Ivormatie magazine
Exciting engineering
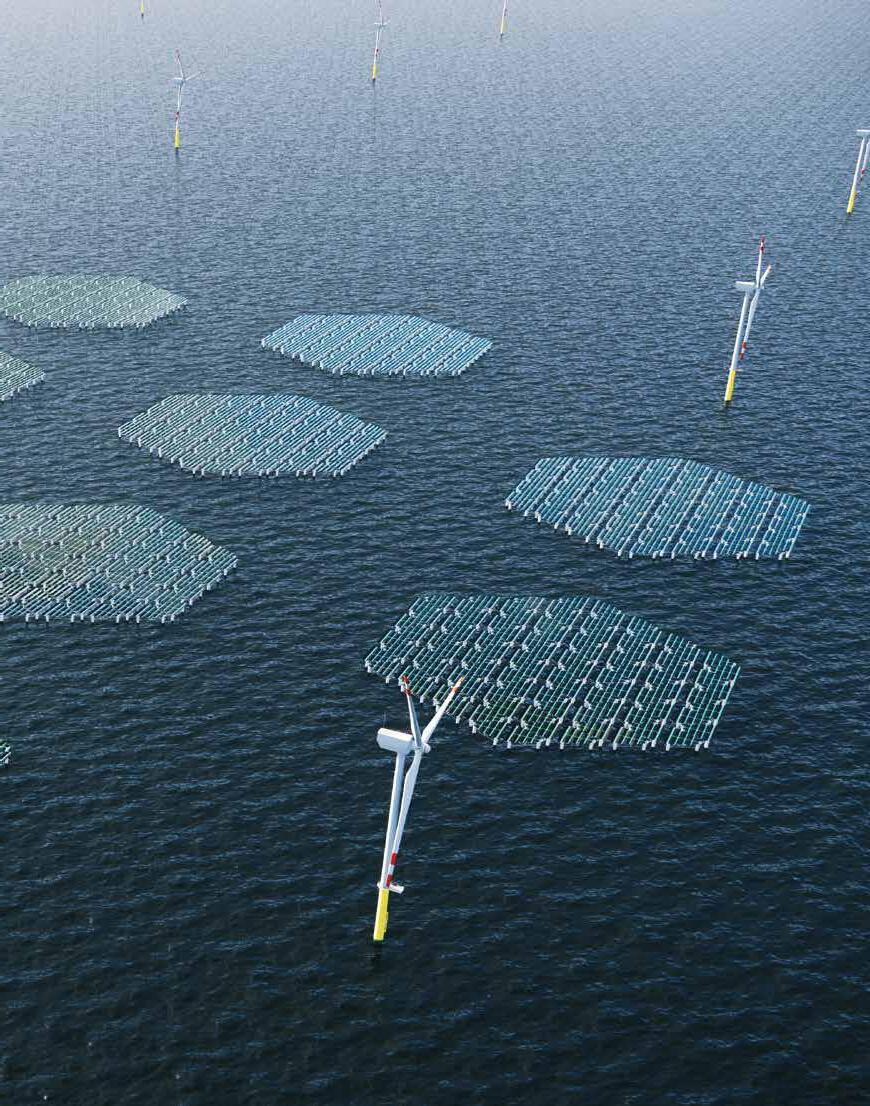
Engineering that excites
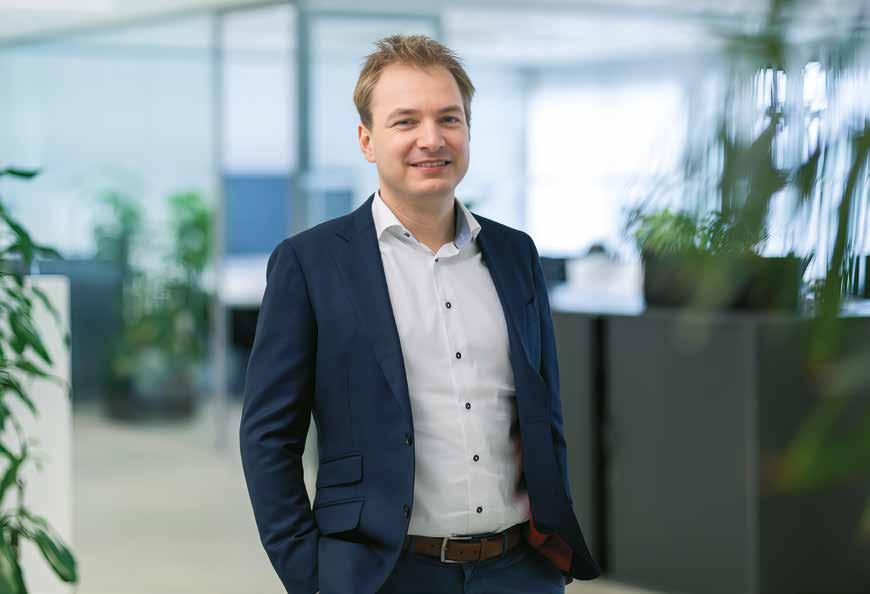
We are called upon to produce solutions that genuinely benefit society.
This month, Iv is officially 75 years old. A special milestone that allows us to look back in depth and with pride on all that we have achieved and done in three quarters of a century.
We have a lot of special things to look back on. But fortunately, an anniversary is not only about the past. It also gives us the opportunity to reflect on what we are currently working on and what lies ahead. And that is a lot! With more than 1,300 colleagues, we work on amazing projects that put us to the test. We are called upon to produce solutions that genuinely benefit society. This is exactly who we aspire to be as a company and what we aim to achieve: working on challenging projects that allow us to utilise our technical expertise fully. In short: engineering that excites!
This approach will ensure that we can continue to focus on special projects with renewed energy now that the summer holidays have ended. For example, for the drinking water company Dunea, we are helping to find a new source of drinking water; a unique project. For PALLAS in Petten, we are working on the design of a new medical isotope reactor that will help treat thousands of cancer patients every day. Another example is the impact of our work on the energy transition: Iv has designed more than a quarter of all existing offshore platforms in the European Union, a significant contribution to the energy transition. You can read all about this and much more in this brand-new issue of Ivormatie.
Our 75th anniversary is also the perfect time to give our magazine a new look. In a new house style, with our new pay-off: engineering that excites. And to prove that we have not lost our passion for technology, look no further than all the wonderful and challenging projects we are working on. We want to be proud of the work we do. In these times, there are more than enough challenges out there where we can get involved and make improvements in the world, whether it concerns sustainability, climate change or safety. I am therefore fully confident that we will be able to satisfy our hunger for magnificent projects in the coming years.
Enjoy reading.
Maarten van de Waal CEO
The history of 75 years of Iv
Henk Veth sets up Ingenieurs- en Architectenbureau H. Veth in his attic room in Rotterdam. From the outset, Koninklijke Hoogovens was Henk Veth’s most important client. The oxygen steel plant at the IJmuiden site, for example, was designed by Iv.
Ingenieurs- en Architectbureau H. Veth is now 20 years old. The anniversary is celebrated in grand style. The company has grown steadily, from a few employees in the early days to around twenty in the 1970s.
Koninklijke Hoogovens is still its biggest client.
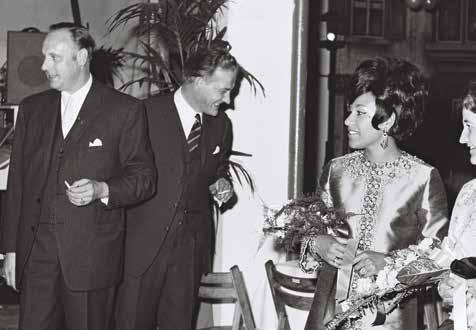
Henk Veth transfers his company to Henk de Kok, who becomes the new CEO and owner. The company name Ingenieurs- en Architectenbureau H. Veth also comes to an end. From then on, the engineering company – now located in Dordrecht – continues as Ingenieursbureau H. Veth BV.
Iv acquires Grootint’s drawing department. The bridge and lock constructor disposed of its drawing department and transferred much of the drawing work to Iv. This represented Iv’s first real growth spurt, resulting in large projects, including the lock gates in IJmuiden. These gates were the predecessors of the current gates in the IJmuiden sea lock, the largest sea lock in the world.
A new Iv tradition begins. A group of Iv employees attend the UEFA European Championship in Germany, where the Dutch national team is crowned European champion for the first time - and for the last time so far. Dozens of Iv employees witness the triumph live.
Rob van de Waal takes over from Henk de Kok, who continues as a member of Iv’s Supervisory Board but transfers ownership and the day-to-day management to Rob. Rob aims to transform Iv into a multidisciplinary engineering company with a broader market focus.
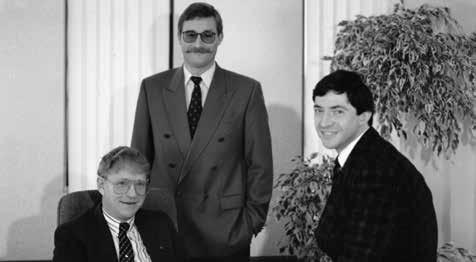
Iv’s first division becomes a reality: Iv-Infra is founded. Not strictly out of the blue, as for the previous eight years, Iv had been part of the Stercon consortium, which, among others, included Wagemaker, BMTR, BVN and Intersec. Iv wins a lucrative framework contract to provide all engineering services for the construction services of the Directorate-General for Public Works and Water Management (Rijkswaterstaat). During these years, Iv built up its knowledge and expertise in the infrastructure sector.
The last year of the millennium was special for Iv, with many highlights. Wim Bal joined Iv as managing director of the new Iv-Oil & Gas division, which focused on the offshore market. The brand-new division immediately won a major project for Petroland. At the same time, the opening of an iconic structure in London took place: the London Eye, the giant Ferris wheel on the Thames reaches a height of 130 metres and weighs 1700 tonnes. Iv-Consult prepared the structural design.
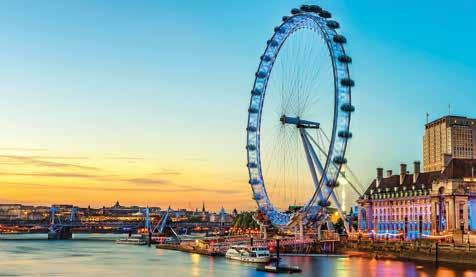
1994
1998
1999
2003 2004 2007 2008 2009
After the turn of the millennium, there are still many realms to conquer. Rob van de Waal, therefore, established Iv-Water. Erik Vegt became managing director of the new division. 2003 is the year that Iv adopted a divisional structure.
The Nederlandsche Vereenigde Scheepsbouw Bureaux, better known as Nevesbu, makes a return and is acquired by Iv in a deal in which Damen also takes a 50 percent stake. Nevesbu, based in Alblasserdam, is the leading maritime engineering company in the Netherlands, undertaking major projects nationally and internationally. The design of the Walrus class submarine for the Ministry of Defence is perhaps the most well-known project.
From this year onwards, Iv completes additional acquisitions at a rapid pace. Starting with Escher Process Modules. Founded in 1925, Escher specialises in process engineering. In recent years, Escher has focused on the design of Crystallisers and recently completed an impressive project in China.
Cumae, with branches in Arnhem and Capelle aan den IJssel, and Triple M from Haarlem are acquired. Together, these two companies form the new division Iv-Industrie. Iv also significantly expands in terms of branches, with Arnhem and Haarlem as new locations. 2008 was also the year when Iv ventured on another trip to the UEFA European Championship in Switzerland and Austria.
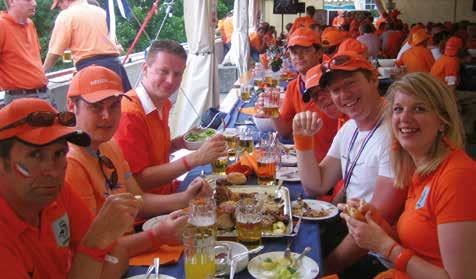
Iv-Industrie was formed from the acquisitions of Cumae and Triple M a year earlier. A small part of the company focuses on utility construction, another branch of activity. For this reason, Rob van de Waal – who marks his fifteenth anniversary as CEO and owner in 2009 – decided to create Iv-Bouw as a new division.
Those who were there can’t stop talking about it: the nine-day trip to South Africa, where the Dutch team qualified for the final of the FIFA World Cup. Oddly enough, football took a back seat on this memorable trip. Sleeping under the stars, a campfire among the elephants, and, of course, going on safari with hundreds of colleagues. The Iv trip to South Africa proved to be an unforgettable experience.
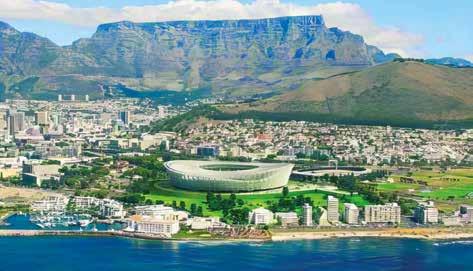
This year, for the first time, Iv proudly holds a position among the top 10 engineering companies in the Netherlands. Rob’s ambition became a reality. Since then, Iv has remained in the top 10. 2012 is also the year another memorable football trip took place: Iv travelled to Ukraine to support the Dutch national team.
This is the project that has undoubtedly given Iv an enormous boost in terms of reputation and brand awareness. The national media were eager to know all the details: one of the most important lock complexes in the world has a Dutch contribution. Iv has been designing the locks of the Panama Canal since 2009. In 2016, the brand new lock complex of the Panama Canal is opened.
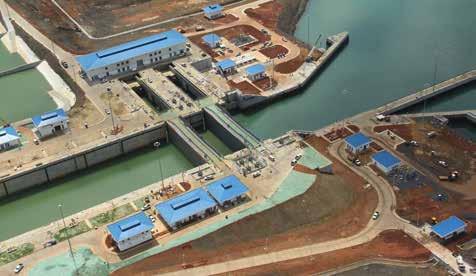
2017 2019
Dutch ingenuity for Iv-Offshore & Energy (established as Iv-Oil & Gas), designer of the Borssele Alpha and Beta offshore wind platforms. Impressive because together, these platforms account for around 1.4 gigawatts of green energy destined for Dutch soil. Enough to supply almost one and a half million households with electricity every year.
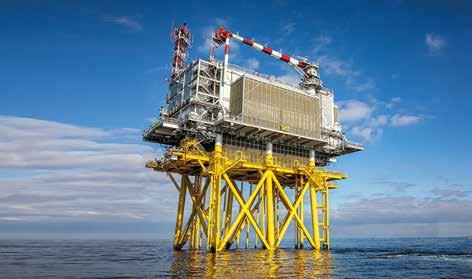
2018
This year, Iv took over the engineering company of Dura Vermeer: Advin. The acquisition brought Iv some 55 new colleagues. This also led to the establishment of a new branch in Den Bosch. Advin also had a branch in Hoofddorp. These colleagues, together with the colleagues from Iv-Infra Amsterdam, moved to Haarlem, where Iv-Industrie and Iv-Infra are now located. 2018 was also the year of the World Cup in Russia. Even though the Dutch team did not participate in the tournament, a large group of Iv colleagues travelled to the beautiful St. Petersburg for an unforgettable football trip.
A new takeover: Iv acquires CAE in Delft. CAE joins Iv-Bouw and retains its branch in Delft. The merger means an increase in the number of employees, but also in the diversity of clients, such as loyal client Rotterdam Zoo (Diergaarde Blijdorp). From 2022, both companies will trade under one name: Iv-Bouw.
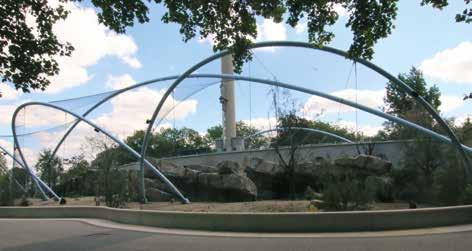
Changing of the Guard: Maarten van de Waal becomes the new CEO of Iv. Rob will remain with the company for the time being but more in the background. In addition to Maarten, the new management consists of CFO Ewout Borg and COOs Fedor van Veen and Wouter van der Wiel. 2022 is also the year Iv ‘breaks’ its football tradition and instead opts for a trip to Monza, Italy, to cheer on Max Verstappen.
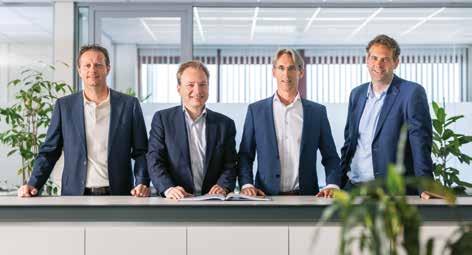
A huge milestone in the energy transition. After Borssele, but also exciting projects such as Thor, Ostwind/Gennaker and Sofia, a groundbreaking project commences in our part of the North Sea: designing the world’s first 2GW platforms for TenneT. Such powerful platforms have never been built before. In the same year, Iv acquires the Polish company Electro Croon Polska (ECP) with more than fifty employees. Iv thus expands with three new branches in Poland and, above all, a lot of knowledge and expertise.
Iv is 75 years old! A milestone of which we are incredibly proud and on which we reflect at length. After exactly 30 years, Rob van de Waal stepped down as CEO of the company he joined in 1979 in Henk Veth’s computer room. 2024 is also the year when all the divisions will be known externally under a single name: Iv!
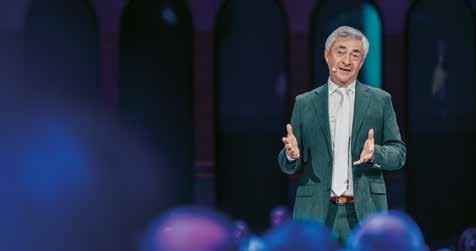
Unsubscribe
Would you prefer to receive Ivormatie digitally? Or do you want to unsubscribe? Let us know via marketing@iv.nl.
Copyright © 2024 Iv. ll rights reserved. Reproduction in whole or in part requires written permission.
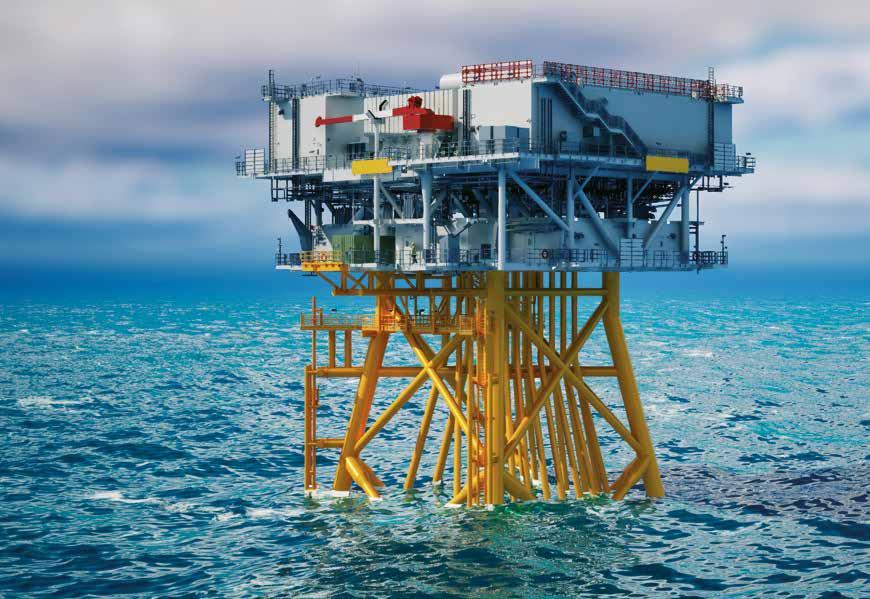
More than a quarter of EU offshore wind substations are Dutchdesigned
The energy transition is gaining momentum. Particularly at sea (offshore), the number and speed at which wind farms and platforms are being built are increasing significantly. The design of these transformer platforms, which enable wind energy to be brought to shore, is a complex task. According to a report by WindEurope, Iv is responsible for the design of more than a quarter of the platforms currently installed in the European Union to connect offshore wind energy. And many more are under development.
