Offshore brochure I September 2024
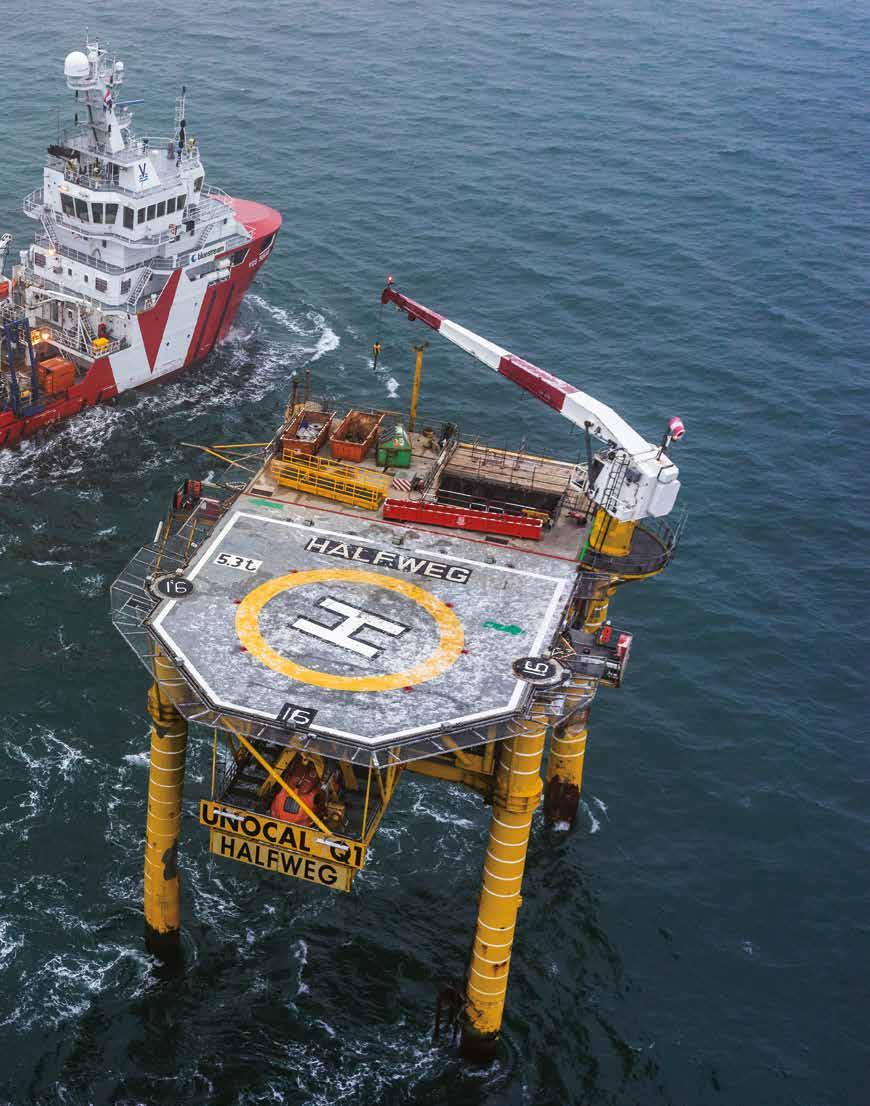
Engineering that excites
Offshore brochure I September 2024
Engineering that excites
Iv is a globally operating multidisciplinary engineering company that provides advanced technical solutions in the following sectors: Energy & Offshore, Infra & water, Industry, Buildings and Maritime.
Within Iv, Nevesbu specialises in naval architecture and marine engineering for the maritime sector.
Nevesbu and Iv are highly specialised in naval architecture and the design and engineering of complex steel and mechanical structures. We deliver advanced solutions for offshore transport, installation, and decommissioning projects. Regardless of the complexity involved, we are a reliable partner, ensuring the safe and predictable execution of offshore operations.
We have worked on a wide range of equipment and vessels, including the Balder, Aegir, Pioneering Spirit, Seafox4 and Nexus. These vessels have successfully carried out some of the most challenging offshore operations. We have also developed various patented innovations that enhance our capabilities.
