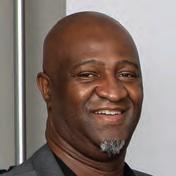
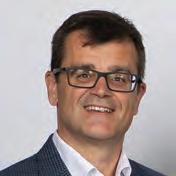
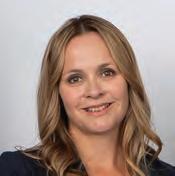

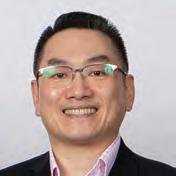
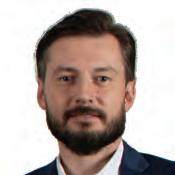
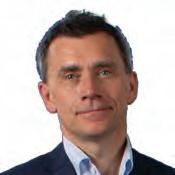
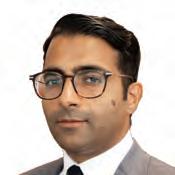
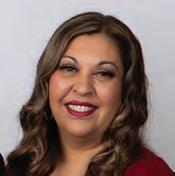
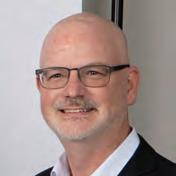
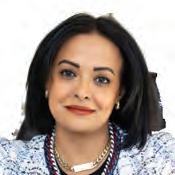
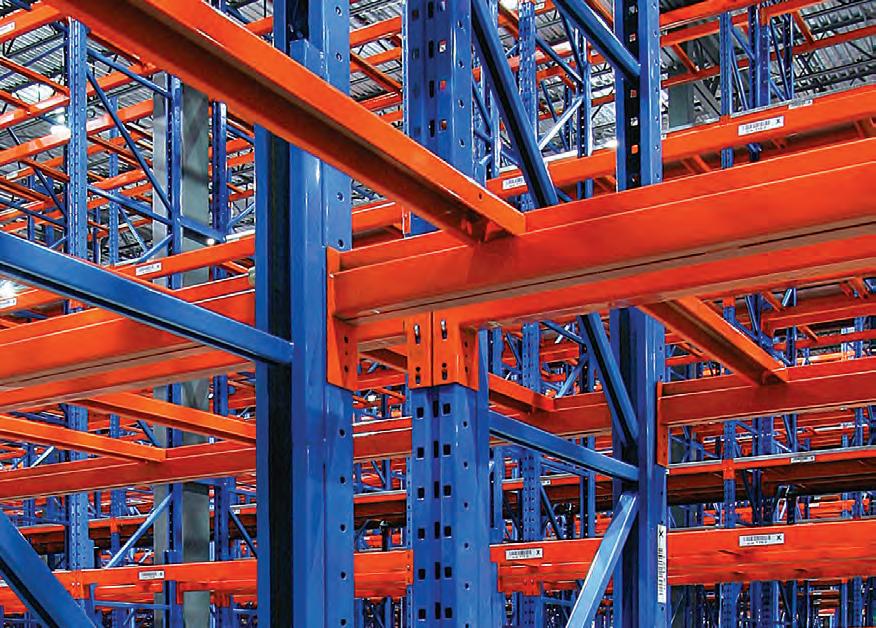
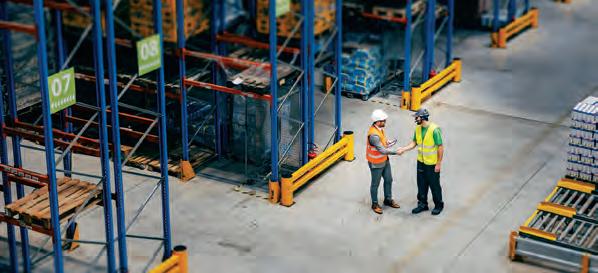
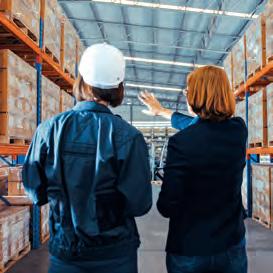
To stay competitive and get ahead, you need innovative, scalable and safe solutions. These solutions can help with better storage, distribution, fulfillment or any combination that can grow with your business as it adapts to change.
As your partner in facilities evolution, you can count on Konstant to transform your facilities. Collaborate with our team to optimize your facility today and evolve, anticipate, adapt and imagine the facility of your future.
Get integrated logistics solutions: racks, shelving, trucks and robotics from our partners including Johnston Equipment and GNJ Automation.
Access comprehensive services for your project lifecycle, from planning to ongoing management with a skilled team ensuring quality at every step.
For more than 50 years, Konstant has served businesses across Canada, adapting our services to evolving facility management needs.
| 1-866-202-0064
The
I recently browsed the online agenda for an upcoming humanoid robotics conference and, as expected from the event’s title, many of the topics sound compelling and cutting edge.
Those topics include things like incorporating machine learning into robotics, human-robot collaboration, and advanced robotics in manufacturing and production.
I’m continually amazed at how fast technology advances and the ways it’s integrated into business. I enjoy watching online videos of humanoid robots doing various interesting tasks – from manufacturing work to dancing.
Robotics and advanced technology will continue to impact practically every area of our lives. There’s a certain flashiness to such advances.
Other, ostensibly lower-tech areas are also evolving rapidly. But such developments often fly under the radar compared to more celebrated areas like humanoid robotics.
Take packaging, where innovation rivals any other area in its ingenuity and benefits, including offering several sustainability wins. It proves that impressive advances are possible within supposedly low-tech areas. Those advances can make a big difference.
There are examples of these advances in our packaging story on page 8. That article references a recent report from the Sustainable Packaging Coalition, which highlights several packaging trends.
The “paperizaton of everything” is one such trend. The report notes that paper has its appeal for several reasons. It’s renewable if handled right. Consumers may also like paper’s “earthy” feel, and it’s often associated with renewability.
The report also notes the trend of deriving packaging material from ocean life. Seaweed, for example, can be used for new packaging applications. Chitin, a polymer derived from the exoskeletons of shrimp and other small creatures, is being used for films, foams, coatings, pellets, and polymers.
As with robots, digital technology is helping to innovate packaging. The report highlights how machine learning is integrated with sortation robots to get better streams of recyclable material. Machine learning is also helping to screen non-recyclable material at recycling facilities, as well as components that needs to be recovered differently, like food and compostable materials. Manufacturing and supply chain problems can cause headaches and seem intractable. But ingenuity and innovation can offer a sometimes-surprising array of solutions.
On another note, check out the news on page 7 about Supply Professional’s partnership with the National Institute of Supply Chain Leaders (NISCL). We’re excited to announce that we’re now the official magazine of the organization.
We have a long history with NISCL. As some of you might remember, we were its official publication when it was known as PMAC and SCMA. Our current partnership means we can combine our knowledge of and access to Canada’s supply chain. This will enhance the coverage we’re able to provide you with.
We look forward to this partnership, and I’m especially interested to hear what you, our readers, think of the arrangement going forward.
EDITOR
MICHAEL POWER 416-441-2085 x7 michael@supplypro.ca
PUBLISHER
FARIA AHMED 416-441-2085 x 5 faria@supplypro.ca
DESIGN
Art Direction ROY GAIOT Design Consultation BLVD AGENCY
EDITORIAL ADVISORY BOARD
LORI BENSON Procurement Compliance, L&D, Engagement and Knowledge Lead | Business Enablement, Ernst & Young LLP
THOMAS HUDEL Manager, Purchasing and AP, Esri Canada Ltd.
WAEL SAFWAT Procurement Director, Black & McDonald
SHERRY MARSHALL Senior Manager, Meetings, Travel & Card Service, PwC Management Services
KIRUBA SANKAR Director, Program Support, Purchasing and Materials Management— City of Toronto
JEFF RUSSELL Corporate Purchasing Manager & Inventory Manager, Miller Waste Systems Inc.
iQ BUSINESS MEDIA INC.
Vice President
STEVE WILSON 416-441-2085 x3 swilson@iqbusinessmedia.com
President & Executive Publisher ALEX PAPANOU
PUBLICATION MAIL AGREEMENT NO. 43096012 ISSN 1497-1569 (print); 1929-6479 (digital)
CIRCULATION
Mail: 126 Old Sheppard Ave, Toronto ON M2J 3L9
SUBSCRIPTION RATES Published six times per year Canada: 1 Year $ 99.95 CDN Outside Canada: 1 Year
Opinions expressed in this magazine are not necessarily those of the editor or the publisher. No liability is assumed for errors or omissions. All advertising is subject to the publisher’s approval. Such approval does not imply any endorsement of the products or services advertised.
Publisher reserves the right to refuse advertising that does not meet the standards of the publication.
No part of the editorial content of this publication may be reprinted without the publisher’s written permission. © 2021 iQ Business Media Inc. All rights reserved. Printed in Canada.
Supply Professional is the Official Magazine for NISCL
Have you ever gone to the cinema, bought a large, buttered popcorn, settled in to enjoy the movie, and while you’re munching on the snack, one of the kernels gets stuck in a back molar? Then you can’t concentrate on anything else except trying to get it out. I’ve experienced something similar, metaphorically, for the past 20 years.
