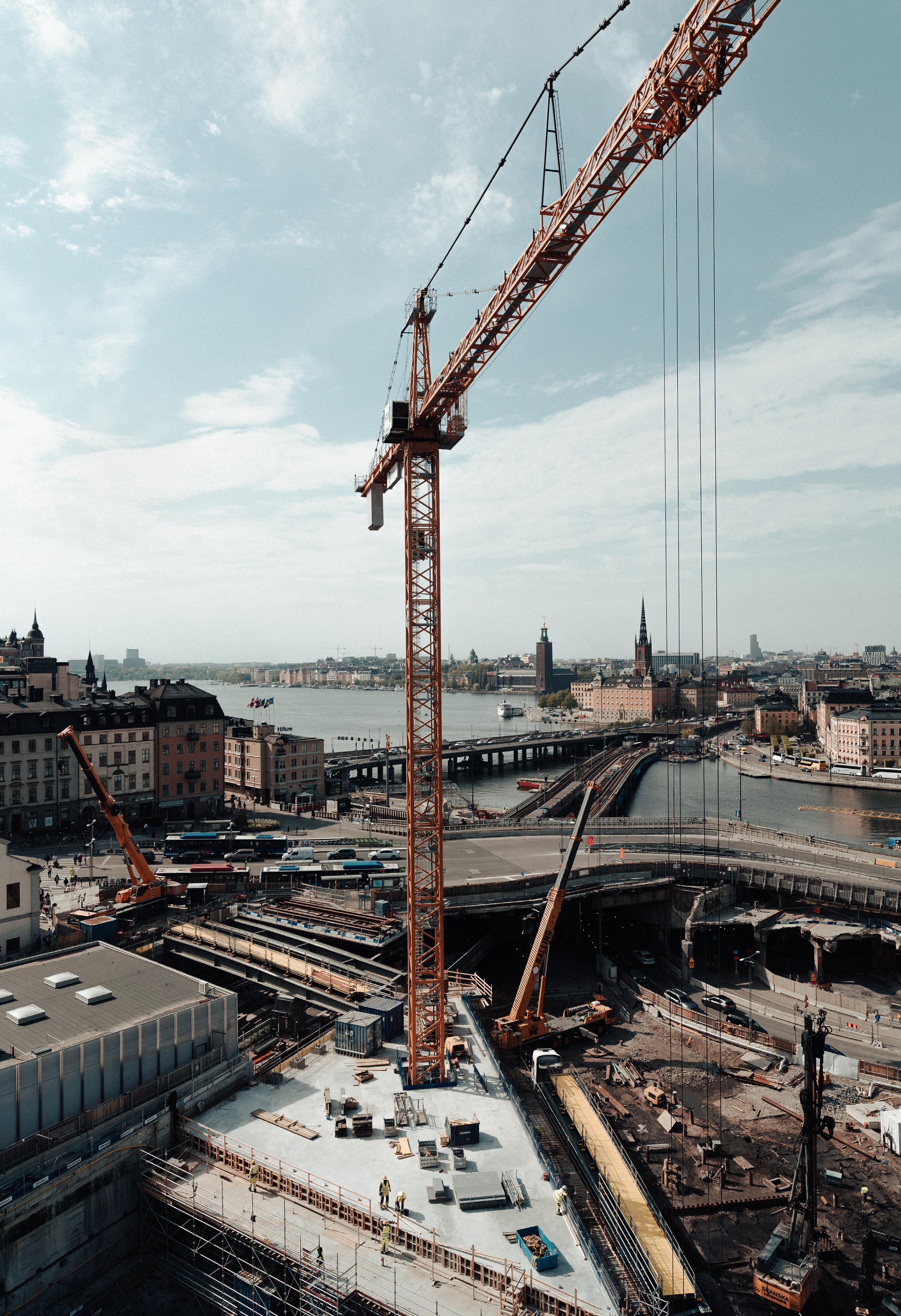
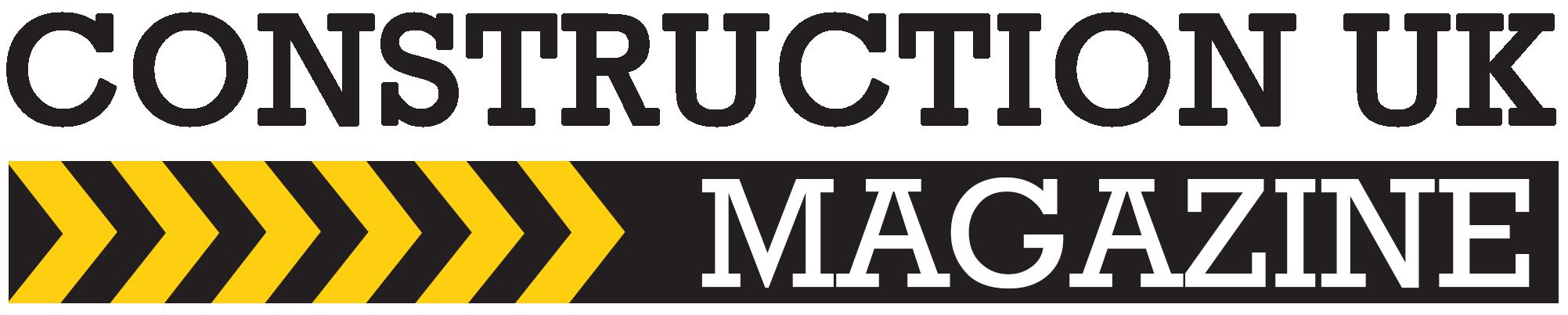
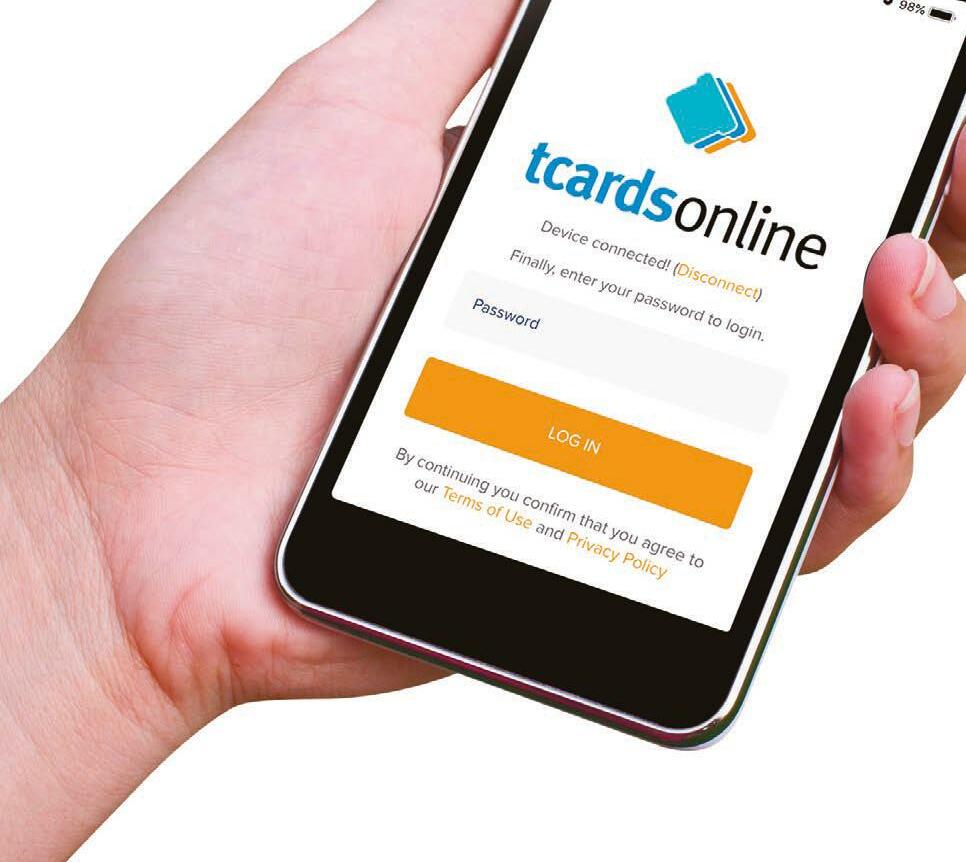

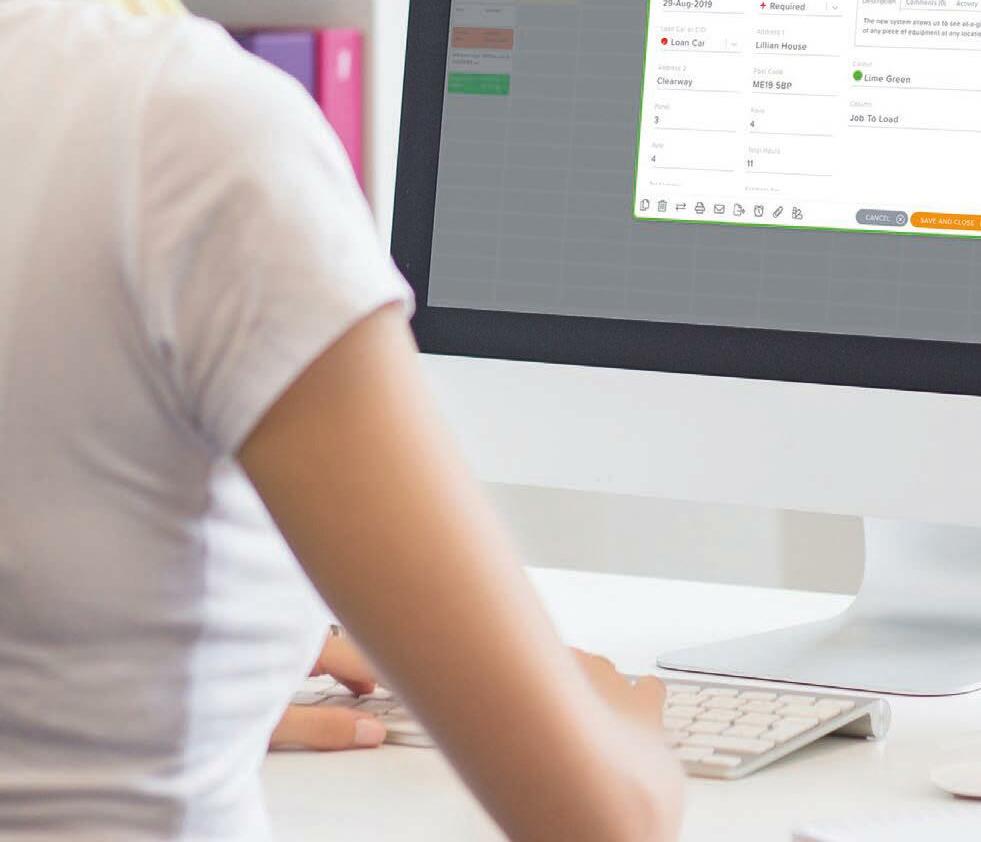
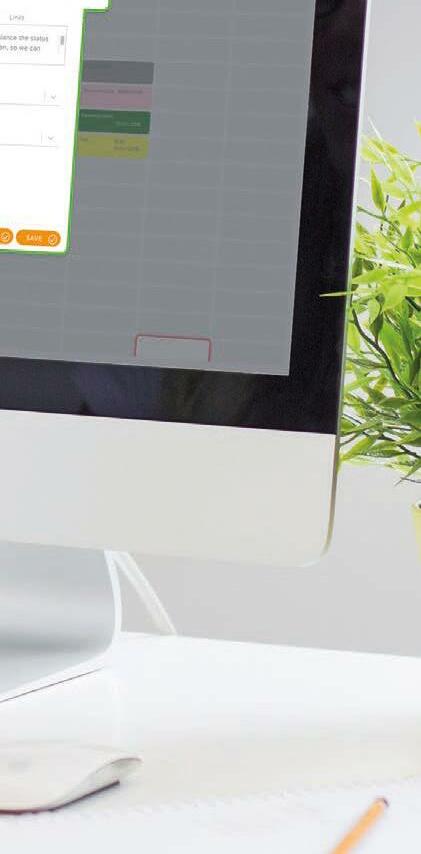
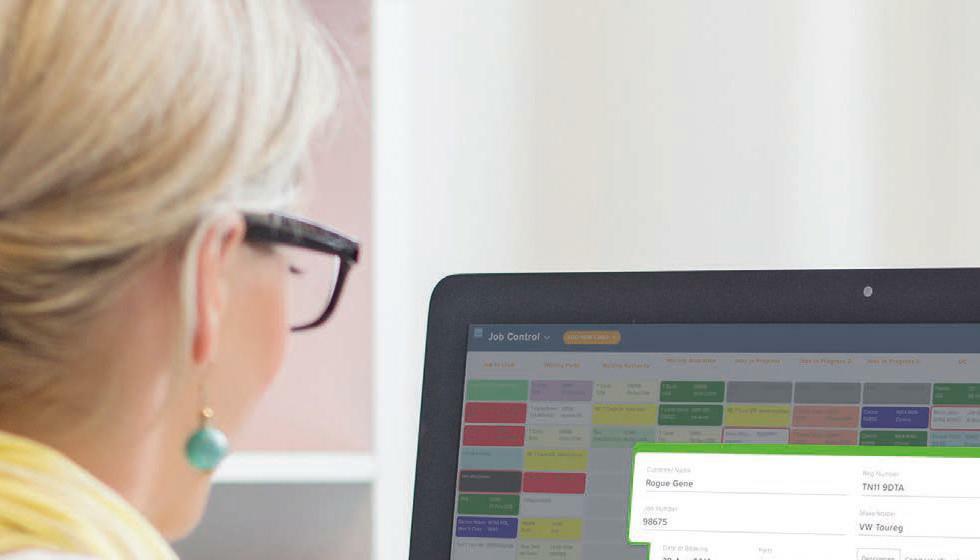



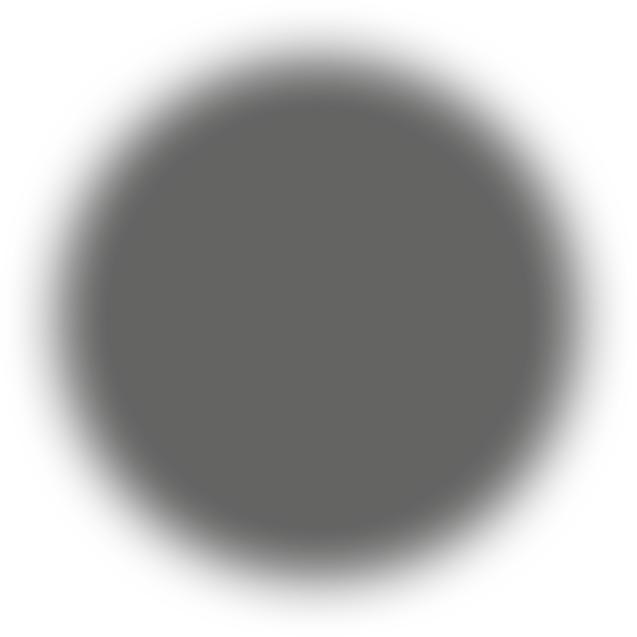

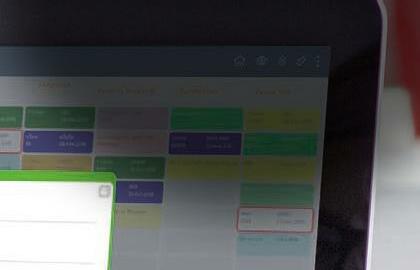
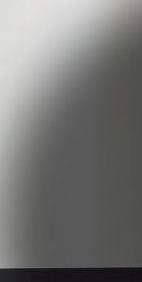
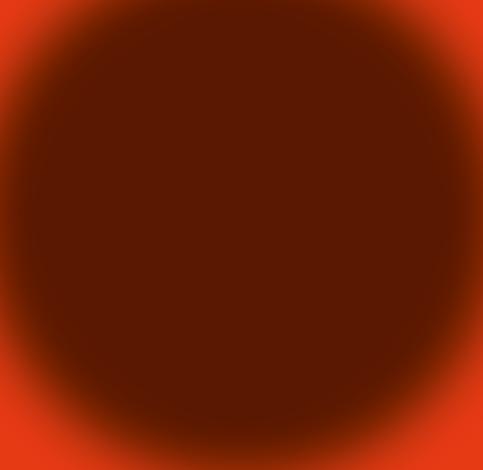
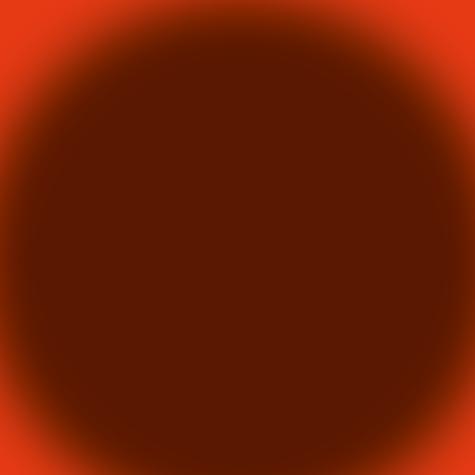
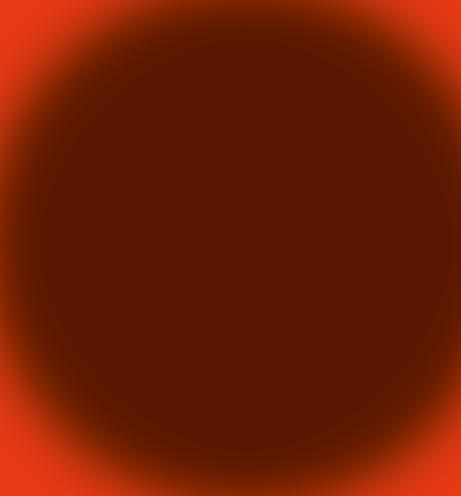
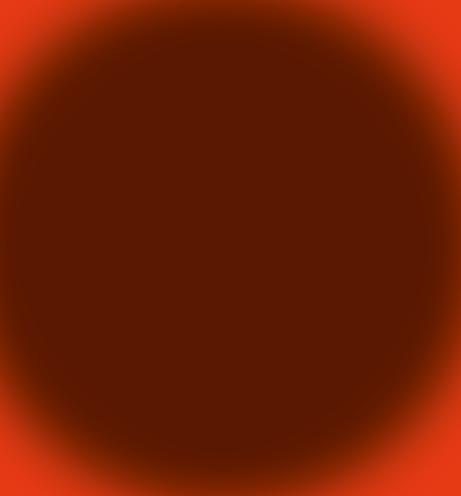
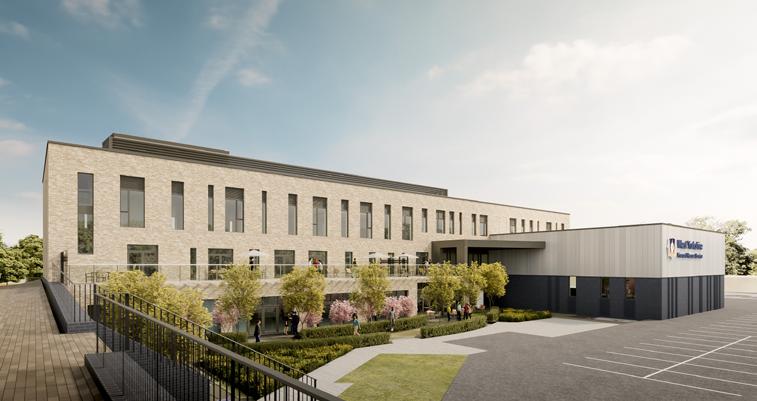
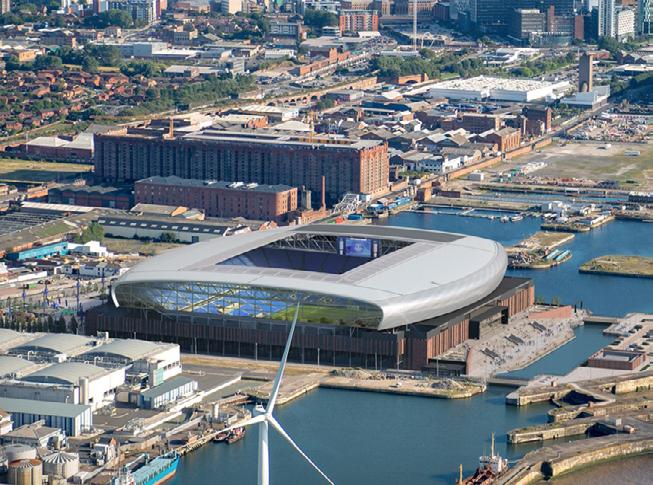
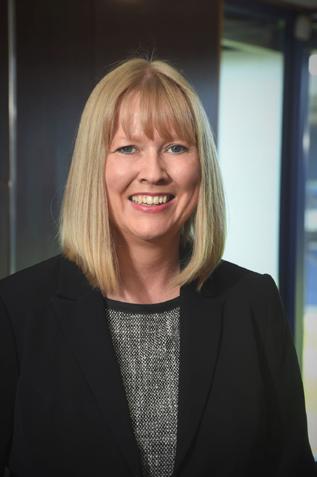
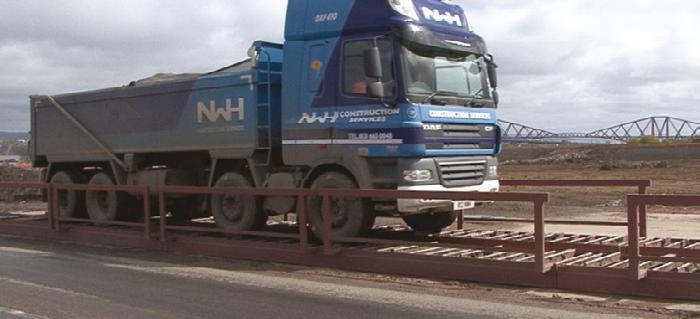

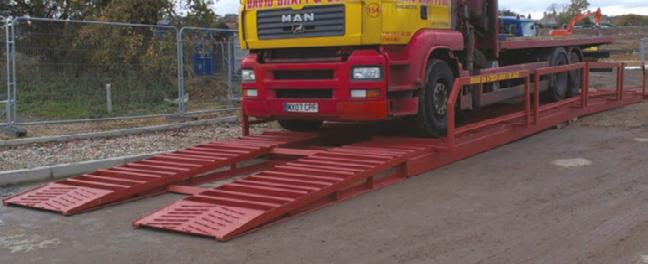

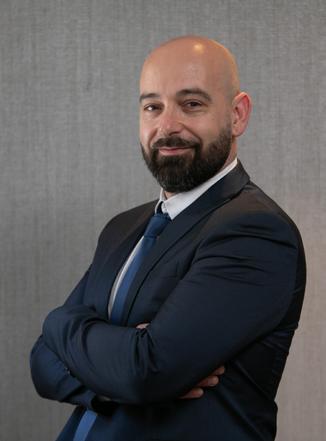
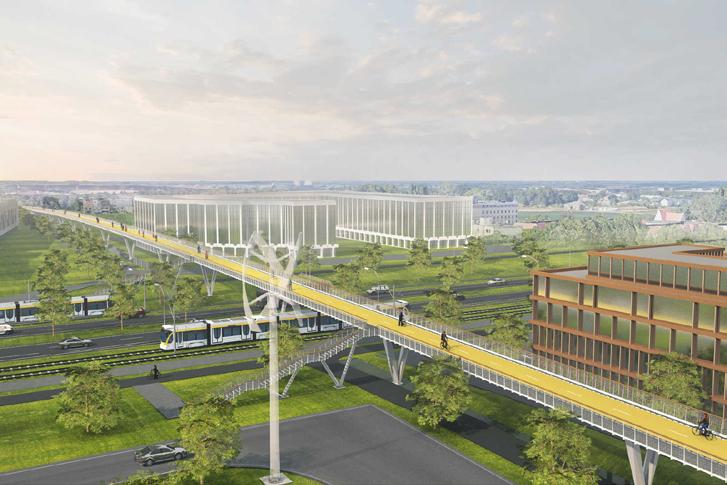
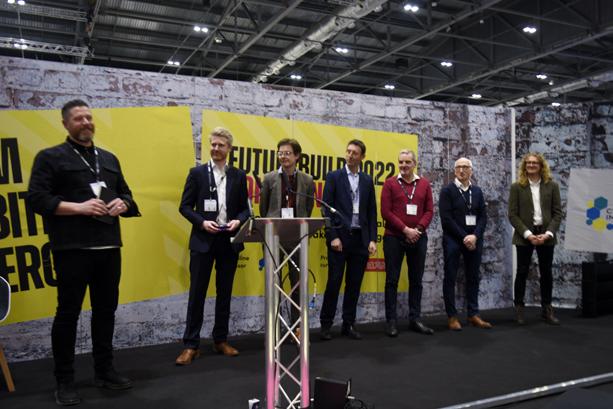
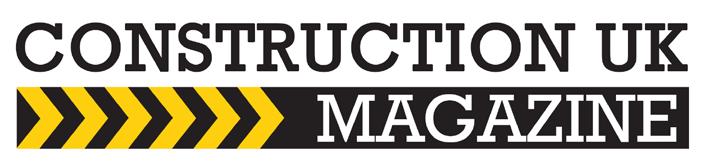
hyperTunnel, a British technology company innovating underground construction, and the University of Birmingham have signed a Memorandum of Understanding (MoU) to work together to progress completely new methods of underground construction, enlargement, monitoring and repair.
New automated construction methods being developed by hyperTunnel are designed to benefit the construction sector and society as a whole by reducing carbon footprint and building tunnels more than 10 times faster and at half the cost of conventional methods.
At the heart of the concept is the use of robots to 3D-print the shell of the underground structure, according to a digital twin. Using this method, the construction material is deployed directly into the ground.
Initially focusing on autonomous tunnelling technologies, imaging and digital simulations, the partnership between the two organisations is likely to include activities such as collaborative research, technology projects, joint publications, secondments, internships and education programmes.
Key to the MoU is the University of Birmingham’s National Buried Infrastructure Facility (NBIF), which is part
of the UK Collaboratorium for Research on Infrastructure and Cities (UKCRIC). UKCRIC is designed to stimulate research activities in the fields of infrastructure and cities through close collaboration between academia, industry and government.
NBIF is currently leading research into areas such as soil/structure interaction, digital twinning, tunnelling and quantumtechnology sensing.
hyperTunnel and the University of Birmingham will also engage in joint activities at the University’s new campus in Dubai, which includes the development of a multi-million pound Tunnelling Centre of Excellence.
“We’re really looking forward to diving into this collaboration,” said Nicole Metje, Professor of Infrastructure Monitoring at the University. “Joining forces with pioneering British organisations like hyperTunnel to expand our research and amplify our impact and theirs is exactly what we’re about. This partnership is a significant milestone for NBIF.”
“The University of Birmingham is one of the top 100 academic institutions in the world and NBIF is a world-class facility,” said hyperTunnel co-founder Jeremy Hammond.
“Both our organisations are deeply involved in radically innovating underground infrastructure and use of underground space. It’s really exciting to think about what we can achieve by combining our expertise like this.”
Funding needs to prioritise developing the skilled workforce to deliver a transformative green agenda
In response to John Swinney’s budget announcement of over £500M Net Zero initiatives, Fiona Hodgson, Chief Executive of the Scottish and Northern Ireland Plumbing Employers’ Federation (SNIPEF), said: “The government’s transformative Net Zero agenda is welcomed and supported by our sector; however, we urge greater priority is given to the skills development of the people needed
to realise these already challenging targets. It is critical that apprenticeship funding is focussed towards developing the essential skills of our next generation of plumbers and heat engineers, as well as upskilling the current workforce in areas such as heat pumps.
“By ensuring the people with the needed skills are recruited and developed today and in the future, the government can showcase to the world that the green economic model contained within their Net Zero ambitions is both viable and sustainable.”
Kier has launched a new digital apprenticeship, providing colleagues across the Group with vital data skills. This has launched in partnership with Multiverse, specialists at delivering data skills training.
The 13-month course will cover core technical skills required to transform data into insights and how to build narratives and present findings.
Apprentices will undertake on-the-job learning and benefit from one-to-one coaching with industry experts; they will also be supported by a thriving community with events, social and mentoring. Upon completion of the course, apprentices will gain a Level 3 qualification.
Louisa Finlay, client and markets director leading on Kier’s digital strategy, said: “We continue to see huge growth in the role of data across a lot of
areas in our lives. It’s important that we invest in our people and provide them with skills, a deeper knowledge and technical ability that will benefit them for years to come. Working with Multiverse has allowed us to offer a relevant and much-needed course to our people.”
Jeremy Duggan, president at Multiverse, said: “The ability to gather and interpret data is one of the most indemand skills in the workplace today, and apprenticeships are simply the best way to enable staff to develop those skills.
Kier’s Data Academy will not only offer employees world-class training with industry experts, but it will enable the company to improve its systems and outcomes with improved use of data.
The first nuclear reactor built for a British power station in more than 30-years is complete and ready for delivery to Hinkley Point C in Somerset.
The “reactor pressure vessel” is the high strength steel cylinder that contains the nuclear fuel and the chain reaction needed to make heat. The heat is used to create high pressure steam for the world’s largest turbines. Teams have spent 80,000 engineering hours on its construction.
At just 13m long and weighing in at 500 tonnes, each of two reactor pressure vessels at Hinkley Point C will help power around 3-million British homes. They are designed to run continuously for 18 months at a time between refuelling.
The reactor has been built by France by Framatome; the same nuclear engineering company which built Britain’s last nuclear reactor, at Sizewell B in 1991. Since it went into operation in 1995, that reactor has provided 247 TWH, which is enough to power every home in Britain for 2 and a half years.
