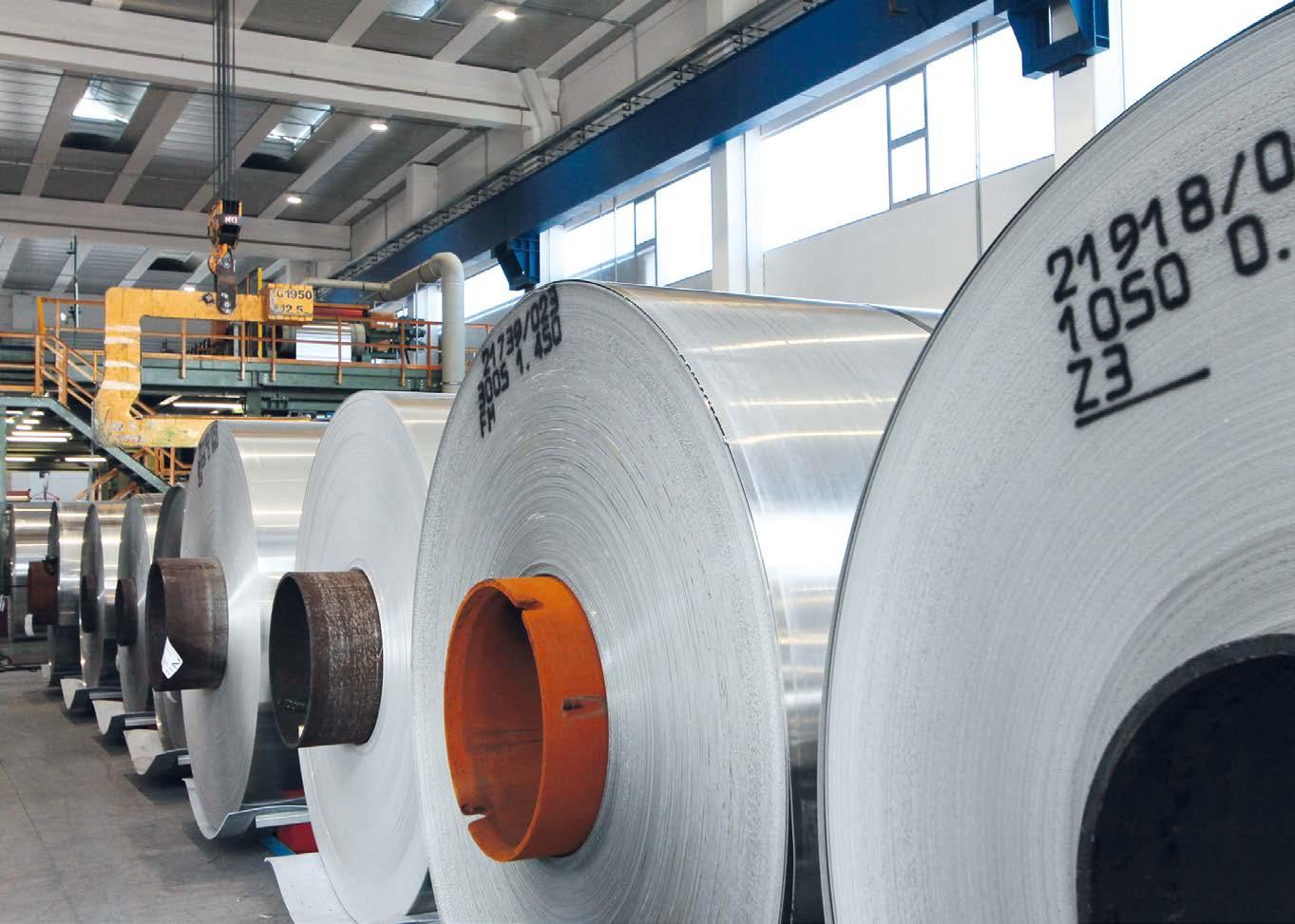
21 minute read
FOCUS ON TECHNOLOGY
Profilglass sceglie il riciclo e un sistema di trattamento acque avanzato per ridurre l’impatto ambientale dei processi di lavorazione dell’alluminio
Monica Fumagalli ipcm®
È possibile rendere la lavorazione dell’alluminio più sostenibile? Su questo delicato tema si interroga da tempo l’industria specializzata nella lavorazione di prodotti in alluminio e nelle sue leghe. Non è da meno Profilglass, società di Fano tra i leader internazionali del settore, che ha deciso di puntare sul riciclo e su una tecnologia di trattamento acque di ultima generazione sviluppata dalla società milanese CIE per trattare i contaminanti organici e inorganici provenienti da processi di finitura diversi.
Una delle principali sfide che l’industria dell’alluminio sta affrontando e dovrà affrontare con maggiore urgenza nei prossimi anni è rappresentata dalla necessità di abbattere l’impatto ambientale dei propri processi di lavorazione senza disattendere la domanda in continua crescita di questo materiale. Secondo i dati riportati dall’International Aluminium Institute1, nell’arco di un anno e in una fase economica resa oscillante dalla pandemia, la produzione di alluminio ha raggiunto i 65.325 milioni di tonnellate. Di fronte a volumi produttivi così elevati l’industria specializzata nella lavorazione e trattamento superficiale dell’alluminio sta cercando nuove strade per rendere i propri processi più sostenibili. Profilglass Spa, azienda di Fano (Pesaro e Urbino) che dal 1982 realizza profili, nastri, lamiere, bandelle, dischi, triangoli e laminati in alluminio e sue leghe, ha scelto la strada del riciclo del rottame e dell’integrazione di sistemi di trattamento delle acque
1 https://international-aluminium.org/statistics/primary-aluminium-production/
© ipcm © ipcm reflue ad elevata efficienza per la gestione dei rifiuti. “In quasi 40 anni la nostra azienda è passata da un’area produttiva di 7 mila m2 di alluminio a oltre 280 mila m2” – spiega Marco Sangiorgio, General Manager di Profilglass. “Lavoriamo una media di 200 mila t all’anno e ci siamo attestati tra i leader del settore a livello internazionale, esportando in oltre 85 Paesi. Non sono molte le realtà italiane che hanno visto uno sviluppo simile al nostro e che hanno deciso di concentrare l’attività aziendale in un unico sito produttivo. La crescita vertiginosa che ha caratterizzato Profilglass ha portato i proprietari Giancarlo e Stefano Paci a una riflessione su quali potessero essere le conseguenze di una lavorazione così intensiva sull’ambiente e sul territorio circostante, in cui la nostra azienda è fortemente radicata. L’analisi di alcune delle principali peculiarità dell’alluminio ci ha offerto la risposta: questo materiale particolare è ecosostenibile, leggero, resistente, atossico, di alta formabilità e lavorabilità, e queste qualità si conservano inalterate anche quando il metallo viene riciclato. Nella nostra divisione dedicata
Foto di apertura: Profilglass produce nastri con processo di colata continua e/o discontinua in alluminio e sue leghe, stati fisici e finiture superficiali.
Una sezione della nuova linea di lavaggio e sgrassaggio alcalino e spianatura dei laminati.
