


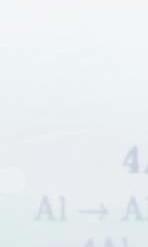

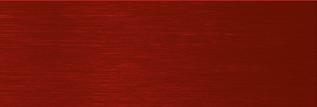
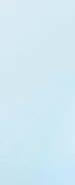
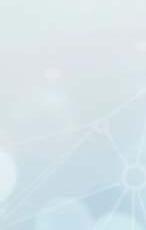
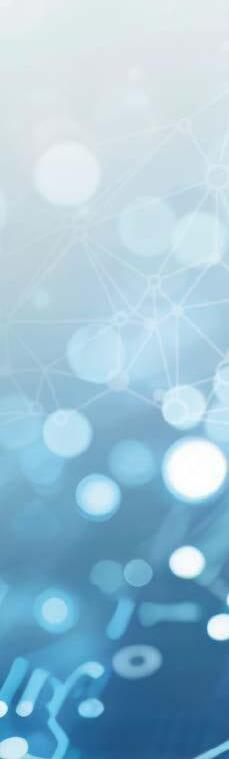
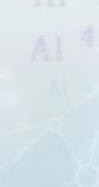
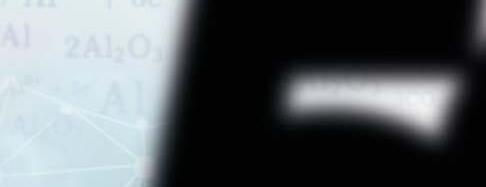
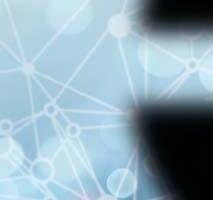


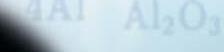
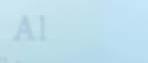
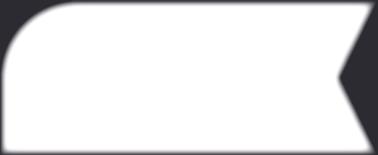
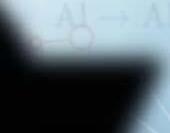
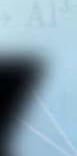

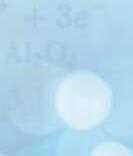



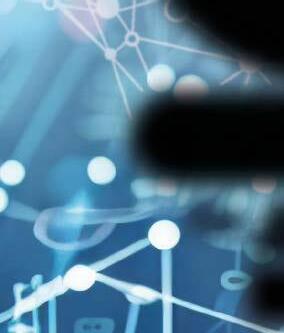
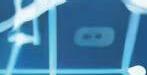
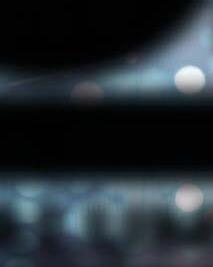









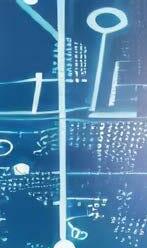
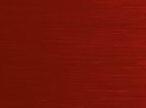

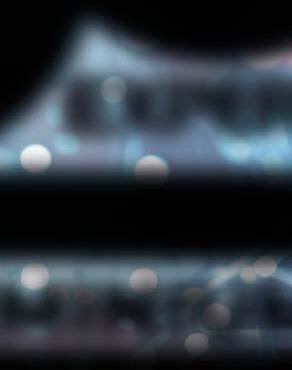









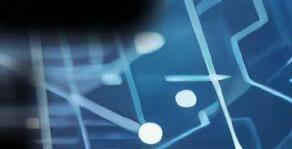
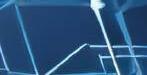
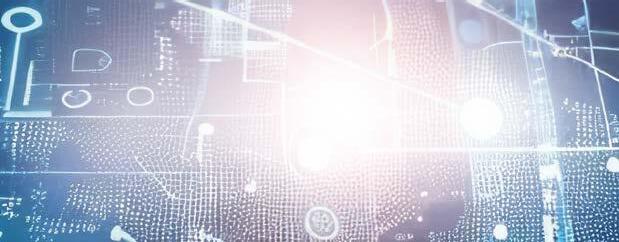
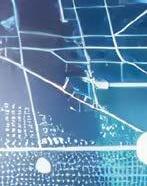



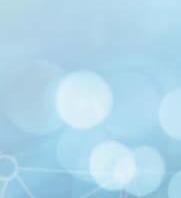
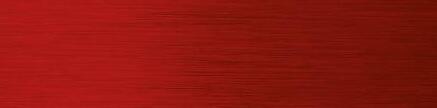
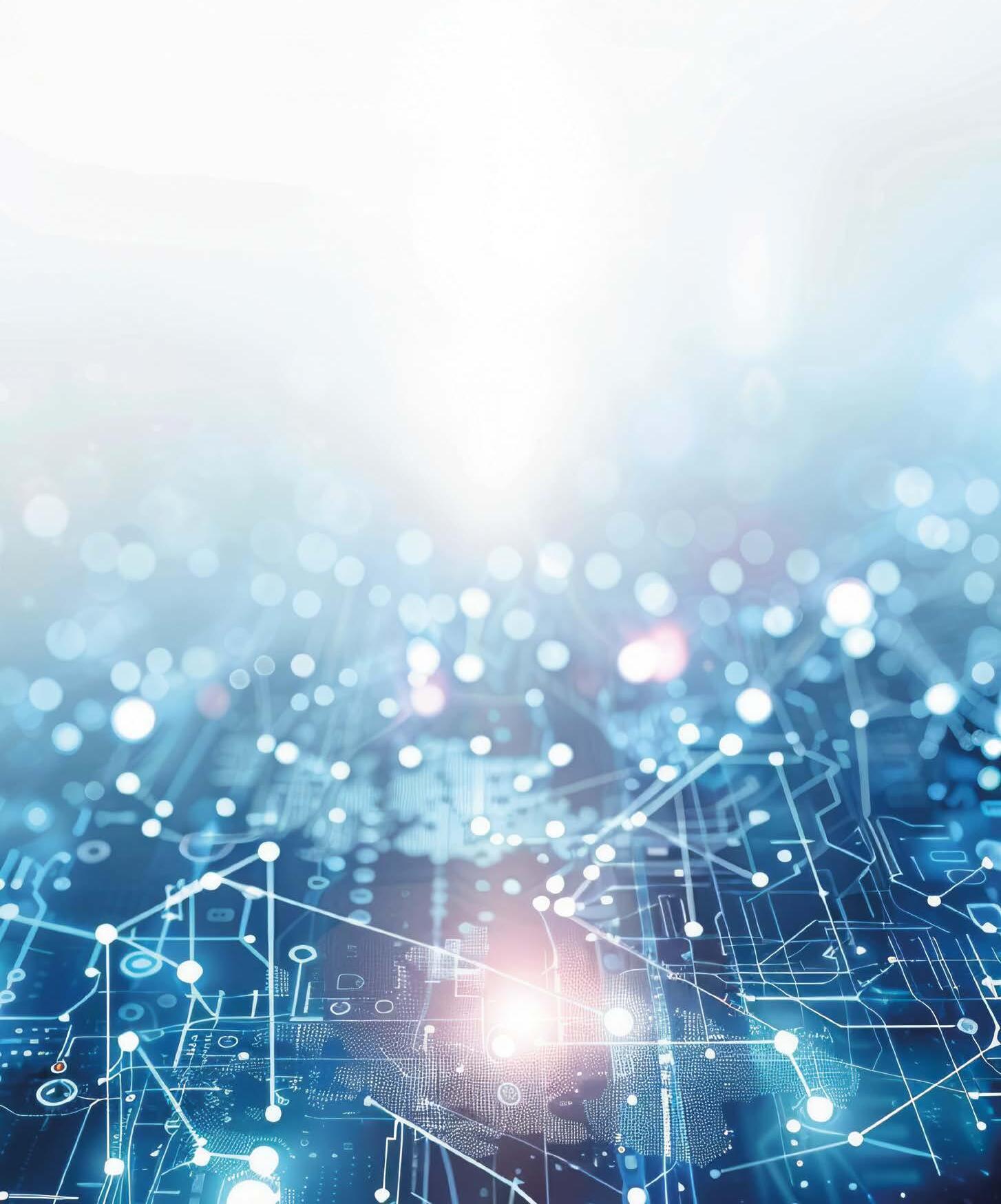
A new line of nanotechnology conversions for corrosion classes C3H - C4H - C5M
DOLLCOAT RS 103 is the first product in a new family of surface conversions for high-performance processes. It gives pre-treated surfaces extremely high-quality protection and corrosion resistance, whatever the nature of the paints used.
MAIN FEATURES
Multimetal no rinse product to be used at room temperature.
Applicable with nebulisation modules, through traditional recirculating or immersion nozzles.
Excellent pre-cataphoresis treatment.
REGISTRATI ORA
ESPOSIZIONE
CONFERENZA
TECHFOCUS
Esplora le più recenti tendenze e tecnologie nel mondo della pittura e dei rivestimenti, mentre stringi preziose connessioni con i leader del settore.
Paint & Coatings: il luogo dove l’ispirazione, l’apprendimento e le opportunità di networking si incontrano per trasformare il tuo business!
Unisciti a Noi per l’Aperitivo di Paint & Coatings!
Quando
Il primo giorno dell’evento, 22 ottobre 2024
Ora Dalle 17:00
Dove
NH Milano Congress Centre
POLYMER ACADEMY
sponsorizzato da
Coatings for Emboss’ Three-Dimensional Cladding Surfaces
Hard and Sustainable Non-stick Coating Revolutionises Shaping Processes In Injection Moulding and Die Casting
The HP series is specifically designed to uniform the thickness of powder applied on all parts of the painted support.
CARATTERISTICHE
La serie HP è pensata specificatamente per uniformare lo spessore di polvere applicata su tutte le parti del supporto verniciato.
Pulverit S.p.A. Italia
Via Carlo Reale, 15/4
20157 Milano-Italy
Tel +39 02 376751
email: pulverit@pulverit.it
Reduction between 15% and 30% of the powder required to paint the support. The HP series considerably reduces the “orange peel” effect due to the accumulation of powder in the parts adjacent to the critical points and minimizes the accumulation effect on the edges.
CARATTERISTICHE
Riduzione tra il 15 % e il 30% della polvere necessaria a verniciare il supporto. La serie HP riduce notevolmente l’effetto “buccia di arancia”
dovuto all’accumulo di polvere nelle parti adiacenti ai punti critici e minimizza l’effetto di accumulo sui bordi.
Pulverit Polska Sp. z o.o. ul. Strefowa 16
43100 Tychy-Polska
Tel. +48 32 329 14 11
email: biuro@pulverit.pl
Pulverit Deutschland GmbH Im Wert 3
73563 Mögglingen- Deutschland
telef.: +49 7174 7193000 email: info@pulverit.de
Pulverit Iberia s.l.u. c/ Caravis, 28, 1º 3ª 50197 Zaragoza Tel. +34 607163259
email: iberia@pulverit.it
ADVANCEMENTS
Evolution on Design: Kenosistec’s PVD Technology for Elegant, Durable, and Sustainable Finishes 90
ROAD TO 2050
Ice Cream Spoons and Golf Tees: Completely Absorbed by Nature 116
102
FOCUS ON TECHNOLOGY
Raising the Bar of Quality: Sirio Galv’s New Liquid Coating Plant for High-End Furniture and Lighting Accessories
146
SUCCESS STORIES
Delco Trailers Revolutionises Its Trailer Finishing Process with a New Automatic Coating Line
FOCUS ON TECHNOLOGY
Luxe Perfil: The Experts in the Impossible Rely on the New PrimeCoat® A109 Pre-Treatment Product’s High Performance
EcodePure: the Road to Water Recycling and Zero Discharge
SUCCESS STORIES
ItalMesh Clads the New Burger King in Rovereto with Perforated and Painted Aluminium Panels
SUCCESS STORIES
RIPOL in Bayreuth: Innovation and Avant-Garde Design 122
SUCCESS STORIES
PAN-DUR Paints Refrigeration
Equipment with Dürr’s EcoPaintJet –Without the Need for Masking
126
ROAD TO 2050
Ahead of Regulation for More Environmentally Friendly Coatings
130 HIGHLIGHT OF THE MONTH
The Evolution of Vernici Caldart: an Italian Success Story Through Fifty Years of Innovation 134 ANALYSIS
The Choice: The Ecological Transition and the HangOn Green Effect
142
150
HIGHLIGHT OF THE MONTH
Defil Srl: Innovation in Industrial Filtration
ROAD TO 2050
Olea FP: a Natural, Sustainable Option for the Paints & Coatings IndustryFrom Waste Stream to High-performance Functional Powders
154
UCIF INFORMS
Corporate Cybersecurity: a Shared Commitment to Digital Security
156
COLOUR STUDY
The Irresistible Charm of Pink
160 MEETING THE INDUSTRY
The strength of Europolveri products does not derive from the sole mixture of carefully selected raw materials, but rather from the people who study, model and formulate powder coatings thanks to more than 40 years of experience, and provide customers with the best solutions on the market A clear corporate philosophy and a shared vision have allowed to supply a vast range of products for three generations With more than 1000 products available in stock and over 40,000 already formulated, Europolveri offers infinite solutions to customer requests
Alessia Venturi Editor-in-chief Direttore Responsabile
Have you ever reflected on the difference between planning and designing, between a project and its development?
It is the same as between dream and reality.
Dreaming, like planning, belongs to a creative, imaginative, detailed, and inspirational phase with unrealistic but visionary traits. It connects the subject with reality, the designer with the issue to be addressed.
Reality, like the design activity, is the construction phase, the realisation of the idea – of the dream, to be more precise – with less vivid colours, with the sacrifice of a few details, and with the necessary compromise between what is feasible and what is not.
In architecture and design, therefore, planning refers to the creative thinking behind a project, the visionary approach intended to guide the subsequent realisation, whereas design refers to the technical process by which an idea is transformed into a tangible product, such as a building or an object.
Bridging the gap between a project and its development requires having all the technologies and materials, including finishes, needed to translate an idea into reality.
This is the most challenging phase for designers, who sometimes lack the necessary technical information on materials and their performance.
That is where CMF (Colour, Materials, Finish) comes in, a field focussing on the chromatic, tactile, and decorative identity of products and environments. Over the years, CMF experts have worked with designers on the one hand and manufacturers of materials and finishes on the other hand, to promote knowledge sharing, training, and collaboration to bring the design world, more inclined to breaking down limits, closer to the industrial one, constantly dealing with technical and scientific limits.
Since its inception in 2010, ipcm® has had the metal architecture sector, including architects and designers, among its preferred targets, providing it with precise information about any innovation in the world of surface finishing materials – in other words, what constitutes the skin of a product, the interface between an object and the environment.
This special Aluminium issue of ipcm® features a series of articles and success stories on the peaks of innovation achieved in the surface treatment of aluminium, a material that is increasingly popular in architecture and beyond.
As in previous years, ipcm® is also a media partner of the most important platform dedicated to the aluminium sector, the international trade fair Aluminium in Düsseldorf (Germany).
We will gladly meet you among the stands to discuss the most significant issues, trends, and developments in the industry.
Gianmaria Guidi,
Germedia
Srl – Brescia, Italy gianmaria.guidi@germedia.it
Unfortunately, and increasingly often in the coating industry too, our society fails to anticipate and avoid the loss of knowledge, skills, and expertise levels. In 1974, Kaufman called this phenomenon “the obsolescence of skills”, referring to the lack of up-todate knowledge or proficiency a worker needs to continue to perform their current or future job properly. More and more often in our professional activities, major problems arise precisely from the failure to compensate for physiological information asymmetries between contractual parties, which can no longer be adequately compensated due to a lack of specific technical expertise. In recent decades, market
dynamics have favoured economic and financial aspects to the detriment of investment in technical training, taking it for granted that the necessary technical elements were simply ingrained in the common consciousness. The case described below attempts to refocus attention on a calculation method that helps define the economic impact of paint products in a coating project.
Practical coverage or consumption calculation criteria Every coating project requires a thorough feasibility analysis that considers various factors and constraints, e.g. time-related,
technological, regulatory and, last but not least, economic. In particular, this article analyses paint coverage as a cost item directly affecting the coating project’s economic factor.
To reach a coating treatment’s expected performance and durability as defined in the design phase, it is necessary to achieve and maintain the specified dry film thickness (DFT) value. That ensures the coating acts as a protective barrier, preventing corrosive agents such as water, salts, and oxygen from reaching the metal surface. Insufficient DFT can indeed leave vulnerable areas, exposing the metal to corrosion. In contrast, adequate DFT increases the coating’s resistance to mechanical and chemical stress, prolonging its service life and protective action and reducing the need for frequent maintenance and repairs. A sound coating project should also use the appropriate terminology to define the desired DFTs, also considering that, in the context of coating treatments, nominal quantities translate into actual measures conditioned by wide tolerances, which are absolutely necessary and unavoidable.
Various international standards can be used to determine the dry or wet thickness of a coating. This article focuses on dry thicknesses as an objective parameter for qualitatively evaluating the applied cycle. The coating work can be divided into two main macro-phases: design and execution. In the design phase, the designer defines the coating’s nominal dry film thickness (NDFT), the required sampling plan, and the
measurement tolerances (e.g. +/- 20%). In the execution phase, the applicator applies the coating and strives to meet and maintain the set standards, initially measuring the applied wet film thickness (WFT) and then checking the final dry film thickness (DFT) achieved after the polymerisation step.
It is important to emphasise that the terminology and acronyms used to define the desired values are not universal but strictly depend on the technical regulations adopted by the designer. For example, in ISO 2808 and ISO 19840, the acronym DFT may refer to two different measurements, one of which rules out surface roughness after shot blasting. These differences are of fundamental importance when calculating the coverage of a coating treatment.
To achieve the specified NDFT, the applicator must calculate the coverage of the products that make up the coating system by taking into account at least the following aspects:
The theoretical coverage of a paint product (fig. 1), considering its dry solid by volume (S.V.) and the possible dilution required for its application, which increases the value of volatile organic compounds (VOCs) and decreases the DRV, with a direct impact on the final DFT.
The correction factor for shot-blasted surfaces, which takes into account the fact that part of the paint is deposited within the surface irregularities, creating a so-called “dead volume” (fig. 2). Although such
volume is filled by the product, it does not contribute to the effective protection of the substrate, as it does not increase the thickness of the dry film covering the exposed areas. Therefore, it is crucial to consider this correction factor when calculating product coverage, as it directly affects the effectiveness of the protection provided by the coating treatment. Ignoring the dead volume could lead to underestimating the amount of paint required to achieve the necessary degree of protection.
The necessary overconsumption factor (NOC), representing an amount of paint product that does not disperse into the environment but rather is deposited on the surface to ensure compliance with the required NDFT values (fig. 3): such overconsumption is not due to the applicator’s lack of skill but is an unavoidable discontinuity in the coating process. Any application method inevitably generates variations in the thickness of the organic film deposited on the surface. Therefore, a larger volume of paint must always be applied to ensure compliance with the minimum DFT value defined in the sampling plan.
The loss factor due to the geometry of the object to be coated mainly affects spray application operations, but it should be considered that, to a lesser extent, it can also affect brush or roller application ones, depending on the complexity of the part’s geometry itself.
The loss factor due to overspray affects spray application and can be
influenced by various elements, such as the distance from the surface, the complexity of the part’s shape, the presence of air currents, the type of atomisation used, and the spray pressure set by the operator.
Any advance estimate cannot be exact and must be confirmed or denied after completion of the process. However, since it is necessary to calculate the economic impact of paint consumption at the quotation stage, it can be useful to resort to computational formulas using theoretical correction coefficients. If a company is consistent in using these formulas and in subsequently verifying the theoretical coefficients initially applied, it will be able to reduce its error margins, thus consolidating its position in the market with a high level of qualitativeeconomic competitiveness.
The theoretical coverage of a paint product expressed in square metres (m2) per litre (l) applied is generally determined using the following formula:
On the other hand, a paint product’s consumption expressed in litres per square metre applied is determined using the following formula:
Where:
TC = Theoretical Consumption
SV = Solid by Volume, the percentage of product remaining on the surface after evaporation of the solvent
DFT = Dry Film Thickness, the required thickness expressed in microns. The formula assumes ideal conditions and does not take into account factors such as overconsumption, dead volume, or losses due to overspray that may reduce the product’s actual coverage.
Dead volume correction coefficient
The correction coefficient for the dead volume (fig. 2) is essential to compensate for the loss of paint product that is deposited within surface irregularities and, therefore, does not contribute to effective protection.
This coefficient helps estimate the actual amount of paint required to
For decades, Radial has been designing, building and installing tailor-made coating plants for metals, plastics and wood. Our systems are the ideal choice for those who desire a cutting-edge turnkey solution.
achieve the desired result.
ISO 19840, in accordance with ISO 8503-1, provides guidance on how to apply this coefficient. Table 1, provided by these standards, simplifies the practical application of this coefficient, allowing the product coverage calculation to be adapted by considering surface discontinuities and their associated losses.
DFT sampling plan. In this article, specific guidance is given according to the geometry of the part to be treated, leaving the reader to adapt the coefficient according to their past and future experience. This factor reflects the actual paint amount deposited on the treated surface, and although it relates to geometry, it does not directly imply the loss of material due to the part’s geometry itself, which will be treated separately. To distinguish these two coefficients, we will use here the acronym NOC followed by the type of object geometry.
NOC for linear geometry:
Linear geometry refers to large, flat-surfaced sheets, profiles, and tubular structures where the spray paint application does not involve frequent direction changes. This application process allows the operator to maintain a constant dispensing position over at least 90% of the surface to be treated. The stripe coating technique is not mandatory, and if used, it should be limited to a maximum of 5% of the total surface area.
Therefore, in the case of a shot-blasted surface, it is necessary to define its type of surface profile and consequently increase the NDFT of the first layer by the correction value.
NOC correction coefficient
As this article introduces a new factor to balance the interests of all parties involved in a coating project, the following considerations will be based on empirical data collected experimentally during inspection activities (fig. 3). It should be noted that this factor is affected by multiple conditions, such as the type of application process, the complexity of the object geometry, the method used, and the tolerances indicated in the
NOC for complex geometry:
Complex geometry refers to sheets, profiles, and tubes assembled to form complex structures. In such cases, the spray application of the paint product requires numerous changes of direction, preventing the applicator from maintaining a constant dispensing position over more than 50% of the surface to be treated. Stripe coating is necessary but should cover a maximum of 15% of the surface.
NOC for intricate geometry:
Intricate geometry refers to sheets, profiles, and tubes assembled to form intricate structures. In such cases, the spray application of the
with a complete service that includes system design manufacturing, installation, technical support and chemicals
paint product requires numerous and frequent changes of direction, preventing the applicator from maintaining a constant dispensing position over the entire surface to be treated. Stripe coat application is therefore necessary and should cover more than 15% of the surface.
Table 2 also provides values for roller and brush application.
Actual paint loss correction coefficient
The actual paint loss must be related to transfer efficiency (TE), which represents the amount of applied paint that actually reaches the surface to be coated (figs. 4 and 5). Two main factors influence such efficiency: the object’s geometry and the application method. Based on the previous definitions, we will use the term “loss” similarly to the acronym NOC, to differentiate the required correction coefficients (table 3).
Loss for linear geometry:
This refers to large, flat-surfaced sheets, profiles, and tubular structures where the spray paint application does not involve frequent direction changes, allowing the operator to maintain a constant dispensing position over at least 90% of the surface to be treated. Under these conditions, almost all the applied paint is deposited on the surface. However, factors such as the type of atomisation technology, the distance from the surface, the geometry of the workpiece, the presence of air currents, and the delivery pressure set by the operator can affect the final result.
SPRAY BOOTHS WATER SLUDGE REMOVAL
RESIN DEMINERALIZATION SYSTEMS
REMEDIATION OF CONTAMINATED SITES
BIOLOGICAL SYSTEMS BATCH TREATMENTS
PHYSICAL-CHEMICAL SYSTEMS
ADSORPTION FILTRATION
REVERSE OSMOSIS
MEMBRANE SYSTEMS
EVAPORATORS
BIOGAS BIOMASS SYSTEMS
OIL SEPARATORS
DESANDERS
DESALINATION SYSTEMS
PYROCHAR
OTHER SYSTEMS
CHEMICALS
Loss for complex geometry:
This refers to sheets, profiles, and tubes assembled to form complex structures, where the spray application of the paint product requires numerous changes of direction and prevents the applicator from maintaining a constant dispensing position over more than 50% of the surface to be treated. In these circumstances, part of the paint is not deposited on the surface due to the geometry of the workpiece, which facilitates the dispersion of the applied product. Additional factors, such as the type of atomisation technology, the presence of air currents, and the dispensing pressure set by the operator, can further aggravate dispersion.
Loss for intricate geometry:
This refers to sheets, profiles, and tubes assembled to form complex structures, where the spray application of the paint product requires continuous direction changes and prevents the applicator from maintaining a constant dispensing position over the entire surface to be treated. In this situation, a significant amount of paint is not deposited correctly on the surface due to the highly complex geometry of the workpiece, which facilitates the dispersion of most of the applied product. Additional factors, such as the type of atomisation technology, the presence of air currents, and the dispensing pressure set by the operator, can further aggravate dispersion.
For computational calculations related to a spray coating project on a structure with linear or intricate geometry and a “coarse” roughness
profile, in order to achieve an NDFT of 200 microns with a paint product (PP) with 80% DRV, the following calculation scheme is suggested as per the two examples
Conducting a thorough preliminary economic analysis is essential to ensure durable coating results. The project variables and their correction coefficients should be discussed and agreed upon in specific meetings between the customer and the contractor.
Corrective factors such as the necessary overconsumption, if not adequately considered, can have significant economic consequences. These costs cannot be overlooked in the design phase nor entirely attributed to the applicators, assuming unrealistic execution skills. All the parties involved should consider and concretely agree on the mentioned correction factors to meet the required treatment performance standards.
Dr. Gianmaria Guidi has over thirty years of experience in the industrial and corrosion protection coating sector. Over the years, he has specialised in the management of technical-legal disputes and is regularly registered with the Official Register of Court-Appointed Experts (C.T.U.) of the Italian Ministry of Justice, further enhancing his previous NACE and FROSIO certifications.
Everything stated and reported here is intended for the benefit of the industry.
EXAMPLE 1
Total NDFT adjusted by the coefficients =
Project NDFT adaptation scheme
Values in µm
NDFT as per design 200
Dead volume correction factor (for the primer only) + 40
NOC correction factor (intricate geometry =40%) + 80
Actual paint loss correction factor (intricate geometry =50%) + 100
Total NDFT adjusted by the coefficients = 420
Theoretical and
Increase over theoretical consumption + 110%
Let‘s talk about powder coating. A technology that is proven since decades and actually, it‘s just getting started with FLOWSENSE. FLOWSENSE? It‘s a software masterpiece and a bunch of small sensors that do big things: Consistent powder output from the first to the last workpiece. Reliability, measured in real time. Put quality on repeat!
The new ALIT-Service Branches in Serbia and Portugal will bring high-quality paint-stripping services closer to its clients.
The chemical paint stripping company ALIT Technologies has recently proudly announced the opening of its first two international branches in Portugal and Serbia, under the brandname ALIT-Service. The expansion testifies the beginning of a new chapter for the Italian business, that is willingly to spread its paint stripping services to new global markets.
“ALIT-Service represents an innovative and strategic initiative, which is set to transform the landscape of industrial paint stripping. What makes our service unique is its bold and personalised approach, exclusively using top products to meet the diverse needs of customers worldwide”, has stated Loris Rossi, the CEO of ALIT Technologies. With the introduction of ALIT-Service, the company then further expands its already extensive range of offerings, in order to bring high-quality services closer to its clients. As a matter of fact, the new openings aim to bridge geographical gaps and meet the growing demand for contract
paint stripping services in regions not yet covered by its distributors. However, the new branches in Portugal and Serbia are just the start of an ambitious expansion project: ALIT Technologies plans to open many more strategic locations around the world. According to the company, its expansion is not only a sign of ambition but also a concrete commitment to supporting economic growth and sustainable development in local communities, creating new jobs and providing increasingly in-demand services.
“With this revolutionary initiative, ALIT Technologies embraces change, redefines industry standards and opens the doors to a new and exciting chapter of global success, demonstrating our vision for a future where innovation and excellence are fundamental pillars,” has concluded Rossi.
For further information: www.alit-tech.com
The acquisition of Monarch Chemicals will strengthen the market position of Brenntag globally.
Brenntag has recently acquired Monarch Group Holdings, a British distributor of chemicals for several industries, including paints and coatings.
“The team at Monarch have built a great product and service offering for their broad customer and supply partner base, and we look forward to growing and expanding that offering together. Brenntag gains expertise, infrastructure, as well as expanded liquid and powder blending capabilities with this transaction. With our acquisition strategy, we expand our last mile service operations to bring a broader portfolio of products and value-added services to customers, supported by our regional supply chain services within our global network. With this extended offering, all our customers in the UK can benefit going forward,” has stated Russel Argo, Regional President Brenntag Essentials EMEA.
“We take great pride in the level of service and support we can offer our supply partners and customers. Our independence made us flexible, but joining Brenntag, a truly global distributor, will give us the scale and network we can use to grow our business and better serve our customers with a wider range of products and services,” has added Jon Hill, Managing Director of Monarch.
For further information: www.brenntag.com
Eurotherm solves every problem concerning painting processes, creating complete lines for the entire process.
Our structure is organized and flexible and able to satisfy the most demanding requests.
Customers who turn to Eurotherm are customers who, despite knowing the “painting process”, want to improve production by adopting highly customized technical solutions.
Employees 205 Plants realized in 2023
(IT)
(FR) Sigmaringen (DE) Brussels (BE) Other locations
Eurotherm S.p.A.
T +39 011 98 23 500 | M info@eurotherm.eu
Eurotherm France S.A.S.
T +33 6 76 72 48 65 | M france@eurotherm.eu
Eurotherm Oberflächentechnik GmbH
T +49 7571 92795 10 | M germany@eurotherm.eu
Eurotherm Benelux Srl T +33 6 47 44 96 27 | M dekergorlay@eurotherm.eu
The upcoming coating system from Dürr will enable Airbus to paint the rear centre tank of the A321XLR aircraft with enhanced energy efficiency and reduced carbon emissions.
The German engineering company Dürr has taken on its most significant individual project to date for the Airbus Group’s division, Premium AEROTEC. The project involves constructing a state-of-the-art paint shop in Augsburg (Germany) for coating the new rear centre tank of the Airbus A321XLR, crucial for the aircraft’s longrange capability, extending its reach by 8,700 kilometres.
The paint shop will be a turnkey system, incorporating cutting-edge technology to enhance energy efficiency and reduce emissions. Notably, it will feature an all-electric exhaust purification system, marking a first for Premium AEROTEC’s facilities. This system, based on regenerative thermal oxidation, promises to significantly minimise CO2 emissions.
Advanced surface protection and energy efficiency
The project will cover the entire coating process, from pretreatment to sealing and painting. The new paint shop will include sealing, cleaning and painting booths, as well as surface and leak testing areas. High standards for corrosion resistance and diffusion will ensure that the tank surfaces withstand extreme conditions without corroding. Moreover, to achieve these high standards while maintaining energy
The fuel tank integrated into the fuselage of the Airbus A321XLR is the key component in transforming the former short- and medium-haul planes into the new long-haul version.
efficiency, Dürr is implementing a component-specific air ducting system. This system reduces the amount of air needed for conditioning – thus lowering energy consumption. The energy recovery systems will also recycle up to 65% of the energy from the exhaust air, further enhancing efficiency.
Sustainable pollutant removal
Premium AEROTEC’s commitment to sustainability is underscored by its adoption of Dürr’s Oxi.X RV all-electric exhaust purification system that operates without an open flame, resulting in very low nitrogen oxide emissions. In addition, it is designed to run on green electricity, eliminating additional CO2 emissions.
Dürr’s Oxi.X RV system also includes a Sorpt.X CD unit that concentrates the exhaust air streams to enhance economic efficiency, reducing the volume and increasing the solvent concentration. This allows the downstream Oxi.X RV unit to be smaller and operate without additional heating energy, optimising the cost-benefit ratio.
For further information: www.durr.com
The exhaust air is purified with a flameless Oxi.X RV in accordance with the principle of regenerative thermal oxidation (RTO).
Lechler Tech water-based CAM-compliant products offer high performance, reduce environmental impact thanks to low VOC emissions and guarantee quality finishes in compliance with European regulations.
