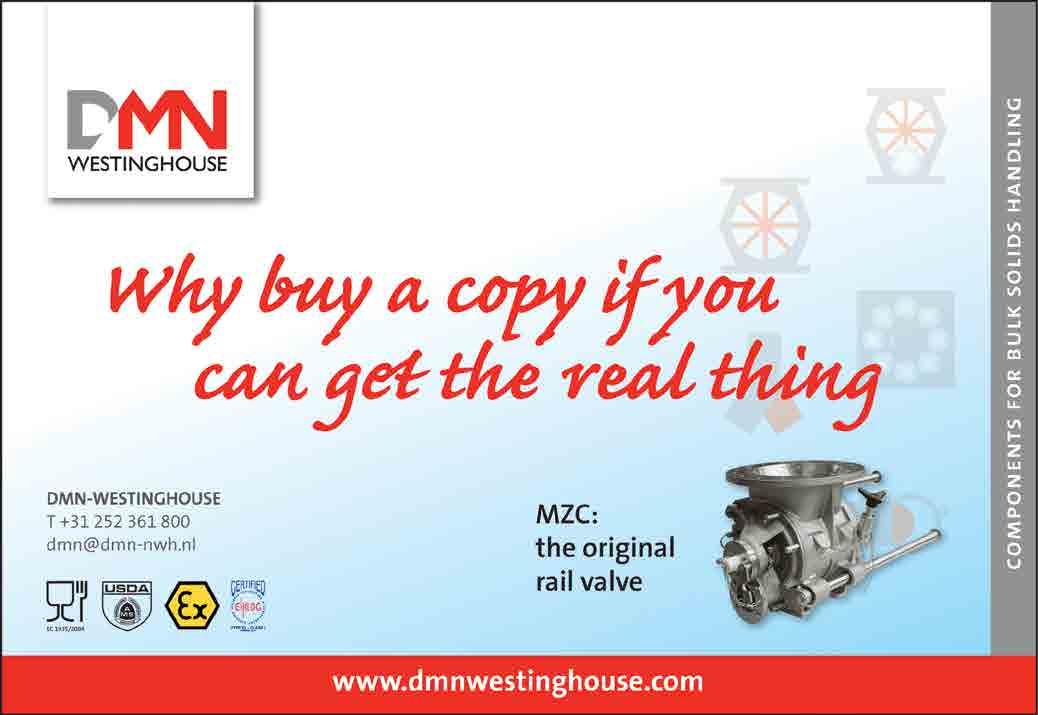
5 minute read
Smooth operator Eton Systems
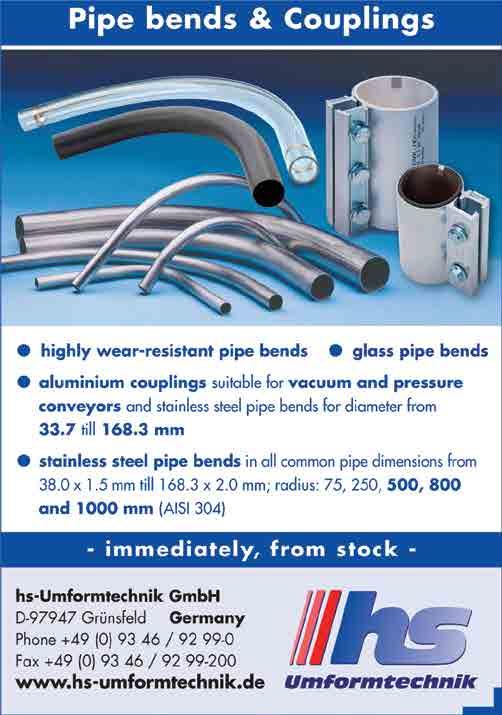

AZO’s Kastor software package, which precisely documents product quantities, will identify the contaminated batch, ensuring that any affected customers can be warned as early as possible.
