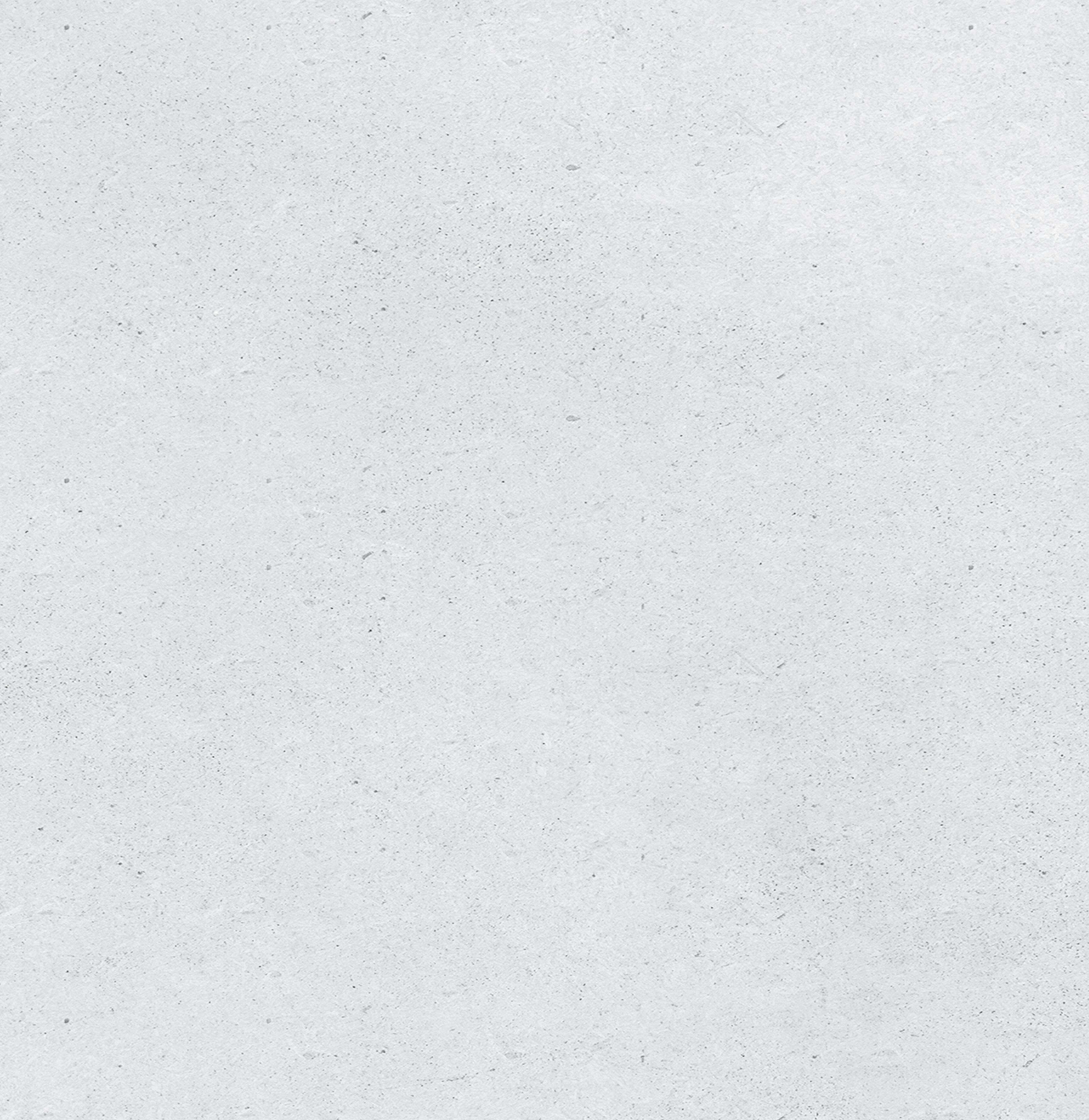
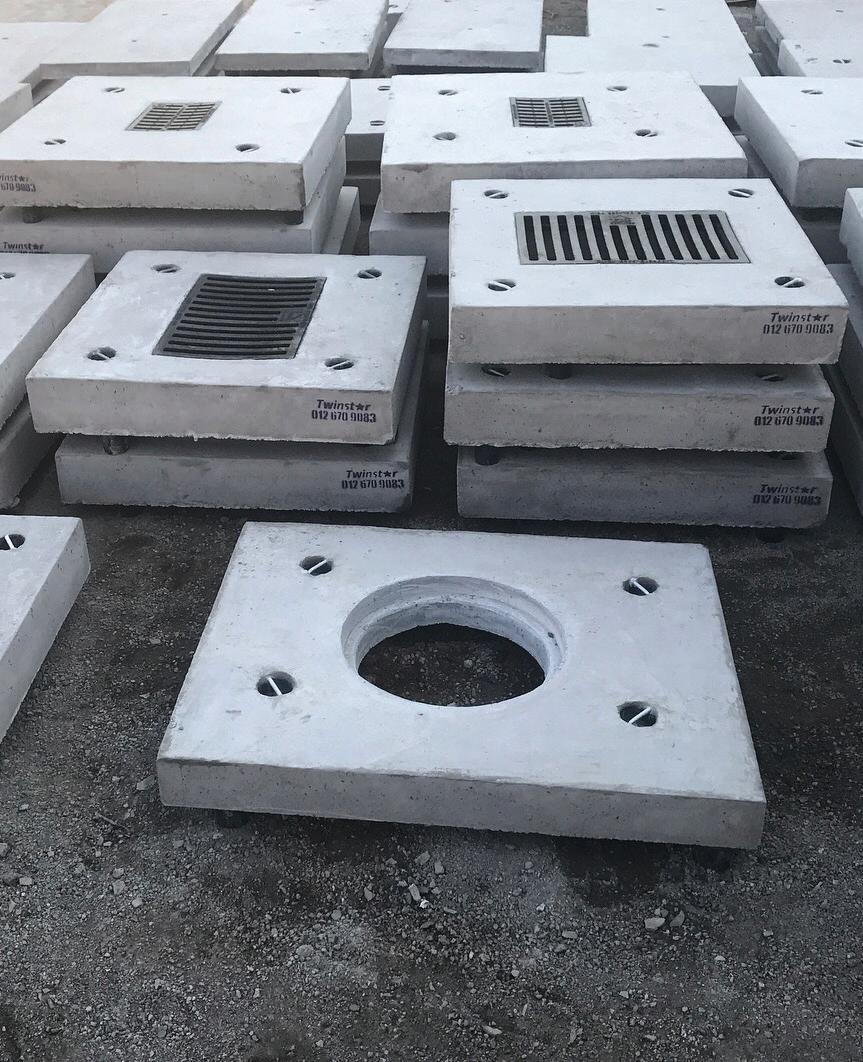

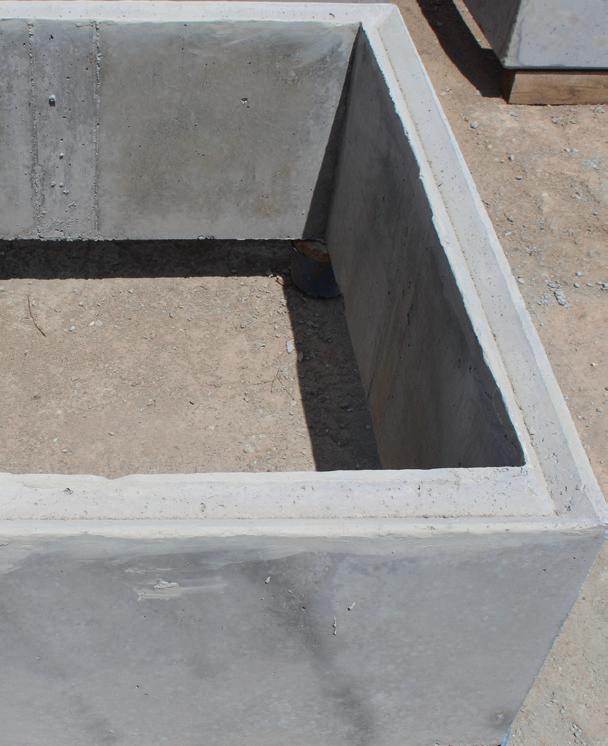
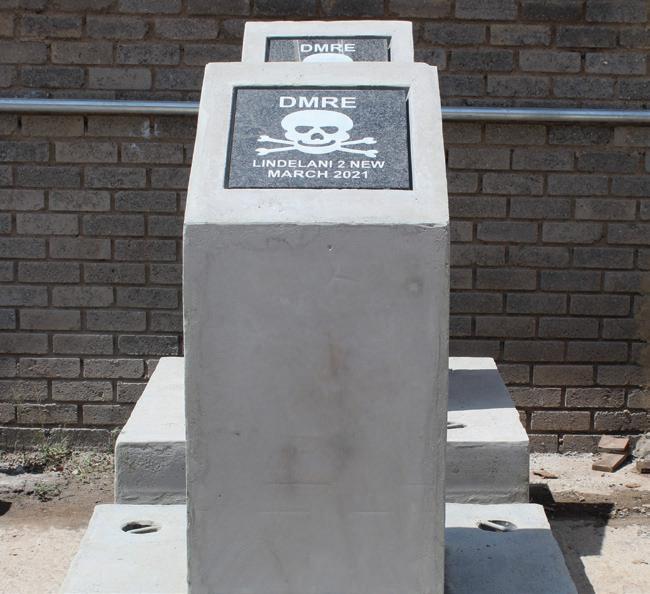
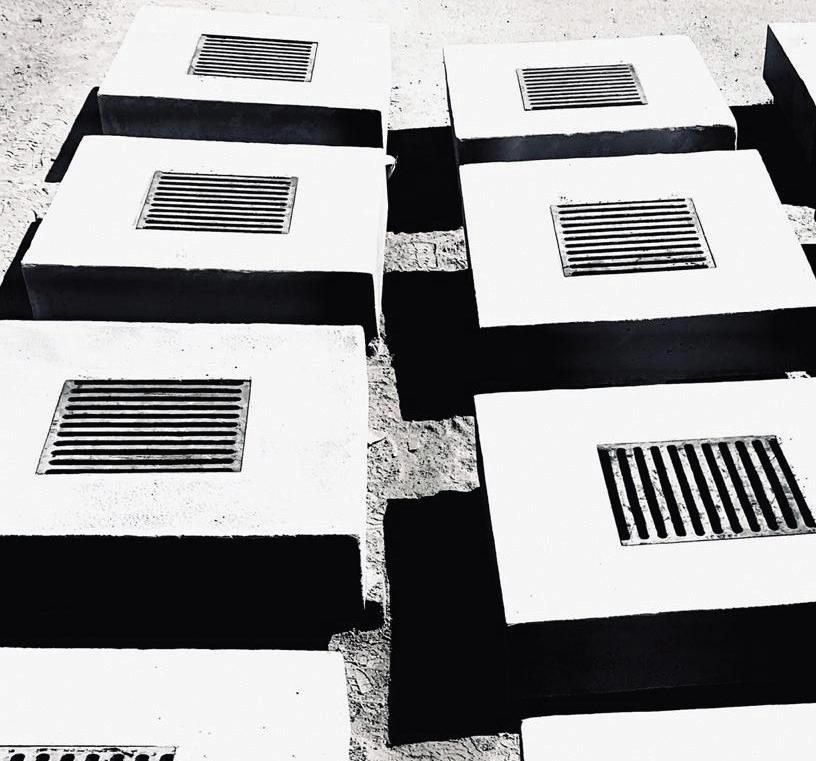
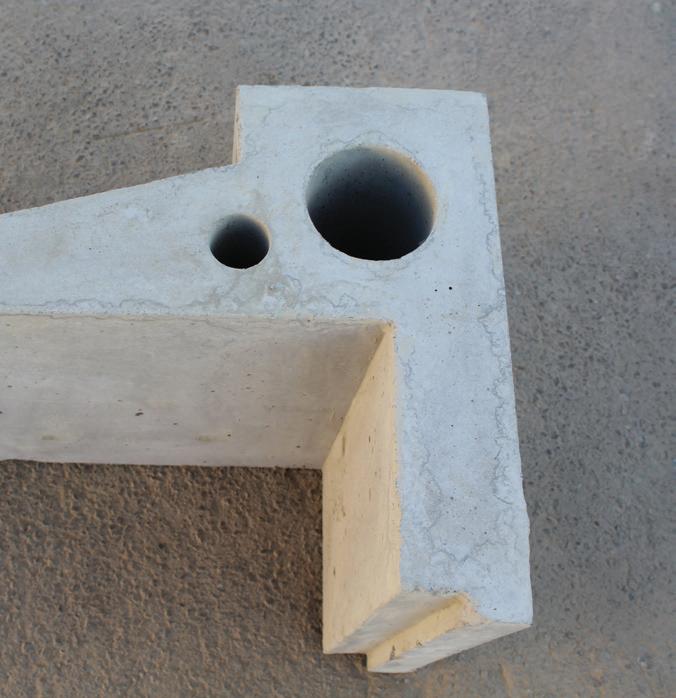
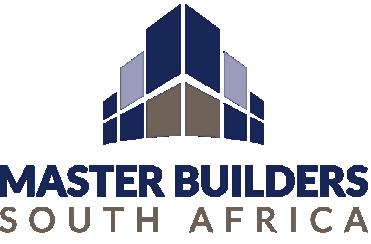
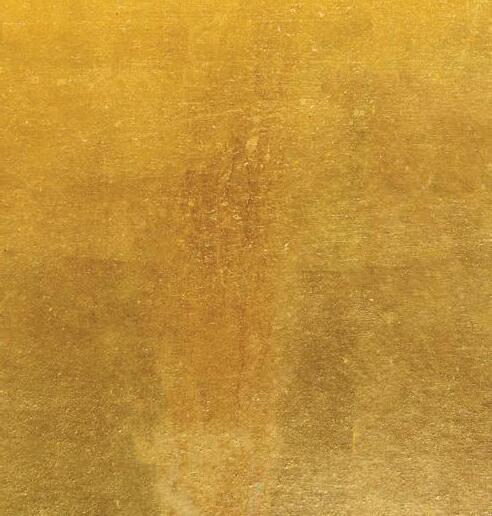

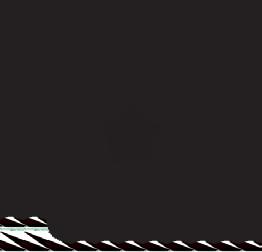
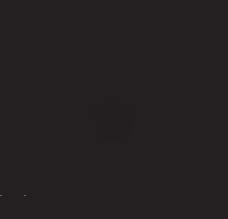
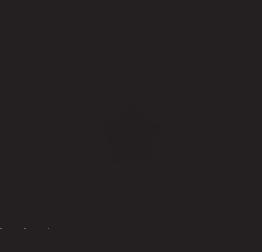
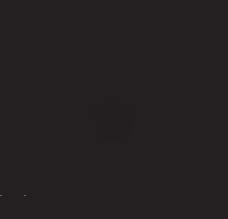
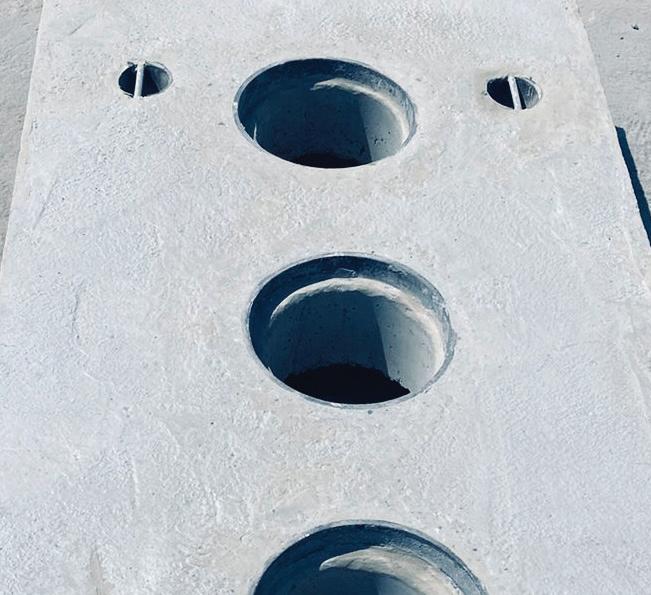
WE ADD MUCH MORE
WE ADD MUCH MORE
Our specialists are standing by to assist you with design, specifications, detailed drawings, and certifications
We’ll also do a rational design to help your plans comply with Sans 10400 XA. Our after-sales service extends to on-site, trade and technical assistance, from placing the order – to installation.
South African Builder is the official journal of Master Builders South Africa, established in 1923. The opinions expressed by contributors are not necessarily those of Master Builders South Africa. SA Builder is a registered trademark of Master Builders South Africa. Any use of this trademark without the express and written approval of Master Builders South Africa is prohibited. No material contained herein may be reproduced in whole or in part without the prior written permission of the publisher. SA Builder © 2023. All rights reserved.
SKILLS AND TRAINING
26 Tech: Bridging the skills gap
BUILDING BUSINESS
32 Inside the property market: Three years after hard lockdown
FEATURE
34 Ennerdale collapse: Who is responsible for safety on landfill sites?
BUILDER'S VIEW
38 New tax incentives boost to solar in SA
PRODUCTS
42 Hansgrohe publishes environmental product declarations
GLOBAL VIEW
44 Accelerating trade in Africa through supply chain integration
CAPTAINS OF CONSTRUCTION
47 Meet Annemerie Coetzee
PUBLISHER
Isikhova Media (Pty) Ltd
10th Floor, Metal Box, 25 Owl Street, Milpark, Johannesburg, South Africa
Tel: +27 11 883 4627
www.sabuilder.co.za /www.isikhova.co.za
CONTRIBUTIONS
Master Builders South Africa
Tel: +27 11 205 9000
E-mail: editor@sabuilder.co.za
www.masterbuilders.org.za
Free download available on: www.sabuilder.co.za
Twitter: @Builders_SA | Facebook: @SouthAfricanBuilder
Editor: Nicholas McDiarmid
E-mail: nicholas@isikhova.co.za
Director: brand strategy: Jenny Justus
Tel: 083 450 6052
E-mail: jenny@isikhova.co.za
Managing director: Imraan Mahomed
E-mail: imraan@isikhova.co.za
Creative director: Joanne Brook
E-mail: joanne@isikhova.co.za
Proud Media Partner
Operations director: Thuli Majola
E-mail: thuli@isikhova.co.za
Copy editor: Anne Phillips
