AUGUST 2022 CHANGE AGENT Maria Greaves-Cacevski on transformation, leadership and seizing opportunities Lubricants and bearings ContainerTheRoboticsupdateandautomation2022GMCTerrainSupplychainoptimization

REQUEST YOUR FREE SIMULATION TODAY DEMANDDRIVENTECH.COM 8099%45% % REDUCTIONSINVENTORYOF LEAD COMPRESSIONSTIMEOF UP TO CUSTOMER SERVICE RATES OF UP TO DEMAND MORE FROM YOUR SUPPLY CHAIN Challenge the status quo and empower your business with Intuiflow, a suite of solutions that leverages Demand Driven Planning Methods and AI/ML to help your business embrace change and power fast, agile business performance. MATERIALS PLANNING S&OP SCHEDULING & EXECUTION CONVENTIONAL PLANNING TECHNIQUES ARE PROVING INADEQUATE IN TODAY’S VOLATILE MARKET ENVIRONMENT. TOP COMPANIES LEVERAGE INTUIFLOW
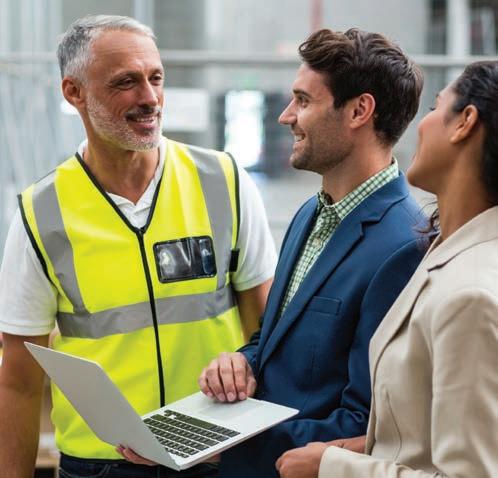
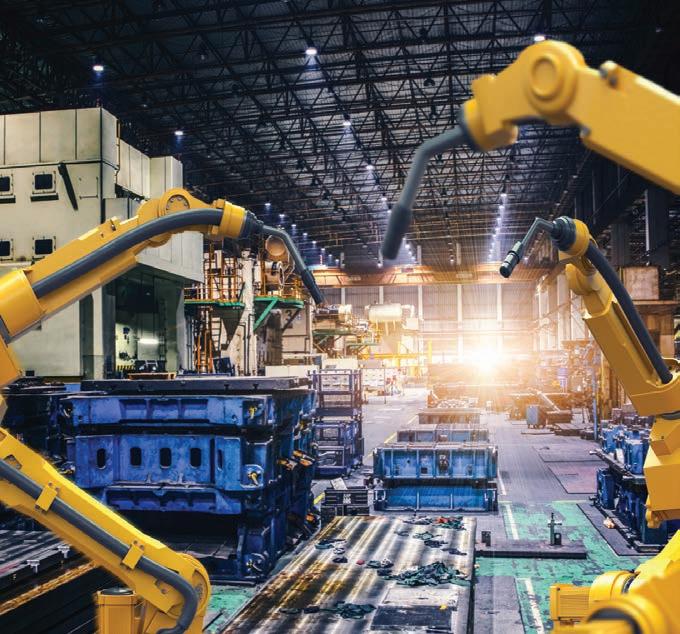

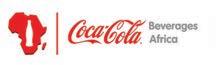
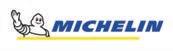
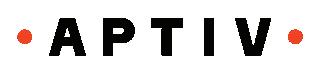

SUPPLYPRO.CA 3 VOL.64 No.4 AUGUST 2022 SUPPLYPRO.CA COVERING CANADA’S SUPPLY CHAIN linkedin.com/company/supplyprofessionalfacebook.com/supplyprofessional@SupplyProMag FEATURES 7 RECESSION-PROOF SUPPLY CHAIN Tips for thriving amid chaos. 8 GREEN PURCHASING Reducing supply chain waste. 10 THE POWER OF TRANSFORMATION For Maria Greaves-Cacevski, people drive positive change. 13 CONTAINER UPDATE Is it easier to come by a shipping container these days? ALSO INSIDE 4 UP FRONT 5 BUSINESS FRONT 6 IN THE FIELD 30 THE LAW 14 SMART MOVES Boosting labour and throughput using robotics. 20 SMOOTH RUNNINGS Here’s what’s new in the world of bearings and lubricants. 22 P2P FOR ESG Today’s P2P technology is critical to your ESG objectives. 23 2014 8 10 ManagementFleet

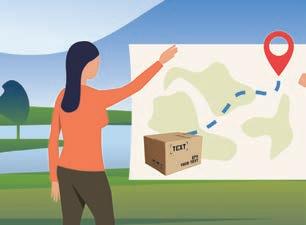
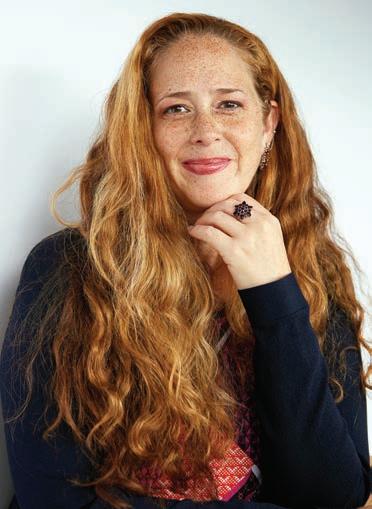

But while innovation is important, we should be careful not to abandon completely the just-in-time model. It has provided advantages to supply chains for decades, allowing for reduced waste, improved efficiencies, reduced cost, and other benefits.
Rather than trying to eliminate the strategy, just-in-time supply chains and manufacturing should evolve. It’s a good idea to rethink how much inventory to keep on hand, as well as where within the supply chain to keep it. A just-in-case model (JIC) of inventory management system can provide advantages as well. But it can also lead to issues including increased stor age costs and potentially wasted stock. Companies usually fall somewhere on a spectrum between the two, and should consider where on that spec trum they belong, based on their needs.
EDITOR MICHAEL POWER 416-441-2085 x7 michael@supplypro.ca PUBLISHER ALEX PAPANOU 416-441-2085 x1 alex@supplypro.ca DESIGN Art Direction ROY GAIOT Design Consultation BLVD AGENCY CUSTOMER SERVICE/PRODUCTION LAURA MOFFATT 416-441-2085 x2 lmoffatt@iqbusinessmedia.com ASSOCIATE PUBLISHER FARIA AHMED faria@supplypro.ca416-919-8338 EDITORIAL ADVISORY BOARD LORI BENSON Procurement Compliance, L&D, Engagement and Knowledge Lead | Business Enablement, Ernst & Young LLP THOMAS HUDEL Manager, Purchasing and AP, Esri Canada Ltd. WAEL SAFWAT Procurement Director, Black & McDonald SHERRY MARSHALL Senior Manager, Meetings, Travel & Card Service, PwC Management Services KIRUBA SANKAR Director, Program Support, Purchasing and Materials Management— City of Toronto JEFF RUSSELL Corporate Purchasing Manager & Inventory Manager, Miller Waste Systems Inc. iQ BUSINESS MEDIA INC. Vice President STEVE WILSON 416-441-2085 x3 Presidentswilson@iqbusinessmedia.com ALEX PAPANOU PUBLICATION MAIL AGREEMENT NO. 43096012 ISSN 1497-1569 (print); 1929-6479 (digital) CIRCULATION Mail: 126 Old Sheppard Ave, Toronto ON M2J 3L9 SUBSCRIPTION RATES Published six times per year Canada: 1 Year $ 99.95 CDN Outside Canada: 1 Year $ 172.95 USD Opinions expressed in this magazine are not necessarily those of the editor or the publisher. No liability is assumed for errors or omissions. All advertising is subject to the publisher’s approval. Such approval does not imply any endorsement of the products or services Publisheradvertised.reserves the right to refuse advertising that does not meet the standards of the publication. No part of the editorial content of this publica tion may be reprinted without the publisher’s written permission. © 2021 iQ Business Media Inc. All rights reserved. Printed in Canada. UP FRONT MICHAEL POWER, Editor
4 AUGUST 2022 SUPPLY PROFESSIONAL
THE END OF JIT?
And while taking a break from all that scrambling, many began to muse about the future of the just-in-time (JIT) model. Was it still effective? Or had it become unnecessarily risky in such an unstable, unpredictable world? It wasn’t just the pandemic that fuelled this JIT scepticism. Other recent catastrophes like the cargo ship, the Ever Given, getting stuck in the Suez Canal for six days in March 2021, clogged ports on the US east coast, as well as the war in Ukraine have all contributed to these just-in-time jitters.
The JIT model was developed by Toyota decades ago and involves only moving material right before it’s needed. That means organizations don’t have to store as much inventory because they only keep as much on hand as they need.
If there’s one thing that supply chain professionals excel at, it’s contingency planning. They’re good at thinking about what might go wrong, then com ing up with solutions to deal with those potential disasters.
Or at least, that was true until the pandemic. Many had never considered contingencies for when 100 per cent of supply dried up. At the height of COVID-19-related lockdowns, those businesses had to scramble to find something, anything, with which to replace certain products.
A few years ago, someone in supply chain or manufacturing might have thought about what to do if, say, 25 per cent of the goods or commodities they need suddenly became unavailable due to natural disaster, political unrest, or similar events. With 75 per cent still available, most businesses could muddle through until supply came back online.
Critics have pointed to the potential fragility of the model, with some suggesting it be replaced with a rebooted structure that wouldn’t leave the supply chain (and ultimately customers) high and dry.
There’s been increased attention on nearshoring as a potential solu tion, but that can never be a complete fix. Bringing manufacturing closer to home can also raise costs, and some things simply can’t be made here in North WhileAmerica.disruption has highlighted its weaknesses, I wouldn’t expect JIT to disappear entirely. Yet businesses may reconsider if it’s best for them, make modifications, or look at backup strategies.


RECESSION DEFINED I’ve been talking about recession without defining it precisely. There are two related, but different, defi nitions. Statistics Canada judges a recession based on the depth, duration, and diffusion of the decline in economic activity. The decline must be of substantial depth, last for more than just a few months, and should be a feature of the entire economy. In other words, it must be felt broadly. The more colloquial definition is two consec utive quarterly declines in real gross domestic product. And based on my own personal experience, I could make an argument that the Hlinka family is experiencing a mini recession right now, largely due to inflationary pressures. Let me explain. I’m a unionized professor at George Brown Col lege. To the best of my recollec tion, the wage increases in our cur rent contract are 1.5 per cent annually. Inflation is in the range of 6 to 8 per cent. If these numbers are accurate, it means that our family is about 5 per cent worse off in real terms, year-over-year. Even if inflation levels off, in another 12 months, we could well be living at 90 per cent of what we did two years ago. That’s a pretty good definition of a recession. However, the nature of my employment is why I believe that not only my family, but Canadians in general, have little to worry about as the economy slips into something that sure looks and feels like a Let’sslowdown.divedeep into the latest Labour Force Survey which was released July 8. Even while employ ment fell, the unemployment rate declined to 4.9 per cent, as fewer people searched for work. Isn’t that curious? People, particularly those aged 55 or older, are voluntarily leaving the job market. Why do people stop looking for work when there are ample opportunities? They don’t need the money.
PUBLIC-SECTOR WORKFORCE Then there’s the nature of the Cana dian workforce. About one in four of us are public-sector employees.
“There are a number of observerseconomic who believe that a recession may have spring.”startedactuallythis
What’s happening now should not surprise anyone. When the deci sion was made to shut down the economy due to COVID-19 and flood the market with money (which is only paper), it made perfect sense that there would be inflation. A year ago, the inflation we saw was assetinflation. The stock market soared, bond prices rallied, and real estate was going straight up. There was enough inventory to handle demand at that time, and because people were nervous, we in North America saved like we hadn’t saved for gener ations. But that spending has been loosened and we’re seeing that reflected in the Consumer Price Index.The nice thing about a market economy is that the invisible hand will adjust. Higher energy prices will dampen demand and lead prof it-maximizers to search for new sources. Food is more expensive, and that will lead farmers to plant more. We can’t overlook that unemployment on both sides of the 49th parallel is low, and to the best of my knowledge, job vacancies greatly outnumber the unemployed. Put all this together, and I’m firmly in the Alfred E. Neuman camp. I just don’t see much to worry about when it comes to recessionary conditions.
SP
There are a number of economic observers who believe that a reces sion may have actually started this spring. There are some signs that this may be the case. The stock market is a reliable leading indica tor (which means it presages the future) and it started to sell off quite dramatically starting in April. The yield curve has been flirting with inversion, which means that what you will earn annually on a shortterm bond exceeds what you will earn on a longer-term bond. The yield curve will likely invert even more if the Central Banks keep raising interest rates.
It’s a cruel and unfair truth that we’re privileged in that we’re reces sion-proof. If you’re reading this and you work in the private sector, your position is vulnerable, and you could understandably feel resent ment. I wouldn’t blame you. Yet at the same time you must recognize that the protection people like I have means that I’ll receive a cheque every two weeks, spending my money and supporting the economy.
SUPPLYPRO.CA 5
When I was a kid, I flat-out loved Mad Magazine. My guess is that many of you reading this column have equally fond memories of that irreverent rag (I describe it that way affectionately). I hadn’t seen any Mad Magazines in a long while, so I did a Google search and discovered that it printed its last edition in April of 2018. The most memorable character was Alfred E. Neuman, the mophaired boy with a gap-toothed smile. His motto: “What, me worry?” That pretty well describes how I’m feeling right now about the prospect of a recession that might hit North America.
BUSINESS FRONT—BY MICHAEL HLINKA network.acrossaCBCcommentaryprovidesMichaelToronto-basedHlinkabusinesstoRadioOneandcolumnsyndicatedtheCBC WHAT, ME WORRY? DO WE FACE A RECESSION WORTH ANGUISHING OVER?
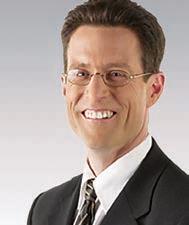
LEADING SKILLS
toforbottleneckspotentialandtheirhowandmothersreturningmapdeterminetoimprovevisibilityidentifytheirreturnwork.”
a gap should consider a career in supply chain: it gives you the opportunity to be successful and have a profitable career while mak ing a difference; you can enter and re-enter at different levels, such as support, mid-range and profes sional; supply chain is now a path to the C-suite; there is less of a pay gap than in some other industries; and you can learn while also pro gressing along the way.
6 AUGUST 2022 SUPPLY PROFESSIONAL
I’ve seen many changes in supply chain during my 12 years as a Cer tified Supply Chain Professional (SCMP). Many of these changes have gained the support of chief procurement officers. This support is noted in several recent surveys, including one published by Deloitte. That survey notes that, for the first time in 10 years, the number-one focus is no longer cost reductions, but operational efficiencies. Why is this shift in focus so important? Such efficiencies emphasize the management side of operations. Stakeholder and suppli er management, data validation, contract management and other areas all represent areas for poten tialWhatefficiencies.doesthis have to do with supply chain needing mothers back in the workforce, you might ask? Note that operational efficiencies in this digitized environment get us focused on resiliency, assessing gaps, innovation and improving by using digital apps.
What are the top-three skills those companies are looking for? What skills do I currently have? How can I upgrade my skills quickly and cost effectively? Can I find someone to watch my children before and after school, or non-school days? Can I volunteer to get a current Creference?anIupdate my attire, get a new hairstyle, update my social media presence, and create a network ing card? Can I contact former bosses and colleagues for support, then send each of them my resume and cover letter? Can I attend industry events and network? Then place the data from your questions into the following prob lem-solvingExecutivesteps:Summary – This is a detailed summary with a strate gic perspective allowing your read er to understand the direction you are taking in implementing your decision. It will briefly outline your relevant background and other issues. Write this section last. Issue identification – This sec tion identifies short- and long-term issues and numbers them in order of importance. What is the main issue and why it is important? How does the environment influence the issue or Environmentalissues? and root cause analysis – This is a detailed analy sis supported by quantitative argu ments that also identifies the root cause of the Alternativesissues.and options – This argues for your chosen direction. Include a pro-con analysis with quantitativeRecommendations,support. monitor and control – What will you do? Out line specific steps you will take. Set priorities or a specific timeline for actions. Explain how you will gain buy-in and how to deal with negative consequences. You can use a gap analysis tool to help identify where you are, versus where you would like to be. It also enables you to focus on needed upskilling efficiently. There are ways to find oppor tunities. You can attend industry events, read economic reports, and be present and professional on social media. It’s also possible to partner with recruiters, watch for news events, attend online events and network after those events. You can also try reaching out to event speakers and moder ators, have detailed discussions with weakest links – they are more likely to recommend you for positions beyond your previ ousFinally,level. here are five reasons a mother returning to work after “Supply chain tools can help
The top skills CPOs are looking for relates back to a 2019 report from Oliver Wyman, a consulting firm, stating that eight out of 10 of those skills focus on stakeholder and rela tionship management. Mothers who have been off work in caretaker roles have developed many of these skills. So how can we support mothers looking to get back into the supply chain workforce? We can work to put in place initiatives like C-suite sponsorship, culture, recruitment, development and promotion, parent and family support, flexible work options and measuring and tracking progress toward gender diversity. Supply chain tools can also help returning mothers map and deter mine how to improve their visibili ty and identify potential bottle necks for their return to work in the supply chain. Combining prob lem-solving steps along with a gap analysis to map and create a game plan, allowed me to understand the business environment, as well as the shortcomings that I had to becoming employable. Some ques tions to ask could include:
SP
Lisa Fenton, CSCMP, is supply chain manager at Rapala VMC Canada.
What local companies are doing well? What positions are they posting for?
GETTING BACK TO WORK SUPPORT MOTHERS’ RETURN TO SUPPLY CHAIN PROFESSIONS.
IN THE FIELD—BY LISA FENTON
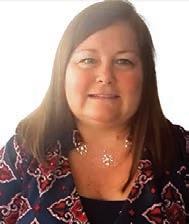
Recent headlines have been pep pered with indicators that we’re in a recession. COVID-19 variants, the war in Ukraine, supply chain woes, inflation and a labour short age are driving world-wide chaos. In a globalized world these issues are systemic, and have become endemic. The next two years will be difficult. How can we protect ourselves from the trials ahead? At Strongpoint Group, we have worked with clients to review their operating models and find opportu nities to increase revenue while reducing costs and minimizing risk. We look at revenue generation and cost management by leveraging twoTheseconcepts.concepts are effectiveness and efficiency. Below, we will focus exclusively on the cost side and offer actions to help businesses not only withstand macroeconomic challeng es but potentially flourish and grow. This methodology calls for all expenses to be justified. The bud getary review, challenging even for sophisticated organizations, requires that every function part ners with an objective third-party that analyzes the needs, wants, costs and potential returns.
1. What does my business need? Ensuring that users understand what they’re buying, and why, is a basic requirement. Yet many organizations end up buying a Porsche when a Honda will do. Calculate the return on the pur chase and understand the risks.
Jonathan Rosemberg is founder and CEO of Strongpoint Group, Inc. Reach him at strongpointgroup.ca.jon@
INTHRIVINGCHAOS HOW SUPPLYPROOFRECESSION-TOYOURCHAIN
Here are five questions to help you succeed with suppliers:
3. Do we know what else is out there? There is a reason why “three bids and a buy” is popular in the procurement world. Understanding market conditions and gathering information through benchmarking is the most powerful data-driven tool for speaking with a vendor.
1. Eliminate layers by expanding the span of control of proven leaders; 2. Jettison redundant or irrelevant roles, functions, and processes; 3. Automate or outsource repeat able activities; 4. Focus on SMART (Specific, Measurable, Achievable, Rele vant, and Time-Bound) goals and quantifiable input metrics; and 5. Overcommunicate context and recognize the impact of all changes.
For example, is it necessary to have an offsite meeting that has been in the books since the compa ny’s inception? The goal is to build budgets around what is essential for the upcoming period, regard less of whether the final number is higher or lower than the previous one. The biggest roadblock to implementing zero-based budget ing is internal politics. Fundamen tal for the approach is C-suite messaging that there are no sacred line items. Every dollar should be questioned. Even entrenched behaviours and relationships should be tested. Holding all lead ers equally accountable is the most critical factor for implementing thisForstrategy.mostcompanies, people costs are at the top of the income statement. Despite how grim it is to make decisions affecting teammates’ lives, analyzing these costs objectively and finding opportunities is a crucial element of any cost transformation. We aim to frame these efforts with the need to spread responsibility more broadly, while letting high per formers shine. This allows for more focus on mentoring teammates and preparing them for duties that transcend their day jobs. The goal is not only to cut staff. It’s also to be mindful before requesting addi tional headcount by looking at the structure and relying on leaders while working on career advance ment. We would rather compensate someone for stretching their role and accountability than hire some one new. Here are the five rules to help look at people costs:
4. Is there a win-win? The success of a negotiation is determined by the satisfaction level of all parties. Asking questions and listening uncovers areas that might have little cost to you while adding value to your supplier.
2. Who is my counterpart? Negoti ation happens in the other party’s mind. When we are sitting across from a large multinational, it is easy to get intimidated. However, the person on the other side has interests, emotions, and thoughts too, and understanding their moti vations can be powerful.
Leaning into your vendor partner ships is hard, and many organiza tions fail at it. But crises are cata lysts to reset relationships and establish mutually beneficial and sustainable terms. The popular view of negotiators is that they are aggressive, doing anything to get what they want. Thankfully, our modern, intercon nected world no longer allows for that type of behaviour without consequences. Good negotiators understand that there is more value in getting a bigger piece of the pie by making the pie bigger than by taking from counterparts. The zero-sum view of dealmaking might still have a place in certain transactions, but it is not the default position for those with business acumen and strategic mindsets.
4. What are the risks and can they be mitigated? Our team is some times called pessimistic because we imagine worst-case scenarios when negotiating a contract. Relation ships between companies are like relationships between people and a crisis can add pressure. Creating mechanisms and governance struc ture ensures that when things go awry, there is space for communi cation and problem solving. Change management is both art and science. There are plenty of frameworks and resources available to transform organizations. Finan cial business cases change minds, but storytelling conquers hearts. Stressing the importance of this work and bringing people along helps to guarantee success. Ensur ing channels for communication, for challenging and for celebrating wins, boosts team engagement and collaboration. Thriving in chaos is an opportunity to build a culture of resilience and positivity.
SP
BY
JON ROSEMBERG
“Goodpiepiemoreunderstandnegotiatorsthere’svalueingettingabiggerpieceofthebymakingthebigger.”
SUPPLYPRO.CA 7

