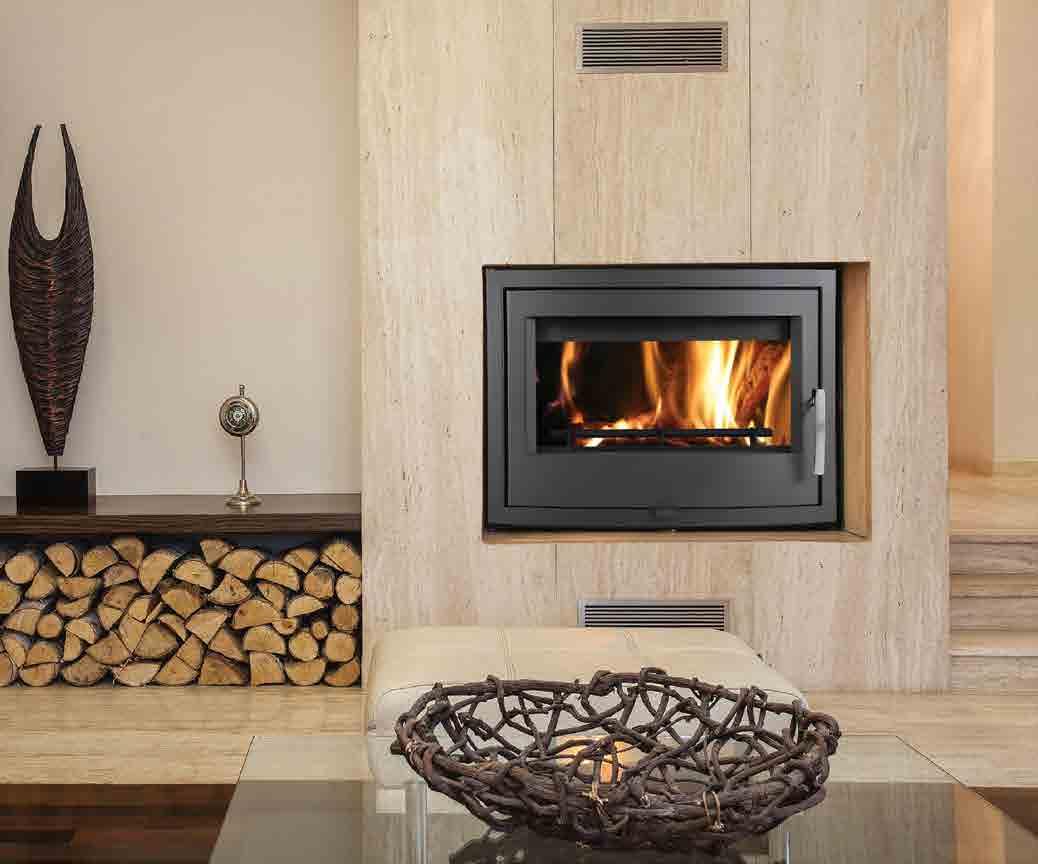
5 minute read
Bringing warmth into your home THORMA
BRINGING WARMTH INTO YOUR HOME
Slovak THORMA, a major producer of stoves and log burners, is seeking to widen its product portfolio and penetrate new sectors. Romana Moares spoke to managing director Jan Sykora about the company’s plans for the future.
