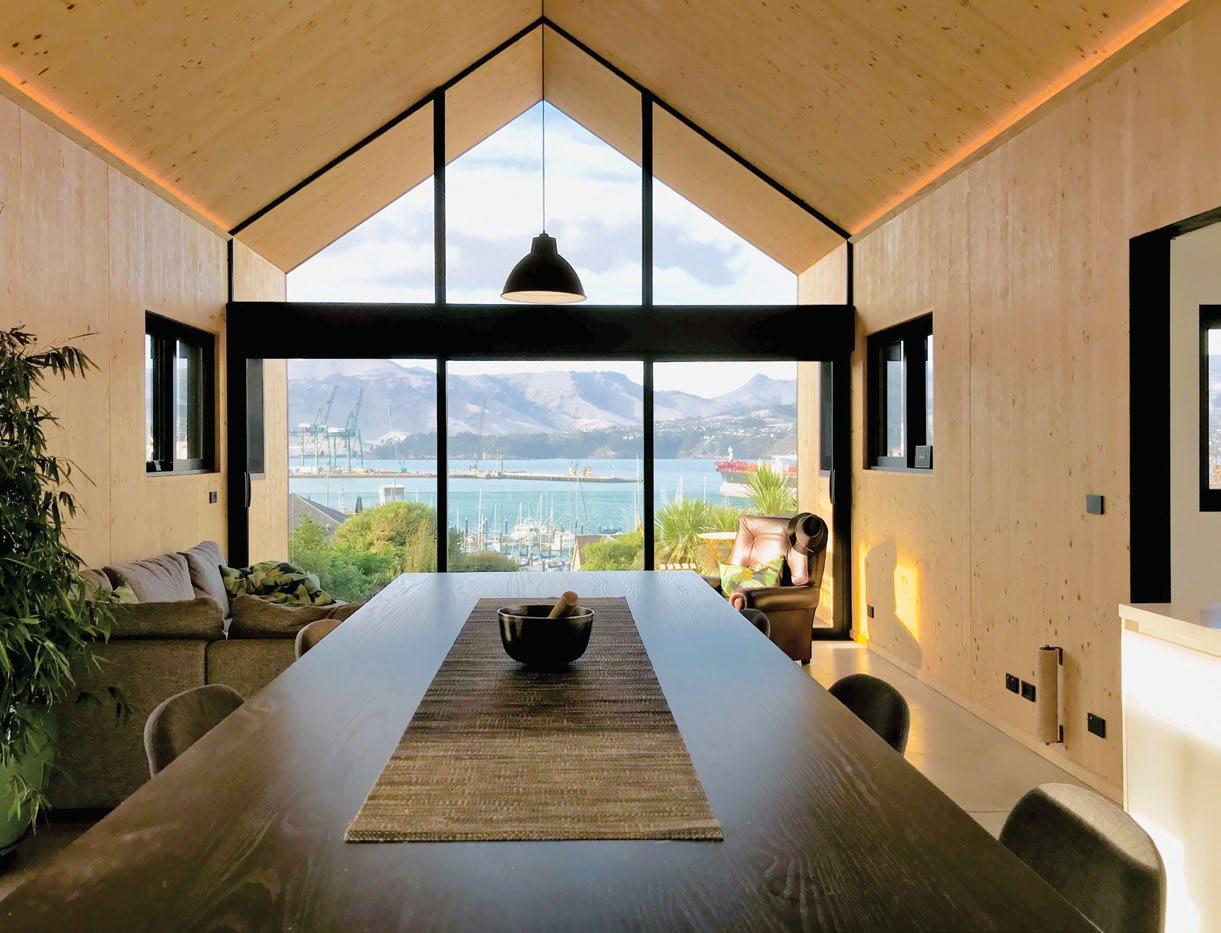
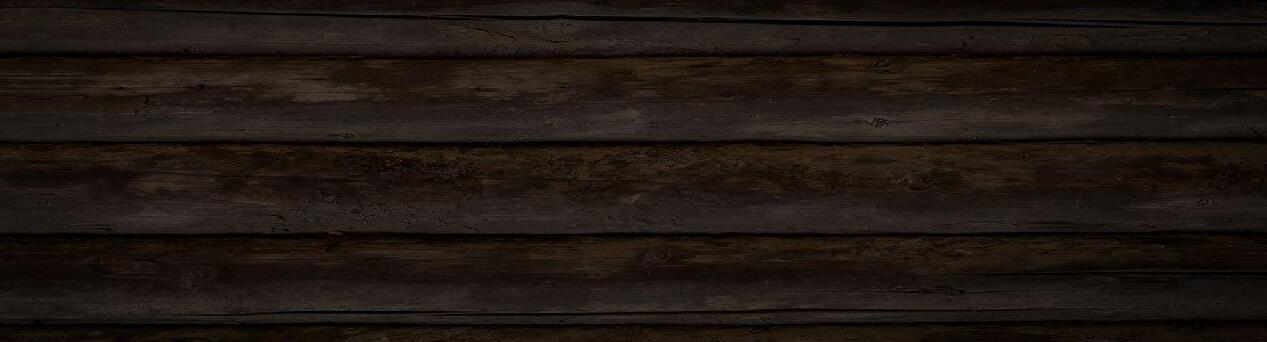
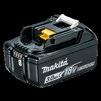
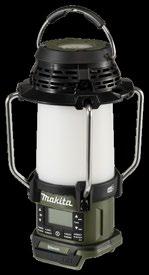
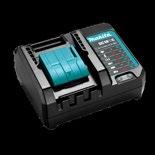
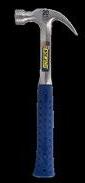
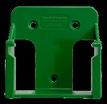
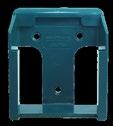
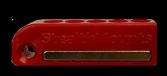

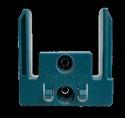
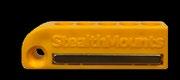

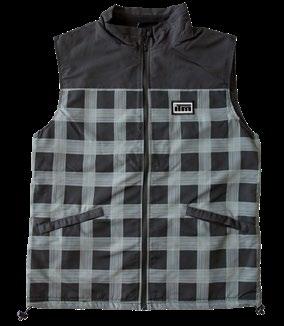
The extraordinary weather events of 2023 are a brutal prelude of what to expect in coming years, and the knock-on effects will have a huge impact on the building industry in New Zealand.
Here’s a summary of important issues builders should consider as the recovery and rebuild programme starts.
Economists recently predicted a slowdown in residential building, but it looks like there will be a pause on that. Any slowdown will likely be confined to geographical areas spared from storm damage.
In the areas most impacted, demand for building services will surge. It’s been estimated that up to 1800 households in Auckland alone will need temporary accommodation while their homes are being repaired or replaced.
In other affected areas, including Northland, Coromandel, Gisborne and Hawkes Bay, the estimated number of displaced people is 10,000 plus.
Moreover, hundreds, if not thousands, of public buildings have been severely damaged and will need remedial work. The most recent estimate to repair the storm damage from cyclone Gabrielle is $10 billion and rising.
▷ The recent extreme weather events in New Zealand will significantly impact the building industry.
▷ Demand for builders in affected regions will surge, and there is a shortage of skilled labour.
▷ Sustainable building practices, including using sustainable materials and designing for energy efficiency, are becoming more important.
Demand for builders in the worst affected regions will likely lead to some re-location of builders from less affected areas, incentivised by higher pay and benefits due to the volume and urgency of work.