The offshore industry is undergoing major developments. The larger size of offshore installations and the greater sea depths at which they are installed require different handling equipment. By combining our expertise across multiple sectors and pushing the boundaries of technology, we provide advanced solutions for even the most complex offshore operations.
Whether it concerns modifications to existing vessels or equipment or the development and integration of new equipment: our services range from feasibility studies and concept designs to (parametric) design of (motion compensated) equipment, workshop drawings, and platform system integration. We ensure that equipment meets stringent safety, reliability, and availability requirements. We also advise on end-of-life applications, sea-proofing calculations, loadout and transport analyses, lift analyses, and drivability analyses.
With an integral approach, we ensure that all subsystems function as a whole, guaranteeing optimum performance at sea. With decades of experience, Iv is renowned for its innovation, offering solutions for heavy lifting, pile handling, cable laying, and modular equipment designs that can be adapted to specific project needs. This wealth of expertise supports the execution of complex offshore projects, and enhances operational safety and efficiency.
The safety, reliability, and availability of offshore assets are crucial for any offshore operation.
To ensure offshore assets continue to perform optimally, we provide support throughout their operational life across various engineering and technical disciplines.
With services such as surveys, maintenance engineering, asset management, obsolescence management, technical assistance, seaworthiness certification & management support, pressure hull stability assessments, damage tolerance analysis, and structural integrity verification, we help clients achieve safety, reliability, maintainability, and availability throughout the entire life cycle.
Equipment must be integrated in the right pllace on the vessel for optimum performance. We integrate new and existing systems into a single, modernised platform using specialist system integration services. We also monitor and manage critical vessel systems, including safety, structural integrity, weight and stability, and compliance with shock, noise, and environmental requirements, ensuring that all subsystems function as an integrated unit.
Marine engineering covers the systems that support a vessel, from power generation and distribution to ballast water management, firefighting and HVAC (heating, ventilation and air conditioning). We take care of the design and engineering of marine systems and the layout of technical spaces from feasibility studies, including review of operational and ergonomic requirements, up to the basic and detailed design of equipment mounting, piping, cable routing, penetrations, etc.
The structural integrity of marine vessels and floating units used for operations at sea is an essential prerequisite for successful operations. We have developed a method with a direct link to FE (Finite Element) analysis to accurately map the response of vessels and offshore structures to specific environmental conditions.
Applying advanced hydro-structural analyses in an early phase of conversion, life extension or redeployment projects provides a more realistic assessment of the hull’s condition. This allows structural reserves to be utilised while identifying weak areas requiring upgrading. A typical example of where such an approach can pay off is the redeployment of FPSOs. Hydro-structural analyses can also be applied to other offshore units such as FLNG units and possible floating energy conversion facilities, for example, for hydrogen production.
Our hydro-structural approach provides the appropriate insight to assess the vessel’s suitability and the extent of structural work required to accommodate the field. The tendency across the industry is to extend the life of high-value assets as much as possible. The processes on board typically govern the asset’s value, while the hull keeps the asset afloat. Typical examples include drilling vessels, pipelaying vessels, heavy lift vessels, but also military vessels. All of which have been shown to exceed the standard thirty-year operational life.
Hydro-structural coupling, particularly in the early phases of conversion or life extension projects, helps to avoid the conservative estimates typically made in initial fatigue calculations. It provides detailed insight into the actual structural condition of the hull by incorporating improved environmental data, operational profiles, and feedback from inspections. This method offers more consistent results than traditional load combination methods, helping to minimise structural modifications and reduce production costs.
General FEA software is not always suitable for analysing equipment for fatigue, so Iv has developed its own fatigue analysis tool that can be used with Ansys Mechanical. This tool allows for efficient and automated fatigue analysis of specific details based on cyclic or spectral loading. The results, including fatigue damage or the required detail categories, are visually represented in a 3D model, allowing problem areas to be quickly identified. Automating the fatigue calculations reduces manual errors, and lead times are significantly improved. The tool supports fatigue analysis in accordance with EN13001, EN1993-1-9 and DNVGL-RP-C203 Recommended Practice.
Offshore operations and fatigue management
In offshore operations, fatigue is a critical factor due to the challenging environment.. Our tool helps to ensure the longevity and safety of offshore structures by providing precise fatigue calculations, reducing the risk of failure, and extending the operational life of offshore assets.
