
5 minute read
Experts in automation AZO
Mr Rupp said, “We were one of the early pioneers when we entered the renewable energy market in 1995, producing IGBT frequency converters for wind turbines based upon the new requirements of the upcoming market. We had specific requirements to meet from the big energy providers such as Eon, and we supplied OEM manufacturers with converters rated up to 6MW. Now in offshore applications we are talking about wind installations that produce 6–10 megawatts of power and the demand for reliability and power quality continues to increase.”
“Initially it was the European market that was driving the industry but this is now a mature market and the main drivers for growth today are the emerging markets such as China, South Africa, India and South America, and in particular Brazil. Our wind turbine converters provide the gateway between the wind turbine and the grid itself and these world-class products control the electrical output of the wind turbine.”
Mr Rupp added, “Our extensive facility here in Kempen, Germany, is the global hub for our offshore applications worldwide and it is here that we specialise in the bigger output converters of 3MW and over. Offshore applications represent the biggest growth opportunity for us and we design our converters to meet the toughest and harshest conditions experienced at sea. Therefore reliability is of utmost importance to operators because servicing offshore installations is a very costly business, both in terms of maintenance and in respect of the revenues lost through an interruption in supply. However, in any event we do offer an unparalleled after-sales and technical support service worldwide and we also work closely with our customers to develop the optimal product to suit their specific requirements.
