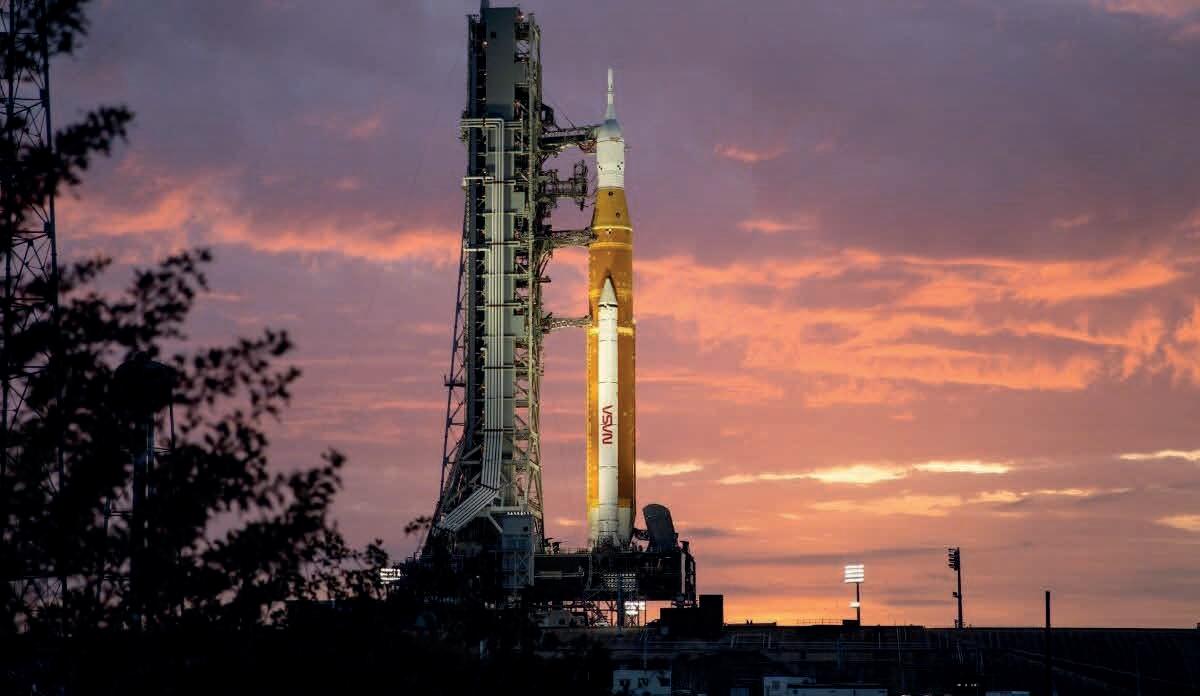
6 minute read
BRAND NEW
© NASA/Ben Smegelsky
Arkema’s Kynar Aquatec Used to Protect NASA’s Iconic Logo as it Blasts Off to Space
The innovative protective coating has been selected to protect NASA’s iconic logo on the Artemis 1 Space Launch System (SLS).
The historic Artemis 1 SLS lifted off from Kennedy Space Center in Florida on Nov. 16 with the mission to send the Orion spacecraft approximately 1.3 million miles, orbiting the Moon. After 3+ weeks, the uncrewed Orion moonship made its splashdown on December 11, 2022. Arkema and its partner, Acrymax®1 Technologies Inc., developed an innovative coating which was able to provide extreme durability to keep NASA’s red “worm” logo on the solid rocket boosters intact while soaring to space. These are the largest, most powerful solid propellant boosters ever built for flight. The clearcoat protecting the logo is powered by Arkema’s Kynar Aquatec®2 PVDF latex to design a water-based protective coating with exceptional durability in low VOC, air-dry systems. “We work hand-in-hand with partners like Acrymax® Technologies to create custom solutions. Their ability to extend this partnership to NASA and develop a formulation strong enough to withstand the intensity of the most powerful rocket in the world is spectacular in many ways,” said Paul Lavallee, global market manager Kynar® Coatings at Arkema. “Kynar Aquatec® PVDF latex is really unique in that it delivers such world-leading performance in a user-friendly fashion. No baking or post-treatment is required.”
1 Acrymax® is a registered trademark of Acrymax Technologies Inc 2 Kynar Aquatec® is a registered trademark of Arkema Inc. Arkema shares its technology with formulator partners through an exclusive licensing program governed by rigorous quality and performance requirements.
