THE ETERNAL LEARNER
Jennifer Souch shares her passion for education and supply chain Spend management

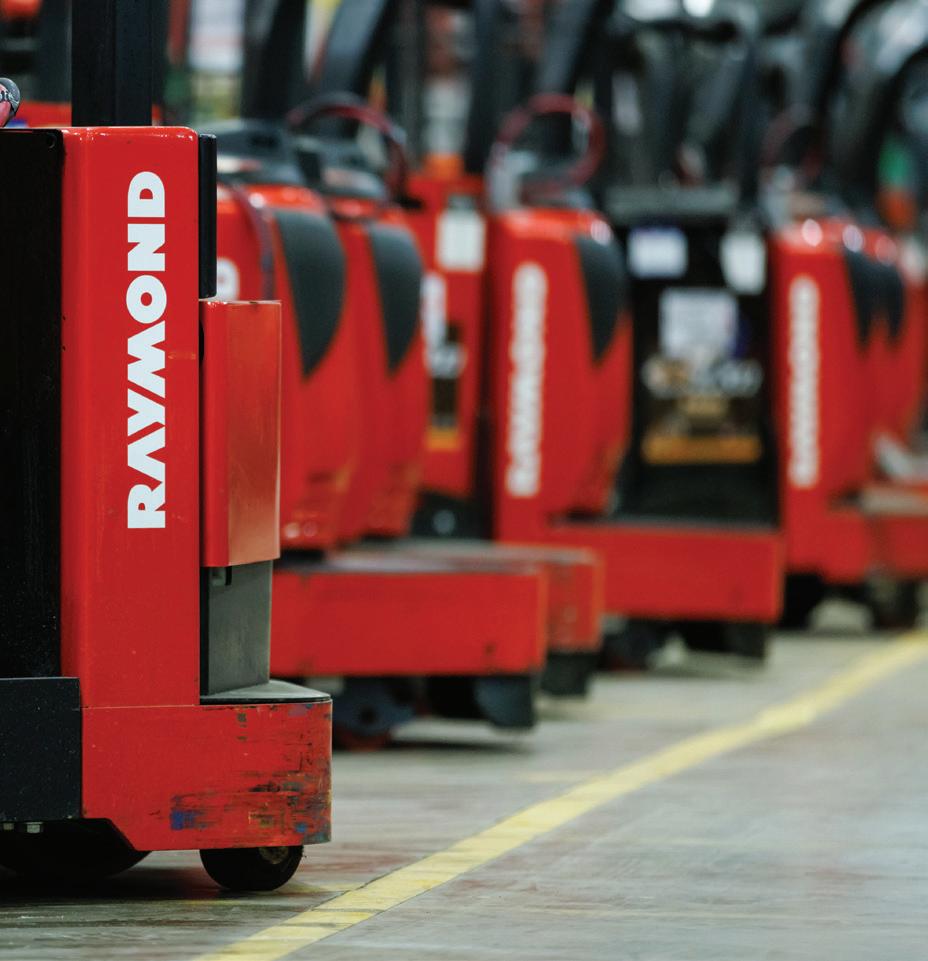
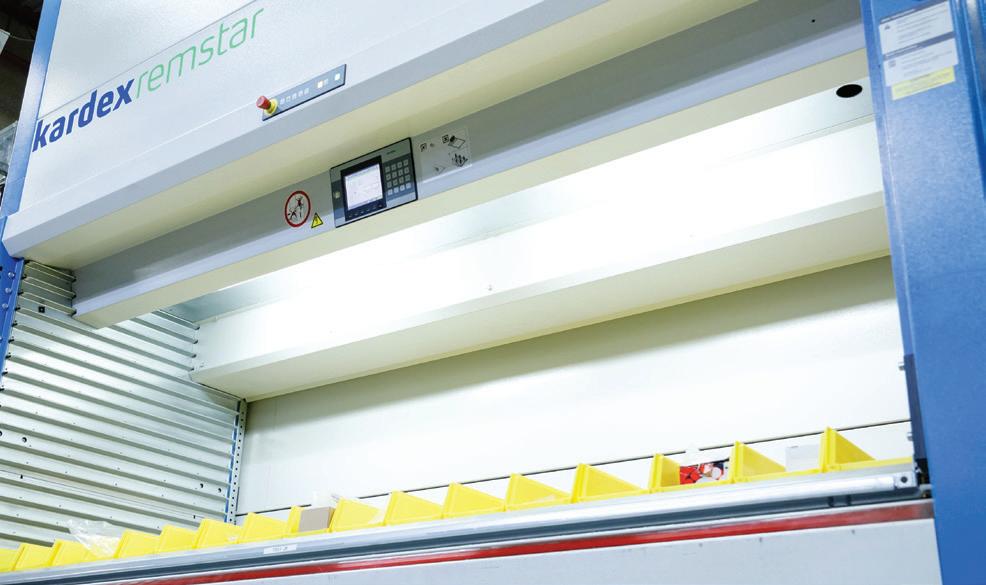
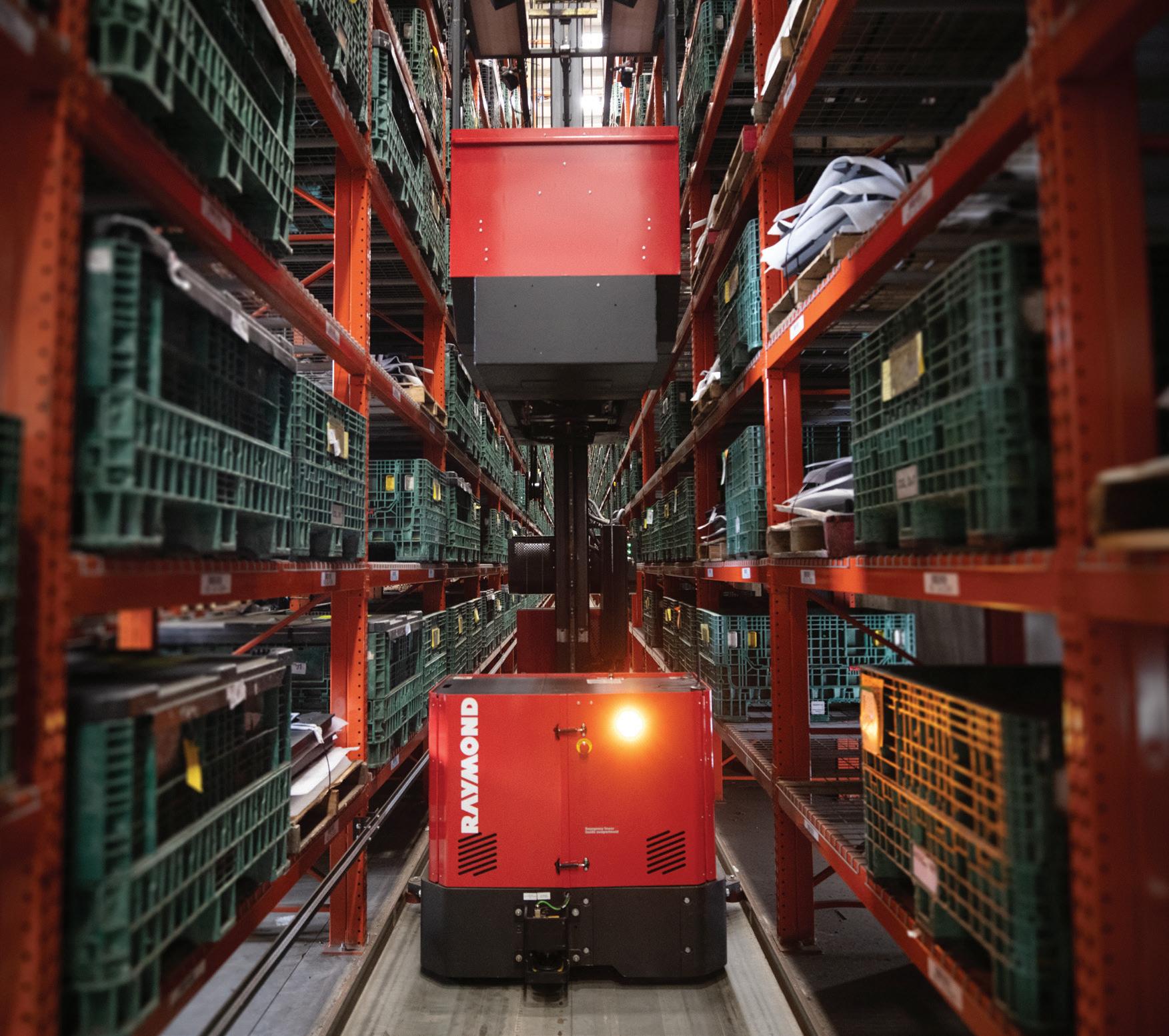


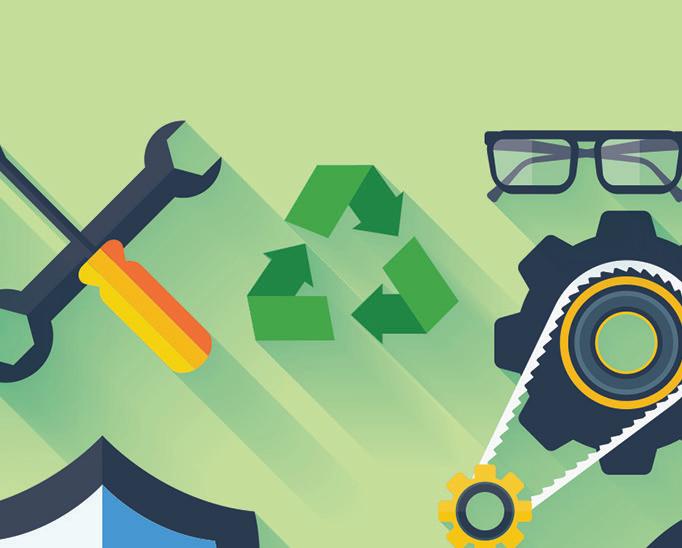
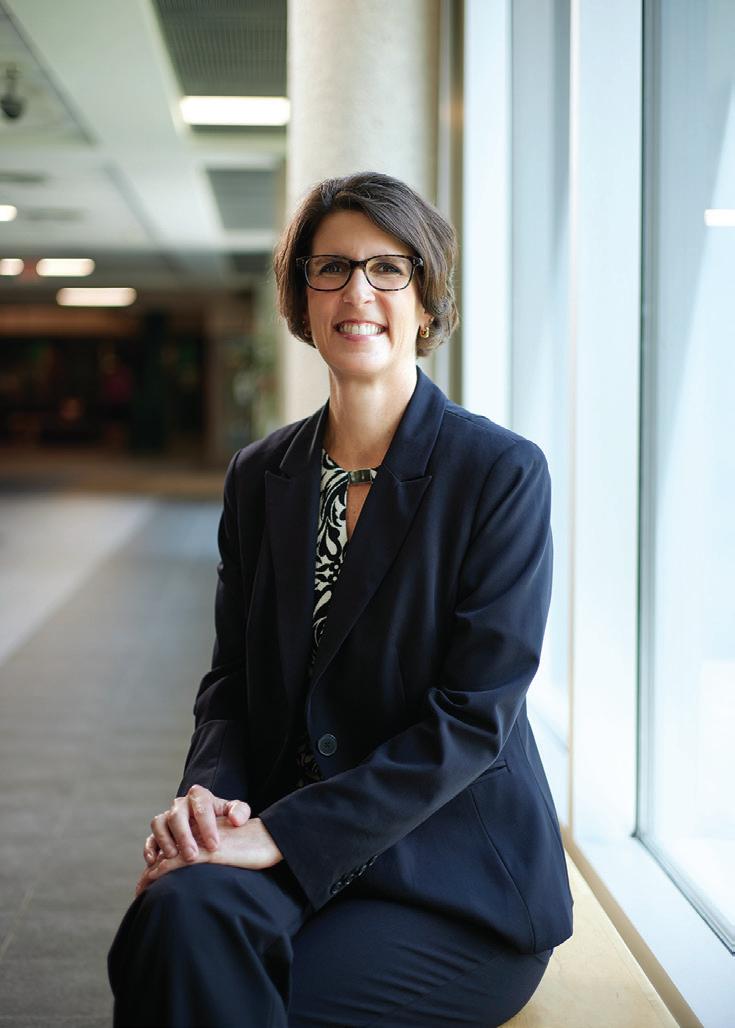
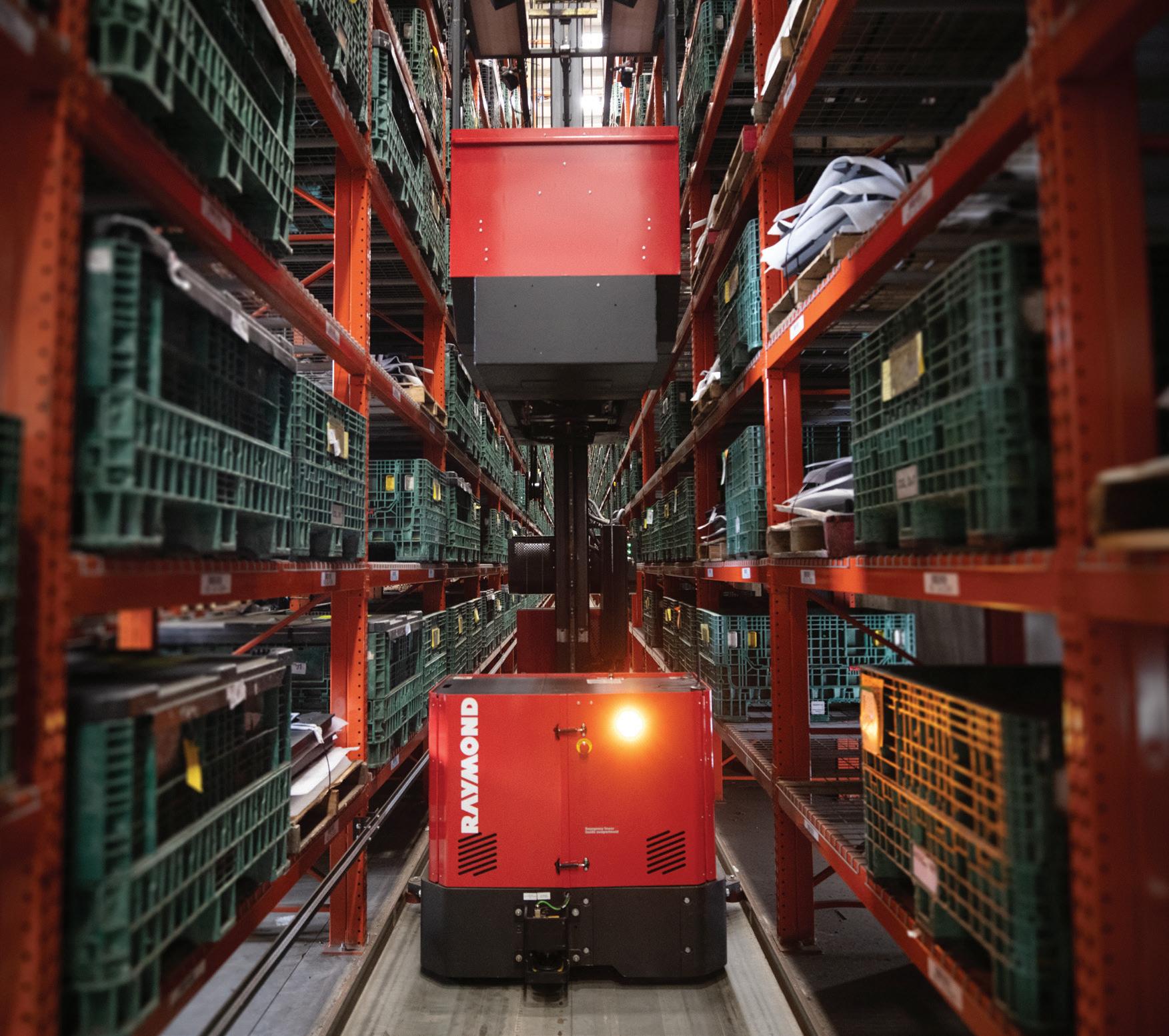
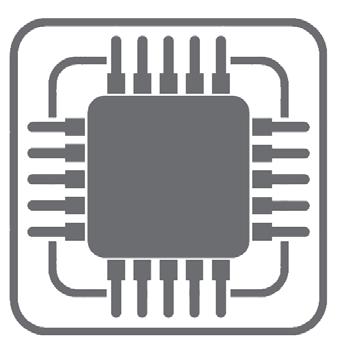
Jennifer Souch shares her passion for education and supply chain Spend management
By most accounts, Canada has a productivity problem. This is despite the fact that the country is growing in several ways. For example, our population recently hit the 40-million mark. In fact, Statistics Canada says that we saw the number of people grow by over one million in 2022. That’s the first time in our history we’ve seen such a jump.
As well, our economy has been more resilient this year than previously expected. According to RBC, both Canada and the US saw a growing GDP in Q1, bolstered by consumer spending, even in the face of higher interest rates and prices.
Yet, our productivity lags. We can define economic productivity as a measure of the rate at which the goods and services output are produced, per unit of output (like labour, capital, or raw materials). Among OECD nations, we rank 18th in terms of our productivity. That productivity also diminished nine per cent between 2000 and 2022, compared to our neighbours to the south. Which puts us at about 72 per cent of that of the US.
There are several reasons that get cited for this low productivity. Among them are a lack of business investment in buildings, machinery, and intellectual property, as well as a decline in research and development spending and the subsequent “innovation gap.” A lack of workforce upskilling is another factor.
It all sounds rather gloomy. There’s also no easy fix and whatever we do about it will take time to work. Yet supply chain can play a role in fostering an increase in productivity.
For example, many organizations are digitizing their supply chains, a critical step in upgrading and modernization. Supply chain professionals must look at what digital capabilities their organizations need in order to increase visibility, become more efficient, and otherwise foster higher productivity.
That means those organizations must also ensure their employees have the skills they need to thrive in a more digital environment. If companies are to update critical functions using technology, supply chain professionals must ensure they are improving their skills to keep pace.
There are several reasons for the skills gap facing supply chain. An aging and retiring workforce, for example, means younger workers must ramp up their abilities fast. It’s as important as ever to ensure your skills are up to date.
Another key is adopting a culture of productivity. Companies that focus on innovation, becoming more dynamic, and updating skills and infrastructure have an advantage towards success.
That’s especially important because supply chain is so embedded in organizations, rather than operating within a silo. Whatever challenges supply chains face reflect the trials of the companies they serve.
Yet, that means that any success supply chains experience can only help their organizations and, by extension, all of our success.
Supply chain leaders and their organizations must therefore work to tackle the productivity gap. Our future prosperity and quality of life depend on it.
EDITOR
MICHAEL POWER 416-441-2085 x7 michael@supplypro.ca
PUBLISHER
ALEX PAPANOU 416-441-2085 x1 alex@supplypro.ca
DESIGN
Art Direction ROY GAIOT
Design Consultation BLVD AGENCY
ASSOCIATE PUBLISHER
FARIA AHMED 416-919-8338 faria@supplypro.ca
EDITORIAL ADVISORY BOARD
LORI BENSON Procurement Compliance, L&D, Engagement and Knowledge Lead | Business Enablement, Ernst & Young LLP
THOMAS HUDEL Manager, Purchasing and AP, Esri Canada Ltd.
WAEL SAFWAT Procurement Director, Black & McDonald
SHERRY MARSHALL Senior Manager, Meetings, Travel & Card Service, PwC Management Services
