for more information. • No tools required • No expensive hardware needed • No more rags stuffed into hoses • No more messy plastic caps • The ultimate contamination control tool • One hand installation • Eliminate hydraulic oil spills & clean up • Quick installation & ease of usage • Safe for personnel & environment • Industry acclaimed Stop The Mess! SAVE TIME SAVESAVEMONEYSAVELABOROIL For more information, call (203) 861-9400 or email www.flangelock.comsales@flangelock.com
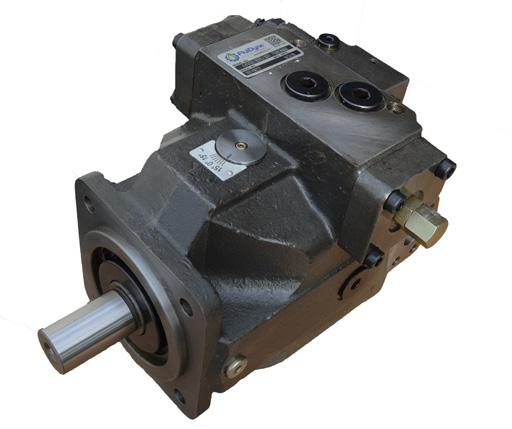
Helios Launches Valve Line by Sun Hydraulics
The ES 2-Way and 3-Way valves feature ultra-low leak rates, fast response, multiple flow rates and cycle life of over 1 billion. Clippard’s proven spider technology utilizes one moving part enabling the ES to operate with exceptional reliability

SPECIAL AD SECTION 24 OCTOBER 2022 WWW.FLUIDPOWERJOURNAL.COM • WWW.IFPS.ORG
» HELIOS TECHNOLOGIES, a manufacturer of highly engineered motion control and electronic controls technology for diverse end markets, recently announced a program launch from one of its operating companies, Sun Hydraulics.Heliossays its Sun Common cartridge valves were developed to offer cross compatibility solutions and are reliable, universal solutions for a broad variety of hydraulic systems, from highly demanding applications requiring multidi rectional fluid flow to simpler, lower pressure requirements.
METARIS BRAND LOW SPEED HIGH TORQUE ORBITAL MOTORS
ForHydraulexmoreinformation, call us at 1-800-323-8416 or visit www.orbitalmotors.net
PRODUCT REVIEW
ES SERIES ELECTRONIC VALVES
The compact footprint coupled with the long life, and exceptional leak resistance make the ES line suited to improve reliability in a wide range of applications including biomedical, dental, test equipment, oxygen control, textile, packaging, pressure control, automation and portable systems.
clippard.com
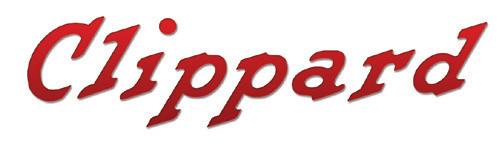
For users who require optimized interchangeability for 3,000-psi sys tems, Sun Common cavity cartridge valves are an ideal drop-in solution. Sun Common cartridge valves utilize the SAE style cavity, meaning they are com pliant to industry standards.
Genuine Metaris Orbital Motors are your best low speed high torque motor option in an economical and compact design. Utilizing proven Roller-Star technology, these motors allow for high efficiency, smooth operation and a long operational life. The motors come equipped with a high-pressure shaft seal and also come in a wide range of displacements. The Genuine Metaris Orbital Motor is a functional replacement for common motors in the market today such as Eaton®/Char-Lynn®, Danfoss®, Parker® and White®
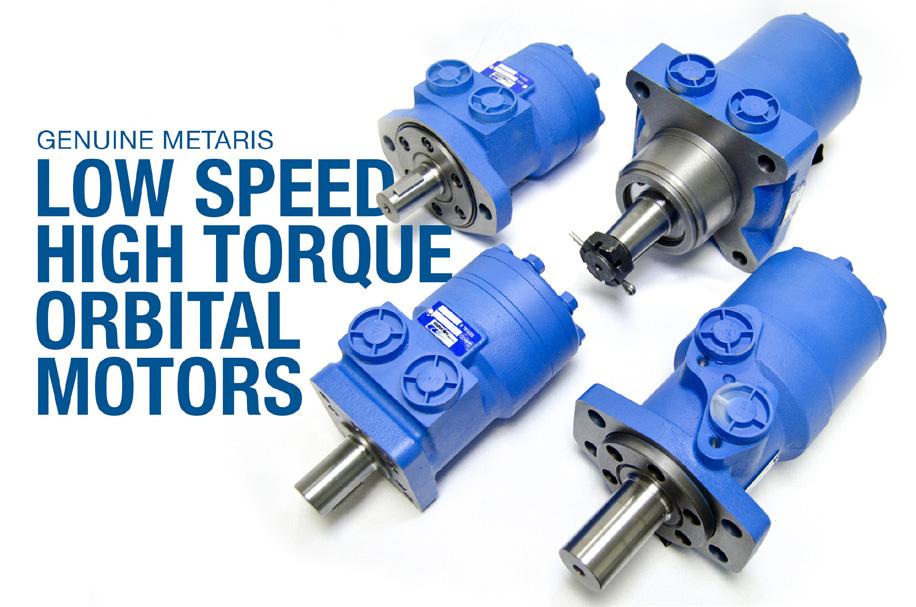
Sun Common cavity cartridge valves offer a wide variety of functions enabling the design of new hydraulic system solutions where a common cavity fits best. This new product family from Sun leverages the company’s product portfolio and delivers common solutions for unique applications.
For more information, visit www.sunhydraulics.com.
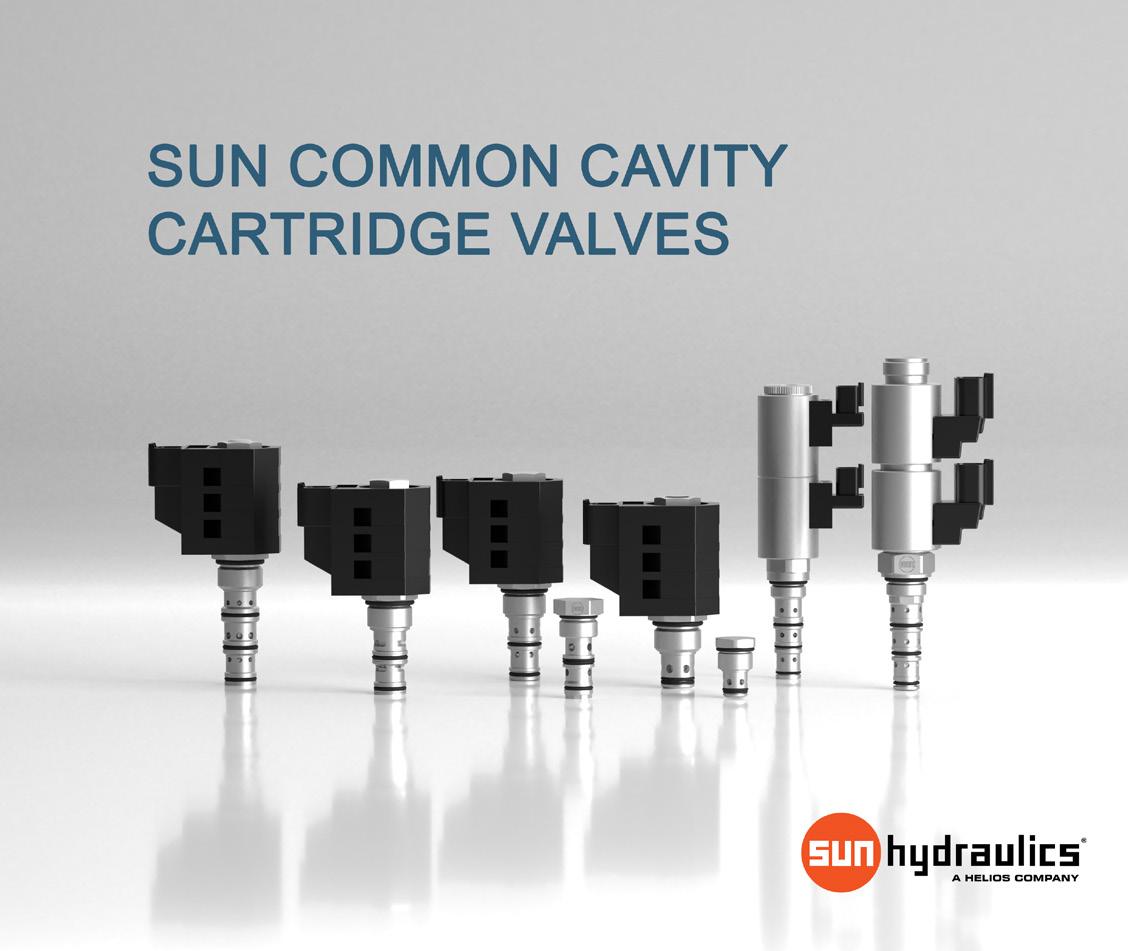
EM
New Problem Compactor Loses Pressure to All Circuits
Robert Sheaf has more than 45 years troubleshooting, training, and consulting in the fluid power field. Email rjsheaf@cfc-solar.com or visit his website at www.cfcindustrialtraining.com
When I arrived, I sketched out the circuit but was con vinced that the pilot orifice in the pilot-operated relief was plugged. They examined the orifice, and to my surprise, it was clear of any contaminant. Both the main ram and door cylinders checked out OK.