The centre of the reactor will have an average temperature of around 300°C and can withstand five times more pressure than a submarine at normal operating depths.
The building which will house the reactor is also taking shape in Somerset. On Monday morning, Big Carl, the world’s largest crane, lifted the final 11.6-metre prefabricated steel ring into place on Unit One - which now stands 44m tall.
The completion of the first reactor pressure vessel marks a major milestone in the construction of Hinkley Point C. Together, the two nuclear reactors will offset 600-million tonnes of carbon dioxide emissions over its 60-year lifetime – driving Britain towards net zero and stronger energy security.
Eight colleges across the country have recently been named a Construction Hub by leading building products manufacturer Forterra, a scheme in alignment with Forterra’s mission to keep Britain building by plugging the existing skills gap.
The selected colleges are Buckinghamshire College Group, Burnley College, Hertford Regional College, Lewisham College, Preston College, Stamford College, Truro and Penwith College, and Warrington and Vale Royal College.
The colleges, all selected via a competitive application process, are looking forward to the extra support they can give their students.
Forterra’s Construction Hubs benefit from expert advice and support from leading figures in the construction industry who will share their industry knowledge through a series of site visits and talks
supporting the emerging talent from each college. The colleges will also enjoy a boost to their resources, with a donation of 12,000 bricks, branded merchandise and the opportunity for one exemplary student to receive £500 worth of tools.
The Construction Hubs are central to the company’s nationwide effort to inspire ambition and foster raw talent in the next generation of construction workers.
With the support of Forterra, the colleges are set to embark on brickwork projects including internal competitions and local community projects, with the aim of increasing the skills and enthusiasm of their students.
Stephen Harrison, Chief Executive of Forterra, said: “We are pleased to announce the eight colleges selected to join the London Brick Construction Hubs. We have been impressed by the high standard of applications received, and have every confidence that these colleges and their students will go on to produce brickwork of the highest quality. Forterra takes pride
in supporting the continued development of high standards and technical skills in the bricklaying industry with the view of bolstering future UK productivity.”
Forterra continues to support upcoming bricklaying talent in a variety of ways, including through the Forterra London Apprentice Challenge and annual Best in London Brick contest at Lewisham College which uses Forterra’s iconic London Brick.
For more information on Forterra’s Construction Hubs, visit https://www.forterra.co.uk/about-us/ community/construction-hubs/
The Home Builders Federation (HBF) has joined forces with Women into Construction to launch a nationwide employment programme for women, helping to address the gender imbalance in the construction workforce, which currently sees just 16% female representation.
Working closely with employers Barratt Developments, Bellway Homes, Cala Homes, The Hill Group, Keepmoat,
Persimmon Homes, Redrow, St. Modwen and Vistry Group, the project hopes to attract women into Site Management roles by offering a funded programme that will provide support with childcare and training costs to make the opportunity more accessible.
The employment programme will include:
• Site visits (central locations and online)
• A week of online insight and development sessions, including Q&As with Site Managers and employers, and employability and health and safety training
• Two-week work placement on site
• 1-2-1 coaching and support from Women into Construction
The work placements will take place at employer sites across England. They will offer participants first-hand experience of the Site Manager role and how they could help industry deliver much needed homes.
Women interested in this exciting opportunity are invited to register to attend an online information session at 11am on Tuesday 31 January 2023. At the event, they will learn more about the programme and meet the employers involved, including current Site Managers from across the country.
Women into Construction’s Business Development Director Jacqui Wordsworth says: “With women representing just 4% of Site Managers, we want to inspire and encourage more women to take up a career in home building – helping us and our employer partners to change the face of construction.”
Jenny Herdman, Director for HBF’s Home Building Skills Partnership, adds: “The home building industry is facing a significant skills shortage. If we are to build the new housing this country desperately needs, it is vital that we attract a broad range of entrants into the industry.
HBF is delighted to be working with Women into Construction to increase the number of female site managers in the industry and show that there are opportunities for people of all backgrounds and talents to develop a rewarding career in home building.
Visit the Women into Construction website to sign up and register for the online information session taking place on 31 January 2023.
Land Remediation Tax Relief is one of the best kept secrets in the UK construction and building industries.
It is available to recover costs of carrying out remediation work prior to receiving planning permission to render the land useable for new developments.
and Remediation Tax Relief is one of the best kept secrets in the UK construction and building industries.
has remained unused from the earlier of 1st April 1998 or date of acquisition can also form the basis of a claim, especially if it has suffered tipping and illegal waste disposal over the years.
Qualifying criteria are few. You must be a registered UK corporate entity and the owner of the land. You cannot claim if you own the land and caused the contamination. From this point most costs associated with the clean-up measures, disposal of waste and making good the finished projects form the basis for cost evaluation and submission of the claim.
It is available to recover costs of carrying out remediation work prior to receiving planning permission to render the land useable for new developments.
Known contaminated land can be claimed for. Derelict land that has remained unused from the earlier of 1st April 1998 or date of acquisition can also form the basis of a claim, especially if it has suffered tipping and illegal waste disposal over the years.
Since Land Remediation must be undertaken before any construction works begin, it is advised to consider remediation preparations early.
Since Land Remediation must be undertaken before any construction works begin, it is advised to consider remediation preparations early.
