

Cranes
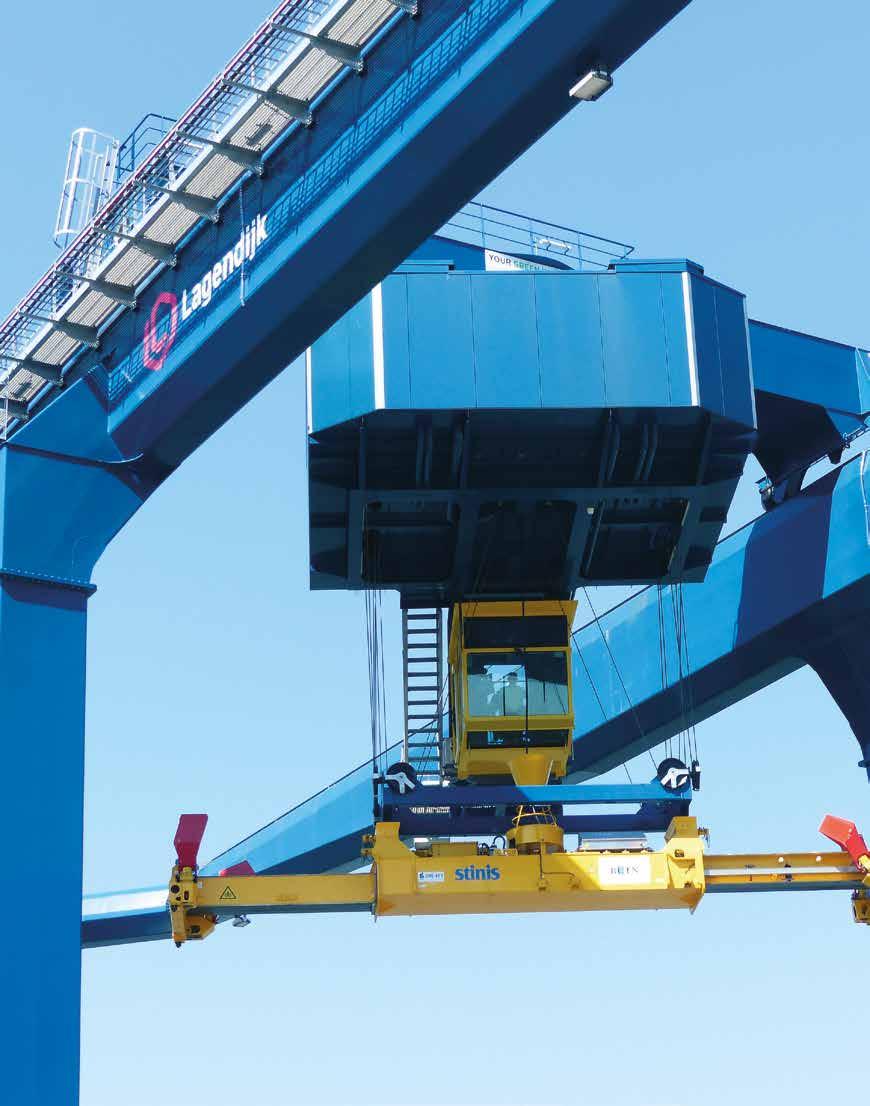

Up for every challenge
Iv is a multidisciplinary engineering company with a rich history dating back to 1949. With expertise in diverse markets such as offshore & energy, infrastructure & water, industry, buildings, and maritime, we remain at the forefront of market developments. We deliver high-quality, practical solutions for challenges of any scale and complexity, with a strong focus on the energy transition.
The key to world-class port logistics
A sustainable and efficient logistics chain in port areas is essential for maintaining a strong and international competitive position. Every year, millions of containers are stored and transshipped in ports. This number is expected to increase in the coming decades. Goods need to be moved to their destination quickly, safely and efficiently, and equipment such as advanced container cranes, heavy lift cranes, bulk handling cranes and ringer cranes play a vital role in ensuring this. Iv has a proven record in designing some of the world’s largest and most complex cranes. We have unique knowledge of steel and mechanical engineering structures, drive mechanisms and control systems, and we deliver innovative solutions that fit seamlessly into the client’s process.
Optimising and maintaining existing assets
In addition to designing new handling equipment, Iv advises clients on the maintenance and optimisation of existing equipment to extend the life and increase the level of automation. We have expertise in asset management and risk management and carry out high-quality inspections and measurements to ensure the reliability and availability of handling equipment. With advanced designs and reliable advice, we ensure logistical processes can continue uninterrupted, even in complex circumstances.
systems
Reliable and efficient drive systems Drive
How do you ensure that drive systems remain reliable and efficient? Iv offers tailored solutions for offshore and yard handling, including upgrades, life extension, inspections, and new construction of drive systems. With our expertise in the logistical and structural layouts of ports and yards, we help companies worldwide optimise their operations and add value to their business.
Upgrading drive systems
A review of the current system is required to upgrade (increase capacity) an existing drive system. This involves careful analysis of each component in the drive system and can include standard catalogue components such as bearings, seals, and couplings, as well as custom-built gearboxes, hoist drums and complex reeving.
Extending the life of drive systems
We can accurately determine the remaining service life based on spectral and cyclic data. We can also analyse how we can extend the life of our clients’ drive systems and determine what adjustments are required to achieve this.
Inspection
Sometimes, on-site inspections are required to determine the possibilities for upgrades and life extension. During these inspections, the degree of damage and/or wear is determined, followed by a report with advice for further
improvements. On-site activities can be combined with 3D scanning for more accurate designs or adding sensors for (full-time) field data monitoring. Iv has many years of experience in performing these inspections.
New drive systems
We also design a 3D model of new drive systems at every project stage, including 2D and workshop drawings. Drive systems can be applied to lifting equipment, conveyors, locking mechanisms and pump units.