By Robert Sheaf, CFPAI/AJPP, CFPE, CFPS, CFPECS, CFPMT, CFPMIP, CFPMMH, CFPMIH, CFPMM, CFC Industrial Training
» I WAS CALLED IN to help with a compactor that bails scrap paper leftover after trimming paper sheets for paper grocery bags. As the circuit on the right shows, the system is simple. However, the customer did not have a circuit to use for troubleshooting, and his first instinct was to replace the pump.
WWW.IFPS.ORG • WWW.FLUIDPOWERJOURNAL.COM OCTOBER 2022 25 FIGURE IT OUT
After installing the new pump, they removed the visibly dirty pressure filter element and reinstalled the housing canister without an element, as they did not have a spare. They started up and still could not get any system pressure. Then they removed the main spool for inspection by remov ing an end cap on the main stage of the valve. It seemed in good condition. Next, they thought the pilot valve on the directional control valve was not shifting the main spool, so they replaced it with one they had in stock. Still no pressure.
What could be the problem?
Solution to the September 2022 problem: Extractor Motor Reverse Speed Rises to an Unexpected Creep
Pressure-reducing valves that pass flow in the reverse direction without a separate bypass check keep the spool in the normal open position, allowing flow in either direction. However, the signal line looks at the oil coming from the motor, and if there is a pressure spike due to higher flows, it causes the pressure reducing valve to close, creating a restriction. They found that the original pump’s volume adjustment reduced the flow about 5%. Reducing the new pump’s flow solved the spike problem.
Operating principles
However, building closed loop flow control systems is complicated and costly. This typically involves a proportional integral derivative con troller to accurately provide constant downstream flow rates. These are complex mechanisms that require experienced pneumatic and software engineers to build.
Consequently, gas flows from the supply, across the compensator spool, and through the variable orifice, while a constant pressure drop across the variable orifice keeps the flow rate constant regardless of changes in pressure between supply and load.
Pressure Compensated Flow Control Valves
By applying a force to the end of the spool attached to the valve housing, a spring keeps the spool attached to it. Flowing past the variable orifice in the outlet of the valve applies an additional force to the anchored end of the spool. There is a pressure gradient along the line leading from the pressure-compensated flow control valve to the load, such as a hydraulic motor or cylinder.
Apressure-compensated flow control valve is designed to provide a constant volume flow rate regardless of the pressure drop across it. By contrast, non-pressure-compensated flow control valves have a variable flow rate that changes when the pressure drop fluctuates. It is possible for pressure-compensated flow control valves to also compen sate pressure fluctuations on either the supply (inlet) or the load (outlet) side of the valve.
26 OCTOBER 2022 WWW.FLUIDPOWERJOURNAL.COM • WWW.IFPS.ORG
Variable orifices are made up of valve stems that have a pointed end that can move toward and away from a seat in order to achieve different sizes of openings. Whenever the tip of the stem is in full contact with the seat, the orifice becomes closed, and no gas can pass. With the stem tip moved away from the seat, the orifice opening becomes larger, and more gas passes through.
Mass flow controllers are another option. They use closed loop technol ogy to provide stable flow rates with varying pressure drops. These flow control devices are a great option to avoid the high cost of developing a custom closed loop device. These controllers have an internal flow or pressure transducer, flow control valve, and proportional integral derivative circuit that can dynamically adjust the current flow output of the internal flow valve.
By adjusting the pass-through area of the orifice, the desired flow rate is set on the variable orifice. You can make this adjustment manually using a knob, screw, or lever on the valve or, alternatively, with electronic signals sent to an actuator attached to the variable orifice. The pressure compensator achieves a constant pressure drop across the variable ori fice by modulating the flow of gas entering the valve. It also provides a constant flow rate across the valve by adjusting the orifice between the inlet flow and the compensator spool.
Flow control valves that are pressure compensated normally consist of a variable orifice and a pressure compensator incorporated into one valve body. Flow goes from the supply valve through the inlet and com pensated orifice, around the compensated spool, through the variable orifice, and then out the outlet.
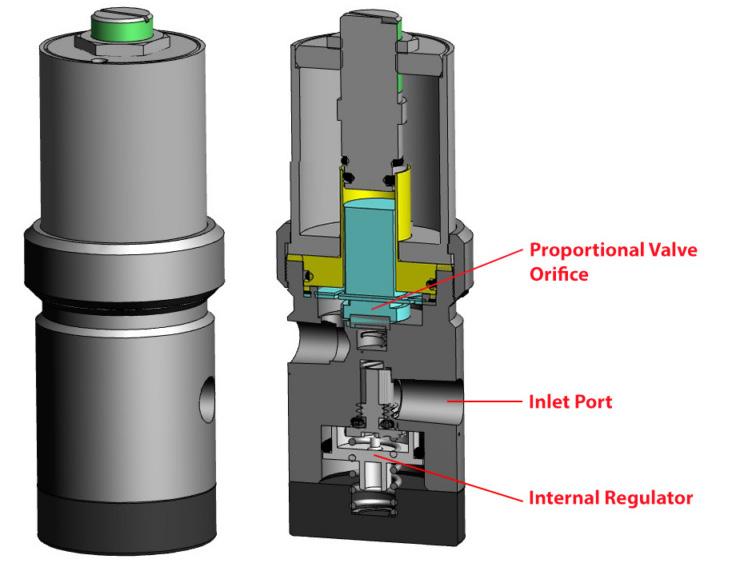
One way to address the problem of changing flow based on a fluctuating pressure drop is to use a flow control valve with closed loop control. This involves adding a flow transducer or pressure transducer downstream from the valve that sends a signal back to a control system, representing the current downstream conditions. This feedback signal can be used to calculate real-time adjustments needed to maintain flow rate, which can be commanded to the flow control valve accordingly.
By John Kelly, Engineering Manager, Kelly Pneumatics
The gas that has passed the variable orifice but not yet reached the inlet and compensator is ported to the other end of the spool (the end opposite the end attached to the spring). A force is applied to the spool at this end by the gas that opposes the force applied by the load pressure and spring pressure. The opposing forces distort the opening of the orifice through which gas flows from the flow source, modulating the opening of the orifice until the forces at either end of the spool are balanced.
A spool valve with a spring anchors the pressure compensator. Com pensation spools consist of a cylindrical barrel with a plunger that slides inside. Plungers have thin and wide sections along their length. As long as the lands and ports are adjacent to each other, they block gas flow. The wide sections of the barrel are called lands. Spools with narrow, wasted sections allow gas to pass through them.
A primary issue with mass flow controllers is the need for a downstream transducer. Since the closed loop control requires a downstream transducer, it can be difficult to find mass flow controllers compatible with some media. For example, some corrosive or caustic gasses cannot be used with transducers.
Given the challenges of using a mass flow controller or building a custom closed loop flow controller, a pressure compensating valve may be a much better solution.
The Versatile Remedy
WWW.IFPS.ORG • WWW.FLUIDPOWERJOURNAL.COM OCTOBER 2022 27

Pressure-compensated flow control valves are used in a variety of hydraulic applications. They are useful, for example, when it is necessary to maintain a constant speed on a hydraulic cylinder, regardless of the amount of load the cylinder is under. Because speed is directly pro portional to hydraulic gas flow rate, a hydraulic cylinder’s speed depends on how much gas is flowing through it.
An integral part of a pressure-compensated flow control valve is the pressure compensator. A valve without it would have a variable flow rate when pressure across the valve varies. Forcing
When you need to get a machine back up and going yesterday, we’re here for you with our Hydraulex Reman™ line. Remanufactured pumps, motors and valves engineered to deliver OEM level performance and that carry an industrybest 24-month warranty. With our unmatched on-the-shelf inventory of units and parts, and our ability to convert or build units in hours instead of days or weeks, we’re sure to have the unit or part you need right now. Speed and availability redefined. Put a Hydraulex Reman™ unit to work for you.