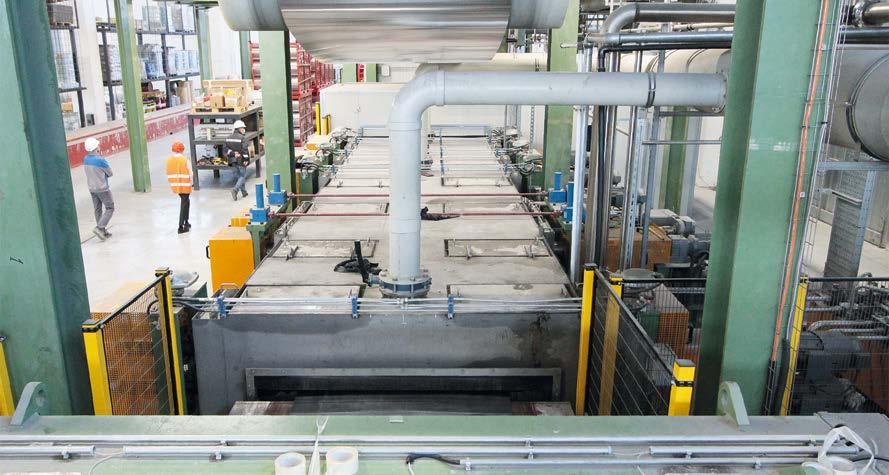
Esterno delle vasche di lavaggio e sgrassaggio.
© ipcm
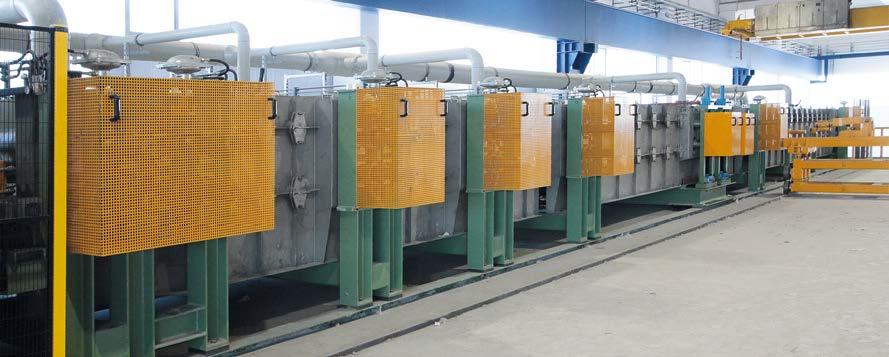
© ipcm
© ipcm
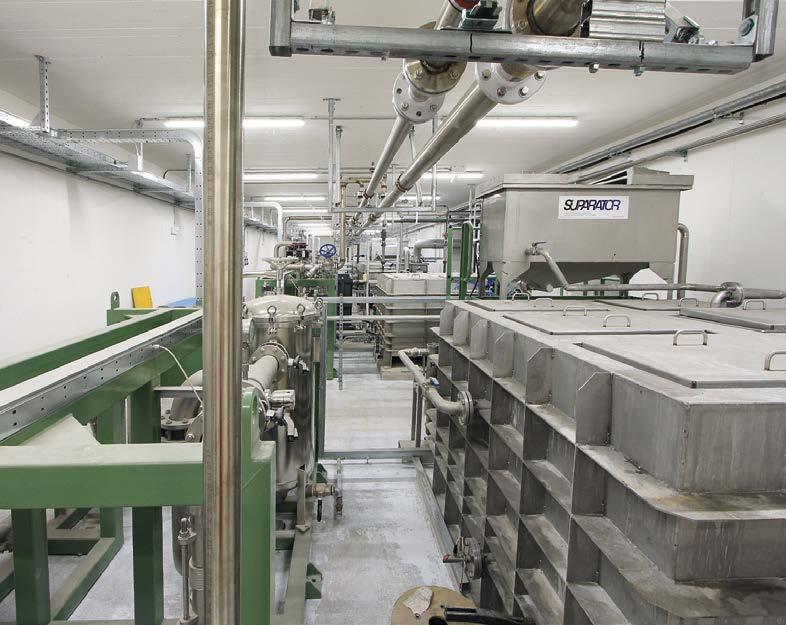
Dall'alto: i dispositivi di filtrazione dei residui oleosi e l’impianto di demineralizzazione.
al recycling, ogni giorno controlliamo e lavoriamo centinaia di tonnellate di materiali di recupero e lattine, impiegando le tecnologie più all’avanguardia per selezionarli, processarli e trasformarli in nuovi semilavorati. Il nostro alluminio deriva così per l’80% dal rottame, nel pieno rispetto dei principi dell’economia circolare”. L’altro fronte su cui si è concentrata la vocazione sostenibile di Profilglass è stato il trattamento delle acque di risulta del lavaggio dell’alluminio. “Per garantire elevati standard di pulizia della superficie in alluminio, i nostri prodotti sono sottoposti a diverse fasi di lavaggio e sgrassaggio in modo che le vernici o le pellicole che sono applicate dai nostri clienti nelle fasi di lavorazione successive del semilavorato aderiscano in modo ottimale. Tra la fine del 2019 e l’inizio del 2020 abbiamo quindi installato due impianti di trattamento acque forniti da CIE, società di San Zenone al Lambro (Milano) specializzata nella progettazione, produzione e installazione di sistemi di trattamento reflui per le linee di finitura dei metalli, in particolare dell’alluminio. I due sistemi filtrano le acque reflue di due linee distinte, una dedicata al lavaggio dei laminati e l’altra alla tempra e passivazione dei laminati destinati al settore automotive e realizzati nella nostra divisione specializzata. Si tratta di prodotti che devono soddisfare precisi e severi requisiti di pulizia”.
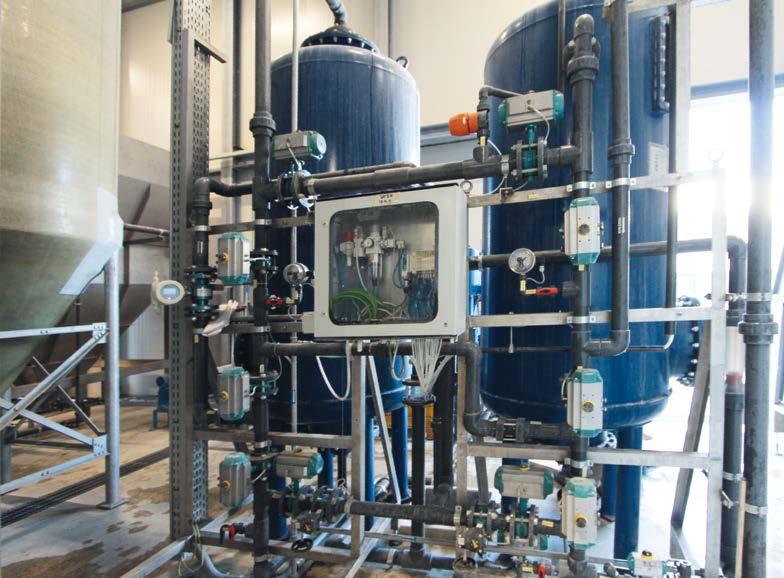
Profilglass: dal 1982 alluminio in evoluzione
L’azienda di Fano ha avviato la propria attività proponendo al mercato un nuovo prodotto, un profilo distanziatore per vetrocamera, nella cui produzione Profilglass si è specializzata. “A partire dagli anni Duemila siamo entrati nel settore della produzione di laminati – prosegue Sangiorgio - per rispondere alla domanda di alluminio in continua crescita e differenziare sempre più i campi di applicazione dei nostri prodotti, che oggi spaziano dal settore edile all’automotive, dall’elettronica ai casalinghi, alla meccanica. Il profilo in vetrocamera è l’unico prodotto che viene verniciato all’interno
del nostro stabilimento, mentre tutti gli altri sono consegnati ai clienti come semilavorati; delle lavorazioni finali si occuperanno i nostri clienti”.