Drive systems I Retractable roof structure
Roof structure of the Johan Cruijff ArenA
The project
The Amsterdam ArenA (now the Johan Cruijff ArenA) opened its doors in 1996 and became the largest football stadium in the Netherlands. The stadium is unique in that it has a retractable roof structure. Iv provided the design, including detailed calculations and working drawings, of the retractable roof structure and later also carried out a residual life analysis on the components of the structure’s drive mechanism.
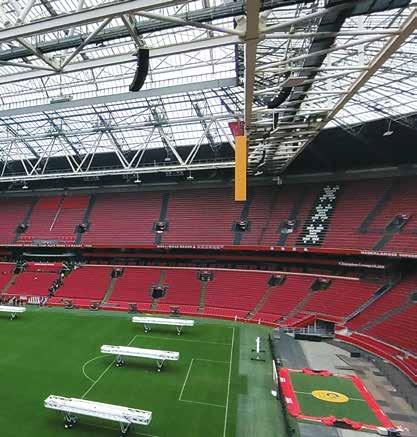
The
challenge
During the design of the roof structure, the ability to open and close quickly, for example, in bad weather, was taken into account. A profoundly complex challenge given its dimensions of 71 by 107 metres. Despite its size, the structure can be closed in 15 minutes. The design allowed for a limited number of closures. However, the roof has been opened and closed many more times, so Iv was recently asked to carry out a residual life analysis. Due to the need for the stadium to be available for events, Iv produced a recommendation within a short time outlining the various components, such as brakes, gearboxes and drive motors, which should be replaced.
The impact
With the residual life analysis, the roof of the Johan Cruijff ArenA will once again meet the set standards and requirements for a longer period, allowing the stadium to host other events in addition to football matches, such as concerts by world-famous artists.
Extending the life of cranes
Crane runway fatigue prevention and remedy
Well-designed and maintained crane runways ensure efficient crane operation, increase productivity, and guarantee safety. They play a vital role in ensuring operational continuity. Iv has over 75 years of specialised knowledge in complex (movable) steel structures and extensive experience in asset management, surveying, and monitoring. This enables us to gain insight into fatigue damage and provide advice on how to continue operations safely. Iv offers a complete package to ensure the optimum performance of crane runways over their entire life.
Crane runway analysis and inspection
Iv has extensive experience in analysing crane runways, both for new construction and renovation projects. The aim is to create a reliable design during the design phase consistent with the required life while extending the service life of cranes and crane runways by designing sophisticated improvement solutions (e.g. in the event of damage or so-called upgrades). State-of-the-art computational models are used for this purpose. These models can represent both damaged and intact structures, allowing the remaining service life to be determined. Based on these calculations, improvements are proposed to reduce fatigue damage and ensure safety.
Crane runways become worn and must be inspected regularly according to a fixed inspection protocol. This protocol specifies the frequency and focus of the inspections, based on the original calculations of the crane runway. Iv also conducts these inspections and prepares the associated reports.
Wireless monitoring
Sometimes, it is not possible to repair fatigue damage immediately, especially when a crane is in continuous operation. In such cases, the development of the damage is carefully monitored, and theoretical knowledge from computational models is used to determine how long it will be safe to work with the damaged crane runway. In collaboration with Villari, Iv offers wireless monitoring of crack growth in steel structures, which helps to plan maintenance and repairs.
We also take time-dependent measurements to see how the crane runway behaves when cranes move along it. These measurements, conducted at various positions, allow for a thorough analysis of the crane runway’s behaviour and can be compared with theoretical computational models, identifying any deviant behaviour.
Crane runway renovation
Renovation or upgrading a crane runway may be necessary for various reasons, such as extending the calculated service life, recurring fatigue damage, or installing new cranes with greater capacity.
Iv offers advice on cost-effective renovation solutions, whereby optimum use is made of the existing structural capacity. The crane runway is given a new lease of life and extended service life by accurately mapping and adjusting critical fatigue details locally.
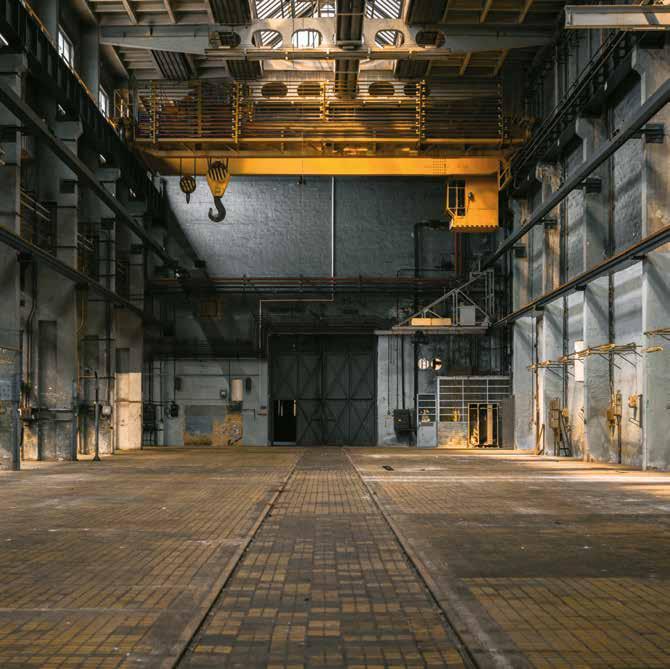
Extending the life of cranes
How sensor technology monitors fatigue in steel structures
How sensor technology ensures the safety of older structures
Older bridges, cranes and buildings are subject to ever-changing loads from both the natural elements and human use. The question is not only how to ensure the safety of these structures but also how to extend their life without the expense of undergoing complete replacement. Through the use of unique sensors, maintenance and life extension decisions can be made in a safe and data-driven manner.
Crack detection system
The crack detection system is a monitoring technology for the monitoring and early detection of crack growth in fatigued steel structures. Using sensor strips, the system detects variations in the magnetic field in the steel structure and expresses these as percentages. These percentage changes provide a reliable method for monitoring potential crack formation over time and providing targeted advice to structure managers. Due to its accuracy and sensitivity, the system can detect crack growth earlier than conventional weld tests such as ToFD and PAUT, thus allowing managers to take timely action to ensure the safety and continuity of operations.
The benefits of sensor technology
Monitoring potential crack formation with sensor technology offers several advantages, such as:
• Lower costs in relation to preventive weld tests;
• Less downtime thanks to continuous monitoring;
• Planned maintenance can be defined in advance;
• Continuous monitoring of steel structures;
• Early warning contributes to safety.
75 years of experience and expertise
“At Iv, we not only have the monitoring technology in-house but also more than 75 years of experience in the design of complex steel structures. From the world’s largest cranes and Ferris wheels to gigantic bridges and lock complexes, our experience is vast. Our background, combined with our highly specialised knowledge, particularly in the field of cranes and fatigue analysis of steel structures, largely derived from the former crane company Kalmar, enables us to proactively advise our clients on the best steps to take to maintain and extend the life of their structures,” says Lennard van Geel, Project Manager Mechanical at Iv. “Many of our clients approach us with questions about the applicability of sensors to their steel structures, such as: Can this technology be applied to my container crane?”
Collaboration and innovation
Iv has teamed up with Villari to conduct the monitoring. This company provides continuous damage monitoring services and has developed a unique wireless sensor for this purpose. These sensors allow large amounts of data to be collected, which can be translated into meaningful parameters such as crack length and growth rate using sophisticated algorithms. The trick, however, is to place the sensors in precisely the right place to obtain the correct information. Together with Villari, we have a complete package of technical knowledge and resources to conduct the monitoring and provide structure managers with advice. This integrated approach ensures that clients always have the best and most accurate information for their life extension maintenance decisions.
Continuous monitoring for optimal structure management
Continuous monitoring of the condition of steel structures ensures that you are always aware of potential risks and can intervene in good time, saving money in the long run and providing a safe environment for all. Do you have a fatigued or ageing steel structure that you would like to use safely without investing heavily? Contact us to find out how our sensors and expertise can help extend the life of your valuable steel structures.
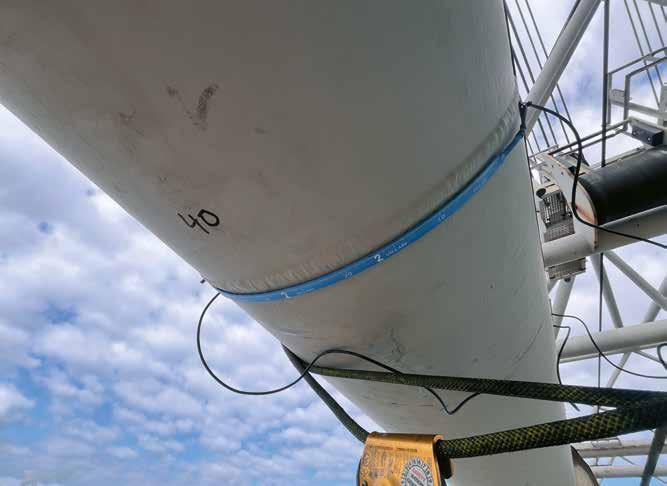

Container cranes I STS cranes
Extending the life of quay cranes at ECT
The project
Hutchison Ports ECT Rotterdam (ECT) faces increasing technical problems with its quay cranes due to years of intensive use. This has led to frequent maintenance and welding repairs. Despite the work carried out to repair the cranes, additional inspections are necessary, requiring a structural solution. By continuously monitoring ECT’s quay cranes, we extend their lifespan.
Iv started monitoring the quay cranes in Rotterdam. What does this monitoring entail? First, we review the cranes’ technical documentation. Then, we model the crane structure, analyse the so-called container handling movements, define an equivalent fatigue load, and perform a life cycle assessment according to the EN 13001 standard. Based on these insights, critical points can be identified. Iv then equips these critical points with sensors for continuous monitoring. If the data collected raises concerns, Iv provides immediate advice.

The challenge
The monitoring method used is unique and largely unknown to crane operators. Correct implementation requires specialist knowledge of the structure and fatigue. We place sensors in precisely the right places on the quay cranes to obtain the necessary information. Although Iv is experienced in life calculations, combining this with sensor placement requires precision and care. Mistakes in placement can have major consequences, which is why we apply internal verification checks to ensure the correct installation of sensors.
The impact
Previously, the quay cranes were inspected twice a year. This was a very time-consuming and costly exercise. Iv’s new monitoring approach provides constant and up-to-date monitoring of the crane’s condition. Physical inspections, such as TOFD measurements, are no longer necessary as they provide only a snapshot of the crane’s condition. With the new approach, sensors collect data continuously, allowing us to identify and address problems early, saving time and costs and thus extending the life of the quay cranes.
Container cranes I STS cranes
Designing cranes and SQC’s
The project
APMT, part of the A.P. Møller – Mærsk Group, had ordered 38 cranes for the terminal on the Second Maasvlakte, including eight semi-automatic Super Quay Cranes (SQC’s). These cranes are designed to load and unload larger container vessels, mainly Maersk Line vessels.
The design and engineering activities have been carried out entirely by Kalmar and Iv. The SQC cranes are rail-mounted, ship-to-shore cranes designed for loading and unloading container vessels. Each crane is approximately 130 metres long and comparable to the Erasmus Bridge in height. These cranes are of the Box Girder type and are equipped with two trolleys: a main trolley for transporting containers from the vessel to the container stacking platform and vice versa, and a second trolley for transporting from the stacking platform to the AGVs (Automated Guided Vehicles). The cranes are capable of serving Super Post-Panamax vessels and can handle 2×40-foot or 2×20-foot containers in a single lift (twin-lift and tandem-lift).

The challenge
Although these cranes may look like standard quay cranes from a distance, they are not simply larger or wider versions of an existing design. The project’s technical challenges were many, and many aspects taken for granted in ‘normal’ container cranes had to be considered in more detail, such as the design of the positioning system and the joints in the crane structure.
The impact
The implementation of near fully automated APM terminals, including semi-automatic SQCs, allows for more efficient and faster operations, ultimately helping the client to recoup the investment in large ocean-going vessel more quickly.
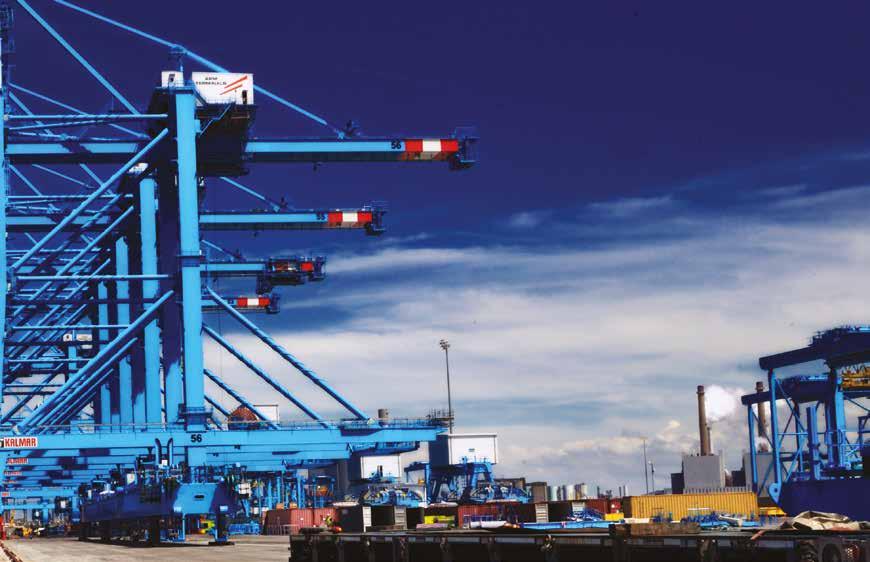
Container cranes I STS crane
STS crane height increase and life extension
The
project
To make an existing STS crane future-proof, Antwerp Terminal Services investigated the possibility of an adaption to increase the crane’s height and extend its life. The first step was to determine whether these adaptations were technically feasible.
Iv assessed the feasibility of the project using a wind tunnel test and a shadow model of the crane. Using a developed FEA model, Iv analysed global strength, fatigue, natural frequencies, stability, and wheel loads. Additionally, Iv assisted in drafting the Request for Quote and the technical evaluation of the quotations.
The challenge
A wind tunnel test was performed to assess the wind load accurately. Iv made a 3D model as a basis for the scale model used in the wind tunnel test, and an FEA model of the existing and adapted crane to process the results. The results were analysed, and the wind load was adjusted accordingly so that the corner loads and stability of the crane could be evaluated.
The impact
With these analyses, Iv provided the client with reliable advice on the feasibility of increasing the height of the crane, its service life and the necessary adaptions. Iv served as the client’s key support, managing various responsibilities, providing documentation and substantiation, supporting discussions with suppliers and answering their questions.


