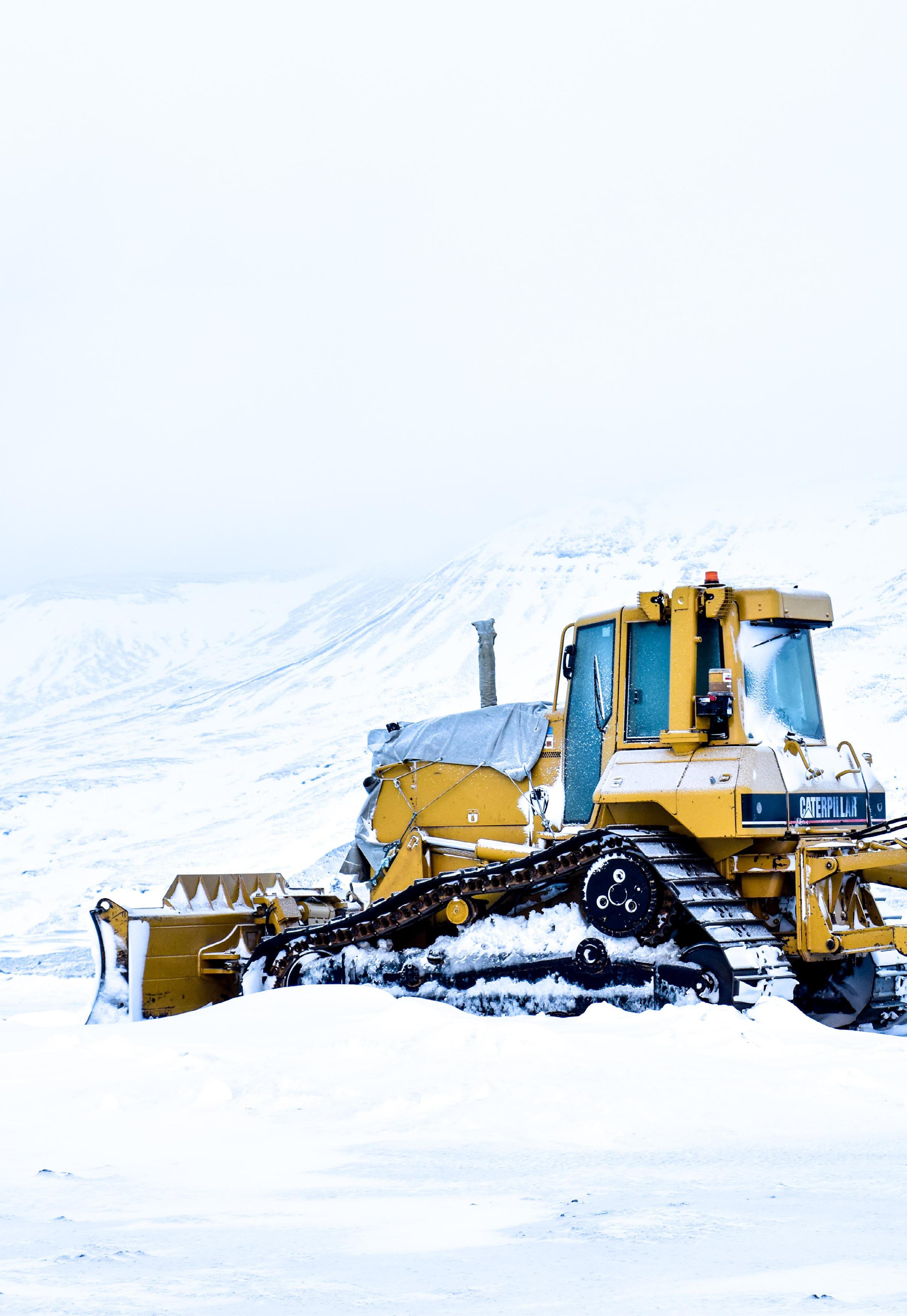

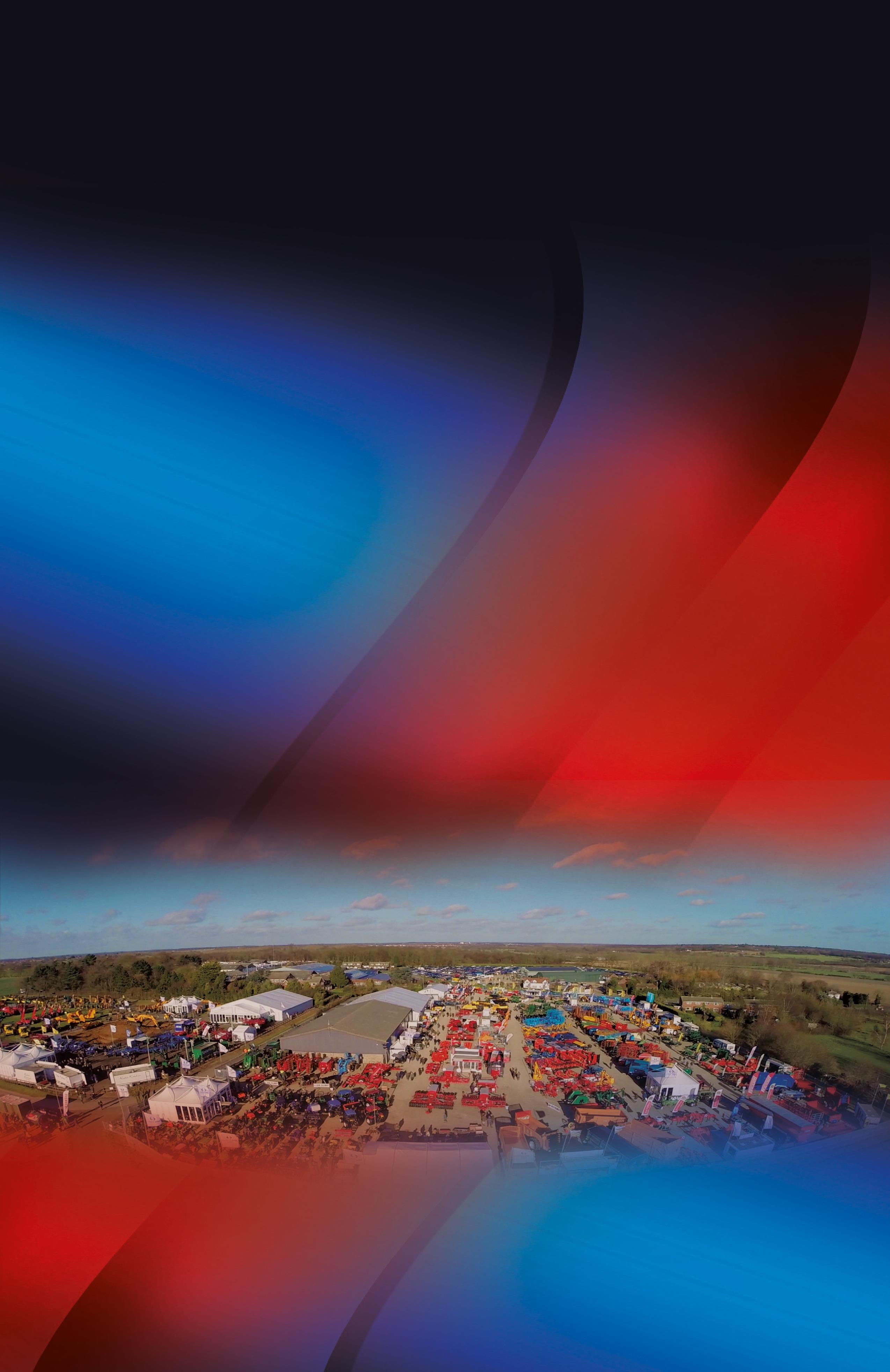
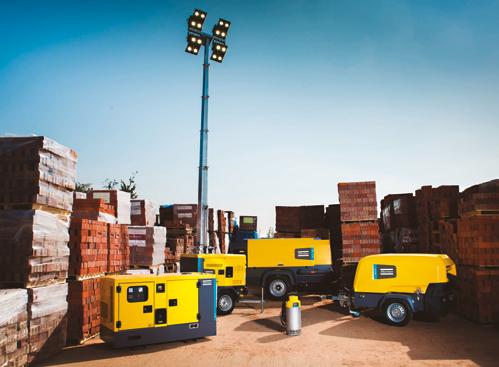

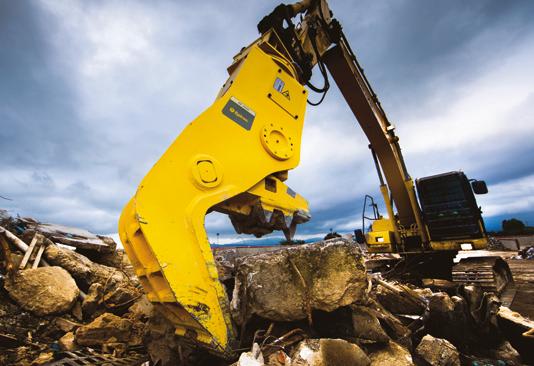

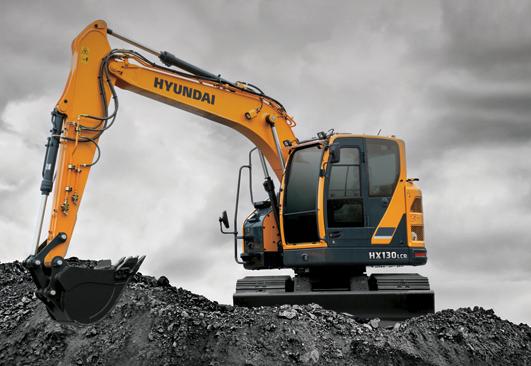
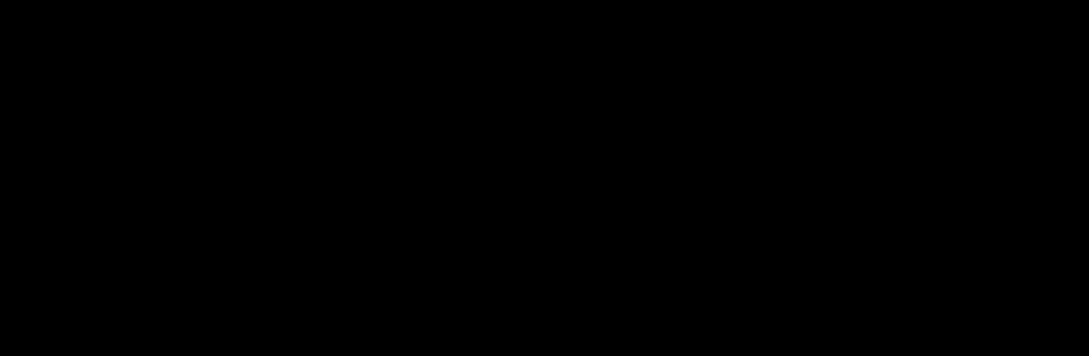

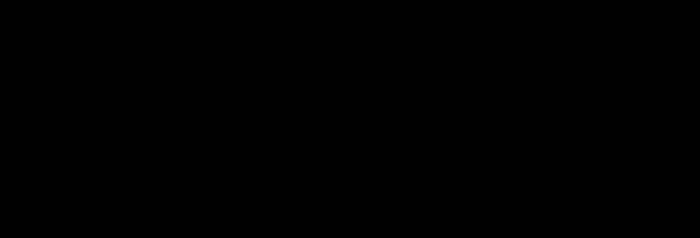



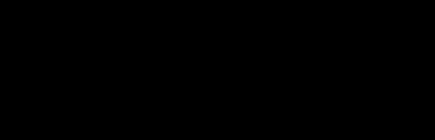
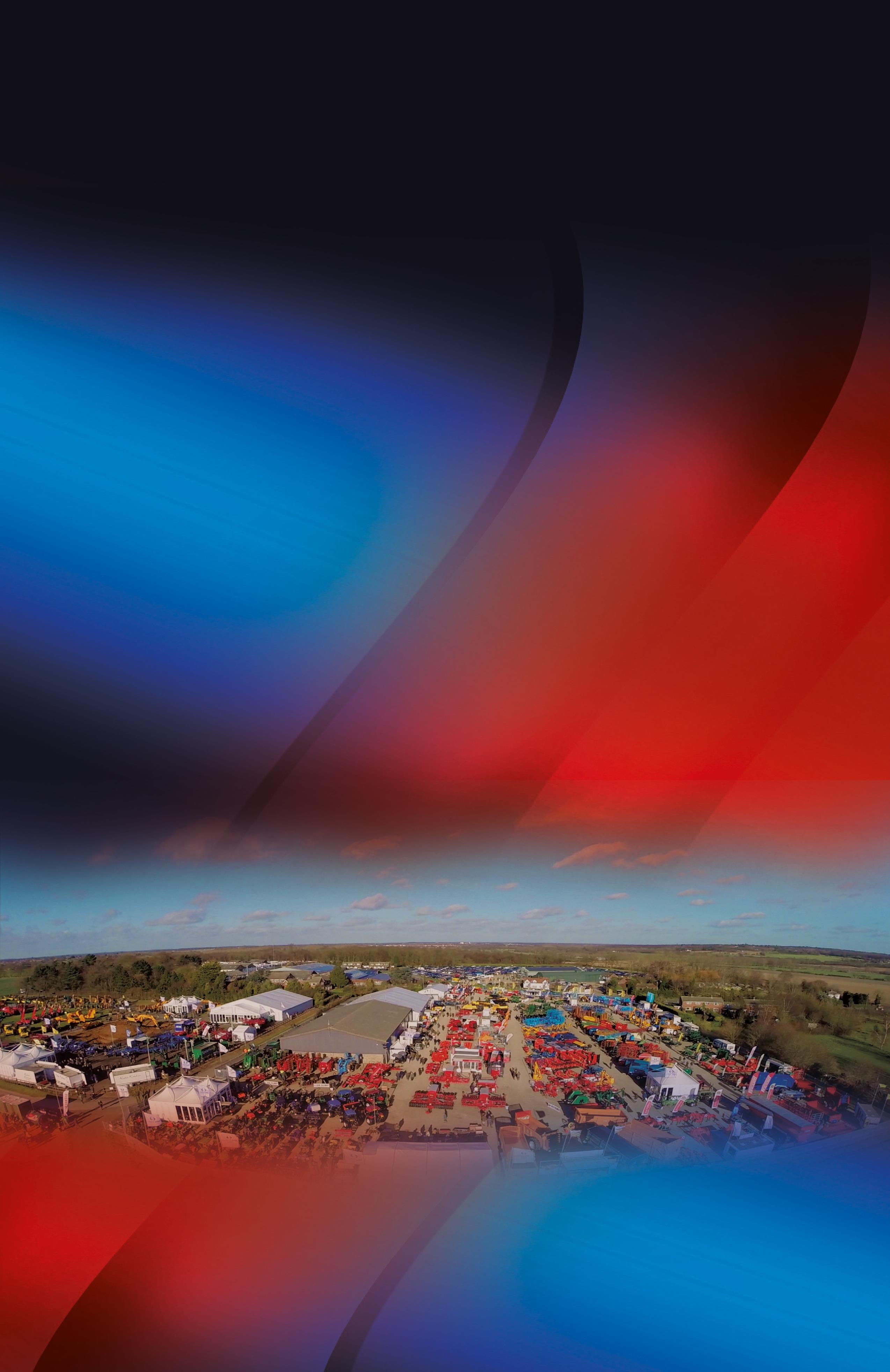
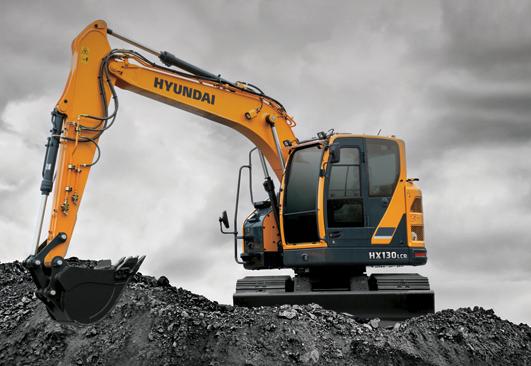

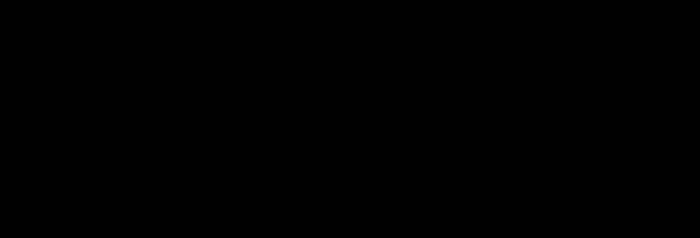

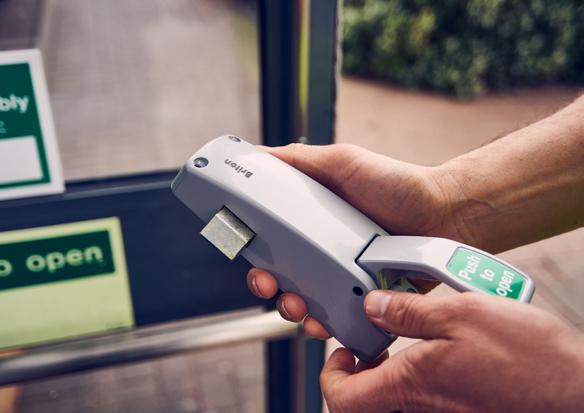
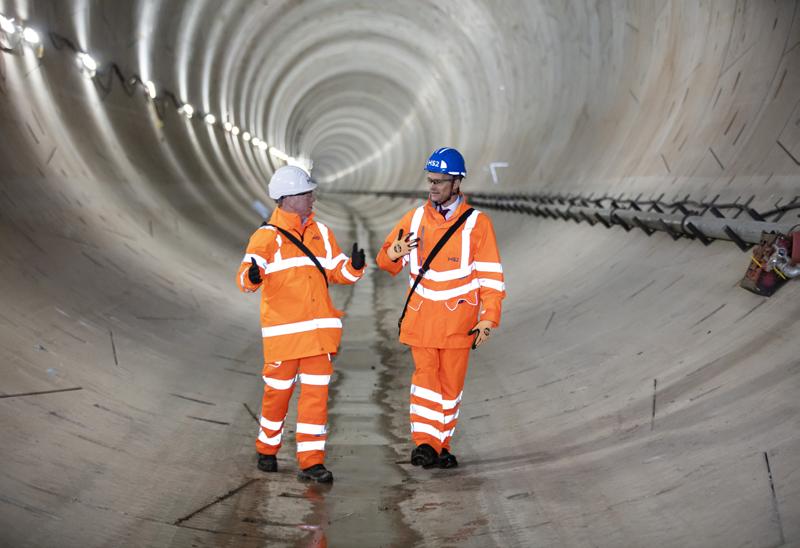
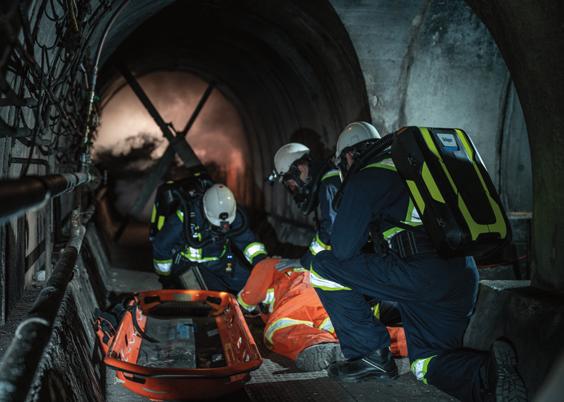
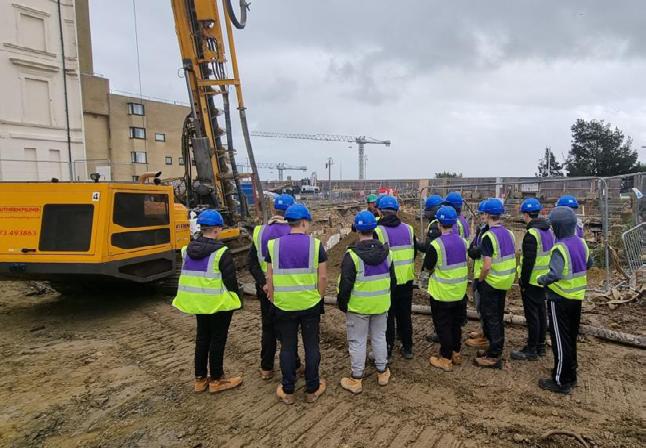
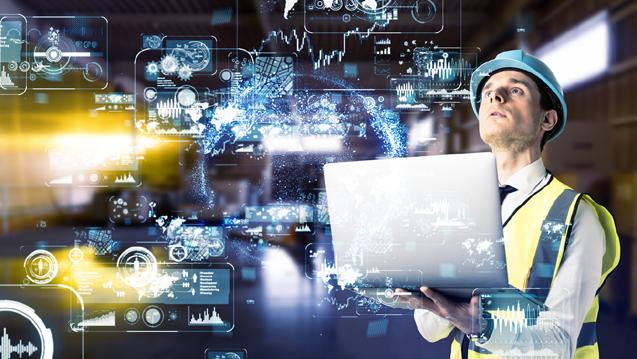
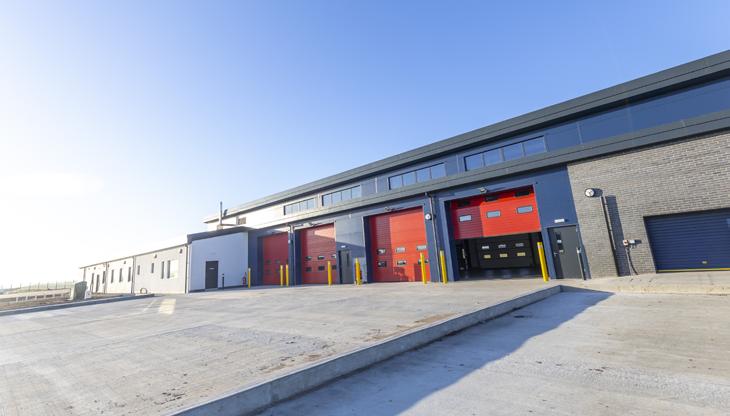
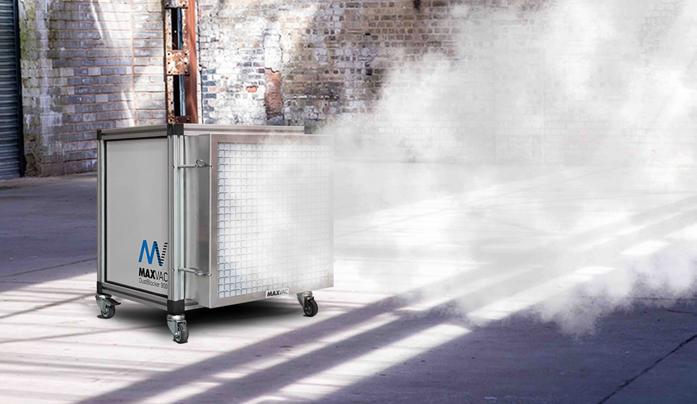
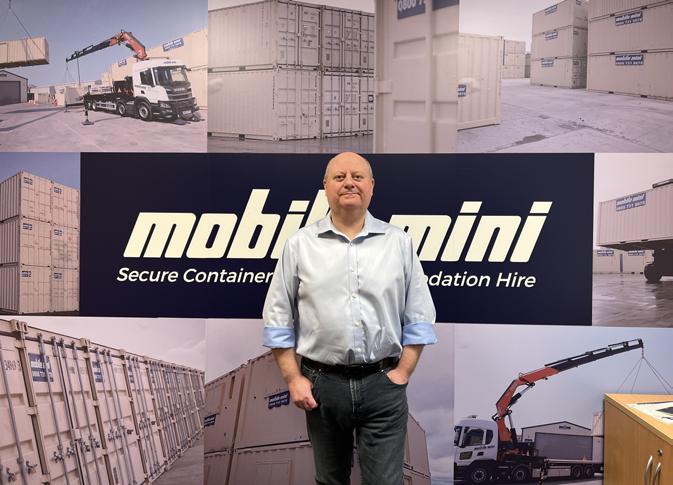
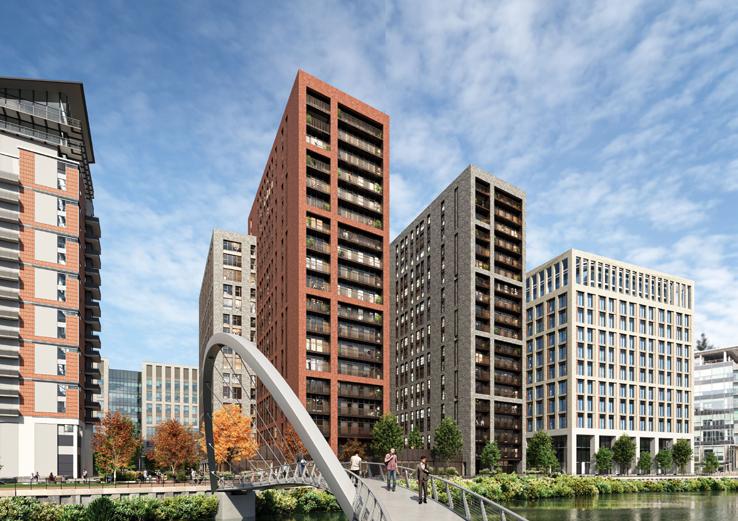
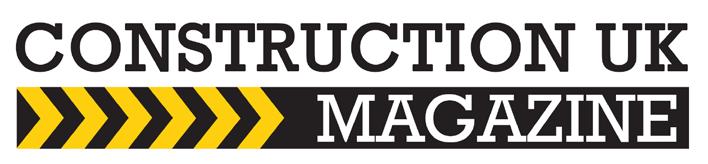
A nationwide insulation funding scheme aimed at middle income householders living in energy inefficient properties has been welcomed by insulation specialist Actis.
The £1 billion ECO+ scheme, which launches in the spring and will run for up to three years, builds on the existing ECO (Energy Company Obligation) schemes, which have been running since 2013.
Actis UK and Ireland sales director Mark Cooper welcomed the move, which covers home owners not eligible for the existing funding, whose target audience is people on benefits or in fuel poverty.
“More than 25% of the UK’s traditional housing stock is more than a century old, much of it very leaky when it comes to keeping heat in,” he said.
“Research shows that more than 12 million homes had EPCs of D or worse in 2020. In fact, we have some of the least energy efficient housing stock in Europe. Installing insulation is the most cost-effective way of
stemming the flow of heat escaping from these homes.
“With energy prices affecting everyone, not to mention the impact on the environment, it makes sense to ensure that the existing building fabric is as energy efficient as possible.
Hopefully this new scheme will encourage people who have been considering improving the energy efficiency of their homes to go for it.
The original ECO schemes have so far seen energy efficiency measures installed in 2.4 million homes nationwide.
The new initiative is aimed at those whose homes are in council tax bands A to D in England, A to E in Scotland and A to C in Wales - and which have EPC (Energy Performance Certificate) ratings of D or lower.
Eligible households will be able to receive grants of up to £1,500 for insulation,
which the government estimates will save them around £310 a year on their heating bills.
Details are yet to be announced, and householders are being advised to contact their local council or energy supplier to find out whether they are participating.
The news follows an announcement in the autumn statement that the government is to invest an additional £6bn between 2025 and 2028 to support its ‘energy demand reduction target’ to reduce demand by 15% by 2030.
Base Structures have recently completed the installation of a series of removable and adaptable temporary fabric screens to aid site access at a prominent city center construction site.
To aid protection from rapidly deteriorating weather conditions, the client was looking for temporary screening to secure a 15-storey office building, guaranteeing their programme of work could continue uninterrupted and meet pre-arranged turnaround times.
To meet the requirements of the proposal, Base Structures installed forty-four screens across the length of the building with a total fabric area of 1,800m². Designed to withstand all relevant British Standard wind
loadings and fire retardancy requirements, new attachment methods were devised with the client to circumvent existing columns not being appropriate. The results were cost effective, versatile, and offered much more flexibility when considering site conditions and access requirements.
Base Structures are committed to the upcycling and re-use of tensile fabric that has not yet reached its end of life, and our zero-landfill policy means that screens like this can find another useful life elsewhere.
To speak to Base Structures about similar projects, or where expertise such as this can add value and time-efficiency to your building programme, get in touch on the details below: T: 0117 911 5250 E: sales@basestructures.com
With the global energy crisis causing concern, Morrison Energy Services is working in partnership with Cadent to deliver the London Construction Management Organisation. Together they have teamed up with community centres in North London to educate and support members of the public.
