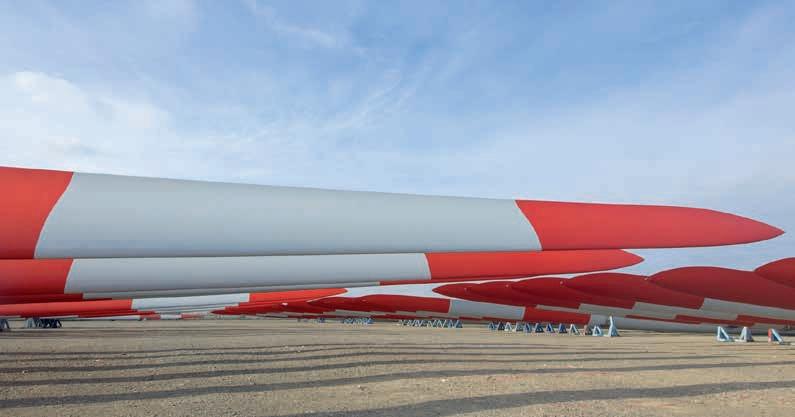
3 minute read
BRAND NEW
Covestro Unveiled its 1,000th Polyurethane Resin Wind Rotor Blade
The ongoing partnership between Covestro and TMT supports the development of longer wind blades.
Covestro and Zhuzhou Times New Material Technology (TMT), a pioneering Polyurethane (PU) wind turbine manufacturer, have recently announced the launch of their 1,000th wind turbine blade. Covestro and TMT have signed a memorandum of cooperation about a year ago and now their wind turbines are being used in commercial wind farms throughout China. TMT produces polyurethane wind blades ranging from 59.5 to 94 meters in length, also with different designs and layups in order to meet the growing demand for longer and larger structures. The 94-meter wind turbine blade, capable of generating 8 MW of energy, is the largest polyurethane application for Covestro so far. “We are very pleased to reach the important milestone of the launch of the 1000th blade with TMT. We believe that industrial collaboration is fundamental to addressing global warming and energy shortage issues, and it is also an important part of Covestro’s commitment to a circular economy,” has stated Christine Bryant, the global head of the Tailored Urethanes Division at Covestro. Under its current five-year plan, China aims to double its wind and solar power output by 2025. Polyurethane resins in windblade production, which have penetrated the epoxy-dominated market in recent years, are a transformative innovation: through an efficient manufacturing process, they provide a more costeffective production solution with better mechanical properties than conventional fiberglass-reinforced epoxy blades. “PU wind blades cater to the growing demand for longer wind blade designs. We hope to further collaborate with Covestro to improve the competitiveness of wind energy through continuous technology innovation,” has declared Binbin Hou, the general manager of the Wind Business at TMT.
For further information: www.covestro.com
© Covestro
People from all over the world attended a three-part webinar organised by DÖRKEN and focused on zinc flake system coatings for components with difficult geometry.
In October, DÖRKEN broadcast a three-part network series called “Zinc flake system coating process for bolts with internal drive” via an online seminar from Herdecke (Germany) into the world. Experts from different industries held presentations on the coating of components with difficult geometries, in this case bolts with internal drives. The goal was to transfer the knowledge that such components can also be coated with a zinc flake system in a reliable way for series production. Experts from DÖRKEN as well as from renowned companies from the fields of bolt production and plant engineering were chosen as speakers. The following presentations were given as part of this series: • Bolt knowledge and the technology internal drive – Michael
Stähler (DÖRKEN) and Robert Kupczyk (Camcar Innovations) • Parameters and adjustment for standard coating lines –
Martin Grün (DÖRKEN) • State of the art: presentation of current concepts of different coating line manufacturers – Janis Barth (WMV), Bruno Forster (Forplan) and Lars Hayen (Sidasa). 63 people from Europe and the USA came together digitally to watch the insightful presentations. Among them were representatives of coating companies, bolt manufacturers and automotive OEMs. Of course, the experts were also available to answer open questions. “We are very pleased that the event series was so well received”, says Tobias Kleyer, Team Lead of the DÖRKEN Coatings Academy and organiser of the events. “The great feedback shows us that there is a huge interest in this topic. We are sure that we were able to show the decision makers in an informative and entertaining way that zinc flake solutions are also ideal for bolts with internal drives.”
For further information: www.doerken.com
© DÖRKEN
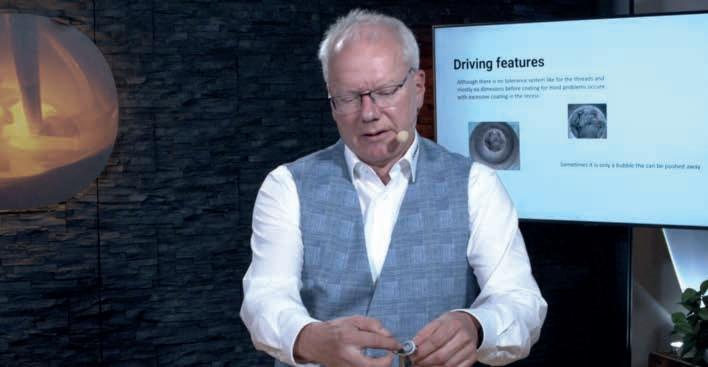