Container cranes I RMG crane
Higher production speed through accurate positioning at BCTN
The project
BCTN, part of the Inland Terminals group, wanted an expansion of their container terminals in Alblasserdam and Roermond. The new container cranes must be capable of positioning the containers more accurately, thus achieving a higher production rate. Commissioned by Lagendijk, Iv handled the entire engineering process, from concept design to manufacturing drawings.
The challenge
The project required a design within the limited clearance profile, which Iv was able to demonstrate met the requirements. After thorough analyses and calculations to optimise the rigidity of the crane structure and the lifting wire system, a cost-saving lifting wire system was chosen. Lagendijk’s construction method, with bended plates for the box girders, provides an optimal design in the context of increased stiffness and reduced wind loads. This construction method did require specific engineering calculations and research. The crane is now in the final testing phase and initial results are positive, showing that the design works well.
The impact
Iv’s design increases the rigidity of the hoisting wire system, increasing the accuracy of container positioning. The new crane speeds up the loading and unloading of ships, saving considerable time. A second crane for the Roermond container terminal is currently in production at Lagendijk. The crane in Roermond is largely similar to the design of the crane in Alblasserdam, the main difference being the smaller reach above the water.

Container cranes I Automatic stacking cranes
Quality assurance of stacking crane designs at ECT
The project
ECT has ordered new stacking cranes to replace the current stacking cranes that have reached the end of their service life. These Automatic Stacking Cranes (ASCs) are designed to efficiently move containers from loading and unloading positions in the ‘stack’ (storage area at the terminal). For this project, ECT ordered cranes from Huisman and from ZPMC.
Iv performs in this project design reviews. Our task is to review the designs of both Huisman and ZPMC to ensure they meet the specified requirements and have a sufficiently long lifespan. This includes performing independent shadow calculations and thorough checks of the designs. During these verification processes, we regularly identify areas for improvement, which contributes to the overall reliability and quality of the cranes.
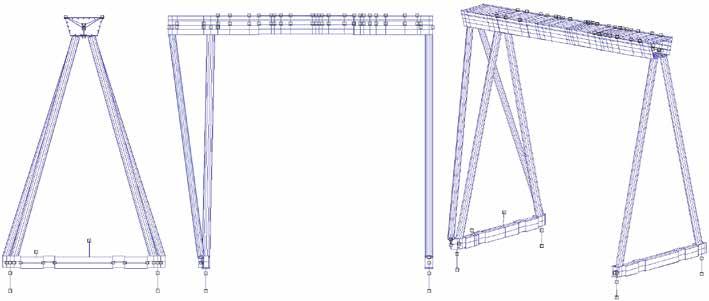
The challenge
The cranes are used in an intensive 24-hour service environment, where they must meet very strict requirements for positioning accuracy, where finding the optimal design is crucial to provide an effective and reliable solution.
The impact
Calculations and checks confirm that the main steel structure of the cranes has the demanded lifespan. This long service life and high utilisation capacity allow ECT to operate more efficiently and safely, which has a significant impact on its logistics processes.