PURCHASINGSUSTAINABLE REDUCING WASTE IN THE SUPPLY CHAIN BY JEFF RUSSELL
The traditional product lifecycle model doesn’t consider communi We hear much about climate change and that we must protect the envi ronment. Yet doing so is challeng ing if we don’t know the differences between today’s economic process es, the traditional linear economy, and the future circular economy. How do we procure products in a circular economy and what are the benefits of this new sustainable purchasing process? and margins and profits grow.
There are economies of scale in production and purchasing enters the tactical phase of buying mate rials to support production. In the maturity stage, the prod uct is in the marketplace and the goal is to maintain market position and profit margins. Purchasing’s role is to find alternative suppliers to help maintain competitiveness. Lastly, in the decline phase, the product is losing market share to other products. Purchasing now supports the aftermarket with lim ited sources and higher costs. New purchasing concepts are changing how products are devel oped, introduced, and procured.
8 AUGUST 2022 SUPPLY PROFESSIONAL
Let’s explore how these concepts relate to purchasing and the environment.Atahigh-level, sustainable pur chasing integrates into the pur chasing process with environmen tal protection as a factor. It ensures compliance with environmental laws and targets, removes hazard ous materials and waste from the supply chain, and ensures suppliers have fair labour practices. Sustain able procurement incorporates a three-dimensional lifecycle, known as the three pillars of sus tainable procurement, as opposed to the one-dimensional traditional economic approach. The three pil lars are: economics (profits), social (people) and the environment (planet). Companies can incorpo rate them into a corporate social responsibility agenda. When developing commodity strategies and reviewing your pur chasing processes, consider these three pillars. Purchasing involves paperwork, so talk with suppliers about paperless transactions and pay-upon-receipt receiving pro cesses. There is a push to evaluate plastics and Styrofoam in packag ing – discuss this with suppliers. Re-evaluate sourcing strategies to determine location and distance travelled to reduce CO2 emissions and use more local suppliers. Consider biodiesel for delivery trucks to help reduce CO2 emis sions. If you source overseas, ensure downstream partners don’t have child labour in product pro ties or the environment. This life cycle has four stages: development, growth, maturity, and decline. During development, a company develops the product concept, con ducting market analysis and launching the product. Purchasing involves sourcing partners, negoti ating long-term pricing contracts, and establishing inventory levels. At the growth stage, sales increase
Historically, our economy has followed a linear process – from sourcing to manufacturing, prod ucts are purchased, consumed, then discarded. Sometimes, a product is refurbished and repro cessed, but from concept design to market, the environmental impact is not a factor.
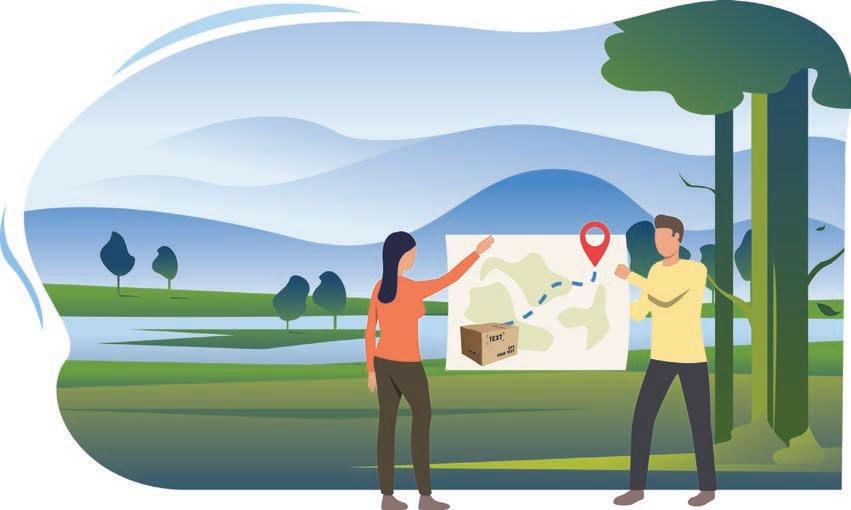
SUPPLYPRO.CA 9 duction. Lastly, in the product lifecycle, discuss socialsuchdevelopmenttherecycled/refurbishedincorporatingmaterialintofinishedproductduringthephase.Advertisingactivitieswillhaveapositiveimpact. KNOWLEDGE IS POWER Understanding the circular econo my helps to develop a sustainable procurement process and redefine product lifecycle to incorporate environmental concerns while eliminating waste. A circular econ omy is closed loop, promoting sus tainable development by ensuring the production and its consumption remain within the marketplace as long as possible, eliminating waste and pollution. It considers the environmental impact at the design stage and focuses on recy cling, refurbishing, reclaiming, repairing, and reusing material. It means not sending material to waste or landfill. As the product 22_001593_Supply_Professional_AUG_CN Mod: June 28, 2022 2:36 PM Print: 07/14/22 page 1 v2.5 KEEP YOUR BUSINESS ROLLING CONVEYORS, BOXES AND MORE π SHIPPING SUPPLY SPECIALISTS COMPLETE CATALOG 1-800-295-5510 uline.caORDER BY 6 PM FOR SAME DAY SHIPPING lifecycle continues, other “R” words arise, with the purpose of reducing supply chain waste. At the manu facture stage, instead of discard ing an old product, reactivate or remanufacture something old into something new. An existing prod uct in the marketplace may need to be revised to be more environ mentallyPurchasingfriendly.strategies must be developed around the Rs of the cir cular economy. Speak with part ners to ensure everyone is doing their part to go green. Can you
“New purchasing concepts are changing how products are developed, introduced, and procured.” re-send packaging back to the sup plier or manufacturer to be re-used repeatedly?Anexample is engine or hydrau lic oil. After using the oil, it can be picked up by a third-party pro cessing company, where it is re-processed into usable oil, repackaged, and sold back into the market. Another example is organ ic food waste, which can be sent to an anaerobic digestor to be con verted to biogas or a digestate. Bio gas can be further processed into electricity or fuel (renewable natu ral gas), to be used to power vehi cles as clean gas. As a digestate, the material is processed into organic fertilizer, animal bedding or other products. As we move towards a greener economy, we must re-evaluate tra ditional purchasing processes and strategies, including the traditional product lifecycle, ensuring new sustainable procurement processes are incorporated. We must ensure strategies that consider environ mental impact and divert as much as possible from landfill. Technolo gy can help us go green, we just need to research those technolo gies and how to incorporate them into purchasing processes.
SP Jeff Russell is corporate purchasing manager at Miller Waste Systems Inc.
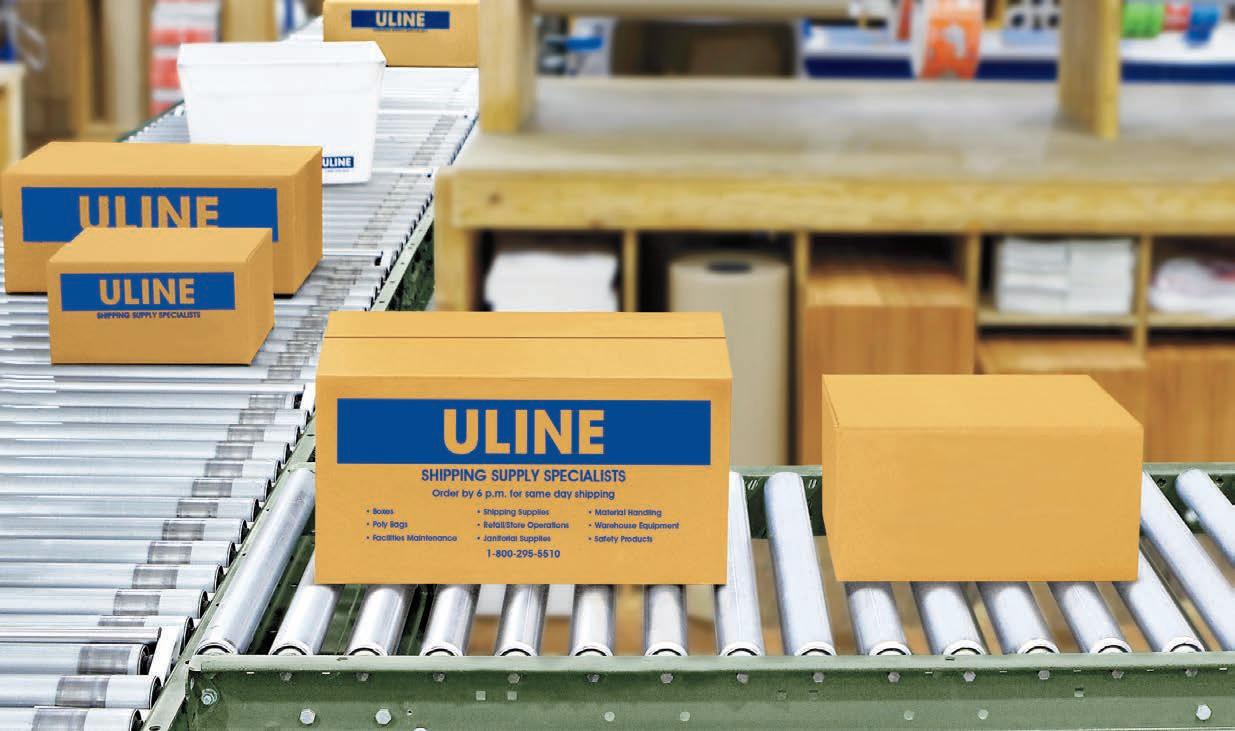
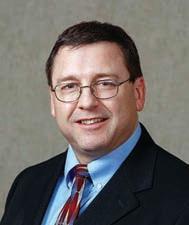
A START IN LEADERSHIP
Greaves-Cacevski’s early roles in business were mostly in retail. That’s where she got much of her supply chain foundation, taking on roles like marketing pricing specialist, buyer and supply planner. Along the way, she began to develop her leadership skills. She also continued strengthen ing her education in the field during this time.
“I don’t see myself so much as a supply chain leader,” says the Toronto-based Greaves-Cacevski, who is now senior category sourcing lead at Chemtrade Logistics. “I see myself as a change leader, as a champion for the supply chain process.” Something that has provided her with this unique perspective, she says, is her status as a sec ond-generation Canadian. Greaves-Cacevski was born in Grenada, an island country in the West Indies northwest of Trinidad and Tobago. Her par ents migrated to Canada in the late 1970s, and she grew up in both Canada and Grenada. This cross-cultural background also provided her with a unique education. Setting her apart from many other supply chain professionals in Canada is her education from the British, Cana dian and American school systems. She returned
“That’s when I started to acquire business cer tificates. This culminated in my Master of Busi ness from Athabasca University in 2015.” Greaves-Cacevski is now working on her Doctor of Business Administration (DBA),
to Grenada with her parents in the early 1990s, completing what’s called in the British education system the General Certificate of Education, or O Level (ordinary level) education. From there, she attended the University of the West Indies in Jamaica, earning a diploma in physical therapy, before returning to Canada. She continued her education here, earning a cer tificate in marketing management from the G. Raymond Chang School of Continuing Stud ies at Toronto Metropolitan University (then called Ryerson University). But her education didn’t stop there, and Greaves-Cacevski also pursued several profes sional“Whendesignations.Ijoinedthe business stream within Canada, I had to acquire education to support my experience and knowledge,” she says.
“While working, I was also taking courses to build my supply chain knowledge, because by now I had learnt the words ‘supply chain,’” she says. “I joined APICS courses for being a certified supply chain professional, as well as The Logistics Institute, where I completed my certificate as a professional logistician (P.Log.).”
Global Supply Chain from Walden University, based in Minneapolis, Minnesota. Although Greaves-Cacevski is a certified physiotherapist, she switched to business when she came to Canada. “Then, slowly, my career came full circle,” she says. “I slowly got into the pharmaceutical field, but on the manufac turingWithside.”aneducation spanning three countries, Greaves-Cacevski has also worked for several iconic Canadian organizations. The time she spent employed at Canadian Tire, Loblaws and The Hudson’s Bay Company taught her not only practical supply chain skills, but also that she was destined for what she considers an uncon ventional career.
“This is where I got my managerial start in terms of leading others,” she says. “In your roles as a buyer or as a planner, you’re indirect ly leading but you don’t have that formal title. When I joined as a manager for procurement
These industry certificates have allowed Greaves-Cacevski to work within the manufac turing sector of the food, cosmetics and pharma ceutical industries. Along the way, she is always looking for a challenge. As well as working full time, she has created learning materials for supply chain and operations at triOS College. She also teaches part time as an adjunct profes sor, supply chain management, at Durham Col lege in AlongOshawa.witha diverse professional background and education, Greaves-Cacevski has also worked in several cities across Canada. These include Red Deer, Vancouver and Moncton, and her current home of Toronto. Her experience in so many locations has provided a sense of what the business world is like across the coun try, she notes. Greaves-Cacevski began working in the pharmaceutical industry when she returned to Ontario. From 2010 to 2015, for example, she worked at Teva Canada as supply chain planner, later promoted to site lead.
A OFCHAMPIONCHANGE MARIA GREAVES-CACEVSKI LEADS PEOPLE AND ORGANIZATIONS THROUGH TRANSFORMATION BY MICHAEL POWER 10 AUGUST 2022 SUPPLY PROFESSIONAL
In many ways, Maria Greaves-Cacevski views her supply chain career as atypical.She has created a unique path in the field out of neces sity, and the journey has allowed her to adopt a unique role within the organizations at which she has worked.
Greaves-Cacevski then works on her priori ties for that day. Regarding time management, what works best for her is identifying those priorities that, if dealt with first, will provide the biggest return. Anything with strategic directive is top priority, followed by operation al issues. Third in the priority queue are tacti cal concerns or administrative tasks. While these
“My day basically involves trying to under stand, high level, what’s on the plate in terms of my priorities, checking in with stakeholders to make sure that everyone is doing OK and that there’s alignment with what our day-to-days are, or what our week involves,” she says. “Then, finally, there’s going through the execu tion. It sort of follows a rinse and repeat cycle.”
In Ontario, she has also worked at ESTEE LAUDER as indirect procurement assistant manager/regional category lead, and at Thermo Fisher Scientific, as strategic sourcing manager. She is now senior category sourcing lead at Chemtrade Logistics, based in Toronto. Her current role has her overseeing 55 sites across Canada and the US while managing the indirect category. “That goes from MRO items to uniforms to corporate travel,” she says. “It’s a wide spectrum of categories that fall under the indirect Greaves-Cacevskibanner.”hasworked to ensure that her typical workday reflects a schedule that works for her. She’s an early riser, she says, and has always worked the early shift. She starts issues take a backseat to the strategic and oper ational, they’re still important and, if ignored, can become fires that needs putting out.
“As you start your shift, you always have a huddle with your team to identify what work was completed and what work needs to be done,” she says. “Bringing that mindset to a corporate environment, I always try to check in with my team just to make sure everyone is OK. Everyone is now online or, if they’re going into the office, we know where everyone is for the day, and where they’re situated so in the case of an emer gency, we can address them accordingly.”
For Greaves-Cacevski , supply chain isn’t a field with clearly defined and regular tasks. Rather, it often involves managing ad hoc issues as timely and efficiently as possible. her day by scanning her emails for issues that need immediate attention. She then checks in with her team – a habit she learned from the manufacturing and retail worlds.
PHOTOGRAPHYFORDMIKE SUPPLYPRO.CA 11 at a contract manufacturer for pharmaceuticals, I was given the opportunity to really use the skills that I’d learnt from my other jobs to try and craft new processes and new policies. That’s why I see myself as a champion for change, not necessarily a supply chain leader.”
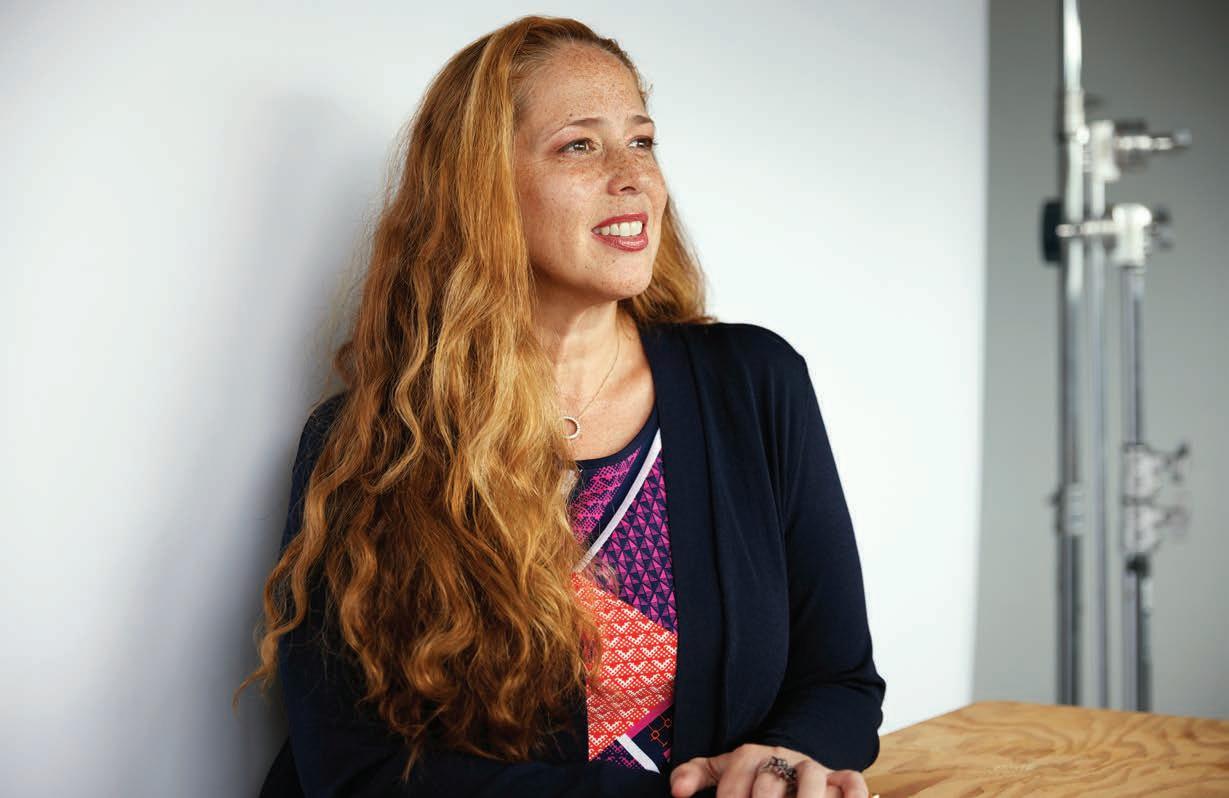
For Greaves-Cacevski, some aspects of her career have come full circle. In the middle of her career she was part of several software proj ect implementations involving, for example, Oracle or SAP products. In those projects she was deemed a contributor in helping to put in place the software to modernize or optimize an organization’s systems. Since then, she has shifted to leading, rather than contributing to, such an implementation. Her current organization is working to improve its legacy system by onboarding a new module to optimize the indirect procurement category. Her role with the implementation involves help ing to design the business solution and establish a supplier network, as well as support end-user training and development.
“One of the challenges is really trying to keep our people focused and engaged,” she says. “It’s a challenge now because we’ve gone through COVID and we’re still kind of going through it. Change has been very dynamic. It’s been constant. Not everybody reacts the same way to change. Some of us thrive in that environment and then some of us don’t.”
“To me, those two awards really stand out, because they fortify that education is a corner stone of my personal growth and development,” she says. “I don’t think I’d be where I am today if I didn’t have that firm foundation from all of the institutions that have trained me over the years.”
For the past four years, Greaves-Cacevski has also worked as an adjunct lecturer and professor at Durham College, where she also earned a post-graduate certificate in project management. She teaches an introductory course. There was no professional roadmap when she began her career, so Greaves-Cacevs ki is grateful for the opportunity to give back.
“I really do see myself as more of a change champion and I think especially in the supply chain industry where it’s constantly changing and evolving with new priorities and new pro cesses, we have to be spearheading those change initiatives,” she says. “We have to be thinking of avant garde ways to be more innovative, to work smarter with less, and to identify and mitigate any of our potential risks, because we are such a global platform right now.”
“Not everybody reacts the same way to change. Some of us thrive in that environment and then some of us don’t.”
BACK TO THE BEGINNING
12 AUGUST 2022
