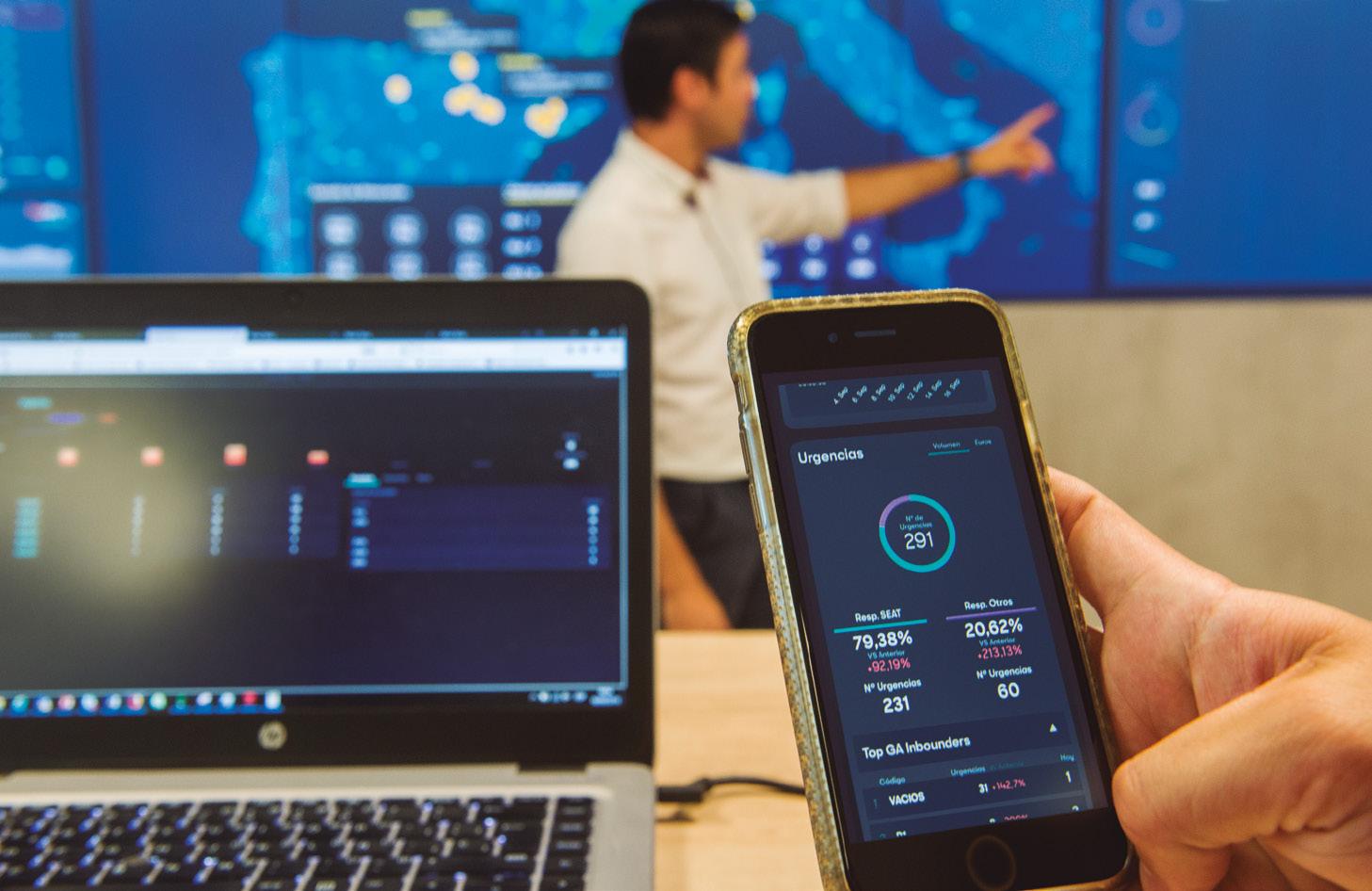
8 minute read
Hiperconexión en la cadena logística
Supply Chain Control Tower en SEAT Gestionar en tiempo real la localización exacta de cada una de las piezas que conforman un coche, contar con información sobre el consumo de materiales; y todo ello conectado con las necesidades de producción. Este es un ejemplo del nuevo paradigma, en el que el consumidor final y sus exigencias influyen en el proceso de producción. A través de este proyecto, SEAT ha flexibilizado y optimizado su cadena logística para adaptar sus procesos a la nueva realidad de la industria.
36 // Las instalaciones de SEAT en Martorell fabrican diariamente 2 300 automóviles, lo que supone gestionar cerca de 16 millones de piezas individuales. En un sector como el de la automoción, ser capaces de reducir los costes en la cadena logística de producción, así como optimizar los tiempos de entrega del producto al consumidor final, se traduce en una mejora de la experiencia del cliente y en un beneficio económico para la marca. Para lograr este objetivo, SEAT ha puesto en marcha un proyecto para la optimización del proceso logístico de entrega de materiales (piezas) a las diferentes líneas de producción de vehículos. Para ello, se ha implantado un sistema de trazabilidad y monitorización online en tiempo real para todas y cada una de las mercancías que se reciben de todos los proveedores de la marca, incluyendo también información de los operadores logísticos encargados del transporte de los materiales de producción. Para conocer todos los detalles de esta auténtica torre de control logística, hemos hablado con David Castilla, responsable del proyecto en SEAT, y con Eva Pueyo, Account Manager y responsable del proyecto en T-Systems, uno de los partners tecnológicos del proyecto y encargado de aportar la inteligencia de la plataforma.