Container cranes I Gantry crane
Cost analysis and engineering for gantry crane
The project
Smulders, located in Hoboken (Belgium), produces foundations for wind turbines and uses a large gantry crane to move these heavy components. The gantry crane has a rail length of over 400 metres and a capacity of 450 tonnes. Smulders asked Iv to investigate whether a new crane with a lifting capacity of 1200 tonnes could be used on the existing rails. Iv conducted a FEED study to map out the options and associated costs.
The challenge
A number of concepts were developed based on a series of requests and requirements. From these concepts, one was selected and developed in more detail. The biggest challenge was to design the lightest possible structure without compromising functionality. The crane is designed with two trolleys to facilitate the lifting and tilting of heavy components. In addition, the load remains at a constant height during both trolley and sheave block movement, ensuring greater accuracy in load positioning.
The impact
Iv drew up an overview of the required components, including costs and the dimensions of the steel. With its extensive welding and manufacturing expertise, Smulders formulated an estimate of the work required and the cost of the steel. The combined result was a total cost that enabled Smulders to make a well-considered decision to invest in a new crane. Although the crane would not (yet) be built, Iv took care of the engineering process and the cost estimates.
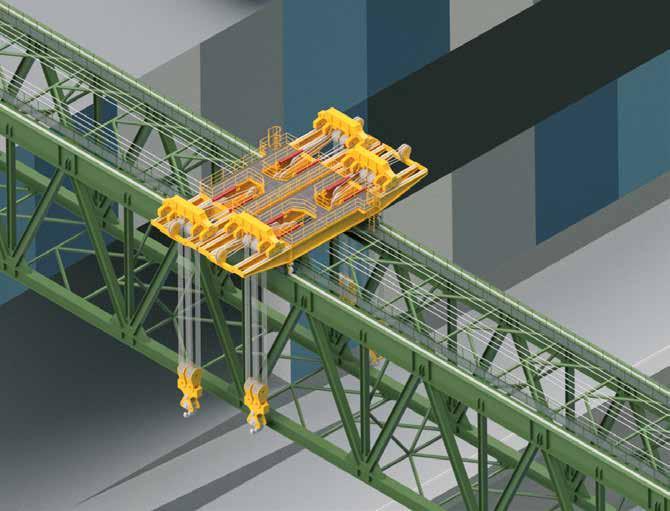
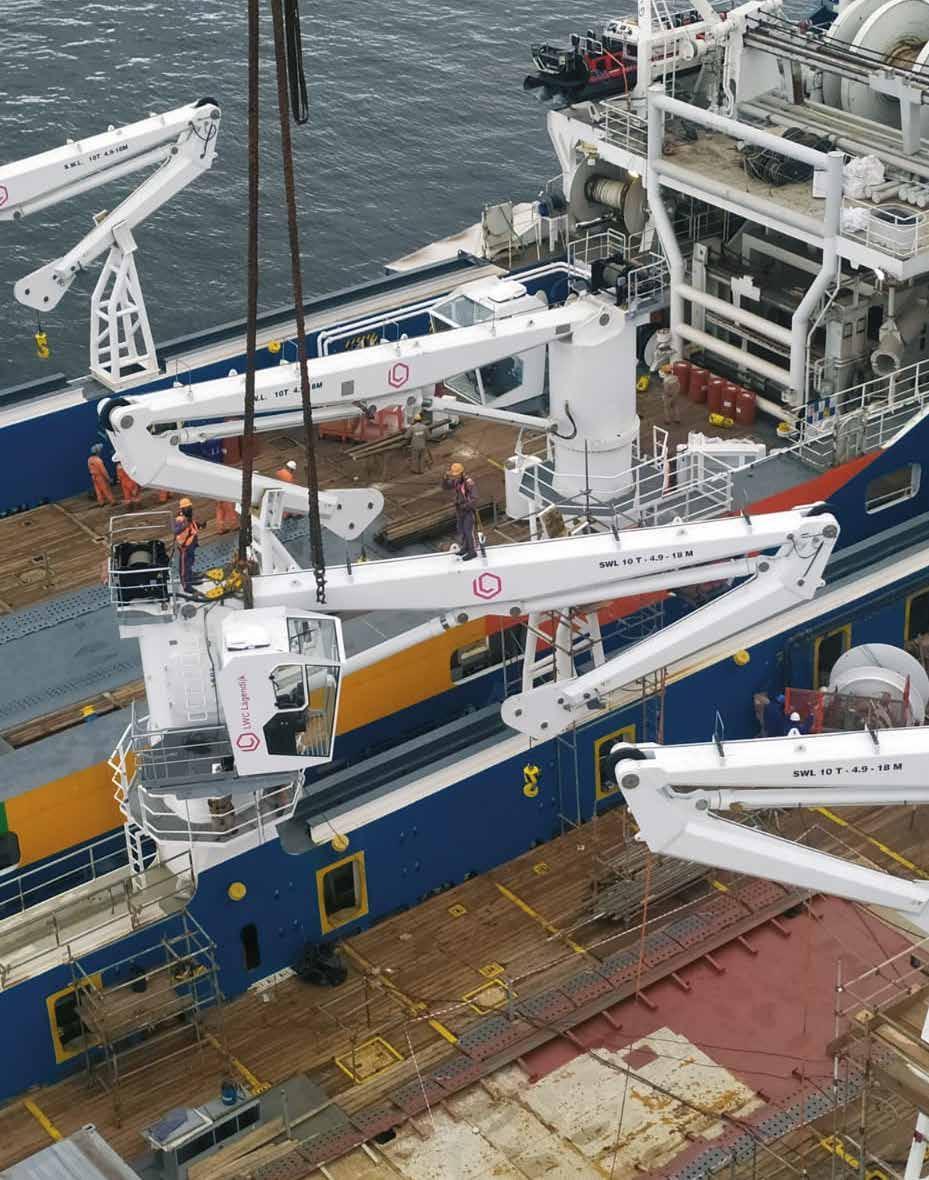
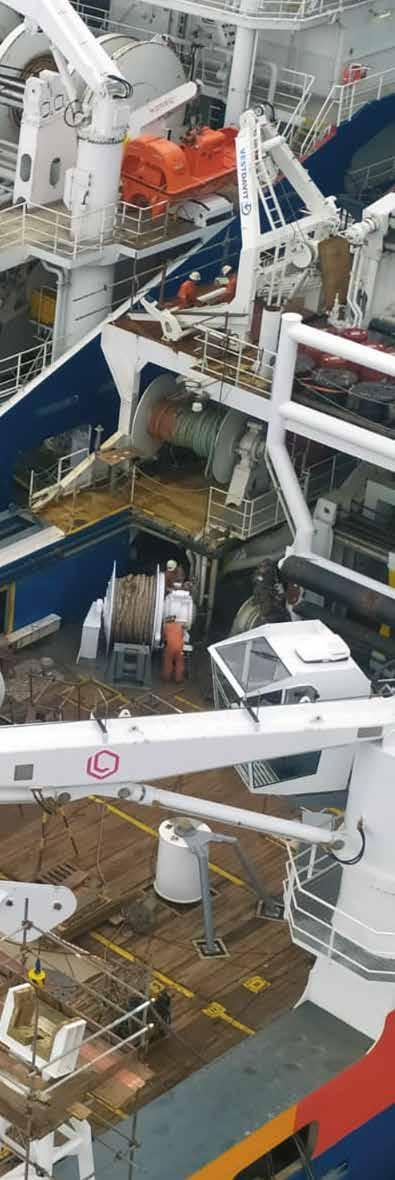
Pedestal cranes I Knuckle boom crane
Customised design for knuckle boom cranes
The project
For the Dutch company LWC Lagendijk, which specialises in the manufacture of offshore equipment, Iv designed four fully customised knuckle boom cranes. These special cranes have a knuckle boom that allows them to be positioned in a versatile and flexible way for loading and unloading materials in a confined space, such as on board a vessel.
The challenge
Iv designed these knuckle boom cranes specifically for LWC. This was a case of reinventing the wheel due to unique specifications such as range requirements, available space and capacity ratios. This type of crane consists of a double knuckle, allowing many different configurations in a small area. A total of four of these cranes have been built and are in operation. The workshop drawings were produced by the Iv team in Malaysia. The design also took into account offshore conditions. The cab has been designed for optimum offshore operation.
The impact
The four custom-built cranes are operational on board a vessel. The versatility of the configurations allows users to work offshore more efficiently, quickly, and safely.
Pedestal cranes I Lemniscate cranes
Upgrade and fatigue analysis of lemniscate cranes
The project
Iv carried out an upgrade and fatigue analysis for a transshipment company to assess the condition of their lemniscate cranes. The reason for the analysis was that the cranes were calculated to lift 26 tonnes in the jaw grab but have been loaded heavier than that in their lifetime. Measurements were also taken to calculate the accelerations of the cranes’ motions and the oscillations of the pontoon. Based on all this data, Iv provided advice on the lifting capacity upgrade, remaining service life and associated modifications to the lemniscate cranes.
The challenge
Lemniscate cranes have a number of unique features. For example, the crane is always balanced by the counterweight. If the crane tilts forward, the counterweight moves backwards and vice versa. In addition, the lemniscate crane is used on a floating platform, such as a pontoon, making it suitable for use in many locations. The crane consists of more pivot points and components than other cranes, making the calculation work very complex.
The impact
By carrying out various calculations and analysis, Iv provided the client with expert advice on extending the cranes’ life, allowing them to remain in service for longer.
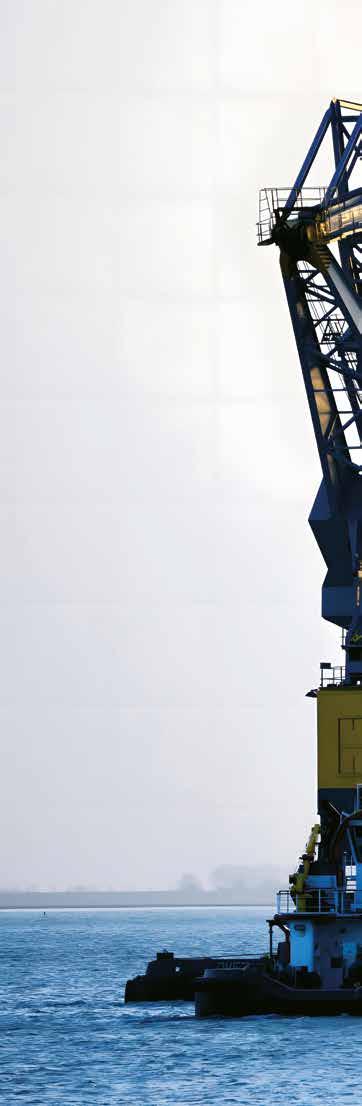
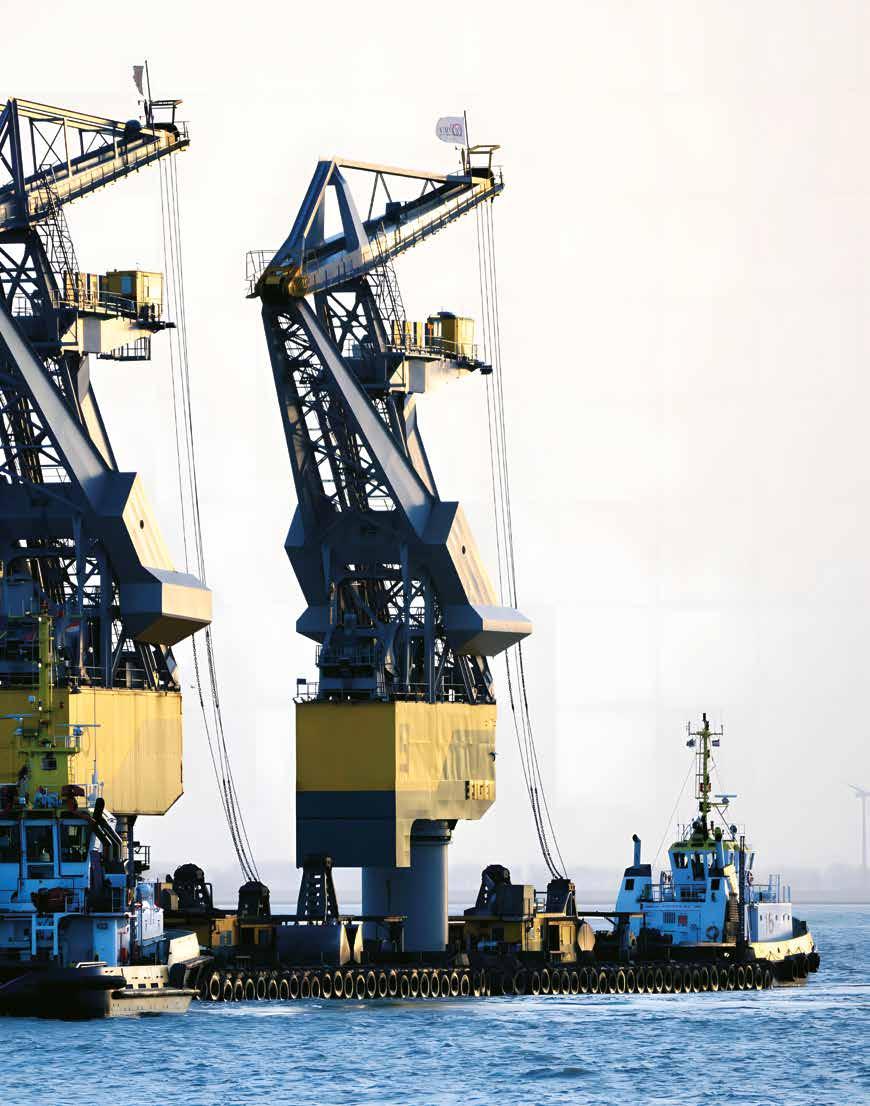
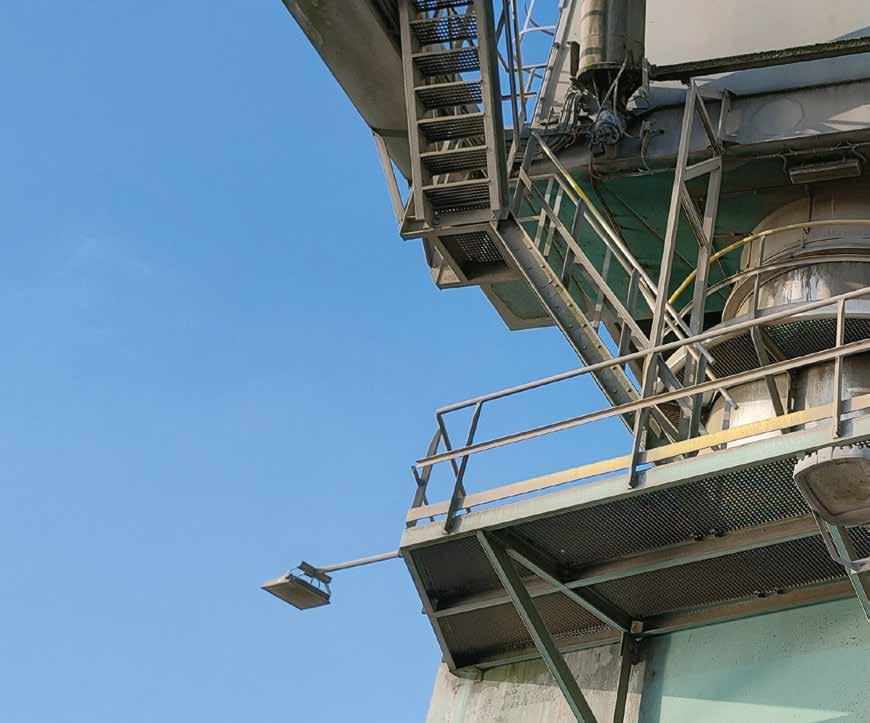
Bulk handling crane I Grab crane
Extendig the life of the grab crane at ENCI Rotterdam
The project
At ENCI Rotterdam, a Dutch cement producer, an old grab crane had already exceeded its expected life expectancy of 2 million lifting cycles. Iv was commissioned to inspect the entire crane and assess whether it could continue its work for another ten years.
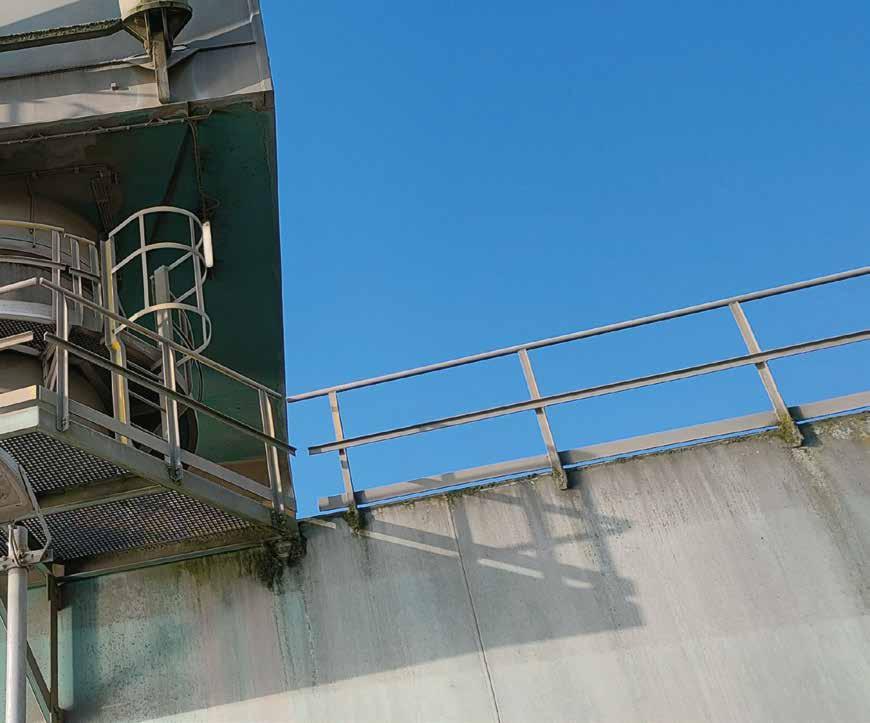
The challenge
As the grab crane had exceeded its expected life, it was essential to assess its safety and formulate an estimate of its remaining life. Iv received data on the number of loads and lifting cycles, after which critical points were inspected for possible crack formation. Wear was detected in several places on the slewing ring. The damage needed to be investigated to determine the cause and whether it could cause problems in the future. Iv advised more frequent lubrication and regular inspections to keep the crane operating safely for longer.
The impact
By properly maintaining and monitoring the crane, it can continue to operate safely for longer. Based on Iv’s advice, it was decided to give the crane a major overhaul.
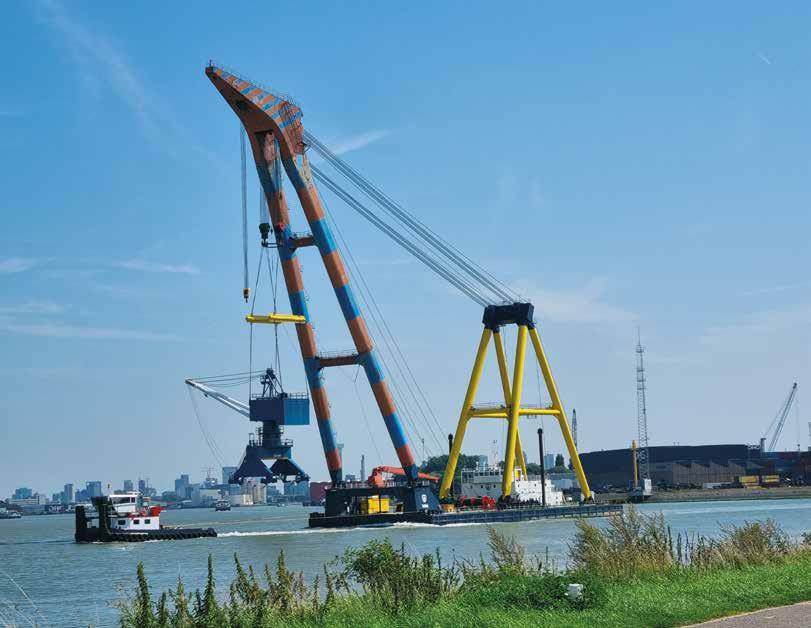
Grab crane renovation for Nobian
The project
The project concerns the renovation of a grab crane for Nobian, used to unload salt from vessels. The existing crane required thorough renovation, and various components needed to be revised or replaced. Iv played a central role in the project by drafting a Request for Quotation (RFQ) document outlining Nobian’s requirements. Iv assisted in guiding the tender process and supervising and monitoring the execution of renovation works from start to finish.