The implementation grew from a previous project that Greaves-Cacevski launched, in which she helped to improve the company’s MRO cate gory. She helped to drive a three-phased approach, with the first step involving standardizing the cat egory. The next step involved consolidation and removing unneeded items. The third step was optimization and ensuring value and cost bene fit from the first two stages.
The couple have a daughter, Olivia, who’s nine, and an 11-year-old black pug. Their dog’s name is Sirna, which means “black” in Macedonian (her husband is from Macedonia).
That guidance is perhaps more important than ever. Supply chain faces unprecedented challenges, not least of which is the mental strain of working remotely and the lack of interperson al connection, Greaves-Cacevski says. That’s why the daily check-in each morning is so important. It helps to ensure everyone is ground ed and knows exactly what they’re doing. It also allows everyone to voice concerns.
“Supply chain doesn’t have a carved-out plan of what you’re going to do, especially with my role,” she says. “It’s basically managing your ad hoc and urgent issues in a timely and efficient manner. I found this is what works best for me.”
SP SUPPLY PROFESSIONAL
Critical to success in supply chain is the con stant search for innovative ways to change and adapt, Greaves-Cacevski says. Also important is the ability to take risks while focusing on professional integrity and improvement, she says. People are more willing to accept guidance from a leader or champion that they relate to, rather than someone who remains emotionally unaffected by change.
The new IT implementation is designed to support and expand those activities. The proj ect will help to standardize how data is entered, maintained, stored, categorized and used, Greaves-Cacevski says.
“I would have appreciated a mentor or guide as to what to expect and what pitfalls to avoid,” she says. “The thing I’m most proud of is being able to use what I’m learning and experiencing day-to-day and to help improve and guide our supply chain students.”
Greaves-Cacevski’s husband, Oliver, is also a supply chain professional and has worked at ESTEE LAUDER Canada for 17 years in supply chain and operations. The couple met at that company. They also completed their master’s degrees together through Athabasca University.
Greaves-Cacevski works to ensure that her work and home life are balanced. She enjoys exercise and goes to the gym or spends time outside. She spends 30 minutes exercising out doors in the early mornings, and does yoga.
The trait paid off, and 15 years later, when graduating with a post-graduate certificate from Durham College, she was awarded the high est-ranking graduate of her fall convocation, based on having the highest GPA.
Along with continuing to push for process improvements through implementing a software solution for her organization’s indirect category, Greaves-Cacevski is working to complete her Doctor of Business Administration through Walden University. She also provides bursaries to primary school students in Grenada who excel academically as they enter secondary school. The bursaries are given anonymously to students at her parents’ former primary schools.
Supply chain is a career that offers almost endless opportunities and possibilities, Greaves-Cacevski advises. But benefitting from those opportunities takes motivation. While there are several core elements, supply chain doesn’t offer a single, clearly defined blueprint to those entering the field. It’s therefore import ant not to compare one career path to another.
“During COVID my mom and I were doing online yoga together,” she says. “We were all able to connect – I’d call in from Canada and my mom and the yoga instructor would be in Grenada. That was our bonding moment.”
“This for me is a huge career highlight, being that about 10 years ago I was in that posi tion as a contributor and now I’m actually lead ing this initiative,” she says.
Change champions must fight constantly against people’s fears regarding shifts to their job struc ture and roles, as well as their ability to adapt.
Another challenge lies in the tactical arena, Greaves-Cacevski says. Implementing new technology has a steep learning curve. Ensuring that people have the technical skills to adapt is important, but so is knowing what will be affected by downstream or upstream changes to the process. As the pandemic winds down, staying con nected with suppliers has also remained a prior ity, she notes. Many organizations are focusing on improving supplier relations and better con tract management systems to mitigate the risk of supply Greaves-Cacevskiinterruptions.says she is especially proud of her academic accomplishments. She was named “Most Consistent Overall Student” when she completed her undergraduate degree. At the time, the label was confusing. But as her career progressed and she began guiding oth ers, she realized the importance of consistency.
BY CHRISTIAN SIVIÈRE
“ThetotheirshortagecontainerhasbeenparticularlydetrimentaltoCanadianexporters,asoceancarrierspreferredtoreturnboxesemptyChina.”
HOW THECHANGEDANDAVAILABILITYCONTAINERHASPRICESINCEPANDEMIC?
If we include fires and other incidents, ocean shipping can be dangerous and importers and exporters should always protect themselves with cargo insurance, all dependent on the Incoterm agreed between seller and buyer. The Incoterm doesn’t just define the cost sharing. It governs the shifting of risks between the parties. Cargo insurance becomes even more important if we consider ocean car riers’ limits of liability, which vary between US$500 and US$900 per container, depending on the terms of the ocean bill of lading and the applicable convention. If nothing happens to your cargo en route, you may still have to pay if the ocean carrier declares “gener al average” during the voyage. This has happened more frequently recently, beginning with the Maersk Honam, the Yantian Express, then the Ever Given in the Suez Canal, the Zim Kingston off the BC coast, the Ever Forward in the Chesapeake Bay, and so on. Costs paid by cus tomers in the event of a general average situation can exceed 50 per cent of the cargo value. These GA risks are covered by standard cargo insurance clauses, the Institute Cargo Clauses A, B and C, so if you have cargo insurance, your insurer pays the GA costs. But without insurance, you’ll have to pay to get your goods from the carrier. SP
Ocean containers have existed since 1956 and over the years have become the enablers of globaliza tion. Boxes were always readily available, there was a good choice of carriers and fierce competition led to competitive pricing. Until just before the pandemic, two factors combined to keep rates reasonable: bigger ships and “trade wars”. Carriers ordering bigger and bigger ships created economies of scale. The “trade wars” started by former US President Donald Trump resulted in a small decrease in international trade in 2019. But two elements pushed in the other direc tion: deregulation and industry consolidation.Fordecades, ocean carriers have been allowed to work together by operating joint services, vessel sharing agreements and alliances which, in effect, limit competition and would be unthinkable in many other industries. Industry consoli dation has been ongoing. In 2015, COSCO merged with China Ship ping and CMA CGM acquired APL. In 2016 Hanjin went under, Maersk bought Hamburg Sud while Japanese carriers NYK, K Line and MOL merged into ONE. The year 2017 saw Hapag-Lloyd buy UASC and COSCO buy OOCL. As a result, there are fewer carriers today, and the big ones tend to increase their market share and to a certain extent, control the market.
For supply chain managers, challenges don’t just come from costs. They are augmented by the lack of container availability, unreliable vessel schedules, blank sailings, tight space on ships, and congestion at port and terminal congestion. The container shortage has been particularly detrimental to Canadian exporters, as ocean carriers preferred to return their boxes empty to China right away in order to pick up another high-paying import load.
CONTAINER SAFETY
CONTAINERSOCEAN
Export rates out of Canada have been much lower than import rates. What is the situation today for ocean containers? According to the recently released Drewry Container Census report, the global pool of shipping containers increased by 13 per cent in 2021, three times the normal trend, to almost 50 mil lion TEUs, as lessors and ocean car riers ordered a record number of new containers. From the ocean carrier side, supply chain conges tion and inefficiencies meant that containers were between 15 and 20 per cent less productive than prepandemic. Drewry estimated that each container averaged 18.1 lifts in 2021 compared to 19.2 in 2020 and between 19.5 and 20.6 in the 2010s. On a positive note, they esti mate that we have as many as six millions TEUs of surplus containers in the global equipment pool. This is good news for shippers.
According to the World Shipping Council’s Containers Lost at Sea report covering 2020-2021, less than one thousandth of 1 per cent (0.001 per cent) of containers were lost overboard. However, the winter of 2020-2021 saw an unusually high number of weather-related incidents and the average number of containers lost at sea increasing by 18 per cent.
When the pandemic hit in March 2020, economic activity slowed down, resulting in a reduc tion of ocean freight volumes of about 30 per cent in the second quarter. Following the rules of supply and demand, ocean rates should have come down. Instead, carriers worked together to limit supply so that rates remained sta ble. When business began picking up in fall of 2020, rates skyrocket ed. If we look at the world’s busi est and most profitable lane, China to the US West Coast, where pre-pandemic rates were around US$3,000 a box, they reached a peak of around US$20,000 in October 2021 and have come down since to about US$8,000. There are gaps between contract rates and spot rates, but the trend remains: although there are still weekly and monthly fluc tuations, ocean rates have been on the way down this year.
SUPPLYPRO.CA 13
Christian Sivière is president at Solimpex.
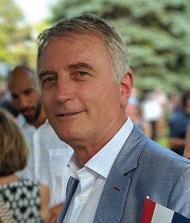
However, because many vendors such as Oracle, SAP and Ariba have made a substantial investment in their equation-based models, their efforts are more focused on bridging the synchronization chasm through the introduction of the somewhat passive service-oriented architectures (SOA)
Jon Hansen is editor and lead writer for the Procurement Insights Blog and was host of the PI Window on The World Show on Blog Talk Radio.
A PRACTICAL WORKSTREAM In 2008, one of my Procurement Insights blog readers sent me a long but thought-provoking ques tion regarding Bill Gates’s 1999 book, Business @ The Speed of Thought. I will share their original text as it will paint a fuller picture of the thought process regarding workstream automation back then.
BY JON HANSEN
Even Oracle’s Larry Ellison admits that the best they can hope to achieve is a ‘near real-time’ capability through this strategy. And near real-time is not indicative of the true synchronized architec tural requirements of a dynamic, agileForenterprise.thisreason, the many orga nizations that have made an equally substantial investment in their cur rent ERP platforms are ‘stuck’ in terms of working within what is quickly becoming an antiquated framework. And it is for these rea sons that, for more organizations, the answer to your question would have to be no.”
NEAR REAL TIME IS STILL NOT ENOUGH Here is why today’s P2P (Web 4.0) technology is critical to achieving your ESG objectives. To start, “the complexity of ratings and multiple frameworks (GRI, SASB, ISI 2600)” makes monitoring performance across a global supply base difficult. Today’s P2P solutions’ ability to synthesize these ratings and mul tiple frameworks to assess and measure supplier adherence is criti cal to ESG success while enabling the procurement team to focus on improving the supply base instead of managing a scoring model. Of course, the above all depends on organizations having reliable access to clean data – but that’s another topic.
First, with my answer’s references to Web 2.0 and Web 4.0, I was talking about going from static ERP-based procurement platforms to the dynamic, P2P AI or digi tal-era solutions now available. The second is that I saw the amazing possibilities of today’s technology first-hand in 1998 and 1999 when, with funding from the Government of Canada’s Scientific Research & Experimental Develop ment program, I developed one of the industry’s first algorithmbased web procurement solutions. Even though I sold the company in 2000, I knew that experience would come in handy one day.
SUPPLY PROFESSIONAL14 AUGUST 2022
SP
ECONOMIC WHY, SOCIAL WHY ESG YEARSTO-PAYPURCHASE-BEGINSSUCCESSWITH20AGO
“If (an ESG plan) falls short on execution, you still get mediocre results.”
My Response to the question was:
THE DIGITAL NERVOUS SYSTEM
When it comes to ESG (environ mental, social, and governance) success, drawing a straight line between the “economic why” and the “social why” depends on more than the understanding and aware ness of that connection and its ben efits. Various ESG initiatives may hit the right buttons across a spec trum of financial and noble social benefits. Still, if it falls short on execution, you still get mediocre results. A 2021 global survey shows this, highlighting that while 81 percent of companies have a “formal ESG program,” only 50 percent believe their company “performs effectively against envi ronmental metrics.”
The member asked: “Almost 10 years ago, Bill Gates of Microsoft wrote a book titled Business @ The Speed of Thought, where he laid out his vision for how organizations should utilize technology to become more responsive, adaptive, agile, etc. Specifically, he drew an analo gy between an organization’s IT infrastructure and living beings’ autonomic nervous systems. Now, reading this book over again, I’m struck by a perception that even now, most organizations still do not have the level of IT integration of which Gates speaks. So, my ques tion(s) to you is this: Does your enterprise/organization have realtime reporting and notification of all important data? Are you able to react and adapt in a very agile way, thanks to your IT systems? Or are you actually constrained in your ability to adapt by those very sys tems? Would you say your organi zation really has a ‘digital nervous system?’ I’m curious to see if my perception – that there will be a lot of ‘no’ answers here is really valid. Additionally, where answers are ‘no,’ I’d be interested to hear about the reasons Lookingwhy.”backon my answer, there are two things I will point out.
“I recently answered a question regarding the future of enterprise software modelling, which relates to the core elements of your ques tion. Here is an excerpt from that answer: You are really talking about the differences between agent-based and equation-based modelling. The latter has been the traditional model used by software developers because it attempts to quantify and therefore confine multiple strands. e.g., the attributes of diverse stake holders into a single, definable ‘stat ic’ stream or process. Outside of finance, equation-based modelling does not translate to other, more dynamic areas of an enterprise, such as an organization’s procure ment or supply chain practice. Agent-based modelling, which has been around for approximately 15 years, first seeks to understand the unique operating attributes of diverse stakeholders. Once under stood, it then attempts to link these seemingly disparate attributes through the utilization of advanced algorithms to produce a reliable, real-world ‘collaborative’ outcome that results in a tangible benefit on a real-time basis. To a degree, Web 2.0 represents the natural evolution of the agentbased model (development efforts are well underway in defining a via ble Web 4.0 model).
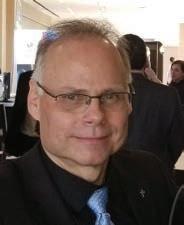

