
17 minute read
Software: Manufacturing Execution Systems in bakeries
from f2m Automation Book
by landmagd
MES in bakeries
Every bakery is familiar with software terms such as cash register system, ERP, merchandise management, recipe management, shipping system and a few more. In the meantime, the term MES has also entered the vocabulary of innovative bakery businesses.
+MES, Manufacturing Execution System is a software solution that manages, controls and monitors a production process. An MES system can map the entire production process from planning to quality assurance, effectiveness measurement and much more, from goods receipt to goods issue.
What is the difference between ERP systems, MES and recipe management?
ERP (Enterprise Resource Planning) systems, also known as merchandise management systems, regulate the business processes in companies. In the ERP system, suppliers are managed in food companies, orders are triggered at suppliers, branches or other customers’ orders are accepted or invoices are created. These are functions that map the commercial process.
MES systems regulate the production process. In MES systems three main resources are managed: Personnel, Material and Equipment. These resources are also used in ERP systems to calculate products. Production plans are also created in the ERP system, but ERP systems lack real-time reference to production.
MES systems are closer to production. In the MES system, detailed production planning is carried out on the basis of the actual availability of resources. Compliance with the production plan can be monitored in real-time and short-term measures can be taken to reschedule in the event of deviations. Qualitative production data acquisition in real-time in the form of continuous quality checks by tapping machine data or recording random checks by employees are also typical features of MES systems.
In contrast to ERP systems, the data in MES systems is recorded promptly and punctually made available to the employee as support in production. In this way, the production manager or line supervisor has a view of the actual situation of production quality and performance at all times and can react immediately in the event of deviations.
Recipe management is a module of a MES system. Recipes are of course also required in ERP systems for product costing. In MES systems, recipes are referred to as processes. Processes take into account all three resources: material, personnel and equipment. In ERP systems, only the material list, the so-called Bill of Material (BOM), is required for price and nutritional value calculation.
In MES systems, the entire production process can be described in the recipes. In this way, technical steps such as kneading times, stirring times for sourdough production, temperature setpoints for production processes, etc. are also defined. These steps are then passed on to the plant or plant section in the correct sequence at the correct time. The actual measured values are returned by the machines as feedback. In this way, it is
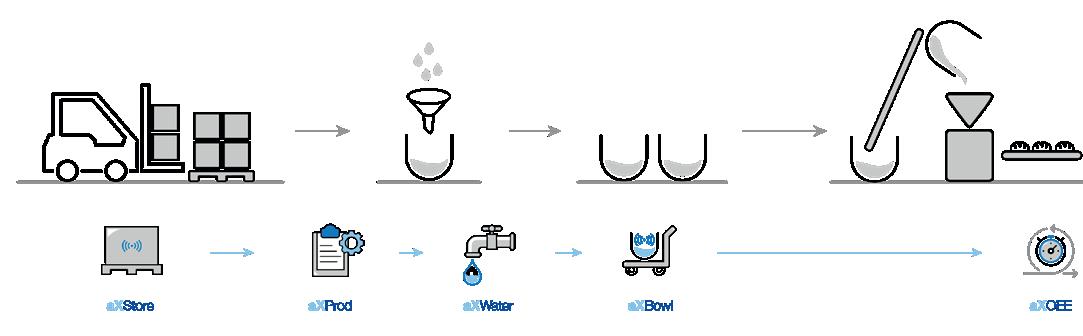
possible to determine whether production has actually run as planned.
In ERP systems, especially in those that offer modules for food companies, the creation of process parameters in their software is also possible, but the reference to the production plant is missing.
What is the interface between the ERP system and MES?
A distinction is made here between the type of data transmission and the content of an interface. In the type of data transmission, different methods have been established in the past. Previously, data was sent from one system to another in file form. Today, data is exchanged in real-time using secure protocols. However, this is basically just the physics of how data gets from one system to the other. Much more important is the content of the interface.
Who is the master of which data?