Grab crane
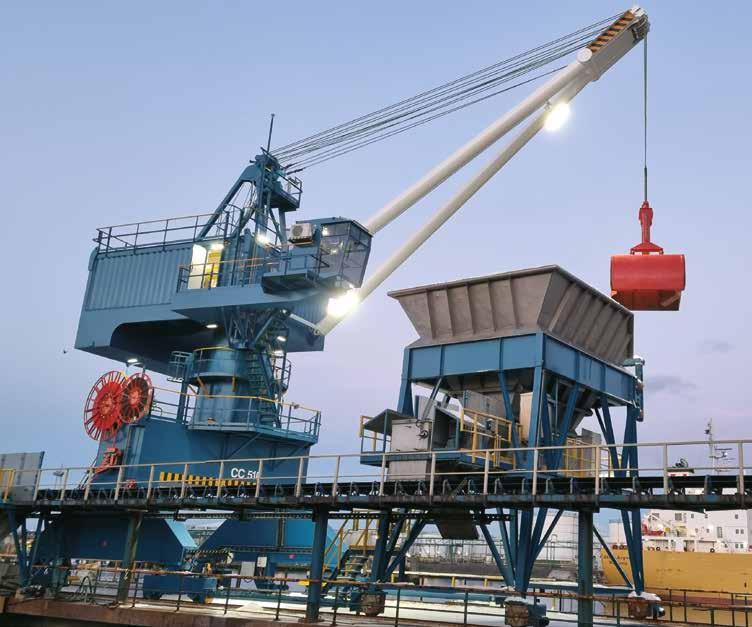
The challenge
Defining an accurate scope and working with the client to determine which components needed to be upgraded or replaced was critical to this project. We advised on the feasibility of a complete renovation versus replacement, resulting in a cost-effective solution. In addition, Iv designed a temporary repair for the slewing drive mechanism to safely bridge the period until the renovation could be carried out.
The impact
The renovation included the entire steel structure and revised gearboxes, contributing to sustainability and cost savings. The renovated crane was ready for operation in September 2021.
Offshore cranes I Gangway Telescopic gangway
Kenz Cranes
The project
Kenz Cranes wanted to develop an advanced offshore motion-compensated gangway capable of compensating for movements in 3D, thereby enabling offshore cargo transport up to 1000 kilograms. This gangway ensures the safe transportation of people and goods between a ship moving on the waves and an offshore installation.
The challenge
In the sometimes harsh conditions of offshore activities, safety is of the utmost importance. The transportation of people and cargo between a moving ship and an offshore installation requires an extremely stable and reliable passage (gangway). Iv was tasked with realizing this technically challenging project. We addressed not only the design of the passage but also its integration on the ship, the main frame, the gangway sections, and the bumper. In this process, we conducted calculations and took care of the mechanical engineering aspect of the project.
The impact
The 3D compensation system ensures that the gangway remains stable even during intense movements of the ship on the waves. This enables the safe transportation of people and heavy cargo to offshore installations, which is essential for the continuation of offshore activities.
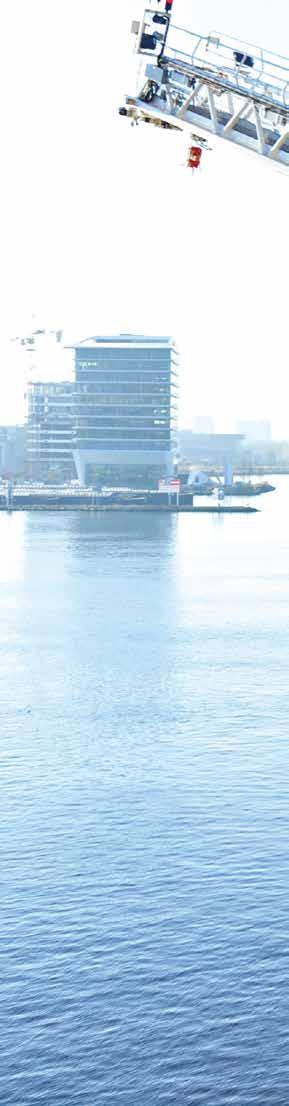
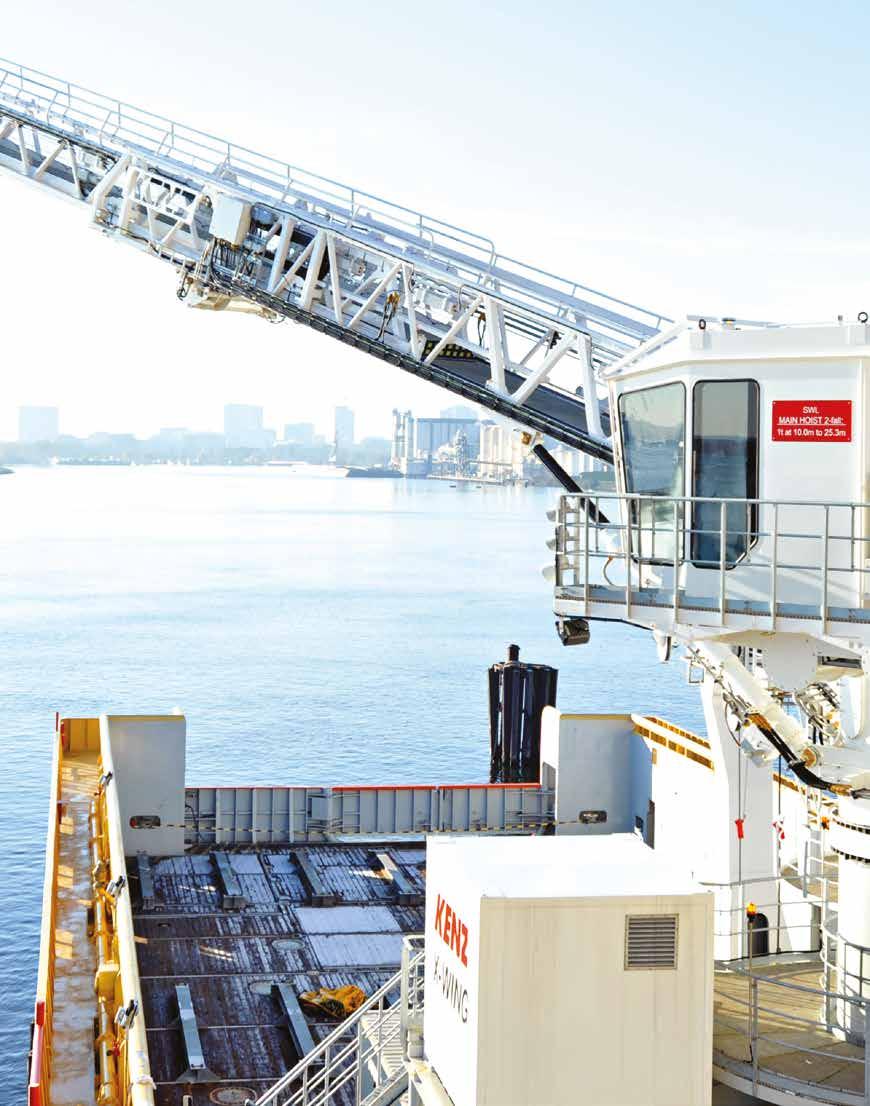
Offshore cranes I Lift analyses
Lift analysis for decommissioning
The project
How can the Murchison offshore platform be dismantled safely and in stages? To gain insight into this, Iv performed lift analyses for various platform modules on behalf of Heerema Marine Contractors. Some modules were missing lifting points and main load-bearing beams due to these being removed during previous works. Iv was commissioned to design new lifting points (pad eyes) and examine the module’s structural safety during the lift.
Iv carried out detailed lift analyses, including the creation of a computational model of the main structure with the correct weights and centre of gravity. The stiffness of the cables and applicable offshore standards were also taken into account. The module’s weight and centre of gravity were determined by weight reconciliation based on a thorough offshore survey. Furthermore, Iv verified the required cables (slings), the hook capacity, and the shackles.
The challenge
When designing the new lifting points, it was vital that they were placed in the correct location, taking into account the strength and stability of the structure, such as the columns and adjacent beams.
Although computers provide valuable insights, it is often essential to perform manual calculations to verify the local strength of the structure. This requires, among other things, a thorough knowledge of the platform’s history and previous structural adaptations. In particular, detailed structural drawings including welds, cross-sections and material types.
The impact
The collaboration between Heerema Marine Contractors and Iv has a long history. It allows us to benefit from each other’s expertise and skills, resulting in a safe and ‘fit for purpose’ outcome. As a result of this collaboration and thorough preparation, the Murchison platform could be safely removed with full assurance of structural safety.
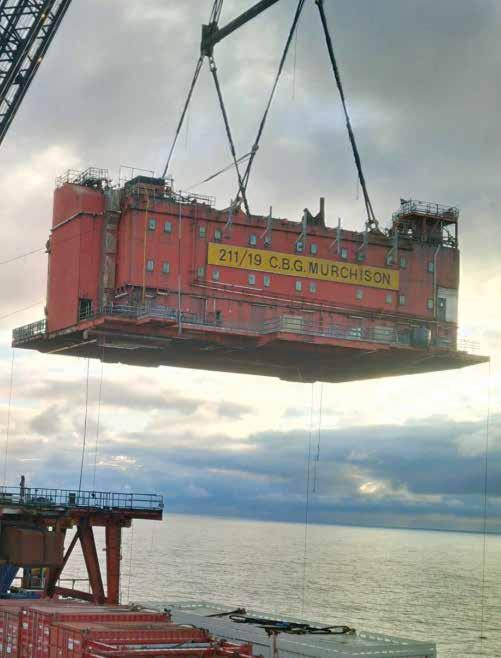
Offshore cranes I Stinger
Buoy handling system for Allseas’ Audacia
The project
For the Wheatstone project in Western Australia, Allseas required a system to handle buoys and other equipment on the stinger of their Audacia pipelaying vessel. In close cooperation with Allseas, Iv developed a feasible concept in the form of a box type crane capable of fulfilling these requirements. The scope of Iv was as follows: Concept design, basic design, detail design and preparation of workshop drawings of the structural and mechanical parts of the system including functional specifications of the required winches. The design of the winches and control unit were excluded.
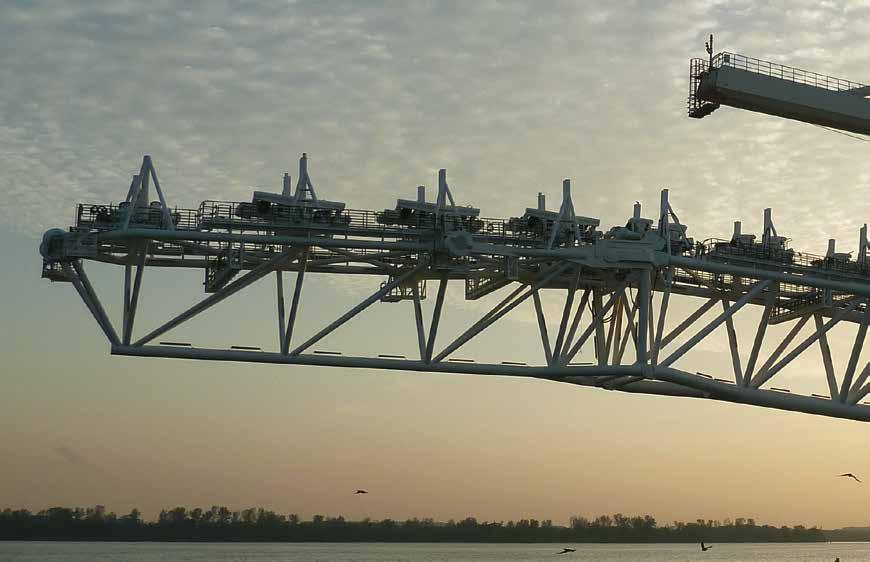
The challenge
Due to the fact that the system had to be installed on the ship during a pre-scheduled, major maintenance stop at a dock in Malaysia, the total lead time for the project was short.
The engineering process started with a rough sketch of a lattice boom attached to the SHF. In a one-day brainstorm session, this idea was abandoned because it did not fulfil some of the essential requirements. Instead, a box type bridge girder design was chosen that met all technical requirements, such as moving loads without an additional hoisting installation, a weight limit of 200 tonnes, and a height restriction to pass under the Bosporus Bridge.
The impact
The Buoy Handling System enabled Allseas to lift and move 35-tonne buoys without entanglement, allowing the Audacia to install pipelines more efficiently and safely in various water depths. The successful installation and operation of the Buoy Handling System contributed to the timely and smooth progress of the Wheatstone project.