That is, I’ve had an idea bouncing around in my head that I’m finally getting down on paper. And for the lack of a better phrase, I call it the 50 per cent solution.
Please keep in mind that this is a column dedicated to economic and business affairs. I would never suggest that what I will be laying out will cure all of the world’s ills. But it does address what is a serious political problem that besets representative democracies like the US and Canada. This problem bleeds into the economic sphere and it means that the almost unbounded potential of North America is not currently being realized and will never be realized. For an old guy like me, it’s not such a big deal. But it has a profound impact on the next generations whom we are currently betraying badly.
If you’re a regular reader of this column, you’ve heard me address this before and it’s the staggering amount of government debt. The day before I sat down to write this column, I heard that the US government has spent in excess of $1 trillion dollars on interest on its national debt this fiscal year. That’s approximately $3,000 for every man, woman, and child. Think of what an extra $12,000 a year would mean for the average working class family. But the short-term motivation for all politicians is to pander
to the public, and selectively bribe certain cohorts of the electorate, running up deficits along the way.
Here’s the challenge. Can we design public policy that balances budgets, eventually reduces national debt, while simultaneously encouraging economic growth?
The answer is yes, and with no further ado, here is the outline of the 50 per cent solution.
It starts with a radically different income tax policy. Unlike the US, Canada does not have an “official” poverty line. But I’m going to use (adjusted) the American rate. It’s $30,000 for a family of four, which would translate into CAD$40,000. For an individual, it would be more like CAD$20,000. The relevant poverty rate would be the deductible, and then the tax rate, for everyone, would be a flat 50 per cent.
Let me use two individuals to demonstrate the point. There are two single people in their early 30s. One makes $30,000 a year and the other makes $100,000 a year. The first person would pay $5,000 in tax [($30,000 – $20,000) x .5 = $5,000] which would result in a tax rate of 16.7 per cent. The second would pay $35,000 in tax [($100,000 – $30,000) x .5 = $35,000] which means 35 per cent. I’ve just demonstrated, empirically, that this is a highly progressive tax system which is something that most people think is both fair and reasonable.
Would that generate enough tax revenue for Canada? Almost certainly not. We would still need to have HST with intelligent exceptions for necessities like basic food,
clothing, and shelter. We would still need tariffs on imported goods which would both encourage domestic production and raise the necessary money to keep the wheels in Canada turning. We would still punitively tax products like tobacco, alcohol, and marijuana to discourage usage. That’s the revenue side of the equation.
Now let’s turn to the expenditure side. Once all the money was spent on projects that only government can execute, whatever is left over would be distributed equally to every citizen of Canada. I’m going to return to the example of the $30,000 and $100,000 wage earner. We’ve established that they would pay $40,000 in tax altogether. For the sake of argument, we’ll assume that half would be spent and half would be distributable. Now the $30,000 earner would end up with $35,000 ($30,000 –$5,000 + $40,000 x .5 x .5) and the $100,000 earner would take home $80,000 ($100,000 –$30,000 + $40,000 x .5 x .5).
One last thing. It would take time to transition to this system because a pillar is that the national debt must be eliminated completely. Canada would be run on a pay-as-you-go basis. It would mean freezing the absolute level of the national debt for a decade, since inflation alone would reduce it significantly in real terms, then over the next decade debt would be shaved by 10 per cent a year until it was zero. The 50 per cent solution would provide the incentive to keep government as lean and efficient as possible. Now back to the feature film! SP
“Can
we design public policy that balances budgets, eventually reduces national debt, while simultaneously encouraging economic growth? The answer is yes.”
A people-centric inventory management approach highlights the need to maintain the right inventory balance. You cannot sell what you don’t have, and you can’t make money on what you can’t sell.
Inventory management encompasses all departments within a business and it makes sense that responsibility for inventory management goes beyond finance. We’ve come a long way in developing inventory systems and we’ve seen relational databases that integrate inventory management with other business systems. We have web-based systems that enable us to access data from anywhere and collaborate with suppliers and customers. Many have progressed to cloud-based inventory management systems facilitating cloud-ERP.
One constant across the evolution of inventory management is people – people to help manage, operate, and improve it. Research and industry reports suggest human error rates for managing inventory may contribute 20-to-30 per cent of inventory inaccuracies. We often take the easier solution when mistakes and errors occur by focusing on the process, as it is more comfortable than dealing with people.
This article explores the human element in inventory management, the human impact on inventory accuracy, and how training, along with leveraging technology, can support accountability.
I’ve seen all kinds of inventory management errors over 15 years. Five typical errors come to mind: data entry, counting errors, misplacement and mislabelling, procedural errors, and communication breakdowns. Other inventory
issues include poorly controlled product catalogs, too few (or too many) performance indicators, focusing on price not cost, poor housekeeping, too many storage points, warehouse space, and too many inventory management tools.
It’s not surprising when you consider all the individuals who touch each stage of the inventory process. Gaining buy-in from stakeholders with different initiatives creates challenges.
The impact of these inaccuracies can translate across the business and include lost sales and customer dissatisfaction, overstock and holding costs, operational efficiencies, expedited shipping and order fulfillment costs, loss of market opportunities and inventory shrinkage.
Companies must decide which performance measures make the most sense for them. Key performance measurements include service levels, inventory levels, inventory accuracy, fill rate ratio, the number of SKUs and obsolescence.
A system that considers reordering quantities and timing by product based on times and safety stock will help with managing inventory.
An inventory performance dashboard can keep employees inspired. Identifying gaps helps you to build action plans and improve processes while empowering people.
Leadership that balances the need to have products for customer service and awareness of the costs of carrying inventory is crucial. One that models the behaviour they wish to see in their employees demonstrated through accountability, collaboration, and prioritization
of improvement. Not correcting persistent errors reduces morale.
Standardized processes, automation, and training helps to develop clear procedures and spot potential issues. Adopting practices such as cross training, spot audits, cycle counts, mobile handhelds with error notifications, double checking high value and critical items and peer reviews can reduce human errors. Streamlining processes, maintaining accurate stock levels, creating designated areas for picking, packing, shipping, and receiving support workflow efficiency and minimize inventory problems. Enhancing your warehouse management system with code to flag address and postal code mismatches can reduce errors.
The use of software is a key part of inventory management. Businesses use tools like Excel, accounting packages, ERP and MRP systems, and often customize these solutions in order to meet specific needs.
Leveraging technology and exploring innovative approaches can significantly improve inventory management. Top initiatives to explore include AI-driven demand forecasting, predictive maintenance, and the use of IoT devices and smart sensors for alerts and automatic reordering. Automation tools like robotic process automation (RPA) can minimize errors and enhance efficiency, while large facilities may benefit from drones for real-time scanning. Radio frequency identification (RFID) can further optimize supply chain movement.
Cloud-based inventory management systems, offering customizable dashboards and reports, can
“When you identify gaps, you can put action plans in place and improve processes while empowering people.”
enable better decision-making. Collaborating closely with suppliers to implement just-in-time systems or vendor-managed inventory (VMI) can reduce waste and increase efficiency. Advanced optimization strategies can include big data analytics. Incorporating sustainable practices, such as adopting circular economy principles and green technology, is another area to explore. Industries might try 3D printing to streamline inventory. Organizations with inventory across various channels could consider exploring omnichannel strategies. At the same time, those seeking an initiative-taking approach should look into reverse logistic strategies that will further refine their inventory processes.
Ultimately, establishing effective processes may only require a conversation to foster a work environment that’s aware of errors. SP
Contract logistics provider Metro Supply Chain has acquired SCI and is integrating it into a single brand. The move will strengthen the company’s position in strategic supply chain solutions, according to a press release.
“The teams have been working hard these past few months to align our deep breadth of services and I am excited to officially bring SCI’s capabilities under the Metro Supply
Chain banner later this fall,” said Metro Supply Chain president and CEO, Chris Fenton.
Marking the 12th business acquisition Metro Supply Chain has made in less than a decade, SCI adds sectors like technology and healthcare to the industries the company serves and reinforces its e-commerce fulfilment capabilities in Canada.
Supply Professional and the National Institute of Supply Chain Leaders (NISCL) have signed an agreement making Supply Professional the official magazine of the organization.
The agreement reinforces both organizations’ commitment to promoting excellence and leadership within Canada’s supply chain community, the two organizations said in a joint press release. Also through the agreement, NISCL will also regularly contribute thought leadership content to the magazine, highlighting key industry trends, insights, and best practices in supply chain management from its community of supply chain executives.
“This agreement with Supply Professional aligns with our vision to enhance the employer recognition for the supply chain profession through the development of functional and leadership excellence,” said Al-Azhar Khalfan, president and CEO of NISCL. “By sharing our expertise through such a well-established publication, we are extending the reach of NISCL and also ensuring increased awareness for the NISCL-CSCL Designation.”
This partnership underscores NISCL’s dedication to enhancing the recognition of supply chain professionals and promoting leadership development across the industry, the organization said. The collaboration will also provide the organization’s community of over 12,000 professionals with access to high-quality, thought-provoking content designed to inspire innovation and drive progress within the supply chain sector.
