
11 minute read
STORIA DI COPERTINA
L’INDUSTRIA È SEMPRE PIÙ SMART E SOSTENIBILE
Prosegue l’implementazione di tecnologie digitali avanzate nei diversi stadi della manifattura. Il controllo della produzione con Manufacturing Execution Systems e l’economia circolare trainano la trasformazione.
Che la pandemia abbia accelerato il percorso di trasformazione digitale delle imprese non è un mistero. Che lo abbia fatto anche nell’ambito, ampio e variegato, del manifatturiero non era scontato. Le evidenze emerse nel corso dell’ultima edizione dello Smart Manufacturing Summit, organizzato in formato digitale a maggio da The Innovation Group, confermano che le aziende (con intensità e velocità diverse a seconda soprattutto delle loro dimensioni) hanno “approfittato” della pausa forzata per rivedere processi e piattaforme tecnologiche. In alcuni casi spinte dalla necessità di tutelare i dipendenti (distanziamento, riorganizzazione della forza lavoro), in altre per rispondere a un cambiamento di passo imposto dall’emergenza (pensiamo al settore farmaceutico e parafarmaceutico, ma anche a parte dell’agroalimentare), in altre ancora per soddisfare esigenze di sostenibilità sia economica sia ambientale. Insomma, il filone di progetti legati a Smart Manufacturing, Industry 4.0 – o comunque si voglia chiamare quell’ormai vasto spettro di soluzioni, tecnologie e piattaforme, che vanno dalla sensoristica fino agli analytics, passando per la connet-

tività 5G e l’intelligenza artificiale – continua a stimolare l’inventiva di manager e imprenditori. Anche perché sono sempre di più i casi di successo, molti dei quali sono stati ospitati proprio sul palcoscenico virtuale dello Smart Manufacturing Summit.
Cresce la voglia di digitale
La propensione verso nuovi investimenti in digitale era emersa già da una survey condotta da The Innovation Group, con il supporto di ContactValue, tra febbraio e marzo 2021 su un campione di 111 imprese manifatturiere italiane. Lo scopo dell’indagine era capire a che punto del processo di trasformazione fossero arrivate le industrie nazionali. Dai principali insight della ricerca risulta che l’81% delle aziende manifatturiere ha già in corso qualche iniziativa riconducibile a Industria 4.0, il 59% anche più di un progetto. Un ulteriore 6% è in via di lancio di progettualità, e un 7% è in fase di studio. Solo il 6% delle aziende manifatturiere non ha in questo momento lanciato progetti per la modernizzazione e digitalizzazione delle attività produttive, una minoranza che probabilmente non ha una reale necessità di automazione (o per motivi dimensionali o perché sta affrontando una crisi strutturale che pregiudica la capacità di investimento). Tra le aziende medio-grandi, con oltre 500 addetti , la percentuale di chi ha più iniziative in corso sale all’80%: unsegnale di come in questo campo le economie di scala sia importanti e di come la cultura digitale, un elemento necessario per intraprendere e concludere con successo progetti di Smart Manufacturing, non sia una risorsa attivabile in tempi brevi se non già presente nel tessuto dell’organizzazione. Con riferimento alla gestione dei progetti Industria 4.0, la maggior parte delle aziende ha definito una roadmap e ne monitora i progressi (42% delle risposte), mentre in un terzo dei casi è stata definita una funzione ad hoc, di innovazione digitale, che si occupa in modo precipuo del tema (32%). Per quanto riguarda invece gli ambiti dell’Industria 4.0 che registrano oggi la maggiore adozione, la ricerca ha evidenziato soprattutto tre tipologie di macroprogetti: il sensor/remote monitoring (il monitoraggio da remoto delle macchine tramite sensori), utilizzato nel 56% dei casi e in crescita rispetto al 43% dell’anno scorso; il digital/remote operator (la possibilità di abilitare gli operatori di fabbrica con capacità avanzate, digitalizzazione, visualizzazione avanzata, operatività da remoto), stabile al 40% delle risposte; e il Mes/Erp (Manufacturing execution systems ed Enterprise resource planning, vale a dire i sistemi informatici di fabbrica che governano e controllano l’intero processo produttivo, dal rilascio dell’ordine fino al prodotto finito), con il 44% delle risposte, in ascesa rispetto all’anno scorso. Ambiti innovativi che stanno dimostrando importanti tassi di crescita sono poi i Big Data analytics, algoritmi analitici per estrarre valore da tutti i dati originati dalle macchine della fabbrica; la convergenza nella supply chain, ossia, l’integrazione della logistica e della catena di fornitura con i gestionali della fabbrica; i digital o virtual twin, cioè la possibilità di riprodurre una versione digitale di un oggetto per testarlo prima di metterlo in produzione, per fare simulazioni oppure per mantenere nel tempo tutti i dati che lo riguardano.