KIRUBA SANKAR Director, Program Support, Purchasing and Materials Management— City of Toronto
JEFF RUSSELL Corporate Purchasing Manager & Inventory Manager, Miller Waste Systems Inc.
iQ BUSINESS MEDIA INC.
Vice President STEVE WILSON 416-441-2085 x3 swilson@iqbusinessmedia.com
President ALEX PAPANOU
PUBLICATION MAIL AGREEMENT NO. 43096012 ISSN 1497-1569 (print); 1929-6479 (digital)
CIRCULATION
Mail: 126 Old Sheppard Ave, Toronto ON M2J 3L9
SUBSCRIPTION RATES
Published six times per year
Canada: 1 Year $ 99.95 CDN
Outside Canada: 1 Year $ 172.95 USD
Opinions expressed in this magazine are not necessarily those of the editor or the publisher. No liability is assumed for errors or omissions. All advertising is subject to the publisher’s approval. Such approval does not imply any endorsement of the products or services advertised.
Publisher reserves the right to refuse advertising that does not meet the standards of the publication.
No part of the editorial content of this publication may be reprinted without the publisher’s written permission. © 2021 iQ Business Media Inc. All rights reserved. Printed in Canada.
I and my family just returned from vacationing in the US. We spent one week in Las Vegas, a city that has special meaning for me. It is where I and my wife got married. It’s a place that has captured the imagination of my seven-yearold son. He loves the place for a variety of reasons. We try to do it on the cheap and one of the ways we save money is by shopping at a Whole Foods just south of the strip (three kilometres south of Mandalay Bay) and dining at fast food restaurants.
This visit we discovered a Panda Express that was a 10-minute walk from our hotel room. There was a “Help Wanted” sign outside, advertising the need for line workers, assistant managers, and store managers, and the wages associated with each position.
I was flabbergasted. The starting pay for line workers is $17 per hour, for assistant mangers $23, and store managers start at $27 an hour. Why was I so taken aback? At $17 an hour, an individual would gross $680 a week, and it is possible to find reasonable, one-bedroom accommodation in Vegas for less than $1,000 a month.
There’s a simple reason why wages are so high. It’s called supply and demand. Over the past year, US unemployment has ranged from 3.4 to 3.7 per cent. What is so interesting to me is that this is with a Democratic President and a Congress that is also dominated by Dems. Let’s return to pre-COVID times. In the nine months leading up to the onset of the pandemic, when there was a Republican President and a Republican-dominated Congress, unemployment ranged from 3.5
to 3.7 per cent, then it ultimately spiked to hit 14.7 per cent in April 2020, before it steadily came down to current levels.
These are US numbers, but the story in Canada is similar. Our unemployment rate stands at 5.3 per cent while pre-COVID-19 it bottomed at 5.7 per cent. For someone like me, who received his formal training in economics in the late 1970s, this is borderline shocking. We were told that “full employment” in the US meant that there would always be four per cent of the workforce unemployed and it would be closer to six per cent in Canada.
This was considered full employment because some people would be leaving work voluntarily for various reasons, and the creative destruction of capitalism would mean that some folks would be thrown out of work against their will.
There are schools of economic thought that would not be surprised by unemployment being as low as it is. Classical economists like Adam Smith and John Stuart Mill believed in the “invisible hand” of the marketplace. Economies would adjust naturally to achieve full employment. Then John Maynard Keynes, writing during the Great Depression, argued that in the absence of government intervention the adjustment process would take an unconscionably long period of time, putting undue suffering on the most vulnerable among us. However, ultimately there is more agreement than disagreement between the Classicals and Keynesians. Humans are by nature an adaptive species.