The article master is basically created and managed in ERP systems. This includes raw materials, semi-finished products, doughs, production items, sales items, etc. Also, product prices, data about different suppliers of raw materials are in the master data of ERP systems. The so-called master data is synchronized with the MES system via the interface. Data is maintained in only one system at a time.
Information and properties of this article master data are added in the MES system. Additions include the specific weight, tolerances for raw material dosing and preferred storage location. Here, it is not possible to define a clear boundary, since ERP systems can also take over MES tasks, and vice versa. Two examples of this are warehouse management and batch tracking. These functionalities are provided in both ERP and MES systems. This raises the question of which should do what.
Warehouse management – ERP or MES
Here we want to look primarily at the raw material warehouses, from the contents of which sales items are produced. This module is available in almost all ERP systems. However, MES systems also cover this function. There are also pure warehouse management systems that are advertised on the market. Maybe the following will guide your decision.
The warehouse management starts with the raw material acceptance in the goods receipt area. The information about delivery date, delivery quantity and the supplier are available in the ERP system. This would lead to the conclusion that logically the goods receipt process and the warehouse process are also carried out by the ERP system. Further questions are in the room, such as who does continuous batch tracing, how are silos filled with raw material etc.. In the latter case, an interface to the MES system or the silo/ recipe administrations is always up for discussion.
Information about the total stock of raw materials is a must in ERP systems. These order from suppliers on the basis of various criteria such as minimum stock, calculated stock range or sales forecasts. However, this does not require detailed information about the respective storage location, but only the total.
© AutomationX
When deciding which system to use for detailed warehouse management based on the section and the location of the storage, the following questions make the decision easier. + Which system guarantees continuous batch tracing? + Which functions does the ERP or MES system offer? + Which do I feel more comfortable handling?
For continuous and, above all, relatively accurate batch tracing from the raw material to the sales item, not only are the goods movements in the warehouse necessary, but also very often information from machines. Let's take the example of a flour dosing point with manual feeding of the kettle to the kneader and then on to the lifting tipper. The kettles can be automatically identified at the individual processing points. This requires reading the RFID information of the respective boilers. Here it could happen that the order of the boilers changes. When the boiler is then handed over at the lifting tipper for processing, the MES system knows exactly the time, the boiler number and the contents of the boiler with the raw materials contained therein that were handed over for processing. This example can be continued up to the sales item. MES systems usually find it easier to collect and process this kind of information, since the integrated interfaces to machines and plants are a feature of such systems. For this reason, the part upstream of production, i.e. the raw materials warehouse, is often managed by the MES system, especially in automated production operations. This means that the data on the movement of raw materials through the individual warehouses to the dough, as well as the data for further processing in kettles or even continuously to the sales item, are recorded and stored in one system. The alternative to managing the raw materials warehouse in the ERP system or even in a separate warehouse
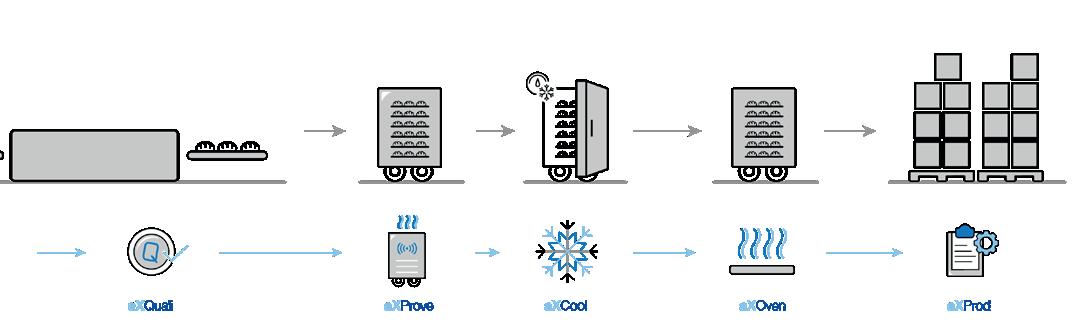

© AutomationX
INTERVIEW MES IN BAKERIES
management system is of course also state of the art. Intelligent data transfer of raw material data from the ERP to the MES and back again also enables traceability in one system.