Cadent has launched three ‘Centres for Warmth’, which help some of the most vulnerable people in society. The Centres are located at Bonny Downs Community Association in Newham, Waltham Forest Community Hub in Walthamstow and St Hilda’s East Community Centre in Tower Hamlets. These areas have some of the highest rates of fuel poverty in the country and this support enables services and activities to be delivered that will benefit these communities.
Some of the topics the Centres will be giving advice on include:
• Benefits
• Carbon monoxide safety
• Debt
• Energy efficiency
• Housing
• Immigration
• Priority Services Registers (PSR) and how those who need extra help can access it if there’s a problem with their energy or electricity supply
• Wellbeing
The Centres for Warmth are a result of funding provided by the regulator Ofgem. The Vulnerability and Carbon Monoxide Allowance provides funding for gas distribution networks to utilise on projects focused on fuel poverty, vulnerability and carbon monoxide safety initiatives.
As a result of this funding, Cadent has offered these communities in North London nearly £200,000 to open and operate the Centres for Warmth for the next 12-24 months.
In addition to this funding, experts at Morrison Energy Services and Cadent are also providing advice to residents in these communities.
At Bonny Downs Community Association’s launch event, the team held a carbon monoxide safety session. This session proved beneficial for many people. One example being a young mother who described symptoms her and her son had been experiencing, typical of carbon monoxide poisoning, and the team were then able to provide useful information and an emergency number for her to contact, which she did.
The team are in the process of expanding the project and have engaged with community centres in Southall, West Drayton and Brent. We look forward to supporting more communities across North London.
At M Group Services, our priority is to put the health, wellbeing and safety of people first. We are committed to making a positive difference to the communities we operate in. Our focus is to work with trusted partners who understand the needs of each community.
A programme to help tackle the productivity challenge in the construction industry is calling on smaller firms to lead the way for change.
Innovation Driven Procurement (IDP), a fully funded programme for SME and Microbusiness Owners in the supply chain, has launched an initiative to create 40 Innovation Champions to solve problems within their business relating to productivity and inspire others to do the same.
Applications to receive this valuable support are open to all UK contractor’s supply chain. Limited places are now available online, where business owners can receive oneto-one coaching and mentoring to do an innovation project and receive the kudos of being an Innovation Champion.
With the construction industry lagging behind other areas of the economy, the initiative was created with a focus on improving productivity, profits, relationships and projects.
The IDP is the brainchild of Nottingham Trent University and Morgan Sindall Construction, supported by Construction Coach with funding from the Construction Industry Training Board (CITB).
So far, the programme has been implemented by multiple businesses with proven success. In one example, subcontractors were able to achieve shorter delivery times and minimise risks on site after engaging with training and implementing innovation and early engagement.
Short CPD modules have been developed with construction supply chain businesses with the aim to streamline construction practices, flushing out potential problems before they arise and generally taking a more collaborative, communicative approach to encourage innovation from the outset. Modules include Collaborative Behaviours, Collaborative Design and the Supply Chain, Collaborative Risk Management using Flow Walks, Innovation and Value in the Supply Chain.
Building work is well underway at a pioneering housing development in Milton Keynes where Bellway is adopting Modern Methods of Construction (MMC).
The developer was selected by Homes England to deliver phase four of Tattenhoe Park, a major extension to the south-west of the city.
The development will include 160 homes, with 40 of these being modular homes built off site in a factory environment, before being assembled on site and connected to mains services.
Construction is continuing apace on the remaining 120 homes which are being built on site using timber frame panels in place of traditional block and brickwork. This system makes the build process quicker and more sustainable.