Lechler Tech offers solutions that meet its customers’ needs without compromising the health of the planet. Choosing waterbased products complying with CAM (Criteri Ambientali Minimi
- Minimum Environmental Criteria) is an important step towards a more conscious future. The features and benefits of Lechler Tech’s CAM-compliant water-based products include as follows:
• Reduced VOC emissions: water-based products have lower emissions of Volatile Organic Compounds (VOC), helping improve air quality and reducing environmental impact.
• Safety: water-based products are generally less toxic and safer to handle than solvent-based products, protecting the health of operators and end users.
• High performance: besides ensuring a reduced environmental impact, Lechler Tech’s products provide excellent performance in terms of durability, resistance, and finishing quality.
• Regulatory compliance: being CAM-compliant means being in line with current European building regulations (Green Public Procurement), which facilitates access to tenders and contracts.
• Compliance with international protocols BREEAM/LEED/WELL: compliance with CAM allows accessing LEED/BREEAM/WELL certifications.
These water-based products have passed the EN 16516 low-VOC emission test required by IAC GOLD in accordance with EN 16000 and are CAM approved, which means they are totally free of HEAVY METALS, with low or no VOC EMISSIONS, and with controlled VOC CONTENT.
Lechler Tech’s water-based products guarantee high-quality finishes on a wide range of metal and plastic substrates. They offer remarkable versatility, allowing for the creation of glossy, matte, pastel-coloured, and even metallic/micalised effects and textures.
For further information: www.lechler.eu
©
Redox One Coat from AkzoNobel Interpon is a powder coating designed to protect metal surfaces from corrosion and UV damage, all while streamlining production time and reducing costs.
The Czech shelving systems manufacturer
Trestles has turned to international paints and coatings supplier AkzoNobel for a quality and durable powder coating, opting for Redox One Coat.
“In the gates and fences sector in particular, there are many companies we compete against, most of whom have more experience than us. To stand out from the competition we need to have the best quality, and since Redox One Coat can be applied to both stainless steel and zinc steel, we are able to deliver the quality our customers are looking for at the price they are willing to pay. In salt spray tests, Interpon Redox One Coat performed the best in protecting our products against corrosion. We also tested it on different steel surfaces, as well as some Beta products we currently have on trial, with excellent results. We wanted to be sure the product would perform, even
in rain or snow, and since using Redox One Coat there have been no complaints,” has stated Daniel Molnár, Procurement Manager at Trestles.
Technically, Interpon Redox One Coat enables Trestles to reach corrosion protection up to C4M and high UV durability in a single coat which requires only a base chemical pre-treatment, while traditional powder coatings require a primer layer for corrosion protection followed by a topcoat for gloss and UV protection. In addition, Trestles offers its product in four colours: Anthracite Grey, Jet Black, Moss Green and Blue/Grey.
“We are looking to increase our production and Interpon Redox OneCoat will help us.
A single coat application will have a positive impact on reducing the time and cost of production and will help keep us competitive. AkzoNobel not only has the products and
colours we need, but its people are also very friendly and flexible to work with. The technical support it provides is certainly one of the reasons why we continue to be one of the most important manufacturers in the entire European Union,” has added Daniel Molnár.
“Businesses like Trestles need simple, effective solutions to get the job done with high quality but quickly, easily and at a lower cost. With Interpon Redox OneCoat we’ve removed the need for a second process for the same job, saving on powder, energy and labour and maximizing productivity while delivering desired quality. It’s helping Trestles to be competitive in a new market, and further improve their business performance,” has added Sanal Limoncuoglu, Commercial Director South and East Europe of AkzoNobel Powder Coatings.
“In a competitive market, Trestles is offering customers a new portfolio of fencing systems, and recognises that quality is key. We demonstrate this quality with what is visible at first glance - the powder coating system of the Interpon Redox One Coat series from AkzoNobel,” has concluded Pawel Nowak, CEO of Trestles.
For further information: www.interpon.com/us/en
BYK-Gardner has appointed its new President and CEO, Dr. Jörg Krames.
The global measuring instrument manufacturer BYK-Gardner, headquartered in Geretsried, Upper Bavaria (Germany) and part of the ALTANA Group, welcomes its new Managing Director, Dr. Jörg Krames. As a trained mechanical engineer with a doctorate in chemical engineering, Jörg Krames takes over the global management of the company with its foreign representatives and around 350 employees. BYK-Gardner is a leading supplier in the field of measuring instruments. The testing and measuring instruments objectively assess the quality of colour, gloss and appearance as well as the physical properties of paint and plastic products. Last year, the company acquired measuring instruments for non-destructive, high-precision coating thickness measurement.
Jörg Krames previously spent 15 years at ECKART, also an ALTANA Group company, as Vice President Global Key Account and responsible for Business Line Management Coatings. Prior to that, he worked for BASF Coatings as Director Key Account in Japan and Germany for leading car brands such as Toyota and Volkswagen. His main goals are to drive forward the brand perception of the premium measuring instrument manufacturer and to drive forward the digitalization of business processes. Looking ahead to the upcoming generational change, transformation projects and the continuous development of employees are among the focal points of his business
strategy to strengthen BYK-Gardner as the market leader. “We are delighted to have found a managing director in Jörg Krames within our own ranks, who not only has excellent professional expertise, but is already very familiar with the ALTANA Group,” said Dr. Jörg Hinnerwisch, BYK Executive management and ALTANA Management Board member. “With his strong focus on customers, technology and innovation, Jörg Krames is continuing to lead BYK-Gardner on the road to success.”
For further information: www.byk-instruments.com
HMG Paints has recently launched Hydrosol, a new range of hybrid coatings designed for the metal fabrication marketplace.
The first product to launch in this range is Hydrosol QD Primer, an alkyd-based, quick-drying primer designed for ultimate versatility and efficiency. In fact, it improves adhesion and moisture resistance, while granting good corrosion protection thanks to the incorporation of modified Zinc Phosphate. This primer is ideal for structural steel, chassis and steel fabrications, and can be applied by using either roller, airless or conventional spray methods.
Moreover, the first user who are adopting the Hydrosol QD Primer are identifying several benefits, including increased coverage compared to competitor products and improved efficiency in application. This is thanks to volume solids of Hydrosol QD Primer which stands at 55% in comparison to approximately 40% for competitor equivalents.
“Our new Hydrosol QD Primer represents a significant advancement in protective coatings and is a testament to the work done by our Research & Development team to bring innovations to the market. This product not only meets the high-performance standards our customers expect from us, but also aligns with our commitment to environmental sustainability. It is the first piece of the jigsaw in our Hydrosol brand, with a variety of exciting products set to join this range in the near future,” has stated Paddy Dyson, Marketing Manager of HMG Paints.
The second to be launched will be the Hydrosol Compliant DTM, a Direct-to-Metal that can be applied directly to bare or primed metal surfaces. This technology is PG6/23 11 Compliant and ideal as a single coat primer finish for stillages, skips, containers, agricultural and construction equipment and machinery. It has lower VOCs in comparison to solvent based equivalent products and it is available in a wide range of colours, including RAL & BS.
For further information: www.hmgpaint.com
The new X-SMART PRO Automatic Dispenser from Fast & Fluid Management combines repeatability and durability.
Fast & Fluid Management has recently presented the new X-SMART PRO Automatic Dispenser, specifically engineered to provide unparalleled repeatability and with a robust design which is tailored for demanding environments. By leveraging an advanced piston pump technology, it delivers precise colour dispensing, crucial for achieving consistent results required in various industries.
The automatic paint dispenser enhances the previous X-SMART series with a durable metal case and an upgraded brush, ensuring optimal cleaning operations. In addition, it also introduces additional safety features – including a front door sensor that guarantees operators safety without compromising functionality.
“In the fast-paced world of industrial tinting, precision and durability are not just simple requirements, but the foundation upon which businesses can build their reputation. So, recognising the challenges faced by different locations across the globe, the X-SMART PRO Automatic Dispenser is engineered to deliver both speed and robustness, crucial for maintaining continuous and reliable operation. Its steel-armoured design ensures it can withstand the rigors of heavy usage, making it an ideal solution for businesses looking to reduce downtime and enhance operational efficiency”, has declared the company.
For further information: https://emea.fast-fluid.com
From Turin to Cassino (Italy): the degreaser CONDORINE SG 576 N developed by Condoroil Chemical, already used in the bumper cleaning line of the Stellantis plant in Turin-Mirafiori, has now also been implemented in the Cassino site’s production line, with considerable savings in energy and water consumption.
Energy saving, ecology, and low environmental impact have always been key elements for the Stellantis Group. With this in mind, about a year ago, Condoroil Chemical began testing its degreaser CONDORINE SG 576 N for integration into the final cleaning phases of plastic components.
Product features
CONDORINE SG 576 N is a one-component low-foam detergent, active even at room temperature. Its use ensures considerable energy savings and lower water consumption compared with traditional products. The almost total absence of foam and the innovative features of its formulation also
reduce dragging issues, thus minimising the progressive pollution of post-cleaning rinsing baths.
A successful project
The project was developed in collaboration with the Painting Process Engineering PPE Materials Approval team at Turin-Mirafiori, where the product is now used in the cleaning phase of the bumper production line, confirming the positive outcome of the preliminary tests carried out. All the quality requirements imposed by Stellantis for product approval were met from the outset, as well as the considerable savings predicted during the design phase.
The benefits for the customer included as follows:
perfect cleanliness of the treated components;
considerable energy savings by applying the product at room temperature;
lower product consumption;
lower water consumption, including for rinsing. An 80% reduction in demineralised water consumption was observed in the final rinse phase (from 500 l/h to 100 l/h).
From Turin to Cassino: implementing CONDORINE SG 576 N Afterwards, CONDORINE SG 576 N was presented to the Plastic Unit of the bumper production and coating department at the Stellantis plant in Cassino (Frosinone), where a two-component solution was used that required a working temperature of at least 55 °C, like almost all current plastic degreasers. Now, by working at room temperature, they achieved considerable savings without any compromise on the quality of results. The implementation of this product in the Cassino plant was possible thanks to the Process Improvement team, which played a vital role in the early start-up phases and continues to closely monitor the regular production process.
For further information: www.condoroil.com
Zuccarelli, Condoroil’s Industrial Coating Sales
The new Gossau-based facility features expanded production areas, advanced testing labs and eco-friendly systems, allowing Gema to enhance its manufacturing capabilities and increase production capacity.
The powder coatings application systems supplier Gema has recently relocated to a new facility in Gossau (Switzerland). This move underscores the company’s commitment to advancing manufacturing capabilities and boosting production capacity.
The new Gossau facility boasts spacious office environments, state-of-the-art meeting rooms and modern technological infrastructure. It features a high-bay warehouse and expanded production areas, enhancing operational efficiency. Additionally, the facility includes a sophisticated test and
customer application laboratory with advanced coating lines, enabling more effective and practical coating tests.
Demonstrating its commitment to sustainability, Gema’s new location is equipped with photovoltaic systems for energy generation and a brine/water heat pump system for heating, highlighting the company’s dedication to environmentally friendly practices.
For further information: www.gemapowdercoating.com/en/
Leading companies rely on vacuum distillation systems for the sustainable treatment of industrial wastewater.
Do you want to benefit from a zero liquid discharge production with VACUDEST aswell?
Just contact our Experts!
KANSAI HELIOS Italy and Weilburger Coatings Italia continue their successful course together.
After KANSAI HELIOS announced the successful acquisition of Weilburger Coatings in May 2024, Weilburger Coatings Italia and KANSAI HELIOS Italy have started to identify and leverage initial synergies. This strategic integration not only expands the production capabilities in Italy but also reinforces KANSAI HELIOS’s position as a system supplier on the market. With local production of both –industrial powder and liquid coatings – the company's expertise and service offerings are now stronger than ever. Additionally, the strategic locations of the production units and the enhanced storage facilities in Bergamo ensure greater flexibility and more efficient supply chains. From now on KANSAI HELIOS Italy and Weilburger Coatings Italia will combine their expertise and strengths to serve the Italian market with a unified approach.
Over the past few years, KANSAI HELIOS Italy has experienced significant growth through strategic investments and continuous improvements on its powder coatings production locations in Riese Pio X (Treviso) and Tezze sul Brenta (Vicenza). The company expanded its production capabilities by adding new production lines and upgrading existing facilities with state-of-the-art equipment. Advanced systems are being implemented to enable paperless production and full product traceability, enhancing both, efficiency and sustainability. Focusing on innovation and sustainability, KANSAI HELIOS Italy is developing new products such as low-temperature cure powders and formulations using recycled or natural raw materials. Their unwavering commitment to excellent customer service is evident in their efforts to ensure maximum product availability, short delivery times, and continuous technical assistance. With 22 different quality approvals, KANSAI HELIOS Italy became a preferred partner for the industry. Weilburger Coatings Italia has also made significant strides in recent years, driven by strategic investments and ongoing improvements. The company specializes in industrial liquid coatings and operates from a state-of-the-art production site in Sotto Il Monte, Bergamo.
The company has been focusing on expanding its infrastructure with projects like the implementation of new warehouses, enhancing both, storage and logistics capabilities. This expansion supports their strategic goal of serving diverse industries including houseware, stoves and heating appliances, railway vehicles, the eyewear industry, small items and zippers, aluminium packaging, and coil and foil sectors.
Weilburger Coatings Italia is committed to quality and sustainability, holding certifications such as ISO 9001-2015, ISO 14001-2015, and ISO 45001-2018. With the acquisition of Weilburger Coatings Italia, KANSAI
HELIOS is significantly expanding its presence in Italy. The strategic alignment of the two companies will not only expand the presence of KANSAI HELIOS in Italy, it also broadens the production capabilities and most of all, strengthens its position as a system supplier. Now, with two central hubs, KANSAI HELIOS offers a comprehensive range of industrial coatings: the Bergamo site for liquid coatings and the Treviso and Vicenza sites for powder coatings, architectural coatings, and car refinishing.
Bine Pangršič, Managing Director of KANSAI HELIOS Italy, assures: “We want to fully utilize the expertise of the Weilburger Coatings team for our customers and confidently place our industrial coatings business in the hands of our colleagues in Bergamo. Weilburger Coatings Italia will thus become the hub for industrial liquid coatings in Italy - also for KANSAI HELIOS products, which of course will be retained. Weilburger Coatings Italia will only take over the trading part and act as a local service partner
with its experts for liquid coatings together with the well-known sales representatives for liquid coatings from KANSAI HELIOS, who will move to Bergamo. This means that the usual contacts will remain.”
By joining forces and focusing on their core businesses, KANSAI HELIOS Italy and Weilburger Coatings Italia are set to improve performance by leveraging synergies and maximizing efficiency. The integration of Bergamo’s production site into the KANSAI HELIOS network offers, for example, extended warehouse options, enabling the relocation of goods from the Piacenza hub to Bergamo and thus closing the offices there.
Zoran Boras, Managing Director of Weilburger Coatings Italia, adds:
“The strategic locations of our production units and the well-developed warehouses at all sites provide a solid foundation for future growth. This setup allows us to maintain greater flexibility and higher storage capacities in the long term, with the opportunity for further expansion in the future. This move, set to be completed by March 2025, aims to keep day-to-day business unaffected, ensuring no impact on deliveries. Additionally, the proximity of the warehouses to production facilities offers seamless logistics and quicker response times.”
The expanded capabilities and enhanced service offerings underscore the company's dedication to being a full system supplier aligned with customers’ wishes and needs. Italy remains one of the strategic markets for the KANSAI HELIOS Group, and this acquisition further extends the offer and strengthens the approach as a system supplier. By joining forces with Weilburger Coatings, KANSAI HELIOS is now stronger than ever on the Italian market, providing a robust platform for innovation and growth.
The two companies are one of the major suppliers of integrated coating systems, including liquid, powder, cataphoresis technologies, gelcoats as well as adhesives and sealants. Together they run three production sites in Italy. For powder coatings one in Riese Pio X (Treviso), with a production of around 7500 tones of thermosetting powder coatings and one in Tezze sul Brenta (Vicenza) with a production of around 2500 tones of thermoplastic powders. The liquid coatings production is located in Sotto Il Monte, Bergamo, where around 2500 tons of coatings are produced. Both companies are members of KANSAI HELIOS, which is part of KANSAI PAINT, one of the world's leading manufacturers of paints, varnishes and coatings.
Interview with Matthias Haarer, Managing Director of Eisenmann GmbH – Böblingen, Germany
Alessia Venturi, Editor-in-Chief of the ipcm® magazines, interviewed Matthias Haarer, Managing Director of Eisenmann GmbH, whose name has always been associated with customised, efficient solutions and the highest quality in industrial coating technology.
Eisenmann is a rapidly growing company. Since the GmbH was founded in October 2020, the number of employees at its headquarters in Böblingen (Germany) has risen from 100 to 190. In addition, there are 40 employees in its branches in Puebla (Mexico) and South Carolina (USA).
At its headquarters in Böblingen, the company pools all its core competencies: research & development, engineering, project management, quality assurance, service, and sales. Eisenmann also operates a technical centre with 8,000 square meters for pre-assembly, logistics, spare parts storage, and research & development. Via business partners (licensees) in China, India, and Spain, and own subsidiaries in Turkey, Italy, USA, Mexico and Saudi-Arabia, the German company maintains reliable business relationships in these markets.
Eisenmann GmbH plans to achieve a total operating performance of over 100 Mio. Euro in 2024, counting on a broad product portfolio and customer base in different industrial field, from the automotive (historically, the company’s core business) and wheels industries to the agricultural and construction equipment, down to the general industry as far as coating of metals and plastics by using dipping, powder and wet application techniques is concerned.
Mr. Haarer, can you offer our readers a concise portrait of Eisenmann GmbH?
“The 2020 founded Eisenmann GmbH is focused on the successful further development of its business unit Paint & Assembly Systems with more than 1,000 patents which include all key products such as E-Shuttle 200 & 300, Vario-Shuttle XL, Vario-Loc, Vario-Mover (AGV), E-Cube and over 2,000 painting systems installed all over the world, of which around 90 are attributable to the alloy wheel sector, a field in which Eisenmann has been a pioneer”.
Modular, energy-efficient dry separation system E-Cube.
What does the brand Eisenmann represent today?
“The brand Eisenmann represents customised, efficient solutions, and the highest quality in industrial coating technology. We offer a worldwide proven and extensive portfolio of coating systems in the metal,
automotive, and wheels industries, including conveyor technology for final assembly.
Having over 2,000 painting systems installed worldwide means that more than 60 million car bodies have been equipped in the PT-ED area with Eisenmann patented technologies, like the conveyor systems for dip coating of the E-Shuttle series or the rotating dip system for higher payloads, VarioShuttle XL. With the new course of the company, we are able to support our customers worldwide with reliable service and spare parts management (24/7). The aim is to ensure that the systems retain their value for as long as possible, so that our customers can reliably achieve their individual production targets and the highest quality. Our expertise also includes the analysis of modernisation measures and the creation of innovative and sustainable retrofit concepts for existing systems”.
What does it mean to customise a paint shop?
“Customers requirements are extremely variable, even within the same industrial field. Each painting system is based on individual planning and
design, it is tailored to the customer’s requirements and is therefore unique. They vary in their complex interplay of process steps and the conveyor systems adapted to them. All our products and solutions are based on the experience we have gained from a wide range of projects in different industries around the world. And it is on this expertise that we will continue to focus on in the future”.
Company culture: how can you define that of Eisenmann?
“Transparency and corporate responsibility, appreciation and tolerance, commitment and genuine practice, boldness, openness to something new, resource-consciousness, and sustainability in focus: these are Eisenmann corporate values. Today, more than 230 employees work every day to ensure the success of our clients. Highly specialised designers combine their many years of engineering experience with fresh ideas from highly qualified young talents. As a result, our product range and services are continually evolving. Our operations have been characterised by agility and the ability to innovate, as well as reliability and ambitious collaboration within the team.
But living our values in our working environment also contributes to customer satisfaction and a good working atmosphere. We work constructively together, keep our promises, and meet our deadlines. This has resulted in a high level of loyalty among our employees and trusting relationships with our partners and suppliers. This is something we are proud of”.
Can you briefly outline Eisenmann product portfolio & services?
“Our technologies provide consistent quality standards throughout the whole process, from pre-treatment to final assembly. What sets us apart is our solution-oriented and customercentric approach, which is always geared towards changing market requirements. Our aim is to develop permanently relevant system concepts that can be optimally integrated into existing processes and open new potential in painting for our customers.
Our product portfolio includes:
Conveyor systems for pre-treatment and
cataphoretic dip coating (PT/E-Coat), for example VarioShuttle XL, E-Shuttle 200, and E-Shuttle 300;
Conveyor systems for the whole coating process, like the VarioMover (Automated Guided Vehicle), VarioLoc, Monorail systems, classic skid conveyor systems, Power & Free-Systems for different payloads (Inverted Power & Free, circular and spindle conveyor) for effective and individual usage in general industries / metal industries as well as the automotive industry;
Various drying systems (most compact and resource-saving: E-SmartOven);
E-Cube, RE-Cube /Dry separation system for collection and disposal of overspray;
Solutions and application technology for automated handling.
The new founded business unit Robotics adds to this wide range of technologies”.
What is the new business unit Robotics about?
“There are high expectations on product
quality and quantity, as well as on production processes and health aspects: precision, positioning accuracy, effectiveness, speed, and ergonomics are becoming increasingly important. A clever combination and safe co-operation between man and machine are indispensable and common practice today. That’s why we are working on reliable concepts for new systems and – also very important – ideas for retrofitting or converting existing paint shops.
Based on a standardised software architecture with uniform operating concepts, we enable the use of robots and application technologies from leading manufacturers.
Our expertise covers all process and applications technologies for:
Seam sealing from bottom;
Seam sealing from top;
Insulating spray;
Cavity preservation;
Material handling”.
What is Eisenmann focus when developing new technologies?
“Economic and ecological sustainability, as well as a focus on energy efficiency, are crucial drivers for all developments. Beside this, we want to offer flexibility, user-friendliness, and easy-integration of the different systems. This is why we have founded the new Robotics BU. Automotive paint shops are massive installations packed with painting technologies, and are energy- and resource-intensive.
Energy-wise, the painting stage is the most intense when it comes to the whole manufacturing process of a car body. Among the various technologies we have developed in this regard, it is worth mentioning the new dry separation system RE-Cube, which uses pyrolysis for a costand energy-effective dry separation of the overspray.
The changeover from wet separation to dry separation of the overspray was already pushed by energy issues. Now that dry separation is well proven and widely used,
we developed the new RE-Cube system from the expertise gained with the two generation of our proprietary E-Cube technology. RE-Cube stands for REcycling Cube and that is the key point. It is a cube with a shell of sheet metal and only the filter parts inside the cube are made of card box. The idea behind is to pyrolyze the card board cube in a pyrolysis oven at 450 °C, using the heat generated by this process for other areas of the paint shop, for example to heat up the ovens or the PT tanks. This is a CO2 neutral process, since you eliminate the need for logistics and transportation and you balance the CO2 emitted during the pyrolysis with the CO2 saved for heating up other stages of the painting process. It is circular economy at its best!”
You mentioned ATLAS, Eisenmann sustainability concept to improve the energy and resource balance. Can you explain this approach in details?
“A paint shop is very resource-intensive. We are
aware of our responsibilities and try to design our products in a way that reduces harmful emissions and conserves resources such as electricity and water. All key ideas and technical approaches that can improve the energy and resource balance are based on the firmly anchored sustainability concept ATLAS that is observed by our employees. ATLAS stands for Advanced Technology for Lowemission Application and Sustainability. We do not want to just place a slogan for sustainability, we really want to live this programme in terms of product categories. An easy example of this is the drying technology in an automotive paint shop. We have developed very efficient smart ovens, able to adapt the drying process to the type of car body entering the oven. We call these ovens “smart” because, in combination with our smart conveyor technologies, like the VarioLoc or the Vario Mover (our own AGV system), they do have the intelligence to direct the warm air individually and precisely to the respective components of the car body by means
of an optimised control of the swivel nozzles. There are many other examples of technologies developed by Eisenmann that comply with the ATLAS approach. In the PT/ED area with the patented Vario-Shuttle XL, a rotating conveyor system for dip coating, even heavy bodies of up to 2,000 kg can be coated with consistently high flexibility, manoeuvrability and efficiency. This meets a new common demand from our customers, which are manufacturing car bodies becoming bigger and bigger every day, in line with the SUV and E-Mobility trend. It is funny, but electrical car bodies are sometimes heavier than those of traditional cars!
To sum up, ATLAS is not just theory put on a web-page: it is a concept, we live it and our products realise it”.
As last question, can you set out briefly what the prospects of the company are?
“Eisenmann is currently planning a new building and will move to its own premises in the neighbouring town of Gärtringen in 2026. This step emphasises the stable growth of Eisenmann GmbH.
A new building offers us the greatest possible flexibility in terms of modern and energy-efficient construction. We go back to the ATLAS
concept: the careful use of valuable natural resources not only determines our actions in the development of our technologies. It is also important to us to consistently realise these goals when designing a modern working environment that optimally meets our needs and also provides an adequate presentation framework for our customers’ investment projects.
We are building a new pre-assembly hall of about 7,000 sqm that will accommodate logistics, testing devices and equipment, the R&D area, and the pre -assembly of our own proprietary products. Besides the pre-assembly hall, a new headquarter building of around 3,500 sqm will accommodate from 250 up to 300 employees.
As I said, this step emphasises somehow the positive development of our new company; sometimes, we need to remind ourselves that it is not just four years that we are back in the business, we did not start from scratch: with a new headquarters we combine the heritage and the future. The investment for the new building will amount to 20 –30 million Euro. The new location in Gärtringen also offers scope for future expansion. We would like to continue to develop as an attractive employer in the region and to create additional jobs”.
via E De Nicola, 18 - I-20090 Cesano Boscone (MI) Italy - tel +39 0255210608 www.ravarinicastoldi.it - dive@ravarinicastoldi.it
Kevin Biller kbiller@chemquest.com
Dear Joe,
What makes one powder fluidize better than another?
Jason Smith Denver, Pennsylvania
Hi Jason,
This is an excellent question. For a powder coating to perform well, many physical and chemical properties must be aligned. Fluidization performance is one of the critical physical properties necessary to successfully apply a powder coating. Fluidization involves incorporating a volume of air into a quantity of powder to prepare it to be transported from the feed hopper to the application gun. This mixture of air and particles not only helps transport the material but also enhances the delivery of electrostatic charge to the individual particles as they exit the spray gun. Particle size distribution (PSD) is the primary factor that influences fluidization. Powder coatings are comprised of a range of different-sized particles, from about 1.0 micron upwards to around 100 microns. The best fluidization occurs within the heart of this range, typically 20-60 microns. Fines (< 10 microns) tend to agglomerate and impair fluidization. Coarse particles (> 100 microns) are difficult to fluidize because of their relatively high mass. Hence, the best fluidizing powder coatings possess tight particle size distributions. This means a minimal level of fines and also a minimum of coarse particles. If you employ a reclaim system to capture and recycle oversprayed powder, this can be a factor in fluidization. The best-suited particles are preferentially deposited on the parts you coat. And as you can surmise, the fines and coarse particles populate the overspray. Reintroducing
overspray into your virgin powder feed will affect fluidization. This increase in fines and coarse particles may require adjustments to your fluidization process. How do you avoid this problem? The best strategy is to use high-quality powder coating from a reputable powder manufacturer. The most reliable suppliers have well-controlled grinding processes that yield relatively narrow PSDs. Narrow PSDs deliver high first-pass transfer efficiency and hence less overspray to contend with.
A secondary factor that contributes to poor fluidization is moisture.
“Wet” powder is very difficult to fluidize and transport through a powder application system. High levels of moisture are usually due to poor storage and handling of powder coating inventory. Powder should be stored in an air-conditioned environment and open bags/containers should be avoided. In addition, you should be careful to avoid introducing “cool” powder into a warmer, moister environment. The cool powder will act as a desiccant and absorb the ambient moisture. It is wise, as you move powder from storage to the application area, to allow it to acclimate to the ambient application environment before opening the package.
Thank you for the question. Best regards, Joe
We currently are planning on using cold-rolled 304 stainless square tubing for our instrument housings, and the tubing comes slightly oxidized and slightly pitted. We are looking to provide the customer a finish for the housing that looks professional and prevents it from going back to the way we received it.
We were looking at possibly painting, powder coating, polishing, or plating the housing, but I am leaning towards powder coating as a cost-effective means to protect the housing. The environment the instrument will be in ranges from -40°C to +100°C and is occasionally dusty, oily, and near sea water (not touching or emerged). Given that the tubing is 304SST, I know adhesion is the big problem. Can you recommend the proper way to prepare the surface of a 304SST material? Details on the type of degreaser to the type of grit (non-ferrous) or chemical (i.e., silane), to the primer type so that UV and sea salt corrosion will not affect the housing for up to 10 years would be greatly appreciated.
I look forward to your reply, Christopher Filoon, Pennsylvania
Hi Christopher,
This is an excellent question, and it is very wise to explore all your options before committing to a new process. Powder coatings are a very good finish for stainless steel if the process is designed and maintained properly. The key is in the cleaning and metal pretreatment process that precedes application of the powder. The process you should consider for powder coating starts with media blasting. A high-quality medium such as aluminum oxide will suffice. Follow the blasting with a wellcontrolled alkaline degreasing step to remove any residual oils, process fluids, and handling contaminants. It is also important to keep your blast media clean. Next, I suggest a passivation step to remove any iron-based residues on the stainless surface, as well as the possible presence of residual sulfides. Trace amounts of either contaminant can act as sites for subsequent corrosion. Passivation of stainless steel typically involves immersing the part in a nitric acid bath, although nitric acid/ sodium dichromate or citric acid solutions can also be used. The concentration of acid can range from 20-50% by volume. ASTM A380 describes standard practices for passivating stainless steel. After thoroughly drying the parts, it is wise to powder coat the passivated surface as soon as possible. Chemically pretreated surfaces have a finite shelf life before they begin to degrade. Using a highquality powder coating precludes the need for a primer coating. Meeting the durability required in the environments you describe requires the powder coating to be applied at a reasonable thickness as specified by the powder coating supplier; 6580 microns are usually sufficient for an outdoor application. It is also critical to ensure that the coated parts see enough temperature and time to complete the cure to the powder coating chemistry. When a powder supplier quotes a recommended bake, they are referring to the time at or above the stated temperature that the part has reached. It is therefore important to factor in the heat-up time needed to reach the bake temperature. As for ensuring acceptable coating performance in the field, I can recommend a couple of practical tests. I suggest that you prepare a few test pieces that have been
run through the entire cleaning/passivation/coating/ curing process and perform the following tests: Simple “X” crosscut dry adhesion. Cut a 40 mm by 40 mm “X” into the coating with a sharp blade. Apply a strong tape such as 3M 2517 or Permacel #99 and pull sharply. The coating should exhibit no loss of adhesion. A similar test can be done with a “crosshatch” as described in ASTM D3359. This entails a perpendicular series of cuts that create a grid. Nevertheless, the simple “X” crosscut test is usually sufficient to determine if adhesion is acceptable.
Hot water immersion adhesion. Place the coated samples evaluated in the adhesion test described above into a 75°C water bath for 24 hrs. Remove and allow them to dry, then recheck tape adhesion. The coating should show little or no loss of adhesion. I would confirm these test results with a 500-hrs Salt Fog test (ASTM B-117). Place the scribed test parts in the corrosion chamber and evaluate every 250 hrs. Most powder coatings pass 1,000-hrs Salt Fog resistance, and 500 hrs is what I consider a minimum benchmark.
Good luck with identifying a finishing technology that provides the necessary cost/performance balance. Best regards, Joe
Ilaria Paolomelo ipcm®
Pulsar, a Polish company specialising in the production of safety devices and accessories for alarm systems, was experiencing some problems with its products’ coating quality. To solve these issues, it decided to switch from a manual to an automatic application system by relying on Lesta. The coating robot supplied by this Italian company enabled Pulsar to obtain uniform finishes, improve process repeatability, and minimise manual touch-ups. This change significantly boosted its productivity, allowing it to handle a daily production of up to 2,000 product sets, with a 400% increase in capacity.
In the modern industrial context, coating is a crucial phase that affects not only the aesthetics of products but also their degree of protection and durability over time. Often, when companies need to install a new coating system, they are faced with a fundamental choice between two application methods: manual and automatic. Each brings specific advantages and challenges that can significantly affect the efficiency and overall quality of the end products.
Manual coating offers a high degree of control and adaptability but strongly depends on the operator’s skills and experience. This process makes it possible to work on complex details and flexibly handle unpredictable variables, such as uneven surfaces or changing environmental conditions. However, it may present limitations regarding uniformity and repeatability of results, increasing the risk of defects and variability in the quality of finishes.
On the other hand, automatic coating systems are designed to operate efficiently, ensure greater accuracy and repeatability of results, reduce processing times, and minimise human error. They are particularly advantageous in large-scale production environments, where consistent
results and speed are essential to maintain competitiveness and meet quality requirements.
