Ivormatie magazine
Exciting engineering
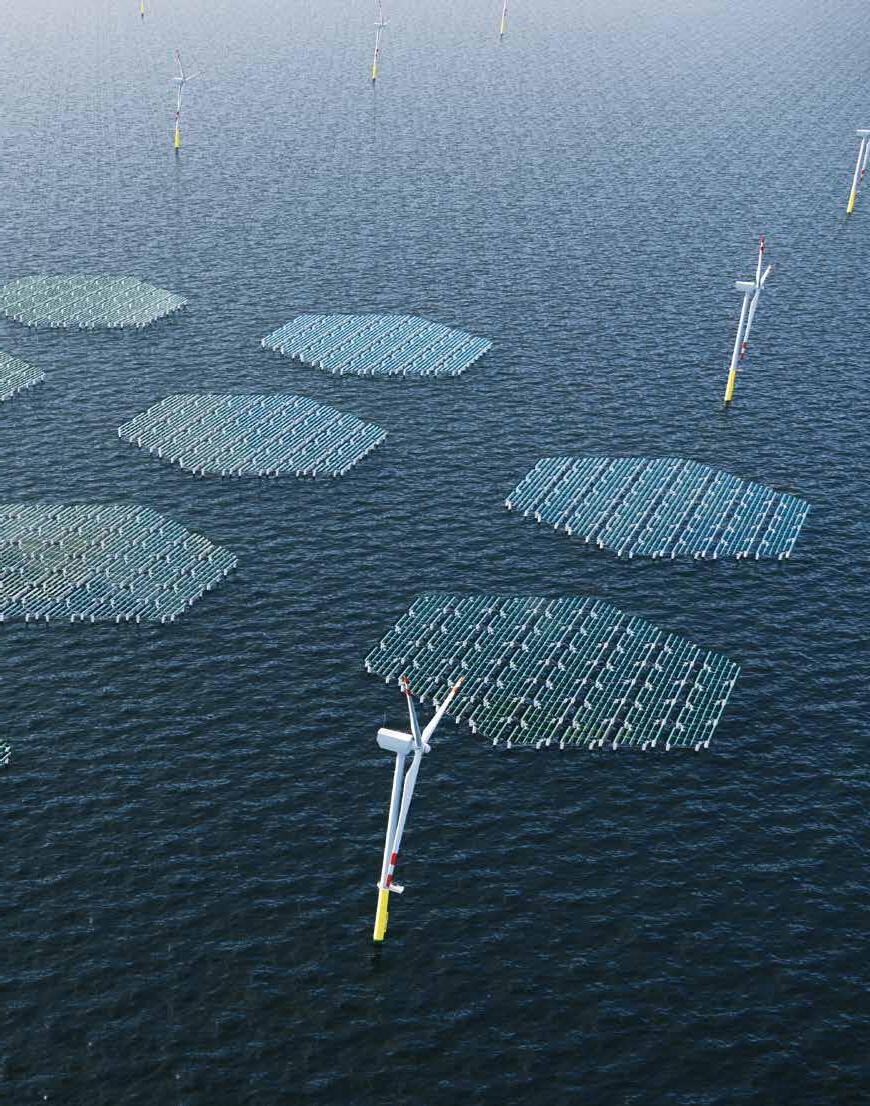
Engineering that excites
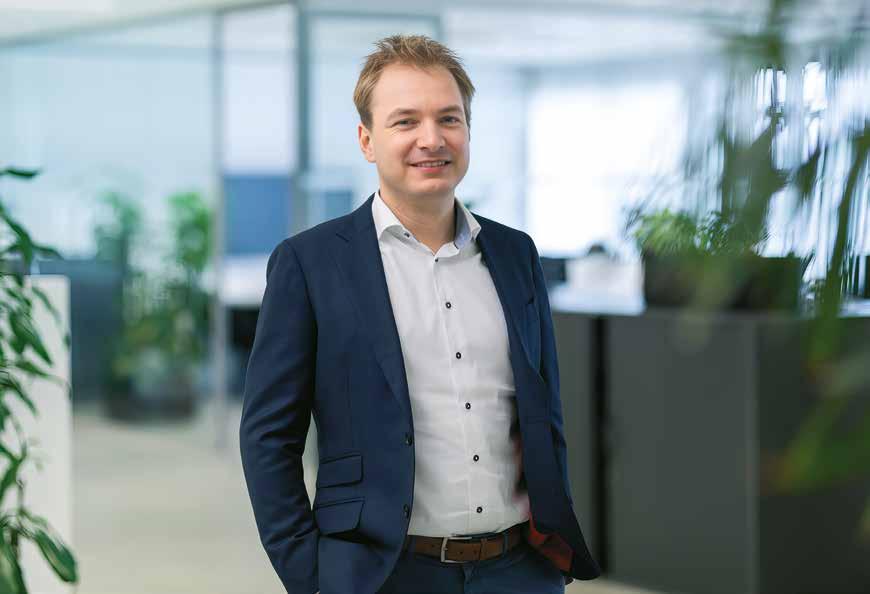
We worden gevraagd om oplossingen te bedenken waar de maatschappij écht iets aan heeft.
Deze maand bestaat Iv precies 75 jaar. Een bijzondere mijlpaal, waarbij we uiteraard uitgebreid en met trots terugkijken op wat we in driekwart eeuw hebben bereikt en gedaan.
We hebben héél veel bijzonders om op terug te kijken. Maar gelukkig draait een jubileum niet alleen om het verleden. Het geeft ons de gelegenheid om stil te staan bij waar we nu mee bezig zijn en wat ons nog te wachten staat. En dat is veel! Met inmiddels meer dan 1300 collega’s werken we aan prachtige projecten die ons uitdagen. We worden gevraagd om oplossingen te bedenken waar de maatschappij écht iets aan heeft. In onze ogen is dat precies wie we willen zijn en wat we willen doen: werken aan uitdagende projecten waar we onze technische kennis optimaal in kwijt kunnen. Kortom: engineering that excites!
Dat zorgt ervoor dat we ons – nu de vakanties ten einde zijn – vol nieuwe energie op bijzondere projecten blijven storten. Bijvoorbeeld voor drinkwaterbedrijf Dunea, waar we helpen met de zoektocht naar een nieuwe drinkwaterbron. Een uniek project. Voor PALLAS in Petten zijn we bezig met het ontwerp van een nieuwe medische isotopenreactor, waardoor dagelijks duizenden kankerpatiënten geholpen en behandeld kunnen worden. Of neem onze impact binnen de energietransitie: Iv heeft meer dan een kwart van alle bestaande offshore platformen binnen de Europese Unie ontworpen.
Daarmee dragen we dus een flinke steen bij aan de energietransitie. Dit en nog veel meer lees je in deze Ivormatie.
Ons 75-jarig bestaan is gelijk een mooi moment om ons magazine in een nieuwe jas te steken. In een nieuwe huisstijl, met onze nieuwe pay-off: engineering that excites. En dat we de passie voor techniek allesbehalve verloren zijn, blijkt wel uit alle mooie, uitdagende projecten waar we mee bezig zijn. We streven ernaar om dingen te doen waar we trots op kunnen zijn. In deze tijd zijn er meer dan genoeg uitdagingen waar we onze stempel op kunnen drukken en de wereld een stukje beter kunnen maken. Of het nu gaat om duurzaamheid, klimaatverandering of veiligheid. Ik heb dan ook het volste vertrouwen dat we de komende jaren onze honger naar mooie projecten kunnen stillen.
Ik wens je veel leesplezier.
Maarten van de Waal CEO
De geschiedenis van 75 jaar Iv
Henk Veth richt vanaf zijn zolderkamertje in Rotterdam Ingenieurs- en Architectenbureau H. Veth op. De Koninklijke Hoogovens zijn vanaf de oprichting de belangrijkste klant van Henk Veth. Zo is de oxystaalfabriek op het terrein in IJmuiden door Iv ontworpen.
Ingenieurs- en Architectenbureau H. Veth bestaat 20 jaar. Dat jubileum wordt groots gevierd. Het ingenieursbureau groeide gestaag. Van een paar man tijdens de oprichting tot rond de twintig richting de jaren ’70. Nog altijd met de Hoogovens als grootste opdrachtgever.
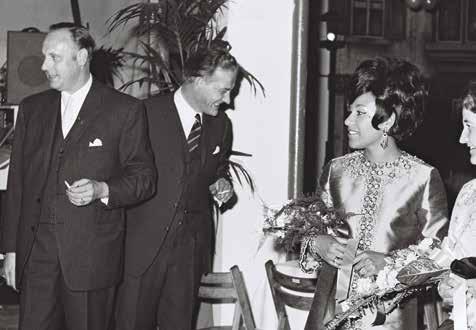
Henk Veth draagt zijn bedrijf over aan Henk de Kok, die directeur-eigenaar wordt. Aan de naam Ingenieurs- en Architectenbureau H. Veth komt eveneens een einde. Vanaf dit moment gaat het ingenieursbureau – inmiddels gevestigd in Dordrecht – verder als Ingenieursbureau H. Veth BV.
Iv neemt de tekenkamer van Grootint over. De bruggen- en sluizenbouwer stootte de tekenafdeling af en gaf veel van het tekenwerk aan Iv. Het betekende een eerste echte groeispurt voor Iv, met grote projecten tot gevolg, waaronder de sluisdeuren in IJmuiden. Inderdaad, de voorgangers van de huidige Zeesluis IJmuiden: de grootste zeesluis ter wereld.
Een echte Iv-traditie begint hier. Een grote groep Iv’ers bezoekt het EK in Duitsland, waar het Nederlands elftal voor de eerste – en tot nu toe laatste – keer Europees kampioen wordt. Tientallen Iv’ers zien het live gebeuren.
Rob van de Waal neemt het stokje over van Henk de Kok, die verder gaat als commissaris van Iv, maar het eigenaar- en directeurschap aan Rob overdraagt. Rob heeft als doel van Iv een multidisciplinair ingenieursbureau te maken, met de focus op verschillende markten.
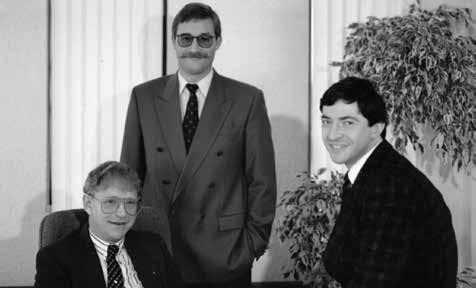
De eerste divisie van Iv is een feit: Iv-Infra wordt opgericht. Dat komt niet uit de lucht vallen. Iv zat in de tien jaar hiervoor in de combinatie Stercon, met onder andere Wagemaker, BMTR, BVN en Intersec. Dat was een lucratief raamcontract voor Iv, waarbinnen het alle ingenieursdiensten voor de bouwdienst van Rijkswaterstaat mocht doen. De kennis en expertise in de infrasector is in deze jaren verzameld.
Het laatste jaar van het millennium is een bijzondere voor Iv, met veel hoogtepunten. Wim Bal komt naar Iv en wordt directeur van de nieuwe divisie Iv-Oil & Gas, gericht op de offshore markt. De kersverse divisie scoort meteen een groot project voor Petroland. Tegelijkertijd wordt een iconische constructie in Londen geopend: het gigantische reuzenrad aan de Theems, de London Eye. 130 meter hoog en 1700 ton zwaar. Het constructief ontwerp komt van Iv-Consult.
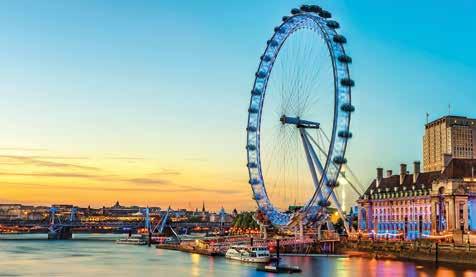
2007
Er vallen nog veel werelden te winnen net na het millennium. Rob van de Waal richt daarom Iv-Water op. Erik Vegt wordt directeur van deze nieuwe divisie. Het is tevens het jaar dat Iv overgaat op een divisiestructuur.
2008
2009
Uit de overnames van Cumae en Triple M, een jaar eerder, komt Iv-Industrie voort. Een klein deel daarvan richt zich op utiliteitsbouw, een andere tak van sport. Daarom besluit Rob van de Waal – die zijn vijftienjarige jubileum als directeur-eigenaar viert – om Iv-Bouw in het leven te roepen als nieuwe divisie. 2003 2004
Het Nederlandsche Vereenigde Scheepsbouw Bureaux, beter bekend als Nevesbu, maakt een doorstart en wordt overgenomen door Iv. Ook Damen wordt voor 50 procent eigenaar. Nevesbu is het meest toonaangevende maritieme ingenieursbureau van Nederland, gevestigd in Alblasserdam, met grote projecten in binnen- en buitenland. Het ontwerp van de Walrusklasse onderzeeboten voor Defensie is misschien wel het bekendste project.
Vanaf dit jaar gaat het snel met de overnames door Iv. Te beginnen met Escher Process Modules. Escher, opgericht in 1925, is gespecialiseerd in procestechnologie. Escher richt zich de laatste jaren op het ontwerp van crystallizers en rondde onlangs een imposant project in China af.
Cumae, met vestigingen in Arnhem en Capelle aan den IJssel, en Triple M uit Haarlem worden overgenomen. Samen vormen deze twee bedrijven de nieuwe divisie Iv-Industrie. Daarmee breidt Iv ook flink uit qua vestigingen, met Arnhem en Haarlem als nieuwe locaties. Het is tevens het jaar dat Iv op voetbalreis gaat naar het EK in Zwitserland en Oostenrijk.
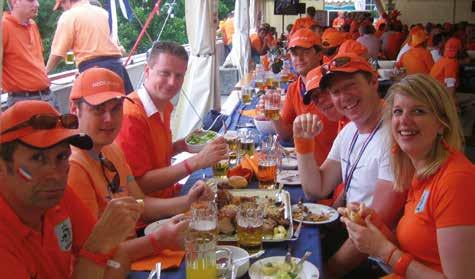
Wie erbij was, houdt er niet over op: de 9-daagse reis naar Zuid-Afrika, waar Oranje de finale haalt van het WK. Gek genoeg is het voetbal bijzaak op deze bijzondere reis. Slapen onder een fonkelende sterrenhemel, een kampvuur tussen de olifanten en vanzelfsprekend met honderden collega’s op safari. De Iv-trip naar Zuid-Afrika is onvergetelijk.
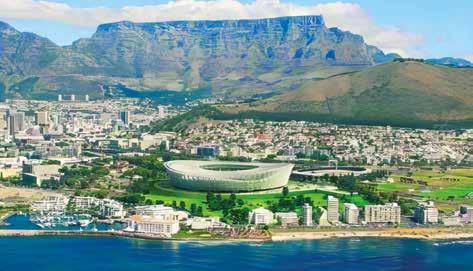
Iv staat dit jaar voor de eerste keer in de top 10 ingenieursbureaus van Nederland. Robs wens is daarmee in vervulling gegaan. Sindsdien heeft Iv de top 10 niet meer verlaten. 2012 is ook het jaar dat er weer een memorabele voetbalreis wordt georganiseerd: Iv volgt het Nederlands elftal naar Oekraïne.
Zonder twijfel het project dat Iv een enorme boost geeft in aanzien en naamsbekendheid. De landelijke media willen er alles van weten: één van de belangrijkste sluizencomplexen ter wereld heeft een Nederlandse inbreng. Iv ontwerpt de sluisdeuren van het Panamakanaal. Het project neemt een hoop jaren in beslag, maar in 2016 wordt het gloednieuwe sluizencomplex geopend.
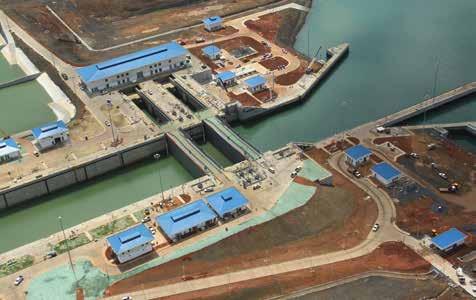
2017
Hollands Glorie voor Iv-Offshore & Energy (opgericht als Iv-Oil & Gas), dat de offshore windplatformen Borssele Alpha en Beta mag ontwerpen. Groots, want deze platformen zijn samen goed voor ongeveer 1,4 gigawatt aan groene energie voor Nederlandse bodem. Genoeg om bijna anderhalf miljoen huishoudens jaarlijks van stroom te voorzien.
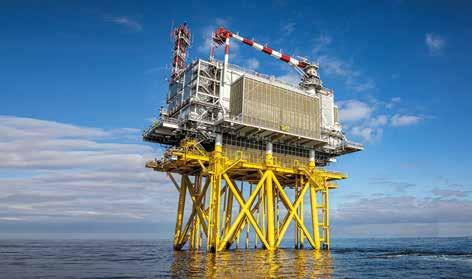
2018
In dit jaar nam Iv het ingenieursbureau van Dura Vermeer over: Advin. Met de overname kreeg Iv er zo’n 55 collega’s bij. Ook ontstond daarmee de nieuwe vestiging in Den Bosch. Verder had Advin een kantoor in Hoofddorp. Die collega’s verhuisden – samen met de collega’s van Iv-Infra Amsterdam –naar Haarlem, waar nu Iv-Industrie en Iv-Infra huizen. 2018 was het ook het jaar van het WK in Rusland. Ondanks dat Oranje niet meedeed aan het toernooi, trok een grote groep Iv’ers naar het prachtige SintPetersburg voor een onvergetelijke voetbalreis.
2019
Een nieuwe overname: Iv neemt CAE uit Delft over. CAE voegt zich bij het bestaande Iv-Bouw en behoudt de vestiging in Delft. De samenvoeging betekent meer mensen, maar ook meer verschillende opdrachtgevers. Zo is Diergaarde Blijdorp een trouwe klant. Vanaf 2022 gaan CAE en Iv-Bouw samen verder onder de naam Iv-Bouw.
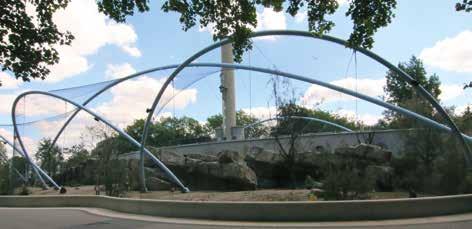
Wisseling van de wacht: Maarten van de Waal wordt de nieuwe algemeen directeur van Iv. Rob blijft voorlopig nog wel aan, maar meer op de achtergrond. De vernieuwde directie wordt, naast Maarten, gevormd door CFO Ewout Borg en COO’s Fedor van Veen en Wouter van der Wiel. 2022 is ook het jaar dat Iv voor één keer ‘breekt’ met de voetbaltraditie en kiest voor een trip naar het Italiaanse Monza om Max Verstappen aan te moedigen.
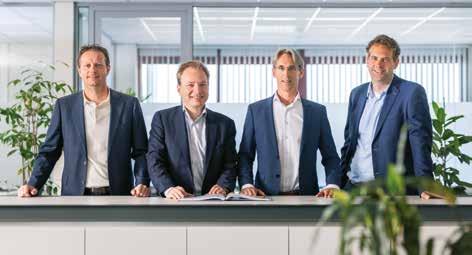
Een gigantische mijlpaal in de energietransitie. In navolging van Borssele, maar ook projecten van allure als Thor, Ostwind/Gennaker en Sofia, start een baanbrekend project voor de eigen Noordzee: het ontwerp van de eerste 2GW-platformen ter wereld voor TenneT. Niet eerder werden platformen met zoveel vermogen gerealiseerd. In ditzelfde jaar neemt Iv het Poolse Electro Croon Polska (ECP) over, bestaande uit meer dan vijftig medewerkers. Daarmee breidt Iv uit met drie nieuwe vestigingen in Polen en vooral veel kennis en deskundigheid.
Iv bestaat 75 jaar! Een mijlpaal waar we ontzettend trots op zijn en uitgebreid bij stil staan. Ondertussen is Iv gegroeid naar bijna 1.200 medewerkers. Na precies 30 jaar neemt Rob van de Waal afscheid als directeur van het bedrijf waar hij in 1979 bij in dienst kwam op de computerkamer van Henk Veth. Het is ook het moment dat alle divisies onder één naam naar buiten treden: Iv!

