MASS TIMBER END-OF-LIFE SCENARIOS
Best Practices In Designing for Reuse
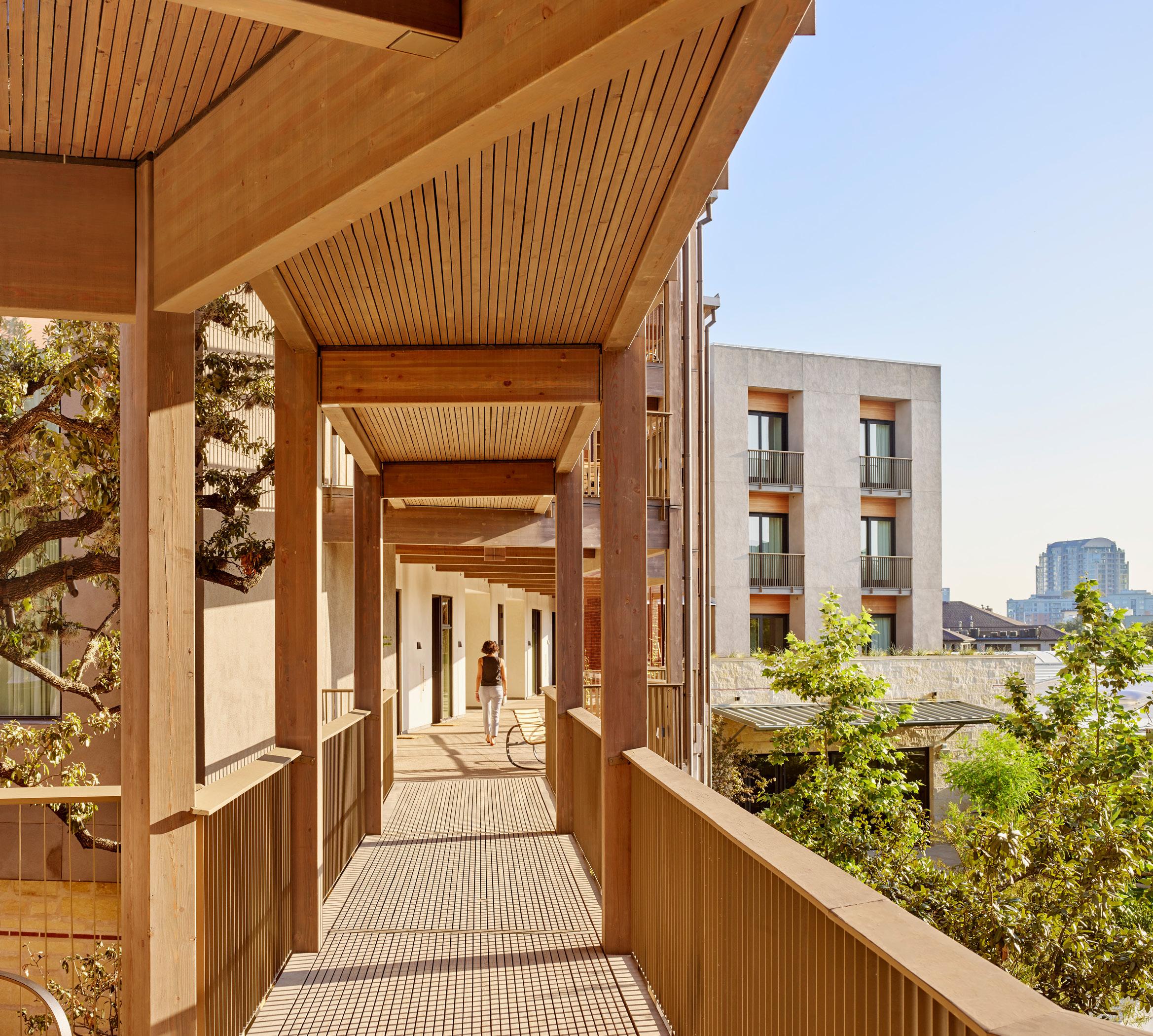
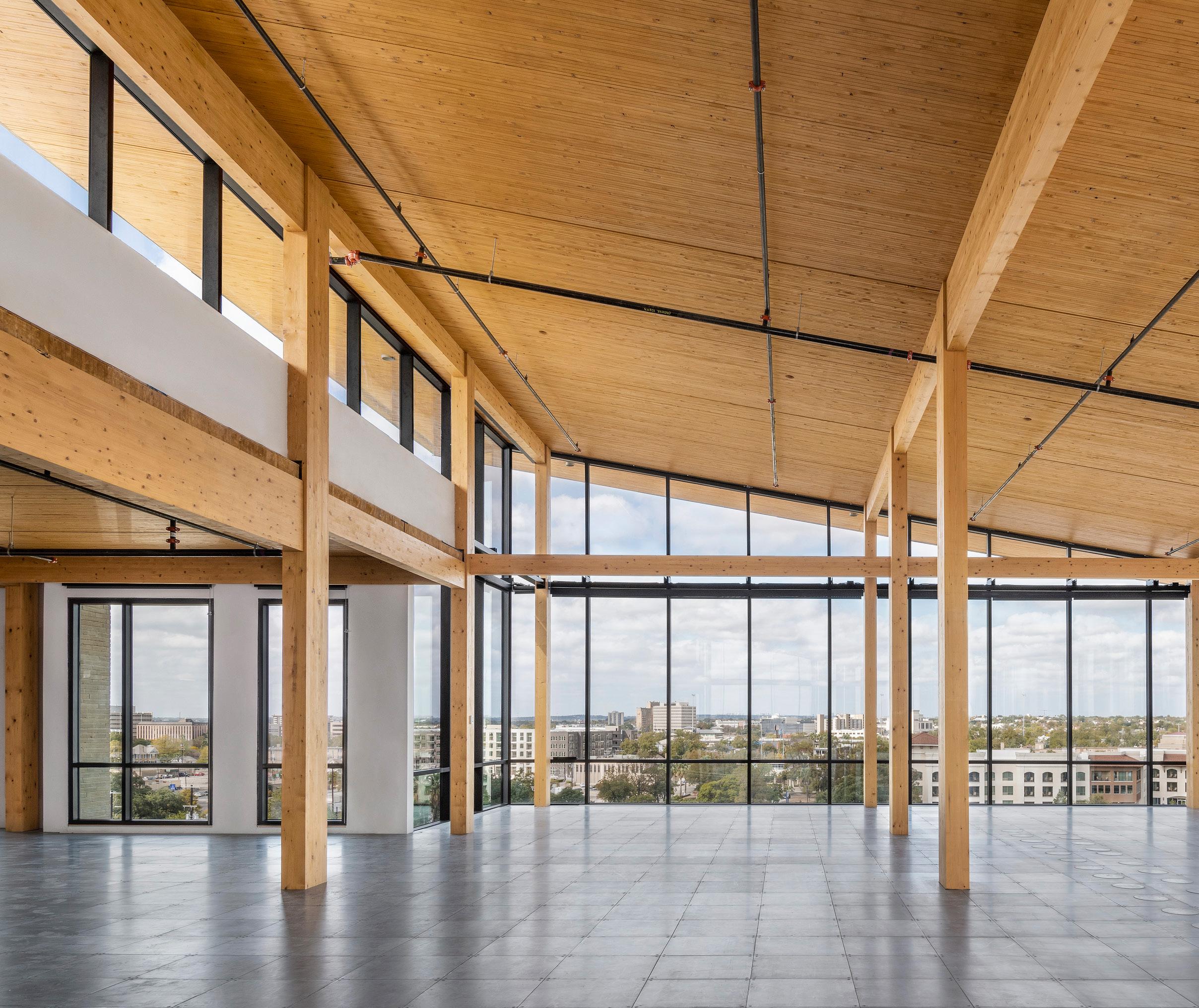
Best Practices In Designing for Reuse
Allison Peitz 2022-2023
How should end-of-life scenarios for mass timber influence the way we design buildings?
