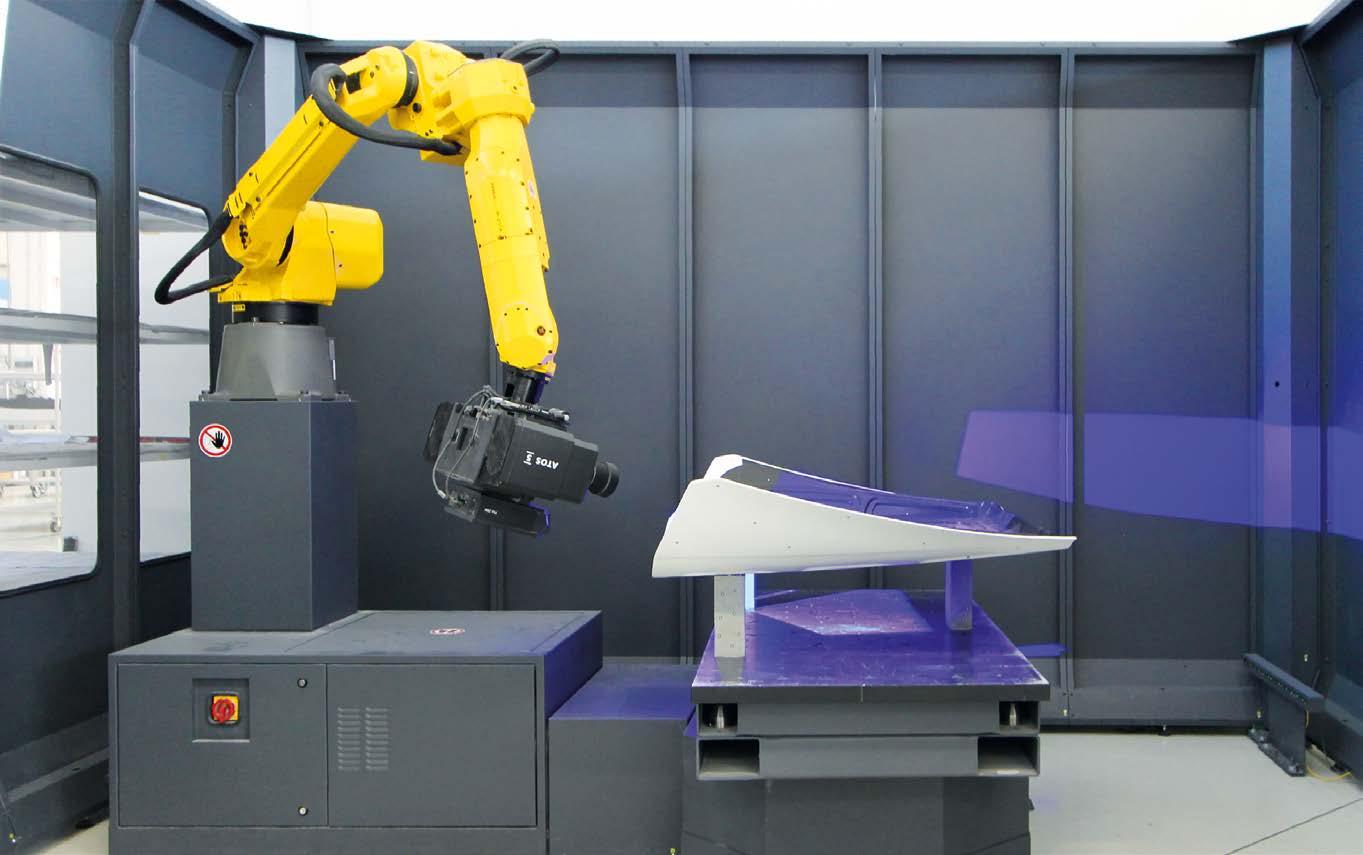
12 minute read
TECHNOLOGY OVERVIEW
A cleaning tunnel suitable for components with various geometries: C.P.C. Group’s challenge
C.P.C. Group is a manufacturer of customised automotive and racing components in composite materials. Continuously investing in innovative technologies to optimise its processes, it chose to turn to Teknox for an ambitious project: a cleaning tunnel that would be suitable for all the part shapes it handles and that would integrate perfectly into its workflow.