Dal rottame al prodotto semi-finito
L’evoluzione di Profilglass è proseguita di pari passo con la verticalizzazione del sistema produttivo. “Contemporaneamente alla crescita dell’azienda abbiamo progressivamente internalizzato i processi e le lavorazioni che ritenevamo più strategiche come per esempio il taglio, le lavorazioni meccaniche, le fonderie con tecnologia sia a colata continua sia a colata discontinua, fino ad arrivare alla creazione di una divisione ad hoc per il settore automotive chiamata LamiAL. L’aspetto più interessante della nostra produzione e quello che più ci contraddistingue è rappresentato dal fatto che il ciclo è completamente integrato. Si parte, infatti, dal rottame che ricicliamo internamente per arrivare al prodotto semi-finito grazie a un sistema produttivo suddiviso in 5 macroaree: • recupero e trattamento del rottame e degli scarti di alluminio non solo interni ma provenienti anche da società esterne; • fonderia, dove viene trasformata la materia prima con una capacità produttiva di 10.000 tonnellate al mese; • laminazione a caldo, grazie a un impianto in grado di laminare circa 150.000 tonnellate/anno di placche di alluminio fino a 5 mm di spessore;
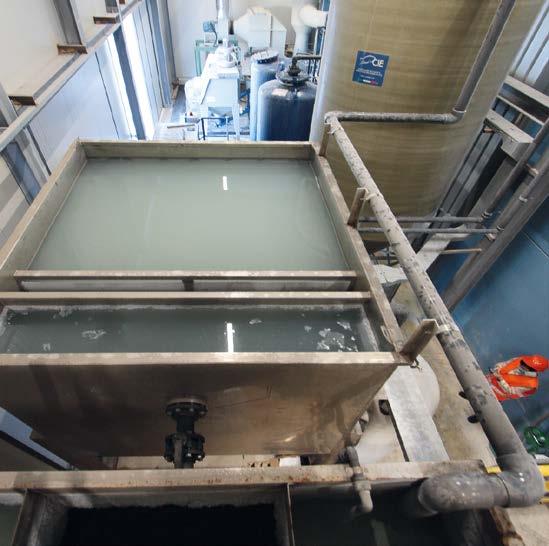
© ipcm
L’impianto chimico-fisico CIE per il trattamento delle acque di risulta delle fasi di lavaggio dei laminati.
AUTOMOTIVE cataphoresis and liquid or powder spray applications
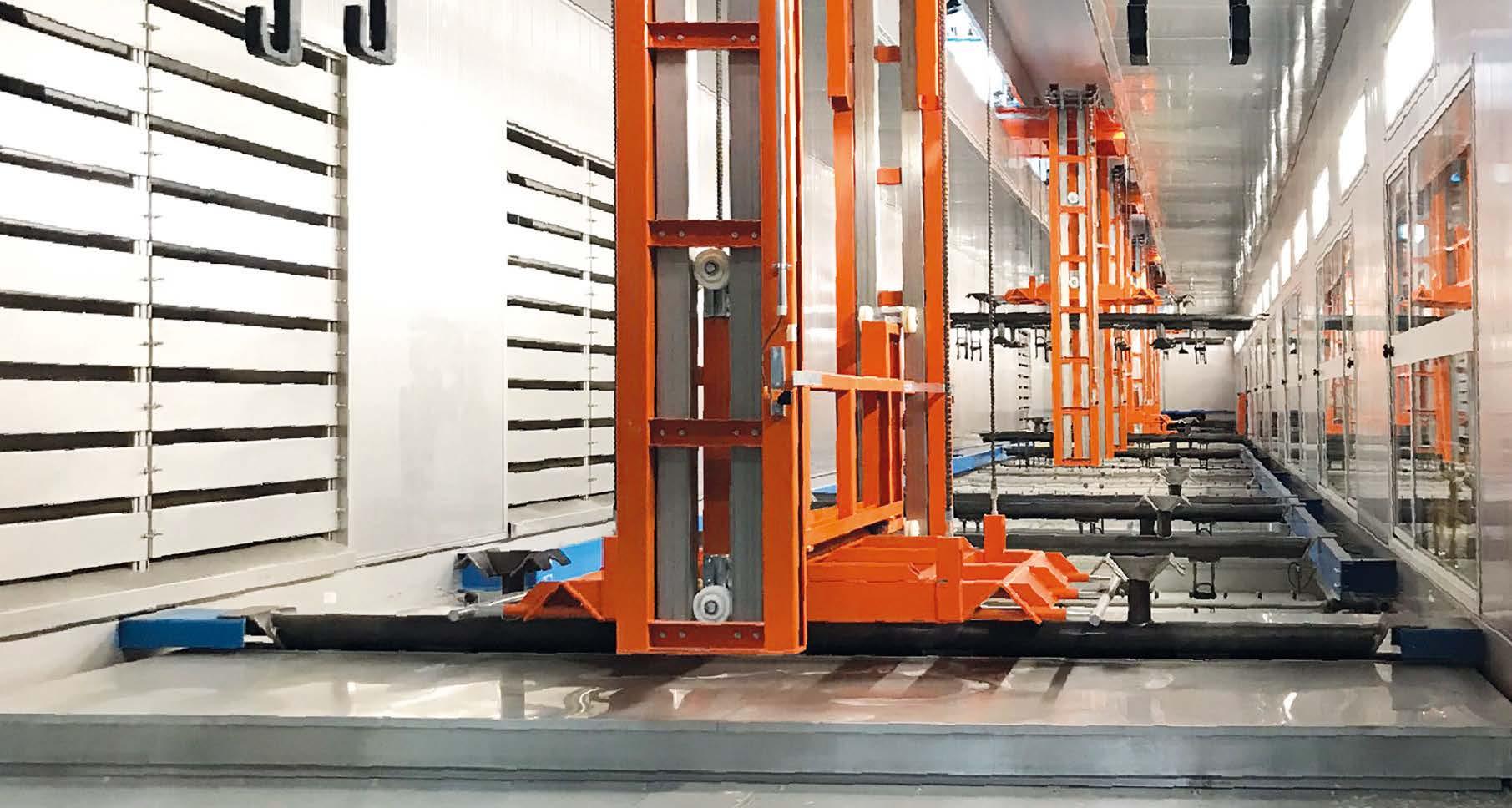
over 60 years of experience in surface finishing lines
© ipcm
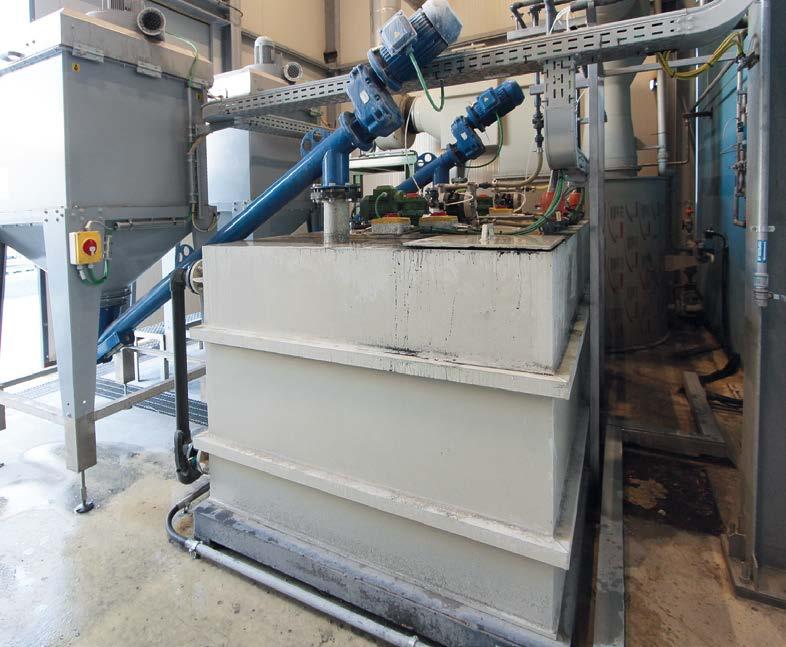
© ipcm
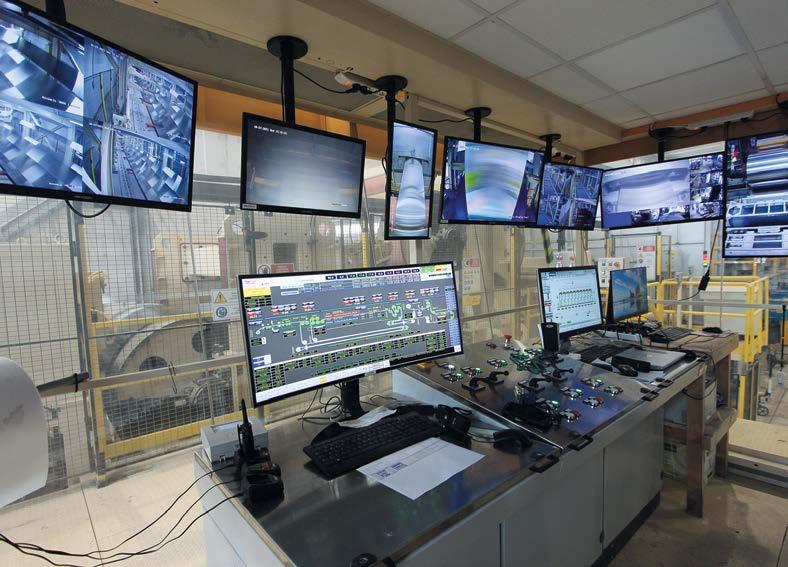
Dall'alto: particolare del sedimentatore e del filtro pressa installati presso la divisione LamiAL e il centro operativo che gestisce e controlla ogni fase del processo produttivo.
