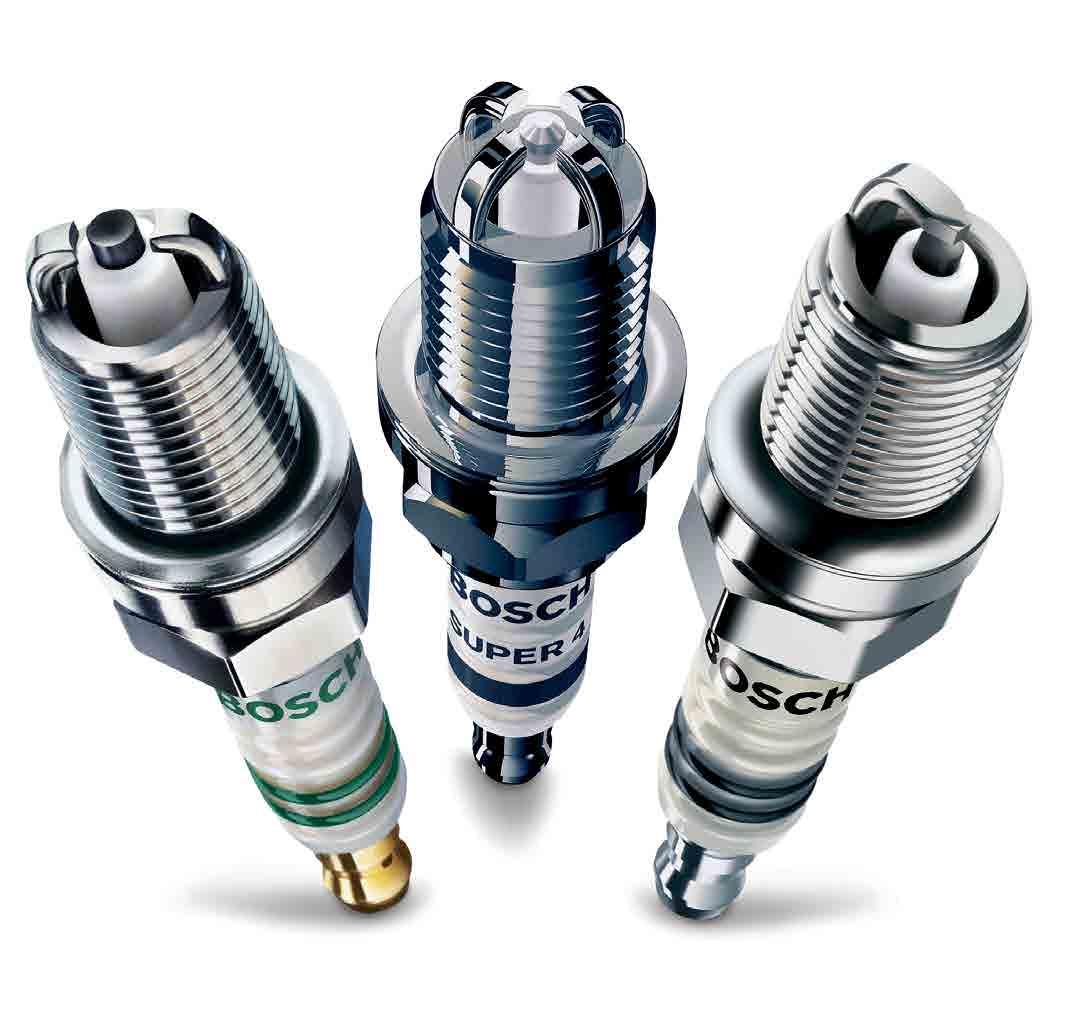
11 minute read
Advanced technology for local needs Bosch Group
ADVANCED TECHNOLOGY FOR LOCAL NEEDS
A new diesel systems plant in India is just the latest stage in the growth of the Bosch Group’s commitment to sustained growth in the country, where it has been active in manufacturing for over 60 years.
IN August 2015 Bosch, the global supplier of innovative technology to the automotive, industrial, consumer, construction and energy industries, officially inaugurated a new state-of-the-art diesel systems manufacturing facility at Bidadi, Bengaluru, in India.
The Bidadi plant is the 14th manufacturing facility that Bosch has established in India since it set up its first production operation in the country in 1953. Total investment in the new plant has been around €45 million since the project was begun in September 2013 and the second phase of construction is due to be completed by 2018.
The new factory is, in fact, the fifth production unit that Bosch has opened in the state of Karnataka in southern India. It will produce diesel products that were previously manufactured at the Adugodi plant, which is also located in Bengaluru, and will employ more than 2600 people. Bidadi will now be the lead plant for the production of single cylinder common rail diesel pumps as well as conventional fuel injection pumps. In phase one of the development Bosch will start production of the common rail fuel injection pumps at Bidadi and expects to be producing the newer version of the pumps by 2016–17.