Pulsar faced this decision, too. Until 2017, it operated with a manual coating plant equipped with two booths, but despite the efficiency of the plant, the results’ quality was not up to expectations: problems with finishing uniformity and quality were compromising the company’s operational efficiency and ability to meet the high standards demanded by its customers.
To solve these critical issues, Pulsar chose to automate the coating application phase by relying on Lesta (Dairago, Milan, Italy) for the supply of a new, six-axis articulated coating robot. Installed within a single coating booth, this works in synergy with the reciprocators: the robot applies paint on the difficult-to-reach surfaces of parts, such as hollow spots, whereas the two reciprocators, each equipped with three guns, coat the flatter surfaces. This innovation has enabled the Polish company to overcome the limitations of the manual process, achieving higher levels of quality and more consistent finishes.
Pulsar: innovation and quality in the production of safety and video surveillance accessories
Since 1994, Pulsar (Łapczyca, Poland) has established itself as a leading
manufacturer of accessories for alarm, access control, and video surveillance systems. Pulsar’s product range is broad and diverse and includes enclosures, power supplies, PoE devices, fire protection systems, transformers, and accumulators. The company has quickly extended its presence to European and Asian markets, consolidating its position through a constant commitment to excellence. “Thanks to a strategy focused on quality and innovation, we have been able to expand into new markets and maintain a leading position,” states Pulsar’s CEO, Krzysztof Tatara.
Today, with over 200 employees and a production site of 8,000 m², Pulsar stands out as a modern and dynamic company, capable of responding flexibly to the global market’s needs. Its success is the result of a carefully curated production cycle in which every stage is designed to ensure high quality standards. “Pulsar uses only the highest quality materials and subjects each product to rigorous controls during all manufacturing stages, from sheet metal processing to coating and from the electrical components’ production and installation to final assembly,” adds Tatara. “In particular, coating is one of the most important steps in our workflow, as it provides each metal part with essential protection. For Pulsar, the finishing cycle plays first of all a functional role and only secondarily an aesthetic one.”
The coating cycle and the booth’s special feature
The coating process is designed to ensure the highest quality and durability of the finished parts while maintaining high production efficiency. “The components are manually loaded by the operator onto the monorail conveyor and taken to the pre-treatment tunnel, where they undergo a degreasing phase, necessary to remove oils and surface residues from the previous processing stages, combined with passivation with iron salts to form a protective layer; a rinse with mains water and further rinse with demineralised water. That is sufficient for Pulsar products intended for indoor use, such as home security systems, which do not require advanced corrosion protection,” notes Łukasz Szczepanik, Sales Manager at Indufinish, the plant engineering company that supplied the coating system.
“The special feature of the pre-treatment tunnel lies in the tanks made of polypropylene, which provides numerous advantages over steel. It is characterised by its high resistance to corrosion, a decisive factor in industrial environments where moisture and chemicals can easily deteriorate steel. Finally, the improved thermal insulation offered by the polypropylene contributes to the greater energy efficiency of the system by maintaining stable temperatures and reducing heat loss,” adds Szczepanik.
After pre-treatment, the operator unloads the workpieces, which then undergo a masking process necessary to prevent certain parts from losing conductivity. They are then placed on special trolleys and transported to the new coating area. “Our products’ hanging precision is crucial as even a shift of a few millimetres can affect their final finishing quality. Therefore, the operator uses laser trackers to position the components correctly on the hooks,” indicates Szczepanik.
The system, equipped with a laser barrier for automatic part contour detection, optimises all the paint application operations. The components are transported into the coating booth at a speed of 1 metre per minute, where the coating process is divided into two stages.
At first, the six-axis articulated robot supplied by Lesta applies the coating in hollow, difficult-to-reach areas using its advanced technology to paint concave surfaces. Subsequently, six reciprocator-mounted guns supplied by PUT Wagner-Service Polska apply the powder on the outer surfaces of the components, which are mostly flat.
“This plant’s key peculiarity,” illustrates Indufinish’s Sales Manager, “is that the robot and the reciprocators coexist in one booth. Unlike other systems where the robot only performs a pre-finishing function, here it is an integral part of the application phase.” Manual post-finishing is performed if necessary, but thanks to advanced robot programming,
this is now rarely required. “The coating booth is designed to enable rapid colour changes thanks to the use of a cyclone that facilitates the reuse of residual powders. At Pulsar, we have an average of five colour changes per week as 80% of production is painted white and the remaining 20% black, grey, and red,” says Tatara.
At the end of the application phase, the parts enter the curing oven for about 20 minutes, and after cooling down, the operator unloads them from the hooks, removes any masking device, performs quality controls, and prepares the products for shipment. Despite the compact size of its coating plant, Pulsar can now process up to 2,000 sets of products, each consisting of two elements, in a 16-hour working day. In some circumstances, the plant can handle up to 5,000 smaller sets.
Reasons behind this choice
Pulsar recently undertook a major renovation of its coating plant. Although the system had been installed in 2017, some challenges related to finishing quality had emerged over time. “The manual system we had in place, although initially effective, was beginning to show some limitations,” explains Pulsar’s CEO. “Differences among our operators caused undesirable variations in the quality of the final products, especially in different shifts. We could not allow this to affect our reputation. That is why we decided to make a technological leap: on the advice of Indufinish, which
we had already approached to install the coating system, we decided to invest in a robot not only to improve our coating results but also to increase our production capacity. Indeed, thanks to the installed technology, this has increased by more than 400%.”
“After a visit to Pulsar’s plant to analyse the reported problems, it soon became clear that a significant part of the manual operations could be optimised with a coating robot. I pointed out an automated system could replace many of the manual tasks, improving the efficiency and quality of the coating process,” says the Sales Manager of Indufinish. “We then organised a meeting with Igor Kania, Lesta’s sales representative for the Polish market, and it was immediately apparent that a robot could solve the problems encountered.”
Although initially not planned, the robot’s implementation became
the key to solving several quality issues and making the process smoother and less dependent on manual labour. Indeed, it has optimised production and even improved the working conditions within the company. “Reducing our employees’ exposure to dust was a priority,” emphasises Tatara. “Now, our operators mainly deal with robot programming rather than coating, which makes their work less burdensome.”
Pulsar’s CEO also expresses great satisfaction with Lesta’s advanced technology and Indufinish’s continued support: “We can only be pleased about our collaboration with Lesta and Indufinish. The technology provided by Lesta lived up to our expectations, and Indufinish’s constant support was instrumental in addressing and solving every challenge that arose along the way. We are very satisfied with the results achieved. We are confident that this partnership with Lesta and Indufinish will enable us to continue to grow and meet our customers’ needs.”
Federica Alberti
SG Projects – Voghera (Italy) federica.alberti@sgprojects.it
SG Projects is the partner company of Solecta that deals with the distribution of their painting and products in Italy, guaranteeing continuous customer support and representing a rapid intermediary ready to solve any problem that may be detected on the ultrafiltration lines. The following is an overview of the advantages offered by ultrafiltration membranes for the electrophoretic process and a quick guide to perform effective maintenance operations.
The core part of the industrial painting process is the cataphoretic bath, where a layer will be deposited by electrodeposition on the items to be painted. At the end of this step, coated items will be rinsed with ultrafiltrate (the liquid part of the paint bath, purified of pigments, with a similar process of RO but with different cut-off). Ultrafiltration is a pressure-driven membrane process capable of separating solution components on the basis of molecular size and shape. Under an applied pressure difference across an ultrafiltration membrane, solvent and small solute species pass through the membrane and are collected as permeate, while larger solute species are retained by the membrane and recovered as a concentrated Retentate.
In electrocoat paint systems, the ultrafiltration permeate contains water and paint solubilizer. The Permeate is used in the paint line rinse section. This recycling method provides a closed loop rinse system for recovering paint solids (drag-out). The Permeate can also be diverted to drain, in order to reduce conductivity of the paint. The degree of paint recovery depends on the quantity of rinsing water which is supplied to the electro-dip coat painting bath. This quantity corresponds to the quantity of filtrate. The filtrate capacity referred to the membrane cartridge surface area at a certain paint recirculation
capacity is the ‘specific filtrate capacity’. It depends on the type of paint used and must be determined from case to case by way of measurement. The specific filtrate capacity is also influenced by the paint recirculation system, i.e.:
Pressure
Temperature
Solids concentration
Cross flow
Carry-over from pre-treatment.
It is necessary to adapt the replenishing material to the use of ultrafiltration.
To be more specific, in the paint process it is necessary to rinse the surface of the plated parts with water first, and then rinse with pure water. Wastewater contains mainly harmful chemicals such as epoxy resin, paint, vegetable oil, carboxylic acid, butanol and pigments. When the painted part is taken out from the electrocoating tank, it needs water to wash off the residual liquid paint on the surface, thus producing electrophoretic paint wastewater.
The electrical coating in the wastewater represents 30% of the paint used. Adopting an ultrafiltration membrane device will form a closed circulation route, allowing to re-use both the paint and the water.
The advantages of ultrafiltration systems
Ultrafiltration may provide advantages in terms of paint recovery, the control of the chemical parameter of the coating and the balancing of the conductivity in the tank. As the electrophoresis process goes on, the content of the water, the cosolvent and the inorganic ions in the electrophoresis solution in the metal tank increases, affecting the quality of the painting process. The ultrafiltration technology can retain polymer coatings and pigments, remove excess water and other impurities in the electrophoresis solution, extend the use-time of the coating solution and improve the quality of the paint.
The ultrafiltration membrane technology offers then the following advantages for the treatment of the wastewater deriving from the electrophoretic painting process:
It has good retention effect, providing a clean and transparent filtrate after the treatment;
The automatic system control is simple and easy to use, guaranteeing safety during operations;
The space-saving equipment has a rigorous structure and a lowenergy consumption;
The large water output is suitable for the recovery of cathode and anode electrophoretic paint;
It possesses a good anti-pollution ability and long-term operations will not affect the water production.
As a matter of fact, the ultrafiltration membrane technology has played a major role for the electrophoretic painting process of car bodies, luggage accessories, electrical appliances and several metal components
for multiple other industrial sectors. The recovery rate has significantly increased and the processing cost has been reduced by 30%.
maintenance of the ultrafiltration membranes
After several operational hours, the e-coat process may be subject to a flux rate decrease. Therefore, a recovery procedure might be required. Several factors from the normal operations of the electrophoretic plant can affect the permeate output deriving from the ultrafiltration membranes, such as the type of paint employed, the percentage of solids, the operational temperature, the conductivity and pH of the tanks, the paint flow and the inlet pressure to the membranes, as well as the drop and drag-in contamination from the pre-treatment tunnel, just to mention a few.
After the start-up, the ultrafiltration flux rate will decline to a steadystate flow within some days: this steady-state flow will be considered the baseline for your system. However, when the system declines to ~70% of the steady-state flow, it is time to clean it. A delay in cleaning can lead to irreversible fouling. Care should be taken to maintain the recommended flow rate for your particular system. On paint, it is recommended to maintain a pressure differential of 2,0 - 2,3 bar, with a minimum outlet pressure of 0,7 bar.
Because the number of variables affecting the proper performance of the ultrafiltration system, it is important that a detailed log is kept and maintained on a regular basis. This will ensure that potential problems could be avoided and the cause of the flux decline be determined more accurately and eliminated as a potential or recurring problem.
Here are the most common problems and the related solutions:
When an unplanned shutdown occurs, the paint must not stand idle in the ultrafiltration system: if it is allowed to stand idle for too long, the membranes may become fouled beyond recovery. So, during shutdowns, it is necessary to immediately drain and flush the system with fresh D.I. or R.O. water (permeate if available) and a chemical cleaning procedure shall be started before the system shutdown.
Moreover, when resin, pigment, solvents or solubilizers are added to the paint, they should be added slowly and according to the recommendations of the provider. Furthermore, the additions should not be made near the intake of the ultrafiltration pump.
Paints always contain some minor percentage of destabilized paint particles, which will cause sediment or agglomerate formation in system areas of zero flow. Because some 10 g of agglomerates can ruin an 8” Element, all necessary pre-filtration procedures must be carried out to avoid sediments and/or agglomerates from reaching the ultrafiltration modules.
One of the main reasons of unsatisfactory performance and flux decline is related to paint fouling. Paint fouling occurs when the stability or solubility of the paint allows agglomeration of the paint particles and the membrane surface becomes obstructed with these ‘gummy’ agglomerates. So, the permeate passes through the membrane with more difficulties.
A healthy paint consists of dispersed paint particles that carry optimum electrical charges to repel each particle from others, inhibiting the formation of agglomerates. The unstable paint may lose these electrical charges because one or more of the following conditions:
Inadequate solubilizer levels causing the paint pH to move out of range;
Contaminants (such as iron) reacting with the solubilizer or paint;
Bacteria consuming the solubilizer or otherwise disturbing the paint solubility;
Flow rates too low to sweep away the fouling layer at the surface of the membrane;
Severely low flow rates resulting in settling, loss of electrical charge and agglomeration;
Improperly introduced replenishment feed material;
Introduction of occluded air into the paint, through vortexing at the pump, etc…
Dosing and nebulization system for the conversion coating of metal and aluminium parts
Drizzling consists of a dosing panel for automatically managing the demineralized water coming from a feed tank and the amount of passivating chemical product, in order to apply an optimally concentrated solution on the material to be treated. The use of special atomizing nozzles and compressed air enables it to produce and evenly distribute a light mist of chrome-free solution.
Electric circuit fully insulated from liquids for greater safety The solution that is sprayed is always fresh and dosed in-line
Suitable to treat different types of metal components
Andreas Michalske
VENJAKOB Maschinenbau GmbH & Co.KG - Rheda-Wiedenbrück, Germany andreas.michalske@venjakob.de
Modern fittings combine form, function and design. The challenge for manufacturers is to meet individual color and design preferences while at the same time ensuring durability and abrasion resistance. Sooner or later, the finish may suffer damage in certain areas, especially under heavy duty use. Together with three technology partners, Venjakob -specialized in customized finishing lines, provides a solution that offers far-reaching economic and ecological benefits.
Wherever there is a demand for chrome-plated fittings with a stylish surface design in a colored, metallic, smooth or glossy look, coating plays an important role. Depending on the material to be coated, the process can be very complex and resourceintensive.
Fittings, for example in bathrooms and kitchens, which are subject to heavy use, must be robust and corrosion-resistant.
“Metallization alone is not enough to achieve long-lasting adhesion of the coating to the material surface,” says Andreas Michalske, sales engineer at Venjakob.
Innovative and resistant surface finishes for metal and plastic components without the use of heavy metals using the HIGH END COATING (HEC) process. The environmentally friendly coating process offers improved technical properties, passes the stringent requirements of the relevant industry tests and offers attractive looks with an almost unlimited choice of colors and gloss levels.
Venjakob presented the patented coating process at this year’s Paint Expo in Karlsruhe/Germany, the world’s leading trade fair for coating technology.
Up to 70 percent savings - without any loss of quality
For the fittings industry, the high-end coating process (HEC) could be the solution to many challenges. This involves a special pre-treatment in a high-vacuum system. The surfaces of metal and plastic parts are given an antistatic functional layer with increased surface tension. This simplifies the subsequent coating process. Pre-cleaning the surface with ionized air is completely sufficient. “In the subsequent coating process, we can manage with layer thicknesses of between 12 and 25 µm. Paint consumption is reduced by up to 70 percent. The components treated in this way have a high-quality appearance and pass all the necessary tests,” explains Michalske. It is important to know that the fittings industry places higher demands on components than the automotive industry, for example. There is a so-called boiling test, in which the components are placed in a boiling medium to test how long they remain intact or do not release any harmful substances. Components in the automotive industry only need to “boil” for one hour. In the German fittings industry, 100 hours are required.
The high-end coating process is completed in just a few steps. The components are pre-treated in a special HEC high-vacuum process and a specially generated vacuum plasma. They are then removed and fed to the coating system for coating. The high-vacuum pre-treatment replaces passivation and phosphating, thus reducing the number of pretreatment steps. There is no edge alignment or edge build-up during the subsequent coating process. The high-end coating process offers many other advantages and can also be integrated into existing series processes.
About Venjakob
Venjakob, founded 1963 and family owned in third-generation, is one of the world’s leading manufacturers for finishing lines. The company develops individual solutions for the entire production line, including pretreatment, coating, drying and automation technology, as well as exhaust air purification plants. All from a single source and individually tailored to the needs of users from a wide range of industries. Venjakob is headquartered in Rheda-Wiedenbrück, Germany, and employs 380 people worldwide. Further production facilities: Venjakob Umwelttechnik GmbH & Co. KG in Sarstedt, Germany and Nutro Inc. in Strongsville, Ohio, USA.
• industrially inspected, tested and proven
• compliance with standards of the fittings, hardware and automotive industries
• one-coat system, without adhesion promoter or additional primer
• can be integrated into existing series processes
• no clean room conditions necessary
• paint material savings of up to 70%
• no disposal costs
• replaces passivation and phosphating
• no additional chemicals or water required
• environmentally friendly, free from chrome and heavy metals
OF THE MONTH
Low Bake Powder Coatings from KABE-Farben: Quality for Architectural Applications
The Collaboration Between DHK, ALIT Technologies and Alufinish Ushers in a New Era in Metal Surface Protection
FOCUS ON TECHNOLOGY
Metallic and Special-Effect Powder Coatings for Emboss’ Three-Dimensional Cladding Surfaces
TO 2050
EcoAl® by Alsan - Chrome-Free Passivation in Pretreatment Processes for Powder Painting
Ultrathin, Hard and Sustainable Non-stick Coating Revolutionizes Shaping Processes In Injection Moulding and Die Casting
ON TECHNOLOGY
Azeta Confirms Itself as a Pioneer in Aluminium Coating Through a New Vertical Line Combined with an Innovative IPS Powder Feeding System
HIGHLIGHT OF THE MONTH ST Powder Coatings Presents the New Green Oasis Range, the Ecological Oasis of the Future
Evolution on Design: Kenosistec’s PVD Technology for Elegant, Durable, and Sustainable Finishes
ON TECHNOLOGY
Luxe Perfil: The Experts in the Impossible Rely on the NewPrimeCoat® A109 Pre-Treatment Product’s High Performance
FOCUS ON TECHNOLOGY
Raising the Bar of Quality: Sirio Galv’s New Liquid Coating Plant for High-End Furniture and Lighting Accessories
EcodePure: the Road to Water Recycling and Zero Discharge
ItalMesh Clads the New Burger King in Rovereto with Perforated and Painted Aluminium Panels
RIPOL in Bayreuth: Innovation and Avant-Garde Design
AkzoNobel strengthens carbon reduction commitment with superdurable range of low-energy powder coatings.
Architectural customers can now take advantage of a superdurable low-bake powder coating developed by AkzoNobel, which helps to protect building surfaces in more challenging environments.
Having launched a standard durability option in 2023, the newly introduced Interpon D2525 Low-E range has been specifically designed to withstand conditions in more extreme and challenging locations. Backed by an Environmental Product Declaration (EPD), it can also improve longevity in standard environments.
Using industry-first technology introduced by the company in the standard durability option last year, the new range can be cured at temperatures as low as 150 °C – while still delivering the supreme levels of quality and performance demanded by customers in the buildings and construction sector.
“This latest innovation reflects our commitment to listening to customers and providing them with a range that combines several benefits – such as longer durability and lower cure – but without compromising on aesthetics,” says Bob Dirks, Global Segment Manager for Architecture at AkzoNobel’s Powder Coatings business. “It also supports the need for a collective responsibility towards a more sustainable future and highlights our commitment to sustainability throughout the value chain.” Interpon D2525 Low-E can either be cured at a lower temperature
(150 °C compared with a standard curing temperature between 180 °C and 200 °C) – cutting energy consumption by as much as 20% – or it can be cured up to 25% faster than conventional powders, allowing for more products to be coated in less time and improving the efficiency of the coating line. As well as supporting customers in reducing their carbon emissions, it will help AkzoNobel achieve its own ambition of reducing carbon emissions across the value chain by 50% by 2030.
It’s ideally suited to any architectural or industrial metal surface, both exterior and interior, such as facades, windows, pergolas, fencing, railings, metal office equipment and doors. Key features include excellent levels of durability to protect colour integrity and performance. Interpon customers can also receive help with calculating the benefits of using its Low-E products, with regards to energy and carbon savings or productivity increases.
The company’s architectural powder coatings feature on some of the world’s most famous buildings, including The Shard and Westminster Abbey in London, UK; the Bird’s Nest stadium in Beijing, China; and La Sagrada Familia in Barcelona, Spain.
For further information: www.interpon.com/gl/en/products/ architectural/interpon-d-low-e
The GSB International Association will participate in the upcoming edition of ALUMINIUM (Düsseldorf, October 8-10, 2024) at booth 3F70-03.
Quality assurance of coatings is of great importance to the aluminium industry. Regardless of the product, the surface is always what catches the eye. Of course, special attention is paid to quality assurance whenever a surface is particularly exposed to outdoor influences and is intended to maintain an impressive appearance for a long time. This is precisely the case when it comes to facades. The buildings are typically constructed to be used for many decades. Depending on the location, they are exposed to various environmental influences. On the shorelines, the salt water of the sea can increase the corrosiveness of the environment. Regions with many hours of sunshine per year have high levels of UV intensity. But not only the environment has an effect, the usage of the building also plays a role. Swimming pools, for example, are cleaned with aggressive cleaning agents. At this point, it is clear that the list of possible stress factors can be continued endlessly.
With its quality assurance system for the coating of aluminium in the architectural sector, GSB International - the leading quality association for surface coatings in the fields of aluminium and steel - takes these external influences into account and thus ensures a stress-free work experience for architects, building owners and planners.
Everyone who is interested in GSB’s extensive quality assurance or has detailed questions about coating is very welcome to visit the experts from GSB at the ALUMINIUM 2024 in Düsseldorf. At booth 3F70-03, the GSB team is looking forward to great conversations about coating. And that’s not all. At the booth, a coating plant will be on site to allow all visitors the opportunity to experience the powder coating process.
For further information: https://gsb-international.de/en/
PRATIC has chosen to rely on IMEL’s expertise to install a new state-of-the-art coating system that ensures high-quality performance for the powder coatings on aluminium pergolas and awnings.
PRATIC S.p.A., part of the STELLAGROUP, a global leader in the production of pergolas and awnings with refined design and architecture, has implemented an advanced powder coating system at its manufacturing facility in Fagagna (Udine), realized by IMEL S.p.A. The coating system has been designed to ensure high performance in terms of durability, offering remarkable versatility in pre-treatment and coating cycles, with a high degree of automation. The system is optimized for energy efficiency and integrates a sophisticated depuration plant that allows for the recovery of wastewater.
The line is distinguished by the use of high-quality equipment, a compact design that optimizes space, and attention to detail—hallmarks of PRATIC’s projects. The system includes a pre-treatment tunnel with separate chambers, made entirely of AISI 316 stainless steel, which allows localized treatment and minimizes contamination of the baths, making it suitable for the use of any chemical agent.
The drying and curing ovens, positioned next to each other, are properly insulated and equipped with doors that ensure optimal thermal maintenance, helping to reduce fuel consumption. The coating plant is also equipped with two Gema Magic Cylinder booths, each equipped with 14 guns powered by a spray system that uses dense phase pumps and a fast colour change system.
A key element of the system is its eco-friendliness: 97% of the wastewater is recovered thanks to a complex depuration system based on mechanical vapor recompression. This innovative process allows for the reuse of
water in the pre-treatment stages, maintaining the baths in optimal condition and reducing water consumption, with nearly zero discharge into the sewer network.
Thanks to its high level of automation and the integration of certain modules from the i4paintshop® platform, the system is able to automatically managing various coating cycles based on the parts’ codes and assigned priorities. The system ensures automatic data flow management, complete process traceability, constant monitoring of energy consumption, and efficient maintenance scheduling. Additionally, with the digital reading of data from each component of the system, it is possible to optimally manage quality and reduce waste, in compliance with Qualicoat standards.
The high coating performance and rigorous process control have enabled PRATIC to obtain the prestigious QUALICOAT SEASIDE certification, which attests the compliance with the most stringent international standards for aluminium treatment and coating quality. This certification ensures maximum paint adhesion and excellent resistance to corrosion caused by atmospheric agents.
Through this collaboration, IMEL has met a new challenge in highend industrial coating treatments, demonstrating its competence and innovative capabilities.
For further information: www.imelspa.com
New TIXO Clear and TIXO Filler. Superior quality for carbon fiber surfaces.
The Tixo line redefines the finishing of carbon surfaces, both glossy and matte. Specifically designed for this material, TIXO products offer extraordinary thixotropy and fullness, allowing for the application of considerable thicknesses with excellent levelling and impeccable aesthetic appearance. Thanks to their high resistance, these UHS paints reduce the number of coats required, ensuring faster and more efficient processing. The exceptional gloss and scratch resistance of TIXO paints elevate quality standards to a superior level.
Discover all Vernici Caldart products designed for Automotive on our website.
The 2024-2025 colour trends have been presented by Axalta in its latest Vibes Colour Journal: nature and technological aspirations come together under the name of Architectural Fusion.
Axalta Coatings has launched the latest edition of Vibes, the magazine through which the company annually offers architects and designers a guide to the latest trends, exploring colour and texture in the built environment. The latest trends have been gathered under the theme ‘Architectural Fusion,’ blending the essence of nature with technological aspirations and emotional depth. Axalta’s new colour trends capture the connection to nature while embracing a technology-driven future, helping architects and designers in their creative endeavours.
This duality inspires creativity and evokes a blend of calm and new beginnings.
In addition, Vibes magazine’s case studies also show that building materials coated with Axalta products are as varied and diverse as modern, global societies. Axalta’s technology portfolio addresses the nature of these diverse materials, such as metal substrates, combining them with an exhilarating colour experience.
“As we present the latest edition of Vibes, we are thrilled to showcase the vibrant intersection of colour, creativity, and innovation, in architectural design. Our curated themes - Earth Unity, Human Evoke, Tech Vision, and Vivid Vibe - reflect a harmonious blend of nature, technology, and human connection, offering designers an inspiring palette of colours and finishes. Each page of Vibes is a testament to Axalta’s commitment to pushing the boundaries of design, fostering a deeper connection with our environment, and embracing the endless possibilities of the future,” has stated Sally Put, Editor of Vibes colour journal and Head of Marketing Communications at Axalta EMEA.
Vibes 2024 presents the following colour trend themes:
Earth Unity: Humanity’s connection with nature and the universe. Shades such as amethyst crystal, ochre, stone and clay are reminiscent of forests and wild berries.
Human Evoke: Emphasising emotional connections. Lighter tones are reminiscent of shell patterns, with hints of stone, precious metals and emotive red.
Tech Vision: Ambitious and curious, technology enthusiast. Colours include straw yellow, pink, green, blue and purple, reflecting innovation and scientific exploration.
Vivid Vibe: A palette that celebrates hopeful creativity. It acknowledges the world as it is while striving for a brighter future. Imagine colours that evoke memories, stimulate the imagination and inspire creativity in design.
For further information: www.axalta.com/vibes
The QUALICOAT certificate ensures that products from WEG Mexico meet the highest quality standards.
The Mexican subsidiary of the global electric-electronic equipment company WEG has recently obtained the QUALICOAT certificate, after inspections conducted by recognised experts and tests performed by accredited laboratories according to ISO 17025 standards. The QUALICOAT seal is a product certification scheme developed by the homonymous global organisation based in Zurich (Switzerland) and specialised in certificates committed to maintaining the quality of painting and coating for aluminium and its alloys for architectural applications. The organisation defines comprehensive quality requirements and monitors their compliance by authorised plants worldwide, ensuring that products meet the highest quality standards and providing buyers the assurance that they will receive a highquality product that offers long-term value and consistent quality.
For further information: www.weg.net
International technology group ANDRITZ, specializing in the manufacture of innovative plants, equipment, systems, services, and digital solutions for a wide range of industries and end markets, has successfully completed the delivery, installation, and start-up of the new continuous surface treatment line and integrated wastewater treatment plant at AMAG rolling GmbH in Ranshofen, Austria.
The modern line with exclusively electric heating and advanced digitalization strengthens AMAG’s position as a leading specialist for high-quality aluminium surfaces and supports the company’s sustainability goals.
The 115-meter-long plant was built on a greenfield site. ANDRITZ’s equipment, especially the highly efficient spray pickling system, enables AMAG to perform high-
quality surface treatment of a wide range of hot-rolled and cold-rolled aluminium strips up to five millimetres thick.
Electric heating of the process with green energy and integration of a state-of-theart wastewater treatment plant contribute to environmentally friendly production.
Advanced digital solutions and modern data analysis methods are used to increase the quality and productivity in surface treatment. An autonomous coil transport system, also electrically powered, enhances the efficiency of the entire production process.
“Realizing this project together with ANDRITZ has been a very good decision,” says Florian Stadler, Managing Director of AMAG rolling GmbH.
“The collaboration between our teams has again been excellent as in previous projects, resulting in the timely completion of commissioning. With this new line we can further enhance the quality of our products and at the same time take another step towards decarbonization.”
International technology group ANDRITZ offers a broad portfolio of innovative plants, equipment, systems, services and digital solutions for a wide range of industries and end markets. Sustainability is an integral part of the company’s business strategy and corporate culture. With its extensive portfolio of sustainable products and solutions, ANDRITZ aims to make the greatest possible
contribution to a sustainable future and help its customers achieve their sustainability goals. ANDRITZ is a global market leader in all four of its business areas – Pulp & Paper, Metals, Hydropower and Environment & Energy. Technological leadership and global presence are cornerstones of the group’s strategy, which is focused on long-term profitable growth. The publicly listed group has around 30,000 employees and over 280 locations in more than 80 countries.
ANDRITZ Metals is – via the Schuler Group – one of the world’s leading suppliers of technologies, plants and digital solutions in metal forming.
The product portfolio also includes automation and software solutions, process know-how and service. In the metals processing segment, the business area offers innovative, sustainable and market-leading solutions for the production and processing of flat products, for welding systems and furnaces with its own burner solutions, as well as services for the metals processing industry.
For further information: www.andritz.com
Europolveri leverages its forty years of experience to offer three powder coatings series specifically developed for aluminium applications in the architectural and design sectors.
Over the years, powder coating treatments have become increasingly more important. As a matter of fact, they represent now a fundamental choice for architects and designers looking for high-performing and captivating finishes
© Europolveri
© Europolveri
for architectural elements, furniture and design items. In this context the role of powder coatings derives from the fact that it gives the possibility of choosing from a wide range of products with an ever-increasing level of specialisation, making it one of the key elements that contributes to the final result of a project, not only in formal aesthetic terms but also in terms of functionality and duration. For over forty years thanks to their technology, applicability, specific characteristics and variety, the powder coatings from Europolveri have represented a point of reference for the surface treatment of several types of objects.
The ArchitecturalPlus series – Qualicoat (class 1 and 2) and GSB certified – is composed by products specifically developed for the world of architecture, formulated to enhance the effects of powder coatings on aluminium components for doors and windows, window frames and curtain walls. It includes a wide range of colours in a smooth, wrinkled and textured finish, according to the specific needs of the customers.
The range ArchitecturalFlex represents the latest novelty proposed by Europolveri, a solution for coil coating that meets the specific requests of bending resistance and of low thickness applications.
The series ArchitecturalLignum, made of sublimation products and powder on powder products, offers the customers the possibility to reproduce the warm finishes of wood on the panelling and on the aluminium profiles.
For further information: www.europolveri.it
ESTAL has analysed the new Industrial Emissions Directive (IED), which came into force last August, introducing significant changes in the field of surface treatment of metals to reduce industrial emissions.
ESTAL, the European Association for Surface Treatment on Aluminium, which aims to promote the interests of its member companies - more than 400 anodizing and coating companies throughout Europe - has been analysing the publication of the latest European Directive on industrial emissions.
This new Industrial Emissions Directive (IED) was published in the Official Journal of the European Union on the 15th of July and entered into force on the 4th of August 2024. It consists of a series of amendments to the previous Directive IED 2010/75/EU, for which a consolidated text is now available1. The revision introduces several changes aimed at reducing industrial emissions, two of which are very important for ESTAL. First, competent authorities are now required to establish the strictest achievable emission limit values using Best Available Techniques (BAT) from the BAT-associated Emission Levels (BAT-AELS), whereas in the past it was only about not exceeding them. Second, when industrial processes are homogeneous across the EU, permits must include binding quantitative performance limit values for water consumption, waste generation, resource and energy efficiency, as appropriate.
1 https://eur-lex.europa.eu/legal-content/EN/ALL/?uri=CELEX:02010L0075-20240804
Where the processes are not homogeneous, the new Environmental Management Systems will have to include indicative benchmarks on these parameters.