The government has also suggested local and national initiatives to build short-term modular accommodation, which could mean constructing temporary “villages” of modular housing or relocating tiny homes and cabins.
The scale of the problem is enormous, and there aren’t enough motels, motor camps or Airbnb’s to accommodate displaced people. Rental properties were as scarce as hen’s teeth before the storms.
In the worst affected areas, many local builders, plumbers and sparkies have been hit hard with damage to their homes, businesses and vehicles, making it almost impossible to do the work they have on their books, let alone the mountain of urgent work ahead. And let’s not forget all the roads that need to be fixed before you can even get to the job site.
There is still a significant shortage of skilled labour in the residential building sector and the wider construction industry. Repairing the widespread damage to infrastructure and the ongoing programme to upgrade infrastructure will put massive pressure on the existing workforce. Economic consultancy Sense Partners released a report last month concluding that New Zealand is experiencing the greatest labour shortage of comparable OECD countries.
“Labour shortages are acute around the world. However, the New Zealand experience is particularly intense,” the report says, due to a combination of an ageing population and a slowdown in immigration. Whereas the Christchurch rebuild was supported mainly by immigrant labour, the labour market worldwide is more competitive now. New Zealand’s attractiveness as a destination for skilled workers is not what it used to be.
Many building materials companies in New Zealand have made significant changes in the way they operate, sourcing raw materials that are sustainably managed and using new manufacturing techniques to reduce overall carbon emissions.
Building companies tendering for governmentfunded projects have to demonstrate a tangible commitment to sustainability, and this attitude is becoming more evident in residential building.
While using sustainable materials to help reduce a home’s carbon footprint when it is first built is a key objective, the home’s design plays a massive role in making the house more energy efficient and sustainable in the long term.
Designers are now paying much closer attention to glazing-to-wall ratios, how a house is orientated
to maximise solar gain in cool months, and how it uses prevailing winds to assist ventilation and cooling in the warm months.
Where solar panels were a ‘nice-to-have’ option in the past, many homeowners now see them as a musthave, with electricity prices increasing every year.
Water usage is another critical area where significant savings can be made. Reducing the number of bathrooms, specifying water-efficient fixtures and fittings and incorporating on-site rainwater harvesting all contribute to reduced water use.
Building requirements will inevitably change to mitigate potential flooding or storm damage in vulnerable areas, but when these changes come into effect is anyone’s guess. It is conceivable that there will be changes to the NZ Building Code to take into account the likelihood of more frequent and more intense weather events.
Regardless of any regulatory changes that may eventually occur, insurance companies will quickly establish new conditions regarding building (or renovating) a home in areas with a consistent history of flooding, land movement or coastal erosion.
In some cases, insurance companies will refuse to insure properties in the most vulnerable locations, and banks won’t provide mortgage finance.
Where a house can be repaired or rebuilt, insurance companies may require that the building be upgraded in some way to avoid future damage. Their policies usually only pay “to reinstate the building to the condition it was in before the damage occurred” and not for improvements that may be required to reduce future risk, such as raising the floor levels of a house.
With over 100 years experience Golden Bay are leading the way in sustainability with EcoSure NZ's lowest carbon GP Cement. EcoSure is helping Golden Bay deliver on a sustainable future for concrete.
The Carbon reduction comes from changes to our manufacturing process including:
Replacing 50% of fossil fuels with alternative fuels (construction wood waste and end of life tyres) Technical innovation of our formulation.
EcoSure is a GP cement that meets NZS3122: 2009
In a natural disaster, Civil Defence conducts rapid building assessments and issues stickers to identify buildings that have been damaged and those that present a severe safety risk. The sticker's colour indicates what access you can have to the building.
Red Sticker
A red sticker means no one is allowed to enter the building because of the high level of risk. This risk might be the building itself, but it might also be from nearby buildings or unstable land. A builder who wants to assess the site for remedial action will need special clearance from the local council.
Yellow Sticker
A yellow sticker means that entry to the building is restricted, except under supervision for a limited time or on essential business. This could be for assessment purposes, which means a builder could inspect the property and evaluate what remedial work is required.
You will need to coordinate any visit with the owners, the council and the insurance company, which will require a detailed quote for any remedial work required.
White Sticker
A white sticker means the building "may be damaged" but is safe to occupy. You can access these sites by arrangement with owners to assess any damage and estimate the cost of remedial work. Many white stickered properties may have sustained minimal water damage in the garage or minor surface flooding.
Initial assessments carried out by Civil Defence are rapid – taking about 20 minutes – and can sometimes be completed by inspectors from outside the building without needing to enter.
After the rapid assessment process, Civil Defence emergency management and council officials can direct the owner of a building to obtain a detailed assessment of the building. These assessments are the responsibility of a building owner and will usually involve input from the owner's insurance company. Insurance companies often have "preferred suppliers" and may direct the homeowner to use tradespeople, designers and geo-tech engineers on their "preferred" list.
If you are assessing a damaged building or plan to do remedial work, you must take all possible measures to safeguard yourself and your team. While SiteSafe has rules and guidelines for work site safety, there are some additional steps you should take when dealing with flood and storm-damaged buildings.
For more information go to: www.chasnz.org/ articles/auckland-flood-remediation-how-to-keephealthy-and-safe-while-working-on-flood-damagedproperty
Flood-damaged homes are particularly challenging when deciding what can be salvaged and re-used. Building Business recently published a story evaluating the pros and cons of demolishing a home versus deconstructing it.
You can read the story here: www.itm.co.nz/demolition
bbi Wood Products has been at the forefront of FSC® certified hardwood decking, leading the New Zealand market with a range of sustainable decking options.
The Forest Stewardship Council® (FSC®) is an international organisation that promotes responsible management of the world’s forests. FSC® sets standards for forest management designed to ensure forests are managed in an environmentally responsible, socially beneficial, and economically viable way. This includes protecting biodiversity, conserving soil and water resources, protecting endangered species, limiting the use of chemicals, and more. bbi recognises the importance of responsible forest management and believes that using FSC® certified timber is one of the best ways to ensure their products are responsibly sourced and produced. By using FSC® certified timber, bbi demonstrates its commitment to responsible forest management and the protection of the rights of workers and local communities, as well as a focus on the environment.
bbi started the shift to only supplying FSC® certified Kwila and Garapa hardwood decking in 2014. With the strongest commitment to ensuring responsible forestry practices forever, bbi became one of the leaders of FSC® certified decking. They wanted the communities, wildlife and all those who use and live within the forests to have a better life. The demand for building low-cost housing with a fast turnaround time is one of the biggest drivers of unsustainable decision-making. bbi aims to help grow the knowledge of responsible forestry within the local communities and promote responsible building practices. bbi strives to be responsible in all aspects of the business, going beyond supply chains and promoting eco-friendly practices throughout the company.
The building and construction industry accounts for 20% of the C02 emissions in New Zealand. With landfill significantly contributing to CO2 output, reducing this is one of the critical steps in the fight against climate change. Construction and demolition waste makes up 40-60% of the total waste in New Zealand landfills. bbi is dedicated to reducing wastage sent to landfill and C02 emissions by offering finger-jointed decking options known as bbi® QuikDeck®. bbi QuikDeck® allows builders to get the exact lengths needed, reducing excess.
With a continued focus on responsible practices, bbi will be shifting to an eco-friendlier packaging option, ensuring that the sustainable process continues through to the product’s end-of-life. bbi is committed to providing a diverse selection of FSC® certified plywood while expanding the range of sustainable and environmentally conscious building products.