“We’re thrilled to partner with NISCL and showcase their thought leadership in Supply Professional,” said Faria Ahmed, publisher of Supply Professional. “As a publication, we provide fresh perspectives and valuable insights to our readers in the Canadian supply chain community. NISCL’s contributions will further strengthen the content we offer.”
NISCL and Supply Professional said they will work together to enhance the visibility of the supply chain profession and foster a community that embraces excellence and leadership.
One in five Canadian businesses hit with payment fraud
A study from Payments Canada says Canadian businesses have a higher rate of payment fraud compared to that of consumers, at 20 per cent versus 13 per cent, respectively, although the types of fraud were similar for both segments.
The rate of payment fraud was consistent from 2023 at 19 per cent, despite 63 per cent of businesses
reporting they feel confident knowing how to protect themselves, and 61 per cent noting they are more aware of how to recognize potential threats. The study revealed that while all businesses are vulnerable to payment fraud, larger-scale commercial businesses saw the highest rate at 26 per cent, compared to large (23 per cent) and small (16 per cent).
Canadians ready for greener EV delivery: study
Canadians generally think highly of using EVs for deliveries, according to a study by Geotab and Angus Reid.
The online survey of 1,500 Canadians reveals 66 per cent of respondents agree commercial truck fleets should invest in EVs where feasible.
One in three are more likely to purchase from companies using EVs. Younger Canadians show a stronger preference: 48 per cent of respondents aged 18-34 said they are more likely to purchase
goods from companies using EVs for deliveries, compared to 33 per cent (age 35-54) and 24 per cent (over 55).
Some Canadians are willing to pay a premium for EV deliveries, with 20 per cent willing to pay a small extra delivery fee, 44 per cent willing to wait an extra day, and 44 per cent accepting their delivery limited to specific days. As well, 58 per cent support government incentives for SME delivery companies to facilitate an EV transition.
BY MICHAEL POWER
at Presentations Plus Training & Consulting. Metals can be recycled and repurposed many times and retain their tensile strength and other properties – if they are collected properly for recycling. Repurposing aluminum for other packaging reduces energy consumption by over 90 per cent, he notes, as opposed to processing bauxite ore into original aluminum materials.
Creating a sustainable supply chain involves multiple moving parts –renewable energy, optimized transportation and logistics, and circular economy principles, among others. Also important is the packaging used to house and protect products as they move through the supply chain.
The push towards sustainable packaging has several benefits, says Matthew Wright, founder and CEO of Specright. Those benefits include cost savings, reduced waste, an improved brand, and increased customer trust, to name some. According to Specright research, 40 per cent of consumers are uncomfortable buying products from companies not working towards sustainability goals, while 25 per cent track government regulations around sustainability to understand the environmental impacts of products.
“Given this increased awareness, consumers are switching up their purchasing behaviours, with primary purchasers often putting their money toward more sustainable products,” Wright says.
Innovations abound as companies work to purge their supply chains of packaging that may be harmful to the
environment. Much of the move towards sustainable packaging recently has involved limiting single-use plastics. That shift has seen paper fiber entering areas traditionally dominated by plastics, says Wright. Amazon, for example, announced earlier this year that it had already replaced 95 per cent of its plastic air packaging with fully recyclable paper filler.
In a report, the Sustainable Packaging Coalition calls this trend “the paperization of everything.” Other recent innovations include water-soluble packaging in the beauty industry and seaweed packaging for some consumer goods, Wright noted.
Coca-Cola even ran a pilot program in which they temporarily removed labels from Sprite and Sprite Zero bottles in the UK, replacing them with information etched onto the bottle instead.
“All these innovations result in less packaging waste in landfills and ultimately aid in companies meeting their sustainability goals,” Wright says.
The paper packaging industry has worked in recent years to meet the demand for renewable alternatives, says Rachel Kagan, executive direc-
tor of the Brampton, Ontario-based Paper and Paperboard Packaging Environmental Council (PPEC). That includes paperboard lids made from fiber wraps to replace large plastic wraps for crates, corrugated baskets for produce, paperboard rings (rather than plastic) for beverage multipacks, among other developments.
The industry is also a pioneer in recycling, Kagan notes, implementing a circular economy long before the concept became widely recognized. As far back as the 1960s, the industry realized it made sense from a business and sustainability perspective to prioritize recycled fibers over virgin as the primary feedstock for products, she says.
“It’s been that way for decades,” Kagan says. “We definitely want to talk about some of the innovations happening in the marketplace, driven by the things that are happening today, but also not lose sight of what was going on 40, 50 years ago. Circularity has been an inherent part of our industry’s operations for a very long time.”
Packaging products in easily recyclable materials make good sustainable options, says Larry Berglund, SCMP, MBA, FSCMA, and principal
“The downside to metals is their weight difference over plastic products for the same intended purpose,” Berglund says. “Making glass and metal containers requires significant amounts of energy to extract and produce, again, costing more than plastics.”
Berglund also points to recent packaging alternatives, like making bottles from paper, as innovative solutions that draws on the circular economy and recycling principles. Bioplastics are another potential solution. The University of British Columbia’s Faculty of Forestry created a bioplastic from grass that only uses waste stalks. Corn has also been used for plant-based plastics.
There’s some controversy surrounding the use of plastics in packaging, Berglund says. There’s a shift towards using mono plastics – made from a single type of polymer – which is regarded as an acceptable move away from multi-layer packaging materials.
“Mono plastic is easier to recycle, requires less energy to produce, it can be repurposed, and requires fewer resources to manufacture,” Berglund says. “Mono packaging materials, while not ideal, align with the circular economy values.”
Alongside innovations in packaging materials, digital technology is helping to keep packaging sustainable. One approach is for companies to monitor the lifecycle of the packaging they use through digitizing its specification data, says Wright of Specright. That data is often housed in various static systems like email, spreadsheets, shared drives and so on that can result in the creation of silos.
Digitization allows organizations to monitor that packaging
from its raw materials and dimensions to production, finished goods, and supplier details while also identifying areas for improvement.
“The process of tackling sustainability doesn’t have to be complex – it simply starts with understanding your products and packaging at the DNA level of data, AKA specification data,” Wright says. “Companies across industries can take the first step by digitizing specifications, saving teams time that would otherwise be spent chasing that data.”
The digital threads that result from this process allow better compliance with the growing body of packaging regulations, he adds. That also allows organizations to be transparent with their customers about the history and sustainability of its packaging and the products those customers purchase.
“Choosing to focus on specification data management, companies improve their overall traceability
“With consumers more aware of packaging’s impact than ever before, the time is now for companies to act on creating more sustainable practices.”
and support more sustainable practices in general by making datadriven decisions,” he says.
The various internationally recognized forest certification organizations can help identify paper fibers that are verified to be responsibly sourced, says PPEC‘s Kagan. The Canadian Standards Association, The Forest Stewardship Association, The Forest Stew-
24_009027_Supply_Professional_OCT_CN
ardship Council, and The Sustainable Forestry Initiative are a few such organizations. These groups assess forestry operations against Canadian law and other standards, which helps with the traceability of those products.
As the push towards sustainable operations continues, it’s important to remember that packaging serves an important function, adds Kagan. Packaging protects its contents, keeping them safe as they travel through the supply chain. It can also provide information to customers.
“Sometimes, people forget that there are bilingual requirements, there are nutrition facts specific for food, but there does need to be information for consumers in some cases,” she says. “So, a lot has to be balanced when we’re talking about packaging.”
Through digitization, it’s possible that products can be both sustainable and cost-effective, says Wright. “With consumers more aware of packaging’s impact than ever before,
the time is now for companies to act on creating more sustainable practices all around, starting with more sustainable packaging.”
Supply chain professionals must stay on top of packaging developments and criteria if they want to protect their products and meet stakeholder expectations, adds Berglund. He also stressed the need for balance between factors like cost, environmental benefits, logistics requirements, and inventory objectives.
“Innovation through design and technology will be an important part of the transition to more responsible packaging; affecting customer perceptions of value may be part of the solution as well,” he said. “Circular economy principles are an encouragement to innovate through technology and designs. Environmental, social and governance practices support responsible packaging. The solutions may not be perfect, but these ideas support a commitment to reduce our footprint.” SP
Recent years have seen myriad supply chain disruptions, at home and abroad. COVID-19, geopolitical unrest, and recent extreme weather events – among other factors – changed how our supply chain ecosystem functions. At the same time, Canada’s supply chain leaders face pressure to meet ambitious enterprise goals that cater to changing customer behaviours and expectations. There’s a transformation afoot and, now more than ever, those leaders find themselves at the vanguard of change.
That’s why our new mandate at the National Institute of Supply Chain Leaders (NISCL) comes at the right time. We’re laser-focused on building strong leadership attributes among supply chain professionals across Canada –attributes to further elevate the profession.
“Supply chain professionals have led the Canadian economy with courage and commitment in the past five years, what is clearly marked as one of the most challenging times in the history of Canada’s economy,” says Al-Azhar Khalfan, NISCL’s president and CEO. “They have been the frontrunners of the Canadian economy during the most challenging and disruptive times. They have demonstrated true
leadership through their ability to think ahead, solve problems and pivot toward innovative solutions. Our rebrand to NISCL is underpinned by our belief that the community we serve and represent are established and aspiring business leaders.”