The Bellway scheme will include one and two-bedroom apartments, and two, three and four-bedroom houses.
Tattenhoe Park will eventually become a neighbourhood of more than 1,300 homes. Bellway’s development, being built on land which the company bought in February 2022, is located just a short walk from Priory Rise School for primary-age children.
Ryan Burgess, Project Manager at Tattenhoe Park, said: “It’s great to be given the opportunity to be involved with this scheme, backed by Homes England, which champions Modern Methods of Construction.
Pilot schemes such as this one, help ease the pressures of material and labour shortages, whilst also providing much needed affordable new build homes.
Leeds City Council planning committee has approved Glenbrook’s plans for a new 500 build to rent apartment development at Whitehall Riverside in the heart of the city centre. This scheme forms part of a wider £280million masterplan which is being brought forward with Leeds-based property investor and car parking operator, Town Centre Securities PLC (TCS).
Designed by Sheppard Robson, the residential element comprises two blocks of 16 and 19 storeys and has been designed with the health and wellbeing of its residents and sustainability in mind. The scheme offers spacious terrace gardens overlooking the River Aire and includes extensive amenities
for residents across the ground and first floors with 4,500 sq ft commercial accommodation at ground floor level.
Speaking about the successful planning decision, Danny Roberts, senior development manager at Glenbrook, commented: “This decision to grant planning consent for the residential element of Whitehall Riverside will unlock the delivery of the wider masterplan. Whitehall Riverside will be a premier, highly sustainable development where people will want to come and spend time both now and in decades to come. The design has been carefully considered to create a resilient scheme which is embedded in its surroundings and will encourage an active community.
A landscaping and public realm proposal designed by re-form will deliver a new riverside park and enhance the biodiversity of the riverside environment. The inclusive design includes new outdoor seating overlooking the river and a generous open lawned space with opportunities for childrens play to create an active and welcoming destination along the river. A series of interlinked green streets and cycling routes will improve connectivity and access, attracting new residents and visitors to the scheme.
We look forward to starting construction in the new year with completion expected in late 2025.Image: © Bellway
A new catalogue of net zero carbon building designs could provide a significant boost to Scotland’s affordable housing sector, as part of a standardised approach for local authorities and housing associations to adopt across a range of future developments.
The energy-efficient design and performance standards have been created by the Edinburgh Home Demonstrator (EHD) programme. The catalogue covers different housing typologies, such as flats, houses and cottage flats, which combine fabric-first energy efficient standards, renewable energy technology, and modern methods of construction – also known as offsite manufacturing.
The £1m EHD programme – involving partners from the City of Edinburgh Council, Offsite Solutions Scotland, Edinburgh Napier University, the University of Edinburgh, Built Environment – Smarter Transformation (BE-ST) and Scottish Futures Trust – is trialling the new approach for high-performing affordable homes.
The first pilot project of the EHD in Granton includes the creation of 75 net zero carbon ready one, two and three-bed flats being constructed by offsite construction specialists, CCG (Scotland), and is funded by the Scottish Government’s Affordable Housing Supply Programme and the City of Edinburgh Council.
The first homes designed using the performance standard are expected to be completed in the summer of 2023 and once occupied, will be monitored to test the approach in the guide.
With the new design and performance standards, the programme hopes to inform new build developments across the Edinburgh and South East Scotland City Region Deal , providing a route map to net zero carbon homes that utilise offsite manufacturing. While the guide recommends common parts, including floorplans and zero gas heating systems, elements such as the external materials and appearance of homes can be customised to ensure buildings remain in keeping with local surroundings.
Ainslie McLaughin, Chair of the Edinburgh Home Demonstrator Programme Project Board, said: “Our ambition is to reduce the carbon footprint of the housing sector by designing new
homes that ultimately consume less energy. Affordable housing plays a significant role among many communities and we want to create homes that are better suited for future generations.
“The flats we are delivering in Granton will be highly energy efficient and will also encourage residents to make low carbon lifestyle choices in relation to services like transport and travel.
Sam Hart, Head of Modern Methods of Construction at BE-ST, said: “We are facing a climate emergency and need to rapidly transform all aspects of the built environment to reduce its carbon footprint. Compared to carrying out the majority of works on site, offsite manufacturing is proven to be more accurate and more efficient, while also reducing waste. This programme is helping to provide local authorities and developers with information about what zero carbon looks like in practice, as well as building evidence to support offsite specialists and other supply chain partners.”
Nicola Jackson, Chair of Offsite Solutions Scotland, added: “With advancing building performance requirements and increasing levels of technology required to be integrated in new homes to improve operational performance, we can better assure this is delivered through manufacturing homes in a controlled, dry factory environment to improve build quality. Offsite Solutions Scotland members have come together as a network of leading offsite timber manufacturing companies to deliver pilot projects as part of the Edinburgh Home Demonstrator programme. This will support the development of a new delivery model for net zero affordable homes using offsite manufacturing.”
For more information, visit: https://www. be-st.build/accelerate-to-zero/modernmethods-of-construction/edinburghhome-demonstrator/
A key output of the pilot project is the evidence we will collect on the performance of the homes. Not only will it inform the next stages of building work here in Edinburgh and the City Deal but it could also influence future designs and procurement practices across all of Scotland’s affordable housing.
A consortium of experts in timber construction and engineering is exploring ways to boost the use of English hardwood forest products across the built environment, in a move which could significantly improve the carbon footprint of the UK’s buildings and support diverse woodland ecosystems.
The project – led by the New Model Institute for Technology and Engineering’s (NMITE) Centre for Advanced Timber Technology (CATT) – is funded through the Forestry Commission’s Timber in Construction Innovation Fund, designed to increase the use of the natural carbon sequestering material in the built environment.
Partners also include dRMM Architects, Ecosystems Technologies, Edinburgh Napier University and Built Environment – Smarter Transformation (BE-ST).
For the first time, researchers will examine the suitability of certain species of English homegrown trees for their use in construction, looking at sawn, engineered, and mass timber products including cross-laminated timber (CLT) and glue-laminated timber (glulam). The species will be chosen according to future availability, and timber potential based on existing data, including more common species such as oak, beech and sweet chestnut, as well as birch, sycamore, ash, alder and willow, where existing research about their suitability is limited.
Focussing on the use of timber in modern methods of construction, partners will
collate data on the potential strength grading of each species while also assessing the use of homegrown coproducts such as wood fibre insulation. The three-year project could help to reduce the UK’s reliance on imported construction materials, as well as providing low-carbon alternatives to concrete and steel.
Kat Scott, sustainability and regenerative design manager at dRMM, said: “By manufacturing viable and scalable homegrown timber alternatives to carbonintensive materials, we are aiming to reduce the UK’s reliance on imported products.
Widening the range of species that provide a domestic wood supply could also provide a boost for localised manufacturing facilities and supply chains.
The research follows the success of the Innovate UK-funded Transforming Timber initiative which set out to prove
the business case for using Scottish wood to create the structural elements of buildings. A demonstrator unit created using homegrown cross-laminated timber (CLT), nail-laminated timber (NLT) and glue-laminated timber (GLT) was found to have an estimated carbon sink of -142kg per m2, compared to +612 kg per m2for an equivalent brick and block construction.
Sam Hart, head of modern methods of construction at BE-ST, said: “As the UK faces a climate emergency, demand is growing rapidly for more sustainable construction approaches such as timberbased offsite design. By building a robust evidence base, we can inform future approaches to forestry and woodland management across England that includes the species best suited for use in the structure of buildings.
“At the same time, the trees will sequester significant amounts of carbon, helping to reduce the environmental impact of the built environment in the years to come.”
Sam Hart, head of modern methods of construction at BE-ST
Professor Robert Hairstans,
Centre
Technologies
NMITE, added: “This research represents a strategic convergence of England’s forestry, manufacturing, and construction industries to drive the increased adoption of homegrown, renewable timber in construction.
“By so doing we can inform future forest strategies to ensure resilience against pests, diseases and climate change and be less reliant on imported resources and the current monoculture of commercial species.”
director of the for Advance Timber atThe concept of a circular economy is not new – in fact, the linear economy characterised by taking, make and dispose of has only existed since the industrial revolution in any particularly meaningful way. In previous eras, very little was thrown away, as nearly everything had an alternative use at the end of its life, even if only for compost. Building materials are a case in point; many old buildings are constructed from stone from demolished buildings, and some old timbered properties are held up by old ships timbers
So why don’t we still do this everywhere? The truth is that it’s far more convenient and sometimes cheaper to manufacture products from virgin material, and nearly always the quality is more consistent.
GreenBlue Urban has always been committed to the circular economy principle – and it is far wider than just product manufacture. A circular economy is a wide economic system that works to challenge global issues such as waste and pollution, but also climate change, biodiversity loss and pollution – both air and water. In setting such massive goals, the circular economy needs a huge shift in thinking, by all of us.
In addition to the issues that the circular economy seeks to tackle, as above, it is designed to benefit not only the environment but to bring prosperity to business and to society. It is regenerative by design, meaning that natural resources do not become so quickly depleted, and therefore new industries came to arise, bringing healthy economic growth.
Planting trees is a perfect example of a circular economy, as the tree provides multiple benefits during its life, and can be used to manufacture products when it is cut down. Removal of a plantation tree
results in space left for new tree planting, bringing employment to often rural areas. But what about urban trees?
Urban trees also form part of a circular economy – but to maximise the benefits, these need to be properly planted, and grow to maturity. This is the raison d’être of GreenBlue Urban – assisting trees in their struggle to survive in a hostile environment. Whether it is providing soil support by using RootSpace soil cells, guiding tree roots with products from the ReRoot root management range, bringing air and water to the rooting zone with RootRain irrigation and aeration solutions or physically protecting the tree from above ground damage with tree grilles and guards
The GreenBlue Urban innovative solutions enable trees to grow to their species potential longevity. All the below-ground products are manufactured from 100% recycled materials and are recyclable up to 5 times once they have finished their life. This is central to the GreenBlue Urban philosophy, as our vision is to bring environmental benefits to communities around the world, and the least possible carbon footprint.
With policy insisting that all developments of more than 150 residential units, buildings over 30m in height or commercial premises over 2500m², a Circular Economy Statement must be submitted, along with a Whole Life Carbon Assessment as part of the planning process. This aims to reduce waste and pollution, and in time, will help achieve the net-zero carbon commitments. It is suggested that circular economy strategies could deliver emissions reductions that could limit the expected temperature rise by half – an incredible benefit.
The circular economy has been described as not just a change in the way we operate, but a new way of thinking. GreenBlue Urban are proud of our story, how we have increased canopy cover globally with the many benefits to our climate, air, water, biodiversity and quality of life for all.
www.greenblue.com
@GreenBlueUrban Tel: 01580 830800
60% of the UK is supplied with hard water, with around £3bn spent combatting the effects of limescale every year. However, despite the positive environmental impact of treating limescale as well as appliance longevity, it is an issue which is largely misunderstood. With carbon savings featuring at the heart of the sustainability agenda in construction, it’s time the industry took note of the significant environmental benefits of treating hard water effectively.
The critical issue is that limescale is an excellent insulator, significantly slowing the transfer of heat from the heating element to the water, reducing energy efficiency dramatically and contributing to embodied carbon losses with damaged equipment.
Just 3mm of limescale raises energy consumption by 25%, significantly reduces the lifespan of appliances, and drastically increases energy bills. In a hard water area, system maintenance requirements are dramatically increased and items such as boilers, calorifiers, hot water cylinders, immersion heaters, thermostatic valves and ‘wet’ system parts fail earlier and more frequently if water is left untreated. Given that the very nature of raw Calcium Carbonate is to build up on itself, 6mm is easily reached in areas like Norwich, London, and Poole, increasing operational energy consumption by over 50%.
An average commercial office with 3 floors and 105 staff consumes around 1.45 million kWh pa, without treatment. Treating hard water can reduce consumption by 62,000 kWh annually, saving 16 tonnes Co2e and associated energy costs which could be as much as £2,000 per year
Preventative action must be taken in order to comply with changing residential and commercial legislation, so the issue of limescale affects a building’s statutory compliance as well as a developer’s environmental goals. However the guidance is grossly inadequate when considering the impact of this problem.
There are many solutions available; some designed to treat individual equipment, and others to treat entire systems. While such devices can reduce limescale accumulation, it’s vital to investigate their environmental credentials to find a truly sustainable solution.
Offering varying levels of effectiveness and longevity, most water conditioning systems require ongoing maintenance and the water treated by many of them reverts back to it’s original ‘bonding’ state within 48 hours.
Salt water softeners dispel brine effluent into the watercourse, rather negating their environmental benefits. They consume large amounts of water as they recharge and require frequent topping up and water testing to ensure efficiency. Water treated with salt is not suitable for plants and watercourses, nor should it be supplied as drinking water, complicating the overall plumbing system design. As many commercial
maintenance teams are stretched, it’s often the salt ordering, topping up and general maintenance that gets pushed down the agenda, allowing limescale to re-enter the picture.
There is an alternative, sustainable solution to the problem: an unpowered device which passes water through a solid state, alloy core, creating a strong galvanic reaction which temporarily but fundamentally alters the structure of the minerals. This chemical and salt-free solution changes the behaviour of the minerals within the water for around 21 days, removing the need for recirculation systems or concerns about reversion.
CEO of Halcyan Water Conditioners, Samantha Mant, states: “The alloy core solution has a proven lifespan of 30+ years and requires no maintenance. As it doesn’t rely on salt or chemicals, there is no requirement for expensive consumables, nor does it expel effluent into the watercourse. The resultant water is potable. Without the need for power or earthing, it protects the entire water supply, including all downstream appliances.”
As we step into 2023, the deadline for the UK Government announcement of its net zero 2050 goal is another year closer. Many businesses have begun to make green commitments and ambitions, carving their path to the 2050 Net Zero target.
Many in the construction sector, have voiced that sustainability has taken a back seat. While the uncertainty of the supply chain, rising costs of raw materials, energy, wages, and utility costs have taken precedence, there is no time like the present to address this important issue.
Daniel Hancox,Business Support Manager at pitched roofing manufacturer Russell Roof Tiles is looking at initiatives to synergise the relationships within the supply chain. The firm has embedded sustainability processes into its operations, and community impact, to ensure end-to-end visibility of carbon emissions and opportunities for reductions.
He comments: “Social housing across the UK amounts to a 17 per cent of the total housing stock, however, there are only a handful of energy-efficient homes being built. There is concern about the lack of understanding when it comes to sustainability, how businesses can implement changes, and how to measure efforts accurately. If these issues aren’t addressed and worked on, they will soon become a cause for concern for both residents and the Government, as urgent action will be required if they do not meet their 2050 Net Zero target.”
Although there are apparent concerns across the sector in the lack of progress being made, there has also been positive
signs of change, where some developers are clearly noticing the effects or irreversible damage that could be caused if they don’t look to make more sustainable and safe choices, soon.
Increasing numbers of developers and contractors are choosing to deliver energyefficient and sustainable projects that are meeting the modern-day needs of their consumers and tenants.
The starting point to setting off on the right foot for 2023, is understanding how to measure sustainability. Companies, such as external sustainability assessors Planet Mark, are dedicated to supporting businesses to set out goals, measure their impact and certify their achievements. The first step to a greener future is to measure and analyse greenhouse gas emissions that are caused by extraction, manufacturing, transportation, deconstruction, disposal, and end-of-life.
Businesses must focus their efforts on comparing the data to the benchmark statistics that are outlined for the construction industry to help to visualise what areas need further attention as well as identifying what is working well.
Setting step-by-step goals, following the UK Government’s plan, has already highlighted that carbon footprint reports show that their direct emissions have decreased 9 per cent.
Socially responsible companies should be dedicated to community outreach and sharing their sustainability stories to encourage as many people as possible to be aware of what the company are contributing to the resolution of carbon emissions.
One of the small changes housing associations can make to be more sustainable is choosing eco-friendly roofing tiles. For example, concrete roof tiles could be considered an environmentally friendly roofing solution as they are strong, durable and use considerably less energy during manufacturing when compared to its similar clay counterparts.
