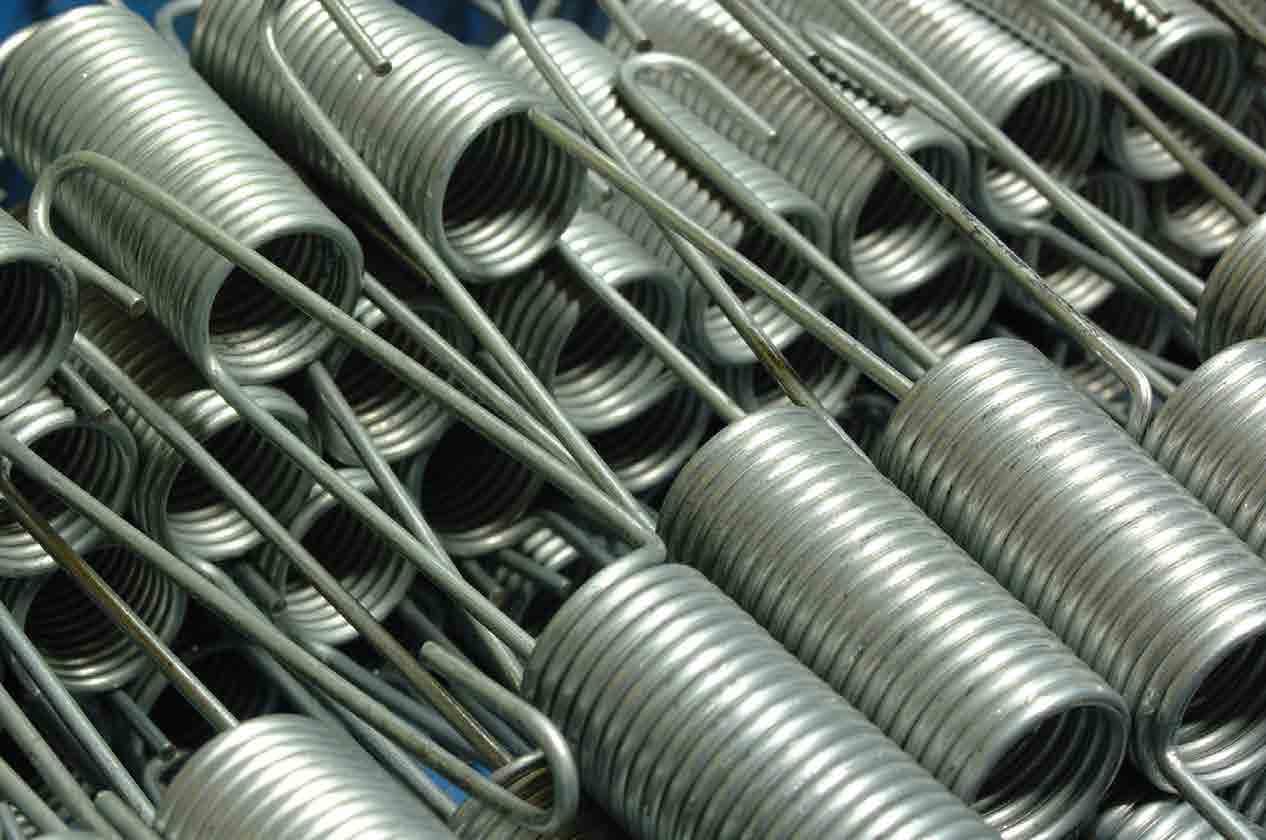
4 minute read
Springing into the future PFS
SPRINGING INTO THE FUTURE
PFS is the largest producer of springs and wire forms in Slovakia. The company was founded 20 years ago and has been growing ever since. Romana Moares reports.