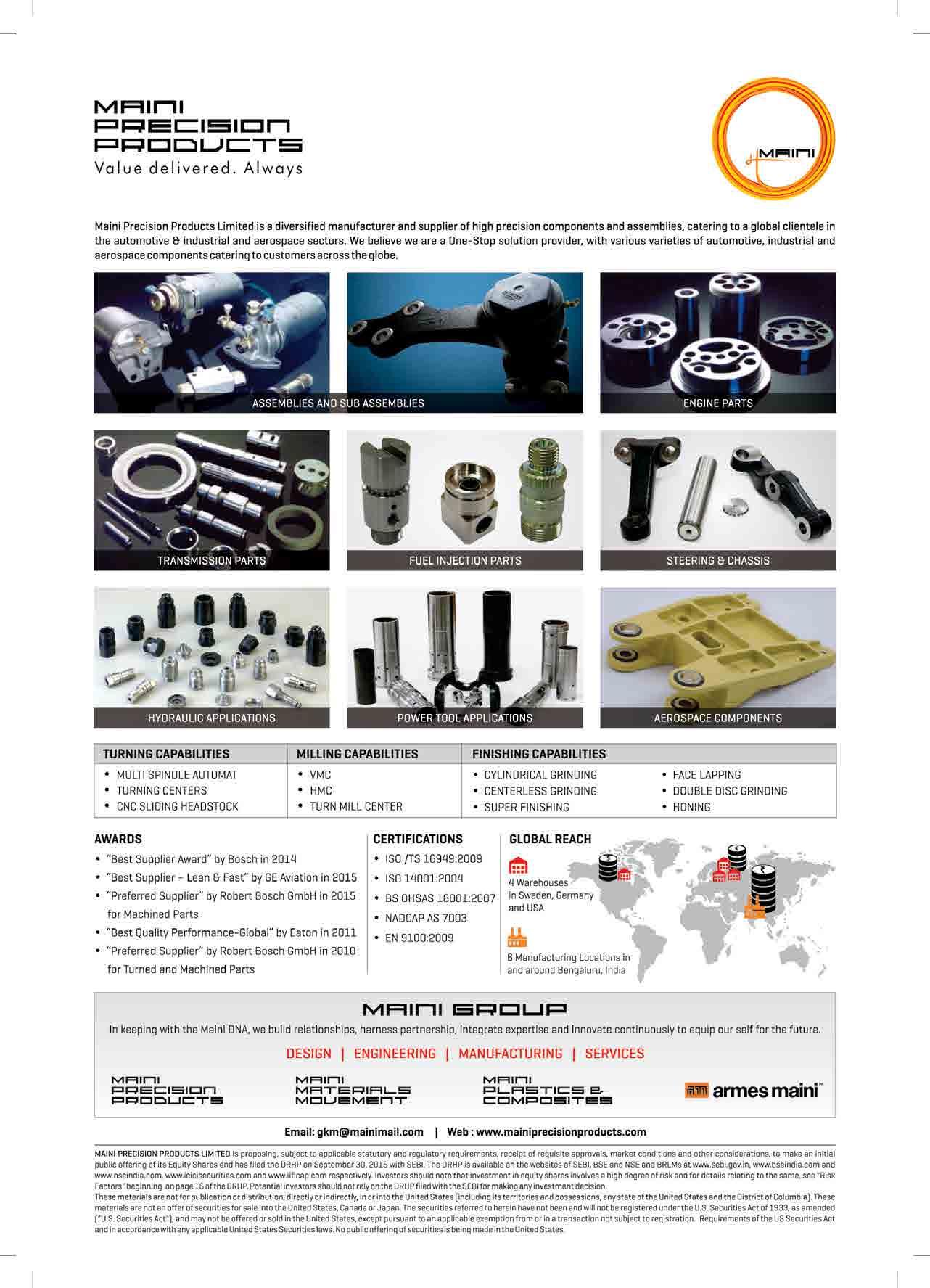
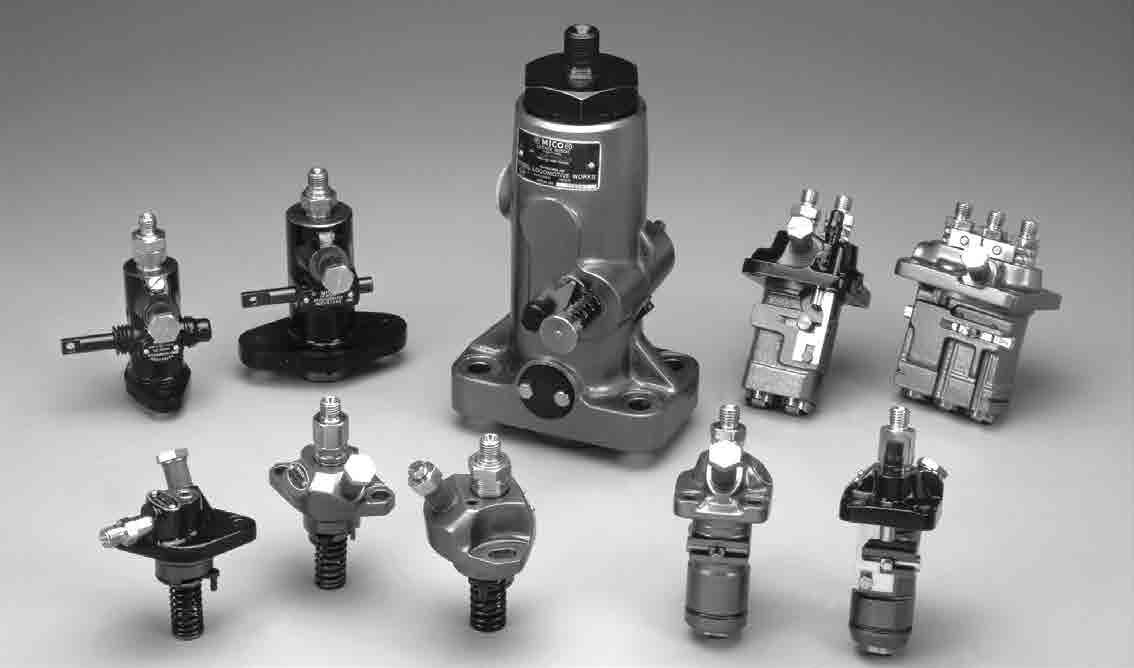
“The developing industrial area in Bidadi will offer more space and better infrastructure support for our future expansion,” said Dr Steffen Berns, president of Bosch in India and managing director of Bosch Limited, the flagship business of Bosch in India, which has its headquarters in Bengaluru. “We see a lot of growth potential in India and are striving to bring more projects, products and manufacturing to the country. Our growth here is interwoven with the close relationship we have with the State of Karnataka and we look forward to further enriching this partnership.”
