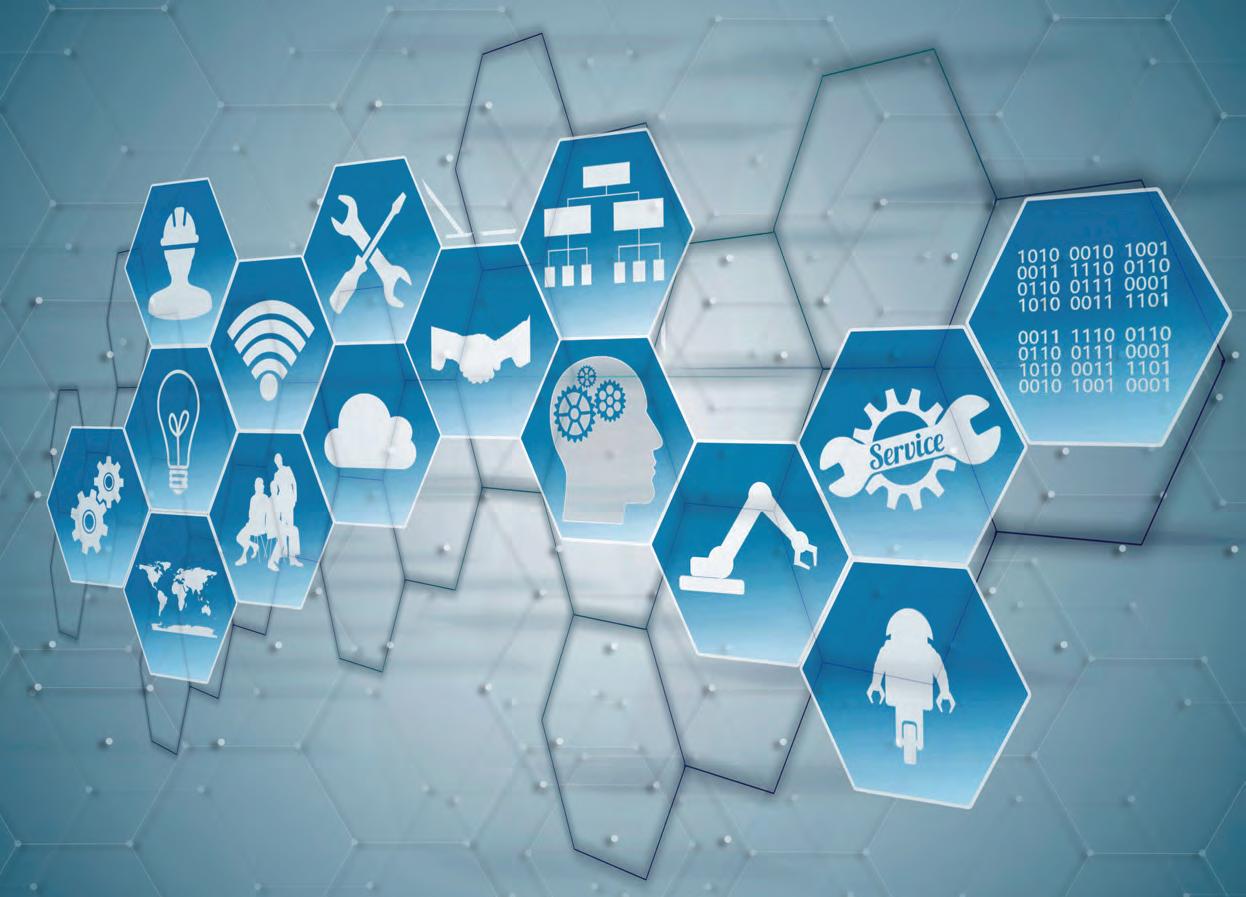
21 minute read
STORIA DI COPERTINA
LA GRANDE OCCASIONE ANCORA DA COGLIERE
Un comparto manifatturiero in salute come, oggi, quello italiano è ancora relativamente poco maturo nell’adozione delle tecnologie 4.0.
