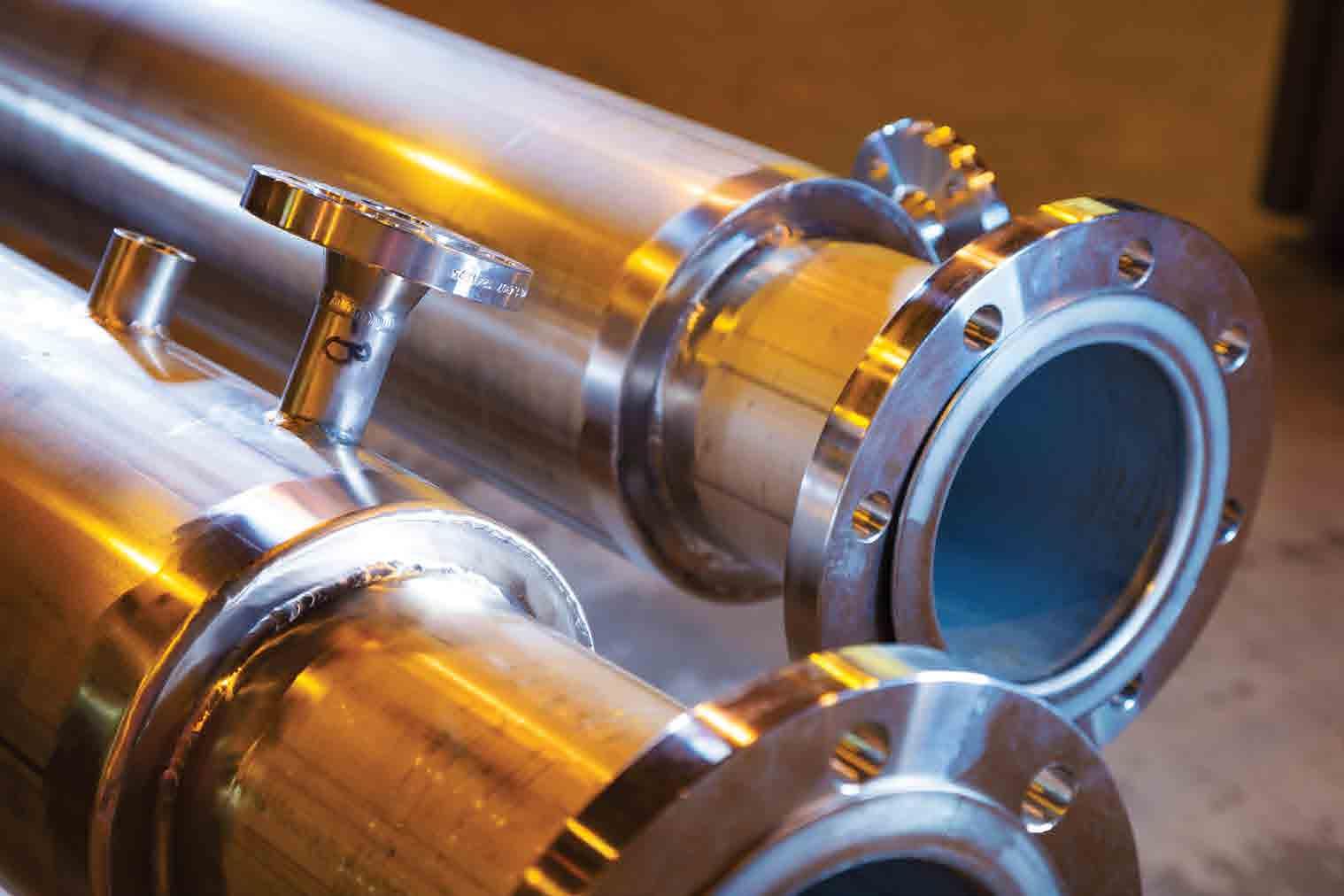
5 minute read
Complex fabrication solutions Uwira
COMPLEX
FABRICATION SOLUTIONS
The Finnish company Uwira supplies welded products and components – mainly pressure vessels and prefabricated piping – for clients throughout the world. In recent years, as Victoria Hattersley found out in a conversation with CEO Samuli Kuusisto, the company has been focusing increasingly on specialist component assembly for a number of high profile projects.
