
5 minute read
Global leader in high-pressure vessels
GLOBAL LEADER IN
HIGH-PRESSURE VESSELS
Austrian Schoeller-Bleckmann Nitec GmbH designs and builds high-pressure vessels for the chemical and petrochemical industries. It is one of the global market leaders in industrial apparatus engineering for the fertiliser industry. Marco Siebel spoke with CEO Hermann Kernberger to find out more.
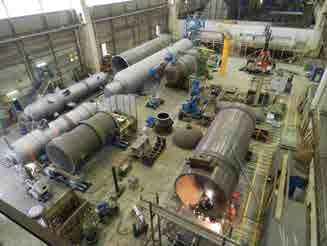
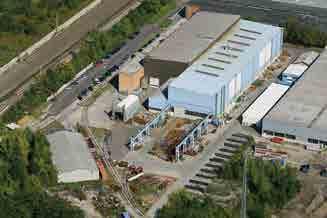
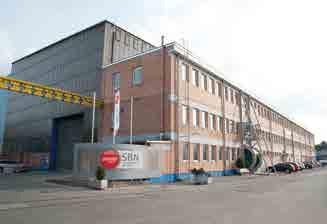
Schoeller-Bleckmann Nitec employs 150 people whose efforts generated a turnover of €50 million in 2014. The company has four production sites, of which two are in Ternitz, a town south of Vienna. The history of the company goes back to 1862, when Alexander Schoeller acquired the iron and steel works in Ternitz. In 1935 Schoeller-Bleckmann began the manufacturing of vessels for the chemical, food and drink industries. In the past 30 years the company has positioned itself as a producer of industrial vessels for the fertiliser industry. Schoeller-Bleckmann Nitec GmbH has been part of the group J. Christof Apparatebau Beteiligungs GmbH since 2008. Vessels for the fertiliser industry
Schoeller-Bleckmann Nitec (SBN) produces high-pressure heat exchangers and high-pressure reactors for urea and ammonia production to be used in the fertiliser industry. The reactors are cladded in highly corrosion-resistant materials, and have built-in liquid distribution systems. The materials used for these products include heat-resistant chrome-nickel steels and nickel-based alloys, as well as pressurised hydrogen resistant steels. The welding is computercontrolled using software developed by Schoeller-Bleckmann Nitec’s own team of engineers and programmers.