Advertising sales: Tel: +27 11 883 4627 Mobile: 072 383 3203/083 450 6052
savvy thinkers smart doers together people
Date: 17, 18 & 19 May 2023
Yonwaba Mfingwana
Deputy Director: Infrastructure Finance
GOVERNMENT TECHNICAL ADVISORY
CENTRE- ENTITY OF THE- NATIONAL TREASURY
Nompumelelo Nzuza
Managing Director/SACAP Board
Member
NZUZA ARCHITECTS CO-OPERATIVE
Mazande Ntshanga
Local Economic Development
Project Manager Capital Projects UnitEconomic Development & Planning
Cluster
ETHEKWINI MUNICIPALITY
Sanelisiwe Ntshanga
Town Planner
HOUSING DEVELOPMENT AGENCY
Mameetse Masemola
DDG: Infrastructure Investment Planning and Oversight
INFRASTRUCTURE SOUTH AFRICA
Buhlebethu Sithole
National Manager: Development Planning & Infrastructure Delivery (RSA) AMANDLA SOCIAL ENTERPRISES
Dr Emma Molobi
Principal Engineer (Rolling Stock Technology)
TRANSNET FREIGHT RAIL
Nonelela Xaba (Noni)
Divisional Human Resources Director SPAR SOUTH RAND
Dr Thelma Ngwenya Engineer MINTEK
INTERACTIVE WORKSHOPS
INVESTING IN MENTAL HEALTH CARE FOR WOMEN IN THE BUILT ENVIRONMENT
Senzekile Shongwe Counsellor & Mental Health FacilitatorVenue: Gallagher Estate, Midrand
Mathabo Masegela
Senior Manager Planning: Engineering
ROADS AGENCY LIMPOPO
Verosha Ganas
Specific Design Project Management (SDPM) Technology, Development & Innovation
TELKOM
Nonku Hlatshwayo
Interior Designer- Managing Director-CEO JUZETTA INTERIORS
Xoli Khoza
Lead Project Manager- KZN Region MAFANYWA MPHAGE QS AND PM
Sitha Mgezuma
Section Head: Asset Operations (Property Management)
SOUTH AFRICAN POLICE SERVICE
MONITORING AND EVALUATION
(M & E) IN THE BUILT ENVIRONMENT
Dr Peter Tobin Chief Executive Officer PETER TOBIN CONSULTANCY (PTC)
ITC is excited to announce the roll out of an out of this world experience As part of the conference delegates will participate in a half-day tour through Soweto, join us for this exciting initiative on day 2. The tour includes a visit to the following places: Mandela House, Hector Peterson Museum, Freedom Square, Drive through Orlando Towers as well as Vilakazi Street & a buffet lunch at Sakhumzi.
Optional Critical Skills Workshop
Experts will teach delegates on the different kinds of reptiles that can encountered on site or remote areas while working. You will learn how to identify the different reptiles, risk associated with them, safety handling as well as alerting the right authorities to ensure safety. This is a critical skill for Women in Built.
NETWORKING FUNCTION FOR ONSITE ATTENDEES & LIVE PERFORMANCE BY VICTOR PHILLIPS
• Discussing the current statistics and inclusion of women in the built environment, what has been done? Are we reaching the desired goals?
