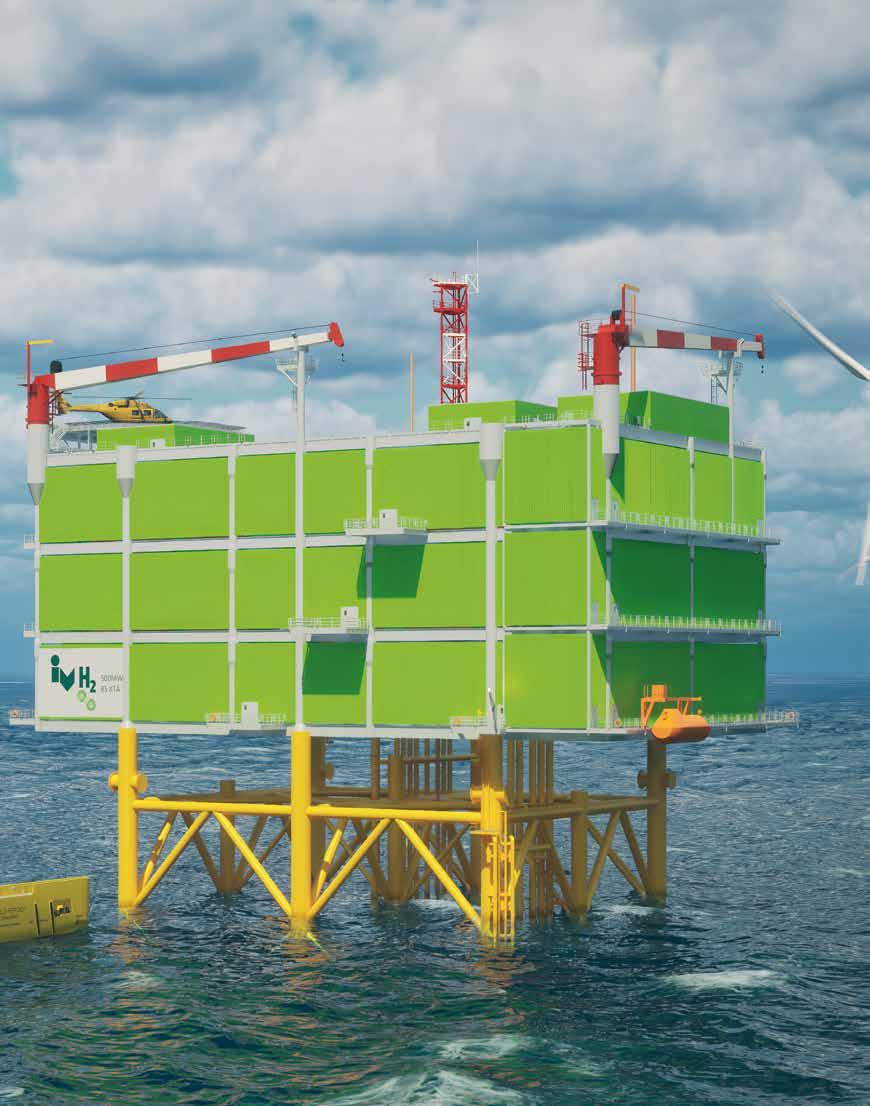
Offshore brochure I November 2024
Offshore brochure I November 2024
5 Combining past and present worlds
6 In-depth experience and a practical approach
9 Safety in design
10 Offshore substations
12 Pilot for offshore hydrogen production
14 Floating offshore substation
16 Sofia HVDC offshore converter platform
18 Neart na Gaoithe HVAC offshore substations
20 2 GW Programme IJmuiden Ver
22 Borssele Alpha & Beta HVAC offshore substations
24 Princess Elisabeth Island
26 Floating solar platform
Although most of our work today is in offshore renewables, our roots are in the oil & gas industry. This experience has provided a solid foundation for developing offshore wind substations, both HVAC and HVDC and, more recently, hydrogen energy solutions such as offshore hydrogen production. As a result, we have developed additional knowledge and skills to meet the challenges of these new projects: adapting to the evolving offshore wind market, meeting new operator requirements, engaging with new stakeholders, incorporating innovative technologies, and handling a broader engineering scope.