New gasoline systems plant
The start-up of the Bidadi Diesel Systems plant came only seven months after the inauguration of a new Bosch manufacturing facility dedicated to production of gasoline fuel injection systems. Opened in January 2015, the plant at Gangaikondan, Tamil Nadu, in south east India, was Bosch’s sixth manufacturing plant in the country and is already playing a crucial role in Bosch’s strategy to enter the highly competitive two-wheeler market in India with electronic fuel injection systems. The new plant is producing power train sensors, fuel delivery modules and air management components for both automotive and two-wheeler applications. Before the opening of this new plant the Gasoline Systems division shared the Bosch Naganathapura facility, in the state of Karnataka, for local production of its fuel injection systems. Naganathapura is part of Bosch’s Automotive Electronics business in India and produces spark plugs, starter motors, alternators and generators.
Moving gasoline injection systems production to the new Gangaikondan facility has enabled Bosch’s Gasoline Systems business to further localise manufacturing and increase cost competitiveness. Commenting on the significance of the investment last January, Dr Steffen Berns said, “It is important for our Gasoline Systems business division to have a strong manufacturing footprint in an important and growing market such as India. The expanded local production capabilities in this state-of-the-art location will help Gasoline Systems to further grow its market share with a highly competitive product portfolio.”
Bosch in India
In the Indian market Bosch is a leading supplier of technology and services in the areas of Mobility Solutions, Industrial Technology, Consumer Goods and Energy and Building Technology. The company operates in India through a total of nine companies – Bosch Ltd, Bosch Chassis

