
15 minute read
FOCUS ON TECHNOLOGY
SPECIAL ISSUE ON ACE & OFF ROAD VEHICLES
Impianto di verniciatura “cartesiano” e nuovo processo di pretrattamento per quintuplicare la resistenza alla corrosione. Alpego: quando la chimica conta.
Alessia Venturi ipcm®
La resistenza alla corrosione di un rivestimento non è mai un one-man show, bensì è determinata da un lavoro di squadra fra vari elementi di un ciclo di verniciatura. Ne è ben consapevole Alpego Spa, azienda leader sui mercati internazionali nella produzione di macchine agricole. Il nuovo ciclo di pretrattamento messo a punto da ALIT Technologies con prodotti Alufinish, combinato con una linea di verniciatura fuori dagli schemi ma perfettamente funzionale alle esigenze di Alpego, ha consentito a quest’ultimo di quintuplicare il risultato di resistenza in nebbia salina.
Una delle machine agricole incluse nella gamma di prodotti Alpego.
© ipcm
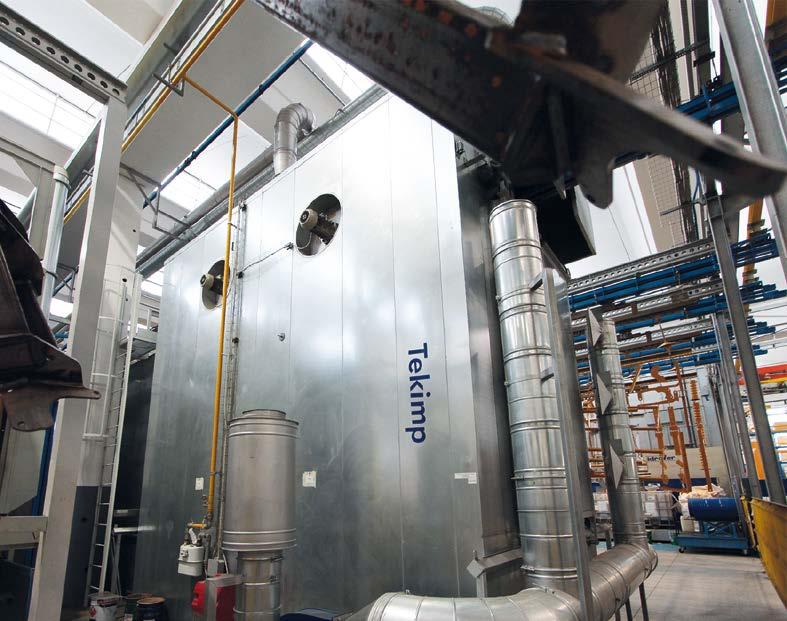
Per problematiche impiantistiche, di sistemi di verniciatura, di resistenze in esterno della finitura e – non da ultimo – di sostenibilità della verniciatura, il settore ACE, ossia quello delle macchine agricole, movimento terra e da cantiere è assimilabile a quello dell’auto. Non solo il mercato delle macchine pesanti e dei veicoli off road richiede ormai finiture con una qualità estetica “da carrozzeria” paragonabili a quelle realizzate dagli OEM dell’auto, ma il tema della durata del rivestimento e della sua resistenza meccanica, chimica e alla corrosione è centrale tanto quanto nel settore automotive. Se i reparti di verniciatura tipicamente utilizzati nelle due industrie non sono fra loro paragonabili, è pur vero che i temi di sostenibilità, efficienza energetica, impatto ambientale dei sistemi vernicianti utilizzati sono parimenti importanti, anche perché nel settore