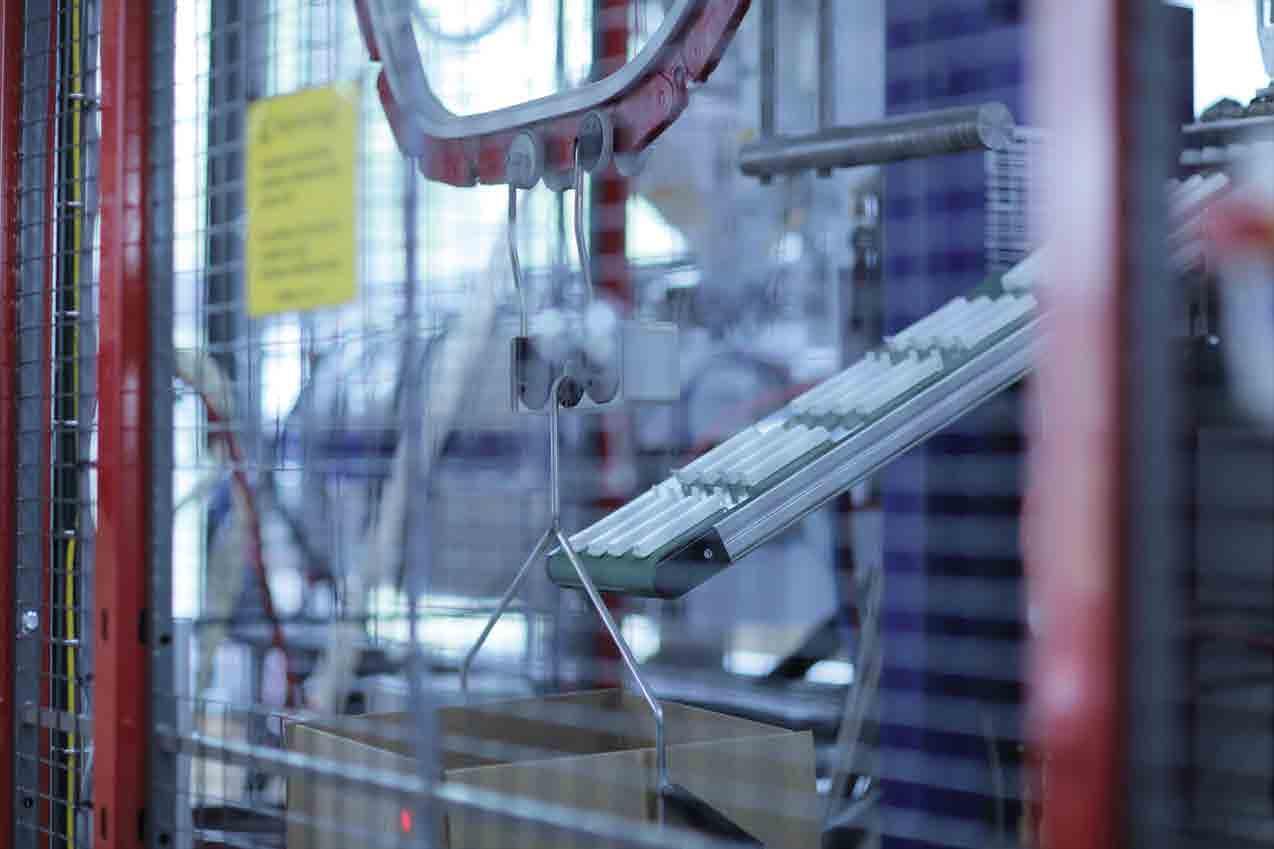
6 minute read
Strength in steel Acciaieria Arvedi
Your Complete Injection Molding Partner
Inca Plast is a family-owned and managed injection molding company located in southern Sweden. Our mission is to be a complete partner when it comes to plastic products. We serve our customers with all processes concerning injection molding: From your idea to a distributed product. The company was founded in 1982 and the family’s experience of injection molding reaches back for three generations.