Acinque anni di distanza dall’introduzione di quello che originariamente venne chiamato Piano Industria 4.0, o più popolarmente Piano Calenda, dal nome dell’allora ministro dello sviluppo economico del governo Gentiloni, il bilancio che si può trarre da ciò che è stato messo in campo a più riprese per sostenere la transizione digitale delle nostre imprese è senz’altro positivo. Con alcuni distinguo, ma positivo. E questo per almeno tre ragioni. La prima è legata al boost che il comparto manifatturiero nel suo complesso ha sperimentato, innanzitutto quello dei costruttori di macchine e impianti, con una ricaduta positiva non solo in termini di occupazione e generazione di PIL a livello nazionale, ma anche di
bilancia commerciale. Vale infatti la pena di sottolineare come nel mondo l’Italia sia uno dei principali esportatori di macchinari e tecnologie per produrre, con alcuni settori di assoluta eccellenza e leadership globale, come quelli delle macchine utensili e dei robot o sistemi di confezionamento e imballaggio. Con oltre 200mila occupati diretti e una quota di PIL generato del 2,5% (fonte Federmacchine), ben si comprende come la salute di questo comparto sia lo specchio di quella del nostro sistema economico nazionale. La seconda ragione di ottimismo è legata alla formazione di coscienza che, grazie al dibattito e alla grande comunicazione sviluppatisi attorno ai temi della digitalizzazione, ha portato molti imprenditori e manager, soprattutto in aziende appartenenti alla fascia delle imprese piccole e medio-piccole, a guardare al digitale non come a una moda, ma quale concreta necessità a cui ricorrere per mantenere e anzi aumentare l’efficienza in ottica di competitività futura. La terza ragione, se così vogliamo dire, può essere considerata la somma delle due. Sappiamo che il parco impiantistico installato in Italia è piuttosto vetusto. Significativa fu l’indagine condotta nel 2015 da Ucimu-Sistemi Per Produrre, in collaborazione con il Ministero degli Affari Esteri, l’Ice e Unioncamere, che mise in luce per il parco delle macchine utensili installate in Italia un’età media di 13-14 anni. Una età a mio giudizio, e per mio sentore derivato da esperienze dirette sul campo, del tutto sottostimata se si considera il totale degli impianti, macchinari e sistemi per produrre installati tout court nell’industria italiana. Ebbene, è stato anche grazie a queste misure – magari utilizzate anche a solo scopo speculativo economico – che molte imprese hanno potuto compiere investimenti in beni sia materiali sia immateriali, investimenti che altrimenti non avrebbero potuto permettersi.
Quanto vale l’industria 4.0 italiana
Stimare un valore del mercato nazionale dell’industria 4.0 è difficile, quasi impossibile. In molti ci hanno provato e tanti numeri sono stati rilasciati. Secondo il Mise, solamente nel primo anno di entrata in vigore del Piano, ovvero nel 2017, quando ancora si parlava di iper ammortamento, gli incentivi si sono concretizzati in 13,3 miliardi di euro di investimenti tra macchinari e software. Una cifra del tutto realistica, anche perché elaborata sui dati raccolti dai modelli dichiarativi reddituali in cui all’epoca vigeva l’obbligo di indicazione. Secondo l’Osservatorio Transizione Industria 4.0 della School of Management del Politecnico di Milano, nel 2021 il mercato nazionale del 4.0 avrebbe sfondato la quota dei 4 miliardi di euro (4,1 per l’esattezza), trainato per l’85% dalle tecnologie IT (3,5 miliardi di euro), contro un 15% appannaggio delle tecnologie OT (0,6 miliardi di euro). Cifra quest’ultima, se mi è permesso, poco plausibile rispetto a quella del software, che appare invece realistica considerando che il mercato delle soluzioni software e Ict italiano si aggira su un valore superiore ai 7 miliardi di euro. Al contrario, se solo si guardano i numeri del comparto rappresentato da Federmacchine, la federazione delle associazioni nazionali dei costruttori di macchine e beni strumentali, gli 0,6 miliardi di euro appaiono una bazzecola. Il consegnato interno nel 2020 è stato infatti pari a 13,6 miliardi di euro, dei quali, a esser cauti, non si sbaglia di certo a dire che almeno il 50% sia stato fornito in “versione 4.0”. E poi va considerato l’indotto economico generato dai fornitori delle tecnologie di automazione digitale: sistemi di controllo, apparati di comunicazione, sensoristica evoluta, eccetera. Un mercato che, secondo le previsioni di Anie Assoautomazione (che tuttavia ancora non ha rilasciato i dati ufficiali), nel 2021 dovrebbe aver registrato un giro d’affari complessivo di circa 5,4 miliardi di euro, di cui cautelativamente si potrebbe stimare un 25-30% dedicato al mercato dei costruttori di macchine 4.0.
Diversi livelli di maturità
Se da un lato è praticamente impossibile riuscire a inquadrare compiutamente dal punto di vista economico il mercato delle tecnologie 4.0, per le evidenti difficoltà di raccolta, analisi e consolidamento dei dati, dall’altro le indagini qualitative sul livello di maturità e di adozione nelle fabbriche italiane restituiscono, invece, dei dati particolarmente significativi. Come quelli che emergono dalla survey realizzata da The Innovation Group insieme a ContactValue, i cui risultati sono stati presentati nel corso dello “Smart Manufacturing Summit 2022”, la terza edizione, tornata in presenza, del più importante evento convegnistico nazionale in tema di innovazione digitale per l’industria manifatturiera. Come sottolineato in apertura di articolo, sebbene gli aspetti positivi legati al cammino di transizione digitale intrapreso dall’industria siano molti, non mancano alcuni distinguo: e questa survey li ha messi in luce. A parte le grandi imprese – che certamente già da tempo, ben consce delle potenzialità del modello 4.0, avevano trovato naturale implementare modelli organizzativi smart e digitali – nella maggioranza degli altri casi le aziende del settore manifatturiero sono ancora relegate in una fase di sviluppo e di prima implementazione delle tecnologie 4.0 al proprio interno. Non che
Foto di Gerd Altmann da Pixabay
delle tecnologie smart le imprese non ne vogliano sapere, anzi. È infatti solamente l’11% del campione ad affermare di non usufruirne (per ora, aggiungo). Ciò che emerge è piuttosto un ritardo generale nell’adozione, tant’è che il 40% degli intervistati dichiara di essere attualmente in una “fase pilota”: uno stadio importantissimo per il successivo deployment dei progetti 4.0, ma la cui collocazione ad oggi (a cinque anni dall’introduzione degli incentivi governativi e a ben undici anni dal conio ufficiale del termine “4.0”, avvenuto alla Industrie Messe di Hannover nel 2011) evidenzia un ritardo diffuso.