Pressure-compensated flow control valves are also useful in maintaining constant rpm of a hydraulic motor independent of load on the motor. Much like the example above, changing loads on the motor results in a fluctuating pres sure drop across the valve ahead of the motor. Pressure-compensated flow control valves com pensate for these fluctuations by maintaining the hydraulic motor’s rpm at a constant level.
Applications
sales@hydraulex.com www.hydraulex.com
differences between the valve inlet and outlet. This decreases the incoming input process on the inlet port to the lowest operation working pressure for the valve to output accurate flow rates. After regulation, this lowered pressure is applied to the proportional valve orifice, thereby allowing for consistent flow rates even with fluc tuating input pressures. So long as the incoming pressure does not drop below the minimum required pressure, accurate proportional flow is maintained to the system. •
1.800.422.4279
more gas through the valve as a result of a higher pressure drop raises the flow rate; a lower pres sure drop lowers the flow rate.
HYDRAULIC PUMPS. MOTORS. VALVES. SERVO VALVES. PROPORTIONAL VALVES.
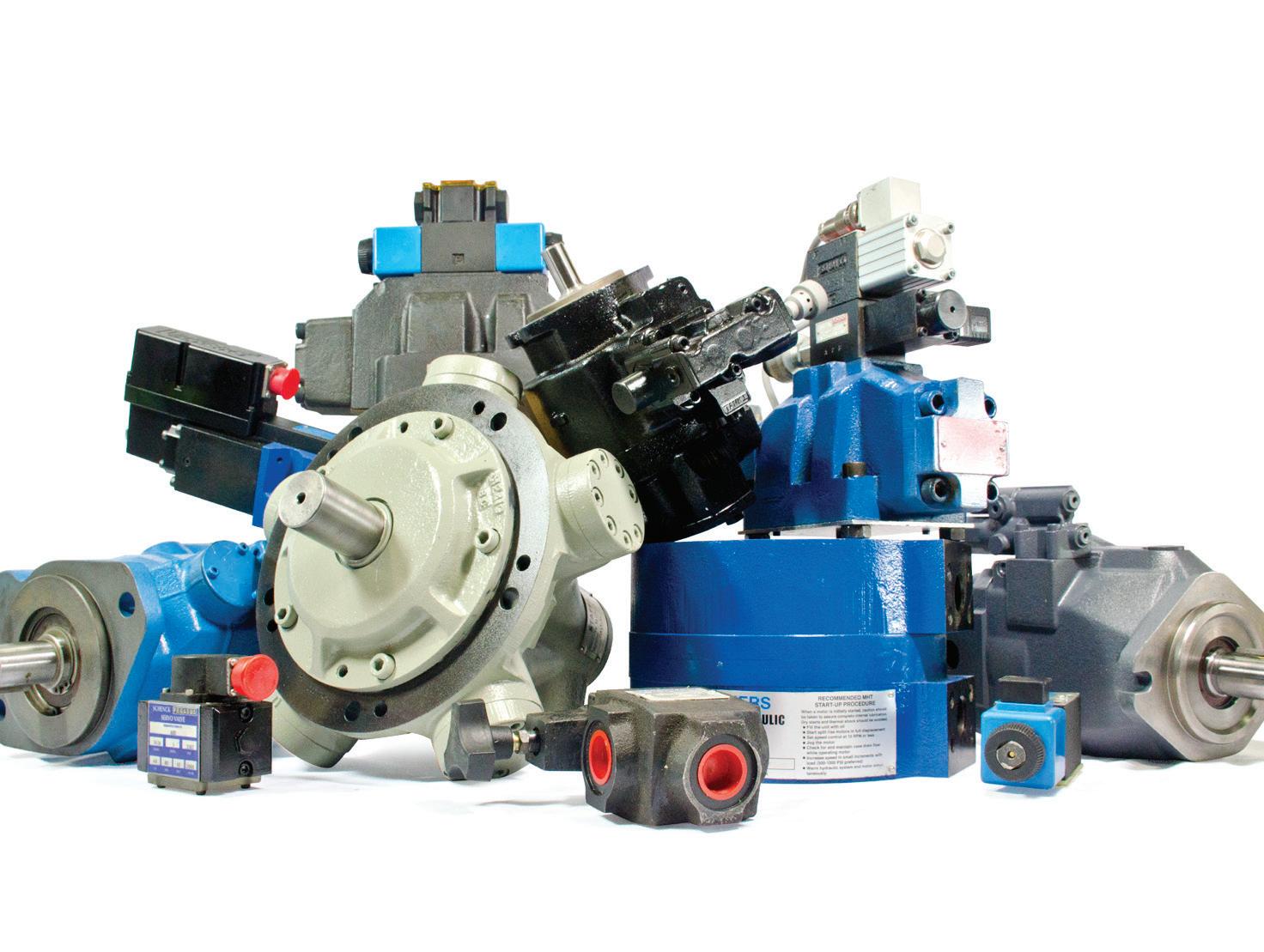
By automatically adjusting the volume flow rate from the flow supply to the variable orifice, the pressure compensator keeps the inter nal pressure drop across the variable orifice constant, regardless of the change in pres sure drop between the inlet and outlet. With a constant internal pressure drop across the variable orifice, the valve produces a constant volumetric flow rate regardless of the pressure
As gas temperature increases, viscos ity also increases, affecting flow rate. Some pressure-compensated flow control valves incorporate a temperature-sensitive element that adapts the position of the compensator when gas temperatures and viscosity vary. This ensures a constant flow rate regardless of gas temperature and viscosity. By using a sharpedged orifice design for the variable orifice, some designs minimize the variations in flow rate due to changes in viscosity.
Kelly Pneumatics offers its pressure compen sated proportional valve for projects that require a pressure-compensated flow control valve. There is a mechanical pressure regulator built into the unit, which lowers the incoming input process on the inlet port to the lowest operating working pressure recommended for the valve to output accurate flow rates. Lowering the pres sure after regulation can achieve a consistent flow rate despite fluctuating input pressures. A proportional flow to the system is maintained so long as the incoming pressure does not drop below the minimum required pressure.
LEAD TIMES OF HOURS. NOT WEEKS.
In a flow control valve without pressure com pensation, the flow rate fluctuates depending on the load on the cylinder. A heavy load on the cyl inder increases the pressure at the valve’s outlet compared to one with a lighter load. Changing the pressure drop across the valve alters the flow rate it delivers to the cylinder. Pressurecompensated flow control valves adapt to such pressure changes to maintain a constant flow rate that provides gas motion at constant speed
Magnetek, a brand of Columbus McKinnon, was challenged by JT Cranes to provide a flexible wireless solution that had the capacity for future enhancements. This wireless solution needed to increase maneu verability and safety for lifted loads, allow operators better control of carrier speed, and decrease the footprint of existing controls.
The challenge
Mounted on continuous tracks and positioned low to the ground, the tracked carrier platform can easily move across rough indoor or outdoor
28 OCTOBER 2022 WWW.FLUIDPOWERJOURNAL.COM • WWW.IFPS.ORG
Case forWirelessStudyControlsTrackedCarrier
By Ben Stoller, Business Development Manager, Columbus McKinnon
Magnetek, working in concert with JT Cranes, designed a custom eight-button handheld wireless control system that improved direc tional accuracy by using buttons configured with proportional control and incorporated four modes of adjustable speed settings for precision control. The system’s transmitter and receiver occupied limited space on the carrier platform, which left a smaller footprint than traditional crane systems and could not handle a large control package.

The solution
The project
As a family firm of crane specialists, John Taylor Crane Services of Bedfordshire, U.K., developed an innovative tracked platform intended to reduce the need for manual handling. This tracked carrier platform was designed to operate where forklifts and other machinery could not maneuver.

Easy on, easy off. Offers a
*Note:
tools
The Flex Pro and MHR integrated so easily with the D40 that JT Cranes plans to install the system on additional tracked carriers. The systems’ flexibility also makes future enhancements, such as engine start-up buttons, a simple modification. • SAE code 61, from lightweight aluminum. leakproof hydraulic
housing and NEMA 4 (IP66) rating, the Flex Pro is made to withstand shock and sealed to operate in a variety of harsh, industrial environments. The Flex Pro transmitter is paired with Magnetek’s patented MHR radio controller, which combines the components of a radio receiver and up to 16 hydraulic proportional valve controllers into a single convenient unit, reducing costs and freeing up valuable space on the equipment. The MHR utilizes an infor mative graphic display to easily view system settings and machine functions. Two-way feedback provides operators with precise information about equipment performance. The MHR’s rugged, waterproof design makes it ideal for outdoor use and harsh environments. Magnetek’s transmitter and receiver system improved the level of control operators had over the tracked car rier. Proportional control provided smooth movements for the safety of lifted loads and greater spatial control for maneuvering the D40 in tight spaces.