Iv is proud to be one of the first to operate in the offshore wind sector, paticularly in the field of offshore substations. We are proud to have developed and engineered the first HVAC substation Horns Rev. A, as well as the first HVDC offshore converter platform BorWin Alpha. Not only were we among the first in substations, we were also at the forefront of the step up to > 1,000 MW HVAC and to 1,300 MW HVDC. Our dedication to innovation did not stop there. A key milestone was the progression to 2GW-525 kV bi-pole HVDC, which is now being brought to life as 2 GW Standard Design for TenneT for application in the Dutch and German North Sea, highlighting our role in pushing the boundaries of offshore wind energy.
We constantly seek the optimum balance between flexibility, efficiency, sustainability and cost, while never compromising on quality and safety in our designs.
Offshore operations are very critical and require strategic and delicate decision-making. Iv has many years of engineering experience with production and wellhead platforms, FPSO’s, compression modules and substations. Additionally, Iv provides 3D laser scanning services for its clients, an effective tool for brownfield projects. We perform projects for all leading operators within the industry and also in joint ventures with large construction yards. Our in-depth experience and practical approach enable our clients to benefit from customised solutions.
Our overall HSE project design objectives are to engineer a safe, reliable and operable facility for the entire service life of the installations. Throughout the design, we constantly ask ourselves and each other, “Can we make our design safer?” We view this as a responsibility towards our clients, stakeholders and their personnel.
Our ‘safety in design’ principle is always developed to at least comply with the applicable legislative codes and standards as a minimum. We are committed to going above and beyond the requirements. We actively encourage every member of our team to critically assess and challenge our chosen solutions to ensure we are adopting the safest practices possible.
UNITED STATES CANADA
EMPIRE WIND
800 + 1,200 MW
VINEYARD WIND
800 MW
SEAGREEN 1,500 MW
BERWICK BANK 1,150 MW
NEART NA GAOITHE 2 X 225 MW
SOFIA 1,320 MW
SOUTH COAST 1,300 MW
MARWIN 420 MW
IJMUIDEN VER BÉTA 2,000 MW
POSHYDON 1,250 MW
NSE HYDROGEN 500 MW
GREATER GABBARD 2 X 252 MW
PRINCESS ELISABETH ISLAND 3,400 MW
HORNS REV B
MW
HORNS REV A
MW
BORKUM RIFFGRUND 2 450 MW
BORWIN ALPHA
OSTWIND 3 300 MW
MW HELWIN BETA
IJMUIDEN VER GAMMA 2,000 MW
DOLWIN ALPHA
MW
BORSSELE ALPHA + BETA
2 X 700 MW
THORNTON BANK
325 MW
GENNAKER EAST + WEST 460 MW
HVAC
• THOR
• GENNAKER EAST + WEST
• OSTWIND 3
• NEART NA GAOITHE
• PRINCESS ELISABETH ISLAND
• BORSSELE ALPHA + BETA
• BORKUM RIFFGRUND 2
• GREATER GABBARD
• THORNTON BANK
• HORNS REV A
• HORNS REV B
HVAC STUDY
• BERWICK BANK
• EMPIRE WIND
• MARWIN
• SEAGREEN
• VINEYARD WIND
HVDC
• SOFIA
• DOLWIN ALPHA
• HELWIN BETA
• BORWIN ALPHA
• IJMUIDEN VER BÉTA
• IJMUIDEN VER GAMMA
HVDC STUDY
• IJMUIDEN VER
• SOUTH COAST
HYDROGEN
• POSHYDON (PILOT)
• NSE HYDROGEN (PILOT)
Client Rijksdienst voor Ondernemend Nederland (RVO)
Platform operator Neptune Energy
Facts
Type: PEM electrolyser
Nr. of cell stacks: 1
Input power: 1 MW
Water consumption: 300 l/h
Hydrogen flow: 246 Nm3/hr
Hydrogen purity: 99.998%
Outlet pressure: 30 barg
Footprint: 2 x 40 ft stacked containers
Lifting weight: <20 tonnes ( 2 x 20 ft cont)
Cable: 9 MVA, 25 kV
Production: 400 kg/day
The Q13a-A hydrogen pilot project aims to demonstrate green hydrogen production offshore, on a live oil and gas production platform. The lessons learned will help enable large-scale green hydrogen production in the North Sea.
Off the coast of Scheveningen (The Hague), the first pilot project for the integration of three working offshore energy systems will take place on the Q13 working platform, which is already electrified with renewable energy via a cable to the shore. Energy from wind and demineralised seawater will be converted into green hydrogen offshore, according to the wind profile of Eneco’s Luchterduinen wind farm. The green hydrogen will be blended with natural gas and transported via existing pipelines, allowing the existing infrastructure to be shared. The platform is expected to be in production by the end of 2024.