If warehouse management is controlled via a MES system, the delivery note data must be transferred from the ERP system to the MES system for the delivery of raw materials. In the goods receipt area, qualitative and quantitative control of the goods takes place. In the process, article master data transferred from the ERP system is enriched with properties such as inspection parameters. Likewise, data on the minimum shelf life (best before date), lot ID of the goods are added via manual entry or scanning of a barcode. The flexibility to add properties and parameters to articles is predominantly higher in MES systems and a standard. In ERP systems it is very product-dependent. Some ERP systems offer very flexible solutions and have integrated MES functionality, others focus on pure ERP functionalities. For example, ERP vendors that serve the bakery segment and want to cover production control, in particular, have added MES functionalities to their products. Other products focus on their very own merchandise management functions and have developed the product in the direction of store management. Some systems use Microsoft products as a base system and develop their own solutions. Depending on the ERP system used, information must therefore be added to one or the other system. Very often, customers wish to keep the ERP system as standard as possible and to map processes that require interaction with production staff in the MES system. The possibility of adapting the operator interface to the warehouse worker according to the customer's wishes and making it as user-friendly as possible is higher in MES systems.
Further bookings in different storage areas, block storage and single place storage are covered by mobile terminals; this is the same in ERP as well as MES systems.
When goods are received into the silo, there is a technical interface to the silo system. The corresponding silo must be released for filling and the batch data must be carried in the silo. This task can also be solved in both systems.
Conclusion: Both systems provide solutions and there are no significant differences. The decision lies in the price/performance ratio of the functionality on offer.
Dosing control – Recipe management
Dough production is an essential sub-process in bakeries. We are not only talking about dosing, but the complete process up to the transfer of the dough to processing, either via continuous conveying or batch production.
Manufacturers of silo plants very often offer – especially for bakeries – their own software solution or software solutions from partners who work almost exclusively for the plant manufacturer. The solutions are in a proven combination – recipe control – silo plant, which is often tested and matured in use. In other industries, e.g. in construction chemistry, this is not common The advantage of procuring everything from one source, however, also has disadvantages. Software solutions that are specifically tailored to the plant construction of one or more manufacturers
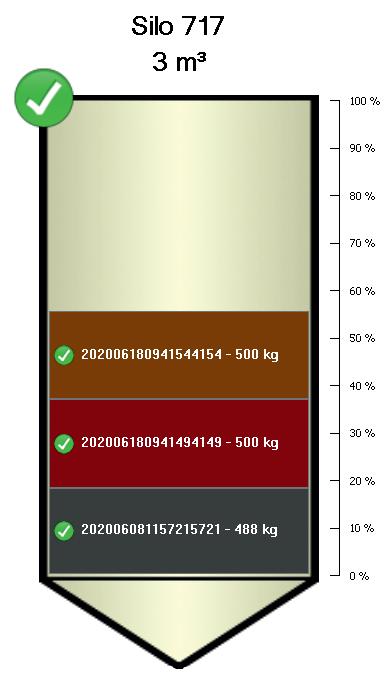
usually do not cover the upstream and downstream processes. Although these systems have been enriched with functionalities in recent years so that the process can be controlled up to the point of transfer to reprocessing, more advanced functions such as quality assurance, efficiency analysis, labeling, batch tracing through to the finished article are usually not available.
If you want to digitally map the entire process up to the finished product now or in the future, it also pays to talk to MES system manufacturers both for control system upgrades and for new plant construction.
Above all, it is important to keep the number of software interfaces and the number of different software systems to a minimum. Higher maintenance and servicing costs will come with more different systems. It also should not be forgotten that software systems have to be updated cyclically.