The Surface Treatment of Metals and Plastics Best Available Technique Reference Document (STM BREF), which will set the permitting basis for the members of National Associations involved in ESTAL, will be among the first to be published under the new IED. This means that the STM BREF, currently under review, will be implemented with these requirements, more stringent than the ones in previous BREFs published under the original 2010 Directive. The ESTAL STM BREF Working Group has been involved in the review process, which started two years ago. Surface treated in batch anodising lines or batch chemical conversion lines being difficult to calculate and processes not being homogeneous, ESTAL considers not feasible to define quantitative resource efficiency requirements but considers appropriate to ask each conversion coating and anodising line to have its own improvement plan, tailored to its specific situation, so that all plants contribute to the objective of protecting the environment.
For further information: www.estal.org
Sometimes it is what is on the outside that counts. Our zinc flake systems are suitable for all screws and bolts and hug every thread perfectly. Premium quality that protects against corrosion, sets defined coefficients of friction and withstands a range of mechanical stresses. However, we are not satisfied with the best and are constantly on the lookout for new solutions and innovations – for every problem, for every challenge.
High cathodic corrosion protection
Complex fastenings no problem
Cross-linking at low curing temperature
Edited by KARL BUBENHOFER AG Gossau SG, Switzerland pulver@kabe-farben.ch
As part of its ongoing research and development efforts, KABE-Farben has recently introduced POLYFLEX® PES-140-SD-NT, a comprehensive low-bake series of highly weather-resistant powder coatings designed for architectural and other applications
For nearly 50 years, KABE-Farben has been synonymous with quality and technological innovation in the field of powder coatings. The KABE-Farben’s Qualicoat-certified powder coatings set benchmarks and reflect its continuous pursuit of the highest performance.
Pioneering work in low bake curing for certified facade applications
Almost 15 years ago, the company achieved a significant milestone: with its first low bake powder coating system for facade applications, certified according to Qualicoat class 1, it redefined standards. Its POLYFLEX® PES-165-NT system (Approval number P-0937) continues to impress with an extraordinary curing window starting from 10 minutes at 160 °C and its phenomenally fast curing capability at higher temperatures. This innovation underscores company’s early focus on developing in new technological areas to maximize both the quality and efficiency of its products.
In recent years, KABE-Farben has continued to invest in the development of low bake polyester powder coatings, specifically for facade applications.
The range has been significantly expanded with various gloss levels and surfaces, all with low bake properties. Specially developed versions for outgassing substrates are particularly noteworthy. Thus, the company offers not only tailor-made solutions for the complex requirements of modern architectural projects but also properties for high application security in other areas.
This year, KABE-Farben proudly presents POLYFLEX® PES-140-SD-NT, a comprehensive low bake series of highly weather-resistant powder coatings for architectural and other applications, all certified according to Qualicoat class 2. Compared to conventional facade quality, Qualicoat class 2 is characterized by significantly enhanced UV and weather resistance, resulting in longer durability —perfectly aligning with a sustainable focus. The product line includes a variety of surfaces, including smooth surfaces in different gloss categories and finely textured finishes.
The curing windows start from 10 minutes at 160 °C object temperature, which is unique in the market. At higher temperatures, the powder coatings further exhibit very short curing times.
These innovative polyester powder coatings offer not only excellent UV and
weather resistance but also outstanding processing properties, good storage stability, and superior surface characteristics. The company is particularly proud of its unique, smooth, matte system POLYFLEX® PES-140-SD-NT-GU smooth Corona Matt with a gloss level around 10 gloss units (60°), which is also certified according to class 2. This innovative, unique system offers not only outstanding aesthetics but can also be cured from 160 °C. Pearl-metallic variants with excellent durability are also available for all mentioned surfaces, providing additional aesthetic options and further enhancing the visual impact of any projects.
KABE-Farben stands for technological progress and highest quality in powder coatings. Its continuous innovative strength and commitment to excellent products make it the ideal partner for demanding architectural and various other applications. Trust in its team’s expertise and be inspired by its highly weather-resistant low bake powder coatings — for results that impress. Incidentally, the company has also been offering an extensive low bake portfolio for interior applications for many years.
In KABE-Farben’s product range, it is possible to find the following Qualicoat-certified low bake powder coatings:
- POLYFLEX® PES-165-NT smooth Corona silk gloss – Approval number P-0937
- POLYFLEX® PES-165-NT smooth Corona silk matt – Approval number P-1979
- POLYFLEX® PES-140-SD-NT smooth Corona silk gloss – Approval number P-2079
- POLYFLEX® PES-140-SD-NT smooth Corona Satin matt – Approval number P-2078
- POLYFLEX® PES-140-SD-NT-GU smooth Corona matt – Approval number P-2053
- POLYFLEX® PES-140-SD-NT fine structure Corona silk matt/matt –Approval number P-2056.
The design company DHK implemented a new plant for the pre-treatment of aluminium components equipped with the DRIZZLING system from ALIT Technologies Spa, which atomises a passivating solution prepared in realtime based on the dilution ratio set through the control panel.
The Belgian company DHK, manufactures and markets terrace covers, custom pergolas, canopies, window sills and aluminium thresholds, as well as supplying aluminium profiles, sandwich panels, steel, PVC and polycarbonate profiles and a comprehensive range of accessories for building structures for architectural use. It has outlets in Genk and Chatelineau (Belgium) and in Luxembourg, but at its Chatelineau site the company has a new and modern line for pretreating and powder coating the metal surfaces it brings to the market. Aluminium, in particular, is the material provided by DHK par excellence, as it offers several advantages that make it perfect for architectural use, especially in exterior structures not subjected to heavy loads.
It is lightweight, fully recyclable, easy to work with, and has excellent corrosion resistance characteristics when adequately pre-treated.
The pre-treatment of aluminium surfaces
Pre-treating an aluminium surface means performing a series of chemical processes to transform it and make it an ideal substrate for anchoring the layer of paint that will be applied to it. The combination of the chemical treatments carried out, added to the paint product applied, will make the coated component resistant to atmospheric corrosion and thus usable in the architectural sector. That is precisely what DHK’s modern pre-treatment and coating line does: Aluminium
parts are hooked onto an overhead conveyor, pass through a spray tunnel where they are degreased, pickled and passivated and are finally transferred to the coating area for the application of the powder paint.
“Initially, the aluminium workpieces are spray degreased and pickled by the combined effect of the acidic pickling agent ALFIDEOX 82/3 and the degreasing additive ALFISID 14. In the subsequent tunnel segments, the parts are rinsed with mains water and then with demineralised water. At this point, their aluminium surfaces are perfectly free of oils and grease, deoxidized and, therefore, reactive and ready for the subsequent passivation treatment. Passivation is a key stage during which polymerbased adhesion promoters and titanium-based corrosion inhibitors are chemically anchored to the surfaces. In this case, we use ALFICOAT 748, a QUALICOAT and GSB-approved product that has passed the strictest tests in the industry, including 10-year outdoor exposure testing. Usually, this is applied by dipping or spraying, but DHK uses an absolutely innovative and effective application technology,” has explained sales engineer Ludwig Liesens, the pretreatment division manager of Alufinish GmbH – the company supplying the pre-treatment products. “
The DRIZZLING system provided by ALIT Technologies Spa
The pre-treatment plant is equipped with a DRIZZLING system, which atomises a solution of ALFICOAT 748 prepared in real-time based on the dilution ratio set through the control panel. The DRIZZLING technology instantly mixes the chemical product with demineralised water in-line and then sprays that mixture on the aluminium components, creating a sort of mist that settles on their surfaces to passivate them. “The great advantage offered by DRIZZLING is that the chemical solution is always freshly prepared and, therefore, extremely reactive and free of contaminants dragged from previous steps.
Traditional passivation tanks and energy-intensive spray pumps are no longer required. The solution is prepared instantly and atomised on the surfaces. Chemical analysis of the liquid in the tank is no longer necessary precisely because there is no longer a tank. In short, the management of the process is remarkably streamlined and the footprint of the system is smaller than that of traditional spray technologies,” has continued Liesens. “Installation was swift: two spray bars were mounted one opposite the other inside the tunnel, whereas the mixing and control panel was installed outside it. As a plug-and-play system, it was ready to be used within a few hours. The technicians from ALIT Technologies assisted the customer during the start-up phase and trained the plant operators.”
Excellent passivation results with minimum consumptions
“There are two ramps with eight atomising nozzles in total. The flow rate of the solution is about 160 liters/hour; the consumption of the ALFICOAT 748 chemical is about 0.5 kg/hour. The quality of the passivation results is excellent. The titanium deposit is regularly checked and is well within the ranges set by supplier Alufinish GmbH. The combination of Alufinish GmbH’s chemical product and ALIT Technologies Spa’s DRIZZLING application system is perfect and will soon be implemented in other aluminium pre-treatment plants. I would like to thank Thibaut Braibant and Jean-Marie Jenicot from DHK for the collaboration in the purchase, start-up and management of the company’s paint shop and for their trust in us,” has concluded Liesens.
For further information: www.alit-tech.com
Alessia Venturi ipcm®
Powder coating, with its evolving colour, decorative, and aesthetic effects that imitate natural surfaces and improve both the appearance and the functional performance of the treated components, is increasingly the preferred choice of architects and designers for finishing architectural elements, such as metal cladding. That is also thanks to the collaboration and joint experimentation between metal panel manufacturers and powder coating manufacturers. In this article, we recount the professional partnership between Emboss Panels, a specialist in the production of metal panels with three-dimensional effects, and TIGER Coatings, which supplies it with special-effect, matte and flat matte, metallic, and anodised-like powder coatings to enrich its products’ sculpted surfaces.
Acladding system is like a skin that protects, decorates, and enhances the underlying material and its shapes. Cladding can be used to accentuate the modernity of a building or room, to curb, contain, and screen light for specific visual effects, to protect an area or isolate it thermally and acoustically, to enhance aesthetics and beauty, and to improve the sustainability and durability of a structure or component. Thanks to its versatility in terms of shapes, materials (it can be made of wood, metal, or composites), and finishes, cladding is one of the most powerful tools for architects and designers to create exclusive, distinctive structures with a soul.
“Sculptured surfaces for architecture”: this is the evocative definition that Emboss (Tezze sul Brenta, Vicenza, Italy), a manufacturer of decorative panels for architecture and interior design founded in 2018, gives of its products. This company represents the combination of different souls into a refined and exclusive solution for exterior and interior cladding, as it has designers and craftspeople work together to create
metal panels with striking decorative effects. Emboss serves architects, designers, installers, distributors, and end users who want to customise their projects with exclusive, attractive-looking panels. Its innovative manufacturing process allows deforming metal sheets to ultimately offer three-dimensional surfaces with vibrant, multiform effects.
“At its foundation, our company was focused on technical design,” says Cesare Zilio, the engineer who established Emboss, “as it was originally a design studio specialising in metal façade cladding. Over the years, however, we have increasingly dealt with the production aspects of metal cladding sheets, developing the concept of panels with threedimensional effects. Experimentation with various manufacturing techniques has gradually led us to define an efficient and innovative process for producing 3D metal panels used for façade cladding, interior cladding, and suspended ceilings.”
Although such machining processes creating 3D effects through sheet metal deformation are already enough to make Emboss’ metal panels
an extremely attractive, unique, and exclusive solution for architectural cladding, the paint products applied on them certainly contribute to further enhancing these effects. “Finishes must emphasise what Emboss has added to the simple metal sheet. They should also be as smooth as possible, as the tactile effect is already inherent in the threedimensionality we give to the metal,” explains Zilio. “Since we prefer to use powder coatings, we choose to work with an industry leader, TIGER Coatings, not only for the quality of its powders but also for its technical support service, its laboratory’s assistance for testing and validation, and its willingness to experiment and formulate products with customised colours and effects.”
Surfaces with a soul
“Emboss’ sculptured surfaces are decorations created with an exclusive production technique: each model is carefully designed and mechanically reproduced with a plastic deformation technique that
combines craftsmanship and industrialisation. This workflow offers numerous opportunities: it is possible to process solid, perforated, or expanded metal sheets in aluminium, galvanised steel, stainless steel, brass, copper, and zinc-titanium (an alloy whose surface, under the action of the weather, becomes covered with a thin, self-protective layer that gives it a naturally ageing and aesthetically pleasing appearance, Ed.),” indicates Zilio.
“Despite being a young company, we are able to supply finished panels ready to be installed, not only formed and coated but, if necessary, also folded and framed. Ideally, Emboss’ three-dimensional panels should be specified directly by designers: by conceiving a project with this type of cladding from the outset, both the aesthetic performance and the production costs can be optimised in terms of sheet division, modules, finishes, and so on.”
Emboss offers several standard patterns, as well as the possibility to customise the effects to make each project original and exclusive.
“Our portfolio includes standard patterns such as Bumps, an organic
water effect; Carapax, an organic effect similar to the previous one but with a denser pattern; Branch, a branching pattern that ensures continuity among panels; Line, with elegant linear stripes; Quilt, a soft, quilted effect; and Sand, with a wavy pattern reminiscent of dunes. At the same time, we place great importance on customisation. We give our customers the opportunity to create personalised designs, and this greatly enhances our offer,” states Cesare Zilio. “Emboss’ main strength is to have investigated lean manufacturing technologies to offer tailor-made solutions at attractive costs and even for small batches.”
All Emboss panels can be made in solid or perforated metal and decorated with different technologies, from anodising to powder or liquid coating, from electro-colouring to polishing and satinfinishing. Thanks to these multiple combinations of substrates, effects, decorations, and cladding functions, Emboss’ panels are a very versatile decorative solution: they can be used both for exterior architectural applications such as façade cladding and roofing and for indoor applications such as false ceilings or wall cladding.
Solid sheet metal panels are typically used for complete roofing systems, whereas perforated or expanded metal ones can be used to create transparencies and interplays of solids and voids, for example, in solar shading and ventilation systems.”
Powder coating:
multiplying the decorative effects available
“Processing all types of metal sheets opens up the possibility of using different surface finishes to enhance each three-dimensional effect in its specific design context. We range from polished steel to satin-finished steel and from pre-anodised aluminium to coated aluminium, which makes up a large part of our volumes. For Emboss’ products, coating is a very flexible and useful finishing solution because it provides a vast range of colours, gloss levels, and special effects. Its only limitation is that it diminishes the metal surfaces’ gloss degree and cannot maintain the mirror effect, which is important for some patterns. Still, with TIGER’s experimentation and technical support, we can offer an excellent compromise between colour, effect, and gloss,” explains Cesare Zilio.
“Working in the metal industry, I was familiar with TIGER and the quality of its products even before Emboss was established in 2018. Our collaboration, including the supply of TIGER paint products and the joint search for the best finishes for our 3D panels, started about two years ago. Today, we have an exclusive partnership for both standard finishes in RAL colours and special-effect finishes, such as, for example, those from its outdoor-specific TIGER Drylac® Series
68, which we find particularly interesting due to its super matte effect. We also use coatings from its 3D Metallics series, all super durable class 2 products. Finally, TIGER also supports us in developing customised and exclusive finishes, including, for example, in NCS colours, which are then produced in small batches upon customer approval. Emboss is not a powder specialist, but we do receive requests for the most diverse finishes: our products are special, so their finishing requirements are also special.
“In particular, for powder application on exterior cladding and façade panels, we rely on the expertise of Pintarelli Verniciature (Trento, Italy) and its certified pre-treatment and coating cycles, whereas for interior applications, we also rely on other contractors. Emboss always provides its contractors with the product code of the powder to be used (colour and chemical class) or, in some cases, purchases the required powders directly from TIGER.”
TIGER Drylac® Series 68 and 3D Metallics
“The matte and flat matte anodised-like colours of TIGER Drylac® Series 68 are particularly suitable for Emboss’ products because they enhance the play of light and shadow created by our 3D patterns,” notes Cesare Zilio. “They emphasise the sheet’s convexity, accentuating its threedimensional effect. In addition, their super durable and highly weatherresistant formulation makes them ideal for finishing cladding panels for outdoor applications.”
TIGER Drylac® Series 68 includes numerous matte or flat matte smooth finishes whose application is not limited to aluminium but can also be extended to steel and galvanised steel. They offer high colour consistency and homogeneity among batches, and they are super durable paints with GSB and/or QUALICOAT certifications, offering resistance for up to 10 years in Florida.
TIGER Drylac® Series 68 3D Metallics also consists of GSB Florida 3-year
and/or QUALICOAT class 2 certified super durable polyester coatings and combines the performance and one-coat application of the Series 68 with the high gloss and depth of effect typical of metallic liquid paints, turning each panel into an exclusive element.
Powder coatings’ unrivalled versatility
“Recently, we have also started assessing the use of liquid paints, starting with a pigmented clear coat for pre-anodised aluminium with a mirror-like finishing,” says Cesare Zilio. “This would allow us to mantain a glossy appearance combined with colour, a special effect not obtainable with powders. At the same time, however, the advantages of powder coatings, such as the degree of customisation, uniformity, repeatability of finishes and colours, their inherent sustainability, and the one-coat application process, remain unrivalled and make this solution our preferred choice.”
The system with OptiSpray All-in-One pump technology and double OptiSpeeder powder hoppers (DualSpeeder) enables the handling and preparation of two independent colours one after the other for ultra-fast colour changes or in parallel for simultaneous coating from both OptiSpeeder powder hoppers.
In an era marked by growing environmental awareness and sustainability concerns, industries are continually seeking innovative ways to reduce their carbon footprint. One such advancement that has gained traction is the shift towards chrome-free passivation in the pretreatment process before powder painting.
Chrome-based treatments have long been a staple in the industrial realm for passivating metal surfaces before coating. Chromium (VI) compounds, particularly hexavalent chromates, have been favoured for their corrosion resistance and adhesion-promoting properties. However, the environmental and health hazards associated with hexavalent chromium have led to stringent regulations and a collective drive to find more sustainable alternatives.
In response to the limitations and risks of traditional chromate-based methods, chromefree passivation has emerged as a safer and more ecologically responsible alternative. The primary aim of this approach is to ensure a high-quality surface finish while minimizing the environmental impact.
Benefits of chrome-free passivation
Environmental preservation: chrome-free passivation substantially reduces the release of toxic substances into the environment, contributing to the preservation of ecosystems and minimizing pollution. This aligns with the overarching goals of sustainable industrial practices.
Human health protection: the elimination of hexavalent chromium from the process safeguards the health of workers involved in the treatment and painting processes, reducing the risk of exposure-related illnesses.
Regulatory compliance: REACH tighten regulations regarding hazardous substances, chrome-free alternatives meet all of REACH requirements.
Resource efficiency: chrome-free passivation processes require lower energy consumption and fewer chemical inputs, leading to increased efficiency, reduced operational costs and carbon footprint.
Performance and quality: contrary to misconceptions, chrome-free passivation does not compromise the quality of the treated surface. Chrome-free alternatives offer comparable corrosion resistance and adhesion properties, ensuring a high-quality finish for powder painting.
Innovation and reputation: embracing eco-friendly practices like chrome-free passivation can enhance a company’s reputation and promote innovation. Businesses that prioritize sustainability are more likely to attract environmentally conscious clients and partners (Fig. 1).
Chrome-free passivation from Alsan: EcoAl®20
EcoAl® 20 is a titanium-based chrome-free passivation which combines titanium compounds and selected polymers to create a protective layer on the metal surface with excellent corrosion resistance and adhesion promotion.
EcoAl® 20 can be applied by immersion, cascade or spray. The conversion layer obtained with the EcoAl® 20 allows excellent results on adhesion and corrosion resistance to be obtained with all types of paints and specifically grants great protection against filiform corrosion. With EcoAl® 20, proper conversion layers could be quickly achieved, just with a short time of contact (around 10-60 seconds), depending on the application method.
The EcoAl® 20 technology is easily adaptable to each process line, including also a fully automated system that guarantees the control of each of the working parameters. In Figure 2 some examples of EcoAl® 20 implementation are shown.
EcoAl® 20 was firstly approved by QUALICOAT in 2003 (A-013). Since then, it has been successfully installed worldwide in both horizontal and vertical lines. Ecoal® 20 is the Qualicoat approved chrome-free pretreatment, leader in the Spanish, Moroccan and Mexican markets. It is estimated that, under QUALICOAT certification, more than 120.000.000 square meters of extruded aluminium are treated with EcoAl® 20 every year around the world. EcoAl® 20 has recently been further recognised by obtaining the prestigious license from GSB International, certifying its compliance with the stringent quality standards of GSB AL 631-2 for chemicals used in aluminium pretreatment (Fig. 3).
Turn key solutions for industrial wastewater treatment
Design and manufacturing of plants and chemicals for industrial wastewater treatment
Chemical-physical plants
Sludge treatment and compactor systems
Ion exchange demineralization systems and reverse osmosis systems
Oil separators
Filtering systems
Batch type systems
Flotation units
Chemicals and spare parts for water treatment
Technical service, support and maintenance of wastewater treatment plants
The adoption of chrome-free passivation EcoAl® in the pre-treatment process before powder painting is a significant stride towards ecological excellence in the aluminium industry. By shunning the use of hazardous hexavalent chromium compounds, businesses can not only improve their environmental stewardship but also contribute to cleaner and safer production processes. The shift to chrome-free alternatives is a testimony to the innovative spirit of industries as they seek to balance quality, performance, and sustainability in their operations.
In the year of Alsan’s 50th anniversary, the company reaffirms more than ever its commitment to sustainability and respect for the environment. These pillars are essential to ensure the future of our planet and the legacy of generations to come. Its dedication to quality and excellence is reflected in the continuous development of products, such as
EcoAl® 20, that are designed to meet the most demanding environmental challenges.
Over the decades, Alsan has proactively taken responsibility for creating sustainable solutions that not only meet today’s quality standards but also set the benchmark for the future. Every improvement implemented in its products reflects its long-term vision, which is centred on the sustainability of the aluminium industry. This commitment was highlighted by the company’s strategic decision, four years ago, to establish its own technical advisor and warehouse in Poland, enhancing its ability to serve and respond to the European market with agility and expert insight (Fig. 4). This move has allowed it to forge closer connections with Alsan’s clients and partners, promoting practices that respect and enhance our environment, thereby ensuring a lasting legacy for future generations.
Klaus Vissing
Fraunhofer Institute for Manufacturing Technology and Advanced Materials IFAM – Bremen, Germany klaus.vissing@ifam.fraunhofer.de
The new UltraPLAS coating developed by Fraunhofer researchers has proven to be a ground-breaking solution to the challenges of primary forming processes. This advanced release and easy-to-clean coating is applied as a gradient layer using a cold plasma process and is suitable for materials such as tool steel, stainless steel and aluminium. The unique physical properties of UltraPLAS enable perfect moulding of even nano-scaled and reflective surfaces. By reducing the number of post-processing steps and renouncing external release agents, the application is classified as highly economical.
How can high-quality and sophisticated tool surfaces be coated in such a way that production is improved, and cleaning processes are significantly delayed or simplified? Researchers at the Fraunhofer Institute for Manufacturing Technology and Advanced
Materials IFAM investigated this question together with partners in the “GlossyCast” and “UltraTrenn” projects funded by the Industrielle Gemeinschaftsforschung IGF. The aim of the research projects was to reduce the demoulding forces and the formation of deposits while
permanently withstanding the specific stresses of zinc high-pressure die casting and plastic injection moulding. Specifically, the injection moulding of technical plastic parts requires solutions to reduce demoulding forces and the formation of deposits. This applies to the production of components with high-gloss surfaces or highly defined microstructures, such as plastic lenses, decorative trims or connectors with high dimensional accuracy. Similarly, in zinc high-pressure die casting, deposits on the mould surface as well as deposits of release agents and lubricants prevent the production of high-quality, glossy zinc castings. This results in considerable costs for post-processing of the cast parts. Irrespective of this, the application of release agent alone can account for up to 20 percent of the cycle time, meaning that there is considerable potential for savings if release agents are not required anymore.
UltraPLAS enables outstanding coating properties
To meet the aforementioned requirement-profile of ultra-smooth, optical surfaces (Ra < 25 nm) within the projects, the coating itself must be smooth and structureless. In order to achieve this, the cold plasma process, the so-called PE-CVD process (plasma enhanced chemical vapor deposition), was used. By building up a gradient layer, this process enables excellent layer adhesion to the product body on the one hand and exceptional non-stick properties with excellent physical characteristics on the product side on the other. The coating produced in this way is characterized, for example, by a high modulus of elasticity (28 - 32 GPa) and a high density (1.5 g/cm³). This results in a Mohs hardness range of 5.5, which is therefore on par with glass or enamel. Characteristically, as a non-stick coating, it also has a low surface energy (< 28 mN/m) with low polarity (< 1.5 mN/m). This behaviour is supported by the fact that the Fraunhofer researchers have succeeded in producing the UltraPLAS coating with a particularly thin layer thickness of less than 100 nm. This even proved to be necessary in the GlossyCast project to provide a good non-stick effect. In addition, the thin, structureless layers allow both nanoscale surface structures, e.g., for the nanoimprint process, and mirror-gloss surfaces to be perfectly reproduced.
Sustainable quality and economical production guaranteed
Extensive practical tests carried out as part of the projects at various industrial companies have shown that demoulding forces and the formation of deposits are reduced in the field of injection moulding.
It has also been shown that the reduction in adhesion forces reduces the total demoulding forces. As a result, the demoulding temperature can be increased, and the amount of friction reduced. In contrast to the state of the art, the coatings can be removed both effectively and gently using plasma technology so that, if necessary, a new coating can be applied several times without any loss of quality. This is particularly interesting for high-gloss tool surfaces, as it eliminates the need for time-consuming polishing or ultra-precision machining. It has also been shown that the direct production of high-quality zinc die-cast surfaces using casting technology can significantly increase economic efficiency.
By significantly improving the surface quality of the cast parts, costly and time-consuming mechanical post-processing steps such as blasting, grinding, and polishing can be simplified or even avoided altogether. In addition, the individual process steps of electroplating can be shortened or reduced.
The development of this durable UltraPLAS release coating for zinc die casting stands for a significant advance in foundry technology. The possibility of cutting release agents opens new potential for improving
casting quality, reducing production costs and making production more environmentally friendly.
As the cast products are manufactured without release agents, the pretreatment time for electroplating is reduced and material consumption is lowered. The manufactured components have the desired roughness. Due to the smoother surface, bright copper plating can be dispensed with, which leads to savings in materials, time and wastewater. Reducing the layer thickness of copper (cyanide) and bright nickel by 50 percent each led to further savings in materials and time.
Background information on the development process
The development of UltraPLAS was preceded by the PLASLON non-stick coating, which is characterized by high hardness (Mohs hardness 4.5 - 5.5) and excellent temperature resistance up to 230°C. This property profile has made PLASLON a popular PFAS-free easy-to-clean coating for cookware. Through continuous innovation and the development of products such as UltraPLAS and PLASLON, our institute makes a significant contribution to improving production processes and promoting sustainability in the industry.
The following projects have been funded by the Federal Ministry of Economics and Climate Protection as part of the program for the promotion of joint industrial funding (IGF) based on a decision by the German Bundestag.
GlossyCast
• Funding reference IGF 22003 N
• Innovation in zinc die casting - Production of mirror-glossy cast surfaces through release agent-free production
• Duration: 01.02.2021 - 31.01.2024
• Project partner: Fraunhofer Institute for Manufacturing Technology and Advanced Materials IFAM fem Research Institute
UltraTrenn
• Funding reference number: IGF 22597 N
• Non-destructive, ultra-thin release coatings with layer thicknesses below 100 nm for reliable demoulding and postprocessing of micro-moulded parts
• Duration: 01.10.2022 - 30.09.2024
• Project partner: Fraunhofer Institute for Manufacturing Technology and Advanced Materials IFAM University of Paderborn.
CHEMTEC’S technologies are designed to have a very limited environmental impact, to reduce consumption of resources and for a greater operational simplicity.
CHEMTEC develops customized solutions that aim to maximize the customer’s satisfaction.
NANOTECHNOLOGICAL CONVERSION COATING
WATER PURIFICATION AND RECIRCULATION
ONE STEP METAL PRETREATMENT
PAINT STRIPPERS
DISCOVER MORE ON WWW.CHEMTEC.IT
Monica Fumagalli ipcm®
Based in Muro Leccese, in the Salento region of Apulia (Italy), Azeta Srl was one of the first businesses in this area to specialise in the processing and surface treatment of aluminium and the first to patent, in the 1990s, a wood-effect coating applied with a liquid-on-powder cycle on this material. It is also the first company in the Italian aluminium industry to have recently installed an automatic vertical powder coating plant by Euroimpianti for profiles combined with Wagner’s latest powder feeding and control device, the IPS system, to increase its production capacity and reorganise its workforce more effectively.
In Italy, the first documented use of aluminium in construction dates back to 1897, when architect Raffaele Ingami used it for cladding the dome of the church of San Gioacchino ai Prati di Castello in Rome. It was only a few years before the beginning of the 20th century, which would have gone on to be called “the century of aluminium” because of the growing importance of this metal in the most diverse applications, thanks to its characteristics of lightness, ductility, lustre, and corrosion resistance, as well as, in more recent years, the possibility of recycling it completely.
The Ruggeri Group specialises in the casting, extrusion, and coating of aluminium profiles, particularly for the door and window industry.
In the space of a few decades, aluminium went from being employed exclusively for jewellery production to widespread use in construction, especially for roofing, in the metallurgical industry at the service of World War I, and even in the nascent aeronautical sector: from 1908, the rigid structure of Zeppelin airships was made of this material, as were some parts of Charles Lindbergh’s Spirit of St. Louis aircraft that made the first transatlantic flight in 19271
Precisely these innovative solutions for the aeronautical and, later, automotive sectors inspired the use of aluminium in architecture as well, which was actually already widespread in the United States, whose skyscrapers and single-family houses, from the Chrysler Building to the experimental Aluminaire House, the first house built entirely in metal, soon became reference models for the Italian construction sector, where the use of aluminium finally came into its own in the 1950s. However, it was only in the 1970s, following the energy crisis and the increased demand for thermal insulation in homes, that this material began to spread in the world of door and window frames, previously the exclusive preserve of wood, especially becoming a constituent element of double windows, characterised by a second frame added to improve the thermal insulation of a wooden one. Following the rapid technological development of this industry, special surface treatments capable of giving aluminium profiles greater resistance to atmospheric agents and attractive aesthetic effects, such as anodising, powder coating, and decoration by sublimation, soon began to become widespread.
“I was one of the first entrepreneurs to introduce aluminium profiles in southern Italy precisely in the years when this material’s qualities were also beginning to be recognised in the window and door industry,” says Salvatore Ruggeri, Azeta Srl’s founder and the current chairman of the Group that has grown around it, as well as a well-known figure not only in the business world but also in the Italian political one, thanks to his past as a parliamentarian. “That is why we chose to specialise in the processing and surface treatment of aluminium: in 1995, we installed the first coating plant capable of applying wood-effect products with a liquidon-powder cycle patented by us. Today, we are one of the best-known and most-awarded aluminium hubs in Southern Italy. For the surface treatment of extrusions, we work with a horizontal coating plant. However, driven by the need to improve and automate production as much as possible,
1 https://dsdra.web.uniroma1.it/sites/default/files/Materiali%20e%20 strutture%2012.pdf
From left to right:
Each booth is equipped with 4 opposing reciprocators.
The monorail conveyor in the foreground and the drying and curing oven in the background.
The machine for cleaning the hooks without chemicals.
we recently decided to experiment with a new type of plant, a vertical powder coating system for profiles designed and installed at the end of 2023 by Euroimpianti (Valeggio sul Mincio, Verona, Italy) combined with Wagner’s latest-generation powder feeding and management plant, the IPS system.”
The Ruggeri Group: a complete aluminium supply chain
Founded in the early 1970s thanks to the entrepreneurial initiative of its current president, the Ruggeri Group, which takes its name from him, is now a consolidated reality consisting of 4 companies, each specialising in a crucial processing phase of the extrusion supply chain.