Founded in Vaasa in 1993, the biggest milestone for Uwira occurred in 2005 when it was taken over by the Leinolat Group, a corporation consisting of seven companies offering a variety of services in the field of metals. Today the group employs 240 people and achieved a turnover of €31 million in 2014.
Uwira serves mainly the Oil & Gas, Marine & Power and Industrial Projects markets. Its activities are perfectly complemented by those of its subsidiary company, Kilkanen, which specialises in flywheels and machined parts. The two companies have grown together from metal works into hi-tech manufacturers working on a range of specialist international projects with globally renowned clients such as ABB and Stena Line.
Mr Kuusisto says of the strong synergies between the two companies: “We have been developing our operations persistently for years jointly with our subsidiary Kilkanen Oy. We have implemented many LNG (liquefied natural gas) projects in recent years and are observing the actively growing LNG market.”
Products and industries
Uwira’s products include standard piping, double walled pipes, welded components and pressure vessels. But Mr Kuusisto is keen to stress that the company’s production focus has seen a shift in recent years. Rather than simply focusing on subcontracted basic welding projects it has adopted a far more project-oriented approach, covering everything from planning and machining to assembly and documentation.
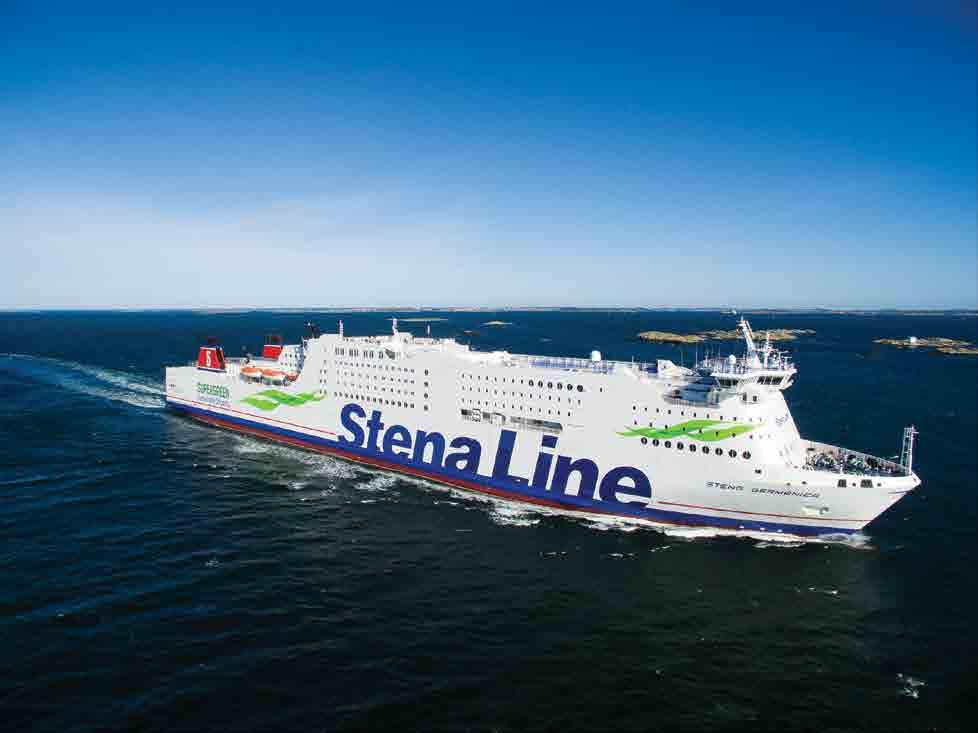
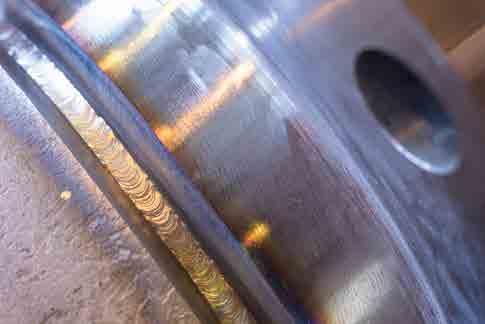
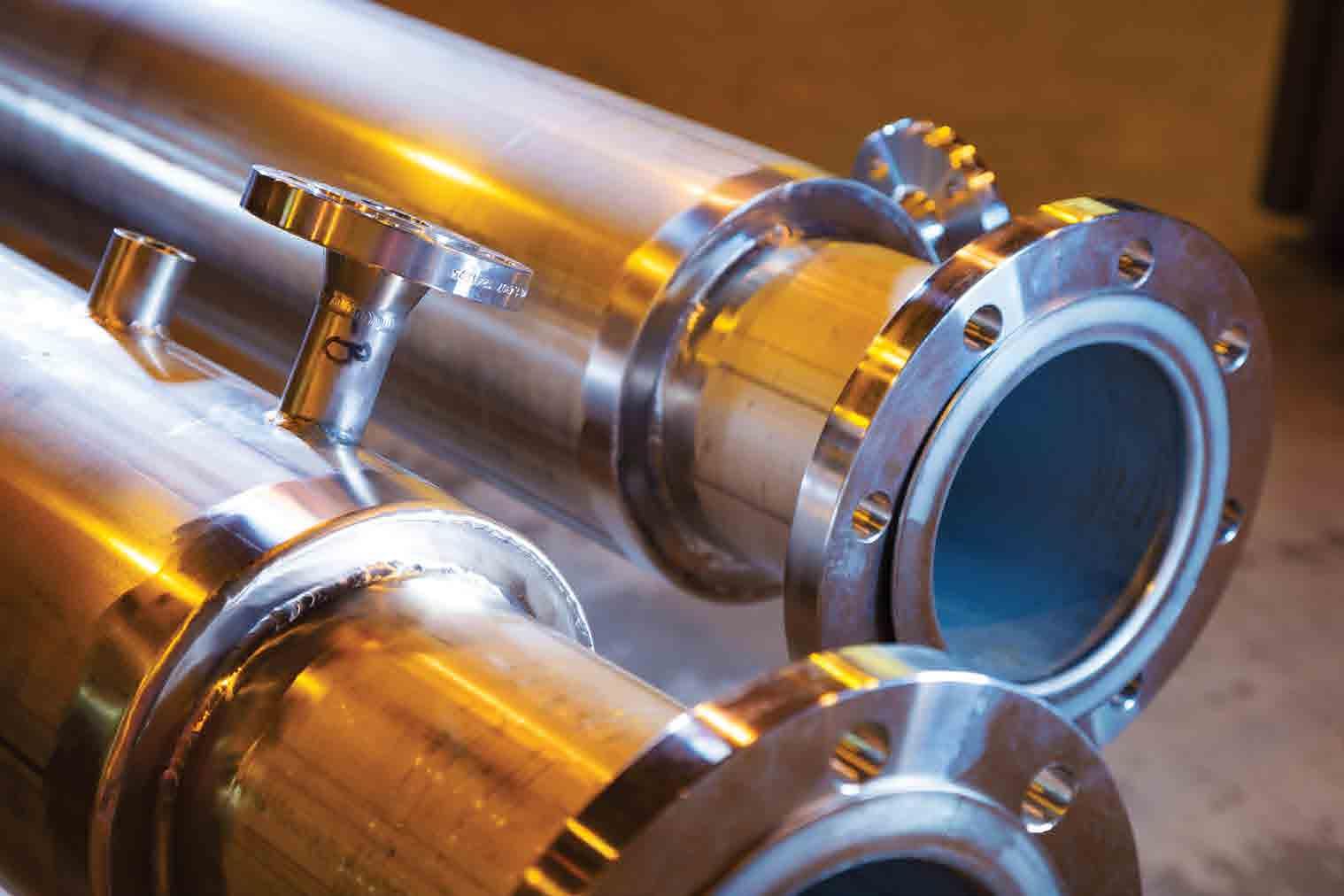
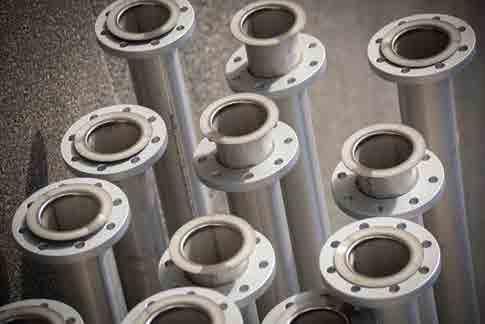
“Today we are much more geared towards special projects with large clients, making more specialist components which are prefabricated at our site and then completed closer to out clients’ sites. This enables us to reduce lead times considerably.”