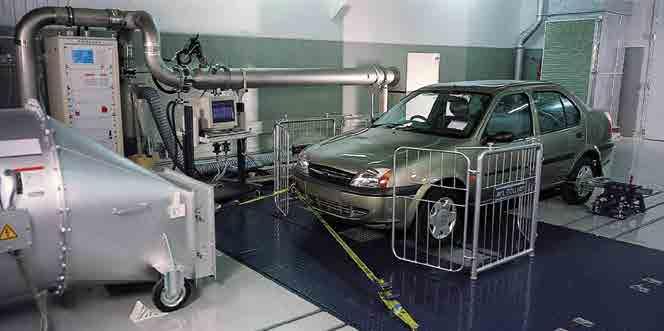
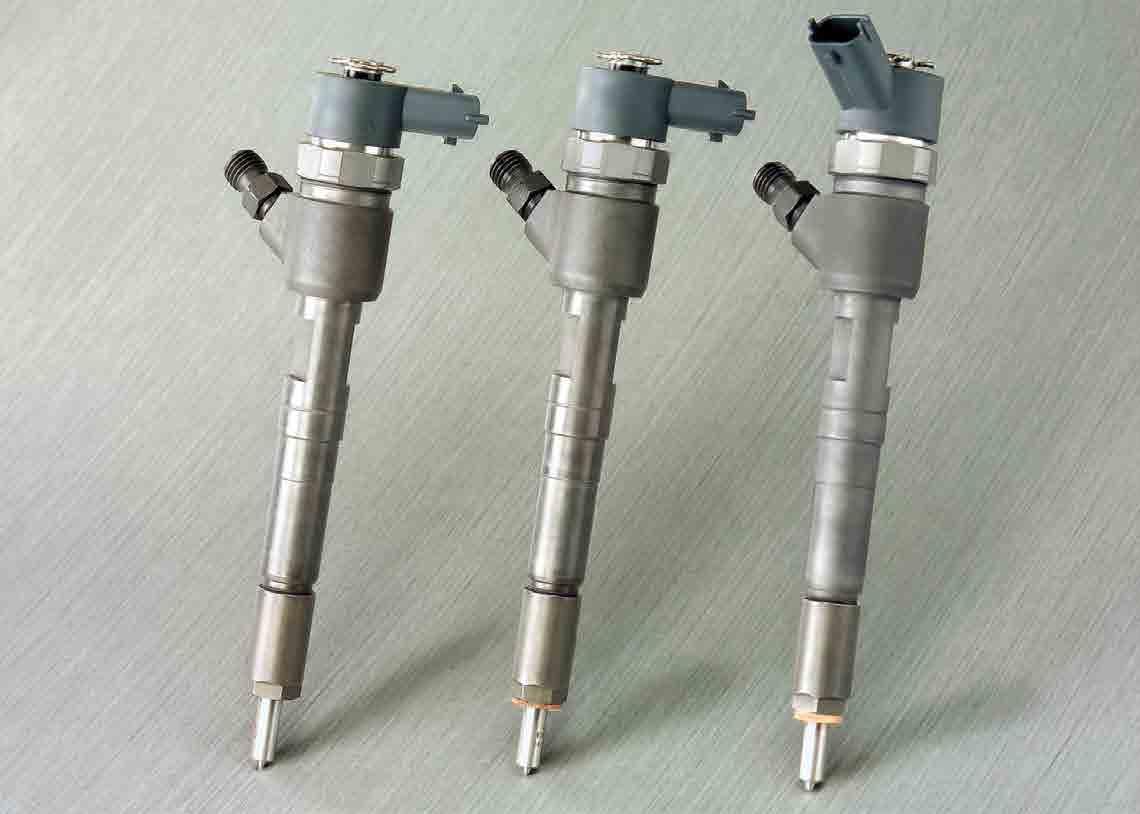
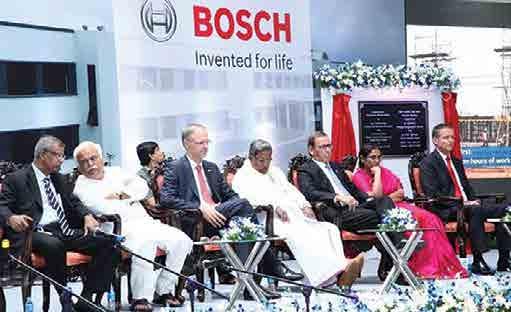
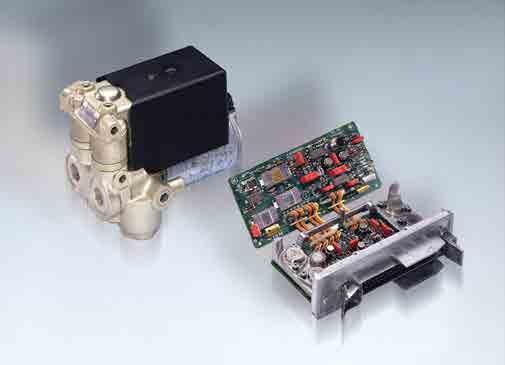
Systems India, Bosch Rexroth India, Robert Bosch Engineering and Business Solutions, Bosch Automotive Electronics India, Bosch Electrical Drives India, BSH Home Appliances, ETAS Automotive India and Robert Bosch Automotive Steering India. Since its manufacturing operations began in the country in 1953 they have grown to include 14 manufacturing sites and seven development and applications centres employing a total of more than 29,000 people. India is also home to the largest Bosch development centre outside Germany and the company employs some 12,000 research and development specialists.
Bosch Limited, the largest of the company’s businesses in India with a workforce of some 12,000, produces a wide range of products, including diesel and gasoline fuel injection systems, automotive aftermarket products, auto electricals, packaging machines, electric power tools and security systems. It operates manufacturing facilities in Bengaluru, Nashik, Naganathapura, Jaipur and Goa and in the last year opened three new plants – the diesel systems plant at Bidadi, the gasoline systems plant at Gangaikondan and a power tools factory at Chennai. In 2014–15 Bosch’s Diesel Systems division achieved growth of close to 10 per cent and the Gasoline Systems division also registered strong double digit growth. Dr Berns commented that the company’s localisation approach to the Indian market had been a key factor in achieving this growth. “In the past year we further expanded our market presence in the automotive aftermarket segment by adding around 300 new distributors to our sales network,” he added.