We believe that strong and reliable relationships with our customers is the foundation for success. This strive, together with a highly automated production process, helps us to generate the highest value as possible for our customers.
Besides injection molding, we serve our customers with assembling, pad printing and distribution.
Inca is a very reliable supplier that always deliver high quality. Inca produce some of our most technical and qualified products in a cost effi cient production setup. “ “
Peter Garnbratt, Sales and Commercial Director, Eton Systems
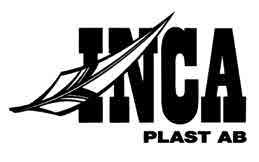
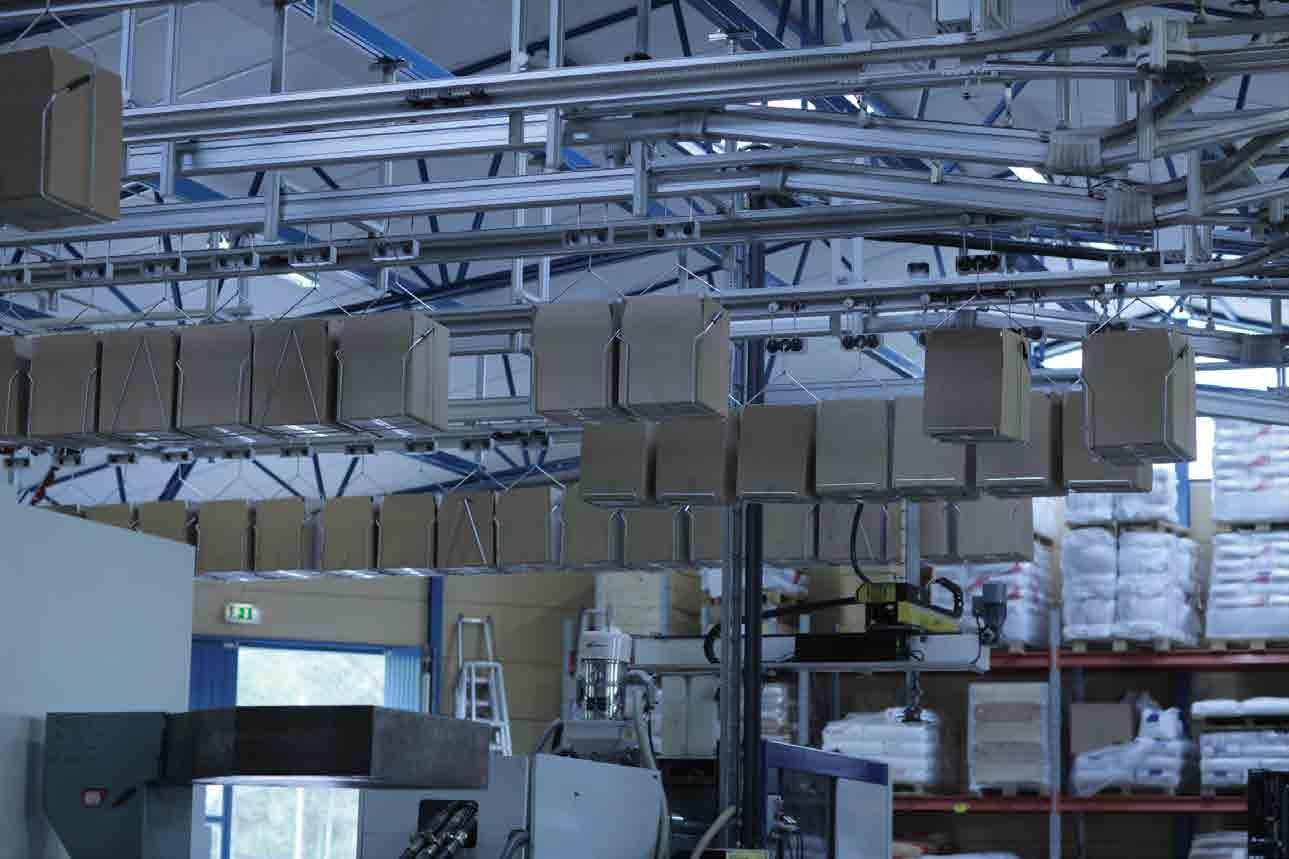
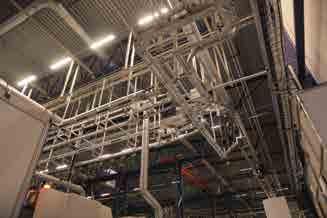
“We focus on many different industry sectors. Today our main focus is on vehicles, plastic, filters, painting, assembly and furniture. For example, in furniture, we have a big advantage by being able to handle both hard and soft material in an effective and efficient way. We have a weight limitation of 12kg, but we are still able to handle the part of the production chain where we can meet the weight limitation. We can then work with our partners who help us to handle the product when it is too heavy for us.”