ACE le masse metalliche in gioco sono molto grandi e questo richiede accorgimenti impiantistici molto diversi rispetto a quelli di un classico paintshop automotive. Per entrambi i settori, comunque, il processo chiave ai fini della durata del rivestimento è il pretrattamento della superficie. Solo una superficie perfettamente disossidata, pulita, passivata e con la corretta rugosità superficiale può garantire un’adesione eccellente del film di verniciatura e aumentarne la resistenza alla corrosione. È chiaro che, una volta trovato il pretrattamento ideale, esso vada poi inserito in un contesto di processo dove i prodotti vernicianti e la loro applicazione avvengono nel modo più efficiente ed efficace possibile. L’esperienza di Alpego Spa, azienda di Almisano, Vicenza, che con le proprie macchine vuole ottimizzare la produzione agricola ascoltando le esigenze di un settore in constante evoluzione, in questo senso è paradigmatica. Dopo anni intensi di studio delle possibili soluzioni impiantistiche di verniciatura che hanno richiesto 7 visite alla fiera PaintExpo in Germania e innumerevoli viaggi in Europa per analizzare quali erano state le scelte
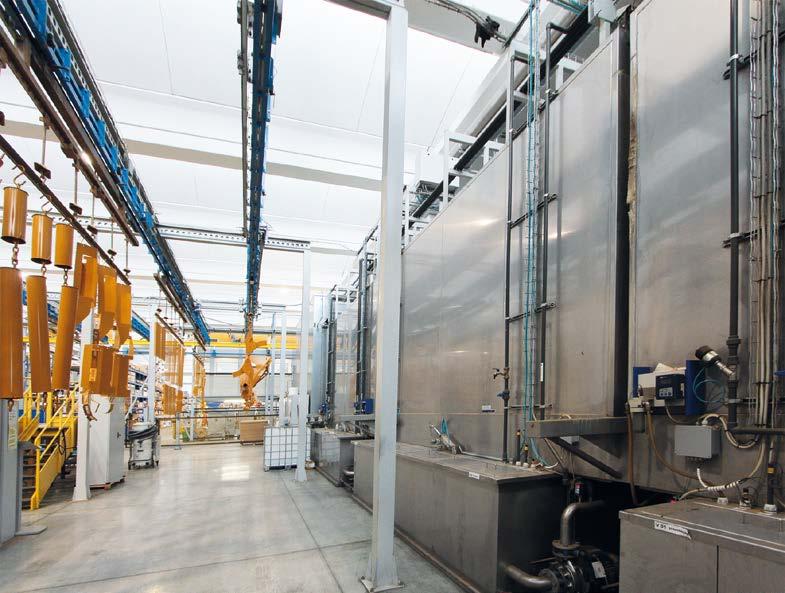
© ipcm
© ipcm
Vista generale del tunnel di pretrattamento e il forno di asciugatura della fase di pretrattamento
Componenti di machine agricole durante la verniciatura a polvere.
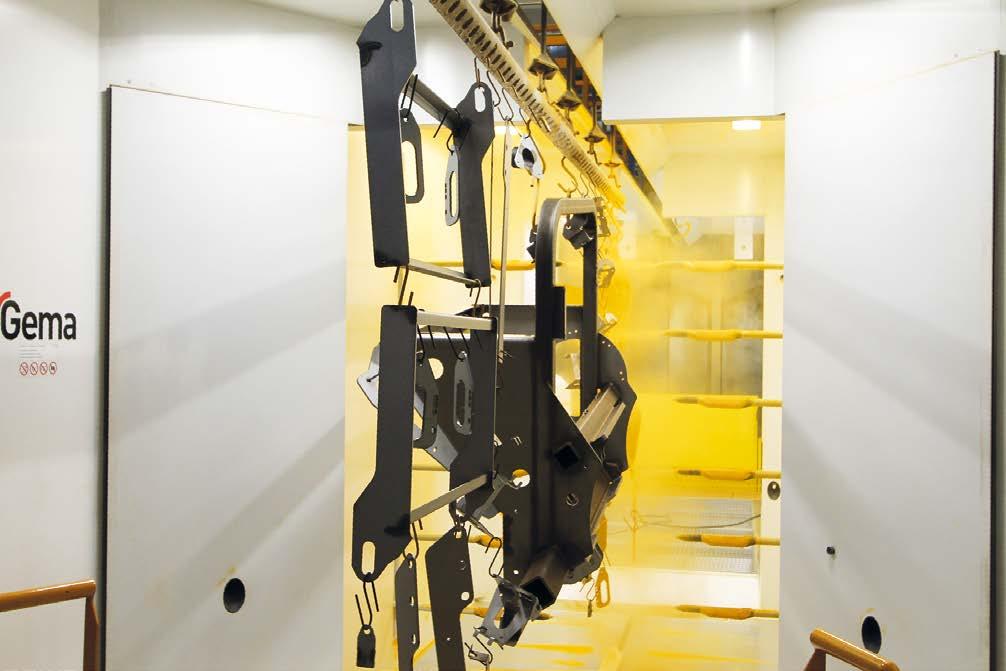
© ipcm
dei competitor, Alpego ha impiegato 4 anni di progettazione per arrivare finalmente, nel 2014, all’impianto di verniciatura perfetto. La collaborazione con il fornitore di prodotti di pretrattamento, Alit Technologies di San Bonifacio, Verona, che è distributore per l’Italia dei prodotti della tedesca Alufinish, è stata strategica per raggiungere gli obiettivi di resistenza alla corrosione.