The FlangeLock™ Tool is the ultimate contamination control tool for protecting your hydraulic systems. It allows for the simple sealing of open
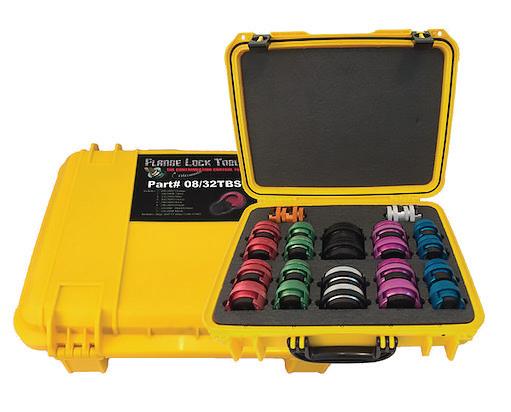
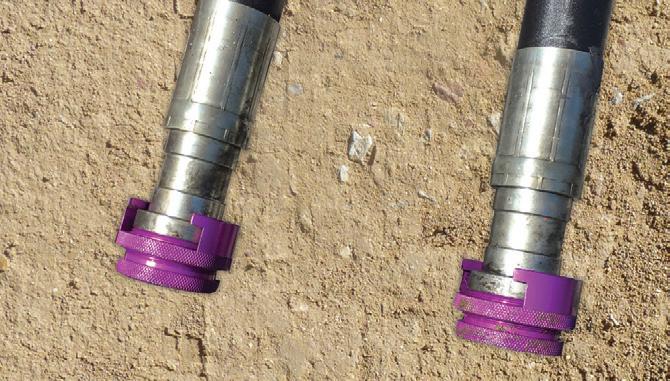
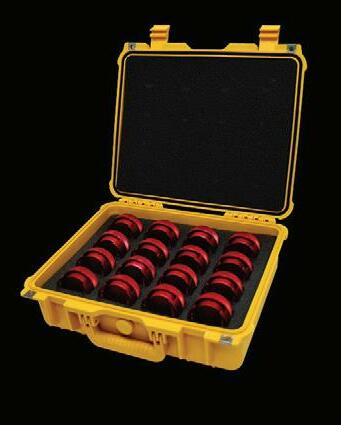
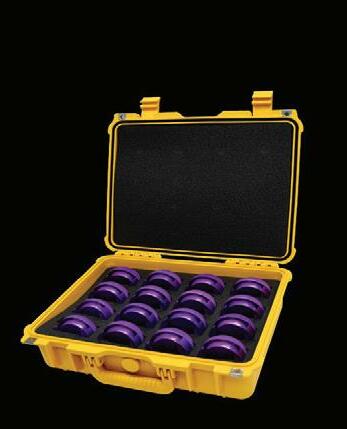
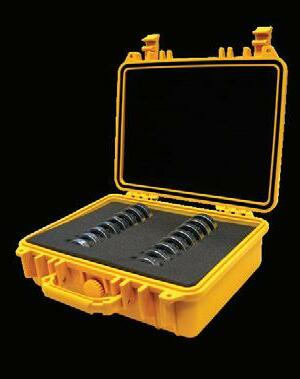
system and environmental cleanliness. FlangeLock™ Tools stop the mess! Stop the Mess SAVE TIME SAVE MONEY SAVE LABOR SAVE OIL For more information, call (203) 861-9400 or email www.flangelock.comsales@flangelock.com. • No tools required • No expensive hardware needed • No more rags stuffed into hoses • No more messy plastic caps • The ultimate contamination control tool • One hand installation • Eliminate hydraulic oil spills & clean up • Quick installation & ease of usage • Safe for personnel & environment • Industry acclaimed This product is Patented, other Patents pending. HITACHI FLANGELOCK TM AND CAP KITS AVAILABLE Part number Part description Applicable machines Weight (kg) SWINGFLGLCK2062 Swing hose FlangeLockTM kit EX3600, EX5600, EX8000 16 x 2062U - red FlangeLockTM 6.7 SWINGCAP2062 Swing circuit cap kit EX3600, EX5600, EX8000 16 x 2062 - cap 4.5 TRAVELFLGLCK2462 Travel hose FlangeLockTM kit EX3600, EX5600, EX8000 16 x 2462U - purple FlangeLockTM 7.7 TRAVELCAP2462 Travel circuit cap kit EX3600, EX5600, EX8000 16 x 2462 - cap 6.4 FRONTATTFLGLCK326162 Front FlangeLockattachmentTMkit EX3600, EX5600, EX8000 14 x 3262U - black FlangeLockTM 4 x 3261U - black & silver FlangeLockTM 8.9 FRONTATTCAP326162 Front attachment cap kit EX3600, EX5600, EX8000 14 x 3262 - cap 4 x 3261 - cap 9.5 BOOMARCHFLGLCK3262 Boom arch hose FlangeLockTM kit EX3600, EX5600, EX8000 20 x 3262U - black FlangeLockTM 9.9 BOOMARCHCAP3262 Boom arch hose cap kit EX3600, EX5600, EX8000 20 x 3262 - cap 11.3

HITACHI MAKING CONTAMINATION CONTROL EASY
62 & CAT-Style hydraulic flanges without tools. Constructed

CONTAMINATION CONTROL
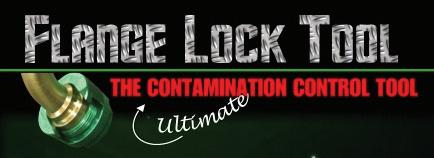
WWW.IFPS.ORG • WWW.FLUIDPOWERJOURNAL.COM OCTOBER 2022 29
The FlangeLock™ tool and caps are the ultimate contamination control tools for protecting your hydraulic system. The FlangeLock™ allows for the simple sealing of open hydraulic flanges without while the caps can be bolted in place of a flange connection. Easy on, easy off, they offer a leak-proof solution to hydraulic systems and environmental cleanliness. FlangeLock tools and caps stop the mess.
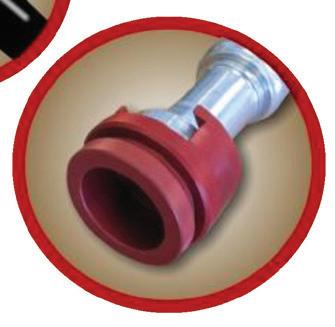
Hitachi have packaged FlangeLock™ tool and caps specifically for Hitachi mining excavators. The Hitachi customised kits make sure no matter which component routine maintenance is being performed on, you will always have the exact number of FlangeLocks™* and caps to help reduce contamination. FlangeLocks are not to be used under
While JT Cranes originally considered a larger bellybox transmitter for the application, they discovered a more compact, versatile option better suited to their requirements: the Magnetek eight-button Flex Pro transmitter. Flex Pro offers precise management and smooth control of all functions. Smooth movements are essential for successful carrier operation, particu larly when moving fragile loads, such as art pieces. Any uneven lifts or unwanted movement while the carrier platform traverses an area or during a lift could mean dropped loads or damaged material.
Routine and scheduled maintenance of hydraulic systems are vital to getting the most out of your Hitachi Mining Excavator. While maintenance plays the largest role in the prevention of unnecessary machine downtime, it can also expose the hydraulic system to high levels of contamination rapidly decreasing component longevity. The importance of contamination control is sometimes overlooked when performing maintenance due to incorrect practices being used.
terrain and traverse ramps of up to 40°. It is able to carry loads up to four tons despite its compact design. Its load carrying platform can rotate 360°, allowing for enhanced maneuverability as compared to standard crane systems. JT Cranes looked to incorporate flexible and precise wireless controls into these carrier systems to enhance their versatility. The tracked carrier platform required the highest levels of maneuverability for lifting in small spaces, moving forward and backward, and getting around tight corners and through standard doorways.
solution to
THE FLANGELOCK™ TOOL AND CIRCUIT BLANKING CAPS
The Flex Pro transmitter was customized by Magnetek to meet the carrier’s exact needs, providing adjustable speed control in a four-mode setting to deliver 25, 50, 75, or 100% output for precise machine movement. Addi tionally, the stepless variable speed control ensures that operators have an enhanced level of control over the carrier while it is in motion. With its tough nylon
pressure Call you local Hitachi Muswellbrook representative or the branch on 02 6541 6300 for more information.