Monitoring and advanced sensor technology
Iv has integrated advanced sensor technology into its fatigue analysis services. The use of crack detection systems, which monitor the early stages of crack formation in fatigued steel, offers significant advantages over traditional methods. These sensors, combined with Iv’s extensive experience in structural design and fatigue analysis, enable clients to maintain and extend the life of their assets in a cost-effective and safe manner. Continuous monitoring provides real-time data, enabling proactive maintenance decisions and improved safety across multiple structures.
The energy transition is in full swing around the world. Accelerating processes to speed up the transition is very complicated. But it is necessary because resources, materials and labour are scarce and often already fully utilised.
Iv has helped the Dutch company Seaqualize develop the design for the Heave Chief 1100 (HC1100), a new lifting tool designed to handle the unique challenges of offshore wind farm installation. This device compensates for vessel movements at sea, enabling a safer, faster and more efficient installation of wind turbine components weighing up to 1100 tonnes. As a result, work on offshore wind farms can continue in stronger winds and higher waves, which is not possible with conventional systems.
The HC1100 from Seaqualize is a breakthrough in this regard. This offshore lifting device is currently the largest active heave compensator in the world. Iv was asked to design this steel colossus and was responsible for the complete engineering, including the workshop drawings. The technology significantly reduces the risk of damage to vessels and materials during installation. The HC1100 has been successfully tested and is operational since the summer of 2023.
“Iv has been a very dependable partner all the way through: they are realistic in their planning, to-the-point and efficient in their communication and they had all the structural design expertise we needed on board. In particular, the knowledge required to design complex, actuated, high-precision, heavy-load offshore tooling was present and available. They are committed to the success of our project, meeting the deadlines and fixing unexpected issues as they arise. They have a ‘let’s fix it’ mentality, don’t waste time on unnecessary discussions, and are available in emergencies. We consider them to be a solid partner in the development of our products.”
Gjalt Lindeboom, Seaqualize
Technical challenges
Installing heavy wind turbine components at sea is a complex task due to the motions of the vessels involved in the operation and the sea state. Traditional lifting methods only allow installation in favourable weather conditions. Iv designed all the mechanical components of the HC1100. Suspended from an existing offshore crane, the heave compensator tool compensates for the vessel’s motions, facilitating a more straightforward installation of heavy components for wind farms. The HC1100 can hold a suspended load of 1100 tonnes still against the vessel’s motions, allowing installation in more severe weather conditions.
Operational impact
The HC1100 offers significant advantages for the offshore installation of wind turbine components. Its compact design enables it to lift and install heavy wind turbine components from a floating vessel onto fixed or moving objects, even as the crane vessel rolls and pitches.
This innovative tool allows offshore operations to continue for more months of the year, helping to accelerate the energy transition. Additionally, the HC1100’s wireless and efficient operation reduces downtime associated with recharging and improves overall installation efficiency.
An offshore motion-compensated gangway assures the safe transfer of people and goods between a wave-riding vessel and an offshore installation, which is essential for continuing offshore activities.
Telescopic gangway
Kenz Cranes wanted to develop an advanced offshore motion-compensated gangway capable of compensating for motion in 3D, thereby enabling offshore cargo transport of up to 1000 kilograms and ensuring stability even in harsh offshore conditions. This stability is crucial for maintaining safety and operational efficiency in offshore environments.
Design and engineering
Iv designed the vessel integration, main frame, gangway parts and bumper, prepared structural calculations, handled the mechanical engineering aspects and produced the workshop drawings. This comprehensive involvement in the design, engineering and integration of the gangway has resulted in a system that significantly enhances safety and reliability in these challenging conditions.
In the Dutch offshore wind farm Hollandse Kust West (HKW) VII, around 53 kilometres off the coast of IJmuiden, the TotalEnergies/RWE consortium is developing a new form of sustainable energy generation. As part of the project, the world’s largest floating solar platform will be integrated alongside wind power generation. The floating solar platform is an innovative solution devised by the Dutch-Norwegian company SolarDuck and will be located between the wind turbines. The platform will consist of floating, interconnected triangular structures with solar panels. SolarDuck selected Iv to conduct the technical development and optimisation of this innovative concept to ensure that it meets all the requirements for installation and use at sea.