Iv is working with several partners in the PosHYdon consortium to create a safe environment for handling hydrogen (and oxygen) on a live oil and associated gas platform.
Technical limitations of co-production of hydrogen and North Sea gas, seawater desalination, power fluctuations and electrolyser performance will be addressed. The other partners in the consortium are responsible for identifying and addressing the requirements related to permitting, certification, and entry specifications.
A logistics, training, and skills gap analysis will also be carried out, and economic calculations will be made to determine how the value of hydrogen can be maintained when blended with natural gas. The economics of large-scale offshore hydrogen production will also be considered.
Iv is responsible for the basic and detailed engineering of the necessary adaptions to the platform to accommodate the electrolyser system, Iv is involved in the risk assessment and mitigation, and provides offshore expertise. Iv also provided the list of offshore requirements for the containers containing the electrolyser, the seawater desalination system and the power conversion system.
For the hydrogen production system to be tested on land, only a few adaptations are needed: power supply, sufficient space for the system, supply of (sea)water, disposal of brine, hydrogen use/release, oxygen release, permits to test, and permits to construct. Iv prepared a conceptual design document describing the system interfaces and further requirements for adaptations and modifications to be carried out onshore.
Weigh
Topside: approx.11,000 mT
Floater: 10,000 mT
Water depth
Over 150 m
Worldwide, the best wind conditions for generating wind energy are often found at sea in areas with deeper water. The question is: how can this be achieved as effciently, reliably, and cost-effectively as possible?
At water depths beyond 150 metres, the costs of the renowned ‘bottom-founded’ offshore structures (such as transformer and converter platforms and wind turbines that are anchored to the seabed via a structure) increase exponentially, making floating solutions an interesting alternative. Iv and Nevesbu jointly developed a concept for an offshore substation. A concept with potential!
Iv and Nevesbu are consistently carrying out innovative studies. In light of the forthcoming energy transition, Nevesbu began investigating which unique floating applications could be devised to provide a solution. Many concepts for floating turbines already exist, but not for a floating substation. We formed a joint initiative because Iv has already designed many offshore wind substations, and Nevesbu has unique expertise in floating structures. The challenges presented with this type of floating solution include the lifespan of the dynamic power cables and the allowable motions of the transformers, rectifiers, and associated systems. Floating an offshore substation weighing roughly 10,000 tonnes with minimal motions is a complex challenge, but our studies show that it is possible.
In Europe, the Mediterranean, North Sea, Bay of Biscay, and the Aegean Sea, in particular, are deepwater areas that are very suitable for generating wind energy. Especially in the area above Scotland and the United Kingdom towards Norway and Denmark, there are almost continuous strong winds. The concept that Iv and Nevesbu have developed is therefore designed for the harsh weather conditions that are characteristic of these areas. The concept also minimises the impact on marine life.
Some essential principles for the design of the floating offshore substation are: the concept must conform to the set requirements for wind energy at sea, it must not be too heavy in steel weight and must not be complex in terms of fabrication. Safety and reliability must also be guaranteed. It must be possible to guarantee a very high availability, and the platform must have a lifespan of at least 30 years. In addition, the social costs of supplying sustainable electricity must remain affordable, and the solution itself should therefore not be too expensive in terms of costs.
The main challenge is the transition from a static bottom-founded substation to a dynamic, floating substation. Wind turbines must be capable of operating in conditions up to Beaufort 8, which means that the floating substation must continue to function when contending with waves of 8 to 12 metres. Existing high voltage (HV) equipment, however, is not suitable for high accelerations. To guarantee motions are kept to a minimum, motion analyses were carried out to calculate how different models behave at sea in strong winds with high waves. These analyses are based on the roughest seas in the world, such as the North Atlantic Gulf Region, the Bay of Biscay and the sea near Santa Barbara, California. If the concept is suitable for these waters, it can certainly also be applied in calmer waters.
The floating offshore substation concept is designed to operate in water depths in excess of 150 metres and with minimal vertical motions in sea conditions. The deck area is 85 by 85 metres and is positioned approximately 20 metres above the water’s surface. When the substation is installed at sea, it will be held in position with the help of so-called ‘tendons’ that are vertically anchored to the seabed. The floating structure is designed to minimise the vertical motions, which also reduces the loads on the export cables suspended below the platform. Tuning the motion behaviour of the platform for different water depths and wave conditions is also relatively simple.
