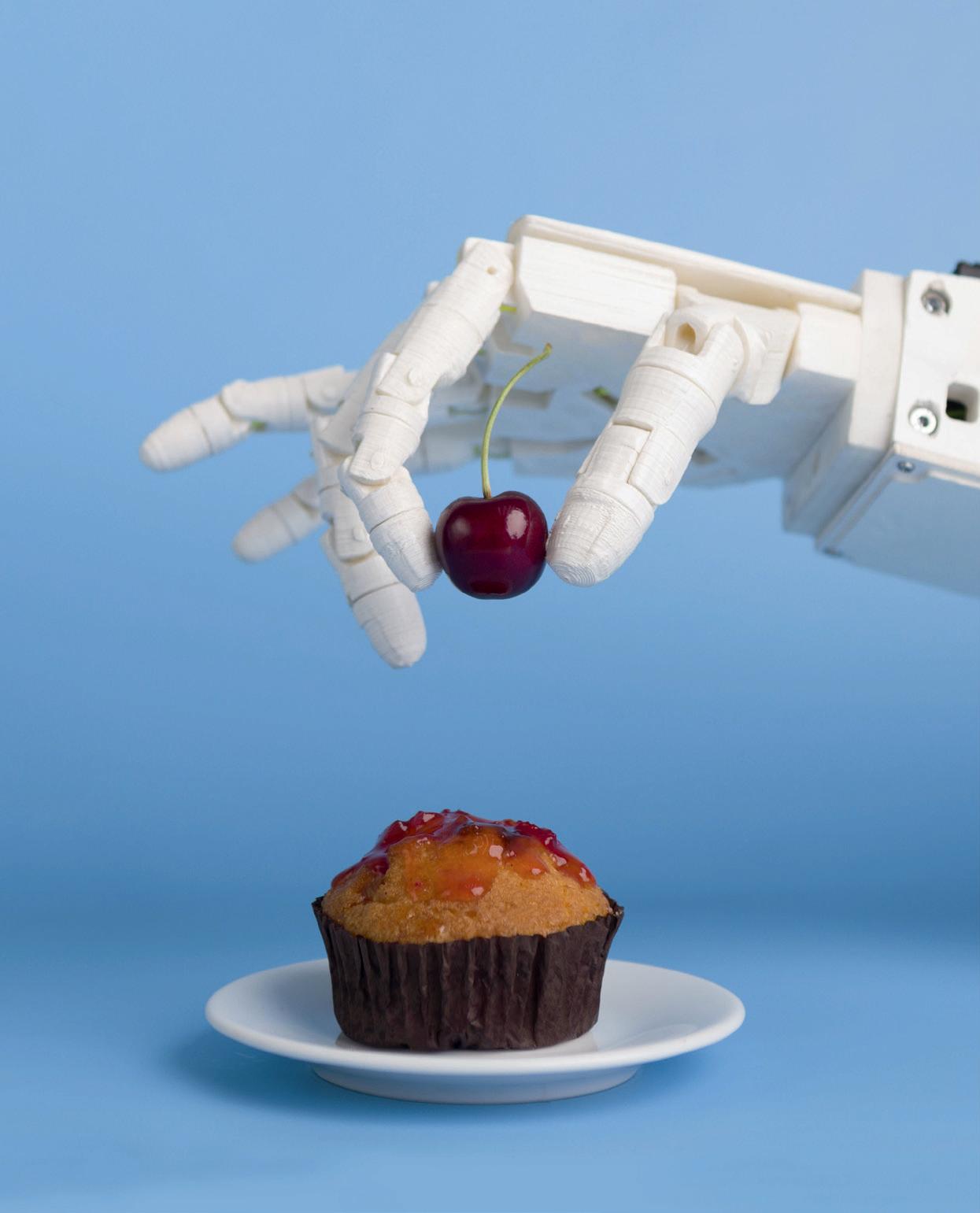
12 minute read
Robotics: Autonomous performance
from f2m Automation Book
by landmagd
Autonomous performance
Baking automation is poised for transformation driven by robotic solutions, as they are increasingly specializing in new applications and expanding their uses out of the packaging stations and into the manufacturing areas.