• laminazione a freddo, in 4 laminatoi con una capacità produttiva di circa 280.000 tonnellate/ anno; • area finiture, dedicata alla produzione di nastri, bandelle e dischi, che costituisce il nostro fiore all’occhiello grazie a 20 macchine di moderna concezione che garantiscono l’accuratezza di taglio e un preciso rispetto delle tolleranze, anche minime, richieste dai clienti finali”. La finitura dei laminati è preceduta dai trattamenti termici che conferiscono al materiale le caratteristiche meccaniche necessarie per la lavorabilità richiesta nelle fasi di finitura e dai trattamenti superficiali che migliorano le performance dell’alluminio, facilitando l’adesione di rivestimenti e vernici, la decorazione o la protezione della superficie dalla corrosione, per conservare un aspetto esteriore costante nel tempo.
La pulizia dei componenti automotive
La divisione LamiAL è attrezzata con un forno di trattamento in continuo e una linea di passivazione, dove è stato installato il primo impianto di trattamento delle acque reflue. Precisa Alessio Guidi, Technical Department Manager. “In questo caso l’impianto di CIE asserve la linea di trattamento termico in continuo dei nastri, a monte della quale abbiamo previsto uno stadio di pre-lavaggio per evitare che eventuali residui dell’olio utilizzato per le lavorazioni meccaniche precedenti, a contatto con il calore del forno di trattamento termico, possano lasciare macchie sul nastro. Questo ulteriore intervento di lavaggio a spruzzo avviene con acqua riscaldata alla temperatura di 60-70 °C. Nella fase successiva il nastro viene riscaldato e poi temprato attraverso il rapido raffreddamento con l’acqua che si contamina a contatto con l’alluminio. Il refluo contaminato da residui di alluminio e olio viene raccolto e convogliato nell’impianto di depurazione, che tratta entrambe le tipologie di rifiuti, solide e liquide. A differenza della linea di sgrassaggio dei laminati, dove sono utilizzati prodotti basici, qui utilizziamo acido
fluoridrico e solforico, opportunamente formulati in concentrazioni predefinite, al fine di ottenere una disossidazione superficiale del materiale. Dopo questa prima fase di decapaggio, i coil possono essere sottoposti ad un processo di passivazione, con prodotti a base di zirconio e titanio, per preservare il nastro da futura ossidazione. Anche in questo caso l’impianto di trattamento delle acque raccoglie gli overflow del processo e le eventuali contaminazioni solide”. “Gli scarichi” – interviene Antonella Monaco, Project Engineer di CIE – “si possono suddividere sostanzialmente in concentrati acidi provenienti dalle fasi di decapaggio e passivazione, concentrati alcalini provenienti dalla fase di sgrassaggio, risciacqui alcalini e risciacqui acidi. Questi reflui, separati in base alle loro caratteristiche di conducibilità (per risciacqui o concentrati) e pH (acidi o alcalini), sono raccolti separatamente in appositi serbatoi”.
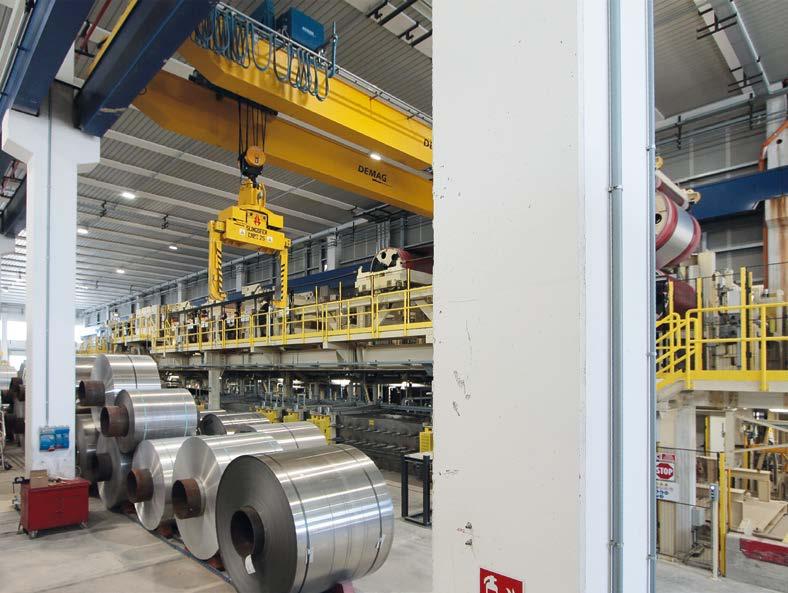
I diversi gradi di pulizia dei laminati in alluminio
“In funzione dell’applicazione che il prodotto Profilglass avrà una volta consegnato – interviene Francesco Berti, Process Engineer di Profilglass - ci sono richiesti diversi gradi di pulizia superficiale. L’aumento della richiesta di laminati sottoposti a sgrassaggio alcalino insieme ai requisiti di planarità, sempre più necessari per la perfetta adesione dei rivestimenti sulla superficie, hanno portato l’azienda ad investire in una nuova linea allo scopo di sgravare il reparto, ormai saturo, e snellire il processo produttivo. La nuova linea integra i processi di sgrassaggio alcalino a spruzzo e tensionatura (spianatura del laminato sotto tensione), prima eseguiti in fasi separate. La rimozione degli oli di laminazione e dei residui superficiali è ottenuta nello stadio di pre-cleaning, dove un’azione meccanica di spazzolatura affianca l’azione chimica per preservare nelle migliori condizioni le successive sezioni della linea ed evitare il rischio di marcature o impronte che possono essere trasferite alla superficie del laminato, soddisfacendo inoltre i requisiti di planarità prima di affrontare l’ultima fase del

© ipcm
© ipcm
Dall'alto: il reparto produttivo della divisione LamiAL e una panoramica dell’impianto di trattamento acque CIE.