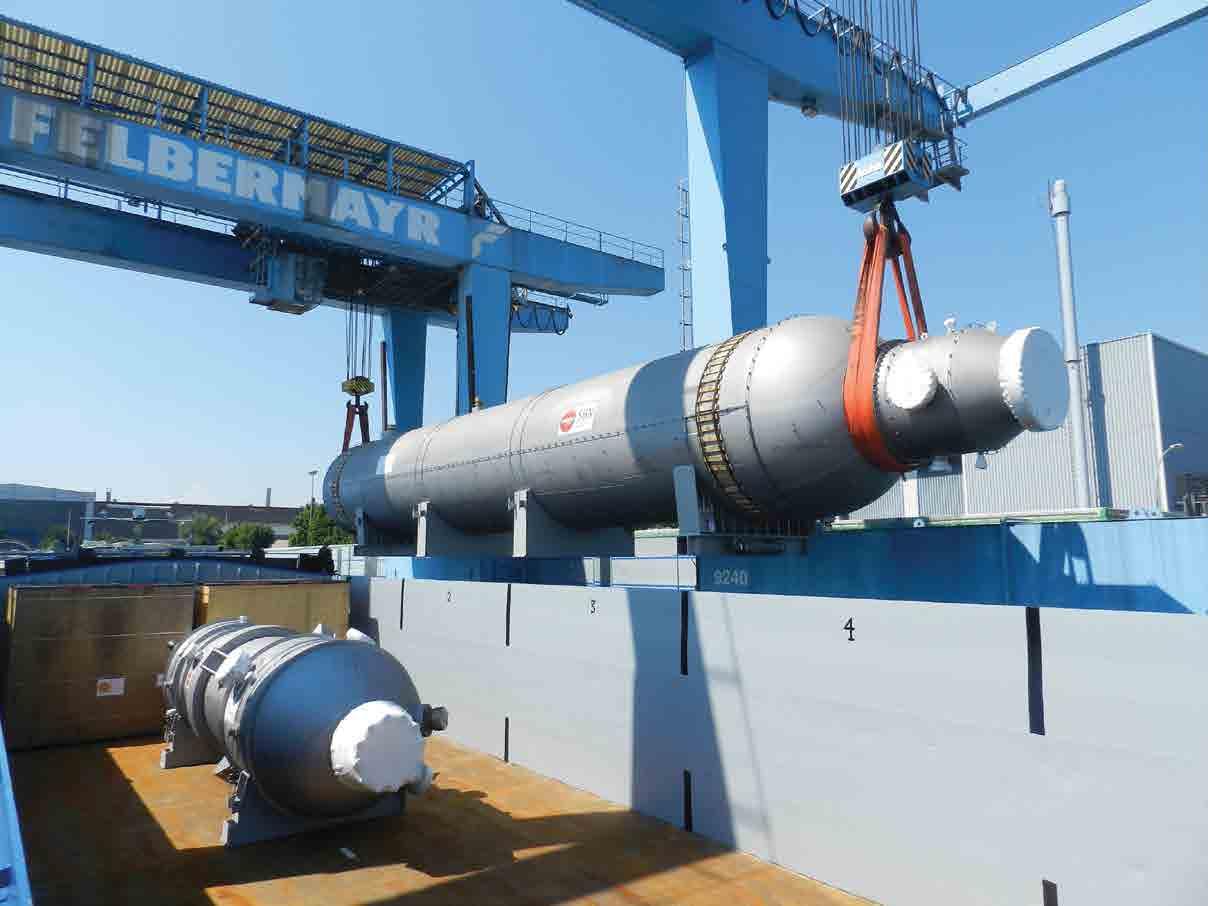
Hermann Kernberger says: “We have some customers in Europe, but most of our vessels are exported to countries in North America, Asia and the Middle-East. Iran is buying a lot, simply because they have the raw material – natural gas – in huge quantities. In China they convert coal to synthetic natural gas. All these SBN customers manufacture the fertilisers that they then export to the agricultural industries abroad.”
Vessels for chemicals and petrochemicals
SBN supplies high-pressure vessels and components for the chemical and petrochemical industries, whether it’s processing crude oil and gas, or processing intermediates and finished products. The company is renowned for its heat exchangers, reactors, separators and columns. Materials used include carbon steels, low-alloyed steels for hydrogen service under elevated temperatures and pressures, austenitic chrome-nickel steels, nickel-based alloys as well as pure nickel or titanium.
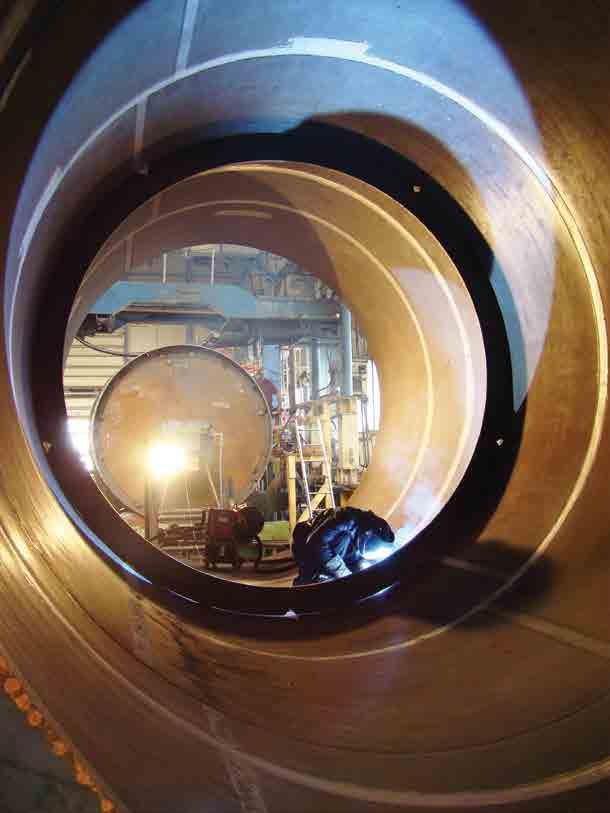
Monowall or multilayer-wall
SBN’s vessels are built either in monowall or multilayer-wall construction. SBN offers high-pressure reactors in classic monowall designs with wall thicknesses of up to 300mm. The high-pressure shell sections are either manufactured from hot rolled and longitudinally-welded plates or from seamless forged shell parts. SBN’s multilayer design is used where high pressures are combined with large-dimensioned high-pressure vessels and shell lengths, for example in urea reactors, pool condensers and pool reactors or ammonia converters.