The automotive sector has several souls. High-end and racing cars, in particular, are characterised by a customisation degree that calls for constant and total collaboration among all parties involved in their design and manufacture, in order to adapt production processes to the needs of individual components.
Un tunnel di lavaggio adatto a componenti con differenti geometrie: la sfida di C.P.C. Group
C.P.C. Group è un’azienda specializzata nella produzione customizzata di componenti per il settore automotive e racing in materiale composito. Caratterizzata da continui investimenti in tecnologie innovative per ottimizzare i propri processi, ha scelto di rivolgersi a Teknox per un ambizioso progetto: un tunnel di lavaggio che fosse adatto a tutte le geometrie di pezzi lavorati dall’azienda e che si integrasse perfettamente all’interno del processo produttivo.
Il settore automotive include diverse anime al proprio interno. Le vetture di alta fascia e da corsa sono caratterizzate da livelli di personalizzazione che necessitano del costante confronto e della totale collaborazione di tutte le aziende coinvolte nella loro progettazione e fabbricazione, al fine di adeguare i processi produttivi alle necessità dei singoli componenti.
A component produced by C.P.C. Group. Un componente prodotto da C.P.C. Group.
© ipcm © ipcm
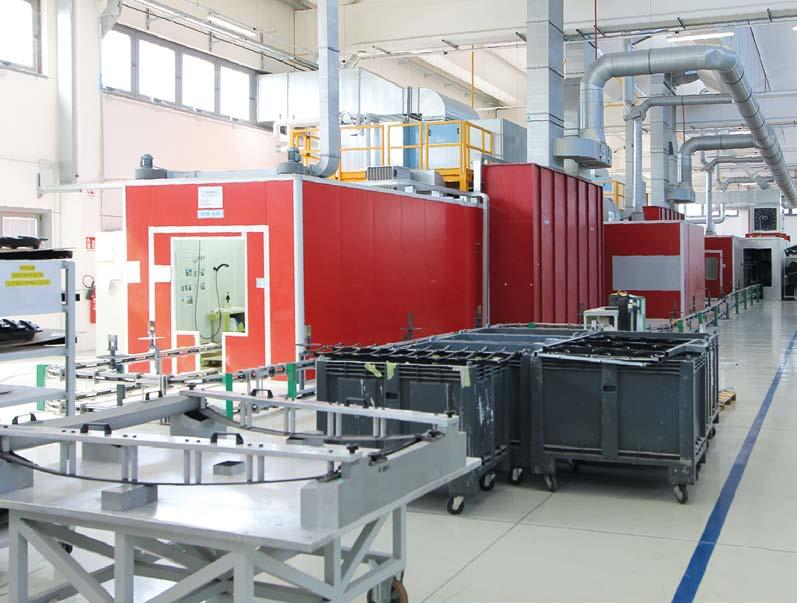
Some equipment manufactured in-house by C.P.C. Group and one of the coating plants available to the company. Alcune delle attrezzature costruite internamente da C.P.C. Group e uno degli impianti di verniciatura a disposizione dell’azienda.