Chi è Alpego
È nel cuore del Veneto, una delle regioni più ricche ed industrializzate d’Italia, ricoperta da vigneti e contornata dallo splendido panorama delle Dolomiti, che negli anni ’80 nasce Alpego come piccola azienda familiare e che tuttora rimane 100% di proprietà della famiglia Pegoraro ed è giunta oggi alla terza generazione. Trinciatrici, ripuntatori, dissodatori, fresatrici, seminatrici, concimatori, attrezzature per vigneto, erpici rotanti, coltivatori costituiscono la vasta gamma di prodotti Alpego, che produce 4000 macchine l’anno. Tutti i prodotti continuano ad essere ideati e progettati internamente per mantenere il completo know-how di ogni singolo progetto. Alpego reinveste il 4% del proprio fatturato in ricerca e sviluppo e vanta 40 brevetti e marchi attivi. Per una scelta di qualità ed affidabilità le macchine Alpego continuano ad essere prodotte internamente o avvalendosi di fornitori italiani di alto livello. Anche l’80% dei componenti acquistati è Made in Italy, mentre le lamiere decapate alto-resistenziali sono acquistate in Svezia, che è produttore leader del settore, e un altro 10% degli acquisti è fatto in Germania e Stati Uniti. Dalla sua fondazione Alpego vanta una crescita costante in tutti i mercati internazionali con un aumento a doppia cifra sia in termini di macchine prodotte che di crescita di fatturato, raggiungendo nel 2021 la soglia dei 40 Mln di Euro con 190 dipendenti. Oggi l’azienda è strutturata in tre stabilimenti che, in tutto, occupano 41.000 m2 di cui 15.000 coperti: • Almisano: la nuova sede dell’azienda dal 2012 che si sviluppa su oltre 21.000 m2. Qui si trovano gli uffici amministrativi, tecnici e commerciali; una vasta area per il montaggio, la linea di verniciatura e la spedizione delle macchine; il magazzino ricambi. • Gambellara: la sede storica dell’azienda che ospita la carpenteria con tutti i più moderni tagli laser, presse piegatrici e robot di saldatura. • Lonigo: uno stabilimento di assistenza all’assemblaggio che è stato da poco acquisito per poter aumentare la capacità produttiva. Alpego vanta una rete commerciale composta da innumerevoli importatori e concessionari, oltre che da due filiali europee Alpego France e Alpego UK.
Genesi di un impianto di verniciatura fuori dal comune
“Alpego ha sempre verniciato le macchine prodotte al proprio interno” esordisce Luciano Pegoraro, attuale titolare di Alpego insieme al fratello Giovanni. “La verniciatura è una fase troppo importante per demandarla a un fornitore esterno. Nella sede originale di Gambellara avevamo una linea di verniciatura a liquido tradizionale con trasportatore aereo, il classico “anello” con fosfosgrassaggio, asciugatura, doppia cabina di verniciatura per applicazione di primer e smalto, forno di cottura finale. Applicavamo un ciclo di verniciatura ad alto solido e, seppure fossimo in regola con le emissioni in atmosfera, l’obiettivo era passare ai prodotti idrosolubili. Tuttavia l’impianto