Anche la sostenibilità entra in gioco
Le tecnologie digitali non sono solo utili a rendere più efficienti i processi di fabbrica, a controllare meglio produzione e qualità, a rendere più sicuri i luoghi di lavoro. Possono anche aiutare le imprese di ogni dimensione a realizzare progetti facenti capo ai concetti di sostenibilità e di economia circolare: un percorso che può arrivare a generare, come alcuni casi di eccellenza già dimostrano, nuovi modelli di business. Così, soluzioni quali intelligenza artificiale, Big Data, manutenzione e controllo in remoto, cloud, edge computing sono in grado di rivoluzionare lo scenario competitivo di qualsiasi segmento di mercato, e le aziende che le implementano in qualche modo costringono anche le altre ad adeguarsi. Lo smart manufacturing non è quindi solo una questione di ambiente o di etica, ma anche di business, come risulta ormai evidente dalla tante iniziative riprese mediaticamente e volte ad aumentare la percezione e la reputazione dei
brand. Chi investe in questi nuovi modelli, quindi, non solo fa bene all’ambiente e alla propria reputazione, ma può conquistare market share a danni delle aziende che si muovono più lentamente o che non hanno la possibilità di dirottare investimenti in economia circolare. I filoni che contribuiscono ad alimentare questa nuova corsa “verde” sono sostanzialmente tre: l’ottimizzazione dei processi, per diminuire drasticamente i consumi energetici e gli sprechi di materiale; la manutenzione predittiva, per allungare il ciclo di vita dei prodotti; e il tracciamento dei manufatti o perfino dei singoli componenti, per favorirne lo smaltimento e il riciclo. Inoltre, il covid-19 ha indotto molte aziende a rivedere, migliorandole, le condizioni di sicurezza del personale, un tema che non ha una diretta connessione con la sostenibilità ambientale ma che ha invece molto a che vedere con i valori etici. La vera economia circolare – cioè un sistema dove materiali ed energia sono al centro di un processo virtuoso in cui quasi tutto viene condiviso, riutilizzato, riparato e possibilmente rimesso sul mercato – sta spingendo in favore di modelli di business di differente natura, accomunati dal saper estrarre quanto più valore possibile da ogni singola unità di risorse consumate. Come è emerso anche durante lo Smart Manufacturing Summit, questi modelli stanno portando alla nascita di nuovi servizi e di nuove opportunità di business, che possono arrivare, nell’accezione più estrema, alla totale “servitization” non solo delle complesse e costose macchine industriali, ma anche dei diffusissimi prodotti di largo consumo. Un esempio, tra quelli raccontati durante l’evento di The Innovation Group, è quello del Gruppo multinazionale Haier, che grazie alla tecnologia IoT da qualche tempo sta sperimentando di vendere non più lavatrici e lavastoviglie bensì lavaggi, addebitando ai clienti un costo per ogni ciclo di funzionamento delle macchine e controllando in modo efficace ed efficiente i consumi di energia, detersivo e componenti soggette a usura. I servizi, gli aggiornamenti e le parti di ricambio chiamati in gioco in questo tipo di modelli di business provocano la nascita di nuove filiere, nuovi ecosistemi, nuovi mercati e rivoluzionano lo stesso scenario competitivo. Insomma, chi sposerà la vera economia circolare potrà puntare a un’espansione della propria quota di mercato, sia che operi nel mondo dei prodotti consumer, sia in quello delle macchine e dei componenti per l’industria o i servizi.