“When I think back to when I started my business,” comments Ruggeri, “I cannot deny that I was faced with several difficulties but also successes and satisfactions. I began by selling iron mouldings. When the first aluminium profiles with special effects began to circulate, I became interested in them, immediately realising the considerable potential of this material. In 1975, with two other partners, I founded Azeta Metalli Sas, launching the painted aluminium profile, which did not exist on the market at the time. This was met with increasing success. Therefore, afterwards, we patented Woodall, the first powder-on-liquid application process to obtain the wood effect on aluminium, which also spread to northern Italy with a powder-on-powder technology. In 1999, we began to see the need to produce profiles ourselves, creating a new factory devoted to extrusion and simultaneously enhancing our coating activities by building an additional hall for them. By this time, production volumes had reached 500 t/month and were increasing steadily. In 2006, we finally opened our own foundry, thus setting up a complete
aluminium supply chain.” Today, the Ruggeri Group, which employs over 170 people, consists of Ruggeri Service Spa, the foundry producing extrusion billets; TO.MA. Spa, specialising in aluminium extrusion and manufacturing extrusions for the door and window frame, architecture, and industrial sectors; Azeta Color Srl, offering hundreds of solutions for finishing aluminium with both liquid and powder paints, from RAL colours to wood-effect coatings with the already mentioned Woodall process as well as the Lignall, PAZ (powder-on-powder), and sublimation ones; and Azeta Metalli Sas, marketing and distributing aluminium profiles and sheets, window and door accessories, and aluminium processing machinery and equipment. “The Ruggeri Group’s companies, therefore, cover the complete chain of transformation, processing, and marketing of aluminium extrusions,” Ruggeri confirms, “meeting the highest product quality standards while fully respecting our surrounding area and the environment. Suffice it to say that we can currently produce billets on demand in 6060 alloy with a recovered material content of 87%, which places us in class A for recycled/recovered content according to the parameters of REMADE certification2.”
Woodall: the first wood effect on aluminium Probably due to the long-standing tradition of woodworking and coating in the Italian door and window industry, aluminium has been slow to be recognised in this country as a valid alternative to elements made of this natural material. Perhaps, however, this very reason was also at the root of the success of Woodall, the process Azeta patented in 1995.
2 https://www.remadeinitaly.it/remade/
Based on the idea to combine the strength and durability characteristics of metal with the warm and natural aesthetics of wood, it blends well with different architectural styles, especially in homes where wood is a central element. “Further advantages of coated aluminium elements compared to wood,” Ruggeri emphasises, “include lower maintenance requirements thanks to high corrosion resistance, better thermal insulation thanks to the techniques implemented (such as thermal cutting, which improves insulation and avoids heat dispersion), lightness to facilitate installation and reduce the overall load on architectural structures, and last but not least, environmental friendliness, as aluminium is 100% recyclable.”
The first vertical coating plant for profiles
Continuous production growth and new market requirements convinced the Ruggeri Group’s management to start an expansion project involving its foundry, whose surface area will be doubled, its coating department, integrated with the new vertical profile coating plant, and its packaging division. The work is scheduled for completion between January and February 2026. Fabrizio Ruggeri, Salvatore’s son, who is joining his father at the company’s helm,
points out: “The system designed and installed by Euroimpianti is the first installed in our factory for vertical profile coating. We have always worked with horizontal coating plants, but this vertical machine immediately proved to bring significant advantages over the others. Before choosing Euroimpianti as the supplier of this technology, we assessed other options, but its solution convinced us with its high automation performance, which would allow us to reassign our staff to other departments, and its increased capacity in terms of coated volumes, around 15 t/day, which would finally enable us to meet the needs of a market requiring increasingly higher quantities. A further benefit of vertical coating relates to the positioning of the heaviest profiles, which, by standing vertically, do not run the risk of bending, as can occur in horizontal plants, thus significantly reducing scrap rates.”
The main features of the coating plant “Every plant designed by Euroimpianti,” indicates Gianluca Baruffaldi, CEO at Euroimpianti Group, “is configured and customised according to the number of aluminium profiles to be coated and the special requirements of each specific workflow. The system installed at Azeta boasts state-of-the-art technology, extreme reliability, and high production capacity,
and it was the subject of an ad hoc study in terms of energy and thermal savings. It starts with a 10-stage pre-treatment tunnel. Every detail of the tunnel, such as segment length, tank characteristics, and interaxle spacing, is designed according to the requirements of Qualicoat and AAMA chemical treatment cycles. The last passivation stage is equipped with the Nebula system, ensuring that the workpieces are sprayed with a solution of consistent chemical quality while reducing water consumption. The machine has a chemical dosing, mixing, and control unit, an operating system with a touch-screen control panel, and spray bars with atomising nozzles. After pre-treatment, the monorail conveyor takes the components to the drying oven designed so that heat can be recovered from the parts as they cool.”
The 2 coating booths belong to the Diamond series, whose name is inspired by their diamond-like shape. “What makes this application booth stand out is undoubtedly its geometry: thanks to the perfect symmetry of its structural components, profiles with any shape and cross-section can be coated with maximum performance,” states Antonio Cimenes, sales agent for the Veneto-based company. “It comprises a powder-coated metal structure that provides support and containment for a series of symmetrically opposed dielectric sheets. 4 reciprocators per side, specially angled gun bodies, and a linear conveyor path during coating ensure flexibility and control of application parameters. The side sheets delimiting the application area feature a software-controlled rotating movement that promotes powder recovery and facilitates and speeds up colour change operations. Cleaning inside the booth is fully automatic thanks to the dust extraction and recovery system consisting of a high-efficiency cyclone separator and a self-cleaning cartridge filter that intercepts dust particles not removed by the cyclone. The floor also consists of a rotating dielectric sheet that is automatically cleaned. The line is completed by a device that allows cleaning the hooks without chemicals.” Among Azeta’s main powder suppliers is Pulverit Spa, whose history began at the same time as the Apulian company.
The vertical plant and the IPS powder management system: a winning combination “This is the first vertical coating plant to adopt Wagner’s innovative IPS powder management system in the italian
aluminium industry,” emphasises Michele De Cesaris, Area Manager-Powder Coating at Wagner. “At the same time, we also supplied Azeta with our classic SuperCenter EVO powder centre, the first designed to be in line with Industry 4.0 parameters and already tried and tested with countless vertical coating systems: the SuperCenter EVO and the IPS plant work perfectly with each of the 2 booths.”
On the other hand, this combination has ensured considerable advantages: “The IPS powder centre increases productivity, guarantees high quality standards, streamlines operations, and reduces colour change times consistently. The powder feeding system is revolutionary, as it is based on the concept of working with a pressurised tank, without the use of pumps (Venturi or pinch), fully meeting the definition of high density. It is equipped with a twofold fresh powder feeding system, allows powder preparation by ultrasonic sieve, vibration, and fluidisation, and features special systems for accurate gun dosing. Its integrated sensors for weight, flow, pressure, and level and its fully automatic colour change system guarantee high productivity and cost efficiency, as the application remains consistent over time – over 2,000 hours without adjustments to the application parameters and therefore without routine maintenance. Thanks to this new powder centre, Azeta can better manage paint consumption and spray fan patterns, thus improving coating performance, the most critical aspect for the Apulian company. “IPS also features the highest level of automation of colour change operations without human intervention, with centralised control of all process steps and real-time detection of powder consumption.”
The chemical-physical waste water treatment plant
The line is also equipped with a wastewater treatment plant for the pre-treatment tunnel, developed by Saita Srl of Limena (Padua). "The water treatment system we installed at Azeta," says Carlo Enrico Martini, Sales Manager of Saita, "is a traditional chemical-physical plant with a capacity of 2,000 liters per hour, where the diluted water discharged from the washing stages is treated continuously, while the concentrated wastewater is stored in a balancing tank and dosed into the same purification system. Demineralised water is produced and recovered in a closed loop within the washing tunnel tanks by a demineraliser with ion-exchange resins in a dual-line system with a capacity of 10,000 liters per hour."
“Thanks to this new coating line, we will be able to consolidate our position as a supplier for the door and window frames industry and become an increasingly important player in the field of coated
aluminium profiles, further increasing our production capacity and coating quality,” concludes Salvatore Ruggeri. “Even though the investment was significant, it is the result that matters. We are also satisfied with the partners we chose: Euroimpianti and Wagner’s teams demonstrated not only excellent skills but also a remarkable ability to adapt to our needs and even go the extra mile, as in the case of the second powder centre that Wagner provided us with to avoid issues with a system that had never before been tested with vertical coating technology. As a result, we have tripled our production capacity, reduced the number of shifts, and relocated our employees to other departments with different tasks.” That is going to confirm Azeta’s strategic role in the aluminium coatings sector: “The wood effect now has a large market, and we are currently developing a coating with the same effect on PVC. We are constantly looking for solutions to meet the demand for profiles with the most unusual effects: our history started there, and we will continue to pursue this path. We believe that Azeta’s future lies in this pioneering approach.”
Enrico Dall’Igna
ST Powder Coatings S.p.A. - Montecchio Maggiore (Vicenza), Italy enrico.dalligna@stpowdercoatings.com
In order to support sustainability, ST Powder Coatings has launched Green Oasis: the new range of powder coatings is based on polyester resins containing a combination of recycled raw materials and/or with part of the components deriving from renewable sources.
It is ever-increasing the number of consumers and companies placing great value on environmental compatibility. So, they are selecting powder coatings for their projects, as these solutions are already considered ecological because of their zero-emissions. However, it is not exactly so: conventional powder coatings are composed by more than 50% of resins obtained from oil and natural gas derived from underground fields.
It is precisely for this reason that ST Powder Coatings aims to constantly select products and manufacturing options that are useful for reducing
the negative impact on the environment. Our time requires innovative solutions which guarantee the liability of our planet, preserving it for future generations.
The objective must then be to minimise harmful emissions in the environment without compromising the quality, competitiveness and standards of the finished product. Therefore, the company has asked itself: can it optimise its production processes and reduce its ecological footprint, maintaining or improving quality and reducing the carbon footprint at the same time?
The new Green Oasis powder coatings range
The research and development laboratory of ST Powder Coatings has always focused on technical innovations that are not only beautiful to look at, but that also benefit people and the environment, offering an added value. Its efforts led to the creation of a first series of powder coatings with raw materials with components deriving from renewable sources already in 2012 – an absolute novelty at the time. Based on the experience gained, the company is now able to present the new Green Oasis powder coatings series, available in three configurations, two of which, the R and PLUS series, will soon be available on the market:
P SERIES: based on polyester resins containing recycled materials;
R SERIES: based on polyester resins with part of the components deriving from renewable sources;
PLUS SERIES: based on polyester resins containing a combination of recycled raw materials and with part of the components deriving from renewable sources. Some of these powder coatings are available with the option of a low curing temperature, to further reduce the environmental impact by reducing energy consumption.
Green Oasis series P
Green Oasis series P uses recycled PET-based components in its production cycle. Recycled PET
(rPET or recycled polyester) is a material obtained from the recycling of waste materials. It comes mostly from the recycling of PET bottles and, to a lesser extent, from industrial polyester or clothing waste.
Looking forward to a truly functioning circular economy, ST Powder Coatings has developed a solid and reliable process to produce powder coatings starting from this recycled polymer, maintaining their very high quality unchanged.
Green Oasis series R
Green Oasis series R uses innovative polyester resins synthesised not only with traditional field gas but, above all, with ecological bio-gas: it means that the sources of the essential raw material to produce the powder coatings is food, agricultural and forestry waste. In this way, the unwanted is transformed into a high-quality raw material. High quality that can be found unchanged in the new range of powder coatings.
Green Oasis series PLUS
Green Oasis series PLUS combines the advantages of the R and P series in a single solution. The PLUS series brings the content of raw materials deriving from renewable and recycled sources to a maximum, offering the best contribution in reducing the ecological footprint.
Edited by Kenosistec
Srl
Casarile (Milan), Italy antonio.angolemme@kenosistec.it
PVD technology takes a front row seat on the stage of design industry finishes with its exceptional aesthetic, functional and sustainable properties. Kenosistec provides designers with the opportunity to create distinctive, durable, and environmentally friendly products through its ability to customise PVD systems and meet specific customer requirements.
Physical Vapour Deposition (PVD) is a biocompatible surface engineering technique that allows depositing thin layers of material on various substrates such as metal and alloys, plastics, glass, ceramics, polymers, and semiconductor materials. PVD forms coatings with specific properties that improve the aesthetic and functional characteristics of products, including resistance to abrasion and thermal shock, thus lengthening their service life. In the design sector, where aesthetics and functionality must always go hand in hand, PVD stands out as a key resource offering almost unlimited creative
possibilities. Thanks to its versatility, this technology has numerous applications, from taps and fittings to furnishing accessories, from jewellery and cutlery to watchmaking and packaging.
Kenosistec Srl has developed advanced solutions to meet the needs of the design market, contributing to the increasingly widespread adoption of PVD. “In this field, Physical Vapour Deposition technologies open up new possibilities for creating customised works with the most diverse finishes and colours. This coating process is particularly appreciated for its adaptability: PVD finishes can be deposited on a wide range of
different substrates, unlike other deposition methods. That makes them an optimal choice for anyone seeking versatility, quality, and precision,” explains Antonio Angolemme, Head of Sales at Kenosistec.
The benefits of PVD: high finishing quality
One of the main reasons for the increasing use of PVD in the design sector is the exceptional quality of the finishes obtained. PVD coatings are resistant to scratches, wear, and corrosion, making the treated products durable even in environments such as bathrooms, where contact with water and chemicals can deteriorate the surfaces of taps and fittings. Moreover, this coating technique allows applying a wide range of colours, enabling designers and architects to follow current market trends. “Gold, bronze, black, and chocolate brown are currently very popular in the furniture industry, but the colour possibilities are almost endless. That makes PVD a preferred choice for distinctive, customised solutions. Thanks to this technology, parts can be produced with ad hoc designed colours, which is ideal for objects with an exclusive character,” says Angolemme. “PVD finishes are glossy and uniform and give every product a refined, high-end appearance.”
An environmentally sustainable solution
In addition to its aesthetic and functional advantages, PVD also stands out for its reduced environmental impact. Unlike other coating processes that may generate toxic waste or require the use of polluting chemicals, this is considered ‘green and clean’ as it does not use solvents, does not release harmful substances at the end of the cycle, and allows for deposition even at low temperatures, helping reduce energy consumption and greenhouse gas emissions. Precise thickness control also minimises the consumption of coating material, contributing to greater production efficiency. Finally, thanks to the long service life of PVD coatings, products finished with this technology ultimately need fewer replacements, thus reducing waste and resource consumption over time. This sustainable approach complies with the European REACH and RoHS regulations, making PVD a safe and responsible choice for companies that want to reduce their environmental impact.
innovation and leadership in the
Founded in 2005, Kenosistec has become a leader in the Italian technology landscape by specialising in the production of customised PVD systems. Belonging to the Angelantoni Industrie Group, this company has consolidated its position thanks to its ability to offer tailor-made solutions for sectors ranging from eyewear and automotive to architecture and furniture accessories. “It is precisely in the design and furniture industry that Kenosistec plays a critical role thanks to the versatility of PVD, which is also widely used in the production of handles, furniture feet, sinks, mixers, appliances, taps and fittings, showers, accessories such as towel rails, and lighting systems,” states Angolemme.
IT‘S THE PROCESS THAT BECOMES YOUR SOLUTION.
We supply you with individualized finishing lines.
“Our Hi.P.Po. and CHROME+ technological innovations have been driving this evolution, offering solutions that not only meet current market needs but are also ready to respond to future challenges.”
The contribution of the Hi.P.Po technology
One of Kenosistec’s most significant innovations to support this industry is the Hi.P.Po. (High Productive Powered Sputtering Cathode) technology, consisting of a next-generation sputtering source designed for large-scale production. Compared to conventional planar cathodes, Hi.P.Po. ensures a 10 times higher deposition rate, greater consistency, and reduced energy consumption by more than a third. It also allows materials such as nitrides and carbides to be deposited, offering a wide range of colours and finishes to meet all the demands of today’s design world.
CHROME+: chrome coating on plastic
CHROME+ is another example of Kenosistec’s innovation capacity. This unique, patented two-layer technology allows applying chrome coatings on plastic without galvanic processes. The resulting glossy and satin finishes meet the rigorous standards of the automotive industry but can also be used in fields such as home appliances and furniture accessories.
Kenosistec's Casarile facilities: a dual -purpose in-house Coating Service
After years of developing PVD finishes to support our partners and help them remain competitive, we have expanded our services to offer PVD treatments directly to the industry. However, our primary goal remains to educate the market and promote PVD as a key player in surface finishing. “We are working hand in hand with an industry willing to innovate, develop, or expand its finishing solutions. Our Coating Center will also co-develop new solutions, introduce new products, reduce time to market, and everything that the industry needs to deepen and enhance its skills in PVD." PVD technology is constantly expanding, from new finishes for unexplored markets to new solutions, e.g. Hipims, for meeting growing production requirements. However, the process adopted is what makes the difference. Through process study, it is possible to achieve perfect efficiency and repeatability and lend special properties to the substrate.
Kenosistec offers assistance and guidance for customers approaching this technology, contributing to establishing a method. In particular, Cleaning Coating Testing is the turnkey service through which this company can take care of the preliminary study to verify the feasibility of a process, design and produce a PVD system, and finally, install and commission the machine, also guaranteeing assistance throughout the plant’s life cycle.
Kenosistec can also be considered the ideal solution for customers wanting to take their first steps into the world of PVD but do not have the possibility of buying a system. It offers a flexible and highly specialised contract coating service ensuring excellent quality and technical support at every stage. That allows finishing one’s components with PVD to test the reaction of the market before acquiring a plant, but it is also suitable for companies that already have one and are facing sudden or temporary production peaks. PVD is going to play a vital role in the future of design, and Kenosistec is at the forefront of this journey, offering services and technologies that enable the creation of beautiful, durable, and environmentally friendly products. With the expansion of PVD applications and the continuous development of new solutions, the possibilities for the design industry are almost endless – and Kenosistec is ready to make the most of them.
In the field of metal architecture, each project requires a unique solution. However, a shared key prerequisite is the quality of the parts and structures that make it up. This is substantially assessed in terms of outdoor durability and corrosion and weathering resistance, both guaranteed by their finishes. Luxe Perfil, the European leader in aluminium coil coating, has chosen a very innovative, unique product on the market, PrimeCoat® A109 from DN Chemicals, to meet the quality specifications of its architectural products.
The industry of aluminium for architectural use is lively and dynamic, characterised by ever-new and more complex requirements in terms of design and performance. Responding promptly to these needs by anticipating them is the speciality of Luxe Perfil, an Italian-Spanish aluminium specialist that produces profiles, doors, bioclimatic pergolas, roller shutters, and insect screens for commercial and private building projects in more than 40 countries worldwide.
It is well known that finishes are an integral part of the quality of an architectural structure because they are its first barrier, its first protection against everything that surrounds and affects it: atmospheric and environmental agents, mechanical and chemical stresses, cleaning cycles, human impact. It is also well known that paint – any paint – alone is not enough to ensure excellence in performance: it always takes a team effort between pre-treatment and coating.
What cannot be done by the latter due to chemical or application limitations is taken care of by the former, with the joint objective of complying with the project’s specifications. That was also true for Luxe Perfil (Chiva, Valencia, Spain) and Alucofer (Robledo, Albacete, Spain), belonging to the same Group specialising in the production, finishing, and transformation of aluminium. Their collaboration with DN Chemicals (Milan, Italy) –already the supplier of the Group’s third subsidiary, the Italian firm Luxe Coat – for the experimentation and then the industrialisation of a highly innovative no-rinse, chrome-free conversion product enabled Luxe Perfil to achieve a corrosion resistance degree never before reached on its liquid and powder-coated coils. The company also managed to reduce its production times and costs, as DN Chemicals’s product even allows skipping the application phase of a conventional primer.
The experts in the impossible With 30 years of experience, 320 employees, 130,000 m2 of facilities in Spain and Italy, and a production capacity of 50,000 tonnes per year of coated aluminium coils and 10,000 tonnes of extruded and coated profiles, Luxe Perfil describes itself as an ‘expert in the impossible’. “The Luxe Perfil Group consists of three companies specialising in aluminium processing, two of which are located in Spain, Luxe Perfil and Alucofer, and one in Italy (L’Aquila), Luxe Coat,” says Giuseppe Procopi, the Group’s General Manager. “Our production activities began almost 30 years ago with the manufacture of customised roller shutters. Then, based on our owner’s idea to respond to evolving market trends, other production processes related to the aluminium industry have been gradually integrated over the years. With 4 coil coating lines (3 of which apply liquid products and 1 liquid and powder products), 4 cutting lines, a foundry, 1 extrusion press, 15 roll forming lines for roller shutters and 2 for shutter boxes, 2 horizontal and 1 vertical powder coating plants for extrusions up to 8.5 m, 1 rolling mill, 2 continuous casting lines, and 1 tension levelling system, the Luxe Perfil Group has now vertically integrated the entire aluminium supply chain, reducing production times and increasing quality.
The coil coating line treating coils up to a width of 1550 mm and a thickness of 3.05 mm with liquid and powder finishes.
One of the two chemcoaters applying the PrimeCoat® A109 no-rinse chrome-free product on Luxe Perfil’s coils.
The liquid coil coating head.
“The first coil coating line was installed here in Valencia to cope with our growing consumption of coated coils. Today, we have three coil coating lines at the Chiva plant. Later, with the significant increase in demand for customised roller shutters, it was decided to invest in extrusions as well because no supplier could keep up with our demand. Alucofer was founded in Robledo 20 years ago. There, we installed our first extrusion press and a horizontal coating line. A few years ago, we added a vertical coating line, the only one in Europe to coat lengths of over 8.5 m, and a liquid coil coating line for small batches (60 cm in width), which were rapidly accounting for an increasing percentage of the total volume of shutters we produced. At Alucofer, we also started the production of PVC profiles with 6 extrusion lines, as well as a foundry for extruding billets and die-
casting accessories, which are then powder-coated on one of the horizontal lines. A sublimation line completes the company’s equipment for finishing our extrusions.”
“The aim of these technological development efforts and the expansion of our production area was to offer an ever-increasing range of products, aiming to be sole suppliers to our customers and facilitate procurement management, especially for foreign ones. In the meantime, the shutter market evolved, specialising in the production of shading and screening elements such as mosquito nets and bioclimatic pergolas, with the latter now being among our core products. We have a diverse customer base to which we offer quick, comprehensive service and excellent technical support thanks to our solid, high-productivity structure.”
Finishing: endless possibilities for just as many performance demands
Luxe Perfil’s products have contributed to iconic architectural projects from Doha to Saransk, from Brussels to Rome and Montreal. “At Luxe Perfil, we are aware of the importance of employing the best finishes available on the market to guarantee unquestionable quality in terms of both aesthetics and outdoor performance. As we tackle projects in more than 40 countries worldwide, the environments in which our products are installed are the most diverse. With regard to the choice of finishes, in the Building sector, it is normally the architects who give precise indications. On many occasions, based on our many years of experience, we have developed colours and effects ourselves, consistently improving our products’ aesthetic impact. Our in-house R&D activities are always aimed at meeting and anticipating the needs we perceive in the market,” comments Procopi. “In the Coil sector, we are among the few in Europe able to coat coils up to a width of 1,550 mm and a thickness of 3.05 mm with liquid and powder finishes. We offer finishes in all RAL colours with different effects, textures, and gloss levels.”
“As I mentioned, it is of fundamental importance to continue to meet the ever-increasing performance requirements of the roller shutter and sunscreen sector: chemical resistance to cleaning products, mechanical resistance to opening and closing cycles, and corrosion, UV, and weathering resistance are the main quality measurement parameters. We should consider that roller shutters are the first exposed element outside a window and are subject to a greater risk of corrosion than the window itself, also because they can remain closed for a long time instead of being used more dynamically. Sometimes, customer demands for corrosion resistance are so high that paint suppliers are unable to meet them: in these cases, the role of the pre-treatment process we perform on our coils becomes strategic for compliance.
“We solved the problem of improving our performance degree through our collaboration with DN Chemicals, which started when we opened Luxe Coat in Italy and began doing application tests with excellent results1. After testing DN Chemicals’s products for several years and based on joint experimentation projects, we decided to also rely on them for Luxe Perfil. Their pre-treatment chemicals, which we use on all our coil lines at both Luxe Perfil and Alucofer, as well as Luxe Coat, guarantee high performance especially in terms of corrosion resistance, which other suppliers cannot provide.”
“We provide Luxe Coat with a tried and tested chromefree pre-treatment cycle,” says André Bernasconi, the General Manager of DN Chemicals. “The innovative aspect lies in the fact that Luxe Coat has installed the world’s first atomisation system for pre-treating high-thickness (1.2 to 3 mm) coils for architectural use, particularly for curtain walls. At Luxe Perfil and Alucofer, on the other hand, the process is carried out with chemcoaters (special machines applying no-rinse products as if they were coatings), which applies an innovative product formulated with a special polymer that is fundamental for corrosion protection but also for giving the coated coils the flexibility required for the post-forming phase.
“The performance of PrimeCoat® A109 is similar to that of a chrome-free product, although it does not have any other metal in its formulation, i.e. 1,000 to 1,500 hours in acetic salt fog depending on the type of aluminium alloy treated. A further advantage is that the application of a conventional primer can be avoided, resulting in obvious cost savings and improved production speed.”
“Luxe Perfil uses DenClean 418 AS for alkaline degreasing and the DenAcid 774 deoxidiser for etching. Alucofer’s coil treatment line employs the same alkaline degreaser and the same conversion product, PrimeCoat® A109, but does not perform the acid neutralisation phase,” adds Gherardo Minotti, Business Development Specialist at DN Chemicals. “Both sites have also installed a water purification system developed in cooperation with us. When we approached Luxe Perfil after a long collaboration with Luxe Coat, we identified the need to modernise its whole pre-treatment phase, so we presented ourselves as a supplier of both tried and tested and innovative products.
“The electrochemical analysis of the performance of PrimeCoat® A109 is very interesting because it demonstrates its high level of protection from the electrochemical point of view, i.e. against corrosion, and its very low water permeability, ideal for preventing the corrosion of the substrate once it is exposed to the weather.”
“Thanks to the integration of these products, in addition to our level of performance, we have also significantly improved our production process, which has become
more stable. We are very satisfied,” says Procopi. “We tend to change suppliers with great difficulty. Implementing DN Chemicals’ technologies at Luxe Coat was easy because it was starting from scratch; on the other hand, at Luxe Perfil, we tend to be very loyal over time unless failures on the part of the supplier itself force us to change. This was not the case with DN Chemicals: after a year of tests, they were very attentive and made it impossible for us to ignore them.”
“The conversion product was first tested on sample sheets in the laboratory, then with a half-day trial, and then with 2 one monthlong trials in 2022 and 2023. In spring 2024, we started supplying it,” summarises André Bernasconi. “It was a nice project, which took some time but was ultimately successful, which is also a source of pride for us at DN Chemicals.”
“A company may undertake a good project but end up not finding the right supplier to implement its vision. With DN Chemicals, it was about testing and implementing a product on which it was already working: we were both in the right place to develop a chemical that did not exist on the market,” concludes Giuseppe Procopi.
Bringing your surface to perfection. Verind offers painting solutions from manual to automatic application, high-quality and easy to integrate.
1 - Degreasing (6 m3, 50 °C) with Denclean 418 AS
2 - Cleaning (2 m3, room temperature)
3 - Acid etching (2 m3, room temperature) with Denacid 774
4 - Cleaning (2 m3, room temperature) with conductivity < 200 microS
5 - Cleaning (2 m3, room temperature) with conductivity < 50 microS
6 - Conversion in a chemcoater with chrome-free PrimeCoat® A109
Line speed: 40 -50 m/min
PrimeCoat® A109 is a water-bed, chrome-free pre-treatment product specifically developed to improve the metal surface’s paint adhesion and bonding characteristics. If pre-treated with it, steel coated with an alloy of aluminium and zinc features excellent and durable adhesion for coil coating paints and good adhesive properties. The adhesive properties of PrimeCoat® A109 were tested in combination with various one-coat coatings and primers + topcoats after exposure to wet conditions, e.g. with humidity and boiling water immersion tests. When a suitable primer + topcoat system is used, the PrimeCoat® A109 pre-treatment process ensures good corrosion resistance, comparable to a conventional no-rinse chromate pre-treatment. Its label includes no hazard pictograms.
DN Chemicals regularly monitors the quality of the process with the following tests:
• T-bend adhesion, adhesion after boiling, and impact tests
• ASTM B117 acetic salt spray corrosion resistance tests
• EIS – ACET electrochemical corrosion resistance tests.
ACET test results
( Ω*cm2)
Ω*cm2)
The Max Z and Min Z values represent the maximum and minimum impedance values recorded from the start to the end of the test. The Delta Z value represents how much the sample degraded from the start to the end of the test. A low value indicates limited degradation. This is confirmed by the Bode diagram below, showing the impedance values recorded during the test: there are 7 overlapping straight lines, which corresponds to very low degradation.
The water uptake value provides an indication of the hydrophobic properties of the coating: in this case, the value is low and, therefore, the coating has very good hydrophobic properties (see image).
Water treatment
The products supplied for the purification plant are as follows:
• Denflok 7315, primary coagulant
• Denflok 7504, polyelectrolyte
• Dencide 7702, antibacterial sanitiser
• Dencal 6304 OS, osmosis membrane treatment product.
Ilaria Paolomelo ipcm®
Quality and aesthetics are determining factors in the world of luxury furniture and lighting. Sirio Galv, which has always been synonymous with excellence in galvanic treatment and painting, recently took a significant step towards raising its quality standards with a new liquid coating system designed and installed by Verona Impianti 2002. In addition to providing excellent finishes, the new line played a key role in supporting Sirio Galv’s environmental policy oriented towards reduced consumption and energy efficiency.
In the heart of Italy’s Veneto region lies an area internationally renowned for its manufacturing tradition in the lighting industry. This industrial district, promoted by the municipality of Piombino Dese (Padua), was formally established in 2008 as the Distretto Veneto dei Sistemi per l’Illuminazione – now Luci in Veneto – to gather a significant number of companies in the sector. Since the second half of the 2000s, it has established itself as a centre of excellence capable of integrating the entire lighting technology supply chain, from the production and assembly of lighting equipment to the marketing of end products. A few kilometres from Piombino Dese, more precisely in Camposampiero (Padua), is the headquarters of Sirio Galv, a company specialising in the galvanic treatment and industrial coating of highend furniture and design accessories. Founded by Claudio Vaccarin in 1996, it has established itself as a strategic partner for companies in the
lighting and furnishing sector thanks to high-quality products and stateof-the-art technologies. One of its most recent investments was the installation of a new liquid coating plant, designed by Verona Impianti 2002 (Colognola ai Colli, Verona), to meet the challenges of an everchanging market with greater efficiency while maintaining high quality and environmental sustainability standards.
Sirio Galv: artisanal excellence and technological innovation
Sirio Galv is the brainchild of Claudio Vaccarin, an entrepreneur who began his career in the field of galvanic treatments and quickly developed a profound knowledge of this industry. Fascinated by the precision and discipline required to produce high-quality chrome, nickel, and gold finishes, Vaccarin set up his own company twenty-
eight years ago and started offering galvanic treatments and coatings first to the lighting industry and then to the furniture one. “When the lighting sector shrank due to production relocation, Sirio Galv was able to reorganise and focus on furnishing while expanding its range with advanced technical solutions, without ever renouncing the degree of craftsmanship that sets us apart,” says Claudio Vaccarin, the company’s owner. Today, Sirio Galv stands out for its production flexibility, thanks to three highly specialised galvanic plants. Two of these are semiautomatic and designed to guarantee impeccable quality on small and medium components; the third is a manual plant machining oversized parts or applying special finishes, thus meeting even the most complex customisation requirements. With a team of more than twenty-five professionals, the company offers galvanic treatments and the highprecision application of chrome, nickel, gold, and other custom finishes, combining advanced technology and expertise for outstanding aesthetic and functional results.
“Our growth and success are the result of a constant commitment to innovation: from optimising our coating processes to adopting increasingly efficient and sustainable solutions, we have been able to seize every change in the market as an opportunity for development,” adds Vaccarin.
Sirio Galv’s production method is characterised by thorough attention to detail and extreme care for quality, which are reflected in every process step, from initial cleaning to final coating. “Every part that reaches our plant goes through a production cycle designed to guarantee the highest standards of precision and aesthetic perfection,” states Claudio Vaccarin.
The first stage – when required – is robotic cleaning to remove any imperfections and machining residues and ensure that the surfaces are ready for subsequent operations. The components are then subjected to a preparation stage prior to the galvanic treatment, which includes degreasing and ultrasonic cleaning to remove any oils, pastes, and other residues left by previous processing phases. “At this point, the components are treated with a layer of nickel, an essential base for ensuring the adhesion of the subsequently applied finishes. Depending on customer requirements, Sirio Galv uses different colours, including gold, copper, and black, guaranteeing high uniformity and durability thanks to a precisely controlled galvanic immersion cycle,” continua Vaccarin.
After the galvanic process, the parts move on to the coating stage.
“The components handled by Sirio Galv are intended for interiors and, therefore, require finishes that focus primarily on aesthetics rather than corrosion protection. The latter is guaranteed by the galvanic layer, whereas the paint product plays an essentially aesthetic role in adding beauty and uniformity to the object. In this industry, aesthetics and functionality must coexist in perfect harmony, and every component must be flawless,” emphasises Marta Vaccarin, the daughter of founder Claudio and the representative of the second generation at the company’s helm.