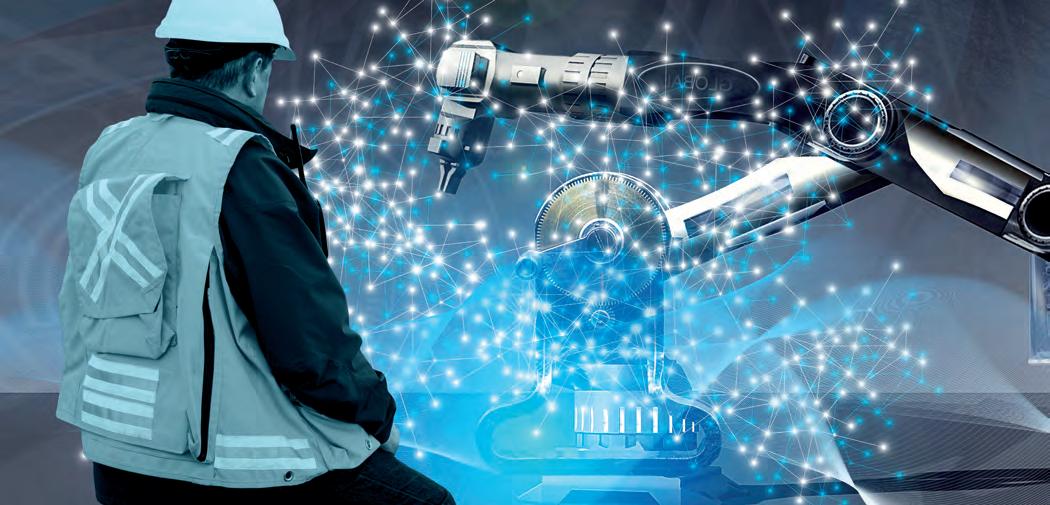
LAVORI IN CORSO NELL’INDUSTRIA ITALIANA
Solo un’impresa manifatturiera su quattro in Italia ha già completato la trasformazione in “industria 4.0”. La ricerca “Smart Manufactuing Survey” di The Innovation Group (condotta tra febbrario e marzo 2022 su un campione di 55 realtà industriali italiane) ha evidenziato che solo nel 25% dei casi gli strumenti di manifattura smart sono usati a piene mani, mentre il 40% delle aziende ha avviato progetti pilota e il 21% è in una fase di roll out. Lo scenario tuttavia potrebbe maturare in tempi abbastanza rapidi, visti i molti lavori in corso e il fatto che il 36% delle aziende abbia definito, se non altro, una roadmap di trasformazione 4.0. Gli ambiti più promettenti sono il monitoraggio remoto e la sensoristica (interessano il 45% del campione), l’Internet of Things industriale (43%), le tecnologie per la convergenza della supply chain (33%) e la stampa 3D. Le motivazioni che spingono le imprese verso il 4.0 sono soprattutto l’ottimizzazione dei processi produttivi (74%), la disponibilità di incentivi e politiche governative a favore (32%) e la volontà di offrire un miglior servizio ai propri clienti (30%).
Il ruolo dei partner IT
Un’ultima nota relativa ai risultati emersi dalla survey riguarda il ruolo svolto dai partner IT nei confronti delle imprese manifatturiere italiane. Se, da un lato, il mondo dell’industria riconosce ai propri partner IT attenzione verso le esigenze manifestate e conoscenza delle dinamiche settoriali, dall’altro emerge il tema dei costi e, soprattutto, quello dei ritardi, segnalato dalla pressoché totalità del campione d’indagine. È un tema, questo, che meriterebbe un approfondimento a parte, che in questa sede non è possibile fare, ma che sta a significare molto: innanzitutto la distanza che ancora, nonostante i grandi passi compiuti, separa il mondo OT da quello IT quando si tratta di raccogliere e integrare la babele dei dati generati dal campo negli ambienti software di più alto livello.
Alberto Taddei, consulente Industry 4.0 e senior partner di ContactValue
DAL “GRANDE RESET” (MANCATO) AL NUOVO PARADIGMA
Dopo due anni di pandemia, la situazione geopolitica e le conseguenti incertezze economiche hanno disatteso le aspettative di “nuovo inizio” per il settore manifatturiero.