In spite of the current challenging market conditions in its major sectors, Bosch sees continuing prospects for significant growth in its Indian businesses. “We are making pro-active investments for infrastructure

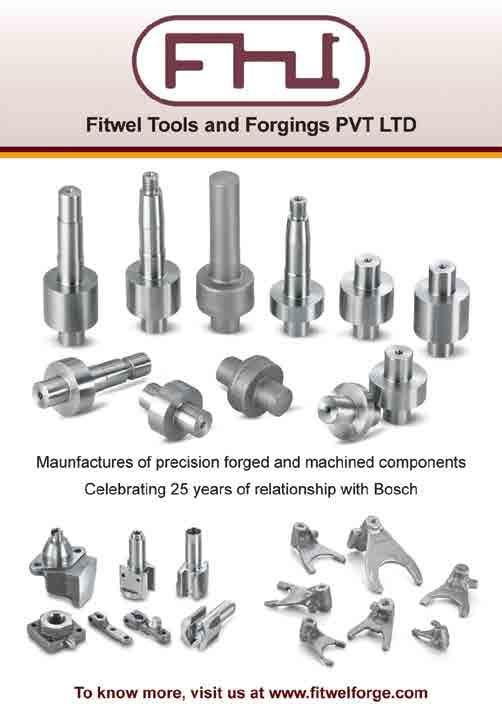
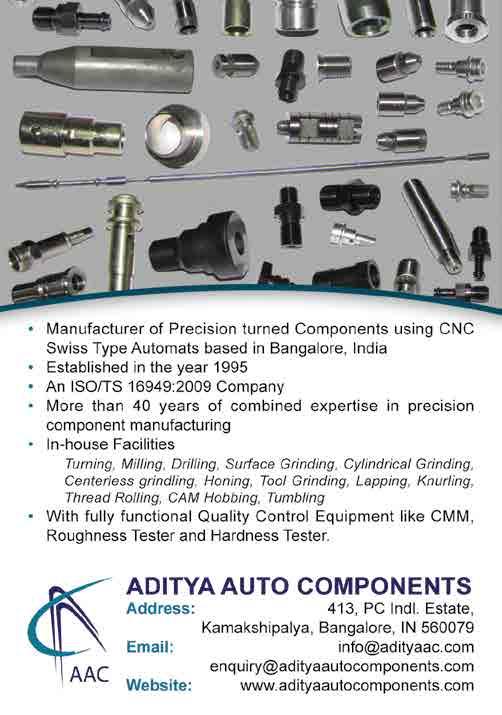
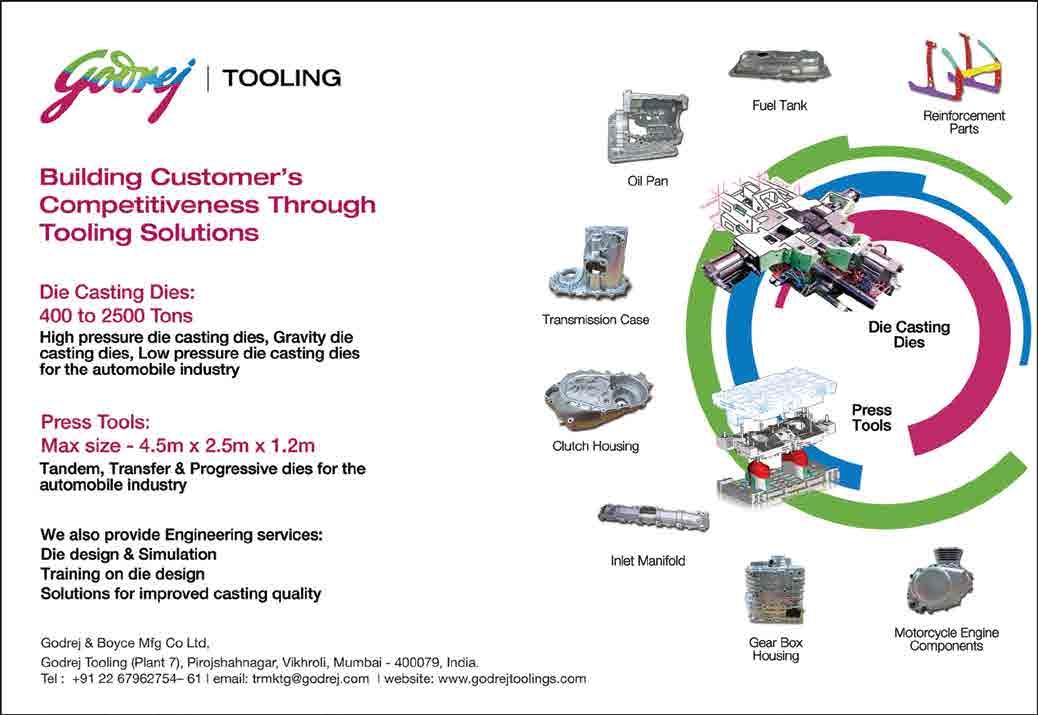
Godrej Tooling – a new link in Bosch SCM
Godrej Tooling, India, has been serving automotive multinationals for the past 20 years. An important opportunity to serve the German OEM came in the form of a major assignment from world-renowned producer Bosch.
The challenge was this: Bosch’s existing suppliers in India had been struggling to meet the basic production and quality requirements owing to a high rejection rate of 30 per cent. It entrusted Godrej with the task of finding a solution to this problem.
Working in close collaboration with Bosch’s experienced team, Godrej was able to design brand new Dies with innovative Slider in Slider concept to address the near-impossible squeezing action at the center profile. An extensive network of jet cooling and spiral cooling arrangements with intermittent cooling cycle were used to address the critical problem of porosity.
The result? At the first trial itself the parts were observed to be 95 per cent acceptable. In mass production this was improved further with less than 3 per cent rejection. Yield was improved by up to 58 per cent.
Godrej Tooling is proud to be associated with Bosch and hopes to continue working with such challenging assignments and growing alongside them.

and technology including efficiency improvements on our products with regard to new emission regulations and CO2 reduction measures,” said Dr Berns. “The market performance in the coming quarters will be determined by factors such as fuel prices, interest rates and the speed of execution of government reforms, as well as by the monsoon season. We expect moderate growth in the Indian automotive industry this year and are cautiously optimistic.”