così come era stato concepito non ce lo avrebbe consentito: troppi erano i parametri da monitorare e regolare per avere una verniciatura di qualità con i prodotti idrosolubili, il processo sarebbe stato incompatibile con quell’impianto. Inoltre, avevamo la necessità di aumentare la resistenza alla corrosione delle nostre macchine, considerando che molte di queste erano esportate via mare. Già con il vecchio impianto collaboravamo con Alit Technologies che ci forniva i prodotti di fosfosgrassaggio. Sui nostri pezzi, principalmente lamiera in ferro nero ad alto spessore (8-10 mm), dovevamo eseguire un decapaggio aggressivo per ottenere una superficie idonea alla verniciatura di qualità. L’unica alternativa sarebbe stata abbinare al pretrattamento chimico una fase di granigliatura controllata. Ma, ancora una volta, la linea non ce lo permetteva”. “Nonostante le svariate messe a punto del ciclo di pretrattamento, con i prodotti di verniciatura e con le condizioni impiantistiche di allora, non riuscivamo a superare le 170 ore di resistenza in nebbia salina ai manufatti Alpego” interviene Loris Rossi, CEO di Alit Technologies e distributore italiano dei prodotti Alufinish. “Il tunnel di pretrattamento presentava un grande problema di inquinamento dei risciacqui e la qualità di preparazione della superficie non era ulteriormente migliorabile senza modificare l’impianto”. “Per tutti questi motivi decidemmo nei primi anni Duemila che era necessario investire in un impianto
© ipcm
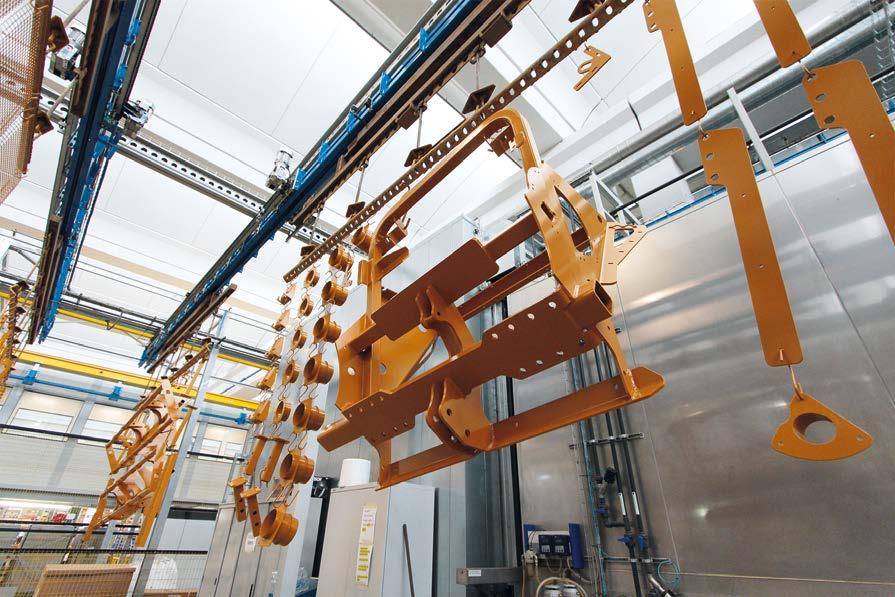
Componenti finite appesi alla linea di verniciatura progettata da Tekimp di Castelfranco Veneto, Treviso.
di verniciatura nuovo” prosegue Luciano Pegoraro. “Tuttavia non volevo installare di nuovo una linea tradizionale con convogliatore birotaia. Trovavo il layout di quelle linee troppo rigido per il nostro tipo di produzione. Inoltre, quel tipo di impianti occupano troppo spazio: infatti il primo progetto che mi sottoposero “mangiava” più di metà nel nuovo stabilimento di Almisano! Abbiamo dunque deciso per un cambiamento netto in varie aree della produzione. Innanzitutto abbiamo cambiato la materia prima: dal ferro nero, siamo passati all’acquisto di sola lamiera decapata, che compriamo principalmente in Svezia; abbiamo introdotto il taglio laser della lamiera in modo da eliminare quanto più possibile il problema dell’ossidazione sugli spessori alti; abbiamo specificato un ciclo di verniciatura a base acqua composto da primer epossidico e finitura acrilica bicomponente e pensato anche a una futura introduzione della verniciatura a polvere (che abbiamo poi effettivamente introdotto). Infine, abbiamo trovato a PaintExpo lo spunto per non progettare più un impianto ad anello bensì una linea a stazioni, con un concept completamente diverso dagli impianti tradizionali”.
Luciano Pegoraro (a sinistra) con Loris Rossi di fronte a svariate macchine agricole Alpego pronte per essere spedite in tutto il mondo.