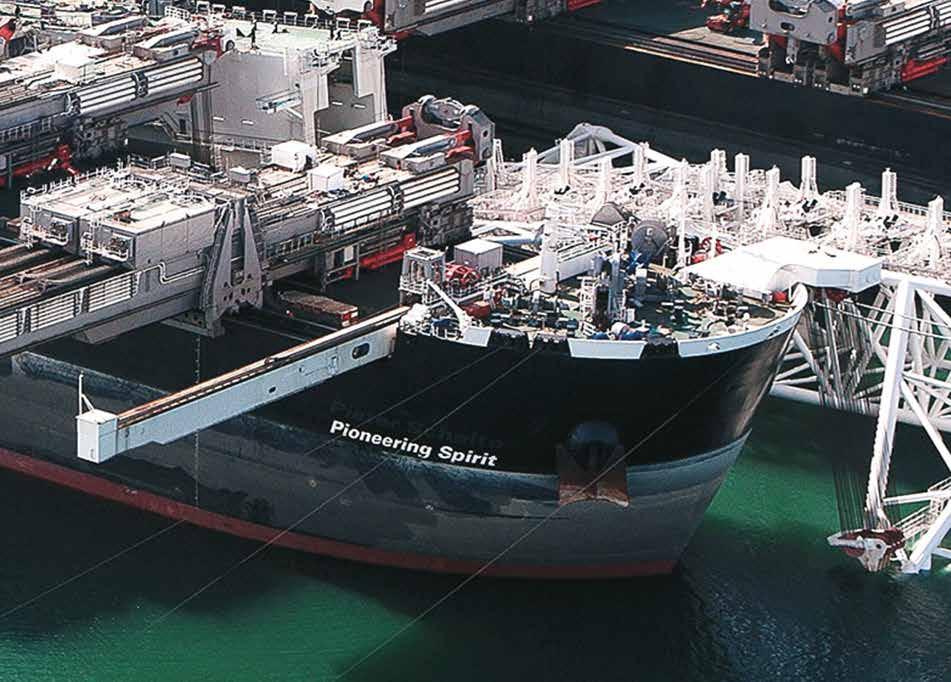
Offshore cranes I Stinger
Increasing efficiency and effectiveness
The project
Allseas’ ‘Pioneering Spirit’, the world’s largest construction vessel (382 x 124 metres), was designed to dismantle old offshore oil and gas platforms, lay pipelines at great depths and install platforms. A vital component of this vessel is the Stinger, which is approximately 210 metres long. The Stinger, which consists of the stinger transition frame and three separate sections of roughly 50 metres apiece, plays a key role in the Pioneering Spirit’s operational capabilities. Iv played a major role in the design of this Stinger.

