
15 minute read
Vergelijking methoden om de hardheid van thermisch gespoten deklagen te bepalen
Voorkom discussies over meetresultaten door duidelijkheid over meetmethode
Vergelijking methoden om de hardheid van thermisch gespoten deklagen te bepalen
Bij thermisch gespoten deklagen speelt de verkregen hardheid van de deklaag een grote rol. Voor applicateurs is het meten van de hardheid zeer zinvol om na te gaan of men wel de juiste procesparameters hanteert. Er zijn meerdere meetmethoden om de hardheid te bepalen, maar regelmatig ontstaan over de meetresultaten vervelende discussies. Dit komt veelal door een gebrek aan kennis over de meetmethoden, het verschillende gebruik daarvan en/of door een verkeerde aanduiding van de meetresultaten. Tijd dus om het één en ander op een rijtje te zetten.
Een harder materiaal laat een kras achter op een zachter materiaal. Dat zal niemand verbazen, maar een verdere uitwerking daarvan is voor het eerst in 1812 vastgelegd door de Duitse mineraloog Friedrich Mohs (1773-1839). Dit resulteerde in de natuurlijke hardheidsschaal van Mohs, een schaal van 1 tot en met 10, waarbij 1 talk is en 10 diamant. Deze schaal is vaak toegepast bij het karakteriseren van mineralen.
VERSCHILLENDE HARDHEIDSMETHODEN In de metallurgie worden andere hardheidsmethoden toegepast. De bekendste daarvan zijn de Brinell-hardheid, Rockwellhardheid en Vickers-hardheid. Het principe van al deze methoden is dat een gedefinieerd indruklichaam met een bepaalde kracht op een oppervlak wordt gedrukt, waarbij de grootte van de indrukking een maat is voor de hardheid van het te meten materiaal. Om afwijkingen in de gemeten hardheid te voorkomen, moet men dezelfde parameters hanteren betreffende indruklichaam, laadgewicht en indruktijd. Daarbij houdt men één van de genoemde hardheidsmethoden aan.
Bij Brinell is het indruklichaam een geharde stalen kogel, bij Rockwell meestal een diamanten kegeltje en bij Vickers een vierzijdige piramide van diamant. Alle methoden laten een indrukking achter op het te meten oppervlak en zijn derhalve destructieve meetmethoden. Ze zijn dus goed te gebruiken bij schadeonderzoek, maar indrukkingen of krassen zijn uiteraard niet gewenst op nieuwe producten waarvan men echter wél vooraf de hardheid wil controleren. Daarnaast moet men meestal een preparaat van het materiaal hebben om met de genoemde methoden de hardheid te bepalen. Dit in verband met de grootte/omvang van de apparatuur (voor een uitgebreide beschrijving van genoemde testen, zie bijvoorbeeld Wikipedia).
HB, HRB, HRC EN HV Bij HB, Hrb of Hrc en Hv (zie kader Afkortingen) moeten zowel het indruklichaam als de kracht en tijd gedefinieerd zijn om de juiste vergelijkingen te kunnen maken. Maar het kenmerkende verschil tussen de hardheden van Brinell, Rockwell en Vickers is dat HB en Hr macrohardheidsmetingen zijn waarbij op het oppervlak wordt gemeten, terwijl de HV-hardheidsmeting een microhardheidsmeting is waarbij loodrecht in het oppervlak wordt gemeten.