Like so many other fishers, I love to catch fish. There is something deeply satisfying about catching a fish and taking it home to feed friends and family. I believe this feeling stems from our evolution. It is only in the last couple of hundred years that we as humans have been able to survive by earning money and purchasing food. Before that, we needed good hunter-gatherer instincts.
To ensure we survived as a species, we needed good instincts to kill, but we also needed good instincts to conserve because if all the fish were taken, all the animals were killed, or the entire crop harvested, there would be no food for tomorrow.
So for those of us that have a passion for fishing, this love of the ocean and it’s inhabitants can, in part, be put down to instinct. Therefore, the people that fish for the love of it are the guardians of the ocean; recreational fishermen are at the forefront of protecting fish stocks from commercial over-fishing where fish are being exploited for commercial gain, with little regard given to sustainability.
Through the show, we can inspire people to get into fishing, and we can also impart tips and advice to existing fishers to help them catch more fish. At the outset, encouraging more people to fish and sharing effective fishing techniques seems to go against our conservation ethos, but here’s how it works.
The more people that can go out and successfully catch a fish to take home, the more people have that connection to the marine environment and, therefore, will want it protected. Sure, they will take a few fish in the process, but catching fish by hook and line to feed family and friends has been sustainable for thousands of years; it is part of the marine ecosystem. And all the recreational catch combined is just a fraction of the 400,000 tonnes taken commercially in New Zealand every year.
Even so, we encourage fishers to only take what they need; “just enough for a feed” is a catch line. We also encourage the release of the larger breeding fish and help with fisheries research by tagging and releasing fish. While the recreational fishing take is comparatively small, it is still significant, and two wrongs do not make a right, so we all need to do our bit.
For a start, we do not preach to them. People enjoy fishing because it is an escape from their busy lives, recreational time is precious, and I’m not likely to get a good response if I stand up and tell people how they should spend their time fishing. So instead, we show people by releasing big fish, and I explain the importance of these bigger fish to the reproduction cycle of the species. If you want a trophy (and let’s face it, most of us do), take a photo before letting it go. That way, you have captured that moment in time to savour forever.
By demonstrating how much enjoyment and satisfaction you can get by catching a feed of fish, releasing a big fish or tagging and releasing a fish, viewers will invariably try it themselves. But we still need to ensure that when we take fish responsibly for food or take the occasional big fish as a hardearned trophy, we do it unashamedly; after all, killing fish is as natural as breathing.
by Matt Watson FishermanAt DuluxGroup, sustainable practices are at the heart of our business. Our Paint Take-Back service was established in 2009 and is a service we are proud to offer as part of our commitment to the environment. Simply return your paint packaging or unwanted paint to any Dulux Trade Centre for Paint Take-Back pick up. Some exclusions apply. Visit painttakeback.co.nz for more information
Be a part of Dulux’s commitment to sustainability by always returning your used packaging.
Our 10 and 15L plastic pails are 100% recyclable in New Zealand by our packaging partner.
100%
1.6M*
units of plastic and steel paint packaging had been recycled through the Paint Take-Back Programme since it started.
50%
When you return your plastic pails through our Paint Take-Back collection points, you’re ensuring that these containers get another life.
With your help, we can reach our goal of incorporating at least 50% post-consumer recycled content in all of our pails by the end of 2025.
As more recyclable pails get returned to us, the more we can ramp up the recycled content in our packaging.
LYTTELTONSustainability is at the heart of the Dulux business, and the drive to do better comes from its partners, customers, and employees. Dulux believes in making positive sustainability impacts with industry-leading safety practices and reducing harmful chemicals while focusing on less landfill waste and contributing to local communities.
Practising sustainability every step of the way
Dulux focuses on the long-term sustainability of the substrates that the paint covers. Coating products are about protection, durability, and extending the useful life of a building or a substrate. On exteriors, it is by protecting the surface from UV, salt, and other climate issues; and for interiors — making coatings that can be washed many times, keeping surfaces looking clean, fresh, and protected for longer.
“Preserving the useful life of the surfaces translates into a longer period between re-coating — resulting in fewer resources used as well as better-quality products, sustaining the built environment”, says Heather Goode, Dulux’s Technical & Quality Manager.
In New Zealand, the Environmental Choice (ECNZ) eco-label is one of the most recognised labels in steering the coatings industry in the right direction regarding waste, chemicals of concern, and volatile organic compounds (VOCs) reduction. In 2022 alone, Dulux added six new products to the ECNZ certification. Dulux UltraAir® is one of the two product ranges recognised by Global GreenTag, a third-party eco-labelling scheme that uses the principles of the United Nation’s sustainability goals to assess a company’s production life cycle and finished products.
Dulux is committed to a sustainable future
Dulux is involved in several programs to ensure it looks after the communities in which it operates. The Dulux Paint Take Back Service, established in 2009, enables the return of left-over paint and packaging to Dulux to be recycled, reused, or disposed of in an environmentally responsible manner.
Water-based paints are donated for uses such as graffiti abatement, while solvent-based paints are sent for solvent recovery or responsible disposal. In addition, Dulux and the Department of Conservation (DOC) Te Papa Atawhai have partnered since 2013 to protect and restore DOC and community huts and buildings. Dulux is proud to support DOC in protecting the natural and historic heritage sites that have inspired the Dulux Colours of New Zealand range.
Cabot’s Timber Finishes, part of the DuluxGroup, is a leading woodcare brand in New Zealand. Cabot’s is an official partner of Trees That Count and has funded the planting of thousands of native trees across the country in its mission to protect the timber for future generations to enjoy.
Dulux has been part of the New Zealand community since 1939, manufacturing locally and striving to sustainably manage its financial, environmental, and social impacts. Dulux is committed to its safety and sustainability vision of “A Future Without Harm” for the success and well-being of its business, stakeholders, and the mana whenua.
E64
• Black lever handle suitable for residential use
• Black lever handle suitable for residential use
• No handing required
• No handing required
• Concealed screw fixing
• Black lever handle suitable for residential use
• Hole prep size 54mm
• Hole prep size 54mm
• Supplied with an adjustable 60 or 70mm latch
• Hole prep size 54mm
• Supplied with an adjustable 60 or 70mm latch
• Door thickness 35 to 45mm
• Supplied with an adjustable 60 or 70mm latch
• Door thickness 35 to 45mm
E64 0800 279 582
E64 0800 279 582
• Door thickness 35 to 45mm
• Concealed screw fixing
• No handing required
• Entrance, Passage, Privacy and Wardrobe functions also available
• Entrance, Passage, Privacy and Wardrobe functions also available
• Concealed screw fixing
• Black finish
• Entrance, Passage, Privacy and Wardrobe functions also available
• Black finish
• Black finish
www.sylvan.co.nz
0800 279 582
www.sylvan.co.nz
www.sylvan.co.nz
Relax. It doesn't mean more paperwork for you right now, but it's a good idea to understand what an EPD is because it will inevitably become an essential part of how we build in the future.
EPD certification is like an international stamp of environmental approval for building products, encouraging manufacturers to make genuine and measurable commitments to sustainable production.
EPDs support carbon emission reduction by making it possible to compare the impacts of different materials and products to select the most sustainable option.
EPD Australasia was established in 2015 by New Zealand and Australian life cycle professional associations (LCANZ and ALCAS), with seed funding from other groups, including BRANZ and the Sustainable Steel Council.
While it is unlikely that EDPs will be necessary for private residential building in the short term, they may become a requirement soon for publiclyfunded buildings such as schools, healthcare facilities, government buildings and public housing.