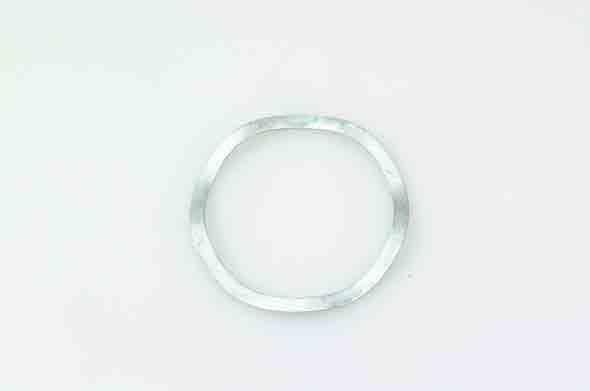
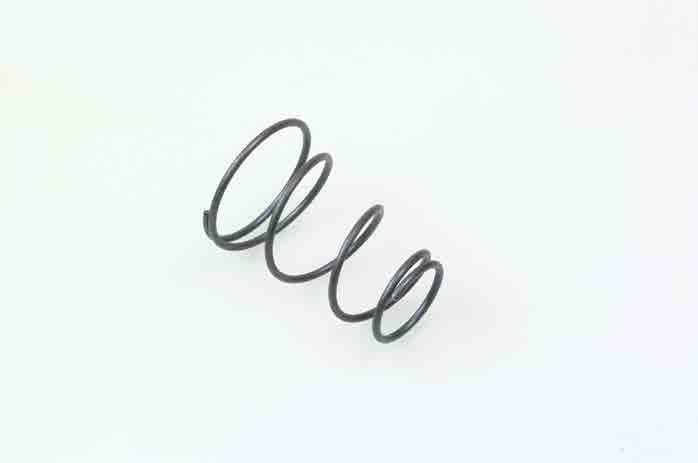

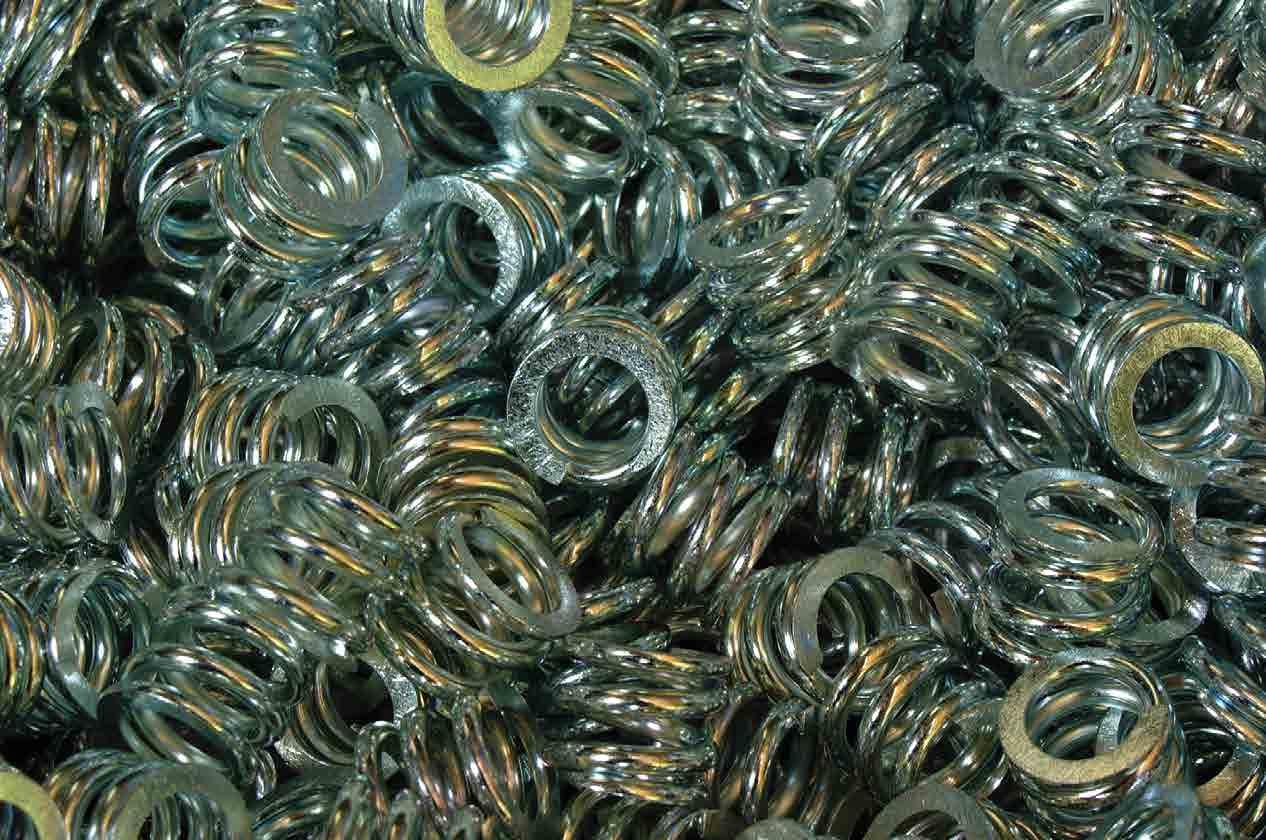
“Our company continues a 50-year tradition of spring manufacturing but the true milestone in its recent history was the transformation into a new business in 1995,” says sales director Bohuslav Plačko. He further explains that in the five years after the recession, a great deal of focus was placed on stabilising the company in terms of its organisation and supplier management.