The definition of what is contaminated land is peculiar to land remediation relief legislation and is broader than for planning purposes as in Environmental Protection Act 1990. It is beneficial to know land remediation relief is available before purchase of land. This reduces possible uncertainty and risk.
Qualifying criteria are few. You must be a registered UK corporate entity and the owner of the land. You cannot claim if you own the land and caused the contamination. From this point most costs associated with the clean-up measures, disposal of waste and making good the finished projects form the basis for cost evaluation and submission of the claim.
All contributory costs should be identified and recorded. These are wide and include your own company costs of labour, management, subcontractors, suppliers, travel and subsistence costs, surveys, tests, disposal and replacement of soil and making good.
All contributory costs should be identified and recorded. These are wide and include your own company costs of labour, management, subcontractors, suppliers, travel and subsistence costs, surveys, tests, disposal and replacement of soil and making good.
Known contaminated land can be claimed for. Derelict land that
Generally, brown field sites and land that has existing buildings will be contaminated, especially where older buildings
Generally, brown field sites and land that has existing buildings will be contaminated, especially where older buildings are suspected of containing asbestos in any form. Used land can contain old foundations, utility services, hydrocarbon and chemicals whatever. If remediation surveys discover radon gas emissions, Japanese
Knotweed and any other invasive plant species and contaminants deposited through earlier occupier activities, these too can be included in remediation costs. Where buildings contain asbestos, costs of removal and either demolition or insitu encapsulation and sealing of the asbestos elements is a claimable cost.
The definition of what is contaminated land is peculiar to land remediation relief legislation and is broader than for planning purposes as in Environmental Protection Act 1990. It is beneficial to know land remediation relief is available before purchase of land. This reduces possible uncertainty and risk.
are suspected of containing asbestos in any form. Used land can contain old foundations, utility services, hydrocarbon and chemicals whatever. If remediation surveys discover radon gas emissions, Japanese Knotweed and any other invasive plant species and contaminants deposited through earlier occupier activities, these too can be included in remediation costs. Where buildings contain asbestos, costs of removal and either demolition or insitu encapsulation and sealing of the asbestos elements is a claimable cost.
MCS Corporate urges its clients to consider all possible sites for development and planning. We can give early assurance of a likely claim and work with you to identify, prepare and submit claims as the remediation proceeds.
MCS Corporate urges its clients to consider all possible sites for development and planning. We can give early assurance of a likely claim and work with you to identify, prepare and submit claims as the remediation proceeds.
Contact T: +44 (0)1926 512475 E: charlotte@mcs-corporate.com W: www.mcs-corporate.com
Contact
T: +44 (0)1926 512475 E: charlotte@mcs-corporate.com W: www.mcs-corporate.com
To qualify for Land Remediation Tax Relief your company must have incurred costs on cleaning up land or buildings considered to be in a contaminated state. The scope of costs allowed is generous.
You must be registered as a limited company in the UK and be the owner of the land or building at the time of the remediation work. In addition, the land or building must be owned either as a freehold or longer-term leasehold.
Common examples of qualifying contamination:
• Asbestos
• Ground and landfill gases
• Japanese Knotweed
• Sulphate contamination in soil and concrete
• Arsenic
• Removal of redundant utility services and concrete foundations
Qualifying costs can include surveys, excavations, soil and groundwater treatments, staff costs, materials and subcontractor costs. Claims can be made for categories of derelict land. This can be advised with relevance to time periods when land could be considered for derelict status.
Regardless of the industry you operate within, if you’ve acquired land or buildings in a contaminated or derelict state for intended commercial use, you could claim.
“Go and put another jumper on” something I heard as a child; but is it something this generation will hear?
We all deserve the right to be warm; building regulations even focus on having suitable heating systems in dwellings to meet a reasonable standard, but can we afford to run these systems now and how can we be sure they operate as efficiently as possible?
How can we reduce energy costs in our homes whilst still living in a comfortably?
The recent energy cost increases are going to impact everyone across the UK, and the only real way to reduce this cost is to reduce how much energy we use.
Different building types have different options available to make them more efficient, with some being relatively easy and others being more challenging.
The first approach to efficiency should always be focussed on the building fabric,
where we look at the current building and evaluate where we may be losing heat and what we can do to reduce that loss.
Some of the easy solutions include introducing insulation to loft or cavity wall. Having the loft insulated will reduce heat loss through the ceilings of the building and stop the cold temperatures striking down, the loft space is usually a ventilated area, which makes it naturally cool, especially in winter, but of course we don’t all have loft spaces.
Cavity wall insulation is a method used to fill the void between the internal wall and the external wall of a building. This cavity can be filled with insulation that will reduce the loss of heat from inside the building and reduce the cold from outside.
New buildings are built with cavity insulation, a method that has been applied for a number of years. If, however, you occupy an older building, it’s highly likely there is not even a cavity.
There are also buildings that are classed as ‘non-traditional’, maybe a prefabricated structure, meaning it was built in pre-made or pre-cast concrete sections, or of poured concrete rather than the traditional bricks and mortar that can prove more challenging to treat Here, options such as internal wall insulation (IWI) of external wall insulation (EWI) might be appropriate, though there are limitations to these techniques and expert advice must be sought before proceeding.
Draught exclusion also needs to be considered. Many homes are not wind or watertight, so addressing some of these basic issues will be beneficial for the efficiency of the building.
From a plumbing and heating perspective we need to look at the way we heat our buildings and how we use the systems that generate the heat.
One of the simple ‘quick wins’ includes insulating our plumbing systems though
accessing the pipework may prove challenging and impractical. If you have any pipework in easy to access unheated voids such as under timber floors and in roof spaces that are not insulated this would be a way to reduce the heat loss in the pipework. This means more heat reaches the radiators; so, rooms will heat quicker and reduce the demand on heating appliances.
Suitable controls are essential for optimum efficiency regarding heating systems. Checking to see what your existing heating controls are set at is simple. Look at the times you have set, and if the heating and hot water are operating at times when the building is not being used, make the required changes. Turning heating thermostats down a degree or two may help.
Modern heating systems are required to have suitable controls to ensure optimum efficiency. For example, a new boiler and heating system or a boiler upgrade is required to have independent time and temperature control for both the hot water and the central heating.
The use of thermostatic radiator valves (TRVs) also allows more localised control in rooms. TRVs are radiator valves that
operate to the temperature in the area they are located, if the area reaches the set temperature it effectively shuts down the radiator, if the area cools, then the TRV will open the valve to allow heat into the radiator.
Modern heating systems are required to have suitable controls to ensure optimum efficiency. For example, a new boiler and heating system or a boiler upgrade is required to have independent time and temperature control for both the hot water and the central heating.
There are a range of control types from easy to operate systems to more complex control systems that incorporate smart devices, such as voice-controlled hubs that use wireless technology. The more complex systems can also use geo fencing, which can determine how far away from home you are and only allow the heating to turn on once you are within a certain distance.
Hot water storage is another area. If you have an airing cupboard with a hot water vessel, you can check the thermostat
attached to the vessel. Hot water thermostats are usually set at 60 degrees Celsius. You may be tempted to lower the thermostat, but this can have major safety issues. The water in the vessel must be heated to 60-degrees Celsius to pasteurise the water and kill off any harmful bacteria such as Legionella.
Another option could be to upgrade the heating system and the appliances, things like a new boiler, radiators, and controls.
There are also renewable energy solutions, for example, solar thermal hot water. This is the use of a solar panel to heat some or all your domestic water. You could also consider a heat pump, that uses energy from the ground or air to heat the home. You need to consider and assess whether this would actually reduce your energy costs as heat pumps use electricity to operate.
Take the advice of a SNIPEF member who provides heating services on any of the topics mentioned above. There is also impartial energy efficiency advice provided through Home Energy Scotland which may direct you to government support including loans and grants to improve the energy efficiency in your building.
With an increase in the built urban environment over the UK and plans to build 300,000 new homes every year, the permeable land across the country is diminishing, meaning surface runoff water is overwhelming drainage pipes. What, if anything, can new homes and commercial property developers, local authorities, and planners be putting in place to alleviate the strain? Here Raj Somal, Director at the sustainable engineering consultancy, Dice, explores why the UK needs to invest in SuDS.
Over the last six years there has been considerable investment in protecting property from the risk of flooding. Government investment between 2015 - 2021 of £2.6 billion has seen over 314,000 homes become better protected with more than 850 new flood and coastal erosion defence projects completed.
It’s suggested that this work is estimated to have reduced national flood risk by five percent.
But for homeowners living in at risk areas, does this offer enough reassurance that the issue of flooding is being taken as seriously as it should? And is investing in SuDS, Sustainable Drainage Systems, the way we should be going?
SuDS mimic natural water systems and are an efficient way to manage surface water drainage.
Here at Dice, we’re committed to the UK investment in SuDS.
SuDS are designed with four key components in mind - water quality, water quantity, amenity, and biodiversity. By designing SuDS which follow these four pillars, they will effectively be used to control, absorb, and treat surface runoff.
They are specifically designed to not cause an eyesore to the area, and are integrated through strategic development and planning into the local landscape.
SuDS can be underground and overground, but it’s those on the surface which provide the most opportunity and benefits for treating surface runoff within the built environment.
Implementing SuDS into the UK’s built environment will allow us to truly make the most of surface water run-off which would otherwise be wasted.
SuDS offer great advantages to the local landscape, vegetation, and wildlife, whilst also helping to reduce the impact of ever growing concerns of flooding.
There are several different types of SuDS which are slowly being implemented across the UK, for both larger and smaller scale projects. For example, detention basins are storage basins covered in vegetation
to capture and store run-off which is then slowly discharged via a restricted outfall, reducing the impact on drainage features downstream.
On a smaller scale, swales are shallow, flat bottomed, vegetated open channels designed to convey, treat, and often attenuate surface water runoff.
But why do these urban drainage systems need to be as sustainable as possible? We recognise the importance of protecting our natural environment, and it is becoming increasingly obvious that the UK must protect its existing resources.
One of which is water. Implementing SuDS into the UK’s built environment will allow us to truly make the most of surface water run-off which would otherwise be wasted. SuDS offer great advantages to the local landscape, vegetation, and wildlife, whilst also helping to reduce the impact of ever growing concerns of flooding.
SuDS can provide better quality spaces to the newly built environment whilst simultaneously being advantageous for the climate and biodiversity of the UK by managing, absorbing and controlling water surface run-off.
Somal RajWater conservation is the key to reducing energy bills. Heating water accounts for nearly 1/5th of energy use in UK homes.
Reducing hot water demand is an effective way to help occupants conserve energy and reduce bills. Some uses are fixed, e.g. the washing machine or dishwasher, here education about full loads and eco settings can have an impact. However, many are not.
Showers account for a quarter of UK domestic water usage.
To reduce this hot water usage there are three options:
• Cold showers, not ideal on a cold winter morning
• Shorter showers, using egg timers or a ‘favourite song’ to cut shower time
• Flow reduction, less water is used while the shower is running.
The first two options require active engagement by all members of the household. The last is a fit and forget method of permanently reducing water use.
‘Eco’ or water saving shower heads are designed to restrict the water flow to a single outlet. They are highly effective but retrofits like these come at a price, especially larger properties with multiple bathrooms. They also do nothing for running taps, whether they’re in the bathroom or kitchen.
A second 1/5th of water usage is the taps in the house, e.g. rinsing the coffee cup, or washing hands. Again, flow restrictors can be fitted to each of these outlets.
For households on an increasingly tight budget, or developers trying to minimise costs, multiple fittings for each tap or shower might not be an investment they are able to make.
Household flow restriction for just £20 per property.
The alternative is whole site flow reduction. Fitting a device such as Groundbreaker’s NRv2 LoFlo, at the meter regulates the level of flow entering customer premises – regardless of network pressure. As the flow of water into the premises is limited, then the amount used in ‘time controlled’ activities is also limited – but without providing a degradation of service. More importantly not requiring any intervention or behavioural change on the part of the customer, so leading to ‘natural’ reduction in consumption.
Showers account for a quarter of UK domestic water usage.
Fitting a device such as Groundbreaker’s NRv2 LoFlo, at the meter regulates the level of flow entering customer premises – regardless of network pressure.
Our water companies are regulated to provide a minimum level of water supply, but in many areas, due to network structure and gravity fed systems, supply is much greater. Households in high pressure areas could be receiving up to three times the required minimum levels. So, run a hose for five minutes at the bottom of the hill, and your lawn will be greener that the gardener that does the same at the top. ‘Time controlled’ uses could be reduced if all households received the same acceptable, ‘standardised’ supply.
Independent research carried out by WRc, showed a theoretical reduction of 2-4% of typical water usage when devices such as LoFlo are installed. However, recent field trials by a major UK water company have showing savings of 5%.
As part of UK Net Zero Carbon targets water companies have been targeted to reduce the water householders are using, Per Capita Consumption (PCC). PCC reduction targets average just under 6% in the UK, so utilising property flow restriction could achieve just 1% off the average PPC reduction targets! However, water companies are also tied to customer performance commitment levels (C-Mex), and some seem to be concerned that a reduction in the supply levels to properties will prompt customer complaints, offsetting the financial rewards of achieving PCC targets.
Field trials of devices such as LoFlo, have shown that most customers are not aware of supply levels in their property,
Contact Groundbreaker Systems
T: 01379 741993 E: sales@groundbreaker.co.uk
groundbreaker.co.uk/products/nrv2/
within certain limits. Especially when moving into a new property, customers accept the levels as ‘being what it is’ and fears of an increase in customer complaints impacting C-Mex values are overrated. In recent trials in England, where occupants did notice the change in supply, it was the positive impact of reduced flow that was cited, e.g. reduced splashing at the kitchen sink.
Not a single occupant wanted the LoFLo to be removed after the trial period.
The NRv2 LoFlo can be easily and simply retrofitted to any meter installation, or meter exchange when upgrading or remediating underground meter chambers. Thus, allowing Water Companies to manage demand, with little or no impact on consumers, at the minimal cost of approximately £20 per household.
The NRv2 LoFlo can be easily and simply retrofitted to any meter installation, or meter exchange when upgrading or remediating underground meter chambers.
As the LoFlo is fitted at the water meter, it is the water companies fitting. Therefore, developers must be proactive in challenging water companies to provide a standardised supply to help UK housing stock to achieve water consumption targets.
No other UK product for concreteto-steel applications satisfies the necessary load-bearing requirements, or meets the current and future thermal performance required by building standards (Part L), than the Schöck Isokorb structural thermal break T type SK. It is a complete system structural thermal break and is used widely on Block B, a collection of nine buildings which make up around a third of the 1400 hundred or so new properties at the Hayes Village development. This is an extensive regeneration programme in Hayes, West London and is built on the original site of the locally iconic Nestlé Factory, which dominated the area for some 80 years before production relocated to Derbyshire. Hayes Village is situated along the Grand Union Canal, surrounded by nine acres of green space and includes play areas and allotments. Original features from the Nestlé factory, including one of the listed art deco style buildings, are carefully woven into the fabric of the new development and although all the buildings have distinct
characteristics, the existing factory buildings have inspired the overall design. As a result, the nine buildings that make up Block B are broken up into a series of elements and layers, each of a different brick tone and although very different in character, have façades with common themes. As a counterpoint to the solid masonry walls which wrap the primary steel frame, the metalwork of the balconies is used as a feature to enrich the façades.
The Schöck Isokorb range of structural thermal break solutions is the largest in Europe and in the UK helps projects meet full compliance with the necessary Building Regulations (and the impending Future Homes Standard criteria where relevant).
The entire project is built with sustainability in mind and minimising any risk of thermal bridging at the balcony detailing is critical for a number of reasons. Local heat loss will result in more energy being required to maintain the internal temperature of the building, while low internal surface temperatures in the area of any thermal bridge can cause condensation. This in turn is likely to result in structural integrity problems. Mould growth too is a possible risk, which in a residential situation can cause asthma and allergies.
Incorporating the Schöck Isokorb T type SK minimises any chance of these outcomes, as it prevents the risk of thermal bridging between cantilevered steel constructions on reinforced concrete components.
A dependable and fully compliant product range
The Schöck Isokorb range of structural thermal break solutions is the largest in Europe and in the UK helps projects meet full compliance with the necessary Building Regulations (and the impending Future Homes Standard criteria where relevant). In addition to the Isokorb type used on this project, there are also solutions for concrete-to-concrete, steelto-steel, renovation projects – and even a maintenance free alternative to wrapped parapets. All products have the security of independent BBA Certification, which provides NHBC approval. The temperature factor requirement (fRSI) used to indicate condensation risk at localised junctions, which must be equal to, or greater than 0.75 for residential buildings, is also easily met by incorporating the Isokorb.
Contact Schöck on 01865 290 890; or visit the website at www.schoeck.com for full details of the Isokorb range
While recent decades have seen
transformed from a near derelict munitions factory to become one of south London’s most iconic redevelopments, restoration and repurposing work continue apace, with a recently completed contract involving steel window specialist, ASWS, highlighting both the challenges and the opportunities the complexity of the buildings can present.
Aside from converted and new-build residential properties, the huge site has also seen numerous businesses and social enterprises established, including Woolwich Works, a creative quarter for the arts which includes spaces such as The Firework Factory, The Laboratory and The Cartridge Factory. ASWS has undertaken a number of contracts within the borough, leading to the local conservation officer recommending the company to Mace Interiors, which was awarded the contract to completely refit five separate buildings, with Bennetts Associates being the architectural practice leading the design work.
For more information on ASWS, please visit asws.co.uk
Chore Max S5 - is the ultimate S5-Certified safety boot which features an outsole designed for slip-resistance, and using compounds that are oil and abrasion resistant, the platform extends with uppers built for the toughest jobs.