Client Seatrium. (formerly Sembcorp Marine Offshore Platforms)
Technical data
Dimensions
Topside: 80 x 43 x 45 m (excl. helideck) (lxwxh)
Jacket: 58 x 39 x 44 m (lxwxh)
Weight
Topside: 11,000 mT
Jacket: 4,350 mT
Water depth
28,5 metres below sea-level
Field power capacity: 1.4 GW
No of offshore substations: 1
No of WTG’s: 100
One of the largest wind farms in Europe, the Sofia Offshore Wind Farm, will be realised 195 km off the coast of North East England, in the area known as Doggersbank. With 100 wind turbines covering a total area of 593 km2, totaling a capacity of 1.4 GW and an innovative high voltage direct current (HVDC) converter platform, this wind farm will supply approximately 1.2 million British homes with sustainable energy in the future.
The Sofia HVDC converter platform, to be installed at the heart of the wind farm, will be one of the largest and most powerful offshore HVDC converter platforms currently in existence or under construction.
A 25-metre-high telecom mast will be placed on the top deck of the topside. This telecom mast will provide a direct connection to the satellite dish on land. However, the challenge here is that when the platform was ready, it was transported by ship around the Cape of Good Hope in Africa. The platform will convert electricity from 66 kV alternating current (AC) to 320 kV direct current (DC). Two export cables of approximately 220 km in length, which together form a single high voltage direct current circuit, will transport the power from the wind farm to the onshore substation in Lackenby.
When converting alternating current to direct current, heat is produced, which must be cooled. The HVAC system (i.e. heating, ventilation, and air conditioning), that is required for cooling the HV system demands a lot of space. Iv has therefore applied a new cooling concept for the Sofia HVDC converter platform. Conventionally, the cooling system is subcontracted to an HVAC contractor to design the system and supply the components.
For this project, Iv is responsible for the HVAC system, including designing it, purchasing the necessary components, and the integrating it with the process systems.
For the Sofia HVDC converter platform, an HVAC system has been chosen that uses cold water to cool the condenser rather than air. Cooling with cold water has the advantage that the highest design temperature of the seawater used is lower than the temperature of the outside air. Furthermore, the heat transfer of water is better than that of air, allowing the system to be more compact.
The water-cooling system allows lower temperatures to be achieved in the air conditioning system, and smaller ducts to be designed, which in turn require less space.
The cutting of the first steel for the fabrication of the platform took place in August 2021.
The construction of the wind farm began in early 2021, with the construction of the onshore substation in Lackenby. The offshore installation has already taken place, and the platform is expected to be operational by 2026.
Client EDF Energy Renewables (EDF-ER)
Technical data
Dimensions
OSS Topside (lxwxh): 36 x 26 x 20 m
Jacket: height 41 m + height of the buckets 12 m
Weight
OSS Topside: 1200 mT Jacket: 1261 mT
Water depth
Variation between (-)28.6 m and (-)29.8 m
Field power capacity: 450 MW
No of offshore substations: 2
No of WTG’s: 54 x 8.4 MW
Accommodation: 12 POB
Iv was awarded the contract to provide the detailed engineering and procurement services for the two Neart na Gaoithe (NnG) alternating current (AC) offshore substations. NnG is a 50:50 JV owned by EDF Renewables UK and ESB. As a subcontractor of HSM, Iv provided the detailed design and procurement of all piping, auxiliary and HVAC equipment, as well as the integration of the high voltage equipment.
Structural workshop drawings for both platforms were also produced by Iv. HSM has joined forces with General Electric Grid System (GEGS) for the engineering, fabrication, load-out and commissioning of this wind park development in the North Sea near the Scottish coast.
The Neart na Gaoithe (‘strength of the wind’ in Gaelic) offshore wind farm consists of a total of 54 Wind Turbine Generators (WTGs), located approximately 15.5 km from Fife Ness and 29 km from the East Lothian coastline. It covers an area of 105 km2. Each WTG has a capacity of 8.4 MW, resulting in a total capacity of 450 MW being fed back to the two HVAC offshore substations by inter-array sea cables.
The two offshore substations are connected via an interconnector. Each one is connected to the onshore support station via an export cable, which then connects to the onshore station to the Scottish grid system. The project will supply renewable energy to around 375,000 Scottish homes and will offset over 400,000 tonnes of CO2 emissions each year.
The offshore substation configuration consists of a receiving end connected to the 66 kV GIS. The main transformer (MT) transfers the power to the export cable at 220 kV.