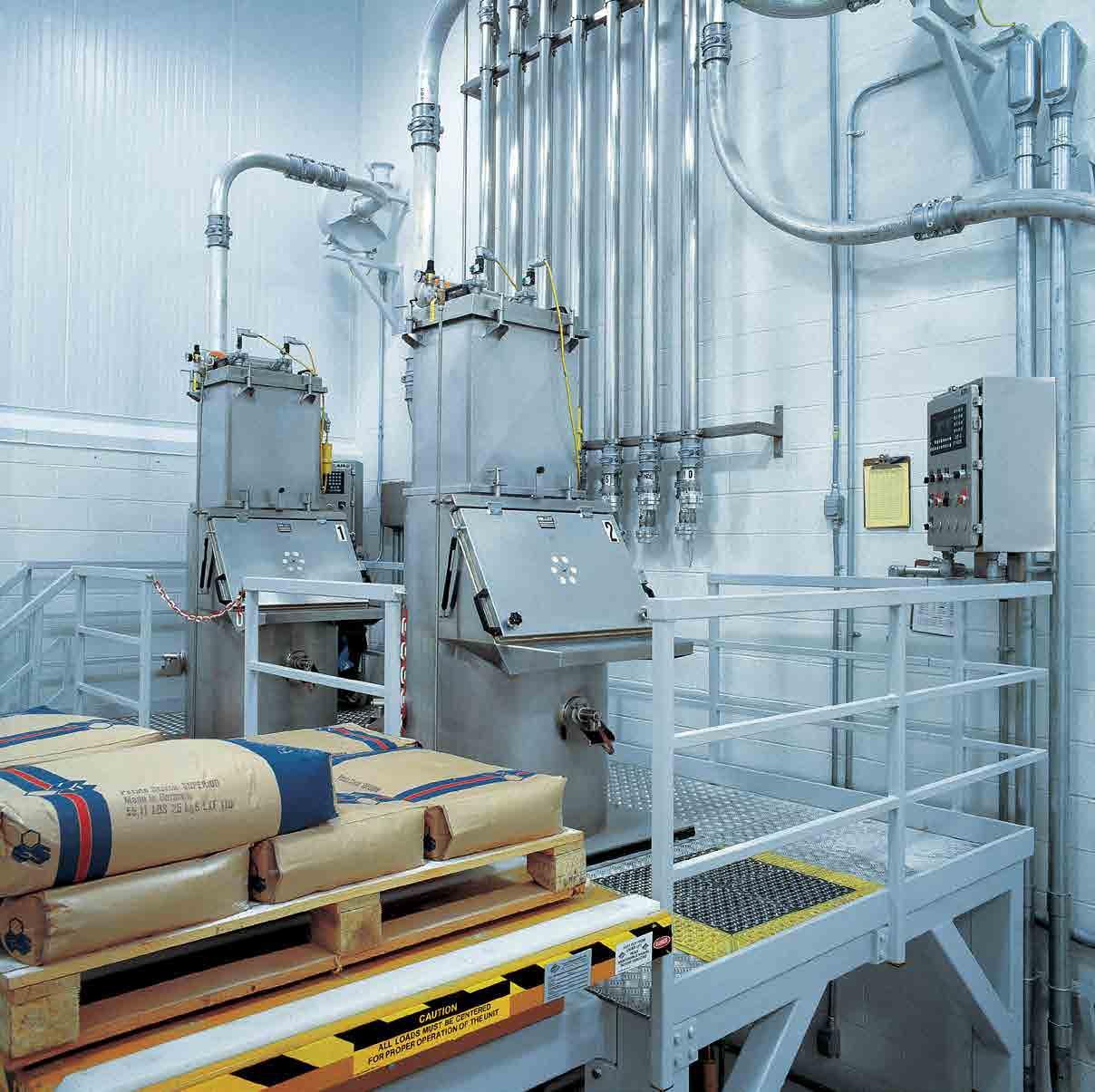
ShuttleDos
AZO’s ShuttleDos system for super-fast batch automation was developed by the company in 2005 and is proving very popular with customers. “We have continued to develop this concept, which has attracted a lot of interest in the market, particularly over the last couple of years,” the spokesperson explained. “The ShuttleDos system’s main advantages are high throughput, lower dust levels and superior hygiene. The ShuttleDos system is especially suited to applications in the food sector, but it could be installed for customers of any one of our four divisions.