The challenge
The main challenge for Iv was to design a stinger that fulfilled the size and strength requirements while remaining operationally efficient in severe weather conditions. The complexity of the Stinger’s functions, such as supporting pipeline laying operations at great depths, required advanced engineering skills and innovative approaches.
The impact
With this design, Iv has helped to increase the efficiency and effectiveness of one of the most critical components of the world’s largest construction vessel. This design has improved the operational capabilities for dismantling offshore installations and laying pipelines. The Pioneering Spirit will continue to be a ground-breaking vessel in the offshore oil and gas industry.

Crane tracks I Dry dock
Designing an efficient covered dry dock
The project
Alblasserdam Yachtbuilding Properties B.V. (AYP) specialises in developing, selling, and building highly exclusive and innovative superyachts under the name Oceanco. To realise yachts up to 140 meters, AYP needed assistance in constructing a covered dry dock. Iv was responsible for the substructure, consisting of the dry dock with foundation, the main dock door, and an intermediate door, as well as additional tasks such as demolishing and modifying a jetty, extending a retaining wall, designing a swivelling crane runway, and providing a sail-out facility for vessels.
The challenge
Designing a swivelling crane runway was a crucial aspect of the project, as the zoning plan did not allow structures on the exterior. Iv developed an innovative concept that made it possible to bring overhead cranes to the riverside. This design made it more efficient to transport hull sections and heavy components inside, which was essential for the construction of the dry dock.
The impact
The development of this dry dock enables AYP to take the next step in building luxury yachts, from 100 to 140-metre-plus yachts. The dry dock offers a highly conditioned workspace, including insulation and floor and wall heating, to ensure a high level of finish on the yachts. This project not only increases AYP’s capacity but also contributes to further growth and innovation in the superyacht industry.
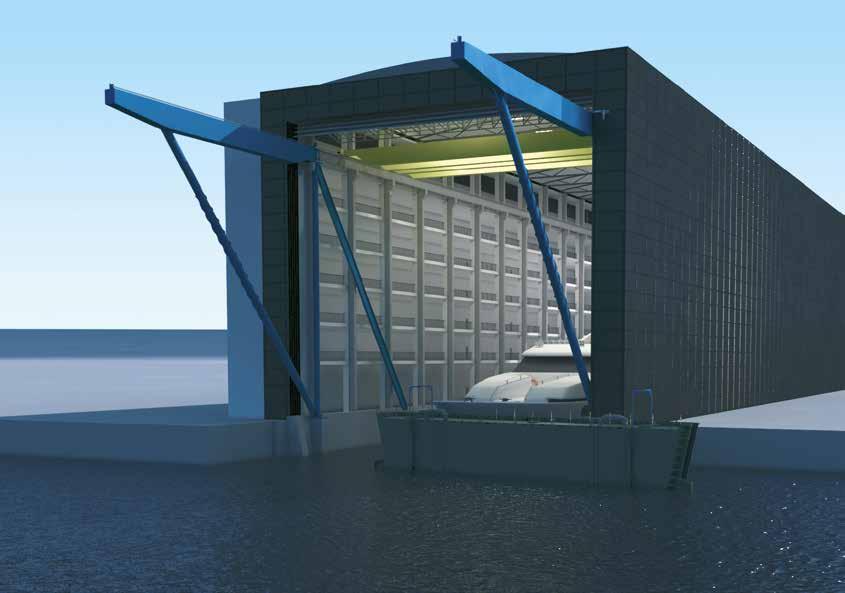
Equipment I Heave compensator
Safe, fast and efficient installation at sea
The project
Utrecht-based company Seaqualize has realised the impressive heave compensator, for which Iv was commissioned to design the steel colossus: the HC1100. The HC1100 tool is designed to make the installation of large components for offshore wind farms safer, faster and more efficient by compensating for the swell caused by waves.
The challenge
Installing heavy wind turbine components at sea is a complex task due to the motions of the vessels involved in the operation and the sea state. Traditional lifting methods only allow installation in favourable weather conditions. Seaqualize has developed the Heave Chief 1100 (HC1100), an innovative lifting tool capable of lifting and installing objects up to 1100 tonnes in sea conditions with wave heights up to 3.5 metres.
Iv designed all the mechanical components of the HC1100. Suspended from an existing offshore crane, the heave compensator tool compensates for the vessel’s motions, facilitating a more straightforward installation of heavy components for wind farms. The HC1100 can hold a suspended load of 1100 tonnes still against the vessel’s motions, allowing installation in more severe weather conditions.
The impact
The HC1100 offers significant advantages for the offshore installation of wind turbine components. It allows offshore operations to continue for more months of the year, helping to accelerate the energy transition. The wireless and efficient operation of the HC1100 reduces downtime associated with recharging and improves the overall efficiency of the installation process.
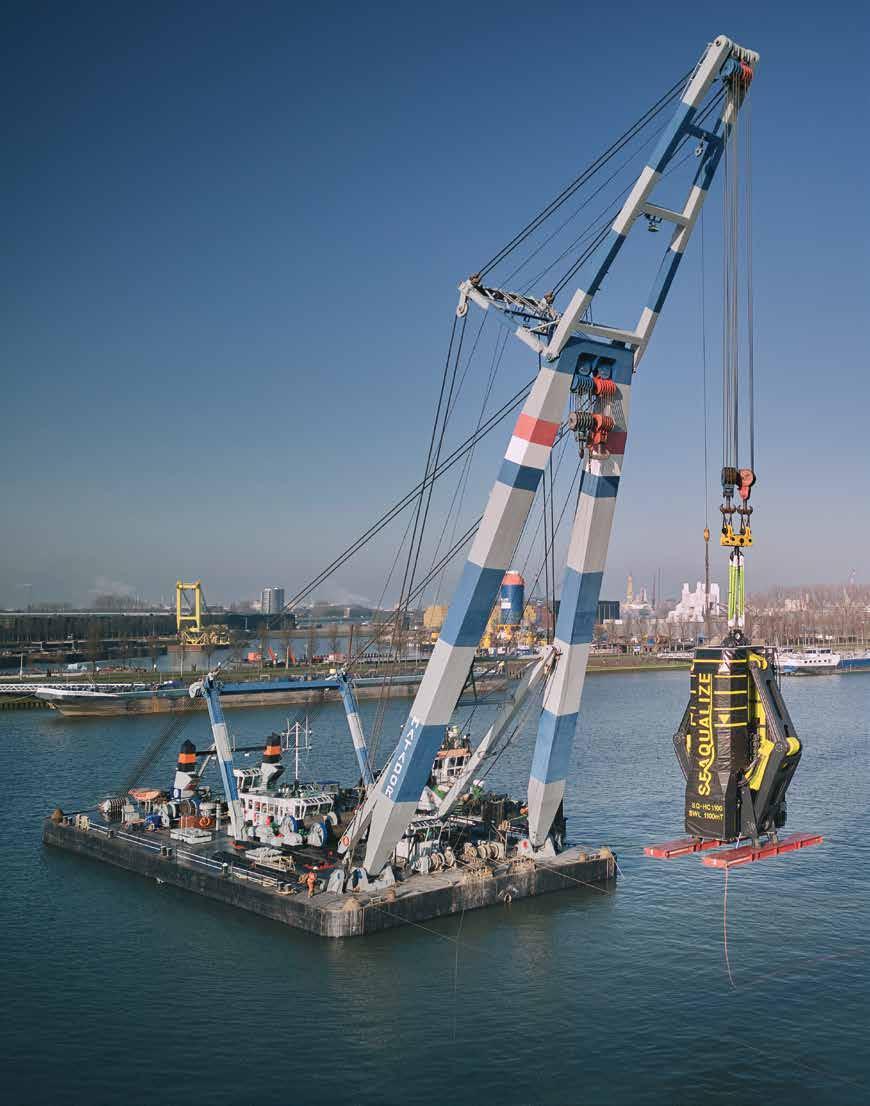
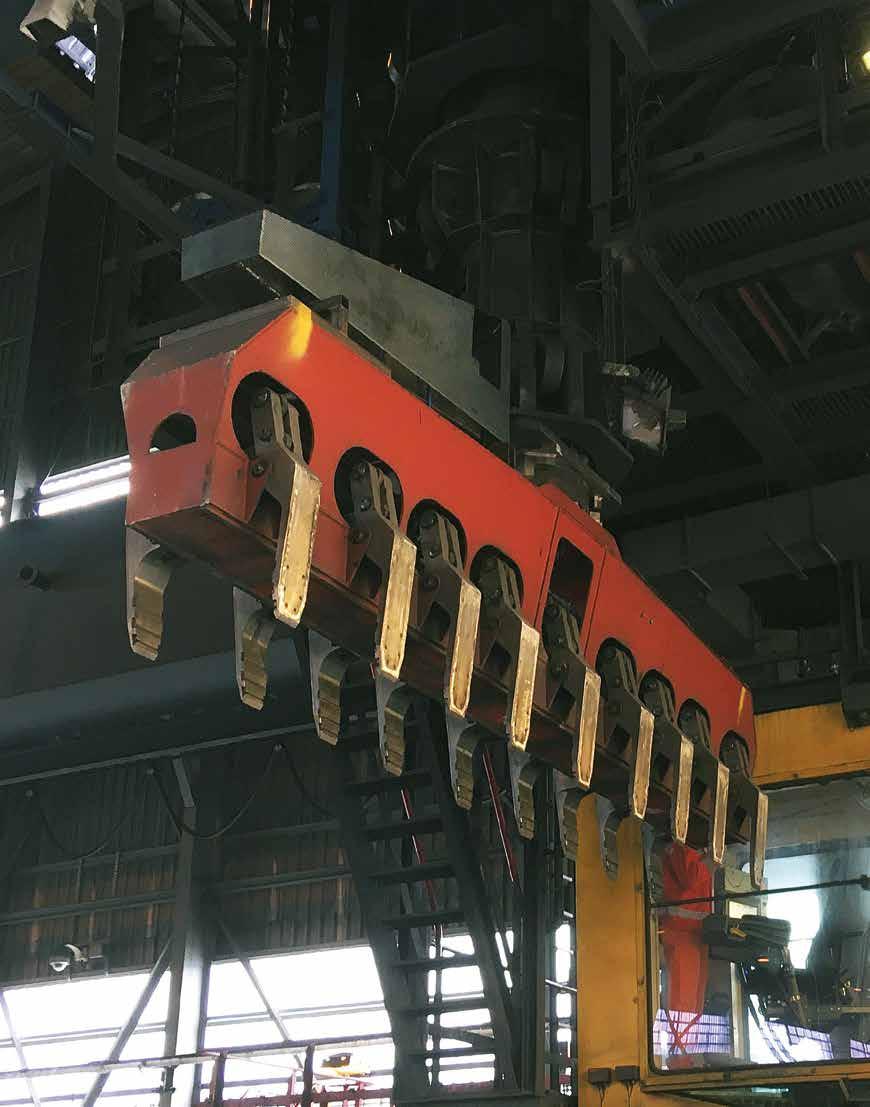
Equipment I Gripper
Redesign of outdated anode lifter
The project
Aluchemie, a now closed company that manufactured anode blocks for the aluminium industry, was using an outdated anode lifter. Anode blocks are carbon blocks used to conduct current when extracting aluminium. The lifter was used to move these heavy blocks safely. The anode gripper showed signs of wear and cracking and was in need of replacement. Iv was commissioned to redesign a new, improved anode gripper. This included performing a FEM analysis, thermal analysis, fatigue analysis and a structural analysis. Based on these studies, Iv provided advice on the best design choices, and working drawings were also made.
The challenge
Because the anode blocks were heated in furnaces, specific materials had to be selected that could withstand the high temperatures. The limited space in the furnace was a challenge when fitting the anode gripper. Moreover, the gripper had to be robust enough to safely move several large, heavy anode blocks simultaneously. The client specified that the design should allow for easy maintenance and that the operator should have a good view of the anodes from above.
The impact
The client received a report and a package of drawings to put the new anode gripper into production. The new anode gripper is designed to last 15 years and meets the requirements for high temperatures and robustness.