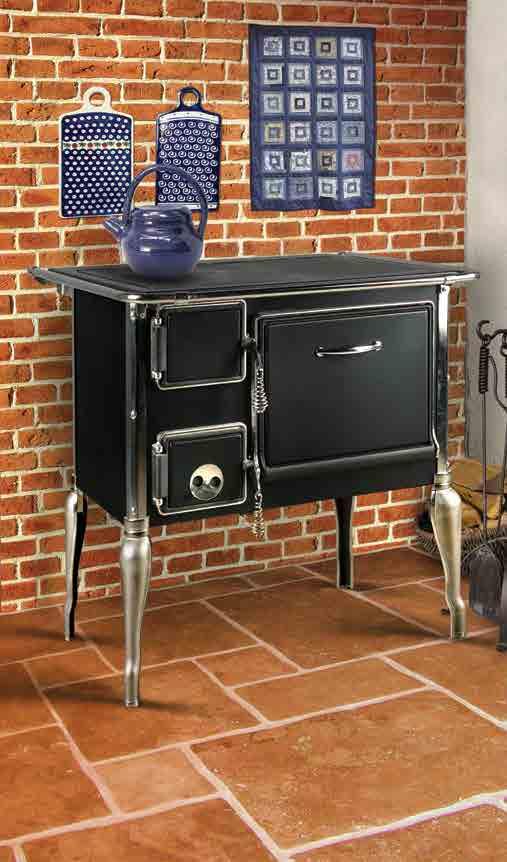
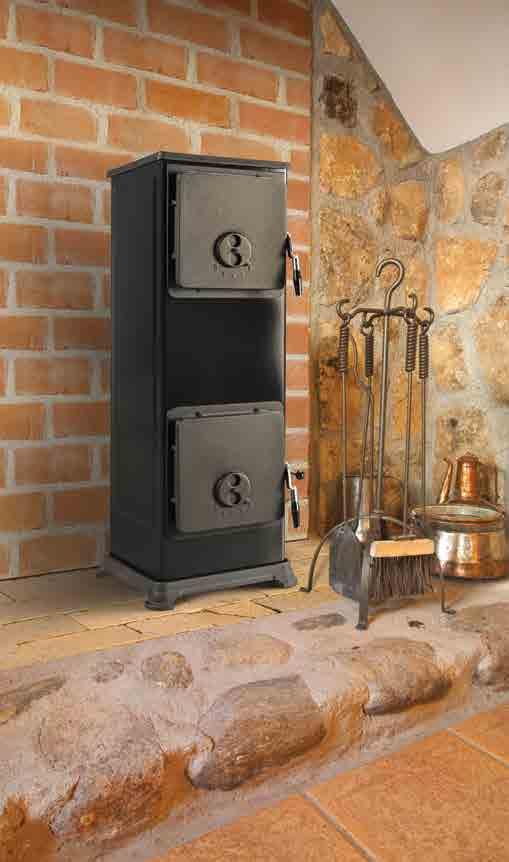
THORMA was established in its present form in 1998 but the company has inherited the more than 100-year tradition and knowhow of the former manufacturing company Kovosmalt Fiľakovo.
The company’s key products include stoves, log burners, fireplace inlays and solid fuel cookers as well as boiler sets and water heaters. In addition to its own products, THORMA also designs and manufactures bespoke heating devices under its customers’ own brands. Its product range is continuously modified to meet market requirements using the in-house product development and design department, construction department and test shop.
The second, albeit much smaller, pillar of the company’s operations is the production of metal parts for the automotive and agriculture machine sectors, including surface treatment services such as enamelling, painting and galvanic coating according to customer requirements. Over 75 per cent of its output is exported, primarily to Germany, Denmark and the Czech Republic.
THORMA’s continuing success is based on the high quality of its products as well as its ability to fully meet the stringent EU requirements (including those for environmental management). However, these are not the only reasons for the company’s growth: “In the past five years we have significantly enhanced our product range and have succeeded in penetrating new markets, such as Australia, the UK and Russia, for which we have developed new products. It is also worth mentioning that we continue to meet EU standards in all of our product lines,” says Mr Sykora. In 2000 the company implemented the EN ISO 9002 quality management system, which was adapted two years later to comply with the EN ISO 9001:2000 requirements. In 2002 the environmental management system EN ISO 14001 was introduced. High priority is given to meeting the strictest combustion parameters to ensure minimum levels of fossil particle emissions. Company processes are fully in line with REACH requirements.
Attractive and efficient
THORMA’s product portfolio currently includes about 100 types of log burners and stoves, reflecting varied customer demands. This ranges from the simplest of models to the most sophisticated, luxurious products. Great attention is paid to the quality of the warranty and post-warranty service which the company provides using its own experts as well as a wide network of external partners. A key strength is its in-house product development department, which enables it to continuously update its product range and meet individual customer requirements to the maximum extent.