A completely independent software solution also offers the advantage of being able to combine different system designs depending on their strengths.
If one decides in favor of an independent solution, there are a few things to consider. In the implementation, there is another interface, namely the one from the software manufacturer to one or more plant constructors. As a rule, the trades are commissioned separately. This can save costs, but the customer also has to coordinate the systems. Here it must be clearly defined in advance who is responsible for what. It is advisable to take a close look at the service, product functionality and manpower of the software company before making a decision. Important questions are: Does the company offer 24/7 support? Who picks up the phone? How many people take turns on the hotline? Do the support staff understand the system?
Take your time making your selection and check carefully. Mechanics are easier to change and replace than the heart of the system, the software!
Quality assurance – a topic for you?
From the processing of the dough to the produced article and the article on sale, quality tests are usually carried out by every company today. Recording results is still done manually in many companies. The data is later transferred to Excel lists and evaluated again later. This is time-consuming and error-prone – both when recording the data and when transferring it to electronic systems.
Often the sampling control is done via the software of scale manufacturers. This in turn has the disadvantage of adding a further interface to an ERP system in which the master data is transferred – unless one manages data twice, which in itself is the most cumbersome and inefficient way.
MES systems have a QA module on board. As mentioned at the beginning of this article, the entire production process can be mapped in MES systems. Thus, quality measuring points can be defined for the reprocessing lines. The production or sales articles from the article master, which is synchronized with the ERP system, are only enriched with information, such as in which cycle the various parameters are to be checked and at which quality measuring points. Weighing data is recorded directly via scales and, of course, does not have to be entered separately. Since MES systems are designed to connect machines and systems, data that is valuable for product quality, such as the humidity and temperature in fermenters, can be recorded automatically.
OEE
Not only is quality decisive for success! But also efficiency paired with top quality is the desired combination, whether in industrial or craft enterprises. MES systems provide a module – OEE – (Overall Equipment Effectiveness) for this purpose.
The use of OEE solutions has been common practice in the automotive industry for decades. In the bakery industry, the demand for corresponding software solutions is increasing in order
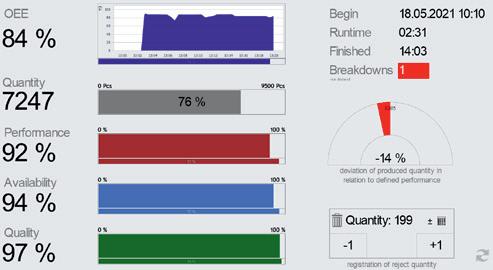
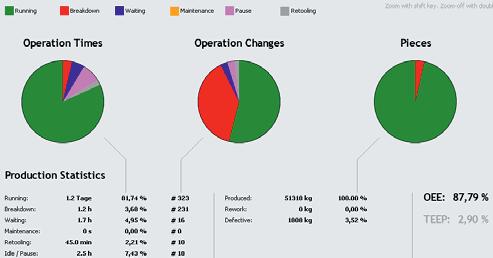
Real-time display of production progress with deviations to be able to produce even more efficiently and with higher quality. A frequent challenge in the bakery industry is the collection of data (production data acquisition – PDA). This can be done automatically or manually. Anyone who believes that everything works automatically is mistaken!
How does the data automatically get from the machine to the software?
Modern machine controls offer the possibility of exchanging data via a standardized interface (OPC UA). Attention! A standard interface is a means to an end The content of the interface must be defined. Not every machine can transmit the same data. For example, in the case of a spiral freezer, the temperature setpoint and actual value are primarily relevant, and in the case of a dough divider, the number of pieces. The data to be exchanged must be provided by the machine manufacturer. In the case of older systems, it is sometimes necessary to install additional sensors if it is not possible to tap the data automatically. In particular, if spare parts are no longer available for the existing control system, consideration should be given to upgrading the system to acquire additional data when replacing the control system. (The data acquisition is mostly an interplay of automatically acquired data, which is then added manually).