38e jaargang, nummer 1, september 2024
Redactie
Iv, Afdeling Corporate Development & Marketing
Ivormatie
Een uitgave van Iv
Redactieadres
Iv Postbus 1155 3350 CD Papendrecht
Nederland marketing@iv.nl www.iv.nl
Afmelden
Wil je de Ivormatie liever digitaal ontvangen? Of wil je je uitschrijven? Geef het door via marketing@iv.nl.
Copyright © 2024 Iv. Voor het geheel of gedeeltelijk overnemen of bewerken van artikelen is toestemming van de redactie vereist.
Inhoudsopgave
12 Ruim kwart van de offshore windplatformen in de EU heeft Nederlands ontwerp
18 De zoektocht naar een nieuwe drinkwaterbron
24 Eindhoven Airport breidt terminal uit voor optimale reizigerservaring
30 Een volgende stap in drijvende windenergie
36 Heeft groene waterstof de toekomst?
40 Renovatie, versterking en uitbreiding van de Schipholbrug A9
46 De nieuwe PALLAS-reactor helpt nóg meer patiënten bij behandeling van kanker
52 Grip op onzekerheden houdt de V&R-opgave behapbaar
56 De realisatie van ’s werelds grootste drijvende solarplatform
60 Verduurzamen van de zware industrie
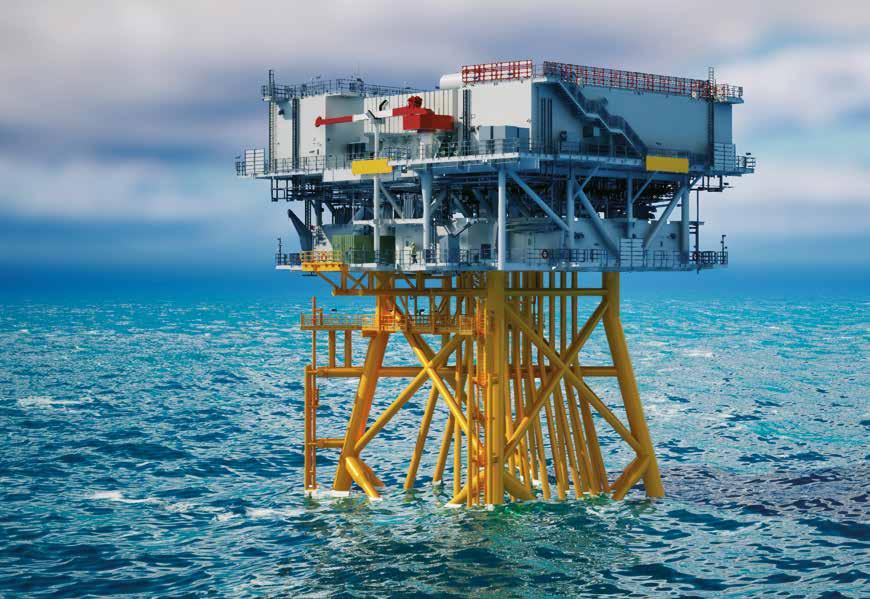
Ruim kwart van de offshore windplatformen in de EU heeft
Nederlands ontwerp
De energietransitie zit in een stroomversnelling. Met name op zee (offshore) nemen de groei en het tempo waarmee windparken en platformen worden gerealiseerd flink toe. Het ontwerpen van deze transformatorplatformen, die ervoor zorgen dat windenergie daadwerkelijk aan land kan komen, is een complexe klus. Iv is verantwoordelijk voor het ontwerp van ruim een kwart van de momenteel geïnstalleerde platformen om windenergie op zee in de Europese Unie aan te sluiten, gebaseerd op een rapport van WindEurope. En zelfs een veelvoud daarvan is momenteel in ontwikkeling.
In 2023 wordt er op zee zo’n 19 gigawatt (GW) offshore windenergie geproduceerd in Europa. Dat is jaarlijks genoeg om bijna 20 miljoen huishoudens van energie te voorzien. Op land is het aandeel groene energie nog een stuk groter: 201 GW. Maar offshore windenergie wint aan terrein. En de komende decennia is de ambitie van de Europese Unie en ook van Nederland nog groter.
Van de 19 GW aangesloten windenergie op zee, is Iv verantwoordelijk voor meer dan een kwart: zo’n 5 GW. Denk onder andere aan de twee platformen Borssele Alpha en Beta (1,4 GW), Dolwin Alpha (800 MW) en Helwin Beta (680 MW). Binnen Nederland is Iv het enige ingenieursbureau met zoveel specialistische ervaring en expertise. Nederland heeft de ambitie om in 2050 liefst 70 GW aan offshore windenergie op te wekken. Eind 2023 staat de teller op 4,7 GW. In 2030 moet dit gegroeid zijn naar 21 GW.
De ambities van Europa,
Nederland en ook van Iv zijn groot en er wordt meer en meer bereikt.
Grootste platformen ter wereld
Het is duidelijk dat daar veel voor moet gebeuren, maar de stappen die momenteel worden gezet, zijn groot. Zo ontwerpt Iv momenteel twee platformen voor TenneT in de Noordzee: IJmuiden Ver Beta en IJmuiden Ver Gamma. Het zijn op dit moment de grootste conventerplatformen ter wereld met elk een vermogen van 2 GW. Behalve de platformen in het windenergiegebied IJmuiden Ver, gaat Iv ook het ontwerp voorzien voor één van de Nederwiek platformen.
Verder werkt Iv aan drie platformen in de Duitse
Oostzee (Ostwind 3 en Gennaker East en West), Thor in Denemarken en ook buiten de Europese Unie is Iv actief. Zo maakte Iv het ontwerp van het Sofia platform dat dit jaar is geïnstalleerd op de Doggersbank voor de kust van het Verenigd Koninkrijk. Deze platformen zijn samen goed voor ruim 2 GW aan offshore windenergie.
Nederland is koploper in 2023 als het gaat om geïnstalleerd vermogen op zee: ruim 1,9 GW.
Recordjaar
De ambities van Europa, Nederland en ook van Iv zijn groot en er wordt meer en meer bereikt. Nederland is koploper in 2023 als het gaat om geïnstalleerd vermogen op zee: ruim 1,9 GW. Dat is meer dan Duitsland, Frankrijk, het Verenigd Koninkrijk en Denemarken bij elkaar.
Buiten de Nederlandse wateren gebeurt ook iets bijzonders; zo’n veertig kilometer voor de kust van het Belgische Oostende ontstaat een wereldprimeur. Voor de Belgische netbeeherder Elia wordt door Iv, HSM en Smulders gewerkt aan het ontwerp, de constructie en installatie van het Prinses Elisabeth Eiland. Dat wordt het allereerste energie-eiland van de wereld. Iv ontwerpt hiervoor vier AC modules (wisselstroom) met een totaal vermogen van liefst 3,4 gigawatt. Iets wat nooit eerder is gerealiseerd.
Het Prinses Elisabeth Eiland – de naam zegt het al –is anders dan al het andere wat in het verleden en momenteel wordt gerealiseerd. Geen platform met een jacket, maar een eiland, waarvan de constructie al is
begonnen in het Zeeuwse Vlissingen. De buitenomtrek van het eiland bestaat uit een reeks betonconstructies (caissons) die in een ring op de zeebodem worden geplaatst. Binnenin wordt het eiland opgevuld met zand.
WindEurope en de cijfers
WindEurope is de stem van de windindustrie, actief in het bevorderen van windenergie in Europa en wereldwijd. Het heeft meer dan 500 leden met (hoofd) kantoren in 35 landen. Onder de leden bevinden zich toonaangevende fabrikanten van windturbines, leveranciers, onderzoeksinstituten, landelijke organisaties, ontwikkelaars, aannemers, elektriciteitsleveranciers, financiële instellingen, verzekeringsmaatschappijen en adviseurs. Daarmee is WindEurope het grootste windenergienetwerk van Europa.
Europa wil tussen 2024 en 2030 liefst 260 gigawatt aan nieuwe windenergie installeren,
zowel on- als offshore.
Het rapport van WindEurope laat een uitgebreide analyse zien van wat er on- en offshore aan windenergie is gerealiseerd in 2023 en geeft een inkijkje in de prognoses en ambities van windenergie in Europa en de Europese Unie. In het rapport valt wel een kanttekening te lezen. Hoewel veel cijfers groei laten zien – waaronder ook in Nederland – zijn er twijfels over het halen van de doelen binnen de Europese Unie. Wel ziet de organisatie dat het toekomstbeeld, mede door enkele uitschieters in de ontwikkeling van on- en offshore windenergie, ten opzichte van 2022 er wel positiever uitziet, met Nederland als één van Europa’s koplopers in de offshore energietransitie.
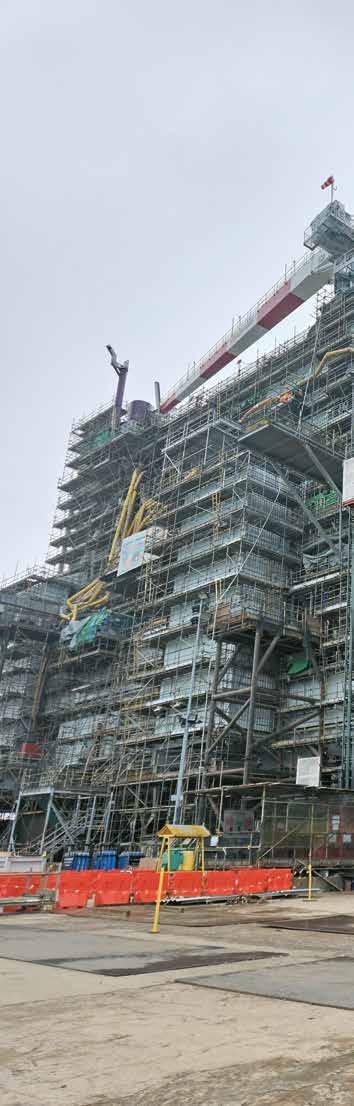
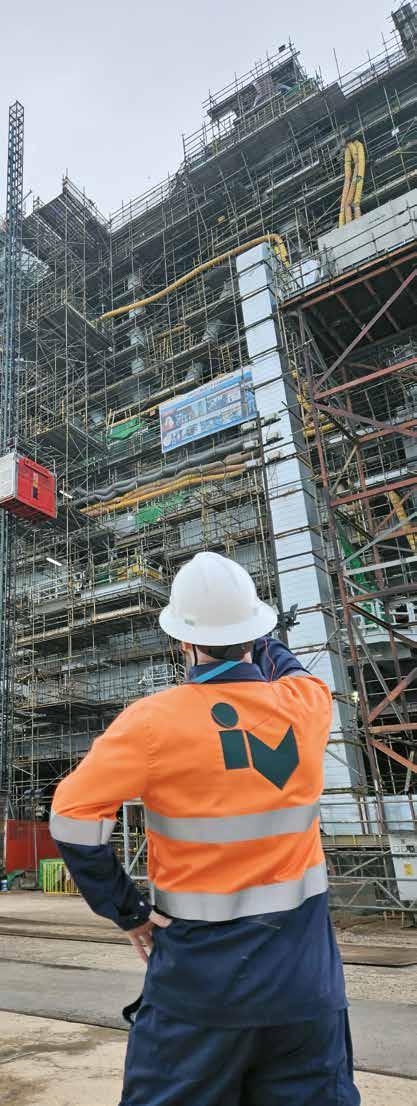
1.906 MW
Volgens het rapport van WindEurope is te zien dat Nederland tot de top van Europa behoort als het gaat om geïnstalleerde windenergie in 2023. In totaal is er bijna 2,5 GW (goed voor het jaarlijks verbruik van meer dan 2 miljoen huishoudens) aan windenergie bijgekomen vorig jaar. Het overgrote deel – 1.906 megawatt – is offshore gebouwd. Daarmee gaat Nederland tegen de trend in, want bijna tachtig procent van al het geïnstalleerd vermogen in heel Europa wordt juist op land gebouwd. Geen land in Europa heeft er in 2023 meer offshore windenergie bijgekregen dan Nederland.
19% windenergie
Van de totale energiebehoefte in de Europese Unie, wordt 19 procent opgewekt door windenergie, dat is een stijging ten opzichte van voorgaande jaren. Denemarken (56%), Ierland (36%) en Duitsland (31%) zijn koplopers op dat gebied. Nederland staat op plek 4 in de EU; hier wordt 27% van de energievraag door windenergie opgewekt.
2030
Het jaar 2030 is een belangrijk jaartal. Europa wil tussen 2024 en 2030 liefst 260 gigawatt aan nieuwe windenergie installeren, zowel on- als offshore. WindEurope verwacht dat de Europese Unie (dus Europa minus een aantal niet-EU-landen) 200 GW voor zijn rekening neemt. Dit komt neer op ongeveer 29 GW per jaar.
Nederland offshore
Met de grootste transformatorplatformen in zijn soort – de 2GW-platformen van TenneT – voor de eigen kust, is het geen verrassing dat Nederland binnen de Europese Unie de meeste windenergie op zee gaat produceren. De Rijksoverheid zet 4,6 gigawatt aan windcapaciteit in de veiling voor de windparken IJmuiden Ver Alpha en Beta. Daar bovenop komt nog eens 11 gigawatt aan geplande capaciteit. Daarmee komt Nederland heel dicht bij het doel van 15,8 GW aan offshore capaciteit in 2030. ●
Door Iv ontworpen offshore windplatformen wereldwijd
SEAGREEN 1,500 MW
UNITED STATES CANADA
EMPIRE WIND
800 + 1,200 MW
VINEYARD WIND
800 MW

BERWICK BANK 1,150 MW
NEART NA GAOITHE 2 X 225 MW

SOFIA 1,320 MW
SOUTH COAST 1,300 MW
MARWIN 420 MW
ATLANTIC OCEAN
IRELAND
UNITED KINGDOM

IJMUIDEN VER BÉTA 2,000 MW




POSHYDON 1,250 MW
NSE HYDROGEN 500 MW
GREATER GABBARD 2 X 252 MW
PRINCESS ELISABETH ISLAND 3,400 MW


HORNS REV B
MW
NORTH SEA




DENMARK
HORNS REV A 160 MW
BORKUM RIFFGRUND 2 450 MW
BORWIN ALPHA

OSTWIND 3 300 MW

MW
MW HELWIN BETA
IJMUIDEN VER GAMMA 2,000 MW

DOLWIN ALPHA
MW
NETHERLANDS


BORSSELE ALPHA + BETA
2 X 700 MW
THORNTON BANK
325 MW
BELGIUM

GERMANY
GENNAKER EAST + WEST 460 MW
HVAC
• THOR
• GENNAKER EAST + WEST
• OSTWIND 3
• NEART NA GAOITHE
• PRINCESS ELISABETH ISLAND
• BORSSELE ALPHA + BETA
• BORKUM RIFFGRUND 2
• GREATER GABBARD
• THORNTON BANK
• HORNS REV A
• HORNS REV B
HVAC STUDY
• BERWICK BANK
• EMPIRE WIND
• MARWIN
• SEAGREEN
• VINEYARD WIND
HVDC
• SOFIA
• DOLWIN ALPHA
• HELWIN BETA
• BORWIN ALPHA
• IJMUIDEN VER BÉTA
• IJMUIDEN VER GAMMA
HVDC STUDY
• IJMUIDEN VER
• SOUTH COAST
HYDROGEN
• POSHYDON (PILOT)
• NSE HYDROGEN (PILOT)
De zoektocht naar een nieuwe
drinkwaterbron
Drinkwaterbedrijf Dunea staat voor een grote opgave. Het bedrijf levert vanuit de duinen tussen Monster en Katwijk schoon drinkwater voor 1,3 miljoen gebruikers in het westen en zuiden van Zuid-Holland, maar door de toenemende vraag is dat niet meer genoeg. Er moet meer drinkwater worden geproduceerd. Omdat dit niet kan met bestaande methoden en locaties, zijn Iv en Arcadis ingeschakeld om – voor het eerst in ruim vijftig jaar – een nieuwe bron te vinden die vanaf 2030 schoon drinkwater levert.
Dunea maakt voor het winnen van drinkwater gebruik van het rivier-duinsysteem. Water uit rivieren de Lek en de Afgedamde Maas wordt richting de duinen gepompt en daar opgewerkt tot drinkwater. Jarenlang was dat voldoende, maar nu kijkt Dunea tegen de grenzen van de capaciteiten aan.
We ondersteunen Dunea bij het maken van de juiste keuze.
Om die reden heeft het drinkwaterbedrijf het programma ‘Drinkwater voor de Toekomst’ in het leven geroepen. Dat plan bestaat uit 5 pijlers, waaronder het stimuleren van bewust en duurzaam watergebruik en het optimaal benutten en onderhouden van het huidige rivierduinsysteem. Een cruciale pijler is het toevoegen van een nieuw systeem van bronnen en zuiveringen. Daar komen Iv en Arcadis in beeld. Het is onze taak om voor Dunea drie varianten uit te werken, advies te geven en een voorlopig ontwerp aan te bieden. Iv richt zich daarbij op het ontwerp zelf vanuit de techniek, Arcadis voert onder andere milieueffectrapportages (MER) uit en houdt zich bezig met vergunningen.
Kern van de zoektocht
Willemijn Bouland-Oosterwijk is programmamanager Drinkwater voor de Toekomst bij Dunea. “We proberen nu het rivier-duinsysteem verder uit te nutten en in stand te houden, maar zelfs dan hebben we in 2030 nog niet voldoende capaciteit. Daarom zijn we bezig om daarnaast nieuwe aanvullende bronnen te vinden: lokaal oppervlaktewater, rivierwater, zeewater of brak grondwater. Dat is de kern van deze zoektocht.”
Voor Dunea is de opgave groot en uitdagend. Waar het drinkwaterbedrijf nu 1,3 miljoen gebruikers voorziet van schoon drinkwater, is dat straks nodig voor 1,6 miljoen gebruikers. Dat komt neer op een groei van 15 miljard liter drinkwater: van 85 naar 100 miljard liter per jaar. “Samen met Iv en Arcadis kijken we op hoog abstractieniveau naar bronnen en zuiveringstechnieken en proberen we nog dit jaar een keuze te maken voor een voorkeursalternatief. Daarbij spelen ook veel omgevingsfactoren mee”, vertelt Willemijn. “Want het water is niet van ons, de ruimte ook niet. In elk alternatief hebben we te maken met verschillende partijen en belanghebbenden.”
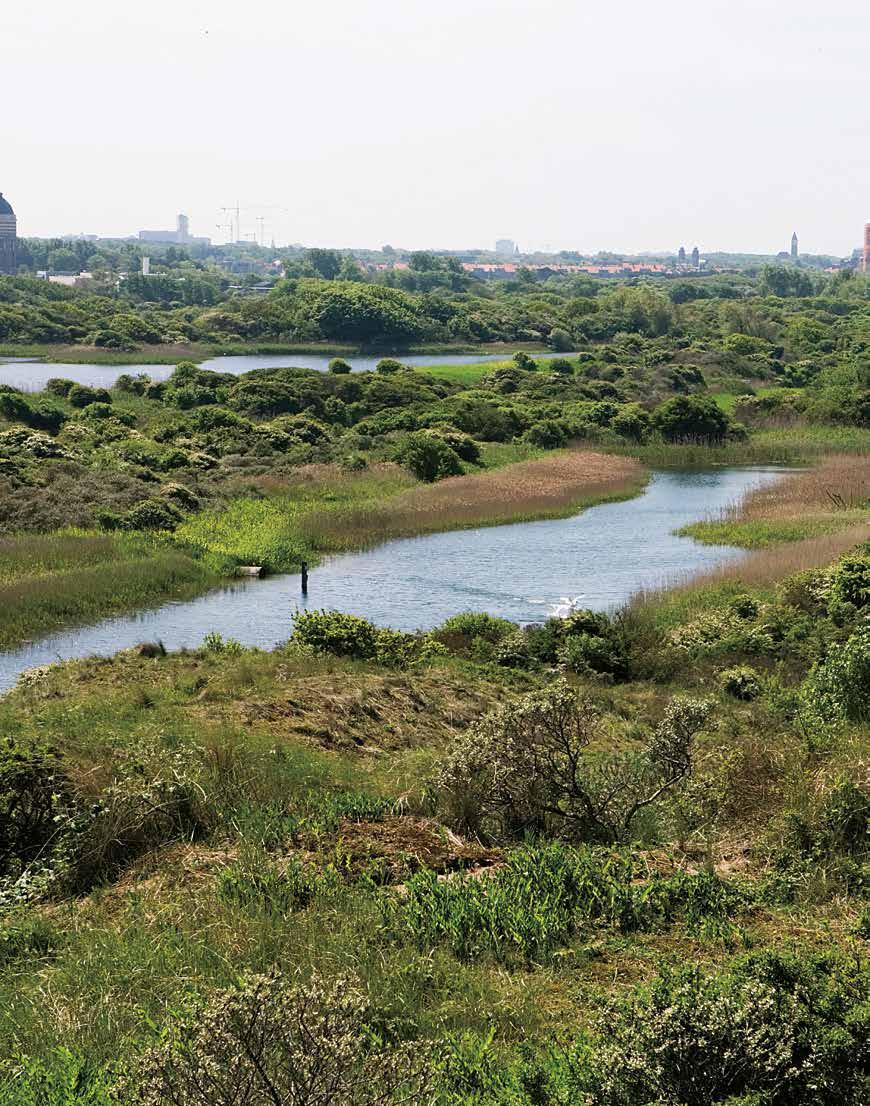
Dat komt neer op een groei van 15 miljard liter drinkwater per jaar.
Voor Dunea is dit een uniek project, want in de afgelopen vijftig jaar is er niet meer gezocht naar een nieuwe waterbron. Het geeft dus ook aan hoe belangrijk en urgent deze zoektocht is. Wie de kranten openslaat en de journaals kijkt, leest en ziet steeds vaker sombere berichten over dreigende tekorten en dringende oproepen om zuinig met drinkwater om te gaan. Dat er schoon water uit de kraan komt, is inmiddels niet zo vanzelfsprekend meer.
Wordt dat zoet oppervlaktewater, rivierwater, brak grondwater of zeewater?
Kennis, capaciteit en kracht
“De druk en verantwoordelijkheid voelen wij enorm”, vervolgt Willemijn. “We agenderen dit ook, om meer bewustwording te creëren, dat is de laatste jaren wat
weggeëbd. Er is heel veel werk aan de winkel en we hebben echt de hulp nodig van andere partijen, zoals Iv en Arcadis, qua kennis, qua capaciteit en kracht. Maar ook van overheden en maatschappelijke partijen om water en ruimte vrij te maken.”
Maar hoe komt het dat we steeds vaker lezen dat er een drinkwatertekort dreigt en dat het nog maar de vraag is of toekomstige nieuwbouwwijken wel op het drinkwaternet kunnen worden aangesloten? Bevolkingsgroei en dus meer woningen zijn de voornaamste reden voor de groeiende vraag. “Maar daarnaast zien we een stop in de dalende trend van waterverbruik per persoon. De laatste decennia hebben we ongemerkt water bespaard door zuinigere apparaten (wasmachines, vaatwassers, red.).
De focus ligt nu meer op energiebesparing, niet meer op waterbesparing. Die combinatie van factoren maakt dat de vraag sterk stijgt.”