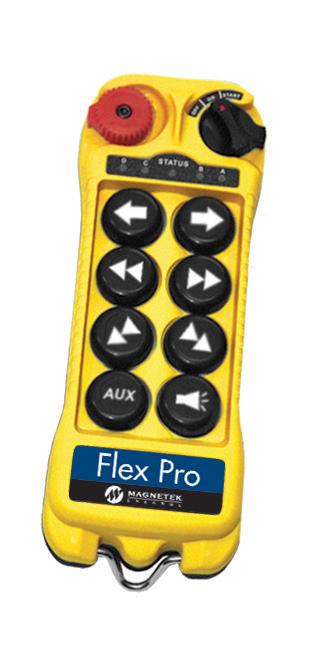
30 OCTOBER 2022 WWW.FLUIDPOWERJOURNAL.COM • WWW.IFPS.ORG Targeted Email Solutions Find. Get. Keep Customers Place your message in the inbox of thousands of potential new customers that directly mirror your best prospects. Customize your audience by zip code, county, state, age, gender, income, personal interests and almost characteristics!limitless PRECISELY TARGET YOUR BEST PROSPECTS BY: -Industry-Location Segment -Large-Products-MarketsScale Trade Show Events -and More! REACH & RETARGET Hyper-target your audience where they are engaging the most Connect with an audience that has expressed brand interest -See improved ROI CRAFT THE RIGHT MESSAGE Being able to precisely target your customers allows you to strategically craft your message to engage the recipient. Design your own email and we’ll deliver it - or work with our creative team to customize and launch your email campaign. BETTER RESULTS -Higher guaranteed click-through -Additional traffic to your website -Increased conversion rates -Improved analytics 3245 Freemansburg Ave, Palmer PA 18045 | Phone: 800.730.5904, 610.923.0380 | Fax: 610.923.0390 | www.fluidpowerjournal.com West Coast Hydraulics & Repair in Atwater, CA purchased the intellectual property of Hypower Hydraulics and will continue to manufacture the products they made. We also can manufacture any hydraulic cylinder you need of any size, any quantity. Small or large runs are welcome with guaranteed lead times. LOOKING HYDRAULICS?HYPOWERFOR Phone : 209-357-7360 Fax : sal_westcoast@yahoo.com209-357-7362 Se Habla Español 281 Business Park Way Suite D • SalvadorAtwater, Owner 281 Business Parkway Suite D | Atwater, CA 95301 EMAIL sal_westcoast@yahoo.com 209-357-7360
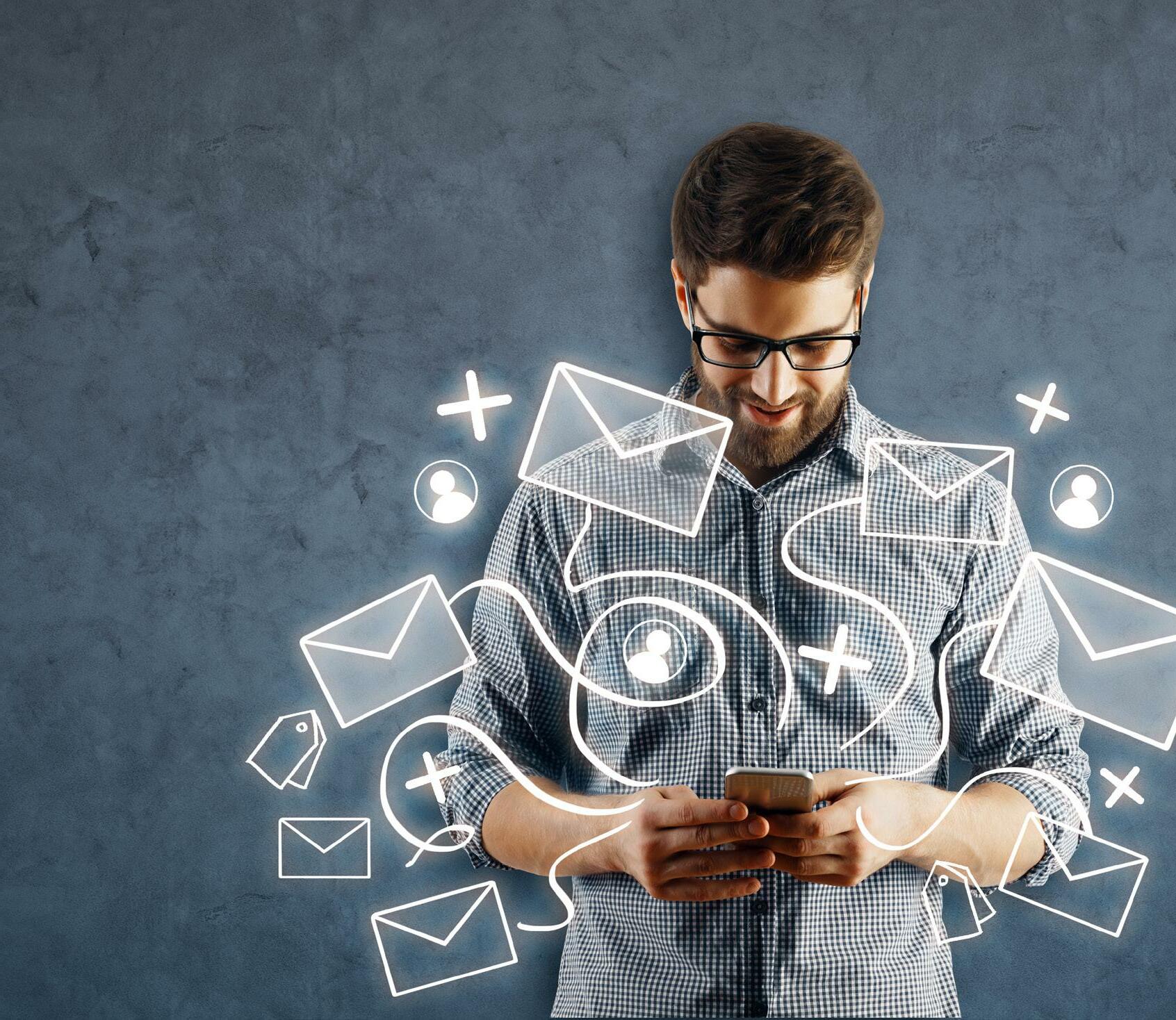
West Coast Hydraulics & Repair ............................... 30 ............................................