+The Braubourg district in Paris became the fitting home to a technological first with the opening of Pazzi in July 2021, a pizza restaurant where the production, handling, packaging and delivery are exclusively in the ‘hands’ of a robot with artificial intelligence, developed by a team of 30 engineers and developers. Eight years of R&D and five patents filled later, Cyril Hamon and Sébastien Roverso opened the autonomous 120 sqm restaurant in Paris, after the launch of the pilot project in a shopping center in 2019. Pazzi can prepare up to 80 pizzas per hour, to be consumed at the restaurant or via delivery or click & collect: one pizza is ready every 45 seconds and it can bake six at a time. The production progress is displayed on screens. The restaurant is fully digital, from placing the order to collecting the pizza – a timely solution concerning safety in distancing times.
The owners had the ambition of changing ‘fast-food’ into ‘fast-good-food’, by perfecting the process and selecting quality ingredients. “We are in a very fast process, with perfect control of time, and control of quality since we have a constancy offered by robotics, and also an environment that is quite cool and relaxed,” said Roverso, one of the inventors of the Pazzi robot. The challenging aspect the robot had to master was the dough. Thierry Graffagnino, a chef consultant at Pazzi and triple world pizza champion, pinpointed the challenge of working
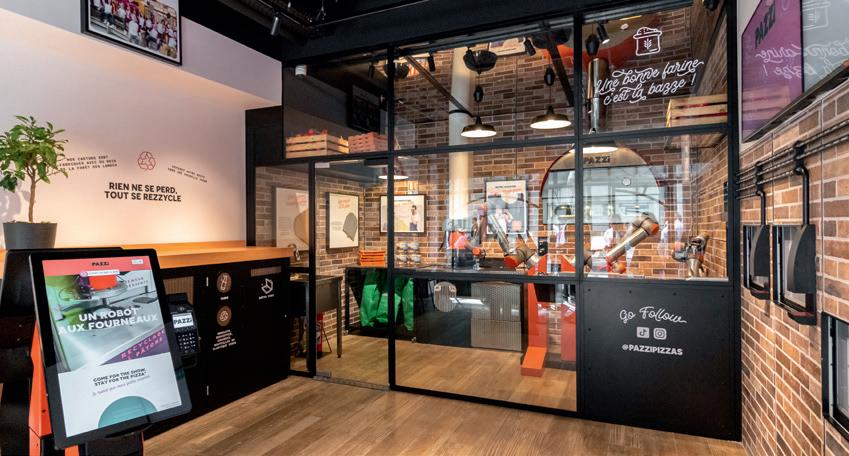
© Pazzi Pizza
AUTONOMOUS PERFORMANCE
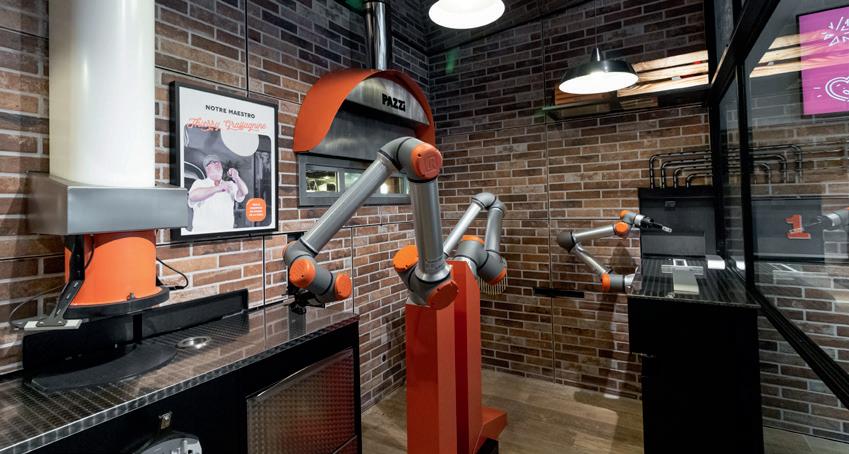
with fresh dough: the machine had to constantly adapt: they had to give the robot the means to make these corrections on its own, and given the fact that some pizza makers can't even manage that themselves. Pazzi aims to expand with two new openings in Paris by the end of 2021 and abroad, with an opening in Switzerland scheduled for the first quarter of 2022.