For global manufacturers
The Slovak company offers a wide range of springs and associated products in many varieties, including compression, extension, torsion and double-torsion springs, wire forms and steel band flat springs, pressed parts, spring washers, split pins, plasterboard ceiling system hangers and many more.
“We produce compression, extension and torsion springs in virtually all possible shapes and sizes, for which we use a wide range of wire forming and coiling machines. Similarly, our technology enables us to produce nearly any shape of wire form and steel band flat springs. Depending on volume we use either general-purpose bending machines with no need for special tools, or bending and press machines with the tool specifically designed for the product – which requires initial investment in the tooling, but the production itself is then quicker and cheaper, therefore suitable for large volumes. For all our springs we also offer various types of surface treatment,” says the sales director.
The springs from Brezova pod Bradlom in western Slovakia are being used in many car components, from lighting systems to clutches. In today’s globalised world, where component manufacturers supply their often unified products to cars of different makes and models, PFS’s springs operate literally on all continents. “Similar principles are applied in other sectors also, from white goods and electrical appliances to agriculture. This naturally increases requirements for top-quality supplied parts and we put maximum effort into ensuring that such quality is ingrained into all of our components,” claims the sales director.
In addition to springs and wire forms, the Slovak company also produces plasterboard ceiling system hangers and for all of its prod-
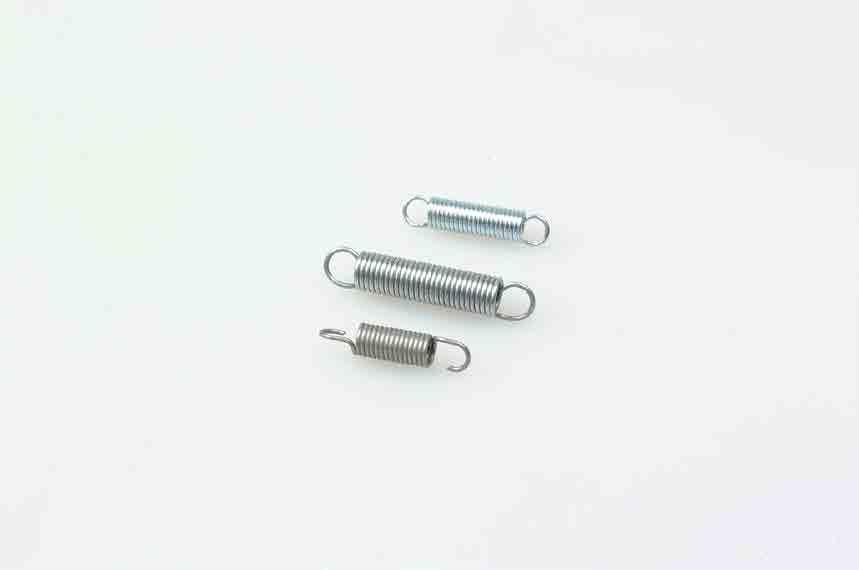
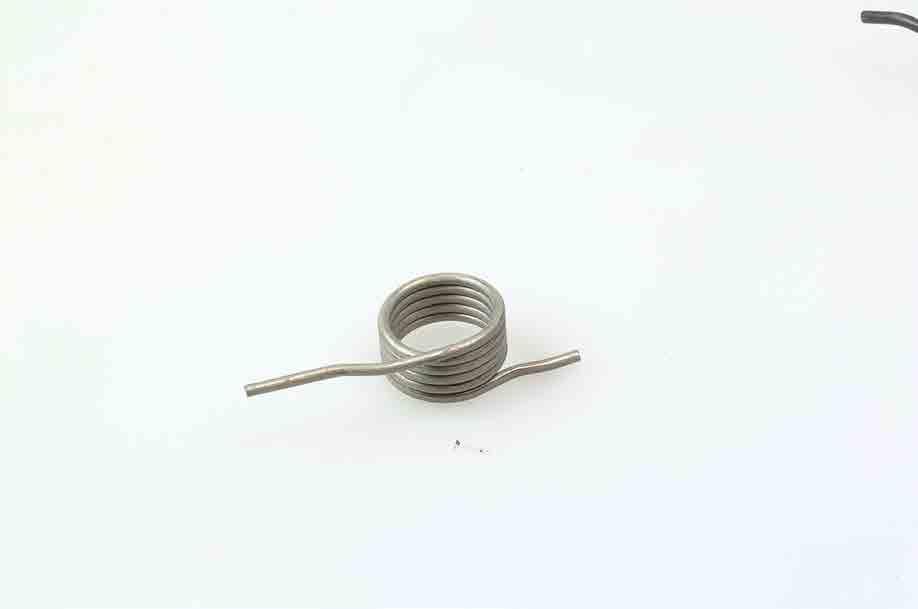
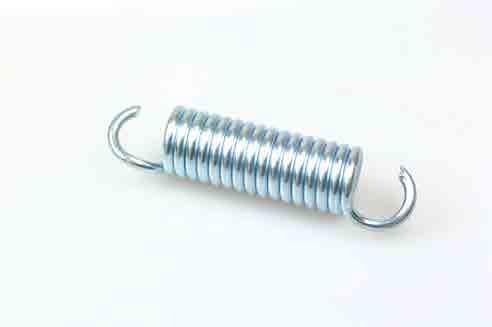

ucts offers the Delta-MKS surface treatment under a Dörken MKS licence, as well as other galvanising services. “We are the only company in Slovakia operating under the Dörken MKS licence, which is required mainly by suppliers to the automotive and construction sectors. The licenced processes ensure increased corrosion resistance and prevent the occurrence of hydrogen embrittlement,” explains Mr Plačko. New and innovative products are being developed on an ongoing basis to reflect customers’ new projects. Today, 70 per cent of total output is being sold to export markets.
