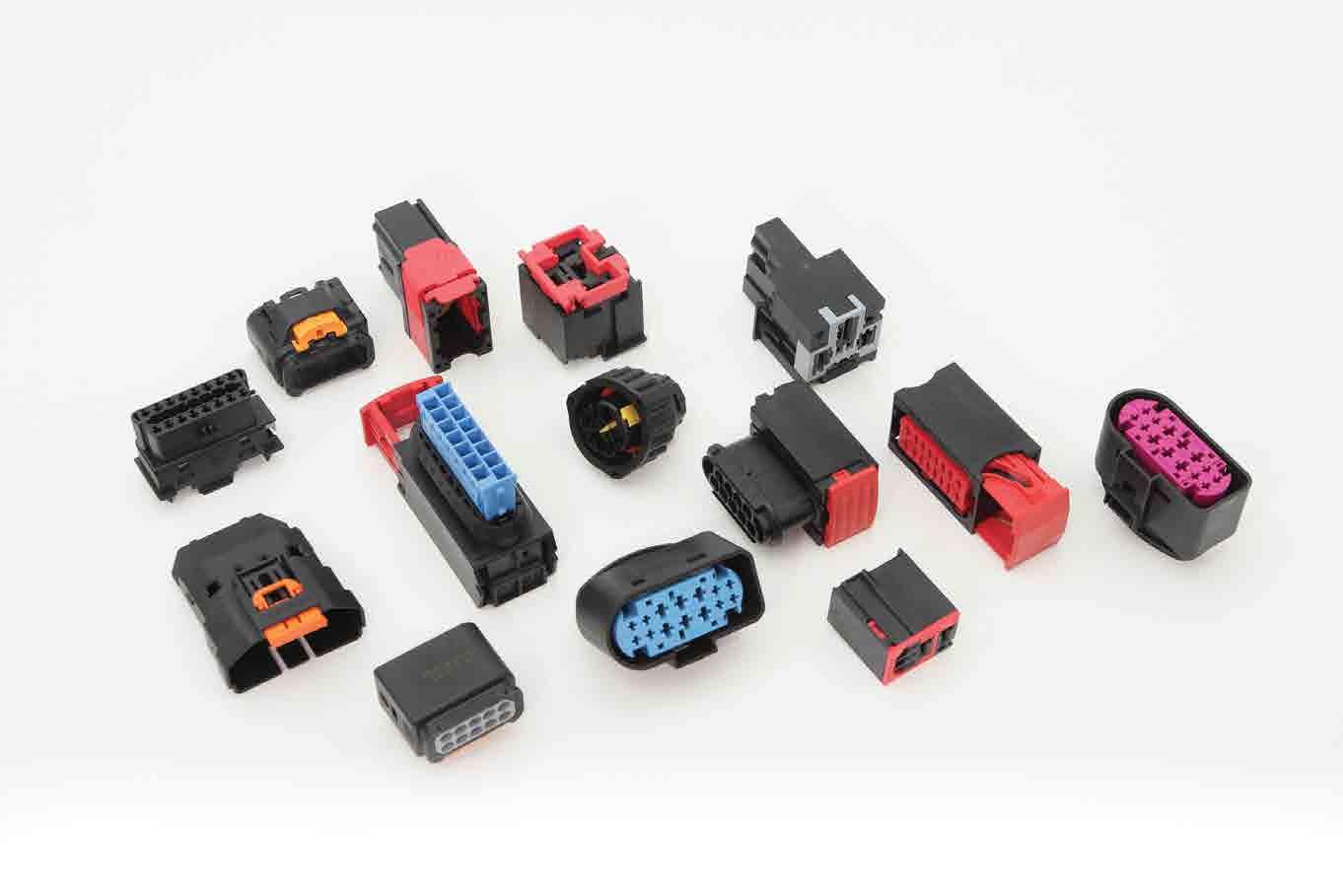
4 minute read
Top-level precision Simon Plastic
TOP-LEVEL PRECISION
Simon Plastic Processing is celebrating its 30th anniversary this year. The Hungarian plastic manufacturing firm started as a one-man operation in 1985. Thanks to a consistent business strategy and its skilled workforce, Simon Plastic has become one of the region’s most significant plastic components manufacturers predominantly targeting the automotive sector. Edina Beale reports.