The floating solar platform
The floating solar platform that will be installed in the HKW VII wind farm is based on the Merganser test platform, a prototype solar platform with an energy generation capacity of 520 kWp (kilowatt peak) that was installed as a pilot 12 kilometres off the coast of Scheveningen in the North Sea. The often-harsh North Sea environment in which the HKW VII wind farm is located is considered one of the most challenging offshore environments in the world. Iv is applying its extensive offshore knowledge and experience to help optimise the existing design for these unique conditions.
By installing the platform between the wind turbines, the space at sea is used as efficiently as possible, and the grid system, which has already been installed for the wind farm, can also transport the electricity yield to shore. In addition, the maintenance of both energy systems can also be combined to take place simultaneously.technique that can be employed globally.
High potential worldwide
The possibility of realising more large solar parks on land in densely populated areas is decreasing. However, the demand for sustainable energy is only increasing, and this trend is set to continue.
The floating solar platform is a solution to help electrify countries worldwide and provide security in supplying affordable, sustainable energy. It is a suitable solution for increasing sustainable energy supply, particularly in densely populated countries with lower average wind speeds and higher solar irradiation levels.
From idea to sea
SolarDuck started with this idea five years ago. But how do you get such an innovative solution to work at sea? How do you achieve a reliable structure that will operate for at least 30 years without maintenance? And how do you ensure that the entire project can be safely installed offshore? In addition to the overall technical optimisation of the design, Iv is advising SolarDuck on hydrodynamics (the motions the structure undergoes due to the waves), anchoring and installation. Iv is also responsible for ensuring that the design is approved by the classification society. The harsh conditions at sea subject structures to fatigue and corrosion, among other things. Besides this, the structure must be able to properly absorb the motions of the waves so that the systems on the structure (such as solar panels and subsystems) are not damaged. Iv, as an experienced engineering company, specialises in such issues.
“It’s awesome to be involved in the development of new technology”, says Pieter de Boer, lead engineer at Iv. “A solar park at sea, fully functional and at this distance from the coast, has never been done before. From a technical point of view, it is incredibly challenging and complex. It takes a lot of creativity to make it technically, financially and safely feasible.”
Simulation
But what makes it so complex? It goes without saying that creating something new is, by definition, no easy task. Among other things, the ‘behaviour’ of all the different platforms of the solar park is special and an important aspect. Pieter: “These all influence each other to a certain extent. It is quite a challenge to simulate the behaviour in the right way. Another factor is that people are present on the platform from time to time. We want them to be able to do their work as safely as possible, so we have to include that in the design.”
Iv is currently researching how the solar park will eventually look in terms of the number of platforms, the layout, and the exact location. The floating solar park is expected to be completed in 2026.
The demand for sustainable energy is only increasing.
For the Wheatstone project in Western Australia, Allseas required a system to handle buoys and other equipment on the stinger of their Audacia pipelay vessel. In close cooperation with Allseas, Iv developed a feasible concept for a Buoy Handling System (BHS) in the form of a box-type crane attached to the SHF.
The crane can be used to guide buoy(s) further down the stinger and for onboard lifts into the firing line. Iv was responsible for the concept design, basic design, detailed design, and preparation of workshop drawings of the structural and mechanical parts of the system, including functional specifications of the winches required.
We are faced with a major challenge: hundreds of oil and gas platforms in the North Sea will be repurposed or decommissioned in the coming years. As a result of the energy transition and sustainability goals set by the Paris Climate Agreement, the use of fossil fuels will continue to be scaled back. Along with this, platforms will be removed. It is essential that these platforms, including topsides, jackets, and infrastructure, are removed in their entirety.
Dismantling oil and gas platforms contributes to the circularity of material use. A platform can easily carry 5,000 tonnes of steel. This steel is cut into pieces at the shipyard and largely reused, saving millions of kilos of steel from unnecessary waste. Moreover, removing old platforms creates space in the North Sea to produce green energy. Iv assists platform owners with the dismantling process, better known as ‘decommissioning.’