New terminals offer optimal efficiency
In February 2013 the company launched two new ground-breaking products, the first a smart touch-screen terminal application and the ‘Eton Standard Apparel’, a new, significantly improved light system developed especially for high volume production operations. With the emerging economies of China, India and Brazil, the main thrust is on system optimisation and the adoption of high-end technologies to achieve optimal productivity levels.
The new touch-screen terminal from Eton Systems can be used on smart phones and tablets and complements Eton’s existing systems. In keeping with Davidson’s concept of innovation combined with simplicity of operation, this latest product offers an everyday tool for operators that increases both their efficiency and their monitoring accuracy. Another major advantage of the terminal application is its mobility. Users can monitor and control production efficiency wherever they are, and it is also designed to be used at all workstations. As a result of its early success, Eton is looking to expand its areas of use to include production managers, thus opening up a new multimedia platform. This could include the uploading of pictures or movie clips to provide instructions and to offer practical demonstrations to operators.
The second product launch in February involved a new concept for large volume production that enhances production capacity per square metre of floor space. This is called the ‘Eton Standard Apparel’ concept. This offers an advanced production tool designed to streamline production line processes that also means greater cost-effectiveness throughout the production cycle. This unique system includes structured, module-based software with standard modules, bundle tracking modules and optional network modules with hardware systems for loading, production control and optional bundle tracking. n
For further details of Eton Systems’ latest conveyer solutions and services visit: www.etonsystems.com


STRENGTH IN STEEL
Acciaieria Arvedi SpA is an Italian company specialising in steel production. Part of the Arvedi Group, its success is built on a continuous series of technological investments which have revolutionised the process of steel production. Industry Europe looks at the latest from the company.
Since being founded in 1992, Acciaieria Arvedi has produced over 20 million tonnes of steel at its plant in Cremona, northern Italy. Overseen by Group President Giovanni Arvedi, the company’s early success was founded on the use of its patented ISP line (in-line strip production) at its casting and rolling plant, which became the world’s second mini-mill for flat-rolled steel production. In 2009, the company took another groundbreaking step with the establishment of a second plant dedicated to Arvedi’s new ESP (endless strip production) technology, which connects casting and rolling in a fully continuous process.
Through a constant drive to break down technological barriers and tireless research, Acciaieria Arvedi currently has a wide European market presence and represents approximately 60 per cent of the Arvedi Group’s entire annual turnover. It has also been expanding elsewhere: for example, in December 2012 it invested in the production of tubes for special applications in the Brazilian market.
Key to success
In order to maintain its success, Arvedi had adopted a continuous investment policy since the very beginning. Since its establishment, there has been a succession of investments covering a range of projects, from the construction of its first plant in Cremona to the recent implementation of an electric oven. In April 2011, it produced the first 0.8mm hot rolled coil with a table width of 1500mm using its own ESP technology. The ESP line has allowed Arvedi to develop products of the highest quality while reducing strip thickness.