Today, supply chain is at the heart of any enterprise strategy. It is no longer a back-office function concerned simply with cost savings. The shift in perception is evident. In this article, we speak with many of those luminaries who discuss the fundamentals of leadership and their perspectives on building a workforce comprised of true supply chain leaders.
Among the topics we discussed was what attributes create leadership within the field. Below are some of their comments on the topic.
Nick Nanos, Chief Supply Chain Officer at LCBO: “Leadership excellence in supply chain is at the very core of driving transformation. Leadership is not essentially reflected by the title that one holds but is demonstrated through mindset and behaviours. For me, leadership attributes include a focus on the customer, the
ability to champion change, the delivery of results, and the power to develop new leaders further.”
Kristie Syndikus, VP-Procurement, Maple Leaf: “Leadership is exemplified by those who are eager to learn, who are self-aware, and who are open to feedback. We value curiosity, insight, and the ability to challenge the status quo. Leadership is a rich amalgamation of various qualities including transparency, humility, integrity, adaptability, vision, and innovation.”
Hugh Amiel, Senior Director - Procurement & Supply Chain, UHN: “For me leadership is a blend of skills, experience, and cultural fit. Key attributes include strong problem-solving abilities, adaptability, and a collaborative mindset. Individuals who demonstrate a proactive approach to learning and growth, possess effective communication skills, and exhibit a genuine passion for their role and the organization’s mission – make great leaders.”
One of the most debated topics within supply chain involves the war for talent. Today, with technology advancing and the digital revolution underway, demand for that talent is at an all-time high. Supply chain leaders must know what to look for to meet their human capital needs.
Todd Campbell, VP - Supply Chain & Manufacturing, The Clorox Company: “While seeking talent for my team, I prioritize individuals who embody strong leadership attributes. These attributes include the ability to provide purpose, direction, and motivation. Additionally, I value strategic thinking, accountability, knowledge, and pride in the supply chain profession. While functional excellence is essential as we elevate the supply chain profession, leadership excellence is paramount as we drive transformation.”
Tharshini Markandaier, Head of Category Management & Procurement, TTC: “When hiring talent, I look for people who are strategic thinkers and can adapt quickly to change. I value strong analytical skills for making informed decisions and foreseeing future needs. Effective communication and teamwork are crucial, as these qualities help align everyone with our goals. I also appreciate candidates who are committed to continuous learning and innovation, as these traits drive our processes forward and ensure long-term success.”
Dimitri Fleitman, NISCL-CSCL/CSCMP, Head of Supply Chain & Strategy, Dole Packaged Foods, Canada: “While critical thinking, an analytical approach, and problem-solving are table stakes, for me, the key differentiator would be someone who can lead with purpose. To truly excel as a supply chain leader, I value someone who can embrace leadership with purpose by inte-
grating social, economic, and environmental considerations into every decision. It is a learning process, but understanding and influencing that supply chain are not just mechanisms for delivering goods, but are powerful levers for driving positive change in the world.”
Future supply chain leaders will have access to more technology, industry data, and resources than their predecessors. Yet, they need guidance from today’s leaders in the field.
James Lin, VP-Procurement, OLG: “Technically, these are two pieces of advice, but they are interrelated. I would advise my team to do things outside of their comfort zone and commit to continuous learning. I firmly believe that as long as you keep pushing yourself to do new things you are uncomfortable with, you will learn and become a better leader. Haven’t done sales before? Try it and learn. Haven’t done public speaking before? Do it and learn. Nervous about presenting to executives? Do it repeatedly, seek out the opportunities to do so, ask for feedback and continue to improve.”
Barbara McDonald, Director – Customer Supply Chain, Sofina Foods: “Be confident. Be a role model to someone. Know your business, know your customers, and most importantly know how to collaborate with your peers. You are not expected to know everything, but you should know who to approach/learn from to provide the level of service your internal/ external customer requires. You will develop your own leadership style over time through listening and learning cross-functionally.”
Ashifa Jumani, Director, Procurement at Telus: “Adopt a growth mindset and believe in your ability to improve through effort and perseverance. This mindset flips failures into learning opportunities and drives continuous improvement. Be humble, surround yourself with people who have different strengths than you. Listen to them and learn from them.”
Talent thrives in the right environment. Organizations must nurture that environment so that their supply chain talent can flourish. We asked our experts what they and other leaders in the field can do to cultivate the right ecosystem.
“While multi-year trends have put pressure on supply chains, the tumult of the past few years has sparked an evolution in the field.”
Steve Radewych, SVP, Supply Chain Operations, Spin Master: “Give team members meaningful opportunities with the risk of failure. More importantly, provide an environment where learning from success is embraced as much as learning from mistakes. At Spin Master, we are investing significantly across all
levels of leadership over the last three years, with a concerted effort at bringing awareness to leadership ‘diminisher’ traits and how to minimize those, while focusing on ‘multiplier’ characteristics as a means of harnessing team performance.”
James Lin, VP-P rocurement, OLG: “The best leaders create other leaders, contributing to the “workforce ecosystem.” Never be afraid that your team members might surpass you. In fact, as a leader, you have only truly contributed if your direct reports have succeeded you or have moved on to take senior positions in other organizations.”
Supply chains are fluid. Recent changes in the field have forced professionals to adapt quickly, providing them with opportunities to grow their skills and influence.
“Leadership is a continuum,” says NISCL’s president and CEO, Al-Azhar, in conclusion. “While multi-year trends have put pressure on supply chains, the tumult of the past few years has sparked an evolution in the field. For the supply chain profession to continue on this growth trajectory, organizations must unlock a continuous learning path where supply chain professionals flourish to become true leaders by demonstrating technical and leadership skills.
“This is an important turning point for the profession and now is the time to harness the momentum gathered in the last few years, while embracing the leadership excellence required by the profession to establish itself as a strategic enterprise function.” SP
BY JENNIFER SOUCH
In today’s fast-paced and intercon nected world, supply chain management (SCM) is a crucial pillar of the global economy. As indus tries advance and challenges grow more complex, staying current with industry knowledge is essential. For supply chain professionals, continuing education is not just about staying relevant – it’s a stra tegic investment in career growth and organizational impact.
The SCM landscape evolves rapidly. Continuing education helps professionals stay informed about trends, tools, and best practices. For instance, learning about advancements like blockchain and AI can impact supply chain man agement and optimization.
In my own career, continuing education has been transformative. Earning a BSc, MSc, and MBA, along with certifications such as PMP, CPIM, and SAP Certified Associate, has advanced my profes sional journey. For example, the
TORONTO APRIL 29 TO MAY 1, 2025, ENERCARE CENTRE
SEIZE THE OPPORTUNITY NOW!
SIAL CANADA 2025 SUPPLY CHAIN/PACKAGING SECTOR IS IN HIGH DEMAND WITH 75% OF SPACES ALREADY FILLED!
Be part of the future at SIAL Canada 2025 agri-food tradeshow! Present your solutions to a global audience and position your brand at the forefront of industry evolution. Don’t miss out—spaces are filling up fast! Secure your spot at SIAL Canada 2025 and leave your mark on the world of food innovation.
SIAL CANADA GIVES YOU ACCESS TO A TARGETED AUDIENCE
2,000+ supply-chain visitors come to SIAL Canada from year to year
900+ visitors looking for logistics solutions
Buyer-visitors from this sector:
Cora Restaurants, Costco, Dollarama, Loblaws-Provigo, Mac’s/Couche-Tard, McDonald’s Canada, MTY Group, Shoppers Drug Mart, CARA Operations, Walmart, etc.
RESERVE YOUR BOOTH NOW!
Canadian Exhibitors
ngaro@expocanadafrance.com
International Exhibitors exhibit.sialcanada@sial-network.com
Want to visit? visitors@expocanadafrance.com
BY JACOB STOLLER
Parallel worlds that exist in cyberspace have long been familiar territory for sci-fi fans and video game enthusiasts. Industry, however, has only recently begun to utilize the full power of this technology.
Digital models have been widely used since commercial 3D computer-aided design (CAD) software was introduced in the 1970s. The technology found initial application in the automotive industry, first in the design and development of components, and then expanding to include assemblies, entire vehicles, assembly lines, facilities, and supply chains.
The game changer has been the transition from static models to dynamic virtual systems that, thanks to the infusion of real time data, can behave just like their counterparts in the physical world.
“Fundamentally, a digital twin is a virtual representation of a physical object, system, process, or anything that you can think about,” says Indranil Sircar, CTO, manufacturing and mobility, Microsoft.
The wide proliferation of the Internet of Things (IoT) has greatly expanded the utility of these models. Instead of providing a static simulation of, for example, an engine component, these digital twins can have a dynamic relationship with the physical world that is constantly updated by data streamed in real time.
“I think where we start to see the real value of a digital twin,” says Sircar, “is how it can use the real time data to simulate and predict behaviour and performance of every component without having to create that in a live environment.”
One example of this is hardware-in-the-loop (HWIL) testing, where the software in an automotive component can be tested in a virtual twin of the hardware environment in which the component would operate. This is particularly valuable in testing autonomous driving components, where live testing would be hazardous.