SUPPLY ONTARIOASSOCIATIONMANAGEMENTCHAIN SUPPLY CHAIN CANADA, ONTARIO INSTITUTE HAS REBRANDED TO Our vision is to advance the profession and make careers better for members, by ensuring global competitiveness, innovation and elevation of the supply chain profession in Canada.

REGULAR PRICE PER INSTALLMENT Member: $149 + HST pp I Non-member: $199 + HST pp I Group (4 or more): $125 + HST pp LEADERSHIPSERIES The Leadership Series is our flagship offering from SCMAO and consists of 1-Day events pertaining to topics that are at the core of the supply chain landscape in the modern world. DIGITAL TRANSFORMATION IN SUPPLY CHAIN November 15, 2022 SUSTAINABILITY & ESG IN SUPPLY CHAIN February 28, 2022 WOMEN IN SUPPLY CHAIN March 30, 2023 SUPPLIER DIVERSITY April 27, 2023 FOR REGISTRATION Contact Katie Cheshire at kcheshire@scmao.ca FOR SPONSORSHIP Contact Kim Sforza at ksforza@scmao.ca LEADERSHIP SERIES ALL ACCESS PASS FOR TEAMS WHO WANT TO ATTEND ALL 4 INSTALLMENTS The Leadership Series All Access Pass allows access to the 4 flagship installments of the Leadership Series 4.0 (Digital Transformation in Supply Chain, Sustainable Supply Chain, Women in Supply Chain & Supplier Diversity) and is available for teams of 10 or more. The Leadership Series All Access Pass allows each member on the team to have access to all 4 installments of the Leadership Series. In fact, this access also allows team members to share their access pass with other members of the team. An All-Access Pass for a team of 10, for all the 4 installments therefore allows 40 registrations across all the 4 installments at $400 + HST pp. Contact Katie Cheshire for details. Set your teams up for success In an era where identifying and retaining talent, and building team productivity has become a challenge, demonstrate your commitment to your teams’ success. Help them upskill and grow with the changing needs of the supply chain environment. ENGAGE, INVIGORATE AND RETAIN YOUR TEAMS CORPORATE ONSITE DELIVERY of any of our existing Curriculum, which includes CPD (Maintenance credit) for Designation Holders, and exemption for future pursuit of Designation, where applicable. FULLY CUSTOMIZED TRAINING can be designed based on the expertise of our instructors and facilitators. Training designed for your specific business needs, and using your own business issues, examples and case studies will deliver on your specific learning outcomes. DISCOUNTS ON GROUP PURCHASES of any course or event we offer, including our online courses. These could include group purchases on the Leadership Series as well as on the upcoming professional development sessions listed below. Take advantage of our cost-efficient and convenient solutions that deliver results within projected timelines LEVERAGE OUR LEADERSHIP SERIES, CSCMP DESIGNATION AND PROFESSIONAL DEVELOPMENT SESSIONS FOR TEAM ENGAGEMENT AND DEVELOPMENT.
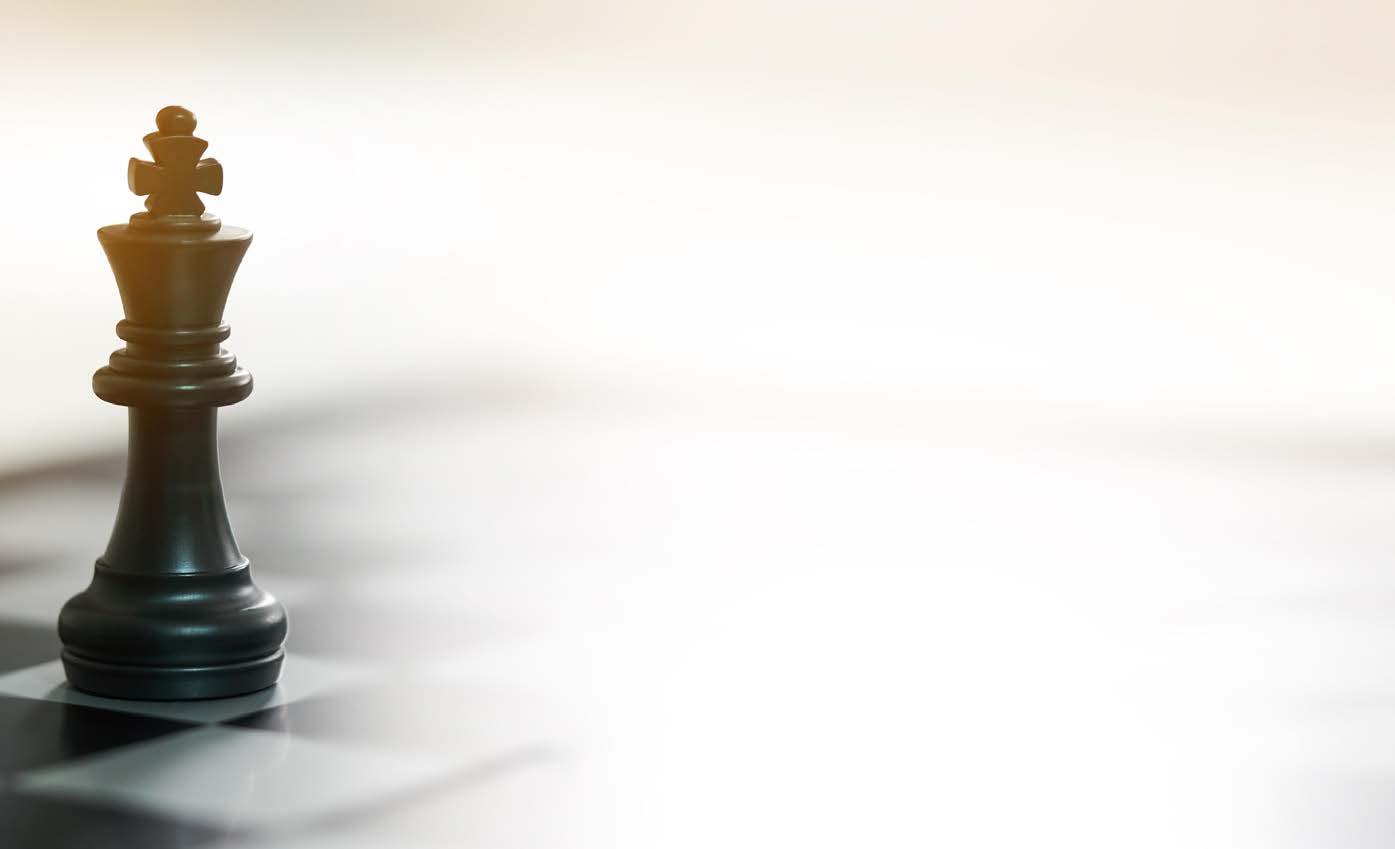