© ipcm
Quintuplicare la resistenza alla corrosione con la chimica giusta applicata con l’impianto adatto Uno scenario nuovo e sfidante
Tekimp di Treviso, parte del gruppo Rimor, ha progettato per Alpego un impianto compatto e funzionale che Pegoraro definisce “cartesiano” e senza accumuli, per sottolineare l’assenza del trasportatore tradizionale in favore di una movimentazione con carrelli che conducono i pezzi alle stazioni di trattamento di competenza, seguendo un percorso preimpostato ma indipendente l’uno dall’altro. L’impianto ha una granigliatrice modulare in linea, che esegue una granigliatura fine dei pezzi ad alto spessore (8-10 mm). Questi pezzi subiscono una doppia fase di pretrattamento, meccanico e poi chimico con il nuovo ciclo Aufinish, mentre i pezzi in lamiera sottile subiscono il solo pretrattamento chimico. Ad ogni bilancella può essere assegnato un diverso grado di granigliatura. Il ciclo di pretrattamento Alufinish fornito da Alit Technologies comprende una prima fase di sgrassaggio fortemente alcalino a 55°C x 10 minuti; un doppio stadio di risciacquo con acqua di rete; una fase di passivazione nanotecnologica; un risciacquo con acqua demineralizzata e asciugatura. Con questo nuovo ciclo di pretrattamento, combinato con i prodotti vernicianti scelti, Alpego è riuscita a raggiungere un valore di resistenza in nebbia salina compreso fra le 500 e le 700 ore, ma soprattutto ha ottenuto una grande costanza di risultato. “È stato un grande lavoro di squadra” commenta Luciano Pegoraro. “Alit ci assicurava già un buon risultato di pretrattamento con le difficili condizioni impiantistiche della linea precedente: sul nuovo impianto il risultato è al top!”. “Alpego si è fidata molto di Alit, abbiamo innescato un buon rapporto di collaborazione già con la vecchia linea, anche grazie alla vicinanza fra le loro sedi e quella di Alit” prosegue Loris Rossi. “I 4 anni di progettazione dell’impianto sono stati anni di crescita tecnica reciproca e di scambio di conoscenze ed esperienze. Alit si è sentita valorizzata da Alpego e abbiamo messo in campo una collaborazione stretta per mettere a punto il ciclo chimico”. “Sicuramente qualche modifica al ciclo è stata fatta anche in corso d’opera ma la strada tracciata in fase di progettazione si è rivelata corretta, sia quella dell’impianto sia quella della chimica” commenta Pegoraro.
Lavorare con il nuovo impianto è stato per Alpego un cambiamento totale di paradigma operativo: dal verniciare la macchina completa, l’azienda vicentina ha iniziato a verniciare i singoli componenti. “Inizialmente l’impianto sembrava gigantesco rispetto a quello che avevamo prima, quindi abbiamo avuti i nostri problemi a farlo funzionare bene!” conclude Pegoraro. “Per i primi 4 anni abbiamo verniciato solo a liquido, poi nel 2018 abbiamo introdotto la finitura a polvere, in mano unica, installando una cabina automatica Gema, separando i componenti che potevano essere verniciati a polvere da quelli che non lo potevano essere. Il nuovo impianto di verniciatura è molto complesso dal punto di vista del software di programmazione della produzione: avviamento e industrializzazione sono stati difficili. Adesso, a distanza di quasi 8 anni l’impianto è saturo e ne avremmo bisogno di uno nuovo. Oltre all’impianto di verniciatura, negli ultimi anni abbiamo realizzato investimenti di 7 mil di euro in macchinari produttivi, tutti Industry 4.0. siamo pronti per una nuova sfida nella verniciatura!”.
