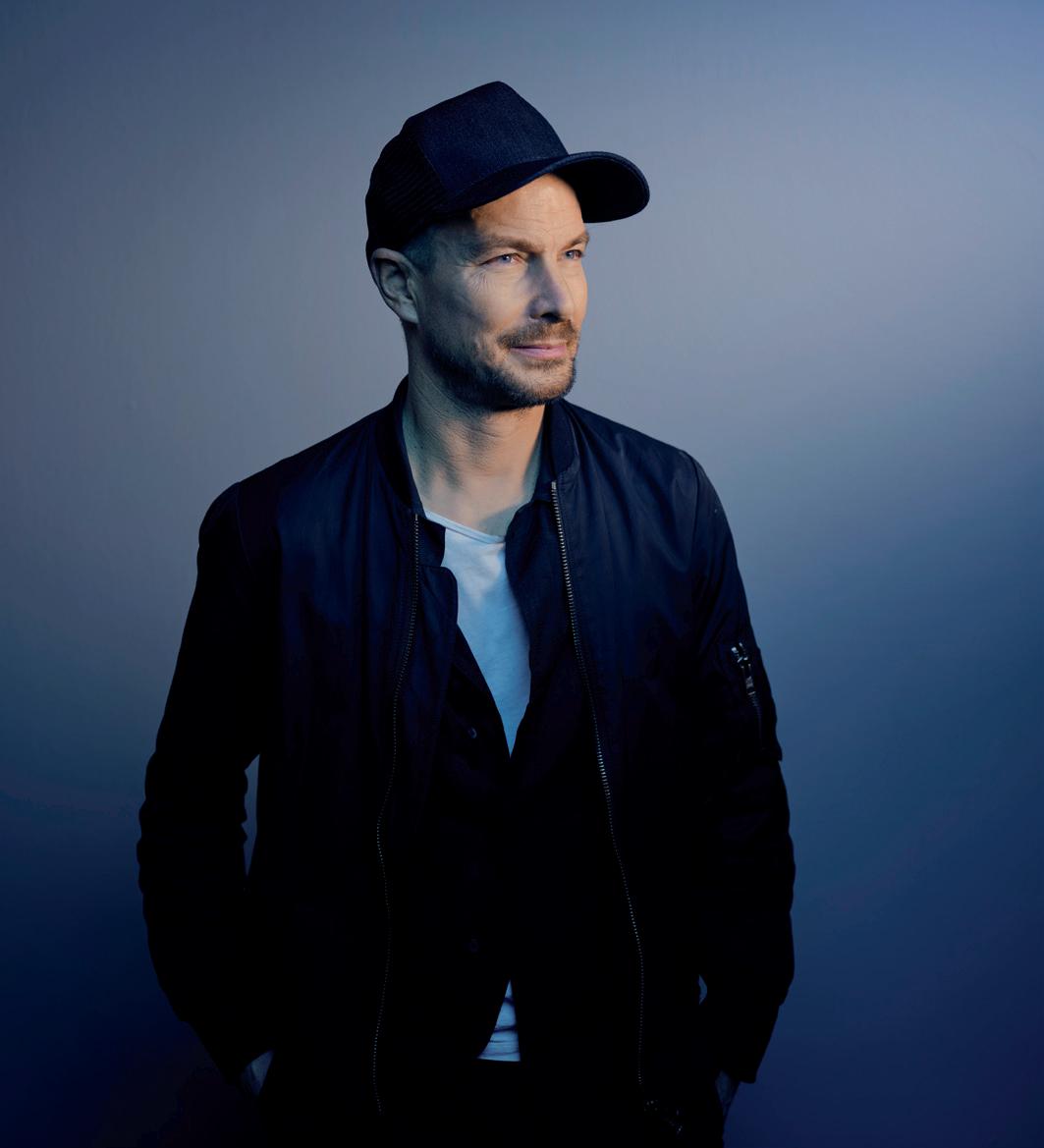
8 minute read
PEOPLE
Photo © Robert Brembeck
INTERVIEW WITH STEFAN DIEZ
text by Francesca Gugliotta
Growing up in a household of 4th-generation carpenters, to the young designers he suggests to start in a workshop, learning about materials and mechanics. He is particularly focussed on the potential of a circular economy to careful use of finite resources, pointing out the importance of repairability and pushing the boundaries to imagine a better sustainable life.