Avrebbe dovuto essere il “grande reset” dell’industria manifatturiera italiana, un’industria che in Europa è seconda solo alla Germania e per la quale lo shock della pandemia avrebbe potuto coincidere con un momento di rilancio. I due anni di pandemia per molti segmenti del manifatturiero (ci sono eccezioni, pensiamo al farmaceutico e ad alcuni comparti dell’alimentare) hanno rappresentato, da una parte, una specie di “tempo sospeso”, tra interruzioni della produzione causate dai lockdown e scarsità della domanda per il crollo delle vendite di molti prodotti; dall’altra, sono stati un momento di relativa tranquillità per pianificare investimenti e ammodernamenti. Non è un mistero, ne hanno parlato anche i principali media nazionali, che gli imprenditori e i manager illuminati abbiano approfittato di questa pausa di riflessione proprio per accelerare la trasformazione digitale nell’ottica delle fabbriche smart, investendo di più invece che tirando i remi in barca. L’obiettivo era farsi trovare pronti alla fine della pandemia (che per la verità non ci ha ancora definitivamente lasciati) con aziende e filiere ancora più competitive e “veloci” di prima. Come noto, purtroppo a febbraio lo scenario – che nel frattempo aveva visto un incremento dei costi energetici solo in parte giustificato dalle condizioni macroeconomiche – è imprevedibilmente cambiato di nuovo, trascinando molte economie europee e mondiali in una vera e propria condizione di guerra,

Foto di Christopher Burns da Unsplash
riflesso del conflitto armato in Ucraina. Così l’energia, le materie prime dell’industria delle lavorazioni meccaniche e anche quelle dell’industria alimentare hanno subìto un’ulteriore riduzione delle disponibilità, inaugurando un probabilmente lungo periodo di scarsità che gli imprenditori del manifatturiero ora devono affrontare. A questo si somma l’effetto psicologico sui mercati, tutti i mercati a parte l’industria bellica, di clienti e consumatori spaventati dal rischio di un allargamento del conflitto. La nuova scarsità farà emergere nuove opportunità? Se la possibilità concreta che vengano bloccate completamente le importazioni di gas dalla Russia causerebbe il fermo di molte imprese, oggi il rincaro dei costi energetici sta già provocando interruzioni a singhiozzo della produzione, che in alcuni casi risulta ormai antieconomica. Come sottolineato da Carlo Alberto Carnevale Maffè, professore associato di Strategia e imprenditoria della Sda Bocconi School of Management, “Siamo entrati nell’epoca delle nuove scarsità: di materie prime, di energia e di capitale umano. Un’epoca in cui è facile che la domanda superi l’offerta, e che quindi le imprese manifatturiere debbano affrontare uno scenario completamente diverso da quello pre pandemia”. “È un momento in cui più che la resilienza conta l’antifragilità”, gli fa eco Michele Mariella, chief information officer di Maire Tecnimont, “e in cui le imprese devono imparare a guidare il caos, non potendo più evitarlo e resistergli”. “Ma spesso le turbolenze e le incertezze creano opportunità”, aggiunge Marco Taisch, professore di Digital Manufacturing alla School of Management del Politecnico di Milano, “e il ridisegno delle fabbriche, il maufacturing-as-aservice, l’industrial smart working, la sostenibilità e la creazione rapida di nuove competenze potrebbero ovviare alla grande e probabilmente strutturale incertezza dei nuovi scenari, provocata dalla fine della globalizzazione e dall’ingresso delle variabili geopolitiche nell’industria”.
Emilio Mango
VERSO IL GREEN
CON EFFICIENZA, DATI E INTEGRAZIONE
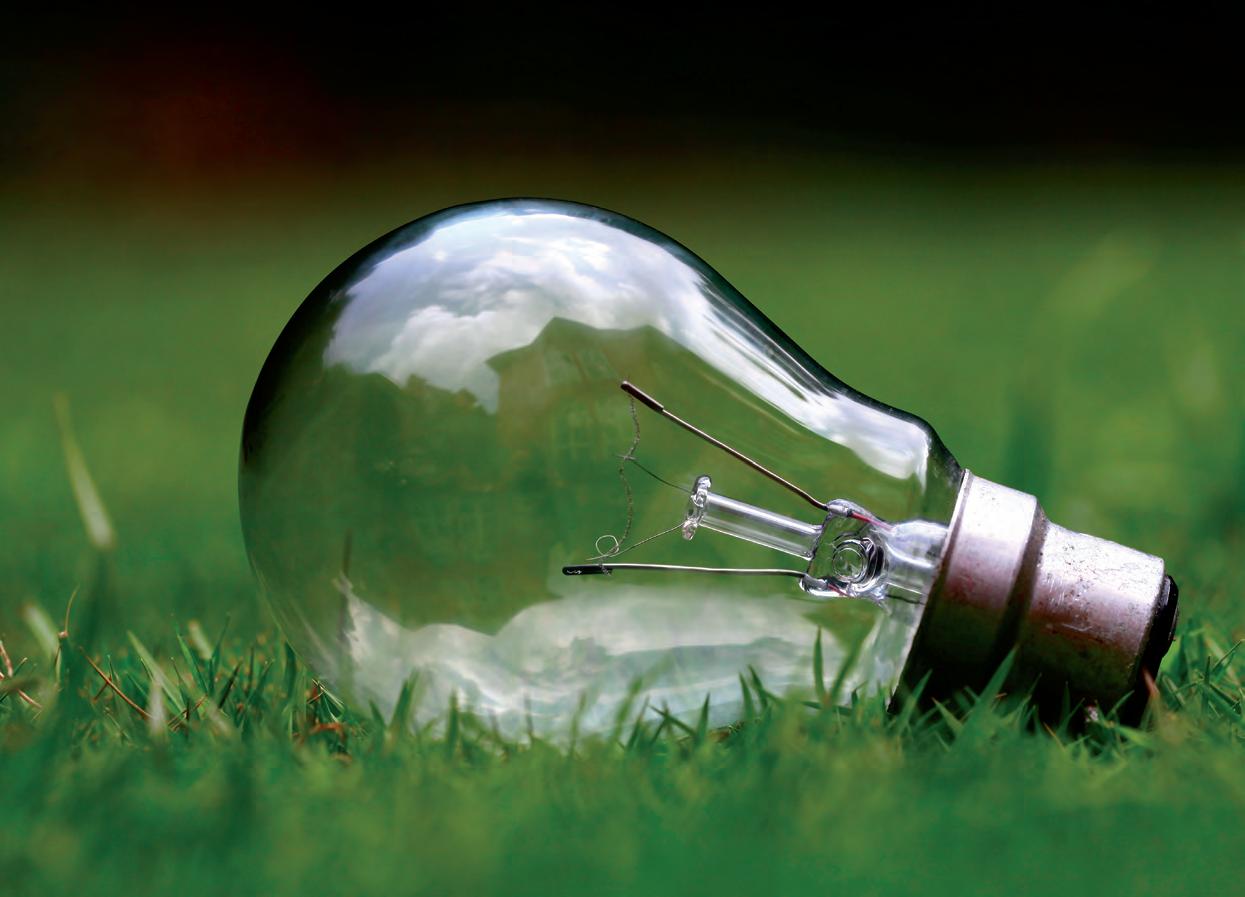
Il software può fare da collante tra sistemi Scada, Mes, tecnologia OT e Internet of Things. Ed è una componente indispensabile della transizione ecologica.