Voordat men de hardheid van een aangebrachte thermisch gespoten deklaag op niet-destructieve wijze kan bepalen, moet eerst een proefplaatje worden gespoten, onder dezelfde operationele condities als bij het feitelijk aanbrengen van de gekozen deklaag. Vaak worden hiervoor proefplaatjes aan het werkstuk gemonteerd, die vervolgens in een polymeer worden inge-
AFKORTINGEN HB = hardheid Brinell Hrb = hardheid Rockwell ball Hrc = hardheid Rockwell cone Hv = hardheid Vickers
bed en gepolijst. De proefplaatjes kunnen ook gebruikt worden om de structuur van de deklaag te bepalen, alsmede de porositeit. De hardheid wordt bepaald met de hardheidsmethode van Vickers volgens de International Standard NEN-EN-ISO 6507-1. Om de resultaten van metingen onderling met elkaar te kunnen vergelijken, moet het gebruikte indruklichaam zijn gedefinieerd, evenals de indrukkracht en tijdsduur. De indrukking in de deklaag, in dit geval de lengte van de diagonaal, is bepalend voor de hardheid van de deklaag. Te verwachten is dat bij een indrukkracht van 50 gram de diagonaal kleiner is dan bij een indrukkracht van 300 gram waarbij de lengte van de diagonaal groter is. Hoe groter de indrukking bij een bepaalde indrukkracht, hoe groter de gemeten diagonaal en hoe zachter het materiaal is. Een veel gemaakte fout in de praktijk is dat van de deklaag verschillende hardheidswaarden worden weergegeven – en dan krijg je vaak
D
D
Rockwell Ball
Stalen bol
D
te testen materiaal h D
F Vierkantige piramide in diamant met basishoek 136º
136º F
te testen materiaal
Brinell
afdruk d1
d2
Vickers
d
d1 d2
136º h
Een vierzijdige piramide van diamant als indruklichaam onder een hoek van 136º. Op beide foto’s gaat het om dezelfde HVOF gespoten deklaag van WcCoCr. Om de hardheid te meten, is hetzelfde indruklichaam gebruikt, maar met een ander laadgewicht wat resulteert in een verschil in indrukdiepte (diagonaal) en dus in een andere gemeten hardheid.


discussie. Meestal is de oorzaak dat er met verschillende indrukkrachten gemeten wordt. Dit is te voorkomen door een juiste weergave van de meetmethode op de tekening. Met andere woorden: daarop moet duidelijk de toe te passen meetmethode vermeld worden en het laadgewicht. Als dat ontbreekt, is het zaak die gegevens bij de klant op te vragen voordat met het werk wordt begonnen.
JUISTE AANDUIDING EN PARAMETERS Het is mogelijk dat van hetzelfde materiaal het volgende gemeten wordt: Hv>1200 (foutieve aanduiding) en Hv200800 (juiste aanduiding, waarbij 200 het gebruikte laadgewicht aangeeft in grammen). In het eerste geval is het laadgewicht niet gedefinieerd en zal de hardheid beduidend lager zijn dan in het tweede geval waardoor een hogere hardheid wordt gemeten.
Bij thermisch gespoten deklagen worden de volgende parameters gehanteerd: • indruklichaam: een diamant vierzijdige piramide 136O • indruktijd: 20 seconden • laadgewicht: 200<laadgewicht<300
Gezien de aard van de structuur van een thermisch gespoten deklaag (lamellair en microporeus), worden laadgewichten hoger dan 300 gram niet aanbevolen. Verkeerde procesparameters kunnen een verhoogde porositeit in de deklaag tot gevolg hebben, waardoor een grotere indrukking plaatsvindt en dus een lagere hardheid gemeten wordt. Kortom, om discussies te voorkomen is het van belang om vooraf met de klant de toe te passen meetmethode precies en volledig af te spreken. ●
Tekst: Ton Kraak, voormalig (gepensioneerd) directeur Aludra/Metaltop en voorzitter van de Vereniging Thermisch Spuiten.