In 2023, around 19 gigawatts (GW) of offshore wind energy was produced at sea in Europe, enough to power almost 20 million homes annually. On land, the share of green energy is much higher at 201 GW. However, offshore wind energy is gaining ground, and in the coming decades, the ambition of the European Union and the Netherlands will only increase.
Iv is responsible for over a quarter, around 5 GW, of the 19 GW of installed offshore wind capacity. Examples include the Borssele Alpha and Beta platforms (1.4 GW), Dolwin Alpha (800 MW) and Helwin Beta (680 MW). Iv is the only engineering company in the Netherlands with this level of experience and expertise. The Netherlands is aiming for no less than 70 GW of offshore wind power by 2050. By the end of 2023, this figure reached 4.7 GW and will rise to 21 GW by 2030.
The ambitions of Europe, the Netherlands and Iv are huge, and increasingly, more is being achieved.
Largest platforms in the world
Much remains to be done to achieve this goal, but the steps currently being taken are great. For example, Iv is presently designing two platforms for TenneT in the North Sea: IJmuiden Ver Beta and IJmuiden Ver Gamma. These are currently the largest converter platforms in the world, with a capacity of 2 GW each. In addition to the platforms in the IJmuiden Ver area, Iv will also design one of the Nederwiek platforms.
Furthermore, Iv is working on three platforms in the German Baltic Sea (Ostwind 3 and Gennaker East and West) and Thor in Denmark. But outside the European
Union, Iv is also active. For example, Iv designed the Sofia platform, which was installed this year on the Dogger Bank off the coast of the United Kingdom. These platforms account for more than 2 GW of offshore wind energy.
In 2023, the Netherlands was leading with more than 1.9 GW of installed offshore capacity.
Record year
The ambitions of Europe, the Netherlands and Iv are huge, and increasingly, more is being achieved. In 2023, the Netherlands was leading with more than 1.9 GW of installed offshore capacity, more than Germany, France, the UK and Denmark combined.
A unique project is underway outside Dutch waters: a world premiere is being created about forty kilometres off the coast of Ostend, Belgium. Iv, HSM, and Smulders are working on the design, construction and installation of the Princess Elisabeth Island for the Belgian grid operator Elia. This will be the world’s first energy island. Iv is designing four AC (alternating current) modules with a total capacity of no less than 3.4 gigawatts. Something that has never been done before.
Princess Elisabeth Island - the name says it all - is unlike anything else that has been built in the past or is being built today. It is not a platform with a jacket but an island, and it is already under construction in Vlissingen, Zeeland. The outer perimeter of the island consists of a series of concrete structures (caissons) placed in a ring on the seabed. The inner area of the concrete ring will be filled with sand to form the island.
WindEurope and the numbers
WindEurope is the voice of the wind industry, active in promoting wind energy in Europe and worldwide. It has over 500 members with offices in 35 countries. Members include leading wind turbine manufacturers, suppliers, research institutes, national organisations, developers, contractors, electricity suppliers, financial institutions, insurance companies and consultants. This makes WindEurope the largest wind energy network in Europe.
Europe aims to install no less than 260 gigawatts of new wind power between 2024 and 2030, both onshore and offshore.
The WindEurope report provides a comprehensive analysis of the wind energy installations realised onshore and offshore in 2023. It provides insight into the forecasts and ambitions for wind energy in Europe and the European Union. There is, however, one marginal comment in the report. Although much of the data shows growth, including in the Netherlands, there are doubts about whether the targets will be met within the European Union. Still, the organisation believes that the future looks more favourable than 2022, partly due to some peaks in the development of onshore and offshore wind energy, with the Netherlands being one of the European leaders in the offshore energy transition.
1.906 MW
According to the WindEurope report, the Netherlands was among the European leaders in installed wind energy in 2023. A total of nearly 2.5 GW (enough to power more than 2 million households annually) of wind energy was
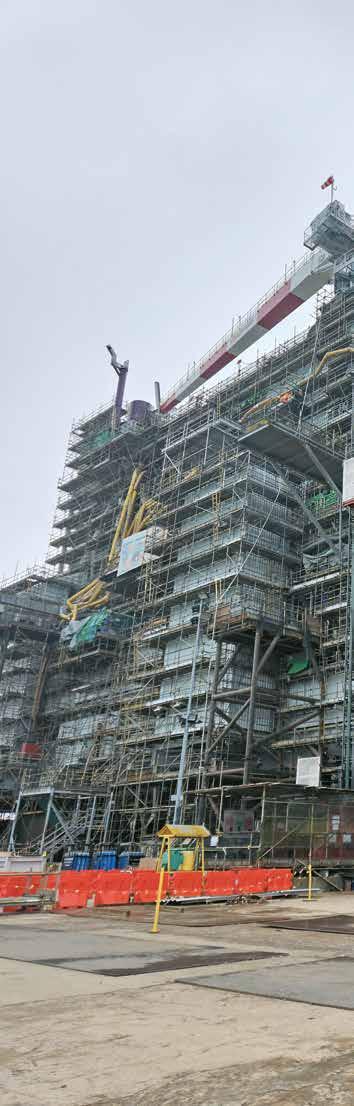
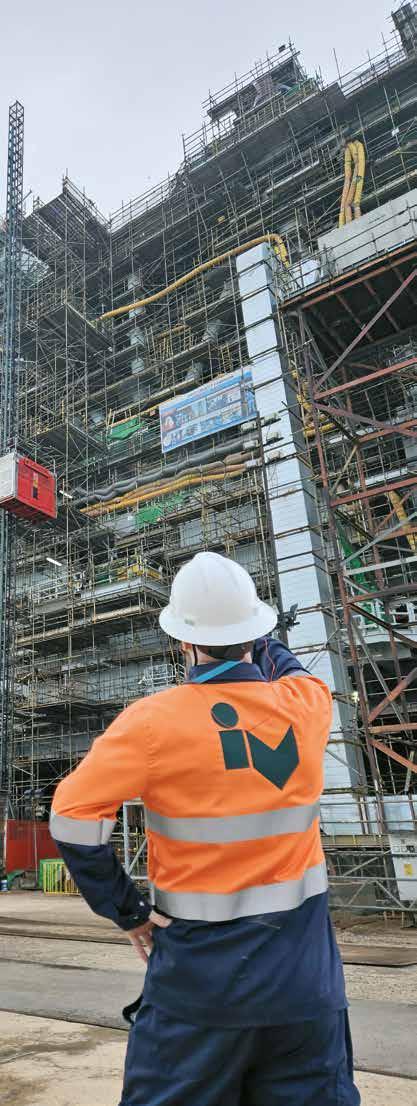
added last year. The vast majority - 1,906 megawatts - was installed offshore. The Netherlands is thus moving against the trend, as almost eighty percent of all European installed capacity is built on land. No country in Europe achieved more offshore wind energy in 2023 than the Netherlands.
19% wind energy
Wind energy provides around 19% of the total energy demand in the European Union, an increase compared to previous years. Denmark (56%), Ireland (36%) and Germany (31%) are leading in this field. The Netherlands ranks 4th in the EU, with 27% of its energy needs met by wind power.
2030
The year 2030 is an important one. Europe aims to install no less than 260 gigawatts of new wind power between 2024 and 2030, both onshore and offshore. WindEurope expects the European Union (Europe minus some nonEU countries) to account for 200 GW. This equates to an installation rate of around 29 GW per year.
Netherlands offshore
With the largest transformer platforms of their kindTenneT’s 2GW platforms - off the Dutch coast, it is no surprise that the Netherlands is set to produce the most offshore wind energy in the European Union. The national government is auctioning 4.6 gigawatts of wind capacity for the IJmuiden Ver Alpha and Beta wind farms. This, together with a further 11 gigawatts of planned capacity, will bring the Netherlands very close to its target of 15.8 GW of offshore capacity by 2030. ●
Iv-designed offshore wind substations worldwide
UNITED STATES CANADA
EMPIRE WIND
800 + 1,200 MW
VINEYARD WIND
800 MW
SEAGREEN 1,500 MW
BERWICK BANK 1,150 MW

NEART NA GAOITHE 2 X 225 MW

SOFIA 1,320 MW
SOUTH COAST 1,300 MW
MARWIN 420 MW
ATLANTIC OCEAN
IRELAND
UNITED KINGDOM

IJMUIDEN VER BÉTA 2,000 MW




POSHYDON 1,250 MW
NSE HYDROGEN 500 MW
GREATER GABBARD 2 X 252 MW
PRINCESS ELISABETH ISLAND 3,400 MW


HORNS REV B
MW
NORTH SEA




DENMARK
HORNS REV A 160 MW
BORKUM RIFFGRUND 2 450 MW
BORWIN ALPHA

OSTWIND 3 300 MW

MW
MW HELWIN BETA
IJMUIDEN VER GAMMA 2,000 MW

DOLWIN ALPHA
MW
NETHERLANDS


BORSSELE ALPHA + BETA
2 X 700 MW
THORNTON BANK
325 MW
BELGIUM

GERMANY
GENNAKER EAST + WEST 460 MW
HVAC
• THOR
• GENNAKER EAST + WEST
• OSTWIND 3
• NEART NA GAOITHE
• PRINCESS ELISABETH ISLAND
• BORSSELE ALPHA + BETA
• BORKUM RIFFGRUND 2
• GREATER GABBARD
• THORNTON BANK
• HORNS REV A
• HORNS REV B
HVAC STUDY
• BERWICK BANK
• EMPIRE WIND
• MARWIN
• SEAGREEN
• VINEYARD WIND
HVDC
• SOFIA
• DOLWIN ALPHA
• HELWIN BETA
• BORWIN ALPHA
• IJMUIDEN VER BÉTA
• IJMUIDEN VER GAMMA
HVDC STUDY
• IJMUIDEN VER
• SOUTH COAST
HYDROGEN
• POSHYDON (PILOT)
• NSE HYDROGEN (PILOT)
The quest for a new drinking water source
Drinking water company Dunea is faced with a major challenge. The company supplies clean drinking water from the dunes between Monster and Katwijk to 1.3 million consumers in the west and south of the Zuid-Holland province, but this is no longer sufficient due to growing demand. More drinking water needs to be produced, and since this is not possible with existing methods or locations, Iv and Arcadis have been brought in to - for the first time in over fifty years - find a new source to provide clean drinking water from 2030.
Dunea uses the river-dune system to extract drinking water. Drinking water is produced by pumping water from the Lek and Afgedamde Maas rivers to the dunes for processing. This method has been sufficient for years, but Dunea is now reaching its capacity limit.
Will the source be fresh surface water, river water, brackish groundwater or seawater?
For this reason, the water company has launched the Drinking Water for the Future programme. This plan consists of 5 pillars, which include promoting conscious and sustainable water use and optimal use and maintenance of the current river-dune system. A crucial pillar is to add a new system of sources and treatments. That’s where Iv and Arcadis come in. Our task is to develop three options for Dunea, provide advice and offer a preliminary design. Iv is concentrating on the technical aspects of the design, while Arcadis carries out the Environmental Impact Assessment (EIA) and manages the permitting process.
The core of the quest
Willemijn Bouland-Oosterwijk is the Drinking Water for the Future programme manager at Dunea. “We’re now trying to utilise and maintain the river-dune system further, but still, we will not have sufficient capacity by 2030, which is why we are trying to find new additional sources: local surface water, river water, seawater or brackish groundwater. This is what lies at the very core of this quest.”
For Dunea, the task is both extensive and challenging. While the company currently provides clean drinking water to 1.3 million consumers, it will soon need to increase its supply to serve 1.6 million consumers. This rise in supply represents an increase of 15 billion litres of drinking water, from 85 to 100 billion litres annually. “Together with Iv and Arcadis, we’re examining sources and treatment technologies with a high level of abstraction, and we aim to select a preferred alternative this year. There are many environmental factors at play”, says Willemijn. “Because the water is not ours, nor is the space. Each alternative involves different parties and stakeholders.”
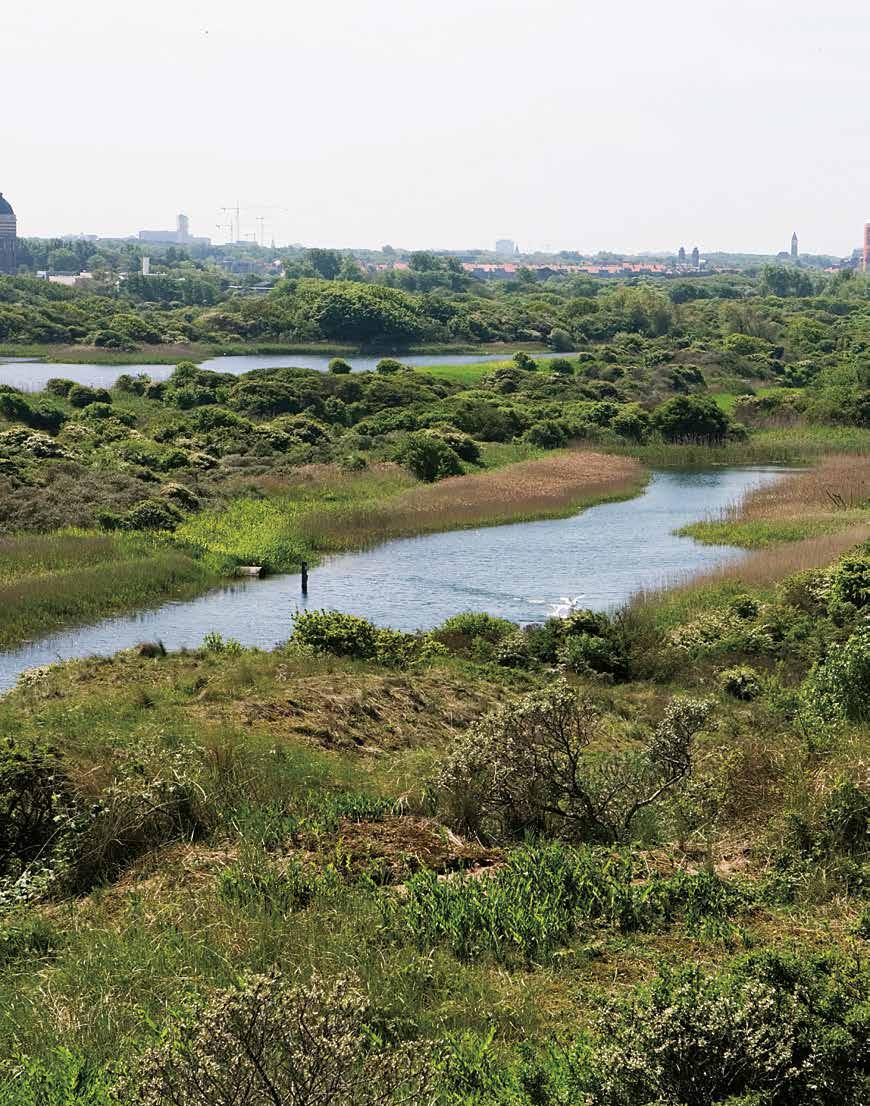
This rise in supply represents an increase of 15 billion litres of drinking water annually.
This is a unique project for Dunea, as no new water sources have been explored in the last fifty years, indicating the importance and urgency of this quest. Whoever reads the newspapers and watches the news will inevitably be confronted with gloomy reports of impending water shortages and urgent calls to conserve drinking water. Clean water from the tap is no longer a given.
We are helping Dunea to make the right choice.
Knowledge, capacity and strength
“We feel a tremendous sense of urgency and responsibility”, Willemijn continues. “We are adding this to our agenda to create more awareness, which has been somewhat lacking in recent years. There is a lot of work
to be done, and we need the help of other parties, such as Iv and Arcadis. In terms of knowledge, capacity and strength. But also from governments and parties within communities to free up water and space.”
So why are we increasingly reading that there is a risk of drinking water shortages and that it is still questionable whether future new housing developments can be connected to the drinking water network? Population growth, and therefore more housing, is the main reason for the increasing demand. “But we are also observing a halt in the downward trend in water consumption per person. In recent decades, we have unknowingly saved water by using more efficient appliances (washing machines, dishwashers, ed.). The focus is now on saving energy rather than water. This combination of factors indicates a sharp rise in demand.”
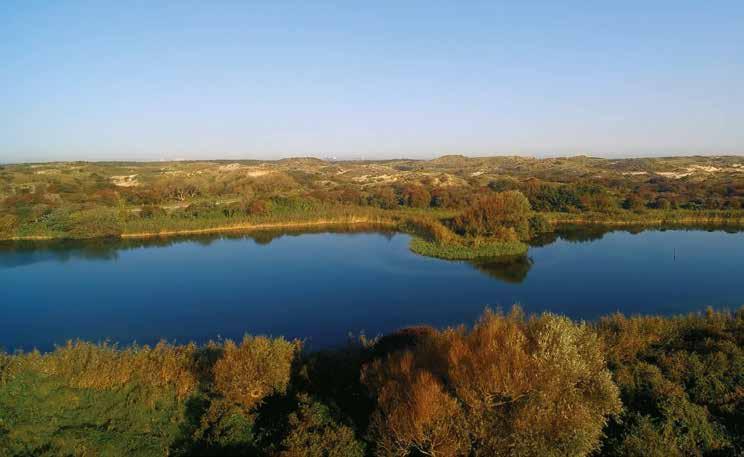
The constant search for overlapping aspects
This quest by the three parties is, therefore, crucial and concrete: to determine and select a new source. Will it be fresh surface water, river water, brackish groundwater or seawater? This question will be answered by the end of the year. Willemijn realises it is not as clear-cut as it seems. “It’s quite complicated to balance what is technically possible and what is actually possible in terms of permits and desirable for the surrounding environment. It’s a big puzzle, and we are constantly searching for overlapping aspects. So, mistakes are also made in this.”
The whole (political) context in which this is taking place, with time being of the essence, makes it very dynamic.
Dunea feels this project is special despite the difficulties and pressure. “We’re doing something together that is very socially relevant, so all eyes are on us. After all, it is not just about our region. We are especially focused on how we can help each other as drinking water companies, so others are curious about what is happening here. And if we succeed? Then we will certainly solve the drinking water problem between now and 2040.”
Relying on each other’s knowledge
Projects like this do not come along very often, not only because the search for a new source of drinking water is unique but also because of the nature of the collaboration. “We work as a single unit”, says Guido van der Wedden, project manager at Iv. “We meet twice a week at Dunea, which keeps the lines of communication short. And that is very useful when – as is now the case –we rely greatly on each other’s knowledge.”
If Guido had to describe the project, he would say it was about designing a ‘new’ drinking water company. But under the Dunea flag. “But what we are doing is coming up with something completely new, so we really have to use our brains. There is plenty of intellectual challenge.” Specifically, the project for Iv involves creating three process technology designs, one for each variant. Guido: “This means we have to consider the connections and integration of existing systems carefully. Once the choice has been made, we will start working on a preliminary design of the chosen variant this autumn. What’s interesting and unique about this project is that we are already involved with Arcadis in the preliminary phase. We are helping Dunea to make the right choice. And that involves many considerations related to technology, costs, risks, but also the overlapping aspects between the environment and the stakeholders.”
That’s where Arcadis comes in. As an environmental consultant, Frans Dotinga is responsible for the EIA. “We and Iv wanted to do this job because it concerns a very interesting, strategic issue. The whole (political) context in which this is taking place, with time being of the essence, makes it very dynamic.”
The purpose of an Environmental Impact Assessment is to show how the alternatives perform environmentally and the impacts of each. How will nature be affected if groundwater is extracted from a particular area? How much CO2 emissions and energy do specific processes produce and use, and how well do the processes comply with stricter water quality regulations?