Emilio Mango
L’IMPORTANZA DI CHIAMARSI “DISTRETTO”
Durante lo “Smart Manufacturing Summit” organizzato da The Innovation Group a maggio, Fabrizio Guelpa, responsabile del servizio Industry and Banking Research della Direzione Centrale Studi e Ricerche di Intesa Sanpaolo, ha disegnato uno scenario dellle imprese italiane, mettendo in evidenza le differenze tra quelle appartenenti a un distretto e quelle “non distrettuali”. Basato sull’analisi dei bilanci di oltre 80mila imprese, il tredicesimo “Rapporto sui distretti industriali” ha messo in luce diversi dati.Il primo è quello previsionale, relativo alla reazione post pandemica: se nel 2019 le aziende distrettuali hanno visto complessivamente un calo del fatturato del 2,9%, invece nel 2020, in pieno lockdown, il valore negativo ha toccato il 12,2%. La stima per 2021, però, è di 11,8 punti percentuali in rialzo, quindi una forte ripresa, che nel dettaglio vede una crescita omogenea per tutti i settori. Si discosta, con una crescita del 5,1%, inferiore alla media, solo il settore agroalimentare, che però è stato tra i meno penalizzati durante la crisi pandemica del 2020. Dotati di alcuni punti di forza che li differenziano dalle altre imprese (maggiori investimenti diretti esteri, marchi registrati a livello internazionale, maggior possibilità di esportazione), i distretti industriali hanno comunque sofferto meno delle imprese non distrettuali e già si distinguevano nel 2019 per i loro investimenti in Ict e meccanica superiori alla media, corrispondenti al 7,1% del fatturato contro il 5,7% delle altre imprese. Questo gap iniziale si è mantenuto nel corso del 2020, quando lo smart working ha visto una diffusione del 23,6% tra le imprese distrettuali contro il 19,8% delle altre. Sempre nel 2020, le soluzioni digitali per i processi produttivi e la logistica sono state adottate dal 30,7% delle imprese distrettuali, mentre nell’altra categoria la percentuale si è limitata al 28,4%. La diffusione delle tecnologie informatiche, anche tra le realtà appartenenti ai distretti, risente però di una grande difformità in relazione alle dimensioni aziendali, visto che tra le micro-imprese la digitalizzazione dei processi produttivi non raggiunge il 20% (si ferma al 19,6%) per superare invece il 45% tra quelle di medie dimensioni. A metà strada, le piccole hanno raggiunto il 32%. Tra i più importanti fattori di crescita e competitività delle imprese distrettuali per il 2021, la Direzione Studi e Ricerche di Intesa Sanpaolo ha individuato l’appartenenza alle filiere di prossimità e la maggior fiducia da parte dei grandi gruppi nei rapporti strategici di fornitura.
E.M.