“In addition to our wind turbine converters, we also manufacture energy storage converters, solar inverters and shore power and dynamic positioning inverters. As an independent supplier we offer flexibility with our products and we are innovative in our approach to product development and customer service. It is also important to remember that we are a truly global organisation and can therefore provide a tailor-made, local service wherever a wind turbine installation may be required anywhere in the world.”
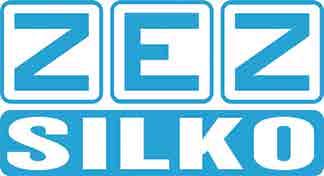
Innovative, modular platforms
Woodward’s Concycle® wind converters set the standards when it comes to reliability, efficiency and innovative technology. This is especially true of the company’s compact, modular MP1 platform. This cutting-edge compact converter is well established in both onshore and offshore wind turbines and is being constantly updated to comply with the latest international grid code legislation requirements.
As a customer-orientated and flexible partner, Woodward also offers a local tender solution in countries where it is necessary for local suppliers to produce a certain percentage of the sustainable value chain. This is often required where a special tender consortium is involved like Brazil. Based upon the individual technology licence contract and the industrial property rights, Woodward is able to provide the appropriate critical elements of the overall project. n
For further information about Woodward’s latest wind turbine converters and services visit: www.woodward.com
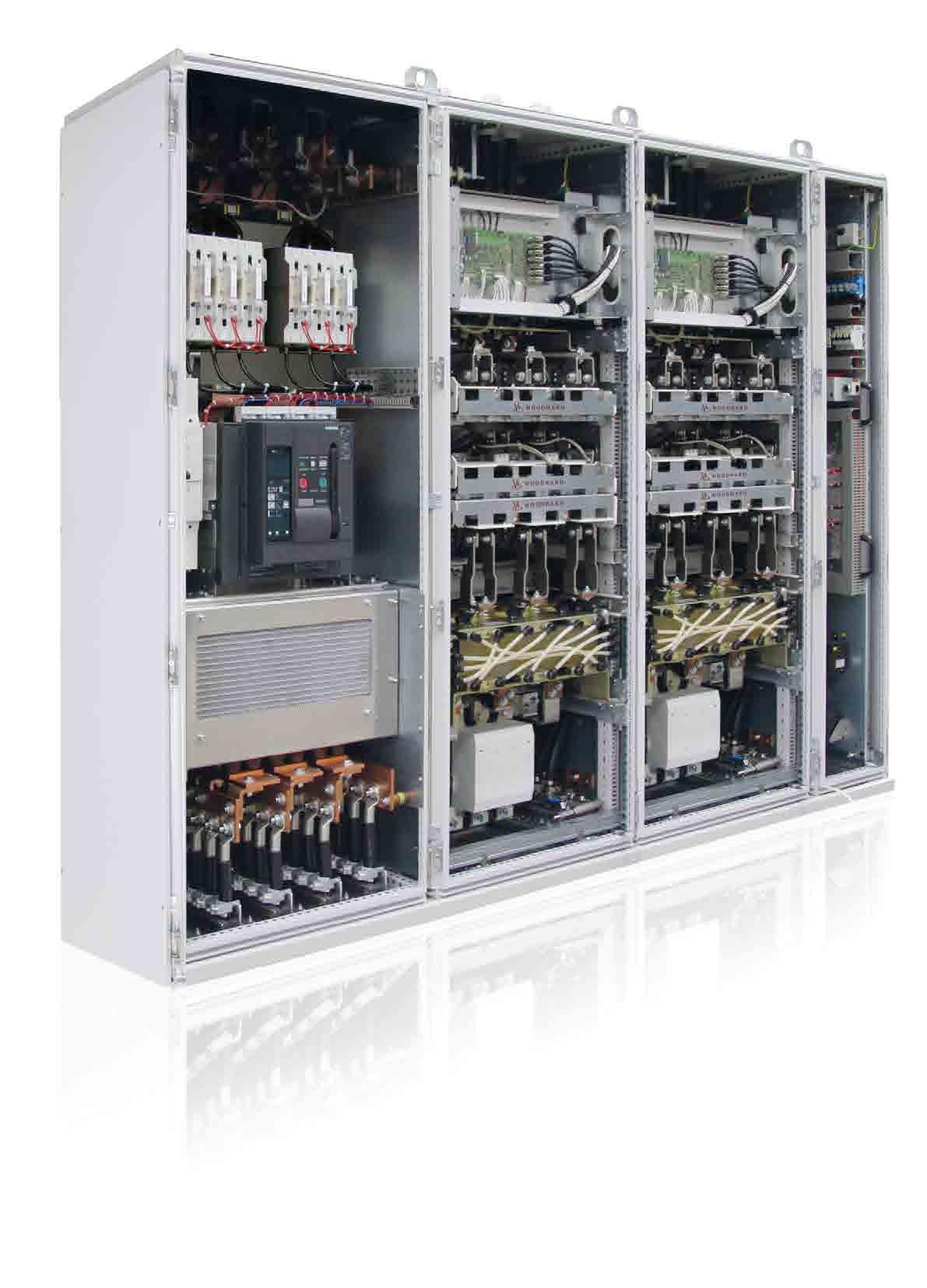
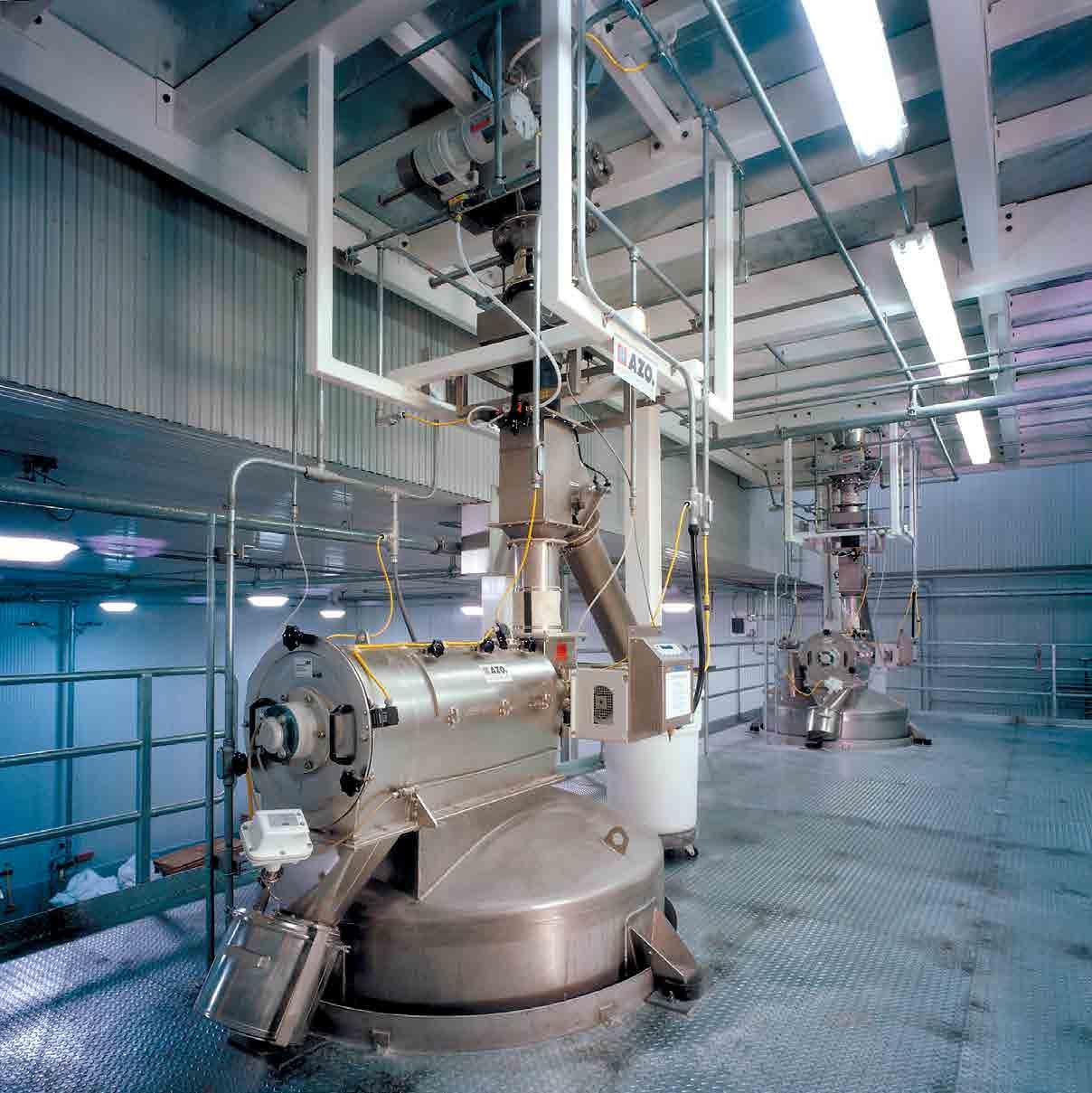
EXPERTS IN AUTOMATION
AZO GmbH & Co. KG designs and produces machines for the automatic handling of bulk goods and powders. AZO’s systems for automated raw material handling are used in the food sector, in the plastics and pharmaceutical industries and by manufacturers of chemical and cleaning products.

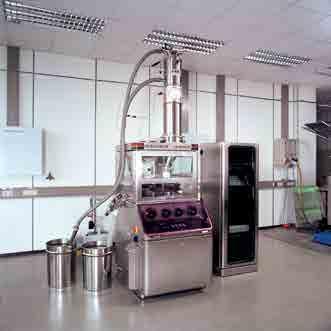
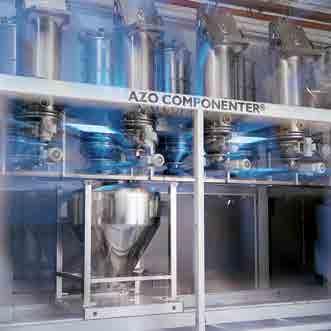