“But we are also examining the target range”, Frans continues. “In other words, are we achieving the necessary volume of drinking water, and what about the security of supply when applying the different systems? In short, the longer the pipes, the higher the risk, because the risk of damage automatically increases. The more steps in the process, the more complex it becomes. We also have to take these aspects into account.”
It has a direct impact on people
Arcadis is currently working on the first part of the EIA. The second part will follow once the preferred alternative has been selected. “We are doing this together, not in parallel”, says Frans. “Iv is helping to write chapters in the EIA, and we provide support in some of the technical issues. The cooperation is superb. We are responsible for different things on paper, but there is a lot of overlap in practice. We are working together on a wonderful assignment. It has a direct impact on people. This is the kind of work we enjoy the most.”
Dunea also views exploring a new source as a unique and impactful challenge. Willemijn: “The investments we make now will help us in the future. Doing something new takes time. But if we succeed, our troubles will be over.” ●
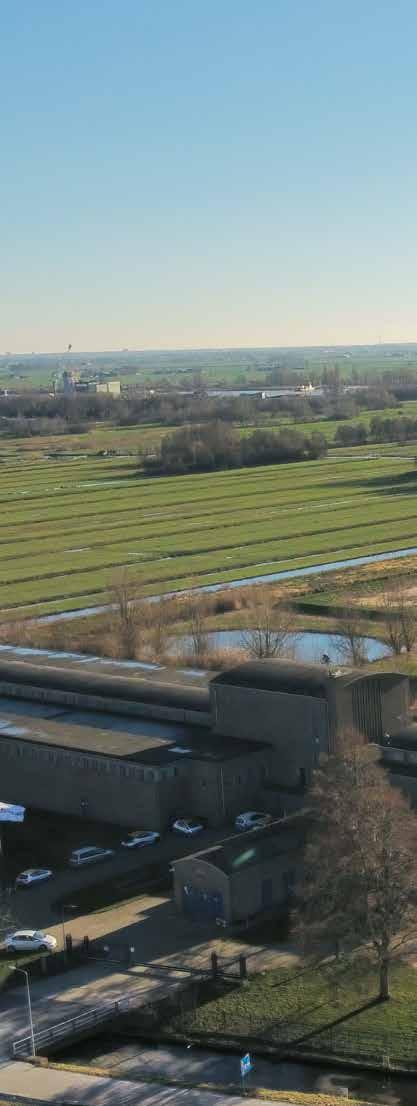
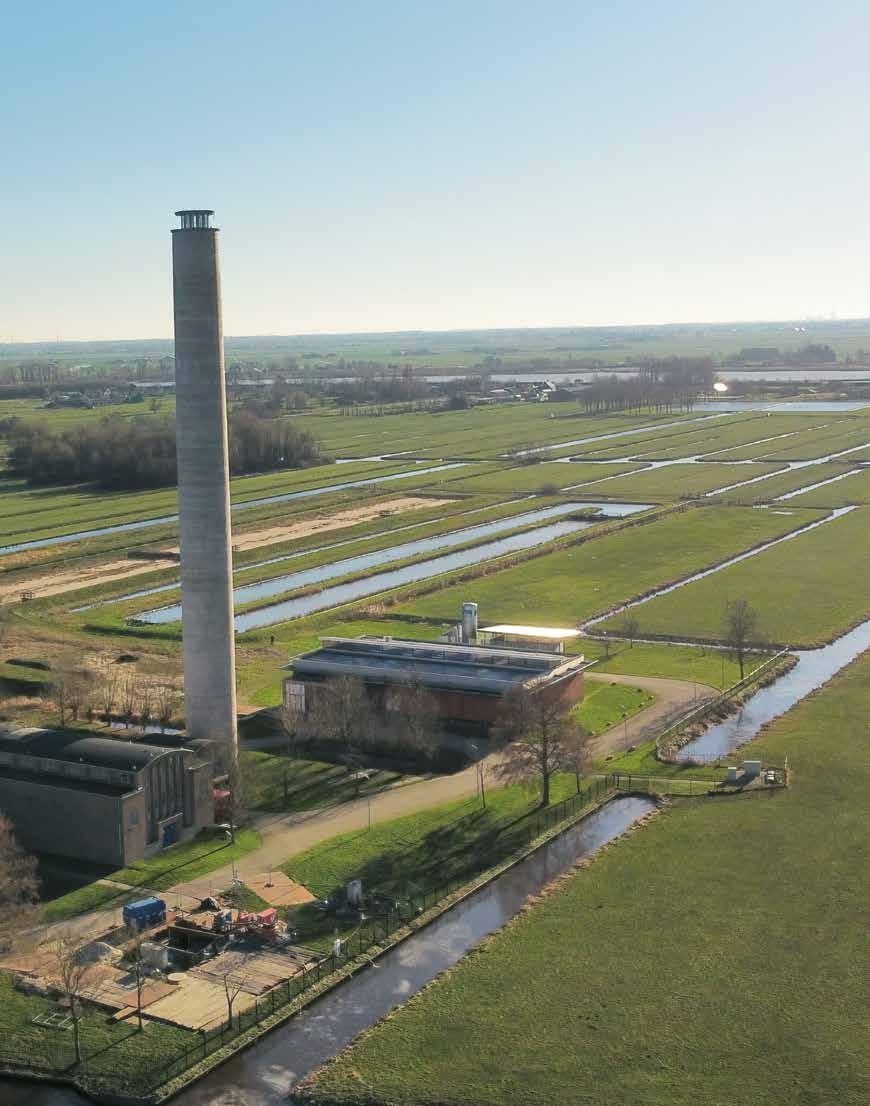
The longer the pipes, the higher the risk.
Eindhoven Airport expands terminal for optimal passenger experience
Eindhoven Airport will start construction of the terminal expansion at the end of this year. The current terminal is too small for the number of passengers. The expansion will provide the terminal with more gates, and the non-Schengen area will be extended. A new baggage hall with an underground baggage basement will be created, and more space will be made for catering and dining facilities. In short, more passenger comfort. EGM architecten, Peutz and Iv prepared the design. Construction company Heijmans will realise the expansion. Iv played a vital role in the final design of this project, focussing on sustainable solutions. The expansion is expected to be completed in 2027.
Sustainability is key
The expansion will add approximately 10,000 square metres to the current airside (beyond the security checkpoint) terminal. On the landside (before the security checkpoint), the terminal will be extended by 2,000 square metres. The distinctive new entrance will also be located here. The entrance will have a forward-sloping glass façade and an overhanging roof, with the front row of columns outside the building tilting forward. The roof structure is made up of triangles that are visible from below. These architectural elements give the entrance a dynamic and welcoming feel and contribute to the modern and transparent appearance of the terminal.
Sustainability is key to this expansion, emphasises Jeroen Stam, senior project manager at Eindhoven Airport.
“Eindhoven Airport is taking responsibility and focusing on significantly reducing CO2 and other greenhouse gas emissions from aviation and its buildings and activities.
This means building smart and circular, reusing materials and replacing gas with sustainable energy sources. By incorporating the latest sustainability applications into the design, the terminal expansion will contribute to our goal of becoming a zero-emissions, zero-waste airport by 2030.”
Rainwater will be used for flushing toilets in the extended part of the terminal.
The design
Iv was responsible for the technical installation and structural design of this project. In addition to the design of the new part of the terminal, this included adaptations to part of the existing building. Two heat and cold storage (ATES) units will be used to heat and cool the building. In addition, displacement ventilation will be used to regulate airflow and optimise ventilation
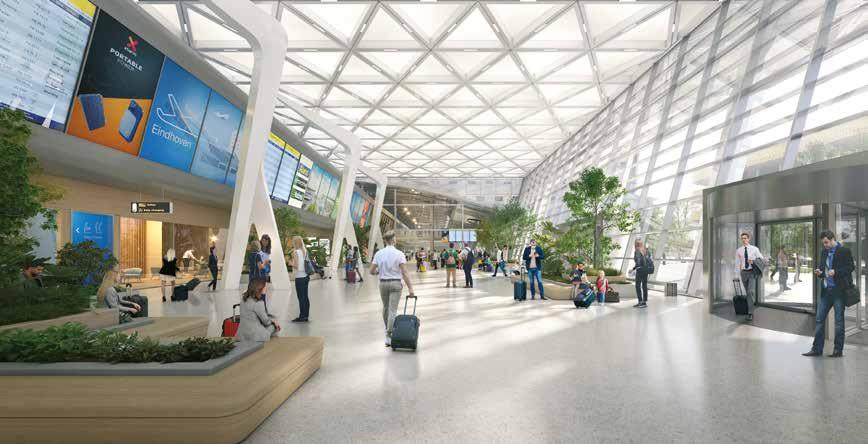
in the various areas. Almost 1,100 solar panels will be installed on the terminal’s roof, generating approximately 363,500 kilowatt hours of energy annually. Part of the roof will be covered with sedum plants to help retain water and insulate the terminal building. A water basin in the basement will be used to collect rainwater for flushing toilets in the extended part of the terminal.
An occupancy survey was carried out to understand exactly how the space was being used. In addition, a detailed analysis collected data on the number of passengers, their movement patterns and length of stay. This information was used to develop a thorough understanding of the occupancy of different airport areas. For example, it was possible to identify how many passengers were in the baggage hall at any given time, how long they waited on average for their luggage and how much time they spent in the terminal. As a result, it was possible to determine precisely how much
ventilation is needed in each area at any given time. This approach allowed the airport’s air conditioning system to be designed more efficiently, resulting in significant cost savings and energy efficiency.
The 12-metre height also presents challenges for the air conditioning system.
The structural design included the planning and development of the load-bearing structure of the building, such as the foundation, basement, columns, stability walls and the beam structure supporting the roof of the building. Iv also reviewed the connections to the existing structure and the stability of the structure as a whole was considered in accordance with the applicable standards. Materials such as steel and timber have been used to create structures that can be easily dismantled and reused at the end of the building’s life.
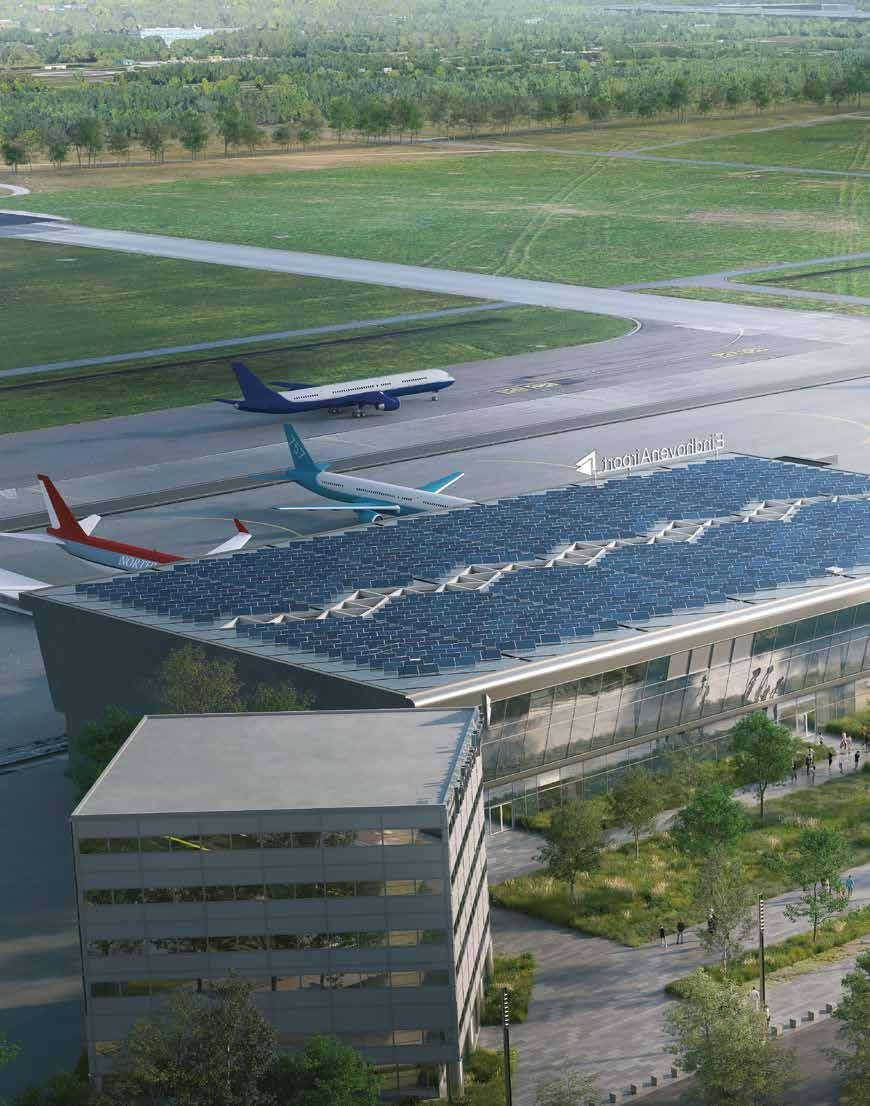
Our goal is to be a zeroemissions, zero-waste airport by 2030.
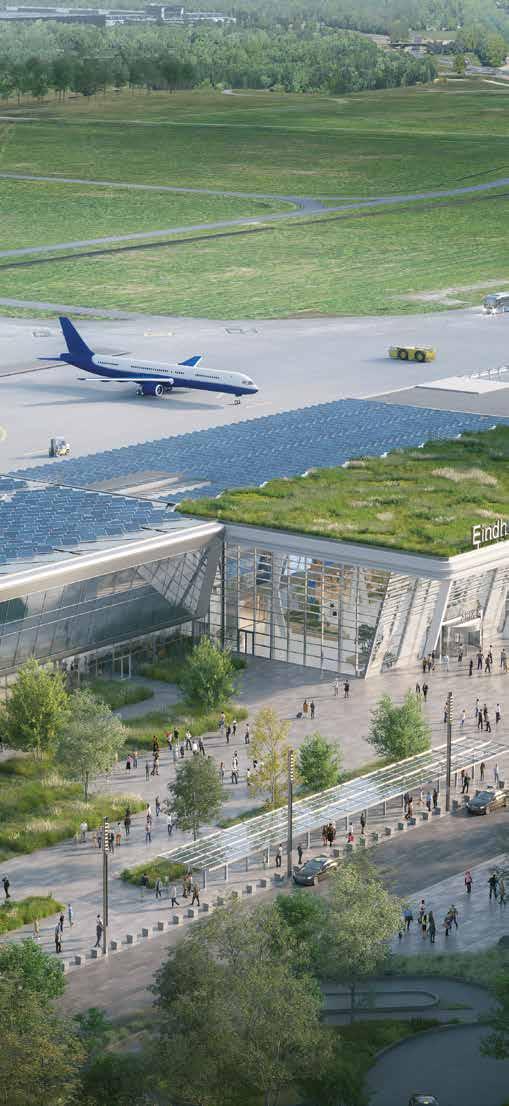
Aesthetic and sustainable ventilation
With a height of approximately 12 metres, the entrance hall and terminal building create a spacious effect. However, this height also presents challenges for the air conditioning system. The entrance hall consists of a metal roof structure with a triangular pattern in which the lighting is integrated, which limits the possibility of installing equipment on the ceiling. Also, the installation of ventilation systems on the ceiling is undesirable from an aesthetic point of view.
Rather than traditional mixed ventilation, whereby air is blown into the area from the ceiling, Iv has developed an installation concept based on displacement ventilation at floor level. This provides a controlled airflow, introducing cool air at lower levels while warm air is driven upwards and expelled.
Despite the airport expansion being an enormous challenge, Eindhoven Airport is making sure that travellers barely notice the work.
“What I like about the ventilation concept is that we added something that was not directly requested but was indirectly needed. We have really shaped the client’s request”, says Dennis van der Beijl, project leader at Iv. Dennis was inspired to use displacement ventilation during a stopover at Istanbul Airport. After conducting some research, he concluded that this technology would also be a suitable option for the expansion of Eindhoven Airport. Displacement ventilation places less stress on the roof structure, and less air is needed to condition an area, resulting in smaller, more efficient air conditioning systems and lower energy consumption.
Challenges require creative solutions
In addition to displacement ventilation, the Eindhoven Airport expansion design presented several complex challenges. In particular, the complexity of the structural design around the entrance hall required creative solutions to make it work. The unique shape, a sloping design with glass façades and large spans between the columns made it complex because of the traction forces and the connection between the existing and new parts of the building complex. In addition, there were challenges associated with the timber roof and the triangular structure, as timber behaves differently from steel. Iv used cross-laminated timber (CLT) girders to
achieve more uniform material properties for the girders. False girders were used for the non-load-bearing sections to achieve weight savings and a uniform aesthetic appearance.
Despite the airport expansion being an enormous challenge, Eindhoven Airport is making sure that travellers barely notice the work. Jeroen: “Continuity of operations is essential for Eindhoven Airport. The project has been designed with this in mind, allowing the airport to continue operating during the expansion. We have organised the construction entirely on the landside, strictly separated from the passenger handling areas. This
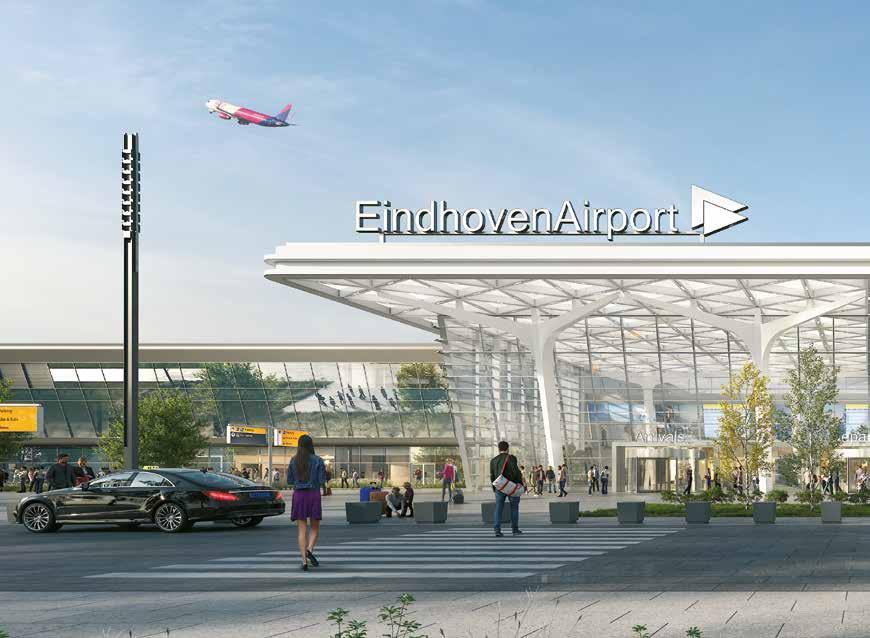
is a challenge because of the limited space and having to work very precisely. It’s like building on a postage stamp; everything has to be carefully planned and executed to ensure that passengers experience as little inconvenience as possible.”