At the heart of Uwira’s business philosophy are three basic principles: safety, traceability and continuous improvement. The first of these is particularly important when there are such high regulatory standards involved, as Mr Kuusisto explains: “Traceability is a big challenge for us and it’s something we have to focus on at every stage of production. Our complete project management capabilities help us here: for example, for our recent Stena Line project (mentioned below) we had to deal with over 1500 pages of documentation.”
Uwira and its daughter company Kilkanen have been working to ensure pipelines operate faultlessly and safely under all conditions with tanker ships, terminals and offshore vessels in down to 300 meter-deep subsea production equipment. Every process has therefore to be documented and quality assured to ensure production is traceable and customer requirements are met.
When it comes to continuous improvement, Uwira regularly invests in new technologies to ensure its products are of the highest standard. It recently invested in a new flanging machine in order to manufacture flanged products without welding, thus improving stability. Kilkanen, meanwhile, recently installed a Mazak multipurpose lathe at its site. The Mazak INTEGREX 300 IV ST x 1500 enables the company to perform a wide range of processes, from milling and turning to finishing, using a single machine tool.
High profile conversion projects
But what exactly are these specialist projects with high profile clients on which Uwira has been working? There are two in particular which stand out thanks to their scale and unique nature. The first of these, completed in 2011, involved the world’s first LNG conversion for Swedish company
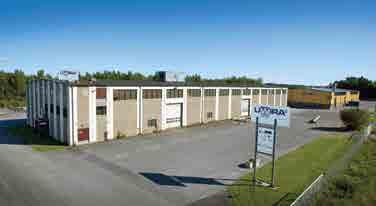
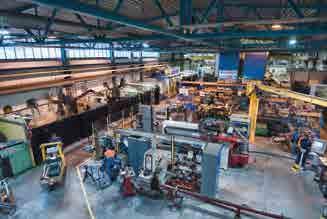

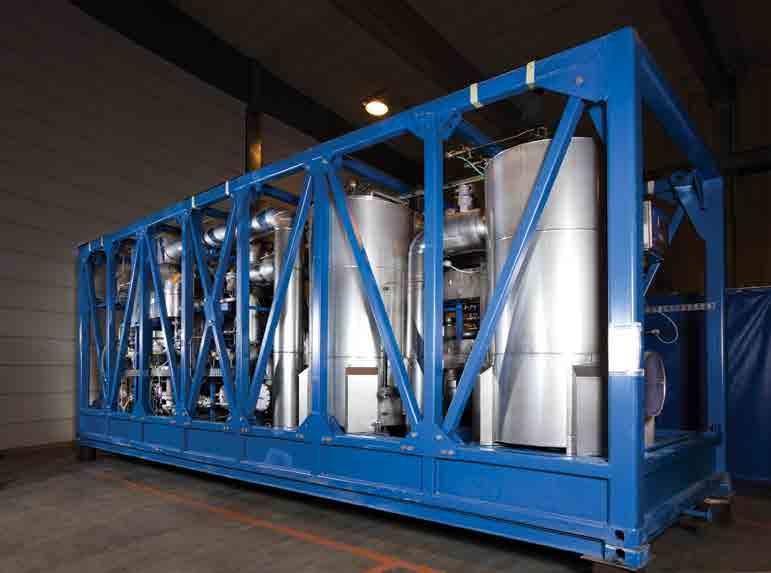
Tarbit Shipping. During this project, the fuel system of the Bit Viking vessel was adapted to make it suitable for use with liquid natural gas rather than the traditionally used heavy fuel oil. Everything was delivered to Tarbit on a turnkey basis and installed on-site.
In the future, ships will be required to use low-emission fuels such as methanol and gas to meet stricter emission requirements, so Uwira is expecting increased demand for its expertise from some of the largest ship owners.
The second major project discussed involved the conversion of Sweden-based ferry company Stena Line’s M/S Stena Germanica to use methanol as its primary fuel. The use of methanol as a marine fuel is one of the latest more environmentally friendly options for shipping. It is sulphur-free and offers significant reductions in emissions of nitrogen, particles and carbon dioxide. For this project, Uwira worked in collaboration with the Vistal Stocznia Remontowa dock in Poland.
During the project, two kilometres of double walled piping manufactured from special material were installed. As methanol has an extremely low flash point, special attention had to be paid to the pipelines through which the fuel moves between the pump room and the engine room. This kind of project puts huge demands on a company’s capabilities, since each welding seam must be able to withstand high pressure when the pipe is in use.