Norgren 1-800-514-0129 www.norgren.com 866-821-7926 www.ryco.com.au 866-629-0780 www.tele-radio.com/us/ TEXCEL 800-231-7116 www.texcelrubber.com 209-357-7360 www.yatesind.com
Tele Radio LLC 9



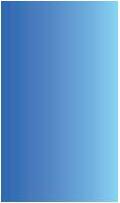

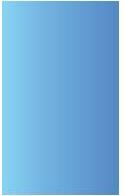
Ryco Hydraulics 9



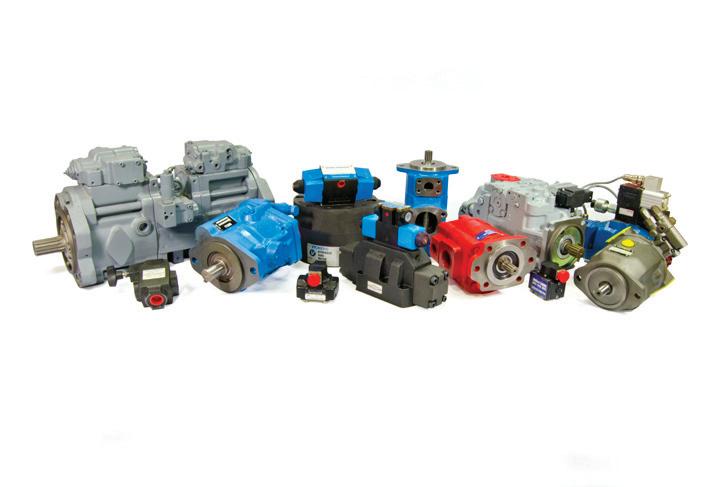
3
Inside Front Cover, 22
ADVERTISER INDEX powerful!quick,Compact,LargeInventory Standard, High Flow, Latching & ISO Series 10 & 15 mm Electronic Valves 877-245-6247 SupportTechnical
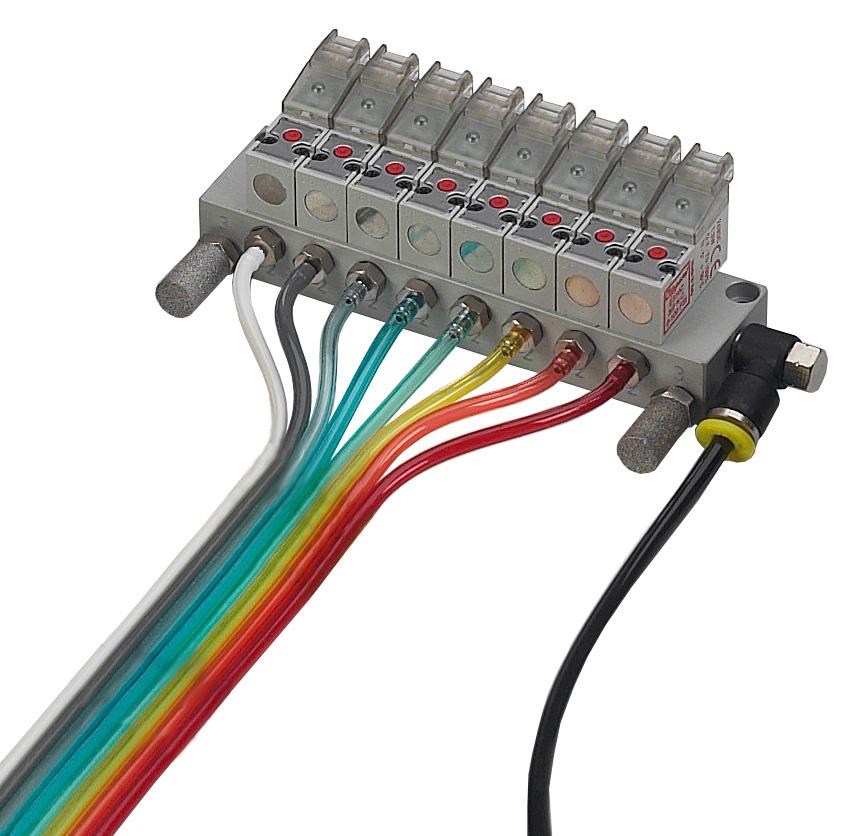


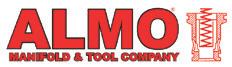
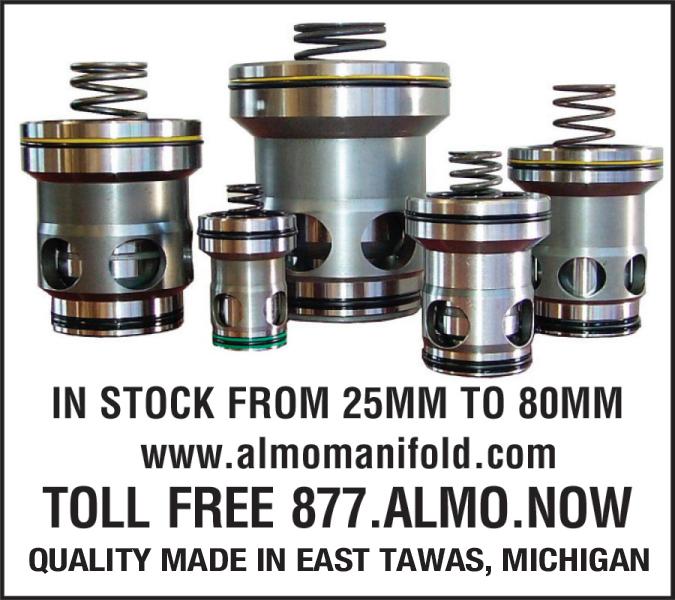

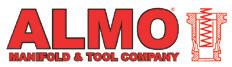
WWW.IFPS.ORG • WWW.FLUIDPOWERJOURNAL.COM OCTOBER 2022 31 PumpsSURPLUSWANTED·Motors·Valves·Servo/ProportionalEmail,callorfaxwithalistofyourSurplus.We’llprovideyouwithapriceoffer! 1-800-422-4279 | 586-949-4240 Fax: 586-949-5302 | surplus@hydraulex.com HYDRAULIC FLANGES and COMPONENTS THE “SPECIAL” YOU WANT IS PROBABLY ON OUR SHELVES MAIN Mfg. Products, Inc. 800.521.7918 fax 810.953.1385 www.MAINMFG.com/fpj HIGH FLOWPROPORTIONALFLOWCONTROL • 16MM to 50mm • Standard ISO 7368 and DIN 24342 cavity • High performance 5,000 psi • On board amplifier • 0-10 volt command almomanifold.com Phone: 989.984.0800 Toll Free: 1.877.ALMO. NOW Fax: 989.984.0830 IN STOCK FROM 25MM TO 80MM MANY COVERS IN STOCK • Pressure, Flow, Directional • Large Flow 90° Valves almomanifold.com Phone: 989.984.0800 Toll Free: 1.877.ALMO. NOW Fax: 989.984.0830 • Single DIN blocks • Active Valves • Monitored Poppets The correct answers to Test Your Skills on page 10 are 1-d and 2-d. CLASSIFIEDS Company Page Phone Web Adaconn/Inserta ..................................................... 5, 22 .................. 215-643-1900, 215-643-0192 ...................... www.adaconn.com, www.inserta.com AEM Inside Back Cover www.IFPE.com Almo Manifold 31 1-989-984-0800, 1-800-ALMO-NOW almomanifold.com Assured Automation 22 1-800-899-0553 www.assuredautomation.com CFC-Solar 13 513-874-3225 www.CFCINDUSTRIALTRAINING.com Clippard 24, 31, Back Cover 1-877-245-6247 www.clippard.com Flange Lock 23, 29 203-861-9400 www.flangelock.com Fluidyne Fluid Power 23, 31 1-586-296-7200 www.FluidyneFP.com Hydraulex ................................................... 11, 24, 27, 31 .........................................1-800-323-8416 ..................................................... www.hydraulex.com Hydraulics, Inc. ...................................................... 14, 22 ............................................ 817-923-1965 ............................................... www.hydraulicsinc.com Main Manufacturing Products 11, 23, 31 1-800-521-7918 www.mainmfg.com MOCAP INC 14 1-800-633-6775 www.MOCAP.com
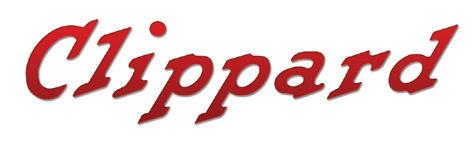
Yates, Inc. ................................................................. 1, 23 .........................................1-586-778-7860 .......................................................