The founder of Simon Plastic, Mr István Simon, took his first steps towards building his empire from the garage of his parents’ house where he manufactured metal products as a selfemployed worker. His product portfolio began to expand steadily with thermoplastic products and with the production of tools.
The company’s rapid development began in 1996 when the first production hall was built in Szabadbattyán, 6km away from the industrial city of Székesfehérvár. The company then became the official Hungarian supplier of General Electric, still one of its key clients. In 2001 the purchase of a new CNC injection moulding facility and the achievement of receiving its first ISO certificate enabled the company to become a supplier for new multinational and domestic corporations. In 2004 Simon Plastic received the Best of the Region award in the category of small and medium sized companies for being the most dynamically developing firm.
In 2008 the Hungarian firm selected Kőszárhegy to establish another production site, meanwhile it refurbished its existing production hall where it implemented modern injection moulding technologies. At the same time a new 1500m2 warehouse facility was also built. In 2010 the company again invested in the development of a nearly 4500m2 factory and extended its technological capacities with the most modern injection moulding and tool making facilities. In March 2014, a ribbon cutting ceremony was organised to open the company’s new 4000m2 assembly hall and warehouse facility.
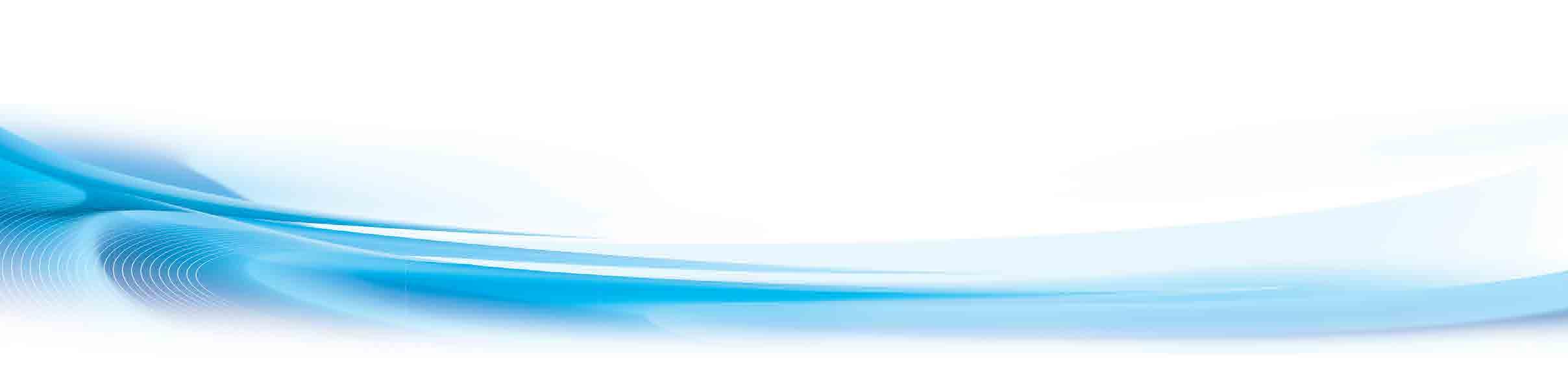