According to Mr Kuusisto: “We are working more and more with increased technology requirements and our R&D department develops ever-safer solutions for these. For example, solutions that have to be double walled for safety reasons – always a priority for us – are becoming more and more in-demand.”
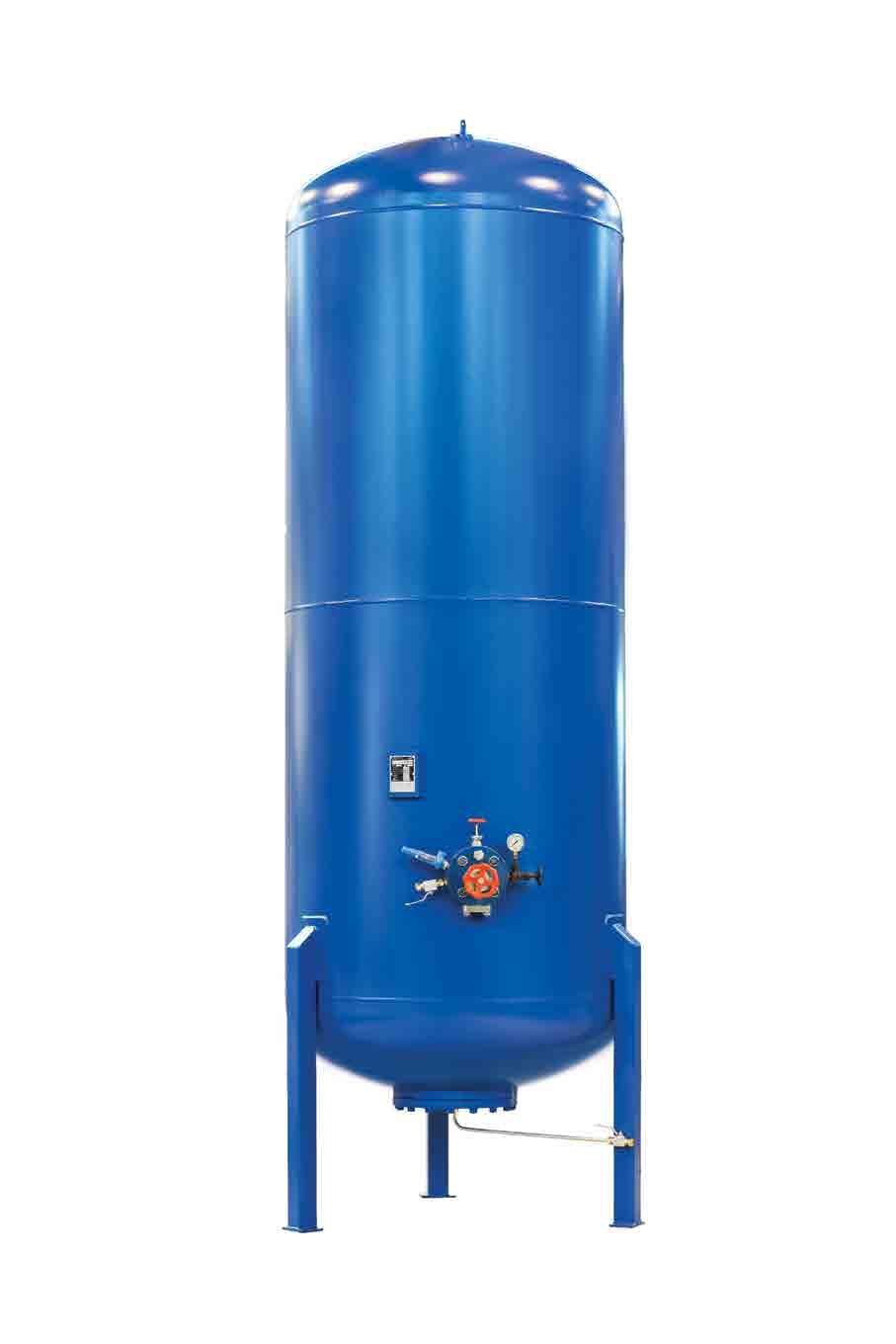

Global growth and future development
The growing renewables market will continue to be an important focus for Uwira as it continues to reach new global markets. Mr Kuusisto tells us: “Kilkanen is currently in the process of setting up a joint venture company in India where we are seeing particularly strong growth in renewables. Many of our clients are dispersed worldwide, with increasing numbers in China and the US. China especially is a huge market so it is possible we will be looking to establish new business partnerships here in the coming years.”