Each offshore substation consists of two deck levels. The cellar deck houses the auxiliary systems for control, platform power, communications, and platform operations, with a dedicated area (the cable deck, part of the substructure) for the pull-in of the inter-array sea cables and export cable. On the main deck, the MT is installed in the centre, with the GIS installed on either side. To improve the overall schedule and allow for the full completion, installation, and commissioning of the HV Equipment before lifting onto the main structure, the GIS modules are built separately from the main structure.
The offshore substations are normally unmanned. However, a shelter (12 POB) will be provided for emergencies. Furthermore, the substations are equipped with lifting trunnions, a pedestal crane, laydown areas, W2W platforms, a heli-lift area, and other facilities to accommodate the installation work and future maintenance services.
The engineering phase started in June 2019. On 15 January 2020, the first steel was cut. The loading of the offshore substations took place in the summer of 2022, and the substations were fully commissioned and handed over to EFD in Q1 of 2023.
On February 26th of 2020, Iv signed the contract with TenneT TSO
b.v. to carry out the Front End Engineering and Design (FEED) for the world’s first 525 kV offshore grid connection. The FEED is part of the development of a new standard design for two network connections to the IJmuiden Ver Wind Farms, located in the North Sea.
The two High Voltage Direct Current (HVDC) platforms, Alpha and Beta, will have a capacity of 2 Gigawatts (GW) and will be the first HVDC platforms in the world based on 525 kV. This level of voltage represents just one example of the HV technologies that have never before been applied offshore.
Because of this innovatively high level of voltage, the platform will be suitably equipped to supply green electricity to roughly four million households. Herewith, roughly half of all private households in the Netherlands could besupplied with suitable electricity.
The technology necessary for this capacity has never been applied before, which makes this project unique. During the entire design process, trade-offs will be made with regard to the lowest “Levelised Costs of Energy (LCOE)” and improving nature. It is Iv’s and TenneT’s intention that nature can benefit from this project. Therefore, environmental measures have been integrated as basic conditions in the design criteria of the HVDC platforms.
Client TenneT TSO b.v.
Technical data
Borssele Alpha
Dimensions
Topside (lxwxh): 58 x 32 x 25 m
Jacket (lxwxh): 28 x 27 x 55 m
Weight
Topside: 3700 t
Jacket: 2900 t
Borssele Beta
Dimensions
Topside (lxwxh): 58 x 32 x 26 m
Jacket (lxwxh): 37 x 35 x 57,5 m
Weight
Topside: 3700 t
Jacket: 2950 t
Piles: 61 m each
Field power capacity: 2 x 700 MW each
The offshore high voltage substations Borssele Alpha and Beta are required to link the wind farms built offshore in the Dutch North Sea. The Borssele Alpha project, followed by the Borssele Beta project, are the first large-scale grid connections to be constructed under the National Energy Agreement for offshore wind farms in the Netherlands.
HSM Offshore has taken on the engineering, procurement, construction, transport, installation, connection, and testing of the offshore substation under an EPCI contract. Iv is the subcontractor for this project and is responsible for the design, engineering, and procurement support, including the integration of the TenneT-supplied high voltage components and the balance of plant materials.
The detailed design and engineering includes both the steel jackets with skirt pile foundations and the liftinstalled topsides.
Iv is responsible for the procurement of all necessary services, materials, and equipment, as well as the onshore and offshore commissioning of all systems for the jackets and topsides, including the TenneT-supplied HV equipment. Iv also manages the interfaces with the other parts of the network connection, such as the 66 kV wind farm and 220 kV export cable connections.
The Borssele Alpha offshore substation was delivered during the summer of 2019. The Borssele Beta offshore substation, which is almost identical to the Alpha platform, was delivered in July 2020.
Client Elia
Location
45 KM off the Begium Coast
Technical data
Dimensions 6 hectares
Weight
9,000 metric tonnes
(all modules combined)
Special features
2 x 1,050 MW AC Modules
2 x 700 MW AC Modules
Facility Module
Garage
2x Diesel Generator skids
General island electrical infrastructure
All modules will be placed on an artificial island
Field power capacity: 3,400 MW
The HSI Joint Venture, consisting of HSM Offshore Energy, Smulders, and Iv, has been awarded the contract for the development of Princess Elisabeth Island—the world’s first artificial energy island off the Belgian coast, commissioned by transmission system operator Elia.