Educating the supply chain and people further afield about sustainability is another change that needs to be made. For many, not understanding the regulations or having the correct training in place to learn about sustainable options and their benefits is one of the reasons why there is a lack of sustainable social houses.
Embracing changes to improve the sustainability of social housing projects will play a significant role in reducing the country’s carbon emissions, which ultimately will help build more greener, safer homes that benefit the people and the communities in which they live in.
Russell Roof Tiles is a leading independent pitched roof tile manufacturer providing leading UK house builders and high-profile social housing and commercial projects, where sustainability and eco-credentials are of the utmost priority.
For more information, please visit www.russellrooftiles.com
At DJS Metal & Lead Roofing Ltd we complete both main contractor and sub-contractor works to both new and historic buildings across the UK such as churches and cathedral through to new housing. With over 30 years of experience within the construction and restoration industry you can be assured that with a great level of knowledge, skill and a great deal of passion and pride in what we do your projects are in safe hands.
DJS Metal & Lead Roofing Ltd had the pleasure of being the main contractor on this beautiful 1960’s chapel in Cambridge. Works that were completed where that of new timber works, insulation & Felt roof coverings, new skylights to the five openings and new milled lead works. This has then a pleasure to work on and with the finished detailing this beautiful structure will stand proud for many years to come.
With new code 5 milled lead sheeting, fascia, capping’s, and flashings supplied by CEL Lead & Hard Metals and Installed by DJS Metal & Lead Roofing Ltd this has now brought the building back to life and also reduced running costs due to the insulation and products installed.
DJS Metal & Lead Roofing Ltd Progress House, 256 Station Road, Whittlesey, PE7 2HA
This 1980’s traditional building was showing signs of age with a number of leaks which had begun to deteriorate the timber roof structure. Following a thorough inspection of the roof area and structure DJS Metal & Lead Roofing Ltd was awarded to project which was to be completed in ZM Zinc Quartz with various timber repairs and warm roof 110mm insulation board installed.
Following the completion of various timber repairs, 110mm insulation boarding and the installation of new VM Zinc Quartz standing seam roof and new Quartz gutters the building can again stand proud. Installation of all works completed by DJS Metal & Lead Roofing Ltd with the supply of VM Zinc from CEL Lead & Hard Metals Ltd.
Tel: 01733 206633 (Option 2)
The uptake of eco-driven landscaping and roofing solutions is increasing as planners and architects look to maximise the green potential of all new developments. Why? Well, aside from the clear benefits to wellbeing, green infrastructure can help private and commercial tenants to reduce their energy consumption, reduce the risk of flooding, and enhance a location’s biodiversity.
With environmental change already affecting the UK’s climate in visible and measurable ways – with drier summers and wetter, milder winters – action can’t come fast enough. In fact, Met Office figures show that since 1998 we have experienced six of the ten wettest years on record and, according to analysis by the University of East Anglia, UK rainfall will continue to increase in intensity in for years to come. The good news is that we already have many of design solutions of we need to address this – green roofs being one.
Green roofs perform a vital role in helping cities adapt to the effects of climate change. This underutilised specification type reduces the need for artificial cooling in hot weather, captures rainwater runoff and can provide a range of habitats for wildlife. The trouble is that there is a tendency to stay resolutely in our lanes when it comes to delivering the individual elements of a project, with little to no comprehensive oversight of the full ecopotential of a project.
Too often, specialists in our field stick to one core discipline and are only involved in one specific part of a client brief, be that the bitumen roof or the landscaping at the end of a project. It means that those responsible for designing our future homes, offices and community buildings are missing out on joined-up thinking from those with the hands-on skills and opportunities for enhancement that comes from being involved in the full specification of a project right from the start.
Given the Government’s continued commitment to ensuring all new developments in England are built to Future Homes Standard from 2025, every small adjustment now will undoubtedly reap far greater returns in future.
Not every client budget will stretch to a wildflower garden, a living wall or comprehensive green podium installation but every roofing specifier should be questioning where the marginal gains are from a sustainability perspective: Is there PV being discussed and, if not, why not? Have we effectively informed the client of the long-term risks in not investing in a blue roof for their urban development?
The sustainability knowledge gap is also a core driver of my team’s approach to training. There is undeniably a scarcity of adequate training in our country to ensure the next generation of roofers are equipped with the skills to take the industry where it needs to go.
Green roofs perform a vital role in helping cities adapt to the effects of climate change. This underutilised specification type reduces the need for artificial cooling in hot weather, captures rainwater runoff and can provide a range of habitats for wildlife.
The Langley Group currently runs a well-established LANTRA accredited green-roof installation training in the UK. So much so that our team provides training to tradesmen and women who work with our competitors too.
We’re happy to upskill people in this way, and the success of our training courses demonstrates a real opportunity for others across the industry. We need more upskilling to ensure that when approaching a new job, all contractors are asking the right questions and looking at the building’s full potential – and we need our architect partners to insist on the industry getting itself up to speed.
Every one of us involved in new development has a responsibility to our clients, and to future generations, to inform and educate on the opportunities available for green infrastructure enhancements, as well as a role in challenging decisions that are working against the interests of the planet and the concept of better living.
A more holistic approach starts from the moment we receive a brief for a flat, pitched or green roof project, by asking: How else can we help to meet your longterm objectives for your building, and help support you in reaching your sustainability goals?
Every project is an opportunity to bolster the urban environment’s ability to tackle the growing threat of climate change. As a sector we need to be far better at encouraging our customers to think beyond the initial scope and educate decisionmakers on how their space could be enhanced even further to leave a lasting, positive legacy. Frankly, we aren’t doing our jobs properly if we aren’t guiding customers towards a more holistic solution – and the planet can no longer afford for us to be shy about doing so.
Langley new build sales manager, Simon Griffiths:Every project is an opportunity to bolster the urban environment’s ability to tackle the growing threat of climate change. As a sector we need to be far better at encouraging our customers to think beyond the initial scope and educate decisionmakers on how their space could be enhanced even further to leave a lasting, positive legacy.Simon Griffiths
Local contractor Henry Brothers has started work on site to build a new energy and data hub for the student village at Loughborough University.
The £3.25m design and build project includes new mechanical and electrical infrastructure, external works and landscaping, housed in a single-storey building on Elvyn Way in the centre of the university’s student village.
It will provide a district heating and hot water scheme for the student accommodation and will replace Whitworth Tower, where the existing energy hub is located.
This is the latest in a number of developments that Henry Brothers has delivered for the university. The company is currently on site building the four-storey SportPark Pavilion 4 - the
first Passivhaus development on the university campus.
Previously Henry Brothers successfully delivered the £30m refurbishment scheme of the W and S buildings, completed the £3.6m Towers dining facility, and was the contractor for the £17m STEMLab building, which opened in 2017.
Designed by David Morley Architects, the energy and data hub will sit into the natural slope of the land.
The work will be carried out in three phases to maximise construction during periods when students are not in residence and is due to be completed by September 2023.
Other members of the team include structural engineer Ridge & Partners, M&E consultants Axis and FPCR landscape architects.
Henry Brothers is on a carbon reduction journey and is committed to cutting its carbon emissions by 50% by the year 2030, and to achieve net zero carbon emissions by 2050.
A group of students from Folkestone College have been granted an in-depth view of work being undertaken at Leas Pavilion, work that will see it restored to its former glory as part of a stunning new residential development.
A total of 14 T-Level Onsite Construction students visited the seafront site earlier this month where groundworks and structural works are underway. It follows the careful removal of the historic building’s terracotta façade, stained glass windows, wooden balustrades and iron gates for cleaning and refurbishment.
During their visit, students, who are studying trades including carpentry, joinery, and bricklaying, were given a guided tour of the Grade II-listed Pavilion site by Lawrence McKenzie, Head of Health, Safety and Environment at the project’s main contractor, Ant Yapi. They were accompanied by Ali Atakan, Construction Manager and Ahmet Ozdemir, Project Director at Ant Yapi.
The project, which is being delivered by development company Gustavia
in consultation with Hythe-based architects Hollaway Studio, will see the Pavilion reborn as a gateway to a highly desirable nine-storey residential development.
For the students, visiting working construction sites is crucial to provide an authentic appreciation of a live building environment, particularly in relation to the health and safety aspect of their vocational courses. It’s also seen as key preparation for work placements through the wearing of PPE and undertaking site inductions. Additionally, site visits provide students with a forum to ask questions and bring to life their college learning experience.
It was the students’ first visit to a live construction site since starting their course in September. As part of their two-year course at Folkestone College, regular visits to Leas Pavilion are being planned. A two-year build programme will offer the ideal live project backdrop to their college course.
Construction work is almost complete on a new housing location in Saffron Walden.
The 200-home Linden Homes development is being built by Vistry Group on land off Radwinter Road in the town and includes a mix of three, four and fivebedroom houses.
Work began on the site in 2017 and is due to come to an end this autumn.
All but eight of the 122 houses being built for private sale have now been purchased, and all 78 affordable homes for rent or shared ownership at the development have been finished and are occupied.
As part of the planning agreement for Saffron View, Vistry is contributing funding totalling £1.68 million towards local services and infrastructure.
Saffron View also features a new children’s playground which was unveiled at the site earlier this year.
One of the UK’s leading build-to-rent providers has submitted a full planning application for 122 apartments in Halifax town centre.
Plans by award winning regeneration specialists Placefirst for the £16m project at Cow Green will see the prominent former multi-storey car park site transformed into high-quality homes for rent.
If approved, the scheme will deliver a mix of one and two-bedroom apartments with bike storage and electric car charging points. Designed as a nine-storey building by JM Architects, the development takes inspiration from the town’s rich heritage and will integrate with the Council’s wider Cow Green highway improvements through attractive landscape features and public realm.
Placefirst is working collaboratively with West Yorkshire Combined Authority on the delivery of the scheme. Pre-application advice has been sought from Calderdale Council and a public consultation took place in October. Maddox Planning is acting as planning consultant.
Plans for Cow Green represent Placefirst’s most sustainable project to date as it transitions towards ‘net zero’. A fabric first approach has been taken to maximise the thermal performance of the building in addition to renewable and efficient technologies including photovoltaic panels, air source heat pumps, mechanical ventilation with heat recovery, and wastewater heat recovery. This will deliver a superior EPC rating which will limit energy consumption and allow for lower bills for residents.
The proposal links closely to Calderdale’s vision for Halifax as a vibrant place to live, work and visit, and plans dovetail with current and future ‘Calderdale The Next Chapter’ proposals for the town centre such as the refurbishment of the bus station and the train station gateway.
Placefirst is well known for creating quality, well-maintained rental neighbourhoods in multiple regions across the UK, and this scheme in Halifax would follow in the footsteps of its other successful developments including ‘Elevate’, 53 high-spec apartments near Manchester city centre, and ‘Skye Edge’, a thriving family community of 113 new build homes with incredible hilltop views across Sheffield. Once each neighbourhood
is complete, Placefirst also maintain a presence on site and manage their neighbourhoods with skilled, friendly in-house teams, and dedicated resident services managers.
If approved, work is expected to start in mid-2023 and would be completed by 2025.
James Litherland, planning and development manager at Placefirst commented: “We are excited to submit our plans to regenerate this area in the
centre of Halifax with our most sustainable scheme to date. We have worked closely with the Combined Authority and Calderdale Council to ensure the scheme delivers the shared objectives of all partners and sets the standard for high quality build-to-rent in Halifax.
We hope that the proposals are well received and look forward to starting work next summer to create new homes for residents.
Laing O’Rourke has appointed Chetan Kotur as Head of Technology and Innovation for its Europe Hub, as it increases its focus on the development and deployment of new technologies with the potential to transform construction productivity and deliver improvements to project programme, quality, safety and sustainability. Chetan, who was named Young Engineer of the Year in 2018 by the Royal Academy of Engineering, joins the company from Polestar, the electric performance car brand, where he was Head of Products for APAC (Asia Pacific). He will begin his new role on 28 November, and will work alongside his predecessor, Dr Chris Millard, in a phased handover of the Technology & Innovation team. Chris will remain with the business focusing on specific projects.
Welcoming Chetan to the business, Chris said: “I am delighted to welcome Chetan to Laing O’Rourke. He is an outstanding engineer with tremendous knowledge and experience of the automotive sector, from which we can learn so much as we continue to develop technologies that accelerate the transformation of construction into a modern, technology-based sector.”
Chetan said: “I was inspired by Laing O’Rourke’s vision of construction and its desire to apply learnings from other sectors, like automotive and aerospace, to change how construction delivers. I believe there is great opportunity to harness new technology and innovations to make advanced manufacturing the norm in construction, and by doing so boost productivity, enable greener building and make a career in construction more attractive to a wider group of people.
“I can’t wait to meet the team, visit the amazing projects and get started.”
Ray O’Rourke added: “I am excited Chetan shares our vision and has opted to swap the automotive sector for construction.
“I remain convinced automotive is one of the sectors we can learn a great deal from as we continue to find ways to push the boundaries of what’s possible in service of humanity, and to lead the industry.
Claire Fairchild has been appointed as Head of Customer Care at Newland Homes, the privately owned housebuilder based in Gloucestershire. This is a newly created position for the company as part of its drive to put the customer firmly at the centre of everything it does.
Claire has an extensive background in customer care, having previously held similar roles at Crest Nicholson and Cala Group, as well as helping to establish a research agency which investigated customer experience post completion for over 100 UK-based regional housebuilders.
She takes the reins of Newland Homes’ existing Customer Care team and intends to empower them in their roles by introducing new data management systems, additional quality control checks and an expanded training programme.
Kier has appointed Gus Wright as regional director for its London business, specifically focusing on the commercial market.
Gus joins in January 2023 and in this newly created role, will be responsible for the operational delivery of Kier’s commercial and residential projects across London.
A commercial and mixed-use specialist, Gus has over 30 years’ experience in the construction industry holding senior roles at Ardmore Group, Mace and most recently, Laing O’Rourke, where recent successes include the delivery of the Brunel Building.
The appointment follows a period of significant growth for Kier in the London blue-chip commercial and residential market, securing over £200m of new contracts which are either on site or in preconstruction.
Gus Wright said: “I am thrilled to be joining Kier, a distinguished organisation with clear core values and a solid reputation. This new role offers a great opportunity to further develop the London business and I look forward to positively contributing to the strategy, working with the site teams and enhancing our client and partner relationships.”
DEFENDER® cable protector systems are able to ensure your safety wherever reliable protection is required in your working environment. They not only protect electrical cables and hoses against damage on building sites, at events, street festivals or on film sets, they also prevent tripping accidents by passers-by, audiences and staff. Easy to install and made of durable, eco-friendly materials, the modular DEFENDER ® cable protector systems help keep a place safe and tidy at all times.
Manningham Housing Association has won the prestigious British Standards Institution (BSI) Users Award for Sustainability.
The accolade, which recognises the use of voluntary standards to enable sustainability, was presented at the BSI Standards Conference and Awards at the Park Plaza Victoria in London.
Formed in 1901, BSI is appointed by the UK Government as the national standards body, holds the Royal Charter, and represents UK interests at the International Organisation for Standardisation (ISO), the International Electrotechnical Commission and the European Standards Organisations.
Its role is to help improve the quality and safety of products, services and systems by enabling the creation of standards and encouraging their use.
In a joint citation, the judges said of the Sustainability Award winner: “Manningham Housing Association has used BS 76005:2017 Valuing People through Diversity and Inclusion to ensure they can provide great customer care to over 6,000 diverse residents who live in their high-quality affordable homes across in Bradford and Keighley.
“Use of the standard has helped them ensure they have a better understanding of all their customers’ needs which in turn enables them retain customer satisfaction ratings of 90%
but also helped them to put in place additional support and programming needed during the pandemic.”
Ulfat Hussain, Manningham Housing Association Deputy Chief Executive, said: “I am proud of the team and delighted at the recognition this high profile award brings them.
Held at the Queens Hotel in Leeds on Thursday 17th November, the INCA Awards (The Insulated Render and Cladding Association) were hosted by comedian and broadcaster Paul Sinha and recognised outstanding workmanship and innovation shown by its members in external wall insulation. Sika stood out against a wide range of exceptional projects winning the EWI Excellence Award for its work with Swansea Borough Council in upgrading the energy efficiency of its housing stock.