To register for a Professional Development session visit scmao.ca/pd or contact Katie Cheshire at kcheshire@scmao.ca. Any discount or offer is exclusive and no two offers can be combined at any point. Canadian Construction Procurement August 31 – September 1, 2022 2 half-days 5 CPD credits Indigenous Awareness Workshop August 17 & 18, 2022 2 - Half Days 10 CPD credits Information Technology Procurement and Related Contracting Sept. 29, 30 & Oct. 6, 7, 2022 4 - Half Days 10 CPD credits Supply Chain Analytics for Business Results Tuesdays & Thursdays from 10 - Half Days 10 CPD credits October 4 - November 3, 2022 Professional Services Procurement October 25-26, 2022 2 - Half Days 5 CPD credits Project Management for Supply Chain Professionals November 2, 3, 9, 10, 2022 4 - Half Days 10 CPD credits Capital Equipment Procurement and Contracting Nov. 30 & Dec. 1, 7, 8, 2022 4 - Half Days 10 CPD credits Service Contracting and Outsourcing Jan. 24, 25, 31 & Fe. 1, 2023 4 - Half Days 10 CPD credits Canadian Construction Procurement February 22-23, 2023 2 half-days 5 CPD credits Drafting A Statement of Work March 20-21, 2023 2 half-days 5 CPD credits Join 2,000+ CSCMP recipients in fuelling the supply chain industry across Canada. The CSCMP Designation will not only provide applied learning to immediately impact performance at work, it will also signal to the organization the excellence and professionalism your team demonstrates. SCMAO is the only institute to have the Bill Pr – 19, an Act that grants SCMAO the exclusive right to bestow CSCMP Designation to members who qualify (complete the program). Why Choose CSCMP? Recognized and Endorsed by Ontario Legislature CSCMP DESIGNATION To enrol from the program please contact Alisha Seguin at aseguin@scmao.ca or +1 416 977 7566 x 2150 to learn more. InteractiveFormatReal-Life Example Based Learning Pay As You GoStudy At Your Own Pace 2,000+ CSCMP RECIPIENTS 5,000+ ORGANIZATIONS 22% HIGHER SALARY THAN THOSE WITH NO CERTIFICATIONS UPCOMING DEVELOPMENTPROFESSIONAL&TRAININGBuildyourteam’scapabilitieswithabreadthofrelevant training, on topics that are pertinent to supply chain strategy and operations. THE FALL 2022 TERM STARTS ON SEPTEMBER 14, 2022. GET 20% OFF FOR A TEAM OF 4 OR MORE
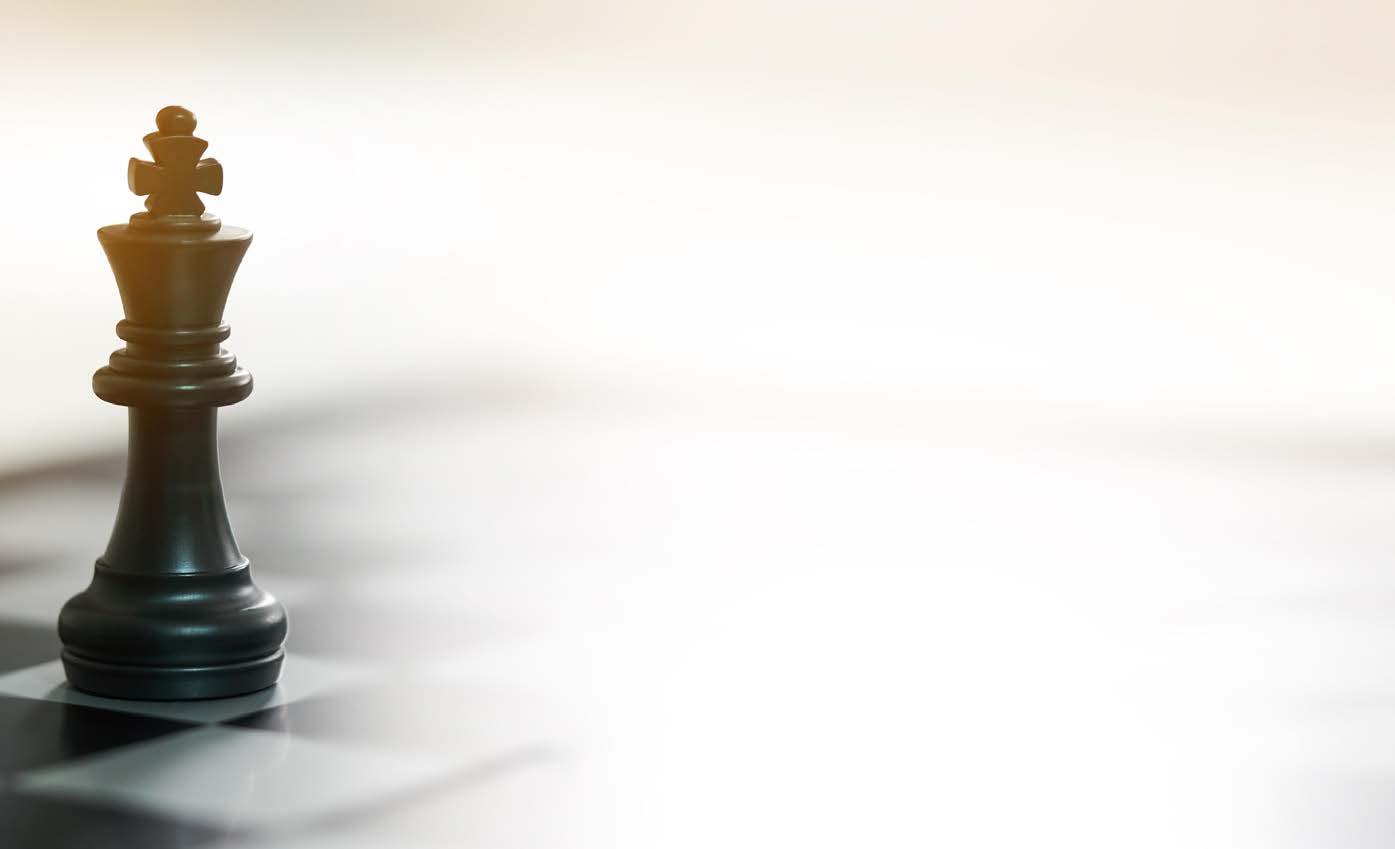

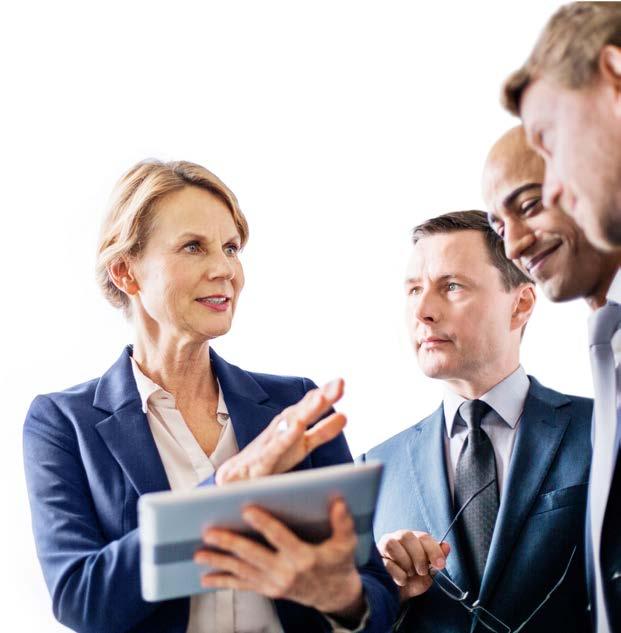

Partner with us to grow your audience, establish your thought leadership and elevate your brand. WHY PARTNER WITH US? WE CONNECT YOU TO 10,000+ SUPPLY CHAIN PROFESSIONALS AND HELP YOU BUILD THE RIGHT RELATIONS FOR YOUR BUSINESS DEVELOPMENT. NEW ADVERTISING OPPORTUNITIES We are introducing NEW advertising opportunities to feature your whitepaper, events and thought leadership pieces in our marketing channels such as newsletter and social media. 12 X LIVE CHAT n 1.5 hour sessions with panel discussions and networking. n Attendance from 150 -200 supply chain professionals. n Partners are entitled to create a series of 3 bespoke Live Chats, to be scheduled throughout the year to stay top of mind. 6 X LEADERSHIP SERIES n Prestigious and Flagship 5 X 1 day events n 4-5 panel discussions, audience participation in Q&A, small group networking and Leadership Panel. n Opportunity to align your brand with the Senior Level VPs from Canada’s most successful organizations. 1 X ALUMNICONVOCATION/EVENT n Celebration of SCMP graduates to bestow upon the CSCMP Designation. n An alumni event to bring together past CSCMP Designation Holders. n Opportunity to connect with some of the most recognized supply chain professionals in the industry. 4 X THINKEXECUTIVETANK n Mutually determined theme based on emerging trends. n Intimate gathering – a maximum of 12 participants per event to allow for a robust and engaging dialogue and quality networking n To include a discussions.recruitedspeaker/facilitatorhigh-profiletobebasedon 2 X STUDENT FOCUSED ONLINE EVENT n Serving students graduating from post-secondary supply chain programs in partner schools, these events will look to create connections between students and tenured supply chain professionals to foster organic networking, mentoring connections, and potentially job-hunting skills. n This event will be guided by our Presenting partner. 1 X HOLIDAY EVENT n Attendance from minimum 500 members and panel discussion with senior leader of top supply chain organization n The event featured our Member Milestones celebration, a Fireside Chat with our Partner Executive and one of our most senior executives, as well as a guest Keynote speaker. 3 X NEW EDUCATION FOUNDING PARTNERS n As we expand our focus on vertical markets, we will endeavour to create new Founding Education Partners, to support our on-going content evolution serving our strongest supply chain communities. Contact Kim Sforza at ksforza@scmao.ca or 416.977.7566 x2134


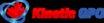

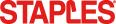





An increasingly common bearing material is phenolics, which provides
Plastic bearings made from poly mer-based materials like Nylon and Teflon have grown in popularity due to their benefits in less demanding applications where stresses like tem peratures are less frequent. Plastic bearings are stronger, more corro sion resistant, need lubrication less often and last longer. speeds and temperatures. This tech nology can help with maintenance, as many systems provide real-time data to track performance and keep maintenance on schedule. Select industries are adopting IOT in bearings, including agricul ture and wind energy. This will con tinue, especially as the automotive industry embraces it. With the growth of electric vehicles, the time is near for multi-purpose bearings such as IOT enabled bearings, as EVs have fewer moving parts than combustion-engine powered cars, requiring fewer bearings. However, the limited number of bearings now in the car demands more functional ity for greater energy efficiency and reduced fuel consumption. Remote monitoring, while beneficial for some applications, isn’t a one-sizefits-all approach across industries and the technology is still limited.
The related bearing lubricant catego ry has also evolved and there’s an increased focus on sustainability. Examples of this include biodegrad able grease, water lubricated bear ings and the correct processing of lubricant waste. Biodegradable grease and water lubricated bearings provide “greener” choices, as these options are less harmful to the envi ronment and employees. As with any
Nylon is common in applications needing quieter operations and higher-than-average abrasion resis tance. Nylon bearings offer better wear resistance, making them good alternatives to all-steel bearings.
A common component in the man ufacturing and industrial applica tions is bearings. These steel pow erhouses play important roles in operating of machinery, like reduc ing friction, maintaining alignment or supporting loads. They come in several sizes, from massive spheres used in wind turbines to smaller ver sions for conveyor systems on pro duction lines or distribution centres. Bearings have evolved the last 20 years in composition, technological functionality and sustainability. Another growing product option is the hybrid bearing. It combines a steel ring with rolling ceramic com ponents. This format can be inter changed with traditional all-steel bearings for improved reliability and excellent electrical insulation proper ties. Hybrid bearings have a higher speed capability and are more resis tant to abrasive particles. This means a longer life than all-steel bearings.
BY MARIETE F. PACHECO strength and shock resistance to acid and water, making them ideal for demanding applications in water tur bines, ship engines or electrical switchgear. Lastly, Delrin, used in automotive and industrial applica tions where water resistance at low cost makes it an alternative to steel.
SUPPLYPRO.CA 19
ADVANCES IN LUBRICANTS
Mariete F. Pacheco, MBA, PMP is managing director at FRW Services Ltd. ADAPT WITH AND
Teflon or PTFE bearings offer the advantages of a low-friction materi al plus higher-than-average self-lu brication. Teflon bearings are often used in applications with high expo sure levels to water or chemicals. But they can be more expensive then metal-based bearings.
The growing interest in incorpo rating technology into static devices like bearings is shifting towards mass industrial adoption. While new, including IOT (internet of things) in bearings lets users monitor bearing performance and conditions, for example vibration analysis, loads,
PERFORMANCEENHANCED BEARINGS AND LUBRICANTS
NEW MATERIALS
TECHNOLOGY
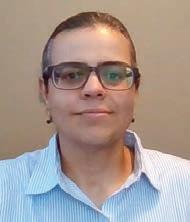
Additional best practices include development of a lubrication pro gram and having a proper storage system. For a lubrication program, identifying each component’s unique needs is paramount. These can include types of greases versus oils, along with how often bearings are lubricated. In addition, ensur ing that training is included in the program is critical so that correct procedures are followed for main tenance, usage and inspection. All of this contributes to equip ment longevity and employee safe ty. Too much or too little lubrica tion can impact friction levels, which can cause excess wear and tear or accumulation of dirt and debris, leading to higher temperatures.Thereisabalance to identifying correct lubrication levels and fre quency. A well-organized and labelled storage system is critical in ensuring the correct lubricants are used, especially when bulk lubricants are packaged in similar formats, confusing users that don’t reviewing the labelling carefully.
Organization and labelling can also help inventory management, as properly labelled inventory can be easily identified and accounted for instead of ordering unnecessary inventory due to poor storage practic es. Adequate storage space is key in a lubrication program. This can include criteria such as indoor versus outdoor space or covered versus uncovered spaces. These can help maintain lubricant performance due to temperature changes, water expo sure or contact with light.
The bearing and lubrication industry is not immune to the global supply chain issues started by the COVID-19 pandemic. Like others, the industry faced raw material and labor shortages, since early on they were directed to produce more urgently needed products like PPE or other healthcare and medical devices. These shortages, coupled with escalating freight costs, drove not only massive price increases but exasperated the situation as organi zations would order more than they needed to hedge against any future supply chain issues. This caused a demand cycle that outpaced supply. There are possible alternatives to mitigate supply chain challenges, including researching substitutions. Pivoting between different suppliers or products offers flexibility to smooth out price swings as well as mitigating product shortages, which is critical in many JIT industries likeBearingsautomotive.and lubricants have pro gressed in performance and material structure, in part due to performance requirements and changing customer expectations, as well as partially due to long-term supply chain concerns. Although a relatively simple compo nent of a much larger system, the bearing and its associated lubricants remain vital to many industries, from energy to automotive to warehousing and most everything in between. They will continue to adapt as mar ket demands shift and new technolo gies arise.
SP
20 AUGUST 2022 SUPPLY PROFESSIONAL
hazardous waste, there is more scru tiny when processing oil-based prod ucts. It’s essential to use licensed waste management companies to collect and dispose of used lubricants due to the growing customer interest in sustainability and the strict regula tory guidelines and associated fines. For bearings and lubricant pur chasers, align the application with the material. As demonstrated above, each material provides a different level of load applications, tempera ture tolerances and durability that can impact its overall performance.
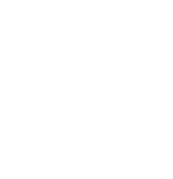
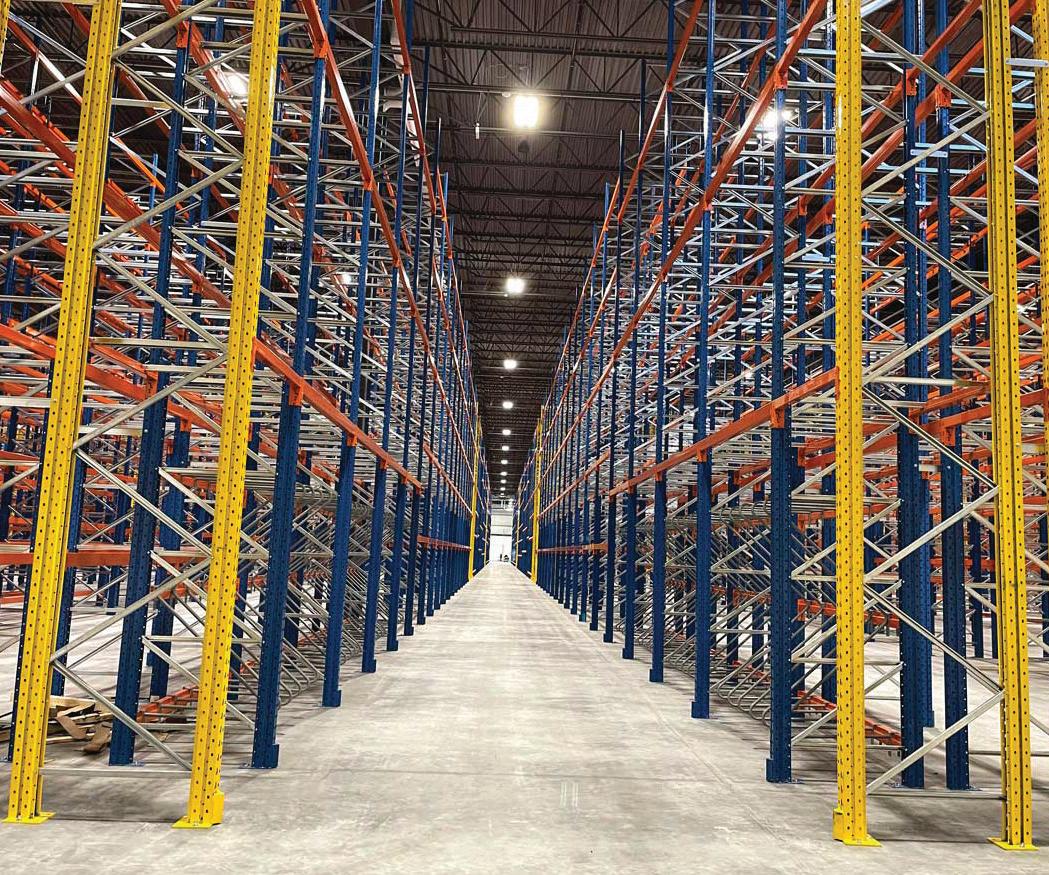