In the European Union, all public procurement bodies must use EPDs to assess the environmental footprint of products, and many other countries follow a similar track.
The NZ Government has already signalled that EPDs will likely be adopted here; they have already been included in the building environment rating scheme, Green Star New Zealand www.nzgbc.org.nz/greenstar
▶ EPDs provide information on the life-cycle carbon footprint and other impacts of a product or service based on a life-cycle assessment (LCA).
▶ The independent, third-party verified data that EPDs provide is valued across the supply chain, from designers to developers.
The organisation has registered 64 EPDs for Australian and New Zealand companies and industry associations since its inception, and over 90% of those are for building and construction products.
▶ Whole life carbon includes the embodied carbon impacts arising from the extraction, manufacture and transportation of construction materials and the building's operational energy needs.
With demand from eco-minded homeowners increasing, building sites are going green. But how do you responsibly deal with the waste that building produces?
When you’re dealing with polystyrene products, that is where EXPOL come in. EXPOL is committed to the environment, and its seven zero-waste factories recycle 400 tonnes of polystyrene annually.
So how can EXPOL help you?
Construction and building site recycling EXPOL has a Construction and Building Site Recycling Programme for builders who have polystyrene waste on their building sites. If the products are from EXPOL, they will collect it from the job site and recycle it.
Thirdly, bag up offcuts as soon as possible to prevent them from being blown around or trampled into the soil.
Finally, book a collection from EXPOL to collect and recycle your polystyrene waste.
A big part of sustainable building is choosing the right materials from the outset. EXPOL’s expanded polystyrene offers exceptional eco-credentials and is ideally suited to the new generation, eco-friendly building projects.
1. Using the bags provided, bag up your polystyrene waste.
2. Request a collection via email, phone, or EXPOL’s Recycling App.
3. An EXPOL truck will collect it from your site.
How to handle polystyrene responsibly on site When handling polystyrene on-site, EXPOL has put together some recommendations to ensure the local environment is not impacted.
Firstly, ensure that polystyrene is stored correctly. Have a flat, accessible storage area to stack product and ensure it is weighted down, especially in windy conditions.
Secondly, keep the site clean when cutting polystyrene. Use a fine tooth saw or a cutting device that reduces dust – a chainsaw is not recommended. Cut your product in a confined area to minimise the spread of dust.
A massive 75% (by volume) of the products that EXPOL manufactures use recycled content. These products are built tough and will last for the life of your build. However, when their use has ended, they can be recycled repeatedly to make new EXPOL products. The ability to continually reuse and recycle these materials in manufacturing makes it a truly sustainable product.
EXPOL is proud to responsibly manufacture products that help Kiwis live in drier, warmer, more energy-efficient homes. If you want to learn more about the sustainable practices at EXPOL and their environmental commitment, visit the resource centre at expolearth.co.nz or call on 0800 86 33 73.
At EXPOL we care about the environment and have developed a programme to help you keep your building site clear of polystyrene waste.
At EXPOL we’ve made a commitment to the environment and take responsible environmental manufacturing seriously. With our focus on a true closed-loop manufacturing process we’ve introduced EXPOL Earth - a resource centre which provides information on our recycling initiatives.
All EXPOL polystyrene products are recyclable. 75% of the polystyrene products (by volume) we manufacture contain recycled content ranging from 10% to 100%.
EXPOL’s range of recycled content products include: EXPOL Tuff Pods, EXPOL StyroDrain, EXPOL QuickDrain, EXPOL ThermaSlab, EXPOL UnderFloor.
This initiative is specifically designed for the construction and building industry who purchase EXPOL product.
Any polystyrene construction waste is collected from the building site and we close the loop by recycling it into other EXPOL product.
Collection of polystyrene waste is easy with EXPOL.
At EXPOL the delivery of your polystyrene construction products is not where it ends. We provide a polystyrene waste collection service via our Recycling App, phone or email. www.expolearth.co.nz
The days when sustainable house design was just a cosy, nice-to-have will soon be behind us. The government has flagged significant upcoming changes in its Building for climate change programme and other workstreams. It’s time for industry to start limbering up for the challenge to come.
The benefits of good sustainable design have been understood since the 1970s, but they are still far from standard in many houses in Aotearoa New Zealand. You don’t need to look hard to find new homes where the carbon footprint is enormous, the north-facing garage steals the winter sun, the large south-facing glazing makes for chilly nights, and the power bills are eyewatering.
The government says that the newly increased insulation requirements to comply with Building Code clause H1 Energy efficiency aim to reduce the energy needed to heat new homes by up to 40% compared with the previous requirements.
What is on the horizon is much more substantial, including:
▶ new requirements to measure and put a cap on the whole-of-life embodied carbon emissions of new buildings
▶ an aim by MBIE to reduce building-related emissions by 0.9–1.65Mt CO₂-e (million tonnes of carbon dioxide equivalent) over 2022–25
▷ New Zealand's Building for Climate Change program aims to reduce building-related emissions and improve thermal performance.
▷ Mid-size companies may face challenges in pursuing sustainable design without sufficient resources or shareholder pressure.
▷ Financial support is available for sustainable building initiatives, such as green loans and subsidies for meeting sustainability standards.
▶ new requirements that will improve the thermal performance of walls and window installation
▶ potentially, new requirements to prevent buildings from overheating.
The H1/AS1 schedule method of determining insulation needs will likely be withdrawn, and modelling will be required for either embodied carbon or energy use or potentially both.
A lot of the progress on sustainability seems to be found among the largest and smallest companies. ‘The larger you are, the more you have a target on your back,’ Jeff Vickers of sustainability consultants thinkstep-anz told Build. He points to large players with overseas owners where some of the initiatives around sustainability are being driven by decisions made in overseas head offices. ‘The reality is that, if you are a large publicly listed company, then you have to act,’ he says.
‘At the same time, we are seeing a lot of great work among small companies, often still run by the founder who either has a personal ethos or passion for sustainability or who is developing environmentally friendly products.
‘It is often the mid-size companies that fall through the cracks – they don’t have the resources or the shareholder pressures to change the way they operate.’
Andrew Eagles of the New Zealand Green Building Council (NZGBC) says that ‘many people struggle to understand the scale of what we have to achieve’. He points to BRANZ/Massey University research that found newly constructed houses were responsible for five times more emissions than they should be if our houses are on track to reach a netzero goal by 2050.
Should the changes be led by clients or industry?
There is no doubt that some clients request sustainable buildings. BRANZ is hearing from around the country that a growing number of clients, including families looking to build a new house, are bringing up the topic of carbon footprints with their designer. But their limited technical knowledge means that the industry can’t sit back and let clients be the primary drivers for sustainability. ‘Encourage clients to use thermally broken window frames if you can,’ says Andrew Eagles. ‘Encourage heat pump water heating, efficient taps, LED lights.’
The government is already moving the industry with its own actions, notably with Kāinga Ora committing to all its new homes being built to at least 6 Homestar standard (with 10 being the highest).
At the large-scale end of the industry, there are cases where a more sustainable way of doing something is possible but just not financially viable. Jeff Vickers points to this being one of the big challenges for basic materials such as concrete or steel.
‘The big challenge is not that companies lack the will to act or lack the capital to make the investment required – it is just that the operational costs of a more sustainable manufacturing process are so much higher that you can’t make a business case for them.’
He uses the example of moving away from traditional ways of smelting steel to using hydrogen as a reductant, producing emissions of water rather than carbon dioxide. It has been shown to be technically feasible but hugely expensive. ‘If a company takes this path, but its competitors keep to the traditional approach, they’ll be stuffed by the competition because they have far higher operating costs.’