What does this mean? We should not be afraid that there will be a dearth of employment opportunities in the foreseeable future. I have heard concerns that self-driving cars will devastate the trucking industry. I have heard concerns that artificial intelligence (AI) will eliminate a wide swath of occupations. Goldman Sachs direly predicted that AI would eventually affect 300 million people worldwide and displace 20 per cent of the workforce. And the World Economic Forum predicts that 25 per cent of jobs will be “negatively impacted” with clerical and administrative positions being hit most directly.
I’m not denying that there will be upheaval in labour markets. Yet at the same time that technology is the problem, it will simultaneously provide at least a partial solution. It is now possible to deliver training and education more quickly and cheaper than ever before. Technology, properly employed, can simplify tasks that were once very complex. It will be necessary more than ever for workers to be flexible and nimble. In the developed world, at least, something like a guaranteed minimum wage is the next development that will ensure both social cohesion and allow the risk-taking that is essential for economic growth.
I have previously noted that I have a seven-year-old son. I see a future for him that is full of opportunity. I truly hope that he will not waste his time, energy, and money with post-secondary education (and I teach both college and university) unless he’s attending
a program like engineering or computer science or he’s picking up a practical trade like plumbing. And look, worst comes to worst, he could start working at a Panda Express while he lives at home, saves his money, and by the time he’s 21, he could be debt-free and own his own condo … maybe just off the Las Vegas strip. SP
“The World Economic Forum predicts that 25 per cent of jobs will be “negatively impacted” with clerical and administrative positions being hit most directly.”
After more than four years of debate, Canada has passed its most significant supply chain law in a generation. Bill S-211, officially known as the “Fighting Against Forced Labour and Child Labour in Supply Chains Act,” addresses the scourge of human rights violations in global supply chains. Effective January 1, 2024, the law places the responsibility on brands, retailers, and importers to identify and prevent forced labour and child labour in their supplier networks.
After complaints that Canada had for too long turned a blind eye to forced labour in supply chains, Bill S-211 represents significant progress, aligning Canada with a growing global trend of legislation aimed at eradicating modern slavery and promoting social sustainability. By some measures, it may be the most sweeping supply chain due diligence law in North America, even moreso than the US’s Uyghur Forced Labor Prevention Act (UFLPA). Where the UFLPA targets goods made in China’s Xinjiang region, Bill S-211 focuses on due diligence obligations for businesses operating in Canada, irrespective of the goods’ origin.
The law applies to both domestic and international businesses that meet at least two of these three thresholds: CD$40 million in gross worldwide revenues; $20 million in assets; or an average of 250 employees or more. Regardless of their industry, companies that meet these criteria must produce annual reports outlining their due diligence measures to identify and mitigate the risk of modern slavery in their supply chains. These reports must include information about a compa-
ny’s policies, procedures, risk assessments, and remedial actions taken to address any identified issues. To ensure transparency, these reports must be published on a publicly accessible website.
The law’s first reporting deadline is May 31, 2024, a date that’s sure to receive attention in boardrooms because of the law’s unique enforcement structure. Businesses that don’t comply will be subject to fines of up to $250,000, and unlike other global supply chain due diligence laws, Bill S-211 holds business leaders personally liable for any company offenses they directed, authorized, or in any way participated in.
Complying with the law will pose considerable challenges, especially for brands and retailers that must navigate complex global supply chains of hundreds of suppliers. That requires coordination, accountability, and visibility. Thankfully, it’s made much more manageable by a multi-enterprise platform, sometimes also known as a multi-enterprise collaboration network. These cloud-based platforms support collaboration between businesses, their suppliers, and their third-party partners, introducing complete visibility into a company’s supplier base, from vendors to factories to raw material providers.
To comply with the law, supply chain managers will need to establish robust systems and processes to identify and address any instances of modern slavery or forced labour within their supply chains. This involves enhanced supplier vetting, auditing, and monitoring mechanisms to ensure compliance and
ethical practices – all of which can be simplified through the supplier relationship management (SRM) tools of a multi-enterprise platform.
These platforms create a window into an enterprise’s entire supplier base, enabling the traceability that Bill S-211 requires. Through supply chain mapping, businesses are granted a fuller understanding of their social and environmental footprint, including where their yarns and fabrics come from, how much carbon they’re emitting, and whether their downstream suppliers are vetted and accredited. An end-to-end platform like this allows businesses to document the chain of custody of every material they use in every product they make, so they can prove that no forced labour was involved.
Multi-enterprise platforms also foster collaboration with industry associations and non-governmental organizations (NGOs) that can also prove valuable in navigating the complexities of supply chain management in light of Bill S-211. TradeBeyond’s multi-enterprise platform can even integrate with sustainability databases from business associations and non-profits like amfori and Worldwide Responsible Accredited Production (WRAP), which monitor and certify the social sustainability of factories and suppliers.
By making critical certification details from these partners available in real time, these integrations eliminate the need for supply chain managers and compliance teams to log in to multiple systems. They create other efficiencies, like saving retailers and brands time through automating the onboarding of vendors and factories and ensuring
that all new suppliers have read and consented to the company’s terms. This way, from the earliest stages of working with a supplier, there’s transparency about your ESG standards and expectations.
This software enforces a company’s social and environmental standards by preventing merchandisers from booking orders with non-compliant suppliers and preventing shipping departments from booking shipments with them.
Bill S-211 will be a tough but necessary adjustment for many. By implementing responsible sourcing practices with a multi-enterprise platform, businesses can protect their reputation, strengthen consumer trust, and contribute to a sustainable global supply chain, while fostering the resilience needed to remain competitive. SP
“Bill S-211 focuses on supply chain due diligence obligations for businesses operating in Canada, irrespective of the origin of goods.”
Walmart Canada has opened its first high-tech fulfillment centre in Western Canada, in Rocky View County, Alberta. The fulfillment centre is a 430,000sqft facility serving as a delivery hub for Walmart’s Western Canada customers. The facility represents an over $100-million investment and will store thousands of items available on Walmart.ca. It’s capable of shipping 20 million items annually from the facility and can handle up to 500,000 unique items to fulfill direct to home and ship-to-store pickup orders.
“We’re on a transformational journey to modernize our supply chain and today’s grand opening marks a major milestone for Walmart Canada,” said Gonzalo Gebara, President and CEO, Walmart Canada. The space will fulfil orders for Walmart Fulfillment Services (WFS), a fulfillment service for third-party e-commerce sellers.
Supply chain software management provider Tecsys Inc. has a position as a challenger in the 2023 Gartner Magic Quadrant for Warehouse Management Systems (WMS).
This evaluation is the 12th time that Gartner has recognized Tecsys’ Elite WMS . Tecsys’ “Ability to Execute” and “Completeness of Vision” are the reasons why it was named a Challenger in the Gartner Magic Quadrant.
“WMS offerings continue to differ in areas such as usability, adaptability, decision support, scalability both up and down market, use of emerging technologies and lifecycle cost,” says the Gartner report. “Customers increasingly favour suites that can support end-to-end supply chain and logistics process orchestration.”
Elite WMS is part of Tecsys’ broader suite of solutions built on a digitally enabled, integrated platform designed to simplify complex supply chain operations.
Supply chain solutions provider DP World has appointed Douglas Smith as chief executive officer of its Canada operations. Smith will be responsible for leading the company’s portfolio of operations.
Smith replaces Maksim Mihic, who will assume a new role for DP World in Dubai, UAE.
“I am honoured to join the DP World’s talented team of professionals in Canada,” said Smith.
The federal government has announced nearly $94 million for a cargo development project at Toronto Pearson International Airport.
The investment comes from the National Trade Corridors Fund. The project is designed to improve cargo capacity by building two new facilities: the South Cargo Transfer Development Facility (YYZ South) and the North Cargo Apron Development (YYZ North).
“The substantial funding from National Trade Corridors Fund for our cargo development project
will enhance our position as a vital gateway for global and domestic cargo operators,” said Deborah Flint, president and CEO, Greater Toronto Airports Authority (GTAA).
“With improved capacity and infrastructure, we will facilitate faster and more efficient goods transfer, benefiting Canadian businesses and consumers.”
YYZ South will increase capacity for incoming cargo, while YYZ North will build more infrastructure for cargo aircraft parking spaces, which will also increase cargo capacity.
A new report reveals innovation in plastic technology has more than tripled since 2015, following legislative action and policy initiatives to tackle plastic waste.
According to the latest figures, plastic innovation has increased threefold in little over half a decade following international legislation such as the 2015 Paris agreement.
Asia is the world leader in plastic innovation, with China and Japan accounting for about half of all patent
applications in the past two decades. Europe is second, with Germany ranking in the top four for patent filings and the UK ranking seventh.
The report by UK Patent Box experts GovGrant analysed all global patent filings in the past two decades, highlighting the countries driving innovation.
Earlier this month, nation-state representatives took the first steps towards a legally binding treaty to regulate plastic globally.
“I look forward to leveraging my experience to further strengthen DP World’s position across the Canadian supply chain landscape and deliver exceptional value to our customers, partners, and stakeholders.”
Smith brings almost 30 years of industry expertise to the role. He began his career with Sealand Service, Inc. and has held key positions at Maersk, APM Terminals, and Global Ports Management. Most recently, he served as joint president and CEO of Mundra and Tuna Ports at Adani Ports and Special Economic Zone in Mundra, India.
Smith holds an MBA in Global Management from the University of Phoenix and a Bachelor of Science in Marine Transportation from the United States Merchant Marine Academy.
ties, we’ve been pushing that into e-procurement tools, and it just continues to get better.”
Adopting the right technology is critical to optimizing an organization’s spend management, says Maria Greaves-Cacevski, senior category sourcing lead at Chemtrade Logistics. That technology is important not only to doing business now, but to predicting trends and market variability going forward, she notes.
“We need to be able to see what we did historically, and we also need to try and see where the variance is leading to in the future,” Greaves-Cacevski says.
Given today’s abundance of technology, finding the right fit is more important than ever. Regarding a spend management strategy, supply chain professionals must choose technology to deal with those fluctuations – automation means less risk of something getting lost in the process.
“Automating the process also helps for you to streamline so that your workers are working more efficiently,” she says. “They know exactly what tasks they’re going to be working on, how many head count or how many inventories they need, what’s the time to fulfill, and then what’s the expected output from that.”
A challenge that Greaves-Cacevski sees in managing spend involves forecasting. Quality issues and incorrect inventory can arise if you’re demand is not accurate or you’re not selling to the market. Increased costs from carrying inventory that doesn’t move can lead to waste and writing off.
The resiliency of Canada’s supply chains has been tested in recent years by everything from the COVID -19 pandemic to the Ukraine war, to the ensuing economic uncertainty of these events. Due to these and other factors, it’s more important than ever to ensure that your organization manages its spend as effectively as possible. Spend management involves governing and continually improving an organization’s spending.
Technology is playing a critical role in that process.
Regarding technology, the last few decades have seen organizations focus mostly on process improvement, says Chris Sawchuk, principal and global advisory practice leaders at The Hackett Group. Tech has been replacing human labour for some time and, for example, 20 years ago human labour was by-and-large responsible for spend analysis. Today, auto-
mated tools are taking over certain tasks. These tools allow organizations to increase visibility into spend behaviour, with continual improvement.
“Technology has been having an impact on what I would call process-oriented type of work,” says Sawchuk. “Activities like transactions, there’s a lot of ways that technology has been taking on that work. If we look at the direct-to-pay process, that transactional set of activi-
The right technology gives organizations flexibility to react to unprecedented or unplanned changes. A lack of visibility means an organization can’t react quickly or change direction when needed.
Yet it’s important to ensure that whatever technologies an organization uses are able to connect with one another, Greaves-Cacevski notes. Having different technologies for different functions can result in an organization becoming inflexible or immobile, since systems aren’t reading each other. Having systems that can talk to one another helps both
boost visibility and remove silos within an organization. As well, unifying processes under one management tool can reduce the risk of human error.