Certainly, customer demand and experience expectations have drastically changed.
“There has been a spike in interest as a result of the pandemic, but I think it created a realiza tion, for a lot of companies, about the vulnerabil ities that they have and problems they were aware of before COVID in terms of processes that were entirely manual,” says Ryan Weaver, vice-president, Commercial at Robotiq. Markus Schmidt, president of Swisslog, agrees. “Not knowing if your workers are going to come to work, during a pandemic or not, has been a nightmare for everyone in the supply chain, not to mention labour costs keep rising,” he says.
Automation has been a key part of logistics for decades—albeit early adopters have mainly been Fortune 500 companies. In the past few years, however, there have been advancements in robotic and automation technology, which has lowered investment costs, making it a more attractive option for any size of operation. Is it the race toward Industry 4.0? Or has this uptick been a result of the pandemic? Industry experts say that it’s a bit of both.
Regardless of an operation’s size, labour has always been an issue and the pandemic has accentuated it more. Not only is there a manual labour shortage, but the reliability of the work force that might be attainable is also a big uncer tainty for many companies.
“When Amazon started offering Prime delivery, that was a huge accelerant to all the automation that’s being adopted. They started to use the fulfillment experience as a weapon rather than just reducing costs. And that’s driven a lot of innovation and pushed everyone forward,” says Leif Jentoft, co-founder and chief strategy officer at RightHand Robotics.
ARTIFICIAL INTELLIGENCE
“In the past five years there has been an explo sion in goods-to-pickers systems like Auto Store or OPEX for auto storage and retrieval. This is interesting because you can increase the storage density, increase the facility through put, and scale your businesses, even in the face of labour shortages. But what we’re seeing is that’s still not enough for companies to deliver a customer experience or meet demands. What people are looking for now is the next step in the process, which is picking and plac ing, and that’s where we live.”
SMART MOVES ROBOTICS AND AUTOMATION HELPS BOOST LABOUR AND MAINTAIN A RELIABLE THROUGHPUT BY NOELLE STAPINSKY SUPPLYPRO.CA 21
“We focused on the piece level. It’s not cases or pallets, but individual items that have varia tions from one piece to the next. Like picking up your sunglasses and then your phone or
“The more you can automate, the more indepen dent you become of those conditions. The other issue is that supply and demand is out of control.”
RightHand Robotics’ RightPick platform is a turnkey modular solution that uses artificial intelligence (AI) to learn as it picks products.
a shampoo bottle,” says Jentoft. “When people deploy our systems, they want something that works like a manual picker. It’s told where to pick from, where to pick to, and reports wheth er it was successful. The AI handles the range of variations of different objects. If you have 15,000 new SKUs coming in at Christmas, you don’t want to have to retrain the robot and our system doesn’t need that. It knows what it sees, what it did, how it happened, and can use that information for new items.”
Once a pallet is completed, a stack light on top of the tower indicates that it’s ready, meanwhile the robot will start building the second pallet.
“By automating the labour intensive, repetitive tasks, the throughput gains will be noticeable when you factor in breaks, sick days, or the days you can’t run production because you don’t have the people. This allows employers the opportunity to avoid workplace injuries and assign the workers they have to higher value tasks,” says Weaver.
The Swisslog CaddyPick is a semi-automated order picking system for mixed case pallets and roll cages that runs on a monorail and is a mixture between a person-to-good and a zone-to-zone picking solution. And its CarryPick mobile robotics system is a goods-to-person application that is an automated storage and picking solution designed for multi-channel intralogistics.
While picking and placing technology is defi nitely a trend that’s picking up steam, Schmidt says that there is a push for mobile robotics because they offer a reasonable investment with a lot of flexibility. “Mobile robotics can replace forklifts and, in some cases, conveyors.
MOBILE ROBOTICS
Two pallets can be placed on either side of the robot, which has sensors confirming the pallets are in place. While other gripper heads are avail able, the AX Series uses a vacuum technology to grip the products or boxes from a conveyor sys tem or another type of infeed and place the item on the pallet. The current AX Series can pick items up to 16kg, but Weaver says that Universal Robots announced the UR20, an arm that will handle a 20kg payload.
Swisslog’s customers are looking for more mechanized and automated solutions. “We look at a distribution’s operations and determine their orders, how many cartons or pallets they need to move and store, and then we come up with a solution around the space and labour require ments,” says Schmidt. “We would estimate an investment around that solution, see if we can off set it by savings on the operations side and justify the use of automation in the financial sense.”
Quebec-based Robotiq’s AX Series Palletiz ing Solution is built around Universal Robots, which is a market leader in collaborative robot ics (cobots). “The fundamental difference between a cobot and an industrial robot is the fact that it has safety built into it to enable it to work alongside a person without the necessity of guarding. It has a lower complexity user interface which provides a better user experi ence compared to script language used with tra ditional robots,” says Weaver. “The AX Series incorporates a vertical lift axis, which means we put the robot on a lift and can coordinate the motion of picking at the conveyor to building a pallet up to 108-110 inches high. That gives us a lot more vertical accessibility than what a robot arm could achieve on a stand.”
In a goods-to-person scenario, where the robots bring the goods to somebody at a pick ing station, it opens new avenues for solutions that were not there before,” says Schmidt.
SP SUPPLY PROFESSIONAL22 AUGUST 2022 SUPPLY PROFESSIONAL
“In the interface, there’s only a few steps the user needs to do. You don’t need to know how to program a robot, you just need to know what your product is and how you want it to be arranged on the pallet. The user enters the box dimensions, what side the label is on and if they want it facing outward, how they want each layer laid out on the pallet. And then all we have to do is define the pick-up location of the box,” says Weaver. This can be tested on the Palletizing Configurator.
“As soon as you automate, you have perfect traceability and a perfect way of collecting all the data involved. But software is key, it’s the heart of every warehouse. And it needs to be nicely orchestrated to function the way the oper ator wants it to,” says Schmidt.
In fact, the return on investment (ROI) for pick and place and mobile robotics solutions presented in this article, according to the com panies, can be two years or as quick as 18 months. In one case, Robotiq supplied a choco late factory with its palletizing solution, and when the company calculated a six-month ROI, it bought six more.
Over the past two years, Weaver says that there has been significant interest in cobotbased palletizing from companies that lack automation on the floor. He says that they are now seeing benefits – especially with a lack of workers – at a price they can justify.
SUPPLYPRO.CA 23 24 Plugged into the grid Policy tips for connected fleet vehicles. 26 Road test Driving the GMC Terrain. 28 managementRecall Preparing for recallmanufacturerswhenvehicles. ManagementFleet Fleet Management is a special section of Supply Professional magazine. It is an important resource for Canadian supply professionals who recommend, select and manage fleet vendors and service providers. EDITORIAL INQUIRIES: Michael michael@supplypro.ca416-441-2085Power,x110, ADVERTISING INQUIRIES: Alex 416-441-2085Papanou, x101, apapanou@iqbusinessmedia.com 26 29 29 anMaintenancedrepairs Keeping fleet upkeep costs under control.
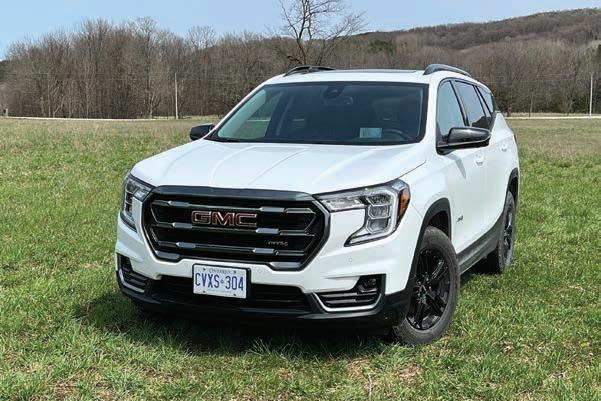
WiredManagement up Policy tips for fleets with connected vehicles
24 AUGUST 2022 FM/SP SUPPLY PROFESSIONAL 1. 2.
We live in a world where people are constantly ‘plugged in’ or con nected to a variety of sources and to each other. Our cell phones pro vide that connection for the most part, but when we step into our vehicles, its embedded technology takes over. Modern vehicles are sensor-laden, mobile, Internet of Things (IoT) devices with systems devoted to three areas:
Vehicle to Pedestrian (V2P): Vehicles use sensors to detect Vpedestrians.ehicletoEverything (V2X): The combination of all types of connectivity is known as V2X With the future of connected vehi cles quite clear, fleet professionals must consider the implications for their organizations and be proactive in putting policies in place to gov ern their use. The following four areas should be addressed – priva cy, allowable features, driver dis traction and reporting. Privacy: Connected vehicles can share the internet with devices inside and outside the car, and at the same time share data with external devices. V2X is becoming standard and comes with privacy risks. Automated and connected vehicles generate an enormous amount of data, some of which is sensitive or personal. Employees may not want to share precise geo location data or the contents of pri vate conversations on a mobile phone that is connected to a vehi cle’s computer system. Another privacy consideration involves vehicle resale. Fleets need to disable remote start or unlocking applications from the driver’s mobile phone prior to remarketing theAlthoughvehicle. privacy is a serious issue, it’s nothing new. Even out side a vehicle, everything we do in public can be seen and tracked by cameras or our mobile phones. Pol icies should acknowledge this and ensure drivers are aware of what information is tracked, what is retained and how it is used. Allowable Features: Connected vehicles can be equipped with a range of smart and convenient fea tures. These features may improve the overall driving experience and enhance safety. They can also, however, create distractions or threaten privacy. Fleet profession als must consider these pros and cons when purchasing vehicles. Even after purchase, they should consider which options or features bring benefits without compromis ing safety or privacy. Some exam ples of desirable features are:
V2V connectivity can notify drivers of road conditions or events like collisions in advance. This allows drivers to slow down and prepare for the circumstanc es in advance, or to reroute.
3. Infotainment – providing infor mation and entertainment to the driver and passengers. Over 90 per cent of new cars are considered connected vehicles, with advanced capabilities and technolo gy on board. Common fleet vehi cles fall into this group, from prac tically every ConnectedOEMvehicles may use dif ferent types of technologies such as: Vehicle to (V2I): CommunicationInfrastructurewith the road infrastructure on traffic, road, weather conditions, speed limits and collisions. Vehicle to Vehicle (V2V): Allows the real-time exchange of information between vehicles. Vehicle to Cloud (V2C): Mainly used for downloading vehicle updates, remote vehicle diag nostics or to connect with any IoT devices.
Connected vehicles may allow connection to pre-loaded enter tainment services. This can make it easy for drivers to lis ten to music without the dis traction of trying to find a radio
Sstation.ecurity features such as realtime location sharing, emergen cy calls in case of a collision and roadside assistance are Organizationalinvaluable. policies should describe the beneficial features of the vehicle, and stress safety and privacy. They should also cover fea tures that should not be used. Driver Distractions: Even before the rise of connected vehicles, dis traction was a factor in 80 per cent of collisions. Adding additional potential distractions could be disastrous. This is where a strong safety policy can help. Policies should define distracted driving and state which behaviours are not allowed. They should give exam ples of actions that a driver may not engage in while driving. This includes use of mobile devices (hands free or handheld), adjusting controls or planning routes. Drivers should adjust controls before a trip.
1. Telematics – vehicle location and activity, driver behaviour and engine diagnostics.
Reporting Matrix: Information generated by connected vehicles is valuable and should be used to ensure efficient fleet management. A reporting matrix is an excellent tool to demonstrate what informa tion should be collected and report ed to what level of management and at what frequency. To create a reporting policy, first establish what information must be gathered. After that, you can design and establish indicators and deter mine how often data will be gath ered and Connectedanalyzed.vehicles are here and fleet policies must catch up. These vehicles bring benefits to fleets with access to a range of infotain ment, advanced navigation sys tems, safety features and enhanced security features. They also bring risks associated with distracted driving and privacy. A robust con nected vehicle policy benefits every organizations dealing with con nected vehicles. FM/SP Kate Vigneau, CAFM, is director of fleet, MCG Consulting Solutions.
By Kate Vigneau Fleet
2. Surrounding environment –vehicle-to-everything (V2X) communication.

The Hyundai Kona EV is a great example of a fleet-friendly BEV. It’s affordable, city-friendly, and qualifies for electric vehicle rebates. It of fers a maximum estimated range of 415 kilometres, which is a healthy amount for a typical fleet’s daily duty cycle. Plus, drivers can make the most of the Kona’s regenerative braking ability to recharge the Kona EV’s battery while on the road, maximizing available driving distance and re ducing range anxiety. Whatever your fleet’s duties and objectives, there’s an innovative powertrain solution to help meet the needs of your business while re ducing your fleet’s fuel-related operating costs. And with a variety of SUV classes and powertrain options to choose from, your drivers can enjoy more powerful and more efficient vehicles whenever they’re out on the road. Hybrid Plug-in Hybrid Battery Electric Vehicle
The plug-in hybrid or PHEV is similar to a conventional hybrid in how it operates, but a larger rechargeable on-board battery means a PHEV can travel for a distance – typically in line with the average daily commute – fully on electric power. For some drivers, this means daily driving can be done without burning any fuel at all, but there’s still a gas-powered motor on board to power longer trips. For drivers who do most trips in the city but occasionally are sent further afield, PHEVs offer the best of both worlds.
Considering electrification for part, or all, of your fleet? You’re not alone.
Both the Tucson and the Santa Fe are available with plug-in hybrid powertrains, in each case through pairing the 1.6-litre turbocharged engine with a larger on-board battery that’s partially recharged by plug ging the vehicle in overnight. In the Santa Fe PHEV, this provides up to 50 kilometres of all-electric range, which can be recovered in just over 10.6 hours through a household outlet or in 3.4 hours by plugging into a Level 2 charger. The Tucson PHEV has an all-electric range of up to 53 kilometres and needs just 1.7 hours to recharge at Level 2. Both vehicles are more powerful than their HEV counterparts, and both can achieve even better efficiency when charged and driven to their full ca pabilities. In some cases, they may also qualify for federal and provincial rebates for electrified vehicle purchases.
When assessing how electrification might make an impact on overall costs, fleet operators most often choose from one or more of the three most common electric powertrains. Find out which one is right for you and your business.Theconventional hybrid or HEV uses one or more electric mo tors powered by a small on-board battery, which recovers its charge from the engine’s operation and through energy recovered from braking, a technology known as regenerative braking. This type of hybrid can’t travel on electric power alone for long distances, but it also doesn’t need to be plugged in to operate at peak efficiency, which means there’s zero learning curve for your drivers.
Advertisement Conventional
The right EV can help any fleet reach its business goals
In a compact SUV like the Hyundai Tucson Hybrid, fleet operators can offer drivers a vehicle with all-wheel drive and 1,097 litres of cargo space, compared to the 1,095 litres found in the internal combustion engine (ICE) version of the Tucson. It offers identical everyday routine and convenience to an ICE vehicle, while achieving a Natural Resources Canada estimated fuel consumption of 6.4 litres per 100 kilometres combined. It combines a 1.6-litre turbocharged four-cylinder engine with an electric motor to produce 227 horsepower and 258 pound-feet of torque: that’s more power and more efficiency than the average ICE compact SUV. Need more space? Consider a mid-size SUV like the Hyundai Santa Fe Hybrid. It takes the same hybrid powertrain, here consuming 7.4 L/100km with nearly identical power figures (226 hp/258lbs-ft), and pairs it up with even more space. The Santa Fe’s 4,188 litres of total interior volume and 2,041 litres of available cargo space behind the front-row seats make it a flexible crossover without compromise.
The battery electric vehicle or BEV uses a battery and electric motors to complete 100% of driving entirely on electric power. This type of vehicle is the cleanest and most eco-friendly solution as it allows all the vehicle’s driving to be done with zero emissions.
The rising cost of fuel is increasing fleet operating costs significantly, and let ting electric motors do some or all of the work in propelling a vehicle through its daily duties can make a noticeable difference to a fleet’s bottom line.