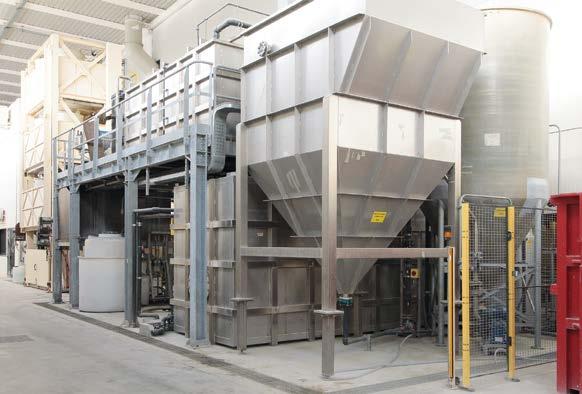
© ipcm
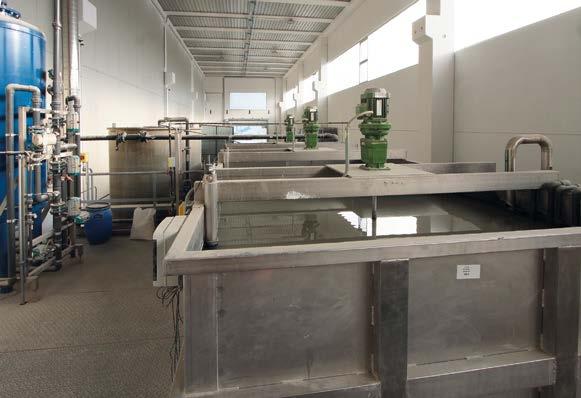
Il reparto di lavaggio della divisione LamiAL.
processo, lo sgrassaggio, che avviene in una sezione dell’impianto lunga circa 40 m. Ogni fase di trattamento chimico è seguita da un risciacquo in acqua demineralizzata prima dell’asciugatura. L’acqua e le soluzioni alcaline vengono recuperate e reimmesse nel sistema di preparazione dei bagni fino a che i parametri di conducibilità risultano conformi. I reflui derivanti da overflow sono inviati all’impianto di depurazione di CIE per essere poi smaltiti”. “Questo impianto – precisa Monaco – “ha una portata massima trattata pari a 10 m3/h e tratta gli scarichi provenienti dalla linea di sgrassaggio alcalino dei coils, suddivisi quindi in concentrati alcalini e risciacqui. L’impianto di depurazione CIE è inoltre in grado di filtrare le acque di spurgo delle caldaie: dal momento che entrambe le linee utilizzano fluidi di processo caldi, il riscaldamento viene effettuato attraverso generatori di vapore in cui sono immessi prodotti chimici per preservarne il funzionamento e che devono essere spurgati periodicamente, una volta superate le soglie relative alla qualità dell’acqua”.
Le caratteristiche comuni dei due impianti CIE
“I due impianti di trattamento chimico-fisici” – prosegue Monaco – “presentano alcune caratteristiche comuni come la sezione di rilanci e accumuli, che include i pozzetti e i serbatoi di raccolta dei reflui e la sezione vera e propria di trattamento, che comprende gli stadi di coagulazione, neutralizzazione e flocculazione. Gli effluenti di questa sezione sono trattati con la calce e 3 prodotti sviluppati da MST Chemicals, la società del gruppo CIE che si dedica alla formulazione di prodotti chimici: PUROSORB M31, un prodotto di fondamentale importanza per adsorbire oli, tensioattivi e ridurre il valore di COD in modo tale da rispettare il valore limite di emissione previsto; PURODEP A11, un coagulante che aiuta anche nella riduzione della concentrazione finale dei fluoruri e PUROFLOC A14, un polielettrolita che permette la formazione di fiocchi, che sedimentano con maggior facilità. Le altre sezioni comuni a entrambi gli impianti sono la sezione di decantazione fanghi, quella di gestione del limpido, ossia l’acqua chiarificata che dopo l’uscita dal decantatore lamellare viene raccolta in uno specifico serbatoio per poi essere filtrata e scaricata nel sistema idrico, e quella relativa ai fanghi provenienti dal fondo del decantatore lamellare, che sono inviati all’ispessitore per poi essere filtropressati, in modo tale da disidratare il fango, raggiungendo una percentuale di secco compresa tra il 35-40%, per cui può essere smaltito come rifiuto speciale non pericoloso”.
© ipcm
Dettaglio del decantatore.
Conclusioni
“La possibilità di avere a disposizione un sistema di trattamento acque che gestisce in modo automatico la preparazione e il dosaggio dei prodotti chimici e ci permette di gestire le diverse tipologie di contaminanti, sia organici che inorganici, è fondamentale per le peculiarità dei nostri processi produttivi”, conclude Sangiorgio. “Le acque, dopo essere state depurate, sono convogliate nel sistema idrico pubblico, mentre i fanghi filtrati tramite filtro-pressa sono smaltiti come rifiuti speciali. Grazie ai prodotti specifici sviluppati da MST Chemicals i due impianti sono ottimizzati per l’abbattimento degli inquinanti rappresentati essenzialmente da alluminio, COD, solfati e fluoruri nel pieno rispetto della normativa locale, più severa di quella nazionale, sia per quanto riguarda i rifiuti liquidi sia quelli solidi. Abbiamo anche studiato con CIE il posizionamento dei due impianti che sono molto compatti e, grazie a questa particolare configurazione, ci permettono di gestire al meglio la logistica degli spostamenti e degli smaltimenti, una flessibilità che l’impianto precedente non ci consentiva. Inoltre la completa automazione del sistema e la predisposizione in ottica Industry 4.0 lo rendono uno dei sistemi più evoluti integrati in azienda, in grado di confermare la vocazione ambientale di Profilglass e la sua presenza tra le aziende dell’industria dell’alluminio che più stanno spingendo verso il futuro sostenibile dei processi di lavorazione di questo metallo”.
FOCUS ON TECHNOLOGY
SIGE SPA rinnova le cabine di verniciatura per migliorare la qualità dei propri manufatti e diminuire l’impatto ambientale della produzione
Gabriele Lazzari ipcm®
La qualità degli accessori in metallo per mobili contenitori è conferita dalla giusta combinazione di caratteristiche estetiche e funzionali, soprattutto protettive, del rivestimento. SIGE opera nel settore da oltre cinquanta anni e ha sempre migliorato i propri processi produttivi, espandendo il mercato dell’azienda in tutto il mondo. L’ultimo investimento nel processo di finitura, due cabine di verniciatura con cambio colore rapido di Gema, le ha permesso di raggiungere una qualità della finitura migliorata dell’80% e di abbattere al contempo i costi e l’impatto ambientale.
Il cibo è da sempre sinonimo di convivialità, perciò non stupisce che la cucina sia uno degli ambienti casalinghi a cui si presta maggiore attenzione durante le decisioni di arredo. Per questo motivo, il settore è in forte crescita1 e si impegna a fornire mobili e accessori di elevata qualità, non solo per quanto riguarda l’aspetto estetico ma anche per la resistenza e la durabilità. SIGE S.P.A., azienda con sede a Polverigi (AN) che produce accessori in metallo per mobili contenitori, ha quindi scelto di modernizzare il proprio impianto di verniciatura inserendo due cabine Gema a cambio colore rapido per conferire ai propri prodotti una qualità di finitura ancora più elevata e diminuire i costi di produzione e l’impatto ambientale.