“It’s critical that when you’re looking at a technology solution for your spend management, you start with what your goal is from that software, and how many of your stakeholders are involved in that process and making sure you have understanding and alignment between each of those cross-functional teams,” she says. “That spend management touches all of their teams, and it rolls that information into one centralized unit.”
A best-in-class spend management system will incorporate finance, HR, sales, procurement, and other departments into a centralized system, Greaves-Cacevski notes.
expectations, its KPIs, and so on. Post-pandemic, many organizations are looking to reduce the number of suppliers they use while focusing on partnership agreements.
“If they know that there’s going to be price increases coming down the pipeline and you’re a partner, they will forewarn you of that and then advise you whether to pre-buy or preload at a certain price point to offset how much cost it is,” she says.
A well-functioning supplier relationship management process can also help organizations to manage their spend, she says. There needs to be agreement between suppliers and an organization’s service-level 23_004907_Supply_Professional_AUG_CN
Another spend management tactic is to ensure that employees are prop-
erly trained to negotiate price with suppliers, she says. When suppliers say they’re increasing prices, it’s tough to say “no” outright – especially when you need their product. Ensuring that input from an company’s operational-tactical level filters up to the strategic level can help, as the operational team is often closer to what’s happening on the ground.
“A lot of organizations are changing some processes internally to give that voice of the employee more of an emphasis than before,” GreavesCacevski says. “Removing those levels of bureaucracy allows us to get a better price faster, because you’re empowering your team at the ground level to negotiate and execute some of those deals firsthand.”
Technology is encroaching even into strategic processes like negotiations, notes Sawchuk, of The Hackett Group. Tools exist that allow for autonomous negotiations, for example. Organizations develop rules for a bot to negotiate with the
supplier on that organization’s behalf, he says. Supply chains must get comfortable with concepts like bot-to-bot negotiations.
As cutting-edge technologies like artificial intelligence are used more widely, certain tasks or types of work may be eliminated, says Sawchuk. Yet that process will lead to accelerating what people are capable of – a process of augmenting human capabilities, at least initially.
Sawchuk likens the process to the Marvel comic film Iron Man, in which a high-tech suit gives the main character, Tony Stark, super-human powers such as incredible strength and the ability to fly, among others.
“He was super smart, but when he put on that Iron Man suit, it allowed him to be smarter,” Sawchuk says. “It was like having a supercomputer with him. In many ways it augmented his human capabilities. I think this augmentation of human capabilities with artificial intelligence is really where we’re headed.” SP
“It’s critical that when you’re looking at a technology solution for your spend management, you start with what your goal is from that software.”BY MICHAEL POWER
When it comes to supply chain, Jennifer Souch’s experience has been unique: it’s not everyone who gets to take a wealth of industry expertise and pass it along to those just starting their careers.
Souch spent years working in the field – honing her skills and knowledge at the General Motors’ Canadian manufacturing plant in Oshawa, Ontario. But she has since entered a second phase of her career, teaching students as professor and program coordinator in the faculty of business at Durham College, also in Oshawa.
The opportunity to pass along that knowledge is a large part of what gives meaning to her role, she says.
“Even as a practitioner, you don’t finish learning,” she says. “As I transitioned my career, education played a big part in my ability to move and, I think, even as a supply chain professional, in my continued development. I’m a lifelong learner. And that’s an important aspect of any supply chain career, whether it’s on the academic
side or in the field. So that’s what I continue to do. And as technology evolves, it’s important to be in front of, or at least on path with, some of those advancements.”
Like many in the profession, Souch ventured into supply chain management almost by accident. She earned a Bachelor of Science degree from the University of Toronto but realized near the end of the program that although she had specialized in biology and chemistry, a career in that field wasn’t for her.
Instead, she began a position at General Motors, which represented her first exposure to supply chain, or what the company called operations management. She expected to work in the company’s paint facility because it seemed to align the most with her science background. But she ended up in the chassis facility, in the manufacturing area.
The automotive industry came with a steep learning curve, Souch says. Yet, she enjoyed the challenges that General Motors offered in her
early days with the company. At the time, the Oshawa facility represented the highest-quality plant within the corporation, she notes.
“I had a really good experience working for General Motors,” she says. “I started there as a frontline manager and progressed through different areas of the company. I was involved in a new manufacturing facility, setting up some of our offline facilities. I was involved in new vehicle development and watching products within our manufacturing facility. Later in my career there, I was involved with the implementation of the global manufacturing system, which is, I’ll say, General Motors’ version of Toyota Production System, and implementing that across our Oshawa sight was some of the most rewarding work that I did early in my career.”
Souch ventured into academics when she took a teaching position at Durham College in 2010. During her time there, General Motors had shifted from traditional automotive manufacturing to a more lean, flexible operation. As a result, Souch was able to do a lot of corporate training on lean initiatives. That gave her the experience she needed to teach courses at General Motors on lean operations and global manufacturing, from the perspective of corporate leaders all the way to frontline staff.
“That was where I dipped my toe in the water before I ventured over to the world of academia,” she says of teaching at the company. “My thought at that time was, ‘if I can teach here, I think I can teach anywhere,’ because there were some tough teaching days, especially in a blue-collar, unionized environment that was very male dominated at that time.”
Souch considers herself fortunate that, while employed at General Motors, the company had a program that allowed her to complete additional education. She therefore earned a Master of Science degree from Kettering University, a small, Michigan-based institution, as well as a Master of Business Administration from Indiana University, Kelley School of Business.
The combination of that education and her experience at General Motors helped her forge a path in teaching when she left the company, she says. She now considers it a “leap of faith” to go from a stable, well-paying job into academia. But her passion for learning propelled her, along with the belief that education can change people’s lives.
“I had a lot of faith that, because of my education and experience, I would land somewhere after parting ways with General Motors,” she says.
Souch is also a designation holder (CPIM)
from the Association of Supply Chain Management (ASCM), and has the PMP designation from the Project Management Institute (PMI).
During a semester, Souch teaches between four and five academic courses across different programming. The clusters of programs that she has under her purview include diploma, advanced diploma, and the recently launched graduate certificate program.
Students enroll either directly from high school or else have another degree or work experience before admission. Students may be young and new to the field, or they may be more seasoned professionals.
And just as in supply chain, no two days in academia are the same.
“It’s a lot of coaching and mentoring, so I feel that I have experience and education to share,” she says. “It’s helping students understand how that curriculum applies in
a real-world setting. I think having the education and the experience in the field helps students. It’s storytelling, and it’s using a lot of my own experience from what I saw as well as tapping into employers.”
To help students on their journey, Souch works to build relationships with those employers. That can include bringing in company representatives for recruitment events, hosting alumni for guest-speaker engagements, along with other strategies to build bridges between students and the supply chain world. Part of the purpose, she says, involves helping students to understand the diversity of the supply chain management field.
“When I look at my day-to-day, it’s about helping students understand the wide span and career pathways in supply chain,” she says. “It’s a challenge, but rewarding, because sometimes students come into a program, and they don’t have a good sense of the broadness or the vastness of career opportunities. So, on a day-to-
day basis I would say, it’s definitely teaching, but coaching and mentoring are really at the heart of everything that we’re doing in the supply chain programs at Durham College.”
Souch’s twin careers in the field and in academia have produced some highlights. At General Motors, the process of launching the Camaro from a concept to the manufacturing stage, to having a sellable vehicle was, for her, a particularly exciting project to be involved with, she says.
At Durham College, launching the global supply chain management graduate certificate program also proved exciting and rewarding, she says. That program emerged during the COVID-19 pandemic, as the public realized
the important contribution that supply chain professionals made in keeping the world running. At the time, Souch was hearing employers’ concerns about the skills and knowledge gap among job candidates. Durham College first offered the program in fall of 2022 and the first class graduated recently.
During her career Souch, along with the teams she’s worked with, has received various awards and accolades. She got the Chairman’s Honors Award at General Motors, and her team at Durham College has been recognized often for their work. That team was, for example, responsible for being one of the first to pilot and launch a formal co-op internship program.
The team hasn’t received any formal award for the program. But Souch stresses that kind of recognition isn’t particularly important to her sense of career accomplishment.
“I would say that our graduates speak for our success,” she says. “We’re there to help develop emerging professionals. And the success of our graduates in the field speaks to that. When you hear from alumni that you taught 13-plus years ago and they say ‘here’s my career path,’ and ‘here’s where I’ve gone,’ that’s the rewarding part – certainly for me and I would say across my faculty team, in terms of why we do what we do in a day.”
Like any field, those graduates face challenges once they enter the workforce. One such demand Souch sees is how dynamic the sector has become. While it has never been static, supply chain is now even more complex than in the past, she says. That’s especially true in the post-pandemic world, where challenges related to how goods are moved, as well as the timeframe, have grown rapidly.
The increased importance of sustainability and the need for more ethical supply chains presents yet another challenge, Souch says. Navigating these issues is important to graduates, who must be prepared to tackle them. That requires an innovative, out-of-the-box vision of the field.
Graduates must understand the implications of their decisions, not only for the business but for the planet as well, Souch stresses. The professional toolkit they need for this has changed over the years, and those entering the field must realize that.
“We’re very fortunate to have employers that provide direct feedback on trends in the field, and can say ‘here’s the gap of skills and knowledge that we’re seeing that we need closed,’” she says. “Data-driven decisions are critical, so in the last five years (we’ve seen) the emergence of business analytics as it relates to all aspects of supply chain. Making
sure from the academic side that our graduates have the skills and knowledge that they need to be effective supply chain practitioners is important.”
With supply chain such a dynamic field, there’s always a need to learn something new, even in academia, Souch says. Those who teach must ensure they stay in front of professional trends. That way, they can prepare graduates for their future careers.
For her own professional development, Souch works to increase her skills and knowledge of the field to support her students. For example, she completed a business analytics certificate through Cornell University just before the beginning of the pandemic. Developing her own knowledge shows her students that, even as a supply chain practitioner, you never finish learning, she says.
Souch lives with her family on a rural property in Durham Region, east of Toronto. She describes her home as “its own little sanctuary,” where she can relax. The family enjoys a lot of time on the property – they take walks on the trails in the winter, go skating on a pond, and otherwise are able to get away from the hustle and bustle of daily life.
“We were fortunate during COVID because we had this property, and I think that my kids never really felt the impact of being confined to indoor space,” she says. “That’s always been an important part of my personal life, just enjoying time with friends and family in our rural setting.”
Souch and her husband have two teenaged children. Her son is just finishing high school, while her daughter has now completed her first year of high school. “My son is planning on going into an apprenticeship in the fall, and that will be following more in my husband’s pathway,” she says.
Part of a teacher’s role is providing guidance to his or her students. Advice that Souch offers her pupils is that there is a place in supply chain for everyone. There is an enormous breadth of career opportunities, and she encourages her students to find an industry and niche they
think they’ll enjoy, and to just go try it. That provides the experience students need to move into other areas of supply chain if they wish.
Supply chain also offers nearly unlimited chances to move across industries, Souch says, as well as opportunities for promotion within organizations. The need for people with supply chain skills is growing, and while in the past many have stumbled into the field accidently, more and more practitioners are making informed decisions to go into supply chain.
“It’s really about understanding the career pathways, and that’s a challenging conversation for incoming students to understand the scope of what they could potentially do,” Souch says. “Whether you’re a new graduate or somebody that’s more seasoned in the field, you have the skills that you need to be successful. If there’s that career move, I would encourage people to take advantage of that and leverage all their previous education and experience.”
Souch encourages supply chain professionals to look to the future while keeping in mind the recognition that the field has received recently. Since the COVID-19 pandemic, the public now understands the importance of supply chain, as well as the impact the sector has not only on business, but also on the planet.