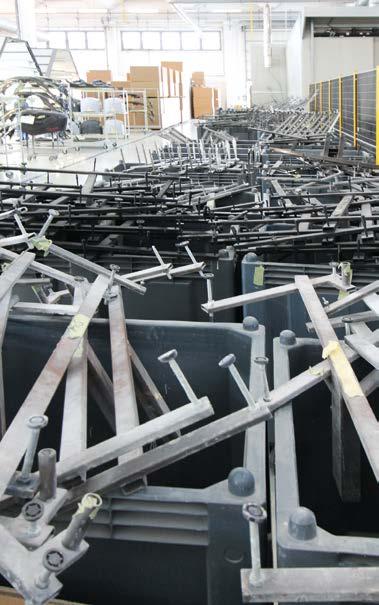
Leveraging its two strengths, namely innovation and continuous research into technologies aimed at optimising its operations, C.P.C. Group (Modena, Italy) has positioned itself in the automotive and racing market as a trusted partner capable of responding quickly to all industry requirements. C.P.C. Group is indeed an innovative company that for over sixty years has distinguished itself in the field of prototyping and machining of composite materials for numerous interior and exterior components of high-end vehicles, such as doors, front and rear wings, bonnets, tailgates, OPT carbon look parts, and complete chassis for various sectors, including automotive, racing, industrial, and aeronautics, thanks to the quality and flexibility of its production. “With its R&D expertise in composite materials and structural design, C.P.C. contributes to the success of its customers in various markets. For us, the art of perfection is the ability to think creatively about new technologically advanced solutions as a response to the increasingly complex and specific requirements of ever-changing production sectors:” this is how C.P.C Group describes itself on its website. It has about 850 employees working in four plants and a production capacity of 150,000 finished parts per year. In order to meet the quality standards imposed by its customers, up Sfruttando i suoi due punti di forza, ovvero l’innovazione e la continua ricerca di tecnologie per ottimizzare i propri processi produttivi, C.P.C. Group (Modena) si è posizionata nel mercato automotive e racing come un partner di fiducia e capace di rispondere rapidamente a tutte le esigenze del settore. C.P.C. Group è un’innovativa azienda che da oltre sessanta anni si distingue nel settore delle prototipazioni e delle lavorazioni di materiali compositi di parti interne ed esterne per autoveicoli di alta gamma come portiere, parafanghi anteriori e posteriori, cofani, portelloni, parti OPT in carbon look e telai completi per vari settori quali automotive, racing, mercato industriale e aeronautico grazie alla qualità e alla flessibilità della propria produzione. “Grazie alla propria esperienza nella ricerca e nello sviluppo in materiali compositi e nel design strutturale, C.P.C. contribuisce al successo dei propri clienti in svariati settori di mercato. L’arte della perfezione è per noi la capacità di pensare in modo creativo a nuove soluzioni tecnologicamente avanzate come risposta alle esigenze sempre più complesse e specifiche di settori produttivi in continua evoluzione”, si descrive così sul proprio sito web C.P.C Group – azienda con circa 850 dipendenti suddivisi su quattro stabilimenti e che è in grado di raggiungere una capacità produttiva di 150.000 pezzi finiti all’anno.
© ipcm
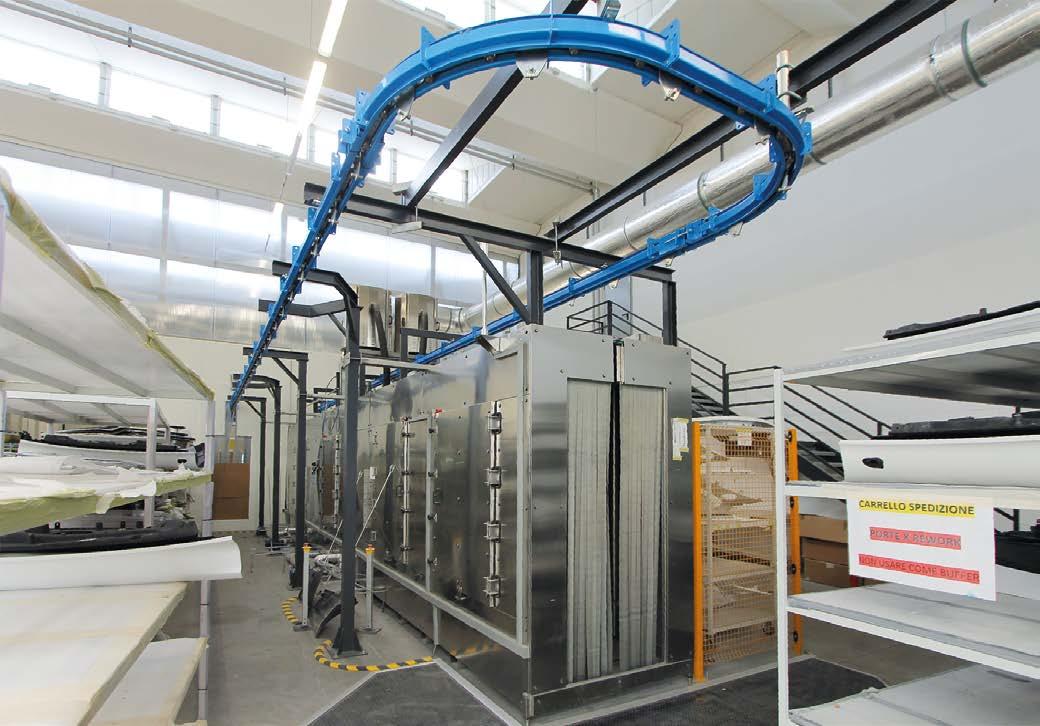
The one-rail overhead conveyor. Il convogliatore aereo monorotaia.