About Arkema
Building on its unique set of expertise in materials science, Arkema offers a portfolio of first-class technologies to address ever-growing demand for new and sustainable materials. With the ambition to become in 2024 a pure player in Specialty Materials, the Group is structured into 3 complementary, resilient and highly innovative segments dedicated to Specialty Materials - Adhesive Solutions, Advanced Materials, and Coating Solutions - accounting for some 85.5% of Group sales in 2021, and a well-positioned and competitive Intermediates segment. Arkema offers cutting-edge technological solutions to meet the challenges of, among other things, new energies, access to water, recycling, urbanization and mobility, and fosters a permanent dialogue with all its stakeholders. The Group reported sales of around €9.5 billion in 2021, and operates in some 55 countries with 20,200 employees worldwide.
EnviroTech Launched the New Corrosion Inhibitor SuperCORR A
SuperCORR A by EnviroTech was specifically developed to protect avionic and electronic components.
EnviroTech Europe Ltd has presented SuperCORR A, a corrosion inhibitor specifically developed to protect avionic and electronic and electrical components from systems failures caused by corrosion, as well as preventing the corrosion of metal surfaces. SuperCORR A is a unique and proprietary formulation with long-lasting anti-corrosion inhibitors and components providing a superior lubrication coefficient and protection against moisture, wear, general and fretting corrosion, static electricity, corona and other electro migration problems. The non-flammable film is only 7 microns thick and is formulated without sulphates, chlorides, petroleum-based material or halogens, to meet the EU RoHS directive. The water displacing lubricant and corrosion protection compound was originally developed for the U.S. Air Force to comply with Mil-DTL-87177B (formerly Mil-L-87177A) specifications and has then become the industry standard for electrical corrosion protection, for in service maintenance by both military and commercial aircraft major repair and overhaul (MRO) facilities worldwide. SuperCORR A is packaged in aerosol cans, in order to © EnviroTech make access to component parts easy for the engineering crew in difficult locations and conditions. Unpainted mild steel will not rust on exterior surfaces directly exposed to sea water environments for at least 6 months, thus protecting electrical connectors, switches, chains and drive shafts from corrosion while maintaining lubrication on moving surfaces.
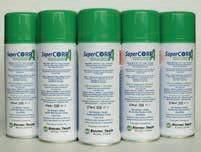
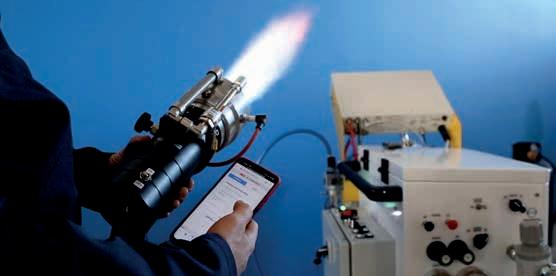
Hempafire Pro 400 Received the EN13381-8 Certification and CE Mark
Hempafire Pro 400 maintains the stability of steel structures in the event of a cellulosic fire for up to 120 minutes.
The international paints manufacturer Hempel has recently announced that its Hempafire Pro 400 passive fire protection coating has been certified according to the EN13381-8 standard and granted the CE mark, complementing the already existing BS-476 and ApplusFire certifications. Passive fire protection (PFP) coatings insulate steel against high heat, extending its load-bearing capacity in the event of a fire, thus providing valuable extra time for evacuation and emergency response. Hempafire Pro 400 allows to maintain the stability of steel structures in case of a cellulosic fire for up to 120 minutes. The intumescent coatings from the range Hempafire Pro have already proved their performances thanks to the exceptionally low thicknesses required to protect steel, that results in reduced total paint consumption, fewer coats to apply and protection delivered in shorter process times. “We’re very pleased to make Hempafire Pro 400 available to customers that require the EN 13381-8 standard and CE mark. After a very successful launch © Hempel last year in the UK and Middle East with the BS-476 standard, we can now provide the same cost advantages and project efficiencies to customers in mainland Europe. Moreover, during this last year we have also further improved the BS-476 loadings at 2 hours and we received an Environmental Product Declaration. Thanks to the reduced quantity of paint needed in a project, Hempafire Pro 400 can contribute to reducing the PFP-related carbon footprint of buildings,” has stated Roger Soler, the product manager for the PFP division at Hempel. Hempafire Pro 400 is fully compatible with Hempafire Pro 315, which is optimised for 30 and 60-minute fire durations. Both products are third party certified according to EN 133818/9 and BS-476 20/2, are available in Fast Dry versions to provide the best results in different climatic conditions and can be used as a single solution for most common steel sections for both in-shop or on-site applications. In addition, they can be used in Type X exterior conditions and C4-High according to ISO 12944. Third party verified Environmental Product Declarations (EPD) are available.