“The future lies with supply chain professionals and they’re really driving a lot of those business decisions and impact on people, planet, and profit – that’s going to be an important part that new and existing professionals have to contend with.” SP
“As technology evolves, it’s important to be in front of, or at least on path with, some of those advancements.”
Would you or your company spend five per cent or more of your salary on upskilling? If so, how would you spend it? Would you research and do a gap analysis first? Looking back on returning to work after 12 years, I researched skills needed to rejoin the workforce. I combined that with a personal gap analysis. I spent $1,600, which I thought was a lot. But it worked out to 4.25 per cent of the annual salary that I earned when I started working.
I looked at the top-three jobs that I was applying to and the top-three skills common from each. I ranked them in order of importance along with the cost and a timeline to get me to my desired state. The question I asked myself once working again was, ‘what can I do to ensure they can’t say no when I transition to my next position?’
Organizations want to attract and retain talent and supply chain professionals must ensure they have the skills and ability to match what organizations want. If you’re unconvinced, here is a stat from The World Economic Forum: for workers planning to stay in their roles, the share of core skills that will change in the next five years is 40 per cent, and 50 per cent of all employees will need reskilling. The top skills employers see rising by 2025 include critical thinking; analysis; problem solving, active learning, and flexibility. This article addresses the following issues: Why must supply chain professionals upgrade their skills?
Why is it important now?
What are the dangers of not getting those skills?
What skills should one acquire or develop? What soft skills are needed and why? What technology should you familiarize yourself with and why?
Where can you get help with skills development?
How can you use technology to gain those skills?
As supply chain professionals, we want to stay competitive, contribute to our organizations and to overall business success. There are several reasons why it is important for us to upgrade our skills:
Evolving industry – the need to stay updated with the latest tools, strategies, and practices.
Globalization – the need to be knowledgeable in international trade regulations, logistics strategies and cultural differences.
Cost optimization – the ability to identify cost-savings opportunities, implement lean practices, optimize inventory levels, and negotiate favourable contracts.
Risk management – managing challenges and protecting against disruptions.
Collaboration/communication –communication with cross-functional teams while ensuring coordination across the supply chain.
Sustainability and ethical practices – how to implement strategies related to them.
Enhanced efficiency and productivity – knowledge in data analytics, lean management and automation to optimize supply chains for productivity and cost reduction.
Growth – personal and professional knowledge, deeper and new industry perspectives.
Multiple factors in the job market make it especially important to invest in upskilling. These include rapid technological advances, increasing complexity and globalization, as well as supply chain disruptions. As well, data-driven decision making, sustainability and ethical practices, and evolving customer experiences, increase the importance of gaining new skills or updating existing ones.
The dangers of not getting these skills are many. There’s the risk of becoming obsolete and losing ground to technological advancements. Skill requirements change, and there is increased competition and less job security. Many organizations promote a culture of lifelong learning, require remote work and digital skills, while the requirements of specific industries can change.
Here is a list of skills to work on that can help you become invaluable in becoming more efficient, competitive and successful:
Data analysis
Supply chain planning and optimization
Supplier management and negotiation
Logistics and transportation management
Risk management and resilience
Communication and collaboration
Technology and digitization
Continuous improvement, leadership, and management
Sustainable and Ethical practices
Some people undervalue soft skills, as they are more difficult to measure and often thought of as common sense. Yet they are necessary, and you can develop and refine
them. Soft skills to develop include communication; collaboration/relationship building; adaptability and flexibility, among others.
Navigating these skills can help us position ourselves for success while ensuring we unlock opportunities and achieve personal fulfillment. As well, help in developing our skills is not far away. It does not have to cost a lot or take much time to realize. One could break their upskilling plan into short- and long-term timeframes to deal with the time and cost involved. Resources include professional associations or organizations, online learning platforms, university programs and certifications, industry conferences/events, publications, internal training and development, and networking.
There is a wealth of knowledge among experts that we can reach out to for help with developing our skills. They include mentors, managers, colleagues and peers, subject matter experts, professional networks, external training providers, and online communities. Technology can also help.
To reap upskilling benefits, invest in personal growth, embrace professional development, enhance your knowledge, acquire new tools and strategies and adapt to emerging industry practices with an upskilling plan in 2023 and beyond. SP
JOYS OF UPSKILLING IT’S MORE IMPORTANT THAN EVER TO DEVELOP YOU SUPPLY CHAIN SKILLSLisa Fenton is supply chain and inventory manager, Custom Plastics International Limited. BY CHRISTIAN SIVIÈRE
Canadian supply chain professionals will have a new challenge next year: compliance with forced labour laws. Following the US lead, with its Uyghur Forced Labor Prevention Act (UFLPA) in effect since July 2022, Canada has passed its own legislation in May this year and enacted the Fighting Against Forced Labour and Child Labour in Supply Chains Act, also known as bill S-211.
The Act will come into effect on January 1, 2024. The objective is more supply chain transparency and to this end, Canadian companies will have new reporting obligations starting next year. These will apply to Canadian entities who meet two of the following conditions: at least $20 million in assets, at least $40 million in revenue and/or having an average of at least 250 employees, during at least one of its most recent financial years. Canadian entities are defined as those producing, selling, or distributing goods in Canada or elsewhere, importing goods in Canada or controlling an entity engaged in these activities. The same obligations will apply to government institutions engaged in these activities.
The reporting entities yearly report will need to identify any risks of modern slavery within their supply chains and the steps they have taken to mitigate them. Companies will have to provide
information on their business structure, their due diligence policies and processes, training provided to key employees in this respect, steps taken to address any potential use of forced or child labour anywhere in their supply chain, as well as describe how they assess the effectiveness of their efforts. Non-compliance penalties can go as high as $250,000 per violation and as is often the case with these sorts of issues, the reputational risk is way higher.
It is useful to know the definitions of “forced labour” and “child labour” contained in the act.
“Forced labour” is defined as labour or service provided by a person under circumstances that could reasonably be expected to cause the person to believe their safety would be threatened if they failed to provide the labour or service, or constitute forced labour as defined in article 2 of the Forced Labour Convention, Geneva, 28 June 1930.
“Child labour” is defined as labour or services provided by persons under the age of 18 that are provided in Canada under circumstances that are against Canadian law, or under circumstances that are mentally, physically, socially or morally dangerous to them, interfere with their schooling by depriving them
of the opportunity to attend school, obliging them to leave school prematurely or requiring them to combine school attendance with excessively long and heavy work, or constitutes child labour as defined in article 3 of the Worst Forms of Child Labour Convention, Geneva, 17 June 1999.
With the first report due by May 31, 2024, Canadian companies will have to conduct due diligence within their organization and with upstream suppliers, to assess and prevent any risk of forced labour and/or child labour used within their supply chains. This continuous, increased supply chain oversight will need to be incorporated in and consolidated with the growing requirements found in other jurisdictions, particularly in the US, but also Mexico and the European Union, who all have new legislation addressing human rights risks.
The US has taken a different approach with its UFLPA, as it specifically targets China. Under that Act, US Customs and Border Protection (CBP) can detain or seize any goods made, in whole or in part, with inputs from China’s Xinjiang Uyghur region, thereby presuming that such goods were made using forced labour.
Importers have 30 days to demonstrate that the goods were either not made using forced labour, or that they do not include any inputs
from the Xinjiang region. Since the prohibition applies to goods made in whole, or in part, and applies to companies that may or may not be located in the Xinjiang province, US importers of products from anywhere in the world are at risk, as inputs from Xinjiang can be used to manufacture goods outside China as well.
Importers must therefore demonstrate due diligence with their suppliers and be in a position to prove the absence of forced labour components in their imports. Of course, this also applies to non-resident-importers, for example, to Canadian exporters selling in the US using the DDP Incoterm (or the UCC term FOB Destination). CBP publish on their website a list of Chinese entities targeted under the UFLPA regulations, as well as a dashboard with the relevant shipment statistics. To date, out of 4,651 shipments held, 872 were denied entry, 1,849 were released and 1,942 were still pending. The shipments count by industry was as follows: electronics 2,156; apparel, footwear and textiles 812; industrial materials 756; agriculture and prepared products 283; consumer products 272; pharmaceuticals and chemicals 212; machinery 156; base metal 149; and automotive and aerospace 31.
Our other North American partner, Mexico, has banned the importation of goods made with forced labour with regulations in force on May 18, 2023. Targeted goods are either designated by Mexico’s Ministry of Labour and Social Welfare (Secretaria del Trabajo y Previsión Social/ STPS) or pursuant to a request made by a Mexican citizen or legal entity, which would trigger an STPS investigation. Mexican importers have 20 working days to respond and the STPS 180 working days to issue a final resolution.
Across the Atlantic, the European Union launched a public consultation earlier this year
on their proposed regulation that would prohibit making available on the EU market any products made, extracted, or harvested with forced labour, whether they are made in the EU, or elsewhere.
Their approach is different due to legal differences between individual EU countries. The EU is not directly targeting the entry of such products in their Customs Union, but instead will ban the placing of such products for sale on the EU market. Discussions are ongoing at the European Parliament and the Council of the European Union for entry into force of these regulations by the end of 2023 or early 2024. SP
“The objective is more supply chain transparency and Canadian companies will have new reporting obligations starting next year.”
Christian Sivière is president at Solimpex.BY NOELLE STAPINSKY
Among the issues the pandemic highlighted, the consumer demand it caused has strained supply chain capacity at all points. Those effects linger today. Major bottlenecks started with the supply of componentry, and of all the recent shortages, semiconductors, or chips, has been the most severe. The surge in demand for consumer electronics during lockdowns prompted big electronic companies to snap up chips. Meanwhile, automakers cut production thinking once demand rebounded, the semiconductor supply would remain. And just like that, consumers shifted spending to experiences rather than goods.
“We can’t be too myopic in our views of demand and supply because that’s what caught the automotive industry by surprise. Just as rapidly as their demand went down, it went back up again,” says Douglas Kent, EVP corporate and strategic alliances at the Association for Supply Chain Management (ASCM).
“This falls on the supply chain as well. Suppliers didn’t warn the automotive industry that there would be consequences because they may not be consuming those supplies, but others are, and auto -
makers should have been aware of that.”
Such fluctuation and lack of supply caused the semiconductor industry to recognize that those requiring them for manufacturing and those using the products realized it’s a shared technology across many different industry sectors. The global nature of semiconductors makes it vulnerable to disruption through dependency on other countries.
“We have a dependency on other countries, particularly Taiwan for the initial fabrication, but also the componentry and packaging which is done throughout Asia. These macro factors are important ones and are leading government response and other efforts to try to de-risk the dependency on foreign nations given the factors, not the least of which are geopolitical,” says Kent.
“The dependency on the Taiwan Semiconductor Manufacturing Company (TSMC) is newsworthy particularly because there is concern about China’s long-term motivations relative to Taiwan. And since that particular entity is a Taiwanese-based company there is certainly concern, especially since a high amount of componentry
is used in defense equipment and by the government.”
Pandemic-era bottlenecks and border restrictions caused a shift from ‘justin-time’ to ‘just-in-case’ strategies to maintain inventory levels. Everyone started looking at reshoring production or gaining access to regionalized suppliers.
“The geo-economic fragmentation is a big story,” says Alan Arcand, chief economist for Canadian Manufacturers and Exporters (CME). “There’s an attempt to not necessarily decouple from China, but de-risk our relationship. Also, due to the disruptions during the pandemic there’s a desire to regionalize and create redundancies and resiliency in the supply chain, so that’s going to drive more semiconductor activity in North America.”
Arcand isn’t the only one who sees the trend.