“Each recipe will have a dedicated container. During the production process, the shuttle system moves the containers from one dosing station to the next. By moving the container within the production system, the shuttle makes it possible to bring in more containers for weighing and dosing. Previously, the weighing scale caused a bottleneck because it had to go through the whole system. With the ShuttleDos system, the containers move around, and instead of the travelling scale, there is a fixed scale under each container.”
Asian markets
Demand for AZO’s services is growing. In 2010, the company built a new production hall in order to increase capacity. The source of the demand is global. Outside Germany, AZO has sales companies not only in Europe but also in emerging economies like China and Thailand. The company spokesperson believes that Asian countries represent a big potential market for AZO.
“People in Thailand are looking for a higher quality of life, with people becoming more concerned about food quality. Indonesia is another big market with great potential. The growth in the Asian population means that the food sector will require new production capacity. In international markets, nothing is guaranteed, so incoming raw materials must be checked to prevent contamination. Asian consumers now attach more importance to food quality. Automation and track-and-trace technology will be needed in order to satisfy their expectations.” n
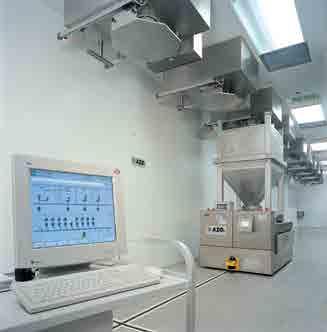
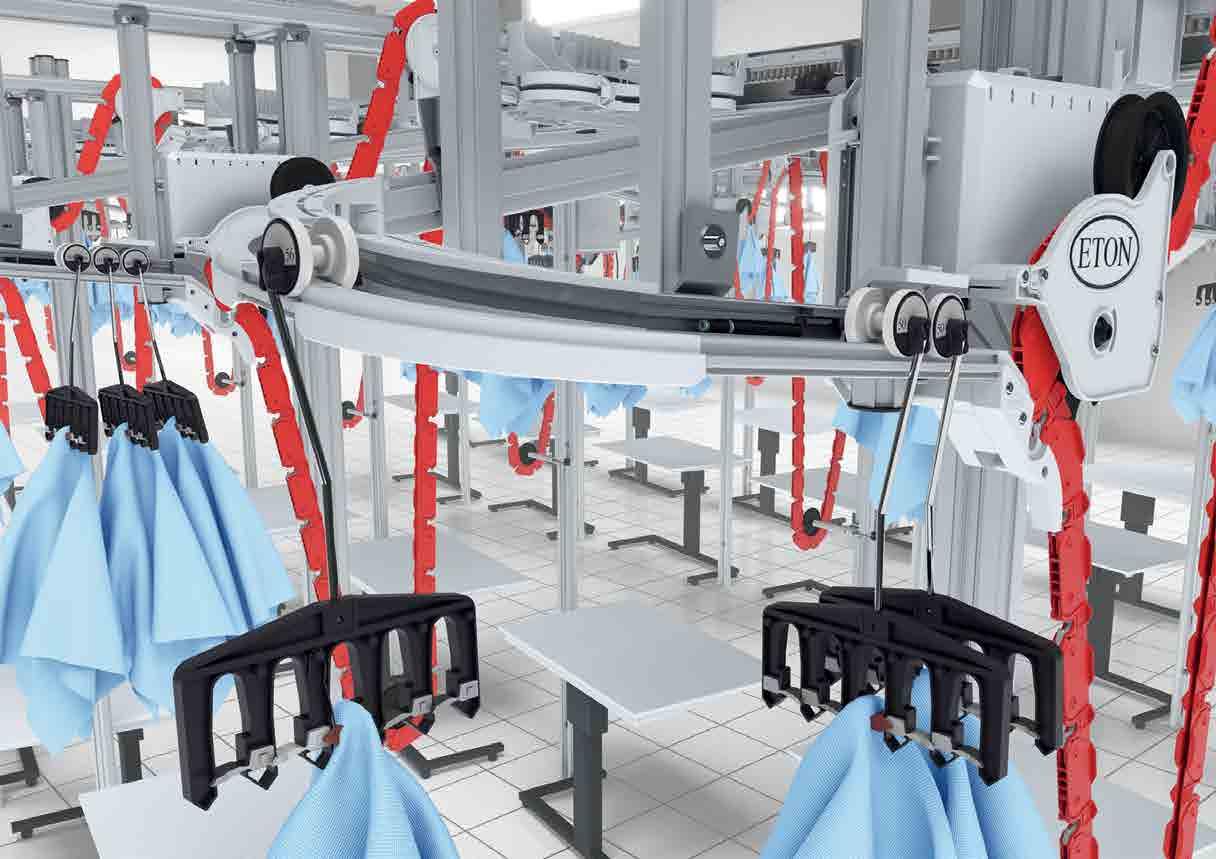
SMOOTH OPERATOR
Eton Systems is the global leader in the design and manufacture of overhead conveyor systems. This innovative company is continuing to broaden the technology gap between itself and its competitors. Recently the company launched a new family of products for handling sensitive surface products as well as an advanced range of control devices that are web-connected for greater flexibility and smoother operation. Philip Yorke reports.

Eton Systems was founded in Sweden in 1967 and evolved from Eton Fashion, a Swedish company that had been making shirts since 1928. As the company grew, it became aware of the benefits of streamlining its production processes in order to minimise down-time and achieve greater production efficiency. This led to the founding of Eton Systems, the world’s first unit production system (UPS), which was inspired by Inge Davidson, a technician and co-owner of the Eton shirt factory. Davidson had fine-tuned the company’s production processes but this was not enough, so he designed an ingenious hanging conveyer system that didn’t take up valuable floor space and required minimal adaptation to fit to existing machines.