Come sarà l’industria del futuro? Raccogliendo dati dai sistemi OT, Scada e Manufacturing Execution System (Mes), dagli oggetti Internet of Things e dal cloud, sarà possibile alimentare applicazioni di analytics di finalità varie, dall’ottimizzazione energetica alla manutenzione predittiva. Il risparmio di tempo e soldi, e dunque l’incremento dei guadagni, non potrà essere, però, l’unico grande obiettivo. Per poter remare a favore della transizione ecologica e degli obiettivi dell’Agenda 2030, l’industria dovrà avere tre caratteristiche: essere sostenibile, digitale e universale. “Possiamo stimare che oggi la temperatura media si sia innalzata di circa un grado rispetto alla temperatura media del periodo pre industriale”,
spiega Giancarlo Terzi, vicepresidente della divisione Field Services di Schneider Electric Italia. “La scienza ci dice che il valore massimo di incremento che il pianeta potrebbe tollerare è di 1,5 gradi. Ma continuando sulla strada attuale la temperatura media salirebbe di tre gradi da qui a fine secolo”.
Le rinnovabili da sole non bastano
Dal 1990 a oggi le emissioni globali di diossido di carbonio sono aumentate del 50% circa. Il surriscaldamento ha provocato in poco più di un secolo, tra inizio Novecento e l’anno 2010, un innalzamento di 19 centimentri nel livello globale medio dei mari. Naturalmente l’industria – insieme al settore energetico, all’allevamento, ai trasporti e ai comportamenti individuali – è parte del problema ma è anche un irrinunciabile motore di occupazione e di ricchezza in un mondo sovrappopolato. Come ben sappiamo, e come evidenziato dagli obiettivi dell’Agenda 2030 e del summit Cop26, la sfida del taglio delle emissioni di gas serra è affrontabile in parte con la transizione dal carbone alle fonti rinnovabili, quali l’idroelettrico, il fotovoltaico e l’eolico. Ma la restante parte dipende dall’efficientamento energetico. Qui le innovazioni hardware (come i processori che riducono l’impegno energetico di computer e server) hanno sicuramente un ruolo, ma non va sottovalutata l’opera dei software e in particolare di quelli che raccolgono e analizzano dati. “Si stima che da qui al 2030 il consumo di energia elettrica aumenterà del 50%, sarà una volta e mezzo quella attuale”, ha proseguito Terzi, spiegando che per poter sostenere l’aumento della domanda si dovrà agire su più fronti, sul green field dei nuovi edifici e dei nuovi impianti, ma anche sul brown field di quelli esistenti, “che dovremo rinnovare, digitalizzare, rendere più efficienti, basati su elettricità e su sistemi di accumulo dell’energia”, ha spiegato il manager di Schneider Electric. “Abbiamo bisogno di software per gestire, mantenere e accudire tutto il lifecycle di questi edifici per far sì che conservino la massima efficienza”. Questo è vero già oggi, ma sempre di più lo sarà in futuro, perché il maggior utilizzo di elettricità renderà le reti smart grid sempre più complesse e ci sarà bisogno di software per gestire tale complessità. E ancora, i software di analytics saranno preziosi per gestire al meglio le attività di riciclo, di riuso energetico, di recupero delle emissioni di gas serra. Negli impianti industriali, il software entra in gioco nella gestione della produzione, nel monitoraggio energetico, nell’automazione degli edifici e anche nella gestione dei data center. “Raccogliamo sempre più dati”, ha sottolineato Terzi, “e abbiamo bisogno di software che ci aiutino a comprenderli e a capire come ottenere efficientamento e altre ottimizzazioni. Inoltre anche i servizi dovranno evolvere. Dobbiamo essere certi di mantenere l’efficienza lungo tutto il ciclo di vita degli impianti, anche riuscendo a prevedere i guasti”.
