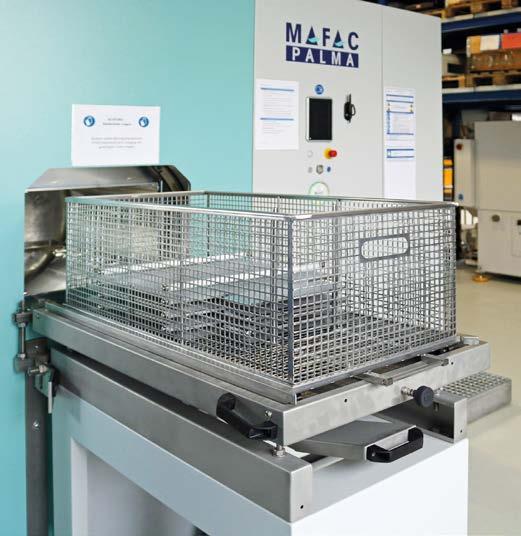
8 minute read
CASE STUDY
© MAFAC © MAFAC
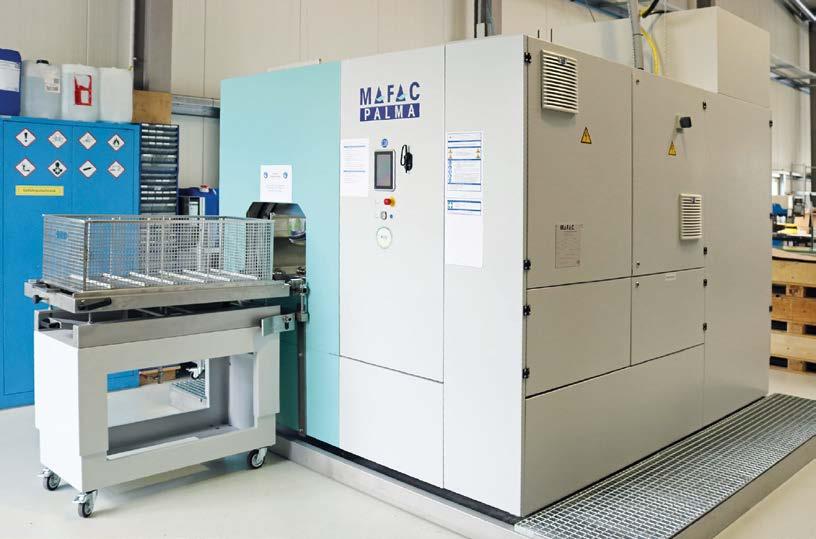
MBengineering can meet the highest medical engineering standards with its specially sized spray-flood cleaning machine MAFAC PALMA 100. The stainless steel sheets are stacked on top of each other in densely packed batches, which is particularly challenging when it comes to cleaning and drying them. Mbengineering soddisfa gli elevati requisiti dell’ingegneria medica con la macchina di lavaggio a spruzzo-immersione MAFAC PALMA 100, di dimensioni speciali. Le lamiere in accio inox sono impilate a formare piccoli lotti, una configurazione impegnativa per quanto riguarda il lavaggio e l’asciugatura.
The system’s flagship: a third tank for rinsing
According to Martin Zepf and Gianni Leocata, the MAFAC PALMA 100 machine meets all these requirements. This spray-flood cleaning machine features a rotating, multi-sided spray system and a counter-rotating basket container with the special dimensions of 1000 x 480 x 338 mm (L/W/H). The spraying and flooding processes can be combined in different ways to ensure maximum process flexibility, as the cycle can be adjusted to any cleaning task in a highly customised manner. Another convincing advantage of MAFAC PALMA 100 was the possibility to add a third tank for rinsing. The cascade layout and the additional rinse guarantee a long bath service life despite the high oil volumes generated by the laser punching and cutting operations: “Currently, we only change the cleaning baths every three to four months, despite the high workload,” explains Gianni Leocata.
The multi-stage cleaning and drying process
The blanks are subjected to both an intermediate and a final cleaning stage in order to be carefully cleaned of any residues and particles and subsequently dried. The cleaning process starts with a ten-minute intermediate treatment during which the oil residues are removed through cleaning, rinsing, and pulse blowing. A mild cleaning agent is added to the first tank to be applied during the spray-flooding
Fiore all’occhiello del sistema: un terza vasca di risciacquo
Secondo Martin Zepf e Gianni Leocata MAFAC PALMA 100 soddisfa tutti questi requisiti. La macchina è dotata di un sistema di spruzzatura rotante e multi-lato e un contenitore controrotante di dimensioni speciali pari a 1000 x 480 x 338 mm. Entrambi i processi, spruzzo e immersione, possono essere combinati in diversi modi per garantire massima flessibilità di processo, poichè il ciclo può essere regolato in base al lavaggio richiesto in modo molto personalizzato. Un altro convincente vantaggio di MAFAC PALMA 100 è stata la possibilità di aggiungere una terza vasca per il risciacquo. Il layout a cascata e il risciacquo aggiuntivo garantiscono una lunga vita utile del bagno, nonostante l’elevata presenza di olio generata da punzonatura e taglio: “Al momento sostituiamo i bagni di lavaggio solo ogni tre o quattro mesi, nonostante l’elevato carico di lavoro”, ha spiegato Gianni Leocata.