For additional protection, this S5-Certified safety boot has anti-penetration midsole, heat resistant outsole, steel toe cap, extended rubber overlay, triple toe and quadruple rubber heel reinforcement. Waterproof construction keeps feet dry, and 3D breathable mesh lining increases airflow to keep you cool, with NzymeTM antimicrobial treatment for odour control.
The Chore Max is a reliable work boot with its rugged and dependable design; perfect for construction and industrial workers. The Chore Max S5 launched last year and is available in three colourways.
Stockists: https://muckbootcompany.co.uk
Willmott Dixon has been appointed for its latest scheme for the emergency services, a transformational headquarters, training centre and new fire station for West Yorkshire Fire and Rescue Service (WYFRS).
Procured via the SCAPE framework, the company has moved onto a site in Birkenshaw, south east of Bradford, to demolish the existing buildings which will make way for the urban search and rescue training centre that will take firefighter learning into the 21st century when open in 2024.
The project forms part of wider modernisation plans for West Yorkshire fire stations, which will enable the service to deliver its vision to keep West Yorkshire people and communities safe. The old headquarters – currently based in the on-site Grade II listed Oakroyd Hallwill be sold once the new build is complete.
Less than half of the overall spend is for the headquarters building, with the rest divided between the training centre, new fire station and to ensure the site is net zero in terms of its carbon footprint.
The green site will generate 50,000kWh of sustainable energy per year through solar panels and will reduce carbon consumption through heat pumps, hybrid ventilation and efficient building materials.
As part of its commitment to the local economy, Willmott Dixon has already created local jobs and training opportunities at the site and is on track to start building the new three-storey complex early next year.
Other recent Willmott Dixon projects for the emergency services include Dorset Police Headquarters, a flagship new headquarters for West Yorkshire Police in the Kirklees district, Nottinghamshire Police Custody Suite, South Wales Police - Police Learning Centre and West Sussex fire service training centre and fire station.
Fairhive Homes’ first ever new-build independent living housing scheme was unveiled this week – setting the standard for independent living in Buckinghamshire.
Located in the beautiful village of Waddesdon and backing onto open countryside, the Anstey Court development comprises 16 flats for residents aged 60 and over, designed and specified for independent living for older residents.
Fairhive is offering priority to applicants who are down-sizing from a larger property and the benefits of living at Anstey Court include the high environmental standards to which the
properties are built, with all flats heated by air-source heat pumps, one of the most energy efficient ways of heating homes.
Anstey Court is just a part of Fairhive’s growth and diversification strategy. In the short term, they aim to deliver almost 1,000 new homes within a 30 mile radius of Aylesbury for those in housing need as part of its 2020 to 2025 programme.
With the environment in mind and in consideration of increasing energy prices, Fairhive pledges to act responsibly to maximise the energy efficiency of its new homes. All new homes provided by Fairhive will aim to achieve an EPC B (Energy Performance Certificate) rating or higher.
The project has been developed through a partnership between Fairhive, Buckinghamshire Council and Homes England. Fairhive received grants of £1.2 million from Homes England and £160,000 from Buckinghamshire Council towards the building of Anstey Court. The partnership also extends to Thame and District Housing Association whose independent living scheme adjoins Anstey Court, and with whom Fairhive have worked to deliver an extended complex of homes for older people in this location.
Milestone Infrastructure, a part of M Group Services’ Transport Division, has been awarded the first part of the third and final phase of the A382 corridor improvements project in Devon providing early contractor involvement (ECI) to support the final design stages.
The final stage of the A382 and Jetty Marsh project involves constructing 3km of new carriageway as well as aligning and improving the existing road.
In addition, the project will enhance cycling and pedestrian facilities around the town of Newton Abbot including building a new footbridge at Forches Cross.
ECI allows the project team to collaborate with the client, Devon County Council, over a period of nine months to design and develop the project ahead of its delivery.
As a result of this partnership, the project team recently attended the Association of Directors of Environment, Economy, Planning & Transport’s (ADEPT) Dragons’ Den presentations for the Live Labs programme. The A382 project is one of 10, narrowed down from 30, invited to attend the Dragons’ Den stage. The project team is waiting to hear the outcome.
Live Labs 2: Decarbonising Local Roads in the UK is a three year, UK-wide, £30 million programme funded by the Department for Transport (DfT). Focused on innovative decarbonisation proposals from local highways authority led ventures, the panel is looking to offer funding to forward thinking projects.
Milestone Infrastructure is drawing on its extensive experience in identifying carbon reduction initiatives to enable the project
Construction sites are often fraught with delays, supply chain incidents, skilled labour shortages, difficulty in procuring raw materials, and breakdown of machinery causing a dip in productivity and profits.
To deliver your construction projects on time and within budget download Site Productivity – a new construction management software. It is a suite of mobile and desktop apps which includes :
• Site Diary – to record and track all field activities
• Site Task – to schedule, assign and monitor tasks
• Site Supervision – to resolve defects and create checklists
to be as sustainable as possible. With the additional funding, the team intends to use innovation to make the project carbon negative.
Throughout the project, Milestone Infrastructure will be working with local suppliers.
The project is adjacent to sites of special scientific interest (SSSI) and the team will be avoiding disruption to these areas and working with stakeholders to make sure the correct procedures are in place to protect these areas of conservation.
Upgrades to the A382 are due to commence in spring 2024.
The A382 corridor improvements project is upgrading local highways to cope with the increased traffic that is anticipated as a result of developments planned in the area.
Site Productivity is a construction management software suite that gives you complete control of your construction projects! Read our success stories. And get a free trial
The UK’s largest container firm is diversifying into the hire and modular markets.
Teesside’s Cleveland Containers has launched the Cleveland Group, encompassing the container arm along with new divisions Cleveland Hire and Cleveland Modular, allowing it to offer a full turn-key service.
CEO Johnathan Bulmer said: “By responding to the needs of our customers, we have seized the opportunity to expand into these markets.”
Meanwhile, Jon Hurford has joined as chief financial officer, Richard Tredwin as non-executive chair and former Mobile Mini managing director Andrew Thompson joins as chief operating officer.
For more information, visit Shipping Containers for Sale & Hire UK | Cleveland Containers
The search is on for the newest and brightest solutions to an array of built environment challenges. The Big Innovation Pitch will be back in action at Futurebuild 2023 and is where the industry’s most exciting innovators will battle it out to showcase their latest game-changing innovations and revolutionary ideas in front of a live audience.
Futurebuild’s annual innovation competition will provide the stage for the very best industry innovations. An exclusive platform for exhibitors, The Big Innovation Pitch will give them the opportunity to submit their innovation for consideration, with all entries then being shortlisted by a panel of expert judges, led by Dr Oliver Jones, Research and Innovation Director at Ryder Architecture.
A shortlist of six innovations will then be pitched live in front of the industry’s top architects, housebuilders and investors at Futurebuild 2023, before one is crowned champion.
This year’s event has a new and added live session with The Big Ideas Pitch being a motivator for any start-ups and SMEs out there who would like to pitch their new innovation to a wider audience. Run in partnership with the Department for Business, Energy and Industrial Strategy (BEIS), the Big Ideas Pitch is a fantastic chance for new businesses to show how their game-changing innovation can potentially disrupt the built environment.
To enter, the innovations across the Big Innovation Pitch and Big Ideas Pitch are about solving real problems and addressing the net zero challenge. Entrants can submit a product or service that can potentially shift behaviours and help solve net zero, either by supporting the circular economy, reducing emissions or providing new ways to improve how we design and build. These solutions will not only have an impact on our built environment but also on our planet.
Commenting on the Big Innovation Pitch, Martin Hurn, Event Director at Futurebuild said: “Our industry relies on innovation and faced with the challenges of net zero, companies that innovate will always stay ahead of the curve. At Futurebuild, this innovation is part of our ethos which is why the Big Innovation Pitch is such a great platform to highlight these innovations. We are also delighted this year to be able to open up the field even further with startups and SMEs being able to bring their breakthrough ideas to a wider audience through the Big Ideas Pitch.
There is wealth of talent across the UK and finding solutions that have the potential to meet wider industry issues is truly amazing, and we are excited to see the companies present their ideas in front of a live audience and get the attention they deserve.
Last year’s hotly contested live final saw Sunamp win the Big Innovation Pitch with their product Thermino Thermal Storage Battery for Domestic Hot Water. It uses food-grade phase change materials for more efficient heat storage, delivering instant hot water while reducing carbon emissions. While the battery is up to four times smaller than an equivalent hot water cylinder, the battery has an energy density around five time greater than water.
As a result of the win, Toby Morris, specification sales manager at Sunamp said: “Winning helped increase our profile at the event and beyond, raised brand awareness and started conversations.
“Sales of Thermino units are strong and are moving into the mainstream. They are now being installed in large scale housing projects across the country and international sales are rising. Our recommendation to other innovators is to go for it and enter, why shouldn’t you?”
All entrants to the Big Innovation Pitch will be featured in the Futurebuild Innovation Gallery and showcased to the top judging panel, as well as over 2.8 million industry professionals via Futurebuild’s extensive marketing and PR campaign.
The closing date for entries is 19th December 2022, with twelve entries selected to supply additional information prior to six finalists that will be announced on 23rd January 2023. The finalists will then pitch live at Futurebuild 2023 on Wednesday 8th March, with one being crowned champion.
Find out more about the Big Innovation Pitch and register today
Futurebuild 2023 will take place from March 7th to March 9th London’s ExCeL.
To exhibit click here
Described as “one of the most exciting vibration control products to emerge in the last 20 years” by leading global scientific and engineering consulting firm, Thornton Tomasetti, CALM®FLOOR makes its debut at Futurebuild 2023 and is not to be missed.
CALMFLOOR is the first ever widely available Active Mass Damping (AMD) solution for controlling floor vibrations and it’s meeting the low-carbon/leandesign construction challenge head on. It’s also radically transforming the lives of occupants by consigning excessive floor vibration to history and, with it, the need
for disruptive, costly, time-consuming and carbon-heavy alternatives such as structural modifications or passive tuned mass dampers.
Developed by the UK-based, worldrenowned experts in pioneering active vibration control in construction, CALMFLOOR is a game-changing lowcost, low mass, low-carbon and highly sustainable solution that can be installed in just hours. Remarkably compact at just 67kg, CALMFLOOR is flexible and robust, and delivers long-term reliability and highly effective vibration control – directly to the exact floor areas that need it.
CALMFLOOR is perfectly suited to open-plan and long-span floor structures, but setting opportunities are literally endless. CALMFLOOR will reduce floor vibration everywhere from airport concourses and shopping malls to open plan offices.
This includes all converted, repurposed and retrofitted spaces in need of low vibration –meeting even standard laboratory vibration requirements with ease.
A revolutionary answer to postoccupancy vibration serviceability crises, CALMFLOOR delivers crucial cost, materials and time savings for newbuild construction and serves as a powerful contributor to Net Zero ambitions.
It can replace the steel and concrete that’s traditionally used to control floor vibrations. CALMFLOOR also boosts the carbon-sequestration qualities of timber construction by addressing the challenges of its low mass and stiffness.
Visit Stand F28 to discover CALMFLOOR and talk to the team about game-changing floor vibration control. Visit calmfloor.com, email enquiries@calmfloor.com or call 0330 133 3801 for more information.
JACKON by BEWI will be at Futurebuild this year and will be promoting its ICF building systems. These are ready for the rigorous new u-value targets for new-builds, when these come into effect in 2025 as part of the Future Homes Standard.
JACKON’s THERMOMUR® ICF and JACKODUR® ATLAS ranges already meet or exceed the new targets for thermal insulation. The THERMOMUR® 350 Super range - currently the company’s best-selling range in the UK - already achieves 0.15 for walls with no added materials, and the JACKODUR® ATLAS insulated raft system can be designed to achieve 0.11.
Visitors to the company’s stand at the Show will be able to find out more about the benefits that JACKON by BEWI’s 60 years’ expertise in XPS and EPS manufacturing can bring to construction projects. JACKON by BEWI building systems make a positive contribution to the construction of highly energy-efficient buildings due to very low energy inputs required for heating or cooling.
More information on JACKON by BEWI’s products is available on the company’s website at www.jackon.co.uk
“Edition 10” and the new product groupings of Green, Blue, SmartSpace and Air.
The design provides a user-friendly and informative experience for all, including Specifiers, Developers, Civil Engineers, Urban Planners, and Contractors.
In conjunction with celebrating 30 years as the world’s leading supplier of Urban Greening Products, GreenBlue Urban are thrilled to announce the launch of its brand-new website!
As GreenBlue Urban expand and innovate as does their industry collateral.
The website encompasses the new branding as seen in the recently launched
Key features of the website include “How we work with you” designed to give a better understanding of services and how they can help no matter what stage the project is at.
The “My Account” area enables improved access to all “Resources” along with detailed product information, enhanced case studies and testimonials from satisfied customers.
GreenBlue Urban are the leading solutions provider in tackling the effects of climate change with a wealth of experience in mitigation measures, they are enabling heathier urban spaces in harmony with nature.
Discover more at www.greenblue.com Tel: 01580 803800
Hello@greenblue.com @GreenBlue.com
Futurebuild provides the stage for inspiring ideas, innovative solutions & knowledge sharing to drive sustainable construction and help us reach our goal of net zero. The exhibition brings together the entire supply chain to showcase, debate and understand the advancements in sustainable construction and the emerging technologies that will make net zero possible.
Futurebuild is taking a stand for a better built environment and is urging companies and professionals throughout the construction supply chain to make a similar commitment by ‘taking a stand’ on an issue they passionately believe will help propel the industry towards a more sustainable future. Join us in taking a stand.
www.futurebuild.co.uk
•
As the construction industry looks to develop more energy efficient buildings that are fit for the UK’s net-zero future, Resideo is on hand to support with a range of heating controls and technologies that can help end-users manage their energy consumption.
Resideo has recently supplied it’s Honeywell Home evohome smart system to Bellway’s ‘Future Home’, part of the Energy House 2.0 research project in Salford, UK. Selected for its smart zoning technology, the evohome uses radiator controllers to wirelessly measure and control temperatures for up to twelve zones individually.
Resideo’s team will be showcasing the Honeywell Home evohome at Futurebuild 2023 on stand M12, alongside their latest range of product innovations
•
•
•
•
•
One of the West Midlands’ fastest-growing providers of affordable homes and social housing has completed a £15m deal to build a new ‘Extra Care’ development in Shropshire.
Keon Homes, which has already seen turnover rise by 33% to £25m in 2022, has purchased land off Bloor Homes at its Hutchinson Gate site in Newport and will now work with The Wrekin Housing Group to deliver a scheme of 70 properties and a host of communal facilities.
Ideally situated just a ten-minute walk into the market town, Queenswood will provide high quality living space and wraparound care and support for people over the age of 55, offering a mix of one and two-bed apartments, private gardens and a café.
Groundworks have already started, with a 20-strong team on site from March with the aim to complete the development in spring 2025.
Queenswood will be the first ‘Extra Care’ scheme completed by Keon Homes, with a second development set to be announced shorly.
Moving into this area of development will help the business capitalise on recent expansion and increase turnover past £25m in 2023.
A 100-tonne bridge deck is being constructed at Everton Stadium to assist with site logistics and provide a vital link to the scenic western wharf in the final scheme.
The concrete bridge in the north west corner, which will eventually provide part of the route for the team coaches arriving the stadium, is being put in place early into the build to assist with the flow of site traffic.
It also serves as a conduit for the utilities and an array of cables, which will connect the outside broadcast compound on the yet-to-be-developed western wharf to all camera positions within the 52-888-seater stadium.
And a change to the original design means the new bridge, which complements the existing isolation structure in the south west of the site, meets sustainability measures by improving the flow of water through neighbouring docks and helping to stimulate marine life.
Gerald Knights, Structures Engineering Lead for Laing O’Rourke, explained: “The bridge is fundamental to the operation of the stadium. It allows a one-way flow of traffic around the stadium, so vehicles can come in on the north side and leave via the south, or loop around the western wharf.
“It’s also a conduit for all the utilities that come from the outside broadcast unit, which sits on the western wharf, and the bridge carries all of the electrical and communication cables into the stadium. Originally, there was another type of structure designed in this location, which would have de-linked some of the water connectivity between the two adjacent docks.
We changed that and turned it on its head and built this structure which spans over the water now, and allows the marine life to repopulate the channel.
The bridge, sitting atop six concrete piles bored 16 metres underground, is made up of four precast concrete beams, each weighing around 28 tonnes and with a span of 15 metres.
“That makes it quite a substantial structure, but one that is more costefficient and sustainable than the previous version that was on the table,” added Knights.
“We are constructing it now because it becomes important for logistics. Once we have the utilities in and we have built the bridge deck, we will be able to start putting traffic on this bridge and it will give us the flexibility, later on, to be able to excavate out around 15,000 cubic metres of earthworks to create the new water channel and a new habitat for all the species that will move into this area. We’re hoping to get it ready for use in January of next year, and then we should be able to see traffic on it not long after.”
Leading Northern Ireland investment company Wirefox has confirmed its £45 million 11-storey Grade A office development ‘The Paper Exchange’ is due for completion and will launch early in the new year.
Construction got under way on the 200,000 sq ft office development in Belfast city centre in February 2020.
Located in the heart of Belfast city centre on Chichester Street, it is Belfast’s largest speculative office development and will house up to 2,000 people once fully occupied.
Co Derry building firm Heron Bros was appointed to carry out the development and around 100 construction jobs were involved in the build process.