Constante zoektocht naar raakvlakken
Deze zoektocht met de drie partijen is dus cruciaal en concreet: de keuze voor een nieuwe bron wordt hiermee bepaald. Wordt dat zoet oppervlaktewater, rivierwater, brak grondwater of zeewater? Aan het einde van dit jaar is daar een antwoord op gevonden. Zo overzichtelijk als het lijkt, is het niet, beseft Willemijn. “Het is best ingewikkeld om synergie te vinden tussen wat technisch kan, en wat vanuit vergunningen en vanuit de omgeving mogelijk en wenselijk is. Dat is een flinke puzzel, waarbij we constant zoeken naar die raakvlakken. Daar maken we dus ook fouten in.”
De hele (politieke) context waarin dit zich afspeelt, onder tijdsdruk: dat geeft veel dynamiek.
Ondanks de moeilijkheden en de druk, ervaart Dunea dit project als een bijzondere. “We doen iets met elkaar wat maatschappelijk heel relevant is, dus de ogen zijn wel op ons gericht. En uiteindelijk gaat het niet alleen om onze regio. We kijken heel erg naar hoe we elkaar als drinkwaterbedrijven kunnen helpen, dus natuurlijk zijn anderen ook nieuwsgierig naar wat hier gebeurt. En als het lukt? Dan lossen we het drinkwaterprobleem zeker tot en met 2040 op.”
Afhankelijk van elkaars kennis
Het is een project zoals ze niet vaak voorkomen. Niet alleen vanwege de bijzondere zoektocht naar een nieuwe drinkwaterbron, ook vanwege de vorm van samenwerken. “We fungeren echt als één team”, vertelt Guido van der Wedden, projectmanager bij Iv. “We zitten
twee dagen per week bij elkaar bij Dunea. Dat zijn korte lijnen. En dat is heel handig als je – zoals nu – heel erg afhankelijk bent van elkaars kennis.”
Als Guido het project moet omschrijven, komt het neer op het ontwerpen van een ‘nieuw’ drinkwaterbedrijf. Weliswaar onder de vlag van Dunea. “Maar wat we doen, is iets totaal nieuws bedenken, daar kunnen we onze hersencapaciteit wel in kwijt. Er is genoeg intellectuele uitdaging.”
Concreet houdt het project voor Iv in dat er drie procestechnologische ontwerpen worden gemaakt, voor elke variant één. Guido: “Dat betekent dat we heel goed moeten nadenken over aansluitingen, integratie van bestaande systemen. Als de keuze gemaakt is, beginnen we dit najaar aan een voorontwerp van de gekozen variant. Het leuke en unieke aan dit project is dat we samen met Arcadis al bij de voorfase betrokken zijn. We ondersteunen Dunea bij het maken van de juiste keuze.
En daar komen veel afwegingen bij kijken. Op basis van techniek, kosten, risico’s, maar bijvoorbeeld ook op het vlak van draagvlak bij de omgeving en stakeholders.”
En daar komt Arcadis ook in beeld. Frans Dotinga is als milieuadviseur verantwoordelijk voor de MER. “Wij en Iv wilden deze klus graag doen, omdat het over een heel interessant, strategisch vraagstuk gaat. De hele (politieke) context waarin dit zich afspeelt, onder tijdsdruk: dat geeft veel dynamiek.”
De kern van een milieueffectrapportage is om aan te tonen hoe de alternatieven het milieutechnisch doen en welke invloed deze hebben. Wat gebeurt er met de natuur op het moment dat er grondwater moet worden
gewonnen in een bepaald gebied? Hoeveel CO2-uitstoot en energie kosten bepaalde processen en in hoeverre wordt er voldaan aan strenger wordende kaderrichtlijnen als het gaat om de waterkwaliteit?
“Maar we kijken ook naar het doelbereik”, vervolgt Frans. “Oftewel: bereiken we het volume drinkwater en hoe zit het met leveringszekerheid bij het toepassen van de verschillende systemen? Kort gezegd is het zo dat hoe langer leidingen zijn, hoe risicovoller het is. Want de kans op schade neemt dan automatisch toe. Hoe meer processtappen, hoe complexer. Ook die aspecten moeten we meenemen.”
Dit raakt mensen direct
Arcadis is momenteel bezig met het eerste deel van de MER. Deel 2 volgt zodra het voorkeursalternatief is gekozen. “We doen dit écht met elkaar, niet naast elkaar”, vindt Frans. “Iv schrijft hoofdstukken mee in de MER en wij ondersteunen bij sommige technische vraagstukken. Die samenwerking is mooi. Op papier doen we andere dingen, maar in de praktijk zit er heel veel overlap. Samen werken we aan een heel mooie opgave. Dit raakt mensen direct. Dat is wat we het liefste doen.”
Ook Dunea zelf ziet deze studie naar een nieuwe bron als een bijzondere en impactvolle uitdaging. Willemijn: “De investeringen die we nu doen, helpen ons in de toekomst om het aan te kunnen. Iets nieuws doen kost tijd. Maar als het ons lukt, zijn we uit de problemen.” ●


Hoe langer leidingen zijn, hoe risicovoller het is.
Eindhoven Airport breidt terminal uit voor optimale reizigerservaring
Eindhoven Airport start eind dit jaar met de bouw van de uitbreiding van de terminal. De huidige terminal is te klein voor het aantal passagiers. Met de uitbreiding krijgt de terminal meer gates, wordt het non-Schengengebied verruimd, komt er een nieuwe bagagehal met ondergrondse bagagekelder en ontstaat er meer ruimte voor horeca. Kortom: meer reizigerscomfort. Het ontwerp werd gemaakt door EGM architecten, Peutz en Iv. Bouwbedrijf Heijmans gaat deze uitbreiding realiseren. In dit project speelde Iv een cruciale rol in het definitieve ontwerp, met de nadruk op duurzame oplossingen. Naar verwachting is de uitbreiding in 2027 volledig afgerond.
Duurzaamheid staat centraal
Met de uitbreiding wordt de huidige terminal aan de luchtzijde (na de security check) met circa 10.000 vierkante meter vergroot. Aan de landzijde (voor de security check) wordt de terminal met 2.000 vierkante meter uitgebreid. Hier komt ook de kenmerkende nieuwe entree. De entree heeft een voorover hellende glazen gevel en een overstek dak, waarbij de voorste rij kolommen schuin voorover hellend en buiten voor het gebouw zijn geplaatst. De dakconstructie is opgebouwd uit driehoeken die zichtbaar zijn van onderaf. Deze architectonische elementen geven de entree een dynamisch en uitnodigend uiterlijk, wat bijdraagt aan de moderne en transparante uitstraling van de terminal.
Bij deze uitbreiding staat duurzaamheid centraal, benadrukt Jeroen Stam, senior projectmanager bij Eindhoven Airport. “Eindhoven Airport neemt haar verantwoordelijkheid en richt zich op een significante reductie van emissies van CO2 en overige broeikasgassen van de luchtvaart, maar ook van onze eigen gebouwen en activiteiten. Dit betekent onder andere dat we slim
en circulair bouwen, materialen hergebruiken en gas vervangen door duurzame energiebronnen. Door gebruik te maken van de nieuwste duurzaamheidstoepassingen in het ontwerp draagt de terminaluitbreiding bij aan onze doelen om in 2030 als luchthaven emissie- en afvalvrij te zijn.”
Hemelwater wordt gebruikt voor spoeling van de toiletten.
Het ontwerp
Voor dit project was Iv verantwoordelijk voor het installatietechnische en constructieve ontwerp. Dit omvatte naast het ontwerp van het nieuwe gedeelte van de terminal ook aanpassingen aan een deel van het bestaande gebouw.
Voor het verwarmen en koelen van het gebouw wordt straks gebruikgemaakt van twee warmte-koudeopslaginstallaties. Daarnaast wordt verdringingsventilatie toegepast voor een gecontroleerde luchtstroom en optimale ventilatie in de ruimtes. Op het dak van de