Mass timber construction has been recognized as a significant tool for combating climate change and supporting the global push for circular economies by creating building stock that also serves as a carbon sink. Beyond these initial benefits, as an inherently lightweight and modular system, mass timber also has high potential for reuse to extend these carbon benefits. This research paper catalogs examples of wood and mass timber reuse in historic civilizations to inform best practices for designing mass timber structures to maximize reuse potential. Additionally, this paper considers methods for accounting for biogenic carbon as part of a Life Cycle Assessment (LCA) and provides recommendations for supplementary tools that can be used to account for reuse scenarios.
Mass Timber, End-of-Life Scenarios, Cradle-toCradle, Circular Economy, Life Cycle Assessment, Tally, Dynamic Carbon Accounting, Biogenic Carbon, Carbon Storage
Mass timber has a critical role to play in addressing climate change and meeting goals to avoid critical tipping points. This method of construction has been called, “The quintessential carbon negative technology for climate change mitigation,” noting that the material’s longevity in use drives the magnitude of this impact (Lippke et al., 2021). The term ‘Carbon’ is often used as shorthand for global warming potential (GWP) and is measured in kilograms of carbon dioxide equivalent (kgCO2eq). Mass timber provides opportunities for climate change mitigation because wood can extract carbon from the atmosphere as it grows and retains this carbon, termed biogenic carbon, within its fibers throughout its lifespan. This ability to store carbon counteracts the typical flows of emissions into the atmosphere to delay the impacts of global warming. These beneficial impacts are optimized if mass timber elements can be reused or re-purposed, therefore retaining carbon for a longer period.
In 2021, the Intergovernmental Panel on Climate Change (IPCC) warned that a 45% reduction in carbon emissions is needed by 2030, followed by a 100% reduction in emission by 2050, to avoid an increase in global warming that will exceed 1.5° C (IPCC, Summary for Policymakers). The building sector alone accounts for 39% of energy and process-related carbon dioxide emissions globally (Toth et al., 2021). The energy that a building consumes while operating is referred to as operational carbon (Lewis et al., 2023). Buildings have become increasingly efficient over time as technology has become more advanced, reducing operational carbon impacts. Efforts have since turned to reducing building’s embodied carbon, or the emissions associated with the
manufacturing, transportation, installation, maintenance, and disposal of construction materials used to produce a building (Lewis et al., 2023).
Within the building and construction sector, the most effective ways to minimize carbon emissions are through adaptive reuse or the deconstruction and reuse of building components, versus recycling (Lippke et al., 2021). This is especially true when it comes to mass timber construction. Mass timber, due to its modularity, lightweight, and durability, has excellent reuse potential.
Every new building constructed with mass timber has potential to serve as a carbon sink, delaying the release of CO2 into the atmosphere. This temporary carbon storage is sequestered for the life of the product, potentially through the lives of multiple buildings. Planning for deconstruction may seem like a concept for the distant future. However, given that the average commercial building has a life expectancy of 50-100 years, the way we choose to design mass timber buildings today will facilitate or impede our ability to reuse, deconstruct, or recycle buildings and their components for the next 50-100+ years (O’Connor, 2014).
This paper is a literature review that compiles relevant research and case studies to answer the question:
This paper will provide an overview of international efforts promoting timber circular economies, reinforcing the need for clear guidelines that can be applied to promote adaptive
reuse and deconstruction for reuse in mass timber buildings and of mass timber products. Second, the paper will dive into the history of wood and mass timber reuse to demonstrate the potential longevity and durability of wood and mass timber products. Third, Life Cycle Assessment (LCA) calculation methods and challenges will be discussed as they pertain to end-of-life scenarios for mass timber and biogenic carbon accounting. Finally, this paper compiles design recommendations that can serve as a reference for design professionals, to promote adaptive reuse and deconstruction for reuse in mass timber buildings. These recommendations will cover structural topics, including grid layouts and connection design, moisture management strategies, systems distribution approaches, and documentation.
Mass Timber: Engineered wood products including glue-laminated timber, cross laminated timber (CLT), and dowel laminated timber (DLT)
Biogenic Carbon: Carbon produced in natural processes by living organisms but not fossilized or derived from geological fossil resources. In the building industry, this most commonly occurs in wood products (The Carbon Leadership Forum, 2019).
Operational Carbon: Emissions generated by fuel consumption for heating/cooling, supplying, fresh water, ventilation, and power over the course of a building’s lifetime (Lewis et al., 2023).
Embodied Carbon: Emissions generated by the manufacturing, transportation, installation, maintenance, and disposal of construction materials used in buildings, roads, and other infrastructure (Lewis et al., 2023).
Carbon Sink: Anything that absorbs more carbon from the atmosphere than it releases through carbon sequestration (Churkina et al., 2020).
Carbon Storage: The sequestration of carbon in products for a period, resulting in a (temporary) reduction of the CO2 concentration in the atmosphere
To meet carbon emission reduction goals put forth by the IPCC, it is important to challenge the traditional linear model of consumption -- where products are made, used, and disposed of – and instead pursue a circular economy approach – where materials are designed to be reused, repaired over time, and/or recycled.
A key concept behind circular economies is that materials should be upcycled: reuse that maintains or increases the previous value of the material (Heinrich & Lang, 2019). For mass timber, this means that structural elements will be reused as structural components. This contrasts with downcycling: reuse or recycling that reduces the value of the material (Heinrich & Lang, 2019). For mass timber, or any other type of wood, downcycling typically involves reuse in furniture or as wall/ceiling finishes, processing for use in wood composite materials, or mulching (Love, 2007). While both upcycling and downcycling avoid raw material inputs, upcycling is strongly preferred because it requires less energy to process and requires a smaller embodied carbon input.
Cascading is a process that acknowledges that maintaining a material at its highest and best use is not always possible as material ages, and instead promotes the use of the waste material in its highest value alternative for as long as possible (Holgmeier et al., 2013).
As of 2021, only 8.6% of our world is circular (The Circularity Gap Report, 2022). Within the building sector, only 20-30% of construction and demolition waste is currently reused
or recycled, leaving the remaining 70-80% to be landfilled (Building a world free from waste and pollution, 2021; Rypkema et al., 2021).