First-class technology base
The sales director explains that material suppliers are carefully selected with regard to strict quality requirements. In addition to standard spring materials, special composition materials or special mechanical properties are also used if required by customers.
The company boasts first-class technology ranging from simple, single-purpose machines to the latest CNC winding, shaping and moulding automats. Final-stage operations include grinding, heat treatment, surface treatment, measuring and testing. Surface treatment is provided to match any specific customer’s requirements for increased corrosion resistance and improved visual properties and may include blackening, phosphate or zinc treatment. If required by customers (again mostly from the automotive sector) modern treatments such as Delta MKS (protective surfaces of the Delta-MKS system are free of heavy metals and the substances used have no carcinogenic and mutagenic effects) may be provided.
“Investing in technology modernisation is an integral part of our business strategy. Older machines are systematically replaced by new ones so that we are able to keep pace with technology development in our sector,” says Mr Plačko.
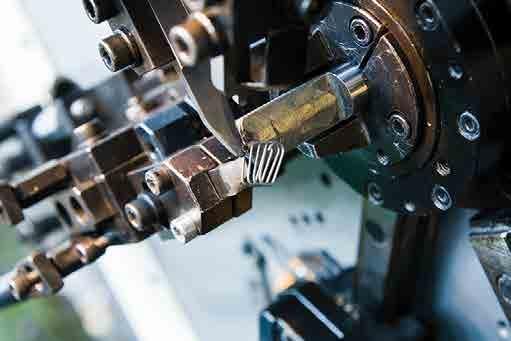
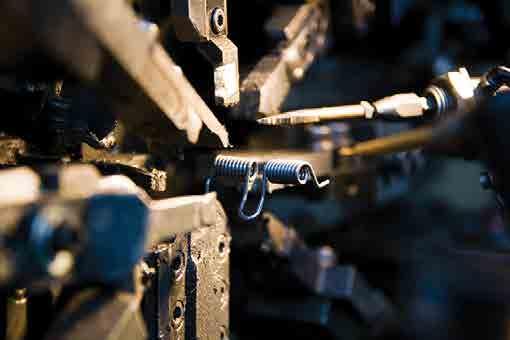
Challenging future
Following the financially record-breaking years of 2006 to 2008, the company was forced to adopt tight crisis measures to keep the business running. The situation was stabilised two years later and gradual growth has been achieved over the past few years. However, market pressures are greater than ever – while PFS exports its products to many countries and competes with producers of similar products on a global scale, companies from western Europe, offering similar products, have now built plants in Slovakia, making trading in the local market harder. However, this has not threatened PFS’s position significantly. “We have secured a stable level of orders for the automotive, white goods and construction sectors,” says Mr Plačko. “In fact, our major problem at the moment is not lack of work but shortage of qualified technicians. But that applies to any engineering business, I believe,” he adds.