Step ahead of customer’s needs
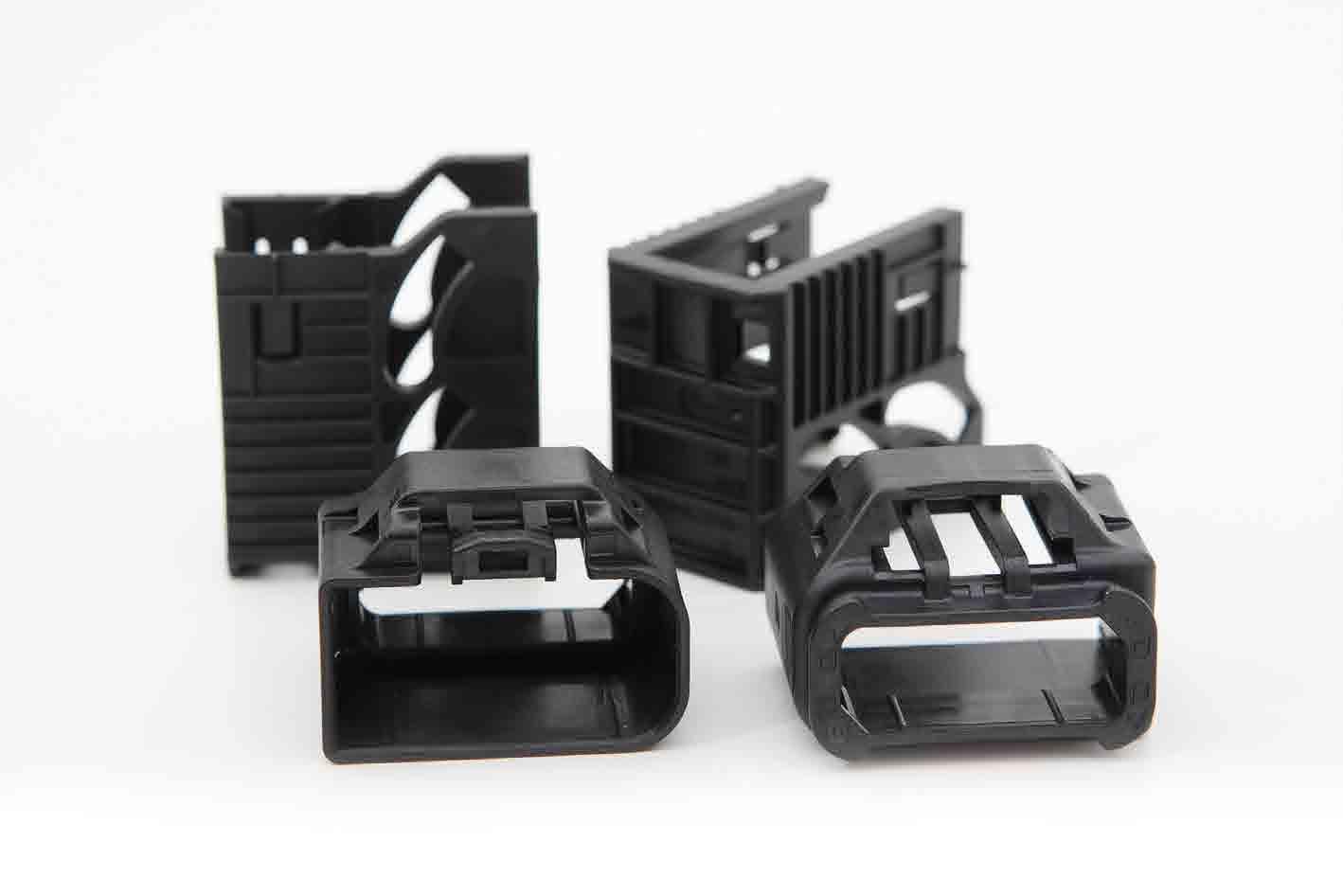
Today Simon Plastic operates in three facilities covering an area of nearly 10,000m2. Its company’s core products are automotive electronic connectors and sound systems, as well as components for the medical, food, electronics and energy industries. Nearly 30 million pieces of components are being produced every month, most of which are used by prominent European car manufacturers including Mercedes, Audi and BMW. Connectors up to 100 pins and 0.4mm wall thickness require state-of-the-art machines, devices, instruments and technologies. Simon Plastic is continuously updating its quality assurance system and has recently received the ISO/ TS 16949 certificate issued by the German TÜV SÜD.
At present the company provides work for nearly 500 people and in 2014 its turnover reached 6.4 billion forint. “We built a large Hungarian enterprise which keeps ahead of changing customers’ needs,” said Mr István Simon. Ranging from 25 tonnes to 350 tonnes in clamp force, there are 90 different plastic injection moulding machines operating across its production sites. Besides the traditional technology, the company offers liquid silicon and co- injection moulding applications and manufactures some of the products using vertical technology.
According to Mr Simon the key policy for development is consistency – the firm aims to become one of the most significant producers in the region operating with 100 machines and using the most modern technology.