Trends in an evolving market
“Speaking of aesthetics, it is essential that the components are not only impeccable in terms of finishing quality but also adapted to the most varied customer requirements,” explains Marta Vaccarin. *“The trends and demands of our target sectors are constantly changing, and we need to respond to a variety of needs by offering a wide range of finishes and colours, with a catalogue of around a hundred coating products.”
Every project starts with a sampling phase during which the customer
approves a series of test results on prototypes, thus ensuring that each finish, whether glossy, semi-matte, or pigmented, meets its expectations perfectly. “Glossy chrome is currently making a remarkable comeback – a marked change from the previous decade, dominated by matte and coloured finishes,” notes Vaccarin.
The coating cycle and the new plant’s technical characteristics
In order to succeed in this competitive, high-end market, Sirio Galv chose to rely on partners of excellence, such as Verona Impianti 2002 for the construction of its new coating plant and Lechler (Como, Italy) for the supply of coating products. “The loading and unloading of components are done manually; for logistical reasons, the two areas are not located in the same place, as is usually the case in coating plants. We designed the loading area to be adjacent to the electroplating tanks, whereas the unloading one is located close to the quality control station before packaging and shipping,” explains engineer Albino Tamellin, the owner and founder of Verona Impianti 2002. After being loaded, the components are dried manually in a compressed-air blow-off phase, then taken by the monorail conveyor to the drying oven, where they
dwell for about 20 minutes, and finally, moved to a storage buffer and subjected to forced cooling. “The conveyor is also equipped with a splash guard tray, which is essential to prevent the chain lubrication oils from contaminating and soiling the hung components,” adds Tamellin. “Subsequently, the parts enter the temperature-controlled coating booth (26 °C). “Done manually by an operator with a gun supplied by Wagner (Valmadrera, Lecco, Italy), this operation is a distinctive element that gives Sirio Galv’s products a unique craftsmanship value. Since we work on small batches, individual parts, and components with complex geometry, manual application enables us to reach surface areas that are difficult to paint and achieve perfect finishes on each workpiece,” notes Claudio Vaccarin. “The number of coats applied varies according to customer requirements. Usually, for our products, we perform a wet-on-wet finishing process or, alternatively, the application of a first layer of topcoat followed by baking at 140 °C for 25 minutes and then of the same topcoat followed by oven drying.” Finally, each component is individually checked before packaging to ensure it meets the quality standards required by a high-end market that demands attention to detail and zero imperfections.
“One of the first requests we received during the design phase of the
new plant concerned sustainability and reduced consumption. We thus paid special attention to limited consumption and energy efficiency. For example, we designed an oven with a degree of thermal insulation that exceeds the drying temperature requirements of the paint products used by Sirio Galv. In addition, to ensure impeccable finishing quality, we designed a filtration system that covers the entire air recirculation area inside the oven and took measures to retain any particles or residues coming from other stations, such as the heat generator. During heating cycles, the parts of the generator that cannot be painted tend to develop small traces of oxide that could diffuse into the oven: in this plant, metal filters suitable for high temperatures ensure complete flux filtration, allowing recirculating completely clean air just like in the car body industry,” says Pietro Tamellin from Verona Impianti 2002.
Determining factors in the plant’s selection: the collaboration with Verona Impianti 2002
When Sirio Galv decided to upgrade its coating system, the choice was driven by specific requirements and the need to respond to new market challenges. Its old plant, installed in 1996 and designed to process chandelier components and small parts, was no longer adequate for the
new demands of the high-end furniture and interior design market. After more than twenty years in operation, it was outdated and unable to meet today’s requirements for efficiency and quality. To address this transition, Sirio Galv consulted some of its partners and suppliers in the industrial coating sector, asking them to recommend manufacturers of state-of-the-art coating equipment. After careful evaluation and several consultations, the company found its ideal partner in Verona Impianti 2002. This company immediately connected with Sirio Galv and understood its specific needs, thus becoming a natural choice.
“We had two main requirements: replacing our previous plant with a new generation system that was in line with our standards of consumption, emissions, and sustainability and solving a pollen pollution issue. Being located close to the countryside, we were often faced with a challenge: pollen is very light, and it tended to settle on freshly coated components. That forced us to repaint numerous parts to eliminate the defects caused by these contaminants. With the new system, we have finally solved this issue: the plant is fully pressurised, and each access point is equipped with air blades that prevent dust particles from entering,” says Vaccarin. In addition, in line with its strong commitment to sustainability and reduced consumption, Sirio Galv has been operating according to a “zero liquid discharge” philosophy since 1996. The water used in its production processes is treated internally and reused, whereas the necessary electricity is produced via a co-generator. “The coating line’s motors are controlled by inverters to optimise power consumption and maintain perfect
pressurisation balance,” indicates Tamellin. Recently, the company also installed a photovoltaic system that powers heat pumps, thus further saving on gas usage.
“Environmental sustainability is not only about reducing consumption but also VOC emissions. Despite using solvent-based liquid paints, we have always paid great attention to what we put into the atmosphere. However, we wanted to reduce our ecological footprint even further. We worked in synergy with the Verona Impianti 2002 team to achieve more sustainable results. Today, our emissions have fallen compared to the much higher values of the past,” adds Vaccarin, highlighting the success of this project.
Finally, reflecting on the installation of the new system, the owner of Sirio Galv points out: “The space we had in our factory for the installation of this plant was very narrow. The galvanic process tanks limited us in terms of width and the building’s walls in terms of length. However, despite these difficulties, we managed to fit all the necessary technology into the available area, and the plant was delivered to us very quickly during the summer period, which allowed us not to delay the delivery of orders. We are extremely satisfied with the collaboration with the Verona Impianti 2002 team and with the system they provided. It is reliable and meets all our needs. We have never had a breakdown, and this has enabled us to continue with our production without any interruption.”
Samples of some of the available finishes.
Sirio Galv specialises in the galvanic treatment and industrial coating of high-end furniture and design accessories.
Jesús Galindo ALSAN - Álvarez Schaer - Paterna (Valencia), Spain marketing@alsan.es
The purification of discharge water constitutes a key element in powder coating and anodising production lines, and its proper functioning is essential to ensure that the final waste satisfactorily comply with the legislation. Compliance with increasingly restrictive discharge parameters, together with the growing scarcity of water, has led Alsan to conduct studies on the reutilization of this valuable resource.
In a conventional depuration process, such as ALSAN’s AludePure system, the precipitation of sulphates, fluorides, aluminium, and other metals is achieved through the use of lime and HCl, which also act as pH regulators. However, some discharge parameters, such as conductivity and sulphate concentration, turn out to be, in some cases, difficult to meet through this classical treatment. The company aimed to enhance the precipitation or removal of contaminants, ensuring that the resulting waters exhibit very low conductivity and low contaminant
concentration. These waters not only fulfil discharge limits but are also suitable for reuse, thereby reducing overall consumption.
EcodePure is the new purifying process developed by ALSAN, and can be easily implemented on an already existing AludePure systems (Figs. 1-3). The main difference lies in the employment of specially developed additives, specifically designed to precipitate sulphates, aluminium and fluorides to values much lower than those usually achieved by conventional processes.
As we will explain further, the diagram for the treatment and reuse of the wastewater varies depending on the type of production line, with separate purification of acidic and alkaline effluents being crucial. Alkaline effluents will follow the standard treatment process which is based on the neutralization and the precipitation of the dissolved aluminium as alumina. On the other hand, the acidic effluent will be subjected to the new purification process effectively reducing the contaminant concentrations below the most demanding discharge limits. It is important to highlight that the entire fluoride and sulphate content is found in the acid effluent. These three parameters: sulphates, fluorides together with conductivity, turn out to be the most difficult to meet currently with standard water treatment processes based on the precipitation of pollutants with lime (Table 1).
Depending on the treatment process, this is, an acid coating pretreatment, a dual pretreatment or an anodising line, the purifying diagram and the percentage of recycled water will be different. ALSAN presents the key solution for powder coating lines through the EcodePure PC system, and for the treatment of anodising wastewaters through the EcodePure AN system. A brief description of the development and operation of each of these solutions follows.
Figures 2 and 3 - Some equipment from the
EcodePure PC: acid pretreatment powder coating line
This line constitutes the easiest scenario since all the generated wastewater is entirely acid, so that there is no need for effluent separation before treatment. This acidic effluent is subjected to the new water treatment process, EcodePure PC, where in a first step it is neutralized with lime and the additives for the precipitation of sulphates and fluorides. Once the precipitate has been separated, the effluent is neutralized with CO2 and filtered, rendering it ready to cover the needs of water in the line rinses. In this case, 100 % of the water employed in the line is reused.
The use of CO2 as reagent in the neutralization stage is essential since it allows to diminish the pH and reduce the calcium content. The use of HCl, which is the most common reagent for pH regulation in water treatment plants, is strongly discouraged if there is a wish to reuse the water, since it would introduce chlorides into the process water, leading to pits of corrosion in the material. A scheme of the water treatment process is indicated in Fig. 4
ALSAN tested the EcodePure PC system with a sample of one of its clients that uses its acid attack product, ALCID 2005RH, and its chrome-free product, Ecoal® 20AH1, in their production line. The wastewater effluent produced in the line is therefore exclusively acid. After undergoing the EcodePure process and subsequent neutralization, the resulting water exhibits a conductivity, sulphate and fluoride concentration low enough to be reused in the process. The parameters of this water before and after treatment are shown in Table 2
In this type of line, effluents will be separated into acidic and alkaline streams and will be treated independently. On one hand, acidic effluents will be treated as explained in the previous case, resulting in a stream with low conductivity and minimal pollutant content. This water, which after the EcodePure PC process possesses an alkaline pH, can be reused in alkaline rinses of the line without needing pH regulation, or it can be neutralized and sent to either acid or alkaline
rinses. The employment of CO2 will be studied for each case. On the other hand, alkaline effluents will be treated in the conventional way to precipitate aluminium and adjust the pH within the range of the discharge standards. In the case of the powder coating line, alkaline effluents originate from rinses that are only slightly concentrated and have low amounts of sulphates and fluorides, therefore, the fulfilling of the discharge parameters does not pose a problem. A schematic representation of the EcodePure PC system for dual pretreatment lines is presented in Fig. 5
The utilization of EcodePure PC in your pretreatment lines allows the reuse of from 50% to 100% of the current water consumption, providing a necessary solution aligned with the protection of our environment.
Like at dual pretreatment coating lines, the separation of acidic and alkaline effluents if crucial at the anodising lines. However, in this case, alkaline effluents generally represent a lower percentage of the total volume of wastewaters, around 20-30% depending on the line. Consequently, by subjecting the acidic wastewaters to the EcodePure AN process, and after neutralization, the volume of recycled water will reach the 65-75% of the water of the process (Fig. 6).
The alkaline effluent, typically highly concentrated, may exhibit a high conductivity effluent even after conventional treatment, so in these cases reverse osmosis equipment will be necessary for the already treated alkaline effluent. It is noteworthy that this treated alkaline effluent mainly contains sodium chloride, so that it is suitable for the reverse osmosis system. The resulting osmotised water can be reintroduced into the production line, thereby increasing the proportion of recycled water to 90% and leaving a rejection from the osmosis, corresponding to 10% of the total water used, which can be managed or evaporated, reaching zero discharge in both cases. In conclusion, the new EcodePure system allows, thanks to the use of specially designed additives, the exhaustive precipitation of metals, sulphates and fluorides to values lower than those established in the discharge limits and the reuse of between 50 and 90% of the water. A recommended solution for all those companies that decide to take a step forward in their commitment to environmental management and care for the natural resources of our planet.
The ItalMesh team engineered and executed the external cladding of the new Burger King restaurant in Rovereto (Italy), opened in 2023.
ItalMesh is an Italian company exceptionally proficient in the realisation of architectural projects using expanded metal mesh and perforated panels, which is well-established both nationally and internationally. ItalMesh products can be used to clad external architectural elements such as façades, sunshades, balustrades, and fences, as well as for interior applications such as false ceilings and other design elements. Its projects are versatile and consistently innovative through a seamless integration of cutting-edge technology, premium materials, and exceptional craftsmanship combined with limitless possibilities in shapes and colours, achieving an ideal balance between aesthetics and functionality.
An example of this is the cladding designed and installed for a new Burger King restaurant, part of the renowned American fast-food chain. Located in Rovereto, in the autonomous province of Trento, it is one of the 250 restaurants distributed across Italy. This project, developed in collaboration with StudioA22 Architettura e Design, also based in Rovereto, utilised approximately 1,250 m² of perforated aluminium sheet, painted with an exceptionally long-lasting white powder coating. Depending on the reflection of sunlight and the observer’s position, the panels create a sense of depth and movement in the structure. ItalMesh also designed all red inserts and profiles, which provide a striking contrast to the glossy white walls. The outcome is a subtle structure that integrates seamlessly into the Trentino landscape while featuring an unmistakable profile that immediately connects it to American fast food, lending tone and character to the exterior.
The company, based in Montirone in the province of Brescia, offers the market over 300 models of customisable expanded metal mesh and perforated panels, produced in various materials and thicknesses. "We carry out the surface treatments of our products using non-toxic thermosetting powders with high resistance to UV rays and corrosion, or via anodic oxidation," explains Luca Baronchelli, Export Manager of ItalMesh. "These finishes offer several advantages, including the self-cleaning properties of the material and the ability to retain their functional and aesthetic characteristics
over time. They are designed not only to deliver special aesthetic effects that enhance each project, but also to provide protective coatings that ensure high durability, even under the most extreme weather conditions. ItalMesh has three state-of-the-art coating plants equipped with anthropomorphic robots, automatic colour change systems, and continuous process control.”
Characterised by a strong focus on sustainability and automation, and supported by an experienced and well-established technical team, ItalMesh guides and assists customers through every phase of a project - from concept and design to engineering, realisation, and installation. This approach has led to significant international success, with its innovative products reaching markets globally, from Canada to Australia, the United States to New Zealand, as well as some of the most demanding regions in the Middle East.
The Brescia-based company has consistently embraced environmentally sustainable technologies with minimal impact.
"Our production has always been mindful of the current challenges posed by Climate Change and the need of Nature restoration," says Baronchelli. "We recycle waste, recover raw materials, and strive to reduce energy consumption, thanks to a photovoltaic system that covers 90% of the plant's needs. We are also committed to developing products with a focus on their environmental impact." One example of this commitment is the company’s Zero Gravity Eden project (which will be explored in more depth in a future issue of this magazine, Editor's note), stemming from the belief that vertical plant technologies offer a sustainable solution for enhancing both urban and industrial environments. This innovative project involves creating expanded and painted metal mesh designed to support plant life, resulting in green walls that grow into true vertical gardens capable of covering the façades of any structure.
ItalMesh’s growth strategy is rooted in over 30 years of experience in the industry, along with the foresight to anticipate market demands with innovative, bespoke architectural solutions that combine functionality, durability, aesthetic appeal, and eco-sustainability.
For further information: www.italmesh.com
The art of powder coating meets innovation at the prestigious Institute for African Studies of the Bayreuth University (Germany).
Always at the forefront of the powder coating industry, RIPOL is committed to providing solutions that combine aesthetics and functionality with a focus on the environment. Our contribution to the Africa-related research centre of the University of Bayreuth’s Institute for African Studies (IAS) is a clear example of this, where our technology merges with innovation to create architecture that leaves the mark.
innovation
An innovative architectural project is taking shape on the university campus in Bayreuth that is destined to become a landmark for innovation and African studies. The laying of the foundation stone on 24 March 2023 marked the start of a journey towards the realisation of a state-of-the-art research centre, scheduled for completion by the end of 2024.
Sustainability, aesthetics, and technology in perfect harmony
The choice of materials was central to this project. Sustainability, aesthetics, and technology were its main pillars right from the construction phase, balancing functionality and style without compromising on the use of sophisticated materials. In particular, the centre’s façade is a harmonious combination of functional vertical
metal pillars that optimise energy efficiency and give the building a distinctive appearance.
Colour palette: a homage to the African research studies conducted in Bayreuth
The choice of colours for this façade, from vivid yellow tones to warm browns and reds (codes NCS S 1070-Y10R, NCS S 2060-Y30R, NCS S 4050-Y40R, and NCS S 4550-Y80R), was influenced by the variety of tints that are often found in African art, as well as in the logo of the Institute of African Studies. The wavy effect created with these colours on the façade adds elegance and modernity to the structure and blends perfectly with the aesthetics of the surrounding buildings.
Technical excellence in coating: the RIPOL 52L series
RIPOL’s 52L Poliestere series of smooth and matte architectural polyester coatings was selected to paint the sunscreens. This includes powder coating solutions designed to meet the performance requirements of the GSB and QUALICOAT architectural specifications. These products are formulated to withstand severe chemical and mechanical conditions, and they have successfully passed laboratory tests that have confirmed their technical properties. They are characterised by exceptional weather resistance, good salt spray and humidity resistance, and excellent colour and gloss retention.
The powder coatings used are manufactured and tested in line with ISO 9001 quality systems to ensure superior performance and batch consistency. Suitable for application on aluminium, steel, and galvanised steel, the 52L series, like all RIPOL products, is environmentally friendly. RIPOL’s powder coatings contain no solvents and do not release Volatile Organic Compounds (VOCs). Any oversprayed powder can be recovered as virgin powder using suitable equipment, with minimal waste. Disposal is easy and safe. Finally, all RIPOL products are free of heavy metals. With this project, RIPOL is proud to reaffirm its commitment to environmentally friendly innovation, offering an ideal solution for any infrastructure that strives to achieve excellence in sustainable architecture and actively contribute to building a greener future.
For further information: www.ripol.com
Dr. Timo Porsch
Managing Director of periplast GmbH & Co. KG - WuppertaL, Germany
Frank Siegel
t.porsch@periplast.de
Sales Manager for the small parts coating division of Walther Trowal GmbH & Co. KG - Haan, Germany f.siegel@walther-trowal.de
Rotamat drum coating clears the way for eco-friendly throwaway goods.
In Europe alone each year billions of plastic ice cream spoons are produced, most of which are carelessly discarded into the environment. periplast produces spoons consisting of a biodegradable granular material – developed in-house – that completely dissolves when it is exposed to moisture. To prevent this dissolution process from happening too early, the spoons receive a thin protective film in a Rotamat coater.
Currently the annual worldwide production of plastic materials amounts to more than 400 million metric tons. Around 50 % of this staggering quantity is used for packaging purposes and throwaway goods, which are only used for a limited time. Only 15 % of these items are recycled, and more than 30 % are carelessly discarded into the environment. For example, ice cream spoons are only used for about half an hour. Subsequently they become garbage … or, worse, are dumped into the
The coating in the Rotamat system ensures that the spoons dissolve only after they have been used. periplast supplies items for one–time use in different colors.
environment. Each spoon weighs just a few grams, but in Germany alone 360 million ice cream spoons are used each year, whereas in Europe this number reaches several billion. For this reason, periplast searched for a solution that allows the cost-efficient production of such spoons which simply dissolve after they have been used.
The solution is the granular material “periamyl“, developed by periplast, and for which a patent application is pending. This is a 100 % natural polymer consisting of corn starch – a naturally growing raw material. When it reaches the environment, it degrades under practically any condition. It can be reproduced naturally at very reasonable costs. periplast produces the granules at its Wuppertal location. Another significant benefit of periamyl is that it can be easily shaped under heat. This allows the cost-efficient production of items for one–time use with standard injection moulding equipment – thus creating ideal conditions for the economic production of throwaway goods on an industrial level. For example, it allows the production of throwaway cutlery pieces or golf tees with a plastic look, but which consist of a 100% naturally growing material that is available in abundance. Above all, the material degrades very quickly, even in salt water.
The first industrial-level application for this material are ice cream spoons. Once they are thrown away, the bacteria in the environment
ensure that they are completely dissolved within a time period of about 20 weeks. However, to make sure that the spoons are not dissolving during use, for example, the consumption of ice cream, they must be coated with a waterproof material. At this point Walther Trowal became involved: For many years periplast has been using Trowal mass finishing equipment for surface finishing of metal components. Through this connection the two partners came to talk about the coating issue for the ice cream spoons … for Walther Trowal a brand-new application for its Rotamat coating equipment.
Based on processing trials in the TTC Test & Training Center at Walther Trowal in Haan a coating material was developed consisting of a multicomponent ceramic solution. This forms a silicon dioxide structure on the surface of the spoons, which is not only stable for a long time but is also tasteless. The standard version of the Rotamat R 80 coater immediately met all the periplast requirements so that no technical modifications were needed.
The thickness of the ceramic coating is such that it remains absolutely stable during use. However, after a few hours the coating is infiltrated by water, for example, through the edges of the spoon. This causes the base material to expand so that the coating, basically consisting of sand, is split off: The dissolution process begins!
It was highly beneficial for the project that the coating aims were achieved with a standard machine from Walther Trowal that required
no technical modifications. At the moment periplast is using the R 80 Rotamat coater for processing batches consisting of around 4,000 spoons. The weight of this batch size allows the manual loading/unloading of the drum without undue stress for the operator.
The actual coating operation runs fully automatically. The people who operate the injection moulding machines are also loading/ unloading the Rotamat coater and monitor the entire process. This means that no additional personnel was required for the coating operation. The machine was commissioned in 2023 and has been working with no problems whatsoever. Maintenance work is limited to the occasional cleaning of the drum and the periodic exchange of the air filters.
Besides ice cream spoons complete throwaway cutlery sets made from periamyl are now also available. During the introduction phase these are supplied in lot sizes of 10,000 pieces. Like ice cream spoons, they also receive a protective ceramic film in the Rotamat coater. Besides their ecological compatibility and sustainability, they offer the additional benefit that the ceramic coating and resulting sharp edges easily allow cutting a steak.
Another item with a huge market potential are golf tees. In Europe alone every year around 1.4 billion pieces are used and thrown away. If only 10 % of the plastic tees are discharged into the environment, over just a few decades huge amounts of plastic will contaminate the soil of golf courses. On the other hand, tees made from periamyl will have dissolved quickly.
The Rotamat system represents an economical solution for coating mass-produced small parts, such as O-rings, handles, springs and screws. It allows the treatment of a broad spectrum of parts made from metal, wood, rubber and all kinds of plastic materials. This includes parts for the automobile and cosmetic industry, components for writing utensils, toys, parts for the textile industry as well as seals and attenuators (dampening elements). The coating materials can be water- as well as solvent-based.
Rotamat systems are used for decorative coatings with numerous water- and solvent-based ornamental and functional lacquers. But they are also employed for coating with anti-friction lacquers, bonding agents, corrosion protection materials or insulation lacquers.
In Rotamat systems batches of small parts are coated in a rotating, closed spraying chamber (drum). Automatic spray guns are evenly applying the coating material onto the work pieces, which
If exposed to water, after six weeks the spoons are nearly completely dissolved.
are continuously tumbling over each other. This results in precisely coated surfaces with an even coating thickness and an excellent life expectancy of the applied coating material.
Even geometrically complex or very delicate parts are discharged from the machine with a highly homogeneous coating, completely dry and without sticking to each other. After leaving the Rotamat the work pieces can be immediately processed in downstream manufacturing or assembly operations.
The coating process runs fully automatically. The operator must only load new batches of raw parts and unload the batches with finished parts. The costly and time-consuming placement of the parts on special racks – required with conventional coating systems – is completely eliminated.
Since 1978 the periplast GmbH & Co. KG company in Wuppertal (Germany) has specialized in the production of highly precise injection moulded plastic components. Ever since it was founded, the familyowned mid-size company produces reels for yarns and wire. A few years ago a second manufacturing location was established in Romania to better serve the customers in this country.
Since 2010 – at its Wuppertal headquarters – periplast has been developing products from bio plastics that can be produced without the need for any fossil materials and which are quickly bio-degradable. The managing director, Dr. Timo Porsch, graduated in Chemistry and has been working for the company since 2015.
Rotoli, pannelli e celle in fibra di vetro
Celle filtranti per alte temperature
Rotoli e pannelli in fibra sintetica
Accumulatore vernice “Columbus”
Filtri “Andreae”
Cartucce filtranti
Filtri assoluti
Applicazioni speciali
Rolls, panels and cells of glass fiber
Filtering cells for high temperatures
Rolls and panels of synthetic fiber
Paint accumulator “Columbus” “Andreae” filters
Filtering cartridges
Absolute filters
Special application
If exposed to soil, discarded golf tees are completely dissolved after just a few weeks.
Walther Trowal - Surface finishing technologies from the inventor of the “Trowalizing” process Since 1931 Walther Trowal has been developing and producing systems for the refinement of surfaces. Initially focusing exclusively on mass finishing – the term “Trowalizing” originated from the company’s cable address “Trommel Walther” – Walther Trowal has continuously expanded its product portfolio. Over time the company has developed a broad range of machinery and systems for mass finishing, shot blasting and coating of mass-produced small components. With the invention of new systems like, for example, drag finishing and the development of special finishing methods for 3D printed components, the company has proven its innovative capabilities again and again. Walther Trowal develops and implements complete surface treatment solutions that can be seamlessly integrated into linked production systems existing at the customers. This includes the entire process technology, perfectly adapted to the specific surface finishing requirements of the work pieces: Equipment and the respective consumables always complement each other in a perfect manner. Each individual work piece and each manufacturing process must meet special technical requirements. That is why the experienced process engineers in our test lab, in close cooperation with the
customers, develop the optimal process technology for the finishing task at hand. The result: Work piece surfaces that meet exactly the required specifications…with short processing times and a high degree of consistent, repeatable results. Walther Trowal is one of the few manufacturers who develops and produces all machines and mass finishing consumables in-house, including ceramic and plastic grinding and polishing media as well as compounds.
The company’s equipment range also includes all kinds of peripheral equipment for handling the work pieces like lift and tip loaders, conveyor belts and roller conveyors, in addition, special driers for mass finishing applications and, last-but-not-least, systems for cleaning and recycling of the process water.
With its exchange program for wear items like work bowls, which are part of a continuous recycling program, Walther Trowal conserves valuable resources and, thus, makes a significant contribution towards sustainability in the field of industrial production. Quick technical support and the global repair and maintenance service ensure high uptimes for our equipment.
Walther Trowal serves customers in a wide range of different industries all over the world, for example, automotive, aerospace, medical engineering and wind power.
The EcoPaintJet, initially introduced for overspray-free paint application in industrial vehicle painting, is now benefiting other industries. Refrigeration manufacturer PAN-DUR insulates glazing for commercial refrigeration equipment and has been using Dürr’s innovative applicator to paint glass surfaces for several months. This technology saves time and materials by eliminating the need for individual screens in the screen printing process.
We are all familiar with large refrigeration units from supermarkets: wall shelving, cabinets, or counters, behind whose glass or plastic panels a wide range of foodstuffs are stored. PAN-DUR uses enhanced safety glass (ESG) for its glass elements.
Opaque decorative stripes are applied to obscure the unsightly bonded and sealed seams at the edges of the glass and the refrigeration technology behind them. Until now, PAN-DUR used a screen printing process for this, which required a new screen or template for every color, size, or design variation.
flexibility, lower costs
The EcoPaintJet’s high edge definition paint application without overspray allows PAN-DUR to avoid the complex screen printing process, increasing flexibility and speed in production while reducing paint costs. Each contour is simply programmed and applied in the desired color to the corresponding predefined area without having to mask the glass surfaces first, eliminating the complex and costly manufacture of individual templates as well as the need to devote valuable space to storing them.
One-stop shop for the full range of process technology
Dürr not only supplied PAN-DUR with the paint applicator but also provided all process technology, from the system for extracting paint from the containers to the system for supplying it to the applicator. The installed components include the Fluid Board color dosing and color changing system, the applicator cleaner, and the EcoAUC control unit. PAN-DUR developed a multi-axis portal to mount
WATER RECOVERY
MINIMIZATION OF WASTE TO BE DISPOSED OF REUSE OF DISTILLATE
DISPOSAL COST REDUCTION
ZLD: ZERO LIQUID DISCHARGE
the EcoPaintJet’s swiveling and height-adjustable application head seamlessly integrating the process technology. “We linked the Dürr process technology with our system’s interfaces. The implementation couldn’t have gone any more smoothly,” explains Jens Verhoef, Head of Development of Electrical and Automation Technology at PAN-DUR. The biggest challenge was finding the right paint for use on glass surfaces. Specialist paint company Votteler, a long-standing partner of PAN-DUR, was also involved in the development. Project manager Uwe Schmidt explains: “Painting glass surfaces is extremely challenging. You need specially developed paints whose rheological properties, coverage, and particle distribution are perfectly tailored to the system. This paint system can also be used on other substrates. So, we needed a few practice rounds until we found the right paint.”
Other industrial applications are also possible for the EcoPaintJet, for example, in the timber industry, in window or kitchen building, and in the field of painting railway vehicles. “There is potential everywhere that straight stripes are applied to flat surfaces and that type of painting still requires masking right now. We’re getting many inquiries from different industries,” says Fabian Schilt, Head of the European Industrial Sales Team at Dürr. An additional advantage that makes the whole system attractive for other uses is that all components are ready to integrate into existing production systems.
For further information: www.durr.com
Edited by NOF METAL COATINGS EUROPE SA Creil, France inforfr@nofmetalcoatings.eu
NOF Metal Coatings unveils PFAS-free topcoat range.
PFAS, or poly- (or per-) fluoroalkyl substances, widely used in different industrial sectors are now coming under increasing scrutiny due to their long-lasting presence in the environment. A possible European ban on PFASs based on REACh, might come into force as early as 2027 for specific industrial segments.
Apart from PTFE, a fluoropolymer currently classified as a “polymer
of low concern” by the Organization for Economic Co-operation and Development (OECD), NOF Metal Coatings Group does not use any other PFAS in its products.
Regardless of potential restrictions imposed by environmental authorities on PTFE, the company has taken this new regulation as an opportunity to develop a new PFAS-free topcoat range generation with worldwide availability.
The ambitious objectives of these developments were to be able to offer a new range of more environmentally friendly products, while guaranteeing the same tribological performance as current NOF Metal Coatings Group’s PLUS® range, the most popular topcoat range:
PLUS® XL 2 Silver: COF 0.06 – 0.09 (ISO 16047)
PLUS® VLh 2 Silver: COF 0.09 – 0.14 (ISO 16047)
PLUS® ML 2 Silver: COF 0.10 – 0.16 (ISO 16047).
Applied on top of NOF Metal Coatings Group's GEOMET® waterborne zinc flake basecoats, these PFAS-free alternatives to PLUS® XL, PLUS® VLh, and PLUS® ML meet or exceed the global OEM requirements and specifications while providing outstanding tribological properties including:
Multi-tightening and high-speed tightening
Compatibility with various mating substrates (e-coat, aluminium, zinc, and steel)
Stick slip avoidance
Behaviour in loosening tests (including at high temperature – PLUS® VLh 2 Silver and PLUS® ML 2 Silver).
From top:
PLUS® XL 2 Silver coefficient of friction according to different standards.
PLUS® VLh 2 Silver against E-coat (MBN 10544).
Total Finishing S stems is a leading designer and integrator of high-q alit and comple ind strial finishing s stems. Whether o need an in-depth process anal sis or req ire finishing eq ipment and components, o r eq ipment e ceeds e pecta ons and o r inno a on and a toma on is ind str leading.
To offer its customers the best products on the market, NOF Metal Coatings Group has taken this opportunity to enhance the aesthetics of the products in this new range by adding aluminium pigments, thus obtaining a uniform silver colour. This enhancement will improve the visual appearance of assemblies where fasteners are visible by customers. In addition to the improved aesthetics with aluminium pigments in the coating, all three new PFAS-free topcoats will include fluorescent pigments for ease of positive identification – a feature unique to NOF Metal Coatings Group topcoats.
On the road to greener future
Meanwhile, in the company’s R&D laboratories, the NOF Metal Coatings Group’s teams are continuing to work on PFAS-free coatings and GEOBLACK® systems, with the addition of black topcoats to PFAS-free PLUS® range to be ready before the end of the year.
Our 70 years experience in Surface Treatment is ready for the E-Mobility market.
Research, innovation, development.
In 70 years, our vision towards the future has never stopped. Today, Tecnofirma provides quality to the electric market which is the most evolving technology in the automotive industry. Our impregnation, cleaning and painting plants are the result of the constant commitment to offer cutting-edge solutions and products anytime, anywhere.
From an interview with Gianluca Zanardo and Cristian Sala Vernici Caldart – Bellusco (Monza e Brianza), Italy gianluca.zanardo@vernicicaldart.it; cristian.sala@vernicicaldart.it
From being a small company specialising in postcard varnishes, Vernici Caldart has gone through a journey characterised by research and innovation that has enabled it to expand worldwide and become a benchmark supplier for multiple industries.
The Italian chemical industry is one of the pillars of the country’s economy as well as a highly competitive and technologically advanced sector. Vernici Caldart operates in this context as a company specialising in the production of industrial liquid paints.