1 https://www.mordorintelligence.com/industry-reports/global-kitchen-furniture-and-fixtures-market Eccellenza marchigiana all’estero
Da piccola attività a conduzione familiare, l’azienda è progredita negli anni fino a raggiungere le dimensioni attuali: un’unità industriale con 11.000 m2 coperti e una presenza molto forte sul mercato estero. “Come molte realtà del Made in Italy siamo partiti come attività locale nel 1969, adesso siamo conosciuti in tutto il mondo: siamo presenti in 57 Paesi e oltre il 90% della nostra produzione è esportata. Questo ci ha permesso di aumentare il livello di fatturato nel corso degli anni e, nel 2021, dovremmo crescere di circa il 30%” esordisce Mauro Galassi, Chief Executive Officer di SIGE. “Il settore delle cucine italiane, specialmente quello marchigiano, è sinonimo di qualità sia in Italia sia all’estero. Abbiamo scelto di focalizzarci sui mercati stranieri durante la crisi del 2007, quando subimmo un calo nel fatturato del 45%. Abbiamo investito molto nella rete commerciale estera, nei prodotti e nella tecnologia. Questa decisione ci ha fornito
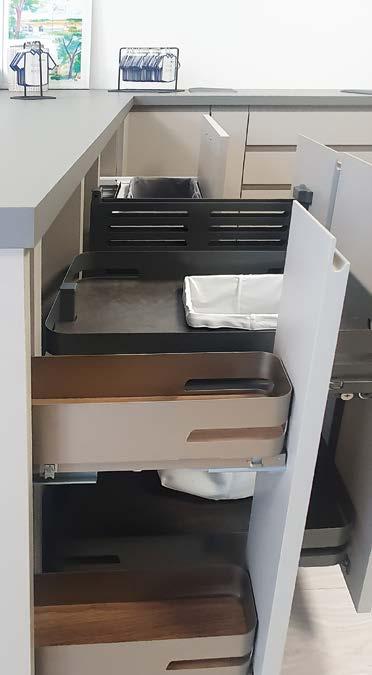
© ipcm © ipcm
Foto più a sinistra: Un mobile contenitore da cucina attrezzato con gli accessori in metallo prodotti da Sige Spa di Polverigi, Ancona.
Negli anni Sige ha aggiunto molti prodotti alla propria gamma ma soprattutto finiture esclusive con colori metallizzati.
la spinta necessaria per crescere e raggiungere le dimensioni odierne”. SIGE è nata inizialmente come produttore di accessori per mobili contenitori da cucina in filo metallico, come il pensile scolapiatti e i contenitori per stoviglie. “Poi però i mercati sono cambiati, e con loro le richieste dei clienti, perciò abbiamo ampliato la nostra gamma di prodotti per soddisfare la domanda emergente: non solo pensile scolapiatti, ma anche tutti gli altri accessori da cucina che sono sugli scorrimenti per le basi e le colonne, come cestello contenitore nei cassetti, cestello portabottiglie, colonne estraibili e contenitori per pacchi. Abbiamo anche iniziato a utilizzare altri materiali oltre al filo metallico, come la lamiera, il vetro e il legno – che ricopre attualmente una parte molto importante della nostra offerta, infatti abbiamo anche inserito un reparto di falegnameria. Per un breve periodo ci eravamo anche interessati ad una possibile espansione nel mercato degli elettrodomestici, ma è un settore che richiede dei rivestimenti completamente diversi rispetto a quelli su cui ci siamo specializzati, perciò abbiamo deciso di dedicarci esclusivamente agli accessori per mobili contenitori”.
Unicità e qualità per rimanere competitivi
Oltre alla qualità dei suoi prodotti, un importante elemento che contraddistingue SIGE è la continua evoluzione in termini di tecnologie adottate: “Il nostro obiettivo è quello di crescere in qualità, tecnologia e ricerca, perché crediamo che siano questi aspetti a consentirci di differenziarci dai nostri concorrenti e rimanere competitivi sul mercato estero.” La continua evoluzione e l’attenzione verso gli sviluppi tecnologici sono dimostrati dagli investimenti che l’azienda ha compiuto nel suo reparto di verniciatura, permettendole di migliorare costantemente la qualità della propria offerta e diminuire l’impatto ambientale della sua attività produttiva. In passato SIGE applicava ai propri manufatti una plastificazione con tecnologia ad immersione, che però aveva delle limitazioni in merito alla gamma dei colori disponibili. “Fino a 5 anni fa, nel nostro settore, la verniciatura non ricopriva un ruolo importante, la finitura galvanica era preponderante. Però poi i mercati hanno iniziato a richiedere la verniciatura a polvere, insieme a una maggiore varietà di colori, specialmente quelli scuri. Abbiamo perciò deciso di differenziarci da altri nostri concorrenti tramite la verniciatura con prodotti in polvere, in modo da offrire dei prodotti di elevata qualità ed esclusivi”, chiarisce Galassi.
Meno cabine di verniciatura ma maggiore efficienza