To challenge this trend, deconstruction programs have been implemented in several cities across the nation focusing on single-family homes. These programs, still in
their infancy, have established flourishing wood salvage materials markets. Wood is the single most valuable salvage material yielded from the deconstruction process in older homes and according to David Greenhill, a deconstructor in Portland, “Selling salvaged wood is the only way to actually make money in this business (Allison Peitz, personal communication, April 13, 2022).”
2x4s are salvaged from the framing of existing structures. Larger timbers are found less frequently. However, heavy timbers that were previously graded can be “grandfathered in”, meaning they do not need to be regraded before use in a second-life structural application.
David Greenhill established Good Wood Deconstruction & Salvage soon after the city of Portland implemented a deconstruction ordinance in 2016. According to a report from 2018, in the first year that the ordinance was implemented, approximately 70% of the material from deconstructed homes was salvaged (Wood, n.d.).
The ordinance sharply increased demand for deconstruction services, drawing newcomers to the market. Greenhill says, “Before the ordinance, there were only two deconstruction companies in all of Portland. Since the ordinance, there are now twelve companies competing for business.” While demand for deconstruction services has increased since the ordinance was implemented, revenue is primarily created by selling the collected salvage materials, with wood holding the greatest value. “Selling salvaged wood is the only way to actually make money in this business,” Greenhill explains.
There are many challenges to extracting wood from old homes. Greenhill’s team often finds wood boards covered in lead paint or residual adhesive from insulation. Removing these coatings requires more time and effort to remove than the wood is worth, making the wood unsalvageable. However,
Deconstruction ordinances provide unique insight into the development of a wood salvage material market that parallels that which will likely come for the mass timber deconstruction industry. It is plausible to expect that many of the same challenges and opportunities encountered through this process would also apply to a salvage mass timber market.
Parallel to these efforts, many are working to address concerns surrounding adaptability and deconstructability during the design process. These efforts are collectively termed Design for Deconstruction and Reuse (DfDR). This concept acknowledges that buildings are not static objects. Rather, they are dynamic structures that should be designed to undergo repair, renovation, replacement, and ultimately deconstruction.
To facilitate deconstruction and reuse, tools are being developed to track material composition, value, origination, and history throughout a product’s lifetime. The most well-known of these is the material passport. Material passports contain levels of data to identify product types, materials, structural properties, and specific components. A serial number or other identifier is physically attached or embedded in the component and can be used to lookup additional product information. Collectively, this information provides a basis of value and capability for present use, recovery, and reuse that will support the development of salvage material markets (Heinrich & Lang, 2019).
In several countries, policy changes are being implemented to promote circularity by shifting responsibility for reuse to manufacturers. Extended Producer Responsibility (EPR) is a policy approach where a producer’s responsibility for a product is extended to the post-consumer stage of the product’s life cycle (Love, 2007). For example, the United States has mandated takeback programs for household batteries, electronics, items containing mercury,
packaging, and pharmaceuticals. Similar take-back programs have been implemented for timber in several countries in Europe, but have excluded treated timber (Love, 2007).
Further development of material passports and EPR policies will be critical to make salvage mass timber markets possible in the future. Given the existing momentum behind the DfDR movement, the hope is that by the time that many mass timber buildings are approaching the end of their first life, precedent for salvage markets and policies will already be well established.
Manufacturer’s name/details
Manufacturer’s article number
Temporal information
Product name/brand
Unique Product Identifiers
Product’s main function
GTIN or EAN number CAS number
Circular Economy: Aims to keep materials, components, products and assets at their highest utility and value always. In contrast to the ‘take, make, use, dispose’ linear model of production and consumption, material goods are designed and produced to be more durable, and to be repaired, refurbished, disassembled, and reused in perpetuity – thereby minimizing resource use, eliminating waste, and reducing pollution (The Delphi Group, 2021).
Upcycling: Reuse in such a way as to create a product of higher quality or value than the original (Heinrich & Lang, 2019). Upcycling avoids the need for raw material inputs, energy required for processing, and minimizes the embodied carbon inputs.
Downcycling: Reduces the value and quality of a material in contrast to upcycling procedures (Heinrich & Lang, 2019).
Cascading: Promotes the use of the waste material in its highest value alternative for as long as possible, and only resorts to energy recovery after its alternative value has diminished (Holgmeier et al., 2013).
Design for Deconstruction and Reuse (DfDR): The design of buildings to facilitate future changes and dismantlement (in part or whole) for recovery of systems, components, and materials, thus ensuring the building can be recycled as efficiently as possible at the end of its lifespan (Critescu et al., 2020).
Material Passports: Data sets describing defined characteristics of materials in products that give them value for recovery and reuse (Heinrich & Lang, 2019).
Extended Producer Responsibility (EPR): An environmental policy approach in which a producer’s responsibility for a product is extended to the post-consumer stage of the product’s life cycle. This approach provides incentives for producers to take responsibility for the environmental impact of their products throughout their entire life cycle (Love, 2007).
Takeback Programs: Programs that mandate that producer’s takeback or recycle products at the end of their useful lives (EPA, 1998).
While there is a limited amount of data available on mass timber’s potential for deconstruction and reuse, there is plenty of historical data available to demonstrate the reuse potential and durability of its core substance -- wood.
The earliest recorded example of wood deconstruction and reuse was in seafaring ships in ancient Egypt (Creasman, 2013). The Egyptians relied upon imports for timber for the construction of seafaring ships used to transport supplies. During the New Kingdom, the Egyptians’ faced challenges importing virgin timber, and it became common for timber from retired ships to be reused in new ships (Creasman, 2013). These ship timbers were joined using mortise and tenon joints and lashed together with rope. Markings were used to facilitate correct placement during the reassembly process. Recovered hull and deck planks have numerous and sometimes overlapping mortises, indicating serial reuse (Creasman, 2013). Creasman suggests that in ancient Egypt, the “Proclivity for repurposing ship timber was a matter of practicality…reuse was the rule rather than the exception (Creasman, 2013).” This historical evidence demonstrates the immense durability and versatility of modular wood elements.
Glue-laminated timber is the earliest form of mass timber known to be used in building construction and many of the earliest glue-laminated timber structures are still in use today. These structures demonstrate the durability and versatility of mass timber construction.
The oldest of these examples preceded any formal patents and was built in 1866 by architect Josiah George Poole. The building was designed to serve as an assembly room for King Edward VI College in Southampton, England. The project required speedy construction on a tight budget, which is ultimately why glue-laminated timber was used (Leonard, 2008). The building is still in good condition and continues to be used as a ceremony venue (Figure E.)
In 1934, the first two glue-laminated timber structures were built in Wisconsin. The first was a high school gym in Peshtigo and the second was a storage building, known as “Building Two” for the Forest Products Laboratory in Madison (Figure F.) The high school gym was converted to a library in the 1980s and is still in use today (Lehman, 2018). “Building Two” served as storage building, a laboratory, and as a lecture hall over the years, but was ultimately decommissioned in 2010. After decommissioning, recovered glue-laminated timber arches were tested to evaluate the loss of structural performance. Minimal loss of structural performance was found in all arches except one, which was exposed to a significant amount of water from extinguishing a fire many years earlier (Spartz, 2014).