The Munich based designer Stefan Diez, growing up in a household of 4th-generation carpenters, he trained as a cabinetmaker before studying industrial design under Richard Sapper and working with Konstantin Grcic for several years. He is particularly focused on the potential of a circular economy, exploring a broad spectrum of everyday products whose raw materials can be recycled and integrated into a more sustainable material cycle, also pointing out the importance of repairability, a very hot topic, not often addressed by companies. Led by curiosity and supported by a network of local craftsmen and specialists, the designer always pushes the boundaries to imagine a better life, with beautiful objects that solve real problems. To his students says: “Complexity is a great opportunity, and that even difficult problems can be tackled through networked work.”
Growing up in a household of 4th-generation carpenters, to the young designers you suggest to start in a workshop, learning about materials and mechanics.
The sensitive, determined handling of materials plays a decisive role in an experimental search for new solutions. In addition to compute, sketching by hand, it is above all practical trial and error in the workshop that is at the heart of the design process. Especially when questions of use and ergonomics, the manufacturing process and material properties are to be explored.
You are focused on the potential of a circular economy as in Costume sofa for Magis.
Latest since the Paris Agreement on achieving the climate goals, the model of the circular economy has increasingly become the guiding idea for a future economy on our planet. The central idea of the circular economy is the careful use of finite resources: at the end of a product’s life cycle, all components should be completely recycled. The energy required for this should come from renewable resources, which is why the effort involved in recycling remains a major challenge. To achieve this, a sofa must be able to be broken down into its components by the last user without much effort, so that each component finds its way back into the appropriate material cycle. Separation by type is the prerequisite for effective recycling of used materials. Dyes, adhesives, additives, etc. should be avoided. At Costume, we have consistently taken such considerations into account. If now, after more than a year of the pandemic, politicians are thinking about the comeback of the economy, then one has to ask oneself whether we should not rather demand a much more radically forward-looking plan. This is another reason why I am now so clearly advocating the idea of a circular economy.
You point out the repairability, as in Ayno lamp for Midgard the parts can be separated and replaced by the users themselves.
Longevity should always precede recycling, because every recycling process consumes energy and also leaves a residual amount of waste. The integrity of the product should therefore be maintained for as long as possible. This results in some requirements for the design of the products themselves, which we designers can already take into account during the design process. Therefore easy reparability should stand in the focus, alongside flexibility and adaptability to new environments. Thinking about recontextualisation as early as the design stage, so to speak, is an interesting strategy. Just like models where the product is rented instead of bought... we have summarised the most important aspects in ten points on how designers can use their influence in the conception, design and production of products and support the transformation from a linear to a circular economy.
Innovate to imagine a better life, as in the D1 chair where a mechanism allows the natural movements. What does design mean for you?
The question of what good design is has always been a controversial one. When designers mainly worked in dialogue with engineers and were responsible for the formal design of products, one liked to make fun of the narrow-mindedness and one-dimensional thinking of engineers and to label this discipline as a hindrance to ideas. Today, the boundaries have become much blurrier. There are still designers who are mainly concerned with form, but it is just as possible to include areas of product development, construction, sourcing of materials etc. in the remit of industrial design. I believe that an approach based on the collaboration of different experts in loose networks will lead to more radical, fascinating and ultimately better solutions that are capable of overcoming real challenges.
You work with complex software and tools, but with care for the local craftsmanship.
Industry and craft are all the stronger in combination: the Houdini would not be possible without the help of computer-controlled machines. The strength of the collaboration with Arita also lies in the combination of handicraft and industrial processes, which was made possible by the many specialised companies in Arita that worked together on the Arita 2016 project. I’m interested in the potential behind new or newly combined things, not so much in preserving old traditions.
What are you working on right now?