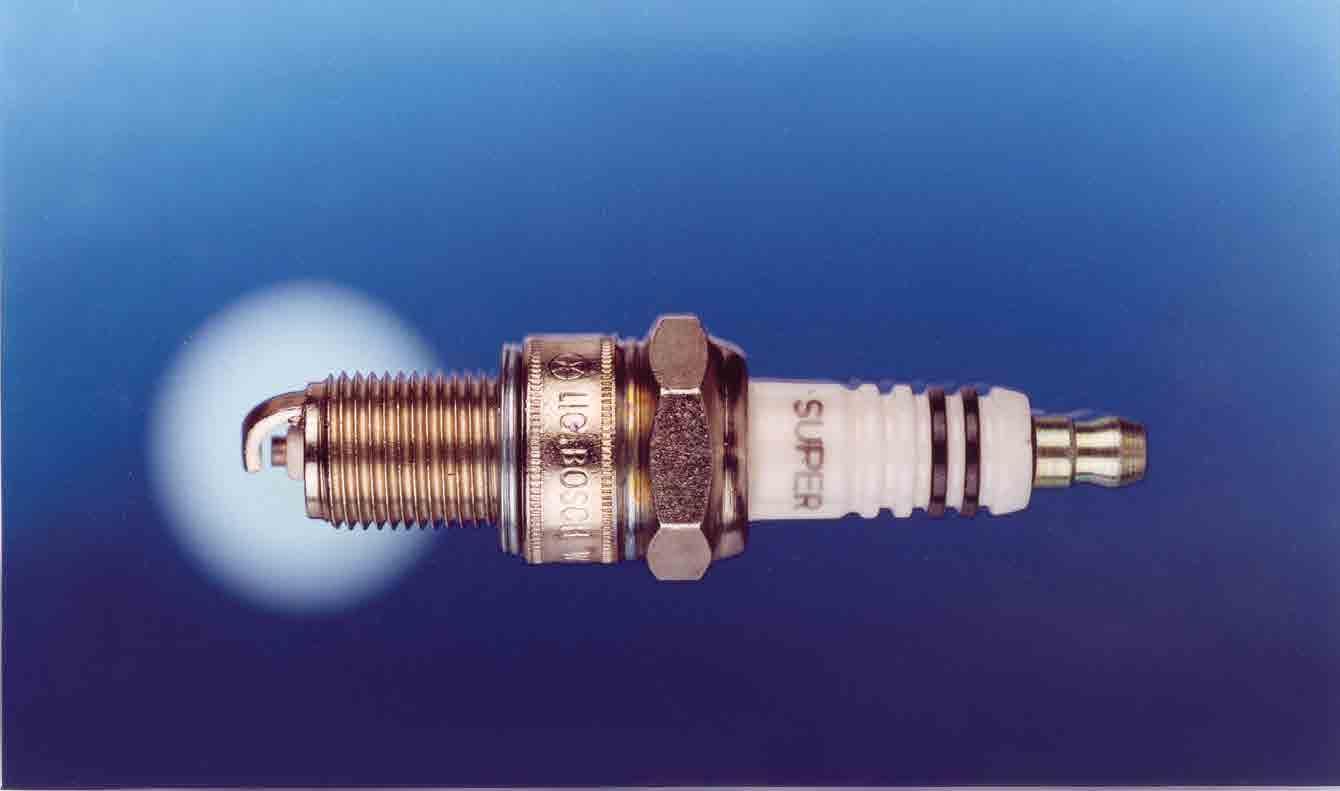
Connected production
A key driver in this expected growth will be the Indian government’s success in improving the business environment in the country to ensure continuing growth in the economy. Bosch expects to see positive developments in the country over the medium and long term; indeed India’s economy is expected to grow by some six per cent this year.
“The new Indian government is systematically addressing key issues such as infrastructure, education and reducing bureaucracy,” said Dr Berns. “Especially in the areas of mobility, infrastructure, industry, energy, security, packaging and health care there are many opportunities for our products and solutions.”
In particular, the new ‘Make in India’ initiative, which aims to advance industrialisation in the country and to modernise production, opens up exciting possibilities for Bosch in the field of ‘connected production’. “We believe that the use of intelligent and connected solutions in manufacturing will play an increasing role in India and Bosch is very well positioned to assist in this,” said Dr Berns. The company already offers a wide range of relevant technologies and services such as drives, automation solutions, sensors, software and predictive maintenance and it is already cooperating closely with partners in Germany and in India to develop connected solutions. It is working, for example, with the IT companies Cisco (in the USA) and Tech Mahindra (in India) to drive forward connectivity in industrial tools as part of the Industrial Internet Consortium.
Bosch’s new research and development centre in Bangalore is taking a lead in these programmes, focusing on areas such as connected technology for the internet of things. Its engineers have, for example, developed software which links all the machinery in a manufacturing faci9lity and enables the collection and analysis of data in real time. This enables production status to be constantly monitored and a material shortages as well as machine failures to be resolved quickly.
The development centre has also recently been focusing on big data analysis. A software model that it has developed for manufacturing performs statistical analysis on the basis of algorithms, enabling specific predictions to be made and changes to be detected. It can be employed in factories to reduce throughput times, enable predictive maintenance and optimise resource use as well as to improve the management of capacity, inventory and logistics. Bosch itself uses this kind of manufacturing data at its plants in Bangalore and Jaipur, for example, to shorten throughput times in the testing and calibration of diesel injection pumps.
Connected technology is also at work throughout Bosch’s logistics procedures worldwide. In its diesel plant in Nashik, for example, RFID radio tags monitor the progress of workpieces through the factory by identifying the position of transport crates. These tags enable precise details to be known about the process steps that each piece undergoes and when the injectors will be ready so that precise schedules can be drawn up for packing, shipping and installation.