terminal worden bijna 1.100 zonnepanelen geplaatst die jaarlijks ongeveer 363.500 kilowattuur energie opwekken. Een deel van het dak wordt voorzien van sedumbeplanting, wat bijdraagt aan wateropvang en isolatie van de terminal. In de kelder komt een waterbassin waar het hemelwater wordt opgevangen. Dat water wordt gebruikt voor spoeling van de toiletten in de uitbreiding.
De hoogte van 12 meter brengt ook uitdagingen met zich mee voor luchtbehandeling.
Om het gebruik van de ruimtes nauwkeurig te begrijpen, is een bezettingsonderzoek uitgevoerd. Met een diepgaande analyse zijn gegevens verzameld over het aantal passagiers, hun bewegingspatronen en de duur van hun verblijf. Op basis van deze informatie kon een gedetailleerd beeld worden geschetst van de belasting van de verschillende gebieden binnen de luchthaven. Zo werd bijvoorbeeld vastgesteld hoeveel passagiers zich op elk moment in de bagagehal bevonden, hoe
lang ze gemiddeld op hun bagage moesten wachten en hoeveel tijd ze in de terminal doorbrachten. Als resultaat kon nauwkeurig worden bepaald hoeveel ventilatielucht nodig was in elke ruimte op elk moment. Door deze aanpak kon het luchtbehandelingssysteem van de luchthaven efficiënter worden ontworpen, met aanzienlijke kostenbesparingen en energie-efficiëntie als resultaat.
Het constructieve ontwerp omvatte het plannen en ontwikkelen van de draagstructuur van het gebouw, zoals de fundering, kelder, kolommen, stabiliteitswanden en de balkenconstructie die het dak van het gebouw draagt. Hiervoor heeft Iv de dimensionering, materialisering, berekening en detaillering uitgewerkt. Tevens heeft Iv de aansluitingen op de bestaande constructie bekeken en is de stabiliteit van de constructie als geheel beschouwd ten aanzien van de van toepassing zijnde normen. Door toepassing van materialen als staal en hout zijn constructies gecreëerd die eenvoudig te demonteren zijn en kunnen worden hergebruikt aan het einde van de levensduur van het gebouw.
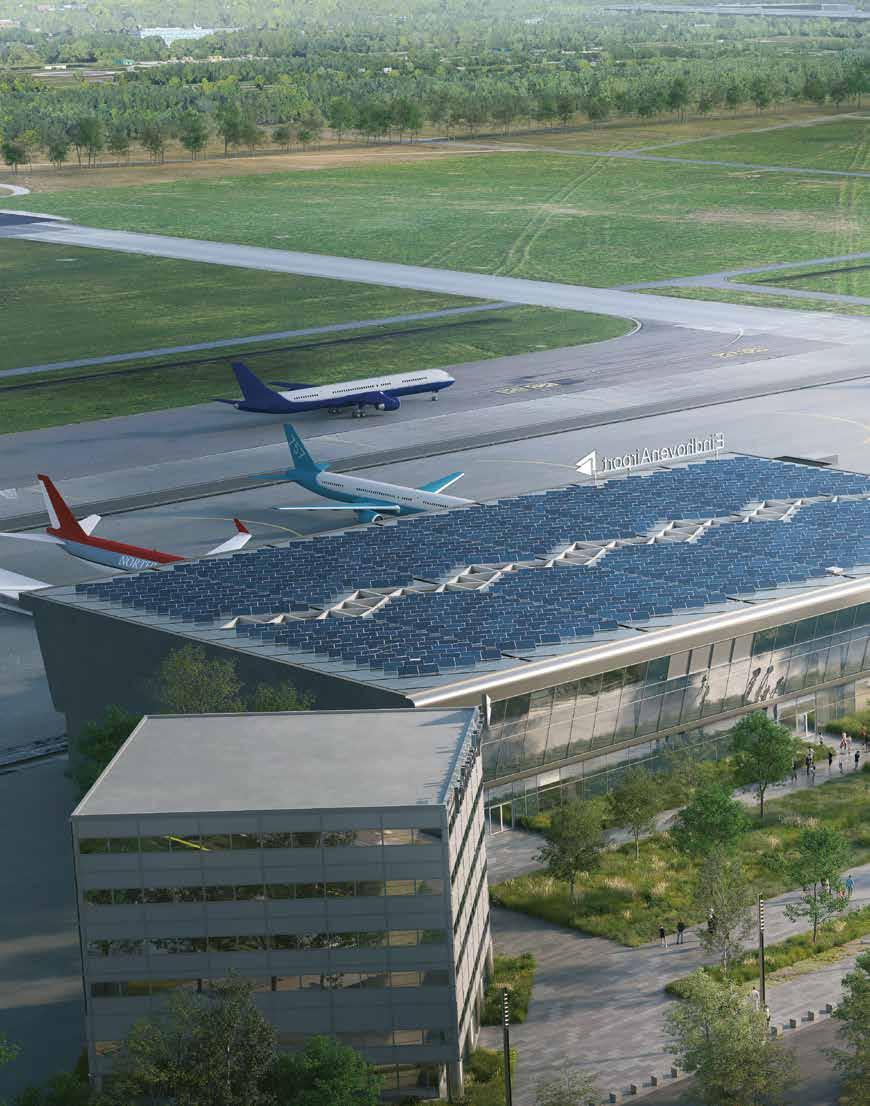
Ons doel is om in 2030 als luchthaven emissie- en afvalvrij te zijn.
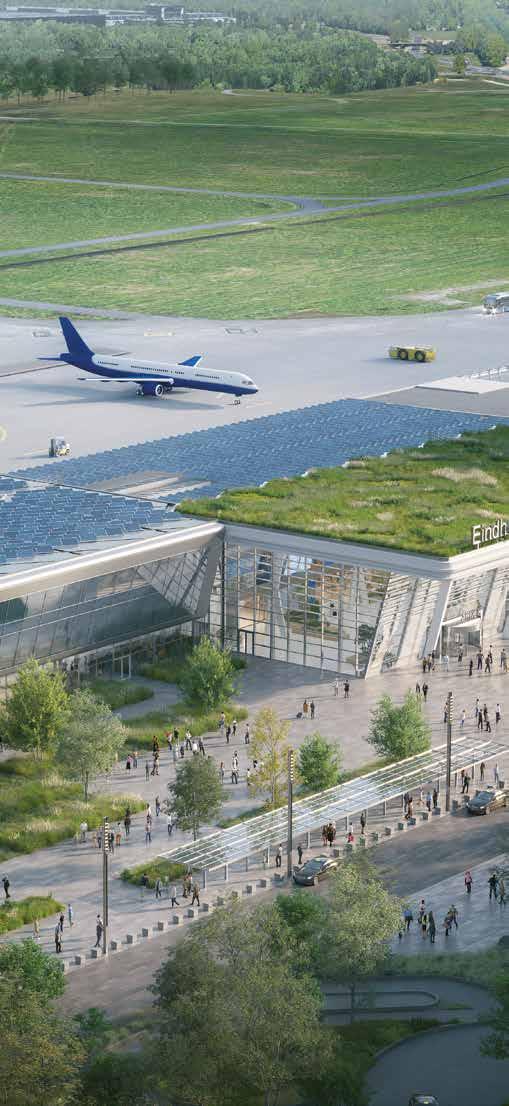
Esthetische en duurzame ventilatie
Met een hoogte van ongeveer 12 meter bieden de entreehal en terminal een ruimtelijk effect. Maar deze hoogte brengt ook uitdagingen met zich mee voor de luchtbehandeling. De entreehal bestaat uit een metalen dakconstructie met een driehoekig patroon, waarin verlichting wordt verwerkt. Hierdoor is de ruimte voor installaties aan het plafond beperkt. Ook vanuit esthetisch oogpunt is het aanbrengen van installaties voor ventilatie aan het plafond ongewenst.
In plaats van traditionele mengventilatie, waarbij lucht vanuit het plafond wordt ingeblazen, heeft Iv een installatieconcept uitgewerkt op basis van verdringingsventilatie op vloerniveau. Dit zorgt voor een gecontroleerde luchtstroom, waarbij koele lucht op de onderste niveaus wordt ingebracht, terwijl warme lucht naar boven wordt gedreven en afgevoerd.
“Wat ik bijzonder vind aan het ventilatieconcept, is dat we iets hebben toegevoegd waar niet direct om werd gevraagd, maar waar wel een indirecte behoefte aan was. We hebben echt vormgegeven aan de vraag van de klant”, vertelt Dennis van der Beijl, projectleider bij Iv.
Dennis werd tijdens zijn tussenstop op de luchthaven van Istanbul geïnspireerd voor het gebruik van verdringingsventilatie. Na onderzoek concludeerde hij dat deze technologie ook geschikt zou zijn voor de uitbreiding van Eindhoven Airport. Door de toepassing van verdringingsventilatie wordt het dak minder zwaar belast en wordt bespaard op de hoeveelheid lucht die nodig is om een ruimte te conditioneren. Dit resulteerde in kleinere en efficiëntere luchtbehandelingssystemen en minder energieverbruik.
Uitdagingen vragen om creatieve oplossingen
Het ontwerpen van de uitbreiding van Eindhoven Airport bracht, naast de verdringingsventilatie, verschillende complexe uitdagingen met zich mee. Met name de complexiteit van het constructieve ontwerp rond de entreehal vereiste creatieve oplossingen om de uitvoering daadwerkelijk te kunnen realiseren. De unieke vorm, een schuin ontwerp, inclusief glazen gevels en grote overspanningen tussen de kolommen, maakte het complex vanwege de trekkracht en de overgang tussen bestaande en nieuwe gebouwdelen. Daarnaast waren er uitdagingen met betrekking tot het houten dak en de driehoekige structuur, omdat hout zich anders gedraagt dan staal. Iv heeft cross laminated timber (CLT) liggers toegepast om meer uniforme materiaaleigenschappen voor de liggers te verkrijgen. Daarnaast zijn fake-liggers
toegepast voor niet-dragende delen, om gewicht te besparen en toch een uniforme esthetische uitstraling te realiseren.
Uiteindelijk draait het om de mensen die met elkaar samenwerken.
Hoewel de uitbreiding van het vliegveld een flinke opgave is, zorgt Eindhoven Airport ervoor dat reizigers hier zo min mogelijk van merken. Jeroen: “De continuïteit van onze operatie is van essentieel belang voor Eindhoven Airport. Het project is hier omheen ontworpen, zodat de luchthaven tijdens de uitbreiding operationeel kan blijven. We hebben de bouw zo ingericht dat deze volledig aan de landzijde plaatsvindt
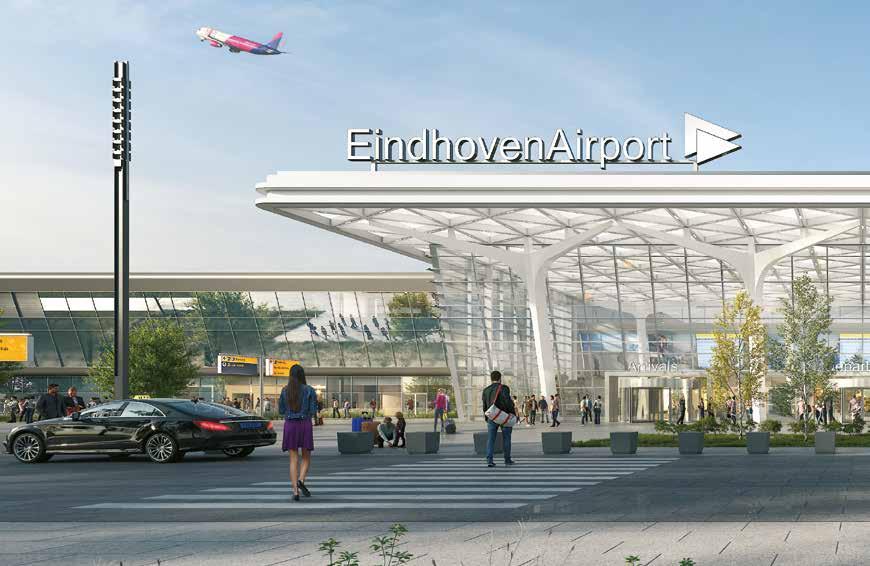
en strikt gescheiden is van het passagiersproces. Dit brengt wel uitdagingen met zich mee, aangezien we beperkte ruimte hebben en erg precies moeten werken. Het is een beetje zoals bouwen op een postzegel; alles moet nauwkeurig worden gepland en uitgevoerd om dit mogelijk te maken. Voor passagiers betekent dit dat zij zo min mogelijk hinder zullen ervaren van de bouwwerkzaamheden.”
Engineering that excites
De uitvoeringswerkzaamheden voor de uitbreiding van de terminal starten eind dit jaar. Als Dennis terugblikt op het project, noemt hij het een bijzondere ervaring.
“Het was mijn eerste project binnen Iv. Werken aan een luchthavenomgeving bracht een heel andere dynamiek met zich mee dan bijvoorbeeld werken aan een
kantoorgebouw. De constante activiteit van vliegtuigen en militaire toestellen gaf een extra dimensie aan het werk. Het ontwerpen vanuit een logistiek perspectief was een interessante uitdaging.”
Hij benadrukt ook de goede samenwerking met EGM architecten. “Uiteindelijk draait het om de mensen die met elkaar samenwerken. Hoewel er altijd uitdagingen zullen zijn, zorgt een goede klik tussen individuen ervoor dat obstakels makkelijker overwonnen kunnen worden.
Deze ervaring heeft me laten zien hoe cruciaal een goede samenwerking is voor het succes van een project, vooral in een uitdagende omgeving zoals een luchthaven.” ●
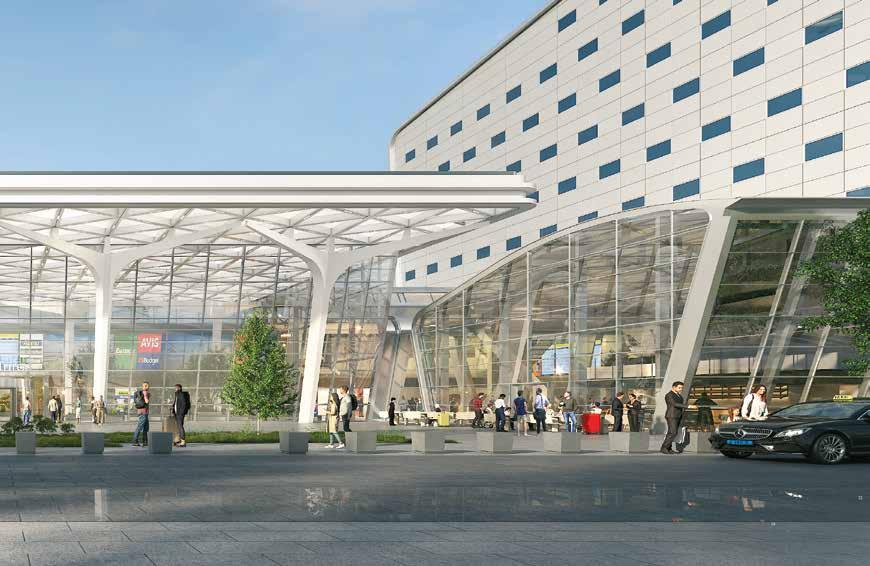
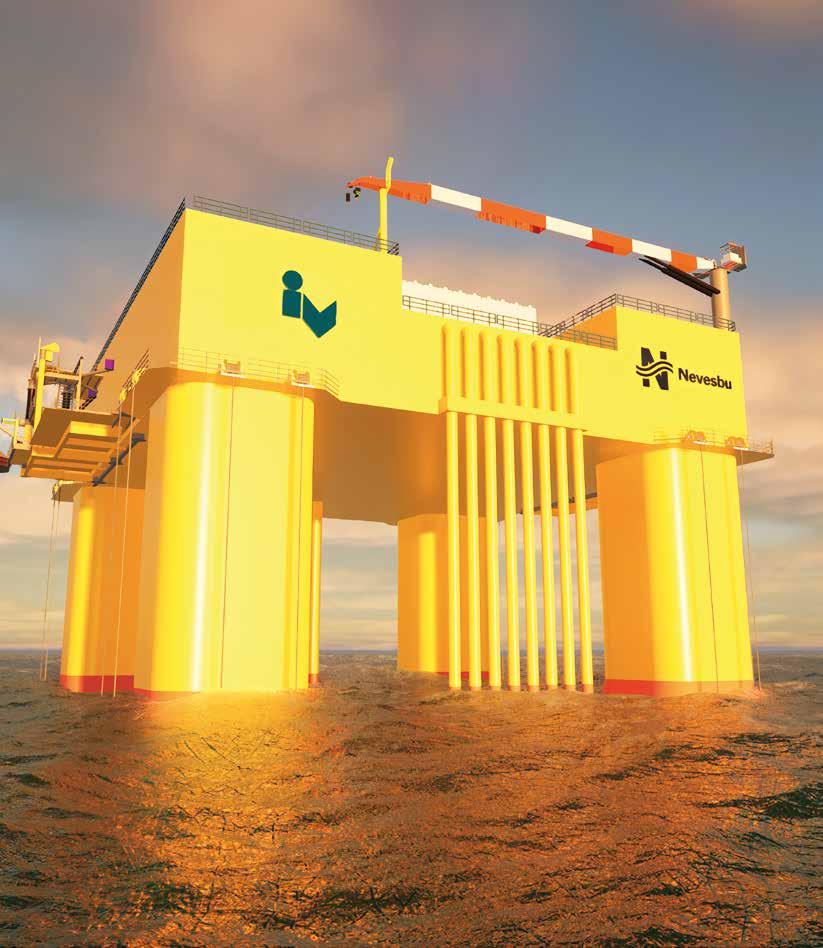
Een volgende stap in drijvende windenergie
De energietransitie is een veelbesproken onderwerp binnen de offshore-industrie, en niet zonder reden. De effecten van klimaatverandering zijn duidelijk merkbaar, wat het noodzakelijk maakt om te investeren in de ontwikkeling van grootschalige duurzame offshore energie. Hoewel het moeilijk te voorspellen is hoe de toekomstige energiemix eruit zal zien, is het duidelijk dat offshore windenergie de komende jaren enorm zal groeien.
Potentieel van drijvende windenergie
Naar verwachting zal er tegen 2050 1.800 gigawatt (GW) aan offshore windenergie worden opgewekt, waarvan 250 GW uit drijvende windparken. Dit vermeldde DNV in het rapport Floating offshore wind: The next five years, dat is gepubliceerd in 2022. Geschikte regio’s voor het opwekken van drijvende offshore windenergie zijn onder andere Californië en Zuidoost-Azië, maar ook Europa, waar de focus ligt op de Middellandse Zee, de Noordzee, de Golf van Biskaje, de Oostzee en de Egeïsche Zee. Al deze gebieden hebben diep water en geschikte windomstandigheden voor het opwekken van duurzame energie.
Een grote uitdaging: in 2050 is de verwachte benodigde drijvende windenergiecapaciteit 250 GW.
Om 250 GW duurzame windenergie efficiënt van zee naar land te transporteren, zijn zogenoemde offshore substations nodig. Deze substations verzamelen de windenergie (AC) van het windpark, zetten de elektriciteit om naar hoogspanningsgelijkstroom (HVDC) of hoogspanningswisselstroom (HVAC) en transporteren dit via 2 of 4 exportkabels naar land. Op deze manier worden de energieverliezen tijdens het transport van
een substation naar land aanzienlijk verminderd. Deze substations worden al veel gebruikt in ondiepe wateren, waar het platform wordt ondersteund door een jacket of andere aan de bodem bevestigde oplossingen. Elk substation is meestal verbonden met 100 tot 150 windturbines, die tussen de 1 en 2 GW aan vermogen opwekken.
Bij waterdiepten van meer dan 150 meter stijgen de kosten van de bekende ‘vaste’ (ofwel: aan de bodem bevestigde) oplossingen exponentieel, waardoor drijvende oplossingen een interessant alternatief worden.
Naar verwachting zullen de substations bij waterdiepten tot 300 meter nog steeds aan de bodem verankerd zijn, terwijl de turbines al gebruikmaken van een drijvende oplossing. In gebieden met waterdiepten van meer dan 300 meter zal een drijvend offshore substation nodig zijn.
Met een verwachte benodigde drijvende windenergiecapaciteit van 250 GW in 2050, staat de markt voor een grote uitdaging. Ervan uitgaande dat het eerste volwaardige drijvende substation in 2035 in gebruik wordt genomen, moeten er elk jaar acht tot tien substations van 2 GW worden gebouwd in de periode van 2035 tot 2050 om deze prognose te halen.
Huidige marktuitdagingen
Momenteel is er een groot aantal concepten in ontwikkeling ter ondersteuning van de drijvende windturbine. Bedrijven onderzoeken de technologieën voor drijvende offshore substations, maar er zijn nog geen bewezen ontwerpen op de markt.
De belangrijkste uitdaging op dit moment is dat de dynamische omstandigheden, zoals ervaren door een drijvend substation, onbekend terrein zijn voor apparatuur- en kabelproducenten (de OEM’s). De bestaande hoogspanningsapparatuur is niet ontworpen voor continue bewegingen en versnellingen zoals die op een drijvend substation zullen worden ervaren.
Vanuit financieel perspectief wordt verwacht dat drijvende windoplossingen duurder zullen zijn dan de vaste oplossingen. Dit hangt uiteraard af van een groot aantal factoren, zoals de levensduur, waterdiepte, grootte van het windpark en vele andere aspecten. Aan de andere kant zou de ontwikkeling van diepwaterlocaties de beperkingen op ashoogte, scheepvaartroutes en de sociale impact van offshore wind kunnen verminderen. Hoewel deze aspecten de projectkosten zullen verlagen, is het moeilijk om dit uit te drukken in lagere kosten voor de totale ontwikkeling. Uiteindelijk zijn verschillen in materiaalkosten tussen de vaste en drijvende substations prominenter en gemakkelijker uit te drukken. Men zou kunnen stellen dat de goedkoopste optie voor een drijvend substation is om de romp van een bestaande tanker te renoveren en om te bouwen tot een drijvend platform, zoals dit gebeurt bij drijvende productie-, opslag- en overslagunits (FPSO’s). Deze oplossing wordt echter niet als haalbaar beschouwd vanwege de verwachte toegestane versnellingen van de HVapparatuur, wat nog steeds wordt onderzocht door de OEM’s.
Technische uitdagingen
Vanuit technisch oogpunt zijn conceptuele studies uitdagend en complex, aangezien er nog veel onbekendheden zijn met betrekking tot:
1. de normen die moeten worden gehanteerd in het algehele ontwerp van de drijvende oplossing;
2. de toegestane bewegingscriteria van de HVapparatuur;
3. de vermoeidheidscapaciteit van de kabels tussen het platform en de windturbines (inter-arraykabels) en de exportkabels.
In de afgelopen jaren hebben Nevesbu en Iv zich gericht op het nader onderzoeken van deze drie onderwerpen. Het is belangrijk om te beseffen dat windturbines in staat zijn om te opereren in omstandigheden tot Beaufort 8, wat betekent dat het drijvende substation operationeel moet zijn met golven van 8 tot 12 meter hoog. Dit maakt de punten 2 en 3 nog uitdagender.
1. Drijvend substation standaarden
In 2021 werd het Floating Offshore Substations (FOSS) Joint Industry Project (JIP), geïnitieerd door DNV, gestart. Het hoofddoel was om de hiaten in de huidige normen voor drijvende offshore substations te bestuderen, voorstellen te doen om deze hiaten te overbruggen, en de huidige stand van technologie en ontwerp te verkennen. Naast de ontwikkeling van deze norm, wordt er een aanbevolen aanpak voorbereid voor het ontwerp en de analyse van hoogspanningsexportkabels. Nevesbu en Iv waren nauw betrokken bij dit JIP, samen met tal van bedrijven uit de industrie. Dit JIP heeft meer inzicht gegeven in de resterende uitdagingen en technologische hiaten voor drijvende offshore substations en in de voorkeursnormen voor drijvende oplossingen. Fase II van deze JIP is in juni 2024 gestart met een kick-off bijeenkomst.
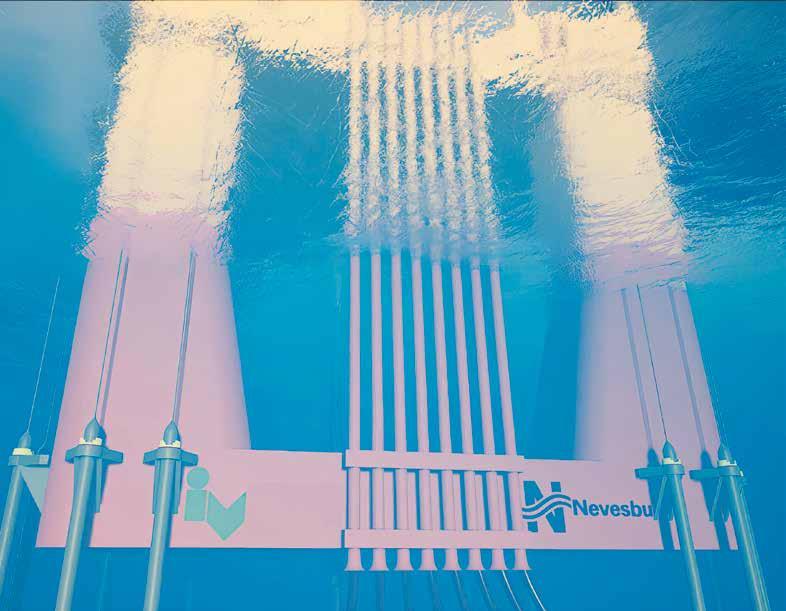
2. Conceptontwikkeling
Nevesbu en Iv hebben de afgelopen jaren verschillende concepten voor drijvende substations onderzocht en vergeleken. Hierbij zijn verschillende drijvende oplossingen onderzocht, zoals SPAR’s, boeien, semisubmersibles en zogenoemde tension leg platforms (TLP’s).
Elk concept moet voldoen aan de vastgestelde eisen voor offshore windenergie, waarbij overmatig staalgewicht moet worden voorkomen en eenvoud in fabricage moet worden gehandhaafd. Verder is het essentieel om
veiligheid en betrouwbaarheid te waarborgen, terwijl ook een zeer hoge beschikbaarheid en een platformlevensduur van minimaal 30 tot 40 jaar moet worden gegarandeerd. Daarnaast moeten de sociale kosten van het leveren van duurzame elektriciteit betaalbaar blijven, en mag de oplossing zelf dus niet te duur zijn qua kosten.
Op basis van deze principes en eisen is een selectie gemaakt van het meest veelbelovende drijftype. Momenteel ligt de focus op de ontwikkeling van een substationconcept dat is gebaseerd op de bewezen ‘tension leg platform’ (TLP) technologie.