The win in this category comes at a time when so many households are facing fuel poverty due to rising energy costs. The improvements to council houses across Swansea, has seen Swansea Council work with Sika in improving the external fabric and increasing insulation as part of efforts to reduce residents’ energy bills.
Darren Bunting, UK Distribution, Business Unit Manager at Sika commented: “This was a fantastic night for Sika and Swansea Council.
We were delighted to have won this award, which is testament to all the hard work of our team and the high standards we deliver across the external wall insulation industry.
Matt Allen, Head of Sales for Building Finishing at Sika added: “We are delighted with the accolade which is a credit to our hard work across this project. It also recognises the unique relationship between Swansea Council and Sika in creating jobs, reducing emissions, reducing fuel poverty and creating more comfortable homes.”
“Manningham Housing Association is a ‘glass half full’ organisation and we always seek to gain positives from every situation we face.”
Barrington Billings, Manningham Housing Association Chair, said: “Winning the BSI Users Award for Sustainability is a remarkable but well-deserved achievement, particularly given our relatively small size.
“We take sustainability incredibly seriously and, despite the many difficulties the pandemic brought, it is heartening to know the judges felt that Manningham Housing Association not only rose to the challenge but raised the bar.
“There are more dark days ahead as the cost of living crisis continues to bite but I know our staff will continue to be guided in all they do by the bright beacon of hope.”
Winning this prestigious award has further enhanced Sika’s reputation for manufacture and supply of market leading external wall insulation systems that set the highest standards.
Covid-19 brought inevitable changes to the way we operate, including a need to use technology more effectively to assist service delivery and monitoring of performance. The move towards greater digitisation made us more sustainable and will continue to serve us well into the future.
More than 600 students of all ages and over 200 industry professionals attended Foundations Live 2022one of the north of England’s biggest construction, trade, networking, and careers events.
Despite the torrential downpour, exhibitors, trades people, students and teachers were all able to keep dry and explore more than 80 exhibition stands inside the huge arena at Bishop Burton College in East Yorkshire.
Hobson & Porter, the event’s main organiser, was joined by the likes of Beal Homes, Vinci Construction, Keepmoat, Balfour Beatty, Spencer Group, Jewson, Dulux, British Gypsum, and Plasmor.
In addition to all the schools, colleges, and training providers from across the region, the Construction Industry Training Board (CITB) and representatives from Talentview Construction were also on hand to help people find first jobs, apprenticeships, and work experience opportunities.
According to the CITB 19,000 extra workers need to be recruited to meet expected levels of work over the fiveyear forecast period.
TV host Mark Millar also returned to the event as Foundations Ambassador. Mark is an experienced project manager who runs a successful building firm in Bristol and is the presenter of Channel 5’s primetime series Dream Kitchens And Bathrooms He’s also one of the most recognised faces on BBC One’s DIY SOS and he’s passionate about developing the talent of the future and promoting the construction industry as a career to the next generation.
Foundations Live will take place next October 2023, for more details visit www.foundationslive.co.uk
Leading Leicestershire developer Springbourne Homes has scooped another national award for its spectacular Hornsey Rise site near Market Bosworth.
Springbourne picked up a silver award in the ‘Best Small Housebuilder’ category at the glittering WhatHouse? awards at the famous Grosvenor House hotel in Park Lane, London.
The awards are regarded as the UK building industry’s ‘Oscars’ and Springbourne Homes chairman Adrian Burr was delighted.
It was the 42nd WhatHouse? Awards and the special guest was former Foreign Secretary and ex-Conservative Party leader William Hague, who handed out the awards.
The WhatHouse? award is the latest accolade for Hornsey Rise which has previously enjoyed national acclaim after winning three gongs at the UK Property Awards, including ‘Best in the UK for Architecture for a Multiple Residence Development’ and ‘Best Residential Development in Leicestershire.’
The ten acre site features 19 stunning homes in an unrivalled location which boasts panoramic views across rolling, open countryside and its own three acre wood.
Hornsey Rise was previously the setting for a care home for retired missionaries and dates back almost 1,000 years to the Doomsday Book and the days of Lady Godiva.
Fairhive Homes, the Buckinghamshirebased affordable housing provider, has recognised its community heroes this month – those voted as going above and beyond for their communities.
Residents/the community were invited to nominate others in the following categories:
• Community Hero - someone who brings the neighbourhood together and makes a difference to the community.
• Green Hero - Improving the green space around them, whether it’s their garden or a communal area.
• Young Hero - For anyone aged 18 and under who is making a positive impact in the community.
• Resident Volunteer of the Year – resident who goes above and beyond in their volunteering role.
The Green Hero award went to Rob Jones for his keen gardening and amazing work to improve the communal spaces where he lives and supporting other local residents to develop their garden patch.
The Young Heroes awards went to Olivia Underwood, age 9, and Oscar Townsend, age 10, who are part of the Aylesbury Wombles, which help to make the town a greener and cleaner place by litter picking.
They work in sections all over villages, parks and roads across Aylesbury.
Pauline Cook, also from Aylesbury Wombles, was awarded Community Hero for being the driving force behind the Wombles becoming a bigger and better team.
Fairhive’s final winner was Elaine Anderson, who won the title Resident Volunteer of the Year.
She was nominated for her great enthusiasm and eagerness towards improving her knowledge and services to residents through her volunteering and getting involved in national groups.
The Defence Infrastructure Organisation (DIO) has completed construction of the new Crash, Fire and Rescue building at RAF Lossiemouth, part of a wider upgrade programme at the Moray station.
DIO awarded the contract to Henry Brothers to construct a new facility for RAF Lossiemouth’s professional in-house firefighters and demolish the existing Crash, Fire and Rescue building, for a total cost of £10.7m.
The new building allows firefighters to reach any part of the airfield in under two minutes. It needed to be robust due to its location close to the busy, operational airfield and provides space for stateof-the-art new firefighting vehicles and supporting training accommodation.
The Lossiemouth Development Programme (LDP) will result in significant upgrades to the RAF Main Operating Base, including providing all necessary facilities for both an additional Typhoon squadron and the new P8A Poseidon. RAF Lossiemouth now has 4 squadrons of Typhoon, a fleet of nine P-8A Maritime Patrol Aircraft and will also be home to the RAF’s new E-7 Wedgetail surveillance aircraft.
Construction of the new Crash, Fire and Rescue building started in August 2021 and is one of many improvements being made at RAF Lossiemouth under the LDP, future-proofing the Moray station for years to come.
The site has already benefitted from early completion of the resurfaced runways, installation of advanced communications and improved drainage among other enhancements to its operating capability.
Through the LDP, DIO will also provide upgraded facilities for IX (Bomber) Squadron later this year and over 300 new en-suite single living accommodation rooms for all ranks in 2023. Over the next few years the LDP, DIO and the RAF plan to construct new in-flight catering facilities and a state-ofthe-art Air Traffic Control Tower.
Darren Keddie, DIO’s Project Manager, said: “The developments at RAF Lossiemouth are an example of the great work that is done to improve our infrastructure through investment, to better support our Service Personnel and armed forces capability in Scotland.
“The new Crash, Fire and Rescue building is a testament to our close working relationship with our RAF colleagues and contractors, enabling us to provide a building that meets their needs and maintain high standards of operational safety.”
George McClelland, Fire Station Manager at RAF Lossiemouth, said: “The new Lossiemouth Crash, Fire and Rescue station is a fantastic new facility; a definite improvement on our previous old and tired building. My team are settling in and looking forward to working operationally from the new site which all personnel are delighted with. This has been an exciting project to be involved in, one which has been in the planning stage for many, many years and
has only been a dream for all previous Fire Station Managers and Firefighters.
“We look forward to welcoming Lossiemouth personnel to the new fire Station for various training events or anyone who just wishes to view our new facility.”
David Henry, Group Managing Director at Henry Brothers, said:
We are very pleased to be handing over this new Crash, Fire, and Rescue building, modernising the infrastructure and facilities on the RAF Lossiemouth site. Henry Brothers has extensive experience working in the defence and blue light sectors, and this project perfectly combined that expertise to create a first-class facility that is fitting for the day-to-day operations and training of the team onsite.
“We are thrilled to have played such an important role in upgrading RAF Lossiemouth’s site, continuing our close relationship with the Defence Infrastructure Organisation and further expanding our portfolio of efficient and advanced builds.”
Now the new facility is in use the team will turn their attention to the demolition of the previous facility, dating back to the 1960s, which is no longer fit for purpose.
The UK’s largest container firm is diversifying into the hire and modular markets.
Teesside’s Cleveland Containers has launched the Cleveland Group, encompassing the container arm along with new divisions Cleveland Hire and Cleveland Modular, allowing it to offer a full turn-key service.
CEO Johnathan Bulmer said: “By responding to the needs of our customers, we have seized the opportunity to expand into these markets.”
Meanwhile, Jon Hurford has joined as chief financial officer, Richard Tredwin as non-executive chair and former Mobile Mini managing director Andrew Thompson joins as chief operating officer.
For more information, visit Shipping Containers for Sale & Hire UK | Cleveland Containers
Mudder S5 - has passed strict independent slip resistance testing with its superior surface traction, designed to perform on wet or dry surfaces.
Made with a durable rubber compound, this outsole has specialised tread spacing with lug side profiles that are specifically designed to shed mud and clay. This boot was built to lock the ankle into the back of the boot to reduce heel slip and maintain fit integrity even in the muddiest conditions. This S5-Certified safety boot has an anti-penetration midsole, heat-resistant outsole, and composite toe cap. Finally, all-day comfort and support are achieved by Muck’s dual-density footbed, with memory foam for a customised fit and a solid foundation. The Mudder S5 is available in two colourways for £110, and launched in Spring/Summer 2022.
“In our first year, 53% of the installations we’re installing are now EnviroHoard™”
Neal James, Managing Director of Construction Site Services company, Panthera Group, reflects on the impact of the introduction of net zero hoarding system, EnviroHoard™, as another installation is completed in the heart of London.
The project to install 200m length of sustainable hoarding to protect the boundary of development site, International Way, is part of client, Telford Homes, objective of achieving a BREEAM scoring of ‘excellent’ for the project. Located adjacent to Stratford International Station, the development will provide almost 400 rental homes with shared gardens and amenities and excellent access to public transport.
EnviroHoard™ enables the project to start as it means to go on, with a carbon-free perimeter solution. Developed by Panthera Group to eliminate single use of timber in hoarding solutions, they systems combines recycled, recyclable uPVC panels with a multi-use patent-pending steel frame and a low carbon block, Enviroblok. Neal’s stated ambition is to replace 100% of timber projects with EnviroHoard and he also wants other manufacturers to follow in his footsteps.
The hoarding for International Way has a 2+ years design life and features a number of sections designed for crowd loading which really highlights the system’s flexibility. The project includes seven vehicle gates and four pedestrian gates for ease of access for site equipment and the construction team.
https://muckbootcompany.co.uk/products/mens-mudder-tall-
Metal window refurbishment specialist, Associated Steel Window Services (ASWS) has successfully completed two very demanding phases of work in refurbishing the exterior facades to the ASOS premises in Watford; renewing a past working relationship with main contractor ISG, while demonstrating its ability to embrace contemporary contracting techniques as well as traditional trade skills.
The property, which dates from late 1990’s, not only required re-glazing and extensive mastic renewal and replacement to its original aluminium curtain walling system, but the articulated, stepped and brise soliel structure also presented real logistical challenges for ASWS, in terms of access and the very tight programme timetable.
Initially, ASWS was engaged to carry out a full survey of the property’s curtain walling, to determine its general condition, highlighting specific areas of damage and deterioration, as well as any glazing units which might require replacement. This included a full external survey using MEWPS and photography. The company was then awarded the contract for the first phase of work under competitive tender, which addressed the whole building envelope across all elevations and roof works.
For more information on ASWS, please visit asws.co.uk.
Sitting adjacent to Manchester Victoria station, the £185m New Victoria mixed development is a two-phase scheme which will initially provide two residential towers of 20 and 25 storeys comprising 520 one, two and three bed apartments. An eight-storey, 150,000ft² office block is scheduled for the second phase. The residential structures are solid in appearance, with profiled panel facades, which run at regular intervals from top to bottom. The panels also extend and wrap around the top of the buildings, providing shelter for the rooftops terraces. The layout of the two structures has been driven by a need to maximise the number of apartments with dual aspect views. As a result there is one central core with three wings of accommodation. These are concrete frame using reinforced flat slab construction – and as always with flat slab construction, the risk of punching failure is a critical issue.
The Schöck Bole shear rail system has been incorporated to prevent any such risk – and enable cost-effective installation that is up to ten times faster than traditional loose links. The dramatically reduced fixing time far outweighs any additional material costs that may be involved with a prefabricated system. Also, when compared with a typical stirrup reinforcement system, an increased shear force resistance of around 70% is achievable with the Schöck Bole. It is a widely trusted and popular
solution consisting of double-headed studs and anchors, with spacing bars, which enable installation after the bottom reinforcement and before the top layer. Two spacer bars are welded to the vertical studs, which ensure the correct distance between uprights. The forged stud heads guarantee a perfect finishing bond with the concrete.
In addition to the standard Bole solution, Schöck has developed two other punching shear reinforcement variants. The type U, designed for installation before the lower mat and type O, for installation after the top reinforcement layer. All products in the range are supplied ready for installation. There is downloadable user-friendly Schöck design software available too, which enables fast and simple dimensioning of the product to British Standards and the export of CAD drawings with dxf-format.
For further information on the Schöck Bole system contact the company on 01865 290 890 or visit www.schoeck.co.uk
Wieland Electric’s podis® flat cable system provides an innovative and decentralized solution for supplying power to electric vehicle charging stations. Wallboxes can be supplied with energy easily and quickly, with significantly less effort and material consumption than a conventional installation, thanks to decentralized supply technology.
The podis® energy bus system is ideal for supplying electricity to charging stations.
A large number of charging stations can be connected to a single supply line using this decentralized power distribution system. This saves time during installation, reduces the amount of material needed, and significantly reduces the distribution cabinet’s dimensions. The feed-in or energy tap-off connection components can be placed at any point on the power bus. The podis® components’ piercing contacts enable quick and flexible positioning of the connection modules. As a result, traditional time-consumers like cutting, stripping, and terminating are rendered obsolete.
The podis® cable is a 5-core flat cable system with a cross-section of 16mm², rated at 63A, 600V. Connection cross-sections of up to 16mm² in the centre feed and up to 70mm² in the end feed are possible.
Web: www.wieland.co.uk
Tel: 01483 531213
•
•
•
Wieland Electric’s ‘Innovation Behind’ is a charging solution for electric vehicles that is fully charged for the future
Fibrelite’s custom lightweight F900 (90-tonne load rated) GRP trench covers were specified for this Northern Irish container port over new cable anchor pits for the gantry cranes.
Maintenance staff required easy, safe access to these new cable anchor pits. Fibrelite trench access covers were specified on the consultant design engineers’ tender drawings to facilitate this.
• F900 (90-tonne) load rated covers light enough for easy/safe manual removal by two people.
• Frames suitable for a port environment, given proximity to the quayside. The standard aluminium material would not be sufficient.
• Tight build schedule, in this instance the frames needed to be delivered in advance of the covers.
• Corrosion resistant covers to resist constant exposure to saltwater.
Communication between the Fibrelite technical team, the third-party contractor and the design consultant enabled Fibrelite to custom engineer, manufacture and supply a unique trench covering arrangement which would meet all the specific design criteria for this project, including the demands of this harsh operating environment.
• Trench covers were stepped 117mm to 150mm deep to achieve the required F900 load rating, reducing cover weight and costs.
• Bespoke hot dip galvanised steel frames (to ISO EN 1464) were manufactured and delivered in line with customer mandate. Steel will not react with the saltwater environment consistent with quayside applications.
• Fibrelite catered to the project’s tight build schedule with a split delivery of the hot dip steel frames followed by the GRP trench covers.
• Fibrelite is the only company on the market who can manufacture F900 (up to 90 tonne) load rated GRP trench access covers.
• Fibrelite covers are lightweight, suitable for easy/safe manual removal using ergonomically designed FL7 lifting handles at all load ratings.