MEER INFORMATIE www.thermisch-spuiten.nl
Lees verder of reageer
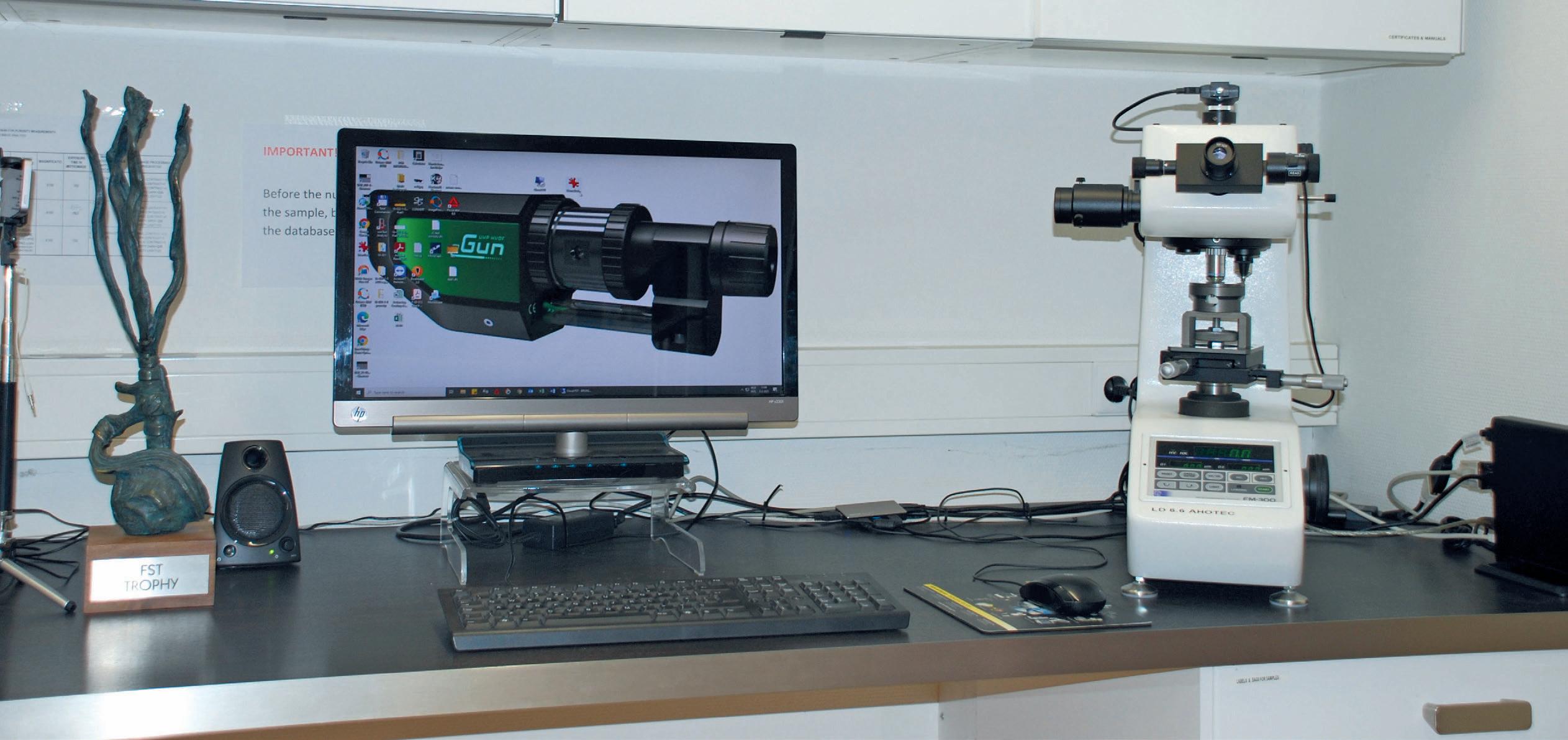
Nieuwe editie veldgids voor inspectie conservering
Onlangs is de tweede editie verschenen van The Paint Inspector’s Field Guide. Dit naslagwerk is bedoeld voor de inspecteur in het veld om conserveringswerken te beoordelen en te inspecteren. In vergelijking met de eerste editie uit 2012 is deze uitgave geactualiseerd en uitgebreid met enkele nieuwe hoofdstukken over nieuwe ontwikkelingen die inmiddels onderdeel zijn van inspectiewerk te velde.
Zoals bij de eerste editie wordt ook deze editie uitgebracht door TQC Sheen (Industrial Physics), een producent en leverancier van een breed assortiment apparaten voor het testen, meten en analyseren van coatings, inkten en algemene oppervlaktebehandelingen. Is het niet wat vreemd dat een dergelijke leverancier ook een boekje uitgeeft? René Bode, senior accountmanager van Industrial Physics | Inks & Coatings Division, legt dat uit.