Designed by Wirefox and TODD Architects, around 150,000 sq. ft of the mixed-use scheme is office accommodation.
The company also confirmed that it had acquired 35-47 Donegall Place in Belfast city centre for an undisclosed sum.
A consortium including Bywater Properties, LRE Capital and Belfast-based Ashmour had previously acquired this prominent site in 2015.
Since then, it has been extensively repositioned and refurbished.
The former bank building, known as 35DP, is a prominent five-story retail and Grade A office space, encompassing 80,000 sq ft, which fronts on to both Donegall Place and Fountain Street, and is located just seconds from Belfast City Hall.
Consisting of three retail units on the ground floor, including flagship store Boots which has occupied the building for 55 years, and four upper floors of distinctive, flexible and modern air-conditioned office accommodation, the property recently benefited from an extensive repositioning and refurbishment by GRAHAM Interior FitOut ahead of its sale.
Main tenant Boots signed a new 10-year lease for the building in 2020.
Around 100 jobs were created during the construction phase which was undertaken by local contractor Heron Bros. The Paper Exchange can accommodate up to 2,000 people.
Wirefox said its ownership of 35DP will complement The Paper Exchange, its newest state-of-the-art Grade A professional office development.
The revised plans to dramatically transform the Oxford and Gloucester buildings on Chichester Street to Grade A office accommodation were approved in November 2019. Around 100 jobs were created during the construction phase which was undertaken by local contractor Heron Bros. The Paper Exchange can accommodate up to 2,000 people.
Both 35DP and The Paper Exchange are being marketed for lease by Savills and Colliers International in Belfast.
Wirefox was advised throughout the acquisition of 35DP by leading local legal firm Davidson McDonnell and by ASM Accountants.Global modular building specialist, Volumetric Building Companies, has developed and launched the first modular prototype for a new hotel concept to help accelerate the expansion of the Fairfield by Marriott brand across Europe.
Fairfield by Marriott is Marriott International’s second largest brand based on the number of hotels, with over 1,200 properties worldwide.
The new 136 guestroom prototype modular hotel has been developed to reflect the principles of European architecture and design, and to deliver fast and adaptable construction using advanced offsite manufacturing technology.
Marriott estimates that the offsite solution will reduce the build programme by around eight months for earlier trading which will have a hugely beneficial impact on revenue and cashflow for developers and operators.
The modular approach to construction will allow the flexibility to adapt the
design to specific site requirements and the needs of each local market. It will be financially competitive to build and operate, generating value for owners and providing consistent quality and service for hotel guests.
This application of advanced modular technology will help to address some of the challenges facing developers – construction will be faster, acoustics are improved with less noise transmission between modules, and quality is more consistent.
The Fairfield by Marriott hotel concept has been designed by Marriott for urban locations and secondary or tertiary cities across Europe, specifically targeting the more mature hotel markets in the UK, Ireland, France, and Germany.
Paul Thomas, Vice President for International Hotel Development at Marriott International, said, “We are extremely pleased with the partnership with VBC and are keen to build on our longstanding relationship. Following this collaboration, we have now launched the first approved modular hotel room in Europe for the fast-growing Fairfield brand. This is a very appealing offer for hotel investors, owners, and franchisees in terms of design, branding and pricing.”
“We think the time is right for expansion of this upper midscale, select service hotel brand across Europe and the prototype has already generated significant interest from developers. This is a highly efficient economic model which will deliver strong results for investors and hotel owners.”
Andy Smith, UK Director at VBC said, “This application of advanced modular technology will help to address some of the challenges facing developers – construction will be faster, acoustics are improved with less noise transmission between modules, and quality is more consistent.”
“Manufacturing the hotel rooms in a controlled factory environment means a reduced carbon footprint and less waste. And by maximising work offsite, developing constrained urban locations is also much easier – from airport sites to out-of-town business parks.”
“This design has been localised and developed specifically for the European market, with different room sizes, fixtures and fittings to the US Fairfield model.
“The prototype was very well received with real excitement when we showcased it in Gdansk in Poland and at an investor event in Munich.”
The prototype hotel room manufactured by VBC reflects the design philosophy of the Fairfield by Marriott brand and is furnished in a contemporary style with a Scandinavian aesthetic.
Each steel-framed module contains a fully furnished room, ensuite, hallway, and corridor section. The VBC system is suitable for hotels up to 20 storeys.
All the furniture and the ensuite for the hotel rooms would also be manufactured inhouse by VBC and installed offsite for a faster, more efficient, and seamless service, and a repeatable quality of finish.
There are two room layouts for the new European prototype hotel which are efficiently designed to deliver exactly what guests want, combined with operational efficiencies and maximum room count.
When designing car park solutions, health and safety considerations are of paramount importance. For car park users, the deck plays a very important role in safety due to the potential of slips and skid risks posed by water and/or slippery automotive oils lying around. Parking has become a vital part of today’s world and as a result, vehicle owners are looking for safe and secure environments to house their vehicles when they are not with them.
Slip resistance is a key safety consideration and a must-have for all car park decks. The decking system needs to have suitable slip resistance not only for foot traffic, but also vehicular traffic to ensure safe movement around the car park. Slips, trips, and falls are both painful and costly accidents and vehicle skidding accidents are no different. When considering safety in car park design, customer interface areas such as stairwells and walkways should be equally considered with extra attention given to turning circles. Slip resistance is a challenge in these areas and more problematic because car tyres need adequate gripping support.
It is important to ensure that the car park is designed to be easily accessible and navigable for all users,
including those with mobility impairments. It is also important to ensure that the car park is well-lit and colourful both to improve visibility and to deter crime. This may involve clear marking with bright demarcation lines and signage, to provide a welcoming impression to drivers.
When considering safety in car park design, customer interface areas such as stairwells and walkways should be equally considered with extra attention given to turning circles.
Finally, ensure that the car park is regularly maintained and inspected to identify and address any potential hazards. By prioritizing accessibility, slip resistance, clear marking, lighting, and regular maintenance, it is possible to create a car park that is safe and welcoming for all users.
Consider Flowcrete’s Deckshield car park protection systemsdesigned with safety in mind.
Sean Esslemont who studies at Moray College and works for Elgin-based McDonald & Munro, lifts Silver Award.
Three Scottish plumbing apprentices, all of whom are employed by SNIPEF members, qualified for the top eight at the UK WorldSkills final held last month at Middlesborough College.
And one of them, Sean Esslemont, who studied at Moray College and is employed by Elgin-based McDonald & Munro Limited, secured a much-coveted Silver Award for his performance.
The two other Scots finalists were Kayne Forsyth of North East College Scotland, employed by Old Meldrum, Aberdeenshirebased Camwater Ltd, and Jack Forbes of Edinburgh College, who works for A Alexander & Son (Electrical) Ltd of Glasgow.
All three SNIPEF competitors were supported by their college lecturers as well as SNIPEF’s Training Manager, Dale Thomson.
He said: “To have three out of eight finalists in this highly regarded UK-wide skills contest, all employed by SNIPEF members and trained at three Scottish colleges, is a great tribute to, and a fantastic reflection of, the high quality of work and training conducted in Scotland.
“It was inspiring to see our SNIPEF apprentices demonstrate their skills under close inspection by industry experts on a series of challenging practical tests and be assessed on their individual knowledge, practical skills and employability attributes against set criteria in a competitively timed environment.”
Paul Dodds MBE, a WorldSkills Judge, said: “The quality of work at the competition this year was of a very high standard and is the closest we have had for many years.”
Fiona Hodgson, SNIPEF Chief Executive, said: “We congratulate Sean, Kayne and Jack on their hard work throughout the competition. All three SNIPEF apprentices did an amazing job to be in the top eight apprentice plumbers in the UK and we are all very proud. We would also like to congratulate Craig Fairweather,
who works for SNIPEF member McDonald & Munro Ltd alongside Sean Esslemont, for picking up the gold medal in the electrical installation competition at the WorldSkills UK Finals.”
David Smith, Finance Director at leading minerals processor, Kilwaughter Minerals has been recognised at the 2022 Institute of Directors Northern Ireland (IoD NI) Director of the Year Awards.
David, who joined Kilwaughter in 2020, was named winner of the Young Director of the Year category at the annual ceremony which took place at the Merchant Hotel, Belfast.
The prestigious awards seek to reward the successes of directors representing a wide spectrum of businesses, organisations and sectors within Northern Ireland.
Speaking following the awards ceremony, David said: “I am very honoured to have been presented with this award and would like to congratulate all other winners on their success.
“I would also like to extend my thanks to the entire Kilwaughter team as this recognition reflects the company’s commitment to the
continued professional development and career progression of all within the business.
As we head towards 2023, Kilwaughter is dedicated to ensuring ongoing growth and development and we look forward to continuing to deliver innovative and high-quality service and products to our valued customers right across the UK and Ireland.
“The development of our ESG strategy is a key part of our journey and we are excited to extend our commitments to our local
communities and environments. We remain focused on the strategic investments that we have planned throughout the coming months and years to ensure that we remain primed to lead our industries.”
Established in 1939, Kilwaughter Minerals Limited is a quarry and mineral processor headquartered on a 75-acre site in Larne, Co Antrim, Northern Ireland.
The company services a growing customer base with products such as through-colour renders, external wall insulation systems, soil health conditioning minerals and livestock bedding lime solutions to control bacteria.
This follows several other recent award wins for Kilwaughter Minerals including Community Business of the Year and Large Business of the Year at the 2022 Larne Business Excellence Awards.
The business was also recognised as one of Ireland’s Best Managed Companies as part of a prestigious awards programme led by Deloitte Ireland.
Meadfleet has been selected as a finalist in the SME category of the 2023 EDIE Awards. These awards recognise sustainability leadership and celebrate organizations that take a responsible and innovative approach to the environment and climate change.
Meadfleet is dedicated to sustainability and longterm management of the 545 acres in its care.
The company’s goal is to reduce its environmental impact and maximize the benefits of green spaces for biodiversity and the fight against climate change.
Since 1995, Meadfleet has been appointed by local authorities and developers to manage and maintain public open spaces, creating a legacy for stakeholders, protecting the developer’s brand, and creating an environment that its customers value. The company currently cares for approximately 320 developments across England and Wales, which have a variety of multi-faceted requirements, including biodiverse species habitat, extensive woodlands, wildflower meadows, and sustainable drainage systems.
At the heart of Meadfleet’s agenda is the enhancement of biodiversity in its open spaces. The company’s ecology team, led by qualified ecologists, has assessed and benchmarked all its developments to identify and implement opportunities to increase biodiversity, often going above and beyond the requirements of planning permission and the original design brief. So far, the company has enhanced around 15% of grassland areas to improve their biodiversity value and has earmarked a further 37 acres for enhancement.
Meadfleet’s teams are also trained in readiness for the forthcoming Biodiversity Net Gain regulations.
Recognising the role of trees in helping mitigate climate change, Meadfleet is committed to protecting, sustaining, and enhancing all trees and wooded areas under its management, and it takes a proactive approach to tree management.
The company launched its Bee Friendly campaign in 2019, partnering with Buglife, the UK’s leading insect charity, to create and promote additional pollinator habitats and provide customer and community engagement activities.
As part of its efforts to educate and engage with its customers and the wider community, Meadfleet hosts educational talks, bat walks, and planting days for schools and community groups. It also provides free wildlife resources, advice, and thousands of items including bird feeders, bird boxes, insect hotels, and wildlifefriendly seeds.
Meadfleet is also dedicated to reducing its carbon footprint and supporting climate action. In 2021, the company committed to the United Nations Climate Neutral Now Pledge and achieved Carbon Neutral status. It supports a UN offsetting scheme that supplies local communities in Malawi with improved fuel stoves, helping children stay in education, creating safer homes, and reducing the use of timber. Meadfleet also donates to a sustainable planting programme and has contributed over 2,300 trees to date.
The company is thrilled that its efforts have been recognized by the judges of the EDIE Awards and looks forward to the awards ceremony in March.
Thomas Bishop-Rowe
Three apprentices who work for a property maintenance company have won awards from the college where they study.
Sam Cooper and Thomas BishopRowe, apprentice property maintenance operatives at Platform Property Care - a subsidiary of Platform Housing Group, one of the UK’s largest social landlords – have both been awarded Apprentice of the Year, Level 2, Year 2 from Herefordshire and Ludlow College; last year Sam was awarded a Best Progress Award.
Thomas Mills – another apprentice property maintenance operative from the firm – was awarded a Best Progress Award.
Platform Housing Group has worked closely with Herefordshire and Ludlow College for more than 15 years, seeing many apprentices complete their studies with its support in areas including plumbing and heating, electrical and carpentry. In 2020, the two organisations worked together to introduce the property maintenance operative – or PMO – role into Platform Property Care under the apprenticeship umbrella.
The college awards take place annually to reward the students for their hard work.
Platform Housing Group has a very close relationship with Herefordshire and Ludlow College and has been offering apprenticeships across the construction industry including carpentry and joinery, electrical installation, plumbing and more recently a newly created Property Maintenance Operative.
Employees from Vistry South East have completed an epic 20-mile trek through the Peak District in aid of the Youth Adventure Trust.
Two teams from the Caterham-based region of the national housebuilder Vistry Group embarked upon the charity’s annual Housebuilder Challenge in September, raising a combined total of £5,000.
The 12 Vistry staff members made up two of the 45 teams from housebuilding companies across the country that took part in the event for the trust, which helps vulnerable young people in Wiltshire and Swindon.
Walkers set off from Castleton in the early hours of the morning and trekked northwards via Edale to the finish at Torside Reservoir near Glossop.
M Group Services secured an impressive four out of seven category wins at the Street Works Awards recently.
Morrison Water Services, a part the Group’s Water Division, scooped three awards, for Sustainable Methods, Innovation Excellence and Communications and Community Engagement.
Morrison Energy Services, part of the Group’s Energy Division, took home the Training Scheme of the Year trophy for its Gas Trainee Scheme in partnership with SQS.
Overall, M Group Services had an impressive 15 entries shortlisted in the seven award categories. In addition to the four wins, Morrison Water Services was highly commended in the Training Scheme of the Year award category for its Visible Streetworks programme, educating people about the challenges of navigating street works with visual impairment and disability.
Morrison Water Services and Galliford Try as a joint venture, was also highly commended in the Project of the Year category for its work in partnership with Southern Water to install 560
metres of pumping main along a main road in Chichester.
Working on behalf of client Cadent on the London CMO, Morrison Energy Services was highly commended in the Communication and Community Engagement Award for its work replacing 100-year-old gas mains in the busy Portobello Market area and in the Innovation Excellence Award, for its Kobus pipe puller.
The Sustainable Methods Award was presented to Morrison Water Services and Yorkshire Water for their partnership to deliver a drinking water spray lining programme, believed to be the first of its kind across the water sector, in AMP7.
Targeting structural and water quality issues within the existing pipework, spray lining is part of a £2m programme targeting 14km of pipework over the coming year for Yorkshire Water.
Spray lining provides significant reductions in carbon, cost and time. It also reduces the disruption for customers, in comparison to the time and extent of Street Works needed for pipework excavations and traditional replacement schemes.
five hours 56 minutes and nine hours 15 minutes respectively.
The Youth Adventure Trust has been supporting 11 to 16-year-olds in Wiltshire and Swindon since 1992.
The punishing route included a total ascent of 1,154 metres and took in the three highest peaks in the national park - Kinder Scout, Higher Shelf Stones, and Bleaklow.
The two Vistry teams completed the challenge in second and 20th places, after finishing the gruelling challenge in
The charity helps up to 360 young people each year develop resilience, confidence and skills through its three-year Youth Adventure Programme, which involves residential camps and activity days.
The trust’s Housebuilder Challenge is now in its fourth year and has raised over £400,000 to date. More information about the charity can be found at www.youthadventuretrust.org.uk
Expert appointment builds on Kier Construction’s strategic capability.
Kier has appointed Anna Baker as head of sustainability for its Construction business. This latest appointment builds on the Group’s newly formed Responsible Business team and underlines its commitment to sustainably delivering infrastructure which is vital to the UK.
Anna will be responsible for delivering Kier Construction’s targets as part of the Group’s ‘Building for a Sustainable World’. These include achieving net zero carbon across business operations by 2039, eliminating avoidable waste by 2035, the delivery of 30p in every £ of impactful social value, and helping customers deliver on their sustainability targets, working with them to co-create sustainability solutions.
Prior to joining Kier, Anna was at Careys where she headed up their sustainability team. With over 17 years’ experience in the sector, Anna has extensive experience in developing and delivering sustainability
strategies, as well as sustainable procurement. At Kier, she will also play a key part in supporting its clients and supply chain to deliver their sustainability plans.
Louisa Finlay, managing director of Clients and Markets at Kier Construction, said: “I am delighted Anna is joining us to spearhead sustainability in our Construction business. Sustainably delivering infrastructure which is vital to the UK is at the heart of our purpose.
“We are committed to supporting the transformation of this industry, through net zero carbon solutions and leaving lasting legacies through our work.
“Anna’s drive to really make a difference and proven ability to see the big picture will complement the work being done across the Group to achieve our targets in sustainability.”
Anna Baker added: “This is an exciting time to join Kier, a business I’ve long admired. With so much great work already underway, I’m looking forward to bringing my experience to the role and leading on the next steps of Kier’s
sustainability journey for the Construction business.”
Kier’s focus on sustainability has seen it recently deliver the UK’s first Passivhaus leisure centre, as well as introducing a number of carbon reduction measures, including a no idling policy across all of the Group’s sites, offices and depots.
order book of profitable work, we needed someone who really understands how we work.