INNOVATIONS: PRESENT&FUTURE
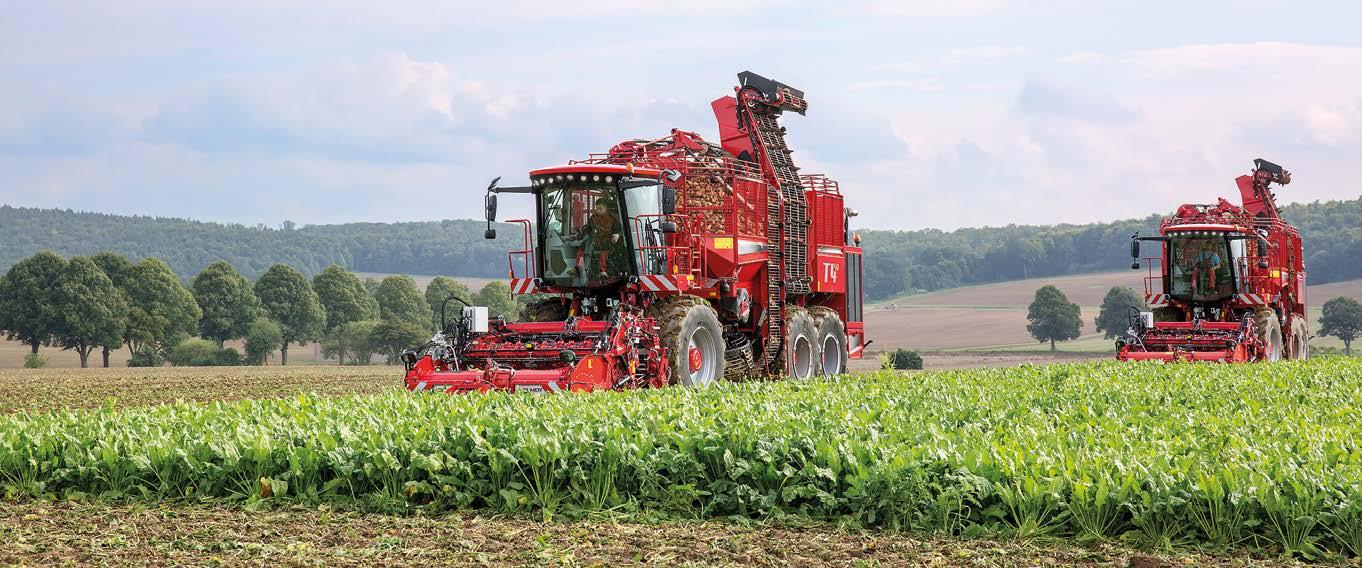
SPECIAL ISSUE ON ACE & OFF ROAD VEHICLES
Proteggere e abbellire le macchine agricole, una sfida ad alta tecnologia
a cura di SAMES KREMLIN
Meylan – Francia marketing@sames-kremlin.com
I produttori di macchine agricole progettano macchine in grado di resistere agli agenti atmosferici, alle aggressioni chimiche e meccaniche, ecc. Oggi devono offrire anche una verniciatura con finiture minuziose come quelle delle automobili. Questa duplice sfida richiede l’uso di apparecchiature applicative ad alta tecnologia.
Chi avrebbe mai pensato che un giorno le vernici metallizzate avrebbero fatto la loro comparsa sulle macchine agricole? Ma è quello a cui stiamo assistendo ora: i colori grigio chiaro, grigio antracite e rosso metallizzato sono utilizzati su trattori e rimorchi, ma possono anche essere personalizzati. La lucentezza delle superfici verniciate è pari a quella delle carrozzerie.
Combinare durata ed estetica, una sfida per i produttori di vernici
Questa ricerca estetica riguarda anche, in misura minore, mietitrebbiatrici, irrigatrici, attrezzature per la preparazione del terreno e per la semina. Le macchine agricole sono da sempre robuste e durevoli per resistere a sole, gelo, pioggia, polvere, urti, vibrazioni, aggressioni chimiche e talvolta nebbia salina. Adesso devono essere anche esteticamente apprezzabili. “È comprensibile che gli agricoltori la pensino così”, afferma Gilles Valbrecq, direttore delle vendite di SAMES KREMLIN in Francia. “L’acquisizione di una macchina agricola è un investimento che copre diversi decenni. La qualità delle finiture è una garanzia di serietà, una rassicurazione sulla durata della macchina e... un modo per apprezzarla, semplicemente”. Questi requisiti hanno portato allo sviluppo di nuovi riferimenti per i produttori di vernici, che non potevano offrire i loro soliti prodotti dedicati al mercato automobilistico. La composizione chimica, infatti, non avrebbe resistito alle condizioni ambientali del settore ACE. Hanno quindi ampliato le loro gamme per le macchine agricole, introducendo colori metallizzati ottenuti principalmente con vernici liquide.
Indurenti, particelle di zinco o titanio...