These sorts of moves are only likely to be made when enormous incentives make them financially feasible. Jeff Vickers says, that if a government opted to ‘crash the price of green electricity’, it would provide an incentive to produce hydrogen using electricity and elsewhere to shift processes currently using natural gas over to electricity.
At the lower level, there are a surprising number of potential sources of financial help for the industry and their clients. The ANZ Business Green Loan is one example, with a discounted interest rate for green buildings, sustainable land use and the like that is 150 basis points below the standard floating rate.
A sustainable 9 Homestar home with a view out to Lyttelton Harbour.Other banks also have or have had offerings in this area. Kiwibank offers support for sustainability on a case-by-case basis, with lending rate discounts of around 50–100 basis points for commercial green buildings, residential buildings with at least an 8 Homestar standard and so on.
ASB had a Back My Build product that gave customers a $3,000 cash rebate if the house they built was 6 Homestar rated or higher – effectively subsidising the margin that building to this level costs.
Territorial authorities are also offering support. Wellington City Council has an Environmental and Performance Accessibility Fund that can support eligible projects for up to $500,000 (commercial developments) and up to $2 million (residential developments). In the residential category, for example, $15,000 per unit (self-contained residence) is available up to a maximum of $1 million for homes that reach a 7 Homestar rating.
The government has clearly flagged that major changes are on the near horizon in the form of its Building for climate change programme. Computer modelling for things like energy use and carbon footprint will eventually be the norm for new buildings, including houses.
While much of the detail still must be worked out, there are already a host of tools that people can experiment with to see what it’s all about.
BRANZ has a cluster, including LCAQuick, which calculates the environmental impacts of any building designs, with a focus on homes and offices.
NZGBC has the Homestar Embodied Carbon Calculator tool – freely accessible on its website – which helps calculate the estimated carbon footprint of a dwelling.
‘One of the really important things for us is helping people prepare for the implementation of Building for climate change,’ Andrew Eagles says. ‘Change is going to happen at a faster rate in the future. We are keen to help people get up to speed now, building the skills and knowledge they will need before they have to use it. Our sector can be an agent for change, inspiring and helping people.
‘That should mean that, instead of alarm and the industry lobbying for delays in implementation, people can say “Yep, I know how to do that. I’ve got that”.’
by David Hindley Freelance Technical WriterThis article was first published in BRANZ Build magazine issue 193, December 2022 www.buildmagazine.co.nz
1. Use passive solar design to reduce the heating/cooling energy that building occupants would otherwise need to buy to stay warm or cool.
2. Think in terms of whole of life. For example, some materials may have slightly lower embodied carbon than others but need to be replaced two or three times over the life of a building. Another option with slightly higher embodied carbon at the start that doesn’t need replacing may be a better choice in the long run.
3. Ask your suppliers about more-sustainable products. For example, talk to your concrete supplier about providing concrete with supplementary cementitious materials, which can reduce the embodied carbon in concrete by 20% or more.
4. Minimise the building site waste that goes to landfill. Separate waste and recycle as much as possible.
5. Don’t buy or specify appliances that run on fossil fuels.
6. Use the tools and resources that are freely available to help you. BRANZ has the Level website and the carbon tools and calculators on the main BRANZ website. NZGBC also has good resources.
20 BRANZ
MBIE-backed research finds low-carbon buildings can be built at no additional cost if clever design choices are made.
To reach our climate goals, Aotearoa New Zealand, needs to build houses with smaller carbon footprints. MBIE’s Building for Climate Change (BfCC) programme proposes new regulatory requirements to cap both operational and embodied carbon in new buildings.
While there’s no doubt that energy-efficient buildings are cheaper to heat and cool, MBIE wanted to know if low-carbon buildings would come at a cost premium at the initial construction stage.
It commissioned thinkstep-anz, engineering consultancy Mott MacDonald and quantity surveyors Prendos to investigate if it is possible to achieve BfCC’s proposed carbon savings without increasing the upfront cost of construction.
Looking at more than 20,000 unique combinations of locally available building elements for residential homes, the research found that reducing the carbon from building materials will typically come at a higher upfront cost.
However, an opportunity exists to reduce or eliminate this additional cost by optimising the building’s design.
Lightweight building design often equals low embodied carbon design. The widespread use of lightweight timber framing and lightweight cladding materials throughout New Zealand means that our homes have a lower-carbon starting point and less potential to reduce embodied carbon than many other countries.
Reductions in carbon footprint per square metre are, therefore, likely to be incremental rather than radical step changes.
While homes with lower embodied carbon were typically more expensive, there was significant variation in building costs for the same level of decarbonisation.
Without changes to building design, reducing the upfront carbon footprint of the reference building selected for this study by 30–40% was achievable through the choice of currently available building elements. However, these reductions come at a price premium of 5–10% per square metre of floor area on average.
The study also showed that, through optimising the design, savings of up to 36% in upfront carbon and 12% in whole-of-life embodied carbon compared with the reference building were possible for no additional upfront cost.
The study found there is no silver bullet to reduce operational carbon, embodied carbon and upfront cost simultaneously. One effective strategy to reduce embodied carbon was to substitute a concrete slab for a suspended timber floor, but this had trade-offs in operational energy performance and upfront cost in some cases.
The construction industry has an important role to play in implementing tools that identify optimal outcomes at the building level. Designers and builders should work with suppliers and demand low-embodied-carbon building systems (such as floors and windows) with equal or better thermal performance than existing systems.
by Jeff Vickers Technical Director, thinkstep-anzThe study used a single reference building from the LCAQuick library as the basis for analysis. It is a single-level detached home with a gross floor area of 218 m² and an internal living area of 170 m². It has 4 bedrooms, 2 bathrooms, 2 living areas, a kitchen and laundry and an internal garage.
The study modelled operational energy/ carbon and embodied carbon for the reference building with different levels of thermal performance and material combinations.
Modelling was done at system level – floors, roofs, walls and windows – rather than material level. Operational energy modelling was done in IES in accordance with NZS 4218:2009 Thermal insulation – Housing and small buildings. Embodied carbon values come from BRANZ’s CO₂RE v2.0 with additional modelling in LCAQuick v3.5.
Overall, 22,032 unique combinations of building elements were considered:
• 6 roof options
• 7 envelope wall options
• 6 internal wall options
• 12 floor options
• 3 window options.
There were also regional scenarios for operational energy/carbon modelling in Auckland, Wellington and Christchurch.
Operational carbon – carbon emissions from energy and water used in the building during its operational life.
Embodied carbon – emissions from the building’s materials and products, the construction process, construction waste disposal, maintenance and refurbishment throughout the building’s life and disposal at the end of the building’s life.
The report Cost-neutral, low-carbon residential construction is available at www.thinkstep-anz
J-Frame is a laminated veneer lumber (LVL) engineered wood product –engineered straight, strong and durable. Suitable for a wide range of uses, including residential and commercial framing and truss systems. It is made from 100% renewable Radiata Pine and proudly manufactured in New Zealand.
J-Frame is CodeMark certified as compliant with the New Zealand Building Code. It is manufactured for consistent strength, stiffness and stability –making it resistant to warp, twist and bow. The A Bond is proven to withstand exposure to moisture and weather and long-term structural performance requirements.
In a world where environment and sustainability are now a priority, it is reassuring to know that wood will always be with us. At Juken New Zealand (JNL), our philosophy and business purpose is “Wood for Life”.
How do you get wood from trees without losing forests? The answer lies in intensively managed forests, and JNL operates theirs to world-class sustainable standards.
