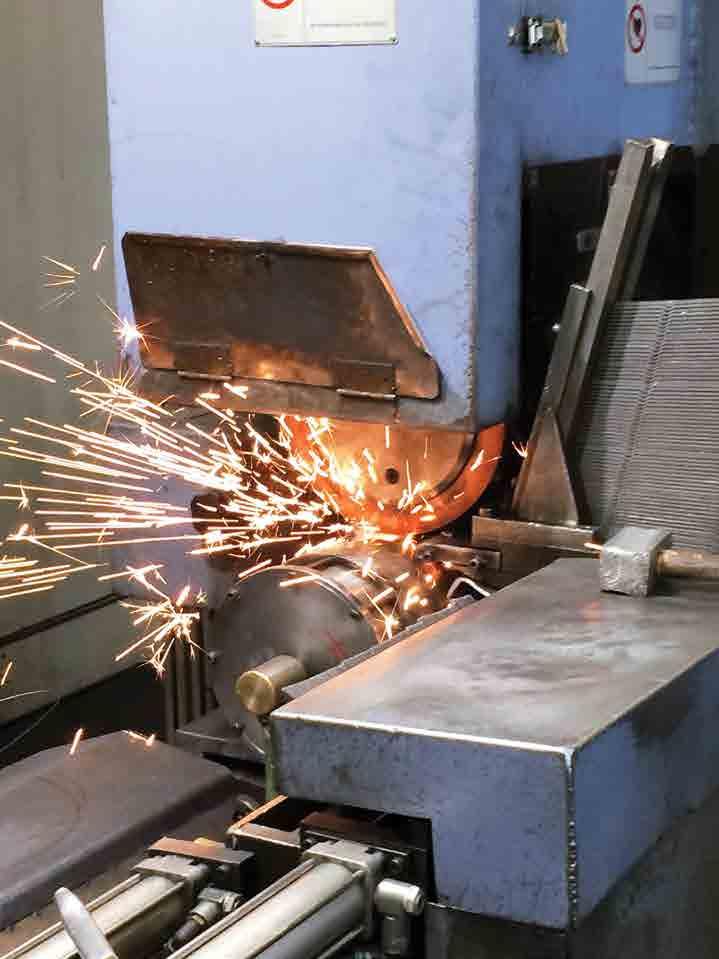
4 minute read
Solid prospects

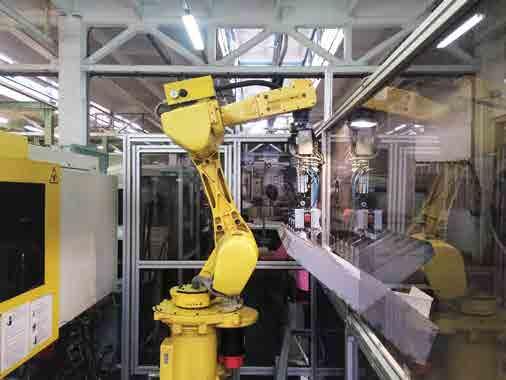
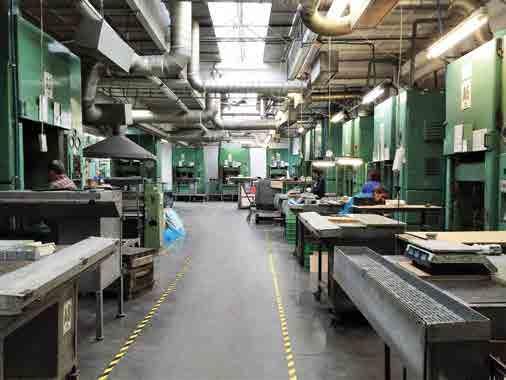

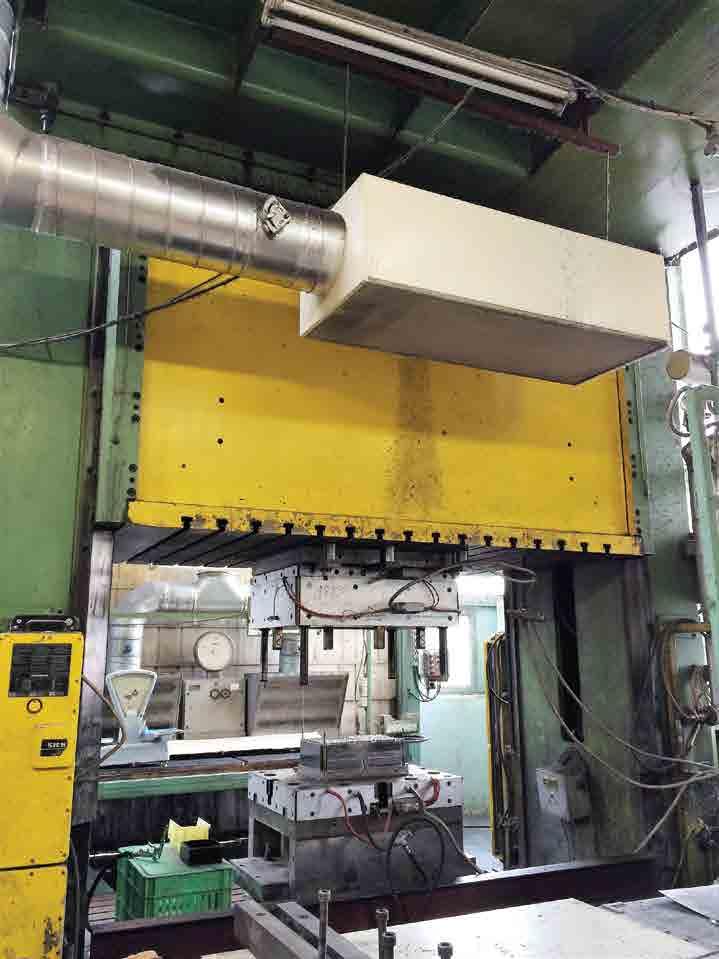
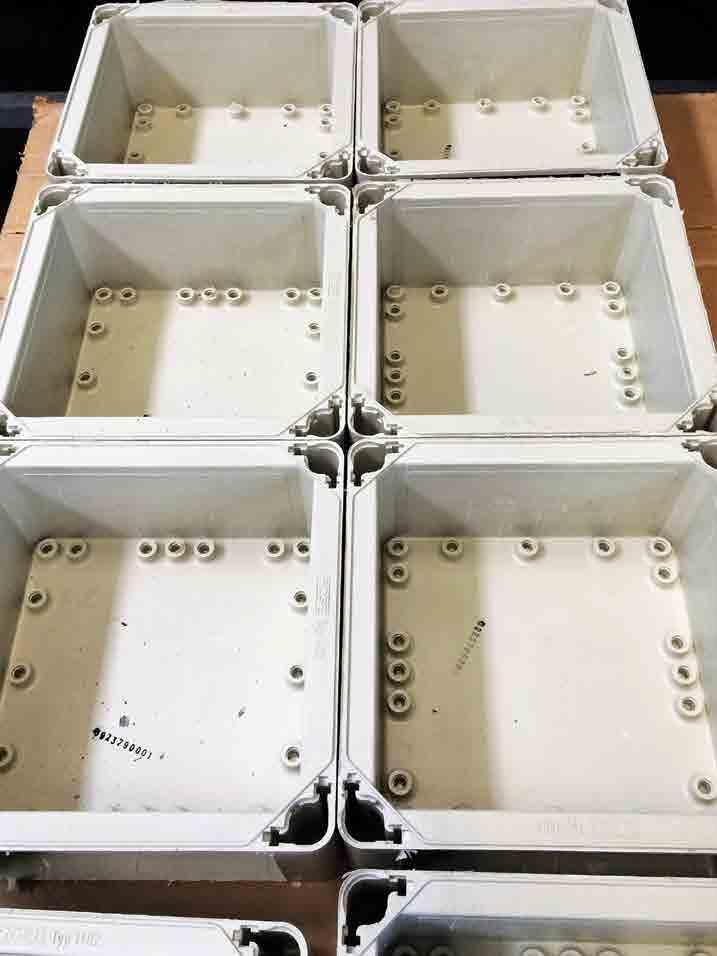
KUNPLAST-KARSAI Műszaki Műanyagipari Zrt is one of the leading plastic processing companies in Hungary and a major employer in the town of Kiskunfélegyháza where it is located. Thanks to its modern technologies and skilled labour force, the previously state-owned Hungarian firm today meets the highest quality requirements set by European car manufacturers. Edina Beale reports.
Established in 1961, the predecessor of KUNPLAST-KARSAI Műszaki Műanyagipari Zrt had been a significant plastic and rubber processing company in its local region for many decades. Two years after its privatisation in 1992, its employees purchased 85.5 per cent of the company. In 26 February 2000 capital funds were raised to 61 per cent and shares became the property of Karsai Holding Rt from Székesfehérvár, hence the company’s adoption of its current name and ownership structure.
Operating on a modern industrial site in Kiskunfélegyháza and providing jobs for 250 staff, today KUNPLAST-KARSAI Műszaki Műanyagipari Zrt has a strong position in the Hungarian and international markets and achieves an annual turnover of €10–12 million. Direct automotive supplier
The company began to test the automotive market in 1988 and has made significant investments to meet the strict quality requirements needed for this sector. Today Kunplast is a reliable supplier of numerous prominent car manufacturing companies including Suzuki and Volkswagen. Besides these, the company supplies high quality component parts indirectly to BMW, Ford, Mazda, Volvo and Volkswagen. At present 47 per cent of production serves the automotive sector. As a high volume automotive product supplier, the company has to meet the basic requirement of 100 per cent faultless products. This is only achievable via the implementation and maintenance of reliable quality assurance systems. Among others,

the company has implemented the ISO 9001:2000 and the ISO/ TS 16949:2002 assurance system, and has also been operating according to the environmental ISO 14001 system since 2002.