On a larger scale, digital twins can be used to determine the feasibil-
ity of accommodating product variations on an existing assembly line.
“You can use a digital twin for planning and testing, so it’s much more than a simulation,” says Dr. Daniel Knödler, director client engagement global manufacturing industries, IBM Technology. “For example, if that assembly line is supposed to produce other vehicles tomorrow than it does today, then you might be interested in getting real data with respect to how the vehicle could be produced on that assembly line, or how that assembly line would behave with respect to productivity if you made some changes to the product. Would it increase the need for maintenance? Would it even work?”
Digital twins are also widely used in the construction industry, where Building Information Modelling (BIM) is becoming the industry standard for large projects. This not only facilitates collaboration and eliminates rework during construction but makes it easier to apply drone inspection and other robotic
technologies in the maintenance of the facility once it is completed.
Knödler mentions a bridge in Denmark where a digital twin provides a reference point by which drones can collect data for ongoing maintenance. Instead of taking a month for physical inspection, the bridge can be inspected in one day, making it cost effective to survey the health of the bridge on an ongoing basis.
Digital twins are also seeing a growing use in predictive maintenance. “Being able to simulate real world conditions can help to predict equipment failure at any point in time,” says Sircar. “But when you combine that across a multitude of applications into a process level, you can see how various conditions impact each other. So, a company can simulate, for example, how they might re-align their assembly lines for a new product. Those simulations are becoming a lot more interesting, because they are making it easier to test innovative
approaches that people might not otherwise have considered.”
Sircar also notes that a virtual model also allows an engineer to collaborate remotely with a factory environment located halfway around the world, or to utilize Generative AI to explore different scenarios.
A major challenge for these systems is having common data standards according to which the contextual meaning of the data is clearly and consistently defined. “To create a digital twin, there has to be a common understanding of what the data means,” says Knödler. “Automotive has this, but there are different ontologies in logistics, supply chain, production, and product development. This is probably why digital
twins have so far been mainly in the automotive industry.”
Consequently, creating a digital twin of a supply chain would involve phenomenal collaboration on data standards between various players who are scattered all across the world.
Accordingly, Knödler suggests, one can look to the automotive sector to discern where the digital twin technology is headed.
“Today’s vehicles constantly need software updates, like our mobile phones,” says Knödler. “From that perspective as an OEM, you’re changing from a product manufacturer into an operator of a fleet with millions of vehicles to update. And these updates vary by country depending on regulations and other things. So, with digital representa-
“You can use a digital twin for planning and testing, so it’s much more than a simulation.”
tion of a vehicle, we can do functional upgrades and retrofits better than we were able before. But to do that, you need to have a digital representation of your entire fleet. Otherwise, you would have to rely on different systems and a lot of manual effort.”
Another forward-looking vision for digital twin technology is the enablement of Industry 5.0, defined on the EU website as a vision that
“places the wellbeing of the worker at the centre of the production process and uses new technologies to provide prosperity beyond jobs and growth while respecting the production limits of the planet.”
“AI can enhance human capabilities by integrating advanced technology to support human tasks,” says Sircar. “So human and a machine collaboration is the key aspect of it. That’s one of the foundational shifts that we are starting to see in the industry. As an example of it, we no longer talk about bringing in AI and automation to replace people. Yes, there are certain tasks that will get replaced by automation, but I think Industry 5.0 is going to enhance the people capability, and that will be accelerated by where digital twin technology is headed right now.” SP
Bring people together. Collaborative SpacesTM fosters teamwork through adaptable environments that can transform at a moment’s notice or evolve over time. Optimize existing spaces with individual pieces or create new ones with the full range of mobile team carts, work tables and accessories. Scale up, scale down, create a space for the way you work. globalfurnituregroup.com
BY AMANDA CHOUINARD
As the global sustainability landscape continues to evolve, public sector organizations are playing an increasingly pivotal role in driving meaningful change. In Canada, efforts to address pressing environmental, social, and economic challenges are gaining traction, fueled by new regulations, innovative strategies, and a growing commitment to long-term resilience. This momentum is reflected in the actions of members of the Canadian Collaboration for Sustainable Procurement (CCSP), where over 50 public sector organizations are leveraging procurement as a tool to advance their sustainability agendas. The 2023 CCSP Annual Report highlights key trends and showcases the strides made by members in embedding sustainability into procurement practices. These trends reflect both the challenges and opportunities facing organizations as they navigate complex supply chains, climate change, and social responsibility.
While Indigenous procurement, supplier diversity, circular economy, electrification, and climate action continue to be prioritized, there are newly emerging risks and opportunities worth paying attention to – from integrating biodiversity considerations and addressing human rights risks to enhancing climate resilience and adopting cutting-edge technology. Below are five
emerging sustainable procurement trends that procurement leaders should consider to progress in their sustainability efforts.
Biodiversity protection is rapidly rising to the forefront of sustainability efforts, alongside the circular economy and net-zero. With the diversity of life on Earth—from microorganisms to entire ecosystems—declining due to deforestation, land degradation and overexploitation of natural resources, the critical role biodiversity plays in regulating natural systems is now undeniable. Healthy ecosystems are essential for climate stability, clean air, soil health, and disease control, all of which are key to resilient supply chains and long-term business viability.
As a result, procurement professionals are being called upon to integrate biodiversity considerations into their sourcing strategies. This goes beyond identifying environmental risks within supply chains; it requires assessing what suppliers are doing to invest in biodiversity protection. Emerging biodiversity credit markets are providing mechanisms for organizations to “unitize” and invest in the
restoration of natural ecosystems, creating new ways to track and support biodiversity initiatives. In Canada, it has been backed up by passing Bill S-5 which grants rights to the natural environment and the introduction of the first science-based targets for nature by the Science Based Targets Network.
As the push for net-zero accelerates, measuring Scope 3 emissions – often comprising up to 90 per cent of a company’s carbon footprint –is emerging as one of the largest problems in sustainability. Scope 3 encompasses all indirect emissions across a company’s value chain, from purchased goods and services, among several other variables. Tackling them is complex, but essential, as more organizations recognize the need to track and reduce Scope 3 to meet climate goals. Tools like Sphera, EcoVadis, Kloopify, and South Pole are increasingly used to gather supplier and product carbon data, driving transparency and improved reporting.
In Canada, new regulations are reinforcing this shift. The Federal Standard on the Disclosure of GHG Emissions and Setting of Reduction Targets mandates that suppliers in large
federal procurements measure, disclose, and set science-based targets through initiatives like the Carbon Disclosure Project (CDP) and Canada’s Net-Zero Challenge. Public Services and Procurement Canada (PSPC) has incorporated these requirements into procurement policies, signaling a broader move toward transparency and accountability. As global procurement practices evolve, both suppliers and procurement professionals need to prepare for better management of Scope 3 disclosure
The global crisis of forced labour has reached alarming levels, with over 50 million people impacted worldwide. In response, Canada introduced the Fighting Against Forced Labour and Child Labour in Supply Chains Act, which took effect on January 1, 2024. This legislation requires certain organizations to submit annual reports detailing their efforts to mitigate forced and child labour risks in their supply chains. The act applies to entities doing business in Canada that meet specific thresholds for assets, revenue, and employees. This legislation marks a significant step in enhancing supply chain transparency, following similar moves by countries like Australia and the UK. The act’s introduction has sparked a renewed focus on human rights in procurement, an area that has often taken a backseat to environmental and social concerns. Buying institutions are now revising their supplier codes of conduct, integrating human rights criteria into RFPs, and establishing due diligence processes to align with these new regulations. As these requirements take effect, procurement professionals must ensure that their practices not only meet legal obligations but also reflect evolving ethical standards, reinforcing Canada’s commitment to combating modern slavery in supply chains.
While much attention is given to climate mitigation and achieving net-zero goals, the need for climate adaptation – protecting communities from the impacts of climate change that are already happening – is becoming increasingly urgent. With rising temperatures, drier summers, and more frequent extreme weather events, resilient infrastructure is critical. Unfortunately, UNEP’s 2023 Climate Adaptation Gap Report reveals that progress is lagging when it should be accelerating. Urban areas, particularly vulnerable to the urban heat island effect, are especially at risk, yet many of Canada’s cities remain unprepared for rising temperatures and increased weather extremes. Organizations are beginning to shift their focus towards climate resilience, retrofitting
“AI adoption offers significant benefits for procurement but also brings challenges, including data privacy concerns.”
existing assets, and incorporating climateready features into new projects. Leading by example, Ontario Northland is enhancing building insulation, UBC is integrating rainwater management and thermal comfort features into its buildings, and the District of Saanich has upgraded a recreation centre with a heat pump conversion that both cuts emissions and improves cooling. These projects demonstrate the importance of prioritizing climate-resilient infrastructure now to safeguard communities, avoid escalating future costs, and protect lives as climate impacts intensify
Generative AI is poised to be a transformative force in the digital age, but procurement and sustainability professionals are still exploring its full potential. From automating RFP creation and enhancing supplier evaluation to streamlining contract management, AI offers vast opportunities for embedding sustainability across procurement processes. Tools like Tealbook, EcoVadis, Supplier.io and FRDM are already
utilizing AI to improve data access, enhance traceability, and deliver better sustainability metrics and reporting. AI’s ability to synthesize large datasets and provide real-time, data-driven insights is especially valuable for sustainability assessments, helping organizations tackle complex supply chain issues such as modern slavery and enabling circular economies by tracking and closing material loops.