Food and pharmaceutical companies rely on AZO’s machines to ensure the efficiency of their production processes. Within the production process, the equipment that AZO supplies covers many different functions, including screening, conveying, dosing and weighing. When bulk goods are delivered to a factory, AZO’s machines are used to screen out contaminants. On the factory floor, AZO’s suction weighing systems transport bulk quantities to a predetermined point in the process and precisely weigh the ingredients that have to be added to the recipe.
To meet the needs of its customers in various industry sectors, AZO is organised into four different divisions: AZO Food, AZO Vital (which serves the pharmaceutical industry), AZO Chem and AZO Poly (for plastics manufacturers). What happens inside a chocolate factory or a pharmaceutical plant is a complex business where a one-size-fits-all approach cannot succeed. For this reason, AZO works in close cooperation with its clients, giving them carefully considered advice on the best way to automate their processes. “We produce systems that provide reliable automation for production processes,” stated a company spokesperson. “Most of them are tailor-made for our customers.”
A tradition of innovation
AZO, based in the German town of Osterburken, is a family company, established in 1949 by Adolf Zimmermann and his wife, Marianne. AZO’s original headquarters were an old sheep shed but the firm now employs over 900 people. The breakthrough came when Adolf Zimmermann created a flour-sieving machine for the bread-making industry, released onto the market in 1952. This pyramidal graincleaning machine was the forerunner of a concept, the cyclone screener, that AZO still sells today. The cyclone screener is a kind of automatic, industrial-sized sieve that can be used as part of a continuous production process. When powder is thrown against a screen, fine particles are small enough to pass through it, while unwanted, coarse particles like contaminants or agglomerates are too big to get through the screen fabric and are discharged.