Hand-to-eye-to-brain coordination
The pandemic has been a catalyst to the adoption of automation features of all kinds, robotics included. Soft Robotics is among the specialists that expanded their operations to meet the demand fueled by pandemic-related changes in manufacturing processes. The company’s SoftAI solution enables industrial robots to have handto-eye coordination similar to human beings. This is achieved with 3D vision and artificial intelligence technologies and it enables the automation of bulk picking. It is the next step for industrial robots to be able to handle product or workspace variations, both commonly found in food processing, baking industry included.
The vulnerabilities in the food supply chain were highlighted by the pandemic. It made it “Clear that automation has graduated from a nice-to-have to a must-have across all large-scale food production operations,” said Jeff Beck, Soft Robotics CEO. The company reported the demand for both its hardware and SoftAI software solutions is increasing at an unprecedented pace. In response, the company is investing in automation solutions that can help safeguard the food supply against disruptions.
Robotics is well underway to transform packaging entirely. Flexible robot technology and fast format changes have already established their usefulness in packaging, especially in connection with handling fragile goods such as biscuits or cookies. They answer needs for diversity in packaging materials as well as formats. Schubert’s flowwrapping machine is an example in this regard, designed to handle plastic and paper-based films, trays made of cardboard and plastic, and U-boards. One of the features in demand is the gentle processing of a wide variety of biscuit shapes, starting right after the production process, through quality control and packaging into flowpack bags, both with and without trays. Such an integrated system can include de-stackers, pick & place F4 robots and the Flowmodul flow-wrapping unit.
Pazzi pizza robot
+6 patents filed + 7 years into development + 80 pizzas/hour can be prepared + 29cm is the circumference available + 2,000+ parts are needed to assemble these robots
To rule out damaged goods entirely, each product also passes through an incident-light scanner. Schubert’s image processing system only passes on the data of qualitatively faultless products to the robots’ control system, rejecting defective units. The baked goods passing the inspection are then either packed directly into a flowpack or stacked into trays or cardboard U-boards, which are in turn packed into flowpacks. Sealing technology also contributes to the efficiency of the robot’s performance. Ultrasonic sealing closes the flowpack longitudinally, followed by a heat-sealing system with a flying cross-sealing unit that adjusts itself automatically to the speed of the upstream pick & place robots for each flowpack.
A clear vision to going mainstream
In the next few years, it is predicted that robotic functionality will increase with richer algorithms, dynamic maneuverability, force control and inherent safety [1], all features rendering robots more adaptable along the processing line and improving their skills in co-working with humans. R&D work is focusing on making robots easier to use, with improved sensory functions for autonomous motion. As advancements are being made, their cost is also declining as estimates are made that the industry will grow by doubledigits in the next years. The tasks robots should excel in include increasing throughput, reducing manual labor, especially work consisting of repetitive tasks, improving staff safety, increasing product quality and consistency, and gaining in manufacturing flexibility with advances in AI and self-learning robots. Automated changeovers and shorter product runs also rank high in the operational improvements they bring.
Applications that stand to benefit from deploying robots are also increasing, driven by their functionality improvements. Bakeries will have more choices in robotic advances to automate anything from cutting, picking, stacking, sorting, packaging, shipping, to carton making, stacking and de/palletizing.