“We’ve seen a lot of our customers exiting China, but not fully because that’s difficult to do,” says Josh Pucci, senior vice-president of sales for Sourceability, a global distributor of electronic components. “But they are looking to add
additional manufacturing in Vietnam, India, Malaysia, and Mexico. There is some [manufacturing] in the US, but they’re still looking for a low-cost solution. The trade wars with China and Taiwan are always at the forefront of everyone’s thoughts. Nothing has happened yet, but it does have an impact because every time there’s a retaliatory from either side—China and the US—they’re restricting more supply to the market, which causes some quick demand when people try to get those products before the restrictions take place.”
Arcand notes that when US President Joe Biden visited Canada last year to announce the CHIPS and Science Act it prompted investment in the semiconductor industry. During that visit, IBM announced it would expand domestic research and development of its advanced packaging of semiconductors in Canada. In a release, IBM said the collaboration with the Canadian government will help bolster the US’s and Canada’s chip design and manufacturing capabilities, as well as global supply.
A recent ASCM report revealed that the border volume shipments coming from Mexico were higher
than port volumes coming through Los Angeles and Long Beach.
“That’s the first time in 20 years that has happened,” says Kent. “Twenty years ago was when we decided offshoring was a great option and chasing low labour prices was the way to go. We really built up and elevated China as the manufacturing epicenter of the world. Now we’re seeing evidence that its returning and we can see that by the volumes. That’s interesting in and of itself, but at the same time we’re seeing legislation with the CHIPS Act to de-risk dependency, but make no mistake, that is not a quick fix.”
While there are complex obstacles to navigate, manufacturers can protect themselves from fluctuating market conditions by diversifying their supplier pool – many already did during the pandemic.
“We talked about reshoring and moving your supply closer, but there are other options out there,” says Pucci. “For key inputs, having more than one supplier is important. Another option is technology and investing in certain supply chain software that will give you a better handle on it and more advanced warning of troubles ahead. And I think a lot of companies are talking or opening up a line of communication with their suppliers more frequently.”
Pucci suggests adding as many approved product numbers as possible to the bill of materials to build a product so that you’re not stuck with one.
“That was a big problem pre-pandemic,” he says. “If that one part has any issues, which could be caused by an earthquake or geopolitical issues or COVID, you only have one part. Diversify as much as you can, which is really the key to avoiding this happening again. If you look at the cost of sitting on product for three to six months, that’s significantly less than having to pay massive increases in shortage costs or not even being able to produce the product.
Sourceability offers a number of programs that are customised to its customers’ needs.
“They are generally centered around a vendor management inventory program. We’ll work on buying the large quantities up front and supplying the smaller piece demands as they come up,” says Pucci. “We also have access inventory, so if a customer has too much product, we have programs that alleviate that and find customers that do have demand. Sourcengine allows customers to send their lists in to get an estimate for the value of the excess based on what we see in the market. We post that availability so that other customers that have demand can see it.”
Kent agrees: “Reducing dependency on a singular supplier is a smart thing to do. We have to have a broader view of purchase potential by broadening the market. Who are potential suppliers? Where are they? What does their pricing look like? We also need to use analytical tools to strengthen our strategy and inventory modeling. Lastly, we need to construct different options from a supply chain network design standpoint. I’m optimistic about companies that have the recognition that these are investments they need to make and that these are critical capabilities they need to have inside their organization.”
In Canada, high interest rates are slowing the economy down, impacting the demand for electronics and other manufactured products. According to Arcand, these high interest rates will constrain consumer spending for some time and won’t likely return to what they were. Assuming the economy keeps slowing, the Bank of Canada will start cutting interest rates in 2024.
The global nature of semiconductors as a shared technology among many industries, and the aggressive move towards electric vehicles, means the industry will remain vulnerable to potential disruptions. To navigate the macro and micro factors affecting semiconductor supply chains, companies must embrace analytical and forecasting technology, diversify their supplier pool and, of course, increase their relationships and communications with suppliers. SP
“The global nature of semiconductors makes it vulnerable to disruption through dependency on other countries.”BY JON HANSEN
Right off the top of your head, why is data important? Like answering the question ‘why is there air?’, answering the above probably took you less than a second to come up with at least one, if not many, answers.
So, here is a tougher question. Why is extracting data and turning it into actionable knowledge challenging? And why are we consistently finding ourselves in a reactive (or descriptive) state, playing catchup rather than being proactively prescriptive?
In a recent article for a German publication, I wrote the following: “Descriptive analytics tell you what happened or is happening, while prescriptive analytics take risk management intelligence to the next level by telling you how to address a problem. It is an evolution of intelligence gathering, analysis, and optimized responses.”
The above is more than wordplay or semantics. However, it is easy to use the words ‘descriptive’ and ‘prescriptive’ interchangeably.
For example, when it comes to responding to volatility in the supply chain, one reader observed: “I am not sure what is talked about in the blog post are prescriptive analytics. Prescriptive analytics tell you what to do and are essentially automating response with a human validation. The blog post, as far as I can see, is talking about enriching real-time data with more insights to make a better call, the industry standard since a couple of years.”
Given our traditional view of business intelligence and digital transformation, it was a reasonable point to raise. In other words, automation – particularly artificial intelligence (AI) – should be about enhancing decision-making and not simply providing data faster.
A top 3PL executive, Shira Yoskovitch, expressed a similar view when I talked to her about what happened with Peloton during the height of the pandemic. When the issue regarding the timely availability of data came up, she said that the problem wasn’t because they didn’t have the information to see what was coming. The problem is they didn’t know how to read it.
Once again, access to timely data, which was a very real problem in the past, is no longer an issue with today’s advanced, digital, AI technologies.
In short, we now have the data. In some cases, we have an overabundance of data. We need the ability to sift through the information beyond knowing what is happening and what we can do about it.
In my response to the reader, I assured them that I believe we are saying the same thing regarding automating response with human validation. For example, how descriptive analytics tell you what happened or is happening, while prescriptive analytics take risk management intelligence to the next level by telling you how to address a problem.
I provided the following case study to demonstrate the evolution of descriptive data capture and availability to prescriptive intelligence gathering, analysis, and optimized responses beyond a conceptual understanding.
When I developed one of the industry’s first algorithm-driven web-based procurement systems for the Department of National Defence in the late 1990s and early 2000s, the buyer entered the weighted parameters for a specific purchase based on policies and priorities.
These weighted parameters could be changed to reflect an immediate change in the situation. At that point, the algorithms would instantly “recalculate” a different solution or answer to address the new scenario. No matter how advanced AI becomes, you still need effective intelligence gathering – including accurate data and human analysis to assess the program’s output to achieve optimized outcomes.
In this context, I likened it to the chess interplay between chess grandmaster Garry Kasparov and IBM’s Deep Blue “technology.”
The first time Kasparov played Deep Blue was in a six-game match in 1996. Kasparov beat the computer four games to two.
For the next match in 1997, IBM upgraded Deep Blue. The result was that the machine defeated the man, winning two games and drawing three.
In recounting his experience, Kasparov wrote, “While writing the book, I did a lot of research –analyzing the games with modern computers, also soul-searching –and I changed my conclusions. I am not writing love letters to IBM, but my respect for the Deep Blue team went up, and my opinion of my own play, and Deep Blue’s play, went down.”
As you read the above quote from Kasparov’s book, what stood out the most? It was his revelation that neither the Big Blue AI technology nor his own chess IQ was a match for the IBM Deep Blue team.
When it comes to AI and data analytics, it is not a machineversus-human or human-versus-machine scenario. It is a collaborative approach to intelligence gathering and analysis to enable organizations to identify and implement optimized responses. This ability is at the heart of
a prescriptive analytics approach to supply chain volatility.
The main takeaway from this article is that data analytics and procurement spend are not static information to enable you to buy better. It is not about contract compliance or budgeting. Data analytics and procurement spend are not really about money at all. OK, maybe they are a little bit.
But it is really about what you achieve or accomplish with the dollars you spend in peaceful times, along with times of great volatility and uncertainty.
To put it another way, what good is a consolidated view of your spend alone if the goods or services you procure are not being delivered because of a disruption? Think of the example of Peloton.
When you think of data analytics, AI and consolidated spend, you must always have the end game or result in mind; otherwise, what is the point? SP
“Prescriptive analytics take risk management intelligence to the next level by telling you how to address a problem. It is an evolution of intelligence gathering, analysis, and optimized responses.”BY AMANDA CHOUINARD
With numerous risks and opportunities woven into our supply chains, procurement is well positioned to be an engine for achieving sustainability outcomes. Sustainable procurement should therefore not be overlooked as a crucial element of a broader corporate sustainability program.
Members of the Canadian Collaboration for Sustainable Procurement (CCSP) are doing just that – over 46 municipalities, crown corporations, and post-secondary institutions across Canada are repurposing used products, contracting with Indigenous businesses, building net-zero facilities and more. The CCSP’s 13th Annual Report on the State of Sustainable Public Procurement in Canada highlights trends, best practices, and case studies from this network.
Drawing from highlights in the CCSP 2022 Annual Report, here are five sustainable procurement trends public sector organizations should leverage to make a positive impact:
1. Leverage reuse to advance circularity and save money
Circularity is about more than just limiting landfill waste. It helps reduce overall consumption, resulting in decreased resource extraction, habitat destruction, GHG emissions and even spending money. “Reuse” is not a new concept. However, this year we saw many Canadian public sector institutions using meaningful initiatives to enable reuse on an ongoing basis, to support their circular economy agendas.
Thompson Rivers University (TRU) first established its TRU RE-USE platform to reallocate surplus products within the university in 2018. In 2022, they surpassed half-a-million dollars in cost savings. Simon Fraser University (SFU) unveiled the development of two new software platforms: SFU Marketplace and Rencyclopedia. SFU Marketplace will help facilitate the reuse of assets so university staff can avoid purchasing new items, while Rencyclopedia is a public directory
to help the broader community dispose of, or repair, their products responsibly. The City of Ottawa also embraced circularity and reuse this year by contracting a local social enterprise to purchase its second-life IT hardware and redistribute it to community members in need.
In Canada, the public sector is responsible for releasing eight million tonnes of GHG emissions annually associated with construction materials, according to one Clean Energy Canada Report. The public sector is making moves to address this area of high impact. The federal government released a new Standard on Embodied Carbon in Construction, which sets minimum requirements for the procurement of design and construction services to disclose and reduce the embodied carbon footprint of major construction projects. The District of Saanich is
designing a new firehall to be made of wood (a naturally lower-carbon material) and meeting the LEED Platinum standard with a net zero construction target. The City of Brampton completed a procurement to retrofit a major recreation centre to become the City’s first zero-carbon facility. The City of Charlottetown also has a city works building under construction that has been specified to meet net zero targets.
In the last few years, social priorities within procurement have been rising to level with the longer standing focus on environmental considerations. This year, many procurement practitioners built on their commitments to social procurement by implementing tools to connect directly with social value suppliers.
Introducing: the supplier portal. Several organizations have begun using third-party supplier directo-
ries, or building their own, to facilitate quick access to a list of social value suppliers. For example, York University has set up a publicly facing directory of local social value vendors. The University of Toronto has also implemented a diverse supplier portal as part of its efforts to support diversity in its supply chain. Notable third-party software’s offering directory services include Tealbook, Supplier.io, and B2Gnow in addition to Canada’s various diverse supplier councils such as: CAMSC, CCAB, CGLCC, and WBE.
4. Commit to increased spending with indigenous businesses Public organizations are increasingly implementing Indigenous procurement activities to advance reconciliation with, and actively support the economic vibrancy of, Indigenous peoples. A significant milestone was the Federal government’s 2021 Procurement Strategy for Indigenous Business (PSIB), which sets a mandatory target that at least five per cent of federal spend go toward Indigenous business. However, other levels of government are also taking action.