In everything from land preparation to harvesting and replanting, JNL standards have been recognised by FSC® and ISO certifications. JNL has 40,000 hectares of planted forests in two regional locations – East Coast and Wairarapa and operates broadly on a 30-year rotational cycle.
This careful stewardship provides JNL with a continual and sustainable supply of raw wood transformed into high-quality products in their processing mills. It is all achieved without touching natural indigenous forest resources.
As both a forestry company and a manufacturer, JNL’s success is built upon its environmental commitment and an overall ethos that is environmentally friendly.
JNL is replacing the use of non-sustainable hardwoods around the world with engineered and solid wood products from sustainably grown sources. They also strive for zero pollution and zero waste in all that they do.
With over 30 years of experience, JNL’s internal best practices are supported by internationally recognised environmental standards, including the Forest Stewardship Council (FSC®) and ISO quality and environmental standards (ISO9001 and ISO14001).
JNL work alongside their local communities and always aim to minimise environmental impact. Some examples include bark used for garden mulch, chemical containers are recycled, forest areas of significance are protected and monitored, and almost all of JNL’s mill energy requirements are fuelled by renewable, sustainable wood residues.
There is a genuine commitment from JNL to ensure they make a lasting impression on the environment and that their customers can feel good about JNL products and the processes involved in growing, producing, and delivering.
Engineered by Juken New Zealand, J-Frame is a laminated veneer lumber (LVL) wood product manufactured with quality in mind from 100% sustainable forestry – and it’s about to make your next building project easier.
Engineered by Juken New Zealand, J-Frame is a laminated veneer lumber (LVL) wood product manufactured with quality in mind from 100% sustainable forestry – and it’s about to make your next building project easier.
Engineered straight, strong and durable, J-Frame is suitable for a wide range of uses; including residential and commercial framing and truss systems. Specify J-Frame for your next project and discover for yourself the difference it can make to the speed of your build. For more information and specs go to jnl.co.nz scan
to learn more
Engineered straight, strong and durable, J-Frame is suitable for a wide range of uses; including residential and commercial framing and truss systems. Specify J-Frame for your next project and discover for yourself the difference it can make to the speed of your build. For more information and specs go to jnl.co.nz scan me to learn more
Every builder knows certain species of wood have unique characteristics making them especially suitable for a specific job: superior strength, incredible hardness, and stunning appearance. But one overriding consideration is critically important when you make your choice. Your conscience.
With recent extreme weather events in New Zealand, there is little doubt that climate change exists. Anything we can all do to reduce emissions and improve the sustainability of the building materials we use is a responsibility no one can ignore.
ITM has adopted a policy of sourcing the most sustainable timber in the world. We fully support the organisations and certification criteria that ensure our building supplies are environmentally friendly.
The Forest Stewardship Council® (FSC®) is an international, nongovernmental organisation dedicated to promoting responsible management of the world's forests.
FSC certification confirms that the forest is being managed in a way that preserves biological diversity, benefits the lives of local people, and ensures sustainable economic viability and healthy, resilient forests for future generations.
With timber from FSC-certified forests, there's no net forest loss over time. This allows forest ecosystems to continue absorbing carbon dioxide and regulating the earth's climate.
Imported timber sustainability mark
New Zealand currently leads the world in ensuring that imported hardwood is ethically sourced. ITM deals exclusively with imported hardwood suppliers that have achieved global FSC environmental certification, supported by the New Zealand Imported Timber Trade Group (NZITTG).
Destruction of tropical rainforests worldwide is accelerating due to the ever-increasing demand for timber. Unsustainable management of these resources and Illegal logging results in the loss of livelihood for millions of people worldwide and is the single most significant contributor to greenhouse emissions.
Around 20% of all emissions in the world are a result of deforestation.
What practical steps can you take on-site to minimise plasterboard construction waste?
If minimising waste is a priority on a project, it’s worth clearly defining:
• Who monitors and implements the waste minimisation initiatives?
• Do clear waste minimisation targets exist?
• Are waste streams regularly reported using data from the waste collection service provider?
• Are waste minimisation targets included in the project contracts and subcontractor agreements to help ensure they remain a priority on the project?
The person responsible for installing the plasterboard should also be the one who is paid to do the site measure and specify the plasterboard sheet lengths and volumes required. An experienced installer uses the most efficient sheet sizes to reduce offcut wastage while guiding other potential installation considerations such as the most efficient delivery method.
Specify on the design plans for the plasterboard to be installed horizontally on walls where possible. This provides a greater opportunity for sheet lengths to be ordered, which work more closely with the total room.
One option worth considering is to move the sheet joint away from corner openings and use a floating joint such as shown here.
Alternatively, consider including a control joint at the edge of the opening for applications prone to high degrees of movement, such as transport homes.
For compact sites, it may be worthwhile considering an early delivery of the plasterboard into an area that’s difficult to access once the building is closed. It may also be best to use a Hiab lift delivery of plasterboard to reach those hard to get to places before installing a window and reduce the need, later on, to manoeuvre long sheet lengths in tight spaces.
Engage with the main contractor on-site to understand their approach to managing waste streams. One option could be separating the main waste streams into common groups, such as plasterboard and treated and untreated timber, to allow waste to be more easily collected and recycled by waste providers.
Horizontal fixing can also reduce the number of sheet joins in a room, reducing the amount of stopping required.
Another potential source of plasterboard waste is where full plasterboard sheets are used around door and window openings to reduce the risk of cracking in the corners.
It’s also worthwhile considering the plasterboard wastage rate factored into the overall project cost. A typical plasterboard wastage rate is around 10%; however, live site trials indicate this figure could be closer to 15%, meaning additional unaccounted-for margin lost for the installer1
For more information on GIB® plasterboard sustainability visit www.gib.co.nz/sustainability
The construction sector has a very important job: cleaning up our act with carbon emissions and waste. Globally, the construction and operation of buildings account for 36% of global energy use, 39% of energy-related C02 emissions and 30% of all waste to landfills. For the health of the planet and the future of humanity, this has to change.
The team at Kingspan recognise and embrace the need to be more environmentally responsible. Under the umbrella of their Planet Passionate programme, Kingspan has introduced initiatives that are contributing to a more sustainable and less wasteful construction sector in New Zealand.
Planet Passionate is a 10-year global sustainability programme to tackle climate change, increase circularity (reuse and regeneration) and protect the natural world. In New Zealand, Kingspan has set ambitious targets to drive carbon out of its business, increase recycling of waste, and accelerate participation in the circular economy.
During 2022, the Kingspan Auckland plant achieved the following:
The scheme and electricity source are verified by New Zealand Energy Certification System.
Achieved by recycling polypropylene building membranes manufacturing waste.
Reducing vehicle emissions
11% of Kingspan’s company cars are now fullyelectric.
For the year ahead, the team at Kingspan Thermakraft aim to advance these gains and introduce new initiatives that will reduce the environmental and climate impacts of the construction industry.
When you choose Kingspan Thermakraft products, you’re joining the good fight and helping to shrink the carbon footprint of your construction business. Read more about Kingspan Thermakraft’s approach to sustainability, innovation and performance at kingspaninsulation.co.nz
Southern Pine supply New Zealand mouldings and weatherboards for generations to come.
New Zealand Radiata Pine is a renewable, natural resource which stores and sequesters carbon making it ideal for building New Zealand homes.
The framework of Environmental, social, and governance (ESG) provides an opportunity for businesses to look at their sustainability impacts. Laminex New Zealand has made strong environmental commitments, and now there is a growing focus on the company’s social impacts and opportunities for development in this space.