“Industrial Physics is een Amerikaanse investeringsmaatschappij die een paar jaar geleden TQC Sheen heeft overgenomen. Wij hebben diverse producten die al langer onder de naam TQC Sheen verkocht worden, vandaar dat die naam nog bovenaan onze website staat. De Paint Inspector’s Field Guide is geschreven door Lee Wilson uit de UK, een zeer deskundige coatinginspecteur met een schat aan ervaring. Bij de eerste editie heeft hij ons gevraagd om te zorgen voor de opmaak, druk en verkoop van zijn boek. Die editie is inmiddels volledig uitverkocht en vorig jaar kregen wij bericht van hem dat hij een nieuwe versie heeft geschreven. En daarbij de vraag of wij dit ook wilden oppakken. Dat hebben wij gedaan, onder meer door de inhoud op juistheid en begrijpelijkheid te boordelen.” NASLAGWERK BIJ INSPECTIE Hij vervolgt: “De internationale wereld van coatinginspecteurs is klein en eigenlijk een wereld op zich. Wij kennen Lee Wilson al vele jaren, omdat wij ook wereldwijd opereren en mensen ontmoeten op beurzen en congressen. We hebben ook best wel veel publicaties uitgegeven. Ongeveer tien jaar geleden zijn we met hem in contact gekomen en heeft hij ons gevraagd zijn boek te gaan uitgeven. Die vraag hebben we ook te danken doordat er al snel een klik is ontstaan tussen ons als gelijkgestemden. Dat voelde goed en vandaar dat wij nu opnieuw werden gevraagd. Ook deze editie wordt uitgegeven in een compact formaat zodat het makkelijk door een inspecteur mee te nemen is. Het beschrijft allerlei facetten die je in het veld tegenkomt op het gebied van corrosiepreventie, coatinginspectie, normen en foto’s met voorbeelden. Het boekje is in het Engels omdat die taal in de wereld van coatinginspecteurs de voertaal is, denk bijvoorbeeld aan NACE, SSPC en Frosio.”
De nieuwe hoofdstukken die eraan zijn toegevoegd, gaan onder meer over Corrosie onder isolatie, de NORSOK M501-1 en TSA. Het is echt een naslagwerk om bij inspectiewerk feitelijke informatie op te zoeken over testen, meten en het interpreteren van getallen. ● The Paint Inspector’s Field Guide, 163 pagina’s, €145,00 exclusief BTW. Te bestellen bij TQC Sheen (Industrial Physics) www.tqcsheen.com



MEER INFORMATIE Lees verder of reageer
Robots hebben grote invloed op organisatie
Bij hightech gereedschappen denk je al snel aan robots. Robotisering is een trend in de branche en komt tegemoet aan twee vragen uit de markt die steeds belangrijker worden: flexibilisering en steeds kleiner wordende seriegroottes. Voor dit themanummer werd het dan ook tijd om Revamo te bezoeken, waar ze al ongeveer 25 jaar robots hebben voor het thermisch spuiten. De komst van robots betekent een flinke verandering in het werk van de operators en het gevraagde kennisniveau.
Revamo in Meppel is inmiddels zo’n 50 jaar een expert in het voorkomen en herstellen van slijtage aan machinedelen. Hiervoor worden diverse vormen van thermisch spuiten en lasercladden toegepast. Naast de traditionele focus op enkelstuks reparatiewerk, ontwikkelt Revamo zich steeds meer naar een productielocatie waar men zowel machinedelen herstelt als nieuwe machinedelen maakt. Daardoor is steeds vaker sprake van seriematig werk. Volgens Erik Mulder, directeur bij Revamo, is de inzet van robots daarbij een logische keuze, omdat ze eenvoudig en betrouwbaar zijn en heel goed in een abrasieve omgeving kunnen functioneren.
“Die kenmerken vormden 25 jaar geleden de basisreden voor het inzetten van robots. Daarna kwam daar het belang van arbeidsomstandigheden bij; je hebt immers te maken met onder meer geluidsbelasting en fijnstof. Met het gebruik van de juiste persoonlijke beschermingsmiddelen kun je wel uit de hand spuiten, maar dat vinden wij onwenselijk. Ons beleid is dat er niet meer uit de hand wordt gespoten. Ook dienden zich andere redenen aan voor het gebruik van robots, zoals procesbeheersing en reproduceerbaarheid om de kwaliteit te kunnen bewaken. Pas daarna komt een reden als het verhogen van de productiesnelheid; die wordt overigens niet bepaald door de robot, maar door alles wat eromheen staat. Het programmeren is best een uitdaging, want bij het uit de hand spuiten, spelen de ogen, oren en motoriek van de spuiter een grote rol. Dat alles moet je zien samen te brengen in het programma voor de robot en dat is best lastig.”