• Transformation through Professional Registration in the Built Environment
• Promoting the involvement of Women in Construction Welding
• Sustaining injury free workplaces through effective Health & Safety measures
• Technical Report Writing
• Exercising emotional intelligence by acting and leading in a more effective manner
• Ensuring women take a seat at the table and make a change by putting inclusivity at the center of your policy making
• Encouraging the built environment to work together to guide MFMA compliance Infrastructure Planning
• The will and ability to actively pursue change in socio economic conditions of beneficiary communities with the difficulties introduced by the prevalence of construction mafias
Media Partners:
Latest Stats SA figures reflect a reality we all anxiously anticipate every day and, like calls from unknown numbers, we do not really know how we are doing until we answer them. As I cautiously faced the unknown from Stats SA, I felt my heart sink and then rise again.
The construction industry did lose R39 billion, as contribution to GDP last year; what we felt was real. But personally, while I feared we losing the industry, we have kept up the side and contributed R107 billion to GDP.
I am not going to minimise the horrendous truth of that loss. And that truth looks like this: despite everything government did and did not do to us, we are ROBUST. And this should motivate us all.
We, as a nation, are led by a president who publicly disavows constitutional responsibility for simply
keeping the lights on. Instead of streamlining the resurrection of our electricity sector, he appears to have brought more noses to the trough of Eskom's self-enrichment programme. We will see what this really means over time.
Yet we South Africans are doing what I have always seen us do. We are finding, making and creating opportunity for ourselves and for each other. This is bringing cohesion to our national character which we have never seen before. If you do not know what I am talking about, just bring up our collective concerns to those with whom you might not naturally fall into discussion. We share a national vision and our attitudes are healthily homogenous.
If government does not change now, it will feel the wrath of South Africans at polling stations in next year's general election.
Nicholas McDiarmid, Editor: SA BuilderPresident Cyril Ramaphosa is commended for acting against extortion rackets – identified as responsible for derailing multibillion rands’ worth of infrastructure in construction projects. Requiring specialised units drawn from the police and the National Prosecuting Authority to tackle “crimes of economic disruption”, the problems wrought by the “Construction Mafia” are now a national priority.
Many of these criminal groups originated from business forums and began abusing the 30% subcontracting requirements provided for in the 2017 Preferential Procurement Regulations. It is alleged that they are now demanding 30% of the value of each public-sector contract awarded, in cash. Failing this, they threaten contractors, or interrupt or stop projects entirely.
In August 2018, National Treasury declared such practices not only illegal, but defeating the aims of economic transformation. Section 217 of the country’s Constitution stipulates that when an organ of state in national, provincial or local government procures goods and services, it must do so in accordance with a system that is fair, equitable, transparent, competitive and cost-effective.
National Treasury also called on provincial treasuries to ensure that organs of state in provincial and local government abide by the Preferential Procurement Regulations and report any interruptions to public projects to law enforcement agencies.
MBSA looks forward to seeing this action being implemented by organs of state when our members are attacked. Enough is enough!
Musa Shangase, President: MBSA
Custom-built precast concrete products are essential construction components: the perfectlysized plinth, the architecturally perfect, but awkwardly-shaped side wall, the perimeter kerbs of a hospital helipad... Twinstar’s reputation as a master of bespoke precast manufacturing is spoken of with unusual frequency, as is its reputation for standardised bulk products: manhole covers, stormwater grates, transformer boxes and more.
Twinstar Precast was established with the express aim of assisting civil engineers and civil
engineering contractors with complex structural challenges by delivering – even to the most complex specifications – the precast solutions they needed badly, but which had so often evaded them.
The opportunity – the “gap in the market” – exists, as there will always be a demand for custom precast products. Success in custom manufacturing is itself custom-made.
“Our commitment to solving our clients’ specific needs requires our very personal involvement at all stages of the process,” explains director and founder Annemerie Coetzee.
“We prize listening above all else. It precedes and guides all other skills, and is continuously developed and built upon Twinstar’s collective experience and my own particular commitment to every one of our clients.
“Listening accurately entails drawing on my technical knowledge and experience as a precast concrete manufacturer and construction design problemsolver, as well as my keen awareness of the myriad concerns clients may face,” says Coetzee. “It’s about much more than just basic listening. Really listening makes the impossible possible.”
The effort and time required to
design and build once-off moulds for bespoke products can only be fully appreciated through hardwon experience.
The artisans, procurement and logistics specialists, machine operators and mould-makers who make up Twinstar bring to the company their collective skills and operational co-ordination, acquired and refined by the extraordinary workflow demanded in order to deliver custom-built precast products.
Proficiency in high-volume, rapid output manufacturing will soon seem rather basic, as the path to profit in custom fabrication reveals why so few have trodden it.
The values lived by Coetzee percolate throughout Twinstar’s operation and are the engine driving its continuous output of a highly diverse range of products, as well as the remarkable forethought applied to each operational requirement of those products.
“We’ve deliberately kept our operations sized for the work we deliver,” she explains. “I know exactly what we can commit to and precisely how to achieve the best outcomes for each client.
“We make our own moulds and have one truck with an excellent crane that enables us to deliver large concrete products in segments, to the great advantage of our clients. By keeping weight within the regulated range, we save clients thousands of rands in transport costs. We guide the placement and fitting of the product and will be on site, if necessary.”
Twinstar Precast (Pty) Ltd
Tel: 012 670 9083 or 082 552 1915
E-mail: info@twinstar.co.za
Website: www.twinstar.co.za
She notes that in most circumstances, Twinstar Precast has the capability to make adjustments to the design required. All practical considerations are made to ensure the product meets a client’s particular requirements.
Twinstar Precast has a unique relationship with mainstream precast concrete companies who use it and pass on referrals to others needing certain nonstandard products.
Twinstar is uniquely positioned to cater for an extremely diverse range of industries. The company is solution-driven in all aspects of precast concrete and creates products ranging in weight from 2kg-6 tons.
With the risk of theft of products in steel and cast iron components increasing by the day, Twinstar’s in-house manufacturing of polymer products offers great value to local councils, developers and any entity needing to minimise loss of manhole covers, frames, stormwater gratings and other components. These can be bought as loose items, or cast into the required precast concrete slabs.
Twinstar Precast’s manufacturing facility is situated in Olifantsfontein, Gauteng and delivers to anywhere in South Africa. Its crane-mounted trucks can offload products directly on site and can also help place slabs during installation. (These transport and installation services are available within Gauteng and the northern provinces.)
There are many instances where homeowners have engaged the services of a contractor, only to discover that the quality of the completed work was poor or disputes arose during the execution of the project. To ensure peace of mind, it is recommended to engage the services of contractors who are members of Master Builders Association KwaZulu-Natal (MBA KZN).
Members of the association subscribe to a members’ code of conduct and understand the importance of, inter alia, quality when it comes to executing a project. In addition, if contractual, regulatory or building-related legal disputes arise, they can be addressed by the association. A contractor who is a member of the association is obliged to account for their actions in line with the code of conduct.
The homeowner who has appointed a contractor anticipates that the project will meet the degree of quality which was predetermined long before actual construction commenced – and
this is defined in the scope of works document. In accordance with the requirements of the client, best practice and the law, a professional provides project specifications that establish the standards for the project’s quality. It is the responsibility of the construction team to meet the required quality and specifications.
requirements of the work to be undertaken and applicable regulations. The contractor needs to demonstrate that they have fulfilled the specifications’ quality requirements.
The “Find a Builder/ Supplier” function on the association’s website enables members of the public to select from a lengthy list of reliable service providers. Utilising the services of members of MBA KZN comes with the assurance that the service provider is bound by the association’s code of conduct and that the association is available to mediate any issues that may arise, at no cost to the client or service provider.
In construction, the project’s quality standards are typically outlined in the specifications. Although these terms are open to interpretation, standards may be briefly defined by the specifications which are based on good practice, the specific
Members of MBA KZN receive expert support and advice for matters relating to their business, which include construction contracts, health and safety, and labour relations. They also have access to training and development opportunities.
When it comes to claims for compensation, many debates have arisen about whether an accident arose out of an employee’s employment. In most cases, this question is asked by the person responsible for accident prevention and keeping the disabling injury frequency rate (DIFR) at zero, in case they are not obliged to report the accident.
Let us look at why it is unlawful to “assess” an accident and then not report it for compensation. The Compensation for Occupational Injuries and Diseases Act (COIDA) states that an accident has to
arise out of and in the course of an employee’s employment, and it must result in personal injury, illness or death. Many employers believe it is their right to assess whether the accident meets these criteria. An example is a receptionist being asked to pick up stationery from a store during her lunch break and being involved in an accident while doing so. Another example is a manager attending a conference and having an accident during the networking session after the event.
Section 39 of the COIDA states that an employer must report an accident within seven days after it was made known to him/her. This “making known” can be done by the employee reporting it, or by
the manager having learnt of it in some other way. If an employee therefore fails to report the accident, but posts about it on social media and the employer or an employee sees the post and reports it, it is regarded as “having learnt of it”. When this occurs, the employer has seven days to report the accident.
The employer may assess the accident during the seven days, but the accident must still be reported, regardless of the outcome of the assessment. Section 39(7) makes this quite clear: “for the purposes of this section [39], an accident includes any injury reported by an employee to his/her employer, if the employee when reporting the injury alleges that it arose out of and in the course of his employment and irrespective of the fact that in the opinion of the employer, the alleged accident did not arise out of and in the course of his employment”.
The Act also allows in Section 39(12) for the employee (or his/
her dependants) to ask for a copy of the reported claim for compensation. In this event, the employer must provide a copy.
The Occupational Health & Safety (OHS) Act and the COIDA have reference for claims for compensation. The OHS Act’s main purpose is to prescribe the establishment of a risk-free work environment and prevent accidents. The main objective of the COIDA is to provide compensation for disablement caused by occupational injuries or diseases sustained or contracted by employees, or for death resulting from injuries or diseases, as well as matters connected therewith.
When an employee is injured and the employer believes that the cause of the accident was not directly related to any provision of the OHS Act, the employer does not have to include it in his/her organisation’s accident statistics. The DIFR, or whatever means is used to record statistics, is a retrospective measure of the efficiency of a health and safety programme. It is generally understood that more effort results in fewer accidents.
If the accident had nothing to do with the actual work performed, it may be disregarded.
Section 8(2) of the OHS Act can serve as a guideline. The “purpose” or long title of the OHS Act should be examined. From this, one can derive a few criteria which can be used to determine whether
an accident can be disregarded for the purposes of statistical analysis and star-gradings.
Firstly, the employer should ask him/herself whether the accident occurred as a result of:
• The production, processing, use, handling, storage or transportation of an article or substance. This could include things such as solid matter, liquids, gases and any physical products.
• The performing of any work. The “work” performed has to be directly linked to the items in points 1-3 and the injured person’s job description or job function.
If any of the answers are “yes”, the employer should proceed to the following question: “Is there a specific provision in the OHS Act, the regulations and the safety standards that is intended to cover this by imposing a duty on the employer?”
If the answer to this question is “no”, then all COIDA claims which did not result from the activities in points 1-4 may be disregarded. If the answer is “yes”, any COIDA claims resulting from these activities may not be disregarded.