Thirty-five years earlier in 1901, the first patent for gluelaminated timber was issued in Switzerland to Otto Karl Friedrich Hetzer, soon followed by a patent for curved glulam. The use of glue-laminated timber soon spread throughout Europe, and became especially useful for temporary structures (Lehman, 2018). At this time, glulam was more affordable than steel, quicker to assemble/disassemble due to its light weight and standard connections, and offered a more elegant, finished aesthetic than steel construction
(Haddadi & Rinke, 2020). Many of these temporary glulam structures were large in scale, in use for only weeks at a time, and intended to be made available to a secondary market following its disassembly. For this reason, these structures used simple, repetitive, and reversible steel connections. Glulam elements were kept light weight, modular, and easy to transport (Haddadi & Rinke, 2020). One example of this was a temporary hall for the Swiss singing festival near Zurich, which was constructed in 1911 and used for one week before disassembly (Figure G.). It was common for secondhand glulam components to be sold either as a full-building package or as singular components. There are even examples of components from multiple buildings being combined within a new structure (Haddadi & Rinke, 2020). Figure H. shows an inventory of glulam pieces from a pavilion at the National Swiss Exhibition that was used to facilitate resale.
Since the earliest glue-laminated structures were built, several breakthroughs have been made in the development of wood adhesives and lamination techniques to make mass timber components significantly more durable and waterresistant.
The earliest glue-laminated beams were bonded using casein glues. Casein glues are derived from animal milk and were used as far back as ancient Egyptian times (Saleh Pascha, 2014). Casein glues are hardly waterproof, have low shear strength, and require long setting times. For this reason, casein glues limited the application of glulam construction until 1928, when the first cold-curing synthetic resin glues were introduced (Saleh Pascha, 2014). Referred to as “Kaurit,”
1866 The first glulam elements are used to build the Assembly Room at King Edward VI College in Southampton, England (Leonard, 2008).
1901 The first glue-laminated timber assembly is patented in Switzerland by Otto Karl Freidrich Hetzer (Lehman, 2018).
1906 Hetzer recieved a patent for curved glue-laminated timber (Lehman, 2018).
1934 Unit Structures, Inc., the first US-based glulam manufacturer is founded in Peshtigo, WA (Lehman, 2018).
Unit Structures, Inc. recieves it’s first two commisions - one for the Peshtigo Gym and the second for a storage building for the Forest Products Laboratory.
Late 1930s Several more glulam manufacturing companies are established. Projects include schools, gyms, stadiums, churchs, factories, and aircraft hangers.
resin glues are fully waterproof and resist fungal growth, which made exterior applications possible (Saleh Pascha, 2014). These glues continued to be improved to the point where the adhesive bond in the glued joints became stronger than the bond between the wood fibers themselves (Saleh Pascha, 2014). Modern synthetic resins are inexpensive, easy to apply, and have become so finely tuned that their setting times can be adjusted to facilitate a speedy manufacturing process (Saleh Pascha, 2014).
Modern mass timber adhesives have also come a long way in minimizing the impact of VOCs. Since 2018, the EPA has regulated formaldehyde emissions in laminated wood products. Strict limits have been placed on the formaldehyde off-gassing during production and after curing in the final product that have significantly lowered the environmental and
health life cycle impacts of glues (US EPA, 2023). In general, polyurethane and phenolic adhesives are preferred over ureaformaldehyde and melamine adhesives.
Given that modern mass timber buildings use adhesives that are far superior in strength and water resistance to those used historically, it’s reasonable to expect that the lifespan of a mass timber building completed today can far exceed those of historic structures that remain in use today.
Biogenic carbon, which is produced in natural processes by living organisms, is derived from the atmosphere and is part of a short-term carbon cycle . On the other hand, fossil-fuel based non-biogenic carbon is part of a long-term carbon cycle. It is derived from the earth and is released into the atmosphere permanently, rather than cycling into and out of the atmosphere like biogenic carbon. Sequestered carbon that is retained within wood for less than one hundred years, is considered temporary carbon storage and does not influence the net LCA calculation. If it is retained for more than one hundred years, it is considered permanent carbon storage (Hoxha et al., 2020). This permanent carbon storage is also known as biogenic carbon and produces a net negative impact in a LCA calculation.
A Life Cycle Assessment (LCA) identifies, quantifies, and assesses environmental impacts from raw material extraction through disposal (Elcock, 2007). When conducting an LCA on a mass timber building, biogenic carbon accounts for a significant portion of the benefits of this construction type. Carbon is retained in the wood fiber of a mass timber component throughout its useful life. At the end of its life, if wood is incinerated or left to decay in a forest, this carbon is released back into the atmosphere. If the wood is reused or recycled, this carbon is retained throughout its second life.
Quantifying the benefits of biogenic carbon is challenging. This is due to uncertainty and variability surrounding forestry practices, transportation distances, and end-of-life scenarios. The industry recognizes that to optimize the potential environmental benefits of mass timber construction, wood
should be sustainably sourced and transportation distances should be limited as much as possible. Compared to steel and concrete, extraction and manufacturing of mass timber has approximately 50% of the global warming impact of steel or concrete (Feitel, et al., 2021) We also know that the environmental impact of end-of-life scenarios for mass timber can vary significantly, as is illustrated in Figure I. End-of-life scenarios for concrete and steel are easier to predict because of their longevity of use, the availability of precedent data, and because methods for recycling are wellestablished. Steel is relatively easy to recycle and typically contains a high amount of recycled content. On the other hand, concrete structures are difficult to adapt and recycle, so many concrete buildings are demolished to make way for new construction. Wood fiber can be repurposed a variety of ways at the end of its life – incineration, recycling, reuse, and landfilling -- each option with a different level of environment impact. Incineration (without methane recapture or energy recovery) produces a nearly instantaneous release of carbon, resulting in net positive emissions. Alternatively, adaptive reuse or deconstruction and reuse of mass timber components has the most beneficial net cooling effect.
There is not yet clear industry guidance on whether biogenic carbon should be included in LCA calculations for projects that include engineered wood products. This disagreement is centered around what happens to these products at the end of their useful lives. Those who advocate for biogenic carbon to be excluded from LCA calculations cite the level of uncertainty surrounding end-of-life, while others argue that most wood products will decompose or be incinerated in this stage, thus releasing the CO2 back into the atmosphere.
Those advocating for the inclusion of biogenic carbon in LCA calculations argue that within a typical building’s lifetime, most biogenic carbon will not have been released to the atmosphere, resulting in some long-term storage (Arup, n.d.). Additionally, not all wood within a landfill decomposes within the timeframe of an LCA study and some amount of this waste could be considered permanently sequestered (Arup, n.d.).
The ISO international standard recommends that biogenic carbon be accounted for as a credit, resulting in net negative carbon storage in Stage D if wood is sourced from sustainably managed forests ( International Organization for Standardization, 2017). Wood sourced from the U.S., Canada,
or from third-party certification programs fall within this classification.