Enkele voorbeelden van producten die behandeld worden. SIMULATIES Lastig, maar niet onmogelijk. Het bedrijf heeft besloten alle complexe onderdelen eerst offline te programmeren in een cad/ cam-omgeving waarin het werk ook gesimuleerd kan worden, zodat je vooraf iets kunt zeggen over de haalbaarheid. Door het programmeren worden menselijke invloeden uitgesloten, zoals variaties in de spuitafstand tussen pistool en substraat of de snelheid waarmee het pistool beweegt. De robot doet immers simpelweg precies wat is geprogrammeerd. De feitelijke uitvoering kan worden gevolgd en vastgelegd, indien gewenst ook op video. Vanuit bijvoorbeeld de scheepvaart, de machinebouw en chemische industrie, worden hoge eisen gesteld aan de machinedelen
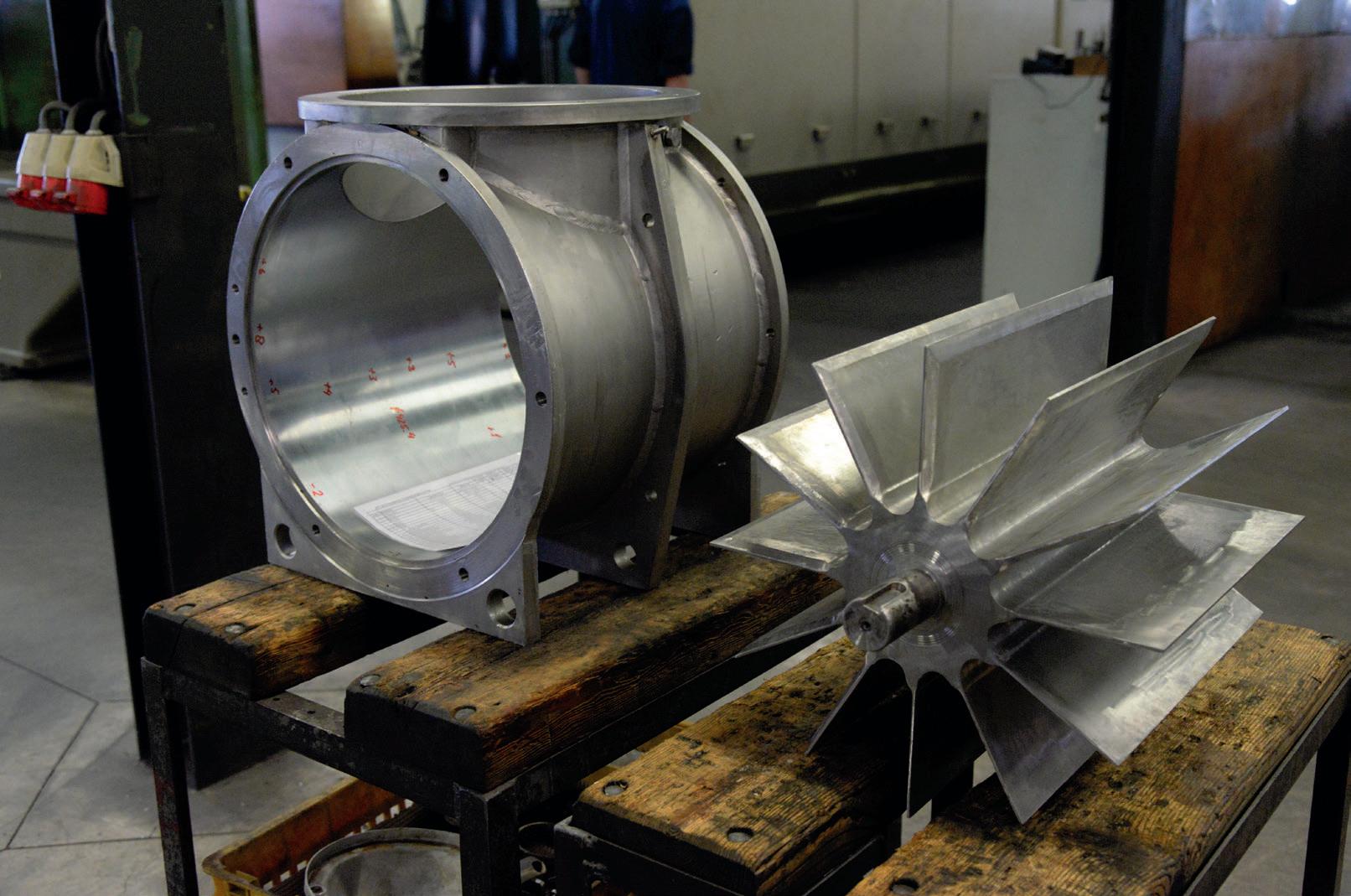
Silicon drift-detektor

Spuitrobot neemt een gedeelte van assen onder handen.