Tuttavia la composizione fondamentale della vernice, quella che ne garantisce la durata, non è cambiata. Si tratta per lo più di vernici bicomponenti che combinano una base (ad esempio una resina epossidica se si desidera la massima durata o una poliuretanica per una finitura impeccabile) e un indurente. Per rafforzare le proprietà
meccaniche del rivestimento, talvolta sono anche incorporate microparticelle di zinco o titanio. Questo mercato molto specifico si affida ad apparecchiature applicative altrettanto specifiche, che servono in primo luogo per prelevare i prodotti dal loro contenitore, fusto o latta. Successivamente i prodotti, in particolare gli indurenti dalle basi a due componenti, sono miscelati e dosati. Infine le apparecchiature li applicano a spruzzo sui pezzi, coniugando precisione, produttività, omogeneità dello spessore e del colore, basso impatto ambientale, ecc. SAMES KREMLIN, uno dei principali attori in questo mercato, basa la propria offerta su una vasta gamma di tecnologie collaudate provenienti da altri settori industriali: automotive, ovviamente, ma anche edilizia, aeronautica, trasporto ferroviario, arredamento, elettrodomestici, ecc.
Dalle pistole manuali alle linee industriali automatizzate
Nel segmento delle macchine agricole, SAMES KREMLIN rifornisce dai piccoli produttori di rimorchi fino alle aziende di livello mondiale. Ai primi offre pistole a spruzzo elettrostatiche manuali per la verniciatura ad altra produttività di pezzi piani di grandi dimensioni (gamma Airmix®) o di pezzi con geometrie complesse dove è necessario proteggere anche il più piccolo traferro (gamma Airspray). Nel secondo caso, invece, realizza linee industriali particolarmente innovative. Un esempio è un’installazione automatizzata nel Nord Europa che applica la vernice in polvere alle raccoglitrici di barbabietole. Comprende un nastro trasportatore a tappeto, una cabina per la verniciatura, un sistema di trasporto e recupero della polvere, un modulo per il cambio colore, le stazioni di pre-ritocco e ritocco e un forno di polimerizzazione. “Una linea di questo tipo permette di verniciare pezzi dalla forma semplice a un ritmo molto elevato”, afferma Christophe Denis-Bosio, Global Business Development Manager. “Inoltre, un sistema di riconoscimento e misurazione dei componenti posiziona le pistole alla distanza ottimale, senza necessità d’intervento umano”. Un altro esempio SAMES KREMLIN per l’applicazione di vernici liquide sono le quattro cabine installate su piattaforme per il trattamento dall’alto verso il basso di pezzi di grandi dimensioni. Da queste navicelle gli operatori possono monitorare i movimenti dei pezzi, oltre ad avere il completo controllo sulle linee di verniciatura, senza dover tornare a terra.
Pompaggio, miscelazione, spruzzatura; gli anelli chiave nella catena della vernice
Per misurare l’elevata tecnicità delle installazioni di verniciatura, la cosa migliore è descriverne le tre fasi principali: pompaggio, miscelazione e spruzzatura. Le basi e gli indurenti sono trasportati dal loro luogo di stoccaggio originale verso un miscelatore tramite pompe. L’indurente deve essere tenuto lontano da ambienti umidi, perché si cristallizzerebbe,
GLOBAL SOLUTIONS FOR WATER TREATMENT
with a complete service that includes system design manufacturing installation technical support chemicals
SPRAY BOOTHS WATER SLUDGE REMOVAL RESIN DEMINERALIZATION SYSTEMS REMEDIATION OF CONTAMINATED SITES BIOLOGICAL SYSTEMS BATCH TREATMENTS PHYSICAL-CHEMICAL SYSTEMS ADSORPTION FILTRATION REVERSE OSMOSIS MEMBRANE SYSTEMS EVAPORATORS BIOGAS BIOMASS SYSTEMS OIL SEPARATORS DESANDERS DESALINATION SYSTEMS PYROCHAR OTHER SYSTEMS CHEMICALS
attaccherebbe le guarnizioni della pompa e intaserebbe gli iniettori. SAMES KREMLIN ha eliminato questo rischio con la sua tecnologia Flowmax®, disponibile sul mercato da 25 anni in questa gamma di pompe: il soffietto brevettato isola completamente l’indurente dall’aria. Il secondo passaggio avviene nel miscelatore, in cui la base è combinata con un indurente. Proprio come in cucina, il corretto dosaggio degli ingredienti e la qualità della miscela sono determinanti per il risultato finale. La dosatrice elettronica Cyclomix™ di SAMES KREMLIN soddisfa questi requisiti, poiché prepara la quantità richiesta di vernice nelle giuste proporzioni. Rispetto alla miscelazione manuale, i vantaggi sono maggiori: ripetibilità dei parametri, nessun rischio di errore umano e perdite di prodotto ridotte al minimo. La vernice ottenuta mantiene caratteristiche costanti, garantendo la stabilità del colore e delle proprietà meccaniche delle motrici o dei rimorchi che escono dalla linea.