What this approach does not account for is the time value of carbon. Similar to investing money, the carbon that is released into the atmosphere today compounds over time. For example, 1,000 kg of CO2 emitted into the atmosphere today has a higher global warming potential than 1,000 kg of CO2 emitted in 50 years (Long-Term Biogenic Carbon Storage, n.d.). This implies that a dynamic approach to biogenic emissions, rather than a static approach like the ISO standard recommends, would be helpful in calculating the full benefits of mass timber reuse and deconstruction
(Long-Term Biogenic Carbon Storage, n.d.). This topic also highlights the importance of designing mass timber buildings with lifespans that exceed the typical 60–100 year average building lifespan.
Research conducted by Dr. Edrit Hoxha, a professor at Aalborg University and an expert in Life Cycle Analysis methods found that, for a wood product, carbon neutrality is achieved in a storage time of about half of the rotation period [of the forest it is sourced from] (Hoxha et al., 2020).” Similar work has been done by Will Hawkins, a lecturer in structural engineering design at the University of Bath whose research focuses on pathways to zero-carbon building structures. His work indicates that biogenic carbon benefits are closely tied to forestry rotation periods for timber products. In a series of calculation Hawkins ran, he found that if wood is sustainably sourced with replanting and carbon absorption, and the structure is in use for one-hundred years, it would be carbon-negative for half of its lifetime [or double an assumed fifty-year harvest cycle]. Alternatively, the same structure demolished after forty years would never reach carbon negative (Hawkins, 2021). This research demonstrates that if mass timber components are designed to be used for over one-hundred years, future buildings that reuse these components after that time could be structurally carbon negative from day one.
To supplement ISO standard recommendations, The Wood Products Council and the Carbon Leadership Forum recommend reporting the amount of biogenic carbon stored in the wood products separate from LCA calculations (How to Include Biogenic Carbon in an LCA, n.d.). Accounting for this value separately allows us to quantify future benefits if the
Non-biogenic Carbon: Derived from the earth, fossilfuel based, and is released into the atmosphere permanently, rather than cycling into and out of the atmosphere like biogenic carbon (The Carbon Leadership Forum, 2019).
Carbon Sequestration: The process of extracting carbon from the atmosphere and storing it in a longterm form. Sequestered carbon can be reported as a negative carbon “emission” (The Carbon Leadership Forum, 2019).
Temporary Carbon Storage: Storage within a 100year period (Hoxha et al., 2020).
Permanent Carbon Storage: Storage for more than 100 years (Hoxha et al., 2020).
Life Cycle Assessment (LCA): A systematic process for identifying, quantifying, and assessing environmental impacts throughout the life cycle of a product, process, or activity. It considers energy and material uses and releases to the environment from ‘cradle to grave’ (Elcock, 2007).
Cradle-to-Grave: From raw material extraction through manufacturing, transportation, use and disposal (Elcock, 2007).
building’s life is extended or the wood products are reused. New tools including Upstream and the WWF Bioenergy Carbon Footprint Tool can be used to run custom scenarios to sharpen projections on the environmental impact of wood sourcing and certification, transportation, and the benefits of adaptive reuse or deconstruction to direct decision-making during the design process.
When considering end-of-life scenarios, it’s important to understand that not all reuse outcomes are comparable. In
line with the concept of cascading, the highest and best use of a mass timber product should be maintained as long as possible. The possible end-of-life scenarios for mass timber exist along a spectrum as shown below.
Lowest to highest value reuse alternatives:
Mass timber waste can be incinerated, resulting in a burst of carbon being released into the atmosphere. When the
time value of carbon is considered, this scenario has the potential to wreak the most havoc on the atmosphere. Mass timber products containing adhesives will contribute more to net warming than those that do not when incinerated (Our Endangered World, 2023).
Landfilling is another low value end-of-life outcome for mass timber construction. In a landfill, some portion of the mass timber waste will slowly decay, releasing biogenic carbon back into the atmosphere. However, some of the wood will not decompose within the timeframe of an LCA study, and could be considered permanently sequestered (Arup, n.d.).
Recycling mass timber into mulch is a form of downcycling. This alternative requires additional processing and associated carbon emissions. Mass timber products containing glues may not be a good candidate for this alternative if they contain glues that have potential for leaching (Our Endangered World, 2023).
The second highest value end-of-life scenario for mass timber is deconstruction for reuse of structural components. Ideally, mass timber elements can be reused as a structural component in a new building or to repair a component in an existing building. The next best alternative is for these elements to be reused for slightly lower value alternatives, such as furniture and interior finishes.
The highest value end-of-life scenario for mass timber is adaptive reuse of the whole building structure. This scenario requires minimal demolition, deconstruction, or reprocessing, and consequently, carries the greatest carbon benefits. To improve the likelihood that mass timber buildings will be adaptively reused, the original design should be aspirational, of high-quality, and should anticipate future change by planning for flexibility.
Alastair Reilly, a Principal at William McDonough Architects and a thought leader on circular economies, advocates for designing buildings for both whole building and component reuse. Anticipating that the demand for housing will increase with growing populations, Reilly designs all new construction office buildings within a 30’ structural grid, which is the standard for multifamily housing, rather than the 20’ structural grid that is more common for office buildings. This adjustment makes the building more adaptable to future demands with minimal investment and will likely have a much longer lifespan as a result (A. Peitz, personal communication, April 14, 2022).
Adaptive reuse and deconstruction for reuse are by far the preferred end-of-life scenarios to optimizing the environmental benefits of mass timber construction. Recycling is a good alternative when adaptive reuse and component reuse is not possible. Other outcomes, including landfilling and incineration, result in loss of value as well negative environmental impacts, and should only be considered when other options have been exhausted (Bergman et al., 2013).
To promote adaptive reuse and deconstruction for reuse, there are several strategies we can apply during the design process. These strategies fall into five categories:
1. Structural Design
2. Finishes + Built-Up Assemblies
3. Systems Distribution
4. Moisture Management
5. Documentation
Hotel Magdalena mass timber erectionThe structural system of a mass timber building should be designed for future adaptability as well as deconstruction. This means designing using large, flexible grids that go above and beyond the needs of first-life program. Grid spans and structural elements should be kept standardized, repetitive, and interchangeable as much as possible to optimize future opportunities for component reuse. This will simplify the initial construction process, and in turn, simplify the deconstruction process.
To accommodate future deconstruction, mass timber connections should be standardized and interchangeable, as well as easy to install (and thus to deconstruct). Avoiding custom or high-capacity connections will facilitate a clear, quick, and easy deconstruction process using standard tools that requires less labor. Connections that require sequential installation should be avoided because they are not intuitive and are likely to stall the deconstruction process or result in damage to structural components. Generally, easy assembly is linked with easy disassembly (Hradil et al., 2014). When permitted by code, connections should be designed with the deconstruction process in mind by keeping connectors exposed .
Screws, bolts, and metal plate connectors facilitate the deconstruction process because they can be removed with minimal damage to the mass timber and connector elements (Hradil et al., 2014; Sandin et al., 2022). Nails require manual removal, are more time-consuming to re-
move, are likely to fail in bending, and therefore are difficult to remove without damaging mass timber components or breaking the fastener (Hradil et al. 2014). Limiting the quantity of mechanical fasteners required for installation is also helpful because it will limit the amount of labor and cost required to install or deconstruct the connection. It is reasonable to expect that salvage mass timber components will be processed similarly to salvage steel. After a steel component is salvaged, its ends are often trimmed off to provide a square, clean base that can be used for a new connection.