until recently it implemented manual cleaning operations to remove sanding dust residues from its components. However, this slowed down production. This is why it relied on Texnox (Prunaro di Budrio, Bologna, Italy) to install a spray cleaning tunnel suitable for its workflow and capable of efficiently cleaning all the parts it manufactures completely in-house, characterised by several different geometries.
C.P.C.’s growth through innovation and far-sightedness
Established in 1958 as Modelleria C.P.C., a small artisan company specialising in the creation of wooden foundry patterns processed and planed by hand by thirty operators, it has gradually differentiated and expanded its activity. In the 1990s, it was one of the first Italian companies to specialise in the use of 3D design software, also equipping itself with 5-axis CNC milling machines and implementing stereolithography and sintering for use in wind tunnels. The company therefore changed its name to C.P.C. S.r.l., in order to reflect the radical Al fine di rispettare gli standard qualitativi imposti dai propri clienti, l’azienda attuava delle operazioni di pulizia manuali per eliminare i residui di polvere di carteggiatura dai propri manufatti, che però rallentavano la produzione. Affidandosi a Texnox, azienda di Prunaro di Budrio (BO), ha perciò voluto installare un tunnel di lavaggio a spruzzo adatto alla propria produzione e in grado di pulire efficientemente tutti i pezzi dalle molteplici geometrie realizzati interamente dall’azienda.
La crescita di C.P.C. attraverso innovazione e lungimiranza
Fondata nel 1958 come Modelleria C.P.C., una piccola ditta artigianale specializzata nella creazione di modelli per fonderia in legno lavorati e piallati manualmente da trenta operatori, ha successivamente differenziato e ampliato la propria attività. Negli anni Novanta fu una delle prime aziende italiane a specializzarsi nell’utilizzo di programmi di progettazione 3D, dotandosi inoltre di fresatrici a controllo numerico a 5 assi e introducendo la stereolitografia e la sinterizzazione per l’utilizzo in galleria del vento. L’azienda
transformation brought about by its new management and its more innovative and dynamic production flow, focused on prototyping and machining of metals and composite materials for the automotive sector, especially Formula 1. The far-sighted decision to invest from the outset in state-of-theart machinery such as Stratasys and 3D System plants, in advanced personnel training, and in new, young, and qualified human resources, has enabled C.P.C. to grow steadily and in a structured manner, thus becoming globally recognised for its technical-professional and economic competitiveness. With the aim of further differentiating its target markets and specialising in additional sectors, the company then opened the C.P.C. Engineering division in 1998, the C.P.C. Protoservice division in 2003, and C.P.C. Compositi in 2007. “We are one of the few European companies capable of carrying out a complete