Remember, this is a suggestion and not a legal requirement. Internal policies and procedures must be created and maintained if this concept is to be used. Nevertheless, employers still have to comply with Section 39 of the COIDA.
• The use of plant. This would include fixtures, fittings, implements, equipment, tools, appliances, etc.
• The use of machinery. This would include any energy source such as electricity, pneumatic energy, hydrodynamic energy, etc.
The COIDA also covers employees against accidents which may not arise directly from their job description. This includes work outside of South Africa, attending training on or performing emergency work such as first aid, working in an ambulance and firefighting, and being transported to and from work.
“ THE EMPLOYER MAY ASSESS THE ACCIDENT DURING THE SEVEN DAYS, BUT THE ACCIDENT MUST STILL BE REPORTED, REGARDLESS OF THE OUTCOME OF THE ASSESSMENT.”
In an age of online shopping and mass production, distribution centres are on the rise. Naturally, the amount of packaging is also increasing and a practical solution is needed to close the loop on recycling so much waste. One major tool distribution company in the US Midwest has found its own “circular economy” answer to this problem by using EcoShield® Heat Sealable Paper to recycle used boxes into dunnage bags.
With thousands of tools going in and out of the aforesaid distribution centre, the facility was inundated with corrugated box waste. Already, the company had implemented a recycling initiative by bundling the boxes and sending them off to the recycling centre. The downside of this process was the large quantity of resources consumed for baling, staging, pickup and transport. Meanwhile, the company still had to buy a large amount of kraft paper for package cushioning and fill material in outbound shipments.
A new idea to recycle the corrugated box waste into something valuable on site was investigated. Special processing equipment from Europe, along with a packaging machine from PAC Machinery’s sister company,
Audion, allowed the facility to chop up used cardboard boxes and automatically pack them inside paper bags made on an adjacent AVM vertical form,
fill and seal machine. These “dunnage bags” could then be placed inside shipping boxes for cushioning and void space fill.
“It’s a great story in terms of packaging and being able to re-use things for your outbound shipping – and the system pairs nicely with the Cortec® Heat Sealable Paper,” says Greg Berguig, vice-president of PAC Machinery. This was the first American installation of the system, which was already in operation at several sites in Europe, and raised the question of how to ensure a reliable supply of heat-sealable paper in a different region. Supply chain concerns were resolved with EcoShield® Heat Sealable Paper, which presented a reliable, recyclable alternative readily
available from Cortec® Coated Products in Wisconsin.
EcoShield® Heat Sealable Paper is a versatile packaging material for a wide range of creative uses. Its heat-sealable adhesive coating can be applied to many different types of paper – white or traditional brown recyclable kraft paper – to make a recyclable packaging material transformable into envelopes, bags, tags or bands. The paper can be printed prior to heat-sealing if special branding marks are required. In the case of the tool distribution centre, a brown version of EcoShield® Heat Sealable Paper was selected for customer validation testing and was subsequently adopted for use on the Audion AVM vertical form, fill and seal packaging machine.
This changeover had dramatic benefits. In addition to eliminating the resources needed to collect and ship used boxes to the off-site recycling centre, the customer saves an expenditure of six figures previously used to buy packaging fill paper. In explaining the rationale for switching from offsite recycling to making dunnage
bags on site out of EcoShield®
Heat Sealable Paper, Mike Gabor, Cortec’s vice-president of sales for Eastern North America, explains: “Firstly, it made financial business sense for this company to do this. It saved a ton of money. Environmentally, it took that whole cycle out of the recycling stream and it did something good for everyone else too. That’s the winwin of this thing.”
This ingenious solution is a great blueprint for any distribution centre or facility that has a high volume of incoming and outgoing packages. By pairing the right equipment with EcoShield® Heat Sealable Paper and corrugated box waste, companies can promote the “circular economy” and close the recycling loop in-house, just as this distribution centre did.
Commenting on President Cyril Ramaphosa’s recent Cabinet reshuffle, Chris Campbell, CEO of Consulting Engineers SA (CESA), states: “Our new Minister of Electricity, Kgosientsho Ramokgopa, needs to seize the opportunity for collaboration with the private sector for funding and with our member companies, who have the technical knowledge and capability to deliver results with the speed our country so desperately needs in order for economic growth.”
While Campbell acknowledges that the reshuffle is unlikely to make much of a difference to the power crisis in the short term, he says he looks forward to Ramaphosa delivering on his promise of improved infrastructure delivery in the next two years, post the “real” Cabinet being announced.
CESA and its near-600 member companies, employing 17 000 people, remain ready and available to partner with government. “We’re here to
support particularly the younger cadre of deputy ministers who’ve been appointed. We look forward to being of service to our country,” says Campbell.
With a firm base of technical expertise and infrastructure in South Africa, construction chemicals and admixtures specialist Chryso Southern Africa has been increasingly serving markets in Central, East and West Africa. The company’s active growth strategy into the continent over more than a decade means that customers there can expect the same high standards of product and support.
According to Armand van Vuuren, commercial manager: exports at Chryso Southern Africa, the company’s expansion strategy has been pursued for almost a dozen
years – with great results. There are now distributors in a range of key markets, including Angola, Botswana, Ghana, Mozambique, Nigeria, Zambia and Zimbabwe.
“We also have an established office in Nairobi, Kenya and are expanding into Tanzania,” he says. “Through our extensive presence across Southern, Central, East and West Africa, we supply not just the
ready-mix and precast sectors, but also specific construction and infrastructure projects.”
The expertise and resources of Chryso Southern Africa’s distributors in these countries are supported by the technical team in Johannesburg, who can step in whenever necessary with the required specialised input. Van Vuuren stresses that these
partners are carefully chosen to act as extensions of the company, delivering the same high level of service wherever their clients work.
“Africa’s an exciting continent and this is where future economic growth’s going to come from,” he says. According to the African Development Bank, the expected growth rates in West and Central Africa are expected to be 4,2% and 4,6% respectively this year, while East Africa will reach 5,5% in growth terms.
Van Vuuren notes the extent to which many countries have invested heavily in infrastructure in recent years – demanding large volumes of concrete for civil engineering projects. The construction work involved in the Decongestion Project for Zambia’s capital Lusaka, for instance, has changed the face of that city in a matter of years.
“Chryso Southern Africa and our distributors have been working with a range of contractors and other businesses to ensure that their concrete meets the exacting specifications of the contract,” says Van Vuuren. “Whether the application’s bridges, dams, mining infrastructure or precast manufacturing, we continue to play a vital and growing role in the continent’s development.”
An important element of Chryso’s presence is the stock held by distributors in their respective regions – giving customers easy access to products as and when they are required. End-customers are provided with full site support from a technical perspective, including access to the specialist team in SA.
“With our current momentum, we’re planning to set up more of
our own offices and production facilities in key regions, paving the way to serve larger and more complex requirements,” says Van Vuuren. “Africa’s leading countries have their plans in place for future development and, despite the occasional setbacks, they’re on track for long-term growth. Chryso Southern Africa’s working with the concrete and construction industries on the continent to help make this happen.”
This strategy is bolstered by its parent company, Saint-Gobain’s acquisitions of companies such as GCP Applied Technologies, which will offer access to innovative products. Firmly committed to customer-centricity and proximity, the organisation has local operations in 45 countries and this footprint provides its service offering to more than 100 countries.
South Africa’s maritime sector generates billions of rands in earnings each year, promoting economic growth and the creation of jobs in the country. Consequently, it forms an indispensable part of SA’s economy and is a more than worthy career path to explore. This is why the construction of the brand-new Maritime School of Excellence (MSoE) in Durban, KwaZulu-Natal (KZN), which is due for completion in March 2024, is a big step forward for the country.
Why build a maritime school, one might ask? The MSoE will introduce nautical studies to high school pupils and prepare them for
important roles in Southern African ports. Efficient ports are crucial to the maritime industry and the transport economy as a whole.
The MSoE will likely become a leading high school that provides pupils with an understanding of the marine industry, marine and terminal operations, port management, port engineering and supplying high-quality seafarers to the market. It opens avenues to new career options and job opportunities.
The flagship project is funded by the KZN Department of Education and implemented by
the Development Bank of SA. The innovative architecture is the work of GIARC Designs and construction is being carried out by GVK-Siya Zama. The project also maximises local employment and procurement, so it will not only benefit school pupils, but will create employment for local labour and contractors.
The MSoE, a first of its kind in the province, provides an environment that is conducive to learning, as well as encouraging a healthy study-life balance. The nautical-themed built structure is designed to facilitate interaction, collaboration, physical activity and access to resources, as well as
more cloistered areas for private study and even boarding facilities.
The school accommodates 700 pupils and has boarding facilities for 400 males and females. There are 24 well-lit classrooms and other learning spaces, including laboratories and a state-of-the-art simulation room that will provide pupils with hands-on experience of steering a ship into and out of a port.
Entering the school through gated and gabion-stone walls, one is greeted by a nauticalthemed gatehouse designed as a lighthouse. The first view is of a full-sized soccer field and the school hall adjacent to it. The hall includes an indoor play area and a seated mezzanine level offering access to the stage for the physically challenged. The hall will be used primarily by the school, but will also be available to the public on weekends.
Next in view is the boarding facility, which is built over three floors with a central dining area, a fully fitted kitchen and all associated facilities, including a refuse area, cold rooms, storerooms, laundry and ironing facilities.
At the front of the site are the administration block and simulation room on the ground floor. The administration block is framed by a double-volume concrete feature which dominates the façade, leading teachers and visitors into the maritime facility. An access ramp to the first floor allows physically disabled individuals –
whether they are teachers, pupils or visitors – to reach it with ease.
The main learning areas or classrooms are built around courtyards that can be viewed from the covered and shaded verandahs or walkways. These verandahs are linked to all blocks on the first floor by means of covered walkways. Light-coloured facebrick, harmonised with softcoloured wall paint and spots of brightly-coloured brickwork and shading devices, gives the school space interest and vibrancy.
Courtyards in the learning and boarding areas form spaces for pupils to gather and relax during breaks, shaded by trees and landscaping. An aerial view of the school reveals the boarding facility and an Olympic-sized swimming pool.
“The architectural style accommodates a balance of open spaces, as well as privacy,” says lead design architect Craig Moodley. “Public spaces encourage pupil interaction, while zones of learning, boarding and sporting activities all consider the essential needs of the youngsters and promote a balanced, healthy lifestyle.”
“The built structures utilise a mix of various construction materials to enhance the aesthetics and exhibit modern architecture. Green technologies have been adopted where possible and sustainable renewable solutions have also been included, such as solar mechanisms and rainwater harvesting. High-quality finishes enhance the aesthetics and are suitable for the coastal location,” says Moodley.
“ THE NAUTICAL-THEMED BUILT STRUCTURE IS DESIGNED TO FACILITATE INTERACTION, COLLABORATION, PHYSICAL ACTIVITY AND ACCESS TO RESOURCES, AS WELL AS MORE CLOISTERED AREAS FOR PRIVATE STUDY AND EVEN BOARDING FACILITIES.”