When designing for deconstruction and reuse potential, dry assemblies are preferred over wet assemblies. This concept also applies to cast-in-place topping slabs. Concrete topping slabs, while typically separated from direct contact with the mass timber deck using a membrane or acoustic mat, still must be demolished, and removed before deconstruction of the mass timber is possible. Every additional step that must be completed before recovering the mass timber reduces the likelihood of deconstruction and component reuse.
Precast concrete panels provide an alternative to the topping slab that does not require demolition before deconstruction. However, the immense weight of these precast panels makes installation or deconstruction labor intensive and costly when compared to cast-in-place systems.
Seismic environments pose a unique challenge that often leads to reliance on a concrete topping slab to perform as a diaphragm and provide lateral support. Alexis Feitel,
a structural engineer and Team Carbon Unit Director at KL&A, notes that their team always advocates for using the mass timber deck as the diaphragm in seismic environments rather than relying on a concrete topping slab. Feitel notes that this approach provides options for using dry alternatives to cast-in-place concrete and provides access to the deck without demolition, which is beneficial for ensuring future reconfigurability of systems (Allison, Peitz, personal communication, May 25, 2023).
A cast-in-place topping slab is often recommended to meet minimum acoustic requirements or to address vibration concerns. However, there are now a variety of topping options that achieve high levels of acoustic performance and meet minimum mass requirements to address vibration using dry assemblies. These floor assemblies make use of cement board, plywood, gypsum fiberboards, bio-based granules, raised access floors, and a variety of acoustic products to achieve these ratings. When using dry assemblies, seams should be thoughtfully considered to anticipate equipment leaks and cleaning methods to ensure that moisture cannot seep through the assembly.
Similar to the challenges encountered during residential deconstruction efforts, wet assemblies that include adhesives present unique challenges. In many cases, the effort and cost required to remove adhesive materials from a mass timber element outweighs the potential benefits for reuse.
Building D(emountable), built in Delft, Netherlands, is an excellent example of deconstructable design using dry assemblies as an alternative to the topping slab and at the exterior envelope. This office building was designed to be relocated and rebuilt or to be deconstructed so that components could be used on future projects. Rather than using a cementitious topping slab on top of their laminated veneer lumber (LVL) deck, the topping selected is an “easily removable bio-based screed…filled with gravel-
like granules in a cardboard honeycomb” and topped with gypsum fiberboards as shown in Figure J. (Critescu et al., 2020). This combination of materials achieves a density that contributes to acoustic performance and serves as a diaphragm. This commitment to demountable construction is carried to the exterior envelope, which is composed of dry mounted prefabricated panels (Critescu et al., 2020). It is important to note that the install process for this dry assembly was likely more labor and cost intensive than a cast-in-place concrete alternative. However, this difference will be made up in the deconstruction process since no demolition will be required for disassembly.
Additional finishes beyond a protective clear coat should be avoided if possible. In a deconstruction scenario, finishes will require additional processing to remove the finish to make it suitable for reuse, potentially deterring recovery of the mass timber.
System distribution strategies should be designed to accommodate reconfigurability and adaptability , rather than customized to accommodate first-life systems. One way to do this is to use a raised access floor system, like that used on the Soto office building in San Antonio, TX (Figure K.) A raised access floor comes in a variety of depths to accommodate a variety of systems, including air distribution. Additionally, it can be reconfigured regularly with no impact on structural components.
Alternatively, the deck can be designed with larger voids that can accommodate new and future systems. The PAE Living Building project in Portland, OR incorporates 2’
wide, shallow raceways between CLT panels, spanned by a plywood panel to create a void for conduit and sprinkler lines as shown in Figure N. (Woodworks Innovation Network, n.d.) After systems were installed, the raceway was covered with panels and fixtures and devices were installed (Libby, 2022).
At the Wood Innovation Center in Prince George, Columbia, CLT panels are staggered to create voids within the ceiling and below the floor as shown in Figure O. At the ceiling, these gaps are screened by gapped wood panels. At the floor, this gap is spanned by a plywood panel that is covered in an acoustic underlayment and finished with carpet tile. Since there is not a concrete topping, this raceway remains
accessible for maintenance or future updates (Wood Innovation and Design Centre, 2015).
Platte Fifteen, a mass timber office building in Denver, Colorado, uses another approach to accomplish a similar level of flexibility as shown in Figure L. and Figure M. below.
Girders run longitudinally. The central bay of the building is free from these girders, allowing systems to run within the depth of the beam structure. Joists are stacked on top of girders, running perpendicular to these systems. Systems run outward from the central bay out to the perimeter of the building through voids created in the stacked structure. This approach eliminates the need for cutouts and provides a hyper flexible distribution strategy.
3’’ reinforced concrete topping slab
conduit and sprinkler lines
2’-0’’
fire protection
7/8’’ plywood sheathing
3-play cross-laminated timber
glulam column beyond
conduit and sprinkler lines ductwork
conduit and sprinkler lines
carpet
CLT panel concrete topping slab
rigid insulation
2-ply plywood
1/4’’ acoustical underlayment
3-ply CLT panel
glulam beam beyond
In addition to structural and connection design, designers should consider moisture management strategies to ensure that the quality and capacity of the mass timber components is not diminished over time. It is understood that exposure to high levels of moisture can reduce the structural capacity of mass timber components. This is reflected in the evaluation of structural components at ‘Building Two,’ which found no loss in structural capacity of mass timber elements that remained protected from moisture over seventy-six years, and a significant loss in structural capacity of the unit exposed to moisture during that time (Rammer & Moura, 2013). Similarly, when regrading timber structural elements for reuse, if the component was previously used in an exterior application or was heavily loaded, the strength grade should be reduced by two steps (Hradil et al., 2014).
Treated mass timber has limited end of life recovery scenarios. Treated timber is very rarely sorted and is usually landfilled (Love, 2007). Methods used to process treated timber and make it safe for recycling, landfill disposal, or incineration are time consuming, expensive, and not generally feasible (Love, 2007).
In addition to levels of exposure intended within the original design, it is also important to anticipate unintended sources of moisture exposure. Every component in the exterior envelope may pose a threat to mass timber if it is not maintained over time. It is important to consider the lifespan of each element, such as a vapor barrier with a lifespan that is less than fifty years. It is best to select materials with longer lifespans to minimize the opportunities for unintended exposure over the lifetime of a building
One of the most impactful things that can be done to ensure that a building can be adapted for future uses is to document the as-built conditions (including shop drawings). Designers should work with the client to create a plan to ensure that drawings will be updated to reflect changes over time and will remain accessible regardless of turnover or sale of the property.
To ensure that structural components can be deconstructed and reused, it is important to understand material composition, sourcing, structural capacity, and past uses. Previously noted processes for identifying structural elements, such as material passports or physical stamping can be utilized to support this process. However, a universal method of labeling mass timber components has yet to be developed. Challenges that will need to be anticipated as solutions are generated are longevity of the label (will this label be legible 100+ years in the future?) and how to incorporate labeling into the manufacturing process in a cost-effective way.
