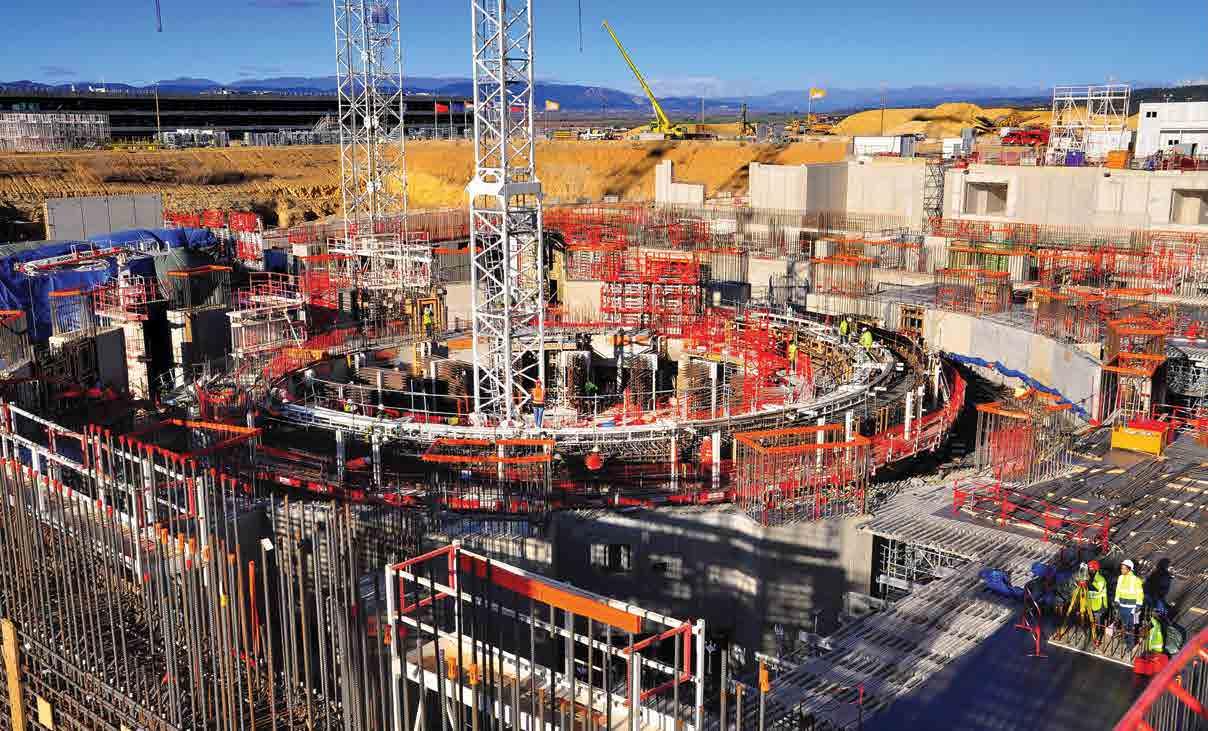
5 minute read
Energy from the stars Construction continues on ITER
ENERGY FROM THE STARS
ITER is one of the most ambitious energy projects in the world today. Construction is advancing at the ITER site at Saint-Paul-lès-Durance in the Bouches-du-Rhône department of France.
IN southern France, 35 nations are collaborating to build the world’s largest tokamak, a magnetic fusion device that has been designed to prove the feasibility of fusion as a large-scale and carbon-free source of energy based on the same principle that powers our Sun and stars.
The experimental campaign that will be carried out at ITER is crucial to advancing fusion science and preparing the way for the fusion power plants of tomorrow.
ITER will be the first fusion device to produce net energy. ITER will be the first fusion device to maintain fusion for long periods of time. And ITER will be the first fusion device to test the integrated technologies, materials, and physics regimes necessary for the commercial production of fusion-based electricity.
Thousands of engineers and scientists have contributed to the design of ITER since the idea for an international joint experiment in fusion was first launched in 1985. The ITER Members – China, the European Union, India, Japan, Korea, Russia and the United States – are now engaged in a 35-year collaboration to build and operate the ITER experimental device, and together bring fusion to the point where a demonstration fusion reactor can be designed.
The tokamak
Inside a tokamak, the energy produced through the fusion of atoms is absorbed as heat in the walls of the vessel. Just like a conventional power plant, a fusion power plant will use this heat to produce steam and then electricity by way of turbines and generators. The heart of a tokamak is its doughnut-shaped vacuum chamber.
Inside, under the influence of extreme heat and pressure, gaseous hydrogen fuel becomes a plasma – a hot, electrically charged gas. In a star as in a fusion device, plasmas provide the environment in which light elements can fuse and yield energy.
The charged particles of the plasma can be shaped and controlled by the massive magnetic coils placed around the vessel; physicists use this important property to confine the hot plasma away from the vessel walls. The term ‘tokamak’ comes to us from a Russian acronym that stands for ‘toroidal chamber with magnetic coils’.
To start the process, air and impurities are first evacuated from the vacuum chamber. Next, the magnet systems that will help to confine and control the plasma are charged up and the gaseous fuel is introduced. As a powerful electrical current is run through the vessel, the gas breaks down electrically, becomes ionised (electrons are stripped from the nuclei) and forms a plasma.