Arvedi’s success can also be attributed to its ability to successfully monitor market trends. Having exclusively served the steel tube sector for its first five years, in 1997 it moved on to a broader range of highvalue sectors such as the automotive and construction industries. According to a company spokesperson, Arvedi’s success is also driven by its strong partnerships with its clients, based on agility and efficiency: “As a company, we pride ourselves on our ability to make decisions quickly in line with market demands whilst continuing to provide highquality products. In the past few years, we have successfully taken part in a number of joint projects within the steel industry. This can be credited to our ability to deal with
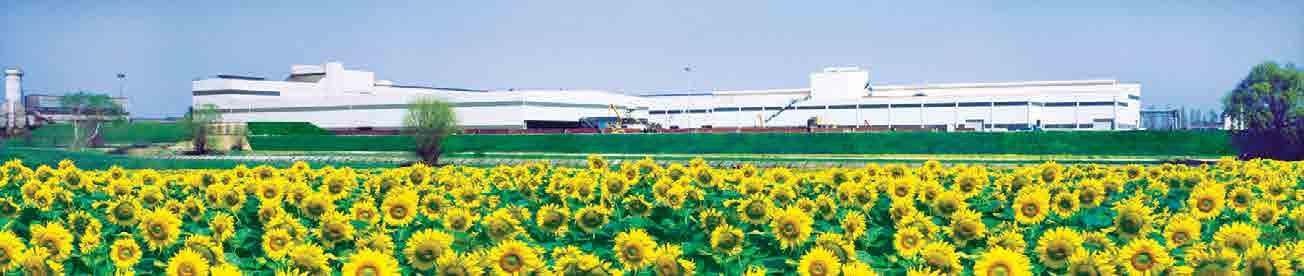
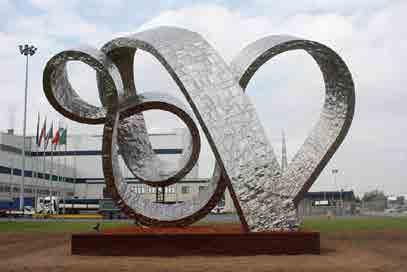


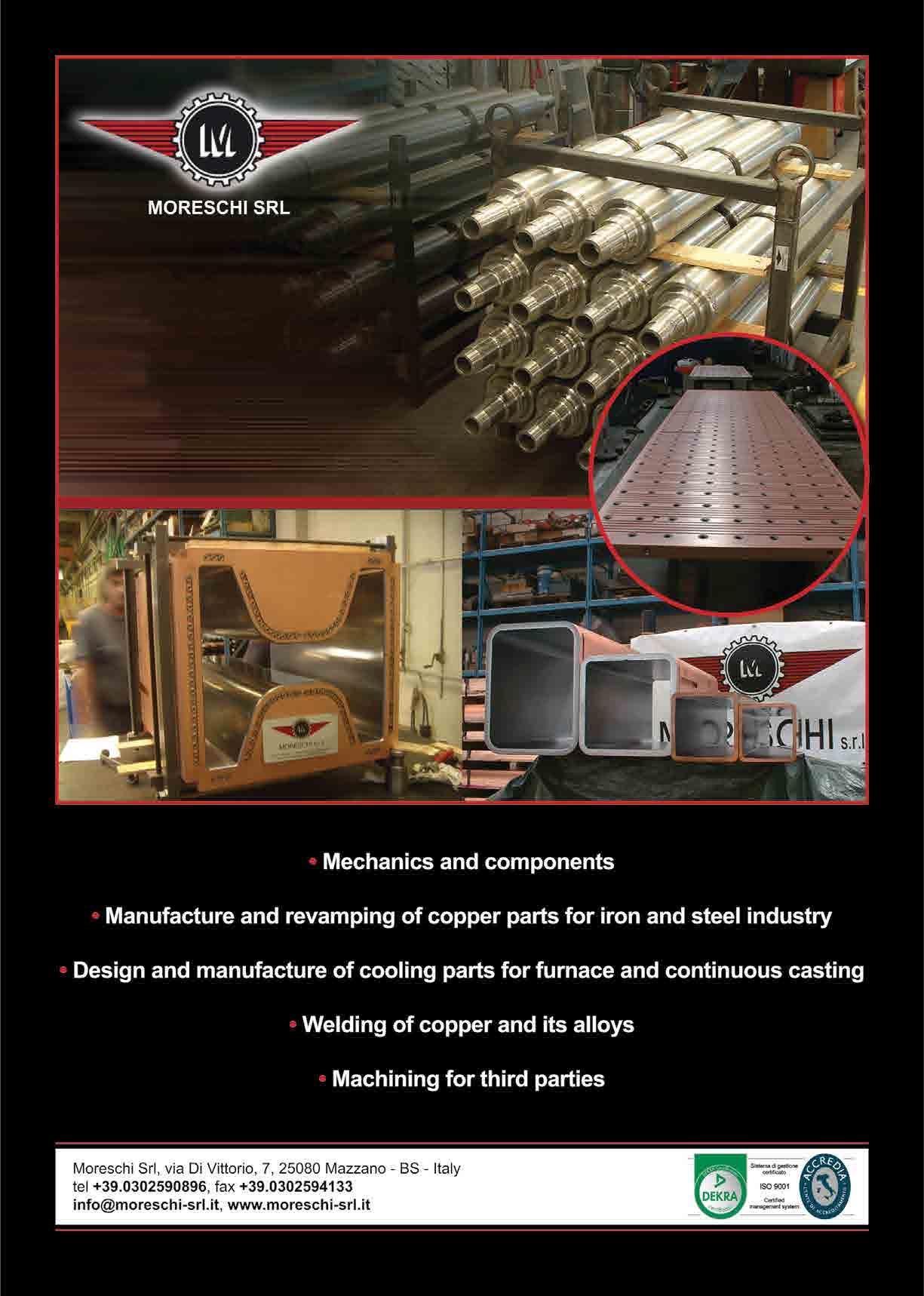
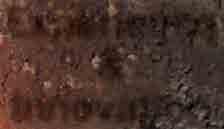
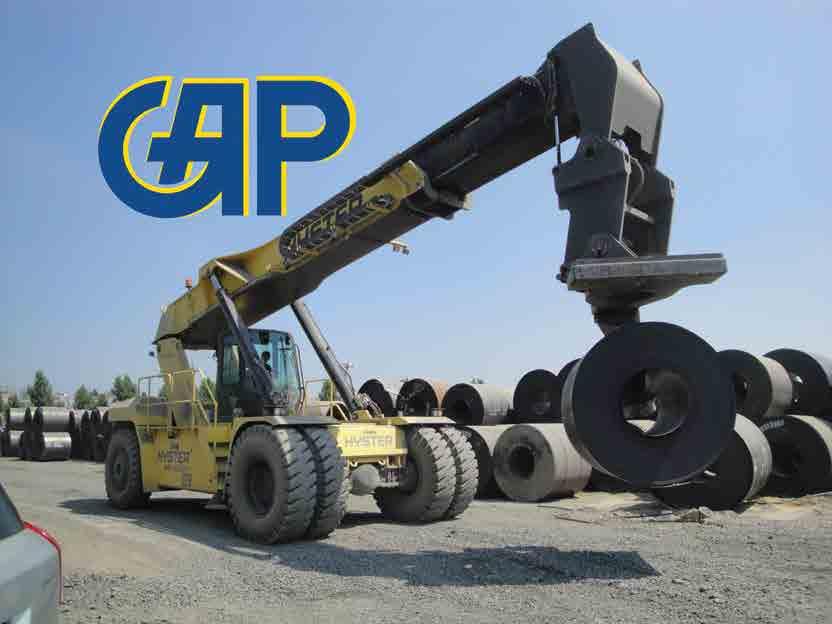
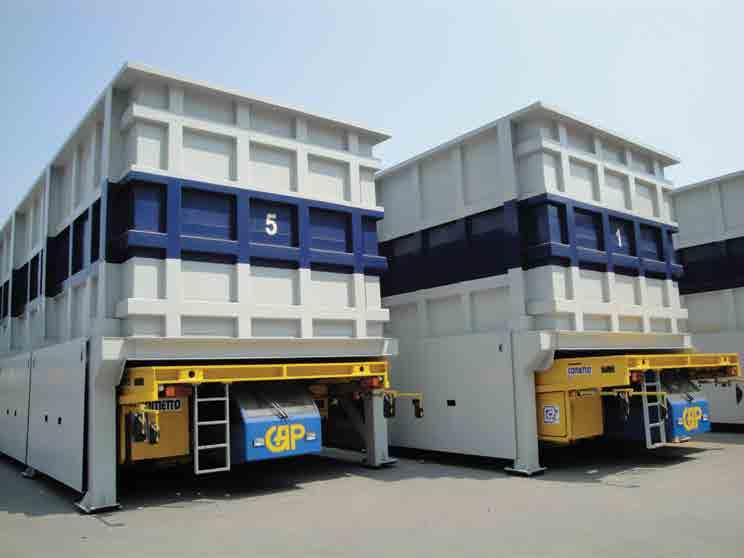