• Corrosion resistant Fibrelite GRP trench covers will last for years to come.
The easy access solution provided by Fibrelite ensures there is no need for specialist personnel or machinery during maintenance or operation.
Key Benefits Of Fibrelite Covers At A Glance:
• Easy safe manual access to trench services using the ergonomically designed Fibrelite FL7 lifting handles.
• Best strength to weight ratio available in the market.
• Corrosion resistant Fibrelite covers will last for years to come.
• Anti-skid/slip tread pattern.
Visit the Fibrelite website for more case studies
Fibrelite’s lightweight trench covers can safely be removed and replaced manually by two people (Image used for illustration purposes and shows a different installation) F900 (90-tonne) load rated covers were required Custom Fibrelite trench access covers with hot dip galvanised steel framesMark Harper, Secretary of State for Transport, and HS2 Ltd Chief Executive Mark Thurston went 33 metres below ground for an exclusive end-to-end tour of the first completed tunnel on the HS2 project.
The Transport Secretary’s historic drivethrough comes a week after Chancellor Jeremy Hunt visited HS2’s Interchange station site, in recognition of the progress the project is making, with almost 30,000 jobs now supported by HS2 and over 2,700 businesses awarded contracts.
Rt Hon Mark Harper MP, Secretary of State for Transport said: “It was absolutely extraordinary to see first-hand the sheer scale and craftmanship of this monumental project which will positively transform the lives of hundreds of thousands of people across the North and Midlands.
“As well as boosting connections, regenerating communities and creating tens of thousands of jobs, tunnels such as this have been designed to ensure Britain’s biodiversity and countryside are preserved during construction and for many decades to come.”
A 2,000 tonne tunnel boring machine (TBM) dug the one-mile tunnel taking the HS2 rail line under Long Itchington Wood in Warwickshire, protecting the ancient woodland above. The TBM - named ‘Dorothy’ after Dorothy Hodgkin who in 1964 became the first British woman to win the Nobel Prize in Chemistry - broke
through the south portal tunnel wall in July this year. The tunnelling team worked around the clock for 7 months, placing 790 concrete rings to build the 10 metre diameter tunnel.
Since the summer breakthrough, a 300-strong site team from HS2’s construction partner Balfour Beatty VINCI (BBV) have pulled the TBM gantries back through the tunnel, for the TBM’s relaunch to start the second bore last week.
Mark Thurston, HS2 Ltd’s CEO said: “It was a pleasure to welcome the Transport
Secretary to site today as the first member of the UK Government to travel the entire length of the completed one-mile tunnel under Long Itchington Wood. This is another fantastic milestone for HS2, demonstrating the huge progress we’re making in the West Midlands, where nearly 7,000 people are working on the project.
Travelling from end-to-end of our first completed tunnel just shows the unstoppable momentum on a project that is providing essential skilled jobs for people today, and in the future will provide zero-carbon public transport and help to levelup the Midlands and North.
Hosted by HS2 Ltd’s CEO Mark Thurston, the Transport Secretary was joined by two Balfour Beatty VINCI apprentices on the tour – 26-year-old Thando Makombe from Coventry who is studying towards a Level 3 Laboratory Technician Apprenticeship, and 24-year-old Rintesha Shekh from Chelmsley Wood, who undertook a Kickstart placement with BBV and is now on a Quality Practitioner Apprenticeship.
Michael Dyke, Chief Executive Officer, HS2 Major Projects at Balfour Beatty, said: “Today was a proud moment for Balfour Beatty VINCI and everyone connected with this site, as we showcased HS2’s first
According to Geoff Martin, Chairman of Thorough Examination accrediting body CFTS: “The winter months can be the perfect time to make sure essential equipment is not only safe but is in good working order. Addressing a small issue now could prevent a much bigger and more costly repair further down the line.”
The latest figures released by HSE confirm that around one quarter of fatal injuries to workers in 2020/21 were in the construction industry – with the fatal injury rate 4 times the all-industry average. As for enforcement, throughout 2020/2021 a total of 1260 notices were served by HSE inspectors in construction
with a sobering 87% conviction rate for at least one offence. The average fine was £80,000 – up 40% on the previous year.
“CFTS has been working within the construction industry for a number of years to improve machinery safety, but much more must be done,” continues Geoff Martin.
There are many different causes of accidents, but a significant number could be eliminated by routine inspection of the equipment. Thorough Examinations are not optional. To meet HSE guidelines, a Thorough Examination should cover the lifting mechanism, mast, forks and chains as required by LOLER, as well as items covered by PUWER including attachments, brakes, steering and tyres.
For more information about CFTS Thorough Examinations visit www.thoroughexamination.org
completed tunnel. t was a great opportunity to explain how we delivered this incredible feat of engineering – an achievement that wouldn’t have been possible without the project team’s hard work, dedication and expertise. Now that our second tunnel bore is well underway here at the same site, we look forward to seeing the next breakthrough in summer 2023.”
The one kilometre square north portal tunnel site in Warwickshire, managed by the BBV JV is one of HS2’s largest construction sites in the Midlands and is contributing to massive job creation in the region. Around 6,800 people are already employed in HS2’s construction in the West Midlands, with thousands more jobs supported through the wider supply chain.
540 people who were out of work in the West Midlands have been helped into jobs on HS2, and 340 apprentices from the region have started new roles on HS2. BBV has joined forces with local colleges in Solihull, Dudley, Wolverhampton and Walsall to increase the number of industry placements it offers to T-Level students.
The tunnel, which preserves the ancient woodland above, forms a key element in how HS2 is managing environmental impacts through the design of the railway, protecting Britain’s precious wildlife habitats. Long Itchington Wood is classified as a Site of Special Scientific Interest (SSSI) with complex ecosystems that have taken hundreds of years to establish.
Excavation of the twin bore tunnel will produce around 500,000 tonnes of mudstone and soil, which is being processed at an on-site slurry treatment plant and separated out before being transported by a 254 metre conveyer to be used to build embankments along the route of the railway.
Leading chartered surveyors and consultancy practice, Trident Building Consultancy, has appointed a new Managing Director as part of a string of senior promotions.
Dan Roe took over the reins of the company from outgoing Managing Director Trevor Dowd who served for 24 years.
He brings 23 years of industry experience to the role, including 18 at Trident where he joined the board in 2017 to become an
Executive Director, as well as heading up the firm’s London office.
Other senior promotions include Louise Logan, based the firm’s Liverpool office, who has stepped up from Finance Manager to Finance Director, and David Juniper who replaces Dan as the Head of the London Office.
Vanessa Darce, also based in Liverpool, steps into Louise’s former role of Finance Manager.
Leading building products manufacturer, Forterra, has announced that Neil Ash will become Chief Executive Officer designate from 3rd April 2023.
This appointment follows the announcement earlier this year that Stephen Harrison would be stepping down as Chief Executive Officer (CEO) during the first half of 2023, allowing time both to commission the new Desford brick factory and support an orderly transition.
Neil has almost three decades’ experience in the building materials sector and an impressive track record of improving performance and delivering growth. Currently at Etex, the Belgian lightweight building materials manufacturer, he leads the Building Performance division which is a €2 billion revenue business. During his time at Etex Neil oversaw major capex projects, significant acquisitions, and
developed its sales approach which delivered strong top line growth.
His experience includes 15 years at Lafarge, where he undertook many roles, including the role of Vice President International Business Development and Sales and Commercial Director UK & Ireland of Lafarge Plasterboard.
Justin Atkinson, Chairman of the Board at Forterra, said “We are very pleased to appoint Neil as the next CEO. His business leadership and extensive building materials sector knowledge will be invaluable to Forterra in the next stages of our development and the Board looks forward to working with him.
“The Board and I are grateful to Stephen Harrison for the significant contribution he has made to the business during his tenure as CEO. We wish him all the best for the future after he leaves Forterra in the second quarter of 2023.”
Dan Brooks-Dowsett, Director at Trident, said the promotions recognise the hard work and commitment of the people within the business, as well as the start of the next chapter for Trident Building Consultancy.
Dan Roe specialises in the delivery of building contract work, dilapidations and due diligence surveys and will lead on the EOT going forward in his new role.
David Juniper specialises in Project Management and Contract Administration for refurbishment/remodelling of existing buildings, as well as acting for clients on preconstruction project related activities such as feasibility studies and pre-acquisition surveys.
Mr Brooks-Dowsett said: “Trident Building Consultancy has built its reputation on employing outstanding staff who deliver excellence to clients. That value is at the heart of everything we do.
“The promotions recognise the contribution these individuals have made to the business so far, and the value they will continue to bring in their new roles.
“It is also part of the ongoing evolution of Trident, ensuring we have the right individuals in place to oversee our ongoing success and growth over the medium to long term.
“I’d like to congratulate Dan, Louise, David, and Vanessa on their well-deserved promotions and wish them luck in their new roles.”
Trident Building Consultancy provides a host of services to construction industry in the UK and Ireland, including building surveying, cost consultancy, project management, and rights of light practice.
Dan Roe Louise LoganSafe Fleet appoints a new Managing Director for its UK businesses.
Steve Powell joins Safe Fleet as Managing Director of Durite and Labcraft. Durite is the UK’s leading brand in vehicle safety, lighting and electrical parts for the commercial vehicle aftermarket and manufacturers. Labcraft is the UK’s leading manufacturer of high performance and energy efficient LED lighting for the commercial vehicle and emergency services sectors.
Steve Powell will lead both businesses, which are collectively known as Commercial Vehicle Europe (CVE). Safe Fleet owns a portfolio of market-leading brands that provide safety solutions to fleet vehicle manufacturers and operators around the world.
“I am delighted to join Safe Fleet and take the helm of both Durite and Labcraft,” said Steve.
“Durite and Labcraft are two strong and well-established brands in the European CV market. I look forward to working with the existing management teams to further grow both businesses, continuing to innovate as we serve the safety needs of the UK and European commercial vehicle fleets.”
Steve has substantial experience in the commercial vehicle market. He most recently served as the Vice President of Webasto’s Europe, Middle East and Africa (EMEA) business unit, where he managed over 400 employees across 17 subsidiaries. Prior to this, Steve held a variety of roles within Webasto, leading the development and execution of sales,
Aberdeen-headquartered problem-solving company, STC INSISO has announced changes to its executive leadership team as it prepares for further business growth. Martin Dunn has moved from his existing role as COMET Delivery Manager to become Head of Operations, while Alan Smith has transitioned from Chief Operating Officer into a newly created role as Head of Investigations.
Prior to joining STC INSISO, both Alan and Martin served in the Police for 30 years having followed similar career paths with senior investigation roles, including Detective Superintendent. This extensive experience uniquely positioned them to adopt key roles within the investigation arm of STC INSISO’s business.
Mark Rushton, CEO at STC INSISO said, “These significant organisational changes come at an extremely exciting time for STC INSISO, as we enter the next phase of our business growth. Having the right people in Alan and Martin, with their unique blend of investigative experience, in the right positions to support this growth of the COMET product suite and services is crucial.”
Martin’s new role as Head of Operations will see him lead the implementation, ongoing
support, and continuous improvement of STC INSISO’s flagship and trusted investigation and root cause analysis suite of products and services, COMET.
Martin said, “I am delighted to assume responsibility and oversee the management of COMET’s operational activity in terms of client interface and delivery.
My aim is to ensure the highest standard of customer care through the deployment of experienced, knowledgeable staff and partner resources.
Alan’s new role will see him lead the company’s Investigation support workstream and through the introduction of an innovative concept `COMET Reach` ensure the expansion of the COMET suite of products. COMET Reach will become the intellectual development arm of the COMET family and will exist to research and test the tools and processes that will further COMET’s capabilities in new and existing industries globally.
Alan added, “At 10 years old, COMET remains a relatively young Root Cause Analysis system, however it is fast becoming the most relevant
marketing, and product engineering strategies to provide power and thermal management solutions to the automotive industry.
“We are pleased to have Steve on board,” said Michael Schulte, President of Safe Fleet, “With his extensive leadership experience in Europe, Steve is a great asset to further strengthen our position as the leading global supplier of safety solutions for fleet vehicles.”
and sought-after incident prevention solution. At the heart of the COMET philosophy is the desire to help organisations pivot towards a more proactive approach to Root Cause Analysis through the identification and mitigation of dormant issues before they become active and cause harm.
This proactive use of COMET transforms Root Cause Analysis into Root Cause Learning and makes the product so much more valuable in terms of incident prevention and organisational improvement.
BELOW: L to R Martin Dunn, Mark Rushton, Alan Smith
Steve PowellWith most of the construction infrastructure already developed, Karen Trigg of Allegion UK explores the process of retrofitting and why it is integral to the progression of our built environment.
Redevelopment, restoration, retrofit. No longer are these terms modestly viewed as construction buzzwords. Across the world, there’s an increasing appreciation and a budding culture that maintaining older buildings is the way forward for our planet and its people.
Globally, cities are said to be responsible for 78% of our energy consumption, of which, buildings account for around a third of the total. And when you consider that up to 80% of today’s buildings are expected to still be in use by the year 2050, it’s evident why so many are now pushing for a conscientious approach.
Across the UK, the built environment also contributes 40% to the country’s total carbon emissions, with its 28
million homes, by most assessments, constituting the least energy efficient in Europe. With so many of our current buildings set to exist 30 years into the future and beyond, why should so much of the focus fall on new-build projects? Output must be improved now, and the real substance of the challenge is retrofitting, we need only unlock its potential, says Karen Trigg of Allegion UK:
“Despite its many applications, in the context of the built environment, a retrofit is often described as the addition of new components or features to older systems. The process is designed to make a building perform better, and because of its benefits - both economically and environmentally
speaking - retrofitting has emerged as a popular solution for advancing the efficiency of buildings.
On an environmental level, it’s widely understood that the construction industry must strive to do better. In many developed countries, four out of the five buildings set to stand in 2050 already exist, meaning the onus of addressing energy consumption lies upon us now. Accordingly, decision makers are obliged, and actively encouraged, to prioritise activities such as retrofitting in order to meet the energy-saving targets as outlined in the Paris Agreement.
“In terms of cost savings, the process of adding better functioning components to our buildings will benefit many. Retrofitting is an attractive proposition for most large or ageing structures as it provides decision makers the ability to improve upon key problem areas without having to consider large-scale reconstruction or demolitionsaving on time, resources and costs. Modern housebuilders and homeowners can look towards retrofitting, too, improving their own footprints and putting money back in their pockets, as they seek to combat the significant rise in energy costs.”
Investment in retrofit projects could have a seismic effect on the construction industry, acting as a catalyst to the economy and improving various areas of our building network. And while it’s true retrofit can play an important role, consequences can arise when a project isn’t approached correctly. Karen Trigg continues:
“Naturally, modern technology developments and legislation changes will continue to drive product enhancements. Take door hardware, for example, a crucial component of a building’s fire safety, security and everyday operation. There will always be a responsibility to ensure the hardware in older buildings remains up to standards and that we are meeting the latest in safety and sustainability regulations.
“As time passes, hardware experiences wear and damage and the replacement of aged components becomes necessary. And in some cases, new products will emerge as an improvement on previous applications. With that, an effective retrofit could significantly enhance the functionality of a door and the fire safety and security of a building - not to mention the environmental benefits
Karen TriggRetrofitting
associated with installing better, long-serving products.line with the Building Safety Bill’s regulatory framework known as the Golden Thread of Information.
“Effective retrofit projects can safeguard the quality of our buildings in the future, making crucial improvements to cost, safety and functionality. Although, without a proper understanding on the subject, mistakes will readily undo the good work that many are aiming towards. A poorly specified or incorrectly installed retrofit could prove costly - in terms of money and time - and even present a danger to the integrity of a building’s fire safety.
and Remediation Tax Relief is one of the best kept secrets in the UK construction and building industries.
has remained unused from the earlier of 1st April 1998 or date of acquisition can also form the basis of a claim, especially if it has suffered tipping and illegal waste disposal over the years.
“A retrofit must be completed consciously and professionally, with reliable replacements. Failing to do so could be a breach of the Regulatory Reform (Fire Safety) Order. Whether an environmental or safety conscious choice, the first step of any retrofit installation is to ensure the selected hardware replacement is suitable for application, and decision makers must understand the reasons behind their choices or seek professional guidance.