Advertisement
D I G I T A L I Z A R L O S P R O C E S O S D E PRODUCCIÓN Se trata de un proyecto que se completó en solo 26 semanas y que permite monitorizar la ubicación exacta de cada una de las piezas necesarias para hacer un automóvil. Esta supply chain control tower permite al fabricante contar con información que se actualiza en tiempo real sobre el flujo y el consumo de material de producción. Hablamos de 200 000 datos clave, un rompecabezas gigante en el que intervienen todo tipo de componentes y parámetros, desde inventarios de proveedores hasta procesos en centros de transporte y logística.
Esta supply chain control tower monitoriza la ubicación exacta de cada una de las piezas de un automóvil
Se trata de conocer, en tiempo real, dónde está cada pieza y cuándo llega, así como saber con antelación si se van a producir posibles retrasos en la entrega. Es un enfoque completamente nuevo en cuanto al modo de integrar la digitalización en los procesos de producción de SEAT, que permite controlar mejor los procesos, ofrecer mejores servicios e, incluso, poner en marcha nuevos modelos de negocio, abriendo nuevos caminos en la configuración dinámica. “Este proyecto sienta las bases y mecanismos de control que nos permitirán ofrecer al cliente una experiencia de compra mucho mejor. El objetivo no solo es asegurar la fecha de entrega desde el inicio, sino reducirla al máximo y, al mismo tiempo, ofrecer al cliente final la posibilidad de realizar algunos ajustes en el transcurso de la fabricación de su vehículo”, nos cuenta David Castilla. Para SEAT, el cliente representa la parte más importante a la hora de planificar la fabricación de un coche. “Es nuestra base para anticipar las necesidades del mercado, los ajustes en los programas de producción o la optimización de los planes de compras a través de una comprensión mayor de las necesidades de nuestros clientes”. Este enfoque hacia el cliente ha sido también un aspecto muy importante desde el punto de vista del partner tecnológico. A este respecto, Eva Pueyo afirmaba lo siguiente: “El cambio más significativo ha sido el enfoque 100% al negocio del cliente. No podemos hablar de planificaciones al uso de proyectos de tecnología en ninguna de sus vertientes. Trabajamos con hitos de negocio con los que tenemos que alinearnos en cada nueva oleada del proyecto. Todo ello sin perder de vista la calidad de lo que entregamos, precisamente en la línea de que el negocio del cliente no se vea afectado en su día a día”.
EL DATO COMO FUENTE DE VALOR Lógicamente, el requisito indispensable ha sido el big data, como explica David Castilla: “Los datos son nuestra materia prima para construir proyectos digitales. Si los datos no son lo suficientemente buenos, la digitalización se vuelve cada vez más compleja y carece de credibilidad. Ser conscientes de esto, y establecer un programa claro para garantizar que la calidad de los datos sea suficiente, contribuye al éxito”. Una de las tareas clave de T-Systems en este proyecto ha sido, precisamente, aportar la inteligencia de la plataforma. Eva Pueyo incide especialmente en el grado de importancia que tiene la calidad del dato: “Si no es correcto, la toma de decisiones basadas en el reporting (visual y analítico) de la solución es imposible o errónea”. El sistema desarrollado por la filial de Deutsche Telekom recoge los datos de los varios cientos de fuentes de referencia de los sistemas de SEAT y los trata para que posteriormente sean analizados y muestren información útil para el negocio. El sistema reconoce de qué fuente debe extraer la información, qué datos debe extraer y cómo procesarlos para que sean explotables desde las unidades de negocio que los soliciten. Así mismo, se ha dotado de un sistema de tracking para los transportistas basado en una app conectada con la plataforma de ingesta de datos. Eva Pueyo profundiza algo más en todo este proceso y en los aspectos que han resultado determinantes para garantizar la adecuada calidad del dato: “Por un lado, hay que contrastar los orígenes para verificar que proporciona la información precisa y necesaria en cada proceso. Por otro lado, hay que nutrir esta información con datos de contexto que proporcionan la visión multidimensional. Por último, hay que comprobar que los informes que salen en las plataformas de visualización