Current and future applications in bakeries
The British Association of Robot Automation (BARA) promotes the use of industrial robots and automation in the UK‘s industry and supports their advancement. The association also represents the interests of its British member companies overseas as a partner of the International Federation of Robotics. The association can advise on sources of independent advice and/or help identify potential suppliers. Robotic solutions have been assisting British bakeries in production for several years, especially high-volume operations. Some of the newest innovations that constitute useful tools in bakery manufacturing, in particular, are improvements in vision capabilities and gripping techniques. Grippers can range from magnets (for tins), mechanical grippers for boxes, pneumatic for products and packages, pins for muffins and something similar to soft fingers for delicate products.
Moreover, advances in the control and feeding of icing materials are making robot automation a viable option in the decorating process, traditionally a time-consuming and skill-dependant step. A possible long-term evolution, based on ongoing trends in their cost and ease of use, would see robots being used more and entering artisan and lowervolume facilities.
BARA is represented on the PPMA Board by Mark Stepney, managing director of Schubert UK. He evaluates that the bakery industry is one of the food production sectors that benefit from a higher level of automation currently, over a multitude of operations, particularly applications in tin handling, packing and palletizing. He highlights how it influences productivity and will increasingly do so: “There has been a significant impact on productivity because the robot systems are highly efficient, do not stop for food breaks
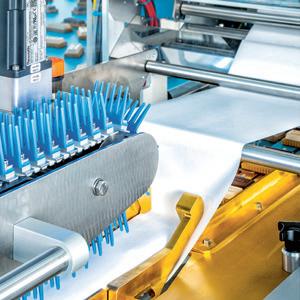
© Schubert
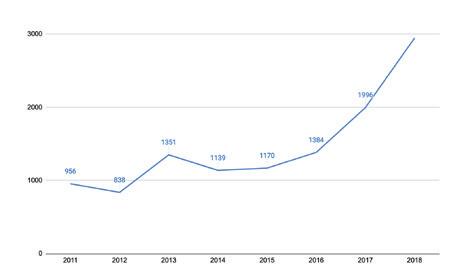
Figure 1: Unit growth in the number of robots shipped, North America [3] and can operate continuously across multiple shifts thus reducing manual labor requirements.”
He also estimates that at present, most robots in bakeries are deployed in the packing stage, generally creating the packs before these are fed onto flow wrappers. However, robots are also in use in all manufacturing stages, e.g., cutting pastry, decorating cakes, and more. The best choice in the structure of the robotic solution to be implemented in bakeries depends on the process to be automated. Stepney recommends: “Packing is often a delta robot where high-speed movements are required, whereas palletizing is typically a four-axis articulated arm robot. In circumstances where a product or package needs to be re-orientated as well as re-positioned, a five- or six-axis robot may well be selected.”
When planning programming/updating for robots working in bakeries, offline tools are often used to simulate their actions and initially offline program the robots, thus reducing downtime during programming. Programming can become more complex in the case of packing systems that utilize vision systems and systems that have product moving on conveyors, for example.
Reprogramming can be necessary when new products are introduced, or when dealing with different pallet layouts, in the case of palletizing. If the original set-up was programmed offline, such changes can be made through the existing simulation. If not, it could require modifications to an existing program. However, this should not be a major challenge, assuming the original program was well defined and annotated in the first place. Various communication interfaces are available for robots to communicate with the automated systems in the facility, including discrete IO or Profinet, to name a few. Synchronization may entail anything from program selection for different products, to production status and error information.
Outlook and opportunities
There was a record 3 million industrial robots operating in factories around the world in 2021, an increase of 10%. Positive developments in China supported sales to rise, despite a slight contraction elsewhere, as countries began experiencing their COVID-19 low points at different times. Almost all Southeast Asian markets are expected to grow by double-digit rates in 2021. The Chinese manufacturing industry began surging in the second quarter of 2020, while the North American economy started to recover in the second half of 2020, and Europe followed suit not long after that. This is the third most successful year in history for the robotics industry, following 2018 and 2017 [2]. “Global robot installations are expected to rebound strongly and grow by 13% to 435,000 units in 2021, thus exceeding the record level achieved in 2018,” according to estimations announced by Milton Guerry, president of the International Federation of Robotics.