According to the sales director, the company’s plans for the future are clear: to continue striving to fully meet customer requirements and to maintain a good mix of price, quality and delivery terms. “The quality of our products has been proven by the ISO 9001:2008 and ISO/TS 16949:2009 certificates. Further quality improvements will be supported by more investment in modern technologies in the near future,” he concludes. n
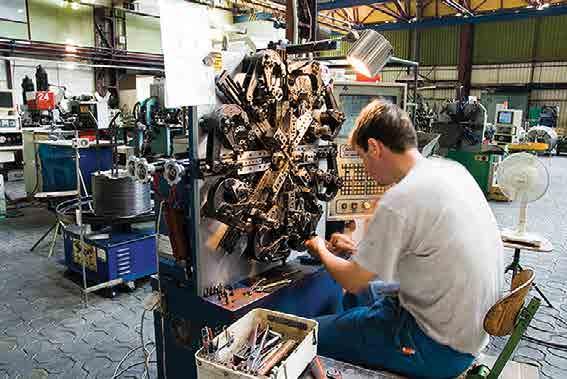
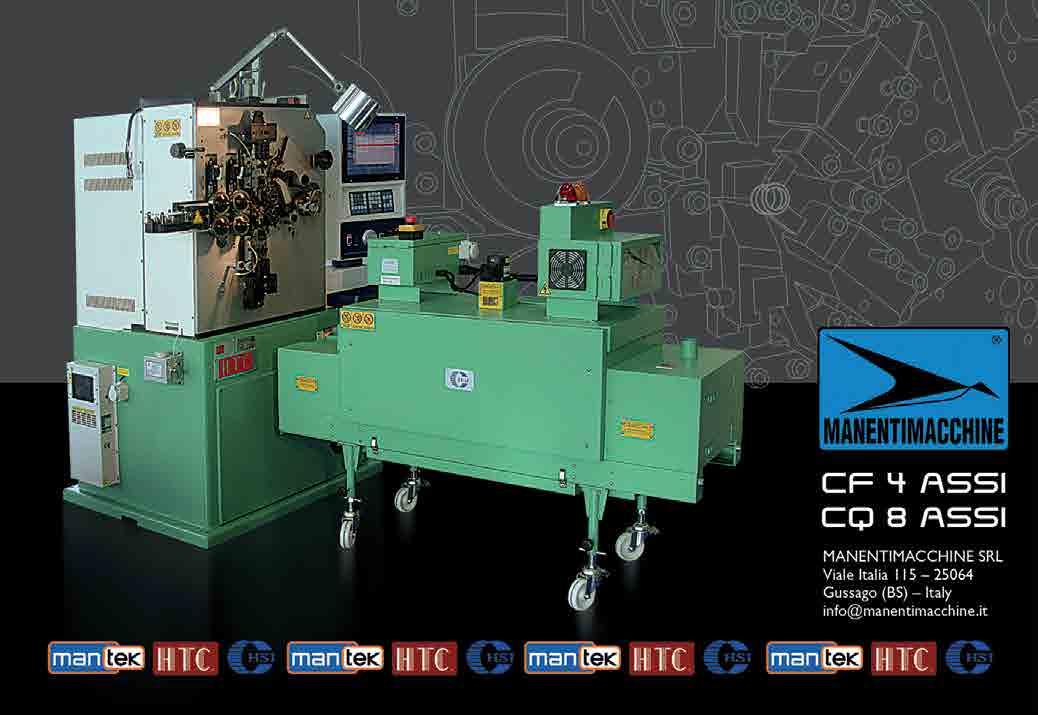