City of Saskatoon also increased its Indigenous spend target to five per cent (approximately $17 million in Indigenous spend annually) and embraced Indigenous art and culture through the procurement of bus shelters and bike racks that incorporated art pieces from local Indigenous artists displaying meaningful symbols and stories from Indigenous culture and history.
The cities of Edmonton and Regina both invested time in engaging with Indigenous stakeholders to inform the development of their Indigenous procurement policies. The Province of Yukon applied a bid value reduction mechanism, which increases the competitiveness of bids from Yukon First Nation (YFN) businesses. As a result, a YFN business was the successful proponent for a demolition contract in 2022, providing employment in the local community.
5. Formalize sustainable procurement through a strategy and action plan
A strategy and action plan is an important element of a sustainable procurement program. It outlines
the long-term vision for an organization’s program and provides a clear course of action for implementing and managing it. In 2022, there was a surge of effort put towards developing and approving strategies, frameworks, and action plans for sustainable procurement.
The City of Winnipeg announced its three-year Sustainable Procurement Action Plan, outlining key activities across environmental, ethical, social, and Indigenous pillars. The City of Brampton passed a Sustainable Procurement
Strategy that commits to three key principles and recommended policies to develop. The City of Charlottetown and Town of Stratford received funding from the Canadian Federation of Municipalities to work together on their Sustainable Procurement Strategy and Action Plan. This is a clear indication that the public sector is formalizing sustainable procurement activities and moving away from the decentralized ad hoc approach.
The Canadian Collaboration for Sustainable Procurement (CCSP) is a member-based network of Canadian public-sector institutions working to align their spending with their values and commitments on sustainability. Members meet virtually to network, share information, and co-create tools to address environmental, social, Indigenous, and ethical opportunities and risks in their supply chains. Reeve Consulting is the secretariat to CCSP and supports program management. SP
“Several organizations have begun using third-party supplier directories, or building their own, to facilitate quick access to a list of social value suppliers.”
This isn’t your parents’ supply chain. Technology continues to reshape the logistics and supply chain landscape significantly, driven largely by digitization.
One specific driver of warehouse digitization has been digital warehouse mapping technology. Warehouse mapping has become an integral way for warehouse managers to optimize their operations effectively, streamline their daily processes, and reduce operational costs.
But there’s a difference between having technology and using it effectively. Many warehouse managers don’t know how to make effective use of the digital warehouse mapping tools available to them. One way to make a
significant improvement in the use of warehouse tech is to partner with an extended WMS provider.
Digital warehouse mapping uses multiple other technologies such as radio frequency identification (RFID), GPS, and barcode scanners, all to provide real-time data on inventory, shipments, and the overall warehouse operations to warehouse managers as well as the business’s executive team.
This technology gives warehouse managers the ability to track the location and movement of inventory within the warehouse. That helps them optimize the layout and improve inventory management. By having a detailed understanding of inventory levels and locations, warehouse managers can allocate resources more efficiently and reduce the time and effort required for picking, packing, and shipping.
Beyond inventory management, a major advantage of working with an extended warehouse management systems (WMS) provider’s warehouse mapping technology is the ability to gain real-time insights into the key performance indicators of efficient warehouse operations.
Real-time insights allow warehouse managers to identify bottlenecks, inefficiencies, and areas for improvement. For example, if a particular area of the warehouse is regularly causing delays or slowing down operations, warehouse managers can use this information to optimize the layout or reorganize the workflow to eliminate the bottleneck.
By constantly monitoring and analyzing the data from warehouse mapping technology, warehouse
managers can make informed decisions to improve efficiency and reduce costs.
As advanced as technology has gotten, human labor is still the backbone of the supply chain. But digital warehouse mapping technology can help streamline daily operational processes through enhanced communication and collaboration within the warehouse.
In addition to helping them make informed decisions, the real-time data provided by an extended WMS provider also allows warehouse managers to share any operational issues with their suppliers, customers, and other stakeholders. This transparency in daily processes can help to build trust and strengthen relationships with partners across the supply chain.
Although digital warehouse mapping offers numerous benefits, it can require specialized skills and resources to implement and maintain, which is why small to medium-sized businesses may find it challenging to justify the investment required to acquire and implement these tools. But that doesn’t mean it’s out of their reach.
This is where extended WMS providers come into play. They can oversee the implementation of warehouse mapping technology and make sure warehouse managers know how to use it to its highest potential. These providers have the expertise, resources, and technology required to implement digital warehouse mapping tools effectively.
Partnering with an extended WMS provider that offers digital warehouse mapping technology can help businesses reduce costs while improving overall supply chain operations, whether it’s inventory management, space utilization, process improvement, asset tracking, or even safety and compliance.
Extended WMS providers have the expertise, resources, and technology to implement digital warehouse mapping tools effectively, freeing you to focus on your core competencies.
Partnering with an extended WMS provider can help your business stay competitive in the rapidly evolving logistics and supply chain landscape, all without incurring significant costs or resources. SP
“Digital warehouse mapping technology can help streamline daily operational processes through enhanced communication and collaboration within the warehouse.”
For 2023, electric vans are no longer a future proposition. This market is being fast populated by models that appeal to business.
According to the World Economic Forum, demand for urban lastmile delivery is expected to grow by 78 per cent by 2030, leading to a 36 per cent increase in electric delivery vehicles in the world’s top 100 cities.
From a service vehicle standpoint, electric vans run all day and charge all night. The electricity cost per kilometre versus gasoline is a fraction of your current fuel expense. Overall maintenance costs are lower (no oil changes, no transmission, no exhaust system, et cetera) and with batteries
improving all the time – a longer service lifecycle is certainly possible.
Ford says the E-Transit is the only all-electric cargo van available in eight different configurations, including three roof heights and three body lengths, plus cutaway and chassis cab versions. The E-Transit can be further customized with the addition of vocational bodies (on chassis cab and cutaway) and equipment like ladder racks and interior bulkhead and storage solutions.
Other built-for-business features on E-Transit include optional Pro Power Onboard, which provides up to 2.4Kw of power for customers to transform the vehicle
into a mobile generator. The maximum payload is 3,880lbs (4,428lbs on the cutaway version). The van interior is 487.3 cubic feet (maximum) and the cargo space dimensions are 81.5-inch (max) height, 69.8-inch width, and 171.5-inch length.
On the heals of the Ford Transit we have the other big van player, with Mercedes launching its own electric van. The all-new 2024 eSprinter will arrive in Canada in the second half of 2023. It is equipped with the largest battery available, which has a usable capacity of 113Kwh. The load capacity is 495 cubic feet, while the GVWR is 9,500lbs. The electric range, according to Mercedes testing, will
be up to 400km (248 miles). The simulated range based on a city cycle will be up to 500km (311 miles).
A home-grown Canadian success story is taking place in Ingersoll, Ontario. The CAMI auto plant, a facility that has produced a variety of GM vehicles over the past 40 years, has been re-tooled and relaunched as the home factory of BrightDrop. Producing the EV600 – an electric light commercial vehicle purpose-built for the delivery of goods and services.
Powered by the Ultium battery system the EV600 has an estimated range of up to 402km (250 miles) on a full charge. The body
of the EV600 is purposely square to offer a usable 600 cubic feet of cargo area. Front sliding pocket doors, wide cabin walkways and a large auto-open cargo bulkhead door all contribute to optimize driver efficiency. It is rated at a GVWR of less than 10,000lbs.
On the heels of the EV600 (which has already been sold to companies like DHL and FedEx) comes a smaller version, the EV410. The EV410 has more than 400 cubic feet of cargo area and a shorter wheelbase. In fact, the EV410 will fit in a standard parking space.
Meanwhile, the all-new Ram ProMaster EV will be introduced later this year. It will be the first fully electric van offered in North
America from Stellantis and the Ram brand. Unfortunately, no other information is available yet.
Once again, for GM, the van business remains steady and unchanged. The maximum payload for the Chevy Express 2500 and 3500 remains 4,503lbs and the towing capacity is 10,000lbs. The van’s interior is 284.4 cubic feet, while the dimensions are 53.4 height, 52.7 width, and 155 length. The 2023 Chevy Express Cut-away 3500-4500 carries over this year, with a max payload of 9,147lbs.
For 2023, the ProMaster is a carry over. However, the 2023 model has
already been shown and is expected late this year. It will carry a host of updates and upgrades. ProMaster is available as a cargo van, window van, chassis cab and cutaway model. It is a front-wheel-drive platform with a max payload of 4,680lbs and towing capacity of 6,800lbs. The interior is 530 cubic feet (max) with a cargo space height of 51 inches.
For 2023 the E-series is the same. It is only available as a cutaway or stripped chassis. Single and dual-rear wheel chassis have GCWRs ranging from 13,000lbs to 22,000lbs. This year is a carry-over year for Transit Connect. It continues to be offered as cargo or passenger equipped wagon.
The maximum payload is 1,610lbs and towing capacity is 2,000lbs. The van’s interior is 145 cubic feet, while the cargo space dimensions are 59.1 inches height, 48.1 inches width, and 72.6 inches length.
Meanwhile, the 2023 Ram ProMaster 1500 to 3500 carries a host of updates and upgrades. ProMaster is available as a cargo van, window van, chassis cab and cutaway model. It is a frontwheel-drive platform. Its maximum payload is 4,680lbs and towing capacity is 6,800lbs. The van’s interior is 530 cubic feet (max) and the cargo space height is 51 inches. FM/SP
According to the World Economic Forum, demand for urban lastmile delivery is expected to grow by 78 per cent by 2030.Ram 3500 ProMaster
Fleet often acts as an invisible, or perhaps a camouflaged, tool for driving business needs—one, which by design is never the primary representation of an organization but can be seen as a sunk cost in support of an organization’s objectives.
From the first purchase of a vehicle or equipment, a fleet’s supposed worth is usually tied directly to its cost, and its importance is hidden behind profit and client satisfaction. And while for many fleets, its definition could be relegated to only that – a necessary cost, fleet has the potential to be so much more. Fleet can and should be considered a strategic asset in action, working not just to support a need but generating a return for the organization it supports.
Here are five considerations to make the case for your fleet as a strategic asset:
Making fleets strategic requires a break with traditional thinking. As trends in fleet shift to match changing needs and demands of
vehicles, drivers, economies, organizations, and technologies, so to must the mindset of the fleet manager. They need to be both agile in response to short-term changes, and forward-thinking, making their role increasingly complex. To manage a strategic fleet, fleet managers must be informed, metrics driven, and inclusive.
Informed – this involves keeping a pulse on global factors; geopolitical conflicts, supply chain disruptions, inflation, talent shortages, increased competition, tightening of legislation, and environmental shifts, not to mention the lingering impacts of the COVID19 pandemic. No region is untouched by these factors, and in turn, no fleet is left unaffected. We can expect to see continued volatility. For these reasons, an informed fleet manager can be more strategic and work to mitigate potential risks surrounding the longevity, compliancy, cost, sustainability, and return on investment of a fleet.
Metrics driven – Constructive fleets are managed by those who can clearly identify and prioritize metrics aligned to business objectives and are ready to implement countermeasures when trends are moving in the wrong direction. These fleet managers also employ a focused strategy when prioritizing metrics. This includes recognizing that not all measures are equal, and that metrics should evolve in line with changes in vehicle utilization, technologies, configurations, and fleet definitions. Inclusive – Progressive fleet managers seek involvement from critical stakeholders when making decisions. Recognizing that no decision is superficial, fleet managers should create a communication and feedback loop with internal and external stakeholders to enhance driver and client satisfaction and in turn growth. Networking with industry peers and benchmarking are also important to gauge feedback.