Engineering that excites
The implementation activities of the terminal expansion will begin at the end of this year. Looking back on the project, Dennis recalls it as a memorable experience. “It was the first project I worked on at Iv. Working on a project involving an airport environment brought a completely different dynamic than working on an office
building. The constant activity of planes and military aircraft added an extra dimension to the work. Designing from a logistics perspective was an interesting challenge.” He also highlights the excellent working relationship with EGM architecten. “In the end, it’s about people working together. Although there will always be challenges, a good click between the people involved makes obstacles easier to overcome. This experience has shown me how crucial good cooperation is for the success of a project, especially in a challenging environment such as an airport.” ●
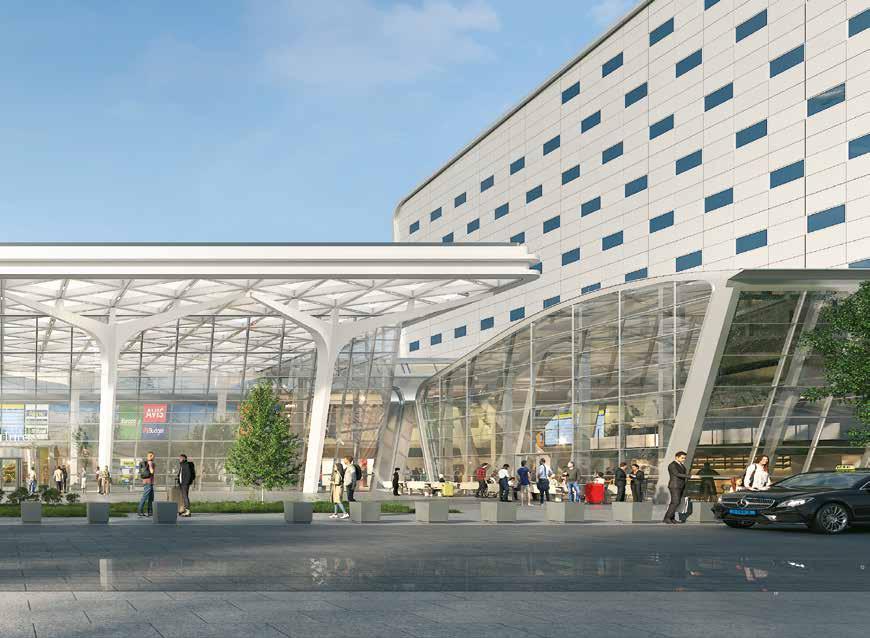
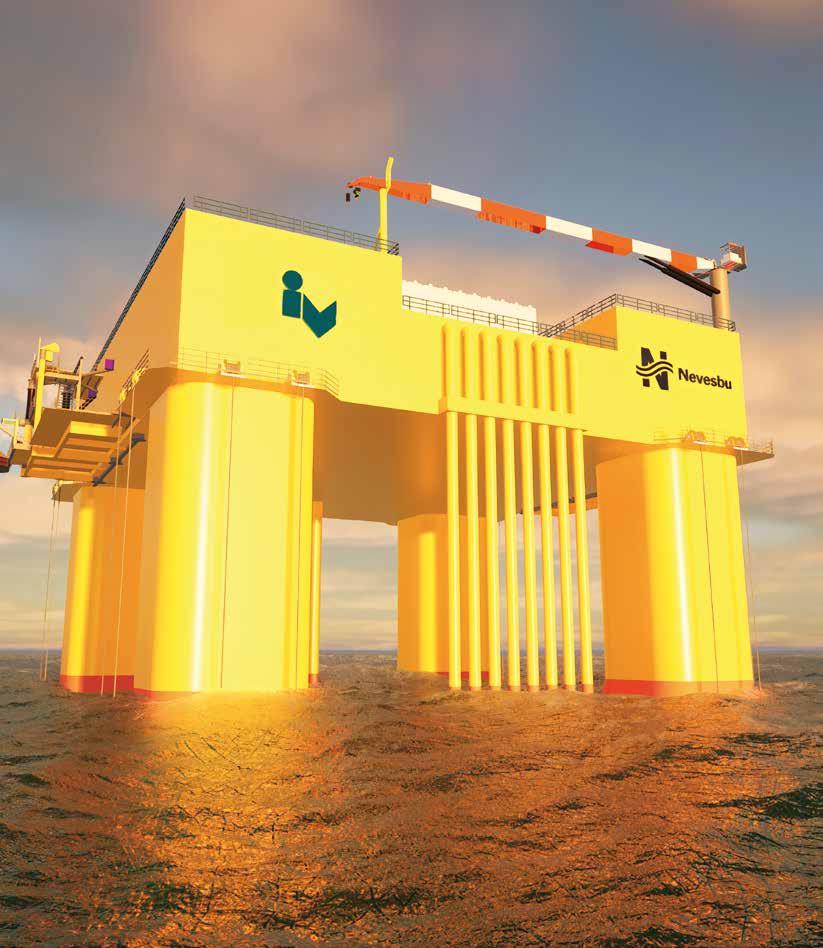
The next step in floating wind
The energy transition is a hot topic within the offshore industry nowadays, and for good reason. The effects of climate change are imminent, and it is necessary to invest in the development of large-scale offshore renewables. What the exact energy mix will look like in the future is difficult to predict, but it is clear that offshore renewable energy will grow tremendously in the coming years.
Floating wind potential
It is expected that 1,800 gigawatts (GW) of offshore wind energy will be generated by 2050, of which 250 GW will be produced by floating wind farms. This was stated in the DNV report Floating offshore wind: The next five years, published in 2022. Suitable regions to generate floating offshore wind energy can be found in California and Southeast Asia, but also in Europe, where the main focus is the Mediterranean Sea, North Sea, Bay of Biscay, Baltic Sea and the Aegean Sea. All of these areas have deep water and suitable wind conditions for generating sustainable energy.
With an expected floating wind energy capacity requirement of 250 GW in 2050, the market is presented with a significant challenge.
Offshore substations are required to efficiently transport 250 GW of renewable energy from sea to shore. These substations collect the wind energy (AC) from the wind farm, convert the electricity to high-voltage direct current (HVDC) or high-voltage alternating current (HVAC) and
transport it to shore through two or four export cables. In doing so, the power losses during transport from substation to shore are significantly reduced. These substations are already widely used in shallow waters, where the station is supported by a jacket or other bottom-founded solutions. Each substation is typically connected to 100 to 150 wind turbines, generating between 1.0 and 2.0 GW of power.
At water depths beyond 150 metres, the costs of the renowned ‘bottom-founded’ solutions increase exponentially, making floating solutions an interesting alternative. It is expected that in water depths of 300 metres or less, the substation will still be bottom founded, while the turbines already utilise a floating solution. In fields with water depths beyond 300 metres, a floating offshore substation (FOSS) will be necessary.
With an expected floating wind energy capacity requirement of 250 GW in 2050, the market is presented with a significant challenge. Assuming that the first fullscale floating substation will be commissioned in 2035, eight to ten substations of 2 GW will have to be built each year from 2035 to 2050 to reach this forecast.
Current market challenges
Currently, there are a significant number of floating concepts in development that support the floating wind turbine. Recently, companies have also started to investigate the technologies for floating offshore substations, but it is fair to say that there are no proven designs in the market.
The main challenge at the moment is that the dynamic conditions, as encountered by a FOSS, are uncharted territories for equipment and cable manufacturers (OEMs). Today’s high-voltage equipment has not been designed for continuous motions and accelerations, as will be experienced on a floating platform.
From a financial perspective, floating wind solutions are expected to be more expensive than bottomfounded solutions. This, of course, depends on a wide range of factors, such as design life, water depth, size of the wind farm and many other aspects. On the other hand, developing deep water sites would decrease the constraints on hub heights, shipping routes, and the social impact on offshore wind. Even though these aspects will reduce project expenses, it is difficult to express this in terms of reduced cost for the overall development. Ultimately, differences in material cost between bottom-founded and floating substations are more prominent and easier to express. One could argue that the cheapest option for a floating substation is to refurbish an existing tanker hull and transform it into a floating substation, as is being done for floating production, storage and offloading (FPSO) units. However, this solution is not considered feasible due to the expected allowable accelerations of the HV equipment, which the OEMs are still investigating.
Technical challenges
From a technical point of view, conceptual studies are challenging and complex, as there are still many unknowns regarding:
1. the standards to be used in the overall design of the floater
2. the allowable motion criteria of the HV equipment
3. the fatigue capacity of the cables between the platform and the wind turbines (inter-array cables) and the export cables
In recent years, Nevesbu and Iv have focused on exploring these three topics in more detail, the present status of which is discussed in the remainder of this article. Wind turbines can operate in conditions up to Beaufort 8, which means that the floating substation must be capable of operating in waves of 8 to 12 metres. This makes the second and third points even more challenging.
1. FOSS substation standards
In 2021, the Floating Offshore Substations (FOSS) Joint Industry Project (JIP), initiated by DNV, was launched. The main goal was to study gaps in the current standards required for floating offshore substations, proposals to bridge those gaps, and explore the current state of technology and design. In addition to developing this standard, a recommended practice is being prepared for the design and analysis of high-voltage export cables. Nevesbu and Iv were closely involved in this JIP, together with numerous companies from the industry. This JIP has brought more insight into the remaining challenges and technology gaps for floating offshore wind substations and the preferred standards for floating solutions. A kickoff meeting was held in June to launch phase II of the project.
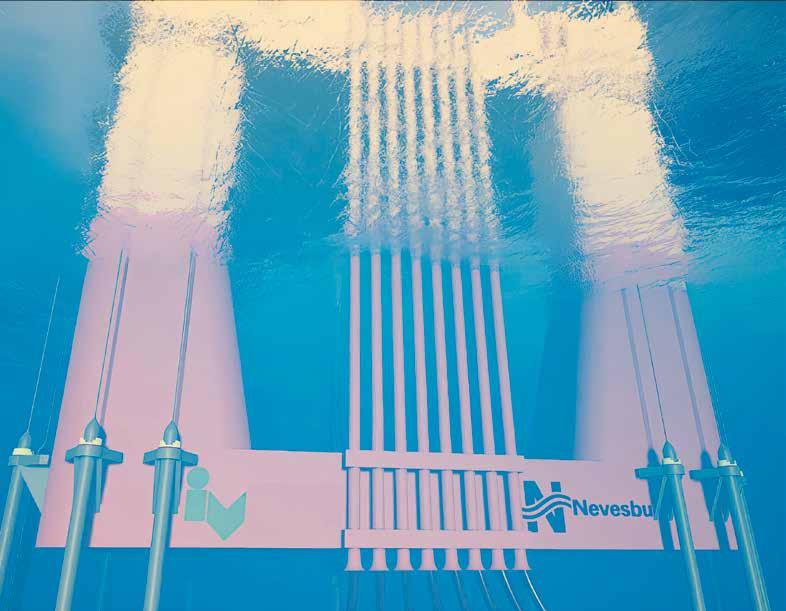
2. Concept development
Nevesbu and Iv have investigated and compared several floating substation concepts in recent years. Various floater types were investigated, such as SPARs, buoys, semi-submersibles and tension leg platforms.
Each concept must adhere to the established requirements for offshore wind energy, avoiding excessive steel weight and maintaining simplicity in terms of fabrication. Furthermore, it is essential to ensure
safety and reliability while guaranteeing high availability and a platform lifespan of no less than 30 to 40 years. In addition, the social costs of supplying sustainable electricity must remain affordable, and the solution should not be too expensive.
Based on these principles and requirements, a selection was made for the most promising floater type. Currently, the main focus is on developing a substation concept based on proven Tension Leg Platform (TLP) technology.
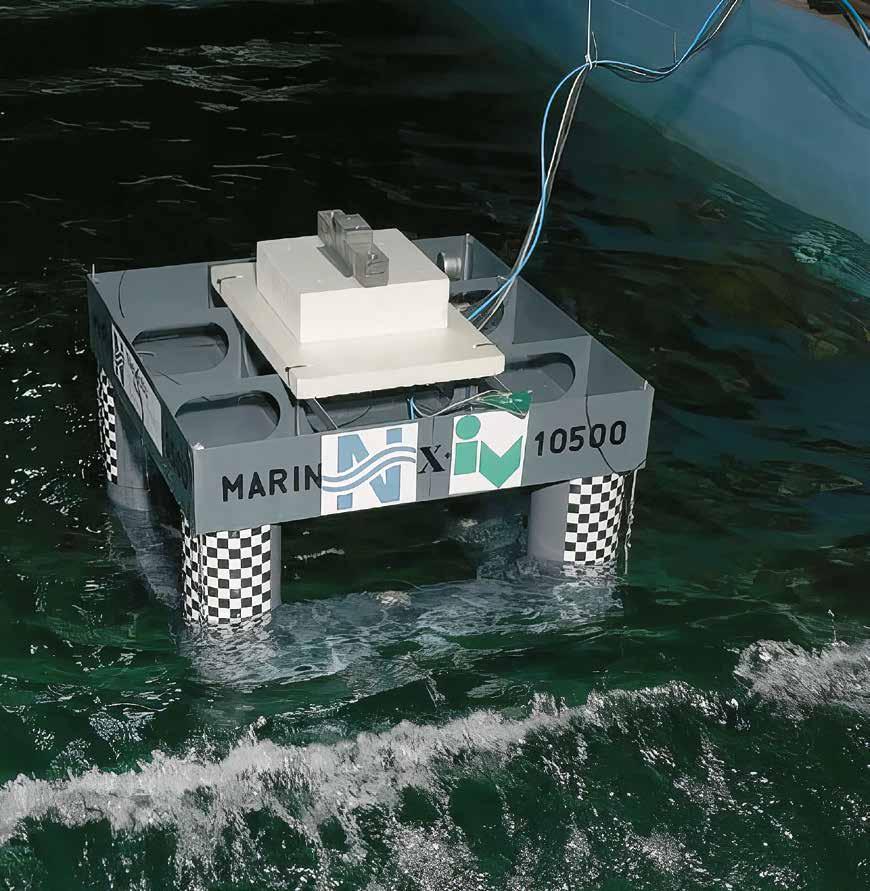
Scan the QR code and watch a video of the floating substation concept being tested with different configurations of the cable guide system (CGS) at MARIN (Maritime Research Institute Netherlands) on a model scale.
The concept has been developed to transform 1.4 to 2.0 gigawatts of power, with a DC export link of 300 to 525 kV. A typical HVDC topside weighs between 13,000 to 20,000 tonnes. The floating HVDC platform has a deck area of 85 by 85 metres and rises approximately 25 metres above the water’s surface. The overall arrangement has been optimised for application on a floating substructure. When the platform is installed at sea, it will be held in position with the help of so-called ‘tendons’ vertically anchored to the seabed, which restricts the vertical motions and accelerations.
The maximum wave height tested in the model basin corresponds to the once-in-100year event occurring to the west of the Shetland Islands.
3. Cable Guide System (CGS)
Dynamic inter-array cables are already being developed and tested at full scale on floating wind turbine pilots around the world and are, therefore, considered mature before the deployment of the first FOSS units. The DC export cables, on the other hand, are even more susceptible to fatigue due to the large core and surrounding metallic sheath. Nevesbu has developed a cable guide system that solves the fatigue problem for the DC export cable.
MARIN MKB model test
In October 2023, Nevesbu tested the floating concept with different configurations of the cable guide system (CGS) on a model scale. The model test was performed within the MKB slot provided by MARIN.
Two primary objectives were established for the model testing campaign. The first series of model tests was conducted to calibrate the numerical model. The second series of tests focussed on the CGS, where the system’s response was examined under different CGS pretension levels in various sea states. To achieve these objectives, the model was equipped with motion and acceleration sensors and load sensors on each tendon and cable guide.
The information for the expected sea states under which the substation will operate was logged. The maximum wave height tested in the model basin corresponds to the once-in-100-year event occurring to the west of the Shetland Islands, which is Hs > 17.0 metres. A first high-level check showed that the measured maximum offset, accelerations and CGS loads in irregular waves are comparable to the outcomes from the numerical model. The exact results of these tests are now being carefully compared and verified by Nevesbu, using the in-house developed numerical model and the data from MARIN.
Concept status and outlook
After the successful testing campaign of the floating substation, in combination with the in-house developed cable guide system, the FOSS concept is at Technology Readiness Level 3 and ready for further development. Based on this solid concept, more detailed fatigue life estimations of the floater, tendons, cable guide system and HV equipment will be carried out to further mature our design solution. Close collaborations with OEMs should be established in parallel to better understand equipment limitations. ●
Is green hydrogen the future?
The development of green hydrogen is in full swing. In the Netherlands alone, there are hundreds of pilot projects, FEED studies and small-scale projects for the production and transport of hydrogen. Larger hydrogen projects are also being launched. A major role in this development is reserved for engineers. And thus also for Iv. A hydrogen future requires an integral approach. Iv provides this approach with the highest quality and specialist expertise from a wide range of markets.
World premiere in green hydrogen production
On 7 May, Iv and its fourteen consortium partners celebrated a unique event: the onshore test of PosHYdon, the world's first operational gas platform to integrate offshore wind, gas and hydrogen. First production from the existing Q13a-A platform of Neptune Energy (Eni) is scheduled for the fourth quarter of this year, a world premiere. PosHYdon is an initiative of the national platform Nexstep and the TNO knowledge institute. Over the past few years, Iv, along with fourteen other partners, has focused on the development of this debut. Among other services, Iv provided the engineering and systems integration for the adaptations to the existing platform required for the production of hydrogen at sea. For this purpose, an electrolysis system that injects hydrogen into the existing gas export pipe will be installed.
Finding viable solutions for the safe and reliable production of green hydrogen is technically complex. In addition to participating in the PosHYdon project, Iv is also a knowledge partner in the North Sea Energy
programme, for which Iv has developed a 500 MW platform for green hydrogen as part of 'Offshore Energy Hubs'.
Ammonia is an excellent hydrogen carrier that can be produced anywhere worldwide by simply removing nitrogen from the air.
Development across the board
Iv is constantly developing and aligning itself across the entire breadth of the organisation because it is certain that hydrogen will play a significant role. However, finding viable solutions for the safe and reliable production of green hydrogen is technically complex and requires highly specialised knowledge from various markets. Iv is pioneering in many areas and is, among other initiatives, working on technical solutions for the import of hydrogen carriers such as ammonia.
We can also provide hydrogen storage and infrastructure solutions for industry and the built environment, enabling the accessibility and availability of green hydrogen to a wider market (not only within the industrial sector but also for SMEs, the transport sector and eventually households).
Thanks to our diverse background and expertise in a broad range of markets, we are playing a key role in the transition to green hydrogen production. We provide technical designs and systems integration, but we also draw on our in-house expertise in water technology, safety, procurement services, and project management.
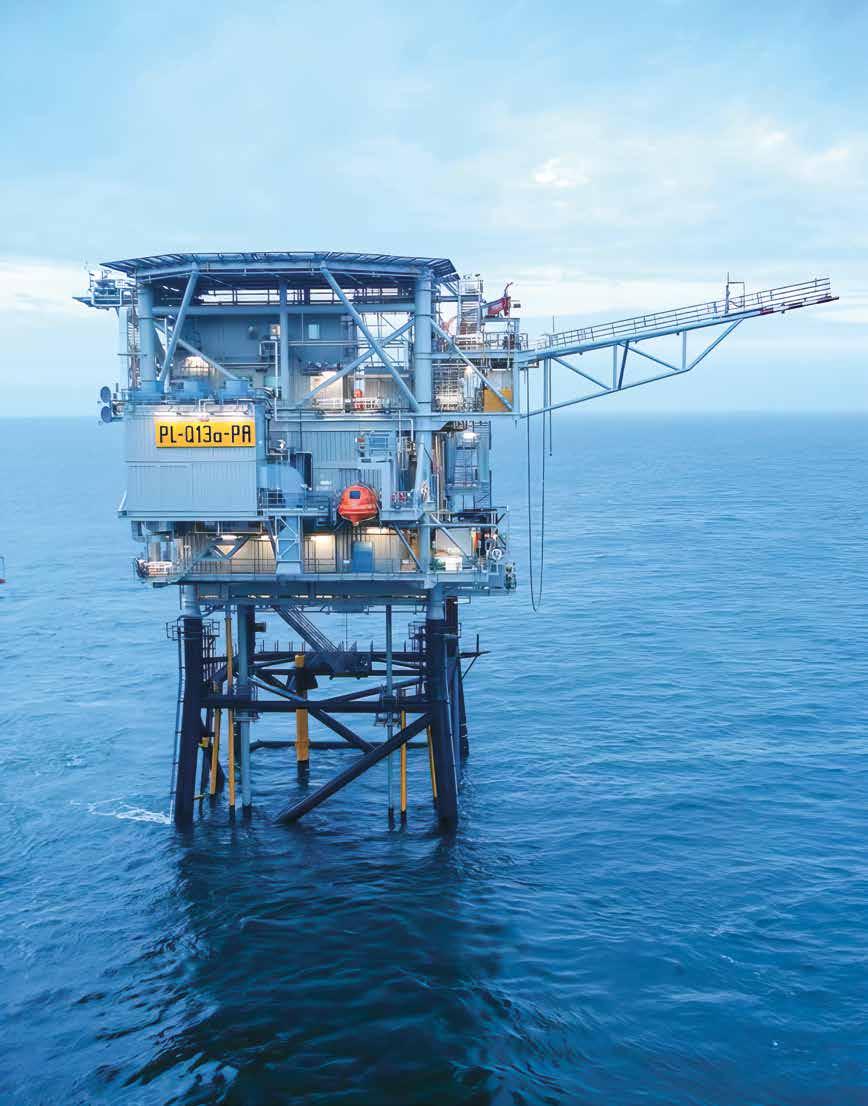
PosHYdon demonstrates the process on a small scale.