SUBSCRIBE BY MAIL primary job only one) Administration: Chairman, President, V.P., Secretary, Treasury, General Manager, Owner, Business Manager, Director, etc. Plant Operations: VP of Manufacturing/ Operation/ Production, Plant Management/ Director/ Manager/ Supervisor/ Superintendent/ Foreman/ Safety Director, etc. Tech., of
01 YES! Please start/continue my complimentary subscription to the Fluid Power Journal 02 NO. Not interested. Signature (required) Title (required) Date (required) / / Telephone Fax E-mail
title? (check
Please
10
Type or Print Clearly: First Name Middle Initial Last Name Company Division Web Address Address Mail Stop City State Zip Code Check here if you would like to keep your name, address, phone and fax numbers confidential, and not released to third parties The address above is my: Home Address Business Address Which edition would you like to receive? Print Digital Both (View a sample of our PAPERLESS digital edition at www.fluidpowerjournal.com)
Fluid Power Tech., etc. 14 Mechanical: Chief Master Mech., Master Mech., Fluid Power Mech., etc. 15 Purchasing: VP/Director
Purch., Procurement Manager, Buyer, Purch., etc. 16 Other: (please specify)_________________________________________________________________________________________________ 3. Number of employees at this location? A 1-19 B 20-49 C 50-99 D 100-249 E 250-499 F 500-999 G 1000+ 4. What is the primary business activity at this location? In the Fluid Power Industry, Outside the Fluid Power Industry 56 Manufacturer 57 Distributor 58 Education 59 Original Equipment Manufacturer (OEM) 60 End User of Fluid Power Products 61 Other: (please specify)__________________________________________ 5. Which of the following best describes your market focus? A Aerospace A Marine & Offshore Equipment B Agricultural Machinery B Material Handling Equipment C Automotive C Mining Machinery D Civil Engineering D Packaging Machinery E Cranes E Plastic Machinery F Drills & Drilling Equip. F Presses & Foundry G Flame Cutting/Welding Equip. G Railroad Machinery H Food Machinery H Road Construct/Maint. Equip. I Forestry I Simulators & Test Equipment J Furnaces J Snow Vehicles, Ski Lifts K Gas & Oilfield Machinery K Steel Plants & Rolling Mills L Heavy Construction & Equip. L Truck & Bus Industry M Military Vehicles M Textile Machinery N Construction & Utility Equip. N Woodworking Machines O Machine Tools O Other (specify)_____________ P Government Related P Fluid Power Industry FILL OUT THIS CARD COMPLETELY, DETACH, AND MAIL OR FAX IT TO START YOUR SUBSCRIPTION MAIL TO: PO BOX 2548 • ORLANDO, FL 32802-9830 • FAX: 1-866-207-1450 YOU CAN ALSO SUBSCRIBE ONLINE AT WWW.FLUIDPOWERJOURNAL.COM. MY COMPANY SHOULD BE ADVERTISING IN OR SUBMIT AN ARTICLE TO THE FLUID POWER JOURNAL. PLEASE CONTACT THIS PERSON: PHONE:TITLE:NAME: SCAN HERE
11
1. Do you specify, select or influence the purchase of components & systems, on new or existing machinery? 03 Yes 04 No. If yes, which technologies? (check all that apply) 05 Hydraulic 06 Pneumatic 07 Vacuum 08 Electronic Controls 09 None of These 2. What is your