Founded over fifty years ago, it has been able to grow and innovate, thus gaining a leading position at the national and international levels. Indeed, it has evolved through the continuous search for advanced and tailor-made solutions for its customers, distinguishing itself in the
production of high-quality paints for various sectors, including eyewear, automotive, general industry, cosmetics, packaging, and metallisation. Thanks to its established knowhow and research laboratories, Vernici Caldart can also develop high-performance paints for all kinds of materials, including metal, plastic, and glass.
We interviewed its directors Gianluca Zanardo and Cristian Sala, the company’s International Sales Director and Italy Sales Director, respectively, to better understand the winning features of Vernici Caldart and its evolution.
Can you briefly describe the history of Vernici Caldart?
Gianluca Zanardo: “The company was founded in 1976 by Carlo Caldart, an entrepreneur originally from Belluno. Initially dedicated to the production of postcard paints, it was described in the as a ‘producer of special paints’. Our characteristics attracted the attention of a well-known eyewear manufacturer in the early 1980s, which was looking for a supplier of coatings for its products. When asked, ‘Do you produce eyewear paints?’ our founder replied, ‘No, but we can try’, which still represents our company’s spirit today. The history of Vernici Caldart has been, and will continue to be, characterised by constant research and development, always oriented towards meeting our customers’ needs.”
How is Vernici Caldart structured today?
GZ: “Specific areas of excellence have now developed within our company, such as our research and development and quality control laboratories. Thanks to the expertise of our technical service team, high-quality raw materials, and state-of-the-art production processes, we manufacture high-performance paint products that are used in many different markets and always combine unique aesthetics enhancing the treated surfaces with the technical characteristics required for each end use.
Cristian Sala: “In addition to our headquarters in Bellusco (Monza e Brianza, Italy), which is responsible for research and development, production, and shipping on behalf of the divisions dedicated to the eyewear and cosmetics industries, we also have a site in Pojana Maggiore (Vicenza, Italy) devoted to the industry/car refinish division. We also operate a warehouse in Apulia and one in Sicily and can count on a network of agents and resellers covering the whole Italian territory, accounting for around 75% of our annual turnover. Abroad, we are active in France, Spain, Poland, Turkey, USA, Brazil, Argentina, Thailand, and China.”
What are your target sectors?
CS: “We specialise in producing polyvalent paints and tinting systems – consisting of solvent- and water-based binders and colouring pastes – for the general industry, but we are also renowned for our products of excellence for the eyewear sector. We are the world’s leading manufacturer of paints
for plastic and metal spectacles, as well as coatings for personal protective equipment for professional and sports use, such as ski and motocross goggles and helmets made in PVC and polyurethane. Our paint products are also used in the cosmetics, beverage, fashion accessories, automotive components, lighting, and furnishing sectors. Finally, our technology is employed in the field of costume jewellery and for small accessories such as hair clips, brooches, and buckles, but also to create perfect finishes for containers, caps, flacons, and various types of bottles.”
CS: “We are also a leading manufacturer of coatings used in metallising, sputtering, and PVD processes. The latter, in particular, is an environmentally friendly technology that is expanding very rapidly. Thanks to its special characteristics, it can replace conventional galvanic coating cycles and performs very well on different substrates, from plastics such as ABS and PP to metal and glass. Another widely demanded solution is our EFT series of chrome-effect paints, which includes one-
and two-component products for direct adhesion on plastic and metal, available in a variety of colours such as grey, silver, blue, red, green, gold, and pink. This range is a valid alternative in the creation of high-quality and low-impact surfaces and visual effects, as they faithfully imitate the appearance of chrome, silver, copper, bronze, nickel, and titanium.”
What are the distinctive elements of your offer?
GZ: “We combine creative drive with the ability to interpret the latest trends on a daily basis, investing in technology that enables us to produce high-quality industrial coatings at competitive costs and with efficient customer service. We also pay the utmost attention to respecting and protecting the health of users and the environment.”
CS: “Our production’s foundations lie in the R&D of coatings in full compliance with environmental and health protection regulations. In order to meet the expectations of our customers and stakeholders, we have implemented a quality management system complying with the requirements of ISO 9001:2015. At the same time, from the very beginning, Vernici Caldart has been characterised by extreme production flexibility: we constantly develop new paints because we strive to tailor our solutions to each customer’s specific needs. In fact, we have recently expanded the space devoted to our research and development laboratories and hired new personnel to further evolve our structure at both the production and managerial levels.”
GZ: “Our site in Pojana Maggiore, in the Veneto region, is a key asset for our operational flexibility. It specialises in the production of grinding products, pastes, and tinting systems and uses modern technologies in line with Industry 4.0 principles. Recently, this plant was expanded
with the addition of new warehouses and a state-of-the-art production department to optimise the manufacturing of paint batches and improve our ability to adapt to customised volumes and requirements. That enables us to guarantee a fast service and offer tailor-made coating solutions. We also created a technical centre with a strategic training area to pass on skills to customers through specialised training sessions.”
Is your product and service portfolio’s constant expansion your key growth driver?
CS: “Simultaneously, we have developed a solid corporate structure that has allowed us to expand our sales and distribution network while also investing significantly in internal training. Our products’ reputation, fostered by word of mouth about their quality and performance, has further contributed to our growth. In 2005, our company’s turnover exceeded 5 million Euros, and since then, it has grown steadily, reaching 16 million in 2017 and 30 million in 2023, the year in which we initiated the closing with the fund Itago SGR S.p.A.”
Can you go into more detail about that acquisition and what it means for your company?
CS: “Before the entry of the Itago SGR fund, Vernici Caldart had just reached a record turnover of 30 million Euros. However, fears emerged within the Caldart family that the lack of a generational transition could lead to stagnation. Therefore, the offer from this fund represented not only a capital gain opportunity for the family but also a strategy to ensure the company’s continuity and future growth potential.
GZ: “Itago SGR expressed interest in acquiring us in early 2023, recognising our steady growth and significant potential. After an in-depth analysis of our business plans, it agreed with our mapped-out strategies and decided to co-invest in the company, supporting us in business development and structuring. With the closing finalised in May 2024, Cristian Sala and I [Gianluca Zanardo, Ed.] were appointed as directors and involved in the shareholding structure, and we initiated a growth plan entailing the expansion of our technical, administrative, and commercial staff to support this new phase of development.
CS: “In summary, the changes will only affect internal organisational aspects, as the fund recognised our managerial expertise and granted us total autonomy in operational management.”
In conclusion, what do you foresee for Vernici Caldart’s future?
CS: “We absolutely want to maintain our position as a flexible and reliable partner for the industry, able to offer innovative and high-quality solutions thanks to our wide range of products and focus on research, enabling our customers to benefit from a highly specialised service and customised coatings for every production requirement.”
GZ: “We are also committed to continuous product innovation and technological evolution, paying attention to constantly changing regulations while respecting the health of users and the environment. Other important factors for us are development, process optimisation, and know-how. In addition, customers from sectors where we are not currently fully present are also starting to turn to us because of our expertise. For example, we are seeing an increase in turnover from the automotive industry, which we would like to grow further. We are investing significantly to expand our production of water-based and UV-baking liquid coatings, responding to the growing demand for environmentally sustainable solutions. This commitment reflects our strong sensitivity to environmental issues and our proactive role in driving change towards more sustainable manufacturing processes, without ever compromising on quality and innovation.”
Adriano Antonelli
Tecno Supply - Ibix Srl, Lugo (Ravenna) – Italy
adriano.antonelli@tecnosupply.com
Today, the issue of energy savings achievable through maximum efficiency of production processes in general and of the coating department in particular is more topical than ever. In this detailed analysis, Adriano Antonelli, the sales manager of Ibix Srl – Tecno Supply, explains how carefully designing a workpiece hanging system can help reduce the energy resources consumed for the coating phase, cutting costs and increasing the lines’ efficiency.
An era of checks and balances is ending that has allowed the international economy to operate in a stable socio-economic environment until recently, providing the conditions for steady and progressive growth over the long term. Above all, Europe was able to receive raw materials such as natural gas and oil at competitive prices from Russia and North African countries. The absence of turbulence allowed for adequate supply without the need for new providers and
infrastructure. The Chinese market enabled us to buy many products as if we were in a deflationary condition. Low-value-added products such as textiles and components, for example, were relocated to exploit cheap labour and loose regulations compared to those in the EU. The US’ supremacy and international policy maintained a balance in the most unstable areas by avoiding possible military interventions. The climate issue, even if it already existed, was not as pressing in public
opinion and did not affect the lives of citizens and businesses at a regulatory level.
All this seems to have crumbled in just a few years. The Chinese market’s growth is considered weak: China’s aggressive international policy implemented through state aid has flooded the European markets with its products. Unfortunately, these are no longer only low-end products but mainly value-added goods such as solar panels and, soon, electric cars – two significant examples of how below-cost selling supported by state subsidy is destroying long-standing and strategic national industrial fabrics in Europe. American policy seems to have changed, focusing more on national borders than on international ones. The previous President’s slogan, “America First”, drew a clear dividing line with the past: no more investments to act as “the international sheriff” but projects to support the country’s own economy and domestic affairs. The withdrawal of troops from countries needing to be stabilised and, above all, from international cooperation projects are the consequences of the new administrations’ choices. Failure to desist from military interventions has resulted in the start of micro-wars in strategic areas such as Russia-Ukraine and the Middle East. Sanctions imposed on some countries and government instability have reduced the supply of vital raw materials for our economy. The climate issue and its related political choices are leading to some questionable regulations. Imposing the use of electric cars by a specific date without the possibility of developing alternative technologies to achieve the same objective, i.e. reducing emissions, could mean completely passing the ball to the Chinese market for the next few decades, which is far ahead of the Western market. This would result in
losing jobs and skills in many fields and market segments. Some warning signs are unnerving the financial markets: the risk of recession looks just around the corner. Until recently, for example, one would have predicted a soft landing for the US economy, keeping the cost of money almost stable and with a strong labour market at its peak. However, this has been disregarded by the latest surveys, which, together with the percentage reduction in American buyers’ purchasing power in the last quarter, were further signs that destabilised the stock markets.
At the same time, climate change calls for further corrective actions in our companies. Reducing emissions, making production more efficient, and starting the transition are now compelling objectives. They are demanded by regulations, markets, and customers, as well as the possibility of increasing profits. Future partners will be selected based on environmental efficiency passports.
Energy efficiency is actually a topic that goes beyond purely environmental issues, especially because it has become a significant part of European and national regulations. For example, not to be underestimated and to be studied in detail is the Transition 5.0 Plan recently launched by the Italian government. The programme aims to support investments in the green transition through tax credits. The companies that successfully reduce their production units’ energy consumption will be rewarded. In addition, investments in the selfproduction of energy from renewable sources and staff training to consolidate green knowledge and technologies will be supported. The Decree is intended to help companies in the challenges of digitalisation and sustainability, two areas in which international economic balances
are likely to be redrawn. Finally, tax credits will be granted for investments in production facilities within the Italian borders that are innovative in terms of consumption of energy resources.
Let us look at the latter aspect, starting with how a coating department can be efficient and
sustainable. The aim should be to increase density and thus fill the production line. Before describing some solutions to improve the efficiency of a coating operation, let us analyse the consumption and CO2 values of surface treatment processes, although we can only do this in a general and approximate way in the space of this article. A coating line emits CO2 due to energy consumption in the various
phases of pre-treatment, coating, baking, etc. The energy source can be electricity, a combination of electricity and gas, diesel, or LPG. The environmental footprint changes dramatically depending on this and on how such energy is produced. Coal-fired electricity, for example, produces over 30 times more CO2 emissions than hydroelectric power. Powder coatings can play a decisive role in calculating the CO2 produced by the treatment cycle, depending on the hanging density (fig. 1). Finally, hanging with hooks and other equipment can result in entirely different emission rates. The use of suitable tools, therefore, can change the line’s efficiency and, thus, its results.
So, what is the HangOn Green Effect? It is the idea that a smart hanging solution ensures maximum density, enabling to achieve the goal of filling the line and increasing the amount of parts that can be coated in one cycle. It should be considered that 80-90% of energy consumption in a coating cycle is constant, regardless of the amount of coated workpieces. That means that increasing the hanging density reduces CO2 consumption per painted product, thus reducing costs and, consequently, increasing profits.
What types of hanging systems can be implemented to bring about a green transition in a coating department? One example is our HQW D system, a 2 mm-diameter tree-shaped frame with fixed hanging points (fig. 2). The range is vast, so every customer can choose its ideal pitch. To have a compact frame (also in terms of packaging, like a box of hooks, for example), the top hanging must be done using a separate hook. This frame is designed to be used when a sudden need arises and to avoid hanging hook after hook. This is key because “chain” hanging results in longer hanging times and significantly fewer pieces than the HQW D solution. At www.hangon.it, you
can find some spreadsheets to test the savings you can achieve by entering your data, but also videos that give you an idea of how this application works. The cost per hanging point is similar to that of a single hook (the total is less than 1 Euro), so the issue of regeneration does not arise.
On the other hand, the new HQW S system (fig. 3) is complete with an upper hook oriented at 0 and 90°, and the hooks have a variable distance. This economical frame avoids improvised hanging with hooks, which can lead to a loss of density and efficiency. The 2 mmdiameter hook and the reinforcement along the frame’s entire length guarantee hanging stability.
A further solution that ensures maximum flexibility is the Flexi Frame system (fig. 4). Its core concept is a frame that can be completely disassembled and stored on a shelf. The frame consists of a T-shaped bar housing two horizontal bar holders. HQL, HCL BHL, H11B, and HQS bars can be accommodated. This system is designed to be stocked and then used in case of urgent need.
It guarantees several advantages, including as follows:
saving storage space and reducing storage problems;
lower transport costs, including one-off ones;
easy handling;
flexible and compact design;
self-locking;
customisable as required;
reduced cost.
The HQS frame (fig. 5) features metal slats for hanging elements from individual parts to profiles. The central 4 or 5-mm hook guarantees an overall frame resistance of up to 100 kg. This frame model has been recently launched on the market with various types of hooks, with which each customer can find the best configuration for its specific use. The tree can be up to 2,400 mm long, whereas the slats are 1.0 mm thick and 18 mm high. It is possible to create different slat configurations, e.g. sheared (i.e. on one side only), zigzag-shaped, or bent from 0 to 180°. This type of frame was designed to avoid using individual hooks. It is manufactured automatically, guaranteeing a low cost equal to single hooks. The new configurations made available allow the users to find the appropriate hook shape for every workpiece to be hung. Another innovation is the adapter that enables HQS frames to be extended using standard or currently available hooks. The HQS frames can be used for hanging small parts, but also workpieces with varying weights, including profiles.
The HQL bar (fig. 6) is produced fully automatically, reducing costs and eliminating the need for regeneration. Hooks with a diameter
electrostatic systems for liquid painting
electrostatic systems and spraying booths for powder coating
pneumatic systems for high-, medium-, and low-pressure painting
robot and reciprocators IR and UV drying systems
of 1 mm can be inserted into it on both sides to hang the workpieces symmetrically. For example, the 800x33 HQL bars accommodate 46 hooks over a length of 800 mm. The bars can be inserted into the HCF universal system. This makes the system modular and enables bars to be inserted according to the length of workpieces. Moreover, the HQL G6 caps guarantee perfect electrostatics. 1.5 mm-hook bars in spring steel are also available for small, heavy parts. Different configurations are available in the range, including the triple-bend one, which provides more secure anchoring for light workpieces that could be lifted into the air during pre-treatment. HQL bars for single-sided hanging are also available, in case it is necessary to hang parts only on one side and thus avoid any shading effects and other issues.
The advantages of using this bar are numerous:
time savings: it is possible to achieve a speed that is 30 times higher than with single hooks;
the hooks leave only a slight mark on the coated parts;
spring steel material;
possibility to configure the bars with special hooks;
smart packaging to reduce transport costs.
A more robust version of the HQL bar is the HQC one. It accommodates hooks with a diameter of 1.5 mm, but only on one side. Its coupling allows hooks to be inserted into a central 10 mm-diameter one. The R 58 bar holder enables the bar to be stable and easily removed, also thanks to the BH G 20 cap. The resulting frame is economical and flexible, as it is also possible to avoid filling all the levels. The hooks have a pitch of 50, 75, or 100 mm. This bar type was also designed to avoid using individual hooks, dramatically reducing the operators’ hanging time. Indeed, the availability of a ready-to-use frame eliminates the need to handle single hooks. In addition, it allows for easy offline pre-hanging. Another advantage is that it can be used for multiple hanging configurations. This bar’s production technology makes its cost similar to an individual hook’s. Therefore, there is no extra cost for purchasing frames rather than standard hooks. Finally, to make this frame even more versatile, a new metal adapter was launched that also allows H11B bars to be inserted. This way, using the same central hook, a bar can be accommodated that allows hooks up to 4 mm in diameter to be inserted, thus achieving horizontal flexibility.
The H11B bar is a punched bar inside which hooks are lodged. That ensures clean and protected contact points as well as the flexibility to change the hanging hooks whenever necessary. Standard or twin hooks can be used with the same bar, fitting between the two punches and remaining fixed. As far as twin hooks are concerned, any configuration can be chosen for even greater flexibility. This bar is highly durable (HangOn has assessed and wrote a report on the weight it can support depending on the length). Even more robust H2B, H25B, and H3B versions are also available. These bars can accommodate hooks up to 10 mm in diameter. Hooks can be welded at their ends to obtain a T-shaped frame. That guarantees part stability, whereas the system’s modularity allows hooks to be inserted where needed without
losing conductivity.
The HCL bar has housings for inserting springs or hooks made from round rods or sheet metal. Its ends are protected with silicone caps that allow easy removal and ensure conductivity. It can have single or double housings to increase hanging density. It is, therefore, extremely flexible, eliminating the need to build a different frame for every part to be coated. Special accessories can be created depending on the workpieces. Two springs can be accommodated inside the hook holder with a 4-end outlet. This bar can also be used for cataphoresis processes thanks to a cap system that protects its ends and prevents the coating product from climbing up.
The flexibility of the HCF universal frame allows using interchangeable bars and, in some cases, bars with accessories that can be inserted depending on the workpiece to
be hung. This leads to a significant reduction in the number of frames required for the different workpieces processed, in the space needed for storage, and in the possible handling problems. The universal frame can also be used for cataphoresis operations: the structure remains the same, but the bars and accessories are changed to guarantee maximum conductivity. Already welded bars with universal hooks are available in the range, allowing for minimal contact. For greater flexibility, we also offer hook holders where universal accessories and, at the top, protective caps can be inserted.
Another interesting application is the use of magnets (fig. 7). In cases where no metallic paint is applied and where it is acceptable to have an unpainted area on one of the two
has always represented customized engineering solutions for economically and ecologically sustainable paint shops for the automotive, metal and wheel industries.
Figure 8 - Besides the automatically produced and standardised HangOn range, frames, hooks, and systems can be tailor-made according to customer requirements.
faces of the metal workpiece, magnets can be employed for hanging. That makes this delicate preparatory phase quicker and trouble-free, especially when there are no holes. Our range includes different magnets depending on the weight to be supported. Silicone masking systems always cover the magnets to prevent them from getting dirty. In addition to the automatically produced and standardised HangOn range, frames, hooks, and systems can be tailor-made according to customer requirements (fig. 8). One-step hanging and masking solutions reduce time and avoid excessive product handling so that the required quality targets are achieved without neglecting hanging density and speed.
Implementing trolleys offers the possibility of managing treatment processes even better (fig. 9), having become essential to reduce process times and increase density. In-line hanging may not be efficient in terms of density when it is not possible to adequately fill the m3 available within the line handling time. Trolleys allow pre-hanging and handling the parts to be coated within the factory. HangOn’s trolleys are
Figure 9 - HangOn’s trolleys are designed to be modular and flexible and to be combined depending on the type of frame used.
designed to be modular and flexible and to be combined depending on the type of frame used. If switching among frames with different coupling devices or sizes, trolleys adapt to the various requirements to perform two functions: that of allowing pre-hanging and bringing all the frames on the coating line and that of storing unused frames in an orderly manner. Special trolleys can be designed according to the various requirements posed by the components’ characteristics.
A tool that can be useful for moving from ideas to figures and comparing different hanging systems is the new CCC calculation system on the website www.hangon.it. Business data such as the cost of powder, the number of people employed on the line, machine costs, and process times can be entered here.
The Italian distribution and technical structure of Tecno Supply - Ibix division is characterised by capillary presence throughout the country, guaranteeing reliable assistance and immediate support for all technical and commercial issues that may arise with coaters.
Lavaggio Industriale
Lavaggio di precisione
Sgrassanti interoperazionali
Miscele di tensioattivi
Protezione temporanea
Galvanica Funzionale
Zinco e leghe di zinco
Passivanti e Sigillanti
Rivestimenti resistenti all'usura
Pretrattamento
SurTec Italia Sas di Externa Holding Srl
Via Boito, 251 Tel.: +39 059 8579901
41019 Soliera (MO) E-Mail: info-it@surtec.com Italia Web:www.SurTec.com
Pretrattamento metalli alla verniciatura
Processi di conversione esenti
Cromo e Fosfati
Fosfatanti a bassa temperatura
Passivanti per acciaio zincato a caldo
Passivazione conduttiva su
Alluminio TCP
Galvanica Decorativa
Rame, Nichel e Cromo
Deposizione su plastica (POP)
Stagno e leghe di Stagno
Pretrattamento
From an interview with Alfredo Pellegrino
Defil Srl - Sesto San Giovanni (Milan), Italy
Defil Srl, a company specialising in filtration, dust collection, and air treatment solutions for civil and industrial structures since 1985, has been investing in new filter production machinery over the past two years, including a new 4.0 electronic pleating machine matched with a new longitudinal cutter. The aim was to improve its quality standards and cut processing times while reducing raw material waste.
The industry of filtration systems for the industrial coating sector is booming, fuelled by the increasing demand for sustainable solutions that optimise production efficiency and reduce environmental impact. Defil Srl (Sesto San Giovanni, Milan, Italy) stands out as a key market player in this landscape. Founded by Nicola Pellegrino in 1985, the company initially focused on distributing and marketing various filter systems, from simple mats for spray booths to complete filter units.
Over the years, it has evolved thanks to the professionalism of its staff and partners and a focus on innovation and quality, moving from being a sales company to a manufacturer of filters under both its own and its customers’ brands. “Today, we offer customised filtration solutions for a wide range of industries, including coating, automotive, pharmaceutical/ chemical, food, cosmetics, energy, and air conditioning, among the many ones served by Defil’s products. We operate in national and
international markets, with a strong presence in Spain, France, Portugal, and Russia, where we work with local distributors to expand our sales network,” explains Alfredo Pellegrino, Sales Manager at Defil.
Industry 4.0-oriented investment: the new electronic pleating machine
The integration of 4.0 technologies transforms industrial productions, making processes more efficient and customisable. Defil, with its constant focus on innovation, has recently taken a major step in this direction by equipping itself with a new electronic pleating machine linked to a cutter.
“We purchased this plant to manufacture pleated filter cartridges while improving our production flexibility and significantly reducing our processing times. This versatile system allows obtaining components with different heights and thicknesses; moreover, thanks to 4.0
technology, we can quickly change production programmes and control raw material consumption in real-time, which enables us to reduce the pleating/cutting times of our filter mats and ultimately improve our process quality, in some cases with a zero scrap rate,” illustrates Alfredo Pellegrino.
“In the past, for some specific processing phases, we relied on external partners that followed our drawings and worked exclusively with our raw materials. Now, we are trying to limit outsourcing as much as possible to cut costs and increase our competitiveness,” says Paola Pellegrino, Quality and Raw Material Purchasing Manager at Defil.
“Our company takes great care to achieve a good level of production quality and thus meet our customers’ needs and demands as best as possible. All this is possible by purchasing raw materials from European parent companies, optimising products in stock, and technically training our staff,” indicates Paola Pellegrino.
One of Defil’s main target sectors is industrial coating, which accounts for about one third of its turnover. “We have developed a range of advanced products for both powder and liquid coating processes. For powder coating, we offer a selection of cartridge or sleeve filters designed and manufactured with different filter mats and characteristics to ensure high performance and meet any customer requirement,” indicates Alfredo Pellegrino.
“For the liquid coating sector, our flagship product is the Max Paint filter, a special, high-performance, honeycomb-shaped filter mat of which Defil is the exclusive dealer for the Italian market. Other widely used products are paint accumulators, dry filters designed for manual or robotised coating booths and based on the principle of separation by inertia, effectively capturing overspray and ensuring excellent application results. Our catalogue also includes original paint stop filters from Andreae Filters, of which Defil is an official dealer for Italy, and fibreglass filters, ideal for capturing fine particles and ensuring air purity. Thanks to the variable arrangement of fibres and their density, these products
offer high dust holding capacity and a lower risk of release, thus further optimising production processes,” adds Alfredo Pellegrino.
Over the years, Defil has expanded its range of coating filters, including filter bags for cataphoresis, cartridges for liquid application, porous mats, and cleaning systems such as Venturi tubes and rotating nozzles.
“Thanks to the experience gained in almost forty years in business, Defil can offer valuable know-how in filtration, workplace health and safety, and air pollution abatement,” summarises Paola Pellegrino.
With an eye always on technological innovation and sustainability, Defil confirms itself as a partner of excellence for customers seeking cuttingedge industrial filtration solutions.
“We plan to automate our panel cutting process for the construction of filter cells, which is currently manual, to achieve a fully digitised and integrated production flow. In addition, we are considering expanding
our offer by insourcing our metal components’ moulding phase, which would allow us to further increase our independence and diversify our product portfolio,” says Alfredo Pellegrino.
Simona Pellegrino, the General Manager of Defil, concludes by expressing great satisfaction with the purchase of the new electronic pleating machine: “We are more than satisfied with our recent investment, which enables us to better position ourselves on the national and international markets. Defil is now a benchmark supplier in the industry, thanks to our ability to constantly innovate and adapt to the needs of an ever-changing market. Investments in 4.0 technologies and continuous efforts to improve our production processes have enabled us to increase the quality of our filters and strengthen our international presence. With an eye on an increasingly automated and sustainable future, we are ready to consolidate our position by continuing to offer advanced solutions.”
Delco Trailers, a company specialising in the production of trailers, has undertaken an ambitious project to automate its manufacturing process by implementing a new, fully automated coating line. The company chose Total Finishing Systems as its strategic partner. The goal? To achieve flawless finishes and increase production capacity to 500 coated trailers per week.
“When seeing a trailer, the first thing anyone will notice is the finish.”
This statement by William Dyck, the COO of Delco Trailers, perfectly encapsulates the challenge this company has been facing in recent years. Headquartered in Brookston (Texas, USA), Delco has embarked on an ambitious journey to automate its production department by investing in a new, fully automated coating line. To tackle this project, it relied on Total Finishing Systems (Montclair, California, USA), a leading provider of turnkey coating solutions.
Delco Trailers’ objective was ambitious and clear: to achieve the highest finishing standards and guarantee aesthetically impeccable products through meticulous control at every stage of the process. At the same time, implementing the new coating line not only improved the quality of finishes but also addressed the need to significantly increase productivity. “Delco aimed to coat around 500 trailers per week – an ambitious target that required an increase in production capacity,” states Total Finishing Systems’ President, Ty Crowder. “With the new system, we were able to achieve this goal.”
Delco’s commitment to innovative solutions and attention to detail ensures that every trailer produced is not only aesthetically perfect but also designed to withstand the toughest challenges. Dyck also emphasises that “each trailer is made entirely of steel, which ensures strength and durability even in the harshest conditions”. This project represents a major step forward for Delco Trailers, further strengthening its reputation as a manufacturer of high-quality trailers in the American market.
The coating line supplied by Total Finishing Systems is a highly sophisticated plant featuring state-of-the-art technology and a complex conveyor system that branches out in several directions to ensure maximum operational flexibility.
There are 27 loading and 27 unloading automated zones to ensure a continuous and organised workflow. “Previously, the operators had to move the trailers manually or with forklifts from the welding area to the storage one and then to the coating line. Now, thanks to the new automated system, an overhead crane automatically takes the
components from the welding to the coating department, significantly reducing the labour input, speeding up turnaround times, and significantly increasing productivity.
“The parts are then subjected to mechanical pre-treatment by shot blasting. This process occurs in two dedicated areas, for manual and automatic shot blasting, respectively,” explains Fabian Cardenas, the General Manager of TFS. “After these, the power&free conveyor, which extends over 2900 m (9500 ft) in length, bifurcates: the components following the primary line pass through a three-stage pre-treatment tunnel and then into a drying oven; those that follow the secondary line, on the other hand, undergo blow-off, manual cleaning, and drying operations.”
In the subsequent phase, the components are transported to the coating application booths. Again, the conveyor branches off to take each part to the correct booth. The two conveyor lines feature two adjacent booths for primer application and two for powder coating application. Each booth is 48 m (160 ft) long and has a powder recovery system with a cyclone. After coating, the components reach the two curing ovens, which are also adjacent to each other. The layout of
Finally, the two lines merge again in one chain to transport the components to the unloading area.
Meeting the company’s needs
“When Delco Trailers decided to adopt a new finishing system, it was already clear about the type of solution it needed, and we are thrilled that they found Total Finishing Systems to be the perfect partner for this project,” states TFS’s General Manager. “When we met at the Fabtech trade fair in Chicago in 2021, Delco was looking for a supplier capable of offering a complex, turnkey coating system to handle heavy components up to 15 metres (52 ft) in length and achieve a production capacity of around 500 trailers per week.”
“A decisive factor in its choice was our ability to design an innovative, tailor-made layout. We fully customised it to meet the precise requirements of the customer, which had a detailed vision of how to organise production.” Another crucial aspect was the limited space.
“Despite the system’s imposing size, there was little space available. We had to use every square metre very carefully,” notes Crowder. “Cost
control was also essential. We worked to provide Delco with the best possible technology without going over budget, producing a system that fully met its expectations.”
In addition to this significant technological investment, Delco is finetuning its internal production processes to optimise its corporate organisation. It primarily aims to improve forecast management and reduce material inventory while enhancing warehouse procedures to track components more efficiently.
Strategic collaboration with a pool of companies
When Delco Trailers decided to implement a new finishing system, the requirements were clear: a highly customised and complex system. “We are proud that they chose Total Finishing Systems as the ideal partner for this ambitious project,” says the General Manager of Total Finishing Systems. Careful analysis and in-depth study were essential to design a layout of such complexity. “Collaboration with our partners was crucial: Erzinger (Joinville, Brazil) supplied the booths and the powder recovery system, Railtechniek (Tiel, Netherlands) built the power & free conveyor,
and Total Finishing Systems was responsible for designing the pre-treatment tunnels and the drying and curing ovens, as well as integrating all technologies along the line,” illustrates Crowder. “Each project stage required great attention to detail and meticulous preparation to ensure that all the customer’s requirements were fully met,” summarises Fabian. “We are thrilled with the results so far. We have already delivered 95% of the system, and we are going to continue to work on perfecting it until it is fully operational.”
Kathrin Schilling Founder & Director of BioPowder - Birkirkara, Malta
All around the world and across industries, businesses are called to be more sustainable, green, and clean. Hence, companies are increasingly required to balance economic, social, and environmental considerations to ensure a better quality of life for current and future generations.
Amidst this push for sustainability, the paints and coatings industry may face some challenges due to the environmental and health impacts of some of the chemicals commonly used in its products. However, the market now provides natural, sustainable options that can even enhance physical and mechanical properties of coating formulations. These alternatives include bio-based binders, biodegradable texturizers, recycled content, and natural pigments.
The incredibly useful olive
A circular raw material that has lately gained wider attention is the olive pit, a by-product from the olive oil mill. Olive oil manufacturing involves compressing of the whole olive, which produces a solid residue of pulp, peel, and fragmented pits. In the past, raw olive pits have mainly been used for combustion. In some countries, they are still considered as waste products and not yet part of any upcycling value chain. According to the International Olive Council1, the global olive oil production volume for the 2021/22 crop year is estimated at 3.10 million metric tonnes, up 2.9% from the year before. Hence, there is a massive amount of olive pomace (pulp) left behind, which comes with certain disposal challenges because of its fat and polyphenolic compound content. Fortunately, new technologies have emerged to recover this waste stream and to break it down into its components. Specialized machines are used to process the pomace in a moist state, and olive pit fragments are separated from pulp and shell through a centrifugation process. The fragments are then mechanically cleaned, dried, and screened based on their particle sizes. Through this complex treatment process, BioPowder recovers light beige granules that are free of any dust/pulp and nearly odorless.
BioPowder2 further processes them into top-grade micronized powders with different surface functionalization options. Marketed under the brand name Olea FP (Functional Powders), they are fully circular additives with desirable properties for modern coating formulations.