“Kyle has successfully led on reshaping the how the business financials are managed and reported, and with that and his impressive work ethic, he was very well positioned to take on the role of Commercial Director. The Board had no hesitation in appointing him. With Kyle now in role, I firmly believe we’re in a safe pair of hands for our next phase of growth.
Leading East Midlands contractor Kori Construction has bolstered its Board of Directors with the appointment of a new Commercial Director.
Kyle Fielding has been promoted to the Board to support the main contractor in achieving its ambitions growth plans for the years ahead.
Kyle first joined Kori Construction in 2019 as a senior quantity surveyor, replacing the company’s Managing Director Jordan
Connachie in the role. Key achievements since then include overhauling the business’s financial reporting processes and leading on the development of the commercial team, taking it from two individuals to five.
According to Jordan Connachie, these achievements made him the natural choice for the role of Commercial Director.
Jordan said: “The business has grown exponentially since Kyle joined back in late 2019 and with a large, secured forward
Kyle said he was delighted to be joining the board at such an important time in the company’s development.
“Kori Construction is really starting to make a name as a main contractor with a pipeline of work across many parts of the UK,” he said. “The business is at a pivotal point and being appointed to the board at this time offers a really exciting challenge. I’m looking forward to working with the other board members to help shape the future for Kori Construction and achieve or exceed our growth plans.”
I would like to take this opportunity to thank him for his hard work and dedication over the past three years and congratulation him of this well-deserved promotion.Kyle Fielding
Highly-experienced sales specialist Glyn Goodwin has joined Access Platform Sales as the company’s sales manager for SouthEast England.
Glyn brings more than 40 years of experience selling powered access platforms to APS, for both manufacturers and distributors, and in the hire industry.
He takes over from Lee Louder who has retired from his position as APS’s southern sales director.
APS Managing Director Steve Couling said: “We’re delighted to welcome Glyn to APS. His industry and technical knowledge is secondto-none. Glyn’s expertise will be a huge asset for our clients, because our service is based on giving them the best long-term advice on platform investment, so they can grow successful businesses.”
Glyn Goodwin said: “I’m looking forward to building APS’s presence in the South-East England powered access market.
“With high-performance brands like LGMG and Hinowa to offer, I believe there is huge potential to build market share.”
The 57-year-old, who lives in Ash, Surrey, currently works at Vistry Southern’s Catherington Park development in Waterlooville, where the region’s construction director Steve Ott presented him with £2,000 and a bottle of Champagne.
Frank joined Try Construction in 1997, and with Galliford Try he spent 12 years working on a programme of improvement works at the All England Lawn Tennis Club in Wimbledon.
Vistry Group was formed in 2020 from the merger of Bovis Homes and Galliford Try’s housing businesses and incorporates Bovis Homes, Linden Homes and Vistry Partnerships.
Frank said: “It’s great to have a job in a fun, fast-paced environment, as I don’t actually feel like I’m working. I enjoy forklift driving, and I’ve been doing it so long now that no one has to tell me what to do or how to do it.
“It didn’t make much of a difference to me when Linden Homes and Bovis Homes joined under the Vistry Group, as it’s still the same demanding job that I love.
“Vistry has been the best company I’ve worked with, as they let me get on with my job the way I like to do it.
My favourite part of the job is the people, as it’s usually the same team on the job, and I know everyone so well now that it feels like one big family. I was pleasantly surprised that Steve came to see me in person to congratulate me, and it really made me feel appreciated by him and the company.
Dawnet Mclaughlin, managing director of Vistry Southern, said: “It’s rare to come across people who are as dedicated and trustworthy as Frank, and his efforts have not gone unnoticed.
“It can be tough to stay in the same place for a long time, but I don’t think the word ‘tough’ is in Frank’s dictionary!
“He is so conscientious and skilled at his job and is still performing each job to a high standard.
“His site managers don’t even need to tell him what to do – he just knows.
“Frank’s work ethic is unsurpassed, and every company would be lucky to have an employee like him. We sincerely appreciate his hard work and efforts year after year.”
Access rental customers are focused, right now, on three things - performance, value, and service support, including fast order fulfilment - and APS delivers on all three, he added.
Glyn Goodwin said: “LGMG platforms across the range of scissor lifts and boom lifts are just what customers want right now - easy-to-use, high quality, high performance platforms, with good availability.
APS is the UK’s largest independent access sales specialist. It is the authorised UK and Ireland distributor for platform manufacturers LGMG, Hinowa and BoSS, and UK distributor for Wienold Lifte material lifts.
Hinowa is cementing its position as a market leader with exciting new products ready for launch in 2023, which I’m looking forward to presenting to the marketplace.Frank Bates Glyn Goodwin Telescopic forklift driver Frank Bates has been thanked for the 25 years of service he’s given to his company.
This research and innovation project has considered solutions around new concrete technologies to reduce the carbon content of currently used conventional Portland cement concrete and steel reinforcement. We aimed to explore the adoption of low carbon materials for use in reinforced concrete with at least a 50% CO2eq reduction over current conventional practice.
The reduction in capital carbon emissions sits within the National Highways environment and wellbeing designated fund plan and concrete is one of the major sources of capital carbon within infrastructure. This project aimed to focus on reducing this capital carbon, initially for use in temporary works, where design constraints are less onerous, and subsequently within permanent works.
The project aimed to build a better understanding of the use of Basalt Fibre Reinforced Polymer (BFRP) reinforcement in Alkali-Activated Cementitious Material (AACM) concrete to enable widespread, low-risk use for temporary works structures that would inform future use in permanent structures. Further to this, it worked towards the potential adoption of corrosion free reinforcement; addressing the requirement to develop longer lasting materials in construction and reduce maintenance of concrete roads.
Carrying out this trial would enable a better understanding of the impact of the use of these materials ahead of the new Eurocode 2 standards that are currently being drafted to incorporate composite materials.
What were the main factors that needed considering before carrying out the trial?
The objective of the trial was to evaluate the performance of a combination of AACM geopolymer concrete and BFRP composite reinforcement for an optimised low-carbon solution. Investigating the performance of this combination of materials through full scale site trails and rigorous laboratory testing would help us develop a better understanding of the of these new materials to enable confident use.
The project was considered to build knowledge of cure, functional properties and
structural behaviour. Our benchmark was a traditional reinforced concrete slab using steel mesh in a Portland Cement / GGBS based concrete mix, designed with a similar strength. It was also considered that at the end of its life, the feasibility of recycling through planning, for re-use of the arisings as a graded sub-base type material, should be investigated. Alongside the conventional tests for fresh concrete, test panels and samples were manufactured to test flexural, shear and pull-out performance.
For permanent structures, the benefit of corrosionfree composite reinforcement is well understood and offers a reduced maintenance cost.
However, there appears to be uncertainty, gradually being addressed by research, regarding whether AACM geopolymers will inhibit the corrosion of steel reinforcement over time. The use of corrosion free BFRP reinforcement is believed to mitigate this risk. We considered it was necessary to carry out literature study research and document the veracity of the above understanding for steel in AACM geopolymers; this would then be used within comparative Assessment of environmental performance for a typical permanent structure.
It was considered that the success of this innovation project would be measured by the generation of recommendations for further research that would enable other schemes to utilise these materials. The key consideration was that to provide sufficiently robust performance data for this combination of materials to National Highways as a starting point for them to assess their use in their permanent works.
Were there any obstacles/problems?
The greatest problem encountered was with the theoretical design approach for a BFRP reinforced AACM concrete slab.
Initially, it was proposed to design a slab arrangement that comprised
1. Ground bearing pavement area
2. Bridging section over some notional buried service
Various design standards would be used to provide equivalent designs for the combinations of material. The trial road slabs would be designed to carry 32 tonne 4- axle rigid heavy goods vehicles (HGVs) as a typical load case.
Initially, the slab was modelled as a beam on springs, with the ground represented by spring stiffnesses, to determine the design effects for the slab. From this analyses moment and shear design values were determined.
It was anticipated that the steel reinforced sections would be designed using EC2 and the BFRP reinforced sections using ACI 44015. It was anticipated that the load factors effects would be reduced from the normally applied values, by the same proportion, in order to cause a higher degree of utilisation in the constructed slabs. The design outputs could be compared to see if there was an equivalence in the proposed designs.
Whilst it was possible to design comparable sections for flexural resistance, shear resistance was more of a problem. The reduced axial stiffness of the FRP reinforcement significantly reduces the concrete shear resistance of those sections. It was found that, unless links were to be added to the design, it was necessary to increase the slab thickness significantly
to produce a slab design that could carry the loads on the bridging section. This meant it was no longer feasible to produce directly comparable designs. The thicker slab depths would produce slabs that were sufficiently robust that the differences in the reinforcement selection was not significant.
At this stage it was decided a different approach was required and a ground bearing solution, without a bridging slab, was preferred. The use of a technical report (TR66) was applied to the design. This method provides a simple pavement design for relatively lightly loaded pavement slabs and hard standings. The method provides tabulated designs based on TRL methods. Analytical designs were not produced for equivalent alternative slab constructions. The decision was taken to provide a material ‘like for like’ in that the same depth and strength of concrete was reinforced with the same areas of reinforcement of the two different types.
Observations would evaluate whether a design incorporating the same strength concrete and same area of reinforcement behave in a noticeably different way.
What were the main outcomes of the trial?
• The failure mode of all test panels was as expected. The steel reinforced panels failed by yielding of the steel rebar and the BFRP reinforced panels by crushing of concrete in the compression zone.
• All panels carried more than the predicted failure loads.
• The BFRP reinforced panels experienced greater deformation but partially recovered when unloaded. The steel reinforced panels failed by yielding of the steel, as expected, and had no recovery.
• The CIIIA/BFRP mix test panel carried a higher failure load than the AACM/BFRP panel. This may be explained by the CIIIA mix concrete having a higher strength at time of testing than the AACM mix slab.
• The failure mode of all test panels was as expected.
• The steel reinforced test panels failed at lower loads than predicted.
• The BFRP reinforced panels failed at significantly higher loads than expected.
How vital is it for the industry to reduce carbon?
It is hugely vital that we all drive to reduce carbon.
We are awash with statistics surrounding carbon but as a couple of rough figures to put things in perspective, the construction Industry is responsible for approximately a third of energy demand and around a third of process-related CO2 emissions.
Furthermore, 4-8% of the worlds CO2 emissions are attributable to the production of concrete, half of which is emitted through the manufacturing process of cement clinker. Something can be done about this and we have a responsibility as leaders in our industry to act.
Our trial produced a long list of areas requiring further work. Too many to list here. However, in direct reference to the two main materials being trialled the suggested areas for further work are as follows.
The trials have highlighted a number of areas for further consideration when conducting live trials on AACM concrete.
• Effect of ambient temperature, -5˚C to +30˚C
• Early life surface abrasion
• Surface damage due to rainfall during placement
• Freeze thaw resistance
• GGBS Characterisation and link to early strength gain / maturity curve
• Taking samples and/or testing to assess long term durability
• Use of AACMs in Cement Bound Granular Material (CBGM) and Roller Compacted Concrete (RCC)
Based on experimental work with BFRP and work with industry on its properties and characteristics, a number of key areas have been summarised for further research:
• Identification of lower carbon footprint resins
• Research into fibre optic sensors (For use in smart bars, structural health monitoring etc)
• The automation and upscaling of BFRP reinforcement and mesh production
• Comparison of sand coated bar with bar with spiral windings particularly with regard to pull-out test performance
• Pull out tests with varying reinforcement diameters and embedment depths
Other materials also need to be considered in this field. Graphene, Limestone and Clay to name a few.
One product (Concretene) although in very early stages of development, when added in very small quantities to a concrete mix, does exhibit promising properties worthy of detailed further assessment. The product is also storage stable.
Further work could include targeted graphene trials to consider various concrete properties, workability, live time (the time fresh concrete remains workable) and ease of pumping.
Portland Limestone Ternary cements (BS EN 197-5) – lower carbon footprint
• These products are likely to be included and published in BS8500 by Q2 2023
Calcined clay
• As a replacement for GGBS in the future.
In Machelen, Belgium, the first symbolic metre was laid of the longest bicycle and pedestrian bridge in Flanders. As part of the consultancy consortium MoVeR0 and commissioned by De Werkvennootschap, architectural studio ZJA produced the architectonic design for the cycle bridge over the A201 Leopold III-Laan in Brussels. With a total length of 710 metres – a deck 510 metres long and sloping approaches of 200 metres – the bridge is a striking feature in the urban landscape. Construction starts in December and the bridge will be open for use in 2024.
Imposing bridge with V-shaped columns Ralph Kieft, architect and partner at ZJA, says, ‘To make this imposing bridge fit its surroundings, we gave it as light and transparent a silhouette as possible. To achieve this, the white bridge is made of steel and rests on V-shaped grey steel columns with cut-away corners. With its gradual gradient in a continuous upward curve and its perfectly straight trajectory, the
Architectonic design: architectural studio ZJA as part of the MoVeR0 consortium, which is made up of Sweco, Arcadis, ZJA, Frank van Hulle, Cluster and Mint
Commissioned by: De Werkvennootschap
cycle bridge makes a long, fluid gesture that marks the boundary between Flanders and the Brussels-Capital Region.’
Pedestrians as well as cyclists can use the bridge. It has a cycle path and a footpath, distinguished from each other by their coloured surfaces. The cycle path is a brownish yellow or light ochre, and the footpath is anthracite in colour. This distinction ensures a safe and easily legible layout on the bridge. At its highest point, over the highway where cars and trams pass, the deck is almost eight metres above street level. The steps that give access to the bridge at the tram stop match the design and appear transparent. They are also elongated and shallow enough to ensure a comfortable climb to the bridge deck.
Because the bridge is so long and straight, its details, which repeat many times along the length of the bridge, create a fascinating visual effect. The corbelled ribs under the deck, supporting the pedestrian footways, have a fixed rhythm and they flow into the balustrades. The resulting impression is
of a regular rhythm that conforms to the fluid line of the bridge deck as it rises, making the bridge seem lighter, floating above the highway and pointing towards the horizon.
The bicycle and pedestrian bridge A201K designed by ZJA not only creates a safe crossing of the Leopold III-Laan, it forms a previously missing link in the cycle network in and around Brussels. The new bridge will improve the accessibility of the surrounding area and the quality of life there, and in particular the traffic safety and mobility of cyclists and pedestrians.
The bicycle and pedestrian bridge A201K is part of the programme ‘Work on the Ring’, with which De Werkvennootschap intends to create better mobility on and around the ring road that encircles Brussels, and to improve the quality of life for those who live there. To achieve this, investment will be made in the coming years in better public transport, the redevelopment of the Ring and safe, rapid connections for cyclists.
In the construction industry, mobile space systems such as site offices, welfare facilities, canteens, workshops and accommodations play a crucial role on every construction site.
One of the “major players” in the market is the cabin, container modular building manufacturer CONTAINEX.
Continuity in product development is one of the strengths of CONTAINEX. Our customers and trading partners can be confident that spare parts –from small parts to entire wall panels – are available for many years.
At the same time, thanks to the flexible panel system, the modules can be designed in a way so complex configurations can be achieved – from single cabins to large modular buildings in various specifications including fire protection and energy efficiency. Later changes to the layout of the building can be carried out easily.
Modules and containers from CONTAINEX can be used in a number of ways: as office and sanitary facilities on construction sites, on company premises and at events, but also as residential modules, additional classrooms or nurseries, sports clubs or as temporary office space during renovations.
Thanks to the high-quality CDC undercoat and the top powder coating, CONTAINEX cabins and containers are not only extremely durable, but also available in a variety of RAL colours and can also be “branded” with large logos.
For more information, visit our website at www.containex.com.
Henry Boot Construction has completed work on a new £9m Special Education Needs (SEN) learning centre on Buckingham Road in Headingley.
Located in the Ford House building on Buckingham Road, the venue is to be known as Headingley Learning Centre and is the third SEN campus of West Oaks School.
Established in 1977, the Ofsted ‘Outstanding’ SEN school also has campuses located in Woodhouse and Boston Spa and delivers accessible learning environments for 500 pupils aged between 2 and 19.
Having started the project back in November 2021, Henry Boot Construction completed phase one of the work in time for the start of the school year in September, before completing the final phase of work earlier this month.
Purchased by Leeds City Council in 2020, Ford House is an 1850s Grade II Listed manor house set within leafy grounds. Leeds City Council partnered with West Oaks School and Henry Boot Construction to complete the necessary work to transform the facility into a contemporary SEN campus –significantly furthering the SEN provision in the city.
The modernisation of the 2,800 sqm building, which included new heating
systems and insulation throughout, had to be carefully balanced with the restoration of the building’s attractive heritage features.
All lime plastered walls, roof tiles, woodwork, sash windows, staircases and ceiling cornicing had to be reviewed and then carefully repaired or replaced – utilising the exact materials and construction methodology defined in the Listed status.
The building’s two striking tower turrets, located approximately 50 metres from ground level, had to be removed via crane lift and then refurbished and recoated off-site by a specialist heritage contractor.
The new campus is now home to around 120 West Oaks pupils, who have access to the very latest therapeutic and training services. The new facility includes high-quality classrooms, curriculum-focused outside play areas, a multi-use games area, interactive activity zones and exhibition space.
A ‘morning mile’ activity path was also created around the site perimeter, providing an important outdoor walking and running track for the pupils.
Yorkshire-based Henry Boot Construction and West Oaks School worked closely with Leeds Local Education Partnership to deliver this project.