Extensive preparatory work is required to completely dismantle oil and gas platforms and safely transport them to shore. This work includes offshore inspections, weight calculations, and determining the centre of gravity of the topside and jacket. Existing documentation is also reviewed and verified. Lifting and transportation analyses are then carried out. Additional measures are taken if necessary, such as applying additional lifting points. The structure used to transport the platform, the ‘grillage,’ is also designed by Iv. Following the arrival of a decommissioned platform at a shipyard, a loadout analysis is conducted.
Decommissioning of the Petrogas Halfweg platform
Iv was commissioned to perform a FEED study to prepare for the removal of the platform. The study aimed to investigate the structural integrity of the platform during removal and sea transport. Towards the end of the tender process, a collision with a chemical tanker occurred. As a result, all plans were frozen, and immediate action was taken to assess and determine the damage. Iv carried out a FEM vessel impact analysis based on damage and distortions photographed and scanned by a drone. The goal was to demonstrate the stability of the platform and identify possible obstacles for the removal. Once all the defects had been identified, the design for the necessary reinforcements to safely lift and transport the platform was prepared.
The offshore wind industry is going through major developments. Heavier wind turbines are needed to generate a higher energy yield in areas with constantly high wind speeds. Large wind turbines with a capacity of up to 20 MW, far above sea level, are preferably placed further from the coast. However, this makes offshore work activities expensive.
Iv has developed a patented concept of a ‘gravity-based’ wind turbine secured to the seabed with tendons (cables). Our self-installing wind turbine is suitable for greater water depths of approximately seventy to five hundred metres and, as an alternative to the ‘gravity base’, the system is easily adaptable for applying so-called ‘suction anchors’.
The further away from the coast the wind farms are, the deeper the water. This makes it much more expensive to install wind farms in the traditional way. This fact calls for new, innovative concepts. Extensive research revealed that it would be almost impossible to produce a new overall concept for floating wind turbines due to the large number of ideas already presented. Instead, it was decided to focus on an innovative concept for greater water depths, resulting in a self-installing wind turbine with tendons (cables) and a ‘gravity base’.
The challenge is to create a self-installing wind turbine that can be used in deeper water where traditional foundation structures are inefficient. Developing the concept required a lot of brainstorming, sketching, designing and discussions within the team. The patent application process was complicated and required extensive review and collaboration, but the final grant of the patent was seen as an outstanding achievement.
Iv has developed a patented method for the faster and quieter removal of monopiles (foundation tubes) from wind farms and offshore oil and gas platforms in the North Sea. Our monopile remover is a patented method for removing entire monopiles from the seabed by allowing plastic deformation. Advantages of the monopile remover:
• Universally deployable from any heavy lift vessel.
• Removal is virtually silent, minimising marine disturbance.
• Monopiles are fully recyclable, leaving no residual parts in the seabed.
Innovative technical solution
Currently, monopiles are sawn off or cut off, leaving a section in the seabed. The pulling technique developed by Iv can remove the pile entirely. The monopile remover is a special crane attachment designed to achieve optimum grip on any slippery pile. This allows the crane to pull the pile right out of the seabed. The crux of this innovation lies in the crane’s special attachment. It clamps around the monopile and squeezes several dents at two different heights in the steel pile. This produces a hump in the profile of the pile, whereby the crane can obtain an optimum grip with the same attachment on the otherwise smooth pile. As a result, vertical forces transfer well, and the crane can pull a pile out of the seabed in no time.
The monopile gripping method allows for an efficient and quiet dismantling of offshore platforms in the North Sea, freeing up space for the further development of green energy. Its unique ability to completely remove monopiles from the seabed and repurpose them reduces the use of new raw materials and remnants in the sea. This actively contributes to a better climate and directly addresses key environmental issues. Furthermore, this method causes virtually no noise disturbance to marine life. The method is not only applicable in the North Sea but also worldwide, making it a universal method that can be deployed globally.
The Seafox 4 is a six-legged jack-up platform for construction, accommodation, maintenance, and well services. The platform can be used throughout the year in water depths of up to 46 metres.
Following an all-over upgrade, the Seafox 4 has now been made suitable for special offshore services, enabling its use for multiple types of projects, thus expanding its range of applications.