manufacturing cycle of parts in composite materials with any geometry, working alongside our customers from design to delivery and part’s installation on vehicles. Our investments in cutting-edge technology and training have enabled us to become a world leader in the manufacture of products in which laminated or pressed composite cambiò dunque nome in C.P.C. S.r.l., in modo da riflettere la radicale trasformazione apportata dai nuovi dirigenti e la realtà produttiva più innovativa e dinamica incentrata sulla prototipazione e lavorazione di metalli e compositi per il settore automotive, specialmente Formula 1. La scelta lungimirante di investire fin da subito in macchinari di ultima generazione quali Stratasys e 3D System, in formazione avanzata del personale e in nuove risorse umane giovani e qualificate, ha permesso a C.P.C. di crescere in modo costante e strutturato – affermandosi a livello globale per la propria competitività tecnico-professionale ed economica. Con lo scopo di differenziare ulteriormente i propri mercati di riferimento e specializzarsi in ulteriori settori, l’azienda aprì poi la divisione C.P.C. Engineering nel 1998, la divisione C.P.C. Protoservice nel 2003 e C.P.C. Compositi nel 2007. “Siamo una delle poche realtà europee in grado di eseguire un ciclo completo di fabbricazione su materiale composito per pezzi di qualsiasi geometria, affiancando il cliente dal progetto fino alla consegna del particolare finito e all’installazione sul veicolo. I nostri investimenti in tecnologie all’avanguardia e in formazione avanzata ci hanno permesso di diventare un’azienda leader a livello mondiale nella realizzazione di
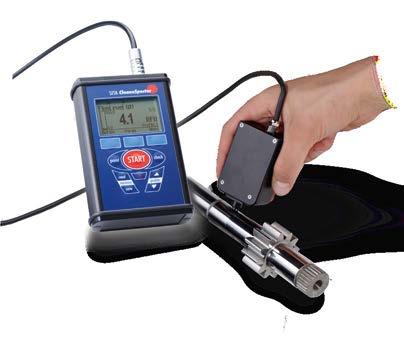
parts2clean 2022 Hall 4 Stand C18

Stable Assurance of Parts Cleanliness
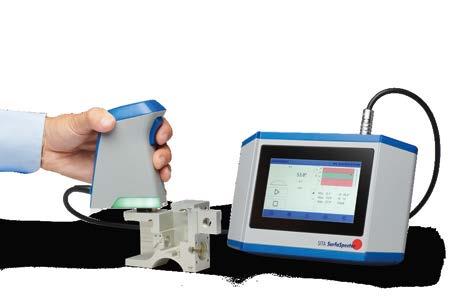
Monitoring Process Liquids Inspecting Parts Surfaces
material parts are combined with mechanical elements,” says Fabio Torelli, the Painting Division Manager of C.P.C. Group. “Using the most advanced technologies and materials available on the market, C.P.C. creates solutions with excellent performance, capable of meeting customer needs in newer and newer and increasingly precise ways.”
C.P.C. Group now produces components with different dimensions and geometries for major Italian automotive brands including Ferrari, Lamborghini, and Maserati. produzioni in cui particolari in materiale composito laminati o fabbricati attraverso la pressa sono abbinati a parti meccaniche”, esordisce Fabio Torelli, Direttore Painting Division di C.P.C. Group. “Utilizzando le tecnologie e i materiali più all’avanguardia disponibili sul mercato, C.P.C. ha saputo creare soluzioni dalle prestazioni eccellenti, capaci di rispondere in modo nuovo e sempre più preciso ai bisogni dei clienti”.
Una produzione flessibile, diversificata e personalizzabile
C.P.C. Group produce oggi componenti dalle dimensioni e geometrie differenti per i principali brand del settore automobilistico italiano, tra cui Ferrari, Lamborghini e Maserati.