One of the most common challenges faced in the field that can be difficult to predict is the use of “non-prescribed fasteners” (Sandin et al., 2022). These are typically nails that are installed in the field that are not indicated in the original drawing set. These nails are usually installed because they are perceived by the installer as necessary to keep an element in place connecting it or required to tighten a joint. These additional fasteners are difficult to detect and remove, can inhibit the deconstruction process and lead to damage of structural components. Furthermore, “non-
prescribed fasteners” can pose a risk to the health and safety of workers during the deconstruction process. During a deconstruction case study at Villa Annenburg, existing trusses were connected with nails that were unknown to the disassembly team. As a crane attempted to lift the trusses, the team was not aware that the trusses were stuck, and the nails yielded suddenly (Sandin et al., 2022).
To avoid non-prescribed fasteners, it is important to include a note within the drawings set that these should be avoided. This message should be reiterated to the mass timber erection team. Additional measures that can be taken are to plan for more elements to be pre-assembled in a factory, where only planned fasteners are used (Sandin et al., 2022).
Beyond this simple list of recommendations, the single most effective thing we can do as designers to promote the reuse of existing building stock is to design beautiful, high quality, durable, well-functioning buildings that people come to love. In return, people will continue investing money and effort into maintaining and adapting these spaces over time.
Steel and concrete structures are robust and resilient enough to last hundreds of years. However, to survive these structures must also be inspiring and beautiful. A building needs to feel precious enough for people to want to maintain and reuse it. Too often, steel and concrete structures fail to capture the hearts of their users, eventually fall into disrepair, and are ultimately demolished.
Mass timber naturally lends itself to creating warm, inviting, beautiful spaces where people feel comfortable. Beyond this, wood is a material whose value can actually increase over time. Unlike other structural materials like concrete or steel, wood shows its age honestly. The older wood gets, the more it reflects its previous lives and experiences. With old wood comes a story that instills the material with character and a sense of authenticity. This is why salvage wood can be sold at a premium to virgin material.
It seems likely that this quality can be leveraged in salvaged mass timber elements as well. Imagine a flourishing mass timber market where “new” buildings are composed of mass timber structural components pulled from various deconstructed buildings -- embracing variations in color and finish, connection type, and wear -- all collaged together
within a single structural system. Structural components from especially notable mass timber buildings may be in highest demand so that “newly” constructed buildings may boast that they own a piece of that previous history, retelling these stories within a lobby or gallery space. A column from a retired multifamily building where a child’s height was marked as they grew may be reused in a new single-family home because of its sentimental value.
This is the vision that designers must strive for as we advocate for design changes that account for the future adaptability of mass timber structures. There is much more work to be done to achieve this vision, including making EPDs an industrywide standard, the advancement of more customizable LCA tools, the development of dry, low embodied carbon assemblies that meet acoustic and fire requirements, additional research simulating the deconstruction process of mass timber components, and the promotion of circular economy through financial incentives, policy, and salvaged material databases.
The decisions we are making today will either facilitate or impede our ability to reuse, deconstruct, or recycle mass timber building components for hundreds of years in the future. As designers we should embrace this future-forward approach on every project and advocate for this level of foresight in every aspect of design.
Bergman, R. D., Falk, R. H., Gu, H., Napier, T. R., & Meil, J. (2013). Life-cycle energy and GHG emissions for new and recovered softwood framing lumber and hardwood flooring considering end-of-life scenarios. Res. Pap. FPL-RP-672. Madison, WI: U.S. Department of Agriculture, Forest Service, Forest Products Laboratory. 35 p.
Brandao, M. Levasseur, A. Kirschbaum, M. U. F., Weidema, B. P., Cowie, A. L., Jorgensen, S. V., Hauschild, M. Z., Pennington, D. W., & Chomkhamsri, K. (2013). Key issues and options in accounting for carbon sequestration and temporary storage in life cycle assessment and carbon footprinting. International Journal of Life Cycle Assessment, 18, 230-240. https://doi.org/10.1007/s11367012-0451-6
Building D(emountable) / architectenbureau cepezed. (2020). ArchDaily. https://www.archdaily.com/936389/ building-d-emountable-architectenbureau-cepezed
Building a world free from waste and pollution. (2021). Ellen MacArthur Foundation. Retrieved March 27, 2023, from https://ellenmacarthurfoundation.org/articles/ building-a-world-free-from-waste-and-pollution
Churkina, G., Organschi, A., Reyer, C. P. O., Ruff, A., Vinke, K., Liu, Z., Reck, B. K., Graedel, T. E., & Schellnhuber, H. J. (2020). Buildings as a global carbon sink. Nature Sustainability, 3(4), 269–276. https://doi.org/10.1038/ s41893-019-0462-4
Circle Economy. (2022). The Circularity Gap Report 2022 (pp. 1-64, Rep.). Amsterdam: Circle Economy.
Creasman, P.P. (2013). Ship Timber and the Reuse of Wood in Ancient Egypt. Journal of Egyptian History, 6, 152-176.
Cristescu, C., Honfi, D., Sandberg, K., Sandin, Y., Shotton, E., Walsh, S., Cramer, M., Ridley-Ellis, D., Risse, M., Ivanica, R., Harte, A., UiChulain, C., De Arana-Fernandez, M., Llana, D. F., Iniguez-Gonzalez, G., Garcia Barbero, M., Nasiri, B., Hughes, M., & Krofl, Z. (2020). InFutURe Wood Report 1: Design for deconstruction and reuse of timber structures – state of the art review. ForestValue.
Elcock, D. (2007). Life-cycle Thinking for the Oil and Gas Exploration. Argonne National Laboratory. https://www.evs. anl.gov/plublications/doc/LCA_final_report.pdf
EPA. (1998). Extended Product Responsibility: A Strategic Framework for Sustainable Products. EPA530-K-98-004. Solid Waste and emergency Response (5306W). https:// archive.epa.gov/wastes/conserve/tools/stewardship/web/ pdf/eprbrochure.pdf
Hawkins, W. (2021). Timber and carbon sequestration. Structural Engineer. 99. 18. https://doi.org/10.56330/ ALFK4016
Heinrich, M., & Lang, W. (2019). Materials Passports – Best Practice. Innovative Solutions for a Transition to a Circular Economy in the Built Environment. Technische Universitat Munchen, in association with Buildings As Material Banks (BAMB).
Höglmeier, K., Weber-Blaschke, G., & Richter, K. (2013). Potentials for cascading of recovered wood from building deconstruction—A case study for south-east Germany, Resources, Conservation and Recycling. 78, 81-91. https:// doi.org/10.1016/j.resconrec.2013.07.004.
Hoxha, E., Passer, A., Saade, M. R. M., Trigaux, D., Shuttleworth, A., Pittau, F., Allacker, K., & Habert, G. (2020). Biogenic carbon in buildings: a critical overview of LCA methods. Buildings and Cities, 1(1), pp. 504-524. https:// doi.org/10.5334/bc.46
Hradil, P., Asko, T., Wahlström, M., Huuhka, S., Lahdensivu, J., & Pikkuvirta, J. (2014). Re-use of structural elements; Environmentally efficient recovery of building components. 10.13140/2.1.1771.9363.
