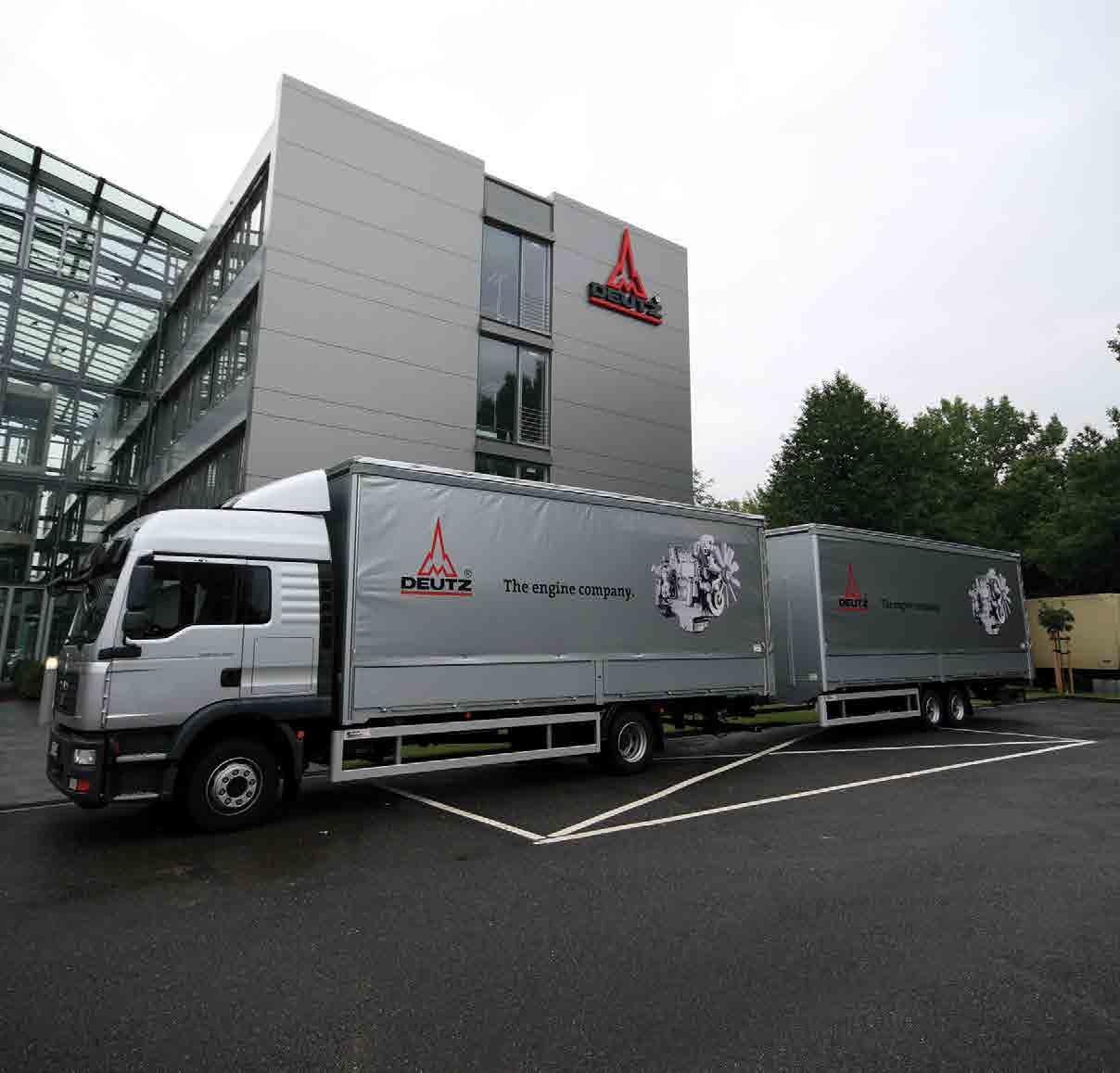
8 minute read
A global engine giant Deutz
A GLOBAL ENGINE GIANT
Deutz was the first engine maker in the world. Industry Europe reports on the German company’s plans to remain first by supplying its customers not only with engines but with complete systems solutions and comprehensive services.