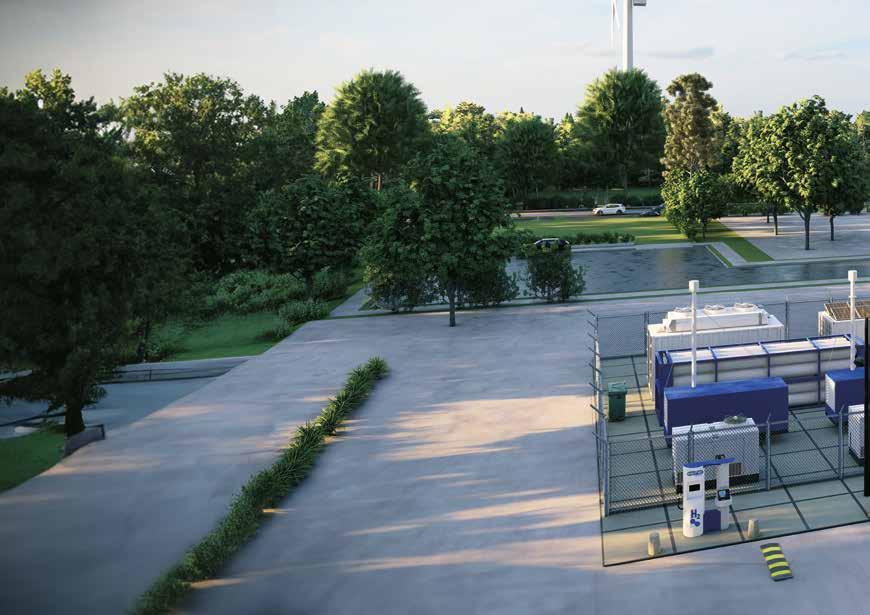
Modular design
It is not surprising that hydrogen has been on the political and business agenda for a long time, given its potential and impact on the world. Nor is it surprising that it needs time to gain a foothold. PosHYdon demonstrates the process on a small scale: a crucial step towards the eventual scale-up and commercialisation of green hydrogen production at sea.
Escher has developed a technology for the decentralised production of green hydrogen from ammonia.
Efficient transport is crucial for bringing green hydrogen to land and (small) industry. Iv is also actively involved in this aspect. Escher has developed a technology for the decentralised production of green hydrogen from ammonia. Ammonia is an excellent hydrogen carrier that can be produced anywhere worldwide by simply removing nitrogen from the air. Escher's technology splits ammonia back into hydrogen and nitrogen to enable separation into almost pure hydrogen and nitrogen. This method of producing hydrogen locally requires only a fraction of the energy used by conventional local hydrogen production using electrolysis. The process is, therefore, much less demanding on the electricity grid.
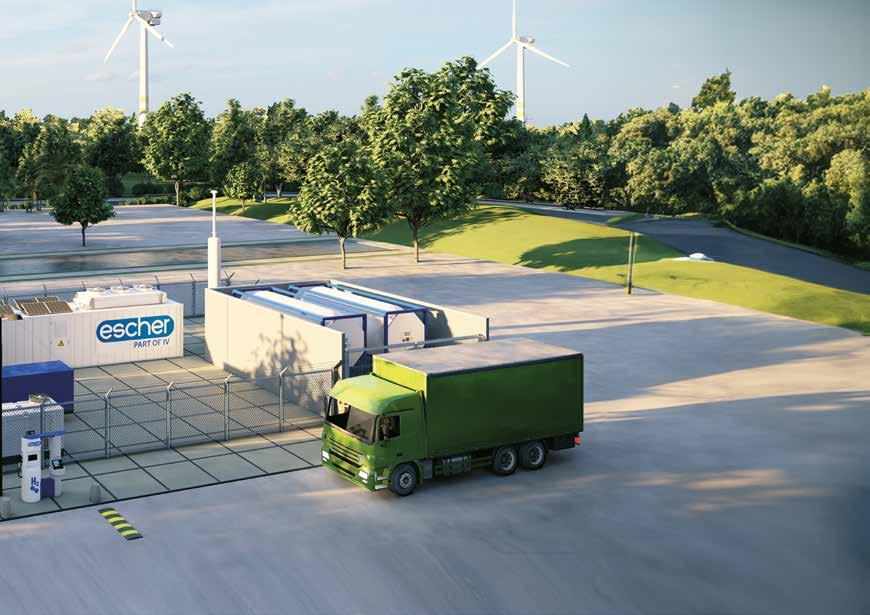
Our role: provide answers and workable solutions.
Widely applicable
As outlined above, Iv is active in the field of hydrogen across the entire breadth of the organisation. It is not just about production and the logistical challenges. Opportunities for hydrogen are being explored within various chains. In the water field, for example, we are looking at what we can do with the oxygen released during electrolysis and its capture in the vicinity of water treatment plants. This oxygen can then be used to feed bacteria, which in turn can be used for the aeration of the water treatment system.
National Hydrogen Programme
Iv recognises the importance of green hydrogen in the energy transition and is closely following national developments within the National Hydrogen Programme and the Hydrogen Roadmap towards large-scale production, import, infrastructure and storage (at sea) of hydrogen in 2030. We also see an important role and responsibility for us as an engineering company to provide answers and workable solutions to the challenges that are part of this journey. ●
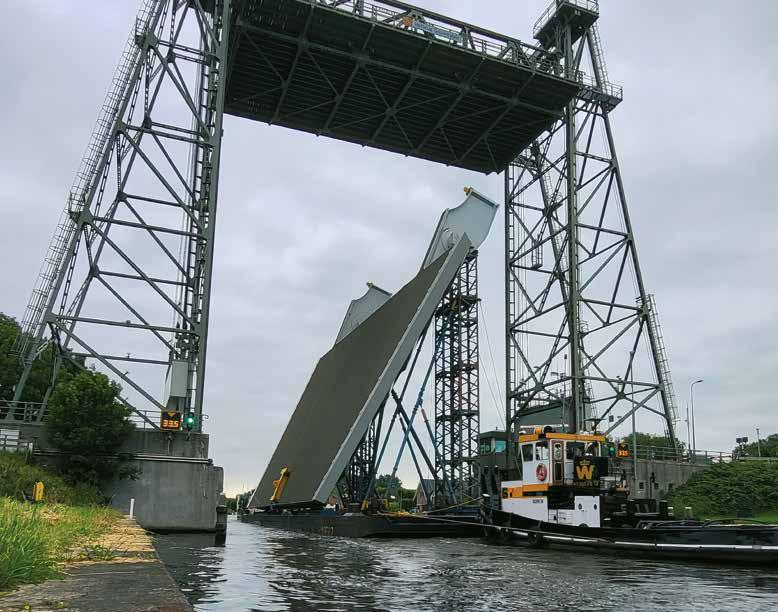
Renovation, reinforcement and expansion of the A9 Schiphol Bridge
Work on the Schiphol Bridge on the A9 motorway is in full swing. The project is being carried out on behalf of the Directorate-General for Public Works and Water Management (Rijkswaterstaat) and is aptly referred to as a technical masterpiece. It represents a huge infrastructure project. When completed, it will be the widest bascule bridge in the Netherlands. But what changes will be made to the bridge?
An important civil engineering structure
The Schiphol Bridge is an essential structure on the A9 motorway, facilitating the intersection between the A9, the Nieuwemeerdijk N231, the Ringvaart (Ring Canal) and the Schipholdijk. It consists of two bridges (northbound and southbound) with two movable steel decks with electromechanical operating mechanisms. The renovation and expansion work includes widening the concrete decks and substructure, renovating the bascule chamber, and constructing a new control building. This bridge structure requires careful design, planning, construction methods, and phasing to achieve a safe, efficient, and sustainable bridge that meets growing traffic demands with a remaining service life of 30 years.
Steel decks
The Schiphol Bridge consists of two sections, one for each direction of traffic. Each bridge is divided into a western approach ramp of approximately 85 metres, an eastern approach ramp of roughly 165 metres, and a movable section spanning approximately 20 metres.
For the new situation, the two existing steel decks and the drive mechanism will be replaced entirely and widened on both sides. The movable part of the bridge consists of an orthotropic deck slab supported by cross girders and main girders. The steel decks of both bridges (northbound deck and southbound deck) are virtually identical in design and detailing, except for the width due to the number of lanes they have to accommodate. The northbound deck is considerably wider than the southbound movable deck.
The counterweight of the northbound bridge is filled with approximately 442 tonnes of solid ballast. The design of the counterweight for the southbound bridge
differs slightly from that of the northbound bridge. The counterweight of the southbound bridge, which has a narrower width, is filled with approximately 362 tonnes of solid ballast.
The electromechanical mechanism allows the bridges to open and close independently for the passage of vessels.
Mechanical equipment
The mechanical equipment of the Schiphol Bridge is vital for its reliability and functional availability. It comprises several components and systems that function together to ensure the bridge’s operational movement, safety and maintainability.
One of the most important aspects of the mechanical equipment is the operating mechanism of the bridge. This electromechanical mechanism allows the bridges to open and close independently for the passage of vessels. It consists of a robust hydraulic system with electric motors and gear mechanisms (Panama wheel-pinion drive with crank mechanism) that ensure powerful and precise operation of the movable bridge sections. In addition, the mechanical equipment includes a crank mechanism that provides a locking force (the ‘locking and securing of the bridge’) to ensure a guaranteed closed position. This contributes to the bridge’s safety and minimises the risk of malfunction.
Sensors and measuring systems are also integrated into the mechanical equipment. These sensors monitor, among other things, the position, speed and forces exerted on the bridge. They provide valuable information to the control and monitoring system, enabling it to
position the bridge accurately and check for deviations during the opening and closing cycles. Based on this data, timely maintenance can be conducted to ensure optimum bridge functioning.
In addition to the above systems, there are other mechanical components such as bearings, seals and emergency drive mechanisms, and both decks are equipped with a manual drive mechanism. These components all play a crucial role in the smooth operation of the bridge and must be regularly inspected and maintained to ensure optimum performance.
To allow maintenance to be conducted with the bridge in the open position, a locking mechanism is provided in the bascule chamber to enable maintenance or replacement of drive components.
Concrete decks
An essential aspect of the renovation and expansion of the Schiphol Bridge is the widening of the existing, in-situ post-tensioned, concrete deck. To accommodate the increased capacity requirements (road widening), the existing concrete decks will be widened, and a coupling will be provided between the existing and new decks.
An advanced coupling between the existing and new decks provides strength, stability, and increased safety to the bridge.
The concrete decks will be widened by adding new in-situ cast post-tensioned decks on either side of the existing decks. The widening of the decks will be carried out on auxiliary bridges on either side, on which the formwork
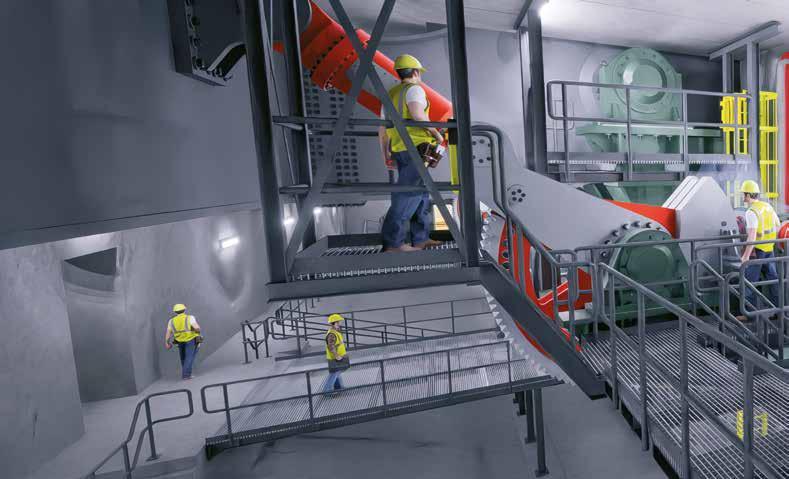
structures will be built over the Haarlemmer Ringvaart (Ring Canal). These new decks, with an advanced coupling to the existing structure, form a seamless transition between the old and new parts of the bridge.
The coupling between the existing and new decks is an important aspect of the concrete deck widening. It will be achieved by creating an integrated system of reinforcement drilled into the existing concrete decks and hydrojetting the exposed existing reinforcement to incorporate additional reinforcement. This form of coupling ensures that the forces exerted on the bridge are evenly distributed over the entire bridge deck, thus providing strength, stability, and increased safety. It also creates a functional, wider deck surface to facilitate expansion.
Bascule chamber
The bascule chamber is an essential part of the Schiphol Bridge. It plays a crucial role in the opening and closing of the bridge’s movable components. The chamber houses the mechanical equipment and provides the necessary strength, stability, and force distribution during the movement process of the drive mechanism, which exerts significant force on the concrete structures and foundations.
The existing bascule chamber will be renovated and adapted to meet the requirements of the new bridge configuration. Various adaptations will be undertaken, such as replacing the expansion joints, renewing the roof of the bascule chamber and strengthening the walls and floor. The front wall, up to a height of approximately 0.5 m NAP (Normaal Amsterdams Peil), will also be completely
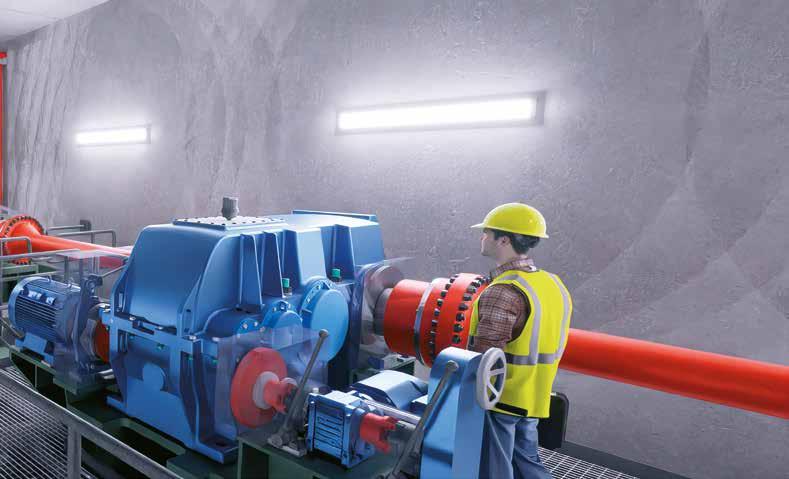
demolished and rebuilt. This renovation work will ensure that the bascule chamber can withstand the increased loads and forces and continues to meet the structural safety standards, with the intended remaining service life of 30 years.
In addition, the bascule chamber will be extended on the north and south sides to accommodate the new configuration of the bridge (road widening). The dimensions of the new part of the bascule chamber are significantly larger than those of the existing part.
Control building
The existing control tower will be completely demolished, and a new control building will be built on the north side of the Schiphol Bridge. The new control building will be constructed as a ‘box-in-box’ structure. The control building has been designed to provide a safe and comfortable working environment for the personnel responsible for operating the bridge. Although hidden from the direct view of road traffic, the control building has been architecturally designed and integrated with functionality and aesthetics in mind.
The control building has rounded corners and various design features to visually differentiate it from the bridge deck. As a result, the building will be a recognisable element of the location and contribute to the overall appearance of the bridge.
Meanwhile, work on the A9 Badhoevedorp - Holendrecht motorway is progressing steadily. The widening of the Schiphol Bridge is set to be completed first. According to current plans, this should be in the summer of 2025. The entire project will be completed in 2027. ●
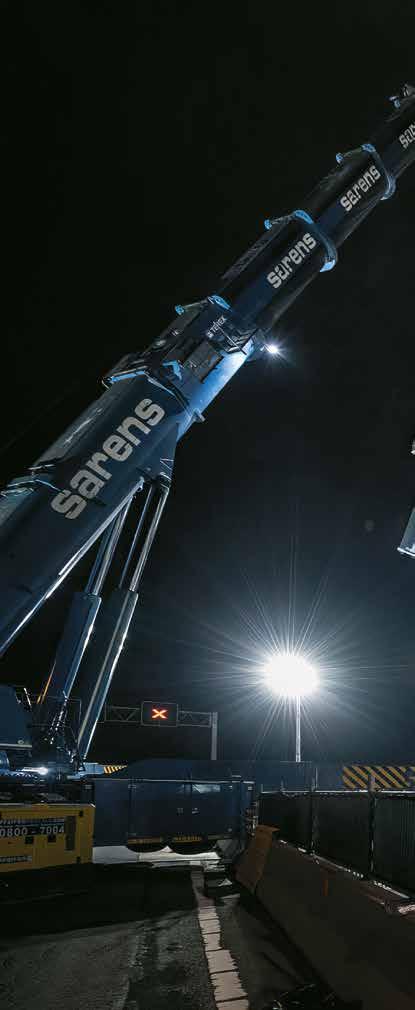
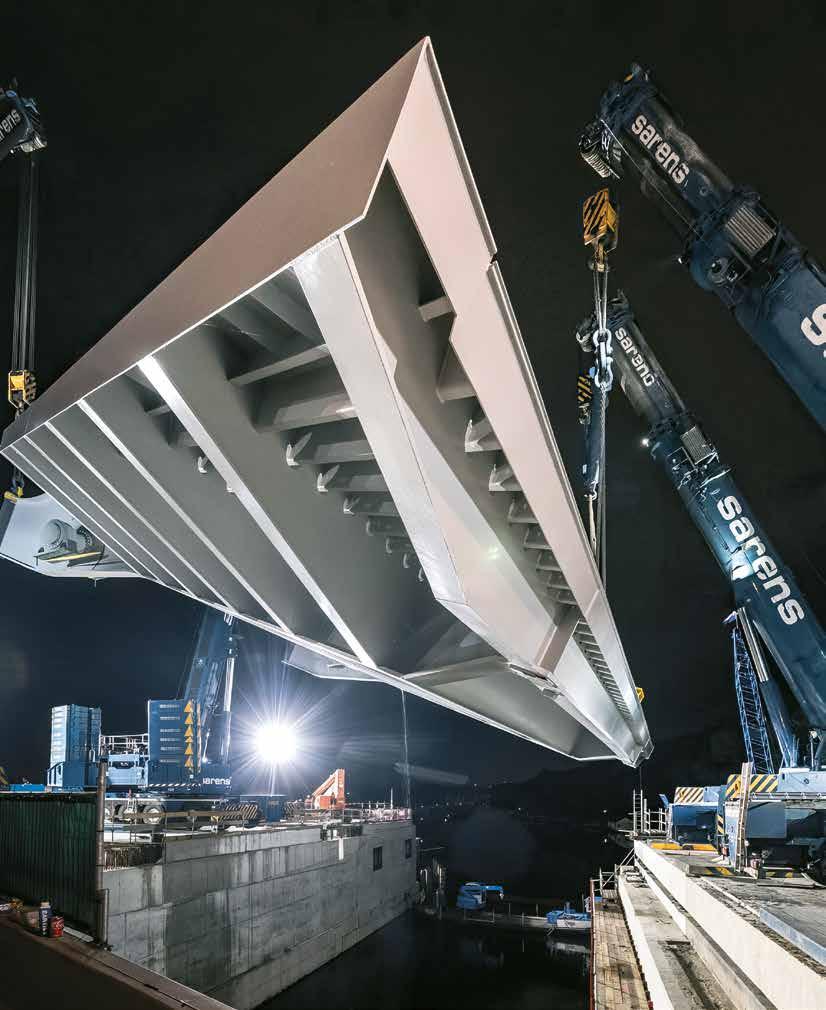
The new PALLAS-reactor will help even more patients with cancer treatments
Did you know that nearly 30,000 patients worldwide depend on the production of medical isotopes every day? These radioactive products are indispensable for the diagnosis and treatment of cancer. The challenge we face is to ensure the production of these life-saving isotopes for the future. This is where the new PALLAS-reactor comes into the picture, a project in Petten in the province of Noord-Holland (The Netherlands), that will secure the future continuation of medical isotope production.