At the moment, for example, we are working on the development of conference tables made of recycled aluminium, which is extracted from post-consumer aluminium with the help of hydroelectric power in Norway. Or a lighting system for Vibia based on conductive belts that can be installed in rooms in an extremely flexible and reusable way. Perhaps our most ambitious project at the moment is the D2 furniture system for Wagner. D2 is not to be sold as a finished piece of furniture, Wagner will only offer the connectors for it and provide assistance with planning. On the one hand, we are developing a fitting made of nylon that connects honeycomb panels made of cardboard or aluminium to each other in a wide variety of constellations; on the other hand, we are working on an infrastructure that will bring local craftsmen, architects and customers into contact with each other. The idea is to optimise transport and storage costs by having D2 produced exclusively locally. But the local craftsmen will later also take over the service and maintenance of the furniture. In the end, a true recycling of the components is to be achieved through the local operations.
Since 2018 you are teach Industrial Design at the University of Applied Arts in Vienna. What do you teach young people?
Since I started teaching design in Karlsruhe in 2008, I have been reflecting much more on my own work and I think that my studio in Munich also benefits from my ongoing involvement with new topics. In general, I try to encourage my students in the understanding that complexity is a great opportunity and that even difficult problems can be tackled through networked work. By making my studio in Munich and our network accessible to the students and by frequently involving external experts and project partners, I try to establish a connection to practice. Apart from that, we have excellent staff in the department: production technology, CAD, workshops from metal to plastic, various joining techniques from sewing to welding, construction technology, formal design, photography and film, etc., that’s what the team brings with it.
Is there a project you would like to do but you haven’t done yet?
There are two topics I would like to work on: mobility in the city and semi-finished products for architecture such as solar thermal elements, electro-voltaic panels, or even just standard elements such as windows, doors or balconies.
1. Ayno lamp by the designer Stefan Diez for Midgards, winner of the German Sustainability Award in design 2021. All the parts can be separated and replaced easily without tools, by the users themselves. The central feature is a fiberglass rod, which is stretched to the bow by the luminaire cable. 2. D2 system for Wagner: “Perhaps our most ambitious project”, says Stefan Diez. “D2 is not to be sold as a finished piece of furniture, Wagner will only offer the connectors for it and provide assistance with planning. The idea is to optimise transport and storage costs by having D2 produced exclusively locally.” 3. Costume for Magis represents a a new sustainable way of constructing upholstered furniture: “A sofa must be able to be broken down into its components by the last user without much effort. Separation by type is the prerequisite for effective recycling of used materials, dyes, adhesives, additives should be avoided.” 4. Plusminus for Vibia, an evolution of the light rail based on a conductive, yet flexible textile belt. Luminaries of different typologies can be freely placed and replaced upon the belt forming extensive compositions of light. The belt could be stretched tightly between walls, ceiling or floor, or hanging loose and crumpled. 5. Houdini chair, a mix of technology and craftsmanship designed for the German brand e15. The chair is inspired by a technique used in aeroplane model making, two-dimensional plywood slabs are stretched by hand around a complexly milled solid wood ring to form the back and another to form part of the seat. 6. D1 chair family by Stefan Diez for Wagner, with a single joint that enables the independent movement of seat, to adapts to the full range of sitting positions. The innovation is condensed into the aluminum encapsulated joint which anchors the tubular steel frame cushioned by rubber buffers below the seat.