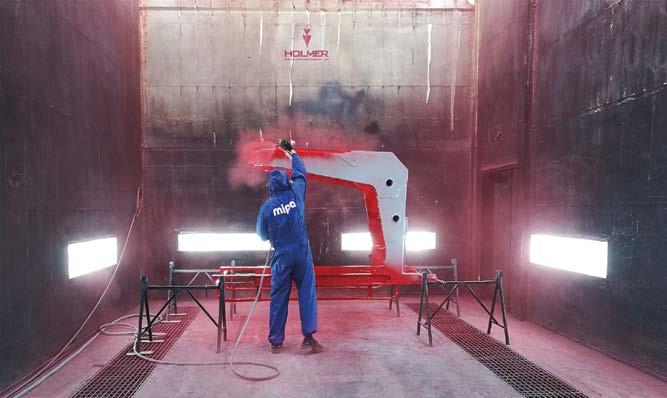
Goccioline e particelle di vernice caricate a 80.000 volt
Infine, la spruzzatura utilizza la tecnologia elettrostatica: le goccioline, o particelle di vernice, caricate elettricamente da un’unità ad alta tensione che può raggiungere gli 80.000 volt, sono attratte dai pezzi metallici da verniciare e vi si depositano. Lo strato risultante è più uniforme rispetto a una pistola manuale non elettrostatica, perché le particelle di vernice caricate si respingono e non si aggregano. La maggior parte della vernice finisce sul pezzo, senza disperdersi come farebbe con una pistola a spruzzo ad aria compressa. Questo conferisce un’“efficienza di trasferimento” - come viene chiamato - del 93% per la pistola a spruzzo elettrostatica manuale Nanogun Airmix® di SAMES KREMLIN. La ridotta quantità di prodotto perso riduce i costi, i volumi di rifiuti e le emissioni di COV, migliorando l’equilibrio ambientale della produzione. SAMES KREMLIN sta lavorando su questo tema anche con installazioni per vernici all’acqua. “Abbiamo già attrezzato diversi clienti. Generalmente applicano un primer a base solvente per una maggiore durata, seguito da una finitura all’acqua”, conclude Gilles Valbrecq.

Dall'alto:
- Applicazione con una pistola elettrostatica manuale per la verniciatura di componenti di ampie dimensioni con tecnologia ad alta produttività Airmix® .
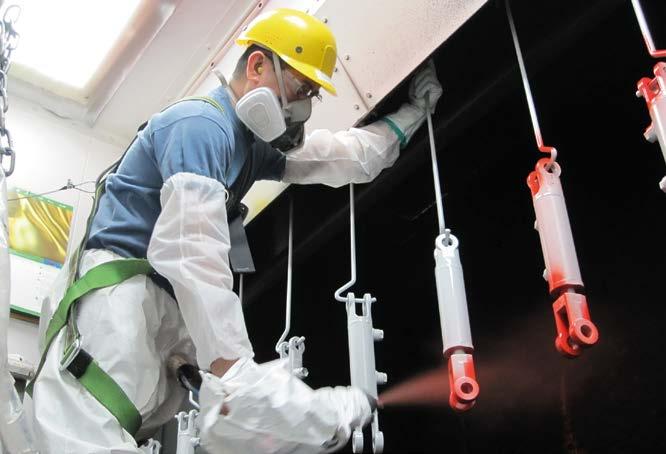
- Applicazione automatica di vernici in polvere.
- Applicazione con pistola elettrostatica.
© SAMES KREMLIN
© SAMES KREMLIN
© SAMES KREMLIN