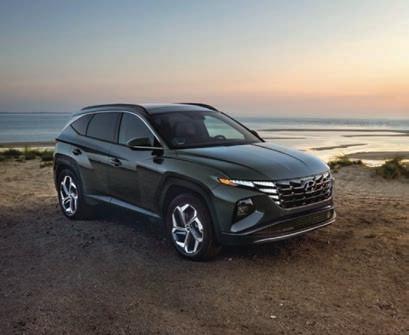
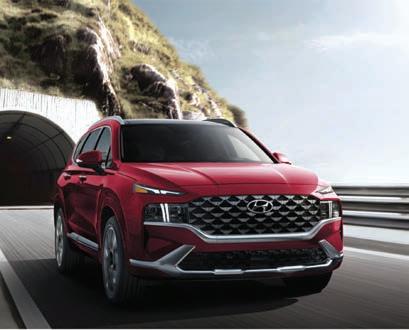

In addition, the refresh adds an Elevation Edition package, priced at $995, for the SLE and SLT grades, which are the best-selling Terrains in Canada. This package includes a darkened front grille, 19-inch gloss black aluminum wheels and black centre caps with GMC lettering, black roof rails, black mirror caps, and black exteri or accents and badging.
Same powertrain What doesn’t change for 2022 is the powertrain: the Terrain still features a 1.5-litre turbocharged four-cylinder engine producing 170 horsepower and 203-pound-feet of torque. This same engine is equipped in the relat ed Chevrolet Equinox SUV, but the Terrain gets a more sophisticated nine-speed automatic transmission to go with it. This engine feels energetic at lower speeds thanks to the turbo charging and short lower gears, but power does taper off in higher-de mand environments such as on high way merges or while climbing hills. A more powerful engine option, at least in the Denali trim, would be a welcome addition. The Terrain’s inte rior is noisier, and the ride is rougher relative to its competition. Shifting is completed through buttons and trig gers, an intuitive solution that frees up some space in the centre console area, as much as some drivers may prefer a traditional shifter. For an internal combustion engine, fuel consumption in the Ter
Rugged look,solid value Test driving the competitively priced GMC Terrain Off-road capability – or, at the very least, the appearance of it – is very much on trend in the automotive industry. Mainstream SUV designs are getting more rugged looking through the addition of roof rails, skid plates, and glossy black accents, to name just a few highlights. For 2022, the GMC Terrain joins in with its new AT4 model, which adds a fourth trim for this model year as part of a mid-cycle refresh for the compact SUV. All 2022 Terrains come with an updated front fascia and more dom inant larger grille. LED headlights and taillamps are now standard and have been redesigned, and new wheel and exterior colour options are available.
26 AUGUST 2022 FM/SP SUPPLY PROFESSIONAL
The Terrain AT4 off-road oriented trim was introduced in 2019 on the Sierra pick-up truck and has slowly been making its way into other GMC vehicles. Starting at $38,198 includ ing fees and a $1,900 destination charge, AT4 gives GMC’s smallest vehicle a steel skid plate under the engine compartment, a drive mode selector with three settings, unique 17-inch gloss black wheels, and con trasting tan interior stitching, along with exterior and interior AT4 logos. Since there are no changes to the sus pension or ground clearance, these changes are largely aesthetic apart from the skid plate. However, the Terrain AT4 is priced affordably and will please buyers looking for an out doorsy appearance.
Fleet Management By Stephanie Wallcraft
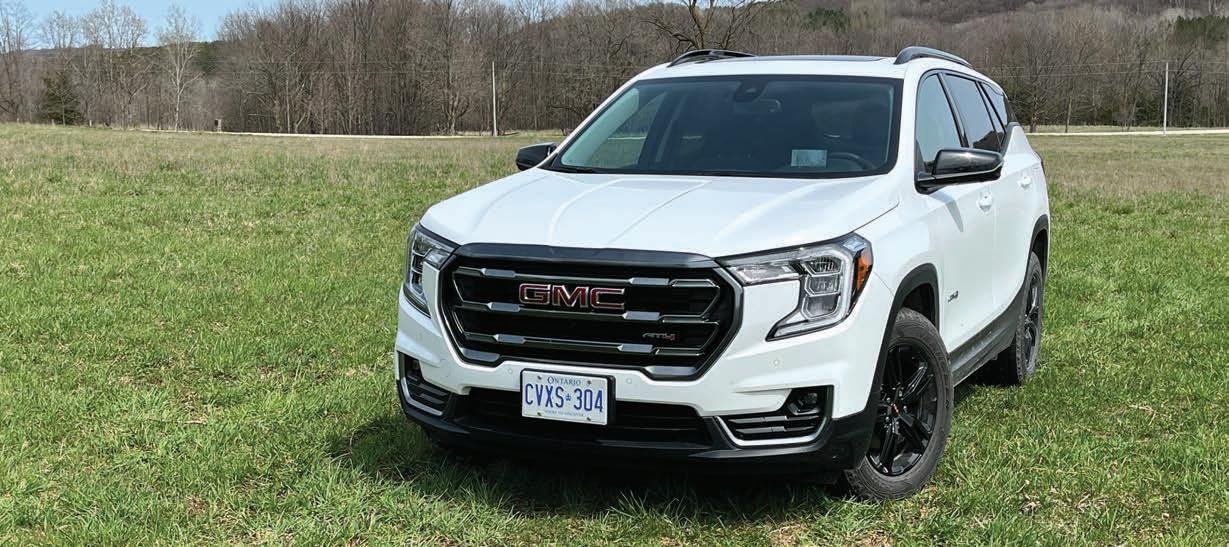
2.
SUPPLYPRO.CA 27FLEET MANAGEMENT
rain is roughly average at 9.2 litres per 100km in city driving, 7.8 on the highway, and 8.6 combined with front-wheel drive, or 9.6 city, 8.3 highway, and 9.0 combined with allwheel drive. It’s worth noting, though, that there are more efficient powertrains on the market in this size class, both electrified and otherwise.
Technology On the technology side, the Terrain now includes standard wireless Apple CarPlay and Android Auto connectivity, a welcome addition to an infotainment system that was already intuitive to operate. Heated and ventilated seat buttons were present on the vehicles we tested, but both features are currently being omitted from builds due to the glob al chip shortage. They will be equipped later at no charge through As Tested (AT4)
1. The 2022 GMC Terrain features standard wireless Apple CarPlay and Android Auto connectivity, while shifting is completed through buttons and triggers, freeing up space in the centre console area.
Price (incl. freight and PDI): $38,198 Engine: 1.5L four-cylinderturbocharged Power: 170hp, 203lbs-ft Transmission: 9-speed automatic Rated Fuel Economy (L/100km): 9.2 city/7.8 hwy/8.6 combined (FWD); 9.6 city/8.3 hwy/9.0 combined (AWD) Observed Combined Fuel Economy (L/100km): N/A (first drive too short to assess fuel economy)
For fleet buyers, the likelycompactTerrainchoosingadvantagegreatesttotheoverotherSUVsisinitsvalue.
2. The vehicle offers 838 litres of cargo space with the rear seats upright and 1,793 litres with them folded. a visit to a dealer once supply catch es up, and GMC is offering a $50 rebate to customers for the inconve nience in the meantime.
Front-wheel drive is standard on the entry-level SLE trim, which starts at $32,598 including fees, a slight price drop from 2021. Allwheel drive is available on SLE for $2,400 more and becomes standard at SLT, which is priced from $37,598. The Denali grade, GMC’s signature line-up topping grade, starts at $43,598. This is $1,000 more than the 2021 model, but there’s now more standard feature content including adaptive cruise control, a head-up display, a sur round-view camera, blind spot moni toring and rear cross traffic alert, parking assist sensors, and more.
For fleet buyers, the greatest advantage to choosing the Terrain over other compact SUVs is likely in its value. Pricing is competitive, and GMC tends to retain excellent resid ual values, which is helpful because it allows for affordable leasing rates and better cost recovery when a vehicle reaches the end of its life cycle within a fleet. While the refresh for the 2022 model year mostly adds aesthetic elements, the 2022 GMC Terrain continues to be a solid and relatively affordable offering in a mid-premi um SUV. FM/SP 1.