2 1
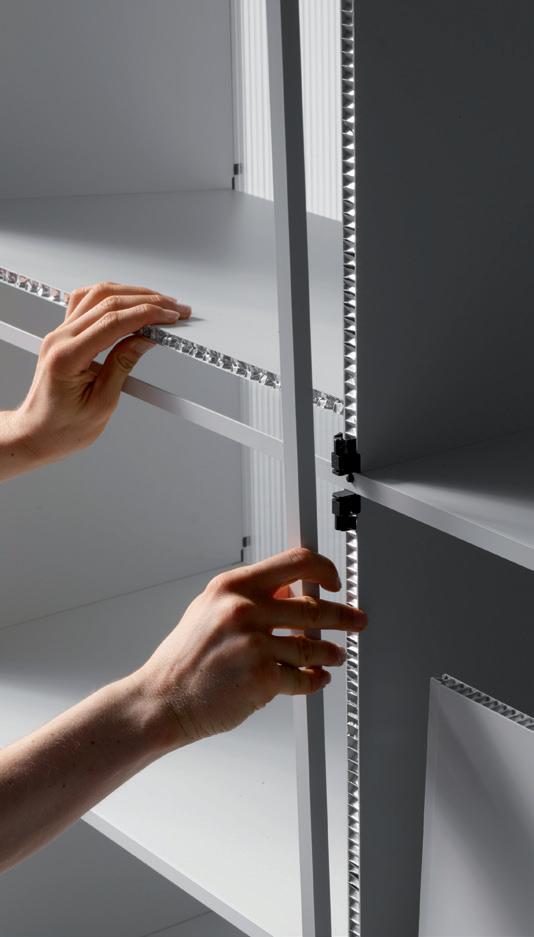
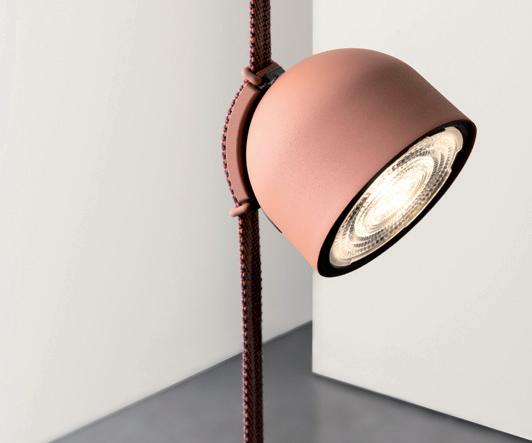
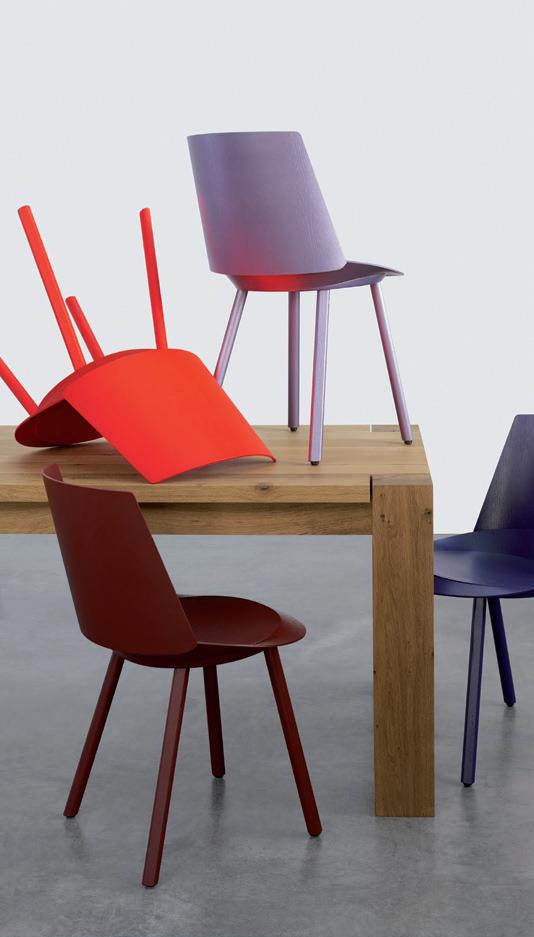
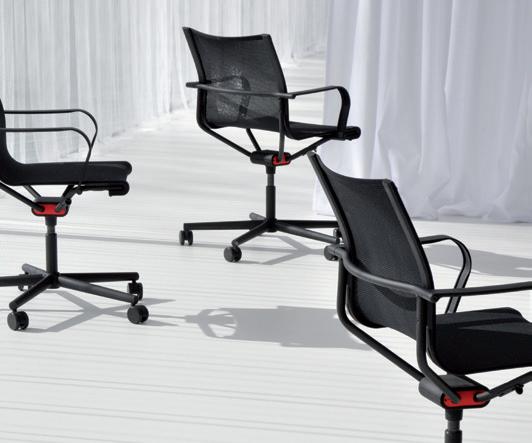
3
4