Nevesbu was responsible for integrating the heavy lift crane into the vessel, conducting the analysis of the helideck prior to its adaptation to handle larger helicopters, performing stability calculations, and securing class approval. The upgrade ensures that the Seafox 4 meets current offshore service requirements and enhances its versatility for a broader range of offshore services, making it a valuable asset for diverse and complex offshore projects.
Van Oord’s Nexus is a new cable-laying vessel designed to install electrical cables for offshore wind farms. The vessel is specifically designed to handle challenging cable installation tasks, ensuring reliable connections for offshore wind energy.
Nevesbu was involved from the very beginning in the design of Nexus. One of the main challenges was ensuring the vessel’s damage stability, particularly with the long and low aft deck, which was crucial for the safety of the many people on board. The final inclination test was made more complex by the significant amount of mission system equipment already on board. Nevesbu completed the project by preparing the onboard stability documentation, which Lloyd’s Register fully approved.
Van Oord’s Nexus is now an essential asset in safely laying electrical cables, contributing to the energy transition and ensuring the long-term success of offshore wind projects.
According to expectations, 1800 gigawatts (GW) of offshore wind energy will be generated by 2050, of which 250 GW will be generated from floating wind farms. Offshore substations are required to efficiently transport 250 GW of renewable energy from sea to shore. At water depths beyond 150 metres, the costs of the renowned ‘bottom-founded’ solutions increase exponentially, making floating solutions an interesting alternative. In fields with water depths beyond 300 metres, a floating offshore substation (FOSS) will be required.
Nevesbu and Iv have investigated and compared several floating substation concepts in recent years, including different floater types. Currently, the main focus is on developing a substation concept based on proven Tension Leg Platform technology, which turned out to be the most promising floater type.
The concept developed by Nevesbu and Iv is designed to convert 1.4 to 2.0 gigawatts of power, with a DC export link of 300 to 525kV. A typical HVDC topside weighs about 13,000 to 20,000 tonnes. The floating HVDC platform has a deck area of 85 by 85 metres and rises approximately 25 metres above the water’s surface. The overall arrangement has been optimised for application on a floating substructure. When the platform is installed at sea, it will be held in position with the help of so-called ‘tendons’ vertically anchored to the seabed, restricting the vertical motions and accelerations caused by waves.
Dynamic inter-array cables are already being developed and tested at full scale in floating wind turbine pilots around the world and are, therefore, considered mature before deployment of the first FOSS units. The DC export cables, on the other hand, are more vulnerable to fatigue due to the large core and surrounding metallic sheath. Nevesbu developed a patented cable guide system that solves the fatigue problem for the DC export cable (CGS).
In October 2023, Nevesbu tested the floating substation concept with different configurations of the cable guide system (CGS) in model scale at MARIN. After the successful testing campaign of the floating substation, in combination with the in-house developed cable guide system, the FOSS concept is at Technology Readiness Level 3 and ready for further development.
The OSPA Convention requires the offshore industry to remove platforms that are no longer in production. The removal of platforms requires considerable engineering and design to ensure the safe operation and transportation of the structure. Iv-Consult has built up a solid track record in offshore decommissioning over the last 12 years, with a strong focus on reusing existing grillage/ materials.
Iv has experience in preparing concepts, detailed designs, and workshop drawings, including facilities for the safe lifting and/or lowering of platforms and design checks in relation to the capacity of the vessel. Designs for installation are considered to be quite similar to those required for removal. Therefore, designs can be made suitable for both loading and unloading situations.
Grillage and sea fastening are crucial for the safe transport of large components by sea, such as platforms and wind turbine components. The grillage ensures even weight distribution and prevents damage to the vessel. This requires the safe securing of loads and an understanding of load movement to ensure the correct choice and installation of fasteners.
When it comes to offshore transport and installation, everything has to be right the first time. Offshore structures may not sustain damage or fall overboard during transport. Iv designs grillage and sea fastening structures that absorb all forces and accelerations, ensuring smooth sea transport. Iv provides top-quality reports and designs to ensure safe and reliable transport in challenging conditions.
Managing all the interfaces is essential as the new generation of offshore structures grows in size and weight, pushing vessels to their limits. Iv performs inspections of the vessel and its structure, calculates the strength, stability, and loads, and designs the connections in accordance with applicable standards. Where possible, Iv aims to reuse the client’s materials.
Engineering that excites