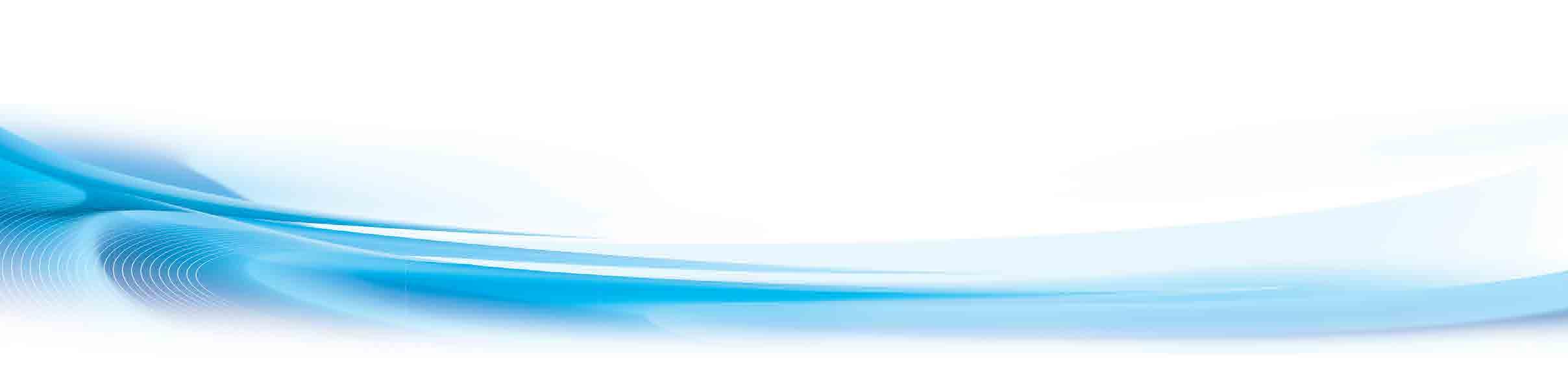
Skilled workforce
It is also an important task for the firm to actively support and train industry professionals and engineers. The company’s initiation of a programme to take on students as trainee employees began last September, and now there are five young students being employed by the firm. The company works closely with colleges and provides practical training courses for students. Simon has also invested in a student workshop room to demonstrate its strong belief in the Hungarian government’s principle: the country and the economy is in need of skilled labourers and engineers,
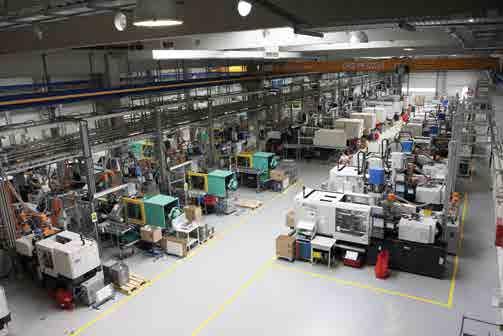
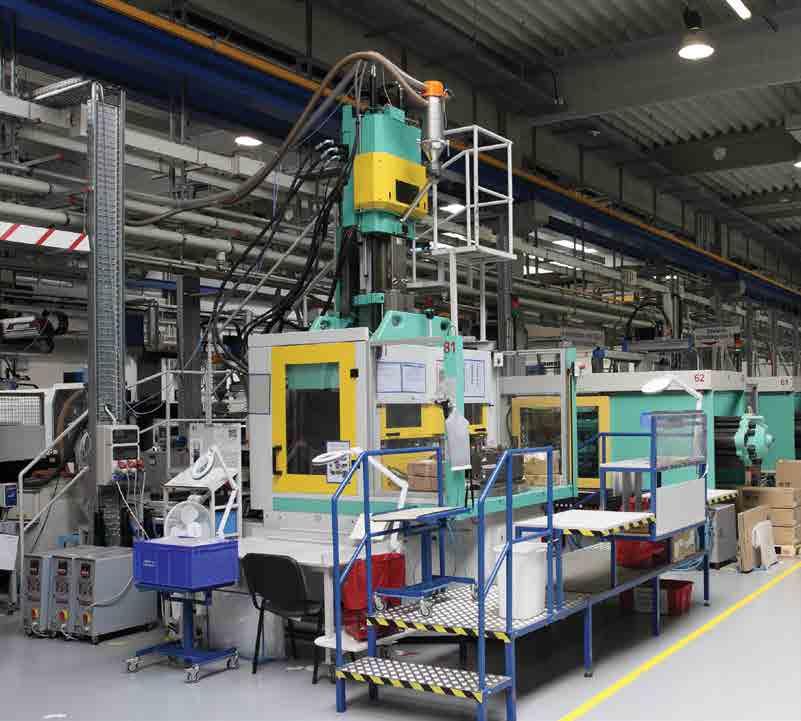
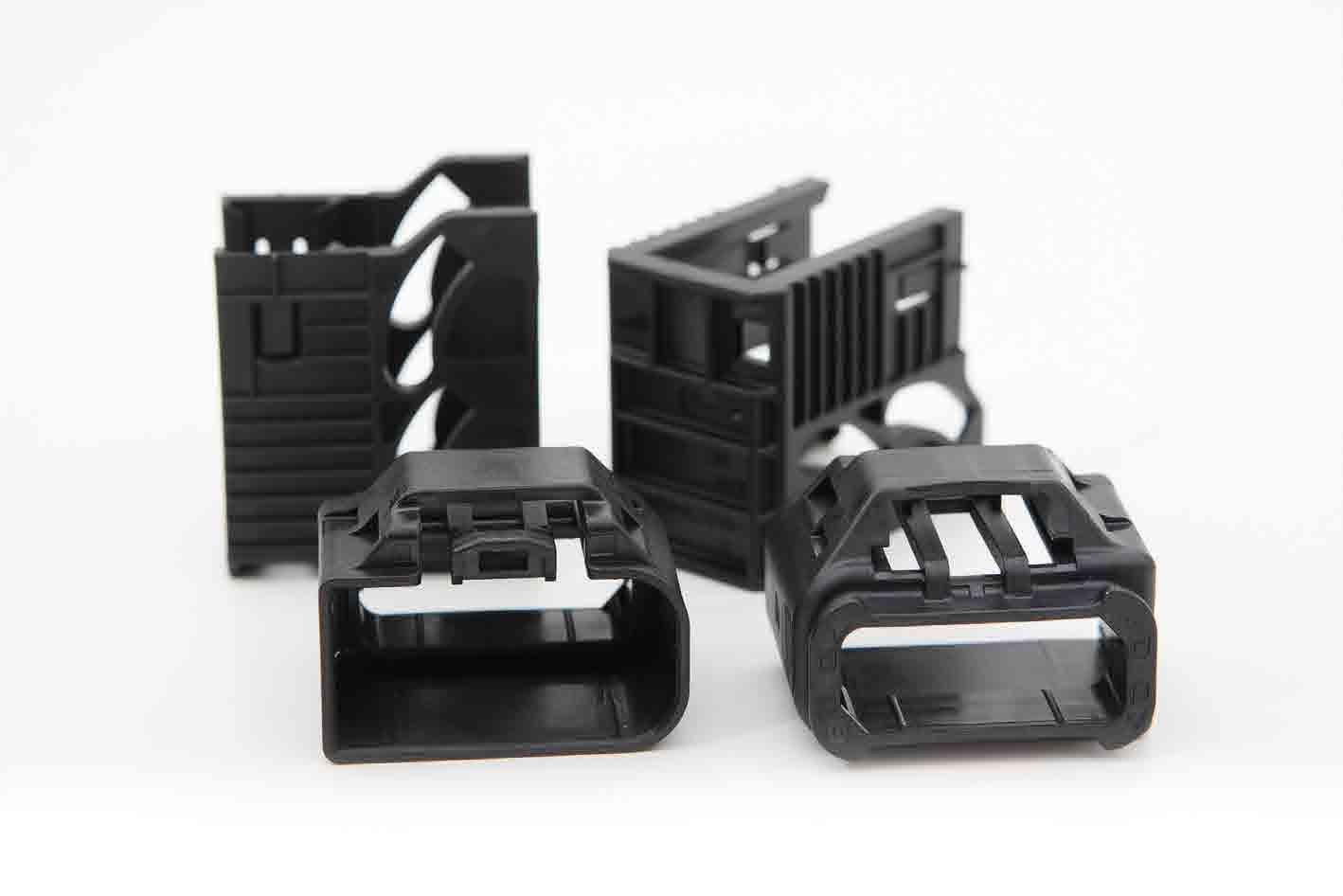
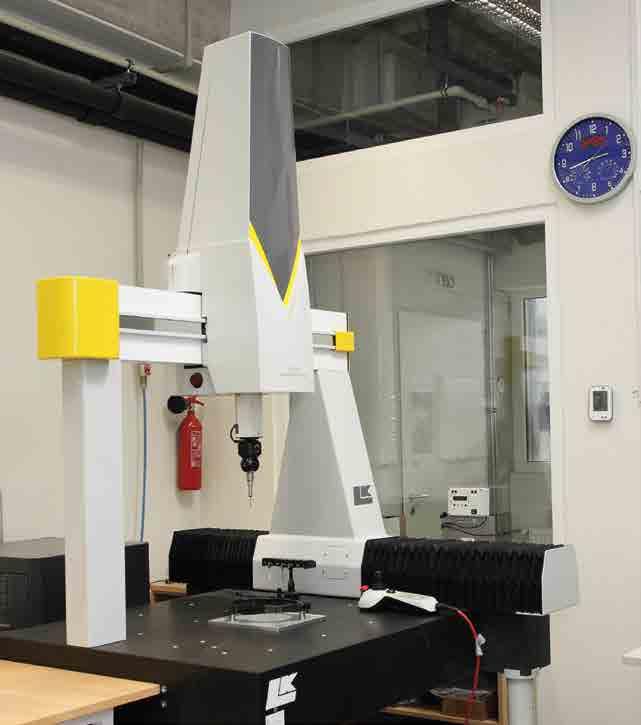