The company’s log burners and stoves represent an efficient and attractive addition to any interior. Their doors are fitted with temperature-resistant ceramic glass. Customers appreciate, in particular, the Airwash system (THORMA’s own design), which cleans the glass using air: inside the device, air currents are guided in a particular
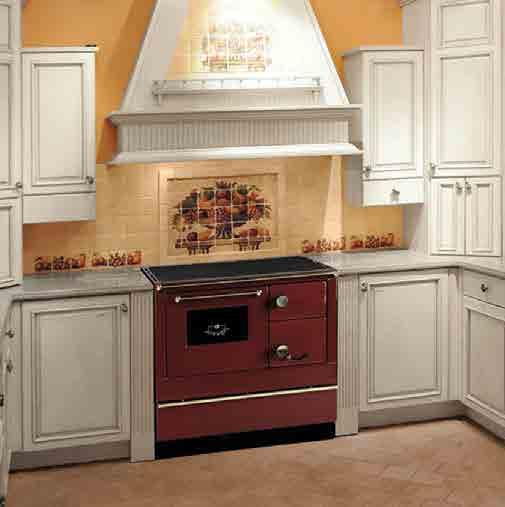
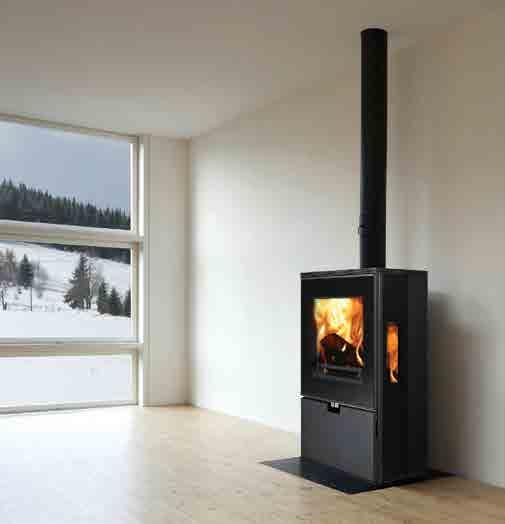
way to ensure that glass is permanently clean. Models with a water boiler may be connected to heating systems currently installed in the house. Another attractive feature is that THORMA products achieve (or exceed) a combustion efficiency of 82 per cent. The most suitable fuels for its stoves and burners are hardwoods, such as oak and beech, or brown coal briquettes.
The current focus is on developing products that accumulate heat and then radiate it throughout a wider area. THORMA’s high-end products also boast highly attractive designs, using Italian and Scandinavian stone with a beautiful structure resembling marble. Its more affordable models are made of fireclay plates boasting the same accumulation properties.
Modern facility
At its only production facility in Filakovo THORMA currently employs 350 people. The plant covers all the specific processes needed for this particular type of production: laser cutting, chamfering, sand blasting, dipping (using an automated line for the pre-treatment, de-greasing and cleaning of metal parts), galvanic coating (zinc or nickel) and enamelling (powder or enamel spray coating in a highvoltage electrostatic field, manual enamelling, dipping and coating).
Over the years, the company has invested heavily in modern technology and equipment and continues to do so. “The latest addition to our facility is a new ERP and Sagiacomo pressing machine, which replaced the older model, commissioned in 2013,” says the managing director, adding that last year the company completed the implementation of a new information system.
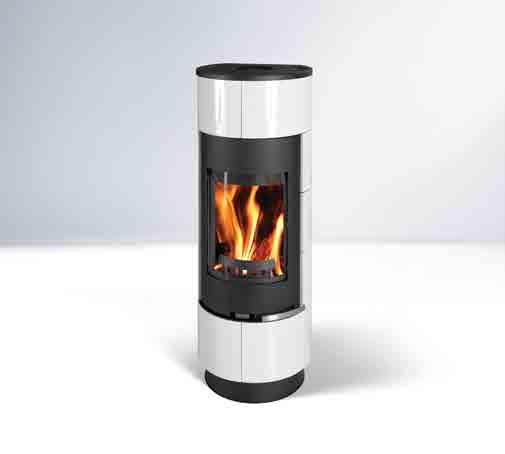
Two directions
In most European countries, the log burners and stoves segment has been stagnating or declining as a result of the drop in energy prices and continuing inadequate growth of the construction sector. In addition, sales have been negatively influenced by warm winters in recent years – which has resulted in excessive stock – as well as by
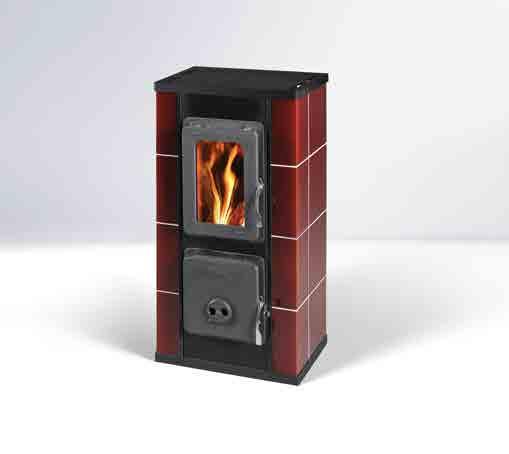
a number of aggressive competitors recently established in Europe. For these reasons, the company has started to look further afield: after considerable success in Australia, it is, according to the managing director, New Zealand next, while North America also offers interesting prospects.
