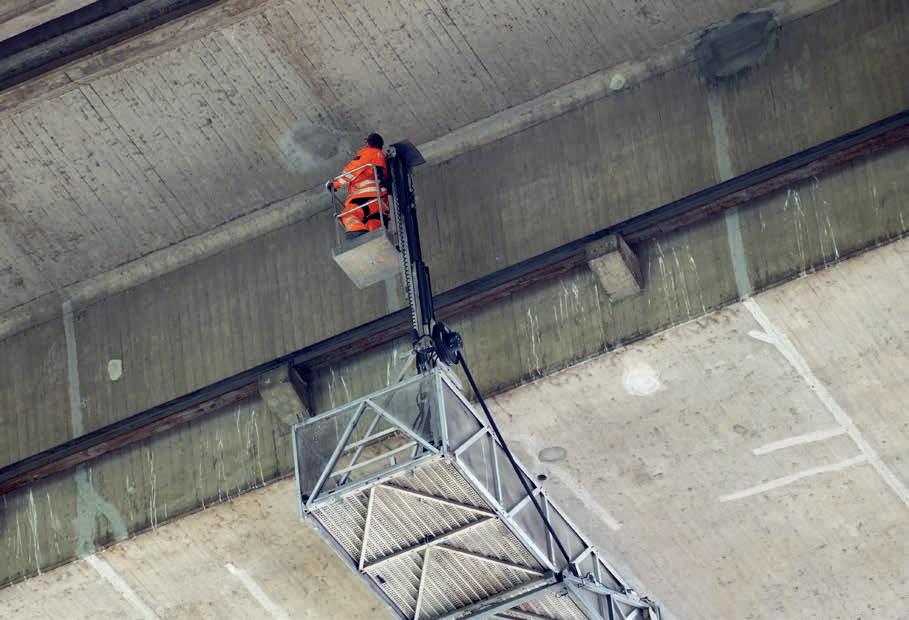
6 minute read
INSPECTION LOGBOOK
© AdobeStock
Coating Inspections - Inspection of Concrete Surface Preparation, Part 2
Massimo Cornago
NACE International Certified Coating Inspector, NACE CIP PEER Reviewer cornago@ipcm.it
Following the previous article regarding the inspection of the preparation of surfaces made in concrete1, which may account for the largest total surface area of all construction materials, we will now describe the tests available for surface contamination after surface preparation.
Incompletely neutralised residual chemicals
Some residual chemicals, such as those left behind from chemical cleaning or etching, may adversely affect the adhesion and performance of coatings applied over prepared concrete surfaces. The Inspector may therefore be required to test the surface pH of the concrete, before
1 https://www.ipcm.it/en/open/protective-coatings/2022/43/48-50.aspx
any coating is applied. To do this, the surface is rinsed with water and the pH (alkalinity or acidity) of the rinse solution is measured. The procedures for testing the pH of a concrete surface are given in the ASTM D 4262 standard. The Inspector should also verify than the surface is vacuumed if specified. This test method is also appropriate for steel surfaces, because it tests rinse water and not the surfaces themselves. The pH test paper strip used should have a range from 1 to 11 pH units, with a capability to measure increments of 0.5 pH units. The procedure is as follows: • After wetting the surface with potable water, place a pH test paper strip in the residual rinse water. • After colour develops on the test strip, select the closest match with the ones included in the standards on the colour chart provided by the pH strip manufacturer.
Grease and oil
After surface preparation, the Inspector may again be required to verify than the surfaces free of grease and oil contamination.
Dust
After abrasion, the concrete surface should be blow down and tested for residual dust. This can be detected visually by applying and removing a piece of transparent adhesive tape or rubbing the surface with a dark cloth, as follows: • Wrap a piece of clean cloth around the index fingertip and make a 150-mm stroke across the surface with medium pressure. • Remove the cloth and visually inspect both the cloth itself and the surface for any traces of dust.
Testing for concrete surface profile (CSP) after surface preparation
After preparing concrete surface for coating, the coating surface profile (CSP) can be determined by visual comparison to the moulded replicates available from the International Concrete Repair Institute (ICRI). These standards range in roughness from a low of CSP 1 to a high of CSP 9 and include surfaces prepared to different levels by acid etching, grinding, shot blasting, scarification, and scabbling. They
© AdobeStock
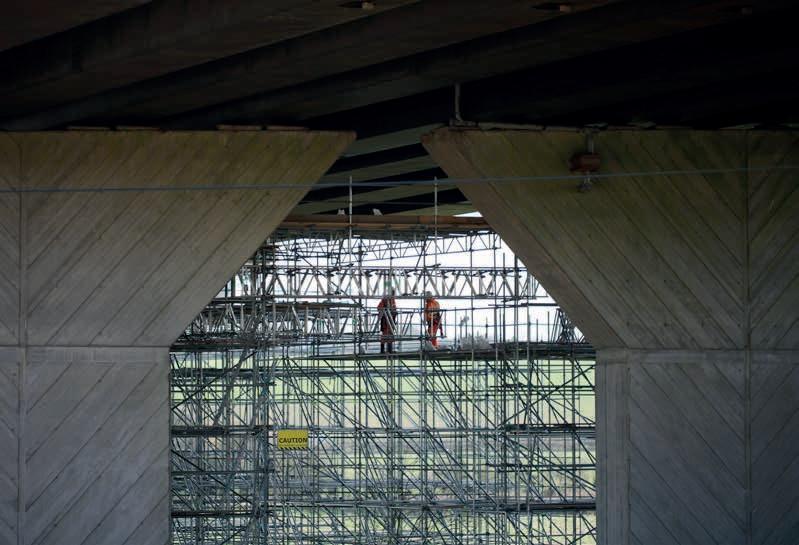
represent degrees of roughness suitable for application of sealers, coatings, and polymer overlays, up to a thickness of 35.6 mm. A chart (Method Selector) provided by ICRI indicates the normal recommended CSPs for these products and the recommended surface preparation methods to obtain them.