Like most great inventions, his system was simple, effective and quite unique, and as a result, workstation operators could focus on sewing garments without wasting

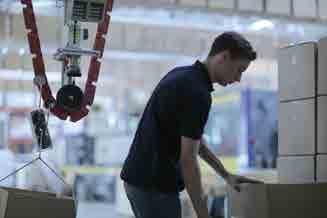

time on handling bundles of unfinished garments. Therefore, not only did productivity greatly improve, but production could now be planned and controlled down to the finest detail. Today, there are more than 4000 Eton systems installed in over 60 countries worldwide and operating in a variety of manufacturing industries that range from apparel and home textiles, to furniture and the automotive industries.
Flexible productivity improves handling
Eton’s ‘Flexible Productivity Concept’ (FPC) is based on two distinct system platforms and provides a wide array of flexible system tools that allows the UPS to be optimised for maximum customer profitability. The company’s systems provide highly efficient solutions which are perfectly suited to an individual customer’s specific operations and requirements.
Peter Garnbratt, Eton Systems’ sales manager, said, “As technology leaders in our field we offer unique solutions that will transport and store goods directly above the active production area to reduce all manual handling. This system takes out the handling of all pallets, pallet racks, forklifts and all heavy manual lifting. By reducing all handling operations and the equipment involved, we increase the active production area by between 50 per cent to 100 per cent. Furthermore, in addition to transportation, we can buffer and sequence the goods to be directed to all desired locations in the factory. The result is balanced bottlenecks and increased productivity in all parallel operations.
Mr Garnbatt added, “In addition to our new touch-screen terminals we are also launching a new product family for sensitive products. Through a new patented system we can buffer large or small items without the parts touching each other or getting soiled.This means we are now able to handle products that have sensitive surfaces and are produced in both clean-room and other sensitive environments.
“Together with INCA Plast AB we developed a new clean product family. Reliable suppliers like Inca Plast that help us to constantly develop new material and functions are essential for our expansion.