He concludes: “Moving forward we will be continuing to increase the level of turnkey support offered in our projects but also the complexity. We will be working more closely with customers on special projects in the near future.” n
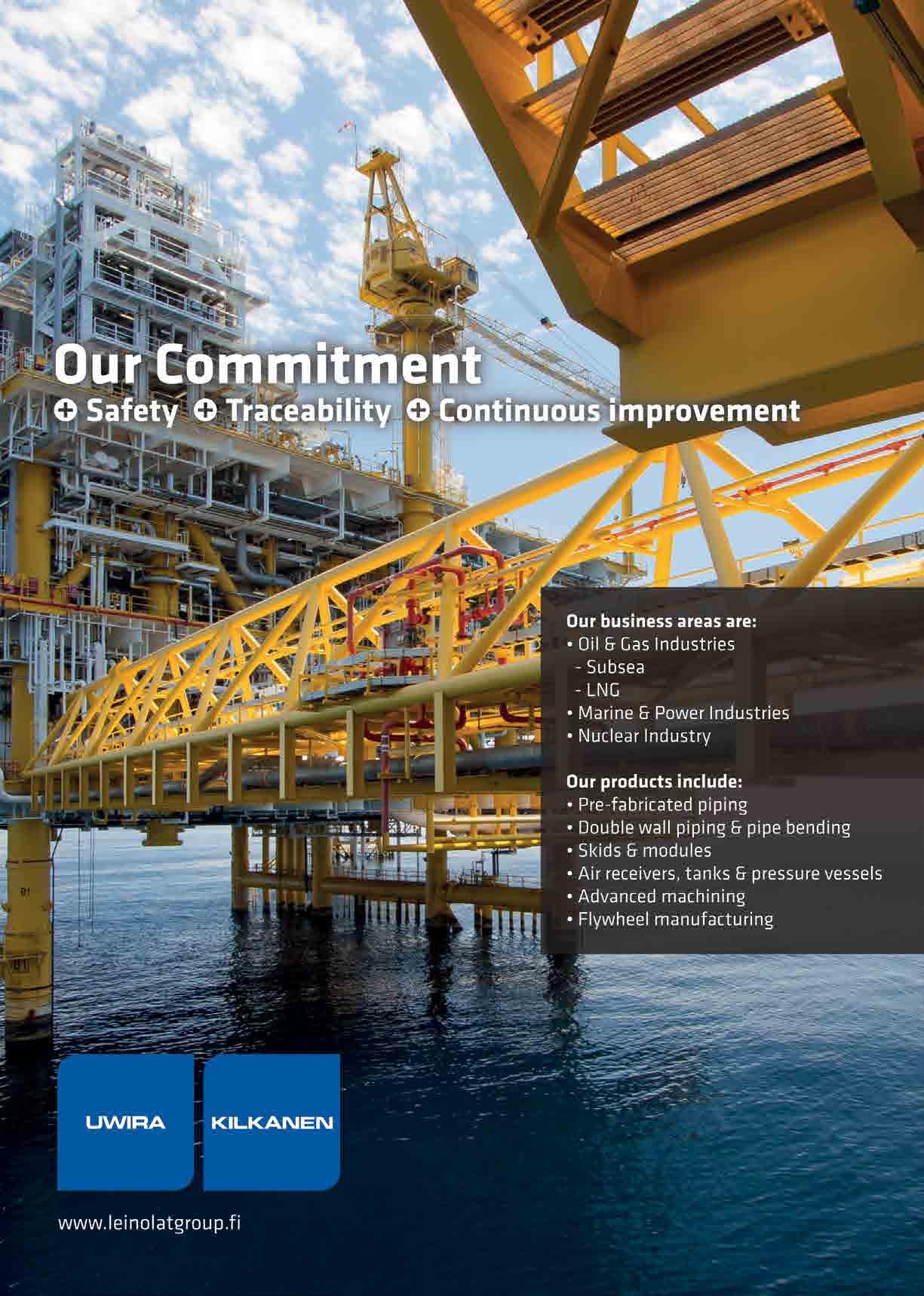