Ryan Schneeberger, production director at GVK-Siya Zama in KZN, says: “The opportunity to build an educational building in SA is always inspiring, given the desperate need to uplift our youth and indirectly assist in the long-term reduction of youth unemployment. This particular project has the added benefit of being part of urban regeneration, as it’s situated in the heart of the Durban CBD.”
“Two challenges for construction teams included the natural congestion of building in a CBD, as well as the fact that the maritime
site’s only 500m away from the Indian Ocean. This meant that construction dewatering had to be incorporated into the costs and programming of the works. However, the team’s managed both of these challenges admirably,” adds GVK-Siya Zama contract manager Charles Cormack.
The school will provide meaningful benefits in other ways too, including making a positive impact on the local economy, improving socio-economic development and growth, supporting SMME development
and local labour, and increasing the infrastructure delivery component of the country.
The MSoE is strategically located at 41 Somtseu Road, Durban, in the eThekwini Metropolitan Municipality, close to the largest port in Africa. A vision that began 13 years ago is finally becoming a reality, driven by the passion of members of the Department of Education to create a modern facility that will use the latest teaching technologies to prepare youngsters for careers in the maritime field.
“ THE SCHOOL WILL PROVIDE MEANINGFUL BENEFITS IN OTHER WAYS TOO, INCLUDING MAKING A POSITIVE IMPACT ON THE LOCAL ECONOMY, IMPROVING SOCIO-ECONOMIC DEVELOPMENT AND GROWTH, SUPPORTING SMME DEVELOPMENT AND LOCAL LABOUR, AND INCREASING THE INFRASTRUCTURE DELIVERY COMPONENT OF THE COUNTRY.”
Get ready to experience the ultimate construction event of the year. Big 5 Construct Southern Africa is celebrating its 10th edition and you’re invited!
Big 5 Construct Southern Africa is a significant contributor to the economic growth, recovery and transformation within Southern Africa’s construction industry with a special focus on facilitating buyer/seller face-to-face connections and showcasing the most innovative solutions for the region.
GROW your network with over 8,500 construction industry professionals
DISCOVER the most innovative products and technologies available
ENGAGE with public and private sector stakeholders over the most critical issues
LEARN about the latest trends, best practice and upcoming construction projects
Simply scan the QR code with your phone’s camera app
Co-located with:
SOUTHERN AFRICA
www.thebig5constructsouthernafrica.com
SOUTHERN AFRICA
AVOID CONCRETE STRENGTH DELAYS.
As winter approaches, the colder ambient temperatures can cause delays in concrete strength development as well as finishing aspects. Rest assured, this challenge can be easily overcome using CHRYSO’s Premia Range of admixtures and demoulding agents.
Top executives of the American Concrete Institute (ACI) recently paid a short visit to South Africa to meet Cement and Concrete SA (CCSA) management to reconfirm the international partnership ACI holds with the SA body.
ACI president Dr Charles Nmai and Bernie Pekor, the institute’s director of international business development, held discussions with CCSA’s CEO Bryan Perrie and business development manager Hanlie Turner.
The ACI, one of the world’s leading concrete associations, was founded in 1904. The non-profit technical society and standards-developing organisation has a mission to “develop and disseminate consensus-based knowledge on concrete and its uses”. Its headquarters are in Michigan, USA and it has an international office in Dubai, UAE, as well as regional offices in California, Illinois and Maryland. Globally, the ACI has a membership of over 30 000 and a student membership of about 15 000. In addition, it has 93 global chapters, over 250 student chapters and 64 international partners.
Turner says CCSA is one of the institute’s international partners. “This valuable collaboration substantially promotes global concrete excellence by making the technical expertise of each organisation available to fellow partners through publications, meetings, conferences, Internet links, committee membership, certification activities and other channels. Some benefits for CCSA include our members having complimentary access to
selected ACI publications via our information centre. In addition, last year the winners of CCSA’s prestigious biennial Fulton Awards were entered into the ACI Awards for Excellence, as will the winners of the Fulton Awards in 2024 be.”
After his visit to SA, Nmai said the ACI’s discussions with CCSA had covered “a myriad of topics”, including sustainability, concrete industry productivity and dissem -
ination of concrete knowledge. He congratulated CCSA on the publication of the 10th edition of the globally acclaimed concrete reference book, Fulton’s Concrete Technology and said that CCSA had a key role to play in helping to advance the quality of concrete construction in Africa.
“GLOBALLY, THE ACI HAS A MEMBERSHIP OF OVER 30 000 AND A STUDENT MEMBERSHIP OF ABOUT 15 000.”
The South African coatings sector is being severely affected by load-shedding, with massive unexpected burdens heaped on already high production costs, says Tara Benn, executive director of the SA Paint Manufacturing Association (SAPMA).
Benn says manufacturing members are losing millions of rands having to work around power outages in production, especially for energy-intense chemical reaction paint products which require a continuous process for the dispersion phase of the manufacturing process.
“In addition to planned load-shedding, sudden outages or related substation failures are major problems. If a production batch is spoilt by a sudden loss of electricity, the results can be catastrophic and there are now increasing cases of end-products having to be dumped or regarded as sub-standard because of loadshedding occurring without prior notice. There are also reports of new clauses in insurance which would exempt the insurers from damages to goods resulting from issues related to the power grid,” she explains.
“SAPMA members have had to add diesel costs, the provision of inverters to home-based sales staff and the costs of back-up systems for their servers to running expenses. Our members feel they can’t pass these costs on to
customers in such a depressed economy. Costs of raw materials and other expenses have already escalated due to the rand’s depreciation against all major currencies.”
Benn says SAPMA members’ customers who cannot afford generators simply send staff home if they know that their loadh-shedding schedule is in the afternoon, or have them start later in the morning, resulting in short pay for employees. “We’re also seeing the slower arrival of goods from warehouses at ports, which is seriously delaying the availability of goods. Load-shedding’s also affecting ancillary industries, with customers responsible for the supplying of coatings for the food and beverage industry, as well
as drum coatings, among others, experiencing escalating shortages.
“Work shifts have been affected and, because of such adjustments, night shifts are now becoming the norm in companies previously only doing day shifts. This is having a negative impact on employees’ personal lives in terms of transport for school children and similar domestic challenges,” she adds.
SAPMA members’ hardware stores are being affected by loadshedding consequences, such as the late arrival of stocks. “It can take delivery vehicles hours longer to reach their destination when traffic lights aren’t working during load-shedding. The DIY stores are already having to cope with a much lower consumer spending than before the Covid-19 epidemic,” says Benn.
Strong and steady sets the pace for constructive progress on the road ahead as we build the future from the ground up. Lay steadfast foundations with leading quality cement produced on Africa’s beautiful playground.
Community housing schemes like sectional title complexes, apartment blocks, residential estates and retirement villages have until 10 May 2023 to ensure that they have a detailed POPI policy in place. This document should outline how they handle personal information and comply with the Protection of Personal Information Act (POPIA).
Specialist community schemes attorney and BBM Law director Marina Constas urges trustees in sectional title schemes and the directors of homeowners’ associations to take this looming deadline seriously. “The penalty for non-compliance with this directive from the Community Schemes Ombud Service is a fine of up to R10 million or 12 months’ imprisonment,” she says.
“Trustees in sectional title schemes and directors of homeowners’ associations are responsible for ensuring their developments’ POPIA-compliance and should have a well-advanced POPIA plan of action by now,” she stresses. She notes that this deadline was extended from 1 July 2021.
“By now, every community housing scheme should have a POPIA policy, or be close to finalising this important document. They should have appointed an information officer who’s the POPIA oversight representative of the scheme, amended their rules, if necessary, to comply with POPIA and have POPIA agreements with stakeholders like auditors and managing agents who have access
to the personal information of owners and tenants,” she advises.
Constas explains that the POPIA policy should include details of whose personal information is collected and held by the complex. “This includes trustees, owners and tenants, as well as visitors. The type of personal information that the complex collects and holds, as well as how the complex collects and stores personal information, must be specified. The purposes for which the complex collects, uses and discloses personal information must also be detailed, along with information on how an individual may access personal information.
“Aspects to be considered by the trustees and directors include access control at the guardhouse and CCTV surveillance cameras. They must be ready to answer questions regarding the information that’s requested from visitors by security guards. Does it include identity numbers and photographs? The trustees and directors must be able to explain why this information’s collected, where it’s stored, for how long it’s stored and when it’s destroyed.
“Community schemes can still make use of CCTV cameras, but there are certain steps they must take to be POPIA-compliant,” explains Constas. “These include notifying owners in writing that cameras exist and where they’re located. Cameras must be positioned in such a way that they don’t infringe on owners’ right to privacy in their own homes. The POPIA policy should clearly explain who’s responsible for the control of images, what’s recorded and how images are utilised. In storing footage, care must be taken that images can’t be corrupted and there must be a process outlined for destroying footage after a certain time. Signage stating that CCTV cameras are in use for the purpose of crime prevention is recommended for sectional title complexes and residential estates, to ensure POPIA-compliance.
“The POPIA policy document must also outline how an individual can complain to the Information Regulator and how the complex or residential estate will deal with that type of complaint,” adds Constas.
“I strongly suggest that, with this final deadline for POPI-compliance looming, all sectional title complexes and community housing schemes obtain professional advice and assistance to review and update their privacy policies and privacy statements.”
ROCLA is South Africa’s leading manufacturer of pre-cast concrete products.
Surpassing 100 years of product excellence.
• Pipes
• Culverts
• Manholes
• Poles
• Retaining walls
Roadside furniture
Including other related products within infrastructure development and related industries. Visit us on www.rocla.co.za for our nationwide branches
“ THEY MUST BE READY TO ANSWER QUESTIONS REGARDING THE INFORMATION THAT’S REQUESTED FROM VISITORS BY SECURITY GUARDS.”
facts from the front, seems almost quaint. While many of us were taught that way and still think of education within those parameters, the reality is fast becoming something quite different.
By Phemelo Segoe, education specialist and marketing manager: Optimi WorkplaceWe often think about the human right to education as relating to children. We imagine them starting their school careers at a young age and being supported as they progress through the years, ultimately emerging from the system as young adults who have the capacity either to study further or to find employment. This is their right. It is enshrined in the Constitution.
The Constitution, however, clearly stipulates another demographic that is entitled to education: the adult population. “Everyone has the right to a basic education,” states Section 29(1), “including adult basic education.”
Many of these adults live with the effects of our apartheid legacy –opportunity was denied to them by law. Yet even those who started and completed their education in the almost 30 years since we became a democracy often lack
the skills and qualifications they need to progress academically or professionally. The right to education remains enshrined in theory, but there is a gap that needs to be bridged in practice.
That bridge is made of many things, but among the most important ones are technology and privatesector involvement.
Education is not what it used to be – quite literally. The idea of students sitting at desks, pens in hand, listening to a teacher expounding
Across disciplines, an increasing reliance on digital innovation is transforming the way we do things – including the way we are taught. Although they existed before the Covid-19 pandemic, hybrid and online learning courses sprouted like mushrooms during the height of the lockdowns and have thrived since. The benefits were immediately apparent to adults seeking to improve their levels of education, as well as corporates endeavouring to upskill their employees.