AI adoption offers significant benefits for procurement but also brings challenges, including data privacy concerns, misinformation risks, and the high environmental impact of data centres due to their water and energy use. To harness AI effectively, procurement teams must prioritize ethical standards and sustainability while driving innovation.
These trends underscore that sustainable procurement is not just a compliance exercise— it’s a proactive approach to securing long-term value for communities, ecosystems, and economies. All organizations must continue embracing these trends to lead the way toward a more resilient and equitable future. SP
In March 2024, the Bank of Canada sounded the alarm on Canada’s productivity and declared that it is time to act and “break the glass” to correct it. Since then, there has been no effort wasted by service providers to capitalize on this proclamation to fuel new technology adoption and AI integration initiatives, all of which claim to be the answer, or conversely, claim that a failure to adopt any innovative technology is the root cause. But to accept this rather low-resolution view of a far more complex problem is careless. Our challenges predate modern digitalization and AI by decades, and the core issues remain unaddressed still today.
It seems prudent then, to examine where we have been already before proclaiming where we need to go.
Productivity in Canadian manufacturing peaked in 1997, but by 2010, the number of medium-sized manufacturers in Canada (firms with 100-499 employees) fell by 51 per cent. At the same time, our imports from China increased by 456 per cent. Today, 94 per cent of our manufacturing firms are in the small category (less than 100 employees) and the medium category continues to shrink.
In this same period, we had two financial crises (the 2001 recession and the 2008 collapse). The Canadian dollar reached parity with the US Dollar, effectively eliminating exchange-based profit margins in exporting companies. And the rise of the internet meant that Canadian manufacturing was thrust into a rapidly changing global market, demanding new approaches to competition and innovation. These stresses drove a cost focus (instead of a focus on value), and our manufacturing sector resorted to chasing the lowest input/unit costs, trying to cut their way to prosperity. The result was predictable: lost economic potential and diminished competitive advantage on the global stage, from which we have never recovered.
I witnessed firsthand how these challenges made managing supply chains and operations increasingly complex. A key issue was a lack of executive focus on strategic supply chain management and value creation. Instead, a tactical focus on siloed departmental management and short-term solutions and metrics dominated conventional management thinking. To be fair, many firms were simply unprepared for the rapid changes. However, nearly 30 years on, not much has changed. Wouldn’t it make sense then that AI and digitalization could counter this? Unfortunately, no. Effective strategies must pre-
“We need a mindset shift away from a transactional focus in supply chains and operations, to a whole-system value (or investment) mindset.”
cede efficiency; otherwise, these tools will only increase costs and accelerate failures. In my 24 years in supply chain, I have witnessed more technology adoption projects than I can count. Nearly all of them failed to realize what they promised, and our decline in national productivity continues to accelerate. I am now seeing small and medium firms in our tech sector, who lead the way in embracing technology, begin to struggle with their own productivity challenges. And for many (but not all) of the same reasons that our manufacturing has for almost 30 years.
Here in Canada, we are obsessed with messages about efficiency, but we will not make the investment to become effective first. We need a shift in mindset away from a transactional focus in supply chains and operations, to a wholesystem value (or investment) mindset. And we need to play the long game as a higher priority over shortterm returns. Particularly in manufacturing, a speculative approach (betting on the outcomes without understanding and investing in the workto get there) is deadly and equal to a business strategy based solely on hope and luck.
When I look at our American manufacturing counterparts, it seems that they often prioritize reinvestment in their operations more than
Canadian firms do, and there is plenty of data out there to support this view. They emphasize long-term resilience and realized productivity-based funding/investing. There is a stronger educational focus on executional knowledge in manufacturing, and strategic system thinking. They also have a much larger appetite for strategic risk taking and investment oriented toward growth. Additionally, they understand supply chains as strategic assets for competitive advantage, and value generators rather than cost centres. Of course, they do have a huge domestic market, but here in Canada we overlook our own domestic markets in favour of nearly exclusive northsouth trade.
For Canadian manufacturers, the path to improved productivity begins with the C-suite’s transformation of how it envisions manufacturing and operational strategy, supported by this-century education on supply chain strategies and active networking among peers to leverage experience-based insights to tackle shared challenges.
The time for superficial fixes is over; it’s time for a fundamental change in how Canadian manufacturing approaches productivity. It’s 1997 all over again. AI and globalization breakdowns are driving the next leap. Canadian manufacturing must finally address core issues urgently before we’re left behind. SP
By Kate Vigneau
Technology and innovation in fleet management is no longer a choice but a necessity. Whiteboards and excel spreadsheets have been replaced by technological tools that are the very heart of effective fleet management. Telematics, artificial intelligence (AI), emissions tracking systems, and driver safety monitoring can address common fleet challenges. Leveraging technology can overcome these issues and enhance performance.
Which functionalities to pursue? If the goal is to enhance efficiency while safeguarding drivers and the environment, these four technologies are worth exploring.
Fleet information management system (FIMS): A fit-for-purpose FIMS goes beyond maintaining the fleet inventory and scheduling the preventive maintenance (PM) program. It’s now the heart of an effective fleet program, facilitating workflows, tracking fleet costs, and generating the fleet replacement plan. Other technological systems feed the FMIS which acts as the repository of everything fleet.
Telematics: These systems provide real-time data on vehicle location, speed, fuel usage, and driving behaviour. This information can be linked to the FMIS to make a wide range of fleet decisions, which could involve optimizing routes, instituting driver training programs, or identifying vehicles for electric conversion.
Artificial intelligence: AI can magnify our ability to process vast amounts of data and quickly identify trends or issues. Corrective solutions can then be put in place to reduce downtime or improve drive safety.
Advanced driver assistance systems (ADAS): Vehicles increasingly have systems that keep drivers safe on the road. ADAS technologies include collision avoidance, lane departure warnings, and even automated braking. While not widely used, autonomous vehicles may take even more guesswork out of driving.
Investment in these technologies can be significant but their worth can be justified in resolving some of the most common fleet challenges.
The first are the rapidly increasing costs of operating a fleet. Maintenance and fuel costs have spiked following a COVID-19 hiatus and many organizations are struggling to deal with skyrocketing operating budgets. Technology can assist by entering and tracking costs in the FMIS and analyzing the data using AI to identify trends. Sometimes a drastic increase in fuel costs can indicate driver fraud or a mechanical issue with a vehicle. Using technology can provide answers. Fleet managers often face an aging fleet with decreased availability. Repair times may be elevated, and adequate vehicles are not on hand to support operations. Technology can assist in resolving this issue in a number of ways. A FMIS can
automate processes to make maintenance shops operate more efficiently. The system can also track repair times which can pinpoint issues with technician productivity necessitating additional training. AI can help with using predictive analytics to prevent maintenance failures. This combination of technology can increase vehicle availability.
Finally, as fleets must meet emissions reduction targets, many managers don’t know where to start. Technology can track the number of hours, distance travelled, and hours spent in their dwelling by fleet vehicles. This information will show which units are suitable for conversion to an alternative fuel, particularly elec-
trification. Location data can also help to establish where charging infrastructure should be installed.
As the pace of technological innovation increases, fleet managers will be challenged to keep pace. Below are a few strategies to help.
Form local interest groups with like organizations. Don’t go it alone. Learn from peers what technology helps with challenges. In a recent project, the Janesville Area Metropolitan Planning Organization (JAMPO) in Wisconsin did a study with six agencies to explore options for fleet electrification.
A fit-for-purpose FIMS goes beyond maintaining the fleet inventory and scheduling the preventive maintenance program.
Join industry associations –NAFA, the Fleet Management Association, and AFLA, the Automotive Fleet and Leasing Association, offer information on emerging technologies at their annual events. They often offer virtual classes that are free to members.
Consult with technology providers. System manufacturers will be willing to answer your questions. They all offer product demonstrations and will assist with pilot programs (in the case of telematics) to ascertain if the product is a good fit for your organization.
Keeping pace with technology is the best way that fleet managers can ensure their fleet is operating efficiently and supporting operations. This can take time, but leveraging your peers, industry associations and manufacturers will help. FM/SP
You
On-board
By Stephanie Wallcraft
There plenty of Toyota compacts we could recommend, but we’re highlighting the Toyota Corolla here because it’s got so much going for it. Not only is the Corolla Hybrid sedan one of the most fuel-efficient models on the Canadian market—it achieves 4.7L/100km combined with frontwheel drive (FWD)—but the Corolla Hybrid is also available with AWD, which brings fuel consumption to a still-reasonable 5.3L/100km combined. Every Corolla regardless of powertrain comes with the Toyota Safety Sense 3.0 suite of safety and driver assistance technologies. With a starting price of $26,385 for the base Corolla L gas and $31,185 for the Corolla Hybrid AWD LE, this compact car is one of the most outright frugal vehicles sold in Canada today.