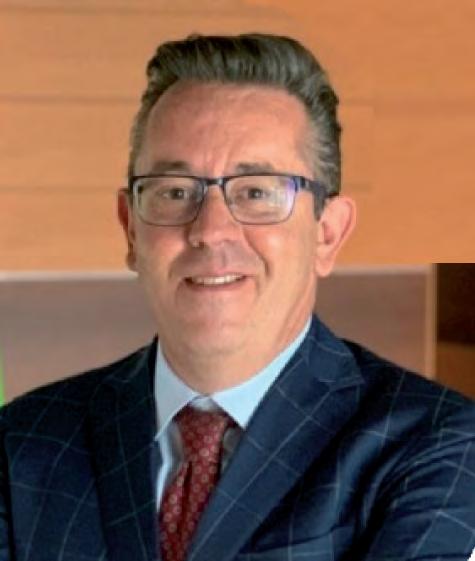
La sfida dell’automazione
All’interno di questa visione su un futuro più sostenibile e fondato sui dati, Schneider Electric ha sviluppato una strategia di offerta che l’azienda chiama “automazione universale”. “In futuro l’automazione sarà molto diversa da quella attuale”, ha illustrato Claudio Giulianetti, vice president industrial automation di Schneider Electric Italia. “Sarà integrata e interoperabile, e consentirà una migliore messa in produzione di macchine e impianti. Altro elemento importante della nostra visione è il software, che sarà sempre più aperto e agnostico, cioè non vincolato all’hardware su cui viene eseguito”. L’aspetto dell’apertura è particolarmente importante in ambito industriale, dove esistono tecnologie operative (Operational Technology, OT) e informatiche (IT) che devono poter lavorare in modo integrato. “Nell’industria difficilmente si riesce a portare un software di automazione da un sistema all’altro”, ha rimarcato Marco Gamba, innovation & communication industry leader di Schneider Electric Italia. “C’è molta chiusura e c’è pochissima flessibilità. Con l’automazione universale proponiamo che i dispositivi abbiano un’anima comune. Bisogna svincolare il software applicativo dall’hardware, così da permettere la portabilità”. Le aziende come Schneider Electric e i loro clienti dell’industria non dovranno poi trascurare un altro aspetto, riassunto nell’espressione lifecycle management. “Come industria”, sottolinea Giulianetti, “dovremo essere capaci di gestire l’intero ciclo di vita di asset, di linee produttive e di impianti efficientando il processo, anche con l’automazione, senza trascurare il fine vita di un processo produttivo e dunque il problema dello smaltimento”.
Valentina Bernocco
Giancarlo Terzi
L’IMPRESA INTELLIGENTE SPINTA DA ALTEA UP
Nata nel mondo Sap, l’azienda di Altea Federation si propone di accompagnare i clienti nel viaggio verso il concetto di intelligent enterprise. Dal manufacturing, è partito un processo di espansione verso altri settori.