Laminex commits to a 30% reduction in carbon emissions by 2030. A carbon roadmap is in place to hold the business accountable for reaching this target. An initiative from this roadmap was the installation of one of New Zealand’s largest solar roof systems at the Laminex Hamilton operational plant. It generates 26% of the site’s energy use annually. Beyond energy efficiency improvements, Laminex intends to decarbonise natural gas from a key operational site.
Laminex is committed to making a positive impact on the communities they operate within. The business believes partnership is required to make the most significant impact. That is why Laminex has partnered with All Heart NZ and is looking to work with not-for-profit organisations such as Habitat for Humanity to donate obsolete products. In 2022, Laminex donated 8,400kg worth of product. This resulted in not only diverting waste from landfill but giving good product a second life and home within the community.
In collaboration with Unitec – Te Pukenga’s School of Architecture, Laminex is assisting students to explore the practical feasibility of a seamless pathway from digital design to digital fabrication. Undergraduate and graduate students designed a ‘feature piece’ for the Ngākōroa School, a brand-
new primary school in Auranga. The design needed to consider Unitec – Te Pukenga and Ngākōroa School’s shared guiding values and principles. Bachelor of Architecture Studies student Kyah Suckling received a Unitec Scholarship to fabricate the project for the official opening of Ngākōroa School.
A partnership is a conduit to moving the dial for positive change. With this ethos, Laminex will continue to explore partnership opportunities to work together to deliver better environmental and social outcomes.
• Easy to install
• Can be used in wet areas
• Codemark certified
There have been several changes to the Building Code that license building practitioners need to get up to speed with. We’ve outlined some of the key points from the 2021 and 2022 updates to be aware of.
The MBIE Building Performance team updates the acceptable solution and verification method Building Code documents regularly. We do this to ensure that the system is effective and keeps pace with modern methods of construction, products and technologies, and that our buildings are safe, healthy and durable.
These changes directly impact your work, so it’s vital that you find out about them as early as possible and get the opportunity to let us know what you think. When we are proposing changes to the Building Code regulations or to the acceptable solutions and verification methods, we run a consultation first. This is your chance to submit feedback on the proposed changes.
There have been several changes recently.
In 2022 we consulted on changes for plumbing and drainage, protection from fire and structural stability of hollow-core floors. You can read the proposal documents on our website www.mbie.govt.nz/haveyour-say/building-code-update-2022
The proposal that received the most interest was the changes to protection from fire for residential buildings. The plumbing and drainage proposals for lead in plumbing products and water temperatures also received a significant number of responses.
The Building Performance team have made decisions on two parts of the proposed changes to the Building Code - lead in plumbing products and the structural stability of hollow-core floors.
The Building Performance team has removed the deemed to comply pathway in B1/VM1 for the design of the supports for hollow-core floor systems to minimise the chance of poorly designed systems being specified in new building work.
The amended Verification Method B1/VM1 will be published along with other documents in November 2023. This change for hollow-core floor systems will take immediate effect when published – there will be no additional transition period.
The Building Performance team is amending Acceptable Solution G12/AS1 to limit the maximum allowable content of lead permitted in plumbing products. The transition period for this change will end on 1 September 2025. As the transition period extends to 2025, the revised acceptable solution will be published in alignment with the rest of the plumbing and drainage updates in November 2023.
By announcing these decisions prior to the publication of the revised acceptable solutions and verification methods, we aim to provide certainty and direction to the sector and give additional time to implement the required change.
Read the summary of the decisions on lead in plumbing products and the structural stability of hollow-core floors on our website www.building.govt.nz/bcu22
Due to the breadth of in-depth submissions received for the 2022 consultations, we will announce the remaining decisions prior to publishing the Building Code acceptable solutions and verification methods in November 2023. This additional time is required to thoroughly work through the submissions and ensure all points of view are considered. This timeframe will also allow us to prepare the necessary supporting educational material such as guidance documents, learning modules and webinars.
In 2021 we published updated acceptable solutions and verification methods for building code clauses B1, E2, G7 and H1. The transition period for the 2021 Building Code updates ended on 2 November 2022. This means that building consent applications submitted on or after 3 November 2022 that use one of the updated acceptable solutions or verification methods as a means of compliance should now use the most recent versions of the documents.
You can access these on our website at www.building.govt.nz/building-code-compliance
R0.37
Roofs
Region A1 = R2.9
Region B2 = R3.3
Floors All climate zones = R1.3
Climate zones 5 and 6 = R0.50
Climate zones 1 to 6 = R6.6
Slab-on-ground floors (Climate zones 1 to 4) = R1.5
Slab-on-ground floors (Climate zone 5) = R1.6
Slab-on-ground floors (Climate zone 6) = R1.7
Other floors (Climate zones 1 to 3) = R2.5
Other floors (Climate zone 4) = R2.8
Other floors (Climate zones 5 and 6) = R3.0
Walls Region A1 = R1.9
Region B2 = R2.0
Skylights
Climate zones 1 to 6 = R0.37
Climate zones 1 to 6 = R2.0
Climate zones 1 and 2 = R0.46
Climate zones 3 and 4 = R0.54
Climate zones 5 and 6 = R0.62
1 Region A comprises all of the North Island/Te Ika-a-Māui excluding the Taupo District, the Ruapehu District and the part of the Rangitikei District north of 39o50’s (-39.83), and all offshore islands north of 37o15’s (-37.25).
2 Region B comprises the Taupo District, the Ruapehu District, the part of the Rangitikei District north of 39o50’s (-39.83), the South Island/Te Waipounamu, Stewart Island/ Rakiura, the Chatham Islands, and all offshore islands south of 37o15’s (-37.25).
Note: R-values are taken from H1/AS1 and are required when using the Schedule method.
The updates to the acceptable solutions and verification methods for H1 Energy efficiency are effective now. The revised documents also provide a staged transition for insulation in housing, as shown in Figure 1.
To help people understand the updated H1 requirements, the Building Performance team have created new learning modules covering insulation, energy efficiency and climate zones.
Module 1 is aimed at homeowners and the general public. It explains why insulation is important in buildings to increase energy efficiency and the benefits of installing better insulation. It helps to identify the climate zones that different parts of the country fall into and the background to the new requirements for houses that will apply from May next year.
Module 2 teaches you about the different compliance pathways for the Building Code’s energy efficiency requirements and how to choose the appropriate acceptable solution or verification method for your building.
Modules 3 and 4 are under development and will be published later this year.
Find building system learning modules at learning. learning.building.govt.nz
We know that there have been a lot of different things to get up to speed with, but we are committed to working alongside the building and construction sector to ensure the successful implementation of these important changes.
You can find out about consultations on changes to the building code, acceptable solutions and verification methods and stay up to date with changes when they come into effect by subscribing for updates on our website www.building.govt.nz
by Liz Ashwin Senior Advisor Information and Education Building System Performance MBIEThis article is relevant to these classes:
The new code of ethics, which came into force on 25 October 2022, sets behavioural standards for Licensed Building Practitioners (LBPs) to give both the industry and the public clarity on what is expected from LBPs, and to hold them to account.
The code of ethics ensures high standards are maintained in the industry while giving the public more confidence that LBPs are undertaking building work safely, legally, and professionally. It also gives people, such as homeowners, an avenue to complain should an LBP breach the standards.
Most LBPs already work to the highest professional and ethical standards. The code of ethics will hold those who do not meet these standards accountable by providing clear grounds for the Building Practitioners Board to take disciplinary action against LBPs who have behaved unprofessionally.