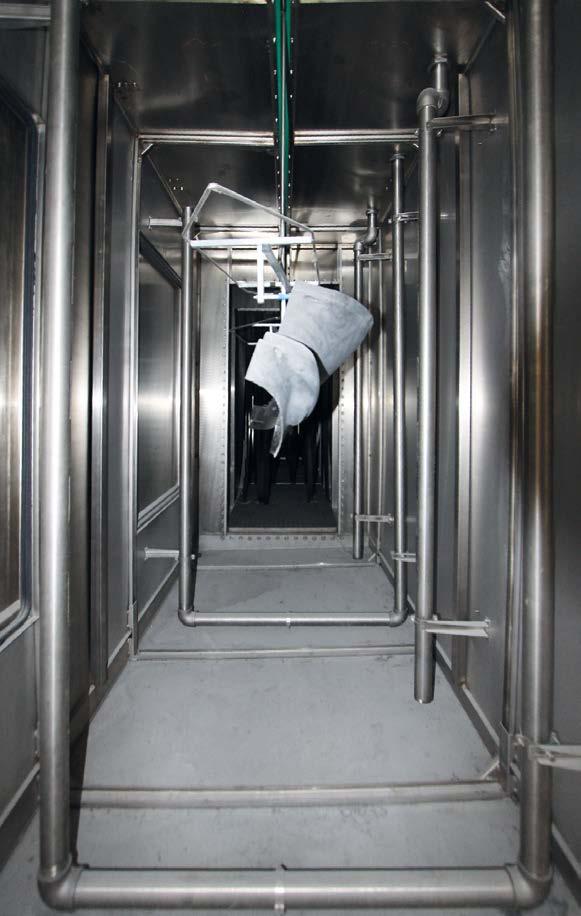
© ipcm
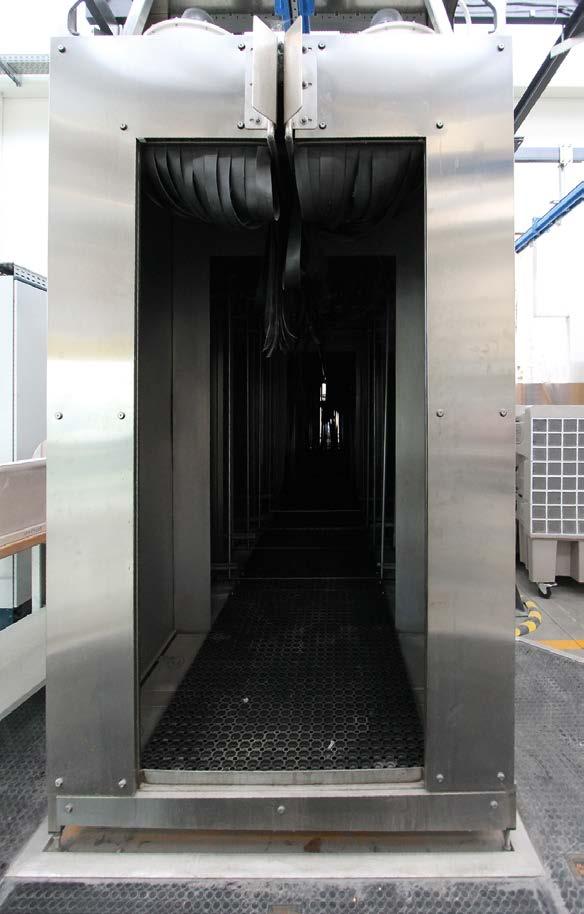
The entrance to the cleaning tunnel designed and built by Teknox. L’ingresso del tunnel di lavaggio progettato e costruito da Teknox.
© ipcm
Automotive parts inside the cleaning tunnel. Particolari per il settore automotive all’interno del tunnel di lavaggio.
“Carbon moulding takes place in our headquarters in Modena, which also deals with machining processes: we have an ever-evolving pressing department, five clean rooms for lamination, a large bonding area, and a wide area devoted to trimming. We listen to requests, we have our technical department design the parts based on the 3D models received from customers, and then we manufacture them, building finished components ready to be assembled with the other car parts,” explains Torelli. In addition, in order to provide a complete service, the company has created a Painting Division with more than 200 operators, performing both manual and robotised processes1 .