Altea Federation può essere vista come una sorta di matrioska tecnologica. Nata nel 1993 come società di consulenza, la realtà si è evoluta nel tempo e oggi ha costituito una galassia di ben 20 aziende riunite sotto un modello definito “olonico-virtuale”, per accompagnare i clienti in un percorso di trasformazione dove competenze umane e supporti tecnologici diventano complemento unico di un’evoluzione destinata a coinvolgere allo stesso tempo business e persone. Dentro questo involucro si colloca Altea UP, system integrator focalizzato nel mondo delle tecnologie Sap, che a propria volta è formato da diverse realtà. Fra queste, AdHocLogica Consulting è una società che da sola fattura 5 milioni di euro (la Federation supera i 130 milioni) e si occupa di fornire capacity e competenze nel controllo di gestione e della produzione. Run Time Solutions, invece, segue essenzialmente le piccole aziende nell’implementazione dell’Erp Sap Business One. L’ultima creatura integrata nel piccolo conglomerato si chiama LuxryUp, deriva dall’acquisizione di Pl Consulting e rappresenta per Altea UP il consolidamento della propria presenza nel mercato del fashion e del lusso. La focalizzazione sul mondo Sap fa sì che la proposizione al mercato segua quella del player di riferimento e, quindi, sia oggi concentrata sull’implementazione di tutto ciò che si può racchiudere nel concetto di intelligent enterprise. “Siamo nati, inevitabilmente, nell’Erp, ma abbiamo seguito il nostro vendor di riferimento nella sua espansione verso Crm, analytics, customer experience e così via”, illustra Roberto Gemma, Ceo di Altea UP. “Oggi siamo fra i partner italiani più importanti e Sap può essere considerata un prolungamento della nostra organizzazione”. La società ha sviluppato una presenza piuttosto consolidata nel campo del manufacturing, oltre che del pharma & chemical, dell’engineering & construction, del retail, del food e dell’automotive. “Si tratta di un comparto fondamentale per l’economia del Paese, essendo l’Italia al secondo posto in Europa e potendo migliorare ancora se solo si riuscisse a muoversi come un sistema, anziché continuare a farci concorrenza interna”, evidenzia Gemma. “Noi lavoriamo per offrire strumenti che, sistematizzando la gigantesca quantità di dati a disposizione, consentono di accelerare i processi decisionali e mitigare l’incertezza che in questo periodo investe diversi ambiti, dalla disponibilità delle materie prime alla Roberto Gemma

pianificazione degli stock, fino al reperimento di risorse specializzate”. Una peculiarità di Altea UP riguarda l’approccio basato sul concetto di partnership con il cliente, anteposto alla pura proposizione tecnologica. Lo dimostra la messa a punto di ValueUP Journey, un servizio di business transformation advisory, destinato più che altro ai C-level aziendali, che serve a delineare una roadmap condivisa, basata sulla circolazione delle informazioni. ll servizio intende unire i vari elementi operativi delle aziende, per coordinare un processo evolutivo strutturato verso l’intelligent enterprise. Fra le concretizzazioni di questo approccio troviamo per esempio il progetto IeS Factory (l’acronimo sta per Intelligente e Sostenibile) attivato in collaborazione con Regione Puglia e Università del Salento, per la creazione di un “experience center”. Qui, l’esposizione di esempi di linee produttive concepite secondo la logica 4.0, l’utilizzo di visori per la realtà aumentata dedicati all’asset management ed esempi di digital boardroom per gestire i board meeting fungono da tracce per far capire anche ai top executive quali siano i concreti effetti della trasformazione digitale. In chiave più verticale, invece, Intelligent Pharma è una soluzione che integra attività di produzione, qualità e logistica, alla quale si è aggiunta di recente la tecnologia di Robot Process Automation per la convalida dei processi propedeutici alla distribuzione dei prodotti ai centri che poi rivendono alla farmacie.
UN PONTE TESO FRA INDUSTRIA E CLOUD
Il system integrator, partner consolidato di Microsoft, fa leva sulle attuali esigenze del mondo del lavoro per sostenere i processi di trasformazione nel manifatturiero.
Il percorso verso la trasformazione digitale riguarda tutti i tipi di azienda, a prescindere dalle dimensioni o dal settore di appartenenza. Naturalmente esistono peculiarità delle quali occorre tener conto, ma uno degli elementi comuni a tutti è certamente poter contare sul supporto di un cloud “intelligente” per ripensare la creazione di valore. Anche i player che vogliano aiutare e indirizzare le strategie dei propri clienti su questo fronte devono adattarsi. Lo ha capito per tempo Alterna, parte integrante di Altea Federation e specializzata nelle tecnologie del mondo Microsoft. “Siamo nati nel 2013, sviluppando competenze a partire dall’Erp, ma sei anni fa abbiamo abbracciato senza riserve il cambiamento ispirato dall’arrivo in Microsoft di Satya Nadella”, ricorda Matteo Giovanditti, Ceo di Alterna. “Oggi abbiamo accesso a