In emerging markets such as India Bosch also focuses on locally developed solutions that are specifically tailored to the requirements of the local market. These have included an electronic hitch control for Indian tractor manufacturers and a common rail system for small engines as well as an affordable and robust engine management system for specially designed for the booming Indian two-wheeler market.
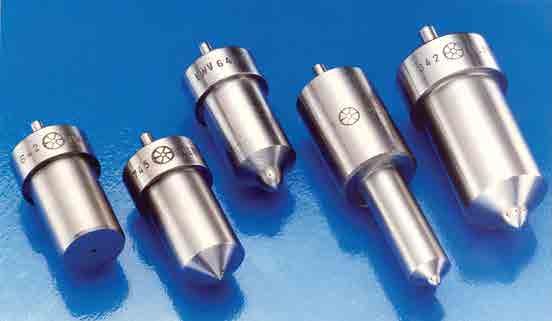
Technology for eye care
Bosch India’s Bangalore development centre is not only focused on innovation for the mobility solutions sector. A recent non-mobility project, for example, has been the in the field of eye care. Engineers at the centre have developed a compact retinal camera with special software that can detect conditions such as cataracts at an early stage.
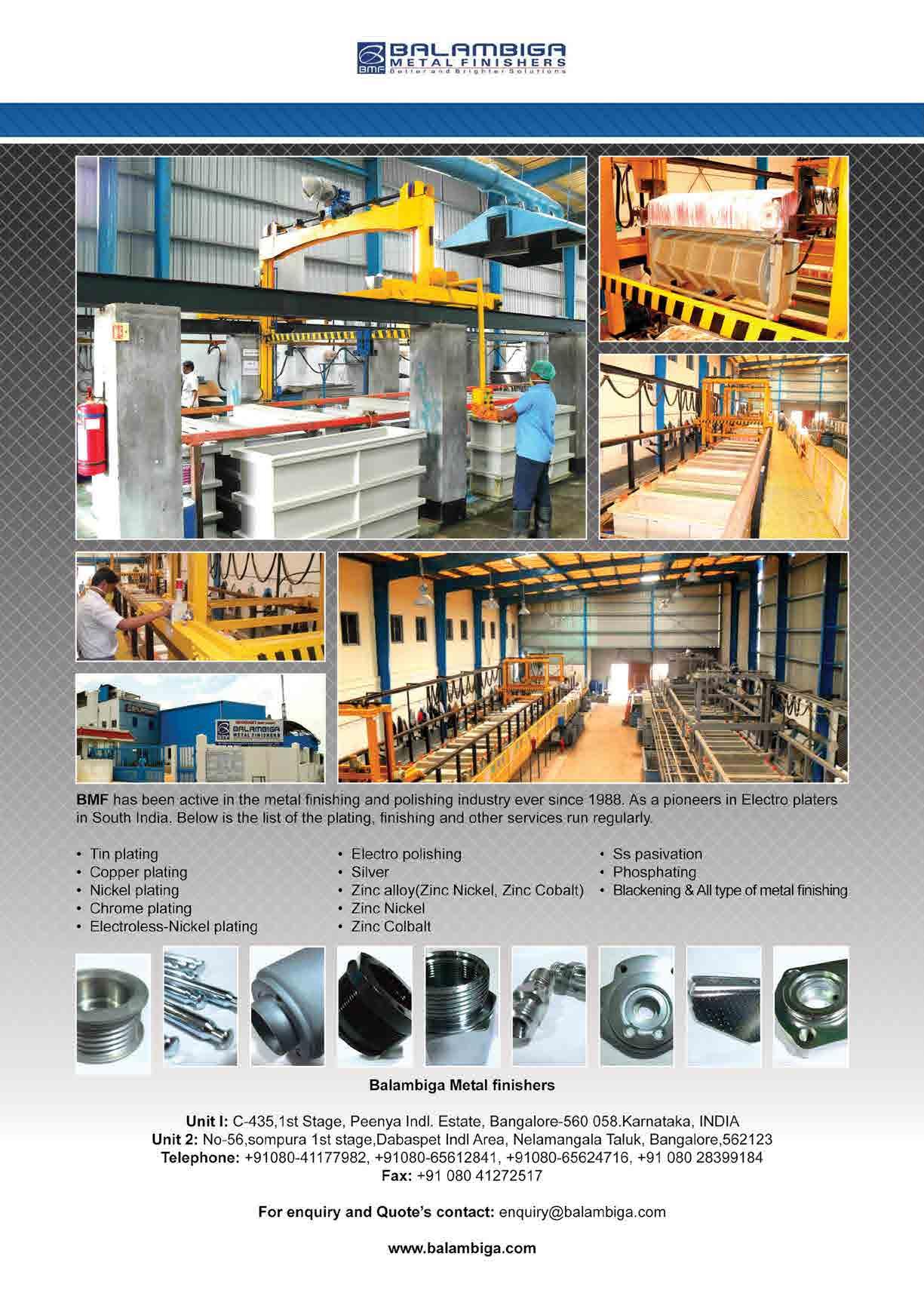
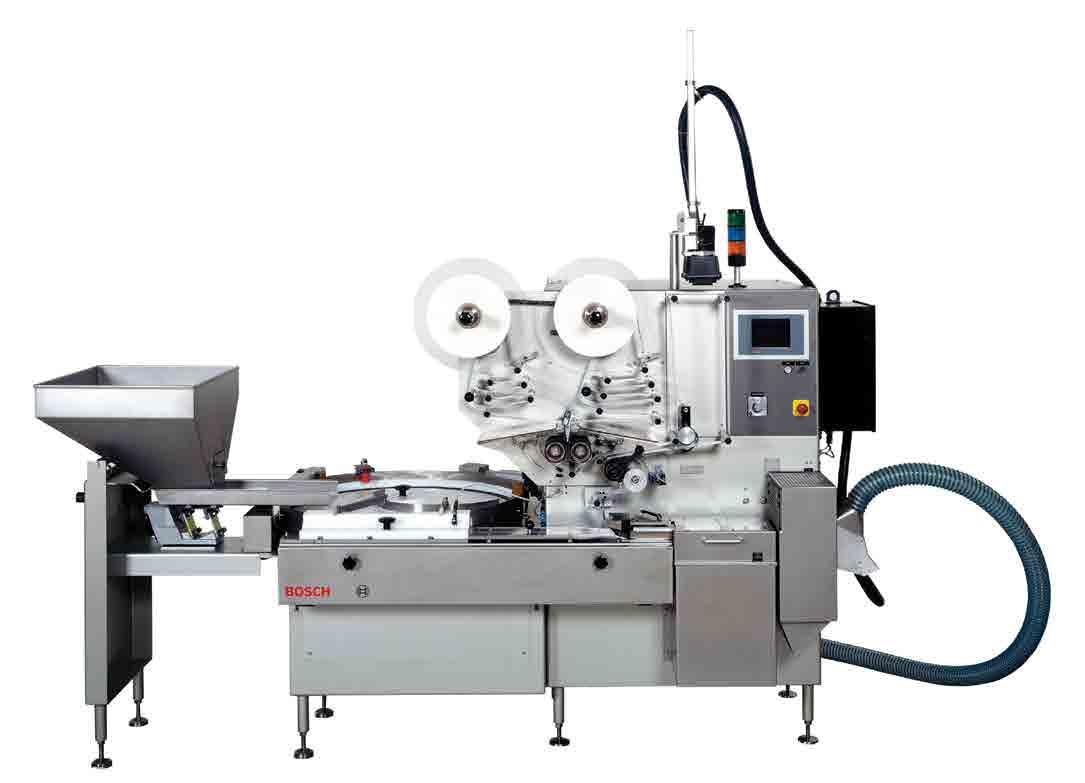
The Bosch Eye Care camera operates on a rechargeable battery so it is lightweight and portable and its findings can be shared over tele-medicine using Bosch’s MediBilder software. The automated detection algorithm can detect and mark conditions such as diabetic retinopathy and glaucoma enabling comprehensive eye screening to be carried out at a primary level,