The world-famous engine manufacturer Deutz claims to offer ‘the most successful engine systems in the world’. But, in fact, the company is also the oldest engine manufacturer in the world, with a history going back to 1864, when Nicolaus August Otto set up an engine factory in a small workshop in the old city of Cologne. Here he developed the first combustion engine to be produced in significant numbers – the atmospheric gas engine – and followed this innovation in 1876 with the first fully-functioning and developable four-stroke engine.
Today Deutz AG is one of the world’s largest independent manufacturers of diesel engines, with a complete product range from 25 to 560 kW for a wide variety of applications including construction machinery, generating sets, agricultural machines, mobile machinery, marine and automotive. It employs some 5,500 people, has production plants in Germany, Spain, China and Argentina and is represented in 130 countries across every continent.
Deutz engine production is divided into two segments: Compact Engines – liquid-cooled engines up to four litres and engines from four to eight litres; and Customised Solutions – air-cooled engines and large liquid-cooled engines with capacities of more than eight litres. The company is involved in the development, design, production, sales and servicing of diesel engines cooled by water, oil and air.
Production network
Deutz’s headquarters in Cologne-Porz is also the site of a state-of-theart engine factory that is the central research and development facility for the company’s compact engines and which produces between 150,000 and 180,000 liquid-cooled engines up to four litres (up to 250
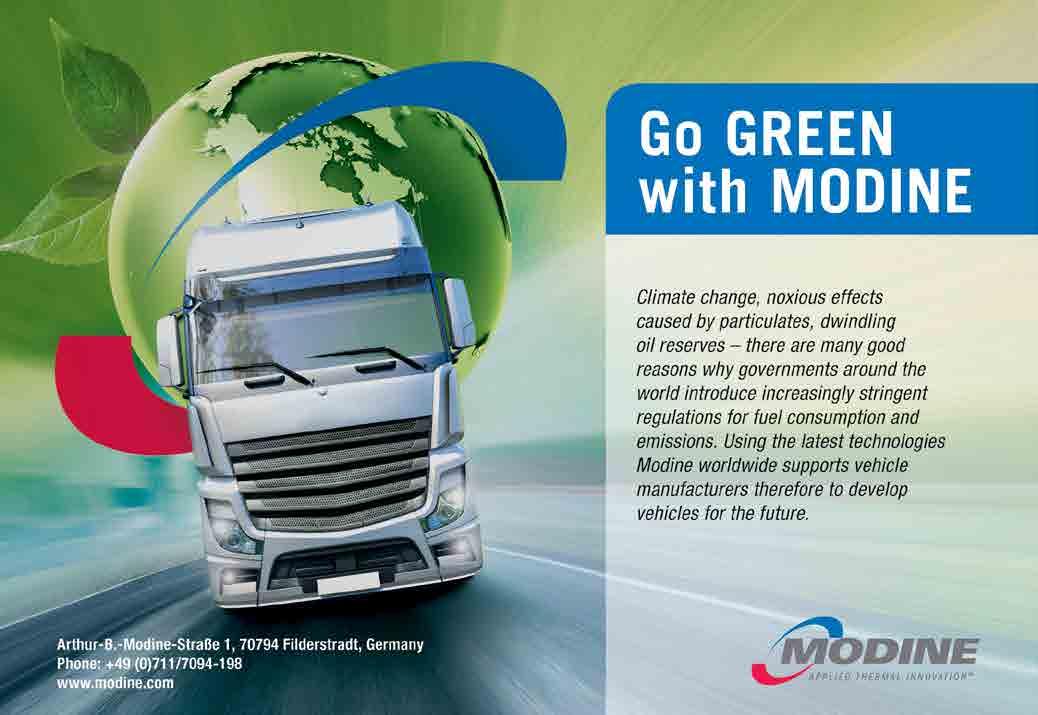
Modine
With a high expertise in the development and manufacturing of heat exchangers Modine has been supplying cooling components and systems to Deutz for almost 17 years. Manufacturers like Deutz increasingly face new regulations that create challenges on a high technological basis.