Some will argue the best Mazda compact is the classic CX-5 SUV. Others will try to steer you toward the new CX-50. We say take a look at the the Mazda3 compact car. It comes in two body styles, sedan, or hatchback, and offers available AWD plus two different engine options, a naturally aspirated version
and a turbo. You can even still get the Mazda3 with a manual transmission. (Note, though, that while these features are offered in various combinations, you can’t package all of them together.) Expect near-luxury quality at a non-luxury price at upper trims, but know you’ll trade it for fuel economy with estimates ranging from 7.5 to 8.9L/100km combined. Pricing for the 2025 Mazda3 starts at $28,281.
Compact vehicles are the most popular non-pickup segment in Canada, so it logically follows that they’re the workhorses of Canadian fleets. These days, “compact” encompasses much more than it used to: cars, SUVs, and even a couple of unibody trucks are available in this diminutive class. Here, we take a closer look at eight compact vehicles we think Canadian fleet managers should consider, whether it be for fuel efficiency, functionality, affordability or otherwise.
Note these are all true compacts. We’ll save the subcompact class –which includes even smaller cars and crossovers like the Nissan Versa and Honda HR-V – for a future roundup.
Canada is one of the top sales markets per capita for Mercedes-Benz’s high-performance AMG line-up. Key among those is the AMG GLC 43 with 416hp and 369lbs-ft of torque from its hybrid-assisted 2.0-litre four-cylinder engine while burning 12.6L/100km in the city and 9.4 on the highway. Opt for the tamer GLC 300 and you’ll receive 255hp and 295lbs-ft of torque, which is still plenty impressive. We’re still awaiting news on the electrified GLC 63 S E Performance, which should be on the way for 2025 or soon afterward. For now, pricing on the Mercedes-Benz GLC starts from $58,900 before fees for the GLC 300 and $79,900 for the AMG GLC 43.
Until two years ago, the Honda Civic was the best-selling car in Canada for nearly a quarter of a century. Unfortunately, it lost that title to the Toyota Corolla just a year shy of the mark amid supply constraints. No matter: the Civic remains enormously popular, not the least of the reasons being it’s built right here in Canada. For 2025, the all-new Honda Civic Hybrid launches in two trims, Sport Hybrid and Sport Touring Hybrid. Each comes with a 2.0-litre four-cylinder engine combined with a twin-motor hybrid system, expected to deliver fuel economy of 4.8L/100km combined. Pricing on the 2025 Honda Civic starts at $29,506 for the gas-only LX, while the 2025 Honda Civic Hybrid starts at $35,262.
For 2025, an important mid-cycle refresh makes the Ford Maverick compact truck better than ever. Previously, buyers could choose a fuel-efficient hybrid powertrain or all-wheel drive, but not both. Now, these features are offered together with an estimated 5.9L/100km fuel consumption rating and available towing capacity of 4,000lbs. A new 13.2-inch infotainment screen
running SYNC 4 is another highlight. Pricing hasn’t yet been announced, but we expect it to be reasonable for what it offers. For fleet buyers who need pick-up truck functionality in a compact and fuel-efficient package, we expect this to be an ideal combination.
The Chevrolet Equinox enters a new generation for 2025 with bold new styling, updated features, and a fresh trim line-up. Inside, the fully redesigned cabin is highlighted by a single-pane dashboard housing an 11-inch digital instrument cluster and 11.3-inch infotainment system with wireless Apple CarPlay and Android Auto. AWD is optional on the base LT trim and standard on the redesigned
If you’re looking for the best outright fuel economy in a compact SUV without any sort of electrification, check out the Nissan Rogue. Its standard 1.5-litre three-cylinder engine with standard all-wheel drive averages 7.6L/100km combined, which is the best rating in the compact SUV class before you get to the hybrids. The Rogue also includes standard driver assistance technologies that aren’t offered at base price by some of its competitors such as blind spot monitoring and rear cross-traffic alert. The 2024 Nissan Rogue also has standard AWD and starts at $36,435, fees in.
Subaru’s rugged compact SUV enters its sixth generation for the 2025 model year, bringing a beefier design, a new 11.6-inch infotainment screen with wireless Apple CarPlay and Android Auto, and a newlyavailable wireless charging pad. The 2025 Forester also includes improved safety technology such as the latest Subaru EyeSight system with a new wide-angle mono camera lens, which is standard on all trims, and a Subaru-first emergency stop assist feature that will bring the vehicle to a halt out of harm’s way if the driver becomes unresponsive. This is on top of the brand’s standard all-wheel drive (AWD). Pricing for the Convenience trim starts at $36,174, fees in.
RS – which has a reconfigured suspension and optional 20-inch wheels – and the all-new outdoorsy Activ trim. There’s also an Equinox EV, though it shares nothing in common with its gas-powered sibling. Pricing for the 2025 Chevrolet Equinox starts in Canada at $35,433.
By Katerina Jones
Earlier this year, fast-food chain Wendy’s got backlash over its use of surge pricing on menu items. Part of the ensuing conversation centered around distinguishing between surge pricing and dynamic pricing. It is important to know that the two are different. In fact, dynamic pricing isn’t just about raising prices when demand exceeds supply. That’s surge pricing. Dynamic pricing also includes lowering prices, both when demand declines and during supply surplus. Dynamic pricing responds to the ebbs and flows of the free market.
Wendy’s new pricing strategies weren’t all that new and, for years, many industries have experienced strategies like dynamic pricing. Businesses that procure heavyduty trucks such as private fleets, for-hire trucking companies and other vendors, have placed purchase orders for trucks for many years with prices based on many economic factors that contribute to “dynamic” prices.
Technology algorithms today make it easier for fleets to understand pricing fluctuations in real time. The key is knowing that not all algorithms are built alike, so companies must understand if they
are leveraging accurate, real-time data for procurement decisions.
Many fleets leverage data for their operations, helping to better understand and manage the operations of their vehicles with more efficiency. Finance and analytics departments are also leveraging data to monitor and assess the optimal time to replace an aging truck.
Today’s real-time sophisticated data, which includes the use of price-setting, can also leverage artificial intelligence and predictive modelling algorithms to analyze large amounts of data and make pricing decisions based on analysis. This type of pricing uses datadriven insights and predictive analytics to determine the price for a heavy-duty truck by the manufacturers, based on economic and industry-driven factors. Independent truck lessors also base their lease payment calculations on costs set by the manufacturer and must also leverage algorithms to account for these varying price fluctuations.
The heavy-duty truck industry has used dynamic pricing for years. Everything from geopolitical tensions affecting the supply of parts
and commodity prices to regulatory changes shaping emission standards have contributed to price adjustments. Traditionally, fixed pricing models struggled to account for these fluctuations effectively. However, dynamic pricing emerged over the years to help OEMs adjust for changing market dynamics, further exacerbated by the rapidly changing supply during the pandemic and the post- COVID-19 era.
A driver of dynamic pricing’s adoption is its ability to capture the true value of heavy-duty trucks in real-time. Unlike static pricing models that rely on historical data and gut instincts, dynamic pricing leverages real-time data including market trends, competitor pricing, raw materials prices and availability, macro-economic trends, and customer behaviour. This approach lets manufacturers set prices dynamically, reflecting changing market conditions accurately. Dynamic pricing empowers manufacturers to respond to supply and demand shifts, like economic expansions or seasonal peaks. During downturns or when facing surplus inventory, prices can be lowered to stimulate demand and clear excess stock.
Truck remarketing has also benefitted from dynamic pricing. The collection and analysis of data and algorithms have become central to optimizing used truck remarketing. Understanding market trends and residual values, buyer behaviour, and past price/demand performance metrics lets sellers adjust their strategy. Advanced data algorithms are used to recognize specific truck characteristics (brand, model, condition, equipment). These algorithms can be invaluable in estimating refurbishment costs, secondary finance options, and truck trade-in values, based on historical data and local market trends.
Heavy duty fleets are partnering with strategic asset management providers with an analytics technology stack, which includes fleet modernization studies, emission studies and comprehensive emission studies with analytics software, which monitors and analyzes each truck’s raw data from their ELDs. This data, along with predictive modelling algorithms, helps to understand dynamic pricing better, and to plan for the upgrade and acquisition of new equipment years down the road.
By harnessing the partnership of asset management providers that leverage the powers of data-driven insights and adaptive pricing strategies, these partners can help fleets see a holistic view of their lifecycle, so they are optimized from planning to procurement to exchange. Fleets can then navigate the future with confidence, maximizing their total cost of ownership while delivering greater value to customers regardless of the fluctuating change in equipment prices. FM/S
EMPLOYEE OF THE MONTH, EVERY MONTH.
Your company deserves committed employees, and that includes your Toyota. With our award-winning electri ed lineup, it’s clear that Toyota vehicles provide sustainable success year after year.
By Howard J Elmer
Ram is the latest brand to bring electrification to its utility van offerings with a new ProMaster – all electric – for 2025. I recently drove one at a demonstration in Michigan. It was everything I expected. Quiet, quick, and simple. In fact, electric service and delivery vehicles are an improvement in this segment that can’t come fast enough. Because delivery vans run set routes, or work in stop-andgo, short-range urban service areas, the drawbacks of electric power are few. These trucks will work all day and recharge overnight. Their usage cases have fewer charging variables than electric passenger vehicles. Also, from a business perspective, over time they will cost less to run, cost less to service, and last longer.