Dudleys Consulting Engineers has completed works to facilitate the installation of a new £1 million elective care hub at Wharfedale Hospital in Otley. Two new temporary theatres have been installed on site by Leeds Teaching Hospitals NHS Trust to tackle the backlog of patients waiting for treatment.
Elective care hubs aim to create Covid-free sites, away from emergency care, providing safe spaces to help manage people who need elective procedures. The trust’s first hub has been installed at Wharfedale Hospital to provide additional theatre capacity to care for 15 to 18 patients a week requiring foot, ankle and upper limb procedures.
Working for main contractor, BAM Construction and Watson Batty Architects, Dudleys has consulted on all structural and civil engineering requirements for the install, including ground foundations, services integration, and firewall construction.
The process was managed to a fast-track timescale with police escort to delivery of the offsite manufactured ‘Vanguard’ units fully fitted out to surgical theatre requirements. Dudley was integral to a large team collaboration to ensure efficient
We were pleased to be a part of the professional team ensuring the rapid turn around of this important installation. There were a number of challenges including planning procedures, firewall construction to protect the existing hospital, and delivery of the units due to Storm Etna affecting the River Wharfe bridge, but we successfully completed the install with levelling and support blocks in place to allow fit out.
installation with minimal disruption to the 24-hour live hospital environment.
Andy Walker, Managing Director at Dudleys, commented, “We were pleased to be a part of the professional team ensuring the rapid turn around of this important installation. There were a number of challenges including planning procedures, firewall construction to protect the existing hospital, and delivery of the units due to Storm Etna affecting the River Wharfe bridge, but we successfully completed the install with levelling and support blocks in place to allow fit out.”
The new theatres are expected to be ready for use by the end of the year. Dudleys is a Leeds based company offering Structural and Civil engineering advice across the UK. Established more than 12 years ago, the privately owned consultancy employs a team of 25 highly skilled engineers. It operates in all key real estate sectors including healthcare, residential, industrial, commercial, retail and education.
Key healthcare development projects include Wharfedale View for Leeds City Council, Riverbank Care Home in Hull and Queenshill Care Home in Leeds. Other key clients include developer CEG, Bettys & Taylors of Harrogate, Leeds Bradford Airport, Leeds United Football Club, Arla Foods and Unilever UK.
Winvic Construction Ltd, a leading main contractor that specialises in the design and delivery of multi-sector construction and civil engineering projects has been appointed by IM Properties to deliver phase three of Hinckley Park. Winvic has returned to the 82-acre Hinckley Park to construct the speculative 340,000 sq ft logistics and manufacturing unit with IM Properties targeting Net Zero Ready in line with the UK Green Building Council (UKGBC) framework.
The delivery of Hinckley 340 is on the remaining 18 acres at Hinckley Park, located next to Junction 1 of the M69. The park is home to DPD who has one of Europe’s largest and most technically advanced parcel depots and a 532,000 sq ft unit let to Amazon. Winvic constructed both of these facilities.
Winvic will be constructing the BREEAM Excellent and EPC A rated Hinckley 340 in line with the UK Green Building Council (UKGBC) framework for IM Properties to target Net Zero Ready by achieving Net Zero in Construction and introducing renewable tech into the building specification.
The unit has two-storey office space totalling 14,000 sq ft, a 3,000 sq ft pod office, a haunch height of 15m, 30 docks, and parking for 305 cars and 54 HGVs.
Winvic commenced earthworks for this next phase at Hinckley Park in September 2022 and will conclude the contract with the final landscaping works in November 2023.
In addition to Hinckley 340, phase three will also include two other, Net Zero Ready smaller buildings of 47,000 sq ft and 60,000 sq ft.
Working in partnership, Winvic and IM Properties continue to play an active role in the community, committing through an Employment and Skills Charter to provide training and employment opportunities for local businesses and individuals during construction.
Winvic’s Head of Industrial, Distribution and Logistics, Danny Nelson, commented: “Our relationship with IM Properties continues to go from strength to strength, and once again we’re delighted the leading developer has put its trust in us to construct a new industrial and manufacturing facility with sustainability at its heart.
“We work extremely well together due to our values being aligned – from meeting quality and commercial goals to social value and sustainability targets – and the whole team is looking forward to completing the remaining external works in June and the unit in late 2023.”
Balfour Beatty VINCI (BBV) has launched a new partnership with STEM Returners to help STEM professionals return to work after a career break.
BBV, a joint venture between Balfour Beatty and VINCI is HS2’s construction partner for the West Midlands. As part of their continued drive to enhance inclusion and invest in people, the organisation will offer a STEM Returners programme for a CAD Technician, Performance Reporting Manager, Site Engineer, and other roles to work on the West Midlands section of HS2’s Phase One route. This section spans around 90km from Long Itchington in Warwickshire to the centre of Birmingham and on to Handsacre in Staffordshire.
STEM Returners will source candidates for the programme, which aims to return or transfer STEM professionals back into industry following a career break. The fully paid placements act as a ‘returnship’, allowing candidates to be re-integrated into an inclusive environment upon their return to STEM.
Natalie Desty, Director of STEM Returners, which is based in Hampshire,
said: “Vacancies in the construction sector remain high as demand for workers continues to outstrip supply. But there is a hidden workforce that are overlooked because they have a gap on their CV.
“We are very proud to be entering this new partnership with BBV, to return highly skilled people back into the industry they love. Only by partnering with industry leaders like BBV, will we make vital changes in STEM recruitment practices, to help those who are finding it challenging to return to the sector and improve diversity and inclusion.”
The STEM Returners programme is BBV’s latest drive to enhance equality and diversity across their sites. BBV has recently achieved Gold standard for ED&I (equality, diversity and inclusion) from Clear Assured, a global inclusion standard.
Annual research from STEM Returners (The STEM Returners Index) has revealed the challenges people who have had career break face, when trying to return – recruitment bias being the main barrier to entry. Sixty-six percent of STEM professionals on a career break said they are finding the process of attempting to return to work either difficult or very
difficult and that nearly half (46%) of participants said they felt bias because of a lack of recent experience.
STEM Returners’ programme aims to eliminate these barriers, by giving candidates real work experience and mentoring during their placement and helping them to seamlessly adjust to life back in work.
Whilst the scheme helps solve the challenge of sourcing talent in sectors that need it, it also has the added benefit of increasing diversity in a host organisation. STEM Returners’ population of experienced professionals who are attempting to return to work are 46% female and 44% from ethnic minority groups, compared to 14% female and 9% from ethnic minority groups working in industry.
Since STEM Returners first launched in 2017, more than 310 STEM Returners candidates have joined programmes across the UK.
To view STEM Returners opportunities, visit https://www.stemreturners.com/ placements/
RHP Group has awarded Kier Places a £75m ten-year contract to deliver repairs, voids and planned works across its housing portfolio of c.10,000 affordable homes in the boroughs of Richmond, Hounslow, Kingston and Hillingdon.
As part of RHP Group’s large scale improvement plan, Kier Places’ skilled teams will carry out works to upgrade homes, including installing new kitchens and bathrooms, as well as making properties more energy-efficient.
Working in partnership with RHP Group, Kier Places will also support residents and the wider community with a range of social value commitments. This will include providing employment and skills opportunities, including apprenticeships. Kier Places will also work with local supply chain partners and support a number of local community schemes.
Iain Roy, operations director at Kier Places, said: “We’re really proud to create this partnership with RHP, supporting their largescale improvement plan for residents. A firm focus on quality, building safety, and community engagement underpins everything we do at Kier Places, and we’ll use our extensive experience of working safely in people’s homes while also minimising disruption for residents.”
Lucy Graley, executive director of customer services at RHP Group, said:
We’re excited to start working with Kier. They stood out in the procurement process due to their passion for customer service, the quality of what they deliver and alignment with our values and culture. We see this new contract and working relationship as an opportunity to build on and improve our service.
Contract mobilisation has begun, with the commencement of services effective from 1 June 2023.
The appointment follows Kier Places’ appointment earlier this year to provide planned improvements under a seven year contract with West Midlands based housing provider, whg.
Building services and engineering consultants FHP has been appointed to support the £2.5bn design and construction of the UK’s first zero carbon mixed use development.
The move has seen FHP provide a package of RIBA Stage 5 electrical, mechanical, public health and design verification services for the Bankside Yards West project on the south bank of the River Thames. There, nine buildings that will provide housing for 650 homes along with 350,000 sq. ft. of office and commercial, cultural and retail space and leisure amenities, are under development as part of an ambitious regeneration project set to transform the local riverside area.
A key feature of the plans is sustainability, with the main Arbor office complex built to deliver a carbon neutral operation and
achieve BREEAM ‘Outstanding’ status. Through careful planning and design, 45% less carbon dioxide will be created during the building’s operation while a 30% reduction in energy consumption will also be achieved when compared to standard buildings.
FHP was appointed to by MEP SubContractor TClarke to provide MEP design expertise and technical services around the development of three new high-rise properties at the Western Yards site off Blackfriars Road.
The work included responsibility for RIBA Stage 4 design and involved verifying critical elements to facilitate a fully coordinated BIM model to LOD 400, which enabled drawings covering the fabrication, assembly, and installation of components to be finalised. Revit and fabrication elements were also utilised
as part of the MEP design completion process.
The Bankside Yards West development is the latest project success for FHP, which continues to see growth and expansion on the back of a pipeline of forward orders and investment in additional staff across its London and Leeds offices.
Tony Hewitt, managing director, said: “This is a high-profile project for us, reflecting our ability to maintain a strategic view of major development projects, while completing design verification work and coordinating MEP services to produce a successful, cost effective and ultimately sustainable solution for clients.
“We are continuing to develop our commercial offer and this latest success with Bankside Yards West comes at a time when we expect to see continued growth and investment over the next 18 months as we look to develop and secure further new work and expand our national operations.”
Developers claim the 1.4 million sq. ft. Bankside Yards site will be the UK’s first major mixed-use regeneration scheme with net zero ‘concept’ offices at the heart of a new generation of modern, green and healthy work and living space in the heart of London.
Robin Aves, divisional director at TClarke, said: “What a pleasure it was to work with FHP again on Bankside Yards following on from our previous successful projects.
“The relationship between us goes from strength to strength as the understanding of their designers of our requirements for an installation approach.
“FHP carried out the full coordination of the mechanical, electrical and ELVS packages on Bankside Yards and we look forward to working with the in the future on a number of varied projects within our business.”
Leading building services engineering practice, Tate Consulting, which expanded into Belfast earlier this year, has made four new appointments after winning a wide range of prestigious contracts.
Senior electrical engineer, Warren Smyth, intermediate mechanical design engineer, Tony Shek and graduate engineers, Ruari Mulvenna and Roger Dawson, are the latest new faces to join Tate Consulting in Belfast.
The Yorkshire headquartered company now employs a team of nine in its Belfast office, which is close to Belfast City Airport, in the Belmont Office Park on Belmont Road, and plans to recruit more mechanical and electrical engineers at all levels in the coming months.
The Belfast office is headed up by an experienced team comprising of Belfast born Jim Lee, who has been a board director at Tate Consulting for the past nine years, and associate director, Aaron Stevenson who brought more than 25 years’ experience to the firm. Well-known mechanical associate, Kevin Gallagher also joined the company earlier this year.
Hungerford-based developer David Wilson Homes has appointed a Sales Director to lead the teams at housing developments across the Southern region.
Emma Hawkins, who lives in Bristol, will be directing and supporting the sales teams at sites across Berkshire, Oxfordshire and Hampshire, including the homebuilder’s flagship Newbury Racecourse development.
From beginning her career in the hospitality sector several years ago, Emma realised she had a passion for interacting with customers and enjoyed the retail sales element of work.
It was her friends in the housebuilding industry who ignited her interest in the sector, and, having started her career as a Sales Adviser with David Wilson Homes over a decade ago, Emma has now moved to the developer’s Southern division to begin a new challenge.
The Sales Director role helps the housebuilder to ensure it delivers business targets and provides a great customer journey to its customers.
Emma said: “Throughout my time at David Wilson Homes, I have progressed by ceasing each opportunity whilst being open to receiving advice and coaching. I have worked with some great people who have mentored me and assisted with my development as a person and in my career.
“I am really enjoying my new role, and my favourite part of the job is visiting the sites and helping to develop the sales teams, watching them succeed in their own roles whilst hitting our targets.”
Emma added: “David Wilson Homes looks after its employees and has a clear strategy. You know what is expected of you in your role and as a business.
“For other people looking to join the housebuilding industry, I’d say go for it! It’s a great sector to work in with a huge variety and no day is the same. As a business and team, my hopes for the future are that we are able to remain focused and motivated going forward and build strength within the team to be the best.”
• Sizes range from the smallest GX84 up to the largest GX126.
The GH Range:
• Boasting 7 model options, 6 sizes - from the small but mighty single axle 6x4’ GH64 to our largest tri-axle workhorse 14x6’
• One of the highest payloads on the Market
• Fully galvanized welded chassis
• Durable leaf-spring suspension
• A choice of sliding skids or full width ramp that can be further enhanced with an aluminium treadplate floor, additional low level lashing points or a toolbox
• Larger models also come with a beavered rear floor section to reduce loading angle with enhanced grip for slippery conditions
• Constructed from folded pre-galvanised steel sections with filled-in sides for greater flexibility
• Trailers are offered with hinged adjustable skids or a full width loading ramp.
• The trailer can be further enhanced by accessories such as a ladder rack, aluminium treadplate floor covering, mesh side extensions
• Standard with three pairs of integral lashing points attached to the body of the trailer.
• GX Models are available with maximum gross weights of 2700kg and 3500kg.
Ifor Williams Trailers – for a trailer that never lets you down.
The Elephant & Castle Shopping Centre first opened its doors in 1965, hosting 115 shops. As needs have evolved over the last 55 years, specialist construction and engineering firm, Keltbray, is demolishing the disused centre to pave the way for a new high-rise development, offering dining options, retail space and 979 new homes.
The redevelopment is part of a £4bn town centre regeneration scheme, featuring the high-rise development, a new tube station for the Northern Line and a new university building.
As part of this regeneration, SOCOTEC Monitoring has been awarded the structural monitoring contract for the construction phase of the works, which will run until 2025. This continues SOCOTEC’s involvement in the development, having already supported with the demolition works that have been ongoing since 2020. Within this element of the project, SOCOTEC was working alongside the client, demolition contractors (including Keltbray) and the engineering designer, WSP. This includes condition surveys and ongoing monitoring. In 2022, the construction phase (including basement excavation, superstructure construction and fit out) of the project has started.
SOCOTEC has continued to work alongside the engineering designer, WSP, and the construction contractor, Multiplex, to collaboratively design a monitoring system based on WSP’s ground movement assessments. The site is in a very congested area of London’s transport network with LUL Bakerloo and Northern Lines, TfL stations and Network Rail assets, all of which are in close proximity. In addition to this, there are multiple other aboveground assets, pavements, vent and lift shafts.
The main requirements of the monitoring system are to:
• Confirm that the structural movements are in line with the predicted ground movements
• Ensure significant movement is identified early to enable sufficient mitigation measures
• Provide evidence to be used if damage occurs.
SOCOTEC was awarded the contract due to its innovative system design, which was developed alongside WSP and suppliers in order to maximise quality data and minimise installation and ongoing costs. This included both automated and manual surveys, as well as a combination of sensors and analysis to calculate convergence, which was partially necessitated by tight restriction in some of the LUL assets. SOCOTEC worked with key suppliers from Osprey Measurement, Geosense, Sick sensors and Topcon in order to design the system that will now be installed.
The construction phase will continue until at least 2025. During this time, SOCOTEC will continue to work alongside the various stakeholders to maintain and manage the system and the data. All data is being delivered to the stakeholders via SOCOTEC’s Calyx Online Monitoring Software™. This platform allows for alarms, reporting and analysis on the data, and SOCOTEC’s in-house engineering team will also review the data daily to better inform decisions.
The complex combination of multiple stakeholders, bespoke systems, challenging installation execution
and ongoing support requirements is increasingly common in demolition and construction monitoring. With integration capability, experience and proactive innovation, SOCOTEC Monitoring offers clients a service set apart from other monitoring providers and equipment manufacturers.
“This is a challenging project to specify the right monitoring systems to mitigate the risks of both demolition and construction phases,” said John Richmond, associate director, WSP.
As with other projects, working with SOCOTEC Monitoring has helped ensure a fit-for-purpose system that is able to be delivered in line with the client’s requirements, ensuring that the right data is available.
Dave Jones, senior project manager, SOCOTEC, added: “Like many other large central London construction projects, the logistics of installing the monitoring system is challenging. The team has great experience in building, testing and installing the equipment in the most efficient way. Our Calyx software team is then able to get the client(s) the data that they need to safely continue with the project construction.”
We offer same and next day dispatch on a wide range of galvanised Feeder Pillars and Belisha Beacons and proper After Sales Service from people who care.
Our versatile and popular BD and useful Mini Pillar SDMP Ranges are in stock for you to order with most arriving next day! In addition, our Bespoke and Made to Order sizes are available from just 2 weeks!
Our reliable LED Belisha Beacon - AmberGLO8 and our LED Illuminated Column version - OlympiadIPB are also available from just 2-3 days from order* in most cases. We also have spares and extras like our LED Lumos4 Crossing Spotlights, Courtesy Shields and also our 4w LED Beacons for retro fitting for both Belisha and Refuge Beacons. All manufactured by us to Highways specifications.
Our high quality products for a wide variety of purposes from Highways & Streetlighting, EV Charging and Outdoor Power & Leisure to Sports Facilities, Car Parks, Markets are proving popular.