Scan de QR-code en bekijk een video van de test van het floating substation concept met verschillende configuraties van het kabelgeleidingssysteem (CGS) op modelschaal bij MARIN (Maritime Research Institute Netherlands).
Het concept is ontwikkeld voor het omzetten van 1,4 tot 2,0 GW aan vermogen, met een DC-exportverbinding van 300 tot 525 kV. Een typische HVDC-topside weegt ongeveer 13.000 tot 20.000 ton. Het drijvende HVDCplatform heeft een dekoppervlak van 85 bij 85 meter en steekt ongeveer 25 meter boven het wateroppervlak uit. De algehele indeling is geoptimaliseerd voor toepassing op een drijvende onderstructuur. Wanneer het platform op zee is geïnstalleerd, wordt het op zijn plaats gehouden met behulp van zogenaamde ‘tendons’ die verticaal verankerd zijn aan de zeebodem, waardoor de verticale bewegingen en versnellingen worden beperkt.
De maximale golfhoogte die in het modelbekken is getest, komt overeen met de gebeurtenis eens in de 100 jaar ten westen van Shetland.
3. Kabelgeleidingssysteem
Dynamische inter-arraykabels worden al op ware grootte ontwikkeld en getest in de drijvende windturbinepilots wereldwijd en worden daarom als volwassen beschouwd voor de inzet van de eerste FOSS-eenheden. De DC-exportkabels zijn daarentegen nog gevoeliger voor vermoeidheid vanwege de grote kern en de omringende metalen mantel. Nevesbu ontwikkelde een kabelgeleidingssysteem (CGS) dat het vermoeidheidsprobleem voor de DC-exportkabel oplost.
MARIN MKB modeltest
In oktober 2023 heeft Nevesbu het drijvende concept op schaalmodel getest met verschillende configuraties van het CGS. De modeltest is uitgevoerd binnen het MKBslot van MARIN. Er waren twee primaire doelstellingen vastgesteld voor deze modeltestcampagne. De eerste
reeks modeltests is uitgevoerd om het numerieke model te kalibreren. De tweede reeks tests was gericht op het CGS, waarbij de respons van het systeem werd onderzocht onder verschillende CGSvoorspanningsniveaus in verschillende zeetoestanden. Om deze doelstellingen te bereiken, was het model uitgerust met bewegings- en versnellingssensoren en belastingssensoren op elke tendon en kabelgeleiding.
Deze informatie is vastgelegd voor de verwachte condities op zee waarin het substation zal opereren. De maximale golfhoogte die in het modelbekken is getest, komt overeen met de gebeurtenis eens in de 100 jaar ten westen van Shetland, wat overeenkomt met Hs > 17,0 meter. Een eerste controle op hoog niveau heeft aangetoond dat de gemeten maximale verplaatsing, versnellingen en CGS-belastingen in onregelmatige golven vergelijkbaar zijn met de resultaten van het numerieke model van Nevesbu. De exacte resultaten van deze tests worden nu zorgvuldig vergeleken en geverifieerd, met behulp van het zelfontwikkelde numerieke model en de gegevens van MARIN.
Status en vooruitzichten van het concept
Na de succesvolle testcampagne van het drijvende substation, in combinatie met het zelfontwikkelde kabelgeleidingssysteem, bevindt het FOSSconcept zich op ‘Technologie Readiness Level 3’ en is het klaar voor verdere ontwikkeling. Op basis van dit solide concept zullen meer diepgaande vermoeidheidslevensduurschattingen van de drijver, tendons, kabelgeleidingssysteem en HV-apparatuur worden uitgevoerd om onze ontwerpoplossing verder te verbeteren. Nauwe samenwerking met OEM’s moet parallel worden opgezet om de beperkingen van apparatuur nog beter te begrijpen. ●
Heeft groene waterstof de
toekomst?
De ontwikkeling van groene waterstof is in volle gang. Alleen al in Nederland lopen er honderden pilots, FEED-studies en kleinschalige projecten voor de productie en het transport van waterstof. Ook grotere waterstofprojecten worden opgestart. Een grote rol in die ontwikkeling is weggelegd voor ingenieurs. En dus ook voor Iv. Een toekomst in waterstof vraagt om een integrale aanpak. Iv levert deze aanpak met hoogwaardige en zeer specialistische kennis uit diverse markten.
Een wereldprimeur in groene waterstofproductie
Op 7 mei vierde Iv met veertien consortiumpartners een unicum: de onshore test van PosHYdon; het eerste operationele gasplatform ter wereld waar offshore wind, gas én waterstof worden geïntegreerd. In het vierde kwartaal van dit jaar staat de eerste productie gepland op het bestaande Q13a-A-platform van Neptune Energy (Eni); een wereldprimeur. PosHYdon is een initiatief van het nationale platform Nexstep en kennisinstituut TNO. Samen met veertien andere partners heeft Iv zich de laatste jaren gestort op de ontwikkeling van deze primeur. Iv heeft onder andere de engineering en systeemintegratie verzorgd voor de aanpassingen op het bestaande platform, die nodig zijn voor de productie van waterstof op zee. Hiervoor wordt een elektrolysesysteem geïnstalleerd dat waterstof in de bestaande gasexportpijp injecteert.
Naast deelname aan het project PosHYdon is Iv ook kennispartner binnen het programma North Sea Energy, waarvoor Iv als onderdeel van ‘Offshore energy hubs’ een 500MW platform voor groene waterstof heeft ontwikkeld.
Ammoniak kenmerkt zich als een uitstekende drager van waterstof die overal in de wereld geproduceerd kan worden door simpel stikstof uit de lucht te halen.
Ontwikkeling in de volle breedte Nog altijd ontwikkelt en oriënteert Iv zich in de volle breedte van de organisatie, want dat waterstof een grote rol gaat spelen, staat vast. Maar het vinden van maakbare oplossingen voor veilige en betrouwbare productie van groene waterstof is technisch complex en vereist zeer specialistische kennis uit diverse markten. Iv pioniert op meerdere vlakken en werkt onder andere aan technische oplossingen voor de import van waterstofdragers, zoals ammoniak.
Ook kunnen we op het gebied van waterstofopslag oplossingen bieden voor infrastructuur, binnen de industrie en voor de gebouwde omgeving, waardoor groene waterstof voor een bredere markt (dus niet alleen de industrie, maar ook het mkb, de transportsector en uiteindelijk huishoudens) bereikbaar en beschikbaar wordt.
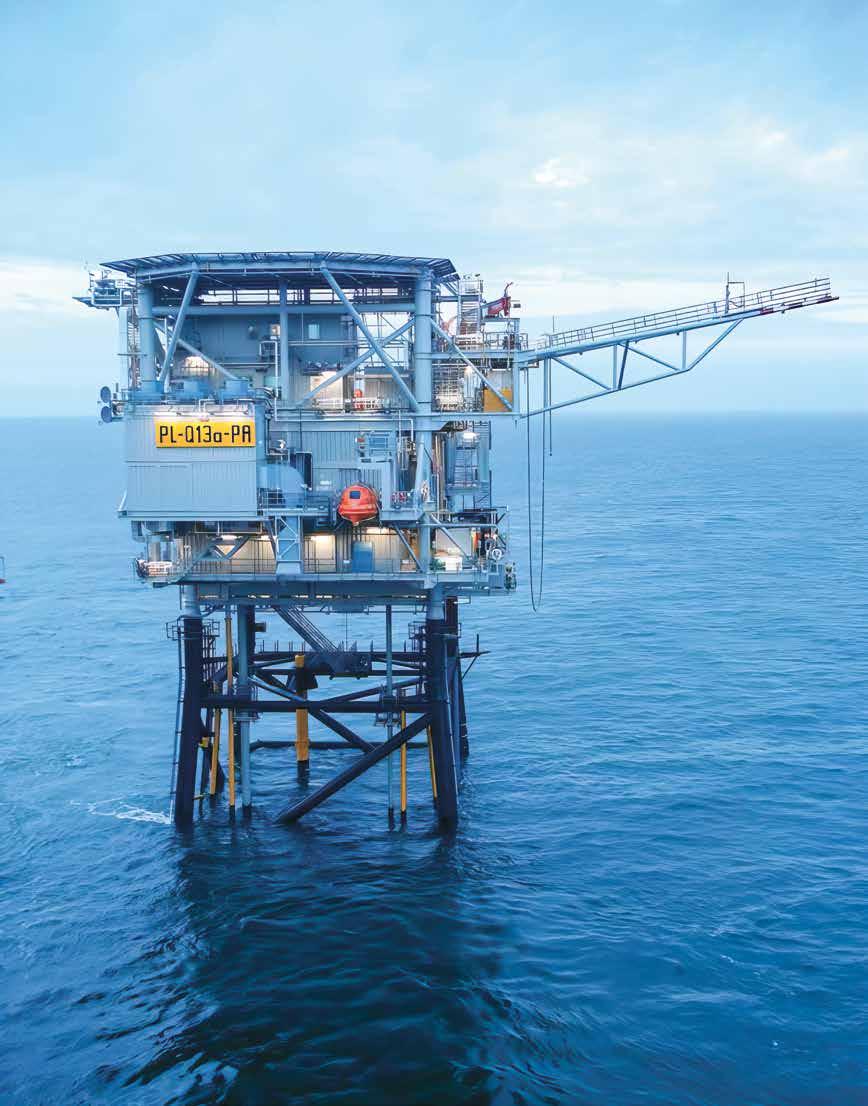
Met PosHYdon wordt de werking aangetoond op kleinere schaal.
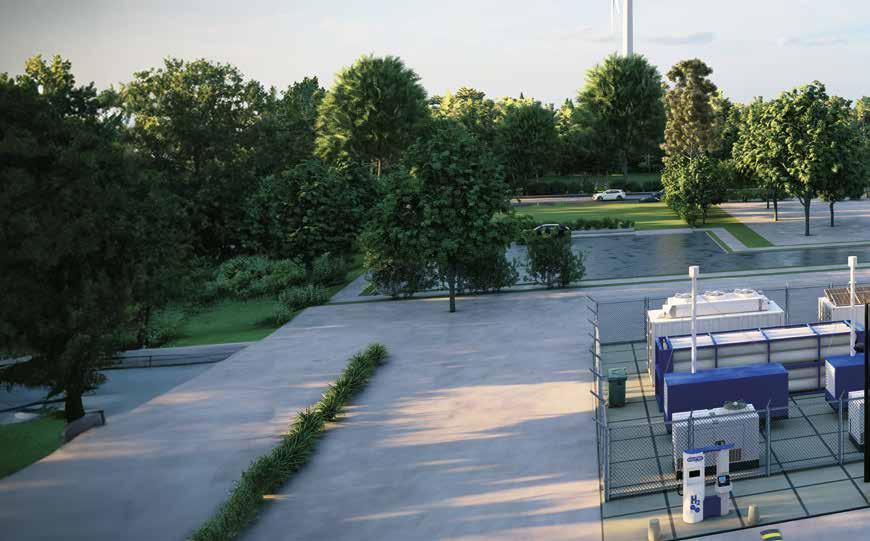
Door onze zeer diverse achtergrond en uiteenlopende expertises in verschillende markten nemen we een belangrijke rol in, in de transitie naar productie van groene waterstof. We leveren technische ontwerpen en systeemintegratie, maar benutten ook onze aanwezige kennis in watertechnologie, veiligheid, procurement services en projectmanagement.
Escher heeft een technologie ontwikkeld voor het decentraal produceren van groene waterstof uit ammoniak.
Modulair ontwerpen
Dat waterstof al lange tijd op de agenda staat in de politiek en het bedrijfsleven, is gezien de potentie en de impact op de wereld niet gek. Net zo min is het vreemd
dat het tijd nodig heeft. Met PosHYdon wordt de werking aangetoond op kleinere schaal: een cruciale stap voor uiteindelijke opschaling en commercialisatie van groene waterstofproductie op zee.
Om groene waterstof aan land en in de (kleine) industrie te krijgen, is efficiënt transport cruciaal. Ook aan die kant is Iv actief. Escher, onderdeel van Iv, heeft een technologie ontwikkeld voor het decentraal produceren van groene waterstof uit ammoniak. Ammoniak kenmerkt zich als een uitstekende drager van waterstof die overal in de wereld geproduceerd kan worden door simpel stikstof uit de lucht te halen. De technologie van Escher splitst het ammoniak terug tot waterstof en stikstof, om vervolgens te worden gescheiden in bijna puur waterstof en stikstof. Deze manier van waterstof produceren kost lokaal slechts een fractie van de energie vergeleken met conventionele
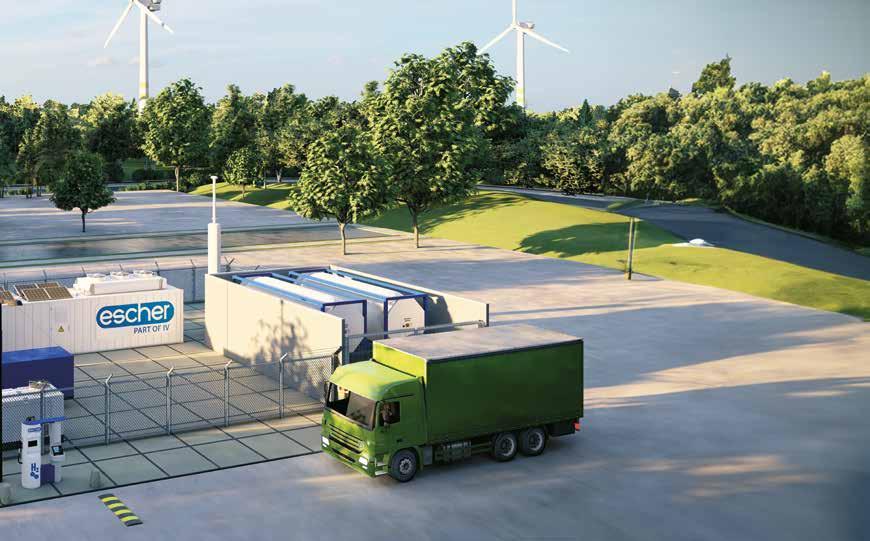
lokale waterstofproductie met elektrolyse. Het proces is daardoor beduidend minder belastend voor het elektriciteitsnet.
Onze rol: het voorzien van antwoorden en maakbare oplossingen.
Breed inzetbaar
Zoals eerder geschetst: Iv is over de gehele breedte van de organisatie actief op het gebied van waterstof. Want bij productie en de logistieke uitdagingen blijft het niet. Binnen verschillende ketens wordt naar mogelijkheden voor waterstof gekeken. In de omgeving van water wordt bijvoorbeeld gezocht naar wat we kunnen met de zuurstof die bij elektrolyse vrijkomt en kan worden afgevangen in de omgeving van waterzuiveringen. Dit
kan vervolgens worden gebruikt voor het voeden van bacteriën, die op hun beurt gebruikt kunnen worden voor de beluchting van de waterzuivering.
Nationaal Waterstof Programma
Iv ziet het belang van groene waterstof binnen de energietransitie en volgt daarin nauwgezet de landelijke ontwikkelingen binnen het Nationaal Waterstof Programma en de Routekaart Waterstof naar grootschalige productie, import, infrastructuur en opslag van waterstof (op zee) in 2030. Ook zien we een mooie rol en verantwoordelijkheid voor ons als ingenieursbureau weggelegd; het voorzien van antwoorden en maakbare oplossingen binnen de uitdagingen die op die route liggen. ●
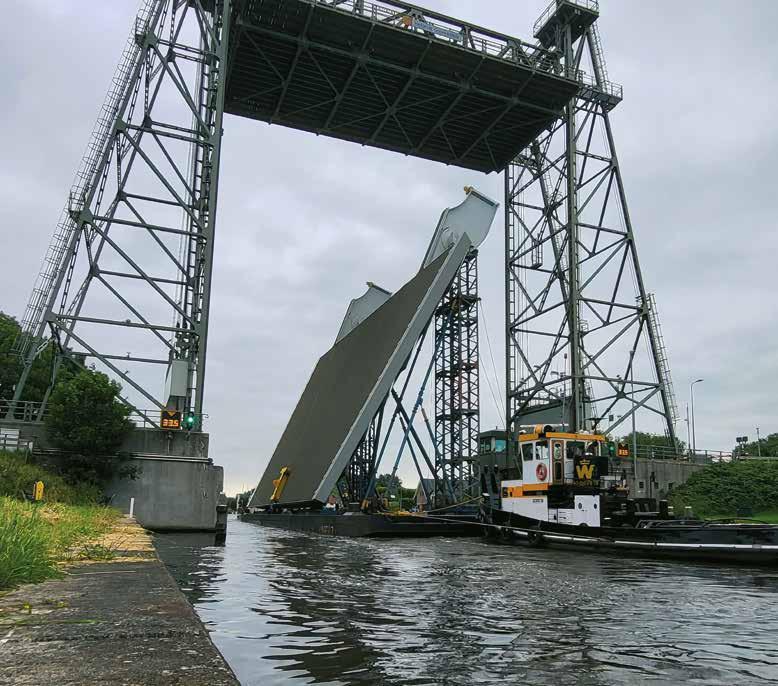
Renovatie, versterking en uitbreiding van de Schipholbrug A9
De werkzaamheden aan de Schipholbrug in de A9 zijn in volle gang. Het project wordt uitgevoerd in opdracht van Rijkswaterstaat en wordt met recht een technisch hoogstandje genoemd. Het is een gigantisch infraproject. Als de brug klaar is, is het de breedste basculebrug van Nederland. Maar wat verandert er eigenlijk allemaal aan de brug?
Een belangrijk kunstwerk
De Schipholbrug is een belangrijk kunstwerk in de A9 dat de kruising faciliteert tussen de A9, de Nieuwemeerdijk N231, de Ringvaart en de Schipholdijk. Het bestaat uit twee bruggen (noordelijk en zuidelijk) met twee beweegbare stalen vallen met elektromechanische bewegingswerken. De renovatie en uitbreiding omvatten onder andere de verbreding van de betondekken en de onderbouw, renovatie van de basculekelder en de bouw van een nieuw bedieningsgebouw. Deze brugconstructie vereist een zorgvuldig ontwerp, planning, bouwmethoden en fasering om een veilige, efficiënte en duurzame brug te creëren die voldoet aan de groeiende verkeersvraag met een restlevensduur van 30 jaar.
Stalen dekken
De Schipholbrug bestaat uit twee delen, één voor elke rijrichting. Elke brug is verdeeld in een westelijke aanbrug van ongeveer 85 meter lang, een oostelijke aanbrug van ongeveer 165 meter lang en een beweegbaar deel met een overspanning van zo’n 20 meter.
Voor de nieuwe situatie worden de twee bestaande stalen vallen en aandrijving compleet vervangen en verbreed aan weerszijden. Het beweegbare gedeelte van de brug bestaat uit een orthotroop rijdek (verschillende materiaaleigenschappen), ondersteund door dwarsdragers en hoofdliggers. De stalen vallen van beide bruggen (noordelijk dek en zuidelijk dek) zijn nagenoeg identiek van opzet en detaillering, behalve in breedte vanwege het aantal rijstroken dat ze moeten faciliteren. Het noordelijk dek is significant breder dan het zuidelijke beweegbare dek.
Voor de noordelijke brug wordt de ballastkist gevuld met een totale vaste ballast van circa 442 ton. De vormgeving
van de ballastkist van de zuidelijke brug wijkt in geringe mate af van de noordelijke brug. De ballastkist van de zuidelijke brug, die minder breed is, is gevuld met circa 362 ton vaste ballast.
Het elektro-mechanische bewegingswerk maakt het
mogelijk om de bruggen
onafhankelijk te openen en te sluiten voor de passage van schepen.
Mechanische uitrusting
De mechanische uitrusting van de Schipholbrug is van vitaal belang voor het betrouwbaar en beschikbaar functioneren van de brug. Het omvat verschillende componenten en systemen die samenwerken om de beweging, veiligheid en onderhoudbaarheid van de brug te waarborgen.
Een van de belangrijkste aspecten van de mechanische uitrusting is het bewegingsmechanisme van de brug. Dit elektro-mechanische bewegingswerk maakt het mogelijk om de bruggen onafhankelijk te openen en te sluiten voor de passage van schepen. Het omvat een robuust aandrijfsysteem, met elektrische motoren en tandwielmechanismen (panamawiel-rondsel aandrijving met krukdrijfstang), die zorgen voor de krachtige en nauwkeurige beweging van de beweegbare brugdelen.
Daarnaast omvat de mechanische uitrusting een krukdrijfstangmechanisme dat zorgdraagt voor een opzetkracht (het ‘vergrendelen en beveiligen van de brug’) ten behoeve van de gegarandeerde gesloten ligging. Dit draagt bij aan de veiligheid van de brug en minimaliseert het risico op storingen.
Ook worden sensoren en meetsystemen geïntegreerd in de mechanische uitrusting. Deze sensoren bewaken onder andere de positie, snelheid en krachten die op de brug worden uitgeoefend. Ze voorzien het controle- en bewakingssysteem van waardevolle informatie, waardoor het mogelijk is om de brug nauwkeurig te positioneren en te controleren op mogelijke afwijkingen gedurende de openings- en sluitingscycli. Op basis van deze gegevens kan tijdig onderhoud worden uitgevoerd om de optimale werking van de brug te waarborgen.
Naast bovengenoemde systemen zijn ook andere mechanische componenten aanwezig zoals lagers, afdichtingen en noodaandrijving en zijn beide vallen voorzien van een handaandrijving. Deze componenten
spelen allemaal een cruciale rol bij het soepel functioneren van de brug en moeten regelmatig worden geïnspecteerd en onderhouden om optimale prestaties te garanderen.
Een geavanceerde koppeling tussen de bestaande en het nieuwe brugdek waarborgt de sterkte, stabiliteit en veiligheid van de brug.
Om de brug in geopende stand te onderhouden is in de basculekelder een vastzetinrichting voorzien voor het geval dat onderdelen van de aandrijving onderhouden of vervangen moeten worden.
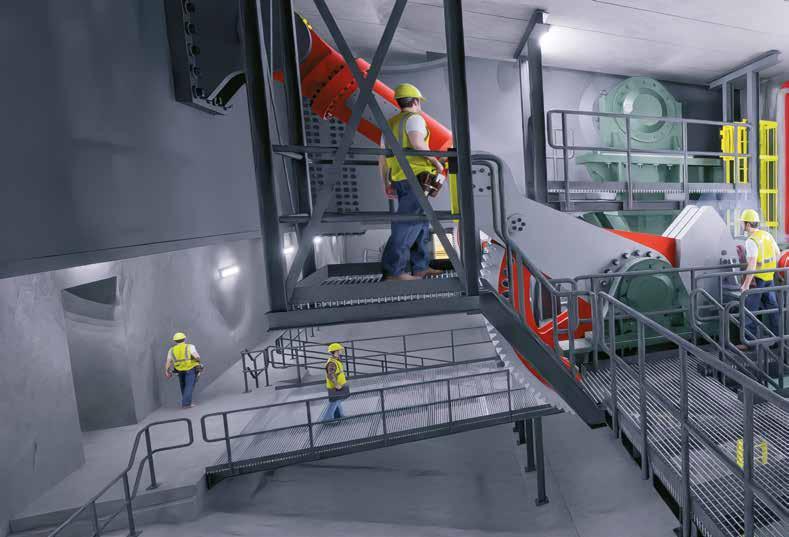
Betondekken
Een belangrijk aspect van de renovatie en uitbreiding van de Schipholbrug is de verbreding van de bestaande, in het werk nagespannen, betondekken. Om de toegenomen capaciteitsvereisten (wegverbreding) te accommoderen, worden de bestaande betondekken verbreed en wordt een koppeling gemaakt tussen het bestaande en het nieuwe dek.
De betondekken worden verbreed door het toevoegen van nieuwe in het werk gestorte, nagespannen dekken aan beide zijden van de bestaande dekken. De verbreding van de dekken wordt gerealiseerd op hulpbruggen aan weerszijden waarop de bekistingsconstructies worden gerealiseerd boven de Haarlemmer ringvaart. Deze
nieuwe dekken, met een geavanceerde koppeling aan de bestaande constructie, vormen een naadloze overgang tussen het oude en nieuwe deel van de brug.
Een belangrijk aspect van de renovatie en uitbreiding van de Schipholbrug is de verbreding van de bestaande, in het werk nagespannen, betondekken.
Een belangrijk aspect van de verbreding van de betondekken is de koppeling tussen het bestaande en het nieuwe dek. Dit wordt gerealiseerd door het creëren van een geïntegreerd systeem van in te boren wapening in de bestaande betondekken en het vrijstralen van
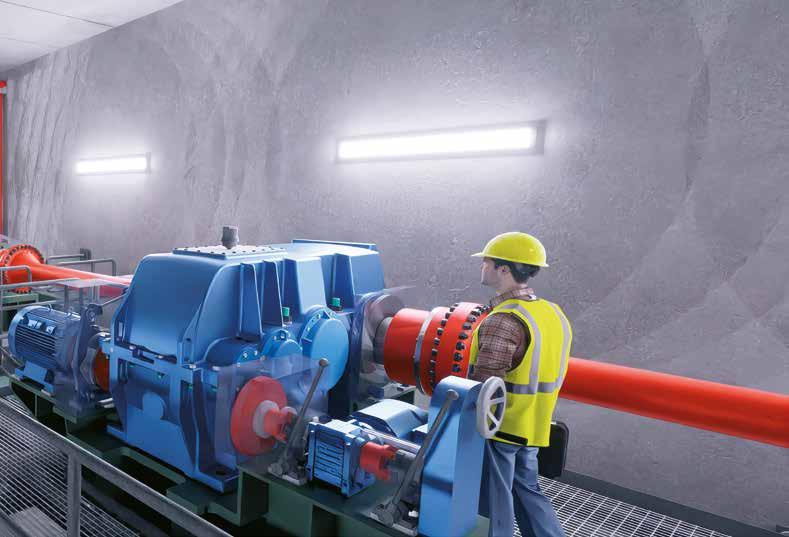
wapening om bijlegwapening te leggen. Deze koppeling zorgt ervoor dat de krachten die op de brug worden uitgeoefend, gelijkmatig worden verdeeld over het gehele brugdek. Zo worden de sterkte, stabiliteit en veiligheid gewaarborgd en ontstaat er functioneel een breder rijdek om de verbreding te faciliteren.
De bestaande basculekelder wordt gerenoveerd en aangepast om te voldoen aan de eisen van de nieuwe brugconfiguratie.
Basculekelder
De basculekelder vormt een essentieel onderdeel van de Schipholbrug. Het speelt een cruciale rol bij het openen en sluiten van de beweegbare delen van de brug. De kelder biedt onderdak aan de mechanische uitrusting en zorgt voor de benodigde sterkte en stabiliteit en krachtinleiding tijdens het bewegingsproces van de aandrijving die flinke krachten introduceert op de betonconstructies en fundering.
De bestaande basculekelder wordt gerenoveerd en aangepast om te voldoen aan de eisen van de nieuwe brugconfiguratie. Verschillende aanpassingen worden doorgevoerd, zoals het vervangen van de voegovergangen, het vernieuwen van het kelderdak en het versterken van de wanden en vloer. Ook de voorwand wordt tot een hoogte van circa 0,5m NAP volledig gesloopt en herbouwd. Deze renovatiewerkzaamheden zorgen ervoor dat de kelder de verhoogde belastingen en krachtswerking kan weerstaan en blijft voldoen aan de constructieve veiligheidsnormen, met de beoogde restlevensduur van 30 jaar.
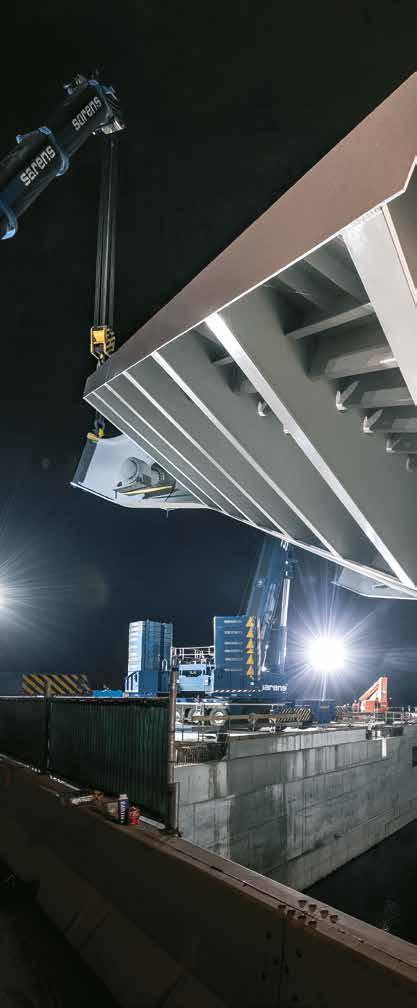