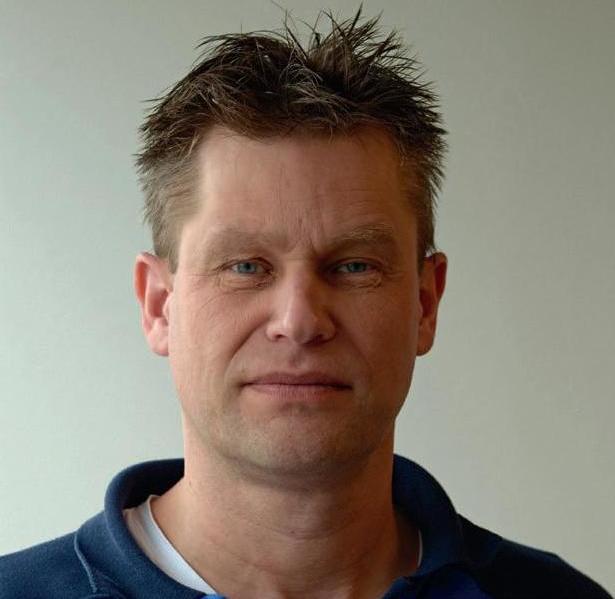
Erik Mulder
en de daarop aangebrachte lagen. Diverse keuringsinstanties willen het proces geborgd zien. Door de aanpak vooraf met de klant te delen en de uitvoering vast te leggen, wordt het proces van begin tot eind voorbereid, geregistreerd en bewaakt.
Erik Mulder: “Vroeger waren geautomatiseerde processen, zoals het werken met robots, gebaseerd op massaproductie. Op een gegeven moment werd dat ook beschikbaar voor serieproductie. Intussen neemt de seriegrootte steeds verder af, terwijl de prijsdruk toeneemt. First time right is dan een absolute voorwaarde. De laatste drie jaar zijn we steeds meer bezig om de productie meer geschikt te maken voor repeterend werk, zowel voor enkelstuks als voor kleine series. Het mooiste is als je precies op de vraag van de klant kunt inspringen en just in time kunt leveren. Als die afspraak wordt gemaakt, kunnen we het product op voorhand helemaal ontwikkelen en op afroep binnen korte tijd leveren. Omdat wij al gewend waren aan enkelstuks productie is het enerzijds niet zo moeilijk om aan deze marktvraag te voldoen, anderzijds vraagt het zeker wel wat van de organisatie. Om gestandaardiseerd te kunnen werken, zijn we een behoorlijke slag aan het maken.”
VAKMANSCHAP Die slag komt er in grote lijnen op neer dat alles in heel strakke banen wordt geleid, dat de eigen inbreng van de operators tijdens de orderuitvoering minder wordt, maar dat daarentegen het belang van engineering aan de voorkant (veel) groter wordt. Dat betekent bijvoorbeeld vooraf 3D-simulaties doen in de computer. Het leren programmeren van de robot kan de robotfabrikant ABB verzorgen. De operators kunnen heel goed beschrijven hoe het spuitwerk gedaan zou moeten worden en zij zijn de eerstaangewezen personen om de robot te programmeren. En als zij er mogelijk niet uitkomen, dan is er een jonge coatingengineer op hbo-niveau die hen ondersteunt. Erik Mulder geeft aan dat daarmee een verschuiving plaatsvindt in het vakmanschap van vroeger en dat het begrip vakmanschap verandert: het gaat om het vooraf bepalen van de juiste procesparameters, de juiste programmering en het vastleggen van deze data, zodat je ze later nog eens kunt gebruiken. Het invoeren van deze werkwijze in de organisatie noemt Mulder een leuk, maar ook wel pittig proces.