Modine therefore invests heavily in the development of newest thermal management solutions to provide innovative technologies to vehicle and engine manufacturers when they need it. They gain importance as further improved combustion processes, leading to increased heat loads, require an improved cooling capacity. At the same time, optimizing the aerodynamics lead to tougher packaging requirements, which in particular, result in the need of higher heat transfer rates, also.
With the additional target to reduce the weight of the heat exchangers, and improve fuel consumption new and more efficient heat exchangers using lighter materials must be developed.
Doesburg Components
For more than 30 years Doesburg Components in the Netherlands has been a supplier to DEUTZ AG of high quality cast iron components e.g. Flywheel Housings, Brackets, Oil sumps and Exhaust Manifolds.
Due to early supplier involvement in the casting design and machining process through the presence of resident engineers within DEUTZ the optimum casting is always being created.
Due to this approached Doesburg Components achieves the highest quality casting, lowest PPM rate and the best price from prototype through to (fully robotized) serial production.
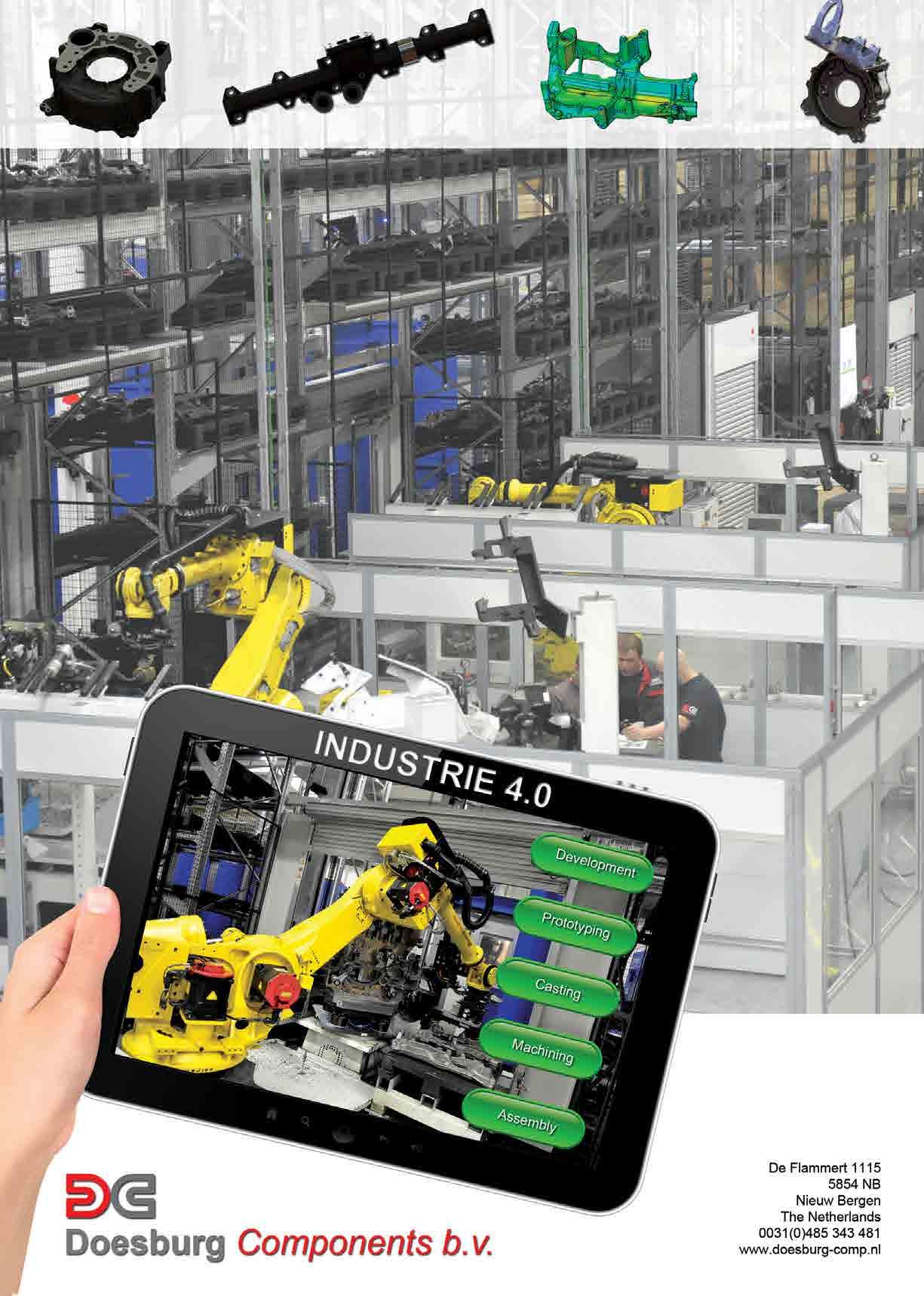
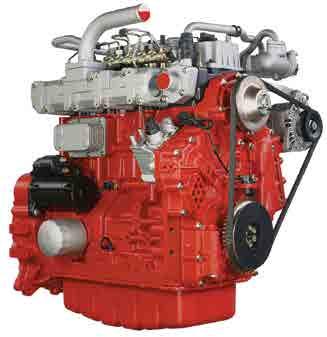


kW) per year. In fact, a new Deutz engines leaves this plant every 90 seconds, to be used in mobile machinery or stationary applications, in agricultural machinery, automotive or marine applications.
Crank cases, crank shafts and cam shafts for the compact engines are produced at a factory in the Deutz suburb of Cologne that is actually the site of a Deutz works that was opened in 1869. The components are delivered directly to the assembly lines at the Porz plant.
Deutz’s Customised Solutions large engines (mostly air-cooled and over eight litres) are designed and manufactured at a plant in Ulm, in south-western Germany. Here between 15,000 and 18,000 engines are produced each year for use in construction equipment, fire fighting vehicles, drilling machines, power generating sets and in railway locomotives. Both the Cologne and Ulm assembly plants are supplied with engine assemblies by a further plant in Herschbach, southeast of Cologne, and by the Deutz factory in Zafra in south-western Spain, which specialises in con-rods, cylinder heads and gears.
Replacement engines