Lavaggio e asciugatura multistadio
I fustellati sono sottoposti a lavaggio intemedio e finale, per eliminare accuratamente qualsiasi residuo, e successivamente asciugati. Il processo inizia con un lavaggio intermedio di 10 minuti, durante il quale i residui di olio vengono eliminati con la sequenza lavaggio – risciacquo – soffiatura a impulsi. Per la fase di lavaggio è stato aggiunto un prodotto delicato nella prima vasca, applicato durante la fase a




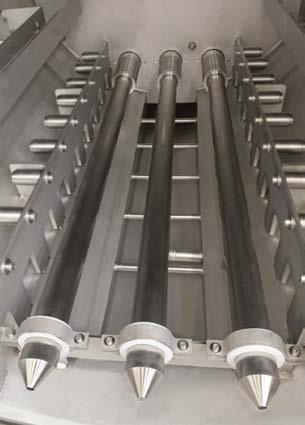
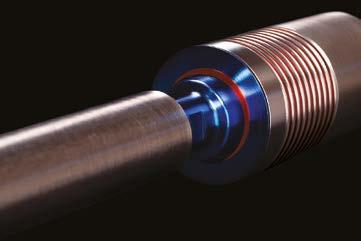

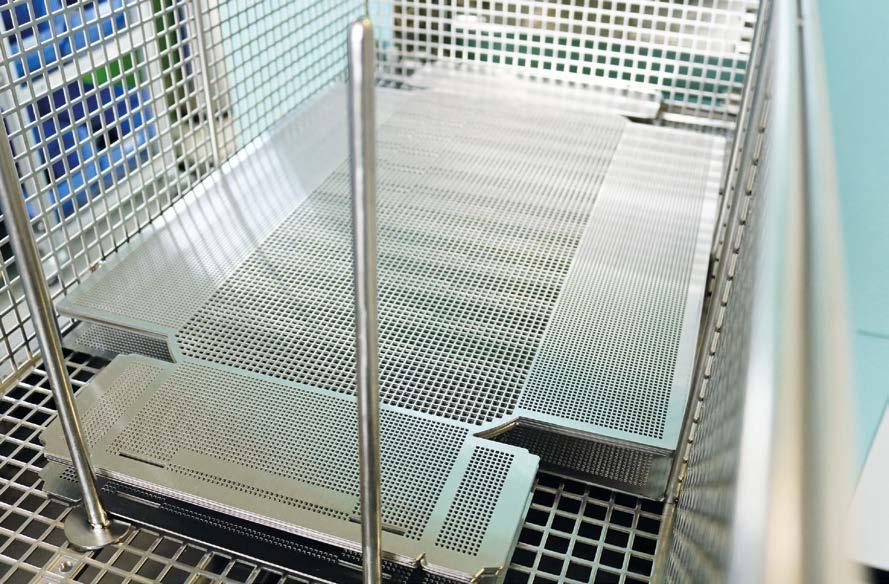
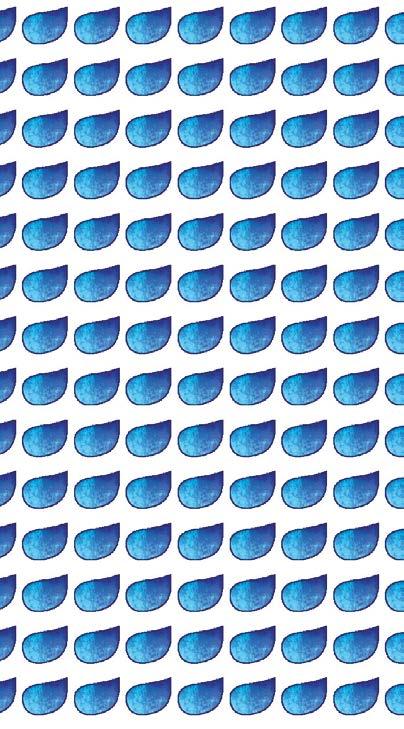
© MAFAC Get more from water
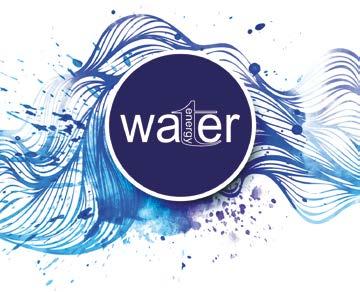
Processing residues such as oil or swarf have been carefully removed and surfaces are absolutely dry. I residui di lavorazione come oli o trucioli sono stati accuratamente rimossi e le superfici sono completamente asciutte.