“We produce almost all our components in Europe to meet very high requirements and to be able to deliver the best quality and most reliable system for our customers.
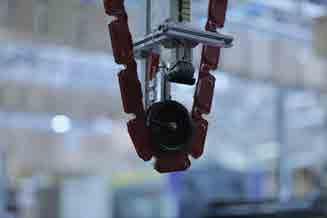

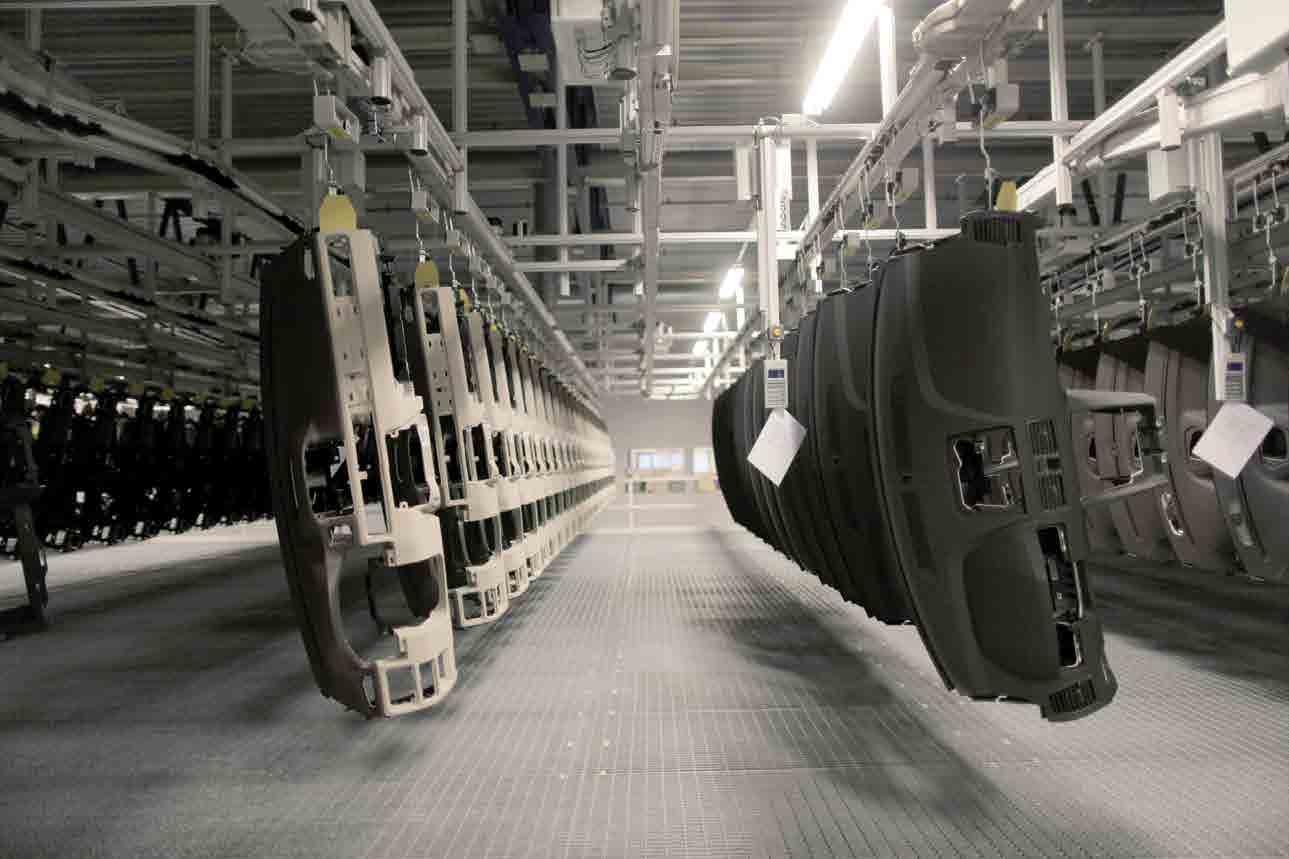