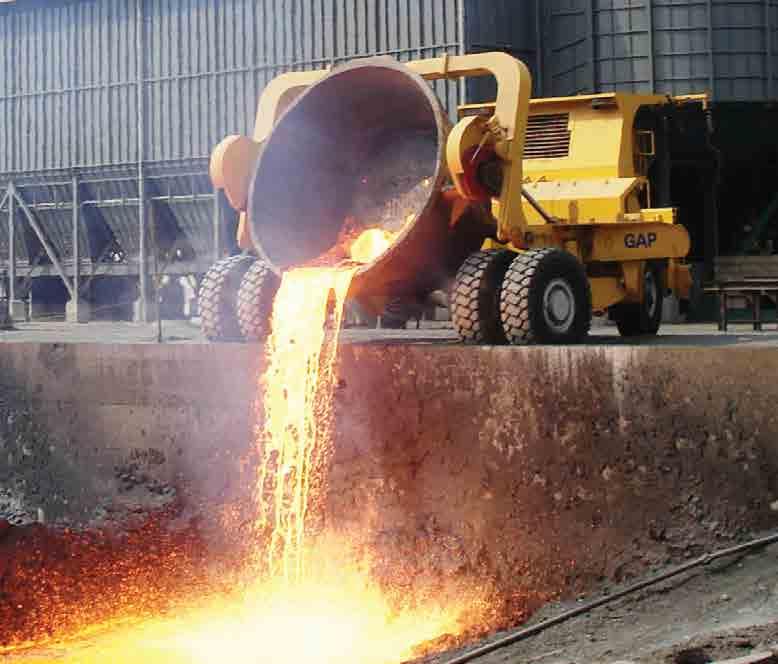
GAP S.p.A. STEEL INDUSTRY SERVICES
• A landmark in the steel industry for more than 60 years • 410 machineries and equipment • 170 employees
Main activities: • Scrap Service • Slag Handling • Metal Recovery • Materials Handling • Logistics and Warehouse Management • Industrial Demolition • Industrial Cleaning • Design and Construction of Industrial Installations
Quality & Safety
Experience & Innovation
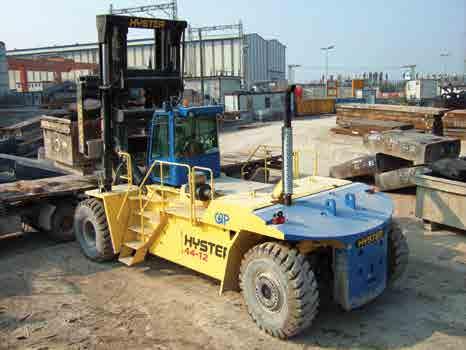