What does the code of ethics include?
The code of ethics is made up of nineteen standards, which sit under the following four key principles:
1. Work safely
- Take responsibility for health and safety
- Report unsafe behaviour by others on a building site
- Avoid harming the environment.
2. Act within the law
- Comply with the law
- Report breaches of the law.
3. Take responsibility for your actions
- Know what building work you are allowed to do
- Explain risks to your client
- Inform and educate your client
- Be accountable for building work carried out by you, or someone under your supervision
- Advise clients of any delays as soon as they become apparent
- Act in your client’s interests
- Generally, you should follow your client’s instructions unless the instructions are dangerous, are contrary to contracts or consents, or would mean you would not be acting within the law.
4. Behave professionally
- Behave professionally
- Act in good faith during dispute resolution
- Price work fairly and reasonably
- Declare and manage actual or potential conflicts of interest appropriately
- Maintain confidentiality of client details unless there is good reason for sharing information
- Acknowledge and respect the cultural norms and values of your clients and colleagues
- Conduct your business in a methodical and responsible manner.
Where can I find more information?
The Ministry of Business, Innovation and Employment has developed information and education resources to help LBPs and the public learn more about the code of ethics.
These are available on the LBP website and include a detailed guidance document and an interactive online learning module. The module takes 20-30 minutes to complete and can count towards an LBP’s skills maintenance activities (note LBPs must log in to the module for it to count towards skills maintenance).
For more information go to: www.lbp.govt.nz/for-lbps/code-of-ethics
by Robyn McClymont Senior Advisor Information and Education Building System Performance MBIEFor article: Building Code Updates (pg 30)
1. Who updates the acceptable solution and verification method Building Code documents?
a) The LBP scheme
b) BRANZ
c) The MBIE Building Performance team
2. The new insulation value of R0.46 for windows and doors in Climate zones 1 & 2 takes effect from when?
a) 3 November 2022
b) 1 May 2023
c) 2 November 2023
3. What’s to best way to keep up with consultations on changes to the Building Code and stay up to date when they come into effect?
a) Subscribe for updates on our website www.building.govt.nz
b) Read them in your local newspaper
For article: New Code of Ethics for LBPs (pg 32)
1. Why have a code of ethics?
a) It ensures high standards are maintained in the industry
b) It gives the public more confidence that LBPs are undertaking building work in a safe, legal, and professional way
c) It provides people, such as homeowners, with an avenue to complain should an LBP breach the standards
d) All of the above
2. Which of the following is not part of the Code of Ethics?
a) Avoid harming the environment
b) Comply with the law
c) Inform and educate your client
d) The definition of restricted building work
e) Price work fairly and reasonably
3. Who does the code of ethics apply to, and can I claim skills maintenance points for learning about it?
a) It applies to all LBPs, and is an elective skills maintenance activity
b) It doesn’t apply to me, and I can’t claim points if I learn more about it
c) Read them in Codewords Answers:
ADD TO LBP ACTIVITY LOG
This article is from Codewords Issue 111.
Log-in to the LBP portal lbp.govt.nz and update your Skills Maintenance activities.
feedback, which identified several issues.
In 2021, MBIE consulted publicly on potential areas for improvement in the Licensed Building Practitioners Scheme focusing on its supervision, licensing classes, and core competencies and minimum standards for entry.
We received a great response from the sector –particularly LBPs, who made up almost half of all respondents. The consultation told us that, overall, the scheme was working well but there were a few areas for improvement.
We are now ready to test our proposed changes to the LBP Scheme based on your feedback in the upcoming consultation document Review of occupational regulation in the building and construction sector.
We are also seeking feedback on issues and proposals across some of the other occupational regulation schemes in the building sector, including the registered architects regime, the plumbers, gasfitters and drainlayers regime and the electrical workers regime. We would welcome your views on how these other regimes are working.
The first area of the LBP Scheme where we want to make changes is the supervision of restricted building work.
Submissions told us that there were problems with the way supervision was being handled, including inexperienced LBPs supervising incorrectly due to power imbalances and not having their competency tested before entering the scheme. Another issue raised was that LBPs are intentionally supervising incorrectly by renting out their supervision or cutting corners to meet deadlines.
The feedback also told us that the scheme did not provide any differentiation between experienced and skilled LBPs and those who had just entered the scheme. To address this, we propose introducing a licence endorsement for supervision.
This endorsement would only allow those who have been in the scheme for 3 years and have been deemed competent by the Registrar of Licensed Building Practitioners to supervise restricted building work. Licence holders without the endorsement would still be able to do restricted building work.
We believe that these proposed changes will increase the quality of supervision by limiting who can supervise to those who have proven themselves competent at doing so.
This change will also provide consumers with an opportunity to differentiate between the more skilled and less skilled LBPs and provide an incentive to LBPs to advance their skills.
The second set of changes MBIE is proposing is some new licensing areas. The submissions from the previous consultation told us that there were various areas that need to be added to the scheme. We propose introducing:
▶ stonemasonry to a renamed Bricklaying and Blocklaying class
▶ specialist areas like plasterboard installation and tanking to a new Specialist Installer class
▶ internal waterproofing, which will also involve expanding the definition of restricted building work.
We believe that these changes will have many positive effects.
The changes will make the scheme more efficient, especially in the case of the Specialist Installer class – unlicensed practitioners will no longer need to rely on an LBP to supervise their work and incur the costs that come with that.
Adding stonemasonry and internal waterproofing will provide regulation in areas that have previously gone untouched, reducing the risks to the public from the financial and life risks that can come from poor-quality work.
As the above work will involve creating new competencies, we consider this is the best time to look at the rest of the competencies that make up the LBP Scheme.
In 2021, we were told that the competencies were not fit for purpose for today’s sector and that the minimum standards for entry needed to be lifted. What we were not told, however, was what needs to be added or how these minimum standards could be raised.
We would like to know where the changes need to be made and what we can do to make them.
As LBPs, you have all been through the licensing process at some stage and will all have first-hand experiences that you can draw on as examples.
While it is important to remember that most of a builder’s training is on the job site and that these assessments are the minimum level for entering the scheme, we want to ensure the LBP Scheme assessments remain a robust process.
The LBP Scheme ensures that Aotearoa New Zealand’s homes are built right, the first time, and we want to keep it that way. Your feedback will be used to help make the LBP Scheme fit for purpose for both today’s and tomorrow’s building sector.
You can access the consultation and survey documents on MBIE’s Have Your Say page at www.mbie.govt.nz/have-your-say/. Submissions can be made either by emailing building@mbie.govt.nz or by completing an online survey.
LBPs have the most experience using the scheme – please take the time to provide your feedback, it will go a long way to making sure that we have a building sector we can continue to take pride in.
by Ben McBride Policy Advisor, Building System Performance MBIE☐ Rangiora ITM 03 313 4862
☐ Timaru ITM 03 688 8074
☐ Waimate ITM 03 689 7427
OTAGO/SOUTHLAND
☐ Dunedin ITM 03 262 1008
☐ E H Ball ITM Invercargill 03 218 3787
☐ Fraser Hardware ITM Balclutha 03 418 0170
☐ Gore ITM 03 208 0649
☐ Mosgiel ITM 03 489 8885
☐ Southbuild ITM Winton 03 236 6055
☐ Southern Lakes ITM Alexandra 03 427 2221
☐ Southern Lakes ITM Cromwell 03 445 0081
☐ Southern Lakes ITM Queenstown 03 451 1567
☐ Southern Lakes ITM Wanaka 03 443 2545