Daarnaast wordt de basculekelder uitgebreid aan de noordzijde en zuidzijde om plaats te bieden aan de nieuwe configuratie van de brug (wegverbredingen). De afmetingen van het nieuwe deel van de kelder zijn significant groter dan die van het bestaande deel.
Bedieningsgebouw
Aan de noordzijde van de Schipholbrug wordt een nieuw bedieningsgebouw gebouwd. De bestaande bedientoren wordt volledig gesloopt. Het nieuwe bedieningsgebouw wordt gerealiseerd als een ‘doos-in-doos’ constructie. Het bedieningsgebouw is zodoende ontworpen dat het een veilige en comfortabele werkomgeving biedt voor het personeel dat verantwoordelijk is voor de bediening van de brug. Hoewel aan het directe oog onttrokken voor het wegverkeer, is het bedieningsgebouw architectonisch ontworpen en ingepast met oog voor functionaliteit en esthetiek.
Het bedieningsgebouw is voorzien van afgeronde hoeken en verschillende ontwerpkenmerken om visueel los te staan van het brugdek. Hierdoor wordt het gebouw een herkenbaar element op de locatie en draagt het bij aan de algehele uitstraling van de brug.
Ondertussen gaat de uitbreiding van de A9
Badhoevedorp – Holendrecht gestaag verder. De verbreding van de Schipholbrug is als eerste gereed. In de zomer van 2025 zou deze volgens de huidige planning klaar moeten zijn. Het totale project wordt in 2027 afgerond. ●
De nieuwe PALLAS-reactor helpt nóg meer patiënten bij behandeling van kanker
Wist je dat er dagelijks ruim 30.000 patiënten wereldwijd afhankelijk zijn van de productie van medische isotopen? Deze radioactieve stoffen zijn onmisbaar voor de diagnose en behandeling van kanker. We staan voor een grote uitdaging: de productie van deze levensreddende isotopen moet worden gegarandeerd voor de toekomst. Hier komt de nieuwe PALLAS-reactor in beeld: een project in Petten, Noord-Holland, dat de toekomst van de medische isotopenproductie gaat continueren.
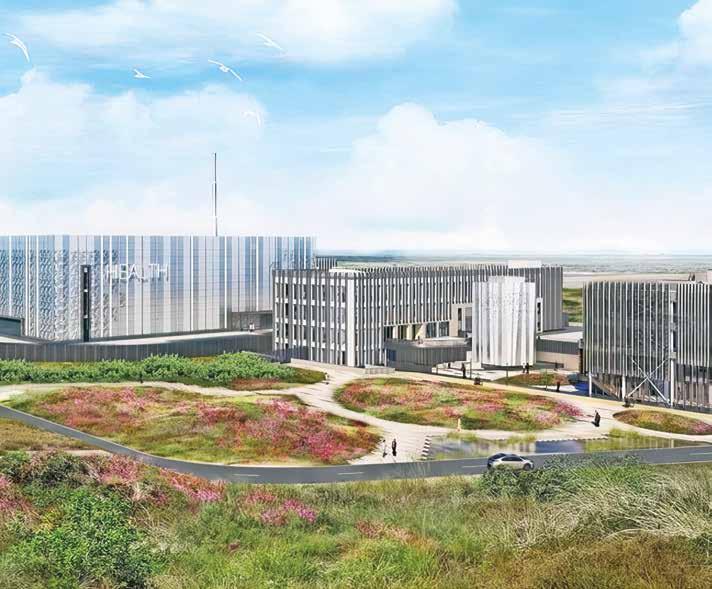
Het belang van de PALLAS-reactor
Maar waarom is de PALLAS-reactor juist nu zo belangrijk?
De huidige Hoge Flux Reactor (HFR), die al sinds 1961 in Petten in bedrijf is, nadert het einde van zijn technische levensduur. Daarnaast heeft de 63 jaar oude reactor steeds intensiever onderhoud nodig en kan hij de groeiende vraag naar medische isotopen niet meer bijbenen. “De HFR was oorspronkelijk bedoeld als materiaaltestreactor en is pas later aangepast voor isotopenproductie. De PALLAS-reactor is daarentegen specifiek ontworpen voor grootschalige productie”, legt Jan van der Marel, projectdirecteur bij PALLAS, uit.
De PALLAS-reactor is ontworpen met een focus op productiecapaciteit voor medische isotopen met daarnaast ook ruimte voor onderzoeksactiviteiten.
Na de voltooiing van de nieuwe PALLAS-reactor zal de productie van medische isotopen naar een hoger niveau worden getild. Hiermee kan Nederland de komende 50 jaar miljoenen mensen blijven helpen. Jan van der Marel: “Met de nieuwe reactor kunnen we niet alleen de vraag binnen Nederland vervullen, maar ook een aanzienlijke bijdrage leveren aan de bevoorrading van medische isotopen in heel Europa en zelfs in de hele wereld.” Hoewel de basis van het ontwerp geïnspireerd is door de OPAL-reactor in Australië, is PALLAS allesbehalve een simpele kopie. Waar OPAL zich voornamelijk richt op onderzoek en daarnaast in beperkte mate medische isotopen produceert, is dit bij PALLAS precies andersom. Deze reactor is ontworpen met een focus op productiecapaciteit voor medische isotopen met daarnaast ook ruimte voor onderzoeksactiviteiten.
Dit maakt PALLAS een unieke reactor die speciaal is afgestemd op de groeiende vraag naar medische isotopen, waardoor er een grote stap voorwaarts wordt gezet in de productie en beschikbaarheid van deze levensreddende middelen.
Hoe gaat het in zijn werk?
Maar hoe werkt de reactor precies? Stel je een grote, met water gevulde reactorpool voor, ongeveer vier meter breed en vijftien meter diep. Onderin deze pool bevindt zich de kern van de reactor. In de reactor worden speciale nucleaire brandstofstaven met verrijkt uranium gebruikt. Deze staven worden in een reflectorvat gepositioneerd waar ze neutronen uitzenden. In de reactorpool bevinden zich ook speciale ‘targets’. Deze targets zijn materialen die ontworpen zijn om de neutronen te vangen. Wanneer de neutronen de targets raken, worden ze omgezet in isotopen. Isotopen zijn een soort speciale atomen die radioactief zijn. Dit betekent dat ze straling afgeven. In de geneeskunde worden ze gebruikt om ziektes zoals kanker op te sporen en te behandelen. Dankzij deze radioactiviteit kunnen artsen precies zien wat er in een lichaam gebeurt en helpen de isotopen bij behandelingen.
Sleutelrollen in reactorontwerp
Het Argentijnse ICHOS speelt een cruciale rol in de ontwikkeling van de nieuwe PALLAS-reactor. José Louis Molina, projectdirecteur bij ICHOS legt uit: “Onze belangrijkste taak is om een productie-installatie voor radio-isotopen te leveren die voldoet aan de hoge prestatienormen van PALLAS.” ICHOS begon zijn betrokkenheid vanaf de vroege ontwerpfase en werkt nauw samen met Iv om ervoor te zorgen dat alle aspecten van de installatie voldoen aan de vereiste kwaliteitsstandaarden.
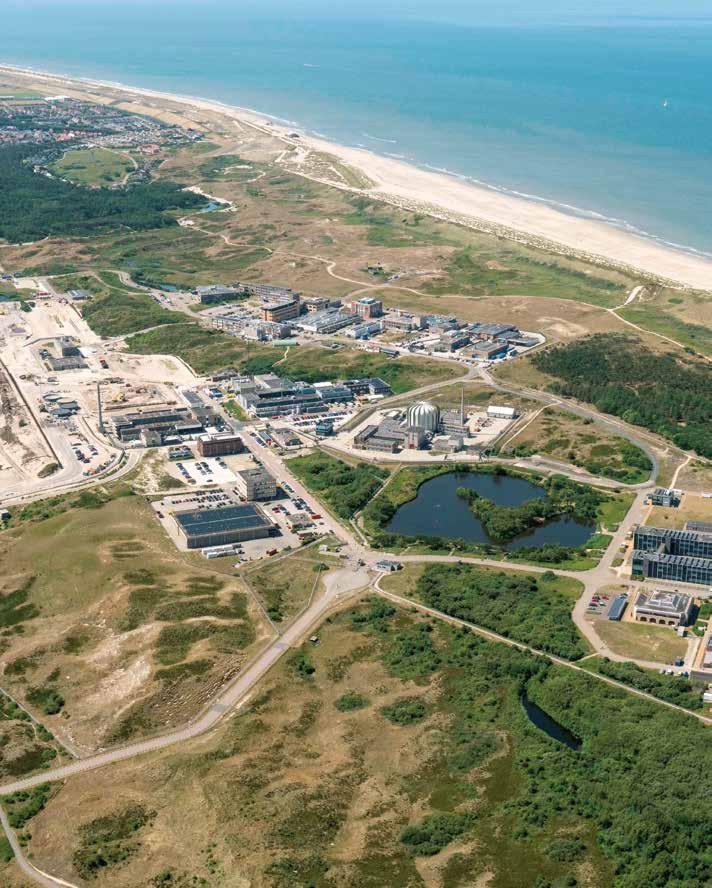
Iv werkt met een team van circa 100 man aan de realisatie van de nieuwe reactor. “Wij zijn verantwoordelijk voor de engineering en ondersteuning van de conventionele systemen die de operatie van de reactor mogelijk maken”, vertelt André van Es, senior projectmanager bij Iv. Dit omvat nucleaire en conventionele HVACsystemen, tap-, afval- en regenwatersystemen, building management systeem, nucleaire afvalwatersystemen, gedemineraliseerd water, persluchtsystemen, industriële gassen en secundaire koelsystemen. “Zonder deze systemen zou het proces niet kunnen plaatsvinden. Daarmee zorgen wij ervoor dat alles wat rondom de reactor nodig is goed functioneert, zodat de productie van medische isotopen betrouwbaar en veilig verloopt.”
Bij een nucleaire reactor is het belangrijk om voor de luchthuishouding verschillende ‘zones’ te creëren om de straling binnen veilige grenzen
te houden.
Naast deze systemen is Iv ook verantwoordelijk voor alle instrumentatie, zoals temperatuur- en drukmeters, die nodig zijn om de systemen te laten werken en te communiceren met andere systemen. Dit is een belangrijke en complexe taak vanwege de vele interfaces en verbindingen die goed moeten worden afgestemd.
“Bij een nucleaire reactor is het belangrijk om voor de luchthuishouding verschillende ‘zones’ te creëren om de straling binnen veilige grenzen te houden”, zegt André. “Vanuit de binnenste zone rond de reactor, daar
waar de straling het sterkst is, mag geen lucht naar de omringende zones stromen. Daarom zorgen we ervoor dat de lucht alleen van de omringende zones naar de binnenste zone kan stromen, zodat er geen vrijzetting is van radioactieve stoffen. Dit doen we door de luchtdruk tussen de verschillende zones goed te regelen. Als er radioactieve stoffen uit de reactor ontsnappen, blijft het binnen de afgesproken zone en wordt het via speciale filters op een veilige manier afgevoerd.”
Veiligheidsnormen
Volgens André komt de ervaring van Iv met vergelijkbare technieken in de farmaceutische industrie goed van pas. Zo worden in vaccinatiefabrieken ook zoneringsprincipes toegepast om te voorkomen dat virussen ontsnappen. Naast de technische uitdagingen van zonering, is ook de logistiek rondom de reactor belangrijk. “In zo’n productieomgeving moet alles snel, veilig en efficiënt verlopen”, legt André uit. “De isotopen worden in ‘hot cells’ behandeld en verpakt. Deze cellen moeten veilig afgeschermd zijn om te voorkomen dat operators blootgesteld worden aan teveel straling. Het is essentieel dat de producten veilig van de reactor via de ‘hot cells’ naar de logistieke ruimten worden verplaatst voor transport, zonder risico op stralingsbesmetting.” André: “Stel je voor: er zijn zes hot cells voor de handling van isotopen. Voor elke cel geldt dat de juiste drukcascade onderling en ten opzichte van de omringende logistieke ruimte gewaarborgd moet zijn, zodat de lucht de juiste kant op stroomt en het risico op stralingsbesmetting binnen de normen blijft. Deze complexiteit maakt het noodzakelijk dat onze systemen goed doordacht zijn, geschikt functioneren en gewaarborgd zijn.”
Bij het ontwerp van de PALLAS-reactor moet aan strenge eisen worden voldaan om de veiligheid te waarborgen. Het belangrijkste aspect is dat alles moet worden ontworpen volgens de Kernenergiewet en de Dutch Safety Regulations for Nuclear Power Plants (DSR). Deze regelgeving zorgt ervoor dat de reactor veilig is in verschillende noodsituaties zoals aardbevingen, overstromingen en vliegtuigincidenten. André legt uit:
“Het ontwerp van de reactor moet bestand zijn tegen extreme omstandigheden. Dit betekent niet alleen dat de systemen zelf betrouwbaar moeten zijn, maar ook dat ze moeten blijven functioneren, zelfs als er een bepaalde calamiteit is. Bijvoorbeeld, als er een overstroming is, moeten de energievoorzienende systemen voor cruciale installaties, zoals de dieselgeneratoren en besturingssystemen, blijven werken om te voorkomen dat de situatie uit de hand loopt.” Ook de straling, in de directe omgeving van de reactor, is een uitdaging voor de toe te passen materialen. De nieuwe reactor moet minstens 60 jaar meegaan. Straling heeft invloed op de materialen in de reactor. Door de constante blootstelling aan straling kunnen materialen sneller verouderen of beschadigd raken. Daarom moeten alle materialen in de reactor bestand zijn tegen deze straling en zo ontworpen zijn dat ze tientallen jaren kunnen meegaan. Daarnaast moeten systemen zoals pijpen en kanalen zo ontworpen zijn dat ze regelmatig kunnen worden gereinigd en onderhouden.
Van uitdaging naar overwinning “Wat mij zo enthousiast maakt over dit project, is de enorme uitdaging van system engineering, inclusief verificatie en validatie (V-model), en informatiebeheer”, zegt André. “Het is niet alleen de technische complexiteit van de installaties die telt, maar vooral het afstemmen
van alle modellen en gegevens. We moeten bijvoorbeeld
alle 3D-modellen elke twee weken centraal beschikbaar stellen in een zogenaamde ‘Common Data Environment’ en zorgen dat ze op elkaar zijn afgestemd. Dit betekent dat we tijdens de engineering al moeten zorgen dat alle informatie over bijvoorbeeld druk, temperatuur en toegepaste materialen direct beschikbaar en aan elkaar gekoppeld is.”
André voegt toe: “Ik denk dat er geen project in Nederland is dat op deze manier probeert de informatie op elkaar af te stemmen en beschikbaar te hebben.” Wat het volgens hem extra complex maakt, is de samenwerking met verschillende (internationale) partijen en systemen die niet altijd naadloos integreren. Het is een enorme uitdaging om ervoor te zorgen dat alle informatie goed samenkomt en dat iedereen met de juiste data werkt.
Het PALLAS-project lost niet alleen de huidige problemen op, maar laat ook zien hoe we in de toekomst andere reactoren kunnen bouwen.
José vult aan: “Wanneer alle 500 systemen uiteindelijk samenwerken en tijdens de commissioning alles functioneert zoals het hoort, voelt het als het scoren van een doelpunt in een WK-finale. We hebben een cruciaal moment in het proces dat we ‘criticaliteit’ noemen. Dit betekent dat we de reactor op vermogen hebben gebracht en deze stabiel kunnen houden. Dit is een enorm moment voor ons, vergelijkbaar met het winnen van de wereldbeker. Het geeft ons de bevestiging dat de reactor werkt.” José benadrukt echter dat criticaliteit
slechts het begin is. “Na criticaliteit moeten we nog de prestaties van het systeem demonstreren. Er is nog veel werk te doen om ervoor te zorgen dat alles aan de eisen voldoet. Maar op dat moment zie je duidelijk dat het project succesvol is. Dan begint de fase van finetuning.”
De blauwdruk voor de toekomst
De PALLAS-reactor vormt niet alleen een belangrijke stap vooruit in de medische isotopenproductie, maar ook een mogelijke blauwdruk voor toekomstige reactorprojecten.
José Louis legt uit: “We creëren een virtueel model (digital twin) van de reactor om operators te kunnen trainen en operaties zo realistisch mogelijk te simuleren. Hoewel dit veel inspanning kost, helpt het om de reactor, die minstens 60 jaar mee moet gaan, veilig te beheren zonder de echte installatie te gebruiken.”
De vraag naar medische isotopen blijft maar groeien. Het PALLAS-project lost niet alleen de huidige problemen op, maar laat ook zien hoe we in de toekomst andere reactoren kunnen bouwen. Al tientallen jaren staat de
huidige PALLAS-reactor op de agenda ter vervanging van de HFR. Jan van der Marel is sinds 2016 bij dit project betrokken. “We hebben vanaf het begin veel obstakels moeten overwinnen als het gaat om vergunningen, bijvoorbeeld. Dus toen we hier aan begonnen, wisten we ook niet zeker of het zou slagen. Maar met de laatste horde, de goedkeuring vanuit het Ministerie van Volksgezondheid, is de weg vrij. Alle uitdagingen die nu nog op ons pad liggen, hebben we zelf in de hand.”
De overgang van de oude HFR-reactor naar de nieuwe PALLAS-reactor is een proces dat de komende jaren zal plaatsvinden. Gedurende een periode van circa 2 jaar zullen beide reactoren draaien om ervoor te zorgen dat de productie van medische isotopen ononderbroken doorgaat. Nadat de PALLAS-reactor zijn volle capaciteit heeft bereikt, zal de HFR uit bedrijf worden genomen. Volgend jaar zal begonnen worden met de constructie van de nieuwe medische isotopenreactor in Petten. Als alles volgens plan verloopt, is de PALLAS-reactor omstreeks 2030 gereed. ●
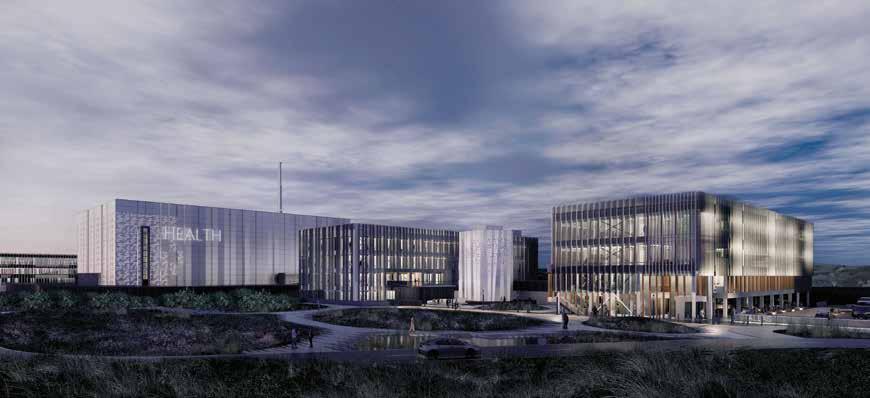
Grip op onzekerheden houdt de
V&R-opgave behapbaar
In ons land ligt voor circa 347 miljard euro aan infrastructuur. Een groot deel hiervan is in de decennia na de Tweede Wereldoorlog gebouwd en zou zo’n 60 tot 80 jaar mee moeten gaan. Het gebruik ervan is echter geïntensiveerd en vaak zwaarder belast dan destijds bij de bouw voorzien. Veel bruggen, sluizen, kademuren en tunnels zijn dan ook (bijna) aan het einde van de levensduur. De komende 75 jaar is liefst 260 miljard euro nodig om de vernieuwings- en renovatieopgave (V&R) te bekostigen. De verwachting is dat deze kosten de komende jaren al flink stijgen. Maar is deze miljardenuitgave écht noodzakelijk? Of kunnen we de kosten terugdringen en uitsmeren over een langere periode?
Kosten stijgen met miljarden Bovengenoemde kostenraming komt uit het 2e Landelijk
Prognoserapport Vernieuwingsopgave Infrastructuur dat TNO eind 2023 publiceerde. Op verzoek van de Rijksoverheid, het Interprovinciaal Overleg en Vereniging
Nederlandse Gemeenten bracht TNO de omvang van de vernieuwingsopgave in Nederland, na een eerste versie in 2021, opnieuw in kaart. Het in kaart brengen van de vernieuwingsopgave op landelijk niveau is een grote uitdaging vanwege de grote hoeveelheid beheerders en de gewenste informatie, die lang niet altijd beschikbaar is. De prognose is dan ook onvermijdelijk met onzekerheid omgeven, daarover later meer.
Volgens het 2e Landelijk Prognoserapport stijgen de verwachte jaarlijkse kosten voor provincies, gemeenten en andere overheden tussen nu en 2040 naar bijna 3 miljard euro. Dit is veel meer dan begroot. De verwachting is dat de jaarlijkse vernieuwingskosten vanaf 2040 verder stijgen naar circa 3,7 miljard euro aan
het eind van deze eeuw. De vernieuwingsopgave van de civiele constructies bepaalt het grootste deel van de kosten. Deze neemt toe van 1,5 miljard euro per jaar tot circa 2,6 miljard euro in 2080.
We maken constructieve beoordelingen van bruggen en kademuren ter bepaling van de constructieve veiligheid en restlevensduur van de objecten.
En dus heerst er onrust bij beheerders en eigenaren van civiele constructies: want wat moet er precies gebeuren, hoe urgent is het probleem en hoe gaan we dit betalen?
Op het eerste gezicht terechte vragen.
Verder kijken
Om deze vragen te kunnen beantwoorden moeten we letterlijk verder kijken dan de beoogde (ontwerp) levensduur van elk van de constructies. In haar 2e