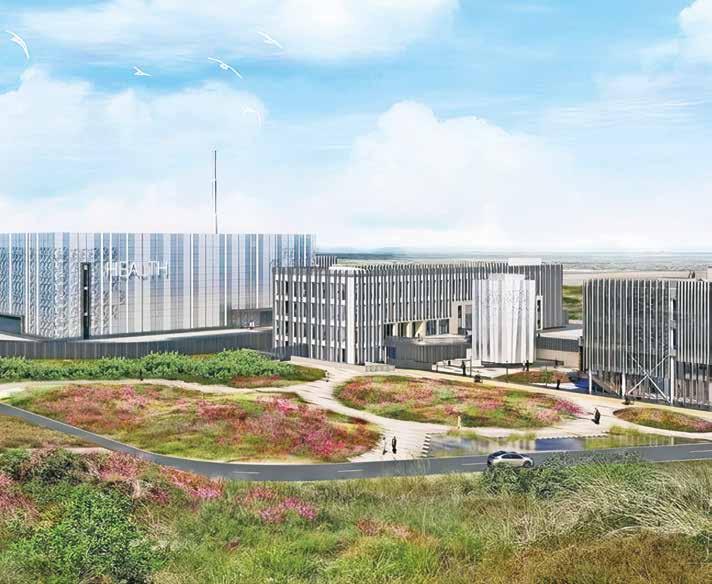
The importance of the PALLAS-reactor
But why is the PALLAS-reactor so important? The current High Flux Reactor (HFR), which has been in operation in Petten since 1961, is approaching the end of its technical life. In addition, the 63-year-old reactor is increasingly in need of intensive maintenance and cannot meet the growing demand for medical isotopes. “The HFR was originally intended as a research reactor for testing materials and was only later adapted for isotope production. The PALLAS-reactor, on the other hand, has been specifically designed for large-scale production”, explains Jan van der Marel, project director at PALLAS.
The PALLAS-reactor has been designed to focus on medical isotope production capacity.
When completed, the new PALLAS-reactor will take the production of medical isotopes to a higher level, enabling the Netherlands to continue helping millions of people for the next 50 years. Jan van der Marel: “The new reactor will enable us not only to meet the demand in the Netherlands but also to make a significant contribution to the supply of medical isotopes throughout Europe and even the world.” Although the basis of the design is inspired by the OPAL reactor in Australia, PALLAS is far from being a mere copy. While the OPAL reactor mainly focuses on research and produces medical isotopes to a limited extent, PALLAS is the exact opposite. This reactor has been designed to focus on medical isotope production capacity, with room for research activities. PALLAS is, therefore, a unique reactor specifically designed to meet the growing demand for medical isotopes, representing a major step in advancing the production and availability of these life-saving resources.
How does it work?
But how exactly does the reactor work? Imagine a large reactor pool filled with water, about four metres wide and fifteen metres deep. The reactor core is located at the bottom of the pool. Special nuclear fuel elements with enriched uranium are used in the reactor. These elements are positioned in a reflector vessel where they emit neutrons. The reactor pool also contains special ‘targets’. These targets are materials that have been designed to capture the neutrons. When the neutrons come into contact with the targets, they are converted into isotopes. Isotopes are a special type of atom that are radioactive, meaning they emit radiation. In medicine, they are used to detect and treat diseases such as cancer. Thanks to this radioactivity, doctors can see what is happening in the body, and isotopes are used to treat cancer.
Key roles in reactor design
ICHOS, a collaboration between Argentina’s INVAP and subcontractors such as Iv for the engineering, is playing a key role in the development of the new PALLAS-reactor. José Louis Molina, project director at ICHOS, explains: “Our main task is to deliver a radioisotope production facility that meets PALLAS’ high performance standards.” ICHOS has been involved since the early design phase and is working closely with Iv to ensure all aspects of the facility meet the required quality standards.
Iv is working with a team of around 100 people on the realisation of the new reactor. “We are responsible for the engineering and support of the conventional systems that enable the reactor to operate”, says André van Es, senior project manager at Iv. These include nuclear and conventional HVAC systems, tap water, waste and rainwater systems, building management systems,
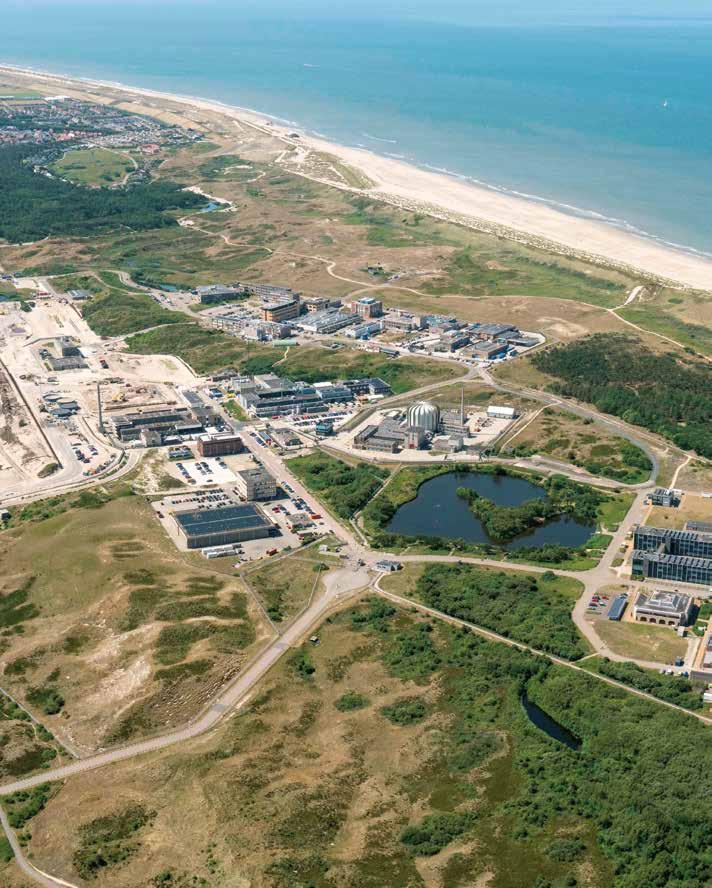
radioactive liquid waste systems, demineralised water systems, compressed air systems, industrial gas systems and secondary cooling systems. “Without these systems, the process would not be possible. In this way, we ensure that everything around the reactor works properly, enabling the reliable and safe production of medical isotopes.”
In a nuclear reactor, it is important to create different ‘zones’ for managing air to ensure that radiation is kept within safe limits.
In addition to these systems, Iv is also responsible for all the instrumentation, such as temperature and pressure gauges, necessary to operate the systems and communicate with other systems – a vital and complex task due to the many interfaces and connections that need to be appropriately coordinated.
“In a nuclear reactor, it is important to create different ‘zones’ for managing air to ensure that radiation is kept within safe limits”, says André. “No air can be allowed to flow from the inner zone, where the radiation is strongest, to the surrounding zones around the reactor. So we have to make sure that air can only flow from the surrounding zones to the inner zone to prevent any release of radioactivity by air. We achieve this by regulating the air pressure between the different zones. Any exposure or release of radioactivity will remain within the dedicated zones. The air within these inner zones is filtered through special filters and safely released into the environment.”
Safety standards
According to André, Iv’s experience with similar technologies in the pharmaceutical industry is very useful in this project. For example, zoning principles are also used in vaccine manufacturing plants to prevent the escape of viruses. In addition to the technical challenges of zoning, the logistics around the reactor are also crucial.
“In a production environment like this, everything has to run quickly, safely and efficiently”, explains André. “The isotopes are handled and packaged in ‘hot cells’. These cells must be safely shielded to prevent operators from being exposed to too much radiation. The products must be safely transferred from the reactor via the hot cells to the logistics areas for transport without the risk of radiation contamination.” André: “Imagine that there are six hot cells for handling isotopes. For each cell, the correct pressure cascade must be ensured between each of them as well as in relation to the surrounding logistics areas, so the air flows in the right direction and the risk of radiation contamination remains within the limitations of the applicable standards. Such complexity makes it imperative that our systems are well designed, function properly and are reliable .”
I don’t think any other project in the Netherlands is coordinating and making information available in this way.
The design of the PALLAS-reactor must meet strict requirements to guarantee safety. The most important aspect is that everything must be designed in accordance with the Nuclear Energy Act and the Dutch
Safety Regulations for Nuclear Power Plants (DSR). These regulations ensure the reactor remains safe in various emergencies, such as earthquakes, floods and aircraft accidents. André explains: “The reactor design must be able to withstand extreme conditions. So this means that the systems themselves must remain reliable and continue functioning, even in the event of an emergency. For example, in the event of a flood, the power supply systems for critical equipment, such as diesel generators and control systems, must continue to operate to prevent the situation from becoming unmanageable.” Radiation in the immediate vicinity of the reactor also presents a challenge in terms of material use. The new reactor needs to last at least 60 years. Radiation affects the materials inside the reactor. Constant exposure to radiation can cause materials to age or be damaged more quickly. Therefore, all materials in the reactor must be resistant to this radiation and designed to last for decades. Furthermore, systems such as piping and ducting must be designed to allow for regular cleaning and maintenance.
The PALLAS project not only solves the current problems but also demonstrates how we can build other reactors in the future.
From challenge to victory
“What excites me about this project is the enormous challenge of systems engineering, including verification and validation (V-model), and information management”, says André. “It’s not only about the technical complexity of the installations but also the coordination of all models and data. For example, we have to make all 3D models available centrally every two weeks in a so-called ‘Common Data Environment’ and ensure full
coordination. This means that during the engineering phase, we have to make sure that all information relating to, for example, pressure, temperature and the materials used is immediately available and linked.”
André adds: “I don’t think any other project in the Netherlands is coordinating and making information available in this way.” According to him, working with different (international) parties and tooling systems that do not always integrate seamlessly makes it even more complex. Ensuring all the information is brought together correctly and everyone is working with the correct data is a huge challenge.
José Louis adds: “When all 500 systems finally work together, and everything operates as it should during commissioning, it feels like scoring a goal in the World Cup final. We have a crucial moment in the process called ‘criticality’. This means we have brought the reactor to capacity and maintained stability. It’s a big moment for us, comparable to winning the World Cup. It confirms that the reactor works.” But José is quick to point out that criticality is only the beginning. “After criticality, we still have to demonstrate the system’s performance. There is still a lot of work to be done to ensure that everything complies with the requirements. But you can already see that the project is successful at that point. Then comes the fine-tuning phase.”
The blueprint for the future
The PALLAS-reactor represents a major step in the production of medical isotopes and is also a possible blueprint for future reactor projects. José Louis explains: “We are building a virtual model (digital twin) of the reactor to train operators and simulate operations as realistically as possible. Such a model involves a lot of
work, but it helps us to manage the reactor safely without having to use the actual installation, which has to last at least 60 years.”
The demand for medical isotopes continues to grow.
The PALLAS project not only solves the current problems but also demonstrates how we can build other reactors in the future. The current PALLAS-reactor has been in the pipeline for decades as a replacement for the HFR. Jan van der Marel has been involved in this project since 2016. “From the very beginning, we have had to overcome many obstacles in terms of obtaining the necessary permits. So, even at the start of the project, we didn’t know if it would be successful. However, now it is
clear that we have successfully overcome the last hurdle: approval from the Ministry of Health. From now on, all the challenges ahead are in our own hands.”
The transition from the old HFR reactor to the new PALLAS-reactor is a process that will take place over the coming years. For a period of around two years, both reactors will continue to operate to ensure uninterrupted production of medical isotopes. Once the PALLAS-reactor has reached full capacity, the HFR will be decommissioned. Construction of the new medical isotope reactor in Petten will commence next year. If everything goes according to plan, the PALLAS-reactor will be ready around 2030. ●
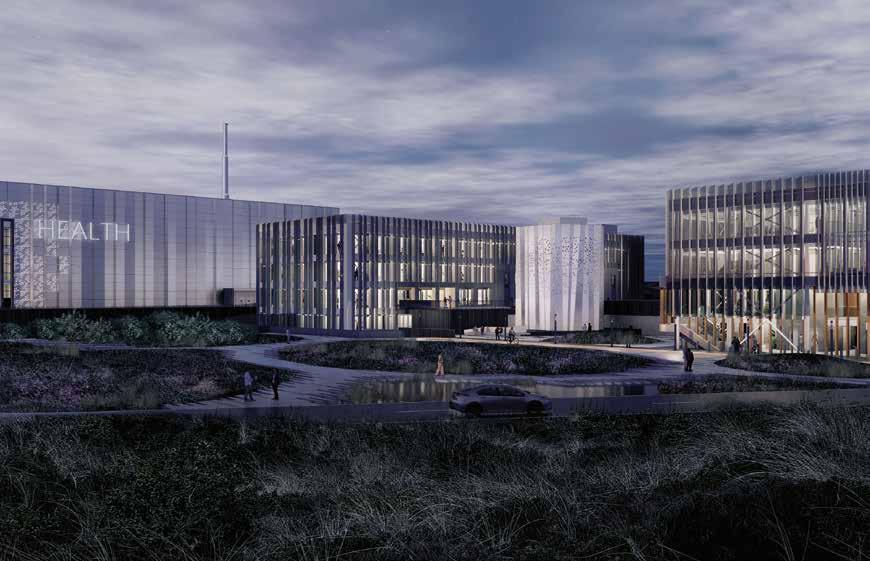
Keeping the R&R task manageable by controlling uncertainties
Our country is home to some €347 billion worth of infrastructure. Much of it was built in the decades after the Second World War and was designed to last sixty to eighty years. However, its use has increased, and it has often been subjected to greater loads than anticipated when it was built. As a result, many bridges, locks, quay walls and tunnels are (almost) reaching the end of their life. Over the next 75 years, no less than 260 billion euros will be needed to finance the Replacement & Renovation (R&R) task. These costs are expected to increase considerably in the coming years. But is this billion-dollar spending spree really necessary? Or can we reduce the costs and spread them over a more extended period?
Costs rising by billions
The cost estimates mentioned above are from the 2nd report of the National Forecast for the Replacement and Renovation of Civil Infrastructure, published by TNO at the end of 2023. At the request of the National Government, the Association of Provinces of the Netherlands and the Association of Netherlands Municipalities, TNO has once again mapped out the scope of the R&R task in the Netherlands, following an initial version of the forecast in 2021. Mapping the R&R task nationally is a major challenge, given the large number of civil structure managers and the fact that the required information is not always available. The forecast is, therefore, also inevitably fraught with uncertainty; more on this later.
According to the 2nd National Forecast report, the expected annual cost for provinces, municipalities, and other authorities will rise to almost €3 billion between now and 2040. This is much more than budgeted. From 2040, the annual cost of R&R will continue to rise,
reaching around €3.7 billion by the end of the century. Civil structures account for the largest part of the R&R costs, which are predicted to rise from €1.5 billion annually to around €2.6 billion by 2080.
We conduct structural assessments of bridges and quay walls to determine the assets’ structural safety and remaining service life.
And so there is unease among managers and owners of civil structures because what exactly needs to be done, how urgent is the problem, and how will we pay for it? These are all initially logical questions.
Explore further
To find answers to these questions, we need to explore beyond the intended (design) life of each structure. In its 2nd National Forecast report, TNO assumes, in all
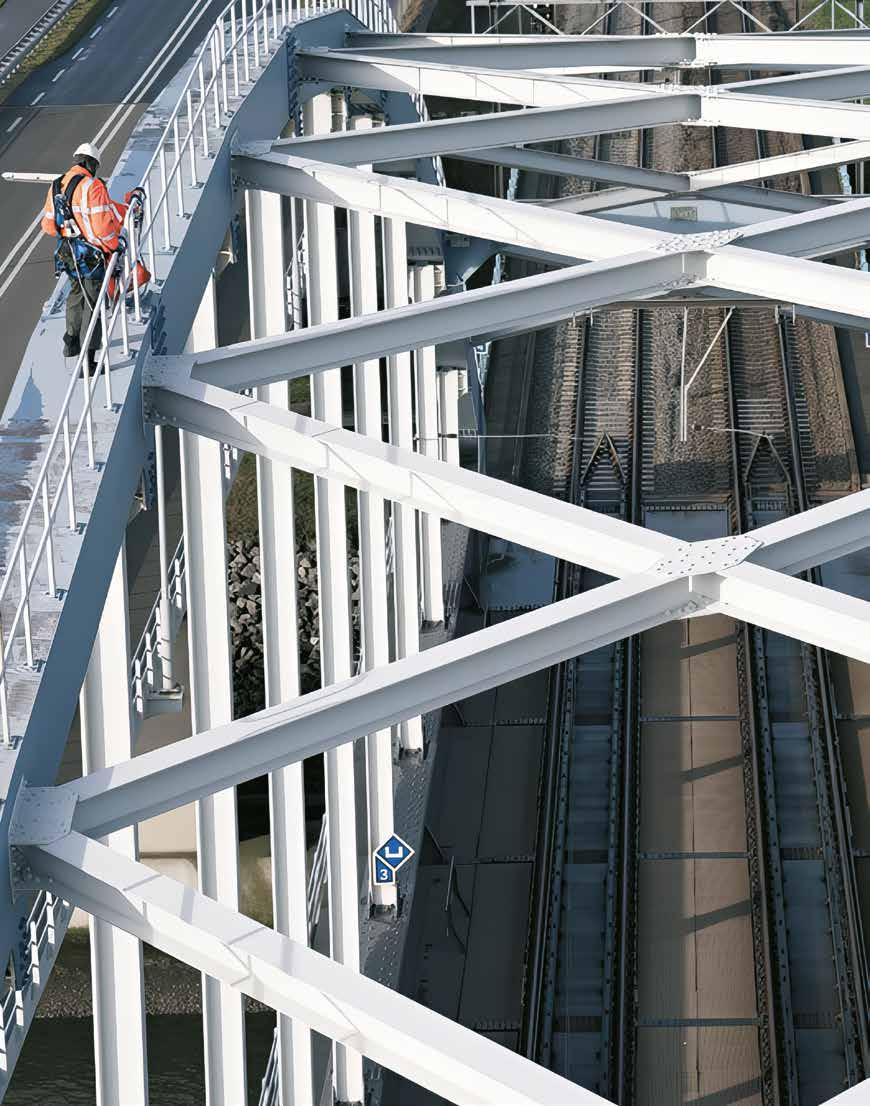
cases, a one-for-one replacement after the structures have reached their expected (average) life. Growth or changes in the area's functionality, such as more intensive use, a different layout, or any possibilities for (circular) life extension, are not considered. Logically, the TNO study does not take into account the actual quality of the area nor the possibility of monitoring the current condition to better determine and hopefully postpone the replacement dates. Forecasting the total R&R task is, of course, subject to a high degree of uncertainty.