It is available to recover costs of carrying out remediation work prior to receiving planning permission to render the land useable for new developments.
Qualifying criteria are few. You must be a registered UK corporate entity and the owner of the land. You cannot claim if you own the land and caused the contamination. From this point most costs associated with the clean-up measures, disposal of waste and making good the finished projects form the basis for cost evaluation and submission of the claim.
Since Land Remediation must be undertaken before any construction works begin, it is advised to consider remediation preparations early.
All contributory costs should be identified and recorded. These are wide and include your own company costs of labour, management, subcontractors, suppliers, travel and subsistence costs, surveys, tests, disposal and replacement of soil and making good.
“For door hardware specifically, retrofit projects must also be compliant under UKCA and CE certifications and be fitted to the manufacturer’s instructions, in accordance with BS EN 1154. Decision makers can refer to the Code for Construction Product Information (CCPI) for clear, accurate, up-todate and accessible product information - in
Known contaminated land can be claimed for. Derelict land that
MCS Corporate urges its clients
to consider all possible sites for development and planning. We E: charlotte@mcs-corporate.com
To qualify for Land Remediation Tax Relief your company must have incurred costs on cleaning up land or buildings considered to be in a contaminated state. The scope of costs allowed is generous.
You must be registered as a limited company in the UK and be the owner of the land or building at the time of the remediation work. In addition, the land or building must be owned either as a freehold or longer-term leasehold.
Common examples of qualifying contamination:
• Asbestos
• Ground and landfill gases
• Japanese Knotweed
• Sulphate contamination in soil and concrete
• Arsenic
• Removal of redundant utility services and concrete foundations
Qualifying costs can include surveys, excavations, soil and groundwater treatments, staff costs, materials and subcontractor costs. Claims can be made for categories of derelict land. This can be advised with relevance to time periods when land could be considered for derelict status.
charlotte@mcs-corporate.com mcs-corporate.com
Regardless of the industry you operate within, if you’ve acquired land or buildings in a contaminated or derelict state for intended commercial use, you could claim.
35
A further two surveyors at DM Hall, one of Scotland’s foremost firms of Chartered Surveyors, and which this year celebrates 125 years since its foundation in 1897, have passed the final professional hurdle of their exhaustive training with flying colours.
The two, Ross Craig and Ruari MacIntyre, now qualified chartered surveyors, sat and passed successfully the Assessment of Professional Competence (APC), which sees them progress to be members of the Royal Institution of Chartered Surveyors (RICS).
Ross Craig in the firm’s Glasgow Commercial department and Ruari MacIntyre in its Aberdeen Commercial department have both successfully attained the highly valued property professional qualification after an extensive course of study. Ross joined DM Hall in 2019 and holds a master’s degree from Edinburgh Napier University. He handles both commercial agency and valuation.
DM Hall recruited Ruari as an intern, also in 2019, after he completed an MSc degree in Real Estate Management and Investment at Edinburgh Napier University.
The Mayor of South Yorkshire, Oliver Coppard, visited Henry Boot Construction’s flagship Sheffield city centre sites last week to learn more about the developments and one of the region’s leading businesses.
Alongside representatives from Sheffield City Council, the Henry Boot team showed the Mayor around some of their key city centre construction sites, which all form part of the Council’s £480m Heart of the City regeneration scheme. This included the evolving Cambridge Street Collective food venue, residential development Kangaroo Works, the ‘zero carbon ready’ office Elshaw House, and Pound’s Park – a brand-new public green space.
The Elshaw House and Cambridge Street site has been designated an Ultra Site – meaning it is recognised by the Considerate Constructors Scheme (CCS) as a beacon of best practice. An ambitious programme of social value is being delivered as part of the Heart of the City masterplan. Across its own four sites, Henry Boot Construction has so far facilitated over 40 site visits and career-education engagements with local learners and the delivery of more than 20 work experience placements (including support for Sheffield City Council’s Construction Sector Routeways Programme). In addition, more than 20 apprentices have worked across the sites and over 40 new employment positions have been created in connection to the projects.
Henry Boot have also recently joined the South Yorkshire Cornerstone Group (a collection of local employers committed to careers education for local young people) as co-Chair. This group sits under the governance of the South Yorkshire Mayoral Combined Authority.
Mr Coppard, who spoke at the Climate Change Summit 2022 last week, was also very keen to learn about the sustainable credentials of the projects. In addition to the lowcarbon specification of the buildings themselves, he was informed about the temporary hybrid power systems being trialled on the Kangaroo Works site. This ground-breaking technology aims to provide sustainable and efficient power to the site with significantly decreased emission levels.
Ross CraigKilwaughter Minerals brand K Systems has received three accolades at the high-profile Insulated Render and Cladding Association (INCA) Awards.
At the national awards ceremony held in Leeds, K Systems won in the High-Rise Refurbishment (render / traditional finish) category and picked up highly commended in both the Low-Rise Refurbishment (render / traditional finish) and MMC / Offsite categories for projects completed across the UK.
The most prestigious awards of their kind for the UK external wall insulation (EWI) industry, the INCA Awards celebrate technical excellence, high quality, innovation and best practice throughout the sector.
Gary Wilmot, CEO of Kilwaughter Minerals, said: “As a leading installer of EWI systems across the UK and Ireland we are committed to providing the highest level of service to our clients. We are therefore exceptionally proud to once again have been recognised at these
most prestigious of industry awards. It is an endorsement not just of the incredible skill of our own teams at K Systems working across the country, but also the first-class capability of our partners that have enabled us to deliver these award-winning projects.
“Many congratulations also go to the other winners across all categories in what has been another busy year for the EWI sector with the continued drive to reducing energy costs and the pathway to carbon reduction.”
Nominations are spread over seven categories, with each submission being rigorously scored by a panel of industry expert judges.
K Systems took top spot in the High-Rise Refurbishment (render / traditional finish)
category for its transformation of Glasgow’s prominent Cartcraigs building.
The project reinvigorated a tired, weatherbeaten city tower block into a modern, fit-for-purpose residential property with a beautiful exterior finish. This included a significantly improved thermal performance along with the highest standard of fire safety rating required for tall buildings across Scotland.
K Systems’ highly commended accolades were awarded for a 23-house refurbishment project in Rochdale and a 70-home, new build residential project in partnership with Glasgow Housing Association which showcased the organisation’s innovation and technical prowess.
Scotland’s major electrical bodies have congratulated two apprentices from north of the border who have triumphed in a prestigious UK-wide competition.
The Scottish Joint Industry Board (SJIB), Scottish Electrical Charitable Training Trust (SECTT) and electrical trade association SELECT have all saluted Craig Fairweather and Andrew Horne for clinching gold and silver respectively in the SkillELECTRIC contest.
Craig, 23, was crowned 2022 SkillELECTRIC champion after a challenging two-day final which saw the cream of young electrical talent from across the UK battle it out for top spot.
Employed by SELECT member firm McDonald & Munro in Moray, and trained by Moray College and SECTT, Craig
excelled in a complicated task to install a range of first and second fix items including PVC/PVC surface clipping, plastic conduit, trunking and fireproof cable.
The runner-up spot went to his fellow Scottish apprentice Andrew, who works for SELECT member firm A Campbell Electrical Services in Stornoway, Isle of Lewis, and is trained by Lews Castle College and SECTT.
The SkillELECTRIC final took place at Middlesborough College on 16 and 17 November, with the winners announced on Friday 24 November during a live WorldSkills UK broadcast with TV presenter Steph McGovern.
Judges assessed the competitors in areas such as measuring accuracy within
2mm, horizontal and vertical alignment, electrical terminations, functionality, containment symmetry, inspection and testing and safe working practices.
The final included two other Scottish apprentices – Robert Rae of Dumfries & Galloway College, employed by SELECT member firm Lotus Electrical Services, and Robbie Neave of Borders College and Braidwood Building Contractors.
Managing your Mental Health has become a topic high on the agenda for the construction industry, with more awareness and support available than ever before.
But how comfortable would you feel approaching your boss about personal concerns or work worries that are causing you sleepless nights? For many, it remains a tough decision whether to open up to colleagues, with fears that raising issues might put your livelihood in jeopardy, or alienate you from peers.
The Construction industry is a sector which has historically suffered from a ‘man-up’ culture. The impact can be devastating and alarmingly, two construction workers still lose their lives to suicide every day.
However, times are changing and increased advocacy for mental health is making a positive impact, as we found out when we spoke to Glen Hamilton, Credit Manager, at Mobile Mini UK, one of the leading worldwide providers of portable accommodation and secure storage containers.
Glen is open about the challenges he has previously faced and is sharing his story to inspire others, indicating that he has been able to turn his life around by making the brave decision to speak to colleagues during his time of need.
What made you realise things were not right?
Things began to spiral a few years ago as I was having some problems outside of work and also dealing with a really stressful project that I felt rested on my shoulders. I was feeling anxious, down and struggling to keep things in check.
Juggling so much stress and pressure at work was depressing but I thought it would be okay after a while so I just struggled on.
Did you make your worries known at work straight away?
No. I didn’t realise how bad it was. I just put my emotions down to tiredness but later realised how lethargic and anxious I had become. These feelings didn’t go away, they grew and I was left feeling more and more under pressure as the days and weeks passed by.
How did you finally share your Mental Health worries?
I was actually attending a Mental Health Awareness Course with my colleague Helen, from Human Resources, when she noticed how moved I was by some of the stories coming out of the training course. Afterwards, she pulled me to one side and asked if I was ok. I completely broke down for the first time and really opened up to her about what was going on and how I was feeling.
Fortunately, the HR team at my company were really supportive and it felt like a weight off my chest being able to talk to someone without feeling judged.
“IT’S
Helen suggested I make an appointment with my GP and as I had already booked a routine check-up with a nurse, I brought up how I had been feeling whilst I was there. The nurse called for the Doctor to see me there and then, who signed me off work and set me on the path to put a strategy in place for managing my feelings of depression and anxiety. This gave me the opportunity to get further professional advice and begin a six month journey of recovery.
Did you feel pressure to return to work sooner?
No, Mobile Mini were fantastic and made sure I didn’t rush back, even though sometimes I wanted to put a brave face on and get back to my job. However, they recognised that I needed more time. Their support meant that going through the steps to build myself back up was life changing and I now feel like a different person.
How has your life changed since you began your Mental Wellness journey?
I am much calmer and no longer rush about feeling anxious or get road rage in the car. I’ve learned to live in the present and no longer look back at things that can’t be changed. I don’t worry about the future so much and things that might not actually happen.
Since addressing my own Mental Health, I’ve trained with the company to become one of its Mental Health First Aiders (MHFA). I’ve gone from someone who would just think to ’get on with it’ to a person who actively helps others open up and begin their own road to recovery if they need it. It’s so rewarding and important in our industry especially, which
is still male dominated, as often men find it harder to open up to each other about personal problems.
Helen and I became the first two qualified Mental Health First Aid (MHFA) professionals at Mobile Mini and there are now 1 in every 20 members of staff fully trained. I have decided to be really open about my own experience to help others, showing it’s ok to talk about your feelings encouraging others to speak up and get help.
How do you feel you are helping those in the Construction industry to open up?
I am determined that no one has to struggle as much as I did at the time. I felt like a bit of a wall was up and I couldn’t really speak about how I felt. Despite good intentions, people didn’t really know what to say about what I had been through. This is why I think we need to end the stigma of talking about our mental health – sitting with your feelings is a very lonely place to be.
Helen and I became the first two qualified Mental Health First Aid (MHFA) professionals at Mobile Mini and there are now 1 in every 20 members of staff fully trained. I have decided to be really open about my own experience to help others, showing it’s ok to talk about your feelings encouraging others to speak up and get help.
I’ve helped many people, both in and out of work – some who were on the brink of desperation and needed guidance on
where to turn for support. This increased through and post-pandemic, but Mobile Mini was brilliant at giving me time to support people without it impacting on my day job.
What should someone do if they think a colleague is struggling?
Knowing how to spot the signs is often key to getting things out in the open and to point someone in the direction of help. Asking how someone is if they seem more withdrawn than usual and raising any major concerns with a Mental Health First Aider in your company or a line manager is really important. I want more people in construction to make themselves available so people have someone to talk to. Often the first step to recovery is admitting there is a problem to yourself. People need to know it is okay to talk and that the workplace is not trying to catch them out – just wanting to help and keep them safe. That trust can only be built through visibility and positive reinforcement.
What’s would you like to see the construction industry do next?
Fortunately, employers like Mobile Mini are addressing the issues faced, but too many examples still exist in the industry where businesses are not as switched on to it yet. The ‘man-up’ culture still causes apprehension and I have even heard elsewhere of people being told to take a holiday if they are feeling down. I’m a huge advocate for people to train as MHFAs –it’s so vital to have these voluntary roles within the company; rather like a First Aider or Fire Marshall.
Illness is illness and does not have to be a physical impairment that you can see. It’s often the strongest of people that push themselves to breaking point and it can happen to anyone, so people must stop worrying about what others might think and help themselves.
Getting your company involved in MHFA and with dedicated charities such as the Lighthouse Construction charity, who Mobile Mini partner with, can open doors to support and improve the knowledge and support for mental health in construction. You never know when a conversation has the potential to save a life.
Every industry creates dust, but it’s the invisible dust that’s the most harmful.
As specialists in dust management, MAXVAC has been working with a wide range of companies who are exploring ways of combating the ongoing Health and Safety concerns with Dust Management. MAXVAC offer a broad spectrum of solutions that are suited to deal with any given dust issue, either on site or in the workspace. By taking air quality measurements and determining what needs to be achieved in affected areas, a qualified recommendation is made. Once implemented the Dust Management Solution will bring dust levels well below any recommended exposure levels and provide a safe working environment. Customers are often surprised at how quickly and easily the solutions can be implemented and often at much lower prices than expected.
Given the variance of construction environments, it’s important to understand the main three origins of the ‘Dust issue’,
1) Dust at source, cutting into a wide range of different materials on site can cause lots of dust, and in some cases hazardous dust, by using extraction vacuums with connectors to the actual tools in use, this method extracts the dust at source.
2) Airborne Dust, a large proportion of this you cannot see. Particles will travel through the air, usually following internal air flows, and find a place to settle, sometimes even 24 hours after the work has finished. This is the dust you breath in, and has always been a source of irritation, not only due to the effects it can have on the body, but because the dust can travel throughout the rest of the site or a client’s property, this usually leads to long and very thorough clean up processes.
However by using the correct mobile Dustblocker/Air cleaner this dust can be reduced by a staggering 98%. Clean down time is dramatically reduced and the air quality both during and after the work keeps lungs free from infection & irritation.
3) Collecting and removing Dust from the Floor, By using the appropriate vacuum, dust can be quickly removed from floor areas which significantly reduces airborne dust caused by other activities such as moving of goods, pallets, sheet materials etc. Even walking can raise potentially harmful unseen dust that can cause damage deep inside the lungs.
Regulation only permits 0.075 mg per m³ of silica dust in the breathing zone of a user (this corresponds to 0.5 cm dust in a plastic coffee cup in a room the size of a football pitch and a height of 4 metres!).
It is virtually impossible to meet these strict requirements without using ‘at source’ devices and localised room cleaners such as dustblockers.
been working on some recent projects with impressive results; ‘We have seen a growing concern from HSE managers with how dust is managed on sites, and we are delighted to be working with HSE Managers who have now seen the results that can be achieved when the correct dustblocker are used. For example, one of our client’s contacted us regarding a project consisting of re-sanding and varnishing a large floor area in a Games room, the concern was three fold. 1. preventing the dust from spreading throughout the rest of the owner’s home, 2. reducing the impact of the smell of varnish throughout the property, 3. due to the surge in energy bills wanted to limit doors and windows being open, and as this project was time sensitive. Once we had understood the work that was being carried out, and taken into account the total volume of floor and air space, we then recommended a number of Dustblockers units which in their own words, ‘had significantly reduced the presence of Dust from the site as well as radically reducing the clean up time, during and after the work was completed’.