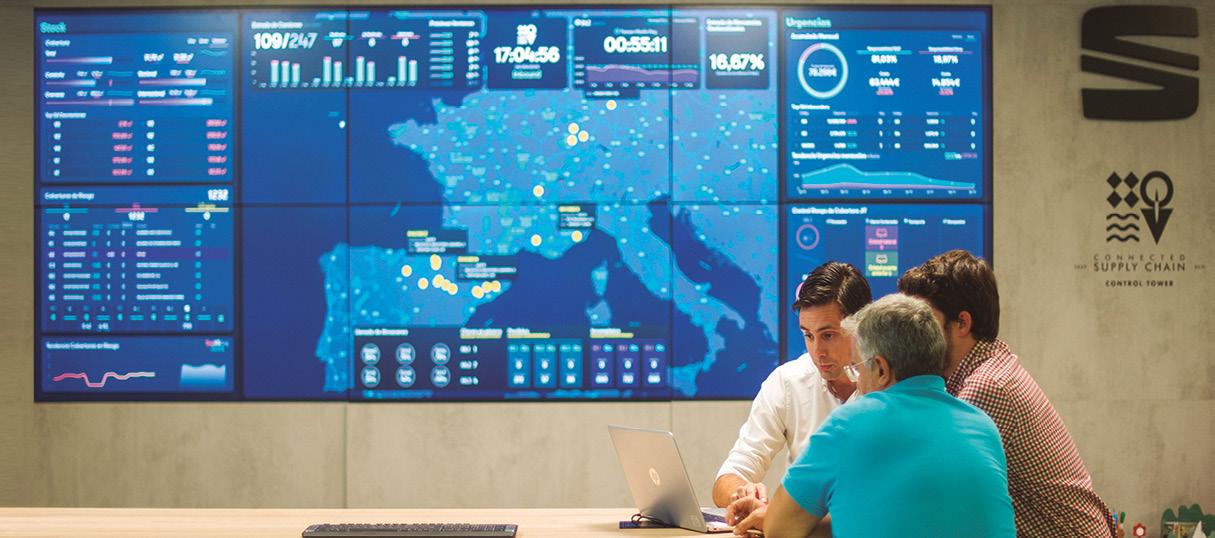
y analítica son los esperados. Todo ello se realiza en cada sprint del proyecto de forma integrada y, posteriormente, se verifica con los usuarios de la plataforma”.
FASES DEL PROYECTO El despliegue de esta solución se está realizando de forma gradual. Actualmente están integrados alrededor de 20 proveedores TIER1 en el sistema de control logístico de entrada de materiales de producción, además de las empresas de transporte asociadas a las rutas logísticas. “En paralelo, a lo largo del 2020 se irán desplegando también algunas mejoras funcionales sobre la solución actual. Posteriormente se seguirá con futuras implementaciones en los procesos de compra y de logística de expedición de producto acabado”, comenta Eva Pueyo. La metodología Agile ha sido fundamental para conseguir que T-Systems logre alinearse con los hitos de negocio de SEAT. En palabras de Eva Pueyo: “En cada sprint se han definido y acordado los entregables a conseguir, en cuanto a la integración de qué tipo de datos y de qué orígenes, empezando con un MVP (producto mínimo viable) que permita dotar de funcionalidad a los usuarios del sistema desde el primer ciclo e ir evolucionando con los nuevos datos, informes y funcionalidades de forma iterativa”. Actualmente, el sistema es analítico/reactivo, aunque el objetivo es desarrollar una plataforma que realice análisis predictivos y pueda, por ejemplo, anticiparse a las necesidades de provisión de materiales. Además, también se extenderá la trazabilidad y monitorización a la expedición del producto acabado, lo que se traduce en la optimización de los procesos de fabricación de coches. Esto permite reducir los costes y mejorar los márgenes, al tiempo que se evitan gastos derivados de errores en la provisión de piezas. Finalmente, también se extenderá el modelo de trazabilidad a las compras, cerrando el círculo del proyecto. Esto hará posible, a través de tecnologías de inteligencia artificial y conformando un sistema predictivo, que SEAT pueda reducir costes de fabricación al elegir los mejores tiempos
para comprar piezas y materiales, planificando la necesidad y adaptándola a la idoneidad de costes, sin dejar desabastecidas las líneas de producción.
L A N U E VA F R O N T E R A D E COMPETENCIA Con esta última fase, el proyecto abarca todo el ciclo de la logística de SEAT, y reconvierte el modelo de provisión, optimizando y flexibilizando también los procesos de producción y comercialización de sus vehículos. En opinión de David Castilla, este tipo de tecnologías revolucionará la gestión actual de las operaciones e interacciones con los clientes, fortalecerá las relaciones entre los actores de las cadenas logísticas y desarrollará modelos de partner para ofrecer los mejores servicios a los clientes finales. “Cualquier proveedor actual evolucionará hacia una hiperconexión con SEAT, que irá de menos a más en función del rol que desarrolle en la cadena de suministro. La conectividad en flujos de información, procesos y resolución de incidencias será la base que permitirá dotar de calidad, velocidad y eficiencias a las cadenas de suministro. Estas serán la ‘nueva frontera de competencia’ y debemos ser los que lleguemos primero, con un mejor producto y la mejor experiencia para nuestros clientes”. Además, continúa David Castilla, “es un modelo perfectamente escalable a cualquier ámbito de las actividades de la compañía, ya que la gestión de la información, los modelos de partnering y la inclusión del cliente como centro absoluto de las decisiones conforman el patrón común a todas ellas”.