Digital courses have helped to level the playing field in terms of access and with more of them available than ever before, students and employers have been able to select the ones that suit them best. While infrastructural challenges persist, particularly in terms of the exorbitant cost of data, even these have been overcome to some extent. Providers such as Optimi Workplace, for example, have made their modules available offline so that students do not deplete their bank accounts while they learn.
“EDUCATION IS NOT WHAT IT USED TO BE – QUITE LITERALLY. THE IDEA OF STUDENTS SITTING AT DESKS, PENS IN HAND, LISTENING TO A TEACHER EXPOUNDING FACTS FROM THE FRONT, SEEMS ALMOST QUAINT.”
Technology has helped to ensure that the right to adult education is realised in an approach that has been welcomed by the private sector.
A matric is still a minimum barrier to entry for almost any South African seeking to enter the workforce and, ideally, further qualifications are required. With so many adults lacking these qualifications and the critical skills they represent, some of the responsibility – and, indeed, the opportunity – for bridging that gap falls on the private sector.
Employers have recognised that workplace training and community education help to right past injustices and support those who failed to qualify the first time. They also offer several material advantages.
Incorporating training and development into your CSI programme offers points in terms of the BBBEE scorecard, for example, as well as tax incentives. More importantly, it helps to nurture a skilled, motivated and loyal workforce. Invest in your employees and they are likely to invest in you.
Learnerships help employees enhance their skills and knowledge and improve their prospects. More broadly, they play a role in decreasing unemployment, alleviating poverty and creating a better standard of living for more South Africans. They help to truly bring the human right to education to life, which – in turn – impacts many other important human rights.
Although there are many ways in which adult education and training
play out in the workplace, one of the most valuable executions lies in technology. By providing employees with the digital tools, skills and support necessary to study remotely, companies make their students’ learning process flexible, independent and more likely to succeed.
This is not to suggest that it is the only way: in-person and hybrid models are also effective. However, the point at which technology and corporate intervention intersect allows for meaningful education and training that can transform the futures of adult South Africans seeking, and deserving, a second chance.
• Optimi Workplace is a division of the Optimi Group. With over two decades of experience in adult education and training in the workplace and over 10 000 students tutored, it is leading the frontier in workforce and community education and training.
True beauty doesn’t fade with time.
Hydro aluminium garage doors are lightweight, corrosion-resistant and extremely durable, which makes them perfect for coastal areas. They’re also easy to clean and maintain. Available as single or double doors in four attractive colours, Hydro aluminium doors will enhance the kerb appeal of any home. For more info, visit hydrodoors.co.za or call 086 110 2425.
“My greatest take-out from the three years following hard lockdown is that opportunity exists in chaos. And, while this is true for the property sector, I think it applies to all industries,” says Malcolm Horne, group CEO of the Broll Property Group.
Businesses that had strong strategies in place pre-pandemic – often fiveyear strategies – saw these plans playing out at an unexpectedly accelerated pace, he says. “In our case, our five-year plan, which incorporated strategies regarding sustainability, continuity, inclusivity, innovation and growth, was implemented within two years.
“Businesses that were able to move quickly from survival mode to sustaining their operations and then to securing their businesses were able to garner greater successes in their respective markets.
“In our case, the success wasn’t what we might ordinarily have defined as success. It related to the people side of the business: there was an enormous amount of growth in their ability to be agile, learn new skills, collaborate and become solution-driven.”
Broll Property Group executives present a consolidated look at how the commercial real estate sector has fared in the “new normal” since the Covid-19 pandemic wreaked havoc in South Africa and around the world.
Sean Berowsky, who heads up capital markets at the group, says following lockdown, the market
(made up of commercial/office, industrial, retail and logistic space) was in a state of semi-paralysis.
“People were – and still are –particularly concerned about the office sector, which has been most affected by the shift to remote and hybrid working. While office occupancy hasn’t returned to prepandemic levels, there are pockets of change. One of the most notable changes is that quality office space was snapped up first, albeit at lower rentals than prepandemic ranges.
“However, there are areas such as Cape Town where a significant amount of space is being taken up for call centres and where rentals have almost reached pre-pandemic levels,” adds Berowsky.
Johannesburg and Tshwane, which have a greater number of developments and larger office areas, have not yet had the same success as Cape Town. “The absorption of office space will take some time to resolve. It isn’t always possible to transform every office building into a residential (or other) space. That said, these options will be investigated and if there’s a case for them, they’ll be taken up,” he says. He notes that there is unlikely to be any major speculative development for some time. “While there may be some development in particular nodes, it’s not expected to reach anywhere near pre-pandemic levels in the foreseeable future, especially due to a lack of demand and the difficulties funds are experiencing when it comes to raising capital in the debt market.
“In most instances, funds’ net asset values are higher than their share prices, which means they’ll be diluting themselves by going to the market. There’s a definite trend towards recycling capital through the selling of non-core older buildings, particularly in the office market space,” says Berowsky.
Pricing in the retail market is where it was expected to be, with some reversions in the larger retail centres. Convenience and lower-LSM centres have been holding their values well, with investor appetite still intact and positive rental growth.
Logistics has been the clear winner overall. “There’s still a demand for logistics space, although it’s now beginning to slow down, as many of the available deals have already been placed. There’s also been a high take-up of fit-for-purpose industrial space and this seems to be growing,” he notes. While the property sector – with high (and increasing) interest rates – is currently a tough environment in which to operate, Berowsky says there are definitely opportunities for investors and landlords to participate in the property cycle. “Investors who know what they want and stick to their knitting will do well in certain pockets of the market and where pricing’s marked down because of deflated nett operating income.”
Surine Griffin, Broll’s head of property management, says the industry has experienced a notable shift towards sustainability and continuity over the past three years.
She says the energy crisis has played a major role in compelling property-owners to ensure uninterrupted service to their tenants and the public. “Essentially, the pandemic’s been replaced by the energy crisis and the other issues raised by Sean. This has seen the implementation of alternative forms of energy, such as generators and solar for the provision of back-up power and water supply.”
In addition, the threat of civil unrest has seen increased investment in security measures for properties, especially malls, distribution centres and logistics premises.
“Malls had to become safer for people who prefer visiting shopping centres, as opposed to buying goods online. Greater security measures such as roller
“PEOPLE WERE – AND STILL ARE – PARTICULARLY CONCERNED ABOUT THE OFFICE SECTOR, WHICH HAS BEEN MOST AFFECTED BY THE SHIFT TO REMOTE AND HYBRID WORKING.”
shutters and reinforced fencing have been implemented, stricter service level agreements have been put into place with security companies and many clients have ensured that their premises can be fully locked down in the event of an emergency,” notes Griffin.
These and other costs, such as increases in rates and taxes, have made it increasingly expensive to be a landlord, with some of the costs relating to power supply and related maintenance getting passed on to tenants. “Top of mind for us, as managing agents, is to try to minimise cost escalations,” says Griffin.
Roger Long, head of valuations at the Broll Property Group, agrees with Griffin’s and Berowsky’s assessments. “From a valuation perspective, the office market has been hardest hit, especially since employees aren’t fully back at the office and working models (home/office/hybrid) are still being deliberated on.
“In the retail sector, we’re witnessing relatively flat rentals, although rental reversions in the more popular regional centres are showing signs of increasing. Activity’s picking up in the industrial sector and there’s a flattening in demand for logistics buildings. What we’re also noticing is greater demand for alternative investments, including data centres, hospitals and student accommodation. However, ever-increasing municipal rates and a high interest
environment are dampening factors,” says Long.
Taking a five-year-plus view, he says that property is a good buy on the stock exchange, with total returns of 10-14% expected for 2023. “Lockdown isn’t the issue now – rather, the main issues are energy, the economy and politics. Property’s a long-term investment and the sector will bounce back, but it still has a hard climb to reach pre-pandemic levels.”
“The reality is that if people run their businesses in the same way they ran them pre-Covid-19, they’ll find themselves in trouble. We’ve seen that embracing innovation within the business and allowing business leaders the freedom to be vulnerable and bring their thoughts to the table has had numerous positive spin-offs.
“It’s also more proactive to look to the future, rather than linger in the past. Yes, there have been some consequences of the pandemic that must be managed, but I think more businesses are becoming self-sufficient and solution-focused,” says Horne.
He believes South Africans are a resilient bunch who know how to celebrate laduma moments, moments of thunder and moments of success, and who help people through failure.
“I’m not talking specifically about property – I’m referring to the mindset of committing to our country: a mindset of growth. We’re here. We’re going to make a difference. We want to be relevant. This is what I’m witnessing post-Covid-19.
Horne says the negative sentiment in SA has compelled corporate leaders to adopt solution-focused mindsets. “This is what I've seen in our business: new solutions, new partnerships and new service lines. These are all part of remaining relevant and staying ahead of the curve.
“As a nation, one factor is a given: we’re able to accept and adapt to left-field circumstances, whether black swan events, energy breakdowns or riots. As South Africans, we have a propensity to look for the silver lining or the next opportunity. It’s in our DNA. When times are bleak, we’re able to focus on people, solutions, innovation, growth and the future – to believe in our country, despite its challenges,” he says.
“ THE REALITY IS THAT IF PEOPLE RUN THEIR BUSINESSES IN THE SAME WAY THEY RAN THEM PRECOVID-19, THEY’LL FIND THEMSELVES IN TROUBLE.”
Choosing your electrical contractor based on price can have deadly consequences! All electrical contractors must by law be registered with Department of Employment and Labour and only registered electrical contractors can legally issue Certificates of Compliance.
Using an unregistered electrical contractor is not only illegal, but also downright dangerous and insurers can refuse to pay any claims arising from illegal electrical work.
Registered electrical contractors ensure that all electrical work is performed in accordance with legislative requirements and the applicable codes of practice and technical standards.
Using an electrical contractor who’s a member of the ECA(SA) is a wise choice because while not all electrical contractors are members of the ECA, all ECA members are registered electrical contractors – and their work is covered by the ECA’s Workmanship Guarantee (terms and conditions apply).
National Office (011) 392-0000 | info@ecasa.co.za
Pretoria (012) 342-3242 | infopta@ecasa.co.za
Johannesburg (010) 271-0686 | highveld@ecasa.co.za
Durban (031) 312-6313 | ecakzn@ecasa.co.za
Cape Town (021) 462-2690 | ecact@iafrica.com
Port Elizabeth (041) 363-1990 | adminpe@ecasa.co.za
East London (043) 726-6359 | adminel@ecasa.co.za
Bloemfontein (051) 447-0859 | nita@ecasa.co.za
HELPDESK 087 944 4555
www.ecasa.co.za
A collapse that claimed the life of a waste-picker at the Ennerdale Landfill on 3 March 2023 begs a general review of safety and operational management at South Africa’s landfills.
This is according to environmental and landfill engineer Nash Dookhi, who is the KwaZulu-Natal chairperson at the Institute of Waste Management SA (IWMSA).