process. The parts are then rinsed in the second tank. Afterwards, they are dried and sent to the straightening and grinding stations. A 30-minute final cleaning process follows to remove the new processing residues through a similar sequence. However, compared with the intermediate cleaning phase, a further rinsing stage is added to this process, taking place in the third tank. This is followed by a twostage drying operation with pulse blowing and hot air, as well as a double vacuum drying stage. The sheets pass through the drying and cleaning stations in densely packed batches. “Due to this, drying takes about as long as cleaning. Nevertheless, we continue to prefer this type of loading arrangement because we can have about 800 punched sheets per shift ready for delivery, thus meeting all our customers’ requests. The results are impeccable: the surfaces leaving our new system are free of any residues, absolutely dry, and free of corrosion,” states Martin Zepf with pride. spruzzo-immersione. Successivamente i componenti vengono risciacquati nella seconda vasca e indirizzati al processo di raddrizzatura e rettifica. A queste segue un lavaggio finale di 30 minuti, che rimuove i nuovi residui di lavorazione con una sequenza simile alla precedente. Tuttavia, rispetto al lavaggio intermedio, il lavaggio finale ha un’ulteriore fase di risciacquo nella terza vasca. A questa segue un’asciugatura a due stadi con soffiaggio a impulsi e aria calda, nonché con doppia asciugatura sottovuoto. Le lamiere passano nelle stazioni di lavaggio e asciugatura impilate in modo molto compatto. “In questo modo l’asciugatura richiede circa lo stesso tempo del lavaggio. Tuttavia manteniamo questa configurazione perché possiamo così avere circa 800 lamiere punzonate per turno pronte per la spedizione, soddisfando così tutte le richieste dei nostri clienti. I risultati sono impeccabili: le superfici sono prive di residui, perfettamente asciutte e senza segni di corrosione”, si rallegra Martin Zepf.
Turn key solutions for industrial wastewater treatment Design and manufacturing of plants and chemicals for industrial wastewater treatment Chemical-physical plants Sludge treatment and compactor systems Ion exchange demineralization systems and reverse osmosis systems Oil separators Filtering systems Batch type systems Flotation units Chemicals and spare parts for water treatment Technical service, support and maintenance of wastewater treatment plants
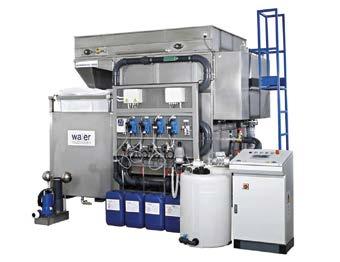
Beware of imitations, buy the original!
Walther Trowal: Perfect surface finishes for products made with additive manufacturing
Walther Trowal will display its mass finishing and coating technologies for 3D printed components at the next Formnext exhibition.
At the Formnext 2022 exhibition (Frankfurt am Main – Germany, 15-18 November), Walther Trowal presents two surface treatment technologies: mass finishing and coating of small components in rotary drums. In the AM post processing machine the surface of 3D printed components is refined by deburring, smoothing or polishing; in the Rotamat coater the component surface is coated with lacquer materials.
In one single operation the AM post processing machine AM 2 eliminates the surface roughness typical for components produced by additive manufacturing.
Con un’unica operazione la macchina di post-lavorazione additiva AM 2 elimina la rugosità superficiale tipica dei componenti realizzati con manifattura additiva.
Walther Trowal: perfetta finitura superficiale per prodotti realizzati con manifattura additiva
Durante la prossima edizione di Formnext, Walther Trowal esporrà le sue tecnologie di verniciatura e finitura in massa per componenti stampati in 3D.
Alla fiera Formnext 2022 (Francoforte – Germania, 15-18 Novembre), Walther Trowal presenterà due tecnologie di trattamento superficiale: finitura in massa e verniciatura di piccoli componenti in tamburi rotanti. Nella post-produzione della manifattura additiva i componenti stampati in 3D sono rifiniti con sbavatura, levigatura o lucidatura; nella macchina Rotamat la superficie del componente è verniciata con smalti.