Iv is responsible for designing four high-voltage substations for Princess Elisabeth Island: two with a capacity of 1,050 megawatts each and two with a capacity of 700 megawatts. The total capacity amounts to approximately 3.5GW, sufficient to meet the annual energy needs of more than three million households.
In addition to designing the four high-voltage substations, Iv is also responsible for the facilities module and garage design. The design, which includes the development of the layout and 3D model of all transmission assets on the energy island, will be carried out from Iv’s office in Papendrecht. For prefabrication, Smulders will use its Belgian facilities, while HSM will use its facilities in Schiedam. Final assembly of the modules will take place at the HSM Offshore Energy yard in Schiedam and at the Smulders yard in Vlissingen.
The project includes 330 km of 220-kV HVAC cables, divided into two contracts of 165 km each. Additionally, the island will feature five HVAC substations equipped with transformers and gas-insulated switchgear (GIS). A unique aspect of this project is that the island will combine high-voltage direct current (HVDC) and alternating current (HVAC) for the first time. Princess Elisabeth Island will also serve as a hub for future hybrid interconnectors, efficiently combining offshore wind energy transmission with cross-border electricity exchange.
The high-voltage electrical equipment market is currently under pressure due to high demand and rising material costs, which has influenced the tender process. Despite these challenges, the contracts were awarded on competitive terms, aligning with current market conditions.
In the Dutch offshore wind farm Hollandse Kust West (HKW) VII, around 53 kilometres off the coast of IJmuiden, the TotalEnergies/RWE consortium is developing a new form of sustainable energy generation. As part of the project, the world’s largest floating solar platform will be integrated alongside wind power generation. The floating solar platform is an innovative solution devised by the Dutch-Norwegian company SolarDuck and will be located between the wind turbines. The platform will consist of floating, interconnected triangular structures with solar panels. SolarDuck selected Iv to conduct the technical development and optimisation of this innovative concept to ensure that it meets all the requirements for installation and use at sea.
The floating solar platform that will be installed in the HKW VII wind farm is based on the Merganser test platform, a prototype solar platform with an energy generation capacity of 520 kWp (kilowatt peak) that was installed as a pilot 12 kilometres off the coast of Scheveningen in the North Sea. The often-harsh North Sea environment in which the HKW VII wind farm is located is considered one of the most challenging offshore environments in the world. Iv is applying its extensive offshore knowledge and experience to help optimise the existing design for these unique conditions.
By installing the platform between the wind turbines, the space at sea is used as efficiently as possible, and the grid system, which has already been installed for the wind farm, can also transport the electricity yield to shore. In addition, the maintenance of both energy systems can also be combined to take place simultaneously. technique that can be employed globally.
The possibility of realising more large solar parks on land in densely populated areas is decreasing. However, the demand for sustainable energy is only increasing, and this trend is set to continue. The floating solar platform is a solution to help electrify countries worldwide and provide security in supplying affordable, sustainable energy. It is a suitable solution for increasing sustainable energy supply, particularly in densely populated countries with lower average wind speeds and higher solar irradiation levels.
From idea to sea
SolarDuck started with this idea five years ago. But how do you get such an innovative solution to work at sea? How do you achieve a reliable structure that will operate for at least 30 years without maintenance? And how do you ensure that the entire project can be safely installed offshore? In addition to the overall technical optimisation
of the design, Iv is advising SolarDuck on hydrodynamics (the motions the structure undergoes due to the waves), anchoring and installation. Iv is also responsible for ensuring that the design is approved by the classification society. The harsh conditions at sea subject structures to fatigue and corrosion, among other things. Besides this, the structure must be able to properly absorb the motions of the waves so that the systems on the structure (such as solar panels and subsystems) are not damaged. Iv, as an experienced engineering company, specialises in such issues.
“It’s awesome to be involved in the development of new technology”, says Pieter de Boer, lead engineer at Iv. “A solar park at sea, fully functional and at this distance from the coast, has never been done before. From a technical point of view, it is incredibly challenging and complex. It takes a lot of creativity to make it technically, financially and safely feasible.”
But what makes it so complex? It goes without saying that creating something new is, by definition, no easy task. Among other things, the ‘behaviour’ of all the different platforms of the solar park is special and an important aspect. Pieter: “These all influence each other to a certain extent. It is quite a challenge to simulate the behaviour in the right way. Another factor is that people are present on the platform from time to time. We want them to be able to do their work as safely as possible, so we have to include that in the design.”
Iv is currently researching how the solar park will eventually look in terms of the number of platforms, the layout, and the exact location. The floating solar park is expected to be completed in 2026.