“What I haven’t seen in the media is a detailed investigation into why this tragedy occurred and what could have been done to prevent it,” he says.
Dookhi’s concern is how landfill sites are being managed in accordance with applicable legislation
and regulations, especially in terms of industrial health and safety.
South African waste is regulated by the National Environmental Management Waste Act of 2008. This legislation requires that every landfill owner obtains a waste management licence and, in addition to the development, engineering and monitoring of the site, stipulates the requirements for operating and managing it.
Besides the waste management licence, these conditions continue to be guided and governed by the Minimum Requirements for Waste Disposal by Landfill, Second Edition 1998,
from the Department of Water Affairs and Forestry. The general operations require that, on a dayto-day basis, waste that is tipped into the landfill should be shaped (ie pushed together), compacted and covered. This is known as the cellular landfilling method.
In the case of the Ennerdale Landfill, the operator is Pikitup, the City of Johannesburg’s official waste management company.
Dookhi, who has over 20 years’ experience in waste management, says landfill engineering is a complex discipline that considers various factors relating to landfill stability. These include the types of waste, compaction, moisture content, cover material used, leachate management and many other variables.
Properly managed, waste is inherently stable because certain waste types embedded in it, such as plastics, cardboard and fibres, act as built-in natural reinforcement that provides it with solidity and an acceptable safety factor.
“The fact that a collapse wouldn’t result from one day’s worth of loose incoming waste suggests a longer-term neglect of the requirements,” says Dookhi.
The Minimum Requirements state that “the department discourages waste reclamation at landfill sites”, with no reclamation being permitted at hazardous waste sites at all.
However, if the licence-holder opts to allow controlled reclamation at a general waste disposal site, they must seek permission on the application for their waste management licence or amend an existing permit/licence.
This indicates that waste-pickers’ access depends on what is formally allowed in the site operator’s licence and that their activities are effectively managed and controlled.
“PROPERLY MANAGED, WASTE IS INHERENTLY STABLE BECAUSE CERTAIN WASTE TYPES EMBEDDED IN IT, SUCH AS PLASTICS, CARDBOARD AND FIBRES, ACT AS BUILT-IN NATURAL REINFORCEMENT THAT PROVIDES IT WITH SOLIDITY AND AN ACCEPTABLE SAFETY FACTOR.”(Below): Rubble from demolition sites has immense value in the production of fresh concrete and also has significance as a carbon mitigation strategy.
Regardless, as per the Minimum Requirements and the waste management licence, the responsibility for the safety of any reclaimers rests with the licence-holder.
The site operator is wholly responsible for meeting the daily operational requirements of the landfill, including the safety of the waste-pickers present.
The IWMSA calls on landfill operators to ensure that they meet their waste management licence requirements and are guided by the Minimum Requirements in every regard, including their responsibility to those on site.
“We acknowledge that there’s a role to be played by the waste-
pickers to promote the circular economy. We also acknowledge that it can be difficult to control pickers eager to reach prime
materials in newly-arrived waste and encourage municipalities to provide effective support and management to the sites,” says Dookhi.
MAPEI offers a complete range of high-quality adhesives for ceramic, porcelain and stone materials. MAPEI stays up to date with growing trends and technology within the market, making it the ideal application solution.
The range includes:
• Polymer modified cementitious adhesives
• Deformable cementitious adhesives
• Fast-setting levelling compounds
• Reactive resin polyurethane and epoxy adhesives
• Water repellent cementitious grouts
• Water based epoxy grouts
In the wake of February’s State of the Nation Address and the subsequent budget speech, it has become clear that the South African government has finally realised something most people in the sector have known for a long time: that providing meaningful incentives for companies and households to install solar power (with the eventual aim of feeding it back into the grid) is very cost-effective.
Once fully implemented, the new tax incentives will allow businesses to reduce their taxable income by 125% of the cost of an investment in renewables. Domestic users, meanwhile, will be able to claim a rebate of 25% of the cost of rooftop panels, up to a maximum of R15 000.
While these incentives are undoubtedly important and a step in the right direction, it is worth asking whether they go far enough. If we are truly to turn as many businesses and households as possible into power producers, are more incentives needed?
In order to answer that question, we need to remember just how bad load-shedding has become. SA experienced 200 days of load-shedding in 2022, eclipsing the previous record by some distance – yet that does not tell the full story.
Things look even more dire once one begins looking at the Gigawatt hours that were shed
through the course of the year. It then becomes apparent that the country has shed almost five times as much electricity in 2022 as it did in 2021 (already a record year in and of itself).
Also of huge concern is the fact that the higher stages of loadshedding can cost the economy about R1 billion a day. This means that, in a year like 2022, hundreds of billions of rands were lost to the economy. Given the country’s well-publicised growth struggles over the past decade or so, along with its unemployment crisis, that is clearly an untenable situation.
Eskom’s chairperson Mpho Makwana recently asked South Africans to prioritise installing solar on their roofs and use as few of Eskom’s products as possible. Coming from the very top tier of the power utility, that is an indication of the state of the organisation going forward.
It should therefore be clear that, unless the incentives cost SA more than R200 billion (which is highly unlikely), they are worth it. We also know that the right incentives can dramatically change the country’s energy prospects.
Vietnam, for instance, added more than 9GW of rooftop solar
in 2020 alone, representing a 25fold increase in solar-generating capacity. That is equivalent to nine stages of daytime load-shedding and more than the combined output of Medupi and Kusile power stations, once they are completed (something which will not happen for some time). Other countries and regions that have accrued similarly powerful boosts by incentivising solar are Germany, California, USA and southern Australia.
However, there is an important difference between the incentives those countries provided and the ones offered in the budget speech. In addition to tax incentives, almost all of those markets offered attractive feed-in tariffs – which means that anyone who has installed solar panels can earn money by feeding energy back into the grid.
To date, the only local government to indicate that it will provide such tariffs is the City of Cape Town. If national government is really serious about using solar to turn SA’s energy fortunes around, it will have to find ways of offering similar feed-in tariffs.
One potential avenue for that is to redirect a portion of the R6,12c it exacts from every litre of diesel bought in the country. Of course, some in government might be reluctant to do so. Apart from a few notable exceptions who benefit from diesel fuel levy refunds, those taxes effectively represent a boost to government coffers every time someone buys fuel for their generator. Yet that is nothing compared with the boost it would get from the economic growth and job opportunities that would result from widespread solar installations.
It is clear, then, that more needs to be done. Unless funding is found for the feed-in tariffs that have worked so well for other countries and regions, the impact of the current incentives will be limited, at best.
“ALMOST ALL OF THOSE MARKETS OFFERED ATTRACTIVE FEED-IN TARIFFS – WHICH MEANS THAT ANYONE WHO HAS INSTALLED SOLAR PANELS CAN EARN MONEY BY FEEDING ENERGY BACK INTO THE GRID.”
AfriSam’s offering to concrete precast manufacturers (CPMs) operating in today’s highly competitive marketplace incorporates several value-adds, designed to improve the performance of their products and help contain costs.
Underpinning the primary products supplied to the market – Rapid Hard Cement (RHC) in the 52.5R strength class and High-Strength Cement (HSC) in the 42.5R strength class in the northern
market, as well as in 52.5N HSC product in the southern market – AfriSam’s value-adds include on-site technical services.
These services, which are rendered by staff from the AfriSam Centre of Product Excellence, assist customers to determine the ideal mix designs for their specific applications and propose aggregates that meet these requirements. AfriSam’s SANASaccredited laboratory services are used to verify and test the efficiency of mixes and product deliveries can be specifically scheduled around customers’ individual activities.
“In the CPM market we focus on helping our customers operate as efficiently as possible,” says Mike McDonald, manager of AfriSam’s Centre of Product Excellence. “This may include the evaluation of their site practices and mix designs, and helping them reduce the overall cost of their final products without compromising the quality or aesthetics of those products. For example, certain customers have successfully switched to our Rapid Hard Cement product as an overall cost-effective alternative to HighStrength Cement in this market.
“There’s no one-size-fits-all approach in the CPM market, so we draw from all the alternatives available to provide the most cost-effective solution for each customer. We value our CPMs and we’re committed to building relationships that will give them a competitive edge. Our success
to date reflects the quality, consistency and high performance of our products.”
The “R” early strength factor in AfriSam’s 52.5R CEM I Rapid Hard Cement and 42.5R CEM II HighStrength Cement is proving to be a real differentiator in the CPM market. Top-of-the-range 52.5R Rapid Hard Cement, developed for specialist concrete product manufacturers, is performing
AfriSam’s 42.5R High-Strength Cement has been specially formulated and activated to allow for further extension and performs very well when used in combination with additional mineral components. This is also true when used in the production of structural concrete. The “R” rating of the HSC is supported by AfriSam’s strict quality control plan and this product is achieving in excess of the SANS 50197 minimum of 20MPa mortar strength at the two-day mark. High-Strength Cement is commonly used to achieve concrete strengths of 10-60MPa, but it is particularly suitable for high-strength concrete, with strengths of 80MPa and higher.
“We’re proud to be able to offer an ‘R’ rating with the two products supplied to the CPMs, while retaining an extremely low carbon footprint. In effect, we’ve introduced technological advances that have boosted performance in terms of strength, performance, durability and workability, without sacrificing sustainability,” says McDonald.
particularly well, achieving in excess of the SANS 50197 minimum of 30MPa mortar strength at the two-day mark. This is enabling CPMs to develop a variety of new high-specification products, such as highway barriers, roof tiles, retaining wall systems, culverts and concrete pipes. AfriSam is the only South African manufacturer to produce a 52.5R strength class cement as a standard product.
“These market-leading products, together with our value-adds, are part of AfriSam’s initiative that seeks to unlock value for our customers across the board in new ways. Our CPM customers are experiencing tangible benefits and this has led to measurable growth in this market for us. Our innovative approach allows us to make a genuine contribution to optimising their operations.”
The Hansgrohe Group has published EPDs for nine AXOR and Hansgrohe product categories. The EPDs provide information about the environmental impact of a product in relation to its entire life-cycle, from the extraction of raw materials, to manufacturing and many years of use, to recycling or disposal. This data provides architects, builders and designers with important information for the sustainability of their construction projects and is particularly important for those subject to international certification systems such as BREEAM or LEED.
The EPDs cover about 1 400 of the best-selling chrome products from the standard AXOR and Hansgrohe collections and product ranges. Products of identical design have been grouped into the nine so-called “average” EPDs: overhead showers, hand-held showers, hoses, shower pipes, basin taps, shower and bathtub taps, kitchen taps, basic bodies and thermostats. The data sheets provide information on flow rates, water and energy consumption and CO2 balances, as well as on the origin and composition of materials and recycling options in the event of dismantling. A total of over 35 environmental indicators are shown.
The approach of transparently presenting the sustainability of products has been pursued by Hansgrohe for a long time. In 2010, it drew up the so-called “PCR Product Category Rules” for sanitary fittings and showers for Germany. One year later, the
premium brand published its first EPD in that country for the Crometta 85 and Croma 100 handheld shower models, thus laying the foundation for the company’s future EPDs.