Al fine di garantire una adeguata preparazione alla verniciatura, gli accessori prodotti da SIGE
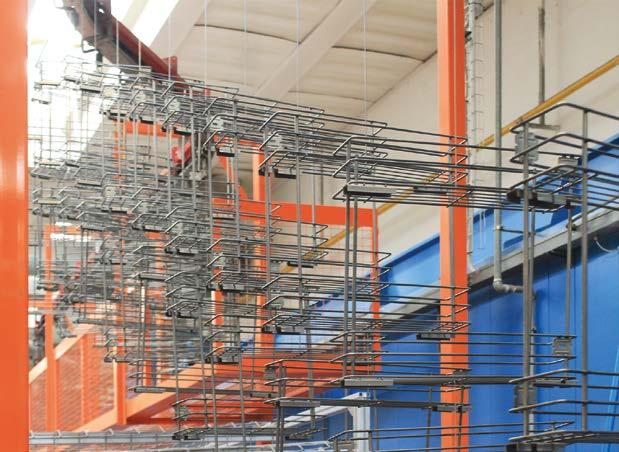
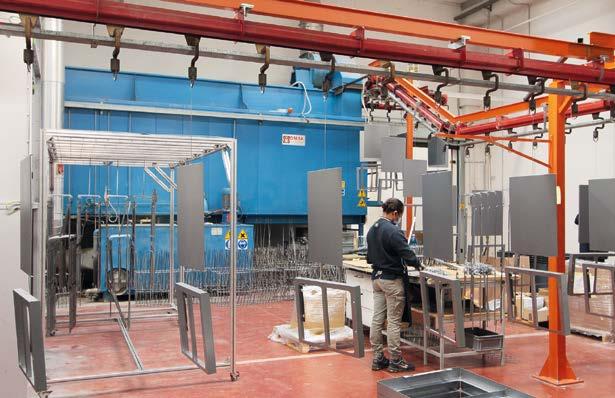
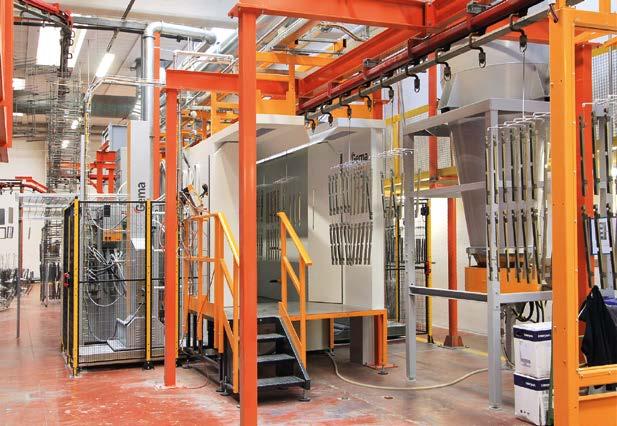
© ipcm
© ipcm
© ipcm sono soggetti a un processo di pretrattamento che prevede due fasi di fosfo-sgrassaggio e due di risciacquo, di cui una con acqua demineralizzata, e infine uno stadio di conversione nanotecnologica. “Questa fase è stata introdotta da meno di due anni, ma la differenza nella qualità del trattamento si è notata da subito”. Per la verniciatura, SIGE utilizzava inizialmente tre cabine con tecnologia triboelettrica. Con l’aumento della richiesta di finiture con colorazioni diverse, a dicembre 2020 l’azienda decise di rinnovare ulteriormente il proprio reparto di verniciatura optando per l’inserimento di due cabine Magic Compact di Gema con centro polveri per il cambio colore rapido, al posto delle tre cabine già in uso. “Quando abbiamo deciso di sostituire le cabine di verniciatura, ci siamo informati sulle varie opzioni disponibili e ne abbiamo testate alcune, tra cui quelle di Gema. Avendo già utilizzato i loro prodotti, ed essendo rimasti soddisfatti dalle analisi effettuate, ci siamo convinti a investire sulle MagicCompact® EquiFlow®,” spiega Galassi. Inizialmente la seconda non includeva il centro polveri. “Ma dopo un solo mese di utilizzo ho richiesto che anche su quella fosse aggiunto il nuovo centro polveri OptiCenter All In One, perché i risultati che avevamo avuto erano eccezionali”. Il sistema di aspirazione dell’aria delle cabine mantiene pulita l’area circostante tramite un ventilatore che aspira l’aria dall’esterno della cabina verso l’interno, impedendo così la fuoriuscita di polvere, mentre il sistema di aspirazione permanente integrato nel pavimento delle cabine consente una pulizia automatica ed evita gli accumuli di overspray. La ridotta quantità di vernice in polvere necessaria e il ciclone rendono le operazioni di recupero e pulizia semplici e veloci, quindi i tempi di produzione di SIGE risultano accelerati rispetto al passato. SIGE applica solitamente cinque colori tratti da due cartelle standard di AkzoNobel con uno spessore compreso tra gli 80 e i 120 µm, ma l’investimento nelle nuove cabine le ha permesso di poter anche personalizzare l’offerta colore a seconda delle specifiche richieste dei clienti. L’impianto che comprende le due cabine di verniciatura di Gema, fornito da O.M.SA srl, è inoltre dotato di un trasportatore monorotaia e due forni di polimerizzazione, che consentono – in caso di richiesta specifica dei clienti – di applicare un doppio strato di vernice senza che i pezzi debbano ripetere nuovamente il percorso originale.
Dall'alto al basso:
- Una delle nuove cabine di verniciatura MagicCompact® EquiFlow® di Gema installate da Sige nel 2021. - La zona di carico dell’impianto di verniciatura fornito da O.M.SA di Besana Brianza, che è dotato di un tunnel di pretrattamento a spruzzo, trasportatore monorotaia e due forni di polimerizzazione.
- Pezzi appesi all’impianto in attesa della verniciatura.
© ipcm
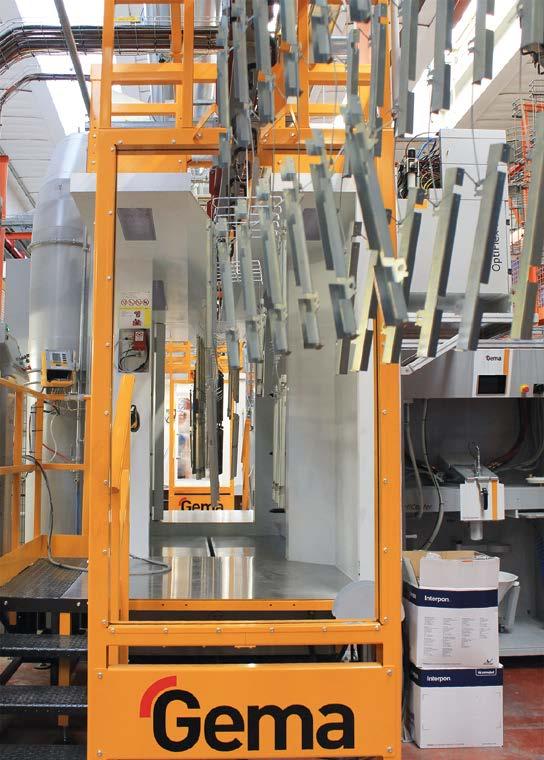
L’ingresso dei pezzi in cabina. Sulla destra è visibile il powder center serie OptiCenter All In One.
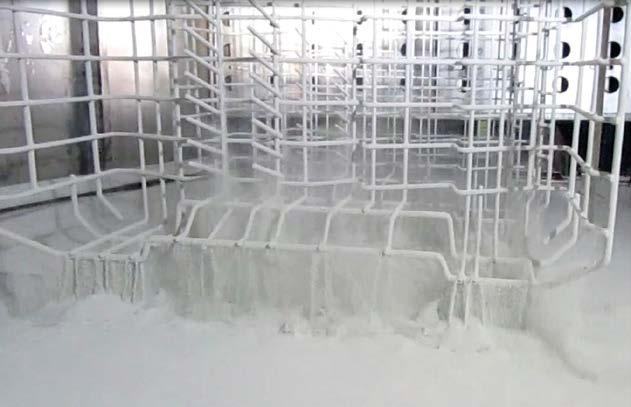
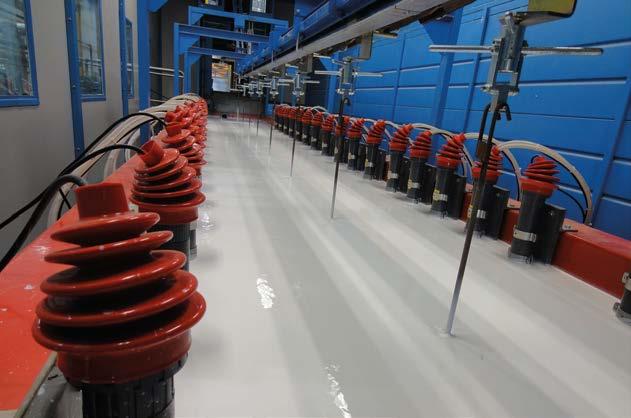
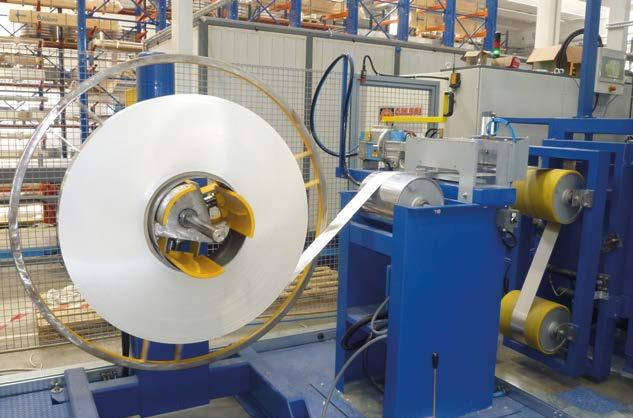
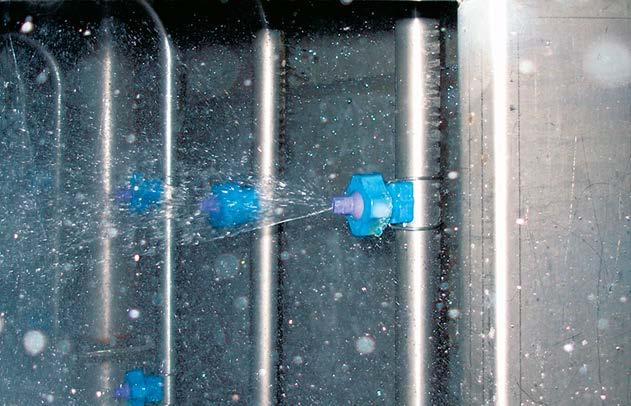
“In questo caso, dopo l’applicazione del fondo e la reticolazione nel forno dedicato, i componenti procedono direttamente nella seconda cabina di verniciatura Gema, dove viene applicata la finitura, e infine nel secondo forno di asciugatura, permettendoci quindi di velocizzare tutto il processo. Ci affidammo a O.M.SA nel 1995. Ci hanno sempre supportato in qualsiasi nostra richiesta in modo eccelso e in tempi rapidi ogni volta che volevamo aggiornare l’impianto. È anche grazie a loro che la nostra produzione ha raggiunto i volumi e i tempi attuali”, commenta Galassi.