Hermann Kernberger continues: “To ensure that the high-pressure equipment we manufacture for the fertiliser industry is state-of-the-
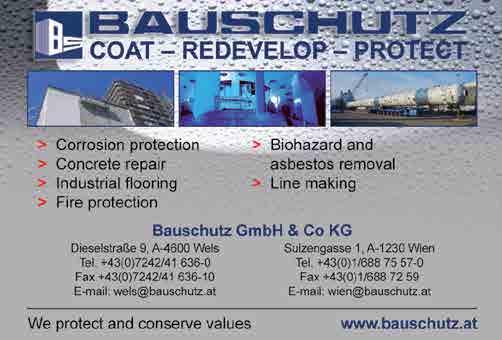

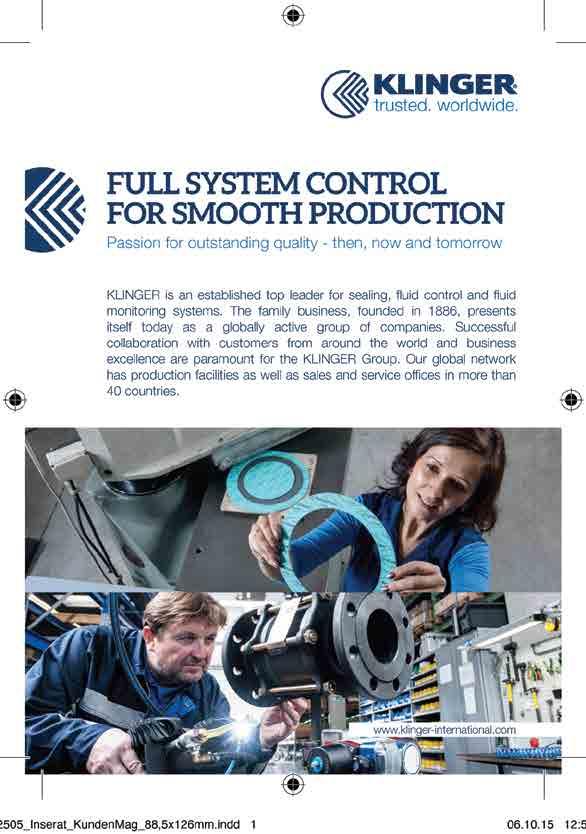
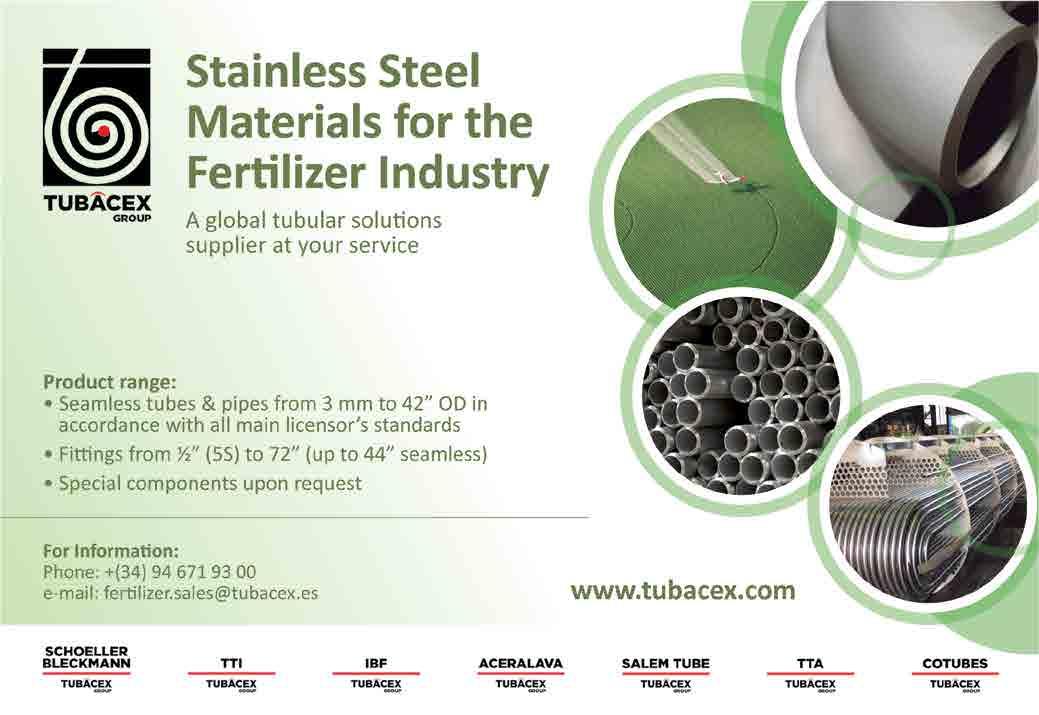
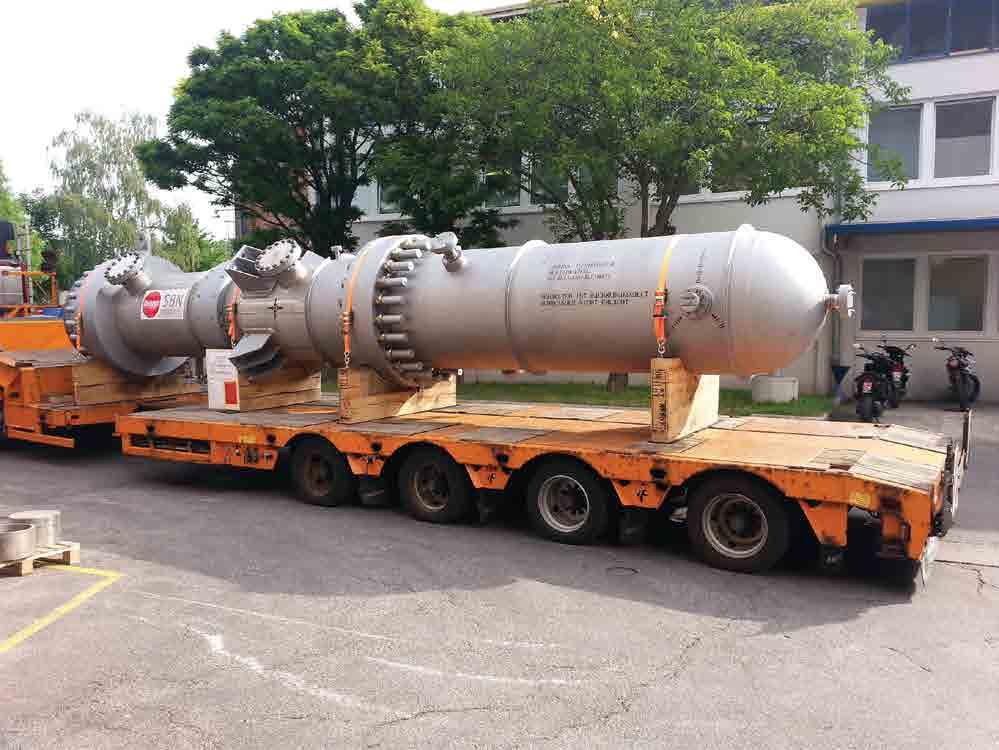
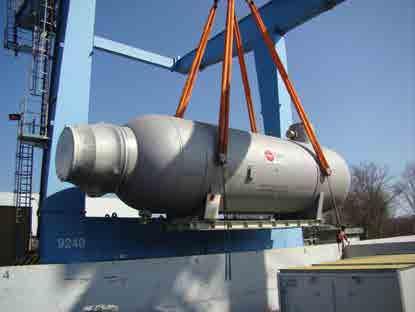
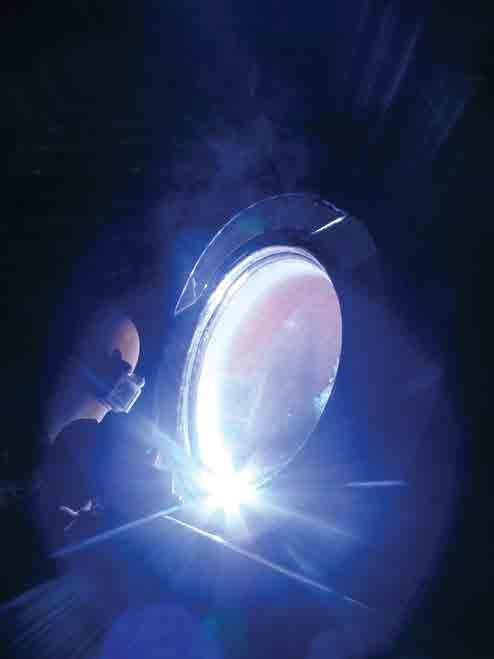
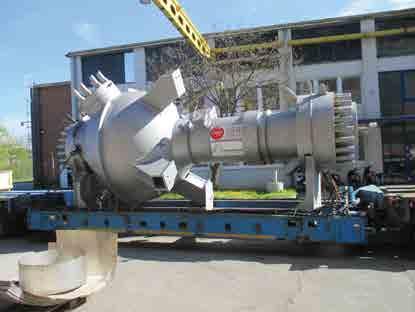
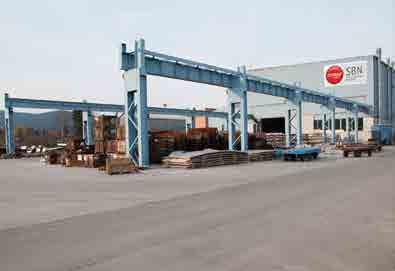
art, we have long maintained close working relationships with licensors and material producers. SBN was a pioneer in the extensive use of Safurex – a super duplex grade developed by Swedish steel producer Sandvik AB and the Dutch process licensor Stamicarbon BV. Our engineers developed the necessary welding technologies in conjunction with Sandvik. We are now working on the next generation of pool condensers and pool reactors, according to Stamicarbon’s Urea 2000 process, which significantly increases productivity in urea plants.”