The upward trend for the adoption of robotics in manufacturing is shown in their sales increase. While food and consumer goods account for about 8% of the total robotics implementation, their utilization recorded a significant increase, by almost 50%, in North America between 2018 and 2019 alone, for example. Only 3% of these sales were collaborative robots in 2017, but this ratio is expected to be well over 30% by 2025.
Asia remains the world’s largest market for industrial robots, with 71% of all newly deployed robots in 2020 installed on the continent, up from 67% in 2019. Installations for the region´s largest adopter China grew strongly by 20% with 168,400 units shipped, the highest value ever
Robots for food and consumer goods
Source: RIA 2018, Statistics for North America
recorded for a single country, indicating the rapid speed of robotization in China. Japan follows China as the largest market for industrial robots, though the Japanese economy was hit hard by the pandemic, as shown by the sales decline by 23% in 2020, with 38,653 units installed. The Japanese robotics market is expected to grow by 7% in 2021 and continue to do so by 5% in 2022. The Republic of Korea was the fourth largest robot market in terms of annual installations, following Japan, China and the US. Robot installations decreased by 7% to 30,506 units in 2020.
In Europe, industrial robot installations were down by 8% to 67,700 units in 2020. This was the second year of decline, following a peak of 75,560 units in 2018. Demand from the automotive industry dropped by 20%, while demand from the general industry was up by 14%. Germany, one of the top five major robot markets in the world (China, Japan, USA, Korea, Germany) had a share of 33% of the total installations in Europe, followed by Italy with 13% and France with 8%. The German robotics industry is recovering, driven by strong overseas business. The ‘boom after the crisis’ is expected to fade slightly in 2022 worldwide, IFR anticipates, expecting average annual growth rates in the medium singledigit range from 2021 to 2024.
Robotics and enhanced automation
Robotics greatly contribute to building smart production facilities. The IFR identifies five scenarios in which robots are connected within broader automation strategies [4], which also apply to the baking industry: automated production (streamlining process steps), optimizing performance (by connecting equipment and robots), digital twins (virtual representations and simulations), robots as a service (robots on a pay-peruse basis), and sense and respond (sensors, vision systems help robots react in real-time).
R&D for innovation in robotics for the food industry is not without challenges. Currently, the occasional issue with robots in bakeries will come from either the client or the supplier misunderstanding the needs of the application or the complexity of the solution. Other issues can be caused by wear, damage, deformation or the inconsistency of items the robot system might be dealing with, such as tins or trolleys for transporting trays, in Mark Stepney’s experience.
Cyber Physical Systems (CPS) can offer solutions, merging theories of cybernetics, mechatronics, design and process science. This interdisciplinary field of research is based on IoT and can help streamline the supply chain and can greatly contribute to the communication of smart food labels and traceability. The food serving sector presents great potential for R&D in robotics, sustained by advancements in sensor fusion, CPS design, HMI, robot learning, vision systems, innovation in altering robot structural configurations. New ideas are emerging in tandem with new technologies. +++
Top five advancements that will make robotics easier to use
1. Dexterity 2. Vision 3. Mobility 4. Connectivity 5. Safety
Source: PMMI, 2019 Robotics Webinar
Author
f2m, editorial team
References
[1] The Association for Packaging and Processing Technologies (PMMI) – Business Intelligence Webinars, 2019
Robotics Webinar; Donna Ritson, DDR Communications
President, May 2019 [2] World Robotics 2021, Industrial Robots and Service Robots – International Federation of Robotics [3] RIA 2018, Statistics for North America [4] https://ifr.org/industrial-robots [5] Prospects of robotics in food industry - Food Science and
Technology (Campinas), by Jamshed Iqbal, Zeashan H.
Khan, Azfar Khalid, April 2017; 37(2):159-165