“The cyclone screener is still a top-selling product,” said the spokesperson. “It is used as part of a system for quality control of ingredients.”
As early as the 1980s, AZO saw the potential of information technology, which enables an industrial process to be controlled from a computer screen. AZO’s subsidiary company, hsh-systeme for process-IT, installs computer systems on production lines to support such tasks as manual weighing and batch tracking. “Computer controls are essential for handling automated processes. They are especially valuable for track-and-trace purposes, where a large amount of data has to be collected.” In the event of a problem at a food factory,
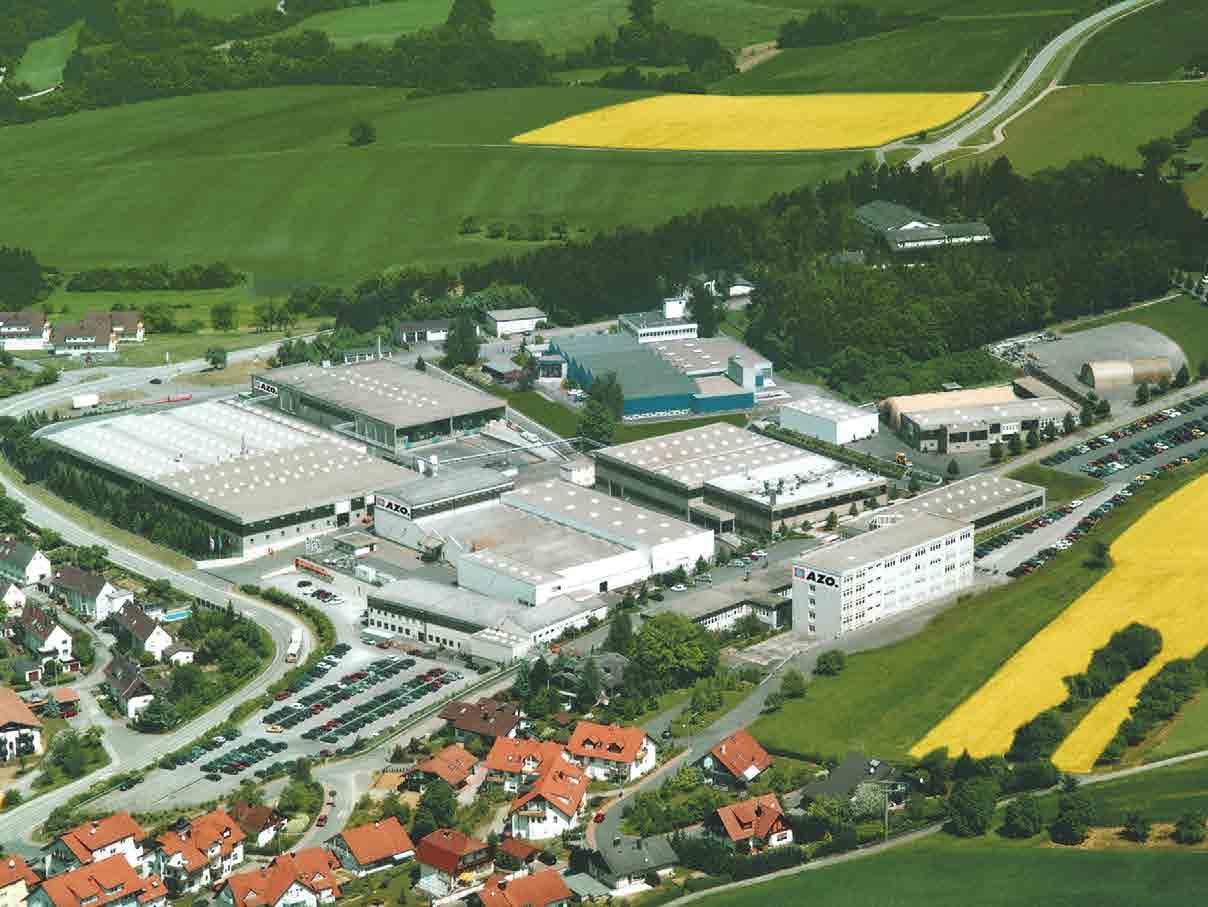