Equipment I Swivel headblock
Swivel headblock optimisation
The project
Container terminals experience problems with their container cranes when lowering and raising the headblock-spreader combination in the ship cells, both with and without a container. Due to deformation and damage in the ship cells, the combination often gets stuck. In these cases, the operator has to pull the combination at an angle to release it, which results in the hoist cables no longer running straight through the cable sheaves, leading to excessive wear of the hoist cables. Iv has developed a design that extends the life of the cables and increases safety without the need for an entirely new headblock. The designed modification allows the cable sheaves to tilt 5 degrees transversely. This ensures the cables remain straight under the headblock sheaves, even when the headblockspreader combination is pulled at an angle in a ship cell.
The challenge
The existing headblock structure had to be modified to allow the cable sheaves to tilt. For this purpose, the sheave blocks were cut loose from the main structure, and a pivot point was added between the main structure and the sheave blocks. End bearings were added to the pivot structure to limit the maximum tilt angle to 5 degrees, while torsion springs ensure that the cable sheaves return to their initial position after tilting.
This modification of the existing headblock, rather than a completely new design, required detailed analysis and recalculation of the steel structure.
The impact
Thanks to the implementation of the modified headblock, the wear on the crane cables is significantly reduced, resulting in lower maintenance costs and longer cable life.
Skills
Technical expertise
• Design & Engineering, upgrades, refurbishment and modifications
• Design review
• RFQ management
• Build management
• Inspections: drone and visual
• Measurements
• Natural frequency analysis
• Wind tunnel testing
• Transport analysis
• Fatigue crack monitoring (by using Villari sensors)
• Lifetime analysis
• Lift analyses
• 3D scanning
• Building Information Modeling (BIM)

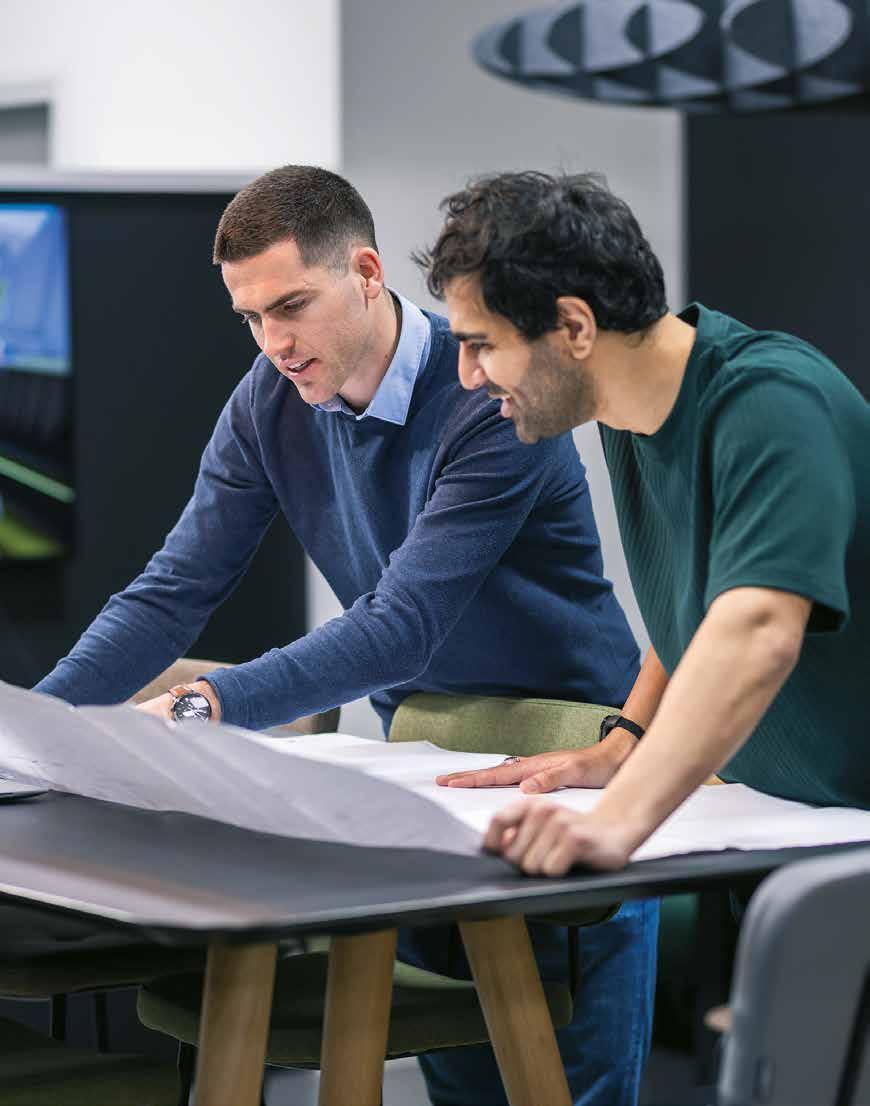

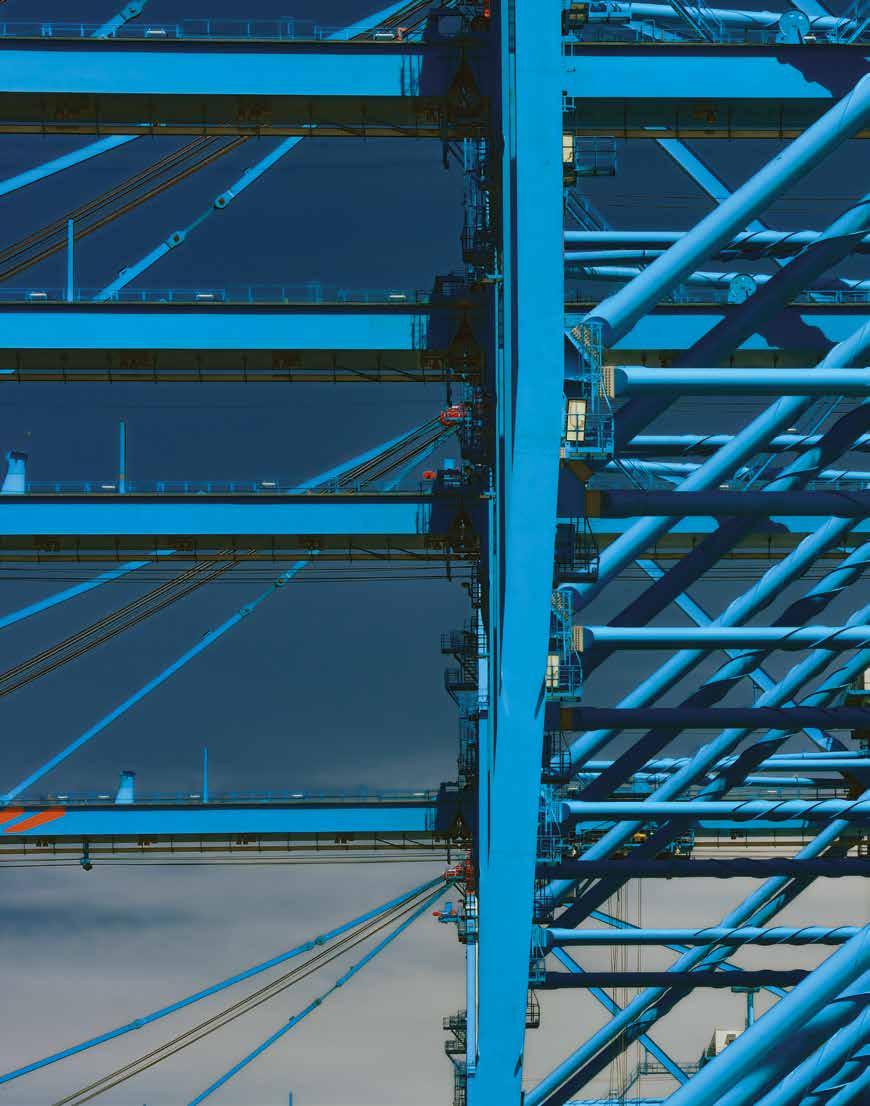