un universo molto vasto di soluzioni e sappiamo come mettere a terra anche le tecnologie più sperimentali proposte dal nostro vendor di riferimento”. Fra i comparti meglio coperti dal cloud system integrator rientra il manufacturing, nel quale l’innovazione spesso già intrapresa nel campo delle applicazioni di business deve sposarsi con l’ambito della produzione, dove invece permangono spesso abitudini e modalità di lavoro ben radicate nel tempo. La società ha approcciato il comparto per supportare percorsi graduali di transizione che partissero dalle componenti più operative delle industrie. “La tecnologia è ormai connaturata alle macchine che queste aziende utilizzano e da lì siamo partiti per lavorare su un’innovazione che preservasse e potenziasse la continuità operativa”, racconta Giovanditti. “Creare la possibilità di monitorare le macchine grazie all’IoT, trasferire le informazioni e rielaborarle con l’intelligenza artificiale, consentendo ai clienti di poter intervenire per tempo per non ritrovarsi a dover gestire situazioni inaspettate, sono solo esempi di come siamo in grado di supportare le imprese manifatturiere”. Soprattutto a cominciare dalla prima parte del 2020, il mondo del lavoro è profondamente cambiato, per adattarsi a una maggior remotizzazione dettata dalle circostanze di scenario globale. Nello shop floor le influenze di questa evoluzione non potevano essere troppo estese, trattandosi di ambienti dove la presenza fisica è ancora determinante. Tuttavia, la logica della collaborazione si è allargata anche su questo fronte: “Microsoft Teams è uno strumento assai più versatile di quanto si possa credere”, illustra Giovanditti, “e con le nostre declinazioni può diventare l’interfacMatteo Giovanditti
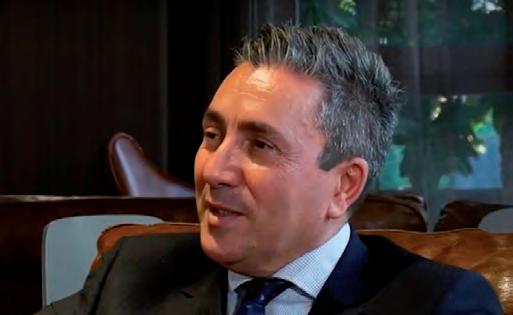
cia più comune per la comunicazione non formale fra dipartimenti, per la strutturazione di interi processi e persino per lo sviluppo di applicazioni low-code”. Nel tempo, Alterna ha aumentato la presenza nel manifatturiero discreto, nel meccanico, ma anche nel fashion, per tutti gli aspetti che coprono la distribuzione dei prodotti, la multicanalità, la raccolta dei feedback o la tailorizzazione dei servizi. Un ambito di innovazione recente riguarda la pianificazione avanzata, basata su algoritmi evoluti, per ottimizzare le catene di produzione. In questo contesto, sono state messe a punto anche partnership con realtà come SedApta con l’aiuto di Nextea – company di Altea Federation, per la gestione della domanda e dei forecast. Guardando al futuro, il system integrator sta già pensando a sfruttare le opportunità collegate al Pnrr per specializzarsi anche nel campo dell’ingegneria e delle costruzioni, rivolgendosi non solo ai colossi del mercato italiano ma anche alle Pmi che spesso entrano nei progetti come subcontractor. È in preparazione, inoltre, un framework in grado di evidenziare il vantaggio che l’intelligenza artificiale può portare alle Pmi. Entro i prossimi tre anni, poi, l’intento è di puntare sulla tecnologia blockchain, per cui già è stata sviluppata una soluzione di gestione integrata della documentazione su base Sharepoint, estendendo proprio grazie alla blockchain le capacità di conservazione digitale, signage e controllo delle identità.
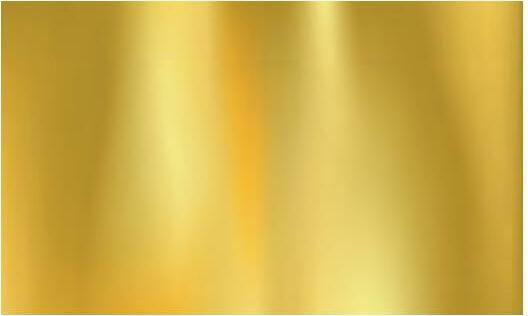
LO SMART RETAIL: IBRIDO E RESILIENTE

Milano | 6-7 Luglio 2022
Hotel Melià
Giunto alla terza edizione, Retail & Fashion Summit è l’unico evento della comunità imprenditoriale e manageriale italiana pensato per promuovere il dialogo tra business e tecnologia e, coinvolgendo i diversi interlocutori interessati ai processi di innovazione, insieme agli stakeholder che predispongono politiche di incentivazione e promozione della trasformazione dei settori Retail, GDO e Fashion del nostro Paese.
Nei due anni di pandemia, gli imprenditori e i manager più illuminati hanno utilizzato il “tempo sospeso” dei lockdown e delle restrizioni per investire in tecnologia e accelerare il processo di trasformazione delle proprie aziende. Oggi quindi il retail italiano, nonostante le difficoltà, si trova nella condizione di riprendere con ancora maggior efficienza. Le minacce però non mancano, sul fronte geopolitico e quindi anche dei costi energetici, logistici e delle materie prime, fattori che rendono lo scenario complesso e sfidante. In quest’ottica, i temi dei finanziamenti (PNRR ma anche molte altre iniziative di sostegno e rilancio), quelli delle strategie energetiche e di approvvigionamento, quelli della gestione avanzata e intelligente dei cicli di vita del prodotto e più in generale della transizione ecologica si affiancano al filone principale dell’evoluzione tecnologica in ottica smart del retail: Cloud, Intelligenza Artificiale, Realtà Virtuale, Aumentata e Metaverso.
L’evento avrà, come di consueto, un’ottica “bifocale” che comprende un taglio più strategico di scenario e allo stesso tempo i tavoli di lavoro volti a distillare le istanze più importanti per la crescita del settore.
INFO MAIL
#TIGINNOVATION