When considering the relevance of a fleet program and policies, it makes sense to consider the impact on risk, compliance, and productivity as they align with organizational objectives. At minimum, a fleet needs programs focused on safety and compliance, funding, fuelling, maintenance, and remarketing. Fleets should also consider programs focused on drivers and clients. To be fully strategic however, fleets need to select and enroll in these programs, using data and metrics to design the right policies to meet organizational needs. Policies should be inclusive of key elements such as the vehicle, driver, partners, and current and future environment.
A company’s mission, vision, clients, employees, reputation, and operations should be reflected in its vehicle selection. While that may appear to be a huge ask, a fleet cannot be strategic without considering these factors. Vehicle selection, including upfitting and equipment, should never be a one-size-fits-all solution,
and should not be a carbon copy of any other fleet. To ensure that a fleet is customized to an organization’s needs, fleet leaders should aim to:
Evaluate the asset needs of every job function regardless of the mode of mobility
Advance the organization’s overall productivity
Answer to vehicle, driver, and organizational risk objectives and thresholds
Comply with regulatory demands
Uphold the company’s reputation
Acknowledge budgetary constraints
Align to market and technology trends
Total cost of operations (TCO) is an inclusive measure of the efficiency of a fleet. It should reflect the usage
of vehicles, driver behaviors, program subscriptions, and compliance with policy. Fleet managers should look at TCO as an important holistic measurement. It should be:
Complete: TCO should include all cost categories, whether
direct or indirect to the physical asset or driver. Strategic fleets also consider opportunity costs, related to actions taken and not taken.
Time-Sensitive: Time can redefine the effectiveness of a fleet, even when costs appear nominally unchanged. Macroeconomic factors such as inflation can have significant impacts, and strategic fleet managers consider cost in the context of time. A thorough evaluation involves an in-depth, retroactive view of both cost categories and drivers to forecast accurately.
Normalized: In addition to time (cost per month/year/lifecycle), TCO should be standardized to compare vehicle, driver, and fleet effectiveness directly. This requires establishing key performance indicators that point to cost or benefit of every cent that gets spent on fleet.
Using a data-driven fleet management approach is essential. That’s especially true with so many options for collecting and transforming data into actionable recommendations. A data-driven fleet is one that delivers reliable and real-time information, enabling informed decisions and strategies. The easiest and most basic path is to subscribe to telematics – with a guaranteed return of visibility and information. Yet, a truly data-driven fleet goes beyond vehicle utilization, performance and driver behavior. It also:
Collects and connects data from sources and systems (internal and external to the organization) that allow for informed and integrated decisions based on comprehensive data and in-depth measures. Endeavors to be prescriptive and predictive in its use of data, both shaping and foretelling trends.
Builds a nexus of technologies, systems, personnel, and policies. These lead to measures that systematically give visibility to the benefit to the business of every mile/hour driven and where impact of decisions on vehicles, drivers, and programs can be measured unambiguously.
Ensuring fleet is valued as a strategic asset for an organization should be a never-ending objective. It’s also a necessary one to reach a fleet’s full potential. A strategic perspective to fleet management requires forward-thinking, and programs, policies, and practices that enable the long-term profitability and viability of the organization it supports. FM/S
When considering the relevance of a fleet program and policies, it makes sense to consider the impact on risk, compliance, and productivity.By Stephanie Wallcraft
When electric vehicles entered the scene more than a decade ago, Nissan was at the forefront. The Leaf was the first EV in mass production, and its early adopters happily took on the growing pains of a budding and promising technology.
Today, EVs are on the verge of mainstream, if they’re not there already. And suddenly, Nissan finds itself behind the eight ball. The consumers considering EVs today expect more practical and family-friendly options with plenty of driving range. And the industry has delivered options. Several other automakers have brought larger SUV-like EVs to market, and most have a two-year head start.
Meanwhile, here we are taking our first look at the long-awaited 2023 Nissan Ariya. The tables, it seems, have turned.
The Ariya lands in Canada with six different trims available, from the Engage front-wheel drive (FWD) priced at $55,843 (all prices include destination and fees) to the Premiere e-4ORCE – that’s Nissan’s term here for all-wheel drive (AWD) – priced at $72,843. There are two different battery sizes available, and here’s where it starts getting confusing: the Engage and the $63,443 Evolve e-4ORCE come with the smaller 63kWh battery, while higher trims such as the Evolve+ FWD we’re testing here ($67,843) come with the larger 87kWh battery.
With all the variations available, power figures and range estimates are all over the map. The lowest-powered model is the Engage FWD at 214 horsepower and 221lbs-ft of torque; our Evolve+ tester has the same torque figure but 238hp, which is plenty for everyday driving. The top two e-4ORCEequipped trims have two motors and the highest power figures of 389hp and 442lbs-ft. On the range side, the lowest figure is on the Evolve e-4ORCE at an estimated 330km, while the peak is 482km from the Venture+ FWD. It’s tricky to wrap one’s head around, even for those of us who have become used to parsing these figures.
Here’s another challenging statistic: the Ariya’s peak Level 3 charging speed is 130kW, which will recover the battery from 10 to 80 per cent in 40 minutes. Granted, there aren’t yet many DC fast chargers around that are capable of charging at that rate. But the future is hurtling toward us faster than ever, and this feels short-sighted when there are affordable EVs already on sale that are capable of 200kW-plus. Mercifully, while the CHAdeMO standard persists on the Leaf, Nissan has dropped it here in favour of the more efficient and more common CCS format.
From the outside, the Ariya is an attractive vehicle. It doesn’t stand
1. The lower dashboard features faux wood panels with fully integrated touch controls. A pair of 12.3-inch screens present a digital instrument cluster and infotainment system.
2. The most important safety and driver assistant systems are standard, including Nissan’s Safety Shield 360, active cruise control, traffic sign recognition, and a driver attention monitor.
out boldly in any particular manner. Yet given that the first-generation Leaf looked like an alien spacecraft, this is a safer approach. The interior, on the other hand, represents a ground-up new design.
The lower dashboard features faux wood panels with fully integrated touch controls. A pair of 12.3-inch screens present a digital instrument cluster and infotainment system. The true puzzler is the poweradjustable centre console. It moves 15cm forward or back with the push of a button. This is interesting but less functionally important in the face of the amount of usable space it gives up. Under the lid, there’s a small bin that fits a thin wallet or a pack of gum, set behind a somewhat
finicky wireless phone charger. Two glove boxes are set under the dashboard to recover some storage, but their positions are less convenient.
The top panel of this console is well-designed. Two cupholders are integrated on the right side, out of the driver’s way. The gear selector is a shift-by-wire system similar to those in the latest Rogue and Pathfinder SUVs, but the Ariya’s is smaller and sleeker. Behind that are buttons for adjusting the Ariya’s drive modes and activating the e-Step. The latter system increases the intensity of the regenerative braking to recover more range. However, unlike the e-Pedal from the Nissan Leaf, the e-Step function doesn’t allow for one-pedal driving.
The most important safety and driver assistant systems are standard, including Nissan’s Safety Shield 360, active cruise control, traffic sign recognition, and a driver attention monitor.
The 2023 Nissan Ariya is a good-looking vehicle, and its well-proportioned and mostly well-featured. The two biggest challenges buyers will encounter are the complicated trim walk and the pricing, which is several thousand dollars higher than similar equipped competition, even after accounting for federal and provincial rebates. The best sales case for the Ariya is if Nissan can deliver it quickly and get ahead of the competition’s oneto two-year wait. FM/SP
Price (incl. freight, PDI and dealer fees, before rebates): $67,843
Range and battery: 465km, 87kWh
Power: 238hp, 221lbs-ft of torque
Transmission: 6-speed automatic
Rated Fuel Economy (L/100km): Not yet rated
Observed Combined Fuel Economy (kWh/100km): 16.9
From the outside, the Ariya is an attractive vehicle. It doesn’t stand out boldly in any particular manner.
As shown by multiple legal rulings across Canada recently, bidders are becoming more assertive in challenging the technical evaluation criteria used by public institutions in evaluation and award decisions. While many evaluation challenges are dismissed, I’ll summarize two recent cases where the Canadian International Trade Tribunal (“Tribunal”) upheld bid protests after finding the government used biased criteria in the bidding process.
In the first recent example in the PricewaterhouseCoopers LLP v. Canada (Immigration and Refugee Board) decision, the Tribunal determined that the Immigration and Refugee Board of Canada (IRB) relied on hidden and biased evaluation criteria in a bidding process for business consulting and change management services. The complainant, PricewaterhouseCoopers LLP (PWC), failed to meet the minimum technical scoring thresholds and challenged the evaluation result. The Tribunal determined that the government’s technical scoring process was “inconsistent and unduly fluid.” Specifically, the Tribunal found that government evaluators applied undisclosed evaluation criteria that biased past experience scoring in favour of prior work performed specifically for the IRB over more general public sector experience. The Tribunal determined that the government failed to disclose the necessary level of detail regarding its evaluation criteria and its preference of institution-specific experience.
The Tribunal determined that “PwC has a valid complaint that its bid was evaluated as against criteria that differed from those of the RFP
or were undisclosed in the RFP.” It determined the complainant should be compensated for its lost opportunity and bid preparation costs.
This case illustrates public institutions should ensure their criteria are transparently defined in their solicitation documents and should avoid applying hidden preference with biased requirements in their evaluations.
In the second case study, in its determination in Rampart International Corp. v. Canada (Department of Public Works and Government Services), the Tribunal upheld a complaint after finding that the government improperly relied on restrictive specifications. The dispute dealt with an RFP issued by the Department of Public Works and Government Services on behalf of the Department of National Defence for a replacement pistol and holster system for the Canadian Armed Forces. The complainant asserted the RFP contained technical specifications biased in favour of a specific competing pistol design and that those specifications were reverse engineered to align with that competing product.
In its defence, the government argued that the specifications were necessary for legitimate operational requirements. But the Tribunal noted that when government technical requirements are challenged, the government institution bears the onus of demonstrating that its specifications do not unnecessarily restrict competition.
The Tribunal determined that the challenged specifications were based on a specific product design
or type, rather than on neutral performance or functional requirements. While the Tribunal noted that the use of product-based specifications is not completely prohibited under the trade treaties, it ruled that the specifications in the RFP had the effect of narrowing competition, since the government failed to allow for equivalent products.
More specifically, the Tribunal determined that the government could not restrict the competition solely to a specific product, that the government was under a duty to consider equivalent products, and that the government should use neutral specifications whenever possible. The government was ordered to cancel the RFP and redraft its technical requirements to, at minimum, allow bidders to bid equivalent products.
As this case illustrates, when purchasing institutions draft specifications that are based on specific products, the trade treaties require public institutions to consider equivalent products that meet the underlying operational needs. Rather than exposing their procurements to specification-based legal challenges, purchasing institutions should draft their contract specifications based on neutral functional and performance-based requirements.
These recent rulings serve as a reminder to all public institutions that their bid evaluation and award decisions should be based on the transparency and neutrality standards mandated by the trade treaties. The increasing level of bidder assertiveness, coupled with expanding bid protest enforcement mechanisms across Canada at all levels of government, underscores
the importance of avoiding technical evaluation traps in the public procurement process since unfair bidding procedures face an increasing risk of being invalidated by adjudicative bodies. To avoid becoming the next bid protest case study, public institutions should adopt internal procedures that mandate project team members to avoid using hidden and biased criteria and should stress test their evaluation criteria and specifications against fair competition standards before releasing their solicitation documents. SP
“Public institutions should ensure that their criteria are transparently defined in their solicitation documents and should avoid applying hidden preference with biased requirements in their evaluations.”
The advantages of a Subaru fleet are endless. With ownership benefits that go beyond cost of acquisition, you can put your team in reliable, safe and efficient vehicles now, while enjoying uncommon reliability and high resale value down the road.