Bosch is working with India’s Aravind Eye Care System to create ‘vision centres of the future’; a programme is already in place to equip around 50 Aravind Eye Care centres with the camera systems.
Energy solutions
Another important and growing business in the Bosch non-mobility sector is Bosch Energy and Building Solutions (BEBS) which has been delivering solar energy projects in India since it was set up in 2014. In August this year BEBS commissioned a 12 MW solar project for Cochin International Airport (CIAL); covering some 50 acres, this is the largest single solar project that has been constructed at any airport in India and will generate around 50,000 units of electricity each day, making the airport completely ‘grid power neutral’.
“Based on installed capacity, CIAL is the largest project that has been executed by the Bosch Energy and Building team in India to date,” said Dr Steffen Berns. “We draw strength from our broad-based technical know-how and experience, our pan-India presence and understanding of the different regions of the country, as well as strong local competence to deliver customised design and engineering projects. India has the potential to achieve the government’s ambitious target of 100 GW of solar power generation in the country by 2022 and Bosch is committed to being a significant part of this success story.” n
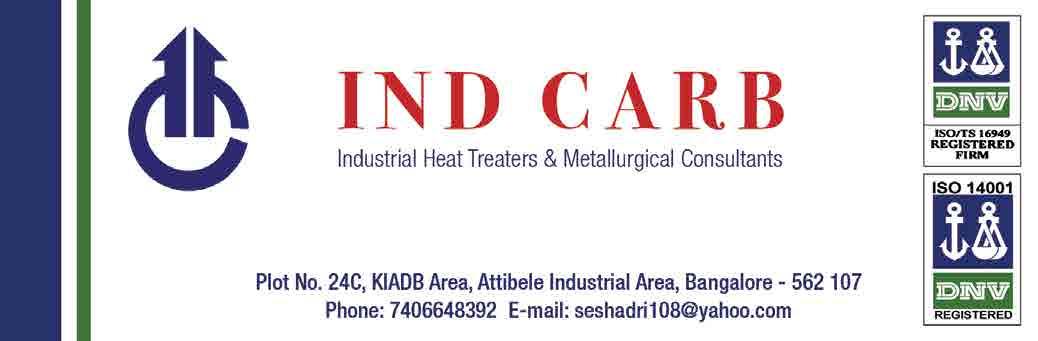