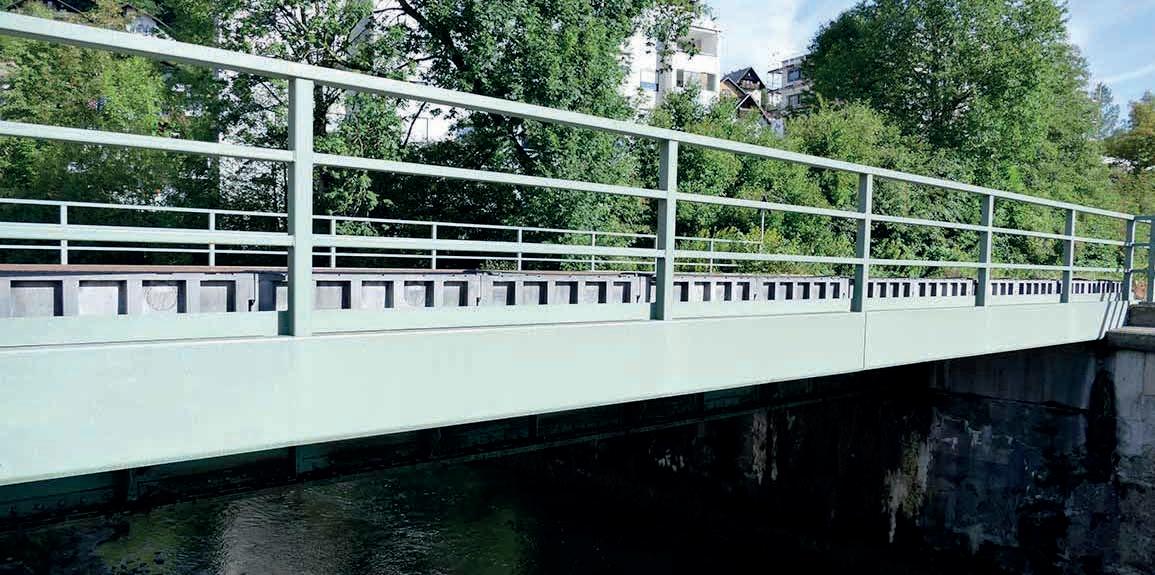
4 minute read
BRAND NEW
New Zinc Flake Pigments Provide Sustainability and Cost Savings for Heavy-Duty Corrosion Protection
The new ProFlake® Zn 3000 zinc flake pigment developed by ECKART GmbH is a sustainable and cost saving corrosion protection solution for heavy-duty industry.
Arecent revision of DIN 12944 and also AMPP (formerly SSPC) with newly generated Paint 29 allow the formulation of compliant, performance-based corrosion protective paints. Thus, there is now more flexibility in formulation compared to the former mandatory use of zinc rich primers. With the new ProFlake® Zn 3000 zinc flake pigment, ECKART responds to that change by providing a product solution that allows for significantly lower zinc content in formulations - a key for more sustainable corrosion protective formulations for heavy duty, including a greatly reduced CO2 footprint compared to currently applied corrosion protective paints. The percolation between these zinc flakes as well as their additional barrier layer formation ensures ideal corrosion protection, providing a clear advantage over zinc rich primers. Other technical benefits are simple handling and application of the ProFlake® Zn 3000 zinc flake-based paint as well as its limited settlement properties. Lean production processes of ProFlake® Zn 3000 guarantee an attractive price-performance ratio. The new 31 µm (D50) product is ideally suited for use in marine, ship or bridge construction coatings, among others.
About ECKART
The ECKART Group, a company of ALTANA AG, is one of the world's leading manufacturers of effect pigments. With 1,750 employees worldwide, the group develops, produces and distributes metallic effect and pearlescent pigments in powder, paste and pellet form as well as concentrates, dispersions and printing inks. ECKART products are used in the coatings and printing industries, the plastics and autoclaved aerated concrete industries as well as in cosmetic products. In the future, ECKART will also drive the optimisation and development of metal powders for 3D printing, thus opening up new areas of application. ECKART is present in over 70 countries.
For further information: www.eckart.net
© ECKART GmbH
Established ProFlake® zinc flakes used in a commercial three-layer corrosion protective system formulated acc. to DIN 12944 applied onto a railway bridge - result after 25 years outdoor exposure.
Hycrome Aerospace Confirms its Ecological Conversion with the New Name HycAero
Hycrome Aerospace, a company specialising in chrome plating and chromic acid anodising in the aerospace and oil & gas industries, will convert these processes in alternative and more sustainable coating methods and will change its name in HycAero.
From January 1st, 2023, Hycrome Aerospace will become HycAero, to better reflect the future direction and capability of the business as it operates alongside its sister company, Hycrome Europe. The rebrand marks a new chapter for its business, its employees, customers, partners and suppliers. Managing Director Andrew Bailey, who started out at an apprentice with Hycrome over 40 years ago, explains the reasons behind the move: “For many years Hycrome has been recognised as a key supplier of protective coatings, precision machining and other special processes to the aerospace and oil and gas industries under the Hycrome Europe and Hycrome Aerospace banners. As the name ‘Hycrome’ suggested, our company has a long legacy of specialising in chrome plating and chromic acid anodising, two processes which we will discontinue by the end of 2023 in favour of more environmentally friendly protective coatings. We recognise that, for some time now, the company name hasn’t truly represented the scope or direction of our organisation, particularly within the aerospace sector, which is why we have decided that, on January 1st , 2023, Hycrome Aerospace will evolve to become HycAero. HycAero is a change in name only and the new brand will slowly begin to evolve within the business in the coming months. As part of the Score Group, our business will continue to thrive and maintain its place as one of Europe’s leading suppliers of special processes and precision machining to the aerospace industry. Since the early 2000s our strategy has been to stay in front of environmental demands and to move away from the use of chemicals containing chrome in our hard coating, anodising and painting processes. In support of this strategy, we have

© HycAero
invested heavily in alternative coating methods. These include HVOF, Plasma and Wire Arc thermal coatings along with Tartaric Sulphuric Anodising (TSA) and thin film Sulphuric Anodising (SAA), all applied by robotic and automated systems. As well as finding innovative solutions to complex problems, we have a strong track record of collaboration and are special process provider of choice for aerospace’s Prime and Tier 1 companies”. Each of Hycrome’s processes have achieved NADCAP, AS9100 accreditations and multiple customer approvals including Airbus, Rolls Royce, Safran and GE Aviation. “Key to the success of Hycrome Aerospace to date has been our ability to evolve, adapt and diversify to meet the requirements of an industry that is at the forefront of technological innovation. Our move to HycAero marks an exciting new era for the business and further demonstrates our longterm commitment to the aerospace sector”, Andrew added.
For further information: https://hycaero.com
© HycAero