prognoserapport gaat TNO in alle gevallen uit van eenop-een vervanging na het bereiken van de verwachte (gemiddelde) levensduur van een constructie. Hierbij is geen rekening gehouden met groei of verandering van de functionaliteit van het areaal, zoals intensiever gebruik of een andere inrichting, of eventuele mogelijkheden voor het (circulair) verlengen van de levensduur. Het TNOonderzoek heeft logischerwijs ook de werkelijke kwaliteit van het areaal niet meegenomen, noch de mogelijkheid tot het monitoren van de actuele staat ervan om de vervangingsmomenten nauwkeuriger vast te stellen en hopelijk uit te stellen. Tot slot is er vanzelfsprekend sprake van veel onzekerheid bij het prognosticeren van de totale V&R-opgave.
We merken in discussies over deze prognoses dat aan bovengenoemde vereenvoudigingen en onzekerheden vaak voorbij wordt gegaan. In het licht van het doel van het prognoserapport zijn deze vereenvoudigingen en onzekerheden begrijpelijk, maar juist daar ligt een belangrijke sleutel tot het behapbaar maken van de V&Ropgave: grip krijgen op de onzekerheden.
Iv grijpt daarom juist hier de kansen om de pijn van de V&R-opgave te verzachten. Dit doen we al vele jaren. Zo maken we constructieve beoordelingen van (arealen van) bruggen en kademuren ter bepaling van de constructieve veiligheid en restlevensduur van de objecten. We doen dat risicogestuurd, van grof naar fijn: op hoofdlijnen waar het kan (bijvoorbeeld met quickscans), en we halen het uiterste uit de constructie als het moet (met inspecties, onderzoeken en berekeningen). Zo zorgen we voor maximale grip met minimale inspanning. We hebben hierdoor al veel constructies ‘van de ondergang’ kunnen redden. De constructieve veiligheid van een object kan veel groter zijn dan op grond van een ‘standaard’
berekening kan worden aangetoond. Dit is iets wat ook menige, door ons ontwikkelde en uitgevoerde, proefbelasting heeft aangetoond.
Wij spreken liever van de instandhoudings-, renovatie- en vernieuwingsopgave: vervangen als het moet, instandhouden als het kan.
Een oproep aan alle beheerders: koester uw kunstwerken! Want in veel gevallen is de constructieve veiligheid – en daarmee dus vaak ook de restlevensduur – beter dan verwacht. De soep wordt dus zeker niet altijd zó heet gegeten: het object blijkt dan zonder of met relatief
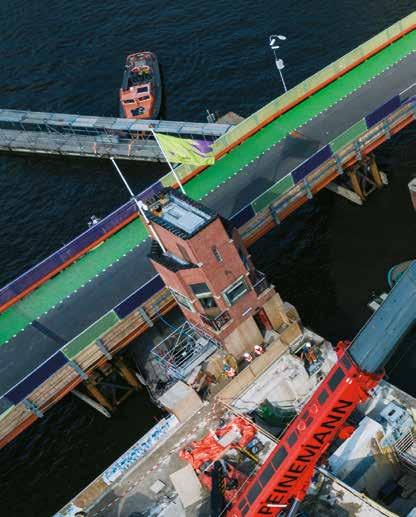
beperkte aanpassingen nog tientallen jaren mee te kunnen, veel langer dan de ontwerplevensduur. In andere gevallen kunnen maatregelen verantwoord worden uitgesteld wanneer monitoring wordt toegepast. Met een uitgebreid palet aan assetmanagementdiensten zorgen we ervoor dat beheerders dat gewenste inzicht in hun areaal krijgen en houden en daarop ook een optimale meerjarenplanning kunnen maken voor het onderhoud of de vervanging van hun infrastructuur. Vervanging is niet het eerste waar we aan moeten denken als een constructie het einde van z’n levensduur nadert: er is zoveel meer mogelijk. We spreken dan ook liever van de instandhoudings-, renovatie- en vernieuwingsopgave: vervangen als het moet, instandhouden als het kan.
De opgave behapbaar maken
Voor Rijkswaterstaat is Iv samen met ARUP en Wagemaker bezig met het in kaart brengen van de constructieve staat van tientallen vaste en beweegbare bruggen in het hoofdwegennet. Aan ons als ingenieursbureau de uitdaging om met de juiste aanpak de juiste keuzes te maken. Indien nodig, en als het verantwoord is, proberen we het uiterste uit de constructie te halen. Zo kunnen fysieke maatregelen verantwoord worden geminimaliseerd en uitgesteld, waarbij de constructieve veiligheid te allen tijde gewaarborgd blijft. Op deze manier dragen we bij aan het reduceren van de hoge maatschappelijke kosten voor de infrastructuur én daarmee belasting voor ons milieu. Zo blijft de instandhoudings-, renovatie- en vernieuwingsopgave voor ons allemaal behapbaar. ●
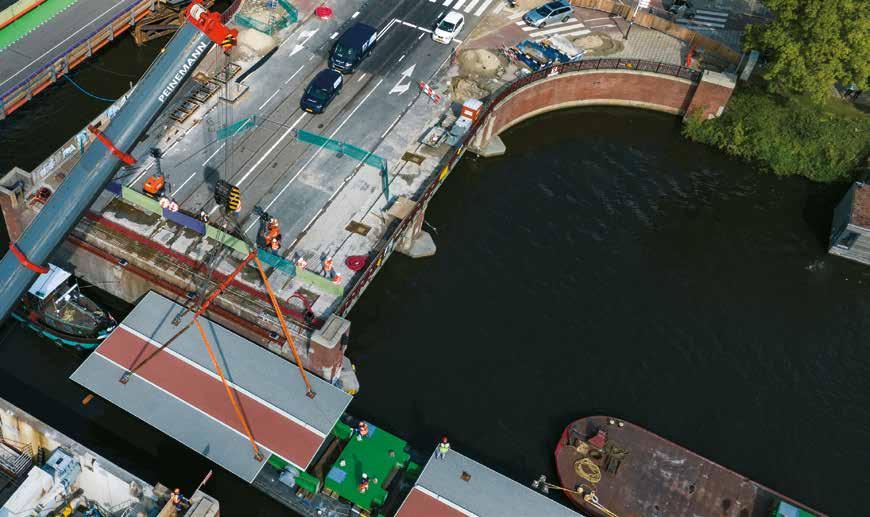
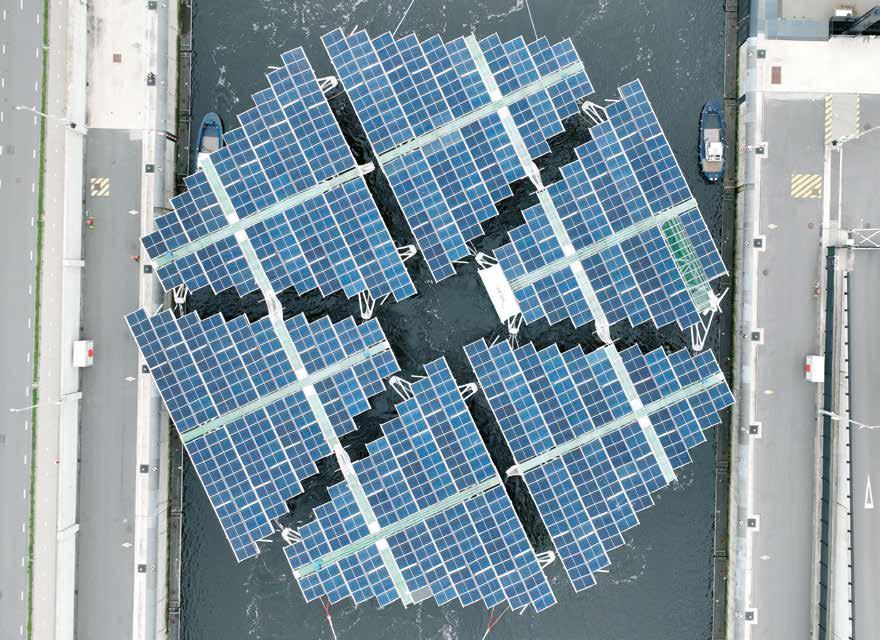
De realisatie van ’s werelds grootste drijvende solarplatform
In het Nederlandse offshore windpark Hollandse Kust West (HKW) VII, op zo’n 53 kilometer uit de kust bij IJmuiden, gaat de combinatie Totalenergies/RWE een nieuwe, duurzame energieopwekking ontwikkelen. Als onderdeel hiervan wordt ’s werelds grootste drijvende solarplatform geïntegreerd naast energieopwekking door wind. Het drijvende solarplatform komt tussen de windmolens in te liggen en is een innovatieve oplossing, bedacht door het NederlandsNoorse bedrijf SolarDuck. Het platform zal bestaan uit drijvende, aan elkaar geschakelde, driehoekvormige constructies met zonnepanelen. SolarDuck selecteerde Iv om het innovatieve concept technisch verder uit te werken en te optimaliseren, zodat het conform alle eisen op zee kan worden geïnstalleerd en gebruikt.
Het drijvende solarplatform
Het drijvende solarplatform dat in het HKW VII windmolenpark komt, is gebaseerd op dat van het Merganser testplatform. Een prototype solarplatform met een energieopwekkingsvermogen van 520 kWp (kilowatt piek) dat als pilot op 12 kilometer vanuit de kust in Scheveningen in de Noordzee is geïnstalleerd. De vaak barre Noordzee-omgeving waarin het HKW VII windpark ligt, wordt gezien als een van de meest uitdagende offshore-omgevingen ter wereld. Iv ondersteunt
Solarduck met offshore-kennis en ervaring bij het optimaliseren van het bestaande ontwerp voor deze bijzondere condities.
In
barre omstandigheden op zee zijn constructies onder andere onderhevig aan vermoeiing en corrosie.
Doordat het platform tussen de windmolens in wordt aangelegd, wordt de ruimte op zee zo efficiënt mogelijk benut en kan het netsysteem, dat toch al is aangelegd voor het windpark, ook worden gebruikt om de opbrengst aan elektriciteit te transporteren naar land. Ook kan onderhoud aan beide energiesystemen gecombineerd plaatsvinden.
Wereldwijd veel potentie
De mogelijkheid om op land meer grote zonneparken te realiseren in dichtbevolkte gebieden neemt af. Tegelijkertijd wordt de vraag naar duurzame energie alleen maar groter. Deze trend zal zo blijven. Het drijvende solarplatform is een oplossing om landen wereldwijd te helpen elektrificeren en leveringszekerheid
van betaalbare, duurzame energie te bieden. Vooral in landen met een hoge bevolkingsdichtheid, waar gemiddeld lagere windsnelheden zijn en juist een hogere instraling van zonne-energie, is het een zeer geschikte oplossing om het aanbod duurzame energie te vergroten.
Van idee naar zee
Vijf jaar geleden is SolarDuck met dit idee gestart. Maar hoe krijg je zo’n innovatieve oplossing werkend op zee? Hoe realiseer je een betrouwbare constructie die minimaal 30 jaar onderhoudsvrij operationeel kan zijn? En hoe zorg je ervoor dat het gehele project veilig offshore geïnstalleerd kan worden? Naast de algehele technische optimalisatie van het ontwerp adviseert Iv SolarDuck over de hydrodynamica (de bewegingen van de constructie door de golven), het afmeren en de installatie. Ook zorgt Iv ervoor dat het ontwerp wordt goedgekeurd door het classificatiebureau. In barre omstandigheden op zee zijn constructies onder andere onderhevig aan vermoeiing en corrosie. Daarnaast moet de constructie de bewegingen van de golven goed kunnen opvangen, zodat de systemen op de constructie (zoals de zonnepanelen en subsystemen) niet beschadigen. Iv is als ingenieursbureau gespecialiseerd in dergelijke vraagstukken.
Er wordt veel van onze creativiteit gevraagd om het technisch, financieel en qua veiligheid haalbaar te maken.
“Het is natuurlijk heel gaaf om mee te werken aan de ontwikkeling van nieuwe technologie”, vertelt Pieter de Boer, lead engineer bij Iv. “Een zonnepark op zee, volledig functionerend en op deze afstand is iets wat nog niet
eerder is gedaan. Technisch is het heel uitdagend en complex. Er wordt veel van onze creativiteit gevraagd om het technisch, financieel en qua veiligheid haalbaar te maken.”
Simuleren
Maar wat maakt het dan zo complex? Natuurlijk, iets nieuws bedenken is per definitie geen makkelijke opgave.
Onder andere het ‘gedrag’ van alle diverse platformen van het zonnepark is bijzonder en een belangrijk aspect.
Pieter: “Deze hebben allemaal tot op zekere hoogte invloed op elkaar. Het op de goede manier simuleren van het gedrag brengt best wat uitdagingen met zich mee.
Verder speelt ook mee dat er van tijd tot tijd mensen aanwezig zijn op het platform. We willen natuurlijk dat zij zo veilig mogelijk hun werk kunnen doen. Dus dat moeten we meenemen in het ontwerp.”
Momenteel is Iv bezig met onderzoeken hoe het zonnepark er uiteindelijk uit komt te zien, bijvoorbeeld qua aantal platforms, de lay-out en de exacte locatie. Het is de verwachting dat het drijvende zonnepark in 2026 gereed is. ●
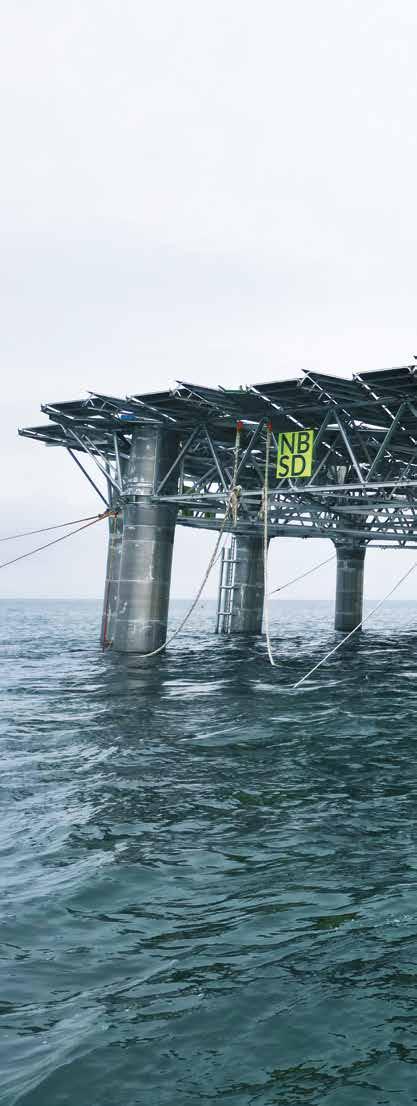
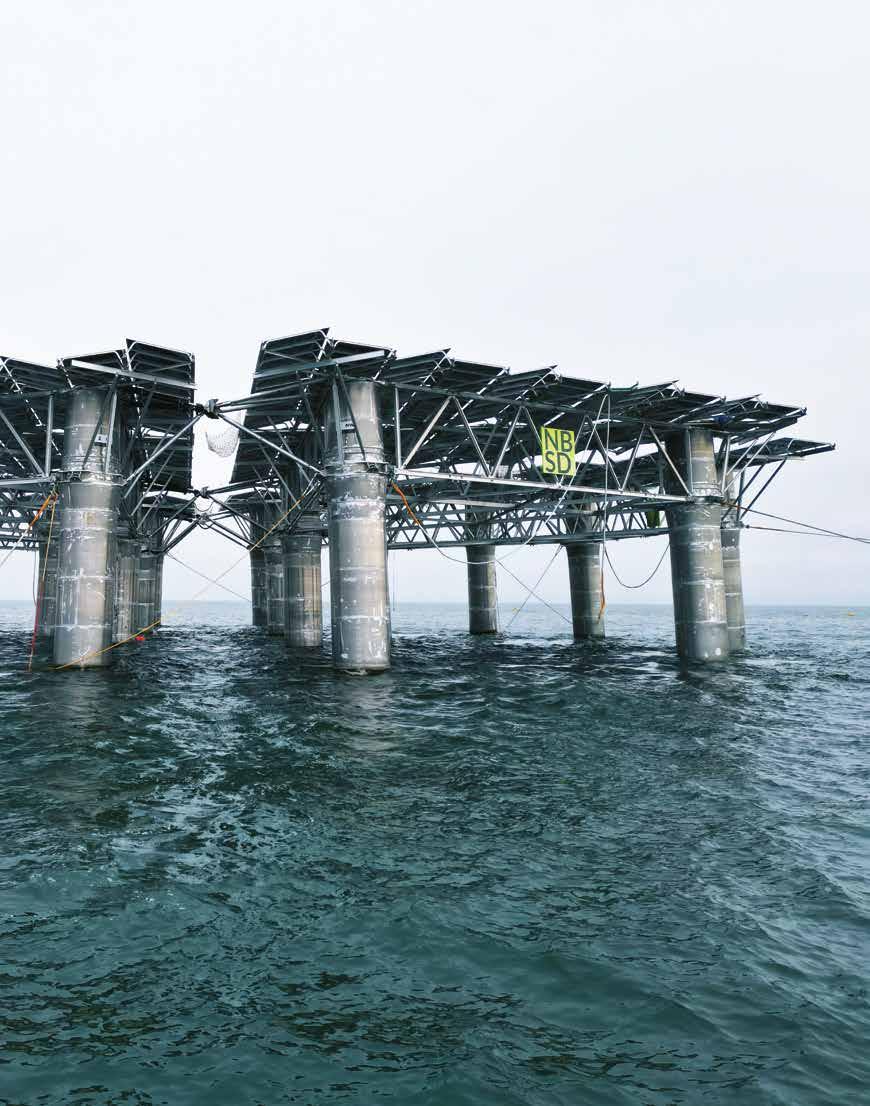