“Het programmeren van een robot vraagt een bepaald denkniveau, maar het is geen probleem om te leren hoe je dat moet doen. Het gaat om de integratie van werkvloer en kantoor, en de drempelloze samenwerking daartussen. Willen we verder komen met automatisering en robotisering, dan is het van essentieel belang dat de scheidslijn tussen kantoor en werkplaats vervaagt of vervalt. De terugkoppeling van praktijkresultaten aan engineering/ werkvoorbereiding is ontzettend belangrijk om het proces steeds verder te kunnen optimaliseren, standaardiseren en automatiseren. De robot is slechts

Ook lasercladden wordt bij Revamo met behulp van een robot uitgevoerd.
een hulpmiddel, niet de oplossing. De robot bedenkt het proces niet, maar doet gewoon wat je vraagt. Veel belangrijker is kennis van het coatproces, zodat je het hulpmiddel goed kan instrueren. Robots zijn gewoon standaardapparaten, maar de integratie van de systemen, dus het afstemmen van de robot op de apparatuur eromheen in de cabine, is maatwerk.”
IMAGO VERANDEREN Revamo heeft voor het thermisch spuitwerk en lasercladden drie dezelfde robots aangeschaft. Hierdoor is het werk voor de robots makkelijk uit te wisselen tussen de operators. De rol van de operator is het programmeren van de robot en het coatproces bewaken met zijn ogen, oren en vakmanschap. Een volgende uitdaging is het automatiseren van de procesbewaking, maar dat staat nog in de kinderschoenen. Robotisering betekent overigens absoluut niet dat afscheid moet worden genomen van operators, benadrukt Erik Mulder. Het gebruik van robots, computergestuurde apparatuur en het digitaal vastleggen van procesparameters vraagt juist om jonge aanwas. Maar het bedrijf heeft grote moeite om mensen te vinden voor dit unieke vak.
“Wij hebben per direct plaats voor een leerling thermisch spuiter. Iemand met een mbo-denkniveau die het vak vanaf de basis wil leren. Onze technieken worden niet in het klaslokaal onderwezen, je leert ze intern. Belangrijker dan een afgeronde opleiding, is de drive om deze unieke processen te leren. Wij zoeken gedreven, betrokken mensen die er trots op zijn iets unieks te doen en daarin vakman/vrouw willen worden. De ervaren medewerkers leren de leerling het vakmanschap en de leerling helpt