Testing for retained moisture (ASTM D 4263)
Retained moisture in concrete may be detrimental to the performance of certain coating systems. The Inspector may therefore be required to test the concrete for retained moisture. Testing for retained moisture may be required before surface preparation. It may also be required after surface preparation if a “wet” surface preparation method such as acid etching or water blasting is used. Here below, we list the most common tests available. a) Plastic sheet method (ASTM D 4263) – One commonly-used method for retained moisture is the plastic sheet method (ASTM D 4263), where a plastic sheet is taped on the concrete surface and left in place for at least 16 hours; thus, when required, this test will delay work by about one day. ASTM recommends testing every 47 m2 for floors, walls, and ceilings, unless otherwise specified. This should include representative sections of each pour. b) Moisture meter – A moisture meter may also be used to detect moisture on or under the surface of concrete. However, it is considered to be more appropriate for plaster or wood than for concrete and to be best used to detect surface rather than interior moisture. The meter uses two needles or probes protruding from a continuity gauge. When the needles are placed on the surface, the gauge indicates whether or not moisture is present there. To detect interior moisture, the substrate must be penetrated by appropriately spaced concrete nails driven 6.4 or 13 mm into the concrete surface. c) Calcium chloride dome test – Another method of testing the retained moisture is the calcium chloride dome test method, under review by ASTM. This method is used to obtain a quantitative value for the rate of moisture emission from a horizontal concrete surface such as a floor. In this method, a pre-weighed sample of anhydrous calcium chloride is placed on the concrete surface and is covered with a sealed plastic dome.
After a designated amount of time (60-72 hours), the plastic dome is removed and the calcium chloride sample is weighted to determine the mass gain due to moisture. Moisture emission is then computed from the mass gain, the contact area of the calcium chloride on the concrete, and the exposure time.

© AdobeStock
Conclusions
Surface preparation of concrete is necessary to remove contaminants that inhibit coating adhesion and to roughen surfaces to improve coating adhesion. Concrete surfaces should be prepared for coating only after they are adequately cured. Prior to surface preparation, concrete may require grinding or stoning to remove protrusions or fill surface holes and indentations. There are several methods of concrete surface preparation that are not intended to roughen the surface profile. These include: • Broom, vacuum, and air blast cleaning, used for removing surface dirt, dust, and other loose materials. • Water, detergent, and steam cleaning, used for removing grease and oil. • Wire brushing, used for removing efflorescence. There are also several methods of concrete surface preparation methods that do roughen surface profile: • Abrading by procedures such as power tools, water blast cleaning, and abrasive blast cleaning. • Acid etching, e.g. with a 10% solution of muriatic acid.
Whatever surface preparation methods are used, the Inspector should monitor them and verify that the specified results are attained. During surface preparation of concrete, the Inspector should also verify that the level of surface contamination (e.g. acidic contaminants, grease or oil, and dust) is within the range allowed by the specification. The Inspector may also be required to test the concrete surface for retained moisture. ‹
MARKETING
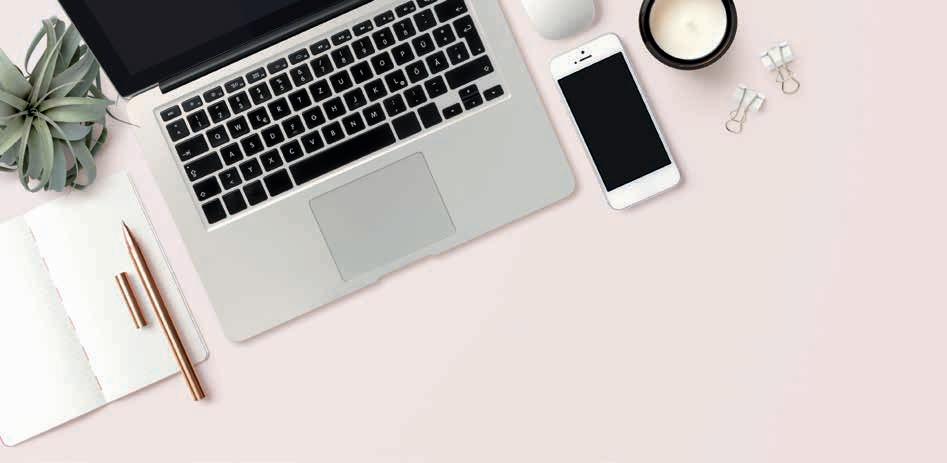
We identify the right digital strategy to reach your target audience. We manage it all, from editorial planning and content creation to publication and performance analysis.
GRAPHIC DESIGN
We take care of all the graphic aspects of your corporate communication, devising or reinventing logos, website graphics, social profiles, and promotional material.
EVENTS
We support you in creating and organising all types of events, taking care of every detail.
CONSULTING
We work at your side and help you implement the best strategic, operational, organisational, and commercial choices to make sure your business grows and hits its goals.
THE PARTNER FOR YOUR COMMUNICATION
Since 2009, we have been helping companies find their way in the world of communication, guiding them in the choice of the best tools and channels and formulating the right communication strategy to promote their brands, products, and services.