therefore businesses should aim to boost training opportunities. Simon Plastic signed cooperation contracts with some prominent colleges in Hungary, moreover it regularly invites students from primary schools for factory visits.
New research and development centre
In order to maintain the company’s steady development, Simon Plastic is now developing a new research and development centre. “Besides capacity increasing, to secure our future we need to make investments in research and development, focus on efficient managing and working methods and employ a skilled workforce to produce goods with the most added value,” says Mr Simon. The brand new 1500m2 centre will provide jobs for 5–10 R&D specialists and will employ skilled workers. Their task will be to work closely with customers and develop products that are being produced by the company from design through implementation and mass production. All this will be paired with the traditional tool making and the production of new tools, too.
From December last year the management of Simon Plastic was taken over by Mr Simon’s son and daughter: Peter Simon has become the managing executive of the factory, whilst Zulejka Simon is responsible for managing the financial and HR areas. They said: “We are working on a new strategy and making special efforts to create new business opportunities and to extend our product profile.”
The company’s next new project demonstrates the firm’s positive future outlook: “There are plans to enlarge the production and assembly facilities by another 15,000m2, which will enable Simon Plastic to perform well for the next 30 years.” n

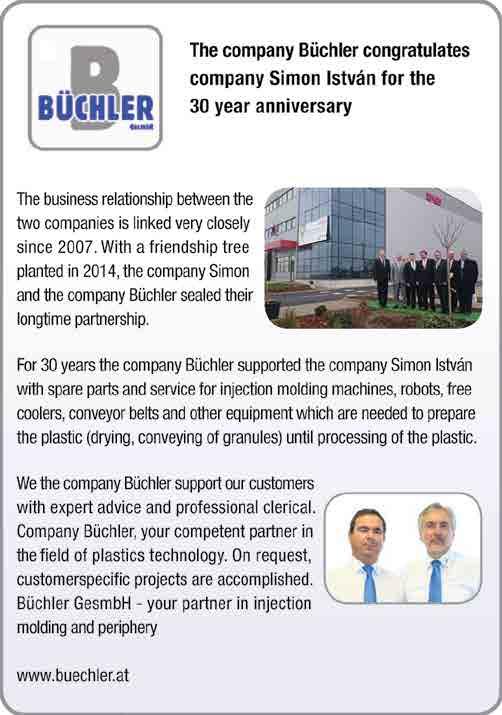