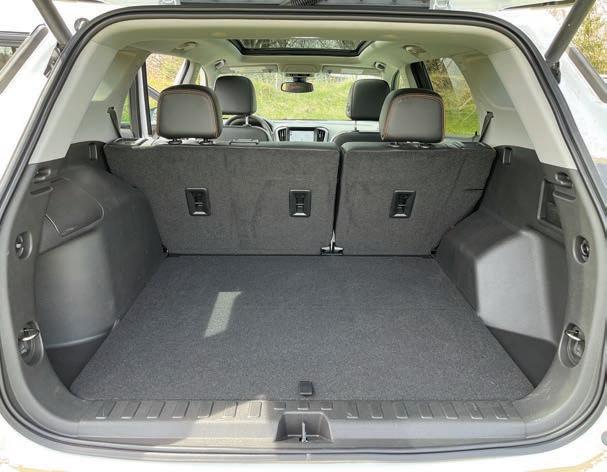
The other big consideration is what happens with leased vehicles? As we already know, only the original owner of record gets a recall notice. So, that would be your leas ing company, not you. To deal with this, first determine who owns the vehicles. In Canada, the most common arrangement will be a financing entity affiliated with the automaker that is the actual owner of the vehicle. Despite this, you as fleet manager can register your VIN numbers on the manufacturer sites, which would give you access to recall notices. The second part of being pre pared and forewarned about recalls on leased vehicles has to do with the lease agreement itself. The prospect of a major safety recall should prompt managers to carefully review their lease con tracts. While automakers are required to provide safe vehicles, it is important to determine how the lease agreement will handle recall situations. As an example, during the highly publicized “Die selgate” scandal, some drivers of Volkswagen leased models were initially told they could either park their cars or turn them in before the term of their contracts expired, which would have come as a financial loss. Breaking the lease may be an option when the con tract stipulates that the leasing company must provide a safe vehi cle at all times. As with everything, planning is key. Know about the recall before the letter arrives and have a plan in place to handle it. FM/SP
FM/SP SUPPLY PROFESSIONAL28 AUGUST 2022 By Howard J Elmer Fleet toReturnManagementsender
Leased vehicles
Tips for fleet managers to handle recalls
new legislation and ongoing dis cussions with manufacturers relat ed to offering consumers the right fix for an issue – whatever it is. Anyone can scan these releases as often as they want. A more direct approach to checking the background (and cur rent condition) of your fleet is to use the VIN search tool that NHTSA provides. Input your vehicle’s VIN number and the site will give you any vehicle safety recall in the past 15 calendar years. Here at home, it’s Transport Canada that is responsible for col lecting recall information and making sure it goes out to those affected. Much of what you’ll find on their safety recall page is identi cal to what NHTSA carries – as the country of manufacturer origin is responsible for collecting com plaints and responding through consultation with the manufacturer.Oncearecall becomes official the method of contact is very archa ic. A mailed letter goes out to the registered owner (and only the first owner) as a notice. So be aware, if you bought a fleet vehicle used, you need to register with the car compa ny so they can mail you the recall letters. Otherwise, the letters will go to the original owner. Recall notices also appear on Transport Canada’s website, the same as on the NHTSA site. Cana da also offers a recall update site where anyone can check out cur rent and past recalls (the database goes all the way back to 1970). However, they also let you sign up for automatic recall updates that will come to your inbox. This is a feature that fleet managers should take advantage of. The other feature that these gov ernment sites offer is proposed future legislation. So, who cares, right? Well in these releases you will find items that are going to cost you and your fleet money, whether sooner or later. For instance, just this month the US Department of Transportation’s National Highway Traffic Safety Administration final ized a rule that updates two Federal Motor Vehicle Safety Standards to improve protection for drivers and passengers in light vehicles in the event of a rear underride crash. Quoting from the release: “These crashes, which are often deadly, occur when the front end of a vehicle crashes into the back of a larger vehicle, such as a large trailer or semi-trailer, and slides under that vehicle. This rule, along with increased research and the creation of an advisory committee on under ride protection is the result of Presi dent Biden’s Bipartisan Infrastruc ture Law and is a key part of USDOT’s 2022 National Roadway SafetyWhatStrategy.”Ireadis that semi-trailers will soon be required to carry a new type of crash prevention fea ture. As a fleet manger, you want to know if you will be responsible for retrofitting your trailers – or will you have to lease new ones? Know ing about this pending cost early is simply good management.
An almost invisible part of a fleet manager’s job is handling manufac turer recalls. In some cases, recalls can be taken care of during sched uled maintenance. In other cases, however, it may mean grounding a vehicle because of imminent safe ty concerns. This possible spectrum of action, from simple fix to parked, carries a rising cost. Despite manu facturer recalls being “free,” han dling them isn’t. In 2021 the National Highway Traffic Safety Administration (NHTSA) in the US issued 1,093 recalls. These vehicle safety recalls come from major light auto manu facturers, motorcycle manufacturers and some medium/heavy truck manufacturers. With over three recalls every day, chances are that at some point your fleet will be affected. So, accepting that recalls are simply part of business, the cheapest way to handle them is to be proactive. Recall process Recalls don’t happen overnight. In fact, the larger ones make the news long before the manufacturer gets around to offering a fix and sending notices to owners. A lag of a year is typical. For this reason, the NHTSA and Transport Canada (which mirrors the American agency’s function in our country) offer a continuous flow of press releases about potential issues,
With over three recalls every day, chances are that at some point your fleet will be affected.
AgingManagement well
Brian Antonellis is senior vice-president of fleet operations for Fleet Advantage.
By Brian Antonellis Fleet
Fleets should leverage data ana lytics for asset management and procurement, along with flexible lease solutions. Finance options like sale-leaseback and temporary lease extensions can satisfy shortterm needs without damaging longterm procurement goals. There are steps to keep fleet vehicles well-maintained, especially with vehicle supply limited, including:
Preventing excess M&R spend
Heavy-duty truck original equipment manufacturers (OEMs) have struggled with inventory trucks and many component parts over the past year. The semicon ductor shortage has also hit assem bly lines for Class 8 buildouts.
2 Understand extended warranty cost from OEM or third party to allow predictable cost increases.
1 Understanding the diesel particulate filter (DPF) lifecycle. Track regeneration frequency by replacing high-DPF regen eration units and focus on upstream causes; and Ensure technician training.
ReviewfocusCPIteam,neededleasing.Withthisvisibilitycomesmuch-confidenceintheleadershipdespiterisingCPIratesandequipmentsupplychallenges.Forfleetslockedinafull-servicelease,feweconomistsseetheratedecliningsoon.Whilelockedin,theyshouldre-evaluatetheirlonger-termtruckacquisitionstrategiesandplantoconverttoamoreflexible,unbundledlease.Thisincludesamulti-yearprocurementforecast,notyearlyplanning.AgingtrucksandanM&Rcanerodebottomlineprofit.M&Rfromoperationsandfinanceangles.Usepracticestokeepawell-maintainedfleetontheroad,withhappydriversandalifecycleapproachtotruckprocurement. FM/SP
In many of these lease agree ments, fleets include maintenance with additional time and materials. So, they’re seeing the consumer price index (CPI) increase in gener al and in parts ranging from 15 to 30 per cent on individual items. Parts availability and shortages complicate this.
Also, it’s still essential that driv ers do daily vehicle pre-trip inspec tions, checking engine lube oil lev els, tire pressure, service brake adjustment and air system leaks. Keeping M&R costs in check is critical, especially amid inflation. Cost control options exist; depending on your lease structure – full-service or unbundled – fleets may have a choice regarding what’s included in M&R costs. There are variable inputs that make up these costs, and it’s not as simple as looking at M&R as one bucket. Fleets must dissect all M&R parts and components, includ ing tires, brakes, service and repairs. Fleet personnel should go line item by line item, reviewing effi ciencies in each maintenance cost centre to determine how rising costs affect scheduled maintenance, preventative maintenance, as well as tire and brakes replacement.
SUPPLYPRO.CA 29FLEET MANAGEMENT
If a fleet typically runs 500 trac tors, and there was an expected downtime of eight to 10 per cent, parts costs and labour have increased if they’re in a full-service agreement and the (CPI) increases.
ACT Research shows subdued Class 8 orders, averaging 21,300 per month and falling to 15,800 in April. This slip in production has caused OEM’S to avoid commiting to 2023 calendar production pricing or slots allowances. The drop will extend high prices for used trucks. Supply chain challenges have put companies in an uncomfortable situation in which norms have been discarded. Budgets that used to increase between one and three per cent are now seeing double-digit increases. Trade cycles that ran for decades are now impossible, as they can’t backfill their equipment.
Regarding tires, review tire data to look for failure trends, pres sure-related failures, and a geo graphic analysis as certain termi nals/DCs can identify high failure rates. Check seasonalities’ impact on temperature and its pressure effects. Review dealer support for inspections and reporting, and leverage data and tools to select the correct tire program for vocation.
Review programs tied to CPI to see if the company can renegotiate or look at different approaches to maintenance, such as unbundled
3 Focusing on basics such as tire inflation and PM compliance. Identify items previously left off the PM check sheet. Extended lifecycles mean more items to inspect: suspension hangers, frame rail corrosion and engine and transmission leaks; Out-of-service items; Extended lifecycle will add maintenance downtime; Add mechanics or partner with a third party; Be prescribed to what you out source; and Track outsourced versus inter nal repairs.
With supply chain issues in the heavy-duty truck industry, like lack of build slots for Class 8 vehicles, it’s crucial to pay attention to main tenance and repair (M&R) spend to keep trucks moving and on time, while keeping drivers happy.
Our recommendations focus on understanding cost changes driven by increasing average age and from the inflationary parts increases. When you look at P&L, understand what impacts your costs down to the line item. Working with a partner can help you understand your cost by VMRS codes and set a strategy for asset procurement.
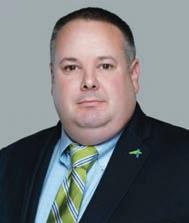
13. DEFINE MINIMUM STAN DARDS: When purchasing institu tions set a minimum past experi ence requirement, they must strictly enforce that standard; close is not good enough. For example, 69 months of experience is insuffi cient when the solicitation calls for a minimum of 72 months. Mini mum standards should therefore be carefully defined to avoid unnecessarily disqualifying bid ders with sufficient experience.
4. CLEAR PROCESS RULES: The solicitation document should clearly define the process rules for con firming the adequacy of past expe rience. Post-bid rectifications to deal with missing past experience information should only be allowed where the solicitation rules specifi cally permit those practices.
While public purchasing institutions typically want to ensure that a bid der has the required experience to perform a contract, the evaluation of past experience is a litigation hotspot that has triggered multiple successful bid protests over the years. The following article sum marizes the governing principles that apply to the evaluation of past experience. The case law has established the following legal principles for the assessment of past experience in public sector bid evaluations:
10. FIRM AND INDIVIDUAL EXPERI ENCE: Purchasing institutions should carefully define whether the past experience pertains to corporate or firm-level experience or to the experience of individuals on the proponent’s proposed proj ect team. For example, past rulings have held that individual experi ence as an employee does not con stitute contractor experience for a firm and that employee experience from prior employers does not count as firm experience for the new employer.
1. DUTY TO REJECT: Purchasing institutions have the right and duty to reject bidders who fail to meet man datory past experience requirements.
11. THIRD-PARTY EXPERIENCE: Relying on third-party past experi ence has proven contentious, par ticularly where the solicitation rules are silent on this issue. Pur chasing institutions should care fully define whether proponent past experience assessments will consider the experience of prede cessor entities, parent companies, subsidiaries, affiliates, subcontrac tors, or other third parties.
7. CONSISTENCY: The past experi ence scoring criteria and rules need to be applied in a manner consistent with the solicitation document. Evaluators should be consistent in scoring proponent past experience and in dealing with concerns of prior performance issues.
SP
2. STRICT INTERPRETATION: While adjudicators may defer to govern ment evaluators on a reasonableness standard when dealing with factual matters, past experience criteria will be subject to strict legal interpreta tion in a bid protest based on the wording in the solicitation document.
8. RECORDS: Evaluators should maintain complete contemporane ous records of their evaluations.
Paul Emanuelli is the general counsel of The Procurement Office and can be reached com.procurementoffice.paul.emanuelli@at IN BID EVALUATIONS
5. PROCEDURES FOR SELF-REFERENCES: Purchasing institutions should avoid past experience requirements that call for them to provide references to their own past suppliers unless they have adopted formal protocols to manage these procedures and their internal proce dures are prompt enough to meet the necessary bid deadlines.
14. AVOID COMPLIANCE TRAPS:
16. AVOID ANECDOTAL EVIDENCE: Evaluators should not rely on their independent knowledge of an incumbent proponent to give that bidder the benefit of the doubt since this can create an unfair advantage. As these case law principles illustrate, to better ensure the defen sibility of their evaluation and award decisions, public purchasing institutions should exercise a high degree of precision in drafting and applying past experience require ments in their bid evaluations.
6. NO ARBITRARINESS: Evaluation teams cannot be arbitrary in assessing past experience. While their evaluation decisions will typ ically be reviewed in a legal chal lenge on a reasonableness standard rather than a correctness standard, even the reasonableness standard of review calls for rational, trans parent, and logical evaluations.
THE LAW—BY PAUL EMANUELLI
30 AUGUST 2022 SUPPLY PROFESSIONAL
3. AMBIGUITY ATTRACTS REME DIES: Ambiguous past experience criteria can undermine the legal defensibility of an evaluation and award decision. A bid protest may result in a re-evaluation order, an order requiring redrafting and reis suing a solicitation document, or the voiding of a contract award made based on a flawed evaluation. In some jurisdictions, flawed eval uations can also attract lost profit awards for prejudiced bidders.
BACKGROUND CHECK ASSESSING PAST EXPERIENCE
12. DEFINE PAST PROJECTS: When assessing past experience, the meaning of a past project is not self-evident and should therefore be described in the solicitation.
Scoring past experience on a man datory compliance pass-fail basis has proven to be impractical and has attracted a disproportionate amount of bid protests. Purchasing institu tions should therefore score past experience with detailed criteria and sub-criteria and apply a minimum passing score, rather than assessing past experience as a mandatory requirement based on ambiguous pass-fail compliance standards.
15. AVOID AMBIGUOUS CRITERIA: When evaluating past experience, purchasing institutions should avoid using ambiguous criteria, hidden sub-criteria, or non-trans parent scoring methods.
9. RESTRICTIVE REQUIREMENTS: Purchasing institutions should avoid unnecessarily restrictive past experience criteria and should be prepared to defend their past expe rience standards as legitimate operational requirements.
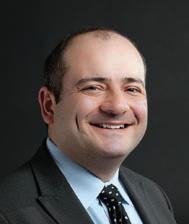
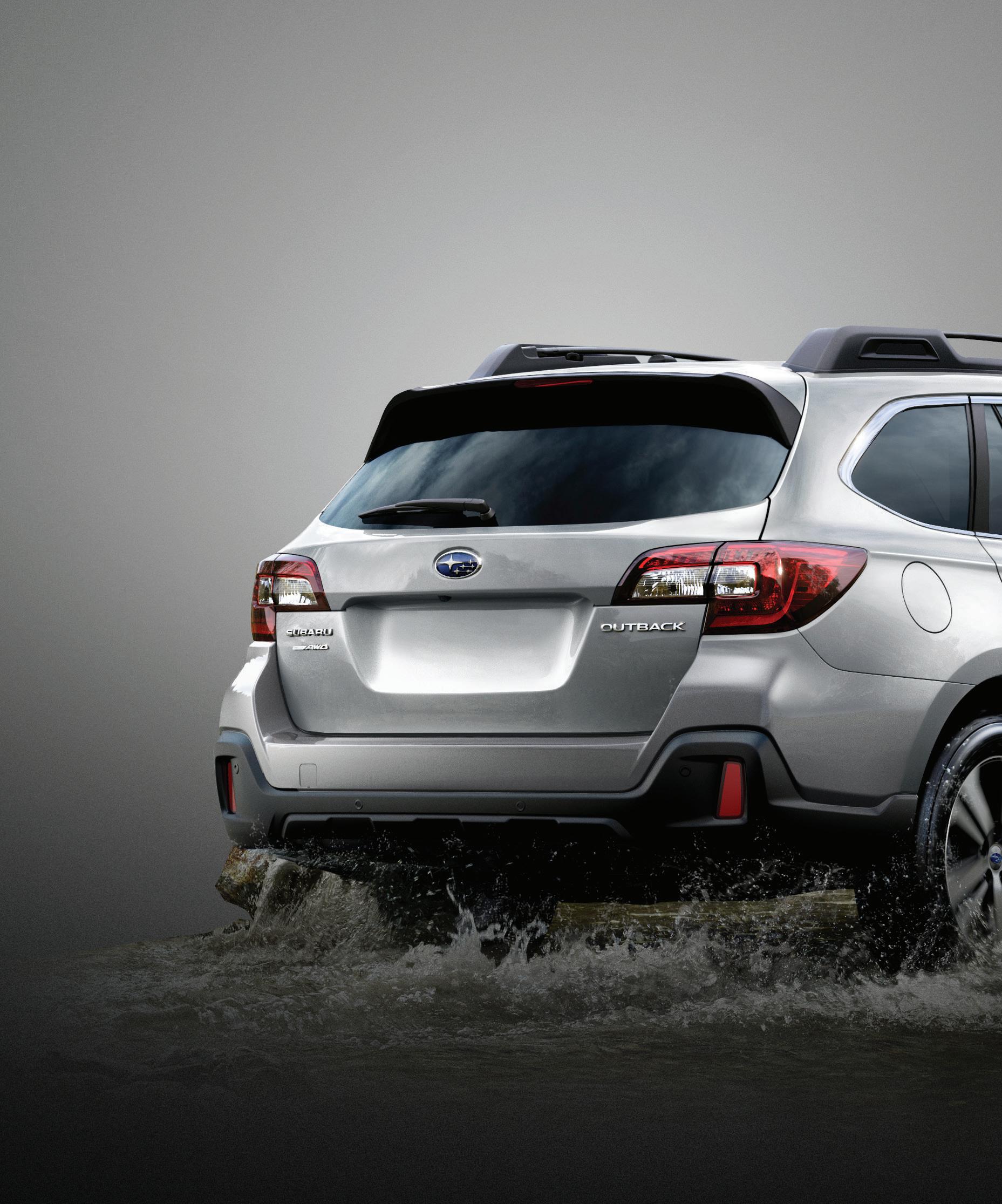
TM Innovative advance warning safety system that helps you avoid potential danger on the road. Subaru’s eye on safety. Full-time all-wheel drive for full-time confidence in motion. Superior drivability, outstanding control and handling you can count on. On-board technology system connecting your Subaru to the world. 24/7 safety and convenience wherever you go.1
From innovative features to expert maintenance, plus leading resale value, Subaru brings safety to your drivers and value to your fleet.
1. SUBARU STARLINK® Connected Services are offered on an initial three-year free subscription on select trim levels. Customers are required to enroll in the SUBARU STARLINK® Connected Services program. To operate as intended, SUBARU STARLINK® Connected Services require a sufficiently strong cellular network signal and connection. See your local Subaru dealer for complete details. 2. Safety ratings are awarded by the Insurance Institute for Highway Safety (IIHS). Please visit www.iihs.org for testing methods.
welcome peaceuncommontoofmind
2 2022 ASCENT IIHS TOP SAFETY PICK+ 2022 IMPREZA 2022 LEGACY IIHS TOP SAFETY PICK+ Visit us at subaru fleet .ca
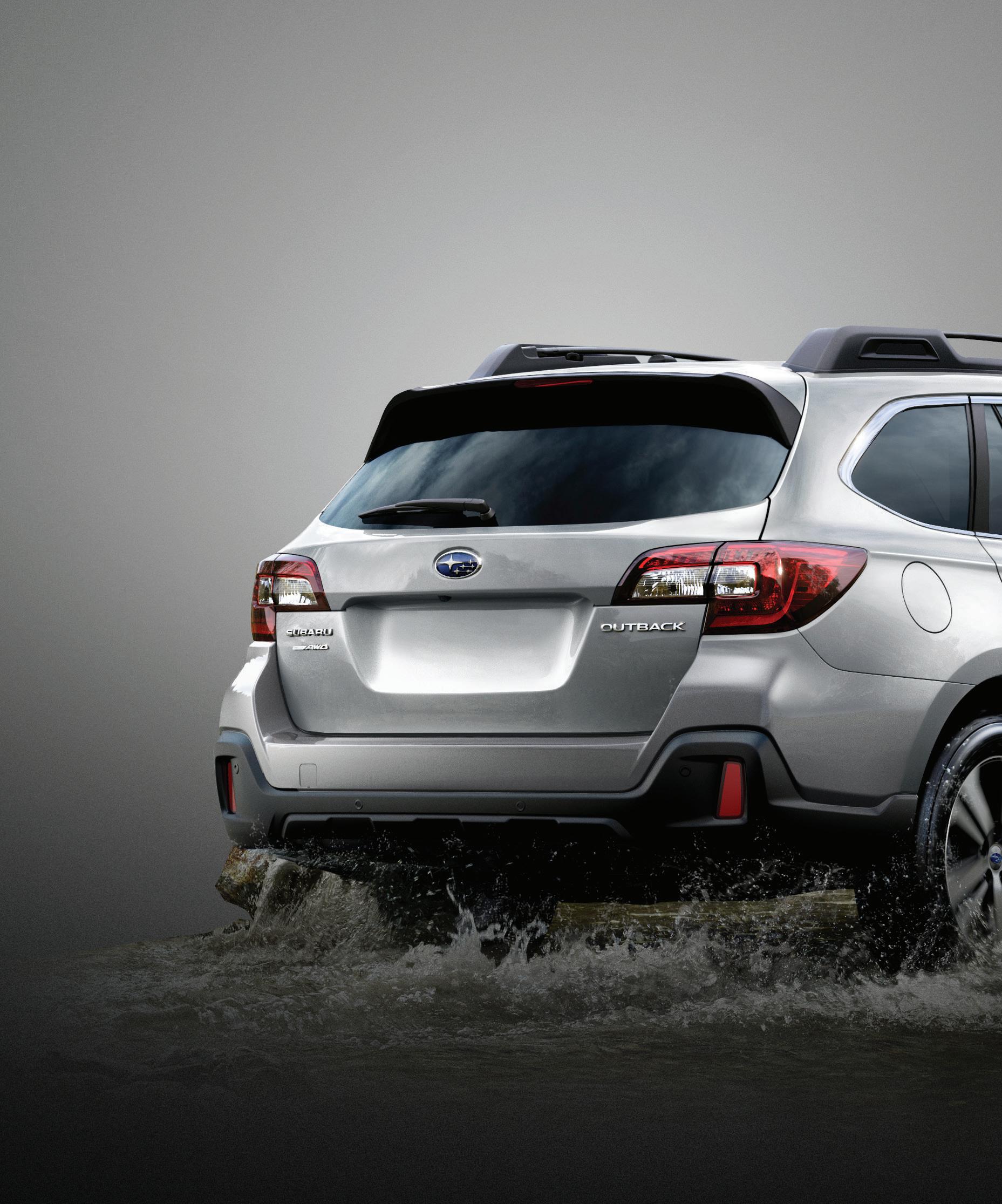

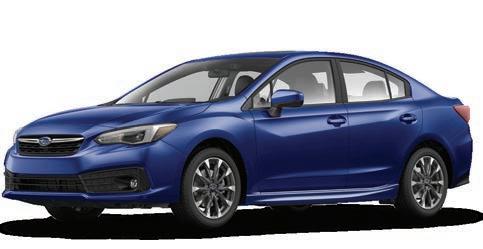

What we really do...What we really do... MANAGE STOREPROTECT What customers think we do... 1.800.668.5586 • www.johnstonequipment.com MOVE This is a unique mix of innovative products, best-in-class methodologies and software-based, data-powered solutions that work together to help you achieve your goals. Johnston Equipment Offers End-to-Endless Intralogistics Solutions. SOLUTIONS™COMPLETE


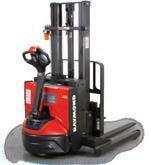
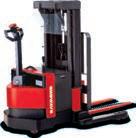


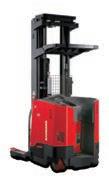
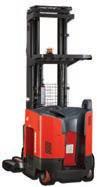
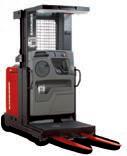
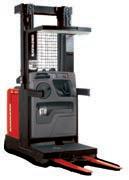
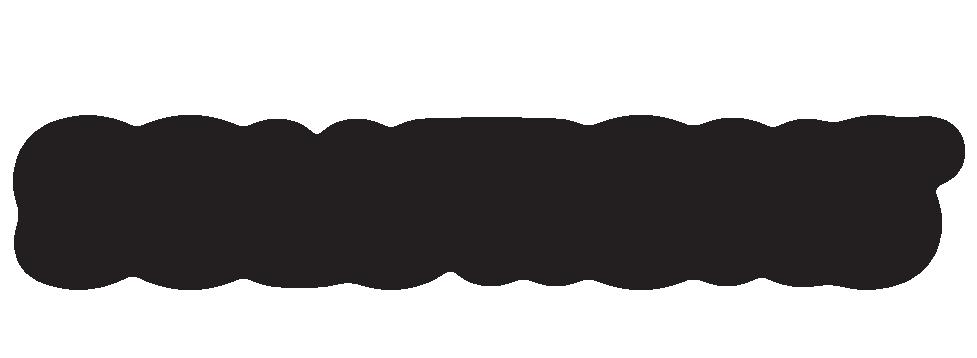
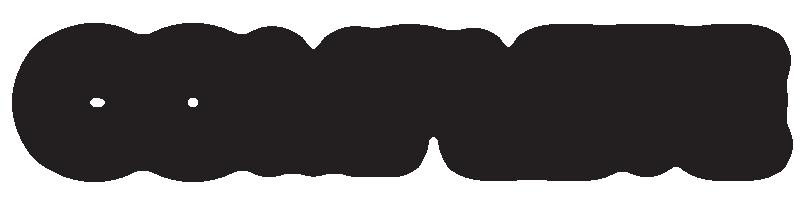