IMMAGINARE È PROGETTARE
Innovazione e immaginazione sono le parole d’ordine per Dassault Systèmes, che nel corso del suo evento mondiale in streaming lo scorso febbraio ha portato sul palco decine di testimonianze di come la sua 3DExperience Platform lasci spazio alla creatività, tanto da avere tra i principali ospiti clienti come Disney. “La modalità di sviluppo tradizionale ha evidenziato i suoi limiti” ha detto Bernard Charlès, vice presidente e Ceo di Dassault Systèmes, “non può più essere confinata alla singola tecnologia di progettazione. Gli utenti devono poter lavorare in una logica di piattaforma e poter sfruttare i vantaggi della terza dimensione, un fattore che consente a tutti gli innovatori nel mondo di godere di un’esperienza più inclusiva e preziosa”. La 3DExperience Platform si basa sulla soluzione Solidworks, che copre diversi processi del ciclo di progettazione e produzione: design 3D, simulazione, gestione dei dati e produzione. Che non si parli più di prodotto ma di piattaforma lo testimoniano anche le recenti esperienze dei clienti Solidworks, i quali sfruttano l’ambiente tridimensionale per creare virtual twin che, a quanto pare, iniziano a diventare un elemento di valore anche per i clienti finali. Le nuove soluzioni 3DExperience Solidworks for Students (destinata agli studenti) e 3DExperience Solidworks for Makers (per i creativi) consentono a un pubblico ancora più vasto l’accesso in cloud per la progettazione, l’ingegneria e la collaborazione innovativa.
SAAS E IOT TRAINANO IL SOFTWARE
Le applicazioni “as a service” e il crescente interesse per l’Internet of Things stanno cambiando la fisionomia dei vendor del settore. La testimonianza di Ptc.
Ptc sta sempre più virando verso le soluzioni “a servizio”, erogate tramite cloud, cioè verso il Software-as-a-Service (SaaS). La multinazionale ha creato appositamente una business unit dedicata a questo mondo e, grazie alle piattaforme e alle competenze maturate con l’acquisizione di Onshape, sta accelerando nella strutturazione dell’offerta in modalità Software-as-a-Service. Il primo prodotto a essere proposto in SaaS, dopo Onshape, è stato Vuforia, mentre in futuro sono previste la migrazione di Windchill e successivamente quella di Creo. In tutti questi casi non si tratta però di un semplice spostamento delle soluzioni sulla nuvola, bensì i prodotti vengono riscritti per essere cloud-nativi. “Utilizzare soluzioni SaaS permette alle im-
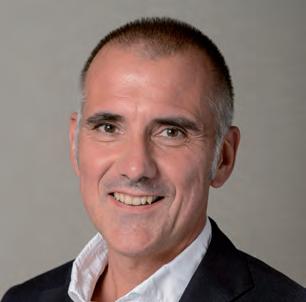
Paolo Delnevo, vice presidente di Ptc
prese di superare i limiti dei sistemi onpremise”, ha detto Paolo Delnevo, vice presidente di Ptc e general manager per l’Italia, “ottenendo maggiori benefici, primo tra tutti la possibilità di fruire delle soluzioni senza doverle acquistare, mantenere e aggiornare”. Nella proposizione SaaS, infatti, tutte queste attività, costose in termini economici e di risorse umane, vengono gestite dal fornitore del servizio. Ma i vantaggi non si esauriscono qui, poiché viene anche incrementato il livello di sicurezza dei dati e degli accessi e si può usufruire di una maggiore scalabilità delle piattaforme. “Tutto questo si traduce in un minore cost of ownership”, ha proseguito Delnevo, “con la capacità di poter permettere l’accesso a soluzioni enterprise anche a realtà più piccole”. Tra gli utenti più convinti di questo tipo di soluzioni c’è Riccardo Gatti, docente del Politecnico di Milano, che ha adottato la piattaforma Onshape come strumento per gli studenti del Master in Industrial Design Engineering and Innovation. In questo modo gli utenti possono collegarsi da qualunque luogo del mondo, raggirando così i limiti dei lockdown conseguenti alla pandemia. Altro importante fattore di cambiamento negli ultimi mesi è stata la crescita della domanda di soluzioni Internet of Things (IoT). “Nell’ultimo anno”, ha commentato Delnevo, “le vendite riconducibili a progetti IoT sono aumentate del 180% in Italia e nulla fa pensare a un’inversione di tendenza”.