© Walther Trowal
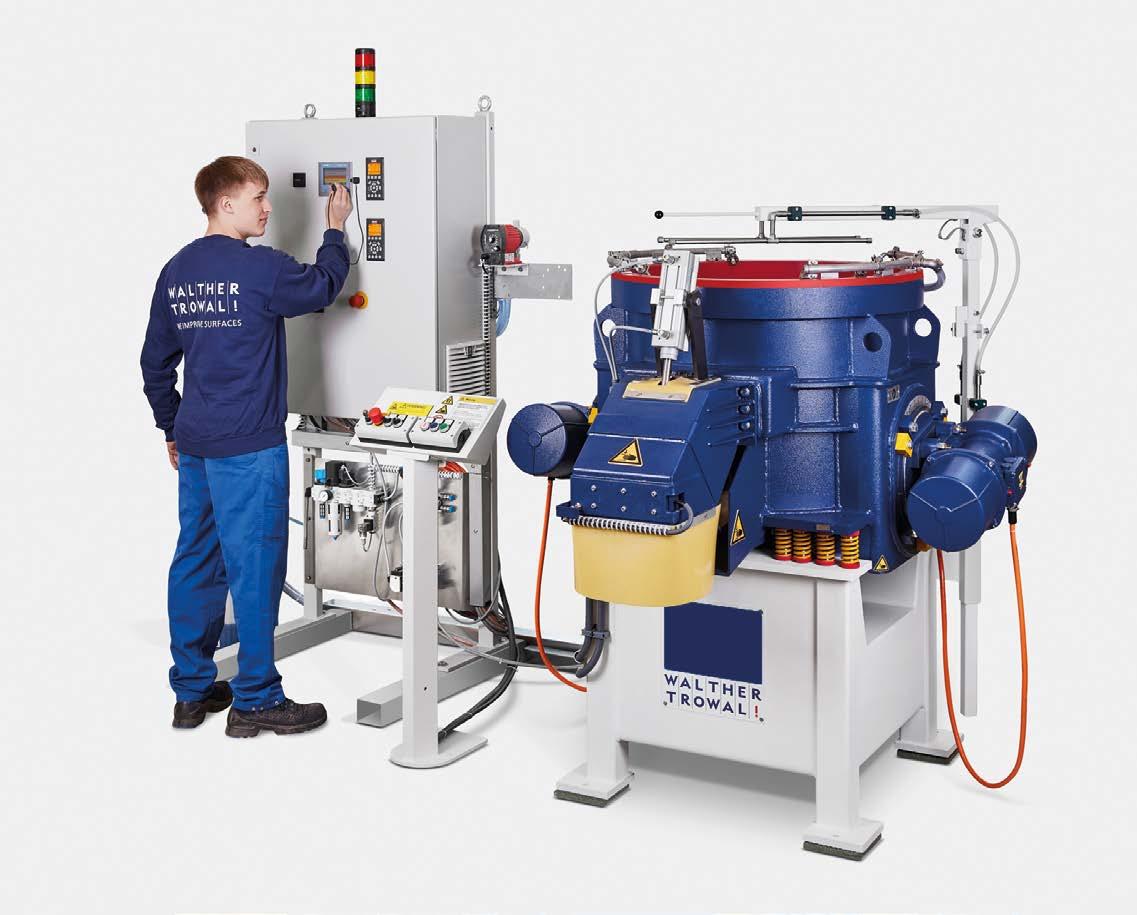
© Walther Trowal
The Rotamat R 60 applies a homogeneous lacquer coating on the surface of 3D printed components. This machine was specifically developed for small work piece batches, which are typical for additive manufacturing. Rotamat R 60 applica uno strato di vernice omogeneo sulla superficie dei componenti stampati in 3D. Questa macchina è stata appositamente sviluppata per lotti piccoli, tipici della manifattura additiva.