The remanufacturing of old or damaged engines also makes up a significant part of Deutz’s business. In fact, the company has been engaged in rebuilding its diesel engines since 1948, when it set up its first remanufacturing plant at a former BMW aircraft engine repair factory at Ubersee, in Upper Bavaria. Today some 170 employees at Ubersee produce around 4,000 Xchange engines annually as well as replacement parts. “Xchange engines provide a very fast and effective solution when an engine that is out of production needs replacing – around half of all orders fall into this category – or when, for example, an engine that is in 24 hour a day use needs a similar unit to be supplied quickly,” explains Michael Wellenzohn, Chief Sales and Marketing Officer. “We can deliver a replacement motor in two to eight days whereas for a new engine the time between order and delivery is more like four to eight weeks. And all our replacement engines come with the same kinds of guarantees as our new units.”
Xchange engines are also produced at Deutz’s 50,000 sq ft facility in Atlanta, Georgia, in the USA. This plant, which serves as the administration hub for Deutz Xchange engines, parts and service throughout the Americas, focuses on production of the company’s 1011/2011 and 912/913 engines, the highest volume units sold in North America, as well as of its 2012 and 2013 models.
Deliveries of spare parts for Deutz engines in Europe are mostly handled by the company’s ultra-modern logistics centre in Cologne-Kalk. Opened in 2001, this facility holds some 80,000 parts, from precision crankshafts to the smallest washers, and fulfils an average of nearly 700 orders every day – that’s equivalent to 4000 automated picks from the storage racks daily. From this centre Deutz supplies customers and dealers all over the world with spare parts and within Europe itself it can guarantee next day delivery. The parts supply operation in Cologne is supplemented, of course, by parts warehouses in the USA as well as in China and Singapore and through stocks at dealerships throughout the world.
Expanding in China
Deutz has two joint ventures in China. Since 2007 it has been producing 3 to 8 litre diesel engines, mainly for the Chinese market, in a JV (Deutz (Dalian) Engine Co Ltd)with the First Automotive Works Group (FAW) in Dalian; these units are widely used in commercial trucks, off-highway vehicles and for stationary applications. The JV also acts as a supporting manufacturer for crankcases, cylinder heads and camshafts for the Cologne assembly plant.