12 Engineering: V.P. Eng., Eng., Design Eng., Director of Eng., Staff Specialist, Chief Eng., Senior Eng., Maintenance/Production Eng., etc. 13 Technical: Chief
FLUIDINTERNATIONALPOWEREXPO MARCH 14-18, 2023 LAS VEGAS, NV, USA The International Fluid Power Exposition (IFPE) is the place where engineers meet to: “ There’s no other show in the world I think that brings the OEM machine manufacturers and the suppliers as close together as this show. It’s a good place to meet and learn about what’s going on. In the Americas, in the Western Hemisphere, this is the show for fluid power.” KEN ROSENBECKER SALES MANAGER NORTH AMERICA | WIPRO INFRASTRUCTURE ENGINEERING IFPE only happens once every three years! SAVE 20% OFF REGISTRATION Register now at IFPE.com and type AD20 in the Promo Code box Discover solutions current suppliers can offer to your unique challenges. Find new partners among suppliers pushing the envelope on what fluid power can do. CONNECT WITH TOP MANUFACTURESCO-LOCATED WITH CONEXPO-CON/AGG (two shows, one price) Including Bosch Rexroth , Danfoss Power Solutions , Poclain , IFM Efector , Hawe Hydraulik , Husco , and 375+ more! Join your peers from these OEMs: ∙ Caterpillar Inc ∙ Volvo EquipmentConstruction ∙ Liebherr ∙ CASE EquipmentConstruction ∙ Komatsu ∙ John Deere Construction ∙ Doosan Bobcat ∙ KOBELCO Construction Machinery USA ∙ LBX Company Spark new ideas with in-depth technical conversations with other engineers. The #1 Trade Show & Conference for Fluid Power, Power Transmission, and Motion Control IFPE20_210x285+3x4.5mm_Bleed_Registration_Ad_062722.indd 1 6/27/22 7:09 PM
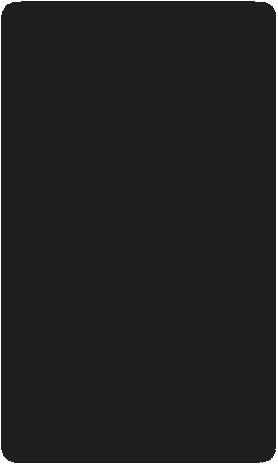
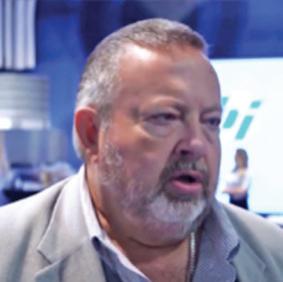
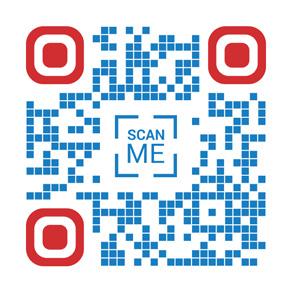

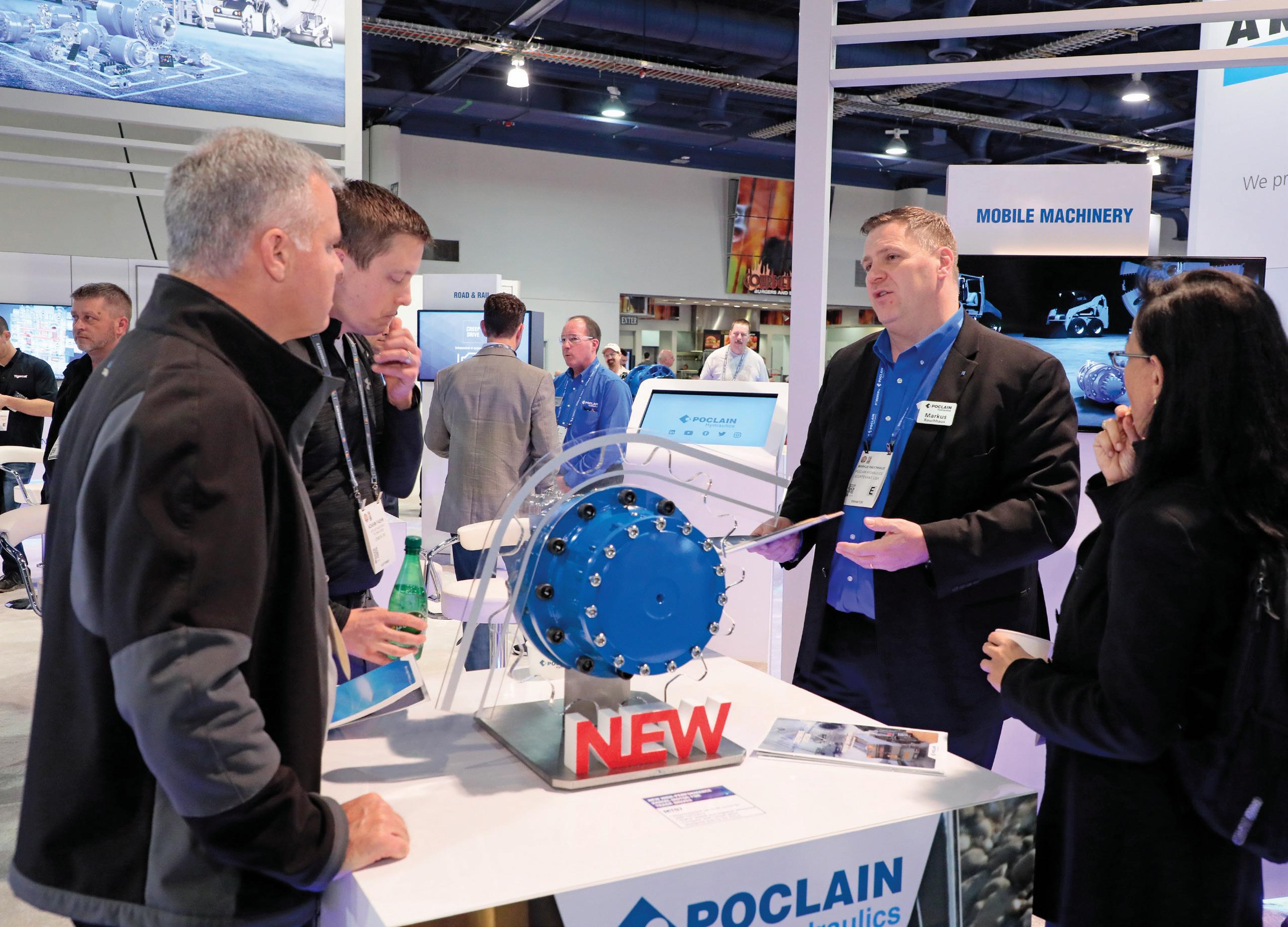
Precise, Linear Digital Pressure Control
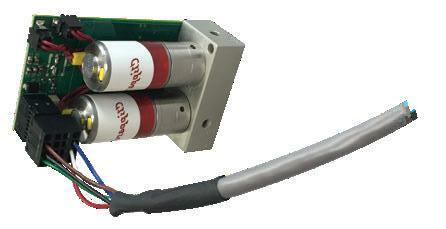
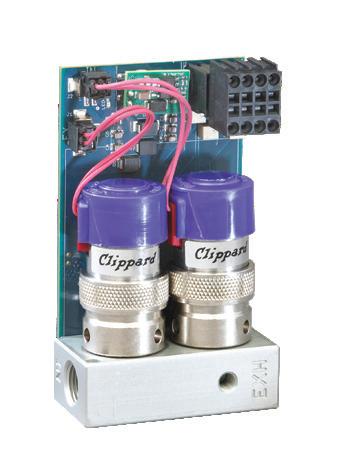
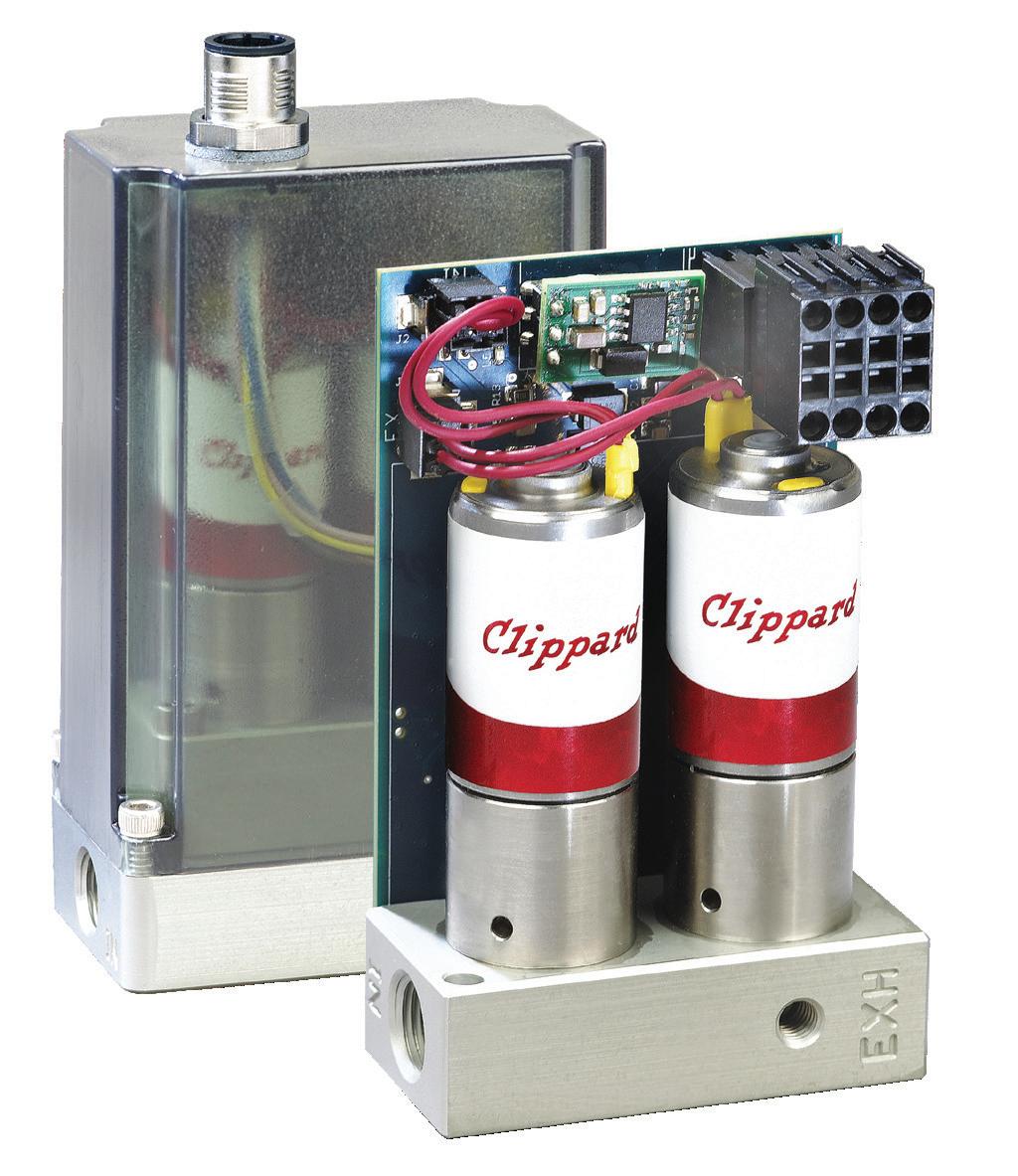
With unparalleled performance and flexibility not possible with current analog proportional controllers, the Cordis makes everything from calibration, to sensor variety, to future development opportunities more accessible and less complicated.
ELECTRONIC PRESSURE REGULATION
Contact your distributor today to learn more about how the Cordis can provide precise, real-time control for your application, or visit clippard.com to request more information.
• Resolution ≤5 mV • Accuracy ±0.25% of full scale • Real-time adjustable PID control • Integrated 0 to 10 VDC, 4-20 mA signal, or 3.3 VDC serial communication • 0 to 10 VDC feedback pressure monitor • Virtually silent • No integral bleed required • Multiple pressure ranges from vacuum to 150 psig • 2.7 to 65 l/min flow control 877-245-6247 CINCINNATI • BRUSSELS • SHANGHAI
Take Control with Cordis
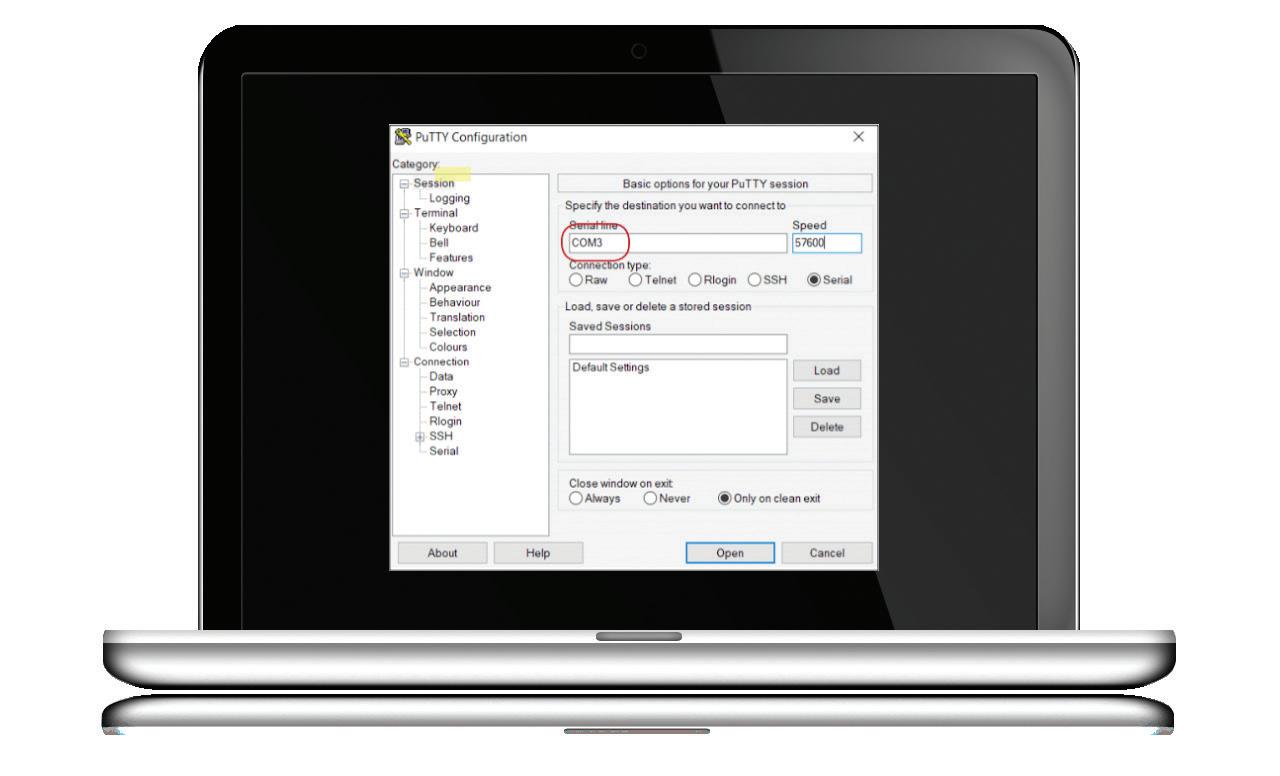
The future of proportional control has arrived— and it’s digital. The Clippard Cordis is a revolutionary microcontroller primed for escape velocity from a proportional control market that has grown stagnant.