Arriving in Canada late this year are two EV models. The ProMaster EV delivery model and the Cargo model. The Cargo model is available as a 12-foot box or an extended 13-foot box. Both versions come with a 110-kilwatt-hour (kWh) battery pack that has a targeted range of 261km in city driving. Most owners will be using a Level 2 wall changer (which delivers up to 11kw), however the ProMaster will also accept a Level 3 DC fast charger that delivers up to 50kw. The charge port illuminates while the vehicle is charging and has an audible sound alert to confirm the connection.
This ProMaster architecture has been designed specifically for electrification, featuring a unibody
design that incorporates the battery pack. The battery is positioned under the floor in the centre of the vehicle, maintaining a flat floor while cargo volume is unchanged from the gas-powered vehicles.
The battery pack drives a 200kw electric drive module (EDM) which delivers 268hp and 302lbs-ft of torque using the standard frontwheel-drive capability.
All versions have a 159-inch wheelbase, and an extended superhigh-roof. Other new driver features include an available heated steering wheel and heated windshield. New available safety and security features include Park Sense with stop, white noise backup alarm and “normal” backup alarm.
Another new feature on this ProMaster is a rear roll-up door. Built of anodized aluminum, its light weight yet durable. A passenger-side sliding pocket door is also now standard on the Ram ProMaster EV delivery vehicle. This will ease ingress and egress while making deliveries.
The handling of cargo is the number-one consideration for van buyers. The ProMaster EV includes best-in-class features, such as 524 cubic feet of cargo space, standard best-in-class interior cargo height of 86 inches, a low load-floor height and max width between wheel wells. The cargo van features up to 1,370kg (3,020lbs) of payload while the
1. The ProMaster EV includes features like 524 cubic feet of cargo space, a standard interior cargo height of 86 inches, a low load-floor height, and max width between wheel wells.
2. The battery pack drives a 200kw electric drive module (EDM) which delivers 268hp and 302lbs-ft of torque using the standard frontwheel-drive capability.
delivery configuration offers up to 921kg (2,030lbs) of payload. Ram Commercial is well known for providing upfitter-friendly offerings. The new Ram ProMaster EV continues this tradition. It has standard upfitter electrical connector and an integrated cab configuration for easy upfitter/conversion solutions. Adding to the new ProMaster design for adaptability, virtually all primary vehicle systems are packaged forward of the cargo area. This body can be upfitted for virtually every conceivable commercial need because of its unique frontdrive system and body-integral construction. It has the most vertically oriented sidewalls in the cargo van category (nearly 90 degrees in rela-
tion to the cargo floor) combined with a best-in-class cargo width of 75.6 inches.
Two key considerations for prospective van buyers are visibility (this means, glass, mirrors, and cameras) and safety systems (both for the driver and pedestrians). Both of these important features have been addressed in the ProMaster EV. For instance, ProMaster features a standard high-resolution backup camera with dynamic grid lines. The available digital rearview mirror displays video in real time in all driving modes from a rear-facing camera and can be turned off to revert to a traditional reflective mir-
ror. The digital rearview mirror is available on all ProMaster models and gives an unobstructed rear view. Also available on the Ram ProMaster is 360-degree Surround View camera. The system offers 360-degree, bird’s-eye views of the vehicle and surroundings, enhanced by dynamic grid lines displayed on a 10.1-inch digital touchscreen.
For 2025, the safety and security list continues to grow and offers features like full-speed Forward collision warning, crosswind assist, rear backup camera with dynamic gridlines, and more. Optional safety and security features include intelligent speed assist, lane keep assist, and adaptive cruise control with stop & go, among others. Ram
Ram ProMaster will also feature secure park, a feature that prevents the vehicle from being shifted out of “park” unless a key is present.
ProMaster will also feature secure park, a feature preventing the vehicle from being shifted out of “park” unless a key is present.
Also of note that there is progression towards autonomous driving. ProMaster has an active driving assist feature that provides Level 2 (L2) automated driving capability. This consists of hands-on-wheel and eyes-on-road automated driving using lane centring with adaptive cruise control. The system uses multiple sensors, including radars and cameras to dictate appropriate roads for the technology.
The 2025 Ram ProMaster EV is available for order now and should be on Canadian dealer lots late this year. FM/SP
This article surveys a broad range of collusive contracting practices that lead to tainted contract awards and calls on Canadian public institutions to adopt proactive oversight measures to detect and deter these illegal and unethical practices.
Bidding-rigging is a quasi-criminal offence under the federal Competition Act. The offence includes bid suppression schemes where bidders avoid direct competition by preselecting a sole bidder who wins an award at an inflated price, as well as price collusion schemes where an inflated low bid is covered up by other bidders who submit higher dummy bids. While bid rigging remains a well-documented problem, resulting in large fines and long prison terms, it is far from the only collusive contracting practice undermining the integrity of public sector contract awards.
Influence peddling, where individuals seek payments in exchange for influencing government contracting decisions, and kickback schemes where contractors bribe accomplices in public institutions to influence contract award decisions, are two criminal offences that also involve collusive contracting practices. As recent rulings reveal, the destruction of government contracting records to cover up improper contract decisions can also, among other things, constitute a criminal offence, as can other fraudulent practices relating to false invoicing or expense claims.
Lobbying activities directed at senior decision-makers can also compromise the integrity of a procurement process, particularly when the lobbying is aimed at improperly
influencing an award decision.
While single-point-of-contract protocols prohibit bidders from communicating with anyone within the public institution other than the officially designed contact person, those institutions need to be vigilant in enforcing these rules to prevent unlawful awards.
Unsolicited proposals, where suppliers pitch a contracting opportunity to a public institution to win a sole-source award that circumvents open tendering rules, and third-party funding schemes that are tied to pre-approved suppliers who never competed for the work, are other murky zones for potentially collusive conduct.
Conflict of interest can also undermine the validity of a contract award. For example, conflicts can taint an award when a government official’s personal interests conflict with the duty to exercise independent judgment in a contract award decision. In fact, Canada’s ethics commissioner has rendered multiple adverse rulings in recent years due to the improper involvement of conflicted cabinet ministers in contract award decisions. In recent years bid protest rulings and public audits have also found multiple unfair advantage situations where contract specifications or bid award criteria were manipulated by the government’s technical advisors to create an unfair bidding advantage for certain suppliers. In fact, unfair advantage is particularly entrenched when incumbent suppliers benefit from biased requirements, unfair informational advantages, or compressed bidding timelines that create an improper advantage over outside bidders.
Recent high-profile audits have also exposed patterns of preferential treatment in the award of multiple sole-source contracts to the same suppliers. These awards are often concealed by contract splitting, through which internal accomplices in public institutions divide contracts into smaller awards or underestimate cost estimates to circumvent open tendering duties. Once these tainted incumbencies are established, they can be leveraged in subsequent sham bidding processes to further entrench the incumbents. While often motivated by expediency and enabled by weak oversight, multiple global case studies show that these preferential patterns are often accompanied by kickback bribes paid by suppliers to their internal accomplices.
Given the above, when solesource awards are made without a well-documented record to support the reason for bypassing a bidding process, those awards should be scrutinized for potential collusion. In fact, domestic and international trade treaty rules include a series of long-recognized anti-avoidance measures that serve as further red flags for potentially collusive practices, including the improper use of false fronting arrangements and third-party purchasing agents to circumvent public tendering duties.
Weak contract administration serves as another telltale sign of potential collusion. When multiple sole-source contracts are awarded to the same supplier and contain
Paul Emanuelli is the general counsel of The Procurement Office and can be reached at paul.emanuelli@ procurementoffice. com.
“Conflicts can taint an award when a government official’s personal interests conflict with the duty to exercise independent judgment.”
vague specifications and weak payment oversight mechanisms, the obvious question is whether these awards were merely the product of administrative incompetence or whether they are evidence of internal collusion.
Flawed public reports are another telltale sign of potentially collusive conduct. When a public institution releases inaccurate or misleading information regarding contract award details that conveniently obscures a pattern of improper sole-sourcing to the same supplier, that cluster of sole-source awards should be investigated for potential collusion.
Given the widespread and well-documented risk of collusive contracting practices, public institutions need to establish proper oversight measures, supported by proper awareness training, to avoid becoming the next collusion case study. SP
Discover the next step in your automation journey
Automation that’s rooted in strategy—the right technology at the right time for the right application—boosts team productivity, engagement and satisfaction. And that’s good for business. No matter what stage you’re in, GNJ Automation brings years of intralogistics expertise to help evolve your systems and empower your people.
READY TO AUTOMATE, INTEGRATE AND INSPIRE?
Connect with a member of our team and let’s start the conversation.
Build smart. Stay agile. Now is the time to take a broader look at your overall intralogistics strategy and optimize. Making adjustments to combat today’s challenges will prepare you for a strong and sustainable future. And we can help.
Together, we’ll analyze the strategy and systems you’ve built to move, manage, store and protect goods and bring forward new ideas to enhance or secure the investments you’ve already made. Let’s get started.