Technical benefits of micronized performance powders from recycled olive stones
For paints, floorings and other coating systems, Olea FP present an exceptional range of opportunities thanks to the following mechanical properties:
High hardness of >3.5 on the Mohs scale
Olea FP have a high level of hardness, making them suitable for use in coatings that require elevated strength, stability, and abrasion resistance. This results in a long lifespan of functional coatings for outdoor and high-traffic areas.
Low oil- and water-binding capacity
Due to their low oil- and water-binding capacity, Olea FP provide particle stability with no risk of swelling or expansion. This feature facilitates incorporation in both water- and solvent-based formulations, improves the durability of coatings and reduces the likelihood of cracking or peeling.
Low density
Olea FP are low in density and therefore ideal for use in lightweight materials. This feature can also offer cost-saving potential by reducing the per-kg amount needed for volumetric batches.
Compact particle shape
The compact particle shape of Olea FP allows for high predictability and ease of incorporation in coatings. The effect is generally a good dispersability leading to a smooth texture.
2 www.bio-powder.com
Reactive particle surface
Surface reactivity of Olea FP can either be taken advantage of or suppressed through functionalization. This feature allows for the production of coatings with tailored properties such as improved adhesion or water resistance.
Thermal resistance and insulating properties
Olea FP have thermal resistance and insulating properties. This is particularly relevant for industrial coatings, e.g. for use in pipelines or storage tanks, where thermal resistance and insulation are critical.
Demonstrated effects of Olea FP in formulations
Reduction of Gloss
One way in which Olea FP can enhance paint and coating formulations is by reducing their gloss. The micronized powders have proven effective as matting agents, among others in the following ways:
As natural pigments in a PU-acrylate matrix: Olea FP was added to a PU-acrylate matrix to modify the color and gloss of the coating. The addition of the powder resulted in a color change towards the red/ yellow spectrum and a gradual opacification of the paint. The overall gloss of the paint was reduced to nearly 50%, creating an increasingly matte finish.
In replacement of polyethylene (PE) matting powders in acrylic paint formulations: a functionalized (hydrophobic) grade of Olea FP was added
at a concentration of 10%. The comparative study showed a reduced gloss at all incident angles, with the 0-100 μm being most effective particle size range. On the whole, the conducted studies demonstrate the effectiveness of Olea FP as a matting agent in various types of paint formulations, including epoxy and acrylic paints. By reducing the gloss of such coatings, Olea FP can help create a matte finish, which is desirable in many applications such as automotive or furniture coatings. Additionally, their use as replacements of traditional matting agents like PE powder can greatly reduce the environmental impact of coatings manufacturing.
The high hardness of Olea FP makes them ideal for use as reinforcing agents in coatings. By adding variable doses of Olea FPs, manufacturers can improve the coatings’ resistance to wear and tear, i.e. caused by impact and abrasion. This feature is particularly useful in applications where coatings are subjected to high levels of stress, such as in marine or industrial settings. As part of a comprehensive study, the following tests were conducted:
Indentation tests: In a PU-acrylate coating reinforced with Olea FP particles, it was found that doses of olive stone powder as low as 5% could increase the hardness of a paint by up to 20%.
Taber tests: The abovementioned PU-acrylate formulation with varying load percentages of Olea FP was subjected to rotating Taber wheels.
The latter applied pressure on the surface, which gradually removed the coating layer. It was found that the use of olive stone powder reduced mass loss by up to 50% in less than 600 cycles. These results demonstrate that olive stone powder improves the abrasion resistance and hardness of formulations. Consequently, Olea FP can help extend the lifespan of coatings, which ultimately boosts efficiency and supports less frequent use. Additionally, the powder’s feather-light properties make it an attractive option for lightweight coatings in applications where every gram counts.
In addition to its use in matting and reinforcement, Olea FP are also an excellent option for creating unique surface textures in coatings. Manufacturers looking for bio-based alternatives can consider using Olea FP for the following uses:
Functional filler and viscosity agent: Incorporating olive stone powder in epoxy, acrylic, or other formulations allows for viscosity and rheology adjustments while improving the overall strength of the formulation.
Surface texture particles: Olive stone particles can be scattered on the surface of coatings to create a decorative and/or anti-slip effect. Olea FP texture particles are available in grain size ranges from <50μm up to 4mm, allowing for a large spectrum of texturing options.
BioPowder’s reinforced linoleum ‘naturazzO’ is a resilient flooring solution that contains up to 40% of Olea FP composite fillers. It has been proven effective for high-load industrial surfaces.
Decorative particles and pigment carriers: Besides being well suited for decorative effects, Olea FP texture particles are powerful pigment carriers. Tests have demonstrated high levels of effectiveness with pigments from both natural and synthetic sources. In response to the high demand for all-natural texture particles, e.g. as alternatives for quartz or polymer particles, BioPowder has recently launched its own color particle range marketed under the brand Olea Colors.
In sum, the use of Olea FP in coatings comes with multiple advantages. As a compostable material, it constitutes an eco-friendly alternative to conventional matting particles. Its resistance and lightweight properties make it an attractive reinforcing option, while its customizable micron ranges provide versatile surface texturing opportunities. Manufacturers would ideally take advantage of these effects in combination to create attractive design coatings from renewable sources.
Bio-based functional powders: green innovation with an optimized carbon footprint
The need of companies to adopt sustainability throughout their value chain has doubtlessly become imperative. But what does it take to be truly eco-friendly and set new standards for responsible manufacturing practices? Specifically, what makes a coating stand out as more
Manufacturers can create unique surface textures with BioPowder’s natural particles. Recommended systems for particle incorporation include epoxy, PU, and poly-aspartic resins.
sustainable? The answer lies in the carbon footprint, and hence a full life-cycle assessment, of all materials used in a formulation.
Measuring the CO2 output in all stages of the manufacturing value chain has become a recognized benchmark. In this regard, BioPowder has committed to lean practices that are deeply ingrained in the circular ecosystem of olive by-products. As a consequence, olive stone particles come with an optimized carbon footprint: they are manufactured 100% mechanically, i.e. with electricity being the main required utility. The use of water is minimal, and production does not generate any waste. Most remarkably, olive trees are among the plants that bind the largest amounts of CO2. Evidence shows that roughly 1.5kg of CO2 is produced per liter of extra virgin olive oil. However, an olive orchard can absorb up to 10kg of CO2 while growing the equivalent quantity of olives3 In conclusion, it can be said that olive stone powders are doubtlessly creating opportunities for carbon-efficient innovation in paints and coatings. The BioPowder team supports coatings manufacturers throughout all stages of R&D and production and looks forward to new project partners.
BioPowder is a responsible producer and supplier of high-grade fruit stone powders and bio-based abrasives that are free of chemical additives. Derived from food processing side streams, the company’s products support a circular economy and enable manufacturers to reduce their environmental impact. Founded in 2017 and headquartered in Malta, the company sources from the Mediterranean region and manages production in Southern Spain. BioPowder is part of a sustainable supply chain that strongly believes in processing agricultural by-products (not crops), sourcing locally or regionally, and ensuring that its activities do not disrupt the food chain.
Manuela Casali UCIF – Italian Surface Treatment Equipment Manufacturers’ Association, Milan, Italy info@ucif.net
Cybersecurity, which used to be the exclusive competence of IT departments, now involves increasingly broader areas of the corporate structure, personally affecting all employees regardless of their role.
In an increasingly digital world, corporate cybersecurity is no longer an exclusive responsibility of the IT department.
Today, every employee plays a crucial role in protecting information and assets. The increasing complexity of cyber threats makes it essential that everyone, regardless of their position in the company, pays attention to potential cyber attacks, including those from unexpected sources.
Most cyber attacks do not start with sophisticated systems hacking operations but rather with something much simpler: a phishing email, a suspicious link, or a USB stick left unattended. These attack vectors exploit the trust and carelessness of employees, turning them into gateways for cybercriminals. This means that even the best security system can be vulnerable if people are not adequately trained and aware of the risks.
One aspect that is often overlooked is the origin of threats. Not only professional hackers or organised groups can pose a risk, but also former employees, external suppliers, and even accidental mistakes by the internal staff can compromise corporate security. Therefore, everyone should be aware of these potential sources of risk and able to recognise suspicious or unusual behaviour.
Training is the first line of defence against cyber threats. Regular cybersecurity refresher courses help employees recognise and correctly respond to threats. Training should not be limited to theoretical sessions but also include practical simulations, such as phishing tests, to prepare the company’s staff to react in real-life situations. At the same time, such a safety culture should be promoted at all levels of the organisation. Employees should feel empowered as
active participants in protecting corporate assets, understanding the impact a single mistake can have on the entire company.
In addition to training, prevention is crucial. Companies should take proactive measures such as constantly updating systems, implementing advanced security software, and regularly checking for vulnerabilities. It is also essential to establish clear procedures for incident management so that the company can respond quickly and limit the damage in the event of an attack.
In other words, corporate cybersecurity is a challenge that requires the active participation of all members of the organisation. Only through a combination of training, awareness, and preventive measures can companies protect themselves effectively against cyber threats. At a time when information is one of the most valuable assets, digital security must be a priority shared by all.
Cybersecurity regulations vary by jurisdiction and industry, but some international and local laws do exist that are crucial for companies and organisations. The main international regulations currently in force include, for example, the GDPR, which applies to all organisations that process personal data of EU citizens, regardless of location; ISO/IEC 27001, an international standard that specifies the requirements for information security management systems; and even the Cybersecurity Act, which came into force in the EU in 2019 and establishes a framework for cybersecurity certification within the European Union. Through its collaboration with ANIMA Confindustria, UCIF offers refresher and training workshops on this subject to help its members keep abreast of new issues and be informed on how best to manage their activities.
Ilaria Paolomelo ipcm®
Often associated with sweetness, love, and femininity, pink has a rich and varied history spanning art, literature, nature, cinema, and mass culture. In this article, we explore the origins of this colour, its meaning, and the ways in which it has been used over the centuries.
As a colour rich in history and symbolism, pink has gone through centuries of cultural and artistic transformation, eventually finding a significant role in film, fashion, and psychology. Rare and precious in ancient times, pink underwent a profound evolution from the Renaissance to the 18th century, becoming a symbol of elegance and power thanks to figures such as Madame de Pompadour. In the 20th century, it took on connotations of femininity and delicacy, although it was also considered a masculine colour in the past. In psychology, pink is associated with tranquillity, compassion, optimism, and creativity and is thought to have a calming power and positive impact on our state of mind. From iconic films like “Breakfast at Tiffany’s” and “Mean Girls” to pop culture and awareness campaigns like the “Pink Ribbon” one, this hue continues to influence and inspire, remaining central in today’s cultural and social trends.
Obtained by mixing red with white, pink has gone through centuries of cultural and artistic transformation. In ancient times, it was difficult to obtain and, therefore, rare and precious. The first use of this colour in art can be traced back to ancient Rome, where it was utilised for frescoes and ceramic decorations. As the centuries progressed, during the Renaissance, pink became more accessible thanks to advances in pigment production and was used in religious paintings to depict human skin and sacred garments.
The word “pink” first appeared in the 17th century, but the colour only spread widely in the 18th century. It was in this period that Madame de Pompadour, King Louis XV’s mistress, was known for elevating pink to a symbol of fashion and prestige, so much so that La Manufacture Nationale de Sèvres, one of the most famous porcelain manufacturers in Europe founded in 1740 in Sèvres (France), christened a shade of pink porcelain “Pompadour Pink” by order of the sovereign himself. At that time, pink was worn by women and men alike and considered an elegant and powerful tint. However, its meaning has changed over time. In the West, it is now traditionally associated with femininity, sweetness, and innocence, a connotation that was consolidated in the 20th century. Before the 19th century, pink was actually often considered a masculine colour, especially for children. In many Asian cultures, pink symbolises
good luck and happiness. Today, this colour is also associated with tranquillity and serenity. Psychological studies have shown that it can have a calming effect and reduce levels of aggressiveness – which is why it is used in environments such as hospitals, prisons, and schools to provide a serene atmosphere.
The origin of the word “pink”
In English, before the end of the 16th century, this hue was called “incarnation”, with the meaning of “flesh colour”. It then began to be called “pink” from the common name of a garden plant with flowers in this colour, called dianthus1 – although earlier, this word indicated a greenish yellow. To further complicate the matter, the origin of this word is unknown. Some etymologists suggest it was taken from an earlier verb that means “to wink,” as some pinks look like the irises of eyes. Other sources indicate that it was derived from a different verb “pink” that means “to perforate in an ornamental pattern,” referring to the jagged edges of most pinks. Or, perhaps, it was from Dutch pink meaning “small” or “narrow,” itself obscure.
1 https://en.wikipedia.org/wiki/Dianthus
In Italian (and similarly in other European languages), the name and adjective rosa is linked to another flower, the rose. This plant had considerable symbolic and cultural importance in ancient civilisations, which led the term to spread widely. In many of these cultures, the rose has been associated with love, beauty, and passion, and these connotations have also been reflected in language. For example, in Greek mythology, it was associated with Aphrodite, the goddess of love, and in Roman times, with Venus.
The colour pink has played a significant role in both literature and art, taking on different meanings and connotations depending on the historical and cultural context. In literature, it is traditionally associated with delicacy and sensitivity. For example, in many of Jane Austen’s works, female characters are often described in pink dresses, symbolising purity and romance. However, the meaning of pink has never been static: in the novel “Bad Girls” by Joyce Carol Oates, for instance, this colour is used to represent rebellion and inner strength, being associated with strong and independent female characters. Pink has undergone significant transformations in art as well. During the Rococo period, it represented elegance and refinement, as shown in the works of François Boucher and Jean-Honoré Fragonard.
In the 20th century, artists like Pablo Picasso and Mark Rothko employed pink innovatively to explore emotion and introspection. Picasso, in particular, went through a “Pink Period” in which his works expressed serenity and warmth. In Postmodernism, artists such as Jeff Koons have used pink to explore mass culture and kitsch, often to comment on the commercialisation of beauty and the superficiality of popular culture.
Pink can be found in nature in many forms, from flowers to landscapes. One of the most famous examples is Japan’s cherry blossoms, or sakura. These flowers colour landscapes with delicate pink tints and take on deep cultural meanings. Celebrated during Hanami, their blossoming symbolises the ephemeral beauty of life and the importance of appreciating fleeting moments.
On the other hand, flamingos are famous for their bright pink plumage due to their diet. Contrary to what one might think, these birds are not born pink but with grey or white feathers. During their lives, they acquire this colour by eating crustaceans and algae rich in carotenoids: these organic pigments, once digested, are metabolised and deposited in their feathers, beak, and skin. The pink colour thus becomes a visual indicator of a flamingo’s health and diet: the richer the diet in carotenoids, the brighter the plumage.
Finally, nature offers us some beautiful landscapes in various nuances of this colour. Described as the “Caribbean of the Mediterranean” and located on the southwestern coast of Crete, Elafonissi Beach is one of Greece’s most popular summer destinations; it is also world-famous
for its pink sand, formed by pink and red foraminifera and shells that pulverise on contact with seawater. The pink beach of Budelli, located in the La Maddalena archipelago in Sardinia (Italy), is also well known for its pink sand, composed of calcareous shells of a unicellular organism, Miniacina miniacea, and fragments of coral.
Pink has had a crucial impact on cinema and mass culture, evoking specific atmospheres and setting characters apart as symbols of elegance, rebellion, and power. This shade has found ample space in numerous iconic films and has left a significant imprint on fashion and social trends.
In the film “Breakfast at Tiffany’s”, pink emphasises the elegance, vivacity, sophistication, and glamour of Holly Golightly, the famous character played by Audrey Hepburn. Similarly, in “Grease”, the “Pink Ladies” group adopts pink as a symbol of friendship and teenage rebellion, creating an enduring icon of 1970s fashion and pop culture. Pink continued to be a distinctive colour in popular culture with films like “Mean Girls”, where the famous line “On Wednesdays we wear pink” became a symbol of conformity and belonging to a social group. Such use of pink to represent power and social dynamics among teenagers has consolidated its role in youth culture.
At the same time, besides cinema, pink is deeply rooted in contemporary mass culture. It is the distinctive colour of many brands and products, including the iconic Italian Big Babol chewing gum, the Victoria’s Secret logo, and Barbie’s packaging. Launched in 1959 by
Mattel, Barbie initially did not have pink as her predominant colour. However, in the 1960s and 1970s, this emerged as a key element in the branding of the world’s most famous doll, reinforced in the 1980s and 1990s through targeted marketing strategies. Today, Barbie Pink has become an iconic and ubiquitous symbol in pop culture, giving the brand and those who wear this tint a strong sense of femininity and glamour.
Such success was further amplified by the movie Barbie, directed by Greta Gerwig and starring Margot Robbie and Ryan Gosling, which was a resounding success at the box office, grossing over 1.4 billion dollars globally and becoming one of the biggest cinematic successes of 2023 as well as the highest-grossing film ever produced by Warner Bros. This movie not only made Barbie fashionable again but also demonstrated cinema’s ability to affect cultural and commercial trends. The dominant bright pink of the setting and costumes awakened and amplified the appeal of this colour, leading to a renewed interest in using this shade in fashion and decoration. An example of this is the powder-pink Arizona sandals produced by German company Birkenstock: according to the online shopping platform Lyst, only one week after the film’s release, online searches for pink Birkenstocks increased by 110%2. The representation of Barbie’s world has fuelled a wave of nostalgia and stimulated a debate on femininity and gender identity-related topics, suggesting that pink will continue to be a central element in pop culture.
2 https://www.yahoo.com/lifestyle/birkenstock-riding-high-searches-soar-143114021.html?
However, pink is also linked to more serious and important issues that usually revolve around women. The “Pink Ribbon”, the international symbol of the fight against breast cancer, is much more than just a pink ribbon. It represents solidarity and hope for millions of people worldwide, helping raise awareness and funds for research and treatment of this oncologic condition. Finally, pink has also been finding significant application in social and political movements. The “Pink Protest”, for example, is an initiative that uses colour to support women’s and minority rights, proving that pink can also be a powerful tool for advocacy and activism.
From left to right:
- Cherry blossom season in Japan.
- The famous pink beach of Budelli, Sardinia.
- The Barbie brand has made pink its dominant colour.
On Saturday, 7 September, the ipcm® team had the pleasure of attending the 40th anniversary of Idrotecnica. It was an important occasion to reminisce about the history of this manufacturer of water treatment systems and celebrate the many successes achieved in four decades of activity.
Idrotecnica, a company designing, producing, and installing water purification and demineralisation systems for various industrial sectors, including cosmetics, pharmaceuticals, research laboratories, and coating, celebrated its 40th anniversary on Saturday, 7 September in its headquarters in Genoa (Italy). This event was an opportunity to celebrate but also look back over these four decades of successes and innovations that have made Idrotecnica a solid and globally recognised company. The participants had the opportunity to take part in a guided tour inside the company’s
production department, where the first water treatment plants supplied by Idrotecnica in the 1990s were on display alongside the most modern and advanced systems in use today. This exhibition offered an insight into the firm’s technological evolution, highlighting its constant commitment to innovation.
One of the most meaningful moments was the speech by CEO Federico Marcenaro, who recalled with great emotion the foundation of the company by his father Alessio, emphasising that passion, commitment, and the continuous search for excellence have guided Idrotecnica in its path of growth. “It has
been an intense 40 years, full of challenges and successes, and we look to the future with the same enthusiasm, determination, openness, professionalism, and above all humility that have distinguished us from the beginning,” said Marcenaro. He also expressed his deep gratitude to all those who have contributed to the company’s success: employees, partners, suppliers, and customers, whose support has been crucial in achieving ambitious goals. Special thanks were reserved for his family, who have always supported the company on its journey. Marcenaro illustrated the importance of innovation and quality, two values that continue to guide Idrotecnica in facing the challenges of the global market. Finally, the event offered a glimpse into the future, with Marcenaro anticipating some of the opportunities and challenges that await the company in the coming years, stating that Idrotecnica will continue to invest in research and development to remain at the forefront of the industry by meeting the needs of everchanging and increasingly demanding markets. The day ended in a festive and convivial atmosphere with a toast and a lunch offered to all those present. “This 40th anniversary is not only an important milestone but also a new starting point for successfully tackling future challenges and continuing to write Idrotecnica’s history in the decades to come,” the CEO concluded.
Helios Quartz has celebrated 85 years of activity by inaugurating a new warehouse and welcoming over 150 guests to honour the employees and their families.
On Thursday 12th September 2024, Helios Quartz celebrated an important milestone: 85 years of history. The historic Italian company based in Cambiago (Milan) and renowned for its quartz glass processing and the production of IR and UV lamps organised an exclusive event in its new facility, welcoming over 150 guests for a moment of celebration and reflection. The evening, reserved exclusively for employees and their families, created a warm and engaging atmosphere, where pride for the path taken merged with hope and enthusiasm for future challenges.
“Helios Quartz continues to consolidate its role as a reference in the sector. I would like to honour our journey by celebrating not only the results that we have achieved, but above all the people who have been part of Helios Quartz and who have contributed to its growth”, has stated the CEO Armando Giro, who has inherited his father’s legacy with the same vision and determination. “The future of Helios Quartz is bright and I am truly excited to share it with all of you.”
Particularly touching was the recognition reserved for Enrico Giro, father of the current CEO Armando, a key figure in the development of the company. However, Giro has also expressed warmth and gratitude towards the employees of the company, considered to be the beating heart of Helios Quartz, underlining how dedication and teamwork have contributed to building the success of Helios Quartz.
Founded in 1940, Helios Quartz was born as a family-owned company and it is now an international group with two production plants - in Italy and Switzerland - and its own sales offices in the USA, China and Asia. The company is now a major international supplier for quartz glass processing and the manufacturing of IR & UV lamps, and it also produces specialised equipment for industrial, scientific, and medical applications. Over 70 years of experience in several different industries has enabled Helios Quartz to acquire advanced technology know-how, deep knowledge of production processes and solid skills in many areas of various applications: Helios Quartz companies are able to approach every request, studying solutions for the most specific and complex applications, also thanks to a cutting-edge testing centre located in the production plant of Cambiago.
The next edition of Paint & Coatings Italy will take place from October 22 to 23 in Milan (Italy).
Paint & Coatings Italy returns for its third year, taking place 22 –23 October at the NH Milano Congress Centre in Assago (Milan, Italy). Supported by AssICC and ASSOVERNICI, Paint & Coatings Italy has been developed with the sector operators in mind. The event is packed with a content that covers a diverse range of topics, combined with an exhibition featuring the leading suppliers active in this industry.
So, regardless of experience level, the event has expertise, creative insights, knowledge, services, tools and targeted professional contacts.
P&C Italy is the opportunity to add colour to the sector’s business. Over the two days, attendees will have the chance to make connections, find solutions, and discover the latest trends, innovations, and technological advancements that will help drive business forward.
The exhibition will be the largest yet, with an increased number of exhibitors at your disposal, thousands of products to find and more industry experts on hand to share their knowledge. Running alongside the exhibition is a comprehensive programme of content that provides a unique opportunity to discover new solutions, form strategic collaborations, and stay updated on industry developments.
The P&C Italy Conference features experts and companies from the chemical and materials sectors discussing current and relevant topics. The main objective is to explore innovative and sustainable solutions that meet increasing environmental demands and current regulations.
Supported by AssICC, the conference will address various regulatory topics, presenting updates on labelling and PCN notification according to the recent CLP regulations. Further content will cover the importance of REACH and CLP controls to ensure compliance with European regulations.
A highlight will be the session dedicated to the certification of coaters and the state of the art in Italy, followed by a presentation on using the Environmental Product Declaration (EPD) to communicate the environmental impacts throughout the product lifecycle.
ERMA, the European Resin Manufacturer Association, will play a crucial role in guiding sustainability discussions, providing both a regulatory framework and practical strategies to help companies become more environmentally responsible. The full program is available at: www.paintcoatings.it/la-conferenza.
Given the success of the Polymer Academy at the previous edition, P&C Italy will once again focus on polymer binders, involving the leading resin producers. This Congress highlights how innovation and sustainability are central to progress in the coatings and polymers sector, with a strong focus on the quality and efficiency of production processes. New for 2024 is the Additives Academy, led by the top additive manufacturers in the industry. The dedicated conference focuses on innovative and sustainable solutions for paints and coatings. The main topics include the use of antimicrobial additives, sustainable marine coatings, PFAS-free wetting agents, and wax-based additives. The discussion also covers performance enhancements in coatings with smart additives, PFAS substitutes, biodegradable waxes, and advanced thickeners. Finally, the conference explores the challenges and opportunities in formulating eco-sustainable paints, with a focus on natural additives, two-dimensional crystals, and pigment recycling.
Paint & Coatings Italy returns to the NH Milano Congress Centre in Assago, ready to solidify its reputation as a flagship event in the national paint and coatings landscape. Lunch and coffee are offered to all visitors arriving onsite before 10 AM.
For further information: www.paint-coatings.it
For many industrial sectors, the “magic metal” aluminium is and will continue to be the material of choice for sustainable and technically unrivalled products. Just under 800 exhibitors from 50 nations will be demonstrating the potential it holds and how the aluminium industry is rising to current challenges and gearing for the future at the world-leading trade fair ALUMINIUM 2024 in Düsseldorf from 8 – 10 October.
Every two years, the biggest showcase of the aluminium industry brings together producers, processors and technology providers along the complete value chain: from raw material production and the segments of primary production, machine and plant engineering to processing technologies and semi-finished and finished products, as well as directional recycling technologies. Here, they will showcase the innovative solutions made possible using aluminium in automotive production, mechanical engineering, construction and engineering, aviation and air space, electronics, packaging and transport. For the international industry giants, ALUMINIUM is the most important meeting point and showroom every other year. Additionally, many SMEs and start-ups also leverage this leading international trade fair to make an appearance on the market, exchange ideas with their customers and network with other industry representatives. To them all, ALUMINIUM serves as both a business barometer and impulse provider. 780 exhibiting companies along the entire aluminium value chain will be presenting themselves in five exhibition halls this year. Halls 1 and 4 are dedicated to semi-finished products while Hall 5 focuses on furnace construction, metal working, joining technologies and automation. In Hall 3 surface treatment and rolling technologies will be centre stage, including the Surface Pavilion and the Surface & Design Lounge. In Hall 6 everything will revolve around casting and heat treatments, furnace construction, primary production and recycling. Here visitors will find not only the Primary and Foundry Pavilion but also the Foundry Community Café, the ideal location for networking and exchange. Another highlight is the relaunch of the Media & Education Lounge in Hall 6. This provides not only a retreat with plenty of reading material but also valuable insights and interesting facts about the material that is aluminium. In addition, information on further training options and skilled labour shortages will be offered here and an accompanying special programme for students and trainees is planned. ALUMINIUM will not only present current solutions and a glimpse of the future to visitors in the exhibition area.
The extensive programme in the ALUMINIUM Conference and the Speakers Corner also offers in-depth insights: the conference, organised by Aluminium Deutschland and considered a central hub for knowledge transfer and experience exchange at the trade fair, provides valuable impulses for current issues, and The Innovation Plaza “Sustainability & Recycling” will again be all about the sustainable, green transformation of the aluminium industry this year.
The trade fair will debut the “Women with Metal – ALUMINIUM Awards” on 9th October to promote gender equality and diversity in the aluminium industry, recognising women’s achievements and addressing skilled labour shortages by encouraging more women to pursue careers in the field.
The ALUMINIUM trade fair will open on 8th October, featuring an industry dialogue between Aluminium Deutschland, IG Metall, and IG BCE on socio-economic transformation. This dialogue aims to foster crucial discussions with policymakers, with speakers including Mona Neubauer, Minister of Economic Affairs for North Rhine-Westphalia.
For further information: www.aluminium-exhibition.com
Eos Mktg&Communication srl www.eosmarketing.it - info@eosmarketing.it www.myipcm.com - info@ipcm.it
Redazione - Sede Legale: Via Pietro Mascagni, 8 - 20811 - Cesano Maderno (MB) - Italy Tel. +39.0362.503215 - Fax. +39.0362.1794768
Prof. Massimiliano Bestetti: Department of Chemistry, Material and Chemical Engineering, Politecnico of Milan –Section of Applied Chemistry and Physics
Prof. Stefano Rossi: Material Engineering and Industrial Technologies, University of Trento - Product Design
EDITOR IN CHIEF / DIRETTORE RESPONSABILE
ALESSIA VENTURI venturi@ipcm.it
EDITORIAL DIRECTOR / DIRETTORE EDITORIALE
FRANCESCO STUCCHI stucchi@ipcm.it
EDITORIAL OFFICE / REDAZIONE
PAOLA GIRALDO giraldo@ipcm.it
MONICA FUMAGALLI fumagalli@ipcm.it
NICOLE KRAUS kraus@ipcm.it
MATTEO SOTTI sotti@ipcm.it
ILARIA PAOLOMELO paolomelo@ipcm.it
GABRIELE LAZZARI redazione@ipcm.it
FEDERICO MELIDEO melideo@ipcm.it
GIULIA GENTILE gentile@eosmarketing.it
EDITORIAL OFFICE AND GRAPHICS
ELISABETTA VENTURI grafico@ipcm.it
MEDIA SALES
FRANCESCO STUCCHI stucchi@ipcm.it
ILARIA PAOLOMELO paolomelo@ipcm.it
NICOLE KRAUS kraus@ipcm.it
LAYOUT/ IMPAGINAZIONE
ELISABETTA VENTURI grafico@ipcm.it
Dr. Fulvio Zocco: Environment and quality
Prof. Paolo Gronchi: Department of Chemistry, Material and Chemical Engineering, Politecnico of Milan –Chemical Engineering Section
Kevin Biller: ChemQuest Powder Coating Research
SUBSCRIPTION SERVICE - SERVIZIO ABBONAMENTI:
Sale only on subscription - Vendita solo su abbonamento E.mail info@ipcm.it
Subscription Rates 2024 - Tariffe Abbonamento 2024:
Annual subscription print + digital:
EMEA 110,00 € (postage included)
Rest of world 350,00 € (fast airmail shipping included)
Abbonamento annuale cartaceo + digitale:
EMEA 110,00 € (spese postali incluse)
Resto del mondo 350,00 € (spedizione via aerea inclusa)
Single copy: 15,00 € EMEA (postage included) - Rest of world (postage excluded)
Back issues: 30,00 € EMEA (postage included) - Rest of world (postage excluded)
Fascicolo singolo: 15,00 € EMEA (spese postali incluse) - resto del mondo (spese postali escluse)
Arretrati: 30,00 € EMEA (spese postali incluse) - resto del mondo (spese postali escluse)
The smart journal for surface treatments
This magazine is wrapped with a biodegradable and compostable film. Questa rivista è confezionata con un film biodegradabile e compostabile.
PRINT/ STAMPA
SEBEGRAF SRL info@sebegraf.eu
Subscriptions can be made via payment online at: www.myipcm.com
Subscription and the sale of individual issues are exempt from VAT under Italian law: Article 74.1, letter C of DPR 633/72, DM 29/12/1989.
Gli abbonamenti possono essere sottoscritti con carta di credito sul sito: www.myipcm.com L’Iva sugli abbonamenti, nonchè sulla vendita di singole copie è assolta ai sensi dell’art.74 comma 1 lett. C DPR 633/72, DM 29/12/1989.
Registrazione al Tribunale di Monza N° 1970 del 10 Dicembre 2009Eos Mktg&Communication srl è iscritta nel Registro degli Operatori di Comunicazione con il numero 19244
POSTE ITALIANE S.P.A. – SPEDIZIONE IN ABBONAMENTO POSTALE –D.L. 353/2003 (CONV. IN L. 27/02/2004 N.46) ART. 1, COMMA 1 LOM/MI/4351
It is forbidden to reproduce articles and illustrations of “ipcm®” without authorization and without mentioning the source. The ideas expressed by the authors do not commit nor magazine nor eos Mktg&Communication S.r.l and responsibility for what is published is the authors themselves.
È vietata la riproduzione di articoli e illustrazioni di “ipcm®” senza autorizzazione e senza citarne la fonte. Le idee espresse dagli autori non impegnano nè la rivista nè eos Mktg&Communication S.r.l e la responsabilità di quanto viene pubblicato rimane degli autori stessi.
There’s no single answer to sustainability, but small changes to the products you use and the way that you use them can make a big difference in the long run. Like choosing Interpon D2525 Low-E, a low energy powder coating. It’s a superdurable powder coating that achieves an industry first in being able to cure at temperatures as low as 150ºC while still being Qualicoat Class 2 certified. Whether you cure at a lower temperature, or at a faster line speed, either way you win by reducing the total energy consumed, lowering carbon emissions, and enhancing production line efficiencies. Interpon D2525 Low-E is easy to apply, provides excellent edge coverage and comes in a wide range of colors and textures, which means more right-first-time results requiring less re-working and near zero rejection rates.