IPCC, Summary for Policymakers. Cambridge, United Kingdom and New York, NY, USA: Cambridge University Press, 2014.
International Organization for Standardization. (2017). Sustainability in buildings and civil engineering works – Core rules for environmental product declarations of construction products and services (ISO 21930:2017).
Lehman, E. (2018). October 15, 1934: Glued Laminated Timber Comes to America. Forest History Society. https:// foresthistory.org/october-15-1934-glued-laminatedtimber-comes-to-america/
Leonard, A.G.K. (2008). Josiah George Poole (18181897): Architect and Surveyor serving Southampton. Journal of the Southampton Local History Forum, 13-27. https://southamptonlocalhistorycentre.files.wordpress. com/2014/11/lhf-journal-13-spring-2008.pdf
Lewis, M., Huang, M., Carlisle, S., & Simonen, K. (2023). AIA-CLF Embodied Carbon Toolkit for Architects. Part I. Introduction to Embodied Carbon. Carbon Leadership Forum.
Libby, B. (December 2022). The PAE Living Building Rises in Portland, Oregon. Metropolis Magazine. https:// metropolismag.com/projects/the-pae-living-buildingportland/
Lippke, B., Puettmann, M., Oneil, E., & Dearing Oliver, C. (2021). The Plant a Trillion Trees Campaign to Reduce Global Warming – Fleshing Out the Concept. Journal of Sustainable Forestry, 40(1), 1–31. https://doi.org/10.1080/1 0549811.2021.1894951
Long-Term Biogenic Carbon Storage. (n.d.). WoodWorks | Wood Products Council. Retrieved March 28, 2023, from https://www.woodworks.org/resources/long-termbiogenic-carbon-storage/
Love, S. (2007). Extended producer responsibility of treated timber waste. Paper presented to Sustainable Building Conference (SB07), Auckland, 14-16 November.
Moody, R. C. & Hernandez, R. (1997). Chapter 1: GluedLaminated Timber. Engineered wood products - A guide for specifiers, designers, and users. USDA Forest Service, Forest Products Laboratory. Chapter 1. p.1-1 - 1-39.
Nunes, Andey & Palmeri, Jordan & Love, Simon. (2019). Deconstruction vs. Demolition: An evaluation of carbon and energy impacts from deconstructed homes in the City of Portland Submitted to: City of Portland Bureau of Planning and Sustainability (BPS).
O’Connor, J. (2004). Survey on actual service lives for North American buildings. Forintek Canada Corporation.
Our Endangered World. (2023). Is Epoxy Resin Bad for the Environment? https://www.ourendangeredworld.com/eco/ is-epoxy-resin-bad-for-the-environment/
Haddadi, R., & Rinke, M. (2020). Early glulam for temporary large scale structures in Switzerland. Iron, Steel and Buildings: Studies in the History of Construction. The Proceedings of the Seventh Annual Conferences of the Construction History Society. 477-488. University of Antwerp. https://hdl.handle. net/10067/1731640151162165141
How to Include Biogenic Carbon in an LCA. (n.d.). WoodWorks | Wood Products Council. Retrieved March 28, 2023, from https://www.woodworks.org/resources/how-toinclude-biogenic-carbon-in-an-lca/
Nicklin, A. & Falk, B. (2020). Reclaiming the Future: What’s New in Used Wood. Docslib. Retrieved March 28, 2023, from https://docslib.org/doc/10857866/reclaiming-thefuture-whats-new-in-used-wood
Rammer, D. R. & Moura, J. (2013). Structural evaluation of the second oldest glued-laminated structure in the United States. In: Gen. Tech. Rept. FPL-GTR-226. Madison, WI: U.S. Department of Agriculture, Forest Service, Forest Products Laboratory. 269-276.
Rypkema, D., Grosicki, B., Swink, R., Cotton, K., Frystak, A., Bruni, C., & Herr-Cardillo, S. (2021). Treasure in the Walls – Reclaiming Value Through Material Reuse in San Antonio. PlaceEconomics.
Saleh Pascha, K. (2014). Developments in timber construction materials. Emergent Timber Technologies Materials, Structures, Engineering, Projects. 36-57. 10.1515/9783038216162.
Sandin, Y., Shotton, E., Cramer, M., Sandberg, K., Walsh, S. J., Östling, J., Cristescu, C., González-Alegre, V., Íñiguez-González, G., Llana, D. F., Carlsson, A., Ui Chulain, Caitriona, Jackson, N., Barbero, M., & Mejía, A. (2022). Design of Timber Buildings for Deconstruction and Reuse — Three methods and five case studies (open access).
Spartz, J. T. (2014). Historic Glued-Laminated Arches Evaluated for Structural Quality Lab Notes. https://www. fpl.fs.usda.gov/labnotes/?p=2593
The Carbon Leadership Forum. (2019). Life Cycle Assessment of Buildings: A Practice Guide. Version 1.1. http://hdl.handle.net/1773/41885
The Circularity Gap Report. (2022). Circle Economy. https://drive.google.com/file/d/1NMAUtZcoSLwmHt_ r5TLWwB28QJDghi6Q/view?usp=embed_facebook
The Delphi Group. (2021). Circular Economy & The Built Environment Sector in Canada. Final Report.
Toth, Z., Volt, J., & Jankovic, I. (2021). A Paris-Proof Retail Real Estate Sector. Taking Stock of Regulatory and Market Developments. Buildings Performance Institute Europe (BPIE).
Unit Structures, Inc. (n.d.). Retrieved March 28, 2023, from https://www.facebook.com/people/Unit-StructuresInc/100063746191371/
When to Include Biogenic Carbon in an LCA. (n.d.). WoodWorks | Wood Products Council. Retrieved March 28, 2023, from https://www.woodworks.org/resources/whento-include-biogenic-carbon-in-an-lca/
Wood, S. (n.d.). Deconstruction Program – City of Portland, Oregon. Bureau of Planning and Sustainability. Webinar Presentation.
Wood Innovation and Design Centre. (2015, November 9). Architect Magazine. https://www.architectmagazine.com/ project-gallery/wood-innovation-and-design-centre_o Woodworks Innovation Network. (n.d.). PAE Living Building. Retrieved March 29, 2023, from https://www. woodworksinnovationnetwork.org/projects/pae-livingbuilding
WWF Webinar on Bioenergy Carbon Footprint Tool. (2021). Webinar. World Wildlife Fund. Retrieved March 28, 2023, from https://www.worldwildlife.org/videos/wwf-webinaron-bioenergy-carbon-footprint-tool
ZGF. (2001). Measuring Lifecycle Impacts of Wood With New Sustainable LCA Tool Retrieved March 28, 2023, from https://www.zgf.com/ideas/3356-new-tool-helpsdesigners-measure-lifecycle-impacts-of-wood
Thank you to:
Alexis Feitel, PE
Structural Engineer + Team Carbon Unit Director
KL&A Engineers & Builders
Kate Sector, LEED GA, LFA, WELL AP
Design Performance Manager
Lake|Flato Architects
Ryan Yaden, AIA, LEED AP BD+C Associate Partner
Lake|Flato Architects
who shared their time and expertise by serving as reviewers for this paper.