Advantages of SBN’s multilayer design
Manufacturing the shell from elements with low thicknesses produces better metallurgical characteristics, such as higher yield strength and higher stability. Significantly greater safety reserves are achieved to prevent the spread of damage through the entire vessel wall.
Hermann Kernberger adds: “For processes involving high corrosion attack, either the core shell is produced from corrosion-resistant material or an appropriate loose lining is installed. The higher the operating pressures and diameters or lengths of the pressure vessel are, the more advantageous is the weight ratio between multilayer and monowall design.”
Production in Ternitz is concentrated in two buildings with a total floor space of more than 5000m2. All prefabrication stages are carried out in a new 3000m2 pressure vessel shop with CNC vertical lathe and BTA deep hole drilling machines, manipulators with capacities of up to 100 tonnes, and six cranes with lifting capacities of up to a maximum of 240 tonnes. SBN has the entire range of the necessary welding equipment, including TIG, MIG and MAG and coated rod welding, submerged arc wire and strip overlay welding, and computerised tube-to-tubesheet welding (conventional and innerbore). There are also a large number of vessel rotators with capacities of up to 500 tonnes.
Hermann Kernberger concludes: “The increasingly larger dimensions and weights of the equipment forced us to invent new ways of manufacturing: our welding processes have changed, along with the knowledge level of our employees. Because of size and weight restrictions on road and rail transport, we have started to scout out new production sites close to the sea. We already have a production site in Linz on the Rhine-Main-Danube Canal, and are now looking for a fifth production site near the sea, either in the Netherlands, Belgium, northern Germany, or Poland.” n
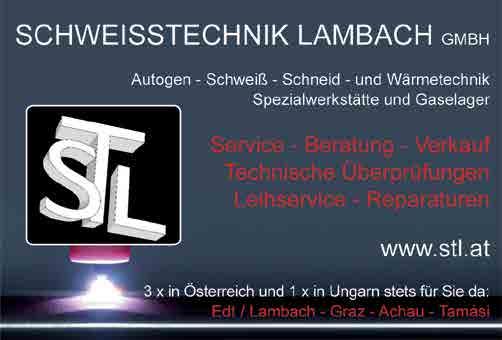