As the plasma particles become energised and collide they also begin to heat up. Auxiliary heating methods help to bring the plasma to fusion temperatures (between 150 and 300 million °C). Particles ‘energised’ to such a degree can overcome their natural electromagnetic repulsion on collision to fuse, releasing huge amounts of energy.
The ring magnets
ITER’s ring-like poloidal field coils are among the largest and heaviest components of the ITER machine. Ranging from 8 to 24 metres
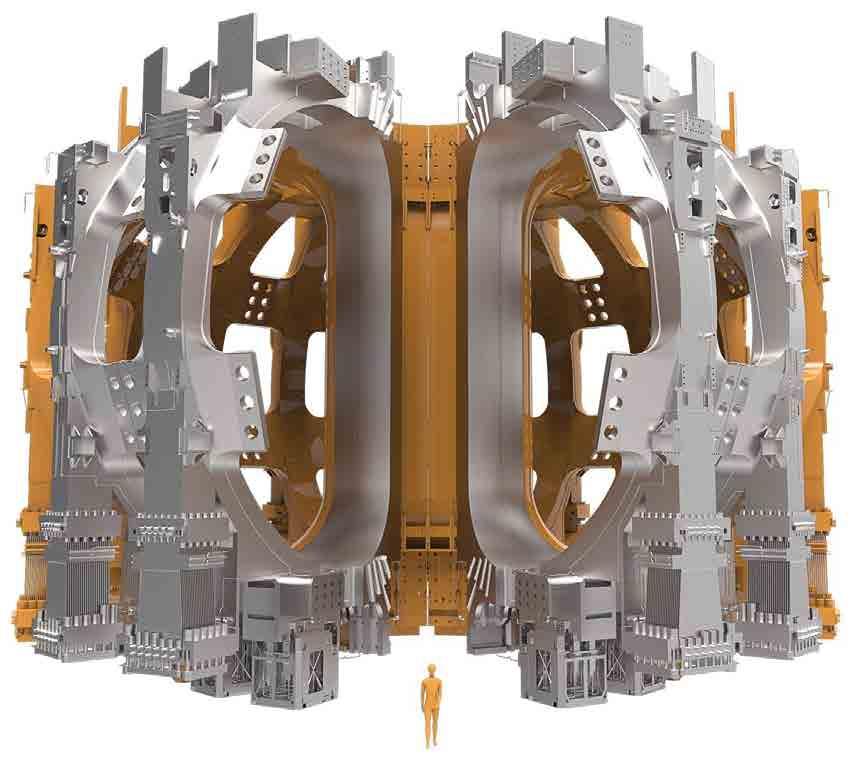
Eighteen ‘D’-shaped toroidal field magnets will surround the torus-shaped vacuum vessel to confine the plasma particles. Measuring 17 metres in height, 9 metres in width, and weighing in at 310 tons each, these coils rank among the largest components of the ITER machine.
in diameter, and from 193 to 396 tonnes, six coils will encircle the ITER vacuum chamber like so many parallels of latitude to influence the shape of the plasma and contribute to its stability by ‘pinching’ it away from the walls.
If the top and bottom coils are small enough to be produced off site and transported to ITER, the size of the four others precludes any transport by public waterway or road. For these massive machine components the European Domestic Agency has built the on-site Poloidal Field Coils Winding Facility, a 257-metre building with 12,000 metres of surface area and a circular spreader beam overhead for handling the components during the assembly process.
On the southern end of the building, contractors are currently installing specialized tooling – reels, de-spoolers, a winding table, impregnation moulds. When taken together they reflect the monumental scale of the undertaking and the complexity of the procedures.
The multistage fabrication process begins with cable-in-conduit conductor (CICC) that will be delivered on large spools from manufacturing facilities in Europe, China and Russia. In this type of conductor, hundreds of superconducting strands are grouped, twisted and bundled together to form a cable that is inserted into a thick stainless steel jacket. Liquid helium circulates at -269 °C in the centre of the conductor to cool the magnets to superconducting temperatures. One metre of poloidal field conductor will weigh more than 25 kilograms; 65 kilometres of material will be necessary to wind the six coils (47 kilometres for the four coils to be produced on site).
As they come off the spools, the lengths of poloidal field conductor will be straightened, cleaned, insulated with glass-fibre tape, and finally wound into spirals called double pancakes. Weighing 16 to 35 tonnes, these double pancakes are transferred to another station for vacuum pressure impregnation (VPI) with epoxy resin in order to harden into rigid assemblies.
In a third area, six to nine double pancakes will be stacked and joined to form the final coils. A second VPI procedure is performed to harden the stacked assembly and additional components added such as clamps, protection covers, and pipes are added. The coils will undergo approximately three months of electric and cryogenic testing before transport to the Assembly Hall – the last stop before integration into the tokamak arena.
As tokamak assembly advances, the poloidal field magnets will be positioned one by one in the tokamak pit beginning with #6 (produced by China under contract with Europe), followed by poloidal field coils 5, 4, 3 and 2 (fabricated by Europe), and finally coil #1, manufactured and delivered by Russia. n