La giusta scelta per la protezione dei manufatti e la sostenibilità
A circa un anno di distanza dal rinnovamento dell’impianto di verniciatura, SIGE riscontra una qualità della finitura decisamente superiore. “In passato avevamo avuto dei problemi di idoneità, specialmente con la lamiera, sulla quale si creava uno strato non uniforme. Da quando abbiamo iniziato ad utilizzare le nuove cabine la qualità della verniciatura è superiore dell’80% circa”. Oltre alla
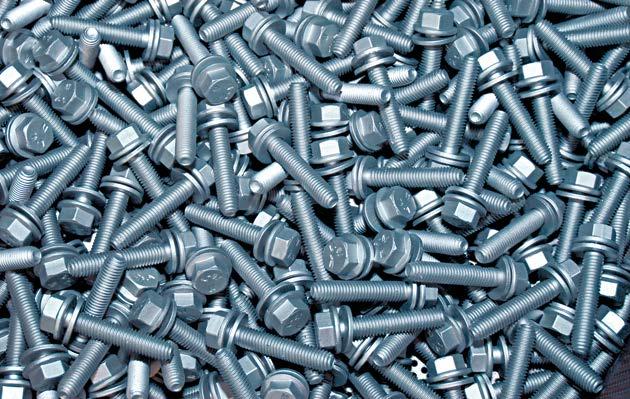
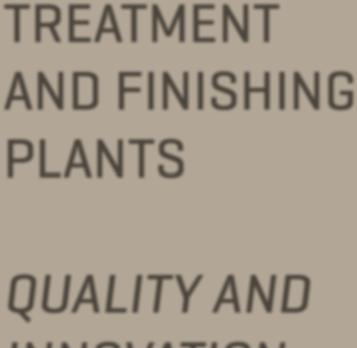
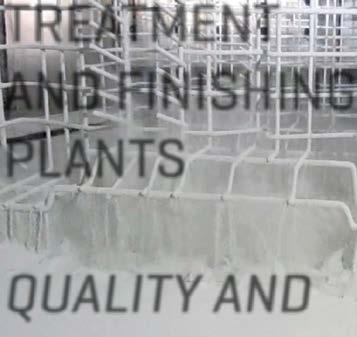
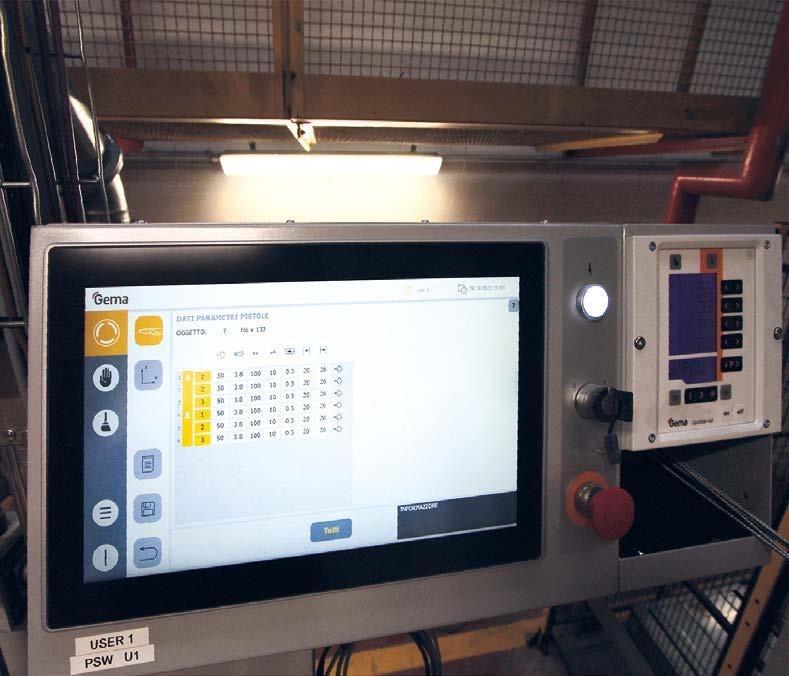
semplicità di utilizzo, le cabine Magic Compact consentono una riduzione del consumo della vernice in polvere del 15-20%. “Ne eroghiamo di meno, ne recuperiamo di più e anche l’efficienza di trasferimento è migliorata, perciò il nostro impatto ambientale e i costi sono diminuiti drasticamente. È stato un investimento importante, ma siamo completamente soddisfatti”. Oltre alla sostenibilità e ai risparmi economici, la verniciatura con polveri termoindurenti conferisce anche delle proprietà protettive che permettono a SIGE di esportare i propri prodotti all’estero senza che questi subiscano danni durante il trasporto. “La resistenza e la durabilità degli accessori per mobili contenitori sono spesso sottovalutati, ma sono fondamentali. Alcuni dei nostri prodotti sono esportati all’interno di container su delle navi per periodi di tempo spesso prolungati, in ambienti corrosivi e con le temperature che a volte superano gli 80° C. A ciò si aggiungono il clima e l’umidità dei Paesi in cui saranno commercializzati. Può sembrare ininfluente, ma la differenza che c’è tra una casa a Milano, una in Cina e una in riva all’oceano può fare la differenza sulla durata di un prodotto. Il principale vantaggio delle cabine fornite da Gema e delle vernici in polvere epossidiche di AkzoNobel è quello di conferire una maggiore resistenza. A ciò si aggiunge anche la possibilità di ottenere delle superfici maggiormente scorrevoli, che sono necessarie per gli accessori che saranno posti sui cuscinetti realizzati con materiali morbidi come il polietilene. In precedenza avevamo avuto dei problemi a conferire questa caratteristica ai prodotti che la richiedevano, ma le Magic Compact ci hanno permesso di migliorare anche questo aspetto”. In oltre 50 anni di attività, SIGE ha sperimentato diversi processi produttivi al fine di offrire degli accessori per mobili contenitori che fossero resistenti, duraturi e che soddisfacessero le richieste di un mercato in continua evoluzione. Le cabine di verniciatura di Gema sono state l’ultimo investimento produttivo in ordine cronologico che ha permesso all’azienda di rimanere competitiva in un settore globalizzato, dove la qualità dei prodotti è di primaria importanza.

© ipcm
© ipcm