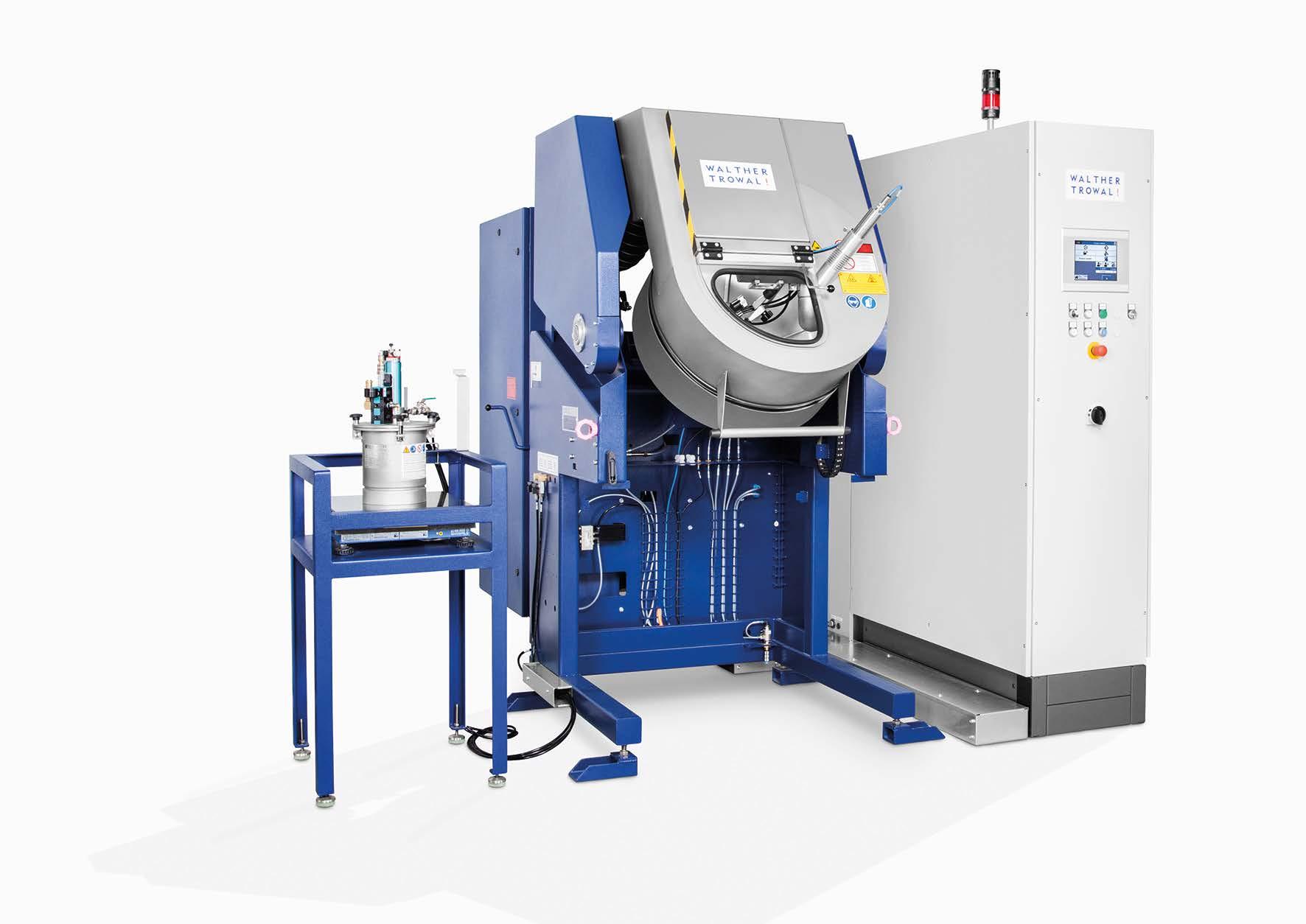
In one single operation the AM post processing machine, model A2, eliminates the high surface roughness that is typical for 3D printed components. Usually, such rough surfaces are caused by the so-called “staircasing” effect, markings from removed support structures and residual powder sintered onto the component surface. Walther Trowal developed the A2 machine specifically for treating complex metal components. Topology-optimized work pieces with intricate – frequently bionic – shapes cannot be finished manually with consistent results. Mass finishing has proven to be the ideal technology for dealing with such challenging finishing applications. The constant “rubbing” of the grinding/polishing media against the work pieces is not only gentle but also produces a homogeneous surface finish. Moreover, La macchina di post produzione, modello A2, elimina con una sola operazione l’elevata rugosità superficiale tipica dei componenti stampati in 3D. Solitamente le superfici così rugose sono causate dal cosiddetto “effetto scalettatura”, ovvero i segni delle strutture di supporto e della polvere residua sinterizzata sulla superficie del manufatto. Walther Trowal ha sviluppato la macchina A2 appositamente per il trattamento di componenti metallici complessi. Infatti, i manufatti ottimizzati per la topologia con forme intricate – spesso bioniche- non possono essere finiti manualmente con risultati omogenei. La finitura in massa ha dimostrato di essere la tecnologia ideale per queste impegnative applicazioni. Lo “sfregamento” continuo del prodotto di smerigliatura/lucidatura sui componenti è delicato e garantisce una