“Future trends are clear – as customers are willing to invest more in thermal house insulation to reduce energy costs, this must be reflected in the offer of new types of stoves and burners with lower consumption, using heat via TUV heating. In line with this trend we will soon introduce new products with better efficiency and a new design,” he claims.
However, THORMA also wants to develop its second pillar – subcontracting for other manufacturers – which today accounts for a mere 10 per cent of total output. “This line of development has been supported by our recent technology investment and in the future we want to provide sheet metal processing not just for the automotive and agricultural but for other sectors too,” says Mr Sykora. “Enamelling, our traditional capability which has been developed in Filakovo over a century, is something which most of our competitors lack. We are now seeking new opportunities in this direction too,” he adds. n
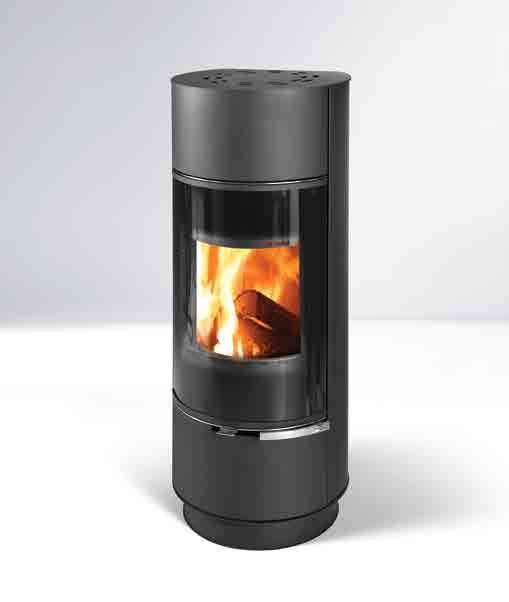
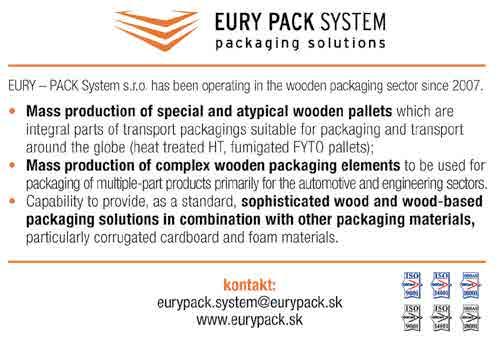
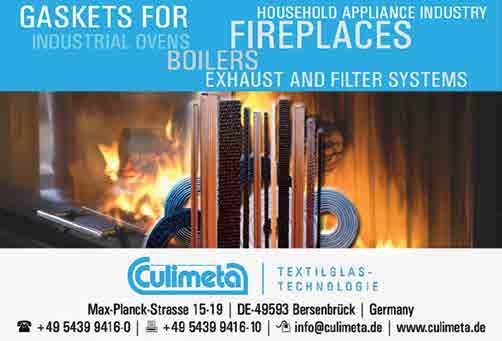
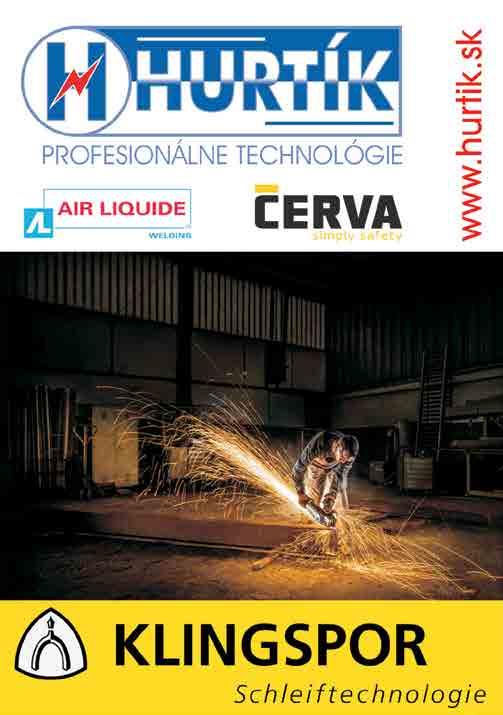