Mark Hawkes, BDM for the Addex Group (Distributors of MAXVAC products) hasIn Great Britain alone over 500 construction workers are believed to die from exposure to silica dust every year. That’s about 10 people a week. Organizations have a responsibility to protect their workforce, the use of outdated equipment or no equipment at all can now have serious legal implications.
MAXVAC continuously improves and develops effective machines and accessories by listening to customers and staying ahead of the latest regulations, are you doing the same?
Seven in ten (70%) social housing tenants lack confidence in the fire safety of their home and two thirds (68%) do not feel the Government has done enough to improve fire safety over the past five years. Ahead of the imminent Fire Safety (England) Regulations 2022, JELD-WEN explores the critical role of fire door safety, what’s due to change and what should happen to better protect tenants in its new white paper, ‘Fire Safety: Time to Shut the Door on Risk.’
Prepared by fire door specialists at JELDWEN, the thought-provoking document sets out the purpose and effectiveness of fire doors, fire doors regulations, manufacturing, installation and maintenance, before exploring research which looks at confidence amongst the social housing community and wider factors, such as the trade skills gap and housing crisis.
It sets a benchmark for perceived progress in the industry, noting that just 30% of people living in social housing feel assured that their home is sufficiently protected against the threat of a fire. Crucially, ahead of the Fire Safety (England) Regulations on 23 January 2023, it also highlights some of the additional measures that can help deliver that progress, with a strong focus on enabling a much more rigorous and transparent approach through stages in the fire door safety chain.
Amongst additional proposed measures, the white paper calls for:
• A legal requirement for all fire door installations and maintenance work to be conducted by qualified installers,
validated through a UKAS-accredited certification scheme.
• A mandatory standard which outlines how fire door information should be stored, updated and shared. To include manufacturer data and third-party certification, installation details, maintenance records, and blueprints all stored in an easily accessible digital format.
• A legal requirement to mark every fire door in the UK with its performance and the name of the manufacturer.
Writing on the white paper, Glyn Hauser, R&D Senior Group Manager at JELDWEN, comments:
Our home is intended to be a safe haven so it’s concerning that millions of social housing tenants still don’t feel that theirs would be adequately protected in the event of fire. While it is our hope that new regulation will help to refocus fire safety standards and build reassurance for tenants, it is our belief that there is still scope to do much more.
“A fire door, for example, can save lives but only when installed and maintained correctly. However, there is still no legal requirement for this critical safety product
to be installed or maintained by a person with any specific formal qualification.
“We also believe the opportunity to apply a standardised or regulated ‘Golden Thread’ approach to the manufacture, installation and maintenance of fire doors could help build better traceability, accountability and trust.”
The launch comes at a pivotal time for the social housing sector, as it prepares to introduce many of the key changes brought in by new regulation - to include quarterly fire door checks and the better provision of fire door safety information.
Indicative of the pressing need for some of these critical measures in respect of fire door safety, JELD-WEN’s research also found:
• Just a quarter (25%) of social housing tenants state they have a good understanding of fire doors and how they work
• One in five (17%) admit that they couldn’t tell the difference between a fire door and a standard door
• Only a third (32%) feel that fire doors have been adequately maintained in their property
Glyn adds: “Clearly, there is still a huge task ahead when it comes to enabling improved fire safety, particularly in respect to fire doors. This whitepaper provides information about fire door safety, what is due to change and what we believe should change to elevate standards across the UK.
“It is our hope that it may prove a valuable resource for those operating in the industry as we work towards a future where every tenant is able to feel safe at home.”
The ‘Fire Safety: Time to Shut the Door on Risk’ white paper is available for free to download. Visit https://www.jeldwen.co.uk/fire-safety-white-paper
Download
With the Building Safety Act and the new Fire Regulations coming into force in 2023, the entire industry is focused on how to meet the new legislation requirements. The new legislation reforms building safety, requiring evidence for fire safety information to be digitally stored, a socalled unique ‘Golden Thread’ for each building and asset, providing all relevant structural data information across each Project Gateway. Efficient construction management is essential for a project’s success, and in 2023 it will be vital to have a digital system in place to minimise risks on-site and keep track of documentation, and of project progress.
It is therefore not surprising that construction companies around the world are looking for new tools to optimise their processes and build it right, first time.
One solution which emerged in the UK in 2019 is PlanRadar, chosen by more than 120,000 users across 65+ countries who aim to deliver projects on-budget and ontime. PlanRadar is an award-winning digital platform that drives time and cost savings across teams in construction and real estate
projects by digitising task management, documentation and communication.
PlanRadar’s aim is to make working together easier, to support traditional construction project management with digital technology, reducing inefficiencies, collating project data in one place, and ultimately saving valuable time and money.
A tool such as PlanRadar simplifies construction management in its entirety: from planning to control, from cost analysis to non-conformity management, relieving managers of many repetitive, time-consuming tasks which can instead be spent on project realisation. An-ever evolving platform, PlanRadar is now also the only digital management platform to offer NFC tags and QR code compatibility. The technology allows all information and relevant documentation for each fire safety element to be retrieved with the click of a button, providing live, accurate building data. The use of QR codes on-site enables the creation of a tamperproof audit trail for each project.
PlanRadar is designed to minimise productivity gaps, track relevant information, connect all project team members, and thus make management simpler and more efficient. Transparent, traceable communication between the various
team members, including employees and subcontractors, ensures the project stays on-track. Communication is one of the most important components of construction project management. The ability to capture live evidence on-site, and send direct messages or share documents, images and voice messages, enables smooth and transparent communication. The main advantage being all relevant project information is accessible on a central platform in a uniform format. In addition, each activity and relevant document or image is logged with a time and data stamp providing a full, tamperproof audit trail.
With this universal change of responsibility and culture within the construction industry, the digitisation of fire safety elements and procedures provides total compliance and peace of mind, particularly in case of future disputes. PlanRadar´s software, which can also be used from smartphones and tablets via an app, is fully customisable and allows users to:
• Immediately capture and resolve risks onsite in real time
• Easily document facts during fire risk assessments
• Build custom form & report versions and have the team complete them in the field;
• Keep forms updated centrally and roll out any changes in real-time. If there is a change in advice, react quickly to ensure best practice;
• Store completed forms securely in the app or export them in custom reports with a single click
• Retrieve fire protection documentation at any time
Fire safety software plays a key role in the fire protection system of any project or building. Fire safety software is any digital solution, platform or app that allows you to implement fire safety regulations and keep a building or structure safe from fire risks.
It can be used by a number of different people: from specialist fire engineers to QSHE managers at construction companies, to property and facilities managers. PlanRadar can accommodate all types of users as its fire risk assessment forms are customisable and users can design their own report templates. Each type of user has somewhat different demands for their fire safety software, and PlanRadar can meet all of them.
In the United Kingdom, the protection and implementation of passive fire protection systems is still a pending issue in many homes and premises. There is a lack of specific or sufficient systems for firestopping. Without adequately constructed fire stops, smoke and flames can swiftly spread through a structure, causing damage, and endangering the lives of any residents.
PlanRadar allows all information and relevant documentation for each fire safety element to be retrieved with the click of a button, providing live, accurate building data. The use of QR codes and NFC tags on each fire safety element creates a tamperproof audit trail on the project site.
Fire safety specialists can assign problems, in the form of tickets, straight to a construction plan using PlanRadar. Each QR code can be attached to a relevant ticket in the software, accessible at any time. They may include supporting documentation in this ticket, including images, videos, voice recordings, written remarks, and maintenance details. This is complemented by in-app bespoke fire safety reports based on collected data, including fire risk assessments, safety checklists, EWS1 forms and passive fire protection needs. Reports can be produced in seconds, saving time, and speeding up project compliance. The simple ability to capture photographic evidence on-site completes the provision of a tamperproof audit trail, with date & time stamps provided for each activity.
To manage a construction project efficiently, you can rely on PlanRadar, a tool for construction professionals. PlanRadar enables users to create the necessary Golden Thread for their project, by providing a full, tamperproof audit trail within the platform. Let PlanRadar help you build your projects on-time and on-budget. Build it right, first time.
PlanRadar?
Book a demo or try it for free
Do you want to know more about
Dräger, an international leader in the fields of medical and safety technologies, is calling for increased regulation and more detailed safety guidance within the tunnelling industry, following recent research highlighting safety as a major concern for those working underground.
The survey gathers a range of perspectives from tunnelling professionals to find out how safety challenges are perceived, and to what extent solutions are considered beneficial, practical and appropriate for the distinct environments found in tunnelling.
The research revealed that the four highest perceived risks were the availability of safety equipment, gas/ vapour leaks, the time taken to evacuate a tunnel, and a lack of robust and upto-date safety plans. These concerns were ranked higher than issues such as the structural integrity of tunnels and working within confined spaces.
Further compounding the issue, just 14.8% believed that all contractors on site had a thorough understanding of safety planning, and more than two in five (40.7%) respondents said they did not think enough priority was given to safety planning in tunnelling projects. Budget and time constraints were cited as reasons, along with the belief that because tunnelling accidents are ‘rare’, safety planning wasn’t always prioritised.
Alarmingly, the research suggests accidents are actually relatively common, as nearly one in three (29.6%) of respondents had been involved in a safety incident while working in a tunnel that required the use of safety equipment, and a further 59.0% stated that they had been involved in a nearmiss incident in the same environment.
Sarah Sanderson, Tunnelling Product Specialist at Dräger, says that these statistics, while alarming, are not a surprise: “Tunnelling environments can be extremely hazardous, with a variety of different machinery being used within a confined space, often at the same time.
“Indeed, we have heard of global projects where stakeholders have been extremely relieved when there have been no major incidents after a year,” she says
“The fact that these incidents are relatively common goes to show that serious accidents are not that rare, and safety
equipment and planning should not be considered a ‘nice to have’, but deemed critical and essential.”
An overwhelming majority of the sample stated safety equipment being damaged or lost was commonplace, with 44.4% of respondents stating it was necessary to be replaced in every project, 25.9% answering replacement was needed in most projects, and a further 25.9% claiming that it was occasionally required.
While traceability and asset registers are generally in place to mitigate and manage issues concerning lost and damaged kit, more than one in ten (11.1%) of respondents were not aware of these registers, and nearly half (48.2%) did not know whether recent projects had had one in place.
“It is our industry’s responsibility to keep tunnelling personnel as safe as possible at all times,” adds Sarah.
Detailed safety and rescue strategies must be planned, coordinated and agreed across all interest groups – and indeed supported by thorough and dedicated regulation.
Hosted by the Tunnelling Journal, the average number of years served in personnel in the tunnelling industry by respondents was 22.9 years, with more than a third (34.0%) of respondents serving for more than 30 years.
For more information on the research findings, please visit: https://tunnellingjournal.com/ archive/tunnelling-journal-octobernovember-2022/
Because pipes, cables, ventilation ducts and other services sometimes need to pass through a hollow plasterboard or lath & plaster ceiling we have introduced new variants of our successful FIROBLOK® range of fire protection sleeves.
Designed specifically for plasterboard or lath & plaster ceilings, these new products have a metal encasement under the reinforced foiled cloth which also serves as a hinge, enabling the sleeve to open up for fitting around existing services. Once, fitted, the adhesive tag is peeled off to seal the two halves together.
Fixing tabs are used to secure the sleeve with screws or toggle bolts as appropriate.
Following the growth in popularity of using metal back boxes in hollow plasterboard walls, we fire tested various combinations of metal boxes, extenders and gaskets in a hollow plasterboard partition wall to ensure that fire integrity of the wall was maintained. Some boxes were mounted flush with the face of the plasterboard and others were set back.
SPATEX 2023: The UK’s only dedicated water leisure exhibition will return to the Coventry Building Society Arena from Tuesday January 31st to Thursday February 2nd. Awash with an impressive line-up of exhibitors and unique networking opportunities, it is a must-attend event for every construction professional in the UK.
Now in its 27th year, the annual exhibition is bursting with the very latest innovations in swimming pools, wellness facilities, water features and all their ancillary equipment. It offers architects, surveyors, specifiers, developers, and all those involved in the construction of facilities incorporating water, whether leisure or ornamental, to meet over a thousand people from the industry in one day.
Many of the one hundred plus exhibitors, drawn from all four corners of the globe, will feature generous show discounts, competitions and prize-giveaways.
With the price of energy and fuel inexorably rising, SPATEX’s focus is on sustainability and showcasing the latest innovations designed to reduce energy consumption and bills.
“We aim to bring the topic of energy saving into sharp focus and make it a forum for discussion and finding solutions,” says SPATEX Organiser, Michele Bridle.
With education, the latest technological advances and careful management, there are effective ways to significantly reduce energy consumption and bills. It’s this positive message that, with the help of our exhibitors and experts, we aim to communicate to our visitors.
SPATEX is the first opportunity to view 2023’s most box-fresh, technologically advanced products. This is the place to pick up the latest labour-saving products to make installation and operation speedier. Viewing the latest trends will ensure your projects reflect the very best in the marketplace.
Pick up free impartial advice from leading industry representatives and associations, such as BISHTA (British & Irish Spa & Hot Tub Association) and SPATA (Swimming Pool & Allied Trades Association). Please call in at the SPATEX Technical Help Desk, at the entrance to the exhibition hall, and the team will be happy to point you in the right direction.
Visitors have the opportunity to build their training and education. Be sure to check out the double seminar arena featuring forty talks and taking place over the course of the three days of the show – all free-to-attend.
In Arena 1, the ISPE (Institute of Swimming Pool Engineers) is staging the ever-popular workshop programme. CPD accredited, the workshops offer all the latest insights and tools the industry has to offer plus the latest standards and guidance affecting all working in wet leisure facilities.
Register now for FREE https://spatex-2023.reg.buzz/
SPATEX 2023 Tuesday January 31st to Thursday February 2nd 2023. The Coventry Building Society Arena, Coventry CV6 6GE is easy to get to - just 500 yards off the M6 and within two hours commuting time of 75 per cent of the population, with 2,000 free on-site car parking spaces.
For more info: helen@spatex.co.uk Tel: +44 (0) 1264 358558.
The construction industry has long been criticised for its lack of innovation and slow adoption of modern business practices. To resolve the issues that exist as a result of this, industry transparency and digitisation is key.
A 2020 report found that construction is slower than any other industry in adopting digital processes (McKinsey’s Report) – despite a RICS report that very same year, finding that 72% of construction firms worldwide would class digital transformation as a priority. Within the same RICS report, it also found that 32% of the firms surveyed invested less than 3% of annual turnover on digitisation. With two years having passed since both McKinsey and RICS published the reports, as an industry, we’re still unable to say that a clear transition has taken place and work still needs to be done.
COP26 renewed the focus on sustainability in the industry, with increased pressure to assess and
report on the environmental impact of a product, process or service and in April this year, the UK government introduced a legal requirement for large corporations to report on emissions, meaning the pressure is now on. Using digital systems such as ISO 14001:2015, companies can report on sustainability and achieve immediate accreditation on their level of sustainability in a project, as this allows for multiple stakeholders to submit their data. There’s a real opportunity here for the industry to harness technology for good and take accountability with transparent data on sustainability.
Recent events have of course disrupted the supply chain, which has had a huge global impact on many sectors, construction included. ONS data recently revealed that the construction industry has seen stock levels fluctuate 5% quarter-to-quarter since 2019, as a result of Brexit, the Covid-19 pandemic and to an extent - the blockage of the Suez Canal in March 2021. Such fluctuation signals issues in ordering, supply and invoicing - all of which can be remedied with better communication, transparency and digitisation. Open ECX’s eOrdering platform ensures there
is no room for error, as a cloud-based technology that integrates all levels of the supply chain, from material manufacturer to the businesses managing projects of any scale. Saving time, expense and helping to avoid human error, Open ECX’s solution automatically processes orders and transmits the data to sales and finance teams, in real time.
In conclusion, the big global events mentioned above have of course had a huge impact on the construction industry – however, they have pushed already existing issues into the spotlight, encouraging the sector to make real changes to ensure a brighter future.
Internally, suppliers, contractors and manufacturers are becoming more transparent every day, with investments into internal technology.
We must now look at how the industry can work together to tackle the climate crisis, improve cash flow and futureproof the industry.
Matthew Jones, Founder of Open ECX, discusses the importance of digital investment for a more transparent industry. Matthew Jones, Founder of Open ECX