Components for electrical and other sectors
Besides its automotive products, the company produces heavy and light current electrical technological plastic components for the Swiss, German and UK markets, whilst supplying many different plastic articles for personal use such as sanitary products to Switzerland. Moreover, plastic floor tiles, storage compartments and products for composting are being manufactured by the factory predominantly to serve the domestic market.
In addition to its core activities of plastic processing, Kunplast is also a mass producer of brake components and sandwich structured aluminium covered heat protection panels for car manufacturers including BMW, Audi and VW.
Plastic processing tool making
Plastic processing tool production now also plays an important role in the company’s business strategy. In 2007 its capacities in the area of large size and precision tool manufacturing were extended. The company implemented a modern CNC machining centre and milling machine whilst investing in the high end Unigraphics NX CAD CAM software package for design as well

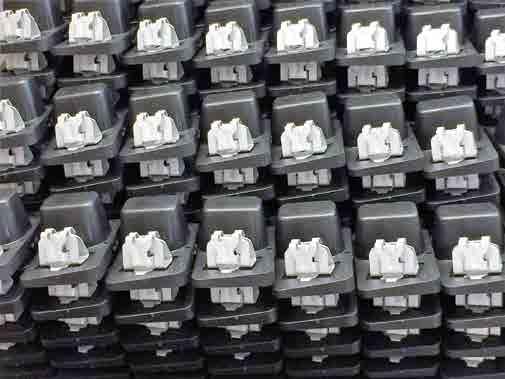
as purchasing a new NC machining centre. “Our aim is to create a European standard production capacity for Hungary’s medium and large size tool making needs in Kiskunfélegyháza,” says Mrs Klára Alter, managing director of KUNPLAST-KARSAI Műszaki Műanyagipari Zrt. In addition to producing tools, the company’s new tool manufacturing facility enables Kunplast to maintain and repair its partners’ tools. This allows it to meet the required quality standards and therefore to increase customer satisfaction.
Diverse technologies
In order to offer diverse services for its partners, Kunplast has invested in two methods of plastic processing and has implemented several other type of technologies. The company operates 19 press machines in its thermoset production hall where it mostly manufactures electrical assembly boxes, known as the Rose product range. This range is manufactured by compression moulding using SMC glass fibre reinforced polyester wax. Products for the automotive and electrical industries predominantly require the use of thermoplastic technologies. The factory has 28 injection moulding machines from 25t to 2200t to process a significant amount of products made from technical compounds including ABS, PA, PC, PS and POM. For products that have lower quality requirements components are produced from PP and PE. Among many other technologies, Kunplast also offers steel forming, laser engraving, ultrasonic and vibration welding.
Positive outlook
In the near future Kunplast is planning to invest in a laser marking and reading system as well as in new production machines as it expects an increase in demand for thermoset products, particularly in the electrical and automotive markets.
A successful history reaching back several decades, high customer satisfaction and effective cooperation with its suppliers are the results of the company’s professional skill, determination and competitive workforce. It puts special emphasis on training and employing skilled workers, and cooperates in many different ways with local authorities and colleges to continuously renew its workforce. Managing director Klara Alter is confident about the company’s future growth: “European car manufacturers see us as a reliable supplier from central Europe, predominantly serving the electrical and automotive sectors. Our long term plan is to double our turnover by 2025 whilst modernising our technologies and putting emphasis on innovation so that the efficiency of human labour will also be doubled.” n
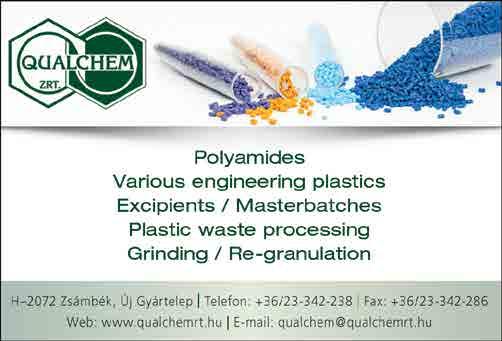
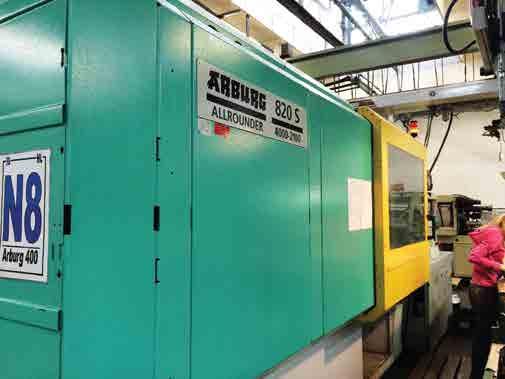
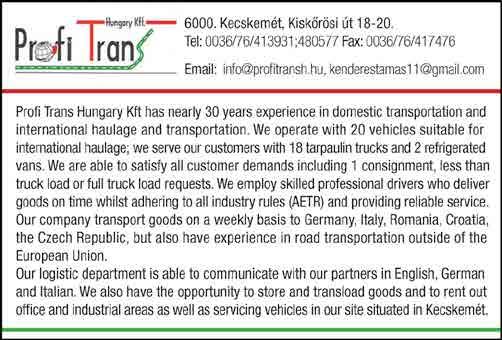