The need for a repeatable cleaning cycle even on customised parts
“All of our parts must meet high quality standards. This means we must carry out multiple cleaning operations, in order to eliminate any defects that might compromise their high performance and aesthetic levels. As major players in the industry, our customers demand imperfection-free components,” Torelli states. In the past, the company used articulated robots to clean its components prior to coating, in order to remove carbon dust generated by grinding and abrasion as well as sanding dust. However, due to the variety of dimensions and shapes of the parts handled, additional manual cleaning operations were sometimes required, such as rubbing and brushing with damp cloths to ensure that contaminants were also removed from deep cavities or other difficult-to-reach areas. “Robots are extremely efficient, but we are required to supply customised products: therefore, in some specific cases, automated cleaning had to be followed by further manual operations. However, we wanted to speed up this production stage and achieve process repeatability and quality consistency. When we acquired a new building for our coating department, therefore, we decided to work with Teknox to design and build a spray tunnel meeting all our cleaning needs and able to subsequently send the dried components to our paint booths in an automatic way”, indicates Torelli.
The spray tunnel’s features
Featuring an inlet opening with a size of 2,000 millimetres in height by 800 millimetres in width, this 16-metre-long tunnel has been specifically upgraded to handle plastic and carbon parts for any
1 Our article on painting automation at C.P.C. will be published in the ipcm® _ International Paint&Coating Magazine issue no. 78, due out in November 2022. “Lo stampaggio del carbonio avviene nella storica sede di Modena, dove hanno luogo anche le lavorazioni meccaniche: abbiamo un reparto in evoluzione per la pressatura, cinque clean-room per la laminazione, una vasta area di incollaggio e un’ampia area dedicata alla rifilatura dei componenti. Ascoltiamo le richieste del cliente, progettiamo insieme al nostro ufficio tecnico i componenti secondo il 3D ricevuto dal cliente e poi li fabbrichiamo, costruendo il particolare finito e pronto per essere assemblato con gli altri componenti del veicolo”, spiega Torelli. Inoltre, al fine di fornire un servizio completo, l’azienda ha creato una Painting Division con circa duecento operatori utilizzando sia processi manuali sia robotizzati1 .
La necessità di un ciclo di lavaggio riproducibile anche con manufatti customizzati
“Tutti i nostri pezzi devono soddisfare elevati standard qualitativi, che ci impongono di effettuare molteplici operazioni di pulizia al fine di eliminare eventuali difetti che potrebbero incidere negativamente sulle prestazioni dei manufatti e comprometterne l’alto valore estetico. I nostri clienti, essendo i maggiori protagonisti dell’industria, richiedono componenti senza imperfezioni”, commenta Torelli. L’azienda utilizzava robot antropomorfi per le operazioni di pulizia dei propri componenti, al fine di rimuovere la polvere di carbonio generata da molatura ed abrasione e la polvere di carteggiatura, preparandoli così alla successiva fase di verniciatura. Tuttavia, a causa delle differenti dimensioni e geometrie dei pezzi, era necessario a volte effettuare delle ulteriori operazioni di pulizia manuali, strofinando la superficie e spazzolandola con dei panni umidi per assicurarsi di aver eliminato le contaminazioni anche da cavità profonde o altre aree difficilmente raggiungibili dai robot. “I robot sono estremamente efficienti, ma i clienti richiedono manufatti personalizzati, pertanto in alcuni casi specifici le operazioni di pulizia automatizzate devono essere seguite da ulteriori interventi manuali. Volevamo però velocizzare questa fase della nostra produzione e ottenere una riproducibilità delle operazioni di pulizia e una qualità costante. Quindi, quando abbiamo acquisito un nuovo stabilimento per il reparto di verniciatura, abbiamo deciso di collaborare con Teknox per la progettazione e realizzazione di un tunnel di lavaggio a spruzzo predisposto per un ciclo di pulizia che fosse adatto a tutte le nostre esigenze e che potesse traslare automaticamente i componenti asciugati verso le cabine di verniciatura”, aggiunge Torelli.
Caratteristiche del tunnel di lavaggio a spruzzo
Il tunnel, lungo 16 metri e con una bocca di ingresso di 2.000 millimetri in altezza per 800 millimetri in larghezza, è stato specificamente aggiornato per trattare particolari in plastica e carbonio per qualsiasi settore, come
1 L’articolo sull’automazione della verniciatura in C.P.C. sarà pubblicato sulla rivista ipcm®_International Paint&Coating Magazine n. 78, in uscita a novembre 2022.