At the beginning of 2012 Deutz extended its operations in China by setting up a further JV with Shandong Changlin Machinery Group – a Chinese manufacturer of agricultural machinery and construction equipment. Deutz (Shandong) Engine Company now manufactures the million-selling 2011 engine series.
Limiting emissions
One of the greatest challenges facing diesel engine manufacturers today is making their products compliant with current and future exhaust emission regulations. This means reducing the concentration of pollutants such as NOx (nitric oxide), CO (carbon monoxide), HC (hydrocarbons), particle emissions and CO2 (carbon dioxide).

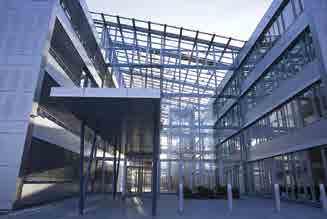
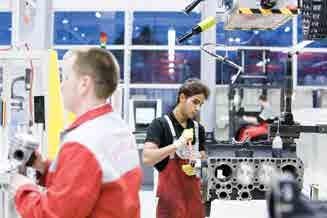

“This is undoubtedly a great challenge to engine manufacturers and will require the addition of further technology modules to our engines. It’s really like having to construct a small chemical plant around each engine to treat the exhaust gases. To reduce CO and HCs, for example, you need a Diesel Oxidisation Catalyst system, to remove particulates you need a Diesel Particulate Filter and to remove NOx you have to have a Selective Catalytic Reduction system. The last of these injects urea into the exhaust but that creates ammonia so you need another filter to take that out.
“Of course the simplest way to reduce pollutants is to improve engine performance and efficiency and reduce fuel consumption with established technology such as fuel injection, turbo-charging and electronic engine management systems and we have been doing that for years. But the continuing demands of regulation are very costly for the industry and make it ever harder to get a payback so it’s essential that we continue to develop ever-smarter solutions.”
Worldwide service
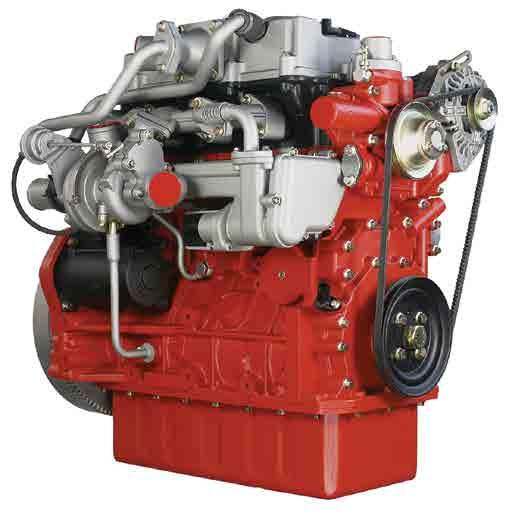
Extending its sales in the agricultural sector is not the only strategy that Deutz is pursuing to support its future growth. The company is also focused on continuing to take market share from its competitors in the construction and stationary applications areas worldwide and on adding value to its engines by providing complete power packs, including control units, frames and systems interfaces. But perhaps most important of all for the future is the expansion of Deutz’s global service business.
“The complexity of our engines has increased considerably over the last ten years, most obviously through the addition of all the different exhaust treatment systems, so whereas in the past an end user such as a construction company could service its own machines, today it is essential for servicing to be carried out by trained specialists,” says Mr Wellenzohn. “That means that we have to put a lot of work into training our distributors and service partners throughout the world to ensure that the end customer gets the service at the distributors and in the field that keeps his equipment running. When we provide this complete service it brings us closer to our end customers who are then more likely to ask their equipment suppliers – our direct customers – to specify our engines. Effectively we are then approaching the market from two sides – getting OEMs to use our engines and encouraging end-users to ask the OEMs to use our engines. What’s certain is that if you don’t deliver a comprehensive and efficient service package, you don’t sell engines in today’s market. Deutz will never make that mistake – we are, after all, ‘The Engine Company’. n