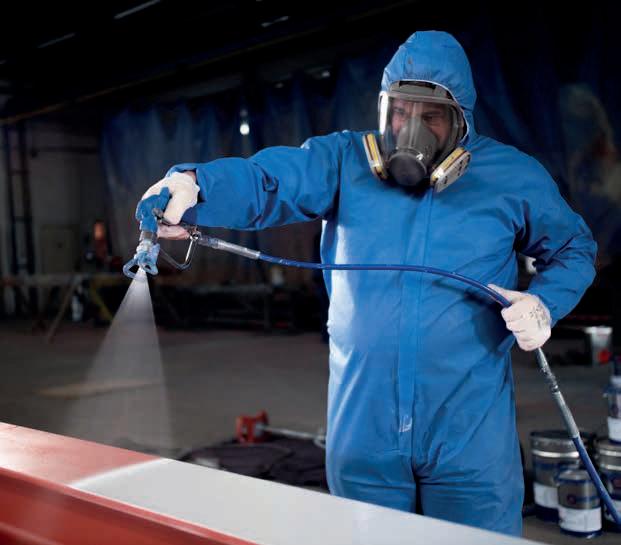
For further information: www.hempel.com
The new VpCI® technology of Cortec simplifies protection for insulated pipes reaching a high range of temperatures.
In order to tackle the dangerous and costly corrosion under insulation (CUI) in the oil and gas industry, Cortec Corporation has developed CorroLogic® CUI Inhibitor Injection, a new Vapour phase Corrosion Inhibitor® technology that simplifies protection for insulated pipes reaching a high range of temperatures. The corrosion under insulation happens when moisture and other corrosive media enter insulation after water barrier wraps or jackets are compromised or when condensation builds up, often unnoticed, beneath the insulation.
The threat is potentially greater on offshore platforms or in other marine environments with chloride-rich sea and with piping that undergoes wet-dry or high-low temperature cycling. Even worse, undetected CUI on pipes carrying hazardous liquids may lead to leaks and potential explosions. CorroLogic CUI Inhibitor is a new hightemperature 100% VpCI that can be injected directly into insulating material. The corrosion inhibiting vapour migrates along the pipe to form a hydrophobic long-lasting protective layer on the metal surfaces that can withstand temperatures up to 350° C. Once piping is installed and insulation is in place, it is difficult to see and correct the problems that may be going on beneath the surface. The new solution developed by Cortec allows a wider timeframe in which to apply preventative measures, increasing the chances of inhibiting and arresting corrosion. CorroLogic® CUI Inhibitor Injection helps pipes last longer and reduces cumbersome repairs on insulated surfaces. In addition, it also minimises the risk for corrosion-related failures, increasing overall plant safety while reducing maintenance costs.
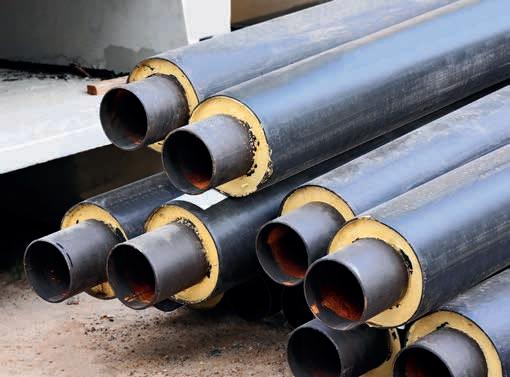
For further information:
https://corrologic.com
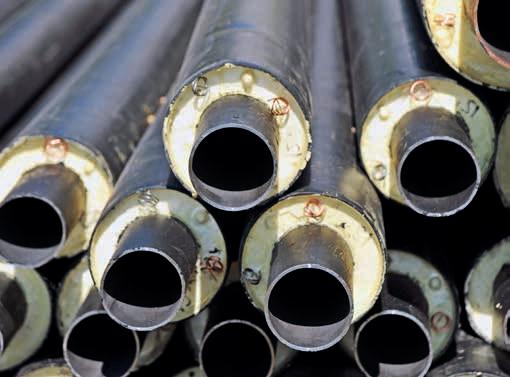
© Cortec
© Cortec