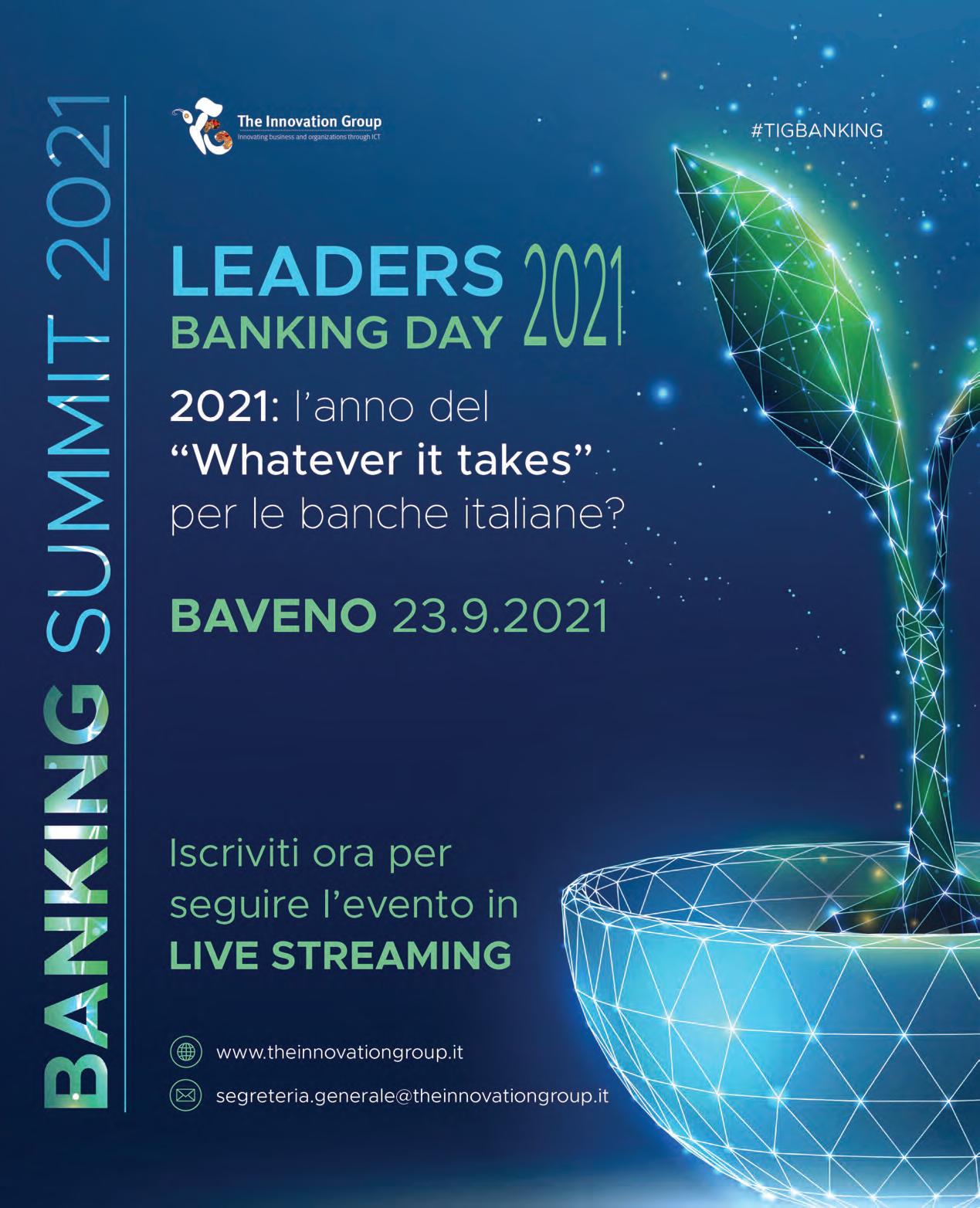