The structural safety of an object can be much greater than that based on a ‘standard’ calculation.
We have noticed that the above simplifications and uncertainties are often overlooked in discussions regarding these forecasts. In light of the objective of the forecast report, these simplifications and uncertainties are understandable, but this is precisely where the key to making this task manageable lies: controlling the uncertainties. Iv, therefore, seizes the opportunities here to ease the pain of the R&R task, and we have already been doing this for many years. For example, we conduct structural assessments of (sections of) bridges and quay walls to determine the assets' structural safety and remaining service life. We do this in a risk-based way, from broad to detailed: in general terms where possible (for example, with quick scans), and we get the absolute utmost out of the structure when necessary (through inspections, research and calculations). This is how we achieve maximum control with minimum effort. As a result, we have been able to 'save' many structures from 'ruin'. The structural safety of an object can be much greater than that based on a 'standard' calculation. Many load tests developed and conducted by us have also demonstrated this.
We prefer the term Maintenance, Renovation and Replacement task: maintain when possible, replace when necessary.
A call to all managers: cherish your civil engineering works! Because, in many cases, the structural safetyand therefore the remaining service life - is better than expected. Things are not always as bad as they first seem: an object may last for decades, much longer than its design life, without or with relatively limited adjustments. In other cases, measures can be postponed responsibly when monitoring is applied. With a comprehensive range of asset management services, we ensure that managers
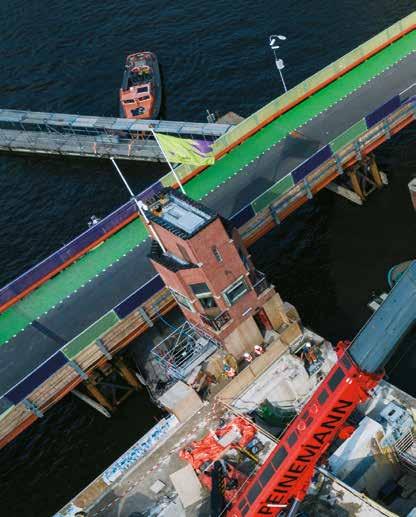
of civil structures gain and maintain the required insight into the condition of their assets, allowing them to create an optimal multi-year plan for the maintenance or replacement of their infrastructure. 'Replacement' is not the first option we should consider when a structure is nearing the end of its life: so much more is possible. Therefore, we prefer the term Maintenance, Renovation and Replacement task: maintain when possible, replace when necessary.
Making the task manageable
For the Directorate-General for Public Works and Water Management (Rijkswaterstaat), Iv is working with ARUP and Wagemaker to map the structural condition of
dozens of fixed and movable bridges in the main road network. The challenge for us as an engineering company is to make the right decisions using the correct approach. If necessary and responsible, we strive to achieve the most out of a structure so that physical measures can be minimised and postponed responsibly while ensuring structural safety at all times. In this way, we help to reduce the high social costs for infrastructure and, consequently, the burden on our environment. So that the Maintenance, Renovation and Replacement task remains manageable for all of us. ●
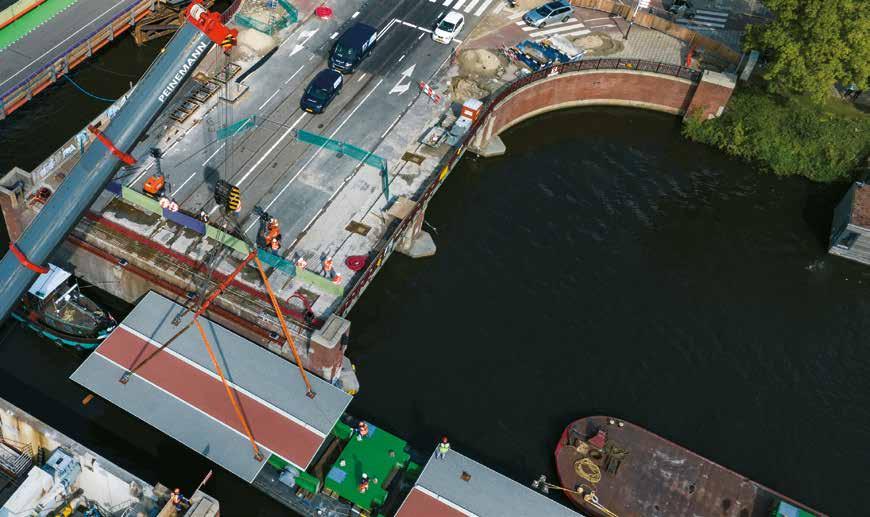
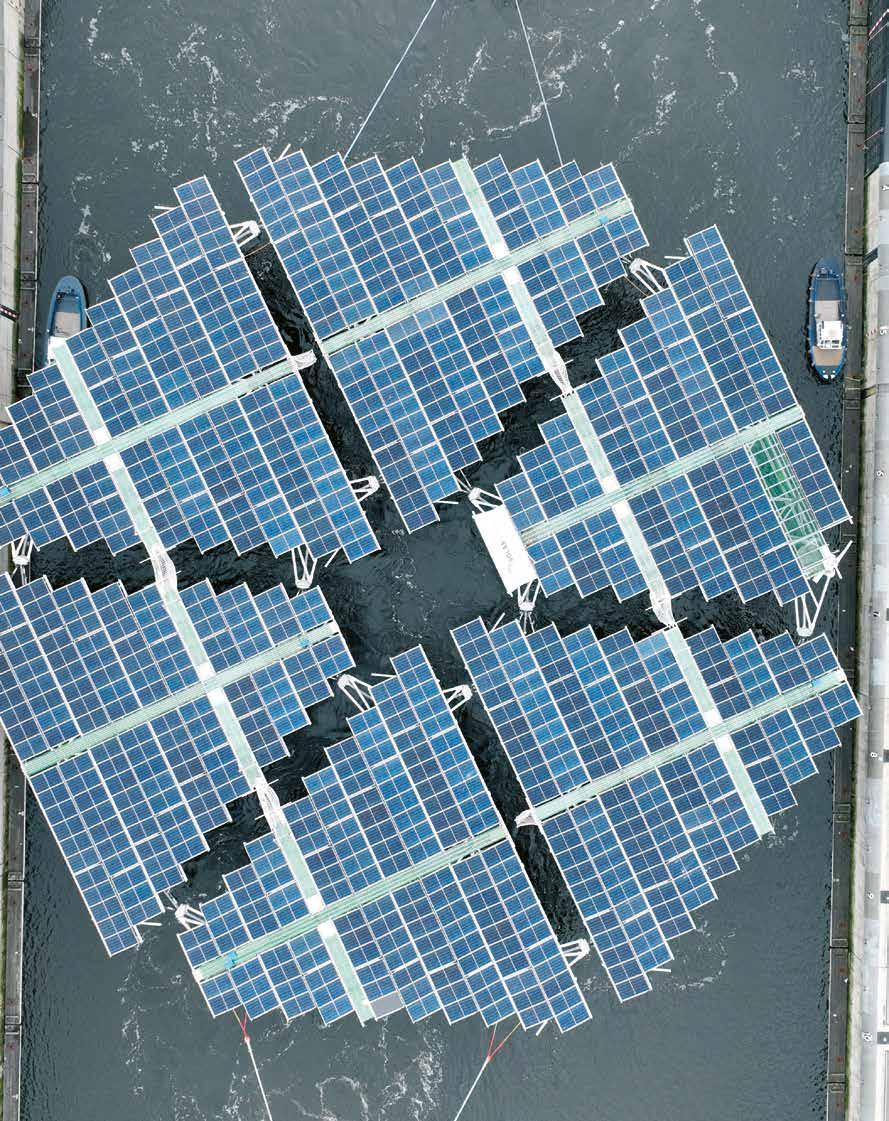
Realising the world’s largest floating solar platform
In the Dutch offshore wind farm Hollandse Kust West (HKW) VII, around 53 kilometres off the coast of IJmuiden, the TotalEnergies/RWE consortium is developing a new form of sustainable energy generation. As part of the project, the world’s largest floating solar platform will be integrated alongside wind power generation. The floating solar platform is an innovative solution devised by the Dutch-Norwegian company SolarDuck and will be located between the wind turbines. The platform will consist of floating, interconnected triangular structures with solar panels. SolarDuck selected Iv to conduct the technical development and optimisation of this innovative concept to ensure that it meets all the requirements for installation and use at sea.
The floating solar platform
The floating solar platform that will be installed in the HKW VII wind farm is based on the Merganser test platform, a prototype solar platform with an energy generation capacity of 520 kWp (kilowatt peak) that was installed as a pilot 12 kilometres off the coast of Scheveningen in the North Sea. The often-harsh North Sea environment in which the HKW VII wind farm is located is considered one of the most challenging offshore environments in the world. Iv is applying its extensive offshore knowledge and experience to help optimise the existing design for these unique conditions.
By installing the platform between the wind turbines, the space at sea is used as efficiently as possible, and the grid system, which has already been installed for the wind farm, can also transport the electricity yield to shore. In addition, the maintenance of both energy systems can also be combined to take place simultaneously.
High potential worldwide
The possibility of realising more large solar parks on land in densely populated areas is decreasing. However, the demand for sustainable energy is only increasing, and this trend is set to continue. The floating solar platform is a solution to help electrify countries worldwide and provide security in supplying affordable, sustainable energy. It is a suitable solution for increasing sustainable energy supply, particularly in densely populated countries with lower average wind speeds and higher solar irradiation levels.
From idea to sea
SolarDuck started with this idea five years ago. But how do you get such an innovative solution to work at sea? How do you achieve a reliable structure that will operate for at least 30 years without maintenance? And how do you ensure that the entire project can be safely installed offshore? In addition to the overall technical optimisation of the design, Iv is advising SolarDuck on hydrodynamics (the motions the structure undergoes due to the waves), anchoring and installation. Iv is also responsible for ensuring that the design is approved by the classification
society. The harsh conditions at sea subject structures to fatigue and corrosion, among other things. Besides this, the structure must be able to properly absorb the motions of the waves so that the systems on the structure (such as solar panels and subsystems) are not damaged. Iv, as an experienced engineering company, specialises in such issues.
It takes a lot of creativity to make it technically, financially and safely feasible.
“It’s awesome to be involved in the development of new technology”, says Pieter de Boer, lead engineer at Iv. “A solar park at sea, fully functional and at this distance from the coast, has never been done before. From a technical point of view, it is incredibly challenging and complex. It takes a lot of creativity to make it technically, financially and safely feasible.”
Simulation
But what makes it so complex? It goes without saying that creating something new is, by definition, no easy task. Among other things, the ‘behaviour’ of all the different platforms of the solar park is special and an important aspect. Pieter: “These all influence each other to a certain extent. It is quite a challenge to simulate the behaviour in the right way. Another factor is that people are present on the platform from time to time. We want them to be able to do their work as safely as possible, so we have to include that in the design.”
Iv is currently researching how the solar park will eventually look in terms of the number of platforms, the layout, and the exact location. The floating solar park is expected to be completed in 2026. ●
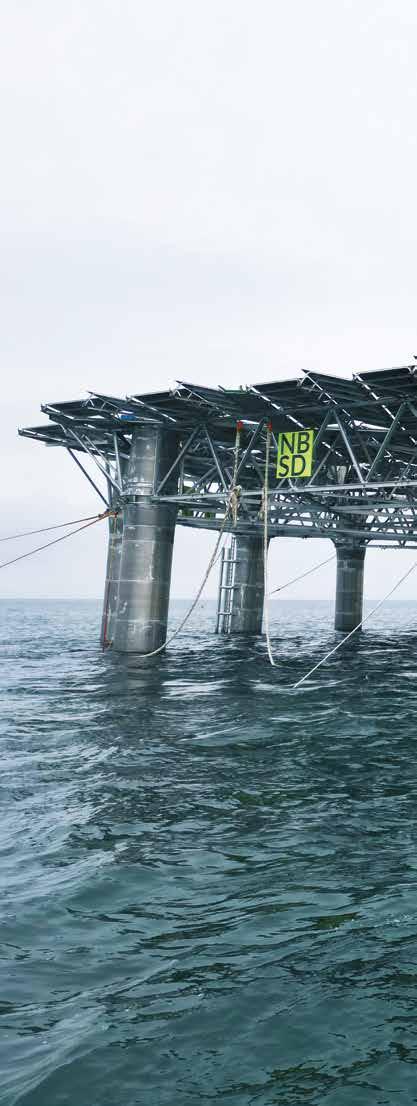
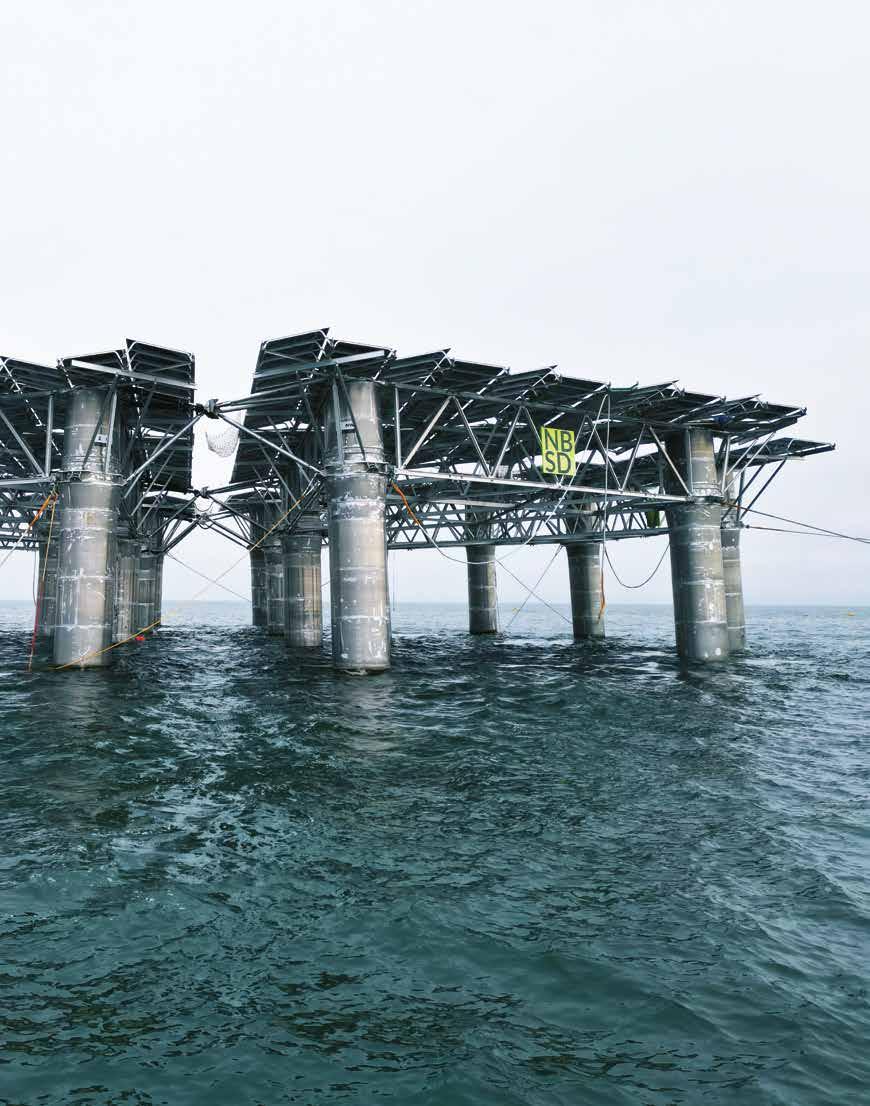
The demand for sustainable energy is only increasing.
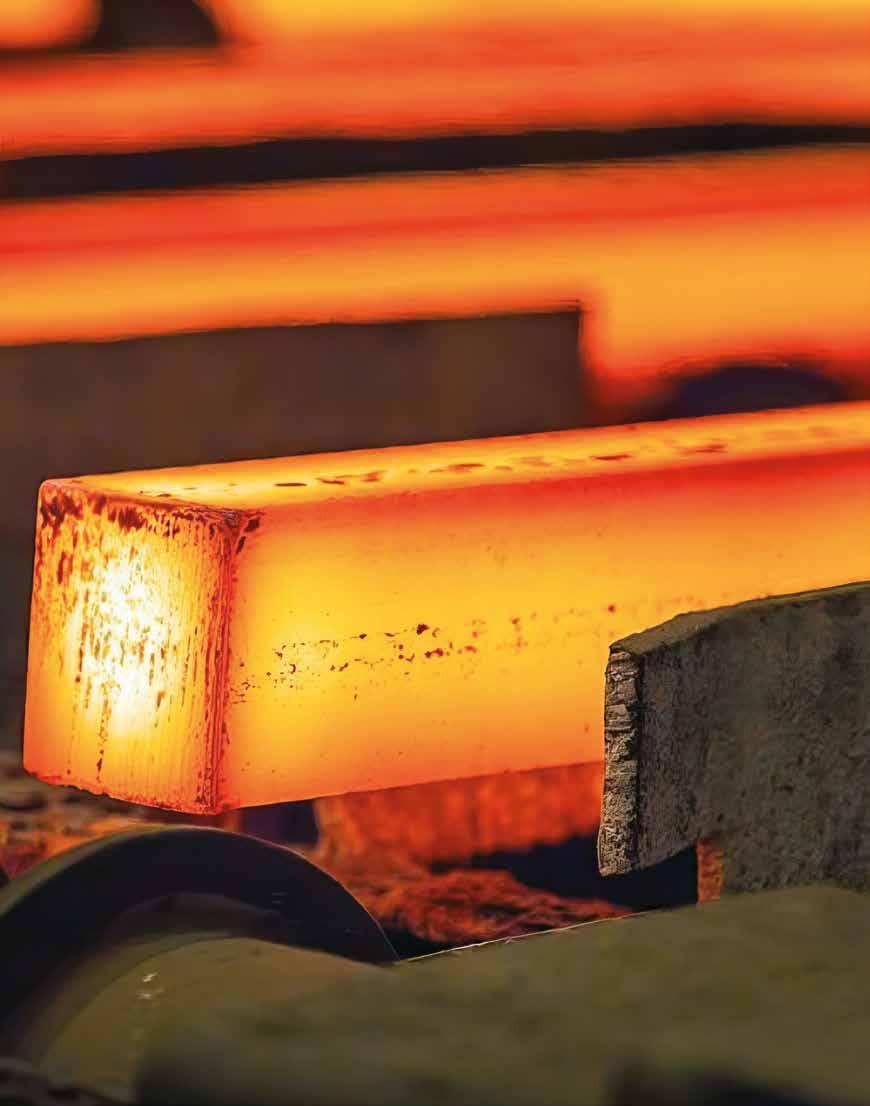
Making heavy industry more sustainable
We are surrounded by steel. From cars, ships and trains to buildings and products such as batteries and refrigerators. It is hard to imagine life without this material. While steel underpins our daily lives, it also poses a serious challenge. The entire steel production chain, from the extraction of raw materials to the manufacture of steel products, emits large amounts of CO2. The question is: how can we make steel without further damaging our planet? This is where Iv comes in. Iv offers support to producers throughout the entire chain to make their future production greener and more sustainable. Moreover, Iv is helping to accelerate this necessary transition.
Why is heavy industry under pressure to become greener?
Significant amounts of CO₂ are emitted throughout the chain within the heavy industry sector, mainly because traditional parts of heavy industry, such as the steel production process, use a Blast Furnace coupled with a Basic Oxygen Furnace, which emits large amounts of CO₂ and other emissions and is very energy intensive. Stricter EU emission targets and ever-increasing customer demands are forcing steel producers to adapt their processes on a large scale. Yet at the same time, they must also guarantee quality. This applies to steel producers and the entire heavy industry chain. These are significant challenges because the new processes are not yet capable of producing the quality and quantities that the existing processes have achieved. The industry is having to invest a lot of money and time in advanced technologies to meet legislation and societal expectations. The biggest challenge? Meeting the new emission requirements, such as reducing CO₂ emissions, without compromising quality and production volumes.