de ervaren medewerkers op het gebied van digitale ontwikkelingen.” Hij wijst op enkele aspecten die naar zijn verwachting per saldo positief uitpakken: “Het verloop onder onze medewerkers is heel laag, omdat ze het hier gewoon hartstikke leuk vinden door de grote variatie in het werk. Helaas heeft dit soort werk bij buitenstaanders onterecht een imago van vies, stoffig en lawaaiig werk. Automatisering en robotisering maken dit vak aantrekkelijker voor de jeugd. Met onze slijtageoplossingen bieden we duurzame, circulaire oplossingen die bijdragen aan de reductie van de CO2-footprint en aan de beperking van het gebruik van schaarse grondstoffen. Dat biedt een goed toekomstperspectief.” ●
MEER INFORMATIE www.revamo.nl
Lees verder of reageer
Trots op het werk
Efteling kiest voor Qotec NanoClear+
Intensief gebruikte objecten hebben een beschermende coating nodig. Dat geldt ook voor de Vliegende Hollander uit de Efteling. Elk jaar genieten miljoenen bezoekers van deze waterachtbaan. De 14-persoons sloepen worden mechanisch zwaar belast. Bij elke rit krijgen ze een forse klap van het water. De Efteling zocht een professionele partij die een beschermende coating kon aanbrengen die lang meegaat, weinig onderhoud nodig heeft en kras- en slijtvast is. Na laboratoriumonderzoek is er gekozen voor NanoClear+ van Steur in Oudenbosch in combinatie met droogijs voorbewerken. Alle tien de boten van De Vliegende Hollander zijn bij Steur ontdaan van alle vervuilingen en verfresten en voorbewerkt met droogijsstralen. Dat laatste creëert een hoge oppervlaktespanning waardoor zonder verdere voorbewerking de epoxy primer kan worden aangebracht die zeer goed hecht. De droogijsbehandeling had ook de voorkeur van de Efteling, omdat het milieuvriendelijk is en geen afval achterlaat. Na het aanbrengen van de primer is op elke boot een basislak gezet, waarna de thematische detaillering is aangebracht. Als topcoat zijn er twee lagen Qotec NanoClear+ met waterafstotende eigenschappen aangebracht. Deze lagen zijn extreem slijtvast waardoor de mechanische belasting opgevangen wordt. Door de toegevoegde UV-blokkers blijft de thematische uitstraling langer behouden. Meer informatie: www.Steur.com/Qotec.nl

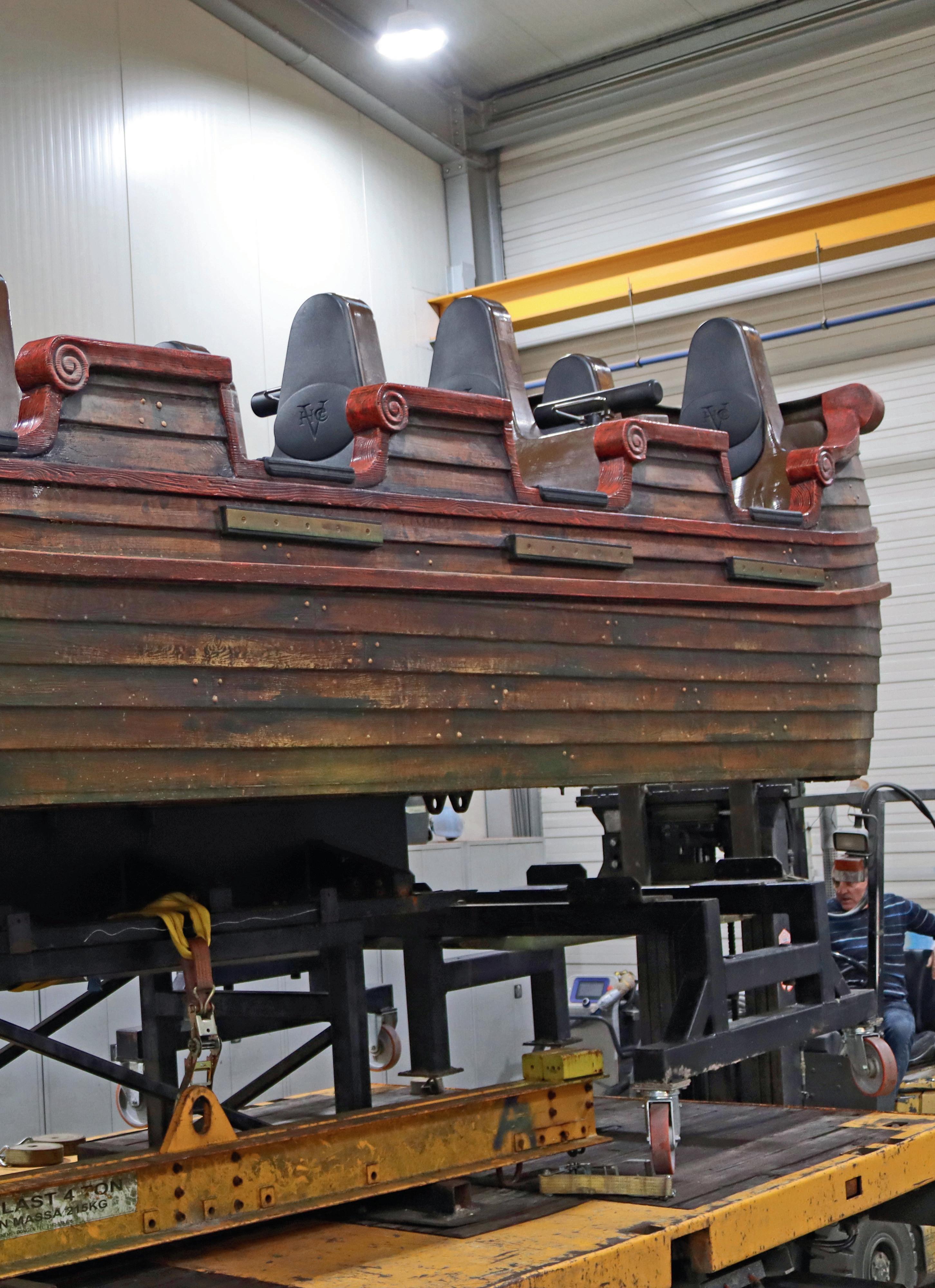