We’ve been celebrating our 40th year in business this year at Fisher & Company and we’ve been busier than ever with returning customers and new business alike. Our high quality products for a wide variety of purposes from Highways & Streetlighting, EV Charging and Outdoor Power & Leisure to Sports Facilities, Car Parks, Markets are proving popular.
We were also proud to receive our certification for Quality Management System ISO 9001:2015 this year, so you can be assured that both the service and product you receive is top notch and that we work to a consistent high quality. We also know that when things go wrong you need to be able to trust that the company you have ordered from will not ignore you and will work with you to resolve the problem – we won’t leave you high and dry or ignore your calls! We’ll always do our best to help you resolve any issue.
With costs rising across the board, getting the most from your investment is more important than ever.
As Stewart Gosling of RDD, UK importers of Mitsubishi Forklift Trucks explains: “Truck price and fuel costs are the headline items
when weighing up your options, but there’s much more to it than that. Safety, maintenance, downtime, and support are all factors that’ll affect your bottom line. Every Mitsubishi Forklift Trucks product that leaves the factory is designed for a long life of high performance and minimal downtime.”
For example, GRENDiA diesel and LPG counterbalance trucks offer exceptional fuel economy, low emissions and robust construction.
Over a typical 5-year span, electric trucks can offer savings in the thousands compared to IC engine equivalents. The EDiA electric counterbalance range — including the award-winning 5.5-tonne EDiA XL — not only matches IC engine trucks in terms of performance but adds a host of cuttingedge advanced features.
Stewart adds: “Where you acquire trucks is of huge importance. With Mitsubishi Forklift Trucks–authorised local dealers not only do you have a local point of contact who will understand your business and your specific requirements, but they also have the support of the UK Mitsubishi Forklift Trucks network. Make sure you look at the whole picture when making your next investment in equipment as the initial outlay never tells the whole story.”
Call the Mitsubishi Greenline on 0845 3713048 or visit www.mitsubishi-forklift.co.uk
The APP Group consists of Air Power Products (Compressed Air Specialist) and Procut Engineering (CNC Precision Engineering) and APP Site Services (Site Supplies and Tool Hire). The group benefits from a full-service department with a wealth of air and hydraulic tool knowledge. We provide an excellent service, not only with the range of products but with the level of care each order is given and the speed with which we can deliver.
The main focus of the business is the hire department for construction tools. The hire fleet has been built up over a long period of time and the tools are always fully serviced and inspected before every hire.
We have a range of tools and associated products available to hire which include Rebar Cutters, Rebar Benders, Hydraulic Splitters, and Pneumatic Picks.
We have a range of hydraulic rebar cutters to suit both factory and on-site applications that can cut up to 40mm Rebar. Designed for professionals that need to cut high tensile rebar in all environments.
We have a range of hydraulic rebar benders to suit both factory and on-site applications that can bend up to 40mm Rebar. Designed for professionals that need to bend high tensile rebar in all environments.
Splitters are handheld demolition devices which controllably split material with the use of hydraulic pressure. They are used when larger conventional demolition devices are ruled out due to their excessive dust, vibration, and flying debris.
The combi shears are the ultimate in handheld demolition. The interchangeable jaw sets mean that this machine is incredibly versatile and can cut and crush a wide range of materials.
We don’t just sell & hire the H11, We have a full range of medium duty demolition picks.
Above are just a few machines we have to offer. For our full range give the office a call on 01909 519 519. Most tools are available for Same Day or next day delivery.
As well as the hire fleet APP Site Services offer a range of site spillage solutions including the mobile spill kit. If you need further information on the range of spillage solutions we have to offer, please visit the website www.appsiteservices.co.uk
As part of the full package, we also stock a range of PPE equipment and workwear for our customers. If you are looking for gloves or a mask to go with your hire or purchase we have got you covered.
www.appsiteservices.co.uk
Tel: 01909 519 519
Everton Stadium is set to enter a transformative phase in 2023, with work ramping up on the internal works.
As the external appearance continues to develop, the race is on to make the build watertight to allow tradesmen to begin work in installing hundreds of miles of piping, wiring and the internal fittings.
“I think we should just warn spectators that in 2023 it will look like things are slowing down from an external perspective,” said Chief Stadium Development Officer Colin Chong.
In real terms, the fit-out is starting in January, when we will start putting all the wires and piping in. People won’t notice it as much, as it’s internal, but it’s equally as important to the stadium development as the roof going up.
“A big milestone that people will want to see is the east stand steelwork that will fill in the gap between the north and south steelwork. However, it will slow down externally, although internally it’s going to
be a hive of activity. In real terms, the fit-out is starting in January, when we will start putting all the wires and piping in.
“People won’t notice it as much, as it’s internal, but it’s equally as important to the stadium development as the roof going up.”
As with the external concrete and steel components, much of the internal walls are pre-manufactured in factory conditions and transported to site in justin-time slots for installation.
All mechanical, electrical and plumbing (MEP) systems in the stadium will be manufactured off-site in the Oldbury (West Midlands) factory of Laing O’Rourke’s specialist MEP business, Crown House Manufacturing.
The six-foot high modules and an innovative product called Techwall, will be delivered to site, lifted into place, connected and commissioned, in an approach that helps save time and energy.
The pipework will arrive pre-manufactured, tested in the factory, and be offered up and connected, so there are less connections throughout the whole building. There’s less welding, so less risk of fire and it’s the modern way of building things.
“There are life-safe systems, resilience to be planned, and all the toilets on the concourses will be coming in in modules, pre-manufactured,” explained Chong, in a special Club podcast on the stadium build.
“The pipework will arrive pre-manufactured, tested in the factory, and be offered up and connected, so there are less connections throughout the whole building. There’s less welding, so less risk of fire and it’s the modern way of building things.
“Again, we’ll be working on all four concourses simultaneously, along with the hospitality lounges starting, probably in March.
“The skeleton of the dressing rooms is already in place (in the west stand). We’ve got the pit for the hydrotherapy pools and all the apertures for all the incoming services.
“There are hundreds of miles of beer pythons that have to go in at some point and they’ll all start to go in next year.
“We ramp up with people and we’ll end up with 1,000 people there next year and probably up to around 1,400 on site the year after.
“There’s a whole host of things going to happen next year, but not a lot of people are going to notice it because it’s going to be hidden.”
Launched in January 2023 The Offsite Guide is the first B2B marketplace in the UK and Europe for MMC - a platform for businesses to explore options for using Modern Methods of Construction (MMC) and interact with specialist manufacturers.
As a marketplace TOG facilitates engagement between key market participants and drives awareness of the many benefits of MMC including more efficient production, economies of scale and repeatability. In doing so it provides a central point of reference for product variety, availability, & pricing specification. Crucially, it provides a platform for direct communication between a wide range of providers and their potential customers in this fragmented market.
At The Offsite Guide we attract and facilitate early interaction with customers, allowing manufacturers of commercial and domestic modular buildings and offsite solutions to showcase a range of their products & help educate potential customers.
“We provide a trusted platform not only for showcasing offsite construction, but also to facilitate initial dialogue and ongoing interaction between customers, manufacturers and MMC suppliers.” Ingrid Orbie – Director
For TOG Partners, listing MMC case studies & solutions on the Offsite Guide marketplace is a cost-effective method for manufacturers to bring in targeted traffic. Partners listings can easily be found under various search categories that can subtlety hand off and complement other marketing channels in the marketeer’s toolbox. Listing as a partner will also assist the partner company’s own website SEO ranking in an effective and cost-efficient way.
For companies offering products and services complementary to MMC, creating an entry in the TOG Directory is an effective way to promote to the sector. These offsite system & product suppliers include companies offering panellised systems, sub-assemblies & components, as well as site based MMC structural components. This also includes offsite main contractors & other professionals including main & general contractors, offsite/modular solutions, offsite consultants & engineers, offsite designers, and digital designers and architects. A wider group of offsite trades people are also included in the Directory such as groundwork companies,
electricians, carpenters, plumbers, landscape & external works contractors, flooring installers, painters & decorators, and all associated construction products like road signs, PPE, damage protection products, health & safety products.
Whether listing as a TOG Partner on the marketplace or as Advertiser in the Directory, TOG offers an opportunity to raise brand awareness, increase a company’s visibility and gain access to new customers. Through TOG’s marketing and launch promotion campaigns TOG is striving to elevate MMC sales channels and engage with the market in a more efficient and effective way.
Until now, there has been a lack of any resource for either private and commercial buyers to search & compare modular buildings and offsite solutions and engage directly with suppliers. The Offsite Guide provides this much needed resource in this fast-developing market.
Online marketplaces are prevalent in many different B2B and B2C markets and are globally recognised as efficient methods of delivering fast, efficient and timely market interaction. By bringing proven marketplace
technology to the MMC market TOG is strengthening the ecosystem of the MMC construction sector.
Housing associations (HAs), developers, builders, self-builders, schools and universities, suppliers, central and local governments are all seeking more sustainable and efficient ways of construction. The TOG marketplace facilitates that search for proven solutions and gives examples and case studies that show ways that organisations and developers can break tradition and drive efficiency using MMC. Ultimately this is a way to share information and experience, as well as to educate the market.
To find out more and to benefit from TOG’s marketing expertise in the built environment and the construction sector go to www.theoffsiteguide.com Partner and Advertiser eBooks can be downloaded from the site that give more detail of the services on offer.
The Build Chain, a unique online platform that connects contractors nationally to merchants locally, has credited the government’s Kickstart Scheme for helping it discover and offer permanent roles to two young people that have become an essential part of the company’s launch plans.
The Build Chain is a subscription-based online platform that connects contractors nationally to merchants locally. Through the easy-to-use dashboard, contractors can submit enquiries, which are then filtered quickly and efficiently to the correct suppliers or merchants. Likewise, suppliers benefit from contractor and sub-contractor enquiries targeted to suit their business, with filters ensuring the enquiry is within the serviceable location of the supplier and fit for their stock offering.
Laurence Anthony joined the business in January this year and Joshua Pell started in November 2021. Both have now taken on full-time permanent positions - Laurence as digital sales and marketing executive, and Joshua as technical support executive. Recognising the skills gap facing the construction industry and the need to equip young people with hands-on training, The Build Chain has provided valuable skills and the chance to develop their professional expertise.
Both Laurence and Joshua participated in the Kickstart Scheme, which was designed to empower young people into employment and incentivised businesses to hire 16-24-year-olds on Universal Credit and at risk of long-term unemployment. The scheme meant that the government covered six months’ salary for Laurence and Joshua and allowed the team to put more funds into growing the business.
Matthew McClune, co-founder and chief commercial officer at The Build Chain, said: “The Kickstart Scheme came at a great time for us as the business was in its early days and still finding its feet. At the time we were balancing on a tightrope between needing more support, but not having enough funds to hire for full-time positions.
“Laurence and Joshua more than filled the necessary gaps while the foundations of the business were being laid, and in doing so we’ve seen them develop their skillset and abilities.
“Once we gained more investment, we were able to increase their hours and salaries - rightly rewarding the loyalty, dedication, and enthusiasm they’d shown. It was an immensely gratifying experience for all of us as the work they had put in directly led to making hiring them as full-time employees possible.
“It was a well-deserved dividend of their hard work and really cemented them as part of the team.”
Laurence Anthony, digital sales and marketing executive, works on new user onboarding and user journeys, said of his experience: “The Build Chain offered me a great opportunity to develop and hone my skills and I’m in no doubt that it was the right choice for me.
In the past year I’ve seen first-hand what it takes to set up a successful business. The tasks I’ve been assigned have afforded me many opportunities to learn and gain confidence in areas I previously had no experience in. I feel reasons like this have given me a greater understanding of the bigger picture of how the moving parts of a business come together, and how to deliver against goals. I’m certain this insight will help me tremendously in my current and future career.
Joshua Pell, technical support executive, said: “Joining a small team like The Build Chain’s meant I had a genuine feeling that
the work I was doing had real impact. It also meant that whenever I needed help overcoming a challenge, there was always someone there to ask for help which is invaluable when you’re starting a new role.
“I now have a much clearer idea of what a career in this industry might look like and I’m looking forward to seeing and doing more every day.”
The Build Chain’s team is further expanding with the additional appointment of Oliver Brennan as data analyst, specialising in monitoring and discovering consumer efficiency trends.
Oliver’s appointment is indicative of further growth for the young business as they go from strength to strength.
Neil Sheldon, co-founder and chief operating officer at The Build Chain, said: “Hiring Laurence and Joshua full-time demonstrates the importance of supporting and fostering emerging talent and is a success story of how businesses can guide young people entering the workforce.
“With the recent addition of Oliver to the team, we’re looking forward to helping all three of them achieve their ambitions, helping develop their skills and experience further as they become more integral to The Build Chain.”
Does the thought of heading out onto site have a different appeal than it used to? Achy bones, sore muscles? Maybe it is time to come in from the cold and consider a role in teaching. And whilst doing so, you would impact the future of your community’s construction industry.
Like construction, the education sector experiences a nationwide industry skills shortage. Teachers with the right technical skills are necessary for students coming up the ranks to take on construction roles. The answer to filling the skills gap in construction and to future-proof its survival is to ensure younger generations come up through the ranks, starting at the grass root level. This is where we come in, sourcing people within the trade to get into teaching.
We need people from within the trade to teach
We work closely with further education colleges up and down the country, and they are always looking for teachers, lecturers, and assessors within the following sectors:
• Bricklaying
• Built Environment
• Civils
• Engineering
• Plumbing & Gas
• Carpentry/Joinery
• Electrical Installation
• P&D / Plastering
• Maintenance operations
If you have technical skills and good subject knowledge, you are a great communicator with good time management and organisation skills; teaching could be a good option for you. If you are already training apprentices and enjoy this element of your role, then the transition to the classroom may be an easy one.
For many colleges around the country, you don’t necessarily need teaching qualifications to teach; experience goes a long way.
How to make the transition
Whether you are looking to transition into a full-time role for a complete career change or taking on some part-time hours, there are many teaching options available. If you don’t have teaching qualifications, the first step would be to work alongside a lecturer as a technician or, in some cases, straight into a lecturing or assessing role.
How much could I earn?
The average starting salary for a STEMrelated full-time teacher is £32k.
The answer to filling the skills gap in construction and to future-proof its survival is to ensure younger generations come up through the ranks, starting at the grass root level. This is where we come in, sourcing people within the trade to get into teaching.
However, temporary positions are always available and offer excellent flexibility as well as highly competitive hourly rates of pay.
As you will be working with those under 18, you need to be enhanced DBS checked, which can be done very easily through us; we have a specialist in-house vetting team that can do this for you.
www.T15International.com
Two International Safety Workshops will be held in London. These events are organised by Efectis UK/Ireland and University College London (UCL) in close collaboration with other experts in various sectors, i.e., Industry; Academy; UK Government.
The workshops aim at dissemination beyond the-state-of-the art knowledge with the focus on Hydrogen and Building Safety. Please register via below links
• February 13, 2023: International Hydrogen Safety Workshop,
• February 14, 2023: International Building Safety Workshop,
For more details, please feel free to contact uk@efectis.com.
A construction director who started in housebuilding as a trainee 10 years ago has encouraged graduates and school leavers to consider a career in the industry.
Daniel Walker, Construction Director at Bellway North East, began his career in the housebuilding industry as a graduate with a degree in journalism from Teesside University.
The 32-year-old said he got into the industry after working for 18 months in a bank then taking a five-week trip to Australia.
Daniel, who lives in Medburn, said: “Banking was not for me so I went to Australia for an extended holiday to think about what I wanted to do. During the university vacations I had helped my dad who was a painter and decorator, so I had a leaning towards the construction industry.
“When I got back home in 2012, I applied for a place on a graduate trainee course with a housebuilder and after two years I qualified as an assistant site manager. Normally you get a position as a trainee assistant site manager but I had done so well they gave me the role straightaway. I knew I had found the career for me.”
Over the years, Daniel worked his way up to site manager before being promoted to contracts manager. He won a prestigious National House Building Council Pride in the Job Quality Award and a Seal of Excellence in 2017 and another Pride in the Job Quality Award in 2018. The chance to take the position as construction director at Bellway North East came along in 2021.
“I had already bought a Bellway house in 2019 when I was working for another housebuilder, so I was well aware of the quality of their homes,” said Daniel. “When I was offered the opportunity to join Bellway I jumped at the chance.
“I am a proud Geordie and Bellway is one of the Newcastle-based companies that everyone in the North East has heard of. It is a well-respected firm whose success is a real source of pride for Newcastle.
“In this industry, I have gone from a trainee to a construction director in charge of 15 developments in the region, in just a decade.
“I am living proof that the construction industry will offer you the opportunities and the training and will give you the reward if you put the hard work in.
What other career gives you the chance to build someone’s dream? The immense pride we feel when we see the happy faces of customers as we hand them the keys to their new home is unbeatable.
“I can honestly say that I believe I have the best job in the world. If you have talent, determination, and the desire to get stuck
in, then this industry could be the career choice for you as a school leaver or a graduate.”
David McCrindle, Managing Director of Bellway North East, said: “It is fantastic to have Daniel leading our construction team at Bellway North East. His passion for the North East, for the housebuilding industry and for Bellway shines through.
“His enthusiasm, dedication and attention to detail are an inspiration to everyone at the company. Daniel’s rapid rise from graduate trainee to construction director is a perfect example of how this industry can provide a dynamic career. We are very excited about the future and are sure that, under Daniel’s leadership, greater success awaits Bellway North East.”
For more information about careers at Bellway visit https://www.bellwaycareers.co.uk
Daniel Walker, of Bellway North East, whose career has taken him from graduate trainee to construction director in just 10 years.