Verduurzamen van de zware
industrie
Staal is overal om ons heen. Van auto’s, schepen en treinen tot gebouwen en producten zoals batterijen en koelkasten. We kunnen ons leven zonder dit materiaal nauwelijks meer voorstellen.
Terwijl staal ons dagelijks leven ondersteunt, brengt het ook een serieuze uitdaging met zich mee. De gehele productieketen van staal, van de inwinning van grondstoffen tot en met de productie van stalen producten, stoot grote hoeveelheden CO2 uit. De vraag is dan ook: hoe kunnen we staal produceren zonder onze planeet verder te schaden? Hier komt Iv in beeld. Iv biedt ondersteuning aan producenten in de gehele keten om hun toekomstige productie te vergroenen en te verduurzamen. Bovendien helpt Iv om deze noodzakelijke transitie te versnellen.
Waarom staat de zware industrie onder druk om te vergroenen?
Binnen de zware industrie wordt in bijna de gehele keten aanzienlijke hoeveelheden CO₂ uitgestoten. Dit komt doordat traditionele onderdelen van de zware industrie, zoals bijvoorbeeld het staalproductieproces met behulp van een ‘Blast furnace’ (Hoogoven) gekoppeld aan een ‘Basic Oxygen Furnace’ (Oxystaalfabriek), grote hoeveelheden CO2 en andere emissies uitstoten en zeer energie-intensief zijn. Door de strenger wordende EU-emissiedoelen en steeds hogere eisen van klanten, moeten staalproducenten hun processen grootschalig aanpassen. Tegelijkertijd moeten ze de kwaliteit waarborgen. Dit geldt niet alleen voor de staalproducenten: dit geldt voor de gehele keten van de zware industrie. Dit zijn zeer grote uitdagingen, omdat de nieuwe processen nog niet de kwaliteit en hoeveelheden kunnen produceren die de bestaande processen inmiddels hebben bereikt. De industrie moet veel geld en tijd investeren in vergroeiende technologieën om aan de wetgeving en verwachtingen van de samenleving
te voldoen. De grootste uitdaging? Het behalen van de nieuwe emissie-eisen, zoals het verminderen van de CO₂uitstoot, zonder concessies te doen aan de kwaliteit en productiehoeveelheden.
Het probleem blijft groeien, omdat mensen nu drie keer zoveel consumeren als vijftig jaar geleden.
Rick de Jong, directeur Heavy Industries bij Iv, legt het zo uit: “Staal is op zich al een heel duurzaam product, omdat het 100% en oneindig vaak recyclebaar is. Het kan dus steeds opnieuw gebruikt worden met behoud van zijn eigenschappen en dus ook van de oorspronkelijke kwaliteit en sterkte. Staal is daarom één van de meest gebruikte materialen ter wereld, vanwege zijn veelzijdigheid in combinatie met relatief lage kosten.
Het probleem ligt echter in het productieproces. IJzererts wordt uit de grond gehaald en in een hoogoven omgezet in vloeibaar ijzer. Tijdens dit proces worden ijzererts,
kooks en kalksteen met zuurstof samengevoegd. Dit proces stoot grote hoeveelheden CO2 uit. Daarnaast maken de unieke eigenschappen van staal het moeilijk om het een-op-een te vervangen. Staal is extreem sterk en veelzijdig, waardoor het een materiaal is voor talloze toepassingen. Dit betekent dat, zelfs als er alternatieve materialen worden ingezet, je veel meer volume van dit vervangende materiaal moet hebben om aan dezelfde eigenschappen te voldoen, wat de milieu-impact niet noodzakelijk verkleint. Daarom is het heel belangrijk om nieuwe en duurzame manieren te vinden om staal te produceren, die het milieu minder belasten en de unieke eigenschappen van staal behouden.”
Sleutelrol
Het is dus duidelijk: de zware industrie moet duurzamer en groener worden. In de hedendaagse zoektocht naar deze verduurzaming speelt Iv een sleutelrol. Hoe?
Iv biedt de zware industrie ondersteuning om hun verduurzaming en vergroening te versnellen. Rick: “Onze aanpak is tweeledig. We moeten nu aanpassingen aan
het bestaande proces doorvoeren om direct al resultaat te behalen. Tegelijkertijd moeten we ook naar de nabije toekomst kijken. Hoewel we de industrie al op bepaalde plekken hebben vergroend, blijft het probleem groeien, omdat mensen nu drie keer zoveel consumeren als vijftig jaar geleden.”
De kracht van Iv ligt in zijn kennis en ervaring in de procesoptimalisatie. “We weten letterlijk hoe het in de praktijk werkt en waar het naartoe moet. Op papier lijken processen altijd perfect ontworpen en te werken, maar de realiteit is dat het vaak jaren kan duren voordat alles goed op elkaar is afgestemd en de gewenste resultaten oplevert. Al sinds onze oprichting, 75 jaar geleden (1949), werken we voor de staalindustrie. Onze praktische kennis en ervaring in combinatie met een pragmatische benadering helpen onze opdrachtgevers om hun processen effectief te optimaliseren.” Iv heeft niet alleen ervaring in de staalindustrie, maar ook in andere sectoren zoals de maak- en energie-industrie . Ondanks dat er verschil is tussen deze sectoren, is de aanpak voor
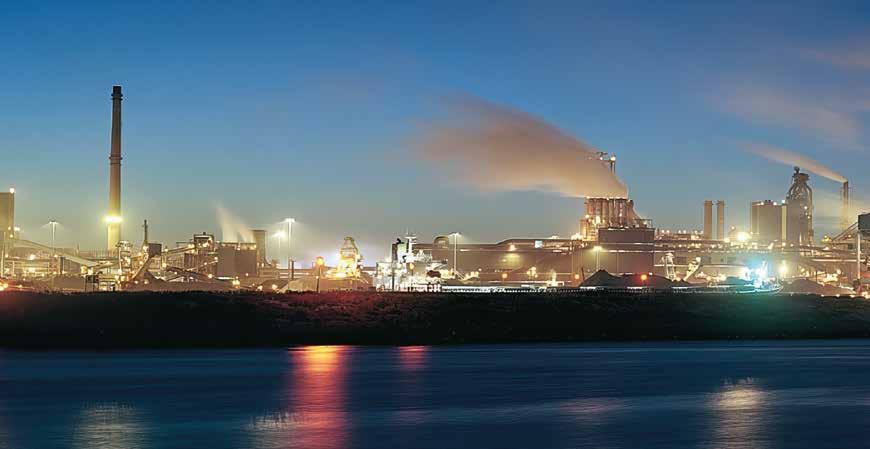
verduurzaming vaak vergelijkbaar. Deze kennis stelt ons in staat om op maat gemaakte oplossingen te bieden die niet alleen de huidige processen verduurzamen, maar ook toekomstige innovaties integreren.
Re-use, remanufacturing en recycling worden steeds belangrijker in de toekomst.
Naast de ruim 75 jaar kennis en ervaring in de zware industrie, werkt Iv de laatste 10 jaar al wereldwijd op grote schaal aan verduurzaamings-, emissieverlagendeen vergroeningsprojecten binnen de industrie. Hiermee heeft Iv een unieke voorspong opgebouwd in plant design en systeemintegratie van toekomstbestendige en ‘groene’ installaties en productieplants.
Verduurzamen van de hele keten
De staalproductie omvat verschillende stappen om van ijzererts eerst ijzer en daarna staal te maken. Het geproduceerde staal wordt vaak verder verwerkt tot
balken en coils voor de volgende productiestap. Naast de staalproductie zelf, is er ook bij down- en upstream veel te doen. Iv heeft ervaring binnen alle onderdelen van deze keten.
Het verduurzamen van de zware industrie begint bij de basis: het winnen van grondstoffen. Dit proces is vaak vervuilend. Bij het delven van grondstoffen in de mijnen en de op- en overslag komen veel schadelijke emissies vrij. De laatste jaren is er al veel tijd en energie besteed om deze stap te verbeteren, binnen Europa lopen we hier echt wel voorop. “In de toekomst zullen kolen langzamerhand plaatsmaken voor waterstof. Dit zal helpen om de CO₂-uitstoot aanzienlijk te verminderen”, vertelt Rick. In deze procestransitie zullen nieuwe installaties, zoals een DRI-plant (Direct-Reduced Iron) met daaraan gekoppeld een EAF (Electric Arc Furnace) eerst op gas en elektriciteit uit wind draaien. Zodra deze processen goed functioneren, zal in een tweede fase de stap naar waterstof worden gemaakt. Iv heeft unieke ervaring met de productie van DRI in de vorm van HBI
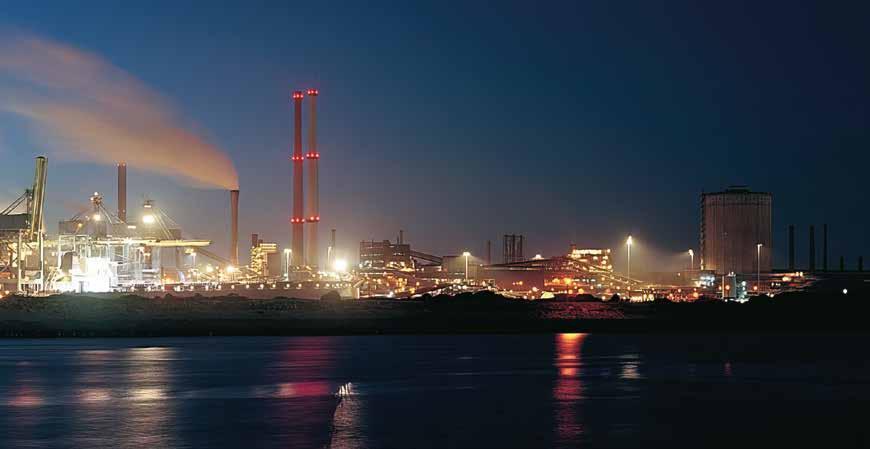
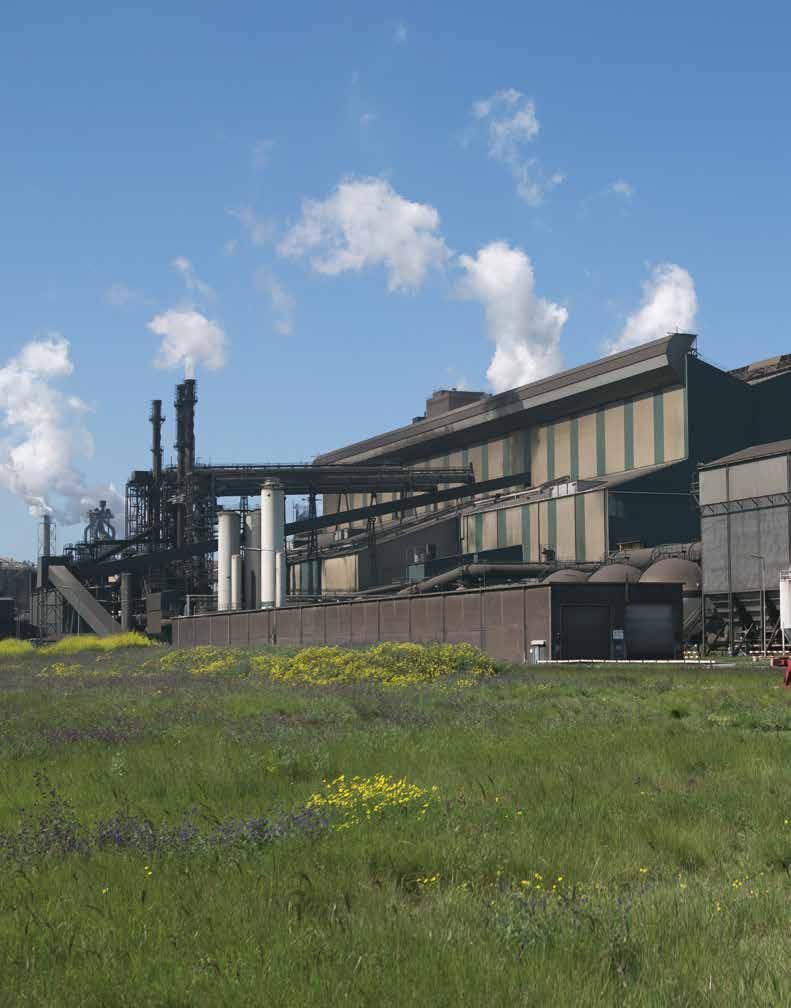
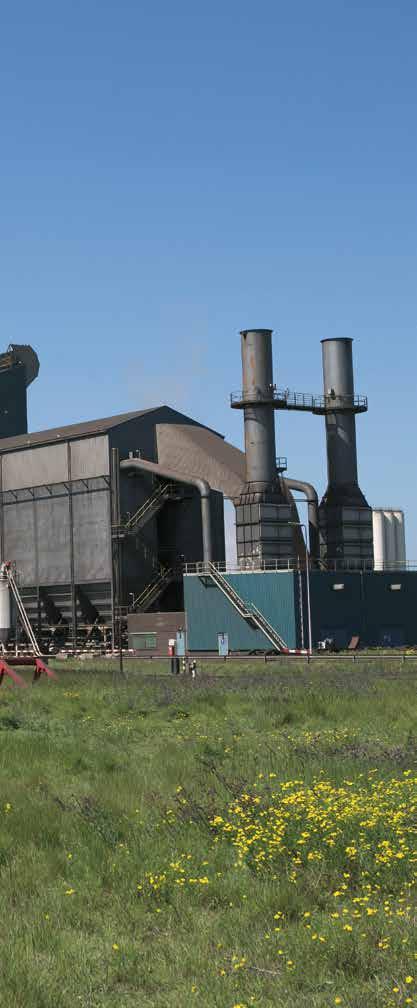
(hot briquette iron) en alles wat daarbij komt kijken. In Texas draait een DRI-plant waarvoor Iv zowel het primaire productieproces als het secundaire proces zoals screening en op- & overslag heeft geoptimaliseerd.
In het kader van duurzaamheid is Iv ook betrokken bij het hergebruik van staal. Re-use, remanufacturing en recycling worden steeds belangrijker in de toekomst. Na de zogenaamde gebruiksfase van staalproducten, zoals koelkasten, wordt het staal ingezameld en klaargemaakt voor hergebruik. Dit proces omvat het verwijderen van zink- en verflagen en andere materialen voordat het staal opnieuw kan worden verwerkt. Al in 1999 speelde Iv een belangrijke rol bij het ontzinken van staal, dat vrijkwam als rest- en afvalmateriaal bij het stansen van carrosserieonderdelen in de automobielindustrie.
Kortom, of het nu gaat om het optimaliseren van productieprocessen of het verbeteren van de logistiek periferique rondom installaties en grondstoffen:
“We helpen bij het ontwerpen van fabrieken, zodat grondstoffen efficiënter en emissieloos worden aangeleverd en er minder transport nodig is. Dit vermindert het energieverbruik en de vervuiling, wat direct bijdraagt aan een schonere wereld”, aldus Rick.
Het
sluiten van fabrieken is geen oplossing; we moeten investeren in de verduurzaming ervan.
Toekomstperspectief
De wereld van materialen, technologieën en productiemethoden verandert de laatste jaren razendsnel; honderd jaar geleden waren er geen kunststof, koolstofvezels of 3D-printbare materialen. Wat toen nog onmogelijk leek, is nu werkelijkheid en
het einde is nog lang niet inzicht. En deze vooruitgang gaat alleen nog maar sneller door. Rick vertelt over de toekomstige mogelijkheden: “Er worden nu al plannen gemaakt om materialen van andere planeten af te halen. Hoewel dat nog ver weg lijkt, kunnen we over 20 tot zeg 30 jaar echt die kant op kijken.” Ook dichter bij huis zijn er kansen. Bijvoorbeeld in Scandinavië (Zweden) liggen nog grote hoeveelheden onbenutte grondstoffen en kansen om in de toekomst op een duurzame en groene manier de industrie voort te zetten.
“Wat ik belangrijk vind, is niet alleen dat we al deze veranderingen doorvoeren voor onszelf of onze kinderen, maar dat we dat voor de kinderen van onze kinderen en verder doen. Als we nu niet handelen, zullen we de impact van onze keuzes in de toekomst echt voelen. Het is niet zomaar een kwestie van vandaag of morgen, het gaat om de wereld die we achterlaten.”
Door in bouwteams samen te werken, kunnen we veel grotere en slimmere oplossingen bedenken en realiseren dan we ooit alleen zouden kunnen.
Terwijl we de noodzaak van duurzame verandering erkennen, is er nog veel werk aan de winkel. Om deze transitie daadwerkelijk te realiseren en draaiende te houden, is er meer nodig dan alleen een mindset. Het sluiten van fabrieken is geen oplossing; we moeten investeren in de verduurzaming ervan. Dit betekent niet alleen het doorvoeren van technische innovaties en het verder ontwikkelen van nieuwe materialen, maar ook het durven veranderen van bestaande processen. “Het is essentieel om de schouders eronder te zetten en te
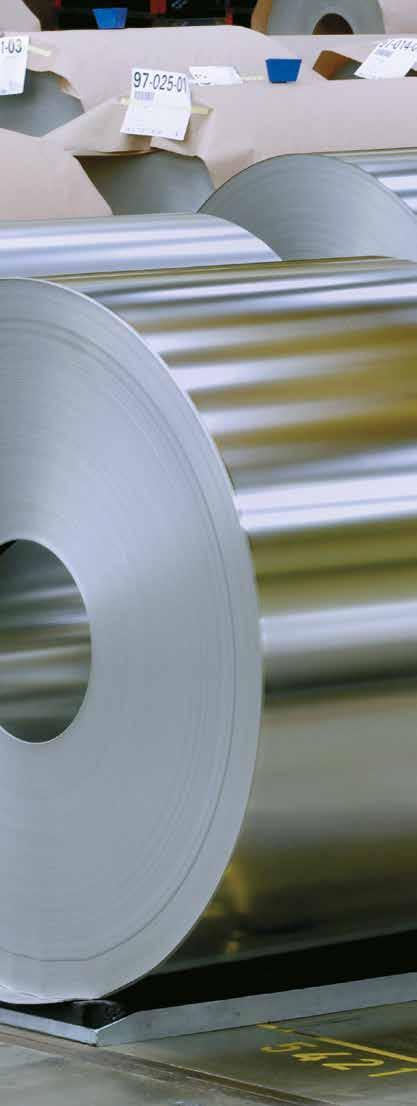

investeren in duurzame oplossingen. We moeten ervoor zorgen dat we de industrie ombuigen naar een duurzame en toekomstbestendige groene industrie, zonder te stoppen”, benadrukt Rick.
Rick is optimistisch over de toekomst: “Ik geloof dat we op den duur zelfs onze duurzaamheidsdoelen kunnen gaan inhalen en positief kunnen bijstellen, maar zover zijn we nu nog niet. Hoewel het misschien nu nog als verre toekomst lijkt, ben ik ervan overtuigd dat de mindset van vandaag, dat we moeten veranderen, als een vliegwiel zal gaan werken. Doelen zijn als een stip aan de horizon die ons richting geeft. Maar naarmate we die richting opgaan, zullen we steeds sneller vooruitgang moeten gaan boeken.”
Bouwteams
Rick benadrukt ook het belang van samenwerking: “De projecten worden zo groot en complex dat ze niet door één enkel bureau, ook Iv niet, kunnen worden opgelost. Daarom geloof ik in sterke samenwerking tussen bedrijven. Samen kunnen we de uitdagingen beter aanpakken dan alleen. Ik ben een groot voorstander van het werken in bouwteams. Dit is essentieel om zowel grote uitdagingen als risicovolle projecten effectief aan te pakken. Als Iv doen wij het beginwerk, het ontwerpen, maar daarna komen fabricage, installatie, gebruik en onderhoud om de hoek kijken. Allemaal belangrijke fases die vertegenwoordigd moeten worden en waarvoor ontwerpcriteria goed moeten worden bepaald en afgewogen. Door in bouwteams samen te werken, kunnen we veel grotere en slimmere oplossingen bedenken en realiseren dan we ooit alleen zouden kunnen. Samen zorgen we ervoor dat alles wat we bedenken ook echt tot leven komt.” ●

Wij zijn Iv. Wij zijn engineers. Engineers die de meest complexe vraagstukken oplossen. De grootste uitdagingen van deze tijd. Onze specialisten bedenken oplossingen voor de energietransitie. Voor het veranderende klimaat. Voor een veilige en toekomstbestendige samenleving. Zo ontwerpen we offshore windplatforms. Onderzeeboten. Maar ook de grootste sluizen ter wereld. Eigenlijk alles wat vraagt om hoogwaardige technische kennis. Geen ander ingenieursbureau is zó divers. Wij komen tot resultaten waar onze samenleving écht iets aan heeft. Dat noemen wij Engineering that excites.
www.iv.nl