“The EPD information enables architects and builders to select the most suitable product from an ecological point of view as early as the planning process,” says Rebecca Weigold, head of Green Company, Hansgrohe SE. ”With our EPDs based on ISO 14025, planning according to LCA criteria will be much easier in the future.“
All EPDs have undergone the verification process of the Institut Bauen und Umwelt eV (IBU), Berlin. They are publicly available on the IBU platform: https://ibu-epd.com/ veroeffentlichte-epds/.
The plan is to gradually roll out the range of EPDs to other product categories.
With its brands AXOR and Hansgrohe, the Hansgrohe Group, based in Schiltach, southern Germany, enjoys a reputation as a leader in innovation, design and quality within the bath and kitchen industry. Founded in 1901 in the Black Forest, the company gives water form and function with its taps, showerheads and shower systems. Its 120-year history is marked by innovations such as the first hand-held shower with multiple spray types, the first pull-out kitchen tap and the first wall bar to hold a handheld shower.The company holds more than 18 500 active property rights and is synonymous with long-lasting quality products and responsibility towards people
and the environment. Sustainable production of resource-conserving products is central to its business activities around the globe. With 34 subsidiaries and 20 sales offices supplying products in 152 countries, Hansgrohe, its brands and products have won won numerous awards, including more than 700 design prizes since 1974. Its products are found worldwide: on renowned cruise ships, in luxurious fivestar and boutique hotels, in international metropolitan cities,
in extraordinary spas, in exclusive bathrooms of lodges and luxury villas and in public facilities, as well as in countless private homes. The group has seven whollyowned production facilities: four in Germany and one each in France, the USA and China. In 2021, the Hansgrohe Group generated a turnover of €1,365 billion. It employs about 5 400 people worldwide, about 60% of whom work in Germany.
“SUSTAINABLE PRODUCTION OF RESOURCE-CONSERVING PRODUCTS IS CENTRAL TO ITS BUSINESS ACTIVITIES AROUND THE GLOBE.”
The recent Africa Supply Chain in Action (ASCA) Conference saw almost 3 000 African supply chain and procurement professionals from 75 countries gather online to examine the skills, strategies and solutions needed to accelerate African economic development and growth in a post-pandemic new world.
The theme of this third ASCA event was “Borderless: Unleashing Africa’s Potential”. The conference, which is the largest Africafocused online learning, knowledge-sharing and networking event for the supply chain and procurement profession, was launched during the Covid-19 crisis by leading industry organisations Smart Procurement and the Professional Body for Supply Chain Management (SAPICS). It has gone from strength to strength, and this year featured 63 exceptional African and international speakers who shared their expertise and insights with 2 780 registered delegates.
ASCA 2023 was opened with a powerful keynote presentation by Saeed Ande, procurement
director at Lafarge Africa Plc. He shared his vision of a borderless Africa, which would be a continent with free movement of capital, goods, services and people. “Such freedom of movement wouldn’t be limited to economically wealthy countries alone, but would be evenly distributed across Africa,” he stated.
Ande said that measures which would help companies adapt to the constant shift in supply chain since the advent of the pandemic included digitalisation, local sourcing, supplier relationship management, inventory decentralisation and sustainable procurement. Upskilling and knowledge transfer, as well as the diversification of the business’s supplier base, were also critical for organisations striving to adapt and remain agile, in order to survive and thrive in an unpredictable business environment, he stressed.
PROCUREMENT 2.0
“Procurement’s Big Reset: Innovation and Localisation in Supply Chain” was the title of the compelling keynote address by Nigerian-based Azuka Okeke, CEO of the Africa Resource Centre for Excellence in Supply Chain Management. “In Africa, for procurement to better contribute to business effectiveness, it needs to innovate,” she said.
Okeke contended that smart regulations, localisation and e-procurement could help Africa leapfrog procurement practices. “Digitisation’s made
it easier than ever before for procurement professionals to navigate the congested business-to-business [B2B] marketplace with a greater sense of trust. Businesses in Africa would benefit from consumer-like experiences in procurement,” she added.
THE 4IR
“Over the past few years, many initiatives across the globe have successfully consumerised B2B e-commerce and e-procurement,” said Okeke. She cited Dooka as Africa’s first enterprise marketplace and said that platforms like this had the potential to transform indirect procurement on the continent. “They enable access to a broad pool of potential vendors operating under a wide range of business models and their value to buyers extends to customisation, dynamic pricing and indirect spend management, as well as controlling important factors even
for sophisticated procurement functions.
free procurement teams from time-consuming, often repetitive transactional work that fails to take full advantage of their more advanced capabilities.”
The second day of the conference kicked off with an absorbing keynote presentation by Michael Sudarkasa, CEO of Africa Business Group SA. He addressed the issue of Africans producing what they do not eat and eating what they do not produce, outlining how intraAfrican trade could be a catalyst for accelerated African economic growth and development.
The solutions he offered to ASCA delegates included the formalisation of enterprises, value addition, industrialisation and the diversification of markets and tax revenues, as well as infrastructure investment. “We need to focus on formalising small and mediumsized enterprises, adding value to raw materials found in African countries, utilising technology
and modern practices and the intensification of labour,” said Sudarkasa. “We need to explore other markets, both off and on the continent. We need policies to support the growth of different industries to help diversify tax revenues. Government needs to be able to support enabling investment in services and infrastructure,” he stressed.
This year’s ASCA event partners were Absa, Dooka, Tradeshift, Global Trade Solutions, the Chartered Institute of Logistics & Transport, the Cameroon Association of Supply Chain, Logistics and Procurement Experts, the Kenya Institute of Supplies Management and the Fédération Africaine des Associations de Logisticiens.
The conference was highly rated by delegates. “This was an awesome event with excellent speakers. It’s one to schedule in your calendar,” said Lee-Ann Bartlett, management reporting specialist at Mon’e Manez Consulting.
Isaac Akainyah, procurement officer at the Volta River Authority Takoradi Thermal Power Station in Ghana, commended the excellent programme, which he said would empower Africa in diverse ways.
“I found it not only inspiring, but also very insightful. African leaders need to forge a way forward to building sustainable value chains and value networks for this beloved continent,” said Ntsane Lesenyeho, procurement manager at Standard Lesotho Bank.
SAPICS’s mission is to elevate, educate and empower the community of supply chain professionals across Africa.
Since its foundation in 1966, SAPICS has become the leading provider of knowledge in supply chain management, production and operations in Southern Africa. It builds operations management excellence in individuals and enterprises through superior education and training, internationally recognised certifications, comprehensive resources and a country-wide community of accomplished industry professionals. This community is ever expanding and now includes a multitude of associates in other African countries, as well as around the globe. SAPICS is proud to represent the ASCM as its exclusive premier channel partner in subSaharan Africa.
The annual SAPICS Conference is the leading event in Africa for supply chain professionals. The 2023 SAPICS Conference will take place from 11-14 June 2023 at the Century City Conference Centre, Cape Town.
• For further information, tel: 011 023 6701, e-mail: info@sapics.org.za or visit: www.sapics.org
Master Builders Association
Boland
Contact: Daniel Uys
E-mail: info@mbaboland.org.za
Tel: 021 863 3330
Master Builders Association
East Cape
Contact: Greg Steele
E-mail: ecmba@global.co.za
Tel: 041 365 1835
Master Builders Association
Free State
Contact: Stephan Claassen
E-mail: admin@mbafs.co.za
Tel: 057 352 6269
Master Builders Association
North
Contact: Mohau Mphomela
E-mail: info@mbanorth.co.za
Tel: 011 805 6611
Master Builders Association
KwaZulu-Natal
Contact: Vikashnee Harbhajan
E-mail: info@masterbuilders.co.za
Tel: 031 266 7070
Master Builders Association
Greater Boland Contact: Duane Phillips
E-mail: info@mbagreaterboland.org.za
Tel: 023 342 6964
Master Builders Association
Northern Cape
Contact: Graham Andrews
E-mail: info@mbanc.org.za
Tel: 053 832 1762
Master Builders Association
Western Cape
Contact: Roekeya Bardien
E-mail: info@mbawc.org.za
Tel: 021 685 2625
Association of Architectural Aluminium Manufacturers of SA
Contact: Johan Heyneke
E-mail: reception@aaamsa.co.za
Tel: 011 805 5002
Annemerie Coetzee, founder and director of Twinstar Precast, spent her childhood in Jan Kempdorp in the Northern Cape. The family later moved to Pretoria, where her father continued to be her greatest influence, teaching her to strive for only the best.
WHAT SHAPED YOUR CAREER AND CURRENT POSITION?
I fell in love with concrete in 1993 while working for a ready-mix company. I later moved into precast concrete and learnt most of what I know today from Dave Salberg, founder of Salberg Concrete Products, where I worked from 2001-2014.
WHAT ARE YOU MOST PROUD OF, PERSONALLY AND PROFESSIONALLY?
Personally, my children and what they’ve achieved in their careers. Professionally, I’m most proud of starting a business at the age of 48 in a known “man’s world”, making a success of it and seeing it still growing after nine years.
WHAT IS THE MOST IMPORTANT LESSON YOU’VE LEARNT IN BUSINESS?
To look after the people I employ. Happy employees are hard workers.
WHERE WAS YOUR MOST RECENT HOLIDAY AND WHAT MADE IT MEMORABLE?
My family and I holidayed in Norway this past December/January. Seeing the Northern Lights 14 times was absolutely extraordinary, but even better was crossing the Arctic Circle and realising that we were literally “on top of the world”.
• Precast concrete plasticising admixtures
• Ready-mixed concrete plasticising admixtures
• Extended workability polymers
• Set retarding admixtures
• Hardening accelerators
• Viscosity modifying admixtures
The consolidated cement and concrete industry body is soaring to new heights
AFRISAM www.afrisam.co.za
• Form release agents
• Synthetic fibres
• Pozzolan-activity mineral additions
• Permeability-reducing admixtures
• Water-repelling admixtures
• Anti-washout admixtures
debbie.harvey@za.afrisam.com
Become a member –be part of the future
011 670 5941
www.cemcon-sa.org.za
CEMENT & CONCRETE INSTITUTE www.cemcon-sa.org.za
hanlie.turner@cemcon-sa.org.za
011 315 0300
CHRYSO www.za.chryso.com
hannelie@chrysosa.co.za
011 395 9700
DMG EVENTS www.dmgevents.com yolandamtshawu@dmgevents.com
021 137 5963
ELECTRICAL CONTRACTOR ASSOCIATION OF SOUTH AFRICA (ECASA)
www.ecasa.co.za
Erika.vanzyl@ecasa.co.za
011 392 0000
quintin@panmixers.co.za
MODERN
AVOID CONCRETE STRENGTH DELAYS. As winter approaches, the colder ambient temperatures can cause delays in concrete strength development as well as finishing aspects. Rest assured, this challenge can be easily overcome using CHRYSO’s Premia Range of admixtures and demoulding agents.