Essentially, the following information is important. Performance data: How many pieces are currently being produced on the machine? If more pieces are produced than specified, the power factor can also be over 100 %. If the machine does not provide this data, this can be realized by mounting additional sensors. Quality data: For some machines, the temperature, relative humidity or other measured parameters influence the product quality. In any case, such data should also be transmitted and recorded. The data is displayed in trends in relation to a product and allows conclusions to be drawn about quality deviations in a simple manner. Fault messages: Ideally, all faults are transmitted to the MES system with their priority defined in the MES system. Many small faults do not affect production and are therefore not interesting for an effectiveness analysis.
Is it possible to record staff time?
Yes, and quite simply. The employee logs on to an order that is displayed on a touch panel, e.g. via RFID or barcode. Personnel times are then added up for the order according to the current order status. If the status ‘Setup’ is selected, personnel times are booked to ‘Setup’.
Does the data acquisition function fully automatically?
No. Machines only provide partial information. An example: The information as to whether a machine is ready for operation, switched off or in operation is usually supplied by the machine. Information about rejects or whether maintenance is currently being carried out is very important for evaluations, but must be entered manually or recorded semi-automatically. In particular, any scrap must be able to be recorded easily. After all, no one counts the individual pieces that are selected from a conveyor belt. Usually, the best
way to do this is to collect the scrap in containers and then weigh it. If the rejects are added to a dough batch again (rework), the batch tracing can also be mapped in the system.
Isn’t manual entry too complicated for an operator?
Ease of use is a key requirement in bakery operations. Here the suppliers of MES systems differ significantly, as different industries also have different requirements. Experience has shown that in the food industry, less is more. The input screen must be clearly designed and easy to use. The screens on the line can also be used for multiple purposes, such as quality data acquisition or weighing.
Who benefits from an MES system?
The data from MES systems are useful for the user on the line up to the company manager. The user on the line receives the order progress and the effectiveness from the OEE module via a large display. For example, it can be seen whether the planned order will be completed earlier or later than planned.
The QA module shows the line operator whether there are deviations in the quality. For example, continuous or random weight measurements after the dough divider are useful in order to maintain the required product weight and not to exceed – and above all not to fall below – it.
The technician can see via an evaluation what faults have occurred, how often they have happened and the duration of the interruptions to operations caused by them. The analysis facilitates prioritization in the elimination of defects. All events, including their causes, are documented. All activities of the respective technicians in their shifts can also be recorded via a shift book.
The production manager receives an overall view of the manufacturing process. In the event of changes to machine settings or the production process, it can be very clearly displayed whether an improvement in performance or quality could be achieved as a result. At the push of a button, the quality manager has a continuous log of the production process from goods receipt to the finished product. In case of deviations in the final product, the data of the individual production steps can be analyzed to find the causes – and this is from the raw material quality and batch number of a used raw material at delivery. The evaluations can be adapted to the needs of users in MES systems. Not everyone requires the same information. This is done by adapting tables such as showing and hiding columns and saving filters and queries, configuring dashboards and much more. By assigning rights, the respective user only sees the information that is important to them.
Also, a report generator is on board, providing PDF reports at certain intervals or when an event is set to generate one (i.e., when an order is completed). These reports can then be sent automatically or stored on a file system to make information from the system available to employees who do not work with the MES system.
Conclusion
In many industries, MES systems are already indispensable support for managing the production process. Bakery companies are constantly working to increase the efficiency of their production processes and the quality of their products. The software industry has recognized this need, and in the meantime manufacturers of MES systems have also adapted their solutions to this market or developed their own modules.
In the experience of AutomationX GmbH, solutions implemented in the bakery industry have shown that the benefits far outweigh the costs of introducing the system. The systems have established themselves as an indispensable part of production control. +++
Author
Thomas Mühlheimer, AutomationX. The company develops solutions ranging from the complete digitization of individual components to plant-wide production optimization.