The
problem continues to grow as people consume three times as much as they did fifty years ago.
Rick de Jong, director of Heavy Industries at Iv, explains: “Steel itself is a very sustainable product because it is 100% and infinitely recyclable. It can be used again and again while retaining its properties, original quality, and strength. Steel is, therefore, one of the most widely used materials in the world due to its versatility and relatively low cost. But the problem lies in the production process. Iron ore is mined from the ground and converted into liquid iron in a Blast Furnace. During this process, iron ore, coke, and limestone are combined with oxygen, emitting large amounts of CO₂. In addition, the unique properties of steel make it difficult to replace on a one-to-one basis with alternative materials. Steel is extremely strong and versatile, making it a material for countless applications, which means that even if alternative materials were used, much larger quantities of the substitute material would
be needed to achieve the same properties, which may not necessarily reduce the environmental impact. It is therefore imperative to find new and sustainable ways of producing steel that have less impact on the environment and retain the unique properties of steel.”
Key role
It is clear: heavy industry needs to become more sustainable and greener. Iv plays a key role in today’s quest for this higher level of sustainability. How? Iv offers heavy industry support to accelerate its sustainability and greening journey. Rick: “Our approach is twofold. We need to adjust the existing process now to deliver immediate results while focusing on the near future. Despite having already made the industry greener in certain areas, the problem continues to grow as people consume three times as much as they did fifty years ago.”
Iv’s strength lies in its knowledge and experience of process optimisation. “We fully understand how it works
in practice and where it needs to go. On paper, processes always seem to be perfectly designed and working, but in reality, it can often take years before everything is properly aligned and the desired results are delivered. We have served the steel industry since our founding 75 years ago (1949). Our practical knowledge and experience, combined with a pragmatic approach, helps our clients to optimise their processes effectively.” Iv’s experience spans not only the steel industry but also other sectors, such as manufacturing and energy. Despite the differences between these sectors, the approach to sustainability is often similar. Such knowledge enables us to offer customised solutions that make current processes more sustainable and integrate future innovations.
Reuse, remanufacturing, and recycling will become increasingly important in the future.
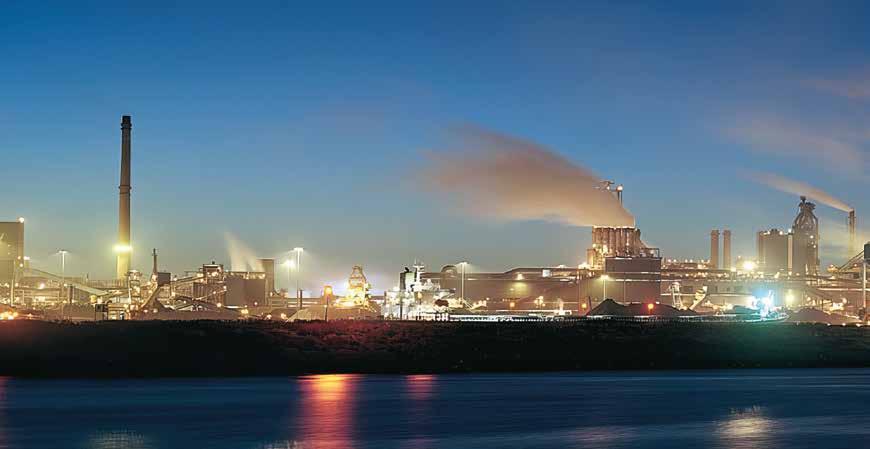
In addition to over 75 years of knowledge and experience in heavy industry, Iv has worked on large-scale sustainability, emission reduction and greening projects in the industrial sector worldwide for the past ten years. This cache of experience has given Iv a unique lead in plant design and systems integration of future-proof and ‘green’ installations and production facilities.
Making the entire chain more sustainable Steel production involves several steps to first make iron and then steel from iron ore. The steel produced is often further processed into beams and coils for the next stage of production. Besides steel production, there is much to be done both upstream and downstream in the process. Iv has experience in all parts of this chain.
Making heavy industry more sustainable starts at the bottom: the extraction of raw materials, a process which is often environmentally damaging. Many harmful emissions are released during the extraction of raw
materials in mines and during storage and handling. In recent years, a lot of time and energy has been spent on improving this step, and we are leading the way in Europe. “In the future, coal will gradually give way to hydrogen. This will help to reduce CO₂ emissions significantly”, says Rick. In this process transition, new installations such as a Direct Reduced Iron (DRI) plant linked to an Electric Arc Furnace (EAF) will initially run on gas and electricity generated from wind power. Once these processes work well, the second stage will be moving to hydrogen. Iv has unique experience in DRI production in the form of HBI (Hot Briquetted Iron) and everything that goes with it. A DRI plant is in operation in Texas, for which Iv has optimised both the primary production process and the secondary process, such as screening, storage and handling.
In the context of sustainability, Iv is also engaged in the reuse of steel. Reuse, remanufacturing, and recycling will become increasingly important in the future. Following
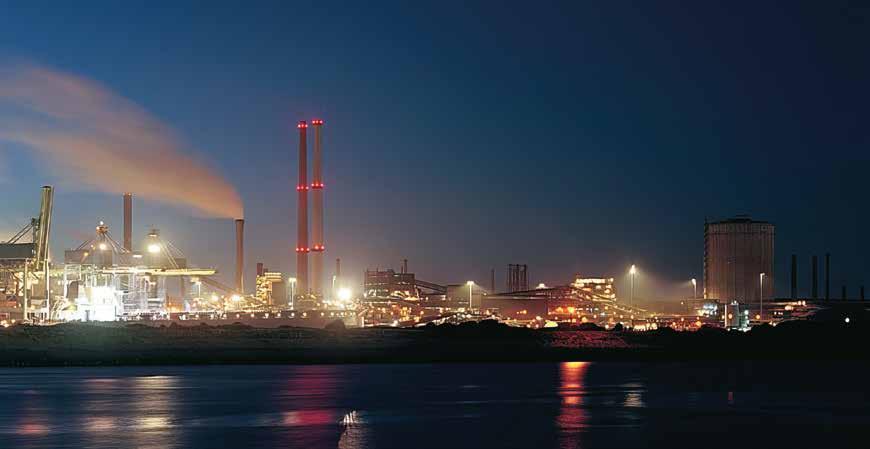
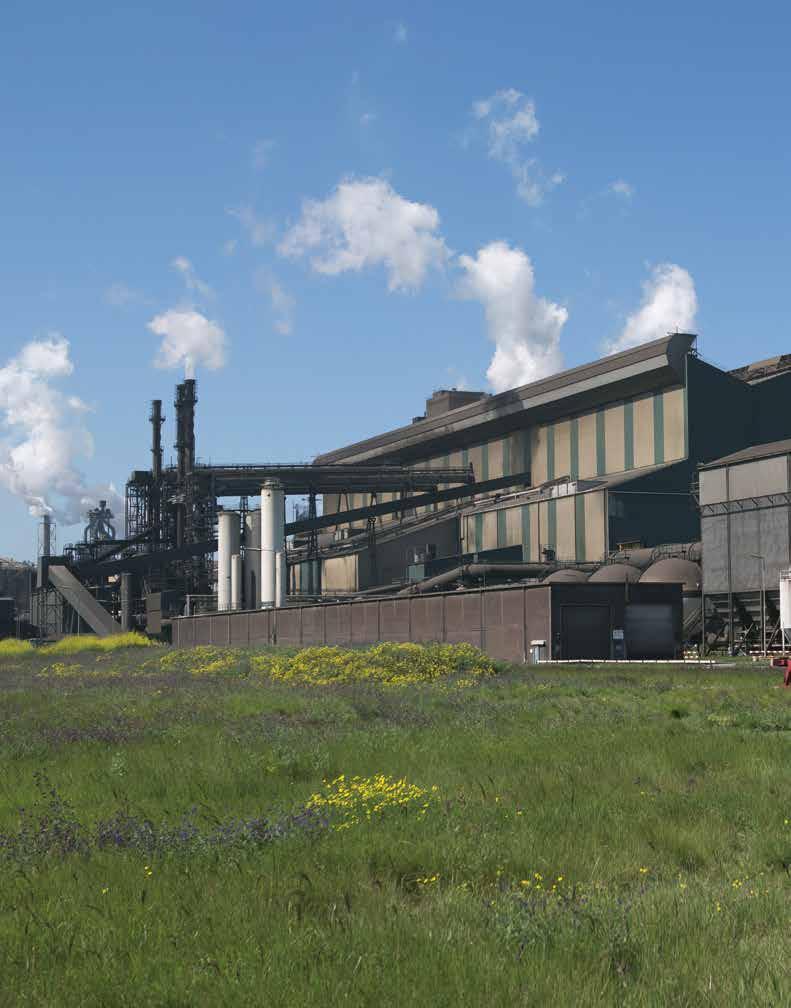
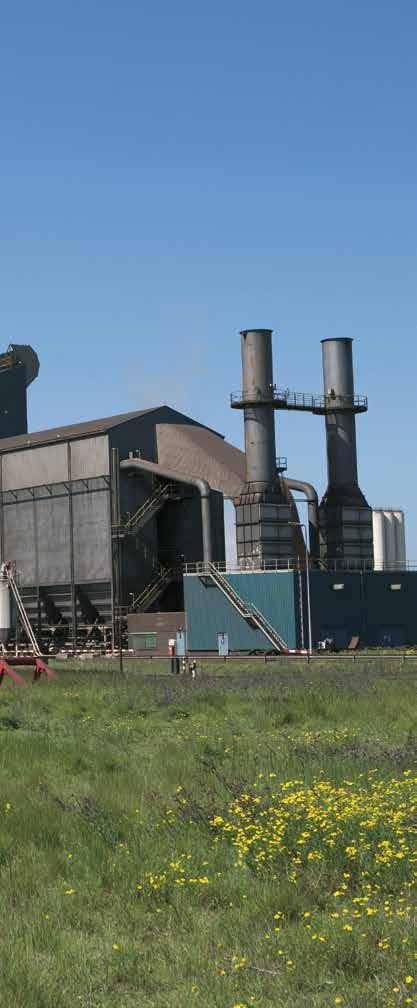
the so-called use phase of steel products, such as refrigerators, the steel is collected and prepared for reuse. This process involves the removal of zinc, paint coatings and other materials before the steel can be reprocessed. As early as 1999, Iv was already playing a pivotal role in the removal of zinc from steel that was released as a residual and waste material during the stamping of vehicle body parts in the automotive industry.
In short, whether it is about optimising production processes or improving the logistical periphery around installations and raw materials: “We help design factories so that raw materials can be delivered efficiently and without emissions, reducing the need for transport. This reduces energy consumption and pollution, which directly contributes to a cleaner world”, says Rick.
Closing factories is not the answer; we need to invest in making them more sustainable.
Future perspective
The world of materials, technologies and production methods has changed rapidly in recent years; a hundred years ago, there were no plastics, carbon fibres or 3D printable materials. What seemed impossible then is now a reality, with no end in sight. And this progress is only accelerating. Rick talks about the future possibilities: “There are already plans to source materials from other planets. Although this may seem a long way off, we could be heading in that direction in 20 to 30 years.” There are also opportunities closer to home. In Scandinavia (Sweden), for example, there are still large amounts of untapped raw materials and opportunities to continue the industry in a sustainable and green way in the future. “What I think is important is not just that we make all
these changes for ourselves or our children, but that we do it for our children’s children and beyond. If we don’t act now, we will really feel the impact of our decisions in the future. It’s not just about today or tomorrow; it’s about the world we leave behind.”
By working together in a design and construction team, we can create and deliver much bigger and smarter solutions than we could ever do alone.
While we recognise the need for sustainable change, much remains to be done. Achieving and sustaining this transition requires more than just a change of attitude. Closing factories is not the answer; we need to invest in making them more sustainable. This means implementing technical innovations, developing new materials, and daring to change existing processes. “It is essential that we put our shoulders to the wheel and invest in sustainable solutions. We have to make sure that we transform the industry into a sustainable and futureproof green industry, without losing momentum”, Rick emphasises.
Rick is optimistic about the future: “I believe that in the long term, we can even overtake our sustainability goals and make positive adjustments, but we’re not there yet. It may seem like a long way off, but I am convinced that today’s mindset, that we need to change, will act like a flywheel. Goals are like dots on the horizon, pointing us in the right direction. But as we move in that direction, we need to make more and more progress.”
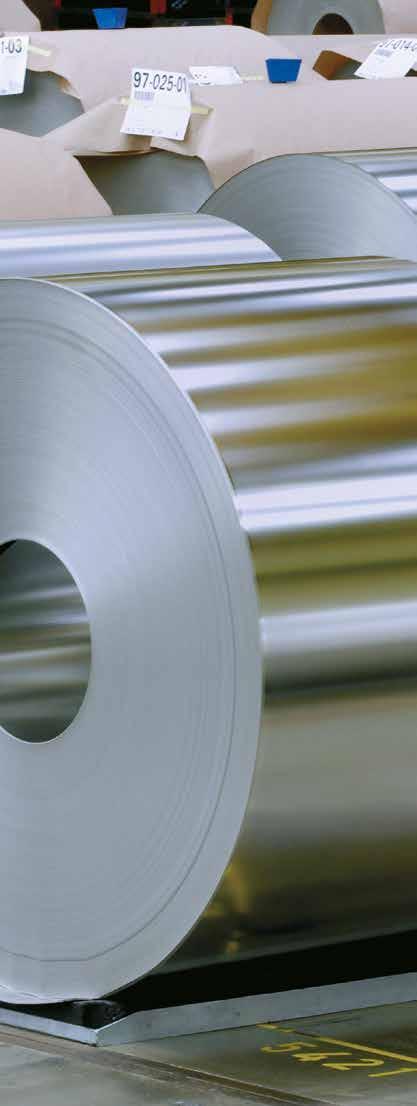
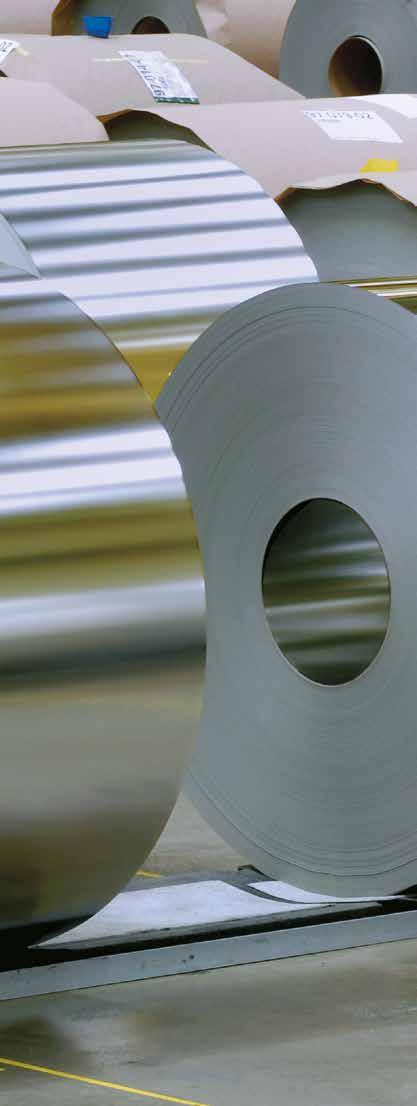
Design and construction team
Rick also emphasises the importance of collaboration: “Projects are becoming so large and complex that they can no longer be tackled by one company alone, including Iv. That is why I believe in strong cooperation between companies. Together, we can meet the challenges better than alone. I am a big advocate of working in a design and construction team. This is essential to tackle both major challenges and highrisk projects effectively. At Iv, we do the initial work, the design, but after that, manufacturing, installation, operation, and maintenance come into play. These are all critical phases that need to be represented and for which design criteria need to be properly defined and considered. By working together in a design and construction team, we can create and deliver much bigger and smarter solutions than we could ever do alone. Together, we ensure that everything we develop really does come to life.” ●
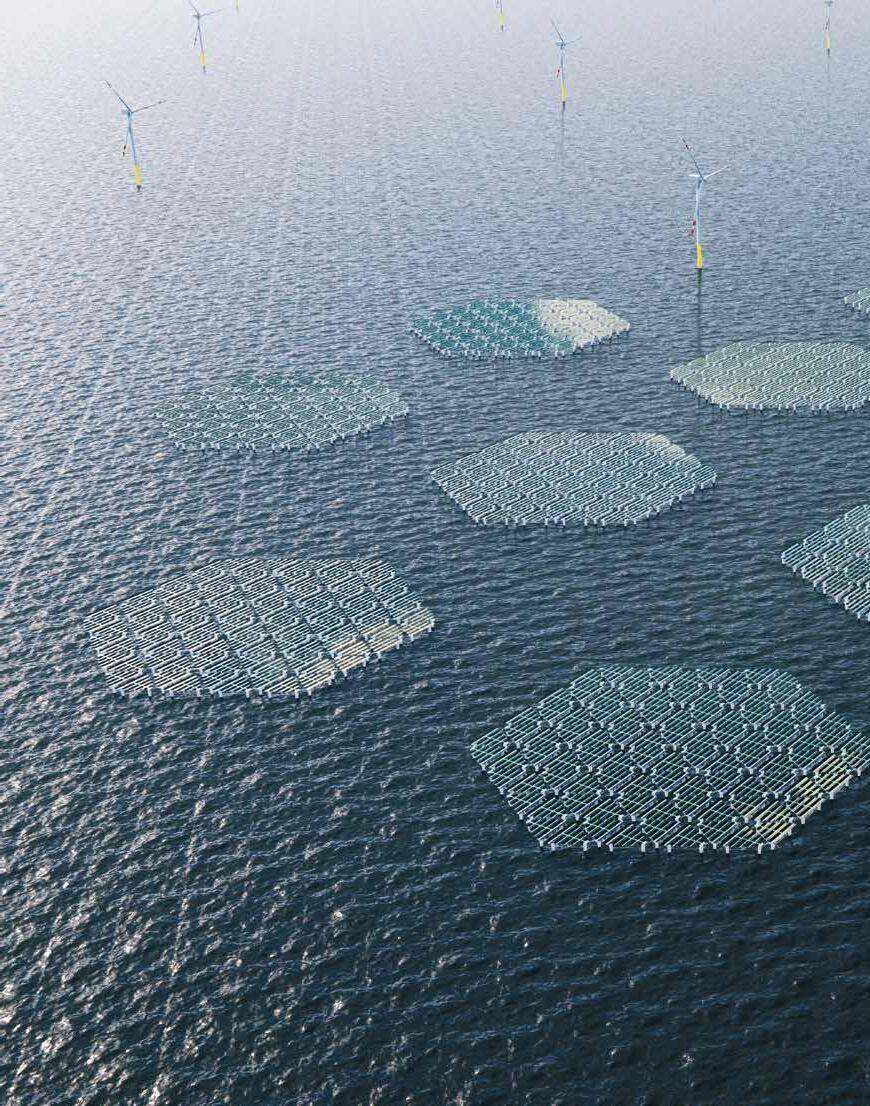
We are Iv. We are Engineers. Engineers dedicated to solving the most complex issues. The greatest challenges of our time. Our specialists devise solutions for the energy transition, the effects of climate change and to ensure a safe and resilient society. We design offshore wind platforms, submarines, and the world’s largest lock complexes. Essentially, we design anything that requires a high level of technical expertise and multidisciplinary knowledge. The diversity of our work is unmatched by any other engineering company, and we deliver results that genuinely benefit society. This is what we call: Engineering that excites.